铁路客车车体钢结构设计技术(精)
铁路站房工程钢结构制作方案 (2)
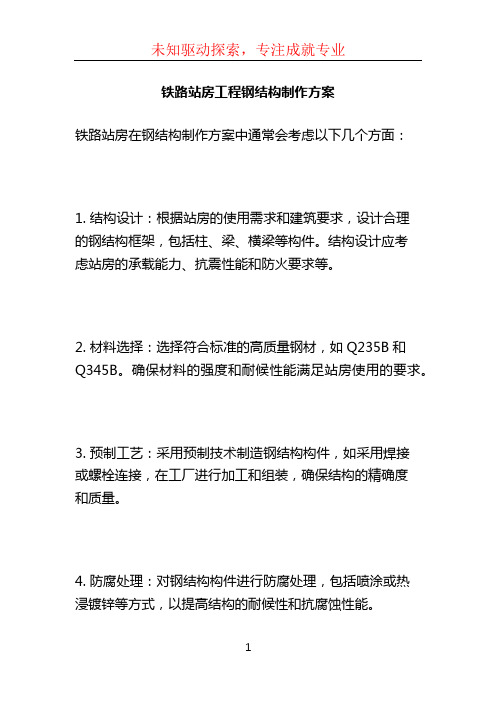
铁路站房工程钢结构制作方案
铁路站房在钢结构制作方案中通常会考虑以下几个方面:
1. 结构设计:根据站房的使用需求和建筑要求,设计合理
的钢结构框架,包括柱、梁、横梁等构件。
结构设计应考
虑站房的承载能力、抗震性能和防火要求等。
2. 材料选择:选择符合标准的高质量钢材,如Q235B和
Q345B。
确保材料的强度和耐候性能满足站房使用的要求。
3. 预制工艺:采用预制技术制造钢结构构件,如采用焊接
或螺栓连接,在工厂进行加工和组装,确保结构的精确度
和质量。
4. 防腐处理:对钢结构构件进行防腐处理,包括喷涂或热
浸镀锌等方式,以提高结构的耐候性和抗腐蚀性能。
5. 安装方案:根据站房地理位置和建筑要求,设计合理的安装方案,包括吊装、固定和连接等步骤,确保钢结构的安全和稳固。
除了以上几个方面,还需要根据具体的站房项目要求,考虑其他细节问题,如排水系统、防水处理、隔音措施等。
制作方案需要根据具体情况进行综合考虑和设计。
铁路车辆车体结构设计改进方法

铁路车辆车体结构设计的改进方法可以从以下几个方面入手:
1. 轻量化设计:采用新型材料和结构,如高强度钢、铝合金等,以减轻车体重量,提高运载能力和能效。
2. 模块化设计:将车体结构划分为若干模块,便于制造、组装和维护,同时提高了设计的灵活性和通用性。
3. 空气动力学优化:通过改进车体外形和减少空气阻力,降低列车运行时的能耗,提高运行速度和稳定性。
4. 结构强度优化:利用有限元分析等技术,对车体结构进行强度和刚度分析,优化结构设计,提高车体的安全性能。
5. 人性化设计:考虑乘客的舒适性和便利性,优化车内布局和设施设计,提高乘客的满意度。
6. 防火、隔音、隔热设计:采用防火材料、隔音材料和隔热材料,提高车体的防火、隔音、隔热性能,保障乘客的安全和舒适。
7. 耐腐蚀设计:选用耐腐蚀材料和表面处理技术,提高车体的耐腐蚀性能,延长车辆使用寿命。
8. 可持续性设计:在设计过程中考虑环保和可持续发展因素,如材料的回收利用、节能减排等。
通过以上改进方法,可以提高铁路车辆车体结构的设计水平,使其更加安全、高效、舒适和环保。
铁道车辆车体结构技术

制动 和空车制 动条件 下几乎 相 同 。
( )较低 的制 动 缸 压力 造 成 空 车 制 动效 率 下 降 , 4 但这影 响不 大 , 因为闸瓦 压力 与车重成 比例 , 纯制 动率
才是影 响效 率 的主要 因素 。
6 结 论
a rou rs o he c r o r es rb d. nd va i s pa t ft a b dy a e d c i e
Ke r s r ln tc ;c ro y;sr cu e a a ywod :ol g so k a b d i tu t r  ̄J p n
为 1 2 4mm ̄ 2 8 6mm 。 5 . 2 .
空 重车调整 比例 正 在逐 步 提 高 , 而可 使 空 车得 从
到较低 的制动缸 压力 。
( )较 高的空重 车调整 比例 意味 着调 整 到空 车制 2 动缸压 力需要获取 较 大 的减 压 , 目前 典 型 的 调节 标 按 准 , 在 6 0 5k a的列车 管压力 下 , 4 8 2k a的 要 2 . P 从 4. P
实现 轻量化 时 , 刚度会 出现 降低 的趋 势 。因此 , 其 要想
单 的“ 体 ” 的弯 曲刚 度 , 照“ 梁 时 按 等效 弯 曲刚 度E e ” lq 来评 价 。等效 弯 曲刚 度根据 式 ( ) 1 计算 :
z
在设 计上提 高刚度 , 势必 会加大 车体质 量 , 能构 成理 不 想 的车体 , 必须兼顾 这种 互相矛 盾 的特 性 , 用经 济 的 选
比例 。 ( )总之 , 低 的制 动缸 压 力 和 制 动效 率 以及 较 6 较
现在几乎所 有新 造货车 都需 要安装 空重车 调整装
铁路站房工程钢结构制作方案
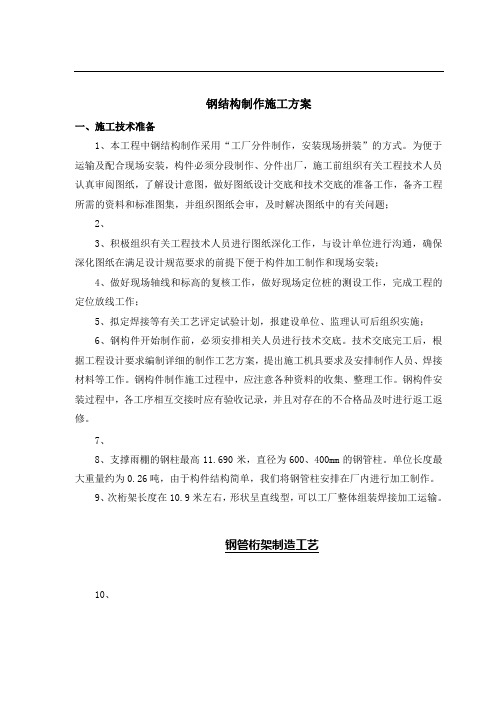
钢结构制作施工方案一、施工技术准备1、本工程中钢结构制作采用“工厂分件制作,安装现场拼装”的方式。
为便于运输及配合现场安装,构件必须分段制作、分件出厂,施工前组织有关工程技术人员认真审阅图纸,了解设计意图,做好图纸设计交底和技术交底的准备工作,备齐工程所需的资料和标准图集,并组织图纸会审,及时解决图纸中的有关问题;2、3、积极组织有关工程技术人员进行图纸深化工作,与设计单位进行沟通,确保深化图纸在满足设计规范要求的前提下便于构件加工制作和现场安装;4、做好现场轴线和标高的复核工作,做好现场定位桩的测设工作,完成工程的定位放线工作;5、拟定焊接等有关工艺评定试验计划,报建设单位、监理认可后组织实施;6、钢构件开始制作前,必须安排相关人员进行技术交底。
技术交底完工后,根据工程设计要求编制详细的制作工艺方案,提出施工机具要求及安排制作人员、焊接材料等工作。
钢构件制作施工过程中,应注意各种资料的收集、整理工作。
钢构件安装过程中,各工序相互交接时应有验收记录,并且对存在的不合格品及时进行返工返修。
