铁路客车车体钢结构设计技术
铁路车辆车体结构设计改进方法

铁路车辆车体结构设计的改进方法可以从以下几个方面入手:
1. 轻量化设计:采用新型材料和结构,如高强度钢、铝合金等,以减轻车体重量,提高运载能力和能效。
2. 模块化设计:将车体结构划分为若干模块,便于制造、组装和维护,同时提高了设计的灵活性和通用性。
3. 空气动力学优化:通过改进车体外形和减少空气阻力,降低列车运行时的能耗,提高运行速度和稳定性。
4. 结构强度优化:利用有限元分析等技术,对车体结构进行强度和刚度分析,优化结构设计,提高车体的安全性能。
5. 人性化设计:考虑乘客的舒适性和便利性,优化车内布局和设施设计,提高乘客的满意度。
6. 防火、隔音、隔热设计:采用防火材料、隔音材料和隔热材料,提高车体的防火、隔音、隔热性能,保障乘客的安全和舒适。
7. 耐腐蚀设计:选用耐腐蚀材料和表面处理技术,提高车体的耐腐蚀性能,延长车辆使用寿命。
8. 可持续性设计:在设计过程中考虑环保和可持续发展因素,如材料的回收利用、节能减排等。
通过以上改进方法,可以提高铁路车辆车体结构的设计水平,使其更加安全、高效、舒适和环保。
浅析轨道客车车体钢结构制造工艺
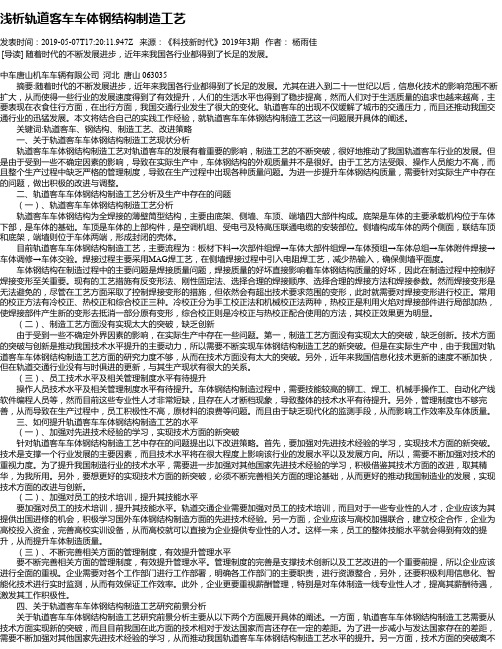
浅析轨道客车车体钢结构制造工艺发表时间:2019-05-07T17:20:11.947Z 来源:《科技新时代》2019年3期作者:杨雨佳[导读] 随着时代的不断发展进步,近年来我国各行业都得到了长足的发展。
中车唐山机车车辆有限公司河北唐山 063035摘要:随着时代的不断发展进步,近年来我国各行业都得到了长足的发展。
尤其在进入到二十一世纪以后,信息化技术的影响范围不断扩大,从而使得一些行业的发展速度得到了有效提升,人们的生活水平也得到了稳步提高,然而人们对于生活质量的追求也越来越高,主要表现在衣食住行方面,在出行方面,我国交通行业发生了很大的变化。
轨道客车的出现不仅缓解了城市的交通压力,而且还推动我国交通行业的迅猛发展。
本文将结合自己的实践工作经验,就轨道客车车体钢结构制造工艺这一问题展开具体的阐述。
关键词:轨道客车、钢结构、制造工艺、改进策略一、关于轨道客车车体钢结构制造工艺现状分析轨道客车车体钢结构制造工艺对轨道客车的发展有着重要的影响,制造工艺的不断突破,很好地推动了我国轨道客车行业的发展。
但是由于受到一些不确定因素的影响,导致在实际生产中,车体钢结构的外观质量并不是很好。
由于工艺方法受限、操作人员能力不高,而且整个生产过程中缺乏严格的管理制度,导致在生产过程中出现各种质量问题。
为进一步提升车体钢结构质量,需要针对实际生产中存在的问题,做出积极的改进与调整。
二、轨道客车车体钢结构制造工艺分析及生产中存在的问题(一)、轨道客车车体钢结构制造工艺分析轨道客车车体钢结构为全焊接的薄壁筒型结构,主要由底架、侧墙、车顶、端墙四大部件构成。
底架是车体的主要承载机构位于车体下部,是车体的基础。
车顶是车体的上部构件,是空调机组、受电弓及特高压联通电缆的安装部位。
侧墙构成车体的两个侧面,联结车顶和底架,端墙则位于车体两端,形成封闭的壳体。
目前轨道客车车体钢结构制造工艺,主要流程为:板材下料→次部件组焊→车体大部件组焊→车体预组→车体总组→车体附件焊接→车体调修→车体交验。
不锈钢地铁车辆车体结构设计的要点研究

不锈钢地铁车辆车体结构设计的要点研究摘要:车体是车辆结构中最重要的部分。
车体材料决定了其结构形式、性能、技术和经济指标。
车体的强度和刚度决定了车体运行的安全性、可靠性和舒适性。
车体的外观和使用寿命取决于车体的耐腐蚀性、能耗、载客量和乘客舒适性,以及与车体重量密切相关的列车编组形式(动拖比)。
目前,中国许多城市已经开始建设轨道交通系统。
在地铁车辆的设计过程中,车体结构非常重要。
本文介绍了不锈钢地铁车辆的主要部件、结构设计方法、车体制造工艺等方面。
关键词:不锈钢地铁车辆;要点;车体结构设计;研究1.不锈钢车辆车体结构特点不锈钢外壳需要外侧板具有平顺性。
不锈钢材质生产出了很好的耐腐蚀性,对于焊接及热变形区有严格要求。
波纹板及波纹下部结构需携带对应重物,同时需要某种强度种类;比重需减小,厚度0.6mm。
侧墙是由整体结构中若干单元组合而成,每一个单元都要承受汽车的重力和多种负荷变形;这些应力集中会使两个主要单体失效,整体系统性能降低。
为确保侧板有合适的刚性与强度,上侧板支撑与横梁之间、下框架等侧板与骨架焊接。
对于大型汽车来说埋弧焊接机器人具有可行性。
当点焊不便,需传递高载荷,可采用环焊、承插焊等等,不会对外观造成影响、降低热效应,提高车体强度等途径。
上部导轨与车体横梁在车体底部总成中所受作用力最大。
焊后须经热处理消除应力集中。
下半身框架拉起缓冲器。
以保证足够强度,传递拉伸,压缩载荷而不产生摩擦,零件用实心焊接工艺。
不锈钢主体因具有自身的特性,对于材料的性能提出了更高的要求,因此,应选择优质钢材制造。
不锈钢的本体主要是钢架构成,提供强度与刚度。
车体整体为焊接部件,疲劳强度高,所述车体下部为全焊接下框架结构。
整个应力过程从车体通过下框架、顶边梁、弯曲梁、各种梁、柱和其他线性骨架结构传递到波纹板和其他薄板结构,形成稳定车体支撑结构的整个应力系统。
结构承受的最大应力是轴向力,主要来自不同类型的梁和柱构件以及外部包层结构。
铁道车辆车体结构技术

