预拌混凝土超时缓凝现象的研究
缓凝时间延长原因分析

关于混凝土凝结时间延长问题原因分析及解决措施1.试验背景自6月1日使用调整的复合粉后,同心花苑以及长青相继出现混凝土凝结缓慢的现象,平均温度25℃以上的条件下,混凝土板面在18个小时还有脚印,另外由于凝结时间较长,混凝土早期表面强度太低导致墙面拆模时出现掉皮。
工地对此相当重视,认定为严重质量问题,耽误了施工工期。
2.试验目的(1)找出混凝土凝结时间延长的具体原因(2)解决混凝土凝结时间延长问题的方法3.原因预分析6月1号后,混凝土中主要材料变化为调整后的复合粉(简称复合粉B),另外缓凝时间的延长与减水剂有密不可分的关系。
因此初步认为混凝土缓凝时间的延长与复合粉和减水剂有一定关系。
4.试验材料4.1复合粉A(未调整的复合粉)4.2复合粉B(调整后的复合粉)4.3顶固减水剂A(未调整,缓凝较多,固含14%)4.4顶固减水剂B(调整后,1%的缓凝组分,固含12.3%)4.5源锦标准型减水剂(高浓,固含15%)4.6武新S95矿粉4.7其他材料:葛洲坝水泥、碎石、黄砂、江砂、海剑掺合料5.试验内容及配比5.1试验内容(1)对比三种减水剂对混凝土缓凝时间的影响(2)对比矿粉与复合粉A、复合粉B对混凝土凝结时间的影响(3)综合分析减水剂及复合粉对混凝土凝结时间的影响5.2混凝土配比试验采用C40标准层配合比,配合比见表1表1 混凝土配合比6.试验结果分析对以上9组配比做混凝土工作性、凝结时间以及抗压强度试验,结果见表2表2混凝土试验结果6.1减水剂对混凝土凝结时间的影响由图1可知,在使用相同复合粉条件下,不同减水剂凝结时间差异较大,凝结时间大小依次为顶固A>顶固B>源锦。
6月1号以前,混凝土使用的减水剂是顶固A,矿粉选用的是复合粉A和S95矿粉,砼凝结时间为17小时,而工地通常拆模时间14-24h,如拆模稍早就可能会出现掉皮现象,但没有发生混凝土未凝现象。
6月1号后,使用的是顶固A和复合粉B,砼凝结时间大大延长,为24h,如混凝土坍落度损失较大,到现场可能会加水或者减水剂,凝结时间还会有所延长,因此出现了混凝土1天左右才凝结的现象。
混凝土的超时缓凝现象

疏忽大意 , 有可 能将缓凝 组分添 加过量 , 送入混凝 土搅拌 站后 , 又 未采取及 时有效 的手段进行检查 , 就用于生产 , 造成 了使 用该批外 加剂 的混凝土超时缓凝。 品混凝土企业使 用的泵送 剂中, 商 缓凝组 分大 多以价格较 为低廉 的蔗糖 为主 , 的也掺 入 了葡萄糖酸钠 等。 有 这些缓凝剂化 合物分子上都具有一定数量 的羟基 ( 0H) 一 、羧基 ( 00H)它们具有较 强 的极 性 , 一C , 吸附在 水泥水 化物 的晶核 上 ,
关键 词பைடு நூலகம்: 凝 土 : 时缓 凝 混 超