7、8、支撑雨棚的钢柱最高11.690米,直径为600、400mm的钢管柱。
单位长度最大重量约为0.26吨,由于构件结构简单,我们将钢管柱安排在厂内进行加工制作。
9、次桁架长度在10.9米左右,形状呈直线型,可以工厂整体组装焊接加工运输。
钢管桁架制造工艺10、12、二、钢结构加工工艺:(二)原材料供应阶段:1、检查钢材的质量保证书是否与钢材上打印记号符合,每批钢材必须具备生产厂提供的材质证明书,写明钢材的炉号、钢号、化学成分和机械性能各项指标,可根据国标(GB700—79)和(YBl3—69)的规定进行核查。
2、核对钢材的规格尺寸,各类钢材尺寸的容许偏差,可参照有关国标或指标中的规定进行核查。
3、钢材表面质量检验,不论角钢、钢板、型钢、槽钢和圆钢表面均不允许有结疤、裂纹、折叠和分层等缺陷。
如有上述缺陷者,应另行堆放,以便研究处理,钢材表面锈蚀深度,不得超过其厚度公差。
铁路客车车体结构参数化分析

1 参数化设计
1 1 参数 化设 计 思想 .
参数 化设 计思 想是 指对 参数 组 的每一 个参数 给予 具体 的数 值 , 图形 的大小 按 所赋数 值决 定 . 对 这组 参数 赋予 不 同的 值 , 得 到结 构 相 似 但 大小 将 不 同的一 组 系列 图形 j参 数 的概 念 总 是 与模 型 .
铁 路 客 车 车体 结构 参数 化 分 析
孙 丽萍 刘 可心 刘岩 王玉艳 , , ,
(. 1 大连交通大 学 交通运输工程 学院, 辽宁 大连 16 2 ;2 北京铁路局 北京动车客车段 , 10 8 . 北京 10 3 ) 0 0 9
摘
要: 根据我国通用铁路客车车体钢结构 的特点 , 在车 体结构有 限元建模 与分 析 的过 程 中, 引入结 构参
大地减轻 了有 限元分 析的工作量.
关键词 : 铁路 客车 ; 车体 ; 参数化 ; P L AD
文献标识码 : A
0 引言
车体钢结构是车体的主要承载部分 , 也是车 辆中安装与连接其它部件的基础 , 车体结构 的设 计不仅要满足车辆总体布置 的要求 , 为乘客提供 良好 的乘 坐环 境 , 且 要 求 车 体 钢 结 构具 有 足 够 而
第3 2卷
第 3期
大 连 交 通 大 学 学 报
J OURNAL OF DA AN LI JA 0NG I 0T UN VER I Y I ST
Vo . No. 132 3 2 1 u .0 1
文 章 编 号 :63 99 (0 )30 0 —4 17 —5 0 2 1 0 —0 70 1
构分 析 中 , 一 地 进 行 建 模 与 分 析 , 复 工 作 量 逐 重 大. 因此 , 在车 体有 限元 建模 与分 析过 程 中引入 参 数化设 计 的思 想 , 用 参 数 化设 计 和有 限元 分 析 利
高速客车车体钢结构静强度计算及优化设计

速 度 200 km/h 高速客车碳钢车体钢结构,是中车 浦镇车辆有限公司继速度200 km/h 高速客车不锈钢车 体 后 ,自主研发设计的全新车体钢结构。车体除辊弯件 和 牵 枕 缓 外 ,热 轧 板 采 用 新 型 耐 候 钢 ,车 体 材 料 耐 腐 蚀 性能提高一倍;并在车体钢结构设计中采用全新的防腐 结 构 ,有效提高车体钢结构防腐蚀能力,减少车体钢结 构 全 寿 命 成 本 。车 体 侧 墙 和 端 墙 立 柱 、纵 梁 及 车 顶 小 弯 梁均采用乙型断面,与侧墙板、侧顶板、端墙板均采用电 阻 点 焊 ,从 而 提 高 外 墙 板 平 整 度 。 1 主要技术参数
880 959 200
2 车体钢结构
速 度 2 0 0 k m /h 客车碳钢车体,采用整体承载无中
梁筒形结构,鼓 型 断 面 ,如 图 1 所 示 。车体钢结构采用 模块化设计,由底架、侧 墙 、车顶、端墙六大模块组成,如 图 2 所 示 。各模块间通过电弧焊连接,以保证车体密封
性 ; 侧 墙 板 、端 墙 板 和 侧 顶 板 与 骨 架 主 要 采 用 电 阻 点 焊 。 3 车体强度设计标准
( ) 进行模态分析时,采用无约束的边界条件。 4 . 4 计算结果
初 步 计 算 时 发 现 ,在 端 部 压 缩 的 窗 下 横 梁 处 300 k N 压缩工况下,有侧门端的端门框处应力超过了 材 料 的 许 用 应 力 ,主 要 由 于 端 门 框 采 用 开 口 槽 型 梁 结 构 ,优化后改为封闭的方梁结构,应力明显下降,如 图 5 所示。
图 3 车体有限元模型图
图 4 局部模型图
4.2 计算工况 计算载荷及工况按照《200 km/h 及以上速度级铁
道车辆强度设计及试验鉴定暂行规定》确 定 ,共 计 1 2 个 工况 (见 表 2)。
铁路客车车体

铁路客车车体一、25型客车车体25型客车车体为全钢焊接无中梁(行李车及部分发电车除外)薄壁筒形整体承载结构。
25G型客车车体主要由底架、侧墙、车顶和端墙等部件焊接而成;25T型客车、时速160公里动力集中电动车组(直车体)拖车及控制车在25G型客车车体基础上增设了车下裙板;控制车还包括司机室钢结构,如图1和图2所示。
25型客车车体材料主要采用耐候钢,主要承载部件(牵引梁、枕梁和中梁等)采用碳素结构钢或低合金高强度结构钢,卫生间地板、洗面间地板及空调机组安装平台的平顶板等易腐蚀部位采用不锈钢。