制动 和空车制 动条件 下几乎 相 同 。
( )较低 的制 动 缸 压力 造 成 空 车 制 动效 率 下 降 , 4 但这影 响不 大 , 因为闸瓦 压力 与车重成 比例 , 纯制 动率
才是影 响效 率 的主要 因素 。
6 结 论
a rou rs o he c r o r es rb d. nd va i s pa t ft a b dy a e d c i e
Ke r s r ln tc ;c ro y;sr cu e a a ywod :ol g so k a b d i tu t r  ̄J p n
为 1 2 4mm ̄ 2 8 6mm 。 5 . 2 .
空 重车调整 比例 正 在逐 步 提 高 , 而可 使 空 车得 从
到较低 的制动缸 压力 。
( )较 高的空重 车调整 比例 意味 着调 整 到空 车制 2 动缸压 力需要获取 较 大 的减 压 , 目前 典 型 的 调节 标 按 准 , 在 6 0 5k a的列车 管压力 下 , 4 8 2k a的 要 2 . P 从 4. P
实现 轻量化 时 , 刚度会 出现 降低 的趋 势 。因此 , 其 要想
单 的“ 体 ” 的弯 曲刚 度 , 照“ 梁 时 按 等效 弯 曲刚 度E e ” lq 来评 价 。等效 弯 曲刚 度根据 式 ( ) 1 计算 :
z
在设 计上提 高刚度 , 势必 会加大 车体质 量 , 能构 成理 不 想 的车体 , 必须兼顾 这种 互相矛 盾 的特 性 , 用经 济 的 选
比例 。 ( )总之 , 低 的制 动缸 压 力 和 制 动效 率 以及 较 6 较
现在几乎所 有新 造货车 都需 要安装 空重车 调整装
铁路客车车体钢结构设计技术(精)

铁路客车车体钢结构设计技术作者杜彦品内容提要:本文叙述了铁路客车车体钢结构的特点及分类,重点介绍了25型客车碳钢车体钢结构的组成部分、结构设计及主要技术要求,对铁路客车车体钢结构材料的选用及结构设计将有积极的帮助。
※※※1概述车体钢结构是铁路客车最基本的结构,为铁路客车走行部、制动装置、连接缓冲装置、车辆内部设备以及内装提供了安装的空间和基础。
新造25型客车车体钢结构为碳钢车体全钢焊接结构,由底架、侧墙、车顶和端墙等四部分焊接而成,俗称薄壁筒形车体结构。
目前我国的新造25型车有两种承载结构:一种是无中梁薄壁筒型整体承载结构,另一种是有中梁薄壁筒型整体承载结构(如行李车和邮政车。
随着车辆的用途和生产工艺条件的不同,各种25型客车的结构不全相同,但其外形尺寸和结构形式则基本一致。
2 车体结构的分类车体结构按车体所用材料分为以下三种:碳素结构钢车体——我国新造25型客车车体;不锈钢车体——我公司正在研制的200km/h客车车体, CRH1“和谐号”动车组的车体;铝合金车体——部分地铁车体、CRH2、CRH3、CRH5“和谐号”动车组的车体。
3 车体钢结构组成车体钢结构按部位可分为四个大部件:底架钢结构、侧墙钢结构、车顶钢结构、端墙钢结构。
车钩缓冲装置、风挡、脚蹬等安装在大部件上。
现就YZ25G(T 型硬座车(无中梁薄壁筒型整体承载结构和XL25G型行李车(有中梁薄壁筒型整体承载结构来详细说明车体钢结构的构造和特点。
YZ25G硬座车车体钢结构如图1所示。
4 底架钢结构4.1 底架结构组成底架钢结构由端牵枕、枕内横梁、枕外横梁、枕后纵向梁、侧梁、枕外铁地板和枕内波纹地板等组成,如图2所示。
端牵枕分为端梁、牵引梁和枕梁,如图3所示。
4.2 底架结构设计4.2.1 端梁端梁由6mm厚钢板压制而成,断面为“[”,YZ25G型硬座车端梁高400mm靠近侧梁处高180mm,称为“转角”。
在转角下翼面焊有3mm的围板,围板可以在端部遮挡脚蹬,起到美观的作用。
25型客车车体结构

2型客车车体结一、车体结构特点25型客车车体钢结构为全钢焊接结构,由底架、侧墙、车顶和端墙等四部分焊接而成。
在侧墙、端墙、车顶钢骨架外面,在底架钢骨架的上面分别焊有侧墙板、端墙板、车顶板和纵向波纹地板及平地板,形成一个上部带圆弧,下部为矩形的封闭壳体,俗称薄壁筒形车体结构。
壳体内面或外面用纵向梁和横向梁、柱加强,形成整体承载的合理结构。
二、车体各部分构成1996年以后生产的25型硬座车车体钢结构,如图1所示。
1、底架底架由牵引梁、枕梁、缓冲梁、下围梁(或称下侧梁)、枕梁间的纵向金属波纹地板及枕外金属平地板等组成。
如图2所示。
底架自上心盘中心到缓冲梁间的中梁称为牵引梁,由两根30a型槽钢及牵引梁上下盖板组焊而成。
缓冲梁由6mm厚钢板压制而成的槽形断面。
枕梁、缓冲梁与牵引梁组成的结构被称为牵枕缓结构,如图3所示。
由于两枕梁间无贯通的中梁,因而作用于底架上的纵向拉压力均由波纹地板和底架侧梁来承担。
由车体钢结构静强度试验表明,纵向波纹地板能承受三分之一以上的总纵向拉伸或压缩力,这种结构的底架称为无中梁底架。
.4 k)图1硬座车车体钢结构1—底架钢结构;2—侧墙钢结构;3—车顶钢结构;4—端墙钢结构;5—风挡;6——、四位翻板安装;7—二、三位翻板安装;8—脚蹬组成; 水箱吊梁一12横梁;一11水箱横梁;一10钩缓装置;一9.图2底架1—缓冲梁;2—牵引梁;3—端梁;4—枕梁;5—侧梁;6—枕外横梁; 加强板一10纵向梁;一9纵向加强梁;一8横梁;一7..图3底架牵枕缓组成1—枕梁组成;2—缓冲梁组成;3—牵引梁组成;4、5、6—补强板;7—冲击座; 8—上心盘;9、10—铆钉2、侧墙25型客车车体钢结构的侧墙外表面为平板无压筋,在理整的外墙板内侧焊有垂直立柱和水平纵向梁,形成板梁式平面承载侧墙结构。
、车顶3车顶由上边梁、车顶弯梁、车顶纵向梁、空调机组安装座平台、水箱盖等组成钢骨架。
在骨架的外面焊有车顶板,共同组成车顶钢结构。
高速客车车体钢结构静强度计算及优化设计

