来料检验流程图
来料检验作业流程图
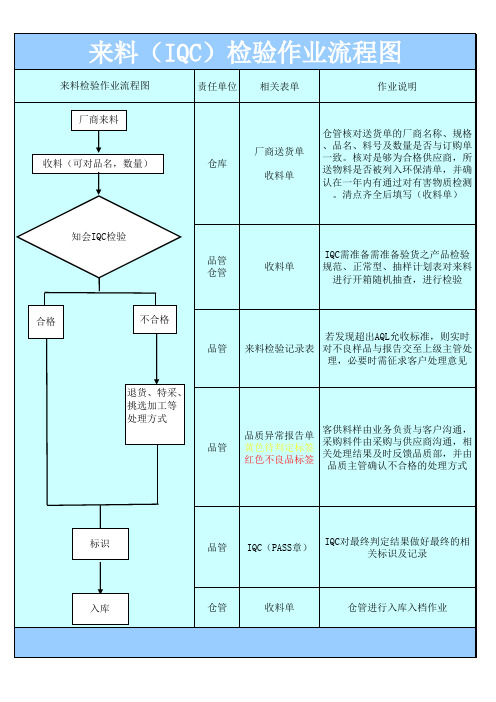
知会IQC检验
品管 仓管
收料单
IQC需准备需准备验货之产品检验 规范、正常型、抽样计划表对来料
进行开箱随机抽查,进行检验
合格
不合格
品管
若发现超出AQL允收标准,则实时 来料检验记录表 对不良样品与报告交至上级主管处
理,必要时需征求客户处理意见
退货、特采、 挑选加工等 处理红色不良品标签
客供料样由业务负责与客户沟通, 采购料件由采购与供应商沟通,相 关处理结果及时反馈品质部,并由 品质主管确认不合格的处理方式
标识 入库
品管
IQC(PASS章)
IQC对最终判定结果做好最终的相 关标识及记录
仓管
收料单
仓管进行入库入档作业
来料(IQC)检验作业流程图
来料检验作业流程图
责任单位 相关表单
作业说明
厂商来料 收料(可对品名,数量)
仓库
厂商送货单 收料单
仓管核对送货单的厂商名称、规格 、品名、料号及数量是否与订购单 一致。核对是够为合格供应商,所 送物料是否被列入环保清单,并确 认在一年内有通过对有害物质检测
。清点齐全后填写(收料单)
来料生产出货检验流程图.doc

东莞市安哲罗电子科技有限公司
IQC 来料检验流程
管理: AZL-01-2017-12
部门名称质量管理部流程名称
部门行政部采购部品质部
来料通知
配合
组织验收
检验分析
合格
入库来料检验流程图
开发部
技术支持
不合格确认
分析
报告
不合格
发异常处理单退换货处理处理意见支会异常处理回复资料存档
拟制:审核:批准
日期:日期:日期
东莞鸿瑞包装制品有限公司
IPQC制程检验流程
部门名称质量管理部流程名称制程检验流程图部门生产部品质部开发部采购部
生产计划单改进
否
审核是
首件确认
技术支持
投产
生产监督
合格
下工序
改进
制程异常
研究、分析
异常分析
反馈、记录
资料存档
拟制:审核:批准日期:日期:日期
东莞鸿瑞包装制品有限公司OQC成品检验流程
部门名称
部门生产部质量管理部
仓储部
流程名称品
质部采购部
成品检验流程图
开发部
出货通知单
组织检验
不合格
返工
合格不
合
格
进仓、出货
分析、记录
仓储抽检
不合格不合格
工艺因素物料因素
场地因素
合格
改善
异常处
理回复
拟制:审核:批准日期:日期:日期:。
IQC检验流程图

填写检验报告、做标示
让步接收
06
IQC
《进货检验 单》
入库
07
仓储部
物料入库单
记录汇总
08
IQC
汇总表
制定/日期:
审核/日期:
图
作业内容 1.提供送货清单、数量。 2.将物料摆放到指定待检区域。 3.提供物料《出货检验报告》。
1.核对报检物料是否与《到货单》 型号、规格一致。
1.核对是否为合格供应商。 2.核对物料是否试样合格。 1.检查资料有无短缺、是否有效。 2.检查仪器是否合格。 IQC依据《物料检验标准书》、《协 议文件》、图纸、样品等文件或资 料进行物料的检验。 1.填写检验记录和报告。
