轧制缺陷图谱、形成原因分析以及预防措施
轧制缺陷分析

裂纹裂纹是指线材表面沿轧制方向有平直或弯曲、折曲,或以一定角度向线材内部渗透的缺陷[1]。
裂纹长度和深度不同,在线材的长度方向上都能发现。
有的裂纹内有夹杂物,两侧也有脱碳现象。
线材表面产生裂纹的主要原因在于钢坯上有未消除的裂纹(无论纵向或横向)、皮下气泡及非金属夹杂物,它们都会在线材表面造成裂纹。
连铸坯上的针孔如不消除,经轧制被延伸、氧化、溶解就会造成成品的线状发纹。
针孔是连铸坯的主要缺陷之一,不显露时很难检查出来,应特别予以注意。
高碳钢线材轧制后冷却速度过快,也能造成成品裂纹,还会出现横向裂纹。
轧后控冷不当形成的裂纹无脱碳现象,裂纹中一般无氧化铁皮。
另外坯料清理不好也会产生此类问题。
轧制过程中形成裂纹的原因主要有:1)轧槽不合适,主要是尖角和尺寸有问题,表面太粗糙或损坏。
2)粗轧前几道导卫的划伤。
3)粗大的氧化铁皮轧进轧件,通常在粗轧前几道产生。
4)导卫尺寸太大。
若产生裂纹,应从以下方面检查,排除故障:1)高压水除鳞是否正常,轧机轧辊的冷却水路是否堵塞或偏离轧槽。
2)导卫是否偏离轧制线,有否氧化铁皮堵塞在某个导卫中。
3)轧槽是否过度磨损或因处理堆钢事故时损伤了轧槽。
4)精轧机是否有错辊,导卫是否对中及尺寸是否对应于所轧的规格。
2.2 折叠线材表面沿轧制方向平直或弯曲的细线,以任意角度渗入线材的表面内,在横断面上与表面呈小角度交角状的缺陷多为折叠[1]。
通常折叠较长,但亦有不连续的,在线材的长度方向上都有分布。
折叠的两侧伴有脱碳层或部分脱碳层,折叠中间常存在氧化铁夹杂。
坯料中如存在缩孔、偏析、夹杂等缺陷,或者坯料修整不好都有可能产生此类折叠缺陷。
在轧制中可能产生折叠的原因有:孔型中过充满、欠充满;机架间张力太大;导卫对中不好可出现单侧充满从而造成折叠;轧机调整不当,轧件尺寸不符合工艺要求或导卫磨损严重;坯料加热温度不均匀。
若产生折叠,应从以下方面检查,排除故障:检查轧辊冷却,粗轧机中氧化铁皮堆积过多可能产生间断折叠;是否有某个导卫偏离了轧制中心线引起过充满;导卫故障,检查滑动导卫内部是否有异物堆积或磨损超标,滚动导卫中导辊是否正常;轧件尺寸是否符合工艺要求,是否过充满或欠充满;检查张力情况;检查坯料出炉温度,沿坯料长度上温度不均也可导致间断性过充满。
热轧带钢缺陷图谱
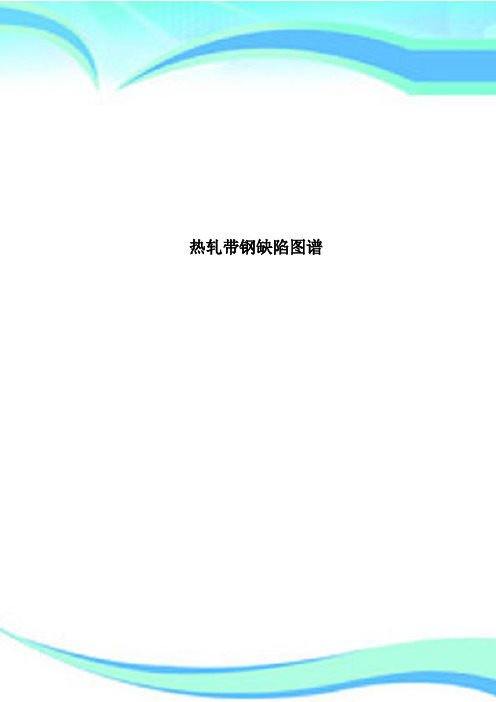
热轧带钢缺陷图谱————————————————————————————————作者: ————————————————————————————————日期:ﻩ热轧带钢外观缺陷Visual Defects inHot Rolled Strip 2.1 不规则表面夹杂(夹层)(IrregularShells)【定义与特征】板带钢表面的薄层折叠,缺陷常呈灰白色,其大小、形状不一,不规则分布于板带钢表面。
【产生原因】板坯表面或皮下有非金属夹杂,这些夹杂在轧制过程中被破碎或暴露而形成夹层状折叠。
【预防与纠正】优化炼钢、精炼工艺,提高钢质纯净度。
【鉴别与判定】肉眼检查,钢板和钢带不得有夹层。
2.2 带状表面夹杂(夹层)(Seams)【定义与特征】板带钢表面的夹杂呈线状或带状不规则地沿轧向分布,有时以点状或舌状逐渐消失。
【产生原因】板坯皮下的夹杂在轧制出现剧烈延伸、破裂而造成。
【预防与纠正】优化炼钢、精炼工艺,提高钢质纯净度。
【鉴别与判定】肉眼检查,钢板和钢带不得有夹层。
2.3 气泡(Blisters)【定义与特征】板带钢表面凸起内有气体,分布无规律,有闭口气泡和开口气泡之分。
【产生原因】板坯由于大量气体在凝固过程中不能逸出,被封闭在内部而形成气体夹杂。
在热轧时,空洞与孔穴被拉长,并随着轧材厚度减薄,被带至产品的表面或边部。
最终,高的气体压力使产品表面或边部出现圆顶状的凸起物或挤出物。
【预防与纠正】优化精炼工艺,保证吹氩时间,使钢水搅拌均匀,避免气体残留;保证中间包烘烤时间;保护渣要符合工艺要求,避免受潮。
【鉴别与判定】肉眼检查,钢板和钢带不得有气泡。
2.4 结疤(重皮)(Scabs)【定义与特征】以不规则的舌状、鱼鳞状、条状或M状的金属薄片分布于带钢表面。
一种与带钢基体相连;另一种与带钢基体不相连,但粘合到表面上,易于脱落,脱落后形成较光滑的凹坑。
【产生原因】由于板坯表面有结疤、毛刺,轧后残留在带钢表面。
冷轧缺陷图谱

精心整理目录冷轧卷缺陷辊印 (2)粘结 (3)咯伤 (4)边裂 (5)平整纹 (7)划伤 (8)05011.图例2.陷;②平整辊印与轧机辊印的区分:平整辊印伤疤处无粗糙度且发亮;轧机辊印伤疤处发暗,有一定的粗糙度。
3.产生原因及危害①轧钢辊表面受损;②轧辊表面粘有异物;③退火过程产生氧化皮后,脱落粘附在平整机轧辊上,平整时产生;④生产过程中其它辊面受损。
危害:①外观不良,加工(冲压)时易发生破裂;②影响镀层效果。
4.5.05021.图例2.②一般粘结分三种:月牙状、折皱状、以及牡丹花状,一般存在于罩式炉的生产中才会产生此缺陷3.产生原因及危害①板形不良②轧机卷取张力过大③退火冷却速度过快④退火前钢卷边部受冲击危害:外观不良,加工(冲压)时易发生破裂4.预防及消除方法①保证前工序板形良好;②退火工艺周期的适当调整;轧机的卷取张力的调整,以及根据轧钢过程中材质和5.05031.图例2.3.①生产过程中各辊上粘有凸起的异物引起;②钢卷摆放位置有异物,导致产生;③小车压痕;④行车吊钩撞击后产生对产品的影响。
危害:①外观不良,镀层后更加明显;②制造用面板无法使用。
4.预防及消除方法①生产过程中对辊面的检查,发现不良及时处理;②钢卷应搬运在适当的优越位置(放置位置环境良好);③对操作工教育,提高操作水平;5.05041.图例2.3.③在酸洗过程中,带钢跑偏或浪形严重导致边部与设备摩擦,边部间断轻折边,经冷轧后边部形成锯齿状;④带钢成分异常;危害:①对产品的外观有直接的影响;②边部无法镀层。
③后道工序生产过程中可能导致断带事故。
4.预防及消除方法①吊运的时候防止撞伤;②酸洗过程中,对中装置适当的调整避免跑偏事故;③严格控制带钢成分及原料卷形、板形缺陷。