速 度 200 km/h 高速客车碳钢车体钢结构,是中车 浦镇车辆有限公司继速度200 km/h 高速客车不锈钢车 体 后 ,自主研发设计的全新车体钢结构。车体除辊弯件 和 牵 枕 缓 外 ,热 轧 板 采 用 新 型 耐 候 钢 ,车 体 材 料 耐 腐 蚀 性能提高一倍;并在车体钢结构设计中采用全新的防腐 结 构 ,有效提高车体钢结构防腐蚀能力,减少车体钢结 构 全 寿 命 成 本 。车 体 侧 墙 和 端 墙 立 柱 、纵 梁 及 车 顶 小 弯 梁均采用乙型断面,与侧墙板、侧顶板、端墙板均采用电 阻 点 焊 ,从 而 提 高 外 墙 板 平 整 度 。 1 主要技术参数
880 959 200
2 车体钢结构
速 度 2 0 0 k m /h 客车碳钢车体,采用整体承载无中
梁筒形结构,鼓 型 断 面 ,如 图 1 所 示 。车体钢结构采用 模块化设计,由底架、侧 墙 、车顶、端墙六大模块组成,如 图 2 所 示 。各模块间通过电弧焊连接,以保证车体密封
性 ; 侧 墙 板 、端 墙 板 和 侧 顶 板 与 骨 架 主 要 采 用 电 阻 点 焊 。 3 车体强度设计标准
( ) 进行模态分析时,采用无约束的边界条件。 4 . 4 计算结果
初 步 计 算 时 发 现 ,在 端 部 压 缩 的 窗 下 横 梁 处 300 k N 压缩工况下,有侧门端的端门框处应力超过了 材 料 的 许 用 应 力 ,主 要 由 于 端 门 框 采 用 开 口 槽 型 梁 结 构 ,优化后改为封闭的方梁结构,应力明显下降,如 图 5 所示。
图 3 车体有限元模型图
图 4 局部模型图
4.2 计算工况 计算载荷及工况按照《200 km/h 及以上速度级铁
道车辆强度设计及试验鉴定暂行规定》确 定 ,共 计 1 2 个 工况 (见 表 2)。
B型不锈钢地铁车辆车体结构优化设计

B型不锈钢地铁车辆车体结构优化设计摘要本文介绍了B型不锈钢地铁车辆车体结构通过材料简统方案、结构优化设计,结合有限元分析及静强度试验验证,有效提升了车体结构强度,优化了焊接工艺及设备接口适应性。
关键词不锈钢车体地铁车辆材料性能优化设计1 前言以编组为“+Tc-Mp-M-T-Mp-Tc+”3动3拖项目车辆车体结构为例。
B型不锈钢车体为薄壁筒型整体承载的焊接结构,通过采用高性能材料、优化结构设计等方式,并通过有限元分析和静强度试验,优化后的车体满足压缩静载荷800kN,拉伸载荷640kN要求的基础上均提升25%左右,并通过改进结构优化焊接工艺与设备接口适应性,车体结构能适应更加复杂严苛的运行情况。
2 车体钢结构材料2.1 材料化学成分和力学性能车体钢结构主要采用城轨车辆专用的轻型高强度奥氏体不锈钢SUS301L材料,其抗拉强度(屈服强度)由大到小分为HT级、MT级、ST级、DLT级、LT级5个等级。
不锈钢化学成分和机械性能符合EN 10088、JIS G 4305中相关要求。
底架端部结构承受冲击力与压缩力较大,主要选用耐大气腐蚀钢[1],其化学成分和机械性能符合TB/T 1979中相关要求。
以提升车体强度并方便板材采购及生产加工为原则,车体板材在以往项目基础上合理的简统,如侧墙、顶棚及底架等零部件选用SUS301L-DLT代替SUS301L-LT;司机室座椅安装座由于受交变载荷受力情况复杂,采用屈服强度高的Q450钢代替低强度耐候钢;底架牵缓组成、连接前端吸能结构与牵引梁组成的纵梁采用Q450钢代替Q345钢。
3 车体结构车体钢结构采用轻量化整体承载结构,主要由底架、顶棚、端墙、侧墙及司机室钢结构组成,底架为无中梁焊接整体结构。
车体结构设计符合EN12663中P-III类型相关要求,车体钢结构的优化设计如下。
以Tc车为例,底架主要由端底架、波纹地板、边梁、主横梁等模块组成。
底架前端设有吸能防爬区,结构详见图1。
简析不锈钢地铁车辆车体结构设计要点

简析不锈钢地铁车辆车体结构设计要点摘要:现阶段,高强度、刚度、动态性能更好地不锈钢车体结构逐渐成为各大轨道车辆厂家和研发人员追求的目标,在地铁车辆中,使用具有轻量化特点的不锈钢车体结构能减少车辆和线路的维护费用,节约能源,因此在地铁车辆车体结构中得到了较为广泛的应用。
基于此,本文首先对不锈钢车体结构的特点进行了简要概述,分析了其在地铁车辆中的设计要点,并结合大连市的地铁车辆结构设计的实例进行说明。
关键词:不锈钢;地铁车辆;车体结构设计1.不锈钢车体结构的主要特点不锈钢车体同碳钢车体一样为整体承载板梁结构,引起具有较高的强度因此,可以实现车体结构的轻量化,如侧墙和车顶外板厚度一般取1.0mm或1.5mm,而碳钢车体一般不低于2.0mm。
不锈钢车体结构具有良好的抗腐蚀能力,因此设计时无需为了抗腐蚀而对板材加厚,而且车体外表面能保持不锈钢材质本色和光泽,一般无需再涂装和表面挖补维修,能进一步降低车体质量。
但侧墙外板材料最好最消光钝化处理,另外考虑到车辆的美观,车体外表面宜粘贴色作为装饰,以增加车辆的动感。
2.不锈钢地铁车辆车体结构设计要点2.1选材不锈钢材料可以满足地铁车体的一切要求,和其他材料相比,它具有抗扭曲、高抗拉强度、耐高温、抗弯曲变形的优势。
对车体的设计,有相关的标准,设计人员必须具备丰富的理论知识和设计经验,对材料的选用,不但要考虑到材料的强度,还要考虑到不锈钢的物理特性。
车体材料按照强度划分,可以分为五个等级,分别是LD、DLT、ST、MT和HT。
轻量化不锈钢车体应通常采用材质为SUS301L和 SUS304的车辆专用不锈钢作为主体,SUS301L相比中SUS304来说,铬和镍的含量比较少,因此其屈服极限比(屈服强度/抗拉强度)亦小于0.8,冲压加工性能更好,而且,如果需要进一步提高抗拉强度,只需要进行冷压加工即可。
不锈钢的物理性能,取决于热传导率、热膨胀系数、比电阻等因素。
不锈钢材料,必须具有低热传导率和较高的热膨胀系数和高比电阻的特点,车体制造时,尽量采用电阻点焊工艺,不用电弧满焊。
铁路客运站建筑钢结构常见问题及对策