2.做检验标识(合格贴绿标,不合格红标)
仓储部依据《进货检验单》的处理 结果,执行物料入库或退货等处理 。
对所有检验结果进行记录汇总来自批准/日期:IQC来料检验工作流程图
流程图 序号 责任人 表单
供应商来料
01
供应商
《送货单》
仓库核对数 量及规格
02
OK
仓储部
《到货单》
来料送至待检区通知IQC
03
仓储部
查看供应商资格,准备 检验资料、工具
04
IQC
《合格供应 商名单》、 《检验指导 书》、图纸
不合格品
抽样检验
退货
05
IQC
《进货检验 指导书》
来料检验流程图定稿版

HUA system office room 【HUA16H-TTMS2A-HUAS8Q8-HUAH1688】
在规范检验工作程序,检验工作标准化。 2.0 适用范围
本程序适用于公司外购、外协件来料检验活动。 3.0 术语
无 4.0 工作程序
责任人
输入
流程
过程描述
输出
仓管
送货单
报检
仓管依据送货指导书
供方检验报 告
检验
检验员依据检验指导 书、图纸进行检验。
供方来料时必须附带检 验报告。
合格品使用白色产品标 识卡进行标识,不合格 品使用黄色产品标识卡 进行标识。
检验报告 检验记录 产品标识卡
仓管 质量部
产品标识卡 NG 标识隔离
OK 入库
采购部 质量部
急件 评审
特采申请单
质量部主导技术,生 产、采购等部门相关人 员进行评审。
部门可参与评审内容:
技术:外观、功能、尺 寸;
不合格品评审 表
品质:外观、功能、尺 寸;
返修作业指导 书
生产:过程装配尺寸;
部门评审权限:
技术:不可接收、让步 放行、返修使用;
质量部 仓管
报检单
生产:挑选、返修使 用、退货;
品质:不可接收、让步 放行、退货;
重新检验 OK NG
退货
可返修的产品,经过返 修后重新送检,检验合 格可入库,不合格则退 货供方。
入库单 退货单
非急 件 退货
采购部
质量部 生产部
不合格品评 审表
技术部
让步接收 挑选使用
返修
仓依据产品标识确定产 品是入库或者隔离。
入库单
检验员检查产品不合 格,如是非急件,可退 货处理。如是急件,则 由采购部提出特采申 请。
来料检验流程图 ppt课件
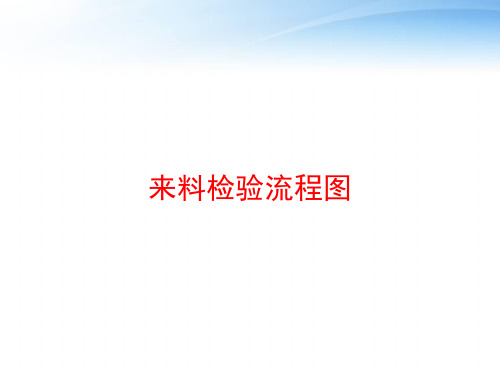
来料检验流程图
来料
供应商
仓库待检区
NG
IQC检验质量
检验合格报告 OK
仓管检验数量
来料合格区
仓管按实际数量接收
贴合格标识
OK
仓管按评审结果接收
品质、生产、采购评审
采购 退货
NG 料不良区
说明
• 1、上述检验流程仅为外观检验流程,需要 进行理化检测的原、辅来料须经集团实验 室检验合格方可使用;
• 2、检验不合格或未经检验的原材料须经制 造总监签批方可特采使用;