5.05051.图例2.3.危害:①对产品的外观有直接的影响;②产品要冲压或深加工时很容易造成开裂。
4.预防及消除方法①应保持轧钢及平整压下量的均衡;②需保持工作辊的适当弯曲度及钢带的对中;③在酸洗过程中对钢带厚度实测,确认热轧的厚度是否均匀。
轧制缺陷及质量控制

轧制缺陷及质量控制一、引言轧制是金属加工中的一种重要工艺,用于将金属坯料通过轧机进行塑性变形,以获得所需的形状和尺寸。
然而,在轧制过程中,由于各种因素的影响,会产生一些缺陷,如裂纹、夹杂物、表面缺陷等,这些缺陷会严重影响产品的质量和性能。
因此,对轧制缺陷进行有效的控制和管理,是确保产品质量的关键。
二、轧制缺陷的分类1. 表面缺陷:包括轧痕、轧花、氧化皮、划伤等。
2. 内部缺陷:包括夹杂物、裂纹、孔洞等。
3. 尺寸偏差:包括厚度偏差、宽度偏差等。
三、轧制缺陷的原因分析1. 材料因素:原材料的质量和成份会直接影响轧制过程中的缺陷产生。
如含有夹杂物、氧化皮等。
2. 工艺参数:轧制过程中的轧制力、轧制速度、轧制温度等参数的控制不当,会导致缺陷的产生。
3. 设备状况:轧机的磨损、不平衡等问题会影响轧制质量。
4. 操作人员:操作人员的技术水平和经验也会对轧制质量产生影响。
四、轧制缺陷的质量控制方法1. 前期控制:在轧制前对原材料进行严格的检查和筛选,确保材料的质量符合要求。
2. 工艺参数控制:根据产品的要求和轧制材料的特性,合理设置轧制力、轧制速度、轧制温度等参数,以减少缺陷的产生。
3. 设备维护:定期对轧机进行检修和维护,确保设备的正常运行,减少设备因素对轧制质量的影响。
4. 操作人员培训:加强对操作人员的培训和技术指导,提高其对轧制过程中缺陷产生原因的认识和处理能力。
5. 检测方法:采用先进的无损检测技术,如超声波检测、磁粉检测等,对轧制产品进行全面的检测,及时发现和排除缺陷。
6. 质量管理体系:建立完善的质量管理体系,包括质量控制计划、质量检验记录、质量问题分析等,确保轧制产品的质量稳定可控。
五、案例分析某钢铁厂在轧制过程中,时常浮现轧制缺陷问题,导致产品质量不稳定,客户投诉频繁。
经过对生产过程的分析和改进,采取了以下措施:1. 强化原材料的筛选工作,严格控制夹杂物和氧化皮的含量。
2. 优化工艺参数,合理调整轧制力、轧制速度和轧制温度,降低缺陷的产生率。
热轧工序典型质量缺陷产生原因与预防措施
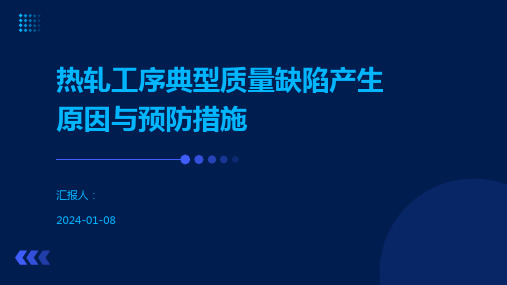
工艺参数设置不合理、工艺流程不完善等工艺因素是导致热轧工序质量缺陷的 重要原因。
详细描述
加热温度、轧制速度、道次压下量等工艺参数的设置对热轧产品的质量有显著 影响。工艺流程中的不合理之处,如冷却速度控制不当、轧制道次不足等,也 可能导致产品出现各种缺陷。
设备因素
总结词
设备故障、维护不当等设备因素是热轧工序中常见的质量缺 陷原因。
热轧工序典型质量缺陷产生 原因与预防措施
汇报人: 2024-01-08
目录
• 热轧工序简介 • 典型质量缺陷类型 • 产生原因分析 • 预防措施 • 案例分析 • 结论与展望
01
热轧工序简介
热轧工序的定义和重要性
定义
热轧工序是将金属材料在高温下 进行轧制的过程,目的是改变材 料的形状并获得所需的机械性能 。
钢材内部碳化物分布不均,导致钢材 性能不均一。
03
产生原因分析
原料因素
总结词
原料质量不均、成分偏析等原料因素 是导致热轧工序质量缺陷的主要原因 之一。
详细描述
原料的化学成分、微观组织结构、夹 杂物含量等因素可能影响热轧过程中 的流动性和变形行为,从而导致产品 出现裂纹、孔洞、夹杂等缺陷。
工艺因素
板形不良产生的原因可能是轧辊磨损严重、轧 制工艺参数设置不合理,或者是来料温度和厚 度波动过大。
厚度超差产生的原因可能是轧辊间隙调整不当 、轧制过程中张力控制不准确,或者是轧制润 滑条件不佳,导致金属流动不均匀。
预防措施实施效果评估
对于表面裂纹,通过优化轧制温 度和润滑条件,加强轧辊检查和 维护,可以显著减少裂纹的产生
2
针对这些质量缺陷,需要采取有效的预防措施, 如控制工艺参数、优化设备参数和加强质量检测 等。
轧制缺陷图谱、形成原因分析以及预防措施

缺陷名称纵裂Longitudinal Crack照片缺陷形貌及特征:缺陷形貌及特征纵裂纹是距钢板边部有一定距离的沿轧制方向裂开的小裂口或有一定宽度的线状裂纹。
板厚大于20mm的钢板出现纵裂纹的机率较大。
缺陷成因:1. 板坯凝固过程中坯壳断裂,出结晶器后进一步扩展形成板坯纵向裂纹,在轧制过程中沿轧制方向扩展并开裂;2. 板坯存在横裂,在横向轧制过程中扩展和开裂形成。
预防:防止纵列纹产生的有效措施是使板坯坯壳厚度均匀,稳定冶炼,连铸工艺是减少纵裂纹产生的关键推荐处理措施:1. 深度较浅的纵裂可采用修磨去除。
2. 修磨后剩余厚度不满足合同要求的钢板可采用火切切除、改规的方法,由于纵裂有一定长度,一般不采用焊补的方法挽救;3. 纵裂面积较大时钢板可直接判次或判废可能混淆的缺陷1. 边部折叠2. 边部线状缺陷缺陷名称横裂Transverse Crack缺陷形貌及特征:缺陷形貌及特征:裂纹与钢板轧制方向呈30°~90°夹角,呈不规则的条状或线状等形态,有可能呈M或Z型,横向裂纹通常有一定的深度。
缺陷成因:板坯在凝固过程中,局部产生超出材料迁都极限的拉伸应力导致板坯横裂,在轧制过程中扩展和开裂形成。
有可能是板坯振痕过深,造成钢坯横向微裂纹;钢坯中铝,氮含量较高,促使AIN沿奥氏体晶界析出,也可能诱发横裂纹;二次冷却强度过高也会造成板坯上的横裂预防:1. 减少板坯振痕;2. 控制板坯表面温度均匀并尽量减少板坯表面和边部的温度差;3. 根据钢中不同合力选用保护渣;4. 合理控制钢中的铝、氮含量。
推荐处理措施:1. 深度较浅的横裂可用修磨的方法去除;2. 修磨后剩余厚度不满足合同要求的钢板可采用厚度改规或切除缺陷后改尺的方法;3. 缺陷面积较大时钢板可直接判次或判废;可能混淆的缺陷1. 夹渣2. 折叠3. 星型裂纹缺陷名称边裂Edge Crack缺陷形貌及特征:边部裂纹是钢板边部表面开口的月牙型,半圆型裂口,通常位于钢板单侧或两侧100mm 范围内,一般沿钢板边部密集分布。