除此之外,车体还包括蹬车脚蹬、防爬盒和扶手等车体附件。
图125T型客车车体、时速160公里动力集中电动车组(直车体)拖车1—底架;2—侧墙;3—车顶;4—端墙;5-裙板图2时速160公里动力集中电动车组(直车体)控制车1—底架;2—侧墙;3—车顶;4—端墙;5—裙板;6—司机室钢结构1.底架底架主要用于承受纵向载荷与垂直载荷。
底架设有转向架、车钩缓冲装置、裙板和车下设备等安装接口。
25型客车底架的外形尺寸基本一致,但结构不全相同,一般采用无中梁结构,行李车及部分发电车采用有中梁结构。
(1)无中梁底架无中梁底架由牵引梁、枕梁、缓冲梁、侧梁、横梁和金属地板等组成,如图3所示。
图3无中梁底架1—牵引梁;2—枕梁;3—缓冲梁;4—侧梁;5—横梁;6—金属地板(2)有中梁底架有中梁底架由牵引梁、枕梁、缓冲梁、中梁、侧梁、横梁和金属地板等组成,如图4所示。
图4有中梁底架1—牵引梁;2—枕梁;3—缓冲梁;4—侧梁;5—横梁;6—金属地板;7—中梁2.侧墙侧墙是与底架相连接组成车体侧面的部件。
25型客车车体侧墙钢结构外表面为无压筋平板,在外墙板内侧焊有垂直立柱和水平纵向梁,形成板梁式平面承载侧墙结构,主要由上边梁、侧立柱、门框、纵向梁和侧墙板等组成,如图5所示。
侧墙上设有侧门、车窗等安装接口。
图5侧墙1—上边梁;2—侧立柱;3—侧门框;4—纵向梁;5—侧墙板3.车顶车顶位于车体的上部,由侧墙、端墙所支撑,断面为弧形,主要由车顶边梁、弯梁、纵向梁、顶板、中部端顶和空调机组安装平台等组成,如图6所示。
铁路客车车体钢结构防腐技术

铁路客车车体钢结构防腐技术作者 徐凤妹内容提要:本文叙述了铁路客车车体钢结构防腐技术,防腐涂料的种类、特性,重点介绍了铁路客车车体钢结构防腐涂料的特性及其表面处理的方式。
※ ※ ※1概述铁路客车车体钢结构防腐技术,是铁路客车生产过程中的重要技术之一,它是提高客车使用寿命和增加其表面装饰性的双重工程。
目前,我国时速200km/h以下的铁路客车车体,大多采用碳钢车体。
时速200至250km/h的铁路客车车体一般采用碳钢车体或不锈钢车体,对于250km/h以上的高速动车组一般采用不锈钢车体或铝合金车体。
碳钢车体主要使用的材料有:普通碳素钢和镍铬系耐候钢。
车体钢结构的寿命主要取决于两个方面:其一,选择耐腐蚀的材料,如不锈钢或铝合金。
其二,在碳素钢的基础上提高防腐技术。
前者由于材料成本高且制造工艺难度较大,在常规客车上难以广泛采用,后者由于成本低,制造工艺相对简单,在常规客车上应用广泛。
在客车产品设计制造过程中,对于金属零部件,合理地选择材料、正确的结构设计、合理选择防腐技术,是设计必须遵循的三个重要原则,在材料和结构确定的前提下,正确选择防腐技术是提高其防腐性能和表面装饰性的关键环节。
本厂车体钢结构的防腐重点主要体现在钢材预处理、钢结构防腐和外皮油漆三个阶段。
这三个阶段分别在压铆车间、钢结构车间和客车车间进行。
对于常规客车车体上述三个阶段的防腐及涂装要求,铁道部在招议标《技术规范》中作出如下规定:1级、局部a) 车体钢结构的钢材表面应进行预处理,进行抛丸处理的钢材表面清洁度应达到Sa22Sa2级;薄钢板表面清洁度应达到有关规定的要求。
b) 车体钢结构内、外表面应在彻底干燥的情况下涂两遍防锈底漆,每遍厚度不小于30μm;车体钢结构内部及底架外部涂完防锈漆后,再涂3mm厚的沥清浆;或在车体钢结构内部及底架外部喷涂厚度不小于200μm厚的重防腐涂料。
c) 车体外部墙面漆应涂两遍,顶板涂三遍,每遍厚度不小于30μm,面漆采用双组份聚氨酯油漆。
基于欧洲标准不锈钢客车车体制造工艺大揭秘
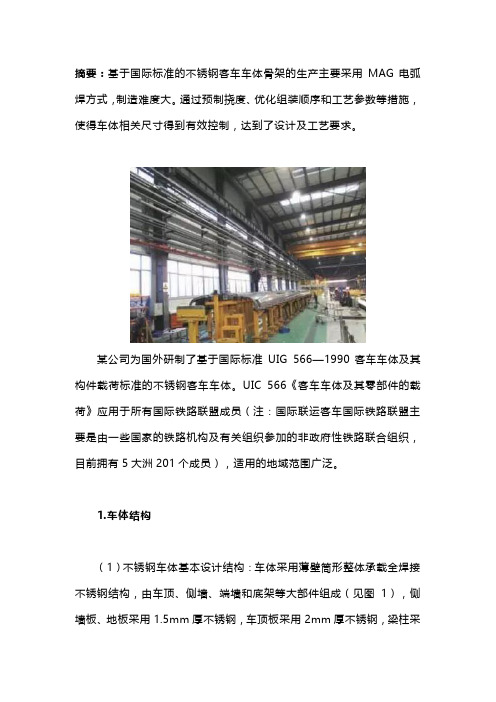
摘要:基于国际标准的不锈钢客车车体骨架的生产主要采用MAG电弧焊方式,制造难度大。
通过预制挠度、优化组装顺序和工艺参数等措施,使得车体相关尺寸得到有效控制,达到了设计及工艺要求。
某公司为国外研制了基于国际标准UIG 566—1990客车车体及其构件载荷标准的不锈钢客车车体。
UIC 566《客车车体及其零部件的载荷》应用于所有国际铁路联盟成员(注:国际联运客车国际铁路联盟主要是由一些国家的铁路机构及有关组织参加的非政府性铁路联合组织,目前拥有5大洲201个成员),适用的地域范围广泛。
1.车体结构(1)不锈钢车体基本设计结构:车体采用薄壁筒形整体承载全焊接不锈钢结构,由车顶、侧墙、端墙和底架等大部件组成(见图1),侧墙板、地板采用1.5mm厚不锈钢,车顶板采用2mm厚不锈钢,梁柱采用2~4mm不锈钢。
不锈钢车体主结构材料采用高强度超低碳奥氏体不锈钢和奥氏体铁素体双相不锈钢,按照客户要求,车顶有1个空调机组平台,侧墙采用通长侧墙板外侧附加一层波纹板结构。
(2)不锈钢车体钢结构工艺特点:由于UIG 566标准对车体强度的要求远高于国内客车采用的TB1335标准,为提高车体强度,除了车体结构进行加强之外,车体骨架焊接大部分采用了MAG电弧焊方式,而非不锈钢车体通常采用的、焊接变形较小的电阻点焊方式,所以焊接变形量更大,焊接变形更难控制。
2.制造工艺难点该不锈钢客车车体制造中存图1 车体结构在如下难点:(1)车体挠度控制。
