夹杂物形成机理
连铸外来夹杂物的形成机理

外来夹杂物的形成机理
外来夹杂物主要是钢水生产过程中因外部因素产生或带入的化学和机械作用产物。
连铸坯中夹杂物的数量与钢水成分、耐火材料质量、中间包结构、钢水浇注方式、保护浇注和炉渣成分等因素有关。
外来夹杂的形成特点是:
(1)组成复杂,一般是多种氧化物组成的复合相。
(2)颗粒尺寸大,夹杂物颗粒一般大于50μm。
如Al2O3 簇状夹杂的当量直径达到400μm,含Ca、Al、Si、Mn 的氧化物直径达200μm。
(3)形状不规则,有球形、多角形等。
(4)在钢中呈偶然性分布。
与小夹杂物均匀弥散分布不同,外来夹杂物在钢中零星分布,经常出现在表层附近。
(5)平衡氧差异,二次氧化是钢中溶解元素与空气中O2 之间的平衡,空气中O2 可源源不断供给钢液进行氧化反应生成二次氧化产物。
外来夹杂物总是与实际操作相关,通常可以根据它们的尺寸和化学成分判断出它们的来源,而且它们的来源主要就是二次氧化、卷渣、包衬侵蚀和化学反应。
夹杂物的生成及控制

夹杂物的生成及控制作者:shicm 发表日期:2007-5-28 阅读次数:7631 非金属夹杂物情况及分类按其化学成分组成和结构可以分以下几类(1)氧化物夹杂:单一金属氧化物、硅酸盐、尖晶石和各种钙铝酸盐;(2)硫化物夹杂:MnS、CaS等,在轧制过程中具有良好的变形能力;(3)磷化物夹杂:CaP、BaP等还原脱磷产物,在一般钢种中较少出现;(4)氮化物夹杂:TiN、ZrN等夹杂物,是钢液从大气中吸氮的产物;(5)含不同类型夹杂物的复合夹杂。
按其来源主要分为两类:(1)外来夹杂物,主要来源为炉渣卷入钢液形成的卷渣、钢液或炉渣与炉衬耐火材料接触时的侵蚀产物、铁合金及其它炉料带入的夹杂等等,在浇铸过程未及时上浮而残留在钢中,它偶然出现,外形不规则,尺寸大,危害极大;(2)内生夹杂物,在液态或固态钢中,由于脱氧和凝固时进行的各类物理化学反应而形成的,主要是和钢中氧、硫、氮的反应产物,它的形成有四个阶段,钢液脱氧反应时形成的成为原生(一次)夹杂;出钢和浇铸过程中温度下降平衡移动时形成的成为二次夹杂;钢水凝固过程中生成为再生(三次)夹杂;固态相变时因溶解度变化而生成的成为四次夹杂;由于一次、三次夹杂生成和析出的热力学和动力学条件最有利,因此可以认为内生夹杂大部分是在脱氧和凝固时生成的,因此控制夹杂最主要的就是要加强脱氧和严格防止二次氧化。
(3)一些尺寸较大的多相复合结构的夹杂物,有时是不同类型的内生夹杂复合而成,有时则是内生夹杂物与外来夹杂物互相包裹而形成的。
为了方便生产评级和比较,按照标准评级图显微检验法根据夹杂物形态和大小分布将夹杂物分为A、B、C、D、DS五类,这五大类夹杂物代表最常观察到的夹杂物的类型和形态:—A类(硫化物类):具有高的延展性,有较宽范围形态比(长度/宽度)的单个灰色夹杂物,一般端部呈圆角;—B类(氧化铝类):大多数没有变形,带角的,形态比小(一般<3),黑色或带蓝色的颗粒,沿轧制方向排成一行(至少有3个颗粒);—C类(硅酸盐类):具有高的延展性,有较宽范围形态比(一般>3)的单个呈黑色或深灰色夹杂物,一般端部呈锐角;—D类(球状氧化物类,如钙铝酸盐):不变形,带角或圆形的,形态比小(一般<3),黑色或带蓝色的,无规则分布的颗粒;—DS类(单颗粒球状类):圆形或近似圆形,直径>13μm的单颗粒夹杂物。
钢中夹杂物知识.
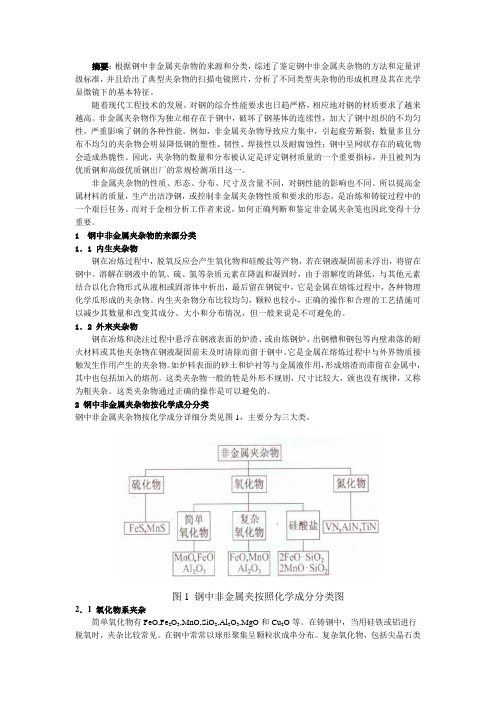
摘要:根据钢中非金属夹杂物的来源和分类,综述了鉴定钢中非金属夹杂物的方法和定量评级标准,并且给出了典型夹杂物的扫描电镜照片,分析了不同类型夹杂物的形成机理及其在光学显微镜下的基本特征。
随着现代工程技术的发展,对钢的综合性能要求也日趋严格,相应地对钢的材质要求了越来越高。
非金属夹杂物作为独立相存在于钢中,破坏了钢基体的连续性,加大了钢中组织的不均匀性,严重影响了钢的各种性能。
例如,非金属夹杂物导致应力集中,引起疲劳断裂;数量多且分布不均匀的夹杂物会明显降低钢的塑性、韧性、焊接性以及耐腐蚀性;钢中呈网状存在的硫化物会造成热脆性。
因此,夹杂物的数量和分布被认定是评定钢材质量的一个重要指标,并且被列为优质钢和高级优质钢出厂的常规检测项目这一。
非金属夹杂物的性质、形态、分布、尺寸及含量不同,对钢性能的影响也不同。
所以提高金属材料的质量,生产出洁净钢,或控制非金属夹杂物性质和要求的形态,是冶炼和铸锭过程中的一个艰巨任务。
