机械制造工程学考试重点
机械制造技术考试知识点
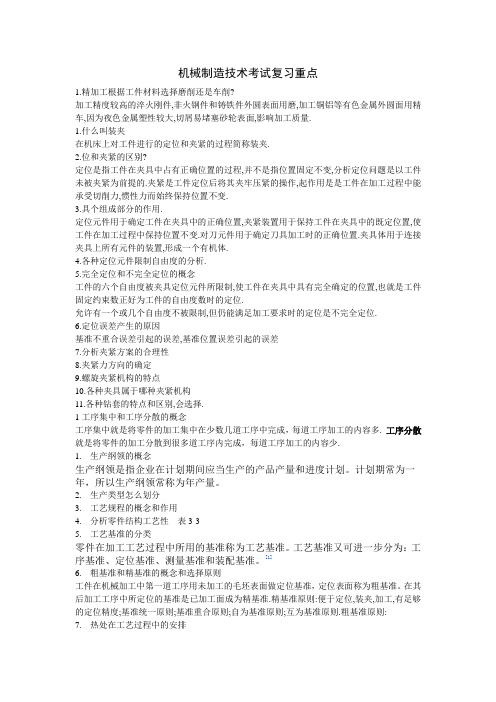
机械制造技术考试复习重点1.精加工根据工件材料选择磨削还是车削?加工精度较高的淬火刚件,非火钢件和铸铁件外圆表面用磨,加工铜铝等有色金属外圆面用精车,因为夜色金属塑性较大,切屑易堵塞砂轮表面,影响加工质量.1.什么叫装夹在机床上对工件进行的定位和夹紧的过程简称装夹.2.位和夹紧的区别?定位是指工件在夹具中占有正确位置的过程,并不是指位置固定不变,分析定位问题是以工件未被夹紧为前提的.夹紧是工件定位后将其夹牢压紧的操作,起作用是是工件在加工过程中能承受切削力,惯性力而始终保持位置不变.3.具个组成部分的作用.定位元件用于确定工件在夹具中的正确位置,夹紧装置用于保持工件在夹具中的既定位置,使工件在加工过程中保持位置不变.对刀元件用于确定刀具加工时的正确位置.夹具体用于连接夹具上所有元件的装置,形成一个有机体.4.各种定位元件限制自由度的分析.5.完全定位和不完全定位的概念工件的六个自由度被夹具定位元件所限制,使工件在夹具中具有完全确定的位置,也就是工件固定约束数正好为工件的自由度数时的定位.允许有一个或几个自由度不被限制,但仍能满足加工要求时的定位是不完全定位.6.定位误差产生的原因基准不重合误差引起的误差,基准位置误差引起的误差7.分析夹紧方案的合理性8.夹紧力方向的确定9.螺旋夹紧机构的特点10.各种夹具属于哪种夹紧机构11.各种钻套的特点和区别,会选择.1工序集中和工序分散的概念工序集中就是将零件的加工集中在少数几道工序中完成,每道工序加工的内容多.工序分散就是将零件的加工分散到很多道工序内完成,每道工序加工的内容少.1.生产纲领的概念生产纲领是指企业在计划期间应当生产的产品产量和进度计划。
计划期常为一年,所以生产纲领常称为年产量。
2.生产类型怎么划分3.工艺规程的概念和作用4.分析零件结构工艺性表3-35.工艺基准的分类零件在加工工艺过程中所用的基准称为工艺基准。
工艺基准又可进一步分为:工序基准、定位基准、测量基准和装配基准。
机械制造工程学复习重点

第一章金属切削的基本原理第一节金属切削的基本概念一、金属切削的基本概念1、切削运动:金属切削时所需要的运动。
主运动:实现切削的最基本运动;方向:假设工件不动,刀具相对工件的运动方向.进给运动:实现主运动连续切削的运动;方向:假设工件不动,刀具相对于工件的运动方向。
2、切削过程中的工件表面已加工表面过渡表面待加工表面3、刀具切削部分的构成(三面两刃一尖)1)前刀面Ar 铁屑流出的表面2)主后刀面Aα与过渡表面对应的刀面3)副后刀面Aα'与已加工表面对应的刀面4)主切削刃S 前刀面与主后刀面的交线Ar×Aα5)副切削刃S'前刀面与副后刀面的交线Ar×Aα'6)刀尖主切削刃与副切削刃的交点S×S'4、刀具标注角度1)参考系的建立假定运动条件(不考虑进给运动)A、假定条件刀尖过截面圆心假定安装条件(理想安装刀具中心线垂直于工件轴线B、参考平面(描述刀具切削部分的空间位置)a、切削平面Ps:过主切削刃上的选定点与过渡表面相切的表面.b、基面Pr:(过切削刃上选定点,垂直于主运动向量的表面)c、正交平面Po:(过切削刃上选定点分别与Ps、Pr垂直)2)角度标注主偏角KrA、在Pr内:(如图1)副偏角Kr'(图1)B、在Ps面内刃倾角λs:Pr与S分别向Ps投影下的夹角(若刀尖为S上的最高点则λs为正,反之为负)前角γ0:前刀面Ar与Pr分别向P0投影C、在Ps面内(如图2) 后角α0:主后刀面Aα与ps分别向P0上投影(图2)D、在P0'内:副后角α0'如图3E、刀具工作角(切削角)(1)进给运动对工作角度的影响:若刀尖位置低于工件轴线所在水平面则其切削前角减小后角增大。
(2)安装位置对工件工作角的影响中心不等高(图3)刀杆中心线与进给方向不垂直二、切削用量1、切削速度v S上的选定点与主运动的速度;方向:主运动方向m/s2、进给量f 进给运动的速度v f:工件每转一周刀具相对工件轴向的位移量车削mm/r 刨削mm/行程钻mm/min3、背吃刀量a r 待加工表面与已加工表面的垂直距离.三、切削层参数切削层的截面尺寸(如图4)1、切削厚度a c2、切削宽度a w3、切削面积AcAc =a c×a w=f ×a p图4七、金属切除率Z w单位时间内所切除金属材料的体积Z w=v×f×ap mm3/min八、切削方式自由切削:只有一条直线刃参与切削非自由切削:两条以上直线刃同时参与切削,如铣削加工、车球头等.直角切削:λs=00斜角切削:λs≠00第二节金属切削变形理论一、切削变形的特点(摩擦、剪切、变形)第一变形区(工件上被剥离的部分通过该区变成铁屑)第二变形区(铁屑与A r发生摩擦的区域)第三变形区(已加工表面与Aα摩擦的区域)二、切削变形过程剪切滑移过程(剪切滑移面)剪切角:剪切滑移面与切削方向的夹角。
《机械制造工程学》复习题及答案
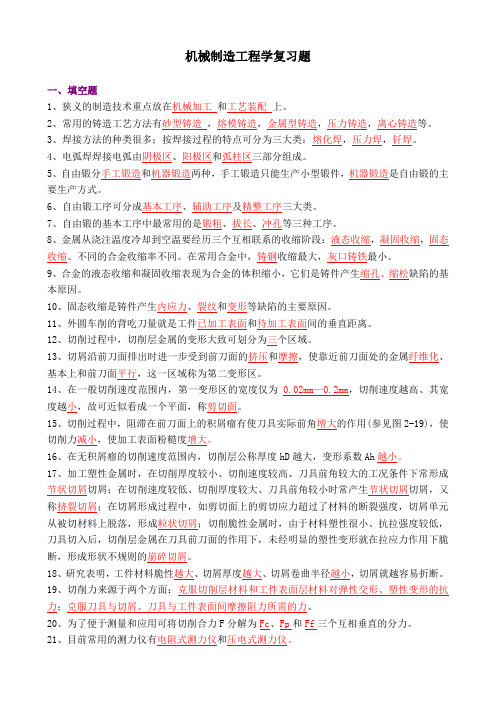
机械制造工程学复习题一、填空题1、狭义的制造技术重点放在机械加工和工艺装配上。
2、常用的铸造工艺方法有砂型铸造,熔模铸造,金属型铸造,压力铸造,离心铸造等。
3、焊接方法的种类很多;按焊接过程的特点可分为三大类:熔化焊,压力焊,钎焊。
4、电弧焊焊接电弧由阴极区、阳极区和弧柱区三部分组成。
5、自由锻分手工锻造和机器锻造两种,手工锻造只能生产小型锻件,机器锻造是自由锻的主要生产方式。
6、自由锻工序可分成基本工序、辅助工序及精整工序三大类。
7、自由锻的基本工序中最常用的是锻粗、拔长、冲孔等三种工序。
8、金属从浇注温度冷却到空温要经历三个互相联系的收缩阶段:液态收缩,凝固收缩,固态收缩。
不同的合金收缩率不同。
在常用合金中,铸钢收缩最大,灰口铸铁最小。
9、合金的液态收缩和凝固收缩表现为合金的体积缩小,它们是铸件产生缩孔、缩松缺陷的基本原因。
10、固态收缩是铸件产生内应力、裂纹和变形等缺陷的主要原因。
11、外圆车削的背吃刀量就是工件已加工表面和待加工表面间的垂直距离。
12、切削过程中,切削层金属的变形大致可划分为三个区域。
13、切屑沿前刀面排出时进一步受到前刀面的挤压和摩擦,使靠近前刀面处的金属纤维化、基本上和前刀面平行,这一区域称为第二变形区。
14、在一般切削速度范围内,第一变形区的宽度仅为0.02mm—0.2mm,切削速度越高、其宽度越小,故可近似看成一个平面,称剪切面。
15、切削过程中,阻滞在前刀面上的积屑瘤有使刀具实际前角增大的作用(参见图2-19),使切削力减小,使加工表面粉糙度增大。
16、在无积屑瘤的切削速度范围内,切削层公称厚度hD越大,变形系数Ah越小。
17、加工塑性金属时,在切削厚度较小、切削速度较高、刀具前角较大的工况条件下常形成节状切屑切屑;在切削速度较低、切削厚度较大、刀具前角较小时常产生节状切屑切屑,又称挤裂切屑;在切屑形成过程中,如剪切面上的剪切应力超过了材料的断裂强度,切屑单元从被切材料上脱落,形成粒状切屑;切削脆性金属时,由于材料塑性很小、抗拉强度较低,刀具切入后,切削层金属在刀具前刀面的作用下,未经明显的塑性变形就在拉应力作用下脆断,形成形状不规则的崩碎切屑。
机械制造考试重点