• 3、评审结果包括:挑选使用、让步接收
需要注意的问题
• 1、评审不合格处理: • 品检科出具《来料不合格检验报告》,并
附事实与依据(不合格照片),提供采购 科,品检科备案处理,作为供应商评分依 据;
• 2、采购科要求供应商提供纠正与改进措施
记录文件备案
• 原材料检验报告表 包括集成材、纤维板、胶合板、木皮、雕 花、玻璃、铝合金条、五金件、纸箱、胶 水、油漆;
检验流程图

返工作业流程图
品质异常报告 品管部
领料 生产部
仓库登记 仓管员
返工作业
生产部
返工品报检
生产部
返工检验 NG 包装 OK
品管部
入库
特采流程图
品质异常报告 品管部
与客户沟通
采购,业务
特采申请单
业务
包装
生产
外箱标示
生产
入库
出库
品质检验流程图
出货 OK OQC抽检 NG NG 特采 OK 入库 OK 生产领用 返修 试生产 NG 生产自检 首件 确认 OK 批量生产 报废 NG NG IPQC 巡检 NG NG 成品全检 OK 成品包装 供应商 成品入库 IQC 检验 成品全检 OK OK 包装检查 NG
NG
NG
IPQC 巡检
半成品流转
过程检验不合格流程图
生产部发现
品管部发现
追溯同类不良 发现者 隔离至不良区 生产部 贴不良标识 IPQC 品质异常报告
生产部 返工
生管部 特采
相关部门
生产部 报废
ቤተ መጻሕፍቲ ባይዱ
不良原因分析 相关人员
重新检验 提出纠正预防措施 生产部 纠正预防措施实施 品管部 措施效果确认
OK
标准化
技术部
NG
成品出货流程图
备货至出货待检区 追溯同类不良 OQC
OK
仓库
贴不良标识
OQC 出货报检
品质异常报告
OQC
放置不良物料区 仓库
NG
不良原因分析 出货检查 生产部 返工 业务部 相关部门 向顾客反馈 仓库 报废
OK
OQC
提出纠正预防措施 重新检验 顾客特许 生产部 纠正预防措施实施 特许标识 品管部 OQC 措施效果确认 特许出货
来料检验流程图

流程图负责单位参考文件
供货商
物管
进料检验员
进料检验员
进料检验员
进料检验员产品质量工程师/IQC主管
进料检验员
进料检验员
进料检验员
采购/生管
物管供货商评鉴与管理作业程序略
抽样计划表、进料检验规范、工程图、进料检验报告单
抽样计划表
工程图,进料检验规范进料检验报告单
工程图、进料检验规范、进料检验报告单
工程图、进料检验规范、进料检验报告单
合格标示
不合格标示
材料进料履历表
不合格品管制程序
成品入库、出货检验程序。
来料检验流程图
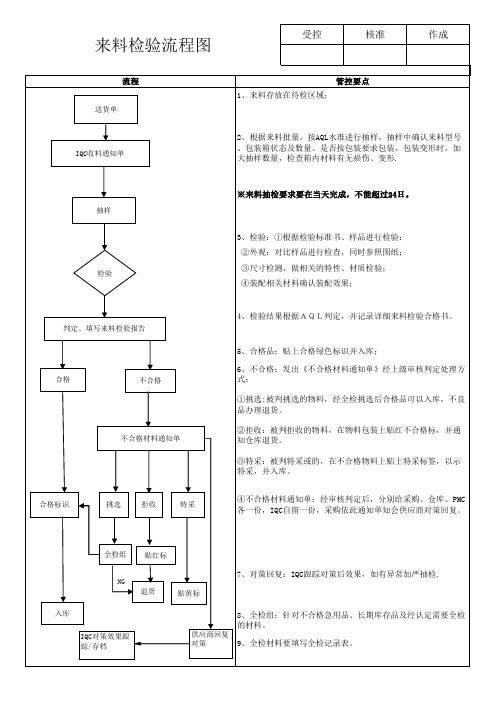
受控
核准
作成
流程 送货单
IQC收料通知单
管控要点 1、来料存放在待检区域;
2、根据来料批量,按AQL水准进行抽样,抽样中确认来料型号 、包装箱状态及数量、是否按包装要求包装,包装变形时,加 大抽样数量,检查箱内材料有无损伤、变形.