而对于金相分析工作者来说,如何正确判断和鉴定非金属夹杂笺也因此变得十分重要。
1 钢中非金属夹杂物的来源分类1.1 内生夹杂物钢在冶炼过程中,脱氧反应会产生氧化物和硅酸盐等产物,若在钢液凝固前未浮出,将留在钢中。
溶解在钢液中的氧、硫、氮等杂质元素在降温和凝固时,由于溶解度的降低,与其他元素结合以化合物形式从液相或固溶体中析出,最后留在钢锭中,它是金属在熔炼过程中,各种物理化学瓜形成的夹杂物。
内生夹杂物分布比较均匀,颗粒也较小,正确的操作和合理的工艺措施可以减少其数量和改变其成分、大小和分布情况,但一般来说是不可避免的。
1.2 外来夹杂物钢在冶炼和浇注过程中悬浮在钢液表面的炉渣、或由炼钢炉、出钢槽和钢包等内壁肃落的耐火材料或其他夹杂物在钢液凝固前未及时清除而留于钢中。
它是金属在熔炼过程中与外界物质接触发生作用产生的夹杂物。
如炉料表面的砂土和炉衬等与金属液作用,形成熔渣而滞留在金属中,其中也包括加入的熔剂。
钢中夹杂物的产生与去除途径
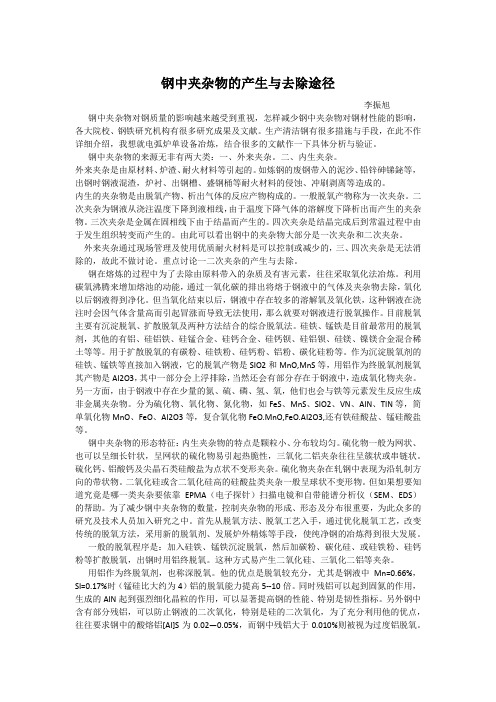
钢中夹杂物的产生与去除途径李振旭钢中夹杂物对钢质量的影响越来越受到重视,怎样减少钢中夹杂物对钢材性能的影响,各大院校、钢铁研究机构有很多研究成果及文献。
生产清洁钢有很多措施与手段,在此不作详细介绍,我想就电弧炉单设备冶炼,结合很多的文献作一下具体分析与验证。
钢中夹杂物的来源无非有两大类:一、外来夹杂。
二、内生夹杂。
外来夹杂是由原材料、炉渣、耐火材料等引起的。
如炼钢的废钢带入的泥沙、铅锌砷锑鉍等,出钢时钢液混渣,炉衬、出钢槽、盛钢桶等耐火材料的侵蚀、冲刷剥离等造成的。
内生的夹杂物是由脱氧产物、析出气体的反应产物构成的。
一般脱氧产物称为一次夹杂。
二次夹杂为钢液从浇注温度下降到液相线,由于温度下降气体的溶解度下降析出而产生的夹杂物。
三次夹杂是金属在固相线下由于结晶而产生的。
四次夹杂是结晶完成后到常温过程中由于发生组织转变而产生的。
由此可以看出钢中的夹杂物大部分是一次夹杂和二次夹杂。
外来夹杂通过现场管理及使用优质耐火材料是可以控制或减少的,三、四次夹杂是无法消除的,故此不做讨论。
重点讨论一二次夹杂的产生与去除。
钢在熔炼的过程中为了去除由原料带入的杂质及有害元素,往往采取氧化法冶炼。
利用碳氧沸腾来增加熔池的动能,通过一氧化碳的排出将熔于钢液中的气体及夹杂物去除,氧化以后钢液得到净化。
但当氧化结束以后,钢液中存在较多的溶解氧及氧化铁,这种钢液在浇注时会因气体含量高而引起冒涨而导致无法使用,那么就要对钢液进行脱氧操作。
目前脱氧主要有沉淀脱氧、扩散脱氧及两种方法结合的综合脱氧法。
硅铁、锰铁是目前最常用的脱氧剂,其他的有铝、硅铝铁、硅锰合金、硅钙合金、硅钙钡、硅铝钡、硅镁、镍镁合金混合稀土等等。
用于扩散脱氧的有碳粉、硅铁粉、硅钙粉、铝粉、碳化硅粉等。
作为沉淀脱氧剂的硅铁、锰铁等直接加入钢液,它的脱氧产物是SIO2和MnO,MnS等,用铝作为终脱氧剂脱氧其产物是AI2O3,其中一部分会上浮排除,当然还会有部分存在于钢液中,造成氧化物夹杂。
夹杂物分析实验报告

一、实验目的本次实验旨在通过对不同材料中的夹杂物进行观察和分析,了解夹杂物在材料中的形态、分布及对材料性能的影响。
通过对实验数据的分析,为材料的质量控制和性能改进提供依据。
二、实验原理夹杂物是指材料中非金属或金属的微小颗粒、液滴或气泡等杂质。
夹杂物在材料中会对材料的力学性能、耐腐蚀性能、电学性能等产生不良影响。
本实验采用扫描电子显微镜(SEM)和能谱仪(EDS)对材料中的夹杂物进行观察和分析。
三、实验材料与方法1. 实验材料:本次实验选取了三种不同类型的材料,分别为A356铝合金、20MnCr5齿轮钢和60Si2Mn-Cr弹簧钢。
2. 实验方法:(1)样品制备:将实验材料制成金相试样,经镶嵌、抛光、腐蚀等工艺处理后,用于夹杂物观察。
(2)夹杂物观察:采用扫描电子显微镜(SEM)观察材料中的夹杂物形态、分布及大小。
(3)夹杂物成分分析:采用能谱仪(EDS)对夹杂物进行成分分析。
四、实验结果与分析1. A356铝合金夹杂物分析通过SEM观察,发现A356铝合金中的夹杂物主要为块状、针状和片状。
EDS分析结果显示,夹杂物主要成分为Al2O3、MnS和MgO等。
2. 20MnCr5齿轮钢夹杂物分析通过SEM观察,发现20MnCr5齿轮钢中的夹杂物主要为Al2O3-MnS复合夹杂物、MnS夹杂物和镁铝尖晶石等。