热轧卷缺陷图谱(勿删)
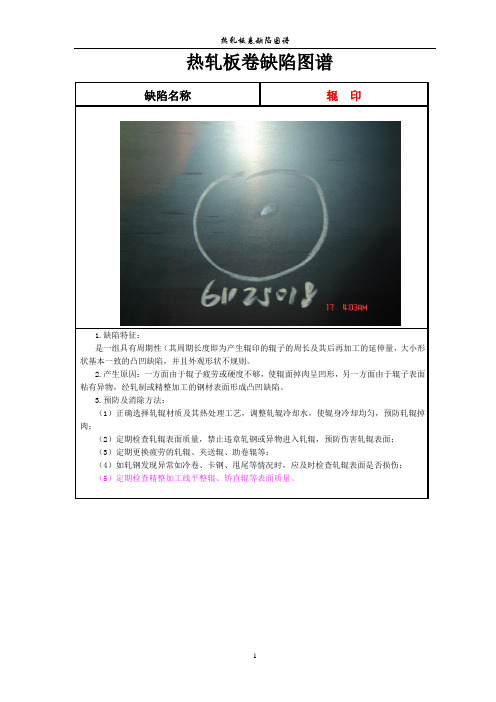
热轧板卷缺陷图谱热轧板卷缺陷图谱缺陷特征:是一组具有周期性(其周期长度即为产生辊印的辊子的周长及其后再加工的延伸量,大小形状基本一致的凸凹缺陷,并且外观形状不规则。
产生原因:一方面由于辊子疲劳或硬度不够,使辊面掉肉呈凹形,另一方面由于辊子表面粘有异物,经轧制或精整加工的钢材表面形成凸凹缺陷。
预防及消除方法:)正确选择轧辊材质及其热处理工艺,调整轧辊冷却水,使辊身冷却均匀,预防轧辊掉)定期检查轧辊表面质量,禁止违章轧钢或异物进入轧辊,预防伤害轧辊表面;)定期更换疲劳的轧辊、夹送辊、助卷辊等;)如轧钢发现异常如冷卷、卡钢、甩尾等情况时,应及时检查轧辊表面是否损伤;)定期检查精整加工线平整辊、矫直辊等表面质量。
缺陷特征:氧化铁皮一般粘附在钢板表面上,分布于板面局部或全部,铁皮有的疏松易脱落;不易脱落。
根据其外观形态不同可分为:红铁皮、线条状铁皮、木纹状铁皮、流线状铁皮、纺锤状铁皮、拖曳状铁皮或散沙状铁皮等。
产生原因:板坯加热制度不合理或加热操作不当生成较厚且较致密的铁皮,除鳞时难以除尽,轧制时被压入钢板表面上;)由于高压除鳞水压力低、水咀堵塞、水咀角度安装不合理或操作不当等原因,使钢坯上的铁皮未除尽,轧制时被压入到钢板表面上。
)氧化铁皮在沸腾钢中发生较多,含硅较高的钢中易产生红铁皮。
缺陷图片缺陷特征:沿钢板的轧制方向呈现高低起伏的波浪形的弯曲。
根据分布的部位不同,分为中间浪、单边浪和双边浪。
产生原因:)辊形曲线不合理,轧辊磨损不均匀;)压下量分配不合理;)轧辊辊缝调整不良或轧件跑偏;缺陷特征:钢卷端部不齐,呈面包状称塔形。
卷边上下错动称卷边错动。
产生原因:)卷取机张力设定不合理;)卷取机前侧导板、夹送辊、助卷辊调整不当;)带钢进卷取机时不对中,带钢跑偏;)带钢存在较大的镰刀弯或板型不良;)卷取机卸卷时将钢卷头部曳出。
缺陷特征:钢卷未卷紧,层与层之间有间隙称松卷。
产生原因:)卷取张力设定不合理;)带钢有严重浪形或因卷取机故障带钢在辊道上温度降低变形;)打捆机故障打捆不紧或吊运过程中断带;)卷取完毕后,因故卷筒反转等。
冷轧板带缺陷及消除方法

冷轧板带缺陷及消除方法浪形浪形是指沿轧制方向高低起伏呈波浪形弯曲,根据分布部位不同分为中间浪、单侧浪、双侧浪、二肋浪等。
浪形的大小是用单位长度内浪峰的高度来衡量的。
浪形发生在钢板边部称为边浪,钢板一侧有浪为单边浪,两侧有浪称为双边浪。
浪形发生在钢板中间的叫中间浪(如图1-25,1-26所示),发生在边部与中部之间的位置上称二肋浪。
如果波形周期性出现则称为周期浪。
各种浪形缺陷的形态、产生原因如表1-12所示表1-12浪形缺陷比较1、严格把好原料关,保证来料板形。
2、按轧制周期定期换辊。
3、合理调节弯曲与倾斜,分段冷却:(1)通过合理调节轧辊倾斜,改善或消除单边浪。
(2)对于双边浪,合理增大弯辊力改善或消除。
(3)合理减小弯辊力改善或消除中间浪。
(4)根据二肋浪产生部位正确选择分段冷却来改善或消除瓢曲瓢曲是指带钢中间呈凸形向上或向下鼓起,切成钢板时,四角向上翘起。
(一)产生原因:1、工作辊凸度太大,或在轧制时轧辊中间温度太高,使带钢中间延伸大于两边。
2、由于某种原因压下量变小,产生中心延伸大于两边。
3、原料瓢曲大,轧后不易消除。
4、板形调节不当。
(二)改善或消除措施:1、合理分配辊型,正确分配压下量。
2、精心操作,勤观察板形。
3、原料横向厚度公差应尽量小。
三辊印辊印是一种常见的缺陷,各工序都能产生。
一般由辊面凸凹缺陷引起,缺陷的部位确定并有周期性。
酸洗辊辊印主要是金属碎块粘在张力辊表面上,又压在带钢表面上产生,压印有规律性。
轧制辊印种类比较多,但其特点是周期出现,印坑形状大小相同。
周期长度L Y 与工作辊径D 有关,即:L Y = u 冗D在成品道次时u= l,其它道次可根据延伸情况计算出来。
按缺陷特点辊印可分为4 种形式:第一种是粘辊辊印。
它是由于轧辊表面粘有金属,从而在轧制时,在带钢表面形成压印。
其形状与粘有金属形式一致,多呈点状、条状或块状。
当原料有破边、折叠等缺陷进入轧机,或者穿带、甩尾时,辊缝不大,带钢与轧辊接触并相对滑动,造成金属粘于轧辊表面上,称做粘辊,如不磨除干净,就在轧制时造成辊印。
轧制缺陷及质量控制
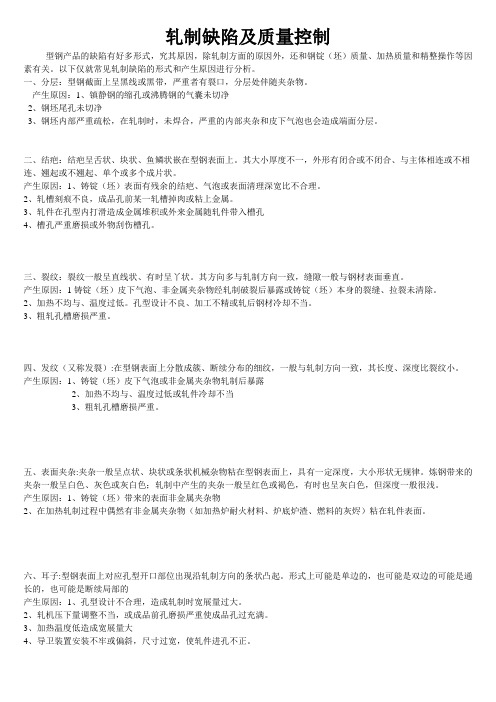
轧制缺陷及质量控制型钢产品的缺陷有好多形式,究其原因,除轧制方面的原因外,还和钢锭(坯)质量、加热质量和精整操作等因素有关。
以下仅就常见轧制缺陷的形式和产生原因进行分析。
一、分层:型钢截面上呈黑线或黑带,严重者有裂口,分层处伴随夹杂物。
产生原因:1、镇静钢的缩孔或沸腾钢的气囊未切净2、钢坯尾孔未切净3、钢坯内部严重疏松,在轧制时,未焊合,严重的内部夹杂和皮下气泡也会造成端面分层。
二、结疤:结疤呈舌状、块状、鱼鳞状嵌在型钢表面上。
其大小厚度不一,外形有闭合或不闭合、与主体相连或不相连、翘起或不翘起、单个或多个成片状。
产生原因:1、铸锭(坯)表面有残余的结疤、气泡或表面清理深宽比不合理。
2、轧槽刻痕不良,成品孔前某一轧槽掉肉或粘上金属。
3、轧件在孔型内打滑造成金属堆积或外来金属随轧件带入槽孔4、槽孔严重磨损或外物刮伤槽孔。
三、裂纹:裂纹一般呈直线状、有时呈丫状。
其方向多与轧制方向一致,缝隙一般与钢材表面垂直。
产生原因:1铸锭(坯)皮下气泡、非金属夹杂物经轧制破裂后暴露或铸锭(坯)本身的裂缝、拉裂未清除。
2、加热不均与、温度过低。
孔型设计不良、加工不精或轧后钢材冷却不当。
3、粗轧孔槽磨损严重。
四、发纹(又称发裂):在型钢表面上分散成簇、断续分布的细纹,一般与轧制方向一致,其长度、深度比裂纹小。
产生原因:1、铸锭(坯)皮下气泡或非金属夹杂物轧制后暴露2、加热不均与、温度过低或轧件冷却不当3、粗轧孔槽磨损严重。