铁路客运站建筑钢结构常见问题及对策摘要:随着我国铁路工程不断进步发展,高铁站房建设中为了使结构设计能够适应大跨度形式新颖,创建良好的乘车环境,高铁站台基本采取雨棚、大空间候车厅。
高大空间以金属屋面体系、钢结构体系为主,随着钢结构在建筑工程施工中得到广泛应用。
同时也存在很多问题,因此本文对钢结构常见问题进行了简要分析.关键词:铁路客运站;建筑;钢结构;对策引言钢结构在建筑工程施工中应用较为广泛,由于结构特性,具有较强的抗震性能,并且材料可以二次开发和利用。
钢结构体系受到外在限制较少,但是施工中可能受到客观因素影响施工质量,需要选择合理的施工质量控制措施,贯穿于建筑工程施工全过程。
通过建筑钢结构施工技术研究,进一步强化施工质量控制,有助于推动钢结构施工技术改进和完善,推动现代建筑施工技术朝着更高层次发展。
1铁路客运站建筑钢结构特点分析1.1 绿色、节能、环保,符合可持续发展理念我国自改革开放以来,提出了可持续发展的理论和观念,进而各个方面的发展也都围绕着绿色、环保来进行,钢结构正好符合这方面的需求,建筑钢结构中的一些基础材料可以进行工业化生产,同时其还具备高强度和高效能这两个特点,更为重要的是,建筑钢结构具备强大的支撑能力。
除此之外,还可以将钢结构利用过程中所产生的一些零碎边角料进行回收利用,实现资源的循环利用,减少施工单位的材料成本,提升施工单位的经济效益。
这种材质自身比较轻便,并且非常符合相应的建筑材料标准,在实际应用和运输的过程中都比较方便。
1.2强度高、抗震性能好钢结构强度极高,并且其弹性模量也比较高,所以在相同的承重条件下,会比其他建筑结构更加节省材料和空间,例如钢筋混凝土结构,最终有效地减少建筑结构的竖向面积,提升建筑结构的使用面积。
除此之外,因为钢的物理性能及内部组织比较均匀,所以在受力情况下各个部分基本相同,如果受力没有超过极限,会产生一定的弹性,工作性能十分良好。
钢材还具备较强的延展性,能够在很大程度上减小地震对建筑结构所带来的伤害,避免结构出现断裂等相关情况。
铁路客车车体

铁路客车车体一、25型客车车体25型客车车体为全钢焊接无中梁(行李车及部分发电车除外)薄壁筒形整体承载结构。
25G型客车车体主要由底架、侧墙、车顶和端墙等部件焊接而成;25T型客车、时速160公里动力集中电动车组(直车体)拖车及控制车在25G型客车车体基础上增设了车下裙板;控制车还包括司机室钢结构,如图1和图2所示。
25型客车车体材料主要采用耐候钢,主要承载部件(牵引梁、枕梁和中梁等)采用碳素结构钢或低合金高强度结构钢,卫生间地板、洗面间地板及空调机组安装平台的平顶板等易腐蚀部位采用不锈钢。
除此之外,车体还包括蹬车脚蹬、防爬盒和扶手等车体附件。
图125T型客车车体、时速160公里动力集中电动车组(直车体)拖车1—底架;2—侧墙;3—车顶;4—端墙;5-裙板图2时速160公里动力集中电动车组(直车体)控制车1—底架;2—侧墙;3—车顶;4—端墙;5—裙板;6—司机室钢结构1.底架底架主要用于承受纵向载荷与垂直载荷。
底架设有转向架、车钩缓冲装置、裙板和车下设备等安装接口。
25型客车底架的外形尺寸基本一致,但结构不全相同,一般采用无中梁结构,行李车及部分发电车采用有中梁结构。
(1)无中梁底架无中梁底架由牵引梁、枕梁、缓冲梁、侧梁、横梁和金属地板等组成,如图3所示。
图3无中梁底架1—牵引梁;2—枕梁;3—缓冲梁;4—侧梁;5—横梁;6—金属地板(2)有中梁底架有中梁底架由牵引梁、枕梁、缓冲梁、中梁、侧梁、横梁和金属地板等组成,如图4所示。
图4有中梁底架1—牵引梁;2—枕梁;3—缓冲梁;4—侧梁;5—横梁;6—金属地板;7—中梁2.侧墙侧墙是与底架相连接组成车体侧面的部件。
25型客车车体侧墙钢结构外表面为无压筋平板,在外墙板内侧焊有垂直立柱和水平纵向梁,形成板梁式平面承载侧墙结构,主要由上边梁、侧立柱、门框、纵向梁和侧墙板等组成,如图5所示。
侧墙上设有侧门、车窗等安装接口。
图5侧墙1—上边梁;2—侧立柱;3—侧门框;4—纵向梁;5—侧墙板3.车顶车顶位于车体的上部,由侧墙、端墙所支撑,断面为弧形,主要由车顶边梁、弯梁、纵向梁、顶板、中部端顶和空调机组安装平台等组成,如图6所示。
铁路客车车体钢结构防腐技术

铁路客车车体钢结构防腐技术作者 徐凤妹内容提要:本文叙述了铁路客车车体钢结构防腐技术,防腐涂料的种类、特性,重点介绍了铁路客车车体钢结构防腐涂料的特性及其表面处理的方式。
※ ※ ※1概述铁路客车车体钢结构防腐技术,是铁路客车生产过程中的重要技术之一,它是提高客车使用寿命和增加其表面装饰性的双重工程。
目前,我国时速200km/h以下的铁路客车车体,大多采用碳钢车体。
时速200至250km/h的铁路客车车体一般采用碳钢车体或不锈钢车体,对于250km/h以上的高速动车组一般采用不锈钢车体或铝合金车体。
碳钢车体主要使用的材料有:普通碳素钢和镍铬系耐候钢。
车体钢结构的寿命主要取决于两个方面:其一,选择耐腐蚀的材料,如不锈钢或铝合金。
其二,在碳素钢的基础上提高防腐技术。
前者由于材料成本高且制造工艺难度较大,在常规客车上难以广泛采用,后者由于成本低,制造工艺相对简单,在常规客车上应用广泛。
在客车产品设计制造过程中,对于金属零部件,合理地选择材料、正确的结构设计、合理选择防腐技术,是设计必须遵循的三个重要原则,在材料和结构确定的前提下,正确选择防腐技术是提高其防腐性能和表面装饰性的关键环节。
本厂车体钢结构的防腐重点主要体现在钢材预处理、钢结构防腐和外皮油漆三个阶段。
这三个阶段分别在压铆车间、钢结构车间和客车车间进行。
对于常规客车车体上述三个阶段的防腐及涂装要求,铁道部在招议标《技术规范》中作出如下规定:1级、局部a) 车体钢结构的钢材表面应进行预处理,进行抛丸处理的钢材表面清洁度应达到Sa22Sa2级;薄钢板表面清洁度应达到有关规定的要求。
b) 车体钢结构内、外表面应在彻底干燥的情况下涂两遍防锈底漆,每遍厚度不小于30μm;车体钢结构内部及底架外部涂完防锈漆后,再涂3mm厚的沥清浆;或在车体钢结构内部及底架外部喷涂厚度不小于200μm厚的重防腐涂料。
c) 车体外部墙面漆应涂两遍,顶板涂三遍,每遍厚度不小于30μm,面漆采用双组份聚氨酯油漆。
基于欧洲标准不锈钢客车车体制造工艺大揭秘
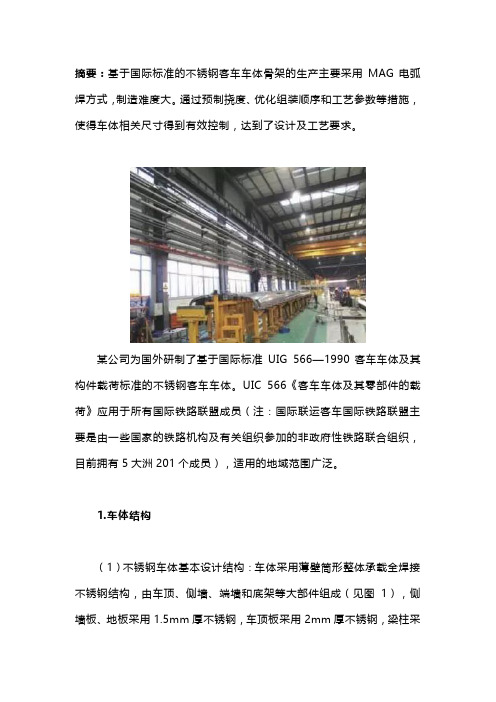
摘要:基于国际标准的不锈钢客车车体骨架的生产主要采用MAG电弧焊方式,制造难度大。
通过预制挠度、优化组装顺序和工艺参数等措施,使得车体相关尺寸得到有效控制,达到了设计及工艺要求。
某公司为国外研制了基于国际标准UIG 566—1990客车车体及其构件载荷标准的不锈钢客车车体。
UIC 566《客车车体及其零部件的载荷》应用于所有国际铁路联盟成员(注:国际联运客车国际铁路联盟主要是由一些国家的铁路机构及有关组织参加的非政府性铁路联合组织,目前拥有5大洲201个成员),适用的地域范围广泛。
1.车体结构(1)不锈钢车体基本设计结构:车体采用薄壁筒形整体承载全焊接不锈钢结构,由车顶、侧墙、端墙和底架等大部件组成(见图1),侧墙板、地板采用1.5mm厚不锈钢,车顶板采用2mm厚不锈钢,梁柱采用2~4mm不锈钢。
不锈钢车体主结构材料采用高强度超低碳奥氏体不锈钢和奥氏体铁素体双相不锈钢,按照客户要求,车顶有1个空调机组平台,侧墙采用通长侧墙板外侧附加一层波纹板结构。
(2)不锈钢车体钢结构工艺特点:由于UIG 566标准对车体强度的要求远高于国内客车采用的TB1335标准,为提高车体强度,除了车体结构进行加强之外,车体骨架焊接大部分采用了MAG电弧焊方式,而非不锈钢车体通常采用的、焊接变形较小的电阻点焊方式,所以焊接变形量更大,焊接变形更难控制。
2.制造工艺难点该不锈钢客车车体制造中存图1 车体结构在如下难点:(1)车体挠度控制。
车体组成挠度要求枕内上挠8~13mm,枕外下垂0~5mm。
由于侧墙组成窗口密集,造成整体刚度较弱,并且侧墙与底架边梁垂向错位,不在同一立面(见图2),侧墙无法带动底架整体变形,车体挠度控制是难点之一。
图2 侧墙与底架连接形式(2)侧墙平面度控制。
侧墙门口平面度直接关系到车门的安装与调试,窗口部位平面度关系到车窗的安装。
该不锈钢客车车体为无涂装车体,墙板原材料表面裸露在外面,墙板表面状态直接影响车辆的整体视觉效果。
不锈钢地铁车辆车体结构设计的要点分析