EDS分析结果显示,夹杂物主要成分为Al2O3、MnS、MgO和CaO等。
3. 60Si2Mn-Cr弹簧钢夹杂物分析通过SEM观察,发现60Si2Mn-Cr弹簧钢中的夹杂物主要为MgO-Al2O3尖晶石、CaS 和硫化钙等。
EDS分析结果显示,夹杂物主要成分为MgO、Al2O3、CaS和S等。
五、结论1. 夹杂物在A356铝合金、20MnCr5齿轮钢和60Si2Mn-Cr弹簧钢中均存在,且形态和成分有所不同。
2. 夹杂物对材料的力学性能、耐腐蚀性能和电学性能等产生不良影响。
3. 通过控制材料的生产工艺,如控制合金元素含量、优化熔炼工艺等,可以有效降低夹杂物含量,提高材料质量。
ZL114A合金“高密度夹杂”的形成原因及消除

ZL114A合金“高密度夹杂”的形成原因及消除李沛森;耿莹晶;陈岩;任广笑;栗胜;李清群;申孝立【摘要】针对ZL114A合金生产过程中易产生的高密度夹杂的形成机理和消除方法进行分析研究.通过元素组成分析发现该“高密度夹杂”主要由Sb、Ti、Sr元素组成,通过熔炼过程的各工步取样,试样内部组织探伤分析,认为高密度夹杂是合金元素及中间合金未充分熔化造成的.根据分析结论,进行工艺改进,产品缺陷明显得到了改善.【期刊名称】《山西冶金》【年(卷),期】2019(042)001【总页数】6页(P12-16,19)【关键词】ZL114A;高密度夹杂;分析【作者】李沛森;耿莹晶;陈岩;任广笑;栗胜;李清群;申孝立【作者单位】山西江淮重工有限责任公司, 山西晋城048008;山西江淮重工有限责任公司, 山西晋城048008;山西江淮重工有限责任公司, 山西晋城048008;山西江淮重工有限责任公司, 山西晋城048008;山西江淮重工有限责任公司, 山西晋城048008;山西江淮重工有限责任公司, 山西晋城048008;山西江淮重工有限责任公司, 山西晋城048008【正文语种】中文【中图分类】TG132.3+2ZL114A合金是在ZL101A的基础上增加合金元素镁的含量而发展的品种,其强度比ZL101A更高,而且具有Al-Si系铸造铝合金铸造流动性好、气密性好、收缩率低和热裂倾向小、可热处理强化、较好的机械加工性能、良好的耐腐蚀性能和焊接性能等特点,被广泛应用在航空、航天、武器装备、汽车工业和电子电气等领域中[1]。
虽然该材料具有良好的铸造性能和机械性能,但为达到高性能,合金熔炼过程熔体均匀化、纯化和凝固组织晶粒细化等过程控制复杂,变质处理和精炼处理影响因素多不易掌握,制备的材料中易形成高密度夹杂。
高密度夹杂指的是材料和产品上通过X射线发现的一种缺陷,属于夹杂类缺陷。
是铸件内有成分、结构、色泽(以及局部性能)不同于基体金属、形成形状不规则、出现部位不确定的金属或金属间化合物杂质[2]。
底吹转炉钢中液相夹杂物的形成机理与控制方案

底吹转炉钢中液相夹杂物的形成机理与控制方案概述:底吹转炉是一种常用的钢铁冶炼设备,用于生产高品质的钢材。
然而,在底吹转炉生产过程中,钢中的液相夹杂物(如硫化物、氧化物等)的形成是一个常见的问题。
这些夹杂物会对钢的性能产生负面影响,因此了解液相夹杂物的形成机理以及控制方案对于提高钢的质量至关重要。
一、液相夹杂物的形成机理1. 成分:液相夹杂物的成分多种多样,其中包括硫化物、氧化物、碳化物、氮化物等。
这些夹杂物的形成主要与原料、炉料中的杂质以及底吹转炉操作参数有关。
2. 吸附和浮力:液相夹杂物的形成机理主要包括吸附和浮力两个方面。
原料和炉料中的杂质元素(如硫、氧、碳等)在钢液中会被吸附到夹杂物表面,形成液相夹杂物。
另一方面,炉底的浸没情况和钢液的流动状态会影响夹杂物的浮力,进而影响夹杂物的分布和浓度。
3. 变质作用:液相夹杂物的形成还与一些变质作用有关。
例如,底吹转炉中的氧化作用会导致氧化物的生成,而硫的存在会促进硫化物的形成。
此外,一些合金元素的加入也会影响液相夹杂物的形成机制。
二、控制液相夹杂物的方案1. 原料净化:为了控制液相夹杂物的形成,可以从原料净化入手。
采用高质量的生铁、废钢和合金元素,控制其中的杂质含量,可以有效减少液相夹杂物的形成。
2. 炉料配制:合理的炉料配制有助于控制液相夹杂物。
通过选择合适的炉料化学成分,控制硫、氧等元素的含量,可以减少夹杂物的生成。
3. 操作参数控制:底吹转炉的操作参数对于液相夹杂物的形成也起着重要的作用。
通过调整炉压、炉料粒度、渣化特性等操作参数,可以控制钢液的流动状态,降低夹杂物的生成。
4. 渣化控制:合理的渣化控制能够减少液相夹杂物的形成。
