铜冶炼厂的危险因素辨识与控制
浅谈铜冶炼企业风险控制点

浅谈铜冶炼企业风险控制点铜是一种重要的金属,广泛应用于建筑、制造和电子等领域。
随着中国经济的快速发展,铜冶炼产业也得到了快速发展。
然而,铜冶炼企业风险也随之而来。
本文将分析铜冶炼企业的风险因素,并提出相应的风险控制点。
首先,铜冶炼企业的运营风险包括市场风险、资金风险和工艺风险。
市场风险是指铜价波动和需求变化导致的销售额下降和存货压力;资金风险是指铜冶炼企业的资金短缺或资金成本上升导致的财务风险;工艺风险是指铜冶炼企业生产过程中因工艺不符合要求、设备维修不及时等原因导致的生产中断和产品质量下降。
市场风险主要由以下因素导致:一是国内外铜供需情况的变化,如铜价格波动、需求萎缩,在铜加工行业可能导致企业市场占有率下降。
其中,铜价波动的影响最为显著,一些企业会出现高价库存和低价销售的情况。
因此,铜冶炼企业需通过建立稳健的采购和销售预测机制、产品质量稳定性控制、多元化销售策略等方式降低市场风险。
资金风险主要由以下因素导致:一是铜冶炼企业资金周转不灵、信用评级下降,导致融资难、融资成本上升;二是外部经济环境和宏观政策的不稳定性,如通货膨胀、利率变化等。
因此,铜冶炼企业应该建立稳定的财务体系,加强内部控制和审计监管,提高信用评级和融资渠道多样化。
工艺风险主要由以下因素导致:一是设备的操作维护不当,导致处理能力下降和产品质量下降;二是工艺设计不合理,导致生产效率降低,生产成本上升。
因此,铜冶炼企业应该采用最新的先进技术,对设备进行定期检查和维护,建立完善的质量控制体系并严格按照操作规程进行生产。
其次,铜冶炼企业的法律风险主要包括税务风险和合规风险。
税务风险是指因税务政策改变、错报税款等原因导致的财务风险。
合规风险是指铜冶炼企业在生产经营过程中未遵循相关法规和章程,导致责任追究和法律诉讼。
因此,铜冶炼企业应加强税务风险管理,保证报税准确性和及时性,建立制度规范合规风险,严格执行公司规章制度,加强内部控制、法律顾问服务。
浅谈铜冶炼企业风险控制点
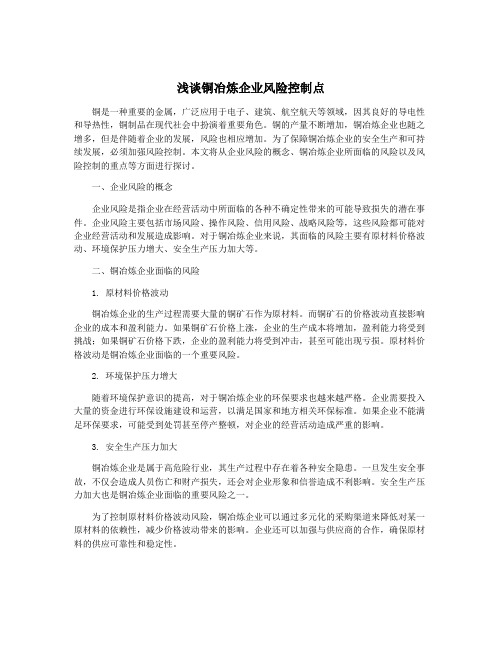
浅谈铜冶炼企业风险控制点铜是一种重要的金属,广泛应用于电子、建筑、航空航天等领域,因其良好的导电性和导热性,铜制品在现代社会中扮演着重要角色。
铜的产量不断增加,铜冶炼企业也随之增多,但是伴随着企业的发展,风险也相应增加。
为了保障铜冶炼企业的安全生产和可持续发展,必须加强风险控制。
本文将从企业风险的概念、铜冶炼企业所面临的风险以及风险控制的重点等方面进行探讨。
一、企业风险的概念企业风险是指企业在经营活动中所面临的各种不确定性带来的可能导致损失的潜在事件。
企业风险主要包括市场风险、操作风险、信用风险、战略风险等,这些风险都可能对企业经营活动和发展造成影响。
对于铜冶炼企业来说,其面临的风险主要有原材料价格波动、环境保护压力增大、安全生产压力加大等。
二、铜冶炼企业面临的风险1. 原材料价格波动铜冶炼企业的生产过程需要大量的铜矿石作为原材料。
而铜矿石的价格波动直接影响企业的成本和盈利能力。
如果铜矿石价格上涨,企业的生产成本将增加,盈利能力将受到挑战;如果铜矿石价格下跌,企业的盈利能力将受到冲击,甚至可能出现亏损。
原材料价格波动是铜冶炼企业面临的一个重要风险。
2. 环境保护压力增大随着环境保护意识的提高,对于铜冶炼企业的环保要求也越来越严格。
企业需要投入大量的资金进行环保设施建设和运营,以满足国家和地方相关环保标准。
如果企业不能满足环保要求,可能受到处罚甚至停产整顿,对企业的经营活动造成严重的影响。
3. 安全生产压力加大铜冶炼企业是属于高危险行业,其生产过程中存在着各种安全隐患。
一旦发生安全事故,不仅会造成人员伤亡和财产损失,还会对企业形象和信誉造成不利影响。
安全生产压力加大也是铜冶炼企业面临的重要风险之一。
为了控制原材料价格波动风险,铜冶炼企业可以通过多元化的采购渠道来降低对某一原材料的依赖性,减少价格波动带来的影响。
企业还可以加强与供应商的合作,确保原材料的供应可靠性和稳定性。
为了应对环境保护压力增大带来的风险,铜冶炼企业必须加强环保设施建设和运营管理,确保企业的生产活动符合相关环保标准。
铜冶炼厂的危险因素辨识与控制
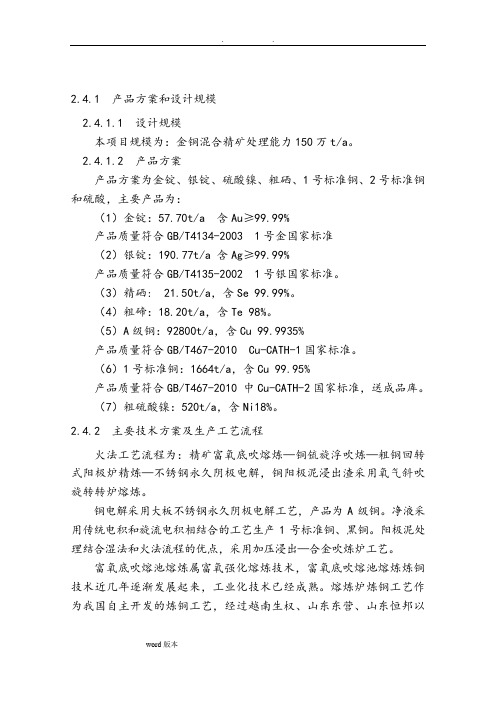
2.4.1 产品方案和设计规模2.4.1.1 设计规模本项目规模为:金铜混合精矿处理能力150万t/a。
2.4.1.2 产品方案产品方案为金锭、银锭、硫酸镍、粗硒、1号标准铜、2号标准铜和硫酸,主要产品为:(1)金锭:57.70t/a 含Au≥99.99%产品质量符合GB/T4134-2003 1号金国家标准(2)银锭:190.77t/a 含Ag≥99.99%产品质量符合GB/T4135-2002 1号银国家标准。
(3)精硒: 21.50t/a,含Se 99.99%。
(4)粗碲:18.20t/a,含Te 98%。
(5)A级铜:92800t/a,含Cu 99.9935%产品质量符合GB/T467-2010 Cu-CATH-1国家标准。
(6)1号标准铜:1664t/a,含Cu 99.95%产品质量符合GB/T467-2010 中Cu-CATH-2国家标准,送成品库。
(7)粗硫酸镍:520t/a,含Ni18%。
2.4.2 主要技术方案及生产工艺流程火法工艺流程为:精矿富氧底吹熔炼—铜锍旋浮吹炼—粗铜回转式阳极炉精炼—不锈钢永久阴极电解,铜阳极泥浸出渣采用氧气斜吹旋转转炉熔炼。
铜电解采用大板不锈钢永久阴极电解工艺,产品为A级铜。
净液采用传统电积和旋流电积相结合的工艺生产1号标准铜、黑铜。
阳极泥处理结合湿法和火法流程的优点,采用加压浸出—合金吹炼炉工艺。
富氧底吹熔池熔炼属富氧强化熔炼技术,富氧底吹熔池熔炼炼铜技术近几年逐渐发展起来,工业化技术已经成熟。
熔炼炉炼铜工艺作为我国自主开发的炼铜工艺,经过越南生权、山东东营、山东恒邦以及包头华鼎等项目的工业化应用后,已经得到了较大的发展,现已成为世界上先进的炼铜工艺之一,成为我国淘汰落后工艺进行技术改造升级采用的首选工艺,能够保证生产过程中的安全、稳定运行。