车体组成挠度要求枕内上挠8~13mm,枕外下垂0~5mm。
由于侧墙组成窗口密集,造成整体刚度较弱,并且侧墙与底架边梁垂向错位,不在同一立面(见图2),侧墙无法带动底架整体变形,车体挠度控制是难点之一。
图2 侧墙与底架连接形式(2)侧墙平面度控制。
侧墙门口平面度直接关系到车门的安装与调试,窗口部位平面度关系到车窗的安装。
该不锈钢客车车体为无涂装车体,墙板原材料表面裸露在外面,墙板表面状态直接影响车辆的整体视觉效果。
轨道客车不锈钢车体焊接工艺研究

轨道客车不锈钢车体焊接工艺研究发布时间:2021-10-28T05:24:03.390Z 来源:《中国建设信息化》2021年12期作者:陈宇王建明[导读] 随着经济的发展和城市化进程的加快,轨道客车制造业越来越受到重视。
不锈钢作为车身材料,能够满足轨道客车耐蚀和轻量化等要求。
陈宇王建明中车唐山机车车辆有限公司客检事业部,河北省唐山市 063000摘要:随着经济的发展和城市化进程的加快,轨道客车制造业越来越受到重视。
不锈钢作为车身材料,能够满足轨道客车耐蚀和轻量化等要求。
采用激光焊接不锈钢车体能够抑制传统电弧焊和电阻点焊时产生的缺陷,满足车体使用性能和外观的要求。
该技术是车体焊接的发展方向,推动轨道客车制造业的发展。
关键词:轨道客车;不锈钢;车体焊接;工艺;分析1导言在我国,轨道客车按车体材质主要分为碳钢车、铝合金车和不锈钢车。
我国于1987年开始在普通铁路客车上使用不锈钢材料,主要用于外墙板及易腐蚀的梁柱。
1996年与韩国韩进公司合作,开发出了点焊结构的不锈钢车体。
但真正意义上的轻量化不锈钢车体的制造,始于2003年制造完成的北京城轨轻量化不锈钢样车、天津滨海线轻轨快速不锈钢客车。
由于不锈钢客车与普通碳钢客车相比具有重量轻、使用寿命长、制造组装工艺简单、无须涂漆、免维修等优点,与铝合金客车相比具有疲劳寿命长、更具耐磨性、损伤后易于修复、且成本低廉的优点,所以不锈钢客车在我国轨道客车发展中将有广阔的前景。
2轨道客车的车体材料随着工业的发展,对城市轨道车辆的要求越来越高。
轨道客车车体材料的强度、刚度、耐蚀性等直接影响着轨道客车的安全性、使用寿命和经济效益。
车体材料的选择在其发展中起着重要的作用。
车体材料主要有普通碳钢、铝合金和不锈钢。
普通碳钢价格低廉,适合多种焊接方法加工,但是会增加车体重量,不具备耐蚀性。
铝合金作为车体材料密度小,可以减轻车体重量,但是价格比较昂贵,限制了其广泛应用。
而不锈钢作为车体材料一定程度上弥补了普通碳钢和铝合金的不足。
某铁路客车车体模块化设计及强度计算

某铁路客车车体模块化设计及强度计算本文主要阐述了铁路客车车体的结构特点和主要部件结构,同时对车体的静强度进行了仿真计算,计算结果表明车体结构强度满足标准要求,同时对碳钢侧墙墙板的焊接提出了新的研究方向。
标签:铁路客车;车体;静强度;仿真1 引言铁路客车车体按照结构材料划分可分为碳钢车车体、铝合金车体及不锈钢车体,目前已经有相关企业已经生产出碳纤维车体,但仍旧处在研发试验阶段,距离实际运用还有很长的路要走。
铁路客车车体作为承载设备和乘客的重要载体,其强度及安全性尤为重要。
2 车体结构要求车辆采用碳钢车体,为满足整车轴重要求,车体设计为整体承载无中梁筒形结构。
端部底架需考虑结构的整体稳定性,以提高侧门的密封性能。
材料选用主要是耐候钢,底架边梁、侧墙上边梁及顶盖边梁均采用普通碳素钢型钢,易腐蚀部位采用不锈钢(如洗手间、厨房等区域)。
车体结构设计首先要考虑的是先要满足车体强度、刚度的要求,尽可能实现等强度或者冗余强度设计,同时也要考虑到车体制造工艺、防腐性等因素。
3 车体结构设计3.1 车体结构整个车体设计采用模块化设计思路,主要由底架、侧墙、车顶、端墙及车钩缓冲装置等组成,在车体方案设计时除考虑总体平面布置等外部接口外,还需对车体各个大部件之间的连接关系进行设计。
侧墙墙板与底架边梁、端墙墙板与底架缓冲梁连接均设计成搭接方式,提高整车美观度。
3.2 底架结构底架作为车体最重要的部件,不仅仅承担着传递整车纵向拉伸和压缩载荷,同时还需要承载底下吊挂设备及车上设备及乘客的载荷。
底架主要由端部底架、边梁、横梁、纵梁、设备吊座和底架地板组成。
底架横梁的布置根据各设备吊挂位置进行设计,需要吊挂设备位置的底架横梁采用刚度较大的口型梁结构,其余部位采用U型梁结构,U型梁横梁及纵梁可以有效的减轻整车重量,同时能为底架地板提供支撑。
3.3 侧墙结构侧墙结构主要由乙型立柱、乙型横梁及L型横梁构成的网状结构,侧墙上的窗口根据总体方案布置,窗口四个角区域容易引起应力集中,所以在侧窗窗口四个角设置有补强块。
铁路客车车体模块化设计技术

铁路客车车体模块化设计技术作者 廖平为了适应现代客车的大规模生产,努力提高客车的设计制造水平,近几年来,在客车设计中全面贯彻模块化设计理念,在制动、车电、暖通和车体的设计中广泛展开了模块化设计,在简化设计工作、提高产品质量、缩短组装周期和提升工厂产量方面取得了巨大的成果。
本文着重对车体模块化设计技术进行介绍,供相关设计人员学习参考。
※ ※ ※1模块化概念所谓模块,实际上就是某一系统集成后所形成的功能单元。
一个模块可以具有一种功能,也可以具有多种功能。