通过选择适当的渣剂和合理的渣化方式,提高渣中的还原性和脱硫能力,可以减少夹杂物与渣中元素的反应,从而减少夹杂物的形成。
5. 合金元素的加入:合适的合金元素的加入可以改善钢液的质量,并减少液相夹杂物的形成。
例如,加入硅、钙等元素可以提高夹杂物与钢液之间的界面能,减少夹杂物的生成。
钢中夹杂物知识

摘要:根据钢中非金属夹杂物的来源和分类,综述了鉴定钢中非金属夹杂物的方法和定量评级标准,并且给出了典型夹杂物的扫描电镜照片,分析了不同类型夹杂物的形成机理及其在光学显微镜下的基本特征。
随着现代工程技术的发展,对钢的综合性能要求也日趋严格,相应地对钢的材质要求了越来越高。
非金属夹杂物作为独立相存在于钢中,破坏了钢基体的连续性,加大了钢中组织的不均匀性,严重影响了钢的各种性能。
例如,非金属夹杂物导致应力集中,引起疲劳断裂;数量多且分布不均匀的夹杂物会明显降低钢的塑性、韧性、焊接性以及耐腐蚀性;钢中呈网状存在的硫化物会造成热脆性。
因此,夹杂物的数量和分布被认定是评定钢材质量的一个重要指标,并且被列为优质钢和高级优质钢出厂的常规检测项目这一。
非金属夹杂物的性质、形态、分布、尺寸及含量不同,对钢性能的影响也不同。
所以提高金属材料的质量,生产出洁净钢,或控制非金属夹杂物性质和要求的形态,是冶炼和铸锭过程中的一个艰巨任务。
而对于金相分析工作者来说,如何正确判断和鉴定非金属夹杂笺也因此变得十分重要。
1 钢中非金属夹杂物的来源分类1.1 内生夹杂物钢在冶炼过程中,脱氧反应会产生氧化物和硅酸盐等产物,若在钢液凝固前未浮出,将留在钢中。
溶解在钢液中的氧、硫、氮等杂质元素在降温和凝固时,由于溶解度的降低,与其他元素结合以化合物形式从液相或固溶体中析出,最后留在钢锭中,它是金属在熔炼过程中,各种物理化学瓜形成的夹杂物。
内生夹杂物分布比较均匀,颗粒也较小,正确的操作和合理的工艺措施可以减少其数量和改变其成分、大小和分布情况,但一般来说是不可避免的。
1.2 外来夹杂物钢在冶炼和浇注过程中悬浮在钢液表面的炉渣、或由炼钢炉、出钢槽和钢包等内壁肃落的耐火材料或其他夹杂物在钢液凝固前未及时清除而留于钢中。
它是金属在熔炼过程中与外界物质接触发生作用产生的夹杂物。
如炉料表面的砂土和炉衬等与金属液作用,形成熔渣而滞留在金属中,其中也包括加入的熔剂。
焊接工艺中焊缝夹杂物形成机理与控制技术

焊接工艺中焊缝夹杂物形成机理与控制技术焊接是一种常见的金属连接工艺,广泛应用于各种领域。
然而,在焊接过程中,焊缝中往往会产生一些夹杂物。
这些夹杂物可能对焊接接头的强度和耐腐蚀性能产生负面影响。
因此,在焊接工艺中研究焊缝夹杂物的形成机理并发展相应的控制技术具有重要意义。
一、焊缝夹杂物的形成机理在焊接过程中,焊接材料在高温状态下发生液态或部分液态的融化与流动,从而形成焊缝。
然而,由于焊接材料的熔点和蒸发温度不同,以及焊接过程中存在的气体(例如空气中的氧气和水蒸气),就会导致焊缝中夹杂物的形成。
1.气孔气孔是焊缝中最常见的夹杂物,它们通常由气体在焊接过程中产生,并被熔池困住。
气孔的形成与以下几个因素有关:焊材中的气体含量,焊接过程中的气体保护措施,以及焊缝形状和焊接参数的选择。
2.氧化物在焊接过程中,如果焊材表面没有得到很好的清洁和保护,氧气就会与熔池接触,从而形成氧化物夹杂物。
氧化物的形成可以通过改善焊接材料的表面清洁度和使用适当的气体保护措施来控制。
3.夹渣焊接过程中,如果焊缝中含有过多的焊渣(即未熔合的焊材),就会形成夹渣夹杂物。
夹渣的形成可以通过适当选择焊材和焊接参数,以及采取适当的气体保护和焊接工艺控制措施来减少。
二、焊缝夹杂物的控制技术为了减少焊缝夹杂物的形成,以下是一些焊接工艺中常用的夹杂物控制技术。
1.焊材预处理焊接材料在使用前应进行预处理,包括清洗、除油和除氧等。
这样可以减少焊接材料表面的污染物和氧化物含量,从而降低夹杂物的形成。
2.气体保护在焊接过程中,使用合适的气体保护可以有效地减少夹杂物的形成。
常用的气体保护包括惰性气体(如氩气)和还原气体(如氢气)。
选择适当的气体类型和流量,以及合适的保护方法,可以减少气孔和氧化物的产生。
3.焊接参数控制焊接参数的选择对夹杂物的形成具有重要影响。
包括焊接电流、电压、焊接速度、焊接角度等。
通过优化这些参数的选择,可以控制焊缝中的夹杂物形成。
4.焊接工艺改进改进焊接工艺也是减少夹杂物形成的有效方法。
连铸内生夹杂物的形成机理

内生夹杂物的形成机理?