Ab ta t T i a tce u ma e t e e s n h t s r c : h s r il s m nz d h r a o t a c u e h v ri ea d n fc n r t n n l z d a s d t e o e me r t r i g o o c e e a d a a y e t t e a v r ee e t ih b o g tt h o c e epe - h d e s f c c ebr u h o t e c n rt r wh
Ke y wors: o cee o e i eadn d c n rt ; v r mertr ig t
发生 , 给施工带来诸 多负面影响。 别是在 处理混凝土超时缓凝事 特
收稿 日期 : ( 6 8 2 2) — — 3 0
故 时往往 由于缺 乏经验导致较大 的损失。本文就超 时缓凝 现象 以
阻碍 了结 晶 继 续 发 展 , 阻 碍 了 水 泥 水 化 , 而 延 长 了凝 结 时 间 。 即 从
同时 , 外加剂 中的某 些减 水组分 , 木钙 、 钙、 如 糖 木钠等 , 都有缓 也
预拌混凝土异常凝结探析
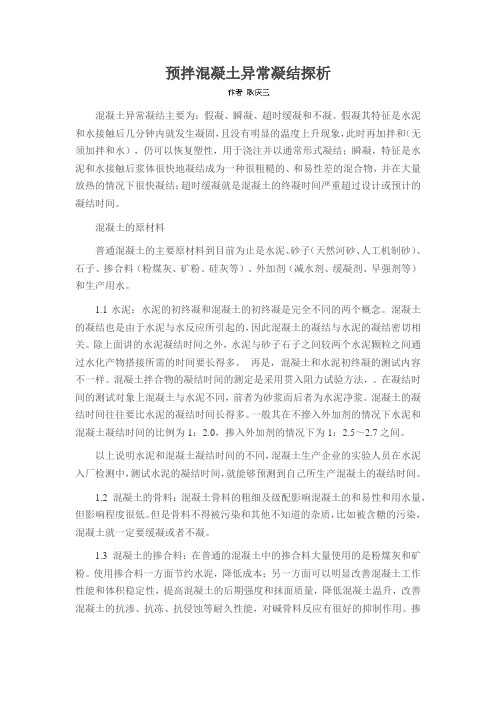
预拌混凝土异常凝结探析混凝土异常凝结主要为:假凝、瞬凝、超时缓凝和不凝。
假凝其特征是水泥和水接触后几分钟内就发生凝固,且没有明显的温度上升现象,此时再加拌和(无须加拌和水),仍可以恢复塑性,用于浇注并以通常形式凝结;瞬凝,特征是水泥和水接触后浆体很快地凝结成为一种很粗糙的、和易性差的混合物,并在大量放热的情况下很快凝结;超时缓凝就是混凝土的终凝时间严重超过设计或预计的凝结时间。
混凝土的原材料普通混凝土的主要原材料到目前为止是水泥、砂子(天然河砂、人工机制砂)、石子、掺合料(粉煤灰、矿粉、硅灰等)、外加剂(减水剂、缓凝剂、早强剂等)和生产用水。
1.1水泥:水泥的初终凝和混凝土的初终凝是完全不同的两个概念。
混凝土的凝结也是由于水泥与水反应所引起的,因此混凝土的凝结与水泥的凝结密切相关。
除上面讲的水泥凝结时间之外,水泥与砂子石子之间较两个水泥颗粒之间通过水化产物搭接所需的时间要长得多。
再是,混凝土和水泥初终凝的测试内容不一样。
混凝土拌合物的凝结时间的测定是采用贯入阻力试验方法,。
在凝结时间的测试对象上混凝土与水泥不同,前者为砂浆而后者为水泥净浆。
混凝土的凝结时间往往要比水泥的凝结时间长得多。
一般其在不摻入外加剂的情况下水泥和混凝土凝结时间的比例为1:2.0,掺入外加剂的情况下为1:2.5~2.7之间。
以上说明水泥和混凝土凝结时间的不同,混凝土生产企业的实验人员在水泥入厂检测中,测试水泥的凝结时间,就能够预测到自己所生产混凝土的凝结时间。
1.2 混凝土的骨料:混凝土骨料的粗细及级配影响混凝土的和易性和用水量,但影响程度很低。
但是骨料不得被污染和其他不知道的杂质,比如被含糖的污染,混凝土就一定要缓凝或者不凝。
1.3 混凝土的掺合料:在普通的混凝土中的掺合料大量使用的是粉煤灰和矿粉。
使用掺合料一方面节约水泥,降低成本;另一方面可以明显改善混凝土工作性能和体积稳定性,提高混凝土的后期强度和抹面质量,降低混凝土温升,改善混凝土的抗渗、抗冻、抗侵蚀等耐久性能,对碱骨料反应有很好的抑制作用。