观。
轻量 化、高 强度 、抗 疲劳 是 目前 不锈钢 车体 设计应 遵循 的基 本
原 则和 发展趋 势 。车 体的 轻量化 能够带 来很 多优点 :提高车 辆 的加
关 键 因 素之 一 。
不 锈 钢 车体 材 料 按 强度 从 弱 到 强分 为 L D、DL T 、S T、MT和 HT等 5 个 等级 ,除 强度不 同外还 具有不 同的物理特性 ,同时 ,不锈 钢 车体设 计必须 严格 遵循相 关标 准 ,只有 具备 了丰富 的理论 知识 和
疲劳等 的要 求 ,通 过有 限元分析 计算 和静 强度 、刚度试 验来 实现 。 有 限元 分析 计算和 静强度 、刚度 试验是 验证 车体结 构设 计是否合 理 的重要依据和 原则 。
速度、 降低运能消 耗、 牵引及制动能耗 低、 减轻对线路 的磨耗及冲 击 ,
扩 大 了运 输能 力。而 车体重 量的 减轻必然 要求车 体结 构 的设 计具 有 较 高 的强度和 抗疲 劳的特 性 ,三者 缺一不 可 。车体的 设计需 综合考
1 不锈钢地铁 车辆车体 的设计 的要点分析
关注 ,如客 室 门角 和司机 室 门角、窗 角 ,底 架枕 梁、车 钩安装 座 区 域等 。对 以往 出现 过类似 问题 的受力 区域 ,也应 注意避 免 ,或 通过
强度计 算验证该结构是 否存在问题 。 由于 H T材料 有在 高温下 强度 会 降低 到 D L T水 平的物理 特性 ,这 样 1 . 5 车 体 的 制 造 工 艺 的结 构 显然不合 理 。考 虑到 这些 问题 ,我 们在 结构设 计时 通过侧 墙 车 体结 构设计 应满足 的重 要原则 即是 制造工 艺性 能 良好 。焊接 下边 梁实现了底架边 梁和侧墙立柱 间的点焊连 接 , 避 免了上述 问题 。 的可行 性和 焊缝 的质量 对车体 的制造 质量 有很大 影响 。 目前 的不锈 在车 体的结 构设 计中 ,并非所 有材料 均选 择不锈 钢材 料 ,需 依 钢 车体结 构形 式与原来 的结 构相 比重量轻 、制造 工艺 简单 。然而 仍 据 实 际的承载 及受 力情况综 合考 虑 。在 底架结 构 的设计过 程 中 ,对 需提高结 构设计的模块化 程度 , 减少零部 件的数量 , 以简化 制造工艺 。 于 承载 比较重 要 的牵引梁 及枕 梁部位 ,选择使 用低 合金 高强度 钢 。 这 是 由于低合金 钢具 有很好 的抗 疲劳特 性和焊 接性 能 。根 据不 同的 2 结 论 受力特点选择合 适的材料是车体 结构设计应 遵循的原则之 一。
铁路客车碳钢车体的轻量化设计与应用

铁路客车碳钢车体的轻量化设计与应用摘要:随着铁路客车运行速度的提升,外界载荷更加复杂、苛刻,而能耗和轴重指标又对车体质量提出更高要求,轻量化设计成为制约铁路客车持续发展的关键。
碳钢客车由于生产成本低、维修性能好,一直是我国轨道交通运输的主力之一,但其却有着自重大的缺点。
通过优化车体部件的结构布局、减小材料使用、增开工艺孔及使用轻型材料等,可进一步提升铁路客车碳钢车体轻量化水平。
关键词:碳钢;车体;轻量化;材料;结构优化引言轻量化设计是铁路客车发展的必然趋势,不仅降低轮轨间相互作用力、改善轮轨磨损与变形、提升车辆加速和制动性能,还减少能源消耗和碳排放。
车体是铁路客车的主要承载结构,车体钢结构及配套设施的质量通常占铁路客车总质量的三分之一以上,降低车体质量是实现铁路客车轻量化的重要途经。
目前,铁路客车车体轻量化手段主要包括:采用新型轻质高强度材料、车体结构优化设计、车体配套设施的轻量化与小型化等,本文主要从车体结构优化入手论述碳钢车体的轻量化设计。
1、车体结构和承载特点碳钢客车车体主要由底架、侧墙、车顶、地板、端墙等组成,车身采用焊接、铆接及螺栓安装等工艺,以确保车辆结构满足整个车体强度要求。
底架由牵引梁、枕梁、缓冲梁、边梁、横梁等组成,除个别部件采用Q345型钢外,几乎所有材料都是09CuPCrNi耐候钢,并且采用机加工成型;侧墙的支撑骨架由立柱、纵向梁、上边梁、窗下支架等组成,墙板由2.5mm耐候钢板蒙皮于骨架外侧焊接而成,立柱和纵向梁构成窗口框架;端墙与侧墙结构相似,中间增加了2个大槽钢作为车辆两端通过门的门框,同时可安装车端风档;车顶采用弯梁、角铁组成框架,外面蒙2mm厚耐候钢板,对应空调、水箱、通风器等位置设置安装框架来满足接口的强度。
2、车体结构设计构成车体的钢结构框架是车辆承载和运行的至关重要的部件,这不仅是为了传递整个车辆的垂直、拉伸和压缩载荷,还需要保证悬挂在车体下或安装于车顶的设备(空调、变压器、油箱、柴油发电机、制动模块、启动装置、电池箱、复合电源、充电器等)的安装强度,对于有较高载荷要求的设备须设置大强度的支架或者吊钩。
某铁路客车车体模块化设计及强度计算