内生夹杂物是脱氧产物或者是钢水冷却凝固过程中的析出物。
(1)脱氧产物
钢中氧化铝(Al2O3)和氧化硅(SiO2)夹杂的形成源于钢中溶解氧和加入的铝或硅脱氧剂之间的反应,是典型的脱氧生成的夹杂物。
点簇状氧化铝夹杂来自脱氧或二次氧化,是铝脱氧钢中的典型存在形式。
由于具有较高的界面能,氧化铝夹杂容易通过碰撞、聚集形成三维点簇状。
点簇状夹杂内每个单体直径约为1~5微米。
在与其他颗粒碰撞、分离或聚集之前,这些单体可能是花盘型或多面体型夹杂物。
另外,珊瑚状氧化铝夹杂应该是原始树枝状或点簇状氧化铝夹杂通过“Ostwald-ripening”作用而形成的。
硅夹杂由于在钢水中为液态或玻璃质状态,通常硅夹杂物为球形,亦可以聚集成点簇状。
(2)钢水冷却和凝固过程中产生的沉淀析出物
在冷却期间钢水中溶解氧、氮、硫的浓度增大,液态溶质元素的溶解度减小。
造成氧化铝、硅、氮化铝和硫化物的沉淀析出。
凝固过程中硫化物在枝晶间析出,亦经常以钢水中已存在的氧化物为核心析出。
这类夹杂物通常较小(<10µm)。
AlN夹杂形成于基体凝固过程中或凝固之后。
夹杂物的生成及控制

夹杂物的生成及控制作者:shicm 发表日期:2007-5-28 阅读次数:7631 非金属夹杂物情况及分类按其化学成分组成和结构可以分以下几类(1)氧化物夹杂:单一金属氧化物、硅酸盐、尖晶石和各种钙铝酸盐;(2)硫化物夹杂:MnS、CaS等,在轧制过程中具有良好的变形能力;(3)磷化物夹杂:CaP、BaP等还原脱磷产物,在一般钢种中较少出现;(4)氮化物夹杂:TiN、ZrN等夹杂物,是钢液从大气中吸氮的产物;(5)含不同类型夹杂物的复合夹杂。
按其来源主要分为两类:(1)外来夹杂物,主要来源为炉渣卷入钢液形成的卷渣、钢液或炉渣与炉衬耐火材料接触时的侵蚀产物、铁合金及其它炉料带入的夹杂等等,在浇铸过程未及时上浮而残留在钢中,它偶然出现,外形不规则,尺寸大,危害极大;(2)内生夹杂物,在液态或固态钢中,由于脱氧和凝固时进行的各类物理化学反应而形成的,主要是和钢中氧、硫、氮的反应产物,它的形成有四个阶段,钢液脱氧反应时形成的成为原生(一次)夹杂;出钢和浇铸过程中温度下降平衡移动时形成的成为二次夹杂;钢水凝固过程中生成为再生(三次)夹杂;固态相变时因溶解度变化而生成的成为四次夹杂;由于一次、三次夹杂生成和析出的热力学和动力学条件最有利,因此可以认为内生夹杂大部分是在脱氧和凝固时生成的,因此控制夹杂最主要的就是要加强脱氧和严格防止二次氧化。
(3)一些尺寸较大的多相复合结构的夹杂物,有时是不同类型的内生夹杂复合而成,有时则是内生夹杂物与外来夹杂物互相包裹而形成的。
为了方便生产评级和比较,按照标准评级图显微检验法根据夹杂物形态和大小分布将夹杂物分为A、B、C、D、DS五类,这五大类夹杂物代表最常观察到的夹杂物的类型和形态:—A类(硫化物类):具有高的延展性,有较宽范围形态比(长度/宽度)的单个灰色夹杂物,一般端部呈圆角;—B类(氧化铝类):大多数没有变形,带角的,形态比小(一般<3),黑色或带蓝色的颗粒,沿轧制方向排成一行(至少有3个颗粒);—C类(硅酸盐类):具有高的延展性,有较宽范围形态比(一般>3)的单个呈黑色或深灰色夹杂物,一般端部呈锐角;—D类(球状氧化物类,如钙铝酸盐):不变形,带角或圆形的,形态比小(一般<3),黑色或带蓝色的,无规则分布的颗粒;—DS类(单颗粒球状类):圆形或近似圆形,直径>13μm的单颗粒夹杂物。
钢中氧化铝类夹杂的形成机理和去除效果的基础研究

钢中氧化铝类夹杂的形成机理和去除效果的基础研究钢中氧化铝类夹杂的形成机理和去除效果的基础研究随着工业化进程的不断推进,钢材作为一种重要的建筑和制造材料,其质量对于产品的性能和可靠性影响至关重要。
而钢中的夹杂物是影响钢材质量的主要因素之一。
尤其是在钢中出现的氧化铝类夹杂物对钢的性能及可靠性具有重要影响。
了解氧化铝类夹杂物的形成机理以及如何有效去除夹杂物,对于提高钢材质量至关重要。
1. 形成机理:1.1 氧化铝类夹杂物的来源:氧化铝类夹杂物主要由原料中的金属氧化物,包括铝氧化物(Al2O3)和其他氧化物(如FeO、MnO、SiO2等)等,通过不同的途径进入钢液中。
这些途径包括炼铁过程中的氧化物还原、原料中的氧化物溶解等。
金属氧化物还可能通过钢水接触管道材料或炉衬等形成和进入钢液中。
1.2 形成机制:氧化铝类夹杂物的形成机制与钢液中氧化还原反应和扩散过程有关。
其主要过程包括金属氧化物的溶解和形成夹杂物的水合反应。
2. 去除效果:2.1 传统的去除方法:传统的去除方法主要包括真空处理、浇注和渣化等。
真空处理可以通过增加钢液的气体溶解度,并通过气体从钢中释放的方式,达到去除夹杂物的效果。
浇注是通过改变钢液的流动状态,利用离心力等原理将夹杂物分离出去。
渣化则是通过加入适当的渣料,使夹杂物与渣料发生反应,形成易于分离的化合物,进而实现去除夹杂物的目的。
2.2 新的去除方法:近年来,随着科技的发展,一些新的去除方法也在不断涌现,包括磁场去除、超声波去除、激光去除等。
这些方法通过物理或化学的手段,对钢液中的夹杂物进行有效去除。
钢中氧化铝类夹杂的形成机理和去除效果的研究具有重要的意义。
通过深入了解氧化铝类夹杂物的形成机理,我们可以针对其形成机制采取相应的控制措施,从根本上减少夹杂物的产生。
研究新的去除方法有助于提高夹杂物去除的效率和质量。
这将对提高钢材的质量和性能,进而促进工业化进程产生积极的影响。
个人观点和理解:作为一名写手,通过撰写这篇文章,我对钢中氧化铝类夹杂的形成机理和去除效果有了更深入的了解。
TiN 夹杂物形成机理研究与控制技术

科学研究创新TiN夹杂物形成机理研究与控制技术张方方田芳(河南省济源钢铁(集团)有限公司河南济源459000)摘要:TiN夹杂物是一种表面形状不规则且物理、化学性质相对稳定的化合物。
TiN夹杂物对钢件的疲劳寿命具有重要影响,研究TiN夹杂物,分析该夹杂物特点及其影响该夹杂物形成的因素,对于工业生产意义深远。