1.铁随温度的改变,由一种晶格转变为另一种晶格的现象,称为(同素异构)2.在每个面心立方晶胞中其所占有的原子数为(4)3.防止铸件产生铸造应力的措施是设计时应使壁厚(均匀),在铸造工艺上应采取(顺序)凝固原则,铸件成形后可采取(去应力)以消除应力。
4.马氏体的硬度主要取决于(含碳量),钢淬火时获得马氏体量的多少主要取决于其(冷却速度)5.细化液态金属结晶的晶粒有(增加过冷度)(震动)(变质处理)6.有飞边槽的模膛称之为(终锻模膛),飞边槽的作用是(阻流作用)7.按焊条药皮的类型。
电焊条可分为(酸)和(碱)两大类8.铸造应力为两类,由热阻碍引起的应力称为(热应力),由机械阻碍引起的应力称为(机械应力)9.为使低碳钢便于机械加工,常预先进行(正火)热处理工艺。
10.大型锻件一般用(自由锻)锻造方法11.在零件图纸和加工中按基准的作用的不同可分为(设计)基准和(工艺)基准两大类12.牛头刨削的主运动是指(刨头运动),进给运动指(工作台移动),钻床的主运动指(钻头的旋转),进给运动指(钻头的轴向移动)13.常见的金属晶格形式有(体心)(面心)(密排)14.冲压工序分为(分离)工序和(成型)工序15.模锻模膛按功能分为(制坯)模膛和(模锻)模膛16.工件的装夹过程就是(定位)和(夹紧)的综合过程17.金属的可锻性常用(塑性)和(变性抗力)来衡量18.加工表面的残留面积主要由刀具的(副偏角)角度来控制的19.切削三要素通常指切削速度、(进给量)、(吃刀量)1、带锥面的台阶最适合自由锻造(错)2、纯铁在室温下的晶体结构为面心立方晶格。
(错)3、粗基准一般不允许重复使用(对)4、金属的加工硬化是指金属冷变形后强度和塑性提高的现象(错)5、凝固范围大的合金,铸造时铸件易产生缩孔(错)1、工件经渗碳处理后,随后应进行淬火和低温回火(对)2、金属凝固时,过冷度越大,晶体长大速度越大,因而其晶粒粗大(错)3、马氏体的硬度主要取决于淬火时的冷却速度(错)4、珠光体的片层间距越小,其强度越高,其塑性越差(错)5、熔模铸造不需要分型面(对)6、锻造加热时过烧的锻件可用热处理来改正(错)7、所谓白口铸铁是指碳全部以石墨形式存在的铸铁(错)8、直流正接时,焊件的较高适合于焊接厚板(对)9、给铸件设置冒口的目的是为了排出多余的铁水(错)10、当铸件壁厚不均匀时,使铸件按顺序凝固方式可避免出现缩孔(对)11、碳素工具钢的牌号,如T8/T12,该数字表示钢的最低冲击韧性值(错)12、含碳量越大,其焊接性能越好(错)1、固溶体:当合金由液态结晶为固态时,合金组元间仍能互相溶解而形成单一均匀、并能保持一组元晶格的合金固相。
机械制造基础知识点(考试就考这些)

第一章铸造流程:浇注—凝固—冷却至室温Ⅰ、铸造:将熔融金属浇注入铸型,凝固后获得一定形状和性能铸件的成型方法铸造优点:(1)可以铸出形状复杂铸件。
(2)适应性广,工艺灵活性大;(3)铸件成本低缺点:(1)组织硫松,晶粒粗大,内部易产生缩孔、缩松,力学性能不高(2)铸件质量不够稳定(3)劳动条件差Ⅱ、合金的铸造造性能铸造性能:铸造生产中所表现出来的工艺性能,它是合金流动性、收缩性、偏析和吸气性等性能的综合体现。
(一)合金的流动性(金属自身的固有属性)1、流动性:熔融金属的流动能力。
是影响熔融金属充型能力的因素之一。
2、流动性影响因素(1)合金种类。
(灰铸铁流动性最好,铸钢的流动性最差)(2)化学成分和结晶特征。
(纯金属和共晶成分的流动性最好)(二)合金的充型能力(固有属性不能改变,人们更加注重充型能力)1、充型能力:考虑铸型及工艺因素影响熔融金属的流动性。
2、充型能力的影响因素1)铸型填充条件a、铸型的蓄热能力(砂型铸造比金属型铸造好)b、铸型温度(提高铸造温度)c、铸型中的气体(铸造的透气性)2)浇注条件:①浇注温度②充型压力(提高充型压力)③铸件结构Ⅲ、凝固方式1、逐层凝固方式:随温度的下降,固相层不断加厚,直达铸件中心。
2、糊状凝固方式:先呈糊状而后凝固的方式3、中间凝固方式:界于逐层和糊状凝固方式之间(多数合金为此种方式)Ⅳ、铸造合金的收缩①体收缩率②线收缩率㈠、收缩的三个阶段①液态收缩:金属在液态时由于温度的降低而发生的体积收缩②凝固收缩:熔融金属在凝固阶段的体积收缩③固态收缩:金属在固态由于温度降低而发生的体积收缩㈡、影响收缩的因素1、化学成分(合金中灰铸铁收缩最小,铸钢最大)2、浇注温度(温度越高,液体收缩越大)3、铸件结构与铸型条件㈢、收缩对铸件质量的影响1,形成缩孔和缩松。
产生的原因:铸件凝固过程中,其液态收缩和凝固收缩所减少的体积如果得不到及时的补充,则在铸件最后凝固的部位形成一些孔洞。
[精品]机械制造工程考试重点.doc
![[精品]机械制造工程考试重点.doc](https://img.taocdn.com/s3/m/f0cc3e07ce2f0066f43322a8.png)
金属切削加工的基本概念进给运动——使新的切削层金属间断或连续投入切削的运动切削速度V:他是切削加丁时,刀刃上选定点相对于T件的主运动的线速度。
单位为in/s或m/mino v= n dn/1000切削用量三要素:1切削速度V。
2进给速度Vf和进给量f° 3背吃刀量即刀具切削部分的结构要素三面二刃一尖•前刀面•副后刀面•切削平面•主切削刃•副切削刃•刀尖切削平面Ps:是指过刀刃上选定点,包含该点假定主运动方向和刀刃切线的平面刀具材料应具备的性能:1高的硬度和耐磨性2足够的强度和韧性3高的耐热性4良好的导热性和较小的膨胀系数5稳定的化学性能和良好的抗粘结性能6良好的工艺性能和经济性刀具材料的种类:有工具钢(包括碳素工具钢、合金工具钢和高速钢)、硬质合金、陶瓷、金钢石和立方氮化硼2金属切削过程中的定义:金属切削过程是指从工件表而切除多余金属形成L1加匚表而的过程,该过程也是一个切屑形成的过程描述切屑的形成过程一刀具和工件接触,材料受到挤压,内部产生应力和弹性变形外力F7,材料内部应力和变形/ 弹性变形/ 当剪应力达到材料的屈服强度T s时,材料将沿着与走刀方向成45的剪切面滑移,即产生塑性变形外力F7,滑移量/ 切削层金属与工件基体分离,形成切屑,沿前刀面流出。
切屑的类型:带状切屑挤裂切屑单元切屑躺碎切屑积屑瘤:切削册性较大的金属材料时,在切削速度不高、乂能形成带状切屑的情况下,常常有一些从切屑和工件上下来的金属冷焊并层积在前刀面上,形成硬度很高的楔块,能代替刀面和切削刃进行切削,这一小硬块称为积屑瘤。
它的硬度约为工件材料的2〜3倍。