五、表面夹杂:夹杂一般呈点状、块状或条状机械杂物粘在型钢表面上,具有一定深度,大小形状无规律。
炼钢带来的夹杂一般呈白色、灰色或灰白色;轧制中产生的夹杂一般呈红色或褐色,有时也呈灰白色,但深度一般很浅。
产生原因:1、铸锭(坯)带来的表面非金属夹杂物2、在加热轧制过程中偶然有非金属夹杂物(如加热炉耐火材料、炉底炉渣、燃料的灰烬)粘在轧件表面。
六、耳子:型钢表面上对应孔型开口部位出现沿轧制方向的条状凸起。
(全)冷轧薄板质量缺陷图谱

粘结纹
表面质量缺陷
气泡
表面质量缺陷
1、定义与外观
气泡是指钢板表面无规律分布的、圆形的、大小不等的凸 包,其外缘比较圆滑,大多是鼓起的,也有不鼓起的,经酸洗 后表面发亮,其截面有分层并呈现凸起性空隙。
2、鉴别
很容易用肉眼判定。
表面质量缺陷
气泡
3、成因
(1)因铸坯存在较多的气泡等缺陷,虽经多道轧制没有 焊合,残留在钢带上。 (2)热轧时,铸坯在加热炉时间长,气泡暴露。
过酸洗
表面质量缺陷
氧化色
表面质量缺陷
1、定义与外观
钢带表面被氧化,其颜色由边部的深蓝色逐步过渡到浅 蓝色、淡黄色。
2、鉴别
很容易用肉眼判定
表面质量缺陷
氧化色
3、成因
(1)退火时,保护罩密封不严或漏气,发生化学反应;
(2)保护罩吊罩过早,高温出炉,钢卷边缘表面氧化;
(3)保护气体成份不纯;
(4)加热前予吹扫时间不足,炉内存在残氧,钢卷在氧化性气氛中退火。
4、消除及预防 (1)加强原料把关。
(2)减少轧制变形率。
孔洞
表面质量缺陷
粘结纹
表面质量缺陷
1、定义与外观
退火钢卷层间互相粘和在一起称粘结。粘合的形式有点状、 线状和块状粘结。粘结严重时,手摸有凸起感觉,多分布于带 钢的边部或中间。平整后为横向折印展平状或弓形。
2、鉴别
很容易用肉眼判定。
表面质量缺陷
(1)吹氩时间短,夹杂物未充分上浮;
(2)连铸时,保护渣带入钢中;
(3)中包液面低,钢渣卷入钢水中。 4、消除及预防
(1)严格执行操作规程,保证吹氩时间; (2)控制好连铸拉速; (3)保证中包液面。
表面夹杂
轧制缺陷及质量控制

轧制缺陷及质量控制一、引言轧制是金属加工过程中的重要环节之一,对于确保产品质量具有重要意义。
本文将详细介绍轧制过程中常见的缺陷类型及其产生原因,并探讨如何通过质量控制手段来预防和解决这些缺陷问题。
二、轧制缺陷类型及原因1. 表面缺陷表面缺陷是指轧制产品表面出现的瑕疵,如麻点、划痕、氧化皮等。
其主要原因包括:- 轧辊表面粗糙度不合格:轧辊表面粗糙度过高或过低都会导致产品表面出现缺陷;- 轧辊表面污染:轧辊表面存在杂质、油污等污染物会直接影响产品表面质量;- 轧制过程中的热裂纹:高温下,金属材料容易发生热裂纹,进而导致表面缺陷。
2. 尺寸偏差尺寸偏差是指轧制产品的尺寸与设计要求之间存在的差异。
常见的尺寸偏差包括过大或过小的厚度、宽度、长度等。
尺寸偏差的原因主要有:- 轧机设备调整不当:轧机设备的调整不当会导致产品尺寸偏差;- 材料厚度不均匀:原材料的厚度不均匀会直接影响轧制产品的尺寸;- 轧机辊系磨损:轧机辊系磨损会导致轧制压力不均匀,进而影响产品尺寸。
3. 内部缺陷内部缺陷是指轧制产品内部存在的缺陷,如气孔、夹杂物等。
内部缺陷的主要原因包括:- 原材料质量问题:原材料中存在气孔、夹杂物等缺陷;- 轧机设备故障:轧机设备的故障会导致轧制产品内部出现缺陷;- 轧制过程中的温度控制不当:温度控制不当会导致金属材料内部产生缺陷。
三、质量控制手段1. 轧辊表面处理为了避免表面缺陷的产生,可以采取以下措施:- 定期对轧辊进行磨削和抛光,确保其表面粗糙度符合要求;- 加强轧辊的清洁工作,防止污染物附着在轧辊表面;- 对轧辊进行定期检测,及时发现并修复轧辊表面的磨损和裂纹。
2. 轧机设备调整与维护为了控制尺寸偏差,需要进行轧机设备的调整与维护工作:- 对轧机设备进行定期的检查和维护,确保其工作状态良好;- 对轧机设备进行精确的调整,确保产品尺寸与设计要求一致;- 定期检测轧机辊系的磨损情况,及时更换磨损严重的辊子。
轧制缺陷及质量控制

轧制缺陷及质量控制一、引言轧制是金属加工中的一种重要工艺,用于将金属坯料通过辊道压制成所需的形状和尺寸。
然而,在轧制过程中,可能会浮现一些缺陷,如裂纹、夹杂物和凹坑等,这些缺陷会降低产品的质量和性能。
因此,进行轧制缺陷的控制和质量管理是至关重要的。
二、轧制缺陷的分类1. 裂纹:轧制过程中,由于应力集中或者金属内部的缺陷,可能会导致裂纹的产生。
裂纹可以分为表面裂纹和内部裂纹两种类型。
2. 夹杂物:夹杂物是指金属中的非金属杂质,如氧化物、硫化物和氮化物等。
夹杂物会影响金属的强度和韧性。
3. 凹坑:凹坑是指金属表面的凹陷,可能是由于辊道表面的磨损或者金属表面的缺陷导致的。
三、轧制缺陷的原因分析1. 材料因素:材料的成份和内部缺陷会直接影响轧制过程中的缺陷产生。
例如,材料中含有大量夹杂物或者过多的硬质相,会增加裂纹和凹坑的产生风险。
2. 设备因素:轧制设备的质量和性能直接影响轧制过程中的缺陷控制。
例如,辊道的磨损和不平整会导致凹坑的产生,辊道的间隙不合适会增加夹杂物的产生风险。
3. 工艺因素:轧制工艺参数的选择和控制对缺陷的产生和控制起着重要作用。
例如,轧制温度、轧制速度和轧制压力的选择需要根据材料的性质和要求进行合理调整。
四、轧制缺陷的控制措施1. 材料控制:选择合适的原材料,并进行必要的检测和筛选,以确保材料中的夹杂物和缺陷控制在合理范围内。
2. 设备维护:定期检查和维护轧制设备,确保辊道的平整度和间隙的合适性,减少凹坑和夹杂物的产生。
3. 工艺优化:根据不同材料的特性和产品的要求,优化轧制工艺参数,如温度、速度和压力等,以减少裂纹和凹坑的产生。
4. 检测技术:采用先进的无损检测技术,如超声波检测和磁粉探伤等,对轧制产品进行全面的检测,及时发现和排除缺陷。
5. 质量管理:建立完善的质量管理体系,包括质量检验、质量控制和质量反馈等环节,确保轧制产品的质量稳定和持续改进。
五、轧制缺陷的质量控制1. 检测方法:采用适当的检测方法对轧制产品进行质量控制,如外观检查、尺寸测量和物理性能测试等。
钢管轧制存在质量问题的原因及改进措施