抽样
检验
判定、填写来料检验报告
合材料通知单:经审核判定后,分别给采购、仓库、PMC 各一份,IQC自留一份,采购依此通知单知会供应商对策回复。
全检组 贴红标
NG 退货
贴黄标
7、对策回复:IQC跟踪对策后效果,如有异常加严抽检.
入库
IQC对策效果跟 踪/存档
供应商回复 对策
8、全检组:针对不合格急用品、长期库存品及经认定需要全检 的材料。
9、全检材料要填写全检记录表。
合格标识
挑选
拒收
特采
※来料抽检要求要在当天完成,不能超过24H。
3、检验:①根据检验标准书、样品进行检验: ②外观:对比样品进行检查,同时参照图纸; ③尺寸检测,做相关的特性、材质检验; ④装配相关材料确认装配效果;
4、检验结果根据AQL判定,并记录详细来料检验合格书。
5、合格品:贴上合格绿色标识并入库; 6、不合格:发出《不合格材料通知单》经上级审核判定处理方 式: ①挑选:被判挑选的物料,经全检挑选后合格品可以入库,不良 品办理退货。 ②拒收:被判拒收的物料,在物料包装上贴红不合格标,并通 知仓库退货。 ③特采:被判特采或的,在不合格物料上贴上特采标签,以示 特采,并入库。
来料检验流程图

来料检验流程图来料检验是指对进入生产环节的原材料、零部件或产品进行检测和测试,以确保其质量符合要求,能够满足生产需要。
来料检验的流程非常重要,它直接关系到产品的质量和客户的满意度。
下面是一个关于来料检验流程的示意图。
来料检验流程图1. 接收原材料:第一步是接收原材料,原材料进入检验区域,同时记录原材料的来源、批次和数量等信息。
在接收过程中,也要注意检查原材料的外观是否符合要求,有无破损、变形或其他异常情况。
2. 抽样检验:接下来进行抽样检验,从原材料中随机抽取一定数量的样品,通常使用抽样计划确定抽样数量,以及抽样方案。
抽样检验的目的是通过样品来评估整批原材料的质量指标。
3. 物理性能测试:对原材料进行物理性能测试,例如强度、硬度、耐磨性等。
这些测试可以通过机械试验仪器进行,测试结果可以直接反映原材料的物性。
4. 化学成分分析:对原材料进行化学成分分析,以确定其化学成分是否符合要求。
这通常会涉及到化学试剂和仪器设备,例如光谱仪、质谱仪等。
5. 尺寸测量:对原材料的尺寸进行测量,以评估其尺寸是否符合要求。
这通常会使用量具和测量设备进行,例如卡尺、显微镜等。
6. 表面质量检查:对原材料的表面质量进行检查,以确定其表面是否有瑕疵、缺陷和污染等。
这可以通过人眼观察或显微镜检查来完成。
7. 判定合格与否:根据检验结果,对原材料进行判定,判断其是否合格。
如果原材料不合格,可以选择退货,或者进行再加工处理。
8. 记录与报告:对来料检验的结果进行记录和报告,包括原材料的检验日期、检验结果、不合格品的处理结果等信息。
这些记录和报告可以用于后续的追溯和问题处理。
9. 存储与转运:合格的原材料可以进行存储和转运,确保其在后续生产过程中的质量不受影响。
存储和转运要注意防潮、防尘、防震和防污染等。
10. 不合格品处理:对于不合格的原材料,根据不同情况采取相应的处理措施。
可以选择退货、返工、报废等方式进行处理。
以上就是来料检验的流程图,通过严格的检验流程,可以保证原材料的质量,提高产品的合格率和客户满意度。
来料检验控制流程图(精)