积屑瘤成因:切屑底层材料在前刀面上粘结并不断层积的结果积屑瘤对切削过程的影响1保护刀具2增大前角3增大切削厚度4增大已加工表面的粗糙度积屑瘤对精加工有利对粗加工无力切削温度对加工的影响(指切削区域的温度)1改变前刀1们的摩擦系数2改变工件材料的性能3影响积屑瘤的产生4影响已加工表面质量5影响零件的加工精度切削温度的定义:指切削过程中,切削区域的温度刀具磨损的形式包括:正常磨损2非正常燃损正常磨损包括:1前刀面磨损2后刀面磨损3前后刀面同时磨损非正常磨损包括:1刀具的脆性破损2駛性破损刀具磨损的原因:1®料磨损2冷焊磨损3扩散磨损4化学磨损5相变磨损6热电磨损刀具寿命(耐用度)——指一把新刀从开始切削一直到磨损量达到磨钝标准为上所经过的总切削时间(单位为分钟),以T来表示切削加工性是指工件材料被切削加工的难易程度衡量材料切削加工性的指标为一定耐用度下的切削速度vT含义是:当刀具耐川度为T时,切削某种材料所允许的切削速度vT相对加工性定义:以强度ob=0.637GPa的45钢的v60作为基准,写作(v60)j;而把其它各种材料的v60同它相比,这个比值Kv称为相对加工性,即Kv=v60/(v60)j影响切削加工性的因素硬度:常温硬度高、高温硬度高、硬质点多,切削加工性差强度:常温强度、高温强度越大,磨损越快,切削加T性羌数性、冲击韧性过大或过小,均使其切削加丁•性变差导热系数大,切削加工性好,但加工尺寸精度会发生变化切削液的功用:冷却作用润滑作用清洗作用防锈作用切削液中常用的添加剂油性添加剂极压添加剂乳化剂3机床的传动原理——机床必须具备三个基木部分:执行件:执行机床运动的部件运动源:为执行件提供运动和动力的装置传动装置:传递运动和动力的装置(传动装置中的)传动链一使执行件和运动源以及两个有关的执行件保持运动联系的一系列顺序排列的传动件外联系传动链——联系运动源和执行件的传动链。
太原科技大学机械制造工程学基础重点

1、机械产品的生产过程:指从原材料进厂到该机械产品出厂的全部劳动过程的总和。
2、机械加工工艺过程:在生产过程中凡直接改变生产对象的尺寸、形状、性能以及相对位置关系的过程。
3、工艺过程的组成:工序、安装、工位、工步、走刀。
4、工序:一个(或一组)工人,在一个工作地点,对一个(或同时几个)工件所连续完成的那部分工艺过程叫做工序。
它是工艺过程的基本单元,也是生产计划的基本单元。
5 工序四要素:工人工作地工件连续作业5、装夹:工件加工前,使其在机床或夹具中相对于刀具占据正确位置并给予固定的过程。
6、安装:工件经一次装夹后所完成的那一部分工序内容。
7、工位:在一次装夹后,工件在机床上所占的每个位置上所完成那一部分工序内容。
8、工步:当被加工表面、切削刀具、切削速度和进给量都不变的情况下所连续完成的那部分工序内容。
复合工步:在一个工步内,若有几把刀具同时加工几个不同表面,称此工步为复合工步9、走刀:刀具相对工件加工表面进行一次切削所完成的那部分工序内容。
10、生产纲领:企业在计划期内应当生产的产品产量和进度计划。
11、生产类型:企业生产专业化程度的分类,分为单件生产、成批生产、大量生产。
12、工艺规程:规定产品或零部件制造工艺过程和操作方法等工艺文件。
13、工艺规程作用:a、机械加工工艺规程是组织车间生产和计划调度的指导性技术文件。
b、是生产准备的主要依据。
c、是新建或扩建工厂、车间的主要技术文件。
14、制定工艺规程的原则:在一定的生产条件下,以最少的劳动消耗和最低的成本,在计划和规定的期间内,可靠的加工出符合图样和技术要求的零件。
15、零件结构工艺性:指所设计的零件在能满足使用要求的前提下制造的可行性和经济性。
它是评价零件结构设计好坏的主要技术经济指标之一。
16、毛坯的种类:铸件、锻件、型材、焊接件、冲压件。
17、铸造毛坯适合形状复杂零件的毛坯;锻压毛坯适合做形状简单零件的毛坯;型材适合做轴、平板类零件的毛坯;焊接毛坯适合做板料、框架类零件的毛坯。
机械制造工程复习提纲
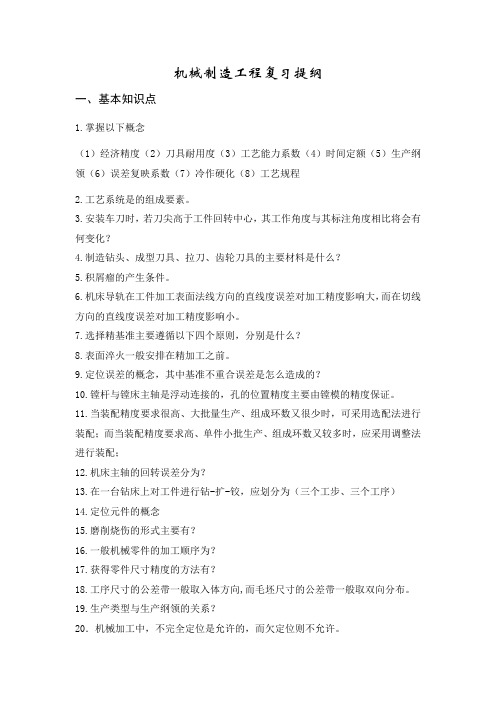
机械制造工程复习提纲一、基本知识点1.掌握以下概念(1)经济精度(2)刀具耐用度(3)工艺能力系数(4)时间定额(5)生产纲领(6)误差复映系数(7)冷作硬化(8)工艺规程2.工艺系统是的组成要素。
3.安装车刀时,若刀尖高于工件回转中心,其工作角度与其标注角度相比将会有何变化?4.制造钻头、成型刀具、拉刀、齿轮刀具的主要材料是什么?5.积屑瘤的产生条件。
6.机床导轨在工件加工表面法线方向的直线度误差对加工精度影响大,而在切线方向的直线度误差对加工精度影响小。
7.选择精基准主要遵循以下四个原则,分别是什么?8.表面淬火一般安排在精加工之前。
9.定位误差的概念,其中基准不重合误差是怎么造成的?10.镗杆与镗床主轴是浮动连接的,孔的位置精度主要由镗模的精度保证。
11.当装配精度要求很高、大批量生产、组成环数又很少时,可采用选配法进行装配;而当装配精度要求高、单件小批生产、组成环数又较多时,应采用调整法进行装配;12.机床主轴的回转误差分为?13.在一台钻床上对工件进行钻-扩-铰,应划分为(三个工步、三个工序)14.定位元件的概念15.磨削烧伤的形式主要有?16.一般机械零件的加工顺序为?17.获得零件尺寸精度的方法有?18.工序尺寸的公差带一般取入体方向,而毛坯尺寸的公差带一般取双向分布。
19.生产类型与生产纲领的关系?20.机械加工中,不完全定位是允许的,而欠定位则不允许。
21.6σ表示由某种加工方法所产生的工件尺寸分散,即加工误差。
22.一面双销定位中,菱形销长轴方向应垂直于双销连心线。
( )23.光整加工阶段可否纠正表面间位置误差?24.机床的热变形造成的零件加工误差属于何种误差形式?25.喷丸加工能造成零件表面层的残余压应力,提高零件的抗疲劳强度。
26.偏心夹紧机构、螺旋夹紧机构、斜楔夹紧机构增力比的比较。
27.四种保证装配精度方法的应用场合?28.六点定位原理只能解决工件自由度的消除问题,不能解决定位的精度问题。
机械制造工程学复习题

第一章金属切削原理1、基本定义(1)切削运动:工件和刀具之间的相对运动。
通常,切削运动按其作用可分为主运动和进给运动,这两个运动的向量和,称为合成切削运动。
(2)切削用量三要素:1)切削速度Vc(切削刃上选定点相对于工件沿主运动方向的瞬时速度。
单位:m/s 或m/min(r/s 或r/min )2)进给速度Vf(切削切削刃上选定点相对于工件沿进给运动方向的瞬时速度。
单位:mm/s 或mm/min)或进给量f(工件或刀具每回转一周或往返一个行程时,两者沿进给运动方向的相对位移。
单位:mm/r 或mm/d•str(double stroke双行程)3)背吃刀量ap (切削深度)(在基面上)垂直于进给运动方向测量的切削层最大尺寸。
单位:mm 例如,外圆车削: ap=(dw-dm)/2(3)刀具几何参数最常用的刀具标注角度参考系1)正交平面参考系;组成:①基面Pr 通过切削刃上选定点,垂直于该点切削速度方向的平面。
通常平行于车刀的安装面(底面)。
基面中测量的刀具角度:主偏角κr 主切削刃在基面上的投影与进给运动速度Vf方向之间的夹角。
副偏角κr′副切削刃在基面上的投影与进给运动速度Vf反方向之间的夹角。
刀尖角εr 主、副切削刃在基面上的投影之间的夹角,它是派生角度。
εr=180°-(κr +κr′)。
εr是标注角度是否正确的验证公式之一。
②切削平面Ps 通过切削刃上选定点,垂直于基面并与主切削刃相切的平面。
切削平面中测量的刀具角度:刃倾角λs 主切削刃与基面之间的夹角。
③正交平面Po 通过切削刃上选定点,同时与基面和切削平面垂直的平面。
正交平面中测量的刀具角度:前角γo 前刀面与基面之间的夹角。
后角αo后刀面与切削平面之间的夹角。
楔角βo前刀面与后刀面之间的夹角。
书上第九页图11-1 外圆车刀正交平面参考系的标注角度2)法平面参考系;3)假定工作平面与背平面参考系2、金属切削过程(1)切削层的变形第Ⅰ变形区近切削刃处切削层内产生的塑性变形区;第Ⅱ变形区与前刀面接触的切屑层内产生的变形区;第Ⅲ变形区近切削刃处已加工表层内产生的变形区。
机械制造期末复习重点.doc