一穿轧制存在的质量问题1、毛管外径偏大或偏小原因:①辊距偏大或偏小②导板板距偏大或偏小③顶头位置向前或靠后④顶头直径偏大或偏小⑤轧辊径向串动量太大⑥上导板座没有固定,上下跳动量大改进措施:根据轧制表的参数选择合适的辊距,导板距,顶头伸入量及顶头直径,加强轧辊和导板的固定,正常轧制时,辊距和导板距保证相对稳定,不能轻易调整,若钢管偏厚或偏薄,可采取进、退顶杆的方法。
2、壁厚严重不均原因:①一穿三个轧辊的外径大小不一②三个轧辊偏离轧制线③三个轧辊调整后不成等边三角形,轧辊前后距轧机牌坊距离不一致;④定心辊未抱住顶杆甩动严重⑤定心孔不对中⑥穿孔机受料槽、一穿轧机、定心机架、顶杆小车的机械中心线不对⑦轧辊轧制过程中跳动太大;⑧顶杆位置过后;⑨轧辊直径过小,轧制大规格钢管时产生滑动现象;改进措施:①安装轧辊时先要测量三个轧辊的辊径,保持三个轧辊的辊径一致;②调整轧制中心线,俣证轧制中心线与穿孔中心线重合,然后可使轧制中心线略低于穿孔中心线0-5mm;③将三个轧辊调整后成等边三角形,保证三个轧辊在轧制过程中受力一致,轧辊前后距牌坊距离一致;④调整定心辊,保证在空载时能抱住顶杆,并使顶杆的水平线与穿孔中心线重合;⑤保证定心孔对中;⑥要求设备测试中心线,保证穿孔机受料槽、一穿轧机、定心机架、顶杆小车的机械中心线在一条水平直线上;⑦临时用铁片调整间隙,保证跳动值不超标。
⑧调整到合适的顶杆位置;⑨更换轧辊,选择合适辊径的轧辊,当辊径小于一定值,予以报废。
3、头尾外径不一致(头大尾小)原因:①坯料加热温度不均匀,头部温度偏低;②穿孔过程中轧辊在辊箱中抖动③穿孔中误动作侧压进装置④管坯开始变形时顶头的轴向阻力加大,轴向延伸受阻,延伸变形减小,横向变形(扩径)加大⑤管坯尾部顶透时轴向阻力减小,使延伸变形容易,同时横向辗轧减小,因而尾部直径变小改进措施:按加热制度加热,保证钢温一致;采取措施固定轧辊,使轧辊在辊箱中不串动;提高操作水平,减少误动作,加强调整,保证轴向变形与横向变形同步。
带钢轧制常见缺陷原因分析

带钢轧制常见缺陷原因分析结疤(M01)图7-1-1图7-1-21. 缺陷特征附着在钢带表面,形状不规则翘起的金属薄片称结疤。
呈现叶状、羽状、条状、鱼鳞状、舌端状等。
结疤分为两种,一种是与钢的本体相连结,并折合到板面上不易脱落;另一种是与钢的本体没有连结,但粘合到板面上,易于脱落,脱落后形成较光滑的凹坑。
2. 产生原因及危害产生原因:①板坯表面原有的结疤、重皮等缺陷未清理干净,轧后残留在钢带表面上;②板坯表面留有火焰清理后的残渣,经轧制压入钢带表面。
危害:导致后序加工使用过程中出现金属剥离或产生孔洞。
3. 预防及消除方法加强板坯质量验收,发现板坯表面存在结疤和火焰清理后残渣应清理干净。
4. 检查判断用肉眼检查;不允许存在结疤缺陷,对局部结疤缺陷,允许修磨或切除带有结疤部分带钢的方法消除,如结疤已脱落,则比照压痕缺陷处理。
7.2 气泡(M02)图7-2-1 闭合气泡图7-2-2 开口气泡图7-2-3 开口气泡1. 缺陷特征钢带表面无规律分布的圆形或椭圆形凸包缺陷称气泡。
其外缘较光滑,气泡轧破后,钢带表面出现破裂或起皮。
某些气泡不凸起,经平整后,表面光亮,剪切断面呈分层状。
2. 产生原因及危害产生原因:①因脱氧不良、吹氩不当等导致板坯内部聚集过多气体;②板坯在炉时间长,皮下气泡暴露或聚集长大。
危害:可能导致后序加工使用过程中产生分层或焊接不良。
3. 预防及消除方法①加强板坯质量验收,不使用气泡缺陷暴露的板坯;②严格按规程加热板坯,避免板坯在炉时间过长。
4. 检查判断用肉眼检查;不允许存在气泡缺陷。
7.3 表面夹杂(M03)图7-3-1图7-3-21. 缺陷特征板坯中的夹杂或夹渣经轧制后在钢带表面暴露的块状或长条状的夹杂缺陷称表面夹杂。
其颜色一般呈棕红色、黄褐色、灰白色或灰黑色。
2. 产生原因及危害产生原因:板坯皮下夹杂轧后暴露或板坯原有的表面夹杂轧后残留在带钢表面。
危害:可能导致后序加工过程中产生孔洞、开裂、分层。
轧制缺陷及质量控制
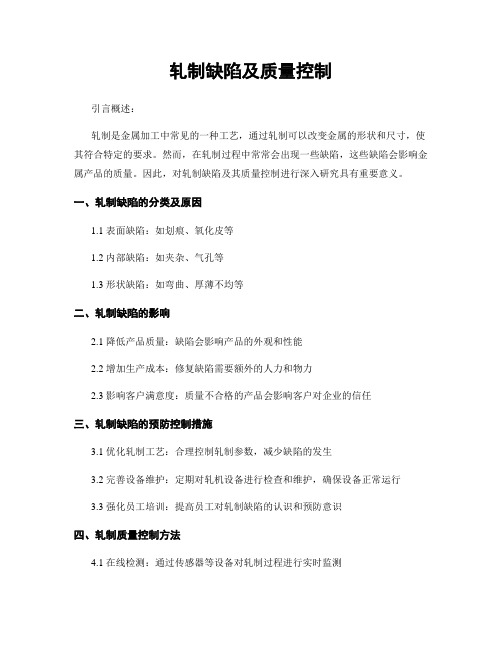
轧制缺陷及质量控制
引言概述:
轧制是金属加工中常见的一种工艺,通过轧制可以改变金属的形状和尺寸,使其符合特定的要求。
然而,在轧制过程中常常会出现一些缺陷,这些缺陷会影响金属产品的质量。
因此,对轧制缺陷及其质量控制进行深入研究具有重要意义。
一、轧制缺陷的分类及原因
1.1 表面缺陷:如划痕、氧化皮等
1.2 内部缺陷:如夹杂、气孔等
1.3 形状缺陷:如弯曲、厚薄不均等
二、轧制缺陷的影响
2.1 降低产品质量:缺陷会影响产品的外观和性能
2.2 增加生产成本:修复缺陷需要额外的人力和物力
2.3 影响客户满意度:质量不合格的产品会影响客户对企业的信任
三、轧制缺陷的预防控制措施
3.1 优化轧制工艺:合理控制轧制参数,减少缺陷的发生
3.2 完善设备维护:定期对轧机设备进行检查和维护,确保设备正常运行
3.3 强化员工培训:提高员工对轧制缺陷的认识和预防意识
四、轧制质量控制方法
4.1 在线检测:通过传感器等设备对轧制过程进行实时监测
4.2 人工检验:对轧制后的产品进行目视检查和尺寸测量
4.3 抽样检测:定期抽取产品进行全面检验,确保产品质量符合标准
五、轧制缺陷处理方法
5.1 修磨:对表面缺陷进行修磨处理,恢复产品表面光洁度
5.2 热处理:对内部缺陷进行热处理,消除缺陷并提高产品性能
5.3 重新轧制:对形状缺陷的产品进行重新轧制,确保产品尺寸和形状符合要求
总结:
轧制缺陷及质量控制是金属加工中一个重要的环节,只有通过科学的方法对轧制缺陷进行预防和控制,才能生产出高质量的金属产品,提高企业的竞争力和市场占有率。
希望本文的内容能够对相关行业的从业人员有所帮助。
冷轧薄板质量缺陷图谱

性能问题预防: 提出预防性能 问题的措施和
方法
04
冷轧薄板质量缺陷预防 措施
原料控制
选用优质原料,保证原料质量
严格控制原料的化学成分和物料的纯净度和均匀性
定期对原料进行检验和测试, 确保原料质量稳定可靠
轧制工艺优化
优化轧制速度:提 高轧制速度,减少 缺陷产生