各主要车间或生产系统工艺流程如下:2.4.2.1 火法冶炼工艺流程(1)原料卸矿、储存及配料火车运输和汽车运输的袋装复杂金精矿和铜精矿在卸矿站采用吊车卸车并拆袋,火车运输的散装精矿也在卸矿站采用卸料设备卸料。
火法炼铜工艺过程中的危险、有害因素辨识与分析

火法炼铜工艺过程中的危险、有害因素辨识与分析火法冶炼铜工艺为:混合精矿配料经富氧底吹炉熔炼,形成铜锍,铜锍在P-S转炉吹炼中经造渣去除杂质,形成粗铜,再经回转式阳极炉去除粗铜中的硫、铁、铅、铋、锑和砷等杂质,以满足电解精炼对阳极化学成分和物理规格的要求。
火法冶炼铜工艺过程中需要用到熔炼炉、转炉、阳极炉、空压机、起重机、鼓风机、浇铸机等设备,以及冶炼过程的燃料、压缩氧、压缩空气等物料。
因此在火法炼铜过程存在的危险、有害因素主要包括:为火灾、爆炸、中毒窒息、坍塌、灼烫、触电(含雷击)、机械伤害、高处坠落、起重伤害、物体打击、车辆伤害、容器爆炸、淹溺、噪声伤害、振动伤害和粉尘伤害等。
(1)火灾爆炸①冶金炉底吹熔炼炉、转炉等冶金炉设冷却水套,若出现水套内缺水,易损坏水套,威胁到炉子的安全;当发生水套大量漏水,冷却水遇到炉内高温熔体,或者冷却水在炉内受高温形成蒸汽,造成炉内压力升高,严重时将造成炉子的爆炸。
放料口发生跑炉时,高温熔体大量流出,遇潮湿或水也有发生爆炸的危险。
铜锍遇潮或水份后,会发生化学反应:Cu2S+H2O=2Cu+H2+SO2FeS+H2O =FeO+H2S反应生成的H2、H2S气体与O2作用激烈,从而引起爆炸,在操作中要特别注意。
另外,冶炼常见事故还有喷炉、死炉和炉体烧穿事故,这些事故也有引起火灾爆炸的危险性。
因此,在生产中要控制好铜铳和渣层高度、炉温、配料和渣型,严格按规程作业,避免事故发生。
②电气火灾带电、用电设备,存在发生电气火灾事故的危害。
③天然气输送管道使用天然气作为燃料时,天然气是火灾和爆炸危险性较大的混合气体,其密度比空气小,如果出现泄漏则能无限制地扩散,易与空气形成爆炸性混合物,而且能顺风飘动,形成着火爆炸和蔓延扩散的重要条件,遇明火回燃。
④氧气管网在氧气的制取、储存及输送的过程中,氧在设备、管道内运行或因设备损坏而泄漏,形成火灾爆炸危险环境,氧气管道未脱脂,遇油污等易燃物有导致火灾、爆炸的危险。
浅谈铜冶炼企业风险控制点
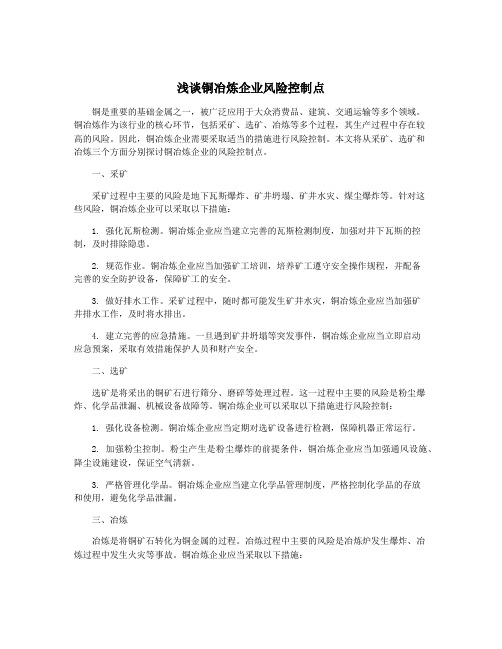
浅谈铜冶炼企业风险控制点铜是重要的基础金属之一,被广泛应用于大众消费品、建筑、交通运输等多个领域。
铜冶炼作为该行业的核心环节,包括采矿、选矿、冶炼等多个过程,其生产过程中存在较高的风险。
因此,铜冶炼企业需要采取适当的措施进行风险控制。
本文将从采矿、选矿和冶炼三个方面分别探讨铜冶炼企业的风险控制点。
一、采矿采矿过程中主要的风险是地下瓦斯爆炸、矿井坍塌、矿井水灾、煤尘爆炸等。
针对这些风险,铜冶炼企业可以采取以下措施:1. 强化瓦斯检测。
铜冶炼企业应当建立完善的瓦斯检测制度,加强对井下瓦斯的控制,及时排除隐患。
2. 规范作业。
铜冶炼企业应当加强矿工培训,培养矿工遵守安全操作规程,并配备完善的安全防护设备,保障矿工的安全。
3. 做好排水工作。
采矿过程中,随时都可能发生矿井水灾,铜冶炼企业应当加强矿井排水工作,及时将水排出。
4. 建立完善的应急措施。
一旦遇到矿井坍塌等突发事件,铜冶炼企业应当立即启动应急预案,采取有效措施保护人员和财产安全。
二、选矿选矿是将采出的铜矿石进行筛分、磨碎等处理过程。
这一过程中主要的风险是粉尘爆炸、化学品泄漏、机械设备故障等。
铜冶炼企业可以采取以下措施进行风险控制:1. 强化设备检测。
铜冶炼企业应当定期对选矿设备进行检测,保障机器正常运行。
2. 加强粉尘控制。
粉尘产生是粉尘爆炸的前提条件,铜冶炼企业应当加强通风设施、降尘设施建设,保证空气清新。
3. 严格管理化学品。
铜冶炼企业应当建立化学品管理制度,严格控制化学品的存放和使用,避免化学品泄漏。
三、冶炼冶炼是将铜矿石转化为铜金属的过程。
冶炼过程中主要的风险是冶炼炉发生爆炸、冶炼过程中发生火灾等事故。
铜冶炼企业应当采取以下措施:3. 建立完善的灭火系统。
冶炼过程中,铜冶炼企业应当建立完善的灭火系统,及时扑灭发生的火灾。
4. 加强员工培训。
铜冶炼企业应当通过安全教育培训等手段,培养员工的安全意识,提高员工的安全素养。
综上所述,铜冶炼企业在采矿、选矿和冶炼过程中,存在一定的风险。
冶金有色行业较大危险因素辨识与防范

冶金有色行业较大危险因素辨识与防范冶金有色行业作为我国的重点行业之一,是我国经济的支柱产业。
然而,冶金有色行业生产过程中存在较多的危险因素,如火灾、爆炸、中毒、高温、高压、高空、机械伤害等。
这些危险因素如果没有得到有效的防范和控制,极可能会对员工的安全和健康造成严重的威胁,同时也会造成生产安全事故,给企业带来不可估量的损失。
因此,正确辨识冶金有色行业较大的危险因素,并采取有效的预防和控制措施,是保障企业生产安全的关键。
一、冶金有色行业较大的危险因素1. 火灾和爆炸火灾和爆炸是冶金有色行业的重要危险因素之一。
这些安全隐患通常与生产过程中的电气、机械和化学反应等有关。
特别是化学反应,如果控制不好,会引发生产装置内的爆炸。
此外,冶金有色行业中,金属、硫、油等易燃易爆物质存储和使用也容易引发火灾和爆炸。
2. 中毒中毒是指在工作场所吸入、进食、皮肤接触或其他方式接触,从而引起身体健康受到损害的现象。
冶金有色行业中,常见的有毒物质包括有害气体、重金属和化学药剂等。
这些毒物对人体的危害严重,如长期接触重金属会引发中毒或肝肾功能衰竭等病状。
3. 高温、高压和高空在冶金有色行业中,很多作业需要高温、高压和高空条件,例如,高温下的热处理、高压下的压力容器制造、在高空进行的基建和装修工程等。
这些作业一旦出现失误,会直接对员工的身体安全造成威胁。
4. 机械伤害机械伤害是冶金有色行业中常见的事故形式之一。
例如,操作不当或机械故障可能会导致机器的零部件脱落或是破损,从而伤害员工。
此外,由振动或噪音等因素引起的职业病也会对员工的健康产生不良影响。