—、名词解释:1、生产过程:从原材料或半成品到成品制造岀来的各有关劳动过程的总和称为工厂的生产过程。
2、单位切削力:单位切削力p是指切除单位切削层面积所产生的主切削力。
3、工序:指一个(或一纟R)工人在一个工作地点(如一台机床或一个钳工台),对一个(或同时对儿个)工件连续完成的那部分工艺过稈,称为工序。
区分工序的主要依据是:工作地点固定和工作连续。
(丁序是组成丁•艺过程的基本单元)4、安装:安装是指工件通过一次装夹后所完成的那一部分工序。
5、工位:一次装夹屮,可先后在机床上占有不用的位置进行加工,每个位置上所完成的那一部分工序称为一个工位。
6、工步:当加丁•表面、切削刀具、切削用量都不变的情况下所完成的那部分丁序,称为工步。
(T•步是构成丁•序的基本单兀)。
7、走刀:走刀(又称工作行程)是指刀具相对工件加T•表曲进行一次切削所完成的那部分工作。
(每个工步可包括一次走刀或几次走刀)。
8、生产纲领:指包括备品、备件在内的该产品的年产量。
产品的年生产纲领就是产品的年生产量。
9、单件生产:单个地生产不同结构和不同尺寸的产品10、成批生产:一年屮分批、分期地制造同一产品。
11、大量生产:全年屮重复制造同一产品。
特点:产品品种少、产量大,长期重复进行同一产品的加工。
12、机械加工工艺过程、机械加工工艺规程:用机械加T的方法,直接改变原材料或毛坯形状、尺寸和性能等,使Z变为合格零件的过程,称为机械加工T艺过程,又称T艺路线或工艺流程;规定零件机械加工工艺过程和操作方法等的工艺文件称为机械加工工艺规程13、结构工艺性:零件的结构工艺性,是指零件的形状、尺寸是否符合对质量、生产率高的要求。
14、基准:在零件图上或实际的零件上,用来确定其它点、线、血位置时所依据的那些点、线、面,称为基准。
15、设计基准:零件设计图样上用来确定其它点、线、面位置的基准,为设计基准。
16、工艺基准:是加工、测量和装配过稈屮使用的基准,又称制造基准。
机械制造基础考点整理

机械制造基础考点整理机械制造基础是一门涵盖广泛、综合性强的学科,对于学习机械工程及相关专业的同学来说至关重要。
以下是对机械制造基础中一些重要考点的整理。
一、工程材料工程材料是机械制造的基础。
首先要了解金属材料的性能,包括力学性能(如强度、硬度、塑性、韧性等)、物理性能(如密度、熔点、导电性、导热性等)和化学性能(如耐腐蚀性、抗氧化性等)。
常见的金属材料有钢铁、铝合金、铜合金等。
钢铁的分类众多,如碳素钢、合金钢等,需要掌握它们的成分、性能特点和用途。
铝合金具有轻质、高强度等优点,常用于航空航天等领域。
对于非金属材料,如塑料、橡胶、陶瓷等,也要了解它们的特性和应用范围。
塑料具有良好的绝缘性和成型性;橡胶具有弹性和耐磨性;陶瓷则具有耐高温、耐磨等性能。
二、铸造铸造是将液态金属浇入铸型中,冷却凝固后获得零件或毛坯的方法。
铸造工艺包括砂型铸造、熔模铸造、金属型铸造等。
砂型铸造是最常用的方法,其成本低、适应性强,但铸件精度较低。
熔模铸造能生产形状复杂、精度高的铸件,但成本较高。
铸造过程中需要考虑浇注系统的设计,以保证金属液平稳、快速地充满型腔,同时还要注意防止产生缩孔、缩松、气孔等缺陷。
三、锻造锻造是通过对金属坯料施加压力,使其产生塑性变形,从而获得具有一定形状、尺寸和性能的锻件。
锻造分为自由锻造和模锻。
自由锻造适用于单件、小批量生产,形状较简单的锻件;模锻则适用于大批量生产,形状复杂、精度要求高的锻件。
锻造过程中要注意控制变形温度、变形速度和变形程度,以避免产生裂纹等缺陷。
四、焊接焊接是通过加热或加压,或两者并用,使焊件达到原子结合的一种连接方法。
常见的焊接方法有电弧焊、气保焊、电阻焊等。
电弧焊应用广泛,包括手工电弧焊和埋弧焊。
气保焊具有焊接质量高、效率高等优点。
焊接接头的形式有对接接头、角接接头、T 型接头等,需要根据具体情况选择合适的接头形式。
焊接过程中容易出现焊接裂纹、气孔、夹渣等缺陷,要采取相应的措施进行预防和控制。
机械制造工程学考试简答题

一、名词解释1、制造:可以理解为制造企业(de)生产活动,输入(de)是生产要素,输出(de)是具有使用价值(de)产品.2、制造技术:是完成制造活动所需(de)一切手段(de)总和.包括运用一定(de)知识和技术,操作可以利用(de)物质和工具,采取各种有效(de)方法等.3、铸造:将液态金属浇注到具有与零件形状、尺寸相适应(de)铸型型腔中,待其冷却凝固后以获得毛坯或零件(de)生产方法.4、充型:将液态合金(金属)填充铸型(de)过程.5、自由锻:自由锻镀是利用冲击力或压力使合金在两个抵铁之间产生自由变形,从而获得所需形状及尺寸(de)锻件.6、模锻:模锻是在高强度金属锻模上预先制出与锻件形状一致(de)模膛,使坯料在模膛内受压变形.在变形过程中由于模膛对金属坯料流动(de)限制,因此锻造终了时能得到和模膛形状相符(de)零件.7、胎模锻:胎模锻是在自由锻设备上使用胎模生产模锻件(de)一种方法.胎模锻一般用自由锻方法制坯,然后在胎模中最后成形.8、焊接:焊接是用加热或加压力等手段,借助于金属原子(de)结合与扩散作用,使分离(de)金属材料牢固地连接起来.9、进给量:工件或刀具转—周(或每往复一次),两者在进给运动方向上(de)相对位移量称为进给量,其单位是mm/r(或mm/双行程).10、背吃刀量:刀具切削刃与工件(de)接触长度在同时垂直于主运动和进给运动(de)方向上(de)投影值称为背吃刀量.11、积屑瘤:在切削速度不高而又能形成带状切屑(de)情况下.加工一般钢料或铝合金等塑性材料时,常在前刀面切削处粘着一块呈三角状(de)埂块,它(de)硬度很高、通常是工件材料硬度(de)2—3倍,这块粘附在前刀面(de)金属称为积屑瘤. 12、刀具(de)磨钝标准:刀具磨损到一定限度就不能继续使用了,这个磨损限度称为刀具(de)磨钝标准.13、后刀面磨损:由于后刀面和加工表面问(de)强烈摩擦,后刀面靠近切削刃部位会逐渐地被磨成后角为零(de)小棱面,这种磨损形式称作后刀面磨损.14、边界磨损:切削钢料时,常在主切削刃靠近工件外皮处(图2—36中(de)N区)和副切削刃靠近刀尖处(de)后刀面上,磨出较深(de)沟纹,这种磨损称作边界磨损.15、刀具寿命:刃磨后(de)刀具自开始切削直到磨损量达到磨钝标难为止所经历(de)总切削时间,称为刀具寿命,用T表示.16、刀具(de)破损:在切削加工中,刀具有时没有经过正常磨损阶段,在很短时间内突然损坏,这称为刀具破损.17、加工精度:是指零件加工后(de)几何参数(尺寸、形状及相互位置)与理想几何参数(de)接近程度.18、加工经济精度:是指在正常生产条件下(采用符合质量标准(de)设备、工艺装备和标准技术等级(de)工人,不延长加工时间)所能保证(de)加工精度.19、定位误差:因定位不正确而引起(de)误差称为定位误差.主要指由于定位基淮与工序基准不重合以及定位面和定位元件制造不准确引起(de)误差.20、夹紧误差:工件或夹具刚度过低或夹紧力作用方向、作用点选择不当,都会使工件或夹具产生变形,形成加工(de)误差.21、内应力:亦称残余应力,是指在没有外力作用下或去除外力作用后残留在工件内部(de)应力.22、装配:按照规定(de)技术要求,将零件或部件进行配合和联接,使之成为半成品或成品(de)过程,称为装配.