各模块通过插接或连接即形成一个局部或整机系统,再通过一定的包装和装饰即形成产品。
随着社会的发展和技术的进步,“模块化”概念已广泛应用于各个领域,尤其在电气行业,由简单的线排到大规模集成电路,电器元件的模块化已普遍采用,一个复杂的电气控制系统现在只要一个电路板和几个功能模块插件就可以实现,并使非常复杂的电气系统变得结构简单,条理清晰,维修方便,计算机行业尤其在集成电路方面取得了高速发展。
一般地说,模块化程度越高,产品就越先进。
模块本身必须具有技术上的先进性,设计上的合理性,性能上的可靠性,成本方面的经济性和寿命长等优势,才能使该产品具有生命力。
当前,铁路客车的设计制造技术正在进入与世界同步发展的轨道,高速动车组设计制造技术已达到世界先进水平,尤其在牵引、制动、控制和转向架等性能方面有了极大的提高,其装备也逐步现代化,舒适度明显改善,但本厂生产的客车在车体结构方面却明显落后,与高速技术的发展和现代化大生产方式不相适应。
为了解决这种状况,引入“模块化”的设计理念就显得十分重要。
2 模块化设计的发展1975以前,钢结构的生产仅有底架和端墙两个胎模,侧墙和车顶的组成均采用散件组装,各梁、柱均采用“搭积木”的方式进行逐件组焊,然后蒙上墙板和顶板。
一辆车体钢结构组成,至少要一个星期,最快也要三天左右,这样的生产方式要想大幅度提高产量和产品质量是根本不可能的,直到1985年钢结构的六大片才实现部件设计并按部件生产,组装开始实现胎膜化。
浅析轨道客车车体钢结构制造工艺
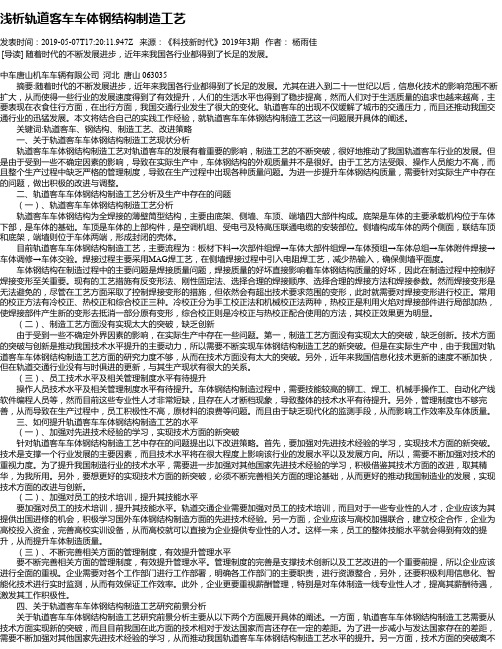
浅析轨道客车车体钢结构制造工艺发表时间:2019-05-07T17:20:11.947Z 来源:《科技新时代》2019年3期作者:杨雨佳[导读] 随着时代的不断发展进步,近年来我国各行业都得到了长足的发展。
中车唐山机车车辆有限公司河北唐山 063035摘要:随着时代的不断发展进步,近年来我国各行业都得到了长足的发展。
尤其在进入到二十一世纪以后,信息化技术的影响范围不断扩大,从而使得一些行业的发展速度得到了有效提升,人们的生活水平也得到了稳步提高,然而人们对于生活质量的追求也越来越高,主要表现在衣食住行方面,在出行方面,我国交通行业发生了很大的变化。
轨道客车的出现不仅缓解了城市的交通压力,而且还推动我国交通行业的迅猛发展。
本文将结合自己的实践工作经验,就轨道客车车体钢结构制造工艺这一问题展开具体的阐述。
关键词:轨道客车、钢结构、制造工艺、改进策略一、关于轨道客车车体钢结构制造工艺现状分析轨道客车车体钢结构制造工艺对轨道客车的发展有着重要的影响,制造工艺的不断突破,很好地推动了我国轨道客车行业的发展。
但是由于受到一些不确定因素的影响,导致在实际生产中,车体钢结构的外观质量并不是很好。
由于工艺方法受限、操作人员能力不高,而且整个生产过程中缺乏严格的管理制度,导致在生产过程中出现各种质量问题。
为进一步提升车体钢结构质量,需要针对实际生产中存在的问题,做出积极的改进与调整。
二、轨道客车车体钢结构制造工艺分析及生产中存在的问题(一)、轨道客车车体钢结构制造工艺分析轨道客车车体钢结构为全焊接的薄壁筒型结构,主要由底架、侧墙、车顶、端墙四大部件构成。
底架是车体的主要承载机构位于车体下部,是车体的基础。
车顶是车体的上部构件,是空调机组、受电弓及特高压联通电缆的安装部位。
侧墙构成车体的两个侧面,联结车顶和底架,端墙则位于车体两端,形成封闭的壳体。
目前轨道客车车体钢结构制造工艺,主要流程为:板材下料→次部件组焊→车体大部件组焊→车体预组→车体总组→车体附件焊接→车体调修→车体交验。
铁路车辆车体钢结构的检修及改造

铁路车辆车体钢结构的检修及改造摘要:铁路车辆车体钢结构大部分为全钢焊接结构,由底架、侧墙、车顶和端部组成。
车辆经过一个厂修期后对钢结构有四种基本的损坏,钢结构的腐蚀、变形、裂纹、松脱。
钢结构是整个车辆的载体,鉴于他在车辆中的作用及重要性,钢结构检修与改造必将推动其他部位的发展。
关键词:工艺流程检修加改加改设计注意正文:车辆车体钢结构大部分为全钢焊接钢结构,由底架、侧墙、车顶和端部组成。
在侧墙、端墙、车顶钢骨架外面,在底架钢骨架的上面,分别焊有侧墙板、端墙板、车顶板和纵向波纹地板及平地板,形成一个上部圆弧,下部为矩形的封闭壳体,俗称薄壁筒型钢结构。
壳体内面或外面用纵向梁、柱加强,形成整体承载的合理结构。
钢结构检修基本上是修车的第一大流程,也可以说是最基础的一个工艺流程,钢结构是车辆的重要部件,它要承受来自各个方向的多种作用力,因此车体需要足够的强度和刚度及稳定性,以确保运营安全。
车体材料通常有碳素钢、耐候钢、不锈钢、及铝合金四种,在改造过程选择时,要考虑降低车辆重量、耐腐蚀性好和良好的加工性能,价格便宜。
钢结构在我们整个生产中也具有十分重要的地位,因为所有设备均都直接或间接的固定在车体钢结构上,钢结构质量的好坏直接影响着下面所有工序的进行,如果在其他工序中发现钢结构尺寸有误,将带来严重的返工。
因为如果要对钢结构进行返工,在我们现有的工艺情况下,几乎所有的工序都要拆掉,才能对钢结构动火处理。
基于对钢结构的特殊性,如有差错将直接导致车辆的安全,而对我们的生产也带来最难处理的返工。