二、冶金有色行业危险因素的防范与控制1. 火灾和爆炸的防范火灾和爆炸是冶金有色行业的重要危险因素之一,为了防范火灾和爆炸,应从以下几个方面入手:1.加强安全教育和培训,提高员工的安全意识;2.检查电气设备和系统,确保其符合安全标准;3.建立及时的通信和报警机制,保证在发生事故时能够及时得到救援和控制;4.加强监督和管理,建立完整的防火、防爆管理体系,及时发现和消除安全隐患。
浅谈铜冶炼企业风险控制点

浅谈铜冶炼企业风险控制点铜是一种重要的金属材料,被广泛应用于电力、电子、通信、建筑等领域。
而铜的冶炼企业在生产过程中面临着各种风险,如原材料价格波动、环境污染、安全生产等问题。
铜冶炼企业需要对这些风险进行有效的控制。
本文将从原材料采购、生产过程、市场销售等方面,探讨铜冶炼企业的风险控制点。
一、原材料采购铜冶炼企业的生产活动离不开原材料的供应,主要的原材料包括铜矿石、硫酸、煤炭等。
原材料价格的波动对企业的成本和利润有着直接的影响。
对原材料采购的风险控制显得尤为重要。
1. 多样化采购渠道铜冶炼企业应当建立多样化的原材料采购渠道,包括直接从矿山或矿业公司采购、通过期货市场等多种方式。
这样一来,企业可以根据市场价格的波动,选择最有利的采购渠道,降低原材料采购成本。
2. 控制原材料库存企业应当建立合理的原材料库存机制,避免过多库存导致资金占用和资产负债率上升,也避免库存不足导致生产中断。
要加强对原材料市场的监控,及时了解市场价格的动向,合理制定采购计划,避免原材料价格波动对企业造成实质性的损失。
二、生产过程铜冶炼企业的生产过程涉及到熔炼、炼铜、铜材加工等环节,存在着多种风险,如安全生产、环境污染等问题。
对生产过程中的风险进行有效的控制非常重要。
1. 安全生产管理企业要加强对生产过程的安全管理,建立健全的安全管理制度和规范操作流程。
引入先进的生产设备和技术,加强对员工的安全培训,提高员工的安全意识和应急处置能力。
要加强对生产设备和生产过程的监控,及时发现并排除隐患,确保生产过程的安全稳定。
2. 环境保护铜冶炼企业在生产过程中会产生大量的废气、废水和固体废物,对环境造成影响。
企业要严格执行国家环保法规,加强污染治理和治理设施的维护,减少环境污染的产生。
可以引入节能环保技术,提高资源利用率,降低环境污染物排放。
三、市场销售铜冶炼企业的产品主要销售给电力、电子、通信、建筑等行业,受到宏观经济形势和行业发展的影响。
浅谈铜冶炼企业风险控制点

浅谈铜冶炼企业风险控制点1.合规风险:铜冶炼企业需要严格遵守国家和地方的环境、安全和劳动法规,确保企业的经营活动符合相关的法律法规要求。
该风险控制点包括建立完善的合规管理制度和流程、定期进行合规性审核和检查等。
2.环境污染风险:铜冶炼企业的生产过程中会产生大量的废水、废气和固体废物,其中包含有毒有害物质。
为控制环境污染风险,企业需要建立严格的环境管理系统,包括废水、废气、固体废物的处理设施和流程,以及定期排放监测和环境保护投入。
3.安全事故风险:铜冶炼企业存在着火灾、爆炸、中毒等安全事故的风险。
为了有效控制安全事故风险,企业需要建立健全的安全管理体系,包括安全生产规章制度、事故应急预案和培训、设备安全保障等。
4.原材料价格波动风险:铜冶炼企业所需的原材料(如铜矿石、煤炭、电力等)价格波动可能对企业的盈利能力产生重要影响。
为控制该风险,企业需要开展市场调研,建立供应商和客户关系,以及制定合理的原材料采购策略。
5.财务风险:铜冶炼企业面临着资金风险、信用风险、汇率风险等财务风险。
为了控制这些风险,企业需要建立健全的财务管理体系,包括预算管理、成本控制、资金管理和风险评估等。
6.供应链风险:铜冶炼企业需要与多家供应商和客户进行合作,故面临着供应链风险。
为了有效控制供应链风险,企业需要建立供应商评估和管理机制,确保供应商的稳定性和可靠性。
企业还需要建立合理的库存管理和供应链协同机制,以应对市场需求的变化。
7.人力资源风险:铜冶炼企业人力资源的稳定和素质对企业的生产经营至关重要。
为了控制人力资源风险,企业需要建立完善的人力资源管理制度,包括招聘、培训、激励和绩效评估等。
企业还需关注员工的职业健康和安全问题,确保员工的身体和心理健康。
铜冶炼企业需要从多个方面进行风险控制,包括合规风险、环境污染风险、安全事故风险、原材料价格波动风险、财务风险、供应链风险和人力资源风险等。
企业需要建立相应的管理制度和流程,以及加强预防措施和反应能力,从而有效应对各种可能的风险。
浅谈铜冶炼企业风险控制点
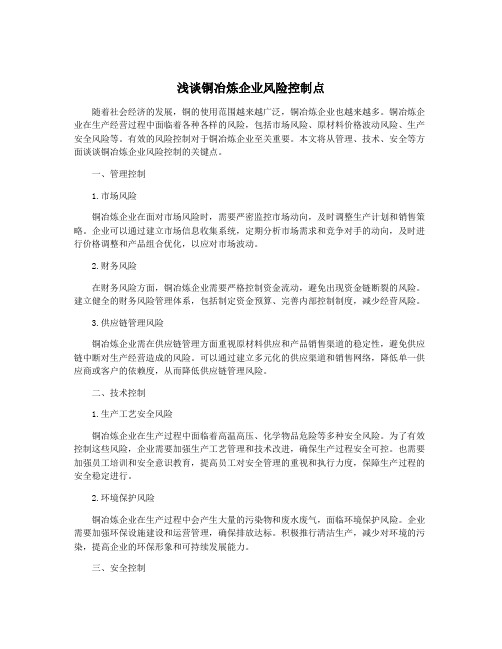
浅谈铜冶炼企业风险控制点随着社会经济的发展,铜的使用范围越来越广泛,铜冶炼企业也越来越多。
铜冶炼企业在生产经营过程中面临着各种各样的风险,包括市场风险、原材料价格波动风险、生产安全风险等。
有效的风险控制对于铜冶炼企业至关重要。
本文将从管理、技术、安全等方面谈谈铜冶炼企业风险控制的关键点。
一、管理控制1.市场风险铜冶炼企业在面对市场风险时,需要严密监控市场动向,及时调整生产计划和销售策略。
企业可以通过建立市场信息收集系统,定期分析市场需求和竞争对手的动向,及时进行价格调整和产品组合优化,以应对市场波动。
2.财务风险在财务风险方面,铜冶炼企业需要严格控制资金流动,避免出现资金链断裂的风险。
建立健全的财务风险管理体系,包括制定资金预算、完善内部控制制度,减少经营风险。
3.供应链管理风险铜冶炼企业需在供应链管理方面重视原材料供应和产品销售渠道的稳定性,避免供应链中断对生产经营造成的风险。
可以通过建立多元化的供应渠道和销售网络,降低单一供应商或客户的依赖度,从而降低供应链管理风险。
二、技术控制1.生产工艺安全风险铜冶炼企业在生产过程中面临着高温高压、化学物品危险等多种安全风险。
为了有效控制这些风险,企业需要加强生产工艺管理和技术改进,确保生产过程安全可控。
也需要加强员工培训和安全意识教育,提高员工对安全管理的重视和执行力度,保障生产过程的安全稳定进行。
2.环境保护风险铜冶炼企业在生产过程中会产生大量的污染物和废水废气,面临环境保护风险。
企业需要加强环保设施建设和运营管理,确保排放达标。
积极推行清洁生产,减少对环境的污染,提高企业的环保形象和可持续发展能力。