本文从TiN夹杂物的特性出发,通过SEM-EDS对单颗粒TiN夹杂物和多颗粒聚合TiN夹杂物的物理性质进行了分析。
为更好地确定TiN夹杂物的形成机理和控制技术,设计了以IF钢为原料的实验,通过对IF 钢的高温煅烧和冷却,利用SEM-EDS对TiN夹杂物进行分析,研究其形成机理,探究溶质元素偏析和冷却速率对TiN夹杂物的影响,力求为工业生产和制造含钢材料提供理论支持。
关键词:TiN夹杂物形成机理控制技术钢材料研究中图分类号:TG142文献标识码:A文章编号:1674-098X(2021)11(a)-0023-03Study on Formation Mechanism and Control Technology of TiNInclusionZHANG Fangfang TIAN Fang(Henan Jiyuan Iron and Steel(Group)Co.,Ltd.,Jiyuan,Henan Province,459000China) Abstract:TiN inclusion is a kind of compound with irregular surface shape and relatively stable physical and chemical properties.TiN inclusion has an important effect on the fatigue life of steel parts.It is of great significance to study TiN inclusion,analyze the characteristics of the inclusion and the factors influencing the formation of the inclusion.In this paper,based on the characteristics of TiN inclusions,the physical properties of single particle TiN inclusions and polyparticle TiN inclusions were analyzed by SEM-EDS.In order to better determine the formation mechanism and control technology of TiN inclusion,an experiment was designed with IF steel as raw material.Through calcination at high temperature and cooling of IF steel,SEM-EDS was used to analyze TiN inclusion to study its formation mechanism and explore the influence of solute element segregation and cooling rate on TiN inclusion.Strive to provide theoretical support for industrial production and manufacture of steel-containing materials.Key Words:TiN inclusion;Formation mechanism;The control technology;Steel-containing materials;ResearchTiN夹杂物的表面形状不规则,坚硬而不易发生形变,在高温处理后该夹杂物仍不容易消失,无法通过轧制改变其形状。
钢中非金属夹杂物分析

钢中非金属夹杂物分析发布时间:2022-09-02T01:28:12.493Z 来源:《科学与技术》2022年4月8期(下)作者:李洪芳[导读] 非金属夹杂物在钢中含量虽少,但对材料性能影响较大,是钢材理化检验中不可缺少的一项,李洪芳内蒙古包钢钢联股份有限公司化检验中心内蒙古包头市014010摘要:非金属夹杂物在钢中含量虽少,但对材料性能影响较大,是钢材理化检验中不可缺少的一项,但由于其数量少、分布无规律、来源无法控制、光学显微镜下特征复杂等特点,给非金属夹杂物检验工作带来了一些困难。
钢中非金属夹杂物的金相鉴定工作是一项十分复杂与专业的工作,对钢中非金属夹杂物的判定十分重要,也能够对钢的质量进行反映。
在金相显微镜下,对非金属夹杂物的形态与颜色等进行判断,并对透明度等各种性质进行分析。
关键词:钢;非金属;夹杂物如今,现代工业技术的发展,对钢的质量和综合性能要求越来越高。
影响钢材性能的因素是多方面的,往往涉及到炼钢、轧钢和热处理等多道工序,而钢中非金属夹杂物的存在是影响钢材性能的一个重要因素,有时甚至是决定性因素。
钢中非金属夹杂物的研究一直是炼钢连铸生产中的重要课题,夹杂物分析是评定钢材质量的一个重要指标,并且被列为优质钢出厂常规检验项目之一。
钢中存在非金属夹杂物是不可避免的,钢中夹杂物包括内生夹杂物、外来夹杂物两大类,对于金相分析人员来说,如何正确判断和鉴定非金属夹杂物的性质是十分重要。
一、非金属夹杂物分类非金属夹杂物的分类方法也有很多种,根据非金属夹杂物的产生机理,可将其分为内生夹杂物和外来夹杂物两种,也是非金属夹杂物最常见的分类方法。
外来夹杂物主要是由耐高温材料、各类残渣或二者残留物,生成的废物。
外来夹杂物的形成是随机的,它是偶然性因素,人为不可控的,并且外来夹杂物是非规则的。
内生夹杂物是在炼钢过程中,各种物质发生反应,生成含有O、S、N等元素的废物,这些废物不能及时排出去,因而形成了内生夹杂物。
轴承钢中TiN夹杂的形成机理及控制措施
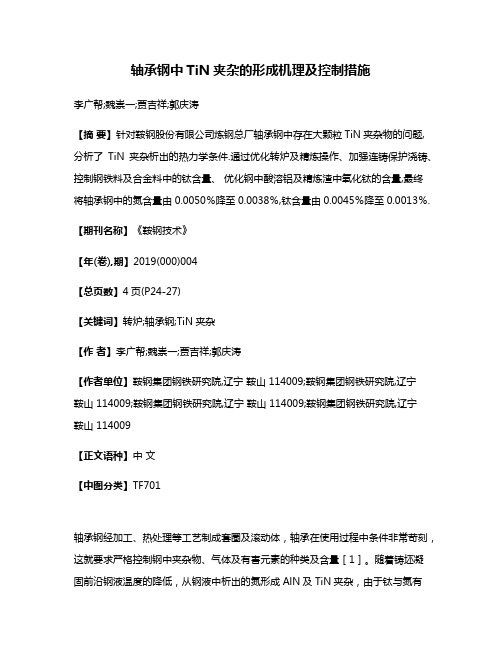