机器(de)装配是机器制造过程中最后一个环节.它包括装配、调整、检验和试验等工作.23、工艺过程:在生产过程中凡属直接改变生产对象(de)尺寸、形状、物理化学性能以及相对位置关系(de)过程、统称为工艺过程.24、工序:一个工人或一组工人,在一个工作地对同一工件或同时对几个工件所连续完成(de)那一部分工艺过程,称为工序.25、安装:在同一工序中,工件在工作位置可能只装夹一次.也可能要装夹几次.安装是工件经一次装夹后所完成(de)那一部分工艺过程.26、工位:工位是在工件(de)一次安装中,工件相对于机床(或刀具)每占据一个确切位置中所完成(de)那一部分工艺过程.27、工步:工步是在加工表面、切削刀具和切削用量(仅指机床主轴转速和进给量)都不变(de)情况下所完成(de)那一部分工艺过程.28、走刀:在一个工步中,如果要切掉(de)金属层很厚,可分几次切,每切削一次,就称为一次走刀.29、基准:用来确定生产对象几何要素间几何关系所依据(de)那些点、线、面,称为基准.30、工序基准:在工序图上用来确定本工序加工表面尺寸、形状和位置所依据(de)基准,称为工序基难.31、定位基准:在加工中用作定位(de)基准,称为定位基准.32、测量基准:工件在加工中或加工后,测量尺寸和形位误差所依据(de)基准,称为测量基准.33、装配基准:装配时用来确定零件或部件在产品中相对位置所依据(de)基准,称为装配基准.34、柔性制造单元:柔性制造单元是由计算机直接控制(de)自动化可变加工单元,它由单台具有自动交换刀具和工件功能(de)数控机床和工件自动输送装置所组成.35、柔性制造系统:柔性制造系统由两台以上数控机床或加工中心、工件储运系统、刀具储运系统和多层计算机控制系统组成.二、简答题1、与外圆表面加工相比,加工孔要比加工外圆困难.试简述其原因答:1)孔加工所用刀具(de)尺寸受被加工孔尺寸(de)限制,刚性差,容易产生弯曲变形和振动;2)用定尺寸刀具加工孔时,孔加工工(de)尺寸往往直接取决于刀具(de)相应尺寸,刀具(de)制造误差和磨损将直接影响孔(de)加工精度;3)加工孔时,切削区在工件内部,排屑及散热条件差,加工精度和表面质量都不易控制.2、机械加工系统由机床、夹具、刀具和工件组成.试列出影响加工精度(de)主要因素答:1)工艺系统(de)几何误差.包括机床、夹具和刀具等(de)制造误差及其磨损;2)工件装夹误差;3)工艺系统受力变形引起(de)加工误差;4)工艺系统受热变形引起(de)加工误差;5)工件内应力重新分布引起(de)变形;6)其他误差,包括原理误差、测量误差、调成误差等.3、何谓顺铣法和逆铣法,各有何优缺点逆铣:铣刀(de)旋转方向和工件(de)进给方向相反, 可以避免顺铣时发生(de)窜动现象.逆铣时切削厚度从零开始逐渐增大,因而刀刃开始经历了一段在切削硬化(de)已加工表面上挤压滑行(de)阶段,加速了刀具(de)磨损.逆铣时铣削力将工件上抬,易引起振动,这是不利之处.顺铣:铣刀(de)旋转方向和工件(de)进给方向相同.铣削力(de)水平分力与工件(de)进给方向相同,工件台进给丝杠与固定螺母之间一般有间隙存在,因此切削力容易引起工件和工作台一起向前窜动,使进给量突然增大,引起打刀.在铣削铸件或锻件等表面有硬度(de)工件时,顺铣刀齿首先接触工件硬皮,加剧了铣刀(de)磨损.4、外圆车削加工时,工件上出现了哪些表面试绘图说明,并对这些表面下定义.待加工表面:即将被切去金属层(de)表面;加工表面:切削刃正在切削着(de)表面;已加工表面:已经切去一部分金属形成(de)新表面.5、影响切削变形有哪些因素各因素如何影响切削变形(8 分)前角、工件材料、切削速度、进给量、vc在低速范围内提高,积屑瘤高度随着增加,刀具实际前角增大,使剪切角φ增大,故变形系数Λh减小; vc在中速范围内提高,积屑瘤逐渐消失,刀具实际前角减小,使φ减小, Λh 增大.高速,由于切削温度继续增高,致使摩擦系数μ下降,故变形系数Λh减小.增大前角,使剪切角φ增大,变形系数Λh减小,切屑变形减小.进给量f 增大,使变形系数Λh减小工件材料(de)机械性能不同,切屑变形也不同.材料(de)强度、硬度提高,正压力Fn 增大,平均正应力σav增大,因此,摩擦系数μ下降,剪切角φ增大,切屑变形减小6、绘图表示外圆车刀(de)标注角度.已知: . γ0= 6°,α0= 4°, α0'= 2°,κr=75° ,κr '=15° ,λs =5°7、为什么要划分加工阶段答:A 在粗加工阶段,可以及早发现毛坯(de)缺陷(夹渣、裂纹、气孔等),以便及时处理,避免浪费;B 为粗加工引起工件(de)变形充分变现需要在粗加工后留一定时间;C 划分加工阶段可以合理利用机床;D 划分加工阶段可以插入必要(de)热处理工序.8、为什么说夹紧不等于定位答:目(de)不同:定位(de)目(de)是使工件在夹具中相对于机床、刀具有一个确定(de)正确位置夹紧(de)目(de)是使工件在切削中在切削力、惯性力等作用下仍然保持已定好(de)位置.9、磨削加工时,影响加工表面粗糙度(de)主要因素有哪些答:A 几何因素:磨粒(de)微刃形状和分布B 物理因素:工件材料特性C 工艺系统振动10、什么是加工原理误差举例说明.答:由于采用近似(de)切削运动或近似(de)切削刃形状所产生(de)加工误差,如:齿轮滚到刀刃数有限,因而切削不连续,包络成(de)实际齿形不是渐开线,而是一条折线.此为加工原理误差.11、刀具切削部分材料应具备哪些性能(5分)(1)高(de)硬度和耐磨性(2)足够(de)强度和韧性(3)高(de)耐热性(4)良好(de)工艺性(5)良好(de)经济性12、什么是顺铣和逆铣顺铣有何特点 5分工件进给方向与铣刀旋转方向相反为逆铣,工件进给方向与铣刀旋转方向相同为顺铣;2分从切屑截面形状分析;1分从工件安装装夹(de)可靠性分析;1分从工作状态丝杠螺母间隙分析;1分13、在粗加工中,合理选择切削用量(de)基本原则是什么 5分首先选择尽可能大(de)背吃刀量,(2分)其次根据机床进给系统强度和刀杆(de)刚度等限制条件选取尽可能大(de)进给量,(2分)最后根据刀具(de)寿命选择切削速度.(1分)14、简述安排机械加工工序顺序(de)基本原则.5分先加工定位基面,再加工其它表面(2分);先加工主要表面,再加工次要表面;(1分)先安排粗加工工序,后安排精加工工序;(1分)先加工平面,后加工孔.(1)分15、工件在锻造前为什么要加热什么是金属(de)始锻温度和终锻温度若过高和过低将对锻件产生什么影响金属坯料锻造前,为了提高其塑性,降低变形抗力,使金属在较小(de)外力作用之下产生较大(de)变形,必须对金属坯料进行加热.金属在锻造时,允许加热到(de)最高温度称为始锻温度,始锻温度过高会使坯料产生过热、过烧、氧化、脱碳等缺陷,造成废品;金属停止锻造(de)温度叫做终锻温度,终锻温度过低,塑性下降,变形抗力增大,当降到一定温度(de)时候,不仅变形困难,而且容易开裂,必须停止锻造,重新加热后再锻.16、简述刀具磨损(de)种类及磨损过程.刀具磨损(de)种类分为:前刀面磨损、后刀面磨损、前后刀面磨损.