三、安全控制1.安全管理风险安全管理是铜冶炼企业风险控制的重中之重,需要建立完善的安全管理体系,包括安全生产责任制、安全生产标准化管理等。
企业需要加强对生产场所、设备、工艺和作业流程的监控和管理,确保生产过程的安全可控。
2.灾害事故风险灾害事故是铜冶炼企业的重大安全风险,企业需要加强对自然灾害和人为事故的预防和应急处置能力,建立健全的安全防护设施和救援预案,确保一旦发生灾害事故,能够及时、有效地进行应急处置,降低事故损失。
研究火法铜冶炼企业的安全

研究火法铜冶炼企业的安全一、铜冶炼企业不安全因素分析1.易燃易爆气体。
铜冶炼不仅需要使用大量的天然气、燃油和煤,为了化学反应的顺利进行,大量使用纯氧或富氧空气,控制不当,极易发生火灾和爆炸事故。
2.有害有毒物质。
铜冶炼过程会产生高浓度的SO2和SO3气体,还会有剧毒的HS、HAS气体产生;含砷高的白烟尘、铜砷滤饼、黑铜泥等,对环境和人身均有伤害。
3.噪音。
铜冶炼企业需要使用空压机、风机等大功率设备,噪音控制是必须面对的难题。
而且工作人员长期接触工业噪音可引起耳鸣、耳背、头晕、失眠等症状,并可引起暂时性听阀移位、永久性听阀移位直至噪声性耳聋等症状。
4.高空作业。
铜冶炼企业都建有超过100m的排气烟囱,部分企业的厂房高度也超过80m,大量的管道架设在高空,为了维持正常的生产,高空作业是难免的。
若未设臵扶梯、防护栏杆或扶梯、防护栏杆不符合规定要求;扶梯踏板和操作平台未采取有效的防滑措施;高处作业操作人员未采取相应的安全防护措施以及违章作业都可能发生高处坠落事故。
二、安全生产实践与探索1.坚持开展安全生产教育培训。
坚持安全教育培训制度,组织开展安全管理人员的专业知识培训和特种作业人员的培训,以及全员的标准化操作培训,组织新员工的“三级”安全教育,考试合格后持证上岗;把员工效果与其经济进行挂钩,通过压力层层传递,使职工由被动接受安全培训变为主动进行学习,实现“要我学习”向“我要学习”转变,员工应知应会的安全技能得到了明显提高,操作日趋规范,三违现象也明显减少。
在生产过程中做到“我不伤害他人、我不被他人伤害、我不伤害自己”三不伤害。
2.加强安全监管力度。
由人力资源课、安环室等部门对各单位的员工安全活动开展情况进行检查,突出活动效果的检查考核;每周组织由职能部门、责任部门和课室关人员参加的检查小组,对基层单位干部及员工应知应会的安全知识和规程、措施的学习、掌握情况进行抽考,对不达标的个人进行处罚,同时对其责任课室主管给予考核,明确年度培训目标对安全有关的人员进行了技能、能力、素质分析,选择有能力的人从事安全管理工作合理分配,要对企业每一位员工的安全负责。
浅谈铜冶炼企业风险控制点
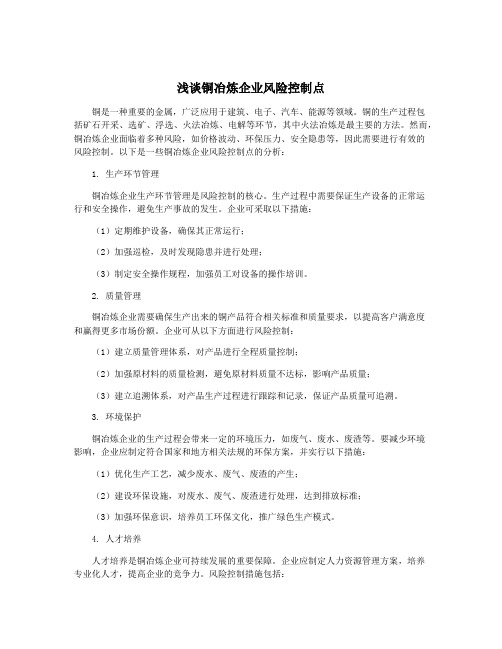
浅谈铜冶炼企业风险控制点铜是一种重要的金属,广泛应用于建筑、电子、汽车、能源等领域。
铜的生产过程包括矿石开采、选矿、浮选、火法冶炼、电解等环节,其中火法冶炼是最主要的方法。
然而,铜冶炼企业面临着多种风险,如价格波动、环保压力、安全隐患等,因此需要进行有效的风险控制。
以下是一些铜冶炼企业风险控制点的分析:1. 生产环节管理铜冶炼企业生产环节管理是风险控制的核心。
生产过程中需要保证生产设备的正常运行和安全操作,避免生产事故的发生。
企业可采取以下措施:(1)定期维护设备,确保其正常运行;(2)加强巡检,及时发现隐患并进行处理;(3)制定安全操作规程,加强员工对设备的操作培训。
2. 质量管理铜冶炼企业需要确保生产出来的铜产品符合相关标准和质量要求,以提高客户满意度和赢得更多市场份额。
企业可从以下方面进行风险控制:(1)建立质量管理体系,对产品进行全程质量控制;(2)加强原材料的质量检测,避免原材料质量不达标,影响产品质量;(3)建立追溯体系,对产品生产过程进行跟踪和记录,保证产品质量可追溯。
3. 环境保护铜冶炼企业的生产过程会带来一定的环境压力,如废气、废水、废渣等。
要减少环境影响,企业应制定符合国家和地方相关法规的环保方案,并实行以下措施:(1)优化生产工艺,减少废水、废气、废渣的产生;(2)建设环保设施,对废水、废气、废渣进行处理,达到排放标准;(3)加强环保意识,培养员工环保文化,推广绿色生产模式。
4. 人才培养人才培养是铜冶炼企业可持续发展的重要保障。
企业应制定人力资源管理方案,培养专业化人才,提高企业的竞争力。
风险控制措施包括:(1)设立培训中心,开展各类技能培训和管理培训;(2)鼓励员工技能提升和创新精神,建立奖惩机制;(3)建立合理的薪酬体系,激发员工积极性。
总之,铜冶炼企业面临着多种风险,风险管理需要从生产环节、质量管理、环境保护、人才培养等多个方面入手,加强管理,降低风险。
企业应把风险管理制度和风险意识融入到企业文化中,推动企业可持续发展。
浅谈铜冶炼企业风险控制点

浅谈铜冶炼企业风险控制点随着经济全球化的加强,中国铜冶炼企业面对着日趋复杂和严峻的经营环境和挑战。
如何在竞争激烈的市场中保持竞争优势,成为每一个企业所面临的问题。
铜冶炼企业的风险控制是一个至关重要的问题,它关系到企业的生存和发展。
本文将从铜冶炼企业的风险控制点方面出发,探讨企业如何有效的进行风险控制,从而更好地避免风险,实现企业的稳定发展。
1、原材料风险控制原材料是铜冶炼企业的核心资源,直接影响企业生产的技术水平和经营效益。
铜矿的开采难度和成本逐年升高,加之铜矿资源的储量和品位逐渐下降,原材料短缺和价格波动风险成为铜冶炼企业的主要风险。
因此,铜冶炼企业应该采取合理的原材料储备措施,寻找更多的进口品种和供应商,降低原材料的依赖程度,同时也应该建立稳定的合作关系,优化采购与供应商间的合作关系。
2、环保风险控制环境保护已成为全球性的议题,也是一个无法回避的问题。
铜冶炼企业在生产过程中对环境的污染是最为明显且直接的。
企业应该遵守国家法律法规,加强环保工作,对废气、废水、废渣和固体废弃物等进行有效的处理和排放。
此外,企业还应该加强环保技术研发和环保投入,开发新型环保技术,降低环境污染风险,避免环保事故的发生。
3、安全生产风险控制安全生产是企业发展的基础,也是企业所面临的一个重要风险。
铜冶炼企业的生产设备和生产条件相对复杂,且存在一定的安全风险。