案例分析方法
观察缺陷特征:观察缺陷的外观、尺寸、位置等特征 分析缺陷原因:根据缺陷特征分析可能原因,如材料、工艺、设备等 制定改进措施:根据分析结果制定改进措施,如更换材料、调整工艺参数、维修设备等 验证改进效果:实施改进措施后,验证改进效果,确保缺陷得到解决
案例分析结果
缺陷类型:表面划 伤、凹坑、麻点等
02
冷轧薄板质量缺陷产生 原因
原料因素
原料质量:原料的纯净度、均匀性等对冷轧薄板的质量产生影响 原料处理:原料的加热、冷却、轧制等工艺过程对冷轧薄板的质量产生影响 原料成分:原料中的元素含量、合金元素等对冷轧薄板的质量产生影响 原料来源:不同来源的原料可能对冷轧薄板的质量产生影响
轧制工艺
轧制温度:影响薄板硬度和 韧性
凸起:表面出现凸起,影响 美观和使用性能
凹坑:表面出现凹坑,影响 美观和使用性能
划痕:表面出现划痕,影响 美观和使用性能
裂纹:表面出现裂纹,影响 美观和使用性能
腐蚀:表面出现腐蚀,影响 美观和使用性能
氧化:表面出现氧化,影响 美观和使用性能
尺寸偏差图谱
尺寸偏差的定义和分类 尺寸偏差产生的原因和影响因素 尺寸偏差的检测方法和标准 尺寸偏差的预防和控制措施
操作规范与培训
制定严格的操作规 范,确保员工按照 规范进行操作
对员工进行定期的 培训,提高员工的 操作技能和意识
轧制缺陷及质量控制

轧制缺陷及质量控制一、引言轧制是金属加工中常用的一种工艺,用于将金属块材或者板材通过辊道进行塑性变形,从而得到所需的形状和尺寸。
然而,由于材料的性质、设备的使用以及操作人员的技术水平等因素的影响,轧制过程中往往会浮现一些缺陷,如表面裂纹、厚度不均匀等,这些缺陷会直接影响产品的质量和性能。
因此,轧制缺陷的控制是保证产品质量的关键环节。
二、轧制缺陷分类及原因1. 表面缺陷表面缺陷是指在轧制过程中金属表面浮现的缺陷,如裂纹、气泡、氧化皮等。
这些缺陷通常由以下原因引起:- 材料的表面质量不良,存在夹杂物或者氧化皮;- 轧机辊道不平整或者磨损严重;- 轧制过程中润滑不良,导致金属与辊道之间磨擦增大。
2. 几何缺陷几何缺陷是指轧制过程中金属产品的形状和尺寸偏差,如厚度不均匀、边部不直等。
这些缺陷通常由以下原因引起:- 轧机辊道调整不当,导致金属材料厚度不均匀;- 轧机辊道磨损严重,失去了原有的几何形状;- 轧机操作人员技术水平不高,操作不当。
三、轧制缺陷的控制方法为了控制轧制过程中的缺陷,提高产品的质量和性能,可以采取以下措施:1. 材料预处理在轧制之前,对原材料进行预处理是非常重要的。
首先,对材料的表面进行清洁,去除氧化皮和夹杂物。
其次,对材料进行退火处理,以提高其塑性和可加工性。
最后,对材料进行表面润滑处理,减少与辊道的磨擦。
2. 轧机设备维护保持轧机设备的良好状态对于控制缺陷至关重要。
定期检查和维护轧机辊道,确保其平整度和几何形状的精确性。
同时,及时更换磨损严重的辊道,以保证轧制过程的稳定性和一致性。
3. 润滑控制在轧制过程中,适当的润滑是减少磨擦、防止表面缺陷的关键。
选择合适的润滑剂,并确保润滑剂的供应充足、均匀。
同时,及时清洗辊道和润滑系统,避免杂质对产品质量的影响。
4. 操作人员培训轧制过程需要经验丰富的操作人员进行操作和监控。
因此,对轧机操作人员进行培训,提高其技术水平和操作规范性是非常重要的。
钢铁材料常见缺陷(图谱)及产生原因
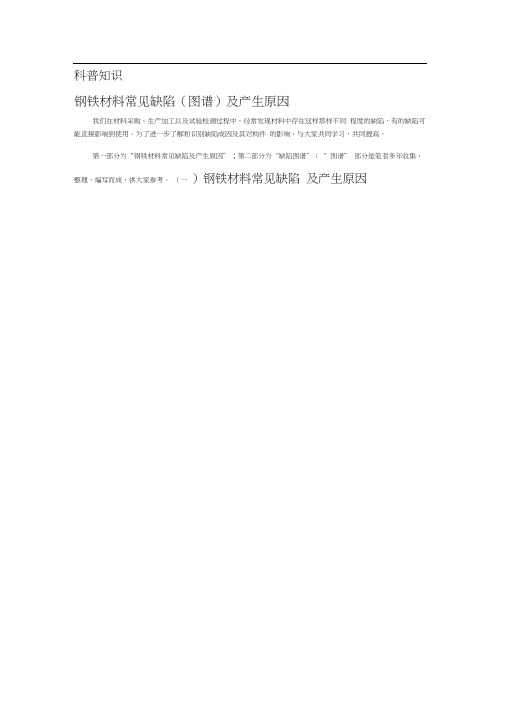
科普知识钢铁材料常见缺陷(图谱)及产生原因我们在材料采购、生产加工以及试验检测过程中,经常发现材料中存在这样那样不同程度的缺陷,有的缺陷可能直接影响到使用。
为了进一步了解和识别缺陷成因及其对构件的影响,与大家共同学习,共同提高,第一部分为“钢铁材料常见缺陷及产生原因” ; 第二部分为“缺陷图谱”;“ 图谱” 部分是笔者多年收集、整理、编写而成,供大家参考。
(一)钢铁材料常见缺陷及产生原因型钢常见缺陷缺陷名称缺陷特征型钢表面上的疤状金属薄块。
其大小、深浅不等,外形极不规则,常呈指甲状、鱼鳞状、块状、舌头状无规律地分布在钢材表面上,结疤下常有非金属夹杂物。
产生原因结疤由于钢坯未清理,使原有的结疤轧后仍残留在钢材表面上。
表面夹杂暴露在钢材表面上的非金属物质称为表面夹杂,一颜色有暗红、型钢表面上,坑,其大小、般呈点状、块状和条状分布,淡黄、灰白等,机械的粘结在夹杂脱落后出现一定深度的凹形状无一定规律。
分层此缺陷在型钢的锯切断面上呈黑线或黑带状,严重的分离成两层或多层,分层处伴随有夹杂物。
(1)钢坯带来的表面非金属夹杂物。
其(2)在加热或轧制过程中,偶然有非其金属夹杂韧(如加热炉的耐火材料及炉渣等),炉附在钢坯表面上,轧制时被压入钢材,冷却经矫直后部分脱落(1) 主要是由于镇静钢的缩孔或沸腾钢的气囊未切净。
(2) 钢坯的皮下气泡,严重疏松,在轧制时未焊台,严重的夹杂物也会造成分层。
(3) 钢坯的化学成份偏析严重,当轧制较薄规格时,也可能形成分层。
气泡(凸包) 型钢表面呈现的一种无规律分布的园形凸起称为凸包,凸起部分的外缘比较园滑, 包破裂后成鸡爪形裂口或舌形结疤,叫气泡。
多产生于型钢的角部及腿尖。
凸钢坯有皮下气泡,轧制时未焊合。
裂纹顺轧制方向出现在型钢表面上的线形开裂,一般呈直线形,有时呈“ Y”形,多为通长出现,有时局部出现。
尺寸超差(尺寸不合、规格不合) 尺寸超差是指型钢截面几何尺寸不符标准规定要求的统称。
热轧带钢缺陷图谱

热轧带钢外观缺陷Visual Defects in Hot Rolled Strip2.1 不规则外表夹杂〔夹层〕(Irregular Shells)【定义与特征】板带钢外表的薄层折叠,缺陷常呈灰白色,其大小、形状不一,不规则分布于板带钢外表。
【产生原因】板坯外表或皮下有非金属夹杂,这些夹杂在轧制过程中被破碎或暴露而形成夹层状折叠。
【预防与纠正】优化炼钢、精炼工艺,提高钢质纯洁度。
【鉴别与判定】肉眼检查,钢板和钢带不得有夹层。
2.2 带状外表夹杂〔夹层〕(Seams)【定义与特征】板带钢外表的夹杂呈线状或带状不规则地沿轧向分布,有时以点状或舌状逐渐消失。