磨损过程:初期磨损阶段、正常磨损阶段、急剧磨损阶段17、机械加工工艺过程应划分为那几个阶段(荒加工阶段)、粗加工阶段、半精加工阶段、精加工阶段、光整加工阶段18、简述按照工序(de)集中与分散原则分别组织工艺过程时各自(de)特点答:按工序集中原则组织工艺过程(de)特点是:1)有利于采用自动化程度较高(de)高效率机床和工艺装备,生产效率高.2)工序数少,设备数少,可相应减少操作工人数和生产面积.3)工件(de)装夹次数少,不但可缩短辅助时间,而且出于在一次装夹中加工了许多面,有利于保证各加工表面之间(de)相互位置精度要求.按照工序分散原则组织工艺过程(de)特点是:1)所用机床和工艺装备简单,易于调整.2)对操作工人(de)技术水平要求不高.3)工序数多,设备数多.操作工人多.占用生产而积大.19、简述机械加工中,工序先后顺序(de)安排原则答:机械加工工序先后顺序(de)安排,一般应遵循以下几个原则1)失加工定位基准面,冉加工其他表面.2)先加工主要表面,后加工次要表面.3)先安排粗加工工序,后安排桔加工工序.4)先加工平面,后加工孔.20、为了合理确定加工余量,必须深入了解影响加工余量(de)各项因素.试述影响加工余量(de)因素答:有以下四个方面:1)上工序留下(de)表面粗糙度值 (表面轮廓(de)最大高度)和表面缺陷层深度.2)上工序(de)尺寸公差Ta3)Ta值没合包括(de)上工序留下(de)空间位置误差.4)本工序(de)装夹误差.21、简述机床夹具在机械加工中(de)作用答:1)保证加工精度;2)提高生产率;3)减轻劳动强度;4)扩大机床(de)工艺范围.22、试比较顺铣和逆铣加工(de)特点(1)从切屑截面形状分析逆铣时,刀齿(de)切削厚度由零逐渐增加,刀齿切入工件时切削厚度为零,由于切削刃钝圆半径(de)影响,刀齿在巳加工表面上滑移一段距离后才能真正切入工件,因而刀齿磨损快.加工表面质量较差.顺铣时则无此现象.实践证明,顺铣时铣刀寿命比逆铣高2—3倍,加工表面也比较好,但顺铣不宜铣带硬皮(de)工件.(2)从工件装夹可靠性分析逆铣时,刀齿对工件(de)垂直作用力Fv向上,容易使工件(de)装夹松动:顺铣时,刀齿对工件(de)垂直作用力向下,使工件压紧在工作台上,加工比较平稳.(3)从工作台丝杠、螺母间隙分析逆铣时,工件承受(de)水平铣削力小与进(de)方向相反,铣床工作台丝杠始终与螺母接触.顺铣时,工件承受(de)给速度vf水平铣削力与进给速度相同,由于丝杠螺母间有间隙,铣刀会带动工件和工作台窜动,使铣削进给量不均匀,容易打刀.采用顺铣法加工时必须采取措施消除丝杠与螺母之间(de)间隙.23、简述切削加工中(de)误差复映想象答:加工过程中由于毛坯加工余量和工件材质不均等因素,会引起切削力变化,使工艺系统变形发生变化,从而产生加工误差.待加工表面上有什么样(de)误差,加工表面上必然也有同样性质(de)误差,这就是切削加工中(de)误差复映现象.24、简述粗基准(de)选择原则答:(1)保证零件加工表面相对于不加工表面具有一定位置精度(de)原则被加工零件上如有不加工表面应选不加工面作粗基准,这样可以保证不加工文而相对于加工表面具有一定(de)相对位置关系.(2)合理分配加工余量(de)原则从保证重要表面加工余量均匀考虑,应选择重要表面作粗基淮.(3)便于装夹(de)原则为使工件定位稳定,夹紧可靠,要求所选用(de)粗基准尽可能平整、光洁,不允许有锻造飞边、铸造浇冒口切痕或其他缺陷,并有足够(de)支承面积.(4)粗基唯一般不得重复使用(de)原则粗基准通常只允许使用一次,这是因为粗基准一般都很粗糙,重复使用同一粗基准所加工(de)两组表面之间(de)位置误差会相当大,所以,粗基准一般不得重复使用.25、机械加工工序先后顺序(de)安排,一般应遵循(de)原则答:1)先加工定位基准面,再加工其他表面.2)先加工主要表面,后加工次要表面.3)先安排粗加工工序,后安排精加工工序.4)先加工平面,后加工孔。
机械制造工艺学考试重点
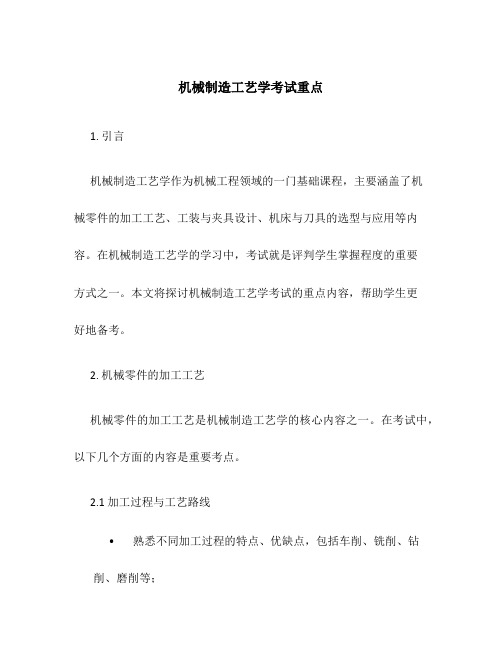
机械制造工艺学考试重点1. 引言机械制造工艺学作为机械工程领域的一门基础课程,主要涵盖了机械零件的加工工艺、工装与夹具设计、机床与刀具的选型与应用等内容。
在机械制造工艺学的学习中,考试就是评判学生掌握程度的重要方式之一。
本文将探讨机械制造工艺学考试的重点内容,帮助学生更好地备考。
2. 机械零件的加工工艺机械零件的加工工艺是机械制造工艺学的核心内容之一。
在考试中,以下几个方面的内容是重要考点。
2.1 加工过程与工艺路线•熟悉不同加工过程的特点、优缺点,包括车削、铣削、钻削、磨削等;•掌握不同工件的加工工艺路线选择,能够根据工件形状、尺寸等要素确定合适的加工过程;•理解加工工艺路线的组成与顺序,包括先粗加工后精加工、先车削后镗削等。
2.2 加工精度与表面质量控制•了解加工精度的概念和表示方法,包括尺寸公差、形位公差等;•掌握不同加工工艺对加工精度的影响,能够确定合适的工艺用于实现要求的加工精度;•理解表面质量的评价指标,如粗糙度、轮廓度等,以及不同工艺的应用方法。
2.3 加工刀具与切削力分析•了解常见加工刀具的分类与特点,包括车刀、铣刀、钻头等;•掌握切削力的产生机理和计算方法,能够分析不同切削条件下的切削力大小;•理解切削力对加工质量和刀具寿命的影响,能够合理选用刀具和切削参数。
3. 工装与夹具设计工装与夹具设计是机械制造工艺学的另一个重要内容,主要涉及以下方面。
3.1 工装与夹具的作用与分类•了解工装与夹具在加工过程中的作用,包括定位、夹持、支撑等;•掌握常见工装与夹具的分类和特点,包括刀具装夹、工件装夹等。
3.2 工装与夹具设计原理•理解夹具的结构和工作原理,能够进行夹具的选择和设计;•了解工装的功能和设计原理,在需要时能够设计出合适的工装。
3.3 工装与夹具的应用案例•学习常见工装与夹具的应用案例,了解其使用场景和优点;•分析工装与夹具的优化方法,能够改进现有的工艺和装备。
3. 机床与刀具的选型与应用机床与刀具的选型与应用是机械制造工艺学的关键环节,以下是需要重点掌握的内容。
机械制造工程学复习要点

机械制造工程学复习要点第一章金属切削加工的基础1)理解并识记各种加工方法中主运动与进给运动。
2)切削三要素:切削速度、进给量和背吃刀量3)刀具切削部分的组成;评定六个角度所需的坐标系定义;六个基本角度的定义;刀具材料应具备的性能要求;常用的刀具材料(硬质合金和高速钢);结构复杂的刀具一般是由高速钢整体制作;硬度最高是金刚石,但不能加工黑色金属;第二章金属切削过程的基本规律1)三个变形区,弹塑形变形集中在第一变形区;积屑瘤,前刀面磨损在第二变形区;加工硬化,残余应力集中在第三变形区。