为降低风险,企业应该建立完善的安全制度和安全管理体系,制定详细的安全操作规程,严格执行安全操作流程,对员工进行安全培训和教育,加强对生产设备、安全生产环境等方面的检查和维护。
市场风险是铜冶炼企业所必须面对的风险之一,其主要表现在市场需求波动、市场竞争激烈以及市场价格变化等方面。
企业应该遵循市场规律,建立正确的市场定位和市场营销战略,增强市场竞争力,进一步提升品质管理能力,拓展产品销售渠道,加强市场调研,提高企业的市场预判与应变能力。
以上所述的四个方面,是铜冶炼企业进行风险控制的主要措施,然而更重要的是企业应该树立正确的经营理念和价值观,全面提升企业的综合素质和经营管理能力,从而使企业在风险控制与发展之间找到平衡点,实现企业的可持续发展。
金属冶炼中的安全与风险控制

定期进行安全检查,确保设备、设施和操作符合安全标准 对员工进行安全培训,提高安全意识和技能 建立隐患排查机制,及时发现并消除安全隐患 加强应急管理,制定应急预案,提高应对突发事件的能力
火灾风险:高 温、易燃易爆 物质、电气设
备等
爆炸风险:气 体泄漏、粉尘 爆炸、压力容
器等
机械伤害风险: 化学伤害风险:
素监测等。
添加标题
《中华人民共和 国劳动法》:规 定了金属冶炼企 业劳动保护的基 本要求,包括劳 动条件、劳动时 间、劳动报酬等。
添加标题
企业必须遵守国家安全生产法 规,建立健全安全生产责任制
企业应加强安全生产管理,确 保各项安全措施得到有效执行
企业应定期进行安全检查,及 时发现和消除安全隐患
企业应加强员工安全培训,提 高员工的安全意识和应急处置 能力
法规要求:遵守国家法律法规,确保安全生产 管理体系:建立完善的安全管理体系,包括组织机构、制度、
流程等 培训教育:加强员工安全教育培训,提高安全意识和技能 风险评估:定期进行风险评估,识别和评估潜在的安全风险
应急管理:制定应急预案,提高应急处置能力 监督检查:定期进行安全检查,发现问题及时整改
安全事故:金属冶炼过程中存在各种安全隐患, 如设备故障、操作失误等,可能导致安全事故
保障员工生命安全:减少工伤事故,提高员工工作满意度 降低企业损失:减少因事故造成的经济损失,提高企业效益
提高企业形象:良好的安全记录可以提高企业声誉,吸引更多客户和合作伙伴
遵守法律法规:遵守国家法律法规,避免因安全事故受到处罚和制裁
案例四:某锌业公司通过加强与政府、行业协会的合作,共同推动行业安全与风险控制标准的制定和实施
自动化技术:提高生产效率,减少人为操作失误 智能监控系统:实时监控生产过程,及时发现安全隐患 环保技术:减少废气、废水、废渣排放,降低环境污染风险 安全防护设备:提高员工安全防护水平,降低工伤事故风险
金属冶炼危险源识别与控制

识别工艺流程中 的危险源
分析危险源的危 害程度
制定控制措施和 应急预案
危险源识别:识别金属冶炼过程中的危险源,如高温、高压、有毒气体等 数据收集:收集金属冶炼过程中危险源的相关数据,如发生频率、危害程度等 数据分析:对收集到的数据进行分析,确定危险源的等级和优先级 数据库建立:建立危险源数据库,包括危险源名称、危害程度、发生频率、控制措施等信息
收集案例:收集国 内外金属冶炼事故 案例
分析原因:分析事 故发生的原因,包 括人为因素、设备 因素、环境因素等
提出对策:针对事 故原因,提出相应 的预防和控制措施
总结教训:总结事 故教训,提高金属 冶炼安全水平
01
案例选择:选择具有代表性的金属冶炼事故案例
03
危险源识别:根据事故原因,识别出可能导致事故 的危险源
加强安全教育,提高员工安全意识 定期进行安全检查,及时发现并消除安全隐患 加强设备维护,确保设备安全运行 制定应急预案,提高应急处理能力
加强员工培训, 提高安全意识
定期进行设备 检查和维护, 确保设备安全
运行
加强现场安全 管理,确保操
作规范
建立应急响应 机制,及时处
理突发情况
建立应急预案,定期进行演练
风险评估 法:通过 风险评估, 识别潜在 的危险源
专家咨询 法:通过 专家咨询, 获取危险 源识别的 建议
事故案例 分析法: 通过分析 事故案例, 识别潜在 的危险源
安全检查 表法:通 过安全检 查表,系 统地识别 危险源
危险源辨 识软件法: 通过使用 危险源辨 识软件, 识别潜在 的危险源
确定金属冶炼工 艺流程
危险源识别:通过现 场调查、资料查阅等 方式,识别金属冶炼 过程中的危险源
金属冶炼安全危险源辨识与管理

执法依据:相关法 律法规和标准
执法流程:发现违 规行为、立案调查 、作出处罚决定、 执行处罚
监管措施:定期检 查、专项整治、约 谈、通报等
金属冶炼安全事 故调查与处理
事故报告制度
事故报告的程序和要求 事故报告的时限和内容 事故报告的审核和归档 事故报告的保密和公开
事故调查程序与方法
现场勘查:收集证据,了解 事故发生经过
培训方式:理论 授课、案例分析、 模拟演练等
培训周期:定期进 行,确保员工掌握 安全知识和技能
金属冶炼安全技 术措施
工艺控制与安全设施
工艺控制:通过优化工 艺参数、控制反应过程 等措施,降低金属冶炼 过程中的安全风险。
安全设施:配备齐全 的安全设施,如防火、 防爆、防泄漏等设备, 以保障生产安全。
金属冶炼安全危险源辨 识与管理
汇报人:
目录
添加目录标题
01
金属冶炼安全危险源 辨识
02
金属冶炼安全管理
03
金属冶炼安全技术措 施
04
金属冶炼安全监管与 执法
05
金属冶炼安全事故调 查与处理
06
添加章节标题
金属冶炼安全危 险源辨识
危险源分类
物理性危险源
化学性危险源
生物性危险源
心理生理性危险源
危险源识别方法
续有效性。
提高员工的安全 意识和应急能力, 加强安全培训和 演练,确保员工 具备应对突发事
件的能力。
安全生产责任制
添加标题
制定安全生产责任制的目的:明确各级管理人员和操作人员的安全职责, 确保安全生产的顺利进行。
添加标题
安全生产责任制的内容:包括各级管理人员和操作人员的安全生产职责、 权限和义务等方面。
浅谈铜冶炼企业风险控制点

浅谈铜冶炼企业风险控制点随着经济的发展和人们生活水平的提升,铜市场需求不断扩大,从而让铜冶炼企业面临着更多的市场风险。
为了有效控制铜冶炼企业的风险,以下从企业内外部角度分析其风险控制点。