某铁路客车车体模块化设计及强度计算本文主要阐述了铁路客车车体的结构特点和主要部件结构,同时对车体的静强度进行了仿真计算,计算结果表明车体结构强度满足标准要求,同时对碳钢侧墙墙板的焊接提出了新的研究方向。
标签:铁路客车;车体;静强度;仿真1 引言铁路客车车体按照结构材料划分可分为碳钢车车体、铝合金车体及不锈钢车体,目前已经有相关企业已经生产出碳纤维车体,但仍旧处在研发试验阶段,距离实际运用还有很长的路要走。
铁路客车车体作为承载设备和乘客的重要载体,其强度及安全性尤为重要。
2 车体结构要求车辆采用碳钢车体,为满足整车轴重要求,车体设计为整体承载无中梁筒形结构。
端部底架需考虑结构的整体稳定性,以提高侧门的密封性能。
材料选用主要是耐候钢,底架边梁、侧墙上边梁及顶盖边梁均采用普通碳素钢型钢,易腐蚀部位采用不锈钢(如洗手间、厨房等区域)。
车体结构设计首先要考虑的是先要满足车体强度、刚度的要求,尽可能实现等强度或者冗余强度设计,同时也要考虑到车体制造工艺、防腐性等因素。
3 车体结构设计3.1 车体结构整个车体设计采用模块化设计思路,主要由底架、侧墙、车顶、端墙及车钩缓冲装置等组成,在车体方案设计时除考虑总体平面布置等外部接口外,还需对车体各个大部件之间的连接关系进行设计。
侧墙墙板与底架边梁、端墙墙板与底架缓冲梁连接均设计成搭接方式,提高整车美观度。
3.2 底架结构底架作为车体最重要的部件,不仅仅承担着传递整车纵向拉伸和压缩载荷,同时还需要承载底下吊挂设备及车上设备及乘客的载荷。
底架主要由端部底架、边梁、横梁、纵梁、设备吊座和底架地板组成。
底架横梁的布置根据各设备吊挂位置进行设计,需要吊挂设备位置的底架横梁采用刚度较大的口型梁结构,其余部位采用U型梁结构,U型梁横梁及纵梁可以有效的减轻整车重量,同时能为底架地板提供支撑。
3.3 侧墙结构侧墙结构主要由乙型立柱、乙型横梁及L型横梁构成的网状结构,侧墙上的窗口根据总体方案布置,窗口四个角区域容易引起应力集中,所以在侧窗窗口四个角设置有补强块。
长途汽车客运总站钢结构制作方案

钢结构制作方案1.原材料控制1.1原材料验收所有主结构钢材由质量员、采购员等共同进行检查。
1.1.1 材料检查方法主材(Q235B)及其连接件采用Q235B, 其化学成分及力学性能应符合《碳素结构钢》(GB700-88)。
钢材在进厂时, 应对钢厂的质量保证书、批号、化学成分和机械性能逐项数据与国标进行核对, 钢材的品种规格应符合国家标准的规定或订货技术条件的规定, 钢材外观质量必须均匀, 不得有分层、夹渣、裂纹、非金属夹杂和明显的偏析等缺陷, 锈蚀限度不能超过规定误差的1/2厚度;用凿子或砂轮清除钢材表面的腐蚀、麻点、划伤、压痕, 其深度值应符合国家现行标准中的规定。
钢材的形状和尺寸用钢尺、卡尺检查, 允许偏差应符合(GB709-88)标准中的规定。
1.1.2 原材料复验根据规范和设计规定对钢材进行抽样复验。
在工程使用的原材料上抽样, 由监理参与, 抽样样品送检测单位进行原材料的复验。
原材料的检测项目应符合国家有关标准的规定和设计规定。
1.2焊接材料1.2.1 焊接接头的焊缝坡口形式按《气焊、手工电弧焊及气体保护焊缝坡口的基本形式与尺寸》(GB985-108)和《埋弧焊焊缝坡口的基本形式与尺寸》(GB986-108)的规定选用。
手工焊接: 对于Q235B钢, 采用E4301.E4303型焊条, 各种焊条应符合《碳素钢焊条》(GB1T5117-95)的规定。
自动焊或半自动焊接时采用的焊丝和焊剂, 应与主体金属的强度相匹配, 并符合现行标准《熔化用焊丝》(GB/T14957-1994)或《气体保护焊用焊丝》(GB/T4958-1994)的规定。
1.2.2 焊接材料的检查由质量员、材料员共同进行。
一方面检查质量证明书的各种技术参数符合规范标准和设计规定;1.3.2焊接材料的外包装应当完好无缺, 抽样检查无受潮、锈蚀等缺陷。
1.3.3钢结构件在制作前需按1: 1比例放样, 若发现尺寸有误或连接点解决不妥,应及时与设计人员联系解决。
铁路客车车体模块化设计技术