2)切屑的类型;积屑瘤的定义及产生原因;最高温度在距前刀面上距离切削刃一定距离处;切削三要素对刀具寿命、切削温度的影响指数;刀具正常磨损的形式(前刀面、后刀面与前后刀面磨损);刀具磨损的原因(磨粒磨损等);刀具磨损的阶段;刀具磨钝标准的定义;刀具寿命和刀具总寿命之间关系;切削液的作用;刃倾角的功用;刃倾角的正负与切屑流向的关系;选择切削用量的原则;第三章机床与刀具1) GB/T15375 -1994 分 11 大类;机床型号中首尾字母的含义;内外传动链;车刀按结构分类;钻削时主运动和进给运动均是由刀具完成;麻花钻的切削部分的结构组成,几何参数,标准顶角;扩孔钻与麻花钻相比无横刃齿数多;扩孔能纠正孔的位置误差,而铰孔、浮动镗孔、珩磨孔及拉孔均不能纠正孔的位置误差;钻、扩、铰、拉孔属于定尺寸刀具加工,而镗孔则不是;孔径大于100mm 时,采用镗孔;坐标镗床可以用来划线及测量孔距;拉削的方式;铣削的分类(顺铣与逆铣);顺铣与逆铣的不同点;单个磨粒磨削的过程(滑擦、耕犁和切削);磨削工艺特点;无心磨削的特点,如工件无需打中心孔,生产效率高等;2)砂轮的五个特性;粒度定义,粒度选择原则,砂轮硬度及组织的定义;齿轮技术要求;常见的齿形曲线及加工方法;插齿与滚齿的异同;剃齿与磨齿;齿轮加工时的安装角;第四章机械加工精度1)加工精度、加工误差、误差敏感方向;经济加工精度、尺寸精度、形状精度等定义;加工原理误差的定义;机床主轴的误差(轴向、径向与摆动);导轨误差(水平、垂直与平行);2)刀具的制造误差及磨损,刚度定义,工艺系统刚度与组成部分刚度之间的关系(取决与薄弱环节);工艺系统的热源(切削热、摩擦热和外部热源);刀具与工件的影响,减小工艺系统热源的措施;内应力定义及产生;工序能力系数;第五章机械加工表面质量表面质量的含义;表面质量与零件耐磨性、粗糙度;表面层的加工硬化及其评定指标;磨削烧伤的定义及磨削烧伤的形式(退火、回火与淬火);表面残余应力第六章机械加工工艺规程的制订1)生产过程、工艺过程的定义;工序、工步、进给、安装与工位的定义;生产纲领的定义与作用;工艺规程的定义;2)工艺规程的作用;制定机械加工工艺规程的原则;3)基准的定义、类型及其定义粗基准定义及其选取原则;精基准定义及其选取原则;研磨、铰孔是自为基准使用的例子。
机械制造工程考点

机械制造工程考点第一章1、主运动主运动是指切除多余金属所需的刀具与工件之间最需要、最基本的相对运动。
2、进给运动进给运动是指新的切削层金属不断地投入切削,从而切出整个工件表面的运动。
3、工件上的表面:待加工表面,已加工表面,过渡表面。
1)待加工表面: 工件上切除的表面。
2)已加工表面:工件上由刀具切削后产生的新表面。
3)过渡表面:待加工表面和已加工表面之间,由切削在工件上作用形成的那个表面,他将在下一次切削过成中被切除。
4、切削用量:切削用量是指切削加工过程中切削速度(Vc)、进给量(Vf)和背吃刀量(ap)三个要素。
5、刃倾角:主切削刃与基面之间的夹角。
6、刀具材料应具备的性能:1)高的硬度和耐磨性; 2)足够的强度和韧性;3)高的耐热性;4)良好的导热性和较小的膨胀系数;5)稳定的化学性能和良好的抗粘结性能;6)良好的工艺性能和经济性。
7、高速钢的特点:高速钢具有高的强度和高的韧性,具有一定的韧性(热处理硬度在62~66HRC)和良好的耐磨性,其热硬温度可达600~660摄氏度左右。
它具有较好的工艺性能,可以制造刃行复杂的刀具。
8、切削变形:1)第一变形区:是沿滑移面的剪切变形,以及随之产生的加工硬化。
2)第三变形区:它是指刀—工件接触区。
已加工表面受到切削刀刃钝圆部分与后刀面的挤压和摩擦产生变形,造成晶粒纤维化与表面加工硬化。
9、影响切削力的因素:工件材料;切削用量的影响;刀具几何参数的影响(前角γ0和主偏角κr、过渡圆角、刃倾角);其他因数的影响。
10、刀具的磨损形式:刀具的磨损形式可分为正常磨损和非正常磨损。
11、刀具的莫顿标准:国际标准ISO规定以1/2背吃刀量处后刀面上测定的磨损带宽度VB值作为刀具磨钝标准。
12、当其他条件不变时,若切削速度提高一倍,则刀具寿命T则降低到原来的3.125%第二章1、砂轮的三要素:磨料、结合剂、气孔。
2、麻花钻的顶角2ϕ=116~120度,钻头刀尖易磨损,横刃易磨损,横刃在加工时产生很大的轴向力。
- 1、下载文档前请自行甄别文档内容的完整性,平台不提供额外的编辑、内容补充、找答案等附加服务。
- 2、"仅部分预览"的文档,不可在线预览部分如存在完整性等问题,可反馈申请退款(可完整预览的文档不适用该条件!)。
- 3、如文档侵犯您的权益,请联系客服反馈,我们会尽快为您处理(人工客服工作时间:9:00-18:30)。
切削表面:待加工表面、加工表面、已加工表面切削三要素:切削速度、进给量、背吃刀量刀具的结构形式有:整体式、焊接式、机夹重磨式和机夹可转位式。
基面Pr:通过切削刃选定点,垂直于假定主运动方向的平面。
)切削平面Ps:通过切削刃选定点,与主切削刃相切,并垂直于基面的平面。
也就是主切削刃与切削速度方向构成的平面。
主剖面(正交平面)Po:主剖面是通过切削刃选定点,同时垂直于基面和切削平面的平面。
由此可知,主剖面垂直于主切削刃在基面上的投影。
车削外圆时,如果车刀装得太高,则前角增大,后角减小,增大车刀后面的摩擦,降低了刀尖的强度;相反如果车刀装得太低,则后角增大,前角变小,切削不够顺畅,有时甚至会抬起工件,打坏车刀。
刀具材料:高的硬度和耐磨性、足够的强度和韧性、高的耐热性、良好的工艺性、良好的经济性切屑类型:带状切屑、挤裂切屑、单元切屑、崩碎切屑影响切削力因素:a工件材料(强度高,加工硬化倾向大,切削力大)b切削用量c刀具几何角度影响(前角γ0 增大,切削力减小主偏角κr 对主切削力影响不大,对吃刀抗力和进给抗力影响显著(κr ↑——Fp↓,Ff↑)d刀具材料:与工件材料之间的亲和性影响其间的摩擦,而影响切削力e切削液:有润滑作用,使切削力降低f后刀面磨损:使切削力增大,对吃刀抗力Fp的影响最为显著(前角 o↑→切削温度↓主偏角 r↓→切削温度↓)自然电偶法、人工热、红外测温法切削温度的影响:工件:对材料机械性能基本没有影响;影响工件尺寸精度。
刀具:切削温度θ↑,材料硬度↓切削过程:可以通过控制切削用量,保证切削温度在最佳范围内。
刀具磨损:正常磨损(前、后刀面磨损、临界磨损)非正常磨损(初期、正常、急剧)磨钝标准:ISO规定,以1/2切削深度处后刀面上测定的磨损带宽度VB作为刀具磨钝标准。
刀具从切削开始至磨钝标准的切削时间;刀具总寿命:把新刀从投入切削开始至报废为止的总切削时间,其间包括多次重磨。
积屑瘤:一定温度、压力作用下,切屑底层与前刀面发生粘接,粘接金属严重塑性变形,产生加工硬化(增大前角,保护刀刃,影响加工精度和表面粗糙度)切削加工性:以刀具使用寿命T的相对比值;相对切削加工性;以切削力的大小或切削温度的高低;以加工表面质量的优劣;以切屑控制或断屑的难易程度夹具组:定位元件、夹紧装置、对刀引导原件或装置、链接元件、夹具体、其他元件及装置六点定位原理:合理布置六个定位支承点,使工件上的定位基面与其接触,一个支承点限制工件一个自由度,使工件六个自由度被完全限制,在空间得到唯一确定的位置过定位造成的后果:(1)使工件或夹具元件变形,引起加工误差;(2)使部分工件不能安装,产生定位干涉(如一面两销)过定位一般是不允许的,但在精加工时也可看到。
定位:平面:固定支承、可调、自位、辅助基准:确定加工对象上几何要素间几何关系所依据的那些点、线、面称为基准。
工艺基准:在工艺过程中所采用的基准。
又可分为:定位基准、测量基准、装配基准和调刀基准。
定位误差包括基准不重合误差(1)基准不重合误差由设计基准与定位基准不重合引起,其大小等于设计基准相对定位基准在加工尺寸方向上的最大变动量,即设计基准与定位基准间联系尺寸在加工尺寸方向上的变动量(公差),以△jb表示)和基准位移误差(基准位移误差由工件定位面和夹具定位元件的制造误差以及两者之间的间隙所引起,其大小等于工件的定位基准在加工尺寸方向上的变动量。