一、内部风险控制点1. 财务风险铜冶炼企业在经营过程中,会面临着资金周转、收支不平衡、资金占用等问题,这些问题与企业的财务风险紧密相关。
企业应该根据自身实际情况,制定合理的财务管理策略,精细化管理企业预算、票据、往来账款,以降低财务风险。
2. 铜矿资源风险因为市场需求的变化和环境问题等因素影响,铜矿资源供给的不确定性,会直接影响企业的生产和经营。
企业需要进行有效的供应链管理,建立优秀的矿石采购渠道,实现对铜矿资源的风险控制。
3. 生产风险铜冶炼企业的生产过程中,仪器设备、人员安全、安全生产等风险时常存在,所以必须制定合理的生产管理策略,实行标准化作业,加强管理,落实岗位责任制。
4. 员工流失风险因为企业内部管理机制不完善或员工自身问题等原因,铜冶炼企业员工流失问题时常存在,会直接造成企业经营和生产成本的增加。
企业应该重视员工的培养和管理,为员工提供良好的工作环境和发展空间,激发员工的创造力,降低员工的流失率。
市场风险是铜冶炼企业面临的最大的风险之一,他们要时刻关注市场的变化,掌握市场最新信息并及时作出合理的决策。
企业应该根据市场的需求和动态制定合理的销售策略,建立稳定的销售渠道和供应链,确保企业的利润稳定。
铜冶炼企业在经营过程中也要面对政策风险的挑战,政策的变化和调整会直接影响到企业的经营和生产。
企业应该密切关注政府政策,了解政策的变化和影响,及时采取措施应对风险。
铜冶炼企业在环保方面的要求越来越高,企业必须加强环保意识,完善环保设施,制定合理的环保管理策略,以减少其对环境的危害,减少安全风险的发生。
总之,铜冶炼企业的风险控制是一个复杂的过程,需要从面内外部两个角度进行综合分析。
企业应该及时发现并分析风险,制定可行的应对措施,加强管理,提升自身实力,最终实现企业持续、稳定的发展。
火法炼铜工艺过程中的危险、有害因素辨识与分析
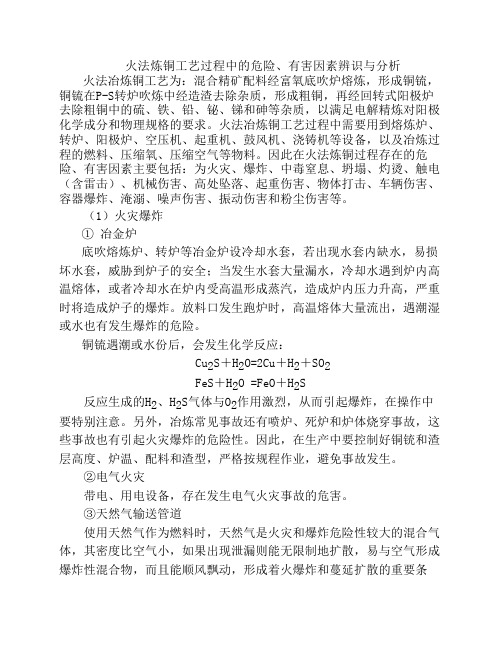
火法炼铜工艺过程中的危险、有害因素辨识与分析火法冶炼铜工艺为:混合精矿配料经富氧底吹炉熔炼,形成铜锍,铜锍在P-S转炉吹炼中经造渣去除杂质,形成粗铜,再经回转式阳极炉去除粗铜中的硫、铁、铅、铋、锑和砷等杂质,以满足电解精炼对阳极化学成分和物理规格的要求。
火法冶炼铜工艺过程中需要用到熔炼炉、转炉、阳极炉、空压机、起重机、鼓风机、浇铸机等设备,以及冶炼过程的燃料、压缩氧、压缩空气等物料。
因此在火法炼铜过程存在的危险、有害因素主要包括:为火灾、爆炸、中毒窒息、坍塌、灼烫、触电(含雷击)、机械伤害、高处坠落、起重伤害、物体打击、车辆伤害、容器爆炸、淹溺、噪声伤害、振动伤害和粉尘伤害等。
(1)火灾爆炸① 冶金炉底吹熔炼炉、转炉等冶金炉设冷却水套,若出现水套内缺水,易损坏水套,威胁到炉子的安全;当发生水套大量漏水,冷却水遇到炉内高温熔体,或者冷却水在炉内受高温形成蒸汽,造成炉内压力升高,严重时将造成炉子的爆炸。
放料口发生跑炉时,高温熔体大量流出,遇潮湿或水也有发生爆炸的危险。
铜锍遇潮或水份后,会发生化学反应:Cu2S+H2O=2Cu+H2+SO2FeS+H2O =FeO+H2S反应生成的H2、H2S气体与O2作用激烈,从而引起爆炸,在操作中要特别注意。
另外,冶炼常见事故还有喷炉、死炉和炉体烧穿事故,这些事故也有引起火灾爆炸的危险性。
因此,在生产中要控制好铜铳和渣层高度、炉温、配料和渣型,严格按规程作业,避免事故发生。
②电气火灾带电、用电设备,存在发生电气火灾事故的危害。
③天然气输送管道使用天然气作为燃料时,天然气是火灾和爆炸危险性较大的混合气体,其密度比空气小,如果出现泄漏则能无限制地扩散,易与空气形成爆炸性混合物,而且能顺风飘动,形成着火爆炸和蔓延扩散的重要条件,遇明火回燃。
④氧气管网在氧气的制取、储存及输送的过程中,氧在设备、管道内运行或因设备损坏而泄漏,形成火灾爆炸危险环境,氧气管道未脱脂,遇油污等易燃物有导致火灾、爆炸的危险。
金属冶炼作业中的危险源辨识与监控

化学品泄漏:如管道破裂、 容器破损等
化学品储存:如储存不当、 管理不善等
生物毒素:如霉菌毒素、细菌 毒素等,可能对人体健康造成 危害
微生物:如细菌、真菌、病 毒等,可能导致疾病传播
生物污染:如动物粪便、植物 残渣等,可能导致环境污染
生物危害:如动物咬伤、植物 刺伤等,可能对人体造成伤害
检查作业环境是否安全,如有隐患及时 排除
检查操作规程是否正确,如有错误及时 纠正
检查监控系统是否正常,如有故障及时 维修
做好记录,以便后续分析和改进
定期检查:对监控设备进 行定期检查,确保其正常 运行
数据分析:对监控数据进 行分析,及时发现异常情 况
改进措施:根据数据分析 结果,制定相应的改进措 施
国际合作:加强与其他国家在危险源辨识与监控方面的合作,共同应对全球性挑战 技术交流:通过国际合作,加强技术交流与共享,提高危险源辨识与监控的技术水平 标准制定:参与国际标准制定,推动危险源辨识与监控的国际化进程 培训与教育:通过国际合作,加强培训与教育,提高危险源辨识与监控的专业水平
汇报人:
制定危险源的监控和防范措施
危险源辨识:通 过观察、询问、 检查等方式,识 别出作业环境中 存在的危险源
危险源分类:根 据危险源的性质、 危害程度等进行 分类,便于管理 和控制
危险源评估:对 危险源进行风险 评估,确定其危 害程度和影响范 围
危险源监控:对 危险源进行实时 监控,及时发现 和处理异常情况, 确保作业安全
及时更新:根据实际情况及时更新应急预 案,以确保预案的有效性和实用性。
定期演练:对应急预案进行定期演练,以 提高应对危险情况的能力和效率。
培训与教育:对应急救援人员进行培训和 教育,提高其专业素质和应对危险情况的 能力。
浅谈铜冶炼企业风险控制点

浅谈铜冶炼企业风险控制点铜是一种重要的金属材料,广泛应用于建筑、电子、航空航天等领域。
铜的加工和制造需要经过铜的冶炼过程,而铜冶炼企业在生产过程中也会面临各种风险问题。
对于铜冶炼企业来说,风险控制是非常重要的。
本文将从几个方面谈谈铜冶炼企业风险控制点。
关于原材料采购的风险控制。
铜冶炼企业的生产需要大量的铜矿石,而铜矿石的质量直接影响到冶炼产品的质量。
企业需要采购优质的铜矿石,并且要与供应商建立长期稳定的合作关系。