因此对钢结构的尺寸及强度、刚度、韧度必须严格要求。
在我厂,钢结构部分不外乎有两种,一种是对钢结构检修、一种是对钢结构的加改。
一、首先车辆经过一个厂修期后对钢结构有四种基本的损坏。
钢结构的腐蚀、变形、裂纹、松脱。
1.钢结构腐蚀后的修理车辆底架钢结构发生腐蚀大都在端部、通过台处。
由于端部大都为厕所和洗手间以及锅炉、茶炉布置。
水很容易渗入木地板到达铁地板处而造成对地板及地梁的腐蚀。
铁路客车车体钢结构设计技术(精)

铁路客车车体钢结构设计技术作者杜彦品内容提要:本文叙述了铁路客车车体钢结构的特点及分类,重点介绍了25型客车碳钢车体钢结构的组成部分、结构设计及主要技术要求,对铁路客车车体钢结构材料的选用及结构设计将有积极的帮助。
※※※1概述车体钢结构是铁路客车最基本的结构,为铁路客车走行部、制动装置、连接缓冲装置、车辆内部设备以及内装提供了安装的空间和基础。
新造25型客车车体钢结构为碳钢车体全钢焊接结构,由底架、侧墙、车顶和端墙等四部分焊接而成,俗称薄壁筒形车体结构。
目前我国的新造25型车有两种承载结构:一种是无中梁薄壁筒型整体承载结构,另一种是有中梁薄壁筒型整体承载结构(如行李车和邮政车。
随着车辆的用途和生产工艺条件的不同,各种25型客车的结构不全相同,但其外形尺寸和结构形式则基本一致。
2 车体结构的分类车体结构按车体所用材料分为以下三种:碳素结构钢车体——我国新造25型客车车体;不锈钢车体——我公司正在研制的200km/h客车车体, CRH1“和谐号”动车组的车体;铝合金车体——部分地铁车体、CRH2、CRH3、CRH5“和谐号”动车组的车体。
3 车体钢结构组成车体钢结构按部位可分为四个大部件:底架钢结构、侧墙钢结构、车顶钢结构、端墙钢结构。
车钩缓冲装置、风挡、脚蹬等安装在大部件上。
现就YZ25G(T 型硬座车(无中梁薄壁筒型整体承载结构和XL25G型行李车(有中梁薄壁筒型整体承载结构来详细说明车体钢结构的构造和特点。
YZ25G硬座车车体钢结构如图1所示。
4 底架钢结构4.1 底架结构组成底架钢结构由端牵枕、枕内横梁、枕外横梁、枕后纵向梁、侧梁、枕外铁地板和枕内波纹地板等组成,如图2所示。
端牵枕分为端梁、牵引梁和枕梁,如图3所示。
4.2 底架结构设计4.2.1 端梁端梁由6mm厚钢板压制而成,断面为“[”,YZ25G型硬座车端梁高400mm靠近侧梁处高180mm,称为“转角”。
在转角下翼面焊有3mm的围板,围板可以在端部遮挡脚蹬,起到美观的作用。
铁路客车车体结构及制造工艺的演变与展望

铁路客车车体结构及制造工艺的演变与展望摘要:铁路客车是指载有乘客的车辆、载有乘客的车辆和载有乘客的火车上用于其他目的的车辆。
根据使用情况,铁路客车可分为硬座车、软座车、硬座车、车门车、行李车、餐费车、邮政车等。
关键词:铁路客车;车体结构;制造工艺;演变与展望引言铁路公共汽车在中国肩负着沉重的运输责任,是运载乘客的铁路运输设备。
作为现代铁路运输系统的支柱,它在国民经济中发挥着重要作用。
随着国家经济技术的发展,铁路客车不断发展,产品范围呈现多元化发展趋势,但高速铁路客车依然是主要力量。
以下是对高速铁路客车车身结构和制造工艺演变的探讨。
一、不锈钢客车的优势1.1抗腐蚀性,低维修性不锈钢材料腐蚀性很强,传统钢结构私家车使用寿命为50年,在使用过程中需在工厂修理4 ~ 5次。
私家车钢结构的墙面和地板经过两次修复后被腐蚀,腐蚀区域需要开挖处理。
钢结构体的腐蚀部分在提取处理过程中必须去除,从而延长了维护时间,在一定程度上损坏了体。
特别是,近年来制造的25型客车车身,其壁面设有无压力平板,修理过程中需要局部处理鞋面,容易导致钢结构变形,从而破坏了整体客车结构。
1.2简化客车生产的工艺流程传统的客车车身制造主要采用钢预处理技术,避免了客车使用过程中出现钢板锈蚀问题。
钢预处理时,应进行除垢、清洗、磷化等过程。
,以提高钢基涂料的粘接性,避免腐蚀问题。
钢预处理技术在应用过程中容易烧墙板,需要重新设计,但这种二次处理可能影响钢结构的整体使用质量,缩短材料的使用寿命。
将不锈钢材料应用于私家车生产可有效利用不锈钢耐蚀性的优势,简化传统制造工艺中的预处理,从而延长主要材料的使用寿命。
二、21型客车和22型客车特点2.1 21型客车是我国第一代客运列车的主要车型,时速80 ~ 100km/h-1,机车长度21975mm,机车宽度3004mm,结构采用复盖层和碳钢焊接相结合的形式。
随着运行需求的变化,机车车身结构得到改善以减轻重量,包括全焊接结构和侧壁压力筋。
- 1、下载文档前请自行甄别文档内容的完整性,平台不提供额外的编辑、内容补充、找答案等附加服务。
- 2、"仅部分预览"的文档,不可在线预览部分如存在完整性等问题,可反馈申请退款(可完整预览的文档不适用该条件!)。
- 3、如文档侵犯您的权益,请联系客服反馈,我们会尽快为您处理(人工客服工作时间:9:00-18:30)。
铁路客车车体钢结构设计技术作者杜彦品内容提要:本文叙述了铁路客车车体钢结构的特点及分类,重点介绍了25型客车碳钢车体钢结构的组成部分、结构设计及主要技术要求,对铁路客车车体钢结构材料的选用及结构设计将有积极的帮助。