超缓凝混凝土凝结时间

超缓凝混凝土凝结时间超缓凝混凝土是一种特殊的混凝土材料,其凝结时间相对较长。
在建筑工程中,超缓凝混凝土的凝结时间对于工程进展和施工安排具有重要意义。
本文将从超缓凝混凝土凝结时间的定义、影响因素、测试方法和应用等方面进行探讨。
一、超缓凝混凝土凝结时间的定义超缓凝混凝土是指在施工过程中,由于掺入了适当的控制剂和缓凝剂,使得混凝土的凝结时间相对较长。
一般情况下,普通混凝土的凝结时间在几小时之内完成,而超缓凝混凝土的凝结时间可以延长到数天甚至数周。
超缓凝混凝土的凝结时间的延长主要是为了适应特殊的施工要求,例如需要长时间进行模板拆除、需要在凝结过程中进行加固等。
超缓凝混凝土凝结时间受到多种因素的影响,主要包括以下几个方面:1. 控制剂和缓凝剂的种类和用量:超缓凝混凝土的凝结时间可以通过掺入适当的控制剂和缓凝剂来调节。
不同的控制剂和缓凝剂具有不同的化学成分和反应机理,因此对凝结时间的影响也不同。
2. 水胶比:水胶比是指混凝土中水和胶凝材料的质量比。
水胶比的大小直接影响混凝土的流动性和凝结时间。
一般来说,水胶比越大,混凝土的流动性越好,凝结时间也相对较短。
3. 温度:温度是影响混凝土凝结时间的重要因素之一。
较高的温度会加快混凝土的凝结过程,而较低的温度则会延缓凝结时间。
4. 环境湿度:环境湿度对混凝土凝结时间的影响较小,但在极端情况下,如高湿度环境下,可能会导致混凝土表面产生裂缝。
三、超缓凝混凝土凝结时间的测试方法为了准确评估超缓凝混凝土的凝结时间,需要进行相应的测试。
常用的测试方法包括:1. 温度测试:通过安装温度计在混凝土试块或构件内部测量温度的变化,从而确定混凝土的凝结时间。
2. 压力测试:通过施加一定的压力或荷载在混凝土试块或构件上,观察其变形情况,从而判断混凝土的凝结程度和凝结时间。
3. 颜色测试:通过观察混凝土试块或构件的颜色变化,如颜色由深变浅,可以初步判断混凝土的凝结时间。
四、超缓凝混凝土凝结时间的应用超缓凝混凝土凝结时间的延长为一些特殊工程提供了便利。
混凝土超时缓凝现象的处理方法
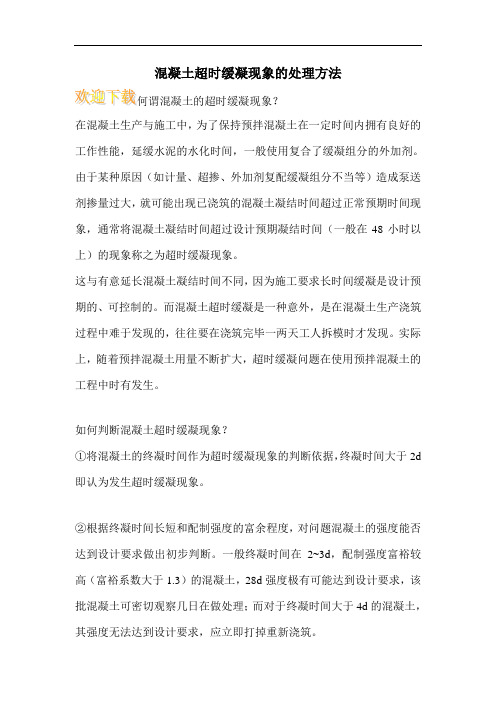
混凝土超时缓凝现象的处理方法
在混凝土生产与施工中,为了保持预拌混凝土在一定时间内拥有良好的工作性能,延缓水泥的水化时间,一般使用复合了缓凝组分的外加剂。
由于某种原因(如计量、超掺、外加剂复配缓凝组分不当等)造成泵送剂掺量过大,就可能出现已浇筑的混凝土凝结时间超过正常预期时间现象,通常将混凝土凝结时间超过设计预期凝结时间(一般在48小时以上)的现象称之为超时缓凝现象。
这与有意延长混凝土凝结时间不同,因为施工要求长时间缓凝是设计预期的、可控制的。
而混凝土超时缓凝是一种意外,是在混凝土生产浇筑过程中难于发现的,往往要在浇筑完毕一两天工人拆模时才发现。
实际上,随着预拌混凝土用量不断扩大,超时缓凝问题在使用预拌混凝土的工程中时有发生。
如何判断混凝土超时缓凝现象?