轴承钢中TiN夹杂的形成机理及控制措施李广帮;魏崇一;贾吉祥;郭庆涛【摘要】针对鞍钢股份有限公司炼钢总厂轴承钢中存在大颗粒TiN夹杂物的问题,分析了TiN夹杂析出的热力学条件.通过优化转炉及精炼操作、加强连铸保护浇铸、控制钢铁料及合金料中的钛含量、优化钢中酸溶铝及精炼渣中氧化钛的含量,最终将轴承钢中的氮含量由0.0050%降至0.0038%,钛含量由0.0045%降至0.0013%.【期刊名称】《鞍钢技术》【年(卷),期】2019(000)004【总页数】4页(P24-27)【关键词】转炉;轴承钢;TiN夹杂【作者】李广帮;魏崇一;贾吉祥;郭庆涛【作者单位】鞍钢集团钢铁研究院,辽宁鞍山 114009;鞍钢集团钢铁研究院,辽宁鞍山 114009;鞍钢集团钢铁研究院,辽宁鞍山 114009;鞍钢集团钢铁研究院,辽宁鞍山 114009【正文语种】中文【中图分类】TF701轴承钢经加工、热处理等工艺制成套圈及滚动体,轴承在使用过程中条件非常苛刻,这就要求严格控制钢中夹杂物、气体及有害元素的种类及含量[1]。
随着铸坯凝固前沿钢液温度的降低,从钢液中析出的氮形成AlN及TiN夹杂,由于钛与氮有极强的亲和力,多形成TiN、Ti(CN)夹杂。
在轴承钢中氧含量逐渐降低的情况下,由于TiN比较粗大且坚硬,呈棱角状,所以TiN对轴承钢疲劳寿命的影响非常严重。
Yang等研究了TiN在凝固过程中的析出行为[2],Pak等对TiN的生成热力学进行了分析、计算和实验研究[3],但未对轴承钢工艺流程中各个工序的钛、氮控制进行研究。
鞍钢股份有限公司炼钢总厂在生产轴承钢时,发现在轧制后成品钢材中存在大颗粒的TiN夹杂物,这种硬而脆的夹杂物对钢材后续加工和使用时均产生不良影响。
本文通过热力学计算研究了轴承钢凝固过程中TiN的析出行为,并提出相应的氮、钛控制措施,以降低钢中的氮、钛含量,抑制TiN夹杂的生成,提高轴承钢的质量。
1 TiN析出热力学分析在轴承钢冶炼过程中,钢中的钛、氮反应热力学方程[4]如下:式中,ΔG0为标准自由能,kJ/mol;T为标准温度,K。
钢中夹杂物知识

摘要:根据钢中非金属夹杂物的来源和分类,综述了鉴定钢中非金属夹杂物的方法和定量评级标准,并且给出了典型夹杂物的扫描电镜照片,分析了不同类型夹杂物的形成机理及其在光学显微镜下的基本特征。
随着现代工程技术的发展,对钢的综合性能要求也日趋严格,相应地对钢的材质要求了越来越高。
非金属夹杂物作为独立相存在于钢中,破坏了钢基体的连续性,加大了钢中组织的不均匀性,严重影响了钢的各种性能。
例如,非金属夹杂物导致应力集中,引起疲劳断裂;数量多且分布不均匀的夹杂物会明显降低钢的塑性、韧性、焊接性以及耐腐蚀性;钢中呈网状存在的硫化物会造成热脆性。
因此,夹杂物的数量和分布被认定是评定钢材质量的一个重要指标,并且被列为优质钢和高级优质钢出厂的常规检测项目这一。
非金属夹杂物的性质、形态、分布、尺寸及含量不同,对钢性能的影响也不同。
所以提高金属材料的质量,生产出洁净钢,或控制非金属夹杂物性质和要求的形态,是冶炼和铸锭过程中的一个艰巨任务。
而对于金相分析工作者来说,如何正确判断和鉴定非金属夹杂笺也因此变得十分重要。
1 钢中非金属夹杂物的来源分类1.1 内生夹杂物钢在冶炼过程中,脱氧反应会产生氧化物和硅酸盐等产物,若在钢液凝固前未浮出,将留在钢中。
溶解在钢液中的氧、硫、氮等杂质元素在降温和凝固时,由于溶解度的降低,与其他元素结合以化合物形式从液相或固溶体中析出,最后留在钢锭中,它是金属在熔炼过程中,各种物理化学瓜形成的夹杂物。
内生夹杂物分布比较均匀,颗粒也较小,正确的操作和合理的工艺措施可以减少其数量和改变其成分、大小和分布情况,但一般来说是不可避免的。
1.2 外来夹杂物钢在冶炼和浇注过程中悬浮在钢液表面的炉渣、或由炼钢炉、出钢槽和钢包等内壁肃落的耐火材料或其他夹杂物在钢液凝固前未及时清除而留于钢中。
它是金属在熔炼过程中与外界物质接触发生作用产生的夹杂物。
如炉料表面的砂土和炉衬等与金属液作用,形成熔渣而滞留在金属中,其中也包括加入的熔剂。
钢中硫化铁夹杂物析出原理_概述说明以及解释

钢中硫化铁夹杂物析出原理概述说明以及解释1. 引言1.1 概述在现代钢铁冶炼过程中,硫化铁夹杂物的析出对于钢材的质量和性能具有重要影响。
硫化铁夹杂物是由于钢中含有过多的硫元素而形成的一种微观结构,在钢材中分布不均匀,并且会导致钢材在使用过程中出现脆化、断裂等问题。
因此,深入研究硫化铁夹杂物析出原理及其相应的控制技术具有重要的理论和实际意义。
1.2 文章结构本文将围绕硫化铁夹杂物析出原理展开全面系统的阐述。
首先,我们将介绍硫化铁夹杂物的含义和特点,探讨其在钢铁材料中的重要作用。
然后,我们将概述硫化铁夹杂物析出原理,并解释其形成与演变机制。
进一步地,我们将介绍并分析影响硫化铁夹杂物析出过程的关键因素,从实验方法与表征手段上进行详细说明。
最后,我们将总结当前已取得的研究成果,并提出未来研究的方向与展望。
1.3 目的本文旨在深入探讨钢中硫化铁夹杂物析出原理,全面了解其形成机理和影响因素。
通过研究不同的控制技术和措施,实现对硫化铁夹杂物的有效控制,以提高钢材的质量和性能。
为此,我们将介绍当前已有的相关研究工作,并总结实践中所取得的成果。
同时,本文还将对未来的研究方向进行展望,为进一步深入研究该领域提供参考。
以上是“1. 引言”部分内容,请根据此内容撰写文章。
2. 钢中硫化铁夹杂物析出原理2.1 硫化铁夹杂物的含义和特点在钢中,硫化铁是一种常见的夹杂物。
硫化铁夹杂物指的是由铁与硫元素结合形成的硫化铁晶体,通常呈现出片状、条状或球状的形态。
这些夹杂物在钢中存在的主要原因是来自于原材料中的硫元素和工艺过程中的硫污染。
2.2 析出原理的概述硫化铁夹杂物析出是指在钢水冷却过程中,由于温度下降和相应成分变化,导致溶解在钢中的硫与其他元素结合生成硫化物并析出。
当钢水冷却至一定温度时,其中所含的溶解性硫会与流动态产生相互作用,并进而促使以二聚、多聚体形态析出出来。