※※※1概述车体钢结构是铁路客车最基本的结构,为铁路客车走行部、制动装置、连接缓冲装置、车辆内部设备以及内装提供了安装的空间和基础。
新造25型客车车体钢结构为碳钢车体全钢焊接结构,由底架、侧墙、车顶和端墙等四部分焊接而成,俗称薄壁筒形车体结构。
目前我国的新造25型车有两种承载结构:一种是无中梁薄壁筒型整体承载结构,另一种是有中梁薄壁筒型整体承载结构(如行李车和邮政车。
随着车辆的用途和生产工艺条件的不同,各种25型客车的结构不全相同,但其外形尺寸和结构形式则基本一致。
2 车体结构的分类车体结构按车体所用材料分为以下三种:碳素结构钢车体——我国新造25型客车车体;不锈钢车体——我公司正在研制的200km/h客车车体, CRH1“和谐号”动车组的车体;铝合金车体——部分地铁车体、CRH2、CRH3、CRH5“和谐号”动车组的车体。
3 车体钢结构组成车体钢结构按部位可分为四个大部件:底架钢结构、侧墙钢结构、车顶钢结构、端墙钢结构。
车钩缓冲装置、风挡、脚蹬等安装在大部件上。
现就YZ25G(T 型硬座车(无中梁薄壁筒型整体承载结构和XL25G型行李车(有中梁薄壁筒型整体承载结构来详细说明车体钢结构的构造和特点。
YZ25G硬座车车体钢结构如图1所示。
4 底架钢结构4.1 底架结构组成底架钢结构由端牵枕、枕内横梁、枕外横梁、枕后纵向梁、侧梁、枕外铁地板和枕内波纹地板等组成,如图2所示。
端牵枕分为端梁、牵引梁和枕梁,如图3所示。
4.2 底架结构设计4.2.1 端梁端梁由6mm厚钢板压制而成,断面为“[”,YZ25G型硬座车端梁高400mm靠近侧梁处高180mm,称为“转角”。
在转角下翼面焊有3mm的围板,围板可以在端部遮挡脚蹬,起到美观的作用。
在端梁中部开有安装车钩用的缺口,宽度为345mm,俗称“钩门”。
YZ25T型硬座车端梁高度为458mm,钩门的宽度尺寸为790mm,端梁在钩门处与牵引梁相互组焊。
4.2.2 牵引梁自枕梁到端梁间的中梁称为牵引梁,YZ25G型硬座车牵引梁由两根30b型槽钢及牵引梁上下盖板组焊而成。
其上盖板厚4mm,宽464mm,下盖板厚8mm,宽490mm。
为了符合在牵引梁腹板间安装车钩和缓冲器的尺寸要求,两槽钢腹板间距为350mm,并将牵引梁靠近端梁的一端加高到400。
在牵引梁两槽钢腹板内侧铆接有前后从板座、焊有磨耗板和防跳板。
YZ25T型硬座车牵引梁由两根8mm的钢板压制而成,其上盖板厚4mm,宽524mm,下盖板厚6mm,宽560mm。
为了符合在牵引梁腹板间安装车钩和缓冲器的尺寸要求,两牵引梁腹板间距为440mm,靠近端梁一端为喇叭状,间距为790mm,高度为458mm。
在牵引梁两腹板内侧铆接有车钩安装座。
4.2.3 枕梁YZ25G型硬座车枕梁由厚8mm、间距为350mm的两重向腹板及厚10mm、宽600mm的下盖板,厚6mm、宽600mm的上盖板组焊而成的闭口箱形断面“Ⅱ”,枕梁近侧梁端为小端,近牵引梁端为大端,它是一个近似的等强度鱼腹梁。
在枕梁下盖板下面与牵引梁交叉处安装有心盘座,以提高该处的承载作用,提高枕梁和牵引梁的连接强度和刚度。
在枕梁两端的上旁承安装处焊有上旁承加强板,枕梁端部还焊有供顶车用的顶车垫板。
YZ25T型硬座车枕梁腹板厚8mm,间距为424mm,下盖板厚12mm,宽600mm,上盖板厚6mm、宽600mm。
在枕梁两端焊有空气弹簧安装座,枕梁端部也焊有供顶车用的顶车垫板。
4.2.4 地板梁枕内横梁位于两枕梁之间,横梁均布, 间距在1m以内,也可根据车下设备的位置进行调整。
枕外横梁位于端梁和枕梁间,有2对,断面为“[”,高180mm、厚4mm(有集便器的为6mm,翼面宽50mm; (有集便器的为60mm。
枕内外第一根横梁一般距枕中1700~2000mm,具体还要根据转向架所占据的空间而定。
这些横梁的两端分别与侧梁和牵引梁或是两端与侧梁焊接。
这些横梁的作用:一是把牵引梁结构与侧梁连接起来形成底架钢结构骨架,从而保证底架有足够的强度和刚度,以承受作用于底架上的各种载荷;二是成为平地板和波纹地板的支撑,在纵向力作用下防止波纹地板的失稳。
枕后纵向梁在枕内,靠近枕梁每端四组,第一组为鱼腹形槽形断面,其余三组断面同枕内横梁。
枕后纵向梁主要起传递纵向力的作用。
4.2.5 侧梁底架两侧有通长的侧梁,其断面为18型槽钢。
在横向,底架的枕梁及全部横梁的端部都与侧梁焊接,金属地板也与侧梁的上翼面搭接;侧墙的立柱、侧墙板分别焊在侧梁的上翼面和腹板外表面上,所以,侧梁是连结侧墙和底架的重要构件。
其连接关系如图1所示。
底架的牵枕缓、侧梁和横梁共同形成底架钢骨架。
4.2.6 金属地板在底架钢骨架的上面焊上金属地板。
在端梁和枕梁上盖板间为平地板,板厚为2mm;两枕梁间为纵向波纹金属地板,波纹地板断面为( 1.5mm。
由底架钢结构骨架和金属地板共同组成底架钢结构。
由于两枕梁间无贯通的中梁,因而作用于底架上的纵向拉压力均由波纹地板和侧梁来承担。
由车体钢结构静强度试验表明,波纹地板能承受三分之一以上的总纵向拉伸或压缩力,这种结构的底架称为无中梁底架。
4.3 有中梁底架结构另外一种有中梁底架,如行李车,下面以XL25G型行李车为例来说明有中梁底架的结构。