①将混凝土的终凝时间作为超时缓凝现象的判断依据,终凝时间大于2d 即认为发生超时缓凝现象。
②根据终凝时间长短和配制强度的富余程度,对问题混凝土的强度能否达到设计要求做出初步判断。
一般终凝时间在2~3d,配制强度富裕较高(富裕系数大于1.3)的混凝土,28d强度极有可能达到设计要求,该批混凝土可密切观察几日在做处理;而对于终凝时间大于4d的混凝土,其强度无法达到设计要求,应立即打掉重新浇筑。
预拌混凝土的超时缓凝现象和处理方法

预拌混凝土的超时缓凝现象和处理方法在预拌商品混凝土生产与施工中,为了保持预拌商品混凝土在一定时间内拥有良好的工作性能,一般要使用含缓凝组分的泵送剂。
如果由于某种原因造成泵送剂掺量过大,就可能出现已浇筑的商品混凝土凝结时间超过预期的问题。
通常将商品混凝土凝结时间超过设计预期凝结时间(一般在2 d以上)的现象称之为超时缓凝现象。
1预拌商品混凝土超时缓凝现象在预拌商品混凝土生产与施工中,为了保持预拌商品混凝土在一定时间内拥有良好的工作性能,一般要使用含缓凝组分的泵送剂。
如果由于某种原因造成泵送剂掺量过大,就可能出现已浇筑的商品混凝土凝结时间超过预期的问题。
通常将商品混凝土凝结时间超过设计预期凝结时间(一般在2 d以上)的现象称之为超时缓凝现象。
这与有意延长商品混凝土凝结时间不同,因为施工要求长时间缓凝是设计预期的、可控制的。
而商品混凝土超时缓凝是一种意外,是在商品混凝土生产浇筑过程中难于发现的,往往要在浇筑完毕一两天工人拆模时才发现。
实际上,随着预拌商品混凝土用量不断扩大,超时缓凝问题在使用预拌商品混凝土的工程中时有发生。
2预拌商品混凝土超时缓凝现象的特征2.1商品混凝土的凝结时间以C30商品混凝土为试验对象,从试验结果表1可以看出,当泵送剂的掺量在正常掺量范围时,商品混凝土的初凝时间为15.5 h,终凝时间为18.5h;而当泵送剂超掺达到3倍及以上时,商品混凝土的初凝时间达到45.5h及以上(>1d),终凝时间更在58.0h及以上(>2d),远远超过商品混凝土的预期凝结时间,商品混凝土产生超时缓凝现象。
从图1可以看出,超时缓凝商品混凝土的初凝与终凝时间间隔大于正常凝结商品混凝土,且超时缓凝越严重,商品混凝土的初凝时间延长不多,但终凝时间却显著延长,初、终凝时间间隔也越长。
这是由于预拌商品混凝土使用的泵送剂的缓凝成分主要为糖和羟基羧酸盐,其作用主要是抑制水泥中C3S的水化,当泵送剂严重过量后,C3S的水化被严重抑制,使水泥商品混凝土体系中水化产物严重不足,难以达到终凝所需的贯入阻力(28 MPa),导致XXX被显著延长;而这种缓凝成分对水化速度很快的C3A作用并不明显,由于C3A的水化贡献,使商品混凝土初凝时间虽有所延缓,但影响程度不及终凝严重。
水泥和缓凝剂对混凝土凝结时间的影响_兼论预拌混凝土的超缓凝及其预防