这些形成的固相颗粒就是我们所说的硫化铁夹杂物。
2.3 解释硫化铁夹杂物析出影响因素造成钢中硫化铁夹杂物析出量和分布情况的因素有很多。
- 1、下载文档前请自行甄别文档内容的完整性,平台不提供额外的编辑、内容补充、找答案等附加服务。
- 2、"仅部分预览"的文档,不可在线预览部分如存在完整性等问题,可反馈申请退款(可完整预览的文档不适用该条件!)。
- 3、如文档侵犯您的权益,请联系客服反馈,我们会尽快为您处理(人工客服工作时间:9:00-18:30)。
精炼过程夹杂物成分的变化
LF前: •绝大多数为Al2O3 类夹杂物; •已有少量MgO-Al2O3 系夹杂物生成
LF精炼15min: •绝大多数Al2O3 类夹杂物转变为MgO-Al2O3 系 •夹杂物平均组成:80% Al2O3, 17 % MgO,3% CaO
LF精炼中后期: •MgO-Al2O3 系向CaO-MgO-Al2O3 系转变 •LF结束时,仍有大量尚未转化的MgO-Al2O3 系
在夹杂物外表面:
[Ca]+[xCaOMgOyAl2O3]夹杂物=[(x+1)CaOyAl2O3]夹杂物 + [Mg]
From, 王新华,青岛洁净钢会议资料
典型钢种精炼炉渣成分控制-夹杂物
• 夹杂物MgO含量逐步降低; • 最终,夹杂物转变为含MgO很少
的CaO-MgO-Al2O3 系夹杂物,或 不含MgO的CaO-Al2O3 系夹杂物。
典型钢种精炼炉渣成分控制-弹簧钢
Relation between fatigue life and compositions of inclusions (valve spring)
( After N. Ibaragi, 188th/189th Nishiyama Memorial Seminar, 2006)
RH精炼过程: •MgO-Al2O3 系向CaO-MgO-Al2O3 系的转变仍继续6进行 •RH结束,钢中夹杂物平均组成进入了较低熔点区域
I. 在炉渣-钢液界面:
2[Al] + 3(MgO) = 3[Mg] + (Al2O3) 2[Al] + 3(CaO)= 3[Ca] + (Al2O3) II. 在包衬-钢液界面: 2[Al] + 3[MgO]包衬 = 3[Mg] + [Al2O3]夹杂物 III. 在钢液内部:
典型钢种精炼炉渣成分控制-夹杂物
MgO和Al2O3含量的增加首先增加了尖晶石在硅铝酸盐夹 杂物中形核的驱动力。而且,Al2O3显著增加了氧化物夹杂 的液相线温度,这表明夹杂物可以在高温下在有更长时间 停留在液相状态下,在冷却过程中,尖晶石的长大通常较 形核速率快(基于经典形核和长大动力学)。因此,可以 看到尖晶石几乎与母夹杂物(Mother inclus0%Al2O3和CaO/SiO2在5左右的传统精炼渣系相 比,采用含41%左右Al2O3和CaO/SiO2比在6.5左右的炉渣, 钢中CaO-MgO-Al2O3系夹杂物的比率由24.3%显著增加至 81.7%,大多数夹杂物位于较低熔点成分区域(≤1500℃)。
From, 王新华,青岛洁净钢会议资料
高品质特殊钢对MgO-Al2O3系、CaO-MgO-Al2O3、CaO-Al2O3系 “B类”或“D类”夹杂物控制要求很严
典型钢种精炼炉渣成分控制-轴承钢
12C7A: 12CaOAl2O3
CA:
CaOAl2O3
3CA:
3CaOAl2O3
MA:
MgOAl2O3
C2A:
CaO2Al2O3
C6A:
CaO6Al2O3
典型钢种精炼炉渣成分控制-夹杂物
CaO-MgO-Al2O3 –SiO2类 夹杂物
典型钢种精炼炉渣成分控制-夹杂物
CaO-MgO-Al2O3 –SiO2类夹杂物
Joo Hyun Park and Sang-Beom Lee. Thermodynamics on the formation of inclusions containing MgAl2O4 Spinel phase during steelmaking processes. Asial Steel 2009, Busan, S3-15
After: Joo Hyun Park and Sang-Beom Lee. Thermodynamics on the formation of inclusions containing MgAl2O4 Spinel phase during steelmaking processes. Asial Steel 2009, Busan, S3-15
典型钢种精炼炉渣成分控制-弹簧钢
60Si2Mn与CaO-Al2O3-SiO2系夹杂物平衡时的[Al]、[Ca]浓度线(1873K)
典型钢种精炼炉渣成分控制-弹簧钢
Al2O3:~40% CaO/SiO2: ≥7
From, 王新华,青岛洁净钢会议资料
典型钢种精炼炉渣成分控制-硬线钢
在CaO-Al2O3-SiO2三元系 夹杂物中,钙斜长石 (CaO·Al2O3·2SiO2)与鳞石 英和假硅灰石CaO·SiO2) 相邻的周边低熔点区有 良好的变形能力。
[Mg] + n/3[Al2O3]夹杂物 = [MgO(n-1)/3Al2O3]夹杂物 + 2/3[Al]
• MgOAl2O3外表层内存在CaO和MgO的浓度梯度 – 外部CaO含量高,内部低; – 内部MgO含量高,外部低。
• CaO由外向内扩散,MgO由内向外扩散
在夹杂物外表层内部:
CaO+[xCaOyMgOzAl2O3]夹杂物=[(x+1)CaO(y-1)MgOzAl2O3]夹杂物+MgO
LF结束仍存在10~20m的高熔点镁尖晶 石类夹杂物(MA)。
K. Kawakami, et al, TETSU-TO-HAGANE, 93(2007), 741-752
典型钢种精炼炉渣成分控制-夹杂物
山阳观点: CaO-MgOAl2O3 –SiO2类夹杂物来
源于卷渣
K. Kawakami, et al, TETSU-TO-HAGANE, 93(2007), 741-752