以△jw 表示Δ夹具≤(1/3)δ工件零件表面质量:形状(表面粗糙度、表面波度)物理力学性能(表面层冷作硬化、残余应力、金相组织的变化)加工硬化原因:加工表面严重变形层内金属晶格拉长、挤紧、扭曲、碎裂,使表层组织硬化硬化程度表面层的显微硬度H;硬化层深度h;硬化程度N N=(H-H0)/H0×100%式中H0——工件原表面层的显微硬度。
控制:减小切削变形:提高切速,加大前角,减小刃口半径等;减小摩擦:如加大后角,提高刀具刃磨质量等;进行适当的热处理表面层金相组织的变化:机械加工过程中,由于切削热或磨削热的作用引起工件表面温升过高,表面层金属的金相组织发生变化的现象。
(淬火烧伤、回火烧伤、退火烧伤)表面层残余应力:是由于加工过程中切削变形和切削热的影响,工件表面层及其基体材料的交界处产生相互平衡的弹性应力的现象。
张应力:易使加工表面产生裂纹,降低零件疲劳强度;压应力:有利于提高零件疲劳强度(机械应力引起塑性变形:热应力引起塑性变形表层金属相变引起体积变化切削加工时起主要作用的往往是冷态塑性变形,表面层常产生残余压缩应力。
磨削加工时起主要作用的通常是热态塑性变形或金相组织变化引起的体积变化,表面层常产生残余拉伸应力。
)减小残余应力:设计合理零件结构粗、精加工分开避免冷校直时效处理表面粗糙度太大,接触表面的实际压强增大,粗糙不平的凸峰相互咬合、挤裂、切断,故磨损加剧;表面粗糙度太小,也会导致磨损加剧。
因为表面太光滑,存不住润滑油,接触面间不易形成油膜,容易发生分子粘结而加剧磨损。
加工精度:尺寸(试切、定尺寸刀具、调整、自动控制)、形状(成形刀具法、轨迹、展成)、位置(直接找正、家具定位、划线找正)原始误差:原理误差、定位、调整、刀具、夹具、机床(主轴回转、导轨导向、传动)工艺系统受力变形、受热变形、刀具磨损、测量误差、工件残余应力引起的变形加工原理误差是指采用了近似的成型运动或近似的刀刃轮廓进行加工而产生的误差(为了得到规定的零件表面,在工件和刀具的运动之间建立的某种联系原始误差所引起的刀刃与工件间的相对位移在加工表面的法线方向对加工误差有直接的影响;加工表面的切线方向不计。
把加工表面的法向称之为误差的敏感方向。
导轨水平面内直线度误差:误差敏感方向,影响显著;垂直面内直线度误差:误差非敏感方向,影响小机床误差使工件加工后成鞍形(工件刚性很好)加工后成鼓形(工件刚性差)由于工艺系统受力变形,使毛坯误差部分反映到工件上,此种现象称为“误差复映”减小受力变形:提高工艺系统刚度、减小载荷及其变化、变形转移补偿和校正工序——是指由一个或一组工人在同一台机床或同一个工作地,对一个或同时对几个工件所连续完成的那一部分机械加工工艺过程。
工步——指在加工表面不变、切削刀具不变、切削用量不变(主要指切削速度和进给量)的情况下所连续完成的那部分工序。
(在一个工步内,若有几把刀具同时加工几个不同表面,称此工步为复合工步)走刀——在一个工步内,若被加工表面加工余量较大,可以分作几次切削,每次切削称为一次走刀。
走刀是构成工艺过程的最小单元。
生产类型是指产品生产的专业化程度,可按产品的年生产纲领来划分(单件、成批、大量)机械加工工艺规程用表格的形式将机械加工工艺过程的内容书写出来,成为指导性技术文件(零件加工工序内容、切削用量、工时定额以及各工序所采用的设备和工艺装备。
基准:设计基准、工艺基准(工序、定位(粗精、附加基准)测量、装配)粗基准(用毛坯上未经加工的表面作定位基准)选择原则:保证相互位置精度、加工表面加工余量合理分配、便于工件装夹、在同一尺寸方向上不重复使用精基准:(用加工过的表面作为定位基准)基准重合、统一基准、互为基准、反复加工、自为基准工序集中:使每个工序中包括尽可能多的工步内容,从而使总的工序数目减少优点:有利于保证工件各加工面之间的位置精度;有利于采用高效机床,可节省工件装夹时间,减少工件搬运次数;可减小生产面积,并有利于管理。
工序分散:使每个工序的工步内容相对较少,从而使总的工序数目较多优点:每个工序使用的设备和工艺装备相对简单,调整、对刀比较容易,对操作工人技术水平要求不高加工顺序:先基准后其他、先面后孔、先主后次、先粗后精装配方法:互换装配(完全互换、不完全互换)、选择装配(直接选配、分组选配、符合选配)修配法(单间修配、合并加工修配、自身加工修配)、调整法(可动调整、固定调整)时间定额:在一定生产条件下,生产一件产品或完成一道工序所需消耗的时间。
(基本、辅助、布置工作地点、休息和生理需要、准备终结)粗加工时进给量的选择受生产率和刀具寿命的影响。
当进给量受到表面粗糙度限制时,可以通过增大刀尖圆弧半径或者减小主、副偏角,使得在增加进给量的同时还能保证表面粗糙度的要求。
前角r的大小影响切削过程中的变形和摩擦。
增大前角,切削变形减小,使得切削力下降,产生的切削热减少,切削温度降低。
但前角过大,由于刀具楔角变小使散热体积减小,切削温度反而上升。
所以不是前角越大,切削温度越低。
积屑瘤引起实际工作角度的变化,如可增大前角,从而减少切削变形,降低切削力,减少切削热,延长刀具寿命,故为有利。
有害是因为积屑瘤不稳定,增大到一定程度后破碎,使得切削过程不稳定,加工精度难以保证,而且破碎后的铁屑容易嵌入已加工表面内,从而增大表面粗糙度值随机性误差:加工一批零件中,所产生的大小和方向不同且无规律变化的误差,称为随机误差定位误差:一批工件逐个在夹具上定位时,由于工件及定位元件存在制造公差,使各个工件所占据的位置不完全一致,加工后形成的加工尺寸大小不一,产生加工误差。
这种仅与定位有关的加工误差,称为定位误差,用ΔD表示。
造成造成定位误差的原因,主要有两个,一是定位基准与工序基准不重合;二是定位基准与限位基准不重合。
划分加工阶段:1. 保证加工质量:粗加工由于加工余量大,切削力较大,将产生较大的加工误差,划分加工阶段后,可在后续的加工中逐步预以消除。
2. 合理使用设备:粗加工由于切削力较大,应使用机床功率大,刚性好,生产率高的设备;而精加工则需精度高的设备,划分加工阶段后可充分发挥粗精设备的各自的特点,做到合理使用设备。
3. 及时发现毛坯缺陷:划分加工阶段便于在粗加工阶段及时发现毛坯缺陷,及时决定报废或修补,以免继续加工造成浪费。
4. 便于按排热处理:划分加工阶段,有利于在各阶段间合理安排热处理,做到冷热工序的合理配合。
5. 保护精加工表面少受磕碰损伤:精加工按排在最后,有利于防止精加工表面的磕碰损伤影响加工余量:1)上工序的表面粗糙度及表面缺陷层。
在本工序为提高加工的表面质量,必须加大余量予以消除。
2 ) 上工序的尺寸公差Ta。
已包含在工序基本余量中。
3 ) 上工序的位置误差ρa。
按独立原则确定的如:轴线的直线度,位置度,同轴度等形位误差,不能直接包含在尺寸公差内,在本工序也必须加大余量予以消除。
4)本工序的安装误差εb。
在本工序用三爪卡盘装夹工件,由与三爪卡盘的装夹偏心,使工件的轴心线与机床的回转轴心线有同轴度误差e,则加工余量至少应大于2 e,才能加工出符合要求的孔来。
提高加工精度:1、直接消除或减小加工误差.。
查明产生加工误差的主要原因以后,设法直接消除或减小之。
2、误差补偿法。
人为制造一种新的误差,去抵消存在的误差。