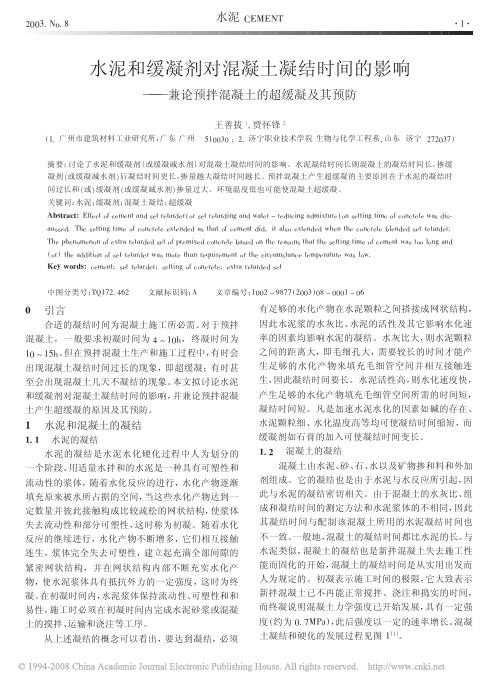
!
引言
合适的凝结时间为混凝土施工所必需。 对于预拌
有足够的水化产物在水泥颗粒之间搭接成网状结构, 因此水泥浆的水灰比、 水泥的活性及其它影响水化速 率的因素均影响水泥的凝结。水灰比大, 则水泥颗粒 之间的距离大,即毛细孔大,需要较长的时间才能产 生足够的水化产物来填充毛细管空间并相互接触连 生, 因此凝结时间要长。水泥活性高, 则水化速度快, 产生足够的水化产物填充毛细管空间所需的时间短, 凝结时间短。凡是加速水泥水化的因素如碱的存在、 水泥颗粒细、水化温度高等均可使凝结时间缩短,而 缓凝剂如石膏的加入可使凝结时间变长。 "# $ 混凝土的凝结 混凝土由水泥、 砂、 石、 水以及矿物掺和料和外加 剂组成。它的凝结也是由于水泥与水反应所引起, 因 此与水泥的凝结密切相关。由于混凝土的水灰比、 组 成和凝结时间的测定方法和水泥浆体的不相同, 因此 其凝结时间与配制该混凝土所用的水泥凝结时间也 不一致。 一般地, 混凝土的凝结时间都比水泥的长。 与 水泥类似, 混凝土的凝结也是新拌混凝土失去施工性 能而固化的开始, 混凝土的凝结时间是从实用出发而 人为规定的。初凝表示施工时间的极限, 它大致表示 新拌混凝土已不再能正常搅拌、浇注和捣实的时间, 而终凝说明混凝土力学强度已开始发展, 具有一定强 度 - 约为 ". /012 3 , 此后强度以一定的速率增长。 混凝 土凝结和硬化的发展过程见图 ( 4 ( 5 。
比值
5= !, "= #, ’ 5= 5, 3= #, 5 5= !, 5= -, ! 5= 5, /= #, -
从上表可看出,掺缓凝剂后混凝土的凝结时间 更长, 文献 ; ! < 也有类似的结论。这里同样要指出, 这 是在特定条件下得到的比值, 请勿随便套用。事实上 影响混凝土凝结时间的因素很多,除了水泥的凝结 时间、 水灰比等因素外, 缓凝剂的种类、掺量和环境 温度等都对混凝土的凝结时间有很大影响。 缓凝剂的掺量对混凝土的凝结时间影响很 大。研究表明 ; !A - < , 缓凝型减水剂掺量增加 5 倍时, 混 凝土凝结时间也几乎增长 5 倍。这主要是混凝土用 缓凝剂的特性所决定的。混凝土中所用的缓凝剂、 缓 凝减水剂主要有:"糖类, 如糖钙等;# 木质磺酸盐 类, 如木质磺酸钙、木质磺酸钠等; $羟基羧酸及其 盐类,如柠檬酸、酒石酸钾钠等;%无机盐类,如锌 盐、 硼酸盐、 磷酸盐等; 如胺盐及其衍生物。 &其它, 这类缓凝剂对水泥的缓凝与水泥中的石膏不同。二 水石膏作为缓凝剂,随着石膏掺量增加水泥凝结时 间延长,但掺量达某一值后,凝结时间几乎不再延
混凝土缓凝与“硬壳”现象

混凝土缓凝与“硬壳”现象(一)混凝土缓凝混凝土凝结时间过长是指超过正常凝结时间,仍未达到终凝的现象,预拌混凝土的凝结时间一般初凝时间为6~8h,终凝时间为8~12h(试验室条件)。