【产生原因】板坯皮下的夹杂在轧制出现剧烈延伸、破裂而造成。
【预防与纠正】优化炼钢、精炼工艺,提高钢质纯洁度。
【鉴别与判定】肉眼检查,钢板和钢带不得有夹层。
2.3 气泡(Blisters)【定义与特征】板带钢外表凸起内有气体,分布无规律,有闭口气泡和开口气泡之分。
【产生原因】板坯由于大量气体在凝固过程中不能逸出,被封闭在内部而形成气体夹杂。
在热轧时,空洞与孔穴被拉长,并随着轧材厚度减薄,被带至产品的外表或边部。
最终,高的气体压力使产品外表或边部出现圆顶状的凸起物或挤出物。
【预防与纠正】优化精炼工艺,保证吹氩时间,使钢水搅拌均匀,防止气体残留;保证中间包烘烤时间;保护渣要符合工艺要求,防止受潮。
【鉴别与判定】肉眼检查,钢板和钢带不得有气泡。
2.4 结疤〔重皮〕(Scabs)【定义与特征】以不规则的舌状、鱼鳞状、条状或M状的金属薄片分布于带钢外表。
一种与带钢基体相连;另一种与带钢基体不相连,但粘合到外表上,易于脱落,脱落后形成较光滑的凹坑。
【产生原因】由于板坯外表有结疤、毛刺,轧后残留在带钢外表。
或板坯经火焰清理后留有残渣,在轧制中压入外表。
【预防与纠正】加强板坯切口熔渣的清理,合理调整中间坯的切头、切尾量,防止毛刺残留。
【鉴别与判定】肉眼检查,钢板和钢带不得有结疤。
- 1、下载文档前请自行甄别文档内容的完整性,平台不提供额外的编辑、内容补充、找答案等附加服务。
- 2、"仅部分预览"的文档,不可在线预览部分如存在完整性等问题,可反馈申请退款(可完整预览的文档不适用该条件!)。
- 3、如文档侵犯您的权益,请联系客服反馈,我们会尽快为您处理(人工客服工作时间:9:00-18:30)。
缺陷名称纵裂Longitudinal Crack照片缺陷形貌及特征:缺陷形貌及特征纵裂纹是距钢板边部有一定距离的沿轧制方向裂开的小裂口或有一定宽度的线状裂纹。
板厚大于20mm的钢板出现纵裂纹的机率较大。
缺陷成因:1. 板坯凝固过程中坯壳断裂,出结晶器后进一步扩展形成板坯纵向裂纹,在轧制过程中沿轧制方向扩展并开裂;2. 板坯存在横裂,在横向轧制过程中扩展和开裂形成。
预防:防止纵列纹产生的有效措施是使板坯坯壳厚度均匀,稳定冶炼,连铸工艺是减少纵裂纹产生的关键推荐处理措施:1. 深度较浅的纵裂可采用修磨去除。
2. 修磨后剩余厚度不满足合同要求的钢板可采用火切切除、改规的方法,由于纵裂有一定长度,一般不采用焊补的方法挽救;3. 纵裂面积较大时钢板可直接判次或判废可能混淆的缺陷1. 边部折叠2. 边部线状缺陷缺陷名称横裂Transverse Crack缺陷形貌及特征:缺陷形貌及特征:裂纹与钢板轧制方向呈30°~90°夹角,呈不规则的条状或线状等形态,有可能呈M或Z型,横向裂纹通常有一定的深度。
缺陷成因:板坯在凝固过程中,局部产生超出材料迁都极限的拉伸应力导致板坯横裂,在轧制过程中扩展和开裂形成。
有可能是板坯振痕过深,造成钢坯横向微裂纹;钢坯中铝,氮含量较高,促使AIN沿奥氏体晶界析出,也可能诱发横裂纹;二次冷却强度过高也会造成板坯上的横裂预防:1. 减少板坯振痕;2. 控制板坯表面温度均匀并尽量减少板坯表面和边部的温度差;3. 根据钢中不同合力选用保护渣;4. 合理控制钢中的铝、氮含量。
推荐处理措施:1. 深度较浅的横裂可用修磨的方法去除;2. 修磨后剩余厚度不满足合同要求的钢板可采用厚度改规或切除缺陷后改尺的方法;3. 缺陷面积较大时钢板可直接判次或判废;可能混淆的缺陷1. 夹渣2. 折叠3. 星型裂纹缺陷名称边裂Edge Crack缺陷形貌及特征:边部裂纹是钢板边部表面开口的月牙型,半圆型裂口,通常位于钢板单侧或两侧100mm 范围内,一般沿钢板边部密集分布。
照片:缺陷形貌及特征:星形裂纹是钢板表面呈不闭合多边形或簇状的裂口,由于其分布类似于多边形的星星形状,故此得名。
星形裂纹深浅不一,但通常清晰可见,在钢板表面的分布位置较为复杂。
一般低合金钢种比碳素钢种更易发生星形裂纹,钢板越厚,出现星形裂纹的机率也越大可能成因:星形裂纹大多出现在锰、硅、铜、铝含量的钢种,由于硅酸盐类夹杂物和铜原子在奥氏体晶界上的富集降低了晶界的强度,从而在板坯上形成星形裂纹。
在板坯加热和轧制过程中进一步扩展和演变成钢板表面的星形裂纹预防:1. 采用热装热送,减少铜原子的富集程度;2. 合理选用保护渣,控制结晶器给水温度;3. 防止板坯过热,过烧;推荐处理措施:1. 深度较浅的星形裂纹可修磨去除:2. 修磨后剩余厚度不满足合同要求的钢板可采用厚度改规或切除缺陷后改尺的方法;3. 面积较大且较深的星形裂纹可直接判次或判废可能混淆的缺陷1. 横裂2. 龟裂缺陷名称龟裂Chap照片缺陷形貌及特征:龟裂是钢板表面呈龟贝状(网纹状)的裂口,一般长度较短,多产生在碳含量或合金含量较高的钢种;缺陷成因:1. 板坯低温火焰清理时,局部温度骤升形成的热应力或冷却过程中产生的组织应力,使板坯表面炸裂;2. 板坯表面固有的网状裂纹在轧制过程中扩展和开裂;3. 板坯加热局部过热并出现较深的脱碳层,在轧制过程中因塑性降低而开裂。
预防:1. 控制板坯火焰清理时板坯余温;2. 防止板坯加热过烧推荐处理措施:1. 较浅的龟裂可修磨去除:2. 修磨后剩余厚度不满足合同要求的钢板可采用厚度改规或切除缺陷后改尺的方法;若合同允许焊补,对于裂纹数量和面积较小的钢板可进行焊补挽救;可能混淆的缺陷:星形裂纹缺陷名称夹渣Slag 照片照片缺陷形貌及特征:在钢板的切割断面上呈现一条或多条平行的缝隙,即钢板局部存在基本平行于钢板表面的未焊合界面。
缺陷成因:1. 板坯中的夹杂物,在轧制后延展为片状并逐渐长大,直至形成分层;2. 板坯中心区域低溶质物质富集,中心偏析带内存在硫化物聚集,形成夹杂性裂纹;3. 板坯内部本身存在内裂,分层,疏松或缩孔等缺陷,轧制后形成分层;4. 板坯氢含量较高,轧制后气体释放不尽,形成氢致裂纹。
预防:1. 炼钢过程中控制钢水的纯净度,减少夹杂物或促使夹杂物充分上浮;2. 控制钢水中的气体含量,控制中间包和覆盖剂的水份含量;推荐处理措施:1. 分层如果分布密集或具有一定的面积应作判次或判废处理;2. 夹杂性分层如果分布比较弥散,且不具有明显的长度和宽度,一般不影响使用。