铁路客车车体模块化设计技术作者 廖平为了适应现代客车的大规模生产,努力提高客车的设计制造水平,近几年来,在客车设计中全面贯彻模块化设计理念,在制动、车电、暖通和车体的设计中广泛展开了模块化设计,在简化设计工作、提高产品质量、缩短组装周期和提升工厂产量方面取得了巨大的成果。
本文着重对车体模块化设计技术进行介绍,供相关设计人员学习参考。
※ ※ ※1模块化概念所谓模块,实际上就是某一系统集成后所形成的功能单元。
一个模块可以具有一种功能,也可以具有多种功能。
各模块通过插接或连接即形成一个局部或整机系统,再通过一定的包装和装饰即形成产品。
随着社会的发展和技术的进步,“模块化”概念已广泛应用于各个领域,尤其在电气行业,由简单的线排到大规模集成电路,电器元件的模块化已普遍采用,一个复杂的电气控制系统现在只要一个电路板和几个功能模块插件就可以实现,并使非常复杂的电气系统变得结构简单,条理清晰,维修方便,计算机行业尤其在集成电路方面取得了高速发展。
一般地说,模块化程度越高,产品就越先进。
模块本身必须具有技术上的先进性,设计上的合理性,性能上的可靠性,成本方面的经济性和寿命长等优势,才能使该产品具有生命力。
当前,铁路客车的设计制造技术正在进入与世界同步发展的轨道,高速动车组设计制造技术已达到世界先进水平,尤其在牵引、制动、控制和转向架等性能方面有了极大的提高,其装备也逐步现代化,舒适度明显改善,但本厂生产的客车在车体结构方面却明显落后,与高速技术的发展和现代化大生产方式不相适应。
为了解决这种状况,引入“模块化”的设计理念就显得十分重要。
2 模块化设计的发展1975以前,钢结构的生产仅有底架和端墙两个胎模,侧墙和车顶的组成均采用散件组装,各梁、柱均采用“搭积木”的方式进行逐件组焊,然后蒙上墙板和顶板。
一辆车体钢结构组成,至少要一个星期,最快也要三天左右,这样的生产方式要想大幅度提高产量和产品质量是根本不可能的,直到1985年钢结构的六大片才实现部件设计并按部件生产,组装开始实现胎膜化。
- 1、下载文档前请自行甄别文档内容的完整性,平台不提供额外的编辑、内容补充、找答案等附加服务。
- 2、"仅部分预览"的文档,不可在线预览部分如存在完整性等问题,可反馈申请退款(可完整预览的文档不适用该条件!)。
- 3、如文档侵犯您的权益,请联系客服反馈,我们会尽快为您处理(人工客服工作时间:9:00-18:30)。
铁路客车车体钢结构设计技术作者 杜彦品内容提要:本文叙述了铁路客车车体钢结构的特点及分类,重点介绍了25型客车碳钢车体钢结构的组成部分、结构设计及主要技术要求,对铁路客车车体钢结构材料的选用及结构设计将有积极的帮助。
※ ※ ※1概述车体钢结构是铁路客车最基本的结构,为铁路客车走行部、制动装置、连接缓冲装置、车辆内部设备以及内装提供了安装的空间和基础。
新造25型客车车体钢结构为碳钢车体全钢焊接结构,由底架、侧墙、车顶和端墙等四部分焊接而成,俗称薄壁筒形车体结构。
目前我国的新造25型车有两种承载结构:一种是无中梁薄壁筒型整体承载结构,另一种是有中梁薄壁筒型整体承载结构(如行李车和邮政车)。
随着车辆的用途和生产工艺条件的不同,各种25型客车的结构不全相同,但其外形尺寸和结构形式则基本一致。
2 车体结构的分类车体结构按车体所用材料分为以下三种:碳素结构钢车体——我国新造25型客车车体;不锈钢车体——我公司正在研制的200km/h客车车体, CRH1“和谐号”动车组的车体;铝合金车体——部分地铁车体、CRH2、CRH3、CRH5“和谐号”动车组的车体。
3 车体钢结构组成车体钢结构按部位可分为四个大部件:底架钢结构、侧墙钢结构、车顶钢结构、端墙钢结构。
车钩缓冲装置、风挡、脚蹬等安装在大部件上。
现就YZ25G(T)型硬座车(无中梁薄壁筒型整体承载结构)和XL25G型行李车(有中梁薄壁筒型整体承载结构)来详细说明车体钢结构的构造和特点。
YZ25G硬座车车体钢结构如图1所示。
4 底架钢结构4.1 底架结构组成底架钢结构由端牵枕、枕内横梁、枕外横梁、枕后纵向梁、侧梁、枕外铁地板和枕内波纹地板等组成,如图2所示。
端牵枕分为端梁、牵引梁和枕梁,如图3所示。
4.2 底架结构设计4.2.1 端梁端梁由6mm厚钢板压制而成,断面为“[”,YZ25G型硬座车端梁高400mm靠近侧梁处高180mm,称为“转角”。
在转角下翼面焊有3mm的围板,围板可以在端部遮挡脚蹬,起到美观的作用。
在端梁中部开有安装车钩用的缺口,宽度为345mm,俗称 “钩门”。
YZ25T型硬座车端梁高度为458mm,钩门的宽度尺寸为790mm,端梁在钩门处与牵引梁相互组焊。
4.2.2 牵引梁自枕梁到端梁间的中梁称为牵引梁,YZ25G型硬座车牵引梁由两根30b型槽钢及牵引梁上下盖板组焊而成。
其上盖板厚4mm,宽464mm,下盖板厚8mm,宽490mm。
为了符合在牵引梁腹板间安装车钩和缓冲器的尺寸要求,两槽钢腹板间距为350mm,并将牵引梁靠近端梁的一端加高到400。
在牵引梁两槽钢腹板内侧铆接有前后从板座、焊有磨耗板和防跳板。
YZ25T型硬座车牵引梁由两根8mm的钢板压制而成,其上盖板厚4mm,宽524mm,下盖板厚6mm,宽560mm。
为了符合在牵引梁腹板间安装车钩和缓冲器的尺寸要求,两牵引梁腹板间距为440mm,靠近端梁一端为喇叭状,间距为790mm,高度为458mm。
在牵引梁两腹板内侧铆接有车钩安装座。
4.2.3 枕梁YZ25G型硬座车枕梁由厚8mm、间距为350mm的两重向腹板及厚10mm、宽600mm的下盖板,厚6mm、宽600mm的上盖板组焊而成的闭口箱形断面“Ⅱ”,枕梁近侧梁端为小端,近牵引梁端为大端,它是一个近似的等强度鱼腹梁。
在枕梁下盖板下面与牵引梁交叉处安装有心盘座,以提高该处的承载作用,提高枕梁和牵引梁的连接强度和刚度。
在枕梁两端的上旁承安装处焊有上旁承加强板,枕梁端部还焊有供顶车用的顶车垫板。
YZ25T型硬座车枕梁腹板厚8mm,间距为424mm,下盖板厚12mm,宽600mm,上盖板厚6mm、宽600mm。
在枕梁两端焊有空气弹簧安装座,枕梁端部也焊有供顶车用的顶车垫板。
4.2.4 地板梁枕内横梁位于两枕梁之间,横梁均布, 间距在1m以内,也可根据车下设备的位置进行调整。
枕外横梁位于端梁和枕梁间,有2对,断面为“[”,高180mm、厚4mm(有集便器的为6mm),翼面宽50mm; (有集便器的为60mm)。
枕内外第一根横梁一般距枕中1700~2000mm,具体还要根据转向架所占据的空间而定。
这些横梁的两端分别与侧梁和牵引梁或是两端与侧梁焊接。