混凝土凝结时间超过24小时即为出现缓凝,超过48h就是超缓凝。
混凝土缓凝现象可分为两种情况:(1)整体严重缓凝;(2)局部严重缓凝。
第一种情况多半是由外加剂原因造成的,由于掺加了不合适的缓凝组分(有很多缓凝组分受温度等影响其凝结时间变化显著),或外加剂掺量超出了正常掺量,造成了混凝土的过度缓凝。
第二种情况如楼板或墙体混凝土的绝大部分凝结正常,局部混凝土缓凝,原因可能有:(1)外加剂采用了后掺法,混凝土搅拌不均匀,造成外加剂局部富集;(2)现场加水,混凝土粘聚性降低,发生泌水或离析,浇捣时振捣使局部浆体集中,水灰比变大且外加剂相对过量;(3)外加剂池中带缓凝组分的沉淀物不易搅拌均匀,造成混凝土局部过度缓凝。
(二)混凝土“硬壳”现象浇筑混凝土后,混凝土表面已经“硬化”,但内部仍然呈未凝结状态,形成“糖芯”,姑且称之为“硬壳”现象。
并且常伴有不同程度的裂缝,该裂缝很难用抹子抹平。
这一现象经常出现在天气炎热、气候干燥的季节。
其实表面并非真正硬化,很大程度上是由于水分过快蒸发使得混凝土失水干燥造成的。
表层混凝土的强度将降低30%左右,而且再浇水养护也无济于事。
除了气候因素,外加剂配料的成分和混凝土掺合料的种类也都有一定的关系,外加剂含有糖类及其类似缓凝组分时容易形成硬壳。
使用矿粉时比粉煤灰更为明显。
解决办法:(1)对外加剂配方进行适当调整,缓凝组分使用磷酸盐等,避免使用糖、木钙、葡萄糖、葡萄糖酸钠等;(2)使用粉煤灰做掺合料,其保水性能比矿粉优异;(3)如表面产生细微裂缝,可在混凝土初凝前采用二次振捣消除裂缝,以免进一步形成贯穿性裂缝。
(4)最有效的办法应该是施工养护措施,即尽量避免混凝土受太阳直射,刚浇筑完毕的混凝土可采用喷雾和洒水等养护方法。
预拌混凝土的缓凝问题及其预防措施

在夏季,混凝土生产过程中常常掺加缓凝剂或缓凝型减水剂以改善其流动性,但有时外加剂使用不当会出现缓凝甚至超缓凝现象,造成混凝土不能及时脱模或几天不凝结。
夏季发生缓凝事故的现象不容忽视,尤其是在外加剂与水泥适应性差时,遇到温度突然降低更容易出现缓凝现象。
(一)水泥和混凝土的凝结(1)水泥的凝结水泥与水发生水化产物,水化产物使水泥颗粒间搭接固化凝结。
水泥的凝结与水泥的活性,水灰比、温度等因素有关,水灰比大时,水泥颗粒间的距离大,需要较多的水化产物填充,凝结时间相对就长。
水泥活性高,水化速度快,生成水化产物的速度也快,凝结时间也就较短,因此,影响水泥水化速率的因素均会影响水泥的凝结时间。
(2)混凝土的凝结混凝土的凝结是由水泥与水发生水化反应所引起的,混凝土的凝结与水泥的凝结密切相关。
环境温度相同的情况下,可以用水泥的凝结时间粗略地推断混凝土凝结时间,例如,水泥凝结时间为(标准稠度用水量27%):初凝185min,终凝260min,混凝土水灰比为0.54,可以推断混凝土的凝结时间(不考虑外加剂因素)是水泥凝结时间的二倍左右。