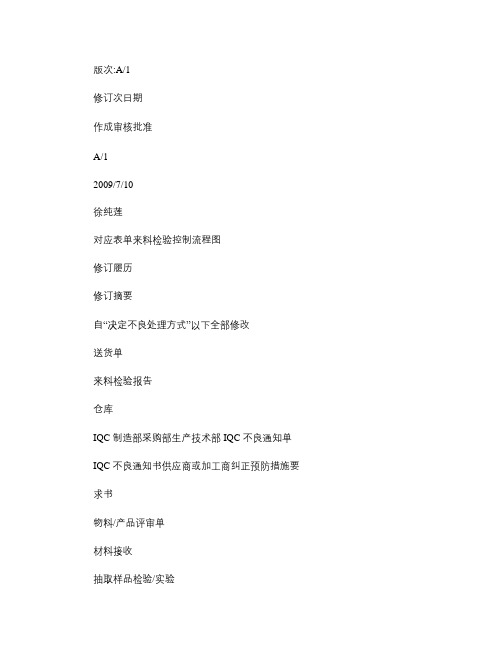
移至不良品存放区
决定不良处理方式(评审组
退货供方申请特采
要求供方反馈纠正预防
挑选GO
NG
进待检区入库特采处理
不合格标识
结案
GO NG
判定
GONG版次:A/1修订次日期作成审核批准
A/1
2009/7/10
徐纯莲
对应表单来料检验控制流程图
修订履历
修订摘要
自“决定不良处理方式”以下全部修改
送货单
来料检验报告
仓库
IQC制造部采购部生产技术部IQC不良通知单
IQC不良通知书供应商或加工商纠正预防措施要
求书
物料/产品评审单
材料接收
抽取样品检验/实验
品管判定技术判定
- 1、下载文档前请自行甄别文档内容的完整性,平台不提供额外的编辑、内容补充、找答案等附加服务。
- 2、"仅部分预览"的文档,不可在线预览部分如存在完整性等问题,可反馈申请退款(可完整预览的文档不适用该条件!)。
- 3、如文档侵犯您的权益,请联系客服反馈,我们会尽快为您处理(人工客服工作时间:9:00-18:30)。
来料检验作业流程
来料检验作业流程管理办法1.0目的
确保进料品质、数量、重量及规格等符合本公司要求,提升原材料供货商和外发供应商的品质,特制定本程序。
2.0适用围
凡对进厂的生产物料、辅料检验作业均适用。
3.0职责
3.1仓务中心:负责外协、外购件的来料送检,不合格品的隔离及数量点收;
3.2采购中心:负责不合格外购物料处置、组织外购分供方进行质量沟通并协助品保中心
外购供方改进行动监督、检查;
3.3品保中心IQC:负责外协\外购件的检验及检验标识;
品质检验及查证;
材质检验及查证。
3.4品保中心主管:负责组织进行外购、外协件的不合格品报告的评审及外观不合格的最定;
3.5研发中心:负责参与外购、外协件的不合格评审及尺寸不合格的最终判定;
3.6 PMC、采购中心、品保中心等单位必要时参与对不合格品的评审及所属围不合格品的处
4.0定义:无
5.0 容
5.1作业流程
5.1.1仓管员收到供方送货员的《送货单》后,仔细核对《送货单》与《采购订单》/
《采购申请单》容是否一致,如无误,则进行收货工作。
5.1.2仓管员核对《采购订单》、《送货单》与产品相符后将物料放入“待检区”或挂
待检牌,在收货30分钟由仓管员开出《来料检验通知单》,送品保中心文员处
报检,并指明物料所在位置,由品保中心文员交相关检验员进行检验作业;
5.1.3 品质员收单24小时按检验标准确定待检物料的检验方案准备好相关的资料(如
《检验规》、《工程图纸》、实物样品、出货检验证明、材质证明)、检验用具(量
具、仪器)等,并依“抽样计划”抽取检验样品,针对检验样本依各项材料检
验标准或图纸或比对样品或以实际装配进行检验,并将检验结果填写在《来料
检验报告》呈单位主管核准,特急用物料于接到《来料检验通知单》后立即开
始检验。
5.1.4 送检物料若判定合格,则进料检验员(IQC)在《来料检验通知单》上写明,品
保主管审批后,由品保中心文员复印此报告给仓务中心和采购中心,仓务中心凭
此报告入仓。
5.1.5当来料检验不合格时,进料检验员在该不合格料外包装上贴红色“不合格”标
签,并在1小时开出《来料检验报告》,如来料体积不大随单附上不合格实样,交品保经理核准(或其代理人品保主管核准)。