企业还需要关注市场的变化,合理制定采购策略,避免原材料价格波动所带来的风险。
关于生产过程的风险控制。
铜冶炼企业在生产过程中会面临各种安全隐患和环境污染风险。
企业需要加强安全生产管理,建立健全的安全生产制度,提高职工安全意识,确保生产过程的安全稳定。
企业还需要加强环保管理,采取有效措施控制废气、废水、固体废物的排放,保护生态环境。
关于市场风险的控制。
铜冶炼企业的产品主要销售给建筑、电子、航空航天等行业,这些行业的需求情况会受到经济周期等因素的影响。
企业需要密切关注市场信息,灵活调整生产计划,避免市场风险带来的影响。
企业还可以通过多样化产品、拓展市场渠道等方式来分散市场风险。
关于管理风险的控制。
铜冶炼企业的管理体系对企业的发展起着关键作用。
企业需要建立健全的内部管理制度,规范企业运作,加强人才培养和管理,确保企业的稳定良性发展。
企业还可以通过建立风险管理体系,加强对各类风险的监控和应对,提高企业抵御风险的能力。
铜冶炼企业在生产经营中存在着各种风险,如原材料采购风险、生产过程风险、市场风险和管理风险等。
为了降低风险带来的损失,企业需要加强风险管理,建立完善的风险控制体系,提高企业的抗风险能力。
企业还需要注重技术创新和产品质量,提升自身核心竞争力,从根本上降低各类风险的发生概率。
希望铜冶炼企业能够认真对待风险问题,不断完善风险控制机制,确保企业的持续健康发展。
- 1、下载文档前请自行甄别文档内容的完整性,平台不提供额外的编辑、内容补充、找答案等附加服务。
- 2、"仅部分预览"的文档,不可在线预览部分如存在完整性等问题,可反馈申请退款(可完整预览的文档不适用该条件!)。
- 3、如文档侵犯您的权益,请联系客服反馈,我们会尽快为您处理(人工客服工作时间:9:00-18:30)。
2。
4.1产品方案与设计规模2.4.1、1 设计规模本项目规模为:金铜混合精矿处理能力150万t/a。
2.4.1、2 产品方案产品方案为金锭、银锭、硫酸镍、粗硒、1号标准铜、2号标准铜与硫酸,主要产品为:(1)金锭:57、70t/a 含Au≥99、99%产品质量符合GB/T4134—20031号金国家标准(2)银锭:190、77t/a 含Ag≥99、99%产品质量符合GB/T4135-20021号银国家标准。
(3)精硒:21、50t/a,含Se 99、99%。
(4)粗碲:18、20t/a,含Te98%。
(5)A级铜:92800t/a,含Cu 99、9935%产品质量符合GB/T467—2010 Cu-CATH-1国家标准。
(6)1号标准铜:1664t/a,含Cu99、95%产品质量符合GB/T467-2010中Cu-CATH-2国家标准,送成品库。
(7)粗硫酸镍:520t/a,含Ni18%。
2.4.2 主要技术方案及生产工艺流程火法工艺流程为:精矿富氧底吹熔炼—铜锍旋浮吹炼-粗铜回转式阳极炉精炼—不锈钢永久阴极电解,铜阳极泥浸出渣采用氧气斜吹旋转转炉熔炼.铜电解采用大板不锈钢永久阴极电解工艺,产品为A级铜.净液采用传统电积与旋流电积相结合得工艺生产1号标准铜、黑铜。
阳极泥处理结合湿法与火法流程得优点,采用加压浸出-合金吹炼炉工艺。
富氧底吹熔池熔炼属富氧强化熔炼技术,富氧底吹熔池熔炼炼铜技术近几年逐渐发展起来,工业化技术已经成熟.熔炼炉炼铜工艺作为我国自主开发得炼铜工艺,经过越南生权、山东东营、山东恒邦以及包头华鼎等项目得工业化应用后,已经得到了较大得发展,现已成为世界上先进得炼铜工艺之一,成为我国淘汰落后工艺进行技术改造升级采用得首选工艺,能够保证生产过程中得安全、稳定运行。
各主要车间或生产系统工艺流程如下:2.4。
2、1 火法冶炼工艺流程(1)原料卸矿、储存及配料火车运输与汽车运输得袋装复杂金精矿与铜精矿在卸矿站采用吊车卸车并拆袋,火车运输得散装精矿也在卸矿站采用卸料设备卸料。
卸矿站卸下得复杂金精矿与铜精矿经胶带输送机倒运到精矿仓及配料厂房储存.当地得复杂金精矿与铜精矿及脱砷金焙砂、渣精矿、精炼渣等物料用汽车运输到精矿仓及配料厂房储存。
精矿仓及配料厂房中复杂金精矿与铜精矿及熔剂、渣精矿得储存时间均为30天,吹炼渣等中间物料得储存时间为7天。
精矿仓及配料厂房中得各种物料分别通过抓斗桥式起重机、圆盘给料机与定量给料机倒运到熔炼上料皮带;返回得熔炼烟尘与吹炼烟尘经计量后倒运到熔炼上料皮带。
配料后得混合炉料经熔炼上料皮带运至熔炼厂房。
(2)熔炼配料后得混合炉料经熔炼上料皮带卸到熔炼炉顶中间料仓中,再经定量给料机与移动式胶带加料机连续地从炉顶加入氧气底吹熔炼炉内。
冶炼需要得氧气从熔炼炉底部得氧枪鼓入,使熔池形成剧烈搅拌,炉料在熔池中迅速完成加热、脱水、熔化、氧化、造铜锍与造渣等熔炼过程,反应产物液体铜锍与炉渣因密度得不同而在熔池内分层,铜锍经粒化、干燥与磨粉后气力输送至吹炼炉炉顶料仓。
炉渣经炉渣排放口排入渣包、通过渣包车送至渣缓冷场。
熔炼渣经冷却后送炉渣选矿车间,选出得渣精矿运至精矿仓及配料厂房返回熔炼配料,渣尾矿外售或堆存。
熔炼炉产出得烟气经余热锅炉回收余热、电收尘净化后送去制酸。
熔炼余热锅炉与电收尘收集得含铜较高得烟尘通过气体输送至精矿仓及配料厂房得烟灰接收仓,含铅、锌等杂质高得白烟尘外售.氧气底吹熔炼炉需要得压缩空气由设在空压站得高压离心压缩机提供,氧气来自于制氧站,氧枪入口处压缩空气与氧气压力0、6MPa~0、7MPa。
当底吹炉氧枪口需要转出熔体面时,在氧枪转出熔体页面后,炉内不再需要氧气与空气,这时将供氧气系统与空气系统中得放气阀打开,氧气与压缩空气排入大气,同时将供氧气与压缩空气管道上得调节阀关闭.氧气底吹熔炼炉连续加料,年工作330d,平均有效工作时间21、6h/d。
(3)铜锍磨碎由于旋浮吹炼炉铜锍喷嘴对入炉物料粒度与水分含量要求较高,对铜锍得粒度要求—325目占80%以上,含水〈0、3%,故铜锍需经粒化、磨粉及干燥后方可入炉。
熔炼产出得铜锍首先经粒化装置粒化,然后经胶带输送机倒运到铜锍仓储存。
在铜锍仓内,铜锍经计量与配料后送立式磨制粉与干燥,粉料通过布袋收尘器收集,然后用埋刮板输送机送往吹炼炉顶料仓。
磨碎过程中得热风由热风炉供给,热风炉燃料为天然气,载气经布袋除尘后直接排空。