为保证钢板的质量,一般均用切除的方法消除分层缺陷。
可能混淆的缺陷切边不足缺陷名称翘皮Shell照片缺陷形貌及特征:翘皮是指钢板表面出现材料搭叠区域,其形状通常呈舌状或山峰状,有闭合的,有张开的,缺陷根部与钢板基体相连。
缺陷成因:1. 板坯本身的皮下气泡在轧制过程破裂延伸造成;2. 连铸过程中非金属夹杂物卷入板坯,在轧制过程中夹杂物破碎而形成;3. 板坯表面有较深的沟槽,或板坯清理表面缺陷后形成的沟槽宽深比过小,在轧制过程中由于表面延伸而形成双金属搭叠;预防:1. 稳定连铸工艺,提高坯料质量;2. 严格遵守板坯清理的有关规定;推荐处理措施:1. 深度较浅的翘皮可用修磨去除,修磨后如果厚度低下限可采用厚度改规或切除缺陷后改尺的方法;2. 严重的翘皮可直接采用切除后改尺的方法;可能混淆的缺陷折叠缺陷名称端部折叠Head fold 照片照片缺陷形貌及特征:边部折叠是指钢板单侧或双侧边部的多条平行于钢板轧制方向的表面裂口,通常呈连续或断续密集分布,表面裂口一般略有弯曲。
展宽比大的钢板边部折叠离开边部的距离较大。
可能成因:1. 板坯边部清理形状不佳,板坯断面有裂纹,在轧制过程中形成边部折叠。
2. 展宽轧制过程中钢板的翘头扣头在转钢90度后被卷入钢板边部,形成距边部一定距离的表面裂口缺陷。
预防:1. 严格按规定进行板坯边部清理。
2. 对展宽比较大的钢板合理控制展宽轧制过程中的翘扣头。
3. 控制板坯加热后的上下表面温差。
推荐处理措施:1. 边部折叠深浅不一,较浅的缺陷可通过修磨去除,较深的需要切除并可能造成钢板该规。
2. 发现批量缺陷且可能导致改规时,可根据缺陷距边的距离通知轧钢适当增加宽度余量。
3. 控制双边剪跑偏可以减少切除缺陷后改规的可能性。
可能混淆的缺陷:1. 边部线状缺陷2. 边裂缺陷名称边部线状缺陷Edge line shape defect照片缺陷形貌及特征:边部线状缺陷是指钢板单侧或双侧边部平行于轧制方向的呈笔直线状的表面裂口,缺陷通常有一定的长度,也有可能与轧制方向形成一个较小的夹角。
展宽比大的钢板边部线状缺陷离开边部的距离较大。
可能成因:1. 展宽轧制过程中钢板的翘扣头在转钢90度后被卷入钢板边部,形成距边部一定的表面裂口缺陷。
2. 板坯边部清理形状不佳,板坯断面有裂纹,在轧制过程中形成边部线状缺陷。
预防:1. 对展宽比较大的钢板合理控制展宽轧制过程中的翘扣头。
2. 严格按规定进行板坯边部清理3. 控制板坯加热后的上下表面温差。
推荐处理措施:1. 较浅的边部线状缺陷可通过修磨去除,较深的需要切除并可能造成钢板改规。
2. 发现批量缺陷且可能导致改规时,可根据缺陷距边的距离通知轧钢适当增加宽度余量。
3. 控制双边剪跑偏可以减少切除缺陷后改规的可能性可能混淆的缺陷:1. 边部折叠2. 边裂缺陷名称一次氧化铁皮Rolling scale照片缺陷形貌及特征:一次氧化铁皮是指板坯加热过程中生成的氧化铁皮在轧制过程中被压入钢板表面的一种缺陷,颜色通常呈灰褐色,其成分为F e3O4,形态呈小斑点,大块斑痕或带状条纹等形式,通常伴有铁氧照片缺陷形貌及特征:二次氧化铁皮是指钢板在轧制过程中生成的氧化铁皮被压入钢板表面的一种缺陷,颜色通常呈红棕色,其成分为F e2O3或F e O,呈散布的点状,块状或条状分布。
缺陷成因:轧机除鳞系统压力不足,喷嘴堵塞或水泵跳电等原因,轧制过程中生成的二次氧化铁皮未能得到有效的清除,造成部分氧化铁皮呈片状或块状被压入钢板本体预防:提高轧机除鳞系统的除鳞效能。
推荐处理措施:1. 对缺陷程度进行确认,不满足合同要求的缺陷可通过修磨去除,当修磨处剩余厚度不满足合同要求时可采取厚度改规或切除缺陷后改尺的方法。
2. 面积较大或深度较深的缺陷也可直接采用切除缺陷改尺的方法或直接判废次。
3. 出现批量氧化铁皮时应及时通知轧钢。
可能混淆的缺陷:一次氧化铁皮缺陷名称氧化铁皮麻坑Scale pit照片缺陷形貌及特征:氧化铁皮麻坑是指钢板表面局部或成片的粗糙面,在钢板抛丸后比较多见。
抛丸前氧化铁皮麻坑附近常伴有氧化物。
缺陷形貌及特征:氧化铁渣压入是钢板表面点状或块状不规则分布的铁氧化物压入,缺陷颜色一般呈黑色,缺陷表面通常高于钢板本体。
缺陷成因:1. 除鳞时从板面上清除的氧化铁皮粘附或堆积在轧机导板、护板、切水板等部位,当受到外力振动时这些氧化铁渣掉落到钢板表面并被压入钢板本体。
2. 氧化铁皮粘附在轧辊表面并被压入钢板。
3. 钢板有翘扣头,在轧制过程中卷入轧机导板外的氧化铁渣并被压入钢板下表面。
预防:1. 定期检查并清理轧机机架各部分堆积的氧化铁渣。
2. 轧制过程中利用除鳞水冲洗,防止氧化铁渣堆积。
推荐处理措施:通常可修磨去除,当修磨处最小厚度不满足合同要求时可切除缺陷改尺或厚度改规可混淆的缺陷:夹渣缺陷名称氧化铁渣麻坑照片缺陷形貌及特征:氧化铁渣麻坑是指钢板表面块状的底部粗糙的凹坑,有时在附近有残留的氧化铁渣,形状各异。
缺陷成因:1. 除鳞时从板面上清除的氧化铁皮粘附或堆积在轧机导板、护板、切水板等部位,当受到外力振动时这些氧化铁渣掉落到钢板表面并被压入钢板本体。
2. 氧化铁皮粘附在轧辊表面并被压入钢板。
3. 钢板有翘扣头,在轧制过程中卷入轧机导板外的氧化铁渣并被压入钢板下表面。
4. 在轧后冷却过程中钢板上的氧化铁渣压入缺陷收缩脱落,或者由于受到外力振动导致钢板上的氧化铁渣压入脱落,形成底面粗糙的麻坑。
预防:1. 定期检查并清理轧机机架部分的氧化铁渣。
2. 轧制过程中利用除鳞水冲洗,防止氧化铁渣堆积。
推荐处理措施:通常可修磨去除,修磨处最小厚度不满足合同要求时可切除缺陷改尺或厚度改规。
可混淆的缺陷:凹坑夹渣压入缺陷名称轧制凹坑Rolling pit照片缺陷形貌及特征:轧制凹坑是指钢板表面点状或块状的热态凹坑,轧制凹坑分布无规则,缺陷形状各异,凹照片缺陷形貌及特征:轧制毛刺压入是指钢板表面呈细条状的热态压痕,缺陷形状通常呈弯曲的细条状,缺陷底面有高温下形成的氧化铁膜,压痕底面的颜色与钢板本体相近缺陷成因:钢板轧制过程中钢板与轧机设备刮擦,形成的毛刺被压入钢板表面。