这些横梁的作用:一是把牵引梁结构与侧梁连接起来形成底架钢结构骨架,从而保证底架有足够的强度和刚度,以承受作用于底架上的各种载荷;二是成为平地板和波纹地板的支撑,在纵向力作用下防止波纹地板的失稳。
枕后纵向梁在枕内,靠近枕梁每端四组,第一组为鱼腹形槽形断面,其余三组断面同枕内横梁。
枕后纵向梁主要起传递纵向力的作用。
4.2.5 侧梁底架两侧有通长的侧梁,其断面为18型槽钢。
在横向,底架的枕梁及全部横梁的端部都与侧梁焊接,金属地板也与侧梁的上翼面搭接;侧墙的立柱、侧墙板分别焊在侧梁的上翼面和腹板外表面上,所以,侧梁是连结侧墙和底架的重要构件。
其连接关系如图1所示。
底架的牵枕缓、侧梁和横梁共同形成底架钢骨架。
4.2.6 金属地板在底架钢骨架的上面焊上金属地板。
在端梁和枕梁上盖板间为平地板,板厚为2mm;两枕梁间为纵向波纹金属地板,波纹地板断面为( 1.5mm。
由底架钢结构骨架和金属地板共同组成底架钢结构。
由于两枕梁间无贯通的中梁,因而作用于底架上的纵向拉压力均由波纹地板和侧梁来承担。
由车体钢结构静强度试验表明,波纹地板能承受三分之一以上的总纵向拉伸或压缩力,这种结构的底架称为无中梁底架。
4.3 有中梁底架结构另外一种有中梁底架,如行李车,下面以XL25G型行李车为例来说明有中梁底架的结构。
图4是XL25G底架钢结构,XL25G型行李车底架钢结构由端牵枕、中梁、枕内横梁布置、一位枕外横梁布置、二位枕外横梁布置、主横梁、一位端铁地板、二位端铁地板、枕内铁地板、站铁组成、底架线管布置、底架配件布置、侧梁组成、侧梁、补强梁等组成。
牵枕缓和侧梁结构与YZ25G型硬座车类似,不同之处为枕内均布有四组鱼腹形的主横梁,厚度为6mm,断面为“”,下翼面尺寸为120mm。
在大拉门处有两组补强梁,厚度为6mm,断面为“”,高度尺寸为280mm,下翼面尺寸为110mm。
XL25G型行李车无枕后纵向梁,有两根30b型槽钢组焊成的中梁,间距为350mm。
枕内外横梁断面均为“”,高度尺寸为110mm,下翼面尺寸为70mm,厚度为4或6mm。
行李间地板为4mm的花纹钢板,其余部分为2mm的平地板。
底架钢结构主要构件断面尺寸见表1表1 底架钢结构主要构件断面尺寸5 侧墙钢结构5.1侧墙结构组成YZ25G(T)型硬座车车体钢结构的侧墙主要由立柱、纵向梁、上侧梁、门柱、门上横梁、门框组成(YZ25T型硬座车无)、侧墙板等组成。
侧墙外表面为平板无压筋,在平整的外墙板内侧焊有垂直立柱和水平纵向梁,形成板梁式平面承载侧墙结构,如图5所示。
5.2 侧墙结构设计侧墙上侧梁断面为“”形,其尺寸为45x90x25x2.5(mm),长度为侧墙全长。
侧墙水平纵向梁共四根,窗上一根,窗下三根,其断面为“形,其尺寸为140x22x2.5(mm)。
这四根纵向梁起到加强侧墙的垂直弯曲强度和刚度的作用,同时也减少了钢板自由表面的面积。
在侧墙窗口间有一条短的窗间小纵向梁其断面为“”形,其尺寸为140x22x2.5(mm),设置目的是增强窗间板的强度与刚度。
在窗口两侧各有一根垂向的窗边立柱,也称为侧立柱,其断面为“”,尺寸为94x70x46x2.5(mm)。
在侧门处均有断面为“”形的门柱,其尺寸为25x60x100x60x25x4(mm),立柱和门柱与所有纵梁、上侧梁、底架侧梁连结起来,组成侧墙钢骨架,并与侧墙板焊结形成侧墙钢结构。
如果侧门为折页门,在门柱处还有一整体的门框组成,断面为“”形。
如果是塞拉门,就无此门框组成。
侧墙板为厚2.5mm 的耐候钢板(09CuPCrNi-B)。
侧墙板上开有大窗孔,尺寸为宽x高,即1064x1014(mm),小窗孔宽x 高为614x1014(mm) 。
每侧侧墙端部有两个侧门孔。
门窗开孔处是侧墙的薄弱区域,通过周边的梁柱予以加强,选择合适的窗角板的圆角半径来降低其应力集中,设计出合理结构。
5.3 行李车侧墙结构XL25G型行李车侧墙钢结构如图6,墙板和梁柱断面与YZ25G型硬座车类似,不同之处每侧侧墙端部有一个侧门孔,中间各有两个大拉门门孔,大拉门处有用方钢管80x60x4制成的门框,行李间还设有长圆形的了望窗,尺寸为960(宽)x310(高) (mm)。
侧墙钢结构主要构件断面尺寸见表2表2 侧墙钢结构主要构件断面尺寸(侧墙板厚2.5㎜)6 车顶钢结构6.1 车顶结构组成车顶钢结构由弯梁、纵向梁、顶板、一二位端顶、平顶钢结构、中部端顶、车顶边梁等组成,如图7所示。
车顶一、二位端(行李车仅一位端)各有一个空调机组安装座平顶钢结构,作为安装空调机组的基础,是安装单元式空调机组的支撑框架。
6.2 车顶结构设计端顶上边为8型槽钢制成的顶端横梁,其断面尺寸为80x43x5(mm)。
25G型行李车二位端无平顶,其二位端顶上边为端顶弯梁,断面为“”形,其尺寸为30x55x62.5x45x2(mm)。
在平顶和圆顶相交的部分为中部端顶,将两部分连接形成整体结构。
圆顶的中间部分有很多断面为“车体纵向均布,间距一般在700(mm)左右,其尺寸为94x46x70x24x2(mm)。
车顶边梁沿车顶两侧全长,断面为“”形,其尺寸为45x75x2.5(mm)。
车顶纵向还有五根纵向梁,其断面为“┐”形,尺寸为 50x50x3(mm)。
车顶吊铁焊在车顶的弯梁或纵梁上,主要吊装设备及内装部件。
车顶板由侧顶板和中顶板两部分组成。
侧顶板是冷轧型钢,将雨檐与小圆弧(R458)板及纵向梁合为一体制造成型,从而提高了侧顶板的平整度,并提高了小圆弧部分的抗弯刚度和强度,还简化了制造工艺。
中顶板为大圆弧板(R2300),车顶板厚度均为2mm。
平顶中顶板为不锈钢板,主要因为此处容易积水,考虑耐腐蚀性能。
中顶板沿车顶纵向倾斜12mm,侧顶向车两侧各倾斜10mm。
车顶钢结构是由纵横弯梁件组成的空间梁系,其上焊有曲面金属顶板(端顶和平顶为平板)组成的板梁结构,共同承受作用于其上的各种载荷,车顶结构具有足够的强度和刚度,并通过防漏雨试验。
车顶钢结构主要构件断面尺寸见表37 端墙钢结构7 1 端墙结构组成客车车体钢结构的两外端,通常称为外端墙,它是车体钢结构最外端的部分。
YZ25G型硬座车端墙钢结构分为风挡框组成、门框组成、端角柱组成、梁柱组成、端墙板组成、端墙配件。
7 2 端墙结构设计风挡框折棚柱断面为“[”形,即24b型槽钢,它是保证端墙强度和刚度的重要构件。
还有两根断面为“形,尺寸为43x45.5x130x3(mm)的端角柱和断面为“”形,尺寸为25x60x100x60x25x4(mm)的侧门柱;两根位于端门两侧断面为“”形,尺寸为50x54x50x28x3(mm)的端门框(端门为折页门时有),位于端门框和端角柱之间的“”形立柱94x70x46x2.5(mm)和“”形横梁140x22x2.5(mm)。