图4是XL25G底架钢结构,XL25G型行李车底架钢结构由端牵枕、中梁、枕内横梁布置、一位枕外横梁布置、二位枕外横梁布置、主横梁、一位端铁地板、二位端铁地板、枕内铁地板、站铁组成、底架线管布置、底架配件布置、侧梁组成、侧梁、补强梁等组成。
牵枕缓和侧梁结构与YZ25G型硬座车类似,不同之处为枕内均布有四组鱼腹形的主横梁,厚度为6mm,断面为“”,下翼面尺寸为120mm。
在大拉门处有两组补强梁,厚度为6mm,断面为“”,高度尺寸为280mm,下翼面尺寸为110mm。
XL25G型行李车无枕后纵向梁,有两根30b型槽钢组焊成的中梁,间距为350mm。
枕内外横梁断面均为“”,高度尺寸为110mm,下翼面尺寸为70mm,厚度为4或6mm。
行李间地板为4mm的花纹钢板,其余部分为2mm的平地板。
底架钢结构主要构件断面尺寸见表1表1 底架钢结构主要构件断面尺寸5 侧墙钢结构5.1侧墙结构组成YZ25G(T型硬座车车体钢结构的侧墙主要由立柱、纵向梁、上侧梁、门柱、门上横梁、门框组成(YZ25T型硬座车无、侧墙板等组成。
侧墙外表面为平板无压筋,在平整的外墙板内侧焊有垂直立柱和水平纵向梁,形成板梁式平面承载侧墙结构,如图5所示。
5.2 侧墙结构设计侧墙上侧梁断面为“”形,其尺寸为45x90x25x2.5(mm,长度为侧墙全长。
侧墙水平纵向梁共四根,窗上一根,窗下三根,其断面为“形,其尺寸为140x22x2.5(mm。
这四根纵向梁起到加强侧墙的垂直弯曲强度和刚度的作用,同时也减少了钢板自由表面的面积。
在侧墙窗口间有一条短的窗间小纵向梁其断面为“”形,其尺寸为140x22x2.5(mm,设置目的是增强窗间板的强度与刚度。
在窗口两侧各有一根垂向的窗边立柱,也称为侧立柱,其断面为“”,尺寸为94x70x46x2.5(mm。
在侧门处均有断面为“”形的门柱,其尺寸为25x60x100x60x25x4(mm,立柱和门柱与所有纵梁、上侧梁、底架侧梁连结起来,组成侧墙钢骨架,并与侧墙板焊结形成侧墙钢结构。
如果侧门为折页门,在门柱处还有一整体的门框组成,断面为“”形。
如果是塞拉门,就无此门框组成。
侧墙板为厚2.5mm 的耐候钢板(09CuPCrNi-B。
侧墙板上开有大窗孔,尺寸为宽x高,即1064x1014(mm,小窗孔宽x 高为614x1014(mm 。
每侧侧墙端部有两个侧门孔。
门窗开孔处是侧墙的薄弱区域,通过周边的梁柱予以加强,选择合适的窗角板的圆角半径来降低其应力集中,设计出合理结构。
5.3 行李车侧墙结构XL25G型行李车侧墙钢结构如图6,墙板和梁柱断面与YZ25G型硬座车类似,不同之处每侧侧墙端部有一个侧门孔,中间各有两个大拉门门孔,大拉门处有用方钢管80x60x4制成的门框,行李间还设有长圆形的了望窗,尺寸为960(宽x310(高(mm。
侧墙钢结构主要构件断面尺寸见表2表2 侧墙钢结构主要构件断面尺寸(侧墙板厚2.5㎜6 车顶钢结构6.1 车顶结构组成车顶钢结构由弯梁、纵向梁、顶板、一二位端顶、平顶钢结构、中部端顶、车顶边梁等组成,如图7所示。
车顶一、二位端(行李车仅一位端各有一个空调机组安装座平顶钢结构,作为安装空调机组的基础,是安装单元式空调机组的支撑框架。
6.2 车顶结构设计端顶上边为8型槽钢制成的顶端横梁,其断面尺寸为80x43x5(mm。
25G型行李车二位端无平顶,其二位端顶上边为端顶弯梁,断面为“”形,其尺寸为30x55x62.5x45x2(mm。
在平顶和圆顶相交的部分为中部端顶,将两部分连接形成整体结构。
圆顶的中间部分有很多断面为“车体纵向均布,间距一般在700(mm左右,其尺寸为94x46x70x24x2(mm。
车顶边梁沿车顶两侧全长,断面为“”形,其尺寸为45x75x2.5(mm。
车顶纵向还有五根纵向梁,其断面为“┐”形,尺寸为 50x50x3(mm。
车顶吊铁焊在车顶的弯梁或纵梁上,主要吊装设备及内装部件。
车顶板由侧顶板和中顶板两部分组成。
侧顶板是冷轧型钢,将雨檐与小圆弧(R458板及纵向梁合为一体制造成型,从而提高了侧顶板的平整度,并提高了小圆弧部分的抗弯刚度和强度,还简化了制造工艺。
中顶板为大圆弧板(R2300,车顶板厚度均为2mm。
平顶中顶板为不锈钢板,主要因为此处容易积水,考虑耐腐蚀性能。
中顶板沿车顶纵向倾斜12mm,侧顶向车两侧各倾斜10mm。
车顶钢结构是由纵横弯梁件组成的空间梁系,其上焊有曲面金属顶板(端顶和平顶为平板组成的板梁结构,共同承受作用于其上的各种载荷,车顶结构具有足够的强度和刚度,并通过防漏雨试验。
车顶钢结构主要构件断面尺寸见表37 端墙钢结构7 1 端墙结构组成客车车体钢结构的两外端,通常称为外端墙,它是车体钢结构最外端的部分。
YZ25G型硬座车端墙钢结构分为风挡框组成、门框组成、端角柱组成、梁柱组成、端墙板组成、端墙配件。
7 2 端墙结构设计风挡框折棚柱断面为“[”形,即24b型槽钢,它是保证端墙强度和刚度的重要构件。
还有两根断面为“形,尺寸为43x45.5x130x3(mm的端角柱和断面为“”形,尺寸为25x60x100x60x25x4(mm的侧门柱;两根位于端门两侧断面为“”形,尺寸为50x54x50x28x3(mm的端门框(端门为折页门时有,位于端门框和端角柱之间的“”形立柱94x70x46x2.5(mm和“”形横梁140x22x2.5(mm。