(4)旋浮吹炼吹炼炉处理得铜锍粉、生石灰粉、石英砂与烟灰按照设定得加料速率,各自通过独立得计量系统、密闭埋刮板输送机加入到反应塔顶得铜锍喷嘴中。
富氧空气在喷嘴中与混合物料混合,并以高速喷入吹炼炉高温反应塔内,铜锍在氧得作用下,发生一系列化学反应,完成造渣与造铜过程,生成得粗铜与炉渣在沉淀池中由于比重得差异澄清分离。
粗铜经排放口、流槽直接进回转式阳极炉火法精炼,吹炼炉渣经粒化后进熔炼配料系统返熔炼炉处理。
吹炼烟气通过余热锅炉回收余热、电收尘净化后送制酸.吹炼烟气在余热锅炉与电收尘收集得烟尘,含铜较高得烟尘用气体输送至原料仓及配料厂房得烟灰接收仓或吹炼炉顶料仓,含铅、锌等杂质高得白烟尘外售。
吹炼炉年工作330d,平均有效工作时间22、8h/d.(5)阳极精炼阳极精炼炉选用2台回转式阳极炉。
阳极精炼得目得就是进一步除掉粗铜中得有害杂质,以满足电解精炼对阳极板化学成分得要求。
粗铜得精炼在回转阳极炉中进行,分加料升温、氧化、还原、浇铸等几个周期.氧化期就是通过设置在阳极炉上得氧化还原口往铜液中鼓入压缩空气,使铜液中得铁、硫、砷、锑、铋等杂质氧化进入精炼渣中被除去。
由于铜液中得杂质较少,为了使铜液中得杂质较彻底得除去,需要通入压缩空气,使铜液中得部分铜氧化,接近饱与溶解度得氧化亚铜再与铜液中得杂质反应,才能使杂质氧化造渣除去。
氧化期结束后扒出浮在铜液上部表面得精炼渣。
接着进入还原期,还原期就是通过氧化还原口鼓入还原剂将氧化期铜液中产生得氧化亚铜还原成铜.本项目采用天然气作为还原剂,采用天然气作还原剂环保比较好,利用率比较高,产出得阳极板质量好。
近年来,透气砖技术与稀氧燃烧技术在铜火法精炼得到成功应用。
透气砖技术缩短了阳极炉得作业周期,提高了阳极炉得产能,改善了铜阳极板得质量;稀氧燃烧技术提高了燃料燃烧效率,降低了燃料消耗,减少了烟气量并降低了烟气温度。
这两项新技术得使用为提高生产效率、降低成本、改善工作环境与提高电铜质量创造了有利条件。
因此,本方案在回转式阳极炉使用这两项技术.2台阳极精炼炉每天共生产2炉次,年工作330d。
(6)残极处理由于旋浮吹炼炉不能处理固体含铜炉料,故电解返回得残极、废阳极、废浇铸模等含铜高得物料需设专门得残极处理系统。
本项目选择用竖炉来处理。
竖炉以天然气为燃料,残极及废阳极在竖炉炉膛中熔化,经溜槽流入回转式保温炉内保温,然后用双圆盘定量浇铸成合格得阳极板后送电解精炼。
(7)阳极浇铸精炼后得阳极铜需定量浇铸成合格得铜阳极板,再送电解精炼。
本项目得阳极板浇铸引进一套带称重装置得双圆盘双包定量浇铸机.残极处理产生得阳极铜也用精炼配套得双圆盘双包定量浇铸机,利用阳极炉浇铸得间隙浇铸成阳极板。
(8)阳极泥处理铜阳极泥先用加压氧浸出脱除阳极泥中大部分铜、镍等杂质,浸出渣经压滤、干燥后,在氧气斜吹旋转转炉中熔炼与精炼,脱除硒、铁、锑、砷、铅、铋、镍、硒、碲、铜等杂质,产出含金银96%以上得金银合金,浇铸成一定规格得金银阳极板送银电解进一步分离金银。
阳极泥处理产生得熔炼渣与精炼渣返回底吹熔炼炉处理,吹炼渣与文丘里尘返回氧气斜吹旋转转炉处理。
2.4.2、2铜电解工艺流程(1)铜电解火法精炼产出得铜阳极板由叉车送至铜电解车间,首先在阳极整形机组上进行整形、矫耳、铣耳,然后按极距100mm排板后用电解专用吊车吊入电解槽内进行电解。
在电流密度280~320A/m2、电解液成分Cu2+:45~50g/l、H2SO4180~200g/l及电解液温度为60~65℃得条件下进行电解作业,作业周期为:阳极周期21d,阴极周期7d。
出槽时阴极经专用吊车吊至阴极剥片机组,经洗涤、剥离、堆垛、称量打包后用叉车运至成品库。
剥片后得不锈钢阴极片经排板后由吊车重新吊回电解槽.残极用吊车运至残极洗涤机组处理,经洗涤堆垛后,称量打包,再用叉车送回火法精炼车间。
电解液由循环槽经循环泵扬至板式换热器加热至~65℃后进入高位槽。
电解液由高位槽经分液包自流至各个电解槽。
电解槽供液采用下进上出,由槽两端溢流嘴溢出,电解液汇总后返回循环槽。
残阳极出槽时,上清液流入上清液贮槽,全部经净化过滤机过滤后返回循环系统;排出得阳极泥浆经管道流至阳极泥地槽(带搅拌),泵送至阳极泥中间槽,阳极泥再经泵送阳极泥处理车间进行过滤,过滤后液返回电解车间循环系统,滤渣即为阳极泥,作为阳极泥处理车间(加压浸出部分)得原料.为保证电解液得洁净度,车间配置了专用得电解液精密过滤器,循环系统每天抽取电解液循环量得30%经精密过滤器过滤后,返回循环系统。
根据电解液中铜及杂质得浓度,每天抽取部分电解液送净液车间处理,保证电解系统电解液中铜及杂质浓度不超过极限值。
铜电解厂房采用单系列循环系统与两套硅整流系统,两套硅整流能够保证电解生产过程中供电得持续性。
当一台硅整流需要检修时用另一台硅整流带动所有电解槽,避免电解槽完全断电后电解槽中阴极铜得返溶,只就是这时得电解槽内电流密度需要调低。
(2)铜电解液净化铜电解液净化主要分传统法标准电积脱铜、旋流电积脱铜除杂、生产硫酸镍三个工序。
标准电积脱铜槽配置在电解厂房内,电解液在电积槽内进行一段电积脱铜.一段脱铜槽使用不锈钢阴极与不溶阳极,脱铜过程中严格控制铜浓度从45g/L降至38g/L生产1号标准铜。
一段脱铜后液泵送至净液厂房旋流电积工段。
旋流电积共分四段,采用钛涂层作为阳极,不锈钢作为阴极。
一二段旋流电积分别控制铜浓度从38g/L到16g/L与从16g/L到6g/L,生产1号标准铜。
其中一段旋流电积电流密度700~800A/m2,二段旋流电积电流密度控制在400~500A/m2。
二段旋流电积后液送至三段旋流电积,三段旋流电积控制铜浓度从6g/L到2g/L,电流密度250~350A/m2,生产含铜99%得黑铜板。
三段旋流电积后液送至四段旋流电积,四段旋流电积控制铜浓度从2g/L到〈0.45g/L,电流密度700~850A/m2,生产含铜55%得黑铜粉,同时,溶液中得As、Sb、Bi约有85%进入黑铜粉从溶液中脱除。
四段旋流电积后液大部分返回电解车间,少部分泵送硫酸镍工序。
送硫酸镍工序得溶液经搪瓷釜浓缩、水冷结晶、冷冻结晶后生产粗硫酸镍.采用制冷得方法将溶液得温度降低至零下-20℃左右进行冷冻结晶,这样可以提高硫酸镍得结晶效率。