若最后判定不合格,由品保文员
复印此单交仓管员与采购中心经理签收,仓管人员依判定结果执行退货作业。
5.1.6 所有原材料、外加工品及外购产品,均须复印《来料检验报告》给仓务中心和
采购中心签收,塑料原材料须做试料报告。
5.1.7 按《来料检验报告》与品质员标识,仓管员将合格品送入仓,将不合格品置于
待处理区。
5.1.8 品质员将《来料检验报告》交品保主管处理,品保主管收单24小时核工作,
并负责统计周、月进料品质状况。
5.1.9 品保主管负责于判定送检进料不合格30分钟启动《不合格品处理流程》处理
不合格品并获得处置结果,特急用物料半小时完成。
5.1.10 接到品保中心的《来料检验报告》后,如是急用物料则由品保经理牵头,组
织采购、生产经理等组成评审小组,各部门经理对该物料能否生产使用在30分
钟作出判定意见。
确定让步放行物料的《来料检验报告》由品保中心在15分
钟回复制造中心(特殊情况可由其授权人签批或请示)。
同意特采的由品保中
心经理据《来料检验报告》明确物料标识状态后交仓管员,仓管员接《来料检
验报告》即办理物料进仓手续,在《送货单》上注明“特采”字样,品质员负
责检查特采物料的《送货单》上有否注明“特采”字样。
经判定可加工挑选使
用的物料则在《来料检验报告》上明确加工挑选部门及完成时间。
品保中心将
评审结果以书面形式向总经理呈报,如需要本厂人员安排进行加工挑选的物
料,品保中心评估预算金额超过5000元的须事先向总经理汇报,经允许后方
可进行加工挑选安排。
5.1.11仓管员依据实际进仓数量与品种,开具《进仓单》,交品质员会签后,将实物
入仓。
5.1.12仓管员在物料入仓归位时立即完成卡帐的记录,当天完成台帐的登录工作。
5.1.13仓管员于次日将相关单据交到相应部门,品保主管及时对每批材料进行统计,
统计供应商材料合格率制成《供应商评估汇总表》,交品保中心经理核准并备
存。
5.2违规处罚
5.2.1仓管员、品质员未及时处理(送检、检验、标识、隔离等)待检物料的,处罚责
任人5元/单,因此造成停工待料、返工等,处罚10-50元/单。
5.2.2 品质员检验完成后1小时未填写《来料检验报告》,处罚相应责任人10-50元
/单。
5.2.3 品质员由开始检验至检验完成期间离开检验现场,未作合格或不合格或检验中
标识的,处罚质检员10元/单。
5.2.4品保主管未按规定时间完成审核,处罚10-50元/单。
5.2.5未遵守作业流程的规定而被举报稽查属实的,一经查实给予当事责任人处罚50
元/单,给予举报人奖励50元/单。
5.3流程关键控制点:
5.3.1收料到送检,仓管员只能在15分钟完成;
5.3.2品质员在仓管员报检后,24小时必须参加检验,正常情况下1小时完成检验与
报告(特殊试验按技术规延时);
5.3.3物料不合格时,品质员必须1小时完成检验与报告,品保主管24小时完成审批;
5.3.4紧急物料品质主管15分钟启动《不合格品处理流程》,其他情况30分钟起动;
6.0相关文件
6.1各种来料检验规、标准
6.2 《不合格品处理流程》
7.0相应表单
7.1《送货单》
7.2《采购订单》
7.3《采购申请单》
7.4《供应商评估汇总表》
7.5《来料检验报告》
7.6《进仓单》
7.7《来料检验通知单》。