这种推断是在试验条件相同或相近时得出的,不宜随便套用。
(二)出现缓凝现象的原因为什么会出现这种超缓凝现象笔者认为主要有以下两方面的原因。
(1)水泥凝结时间过长混凝土的凝结主要是由于水泥的凝结所引起,因此水泥的凝结时间就决定了混凝土凝结时间的长短。
水泥凝结时间长,混凝土凝结时间相对较慢,尤其在混凝土水灰比大或缓凝剂(或缓凝型减水剂)掺量大的情况下,很容易出现凝结时间较长或超长现象。
(2)缓凝剂或缓凝型减水剂掺量过大缓凝剂或缓凝型减水剂掺量过大是混凝土凝结时间长甚至几天不凝结的主要原因。
混凝土中使用的缓凝剂或缓凝型减水剂主要有:1.糖类,如糖钙等;2.木质磺酸盐类,如木质素磺酸钙、木质磺酸钠等;3.羟基羧酸及盐类,如柠檬酸、酒石酸钾等;4.无机盐类,如锌盐、硼酸盐、磷酸盐等;5.其它,如胺盐及其衍生物。
【大体积混凝土超时缓凝现象的原因分析及处置措施】

【大体积混凝土超时缓凝现象的原因分析及处置措施】一【大体积混凝土超时缓凝现象的原因分析及处置措施】1.介绍本文档旨在分析大体积混凝土超时缓凝的原因,并提出相应的处置措施。
通过对该现象的研究,旨在提高混凝土施工效率和质量,确保工程的顺利进行。
2.原因分析2.1 水胶比过高导致混凝土中可溶性物质含量增加,引起超时缓凝现象。
2.2 水灰比过低导致混凝土早期缓凝后的水化反应速度降低,导致超时缓凝。
2.3 混凝土配制过程不严格,导致材料比例不准确,引起超时缓凝。
2.4 大体积混凝土施工过程中的温度控制不当,导致水化反应速度过慢,引起缓凝现象。
3.处置措施3.1 控制水胶比,减少混凝土中可溶性物质含量,防止超时缓凝。
3.2 调整水灰比,提高混凝土的早期水化反应速度,防止超时缓凝。
3.3 严格控制混凝土配制过程,确保材料比例准确性,避免超时缓凝。
3.4 合理控制施工温度,提高水化反应速度,防止缓凝现象的发生。
4.附件本文档涉及的附件包括混凝土配制记录表、温度控制记录表、混凝土成型过程控制记录表等。
5.法律名词及注释5.1 混凝土:指由水泥、石料、砂料和适量的水按一定比例组成的均质胶状物质。
5.2 超时缓凝:指混凝土在规定的凝结时间内未能达到预期强度的现象。
二【大体积混凝土超时缓凝现象的原因分析及处置措施】1.引言本文档对大体积混凝土超时缓凝现象进行深入分析,并提供相应的处置措施。
通过研究该现象,旨在改善混凝土施工质量,确保工程的顺利进行。
2.原因分析2.1 水胶比过高:水胶比过高导致混凝土中可溶性物质含量增加,从而引起超时缓凝现象。
2.2 水灰比过低:水灰比过低导致混凝土早期缓凝后的水化反应速度降低,从而引起超时缓凝。
2.3 配制不严格:混凝土配制过程中如材料比例不准确,也会导致超时缓凝现象的发生。
2.4 温度控制不当:大体积混凝土施工过程中,若温度控制不当,会引起水化反应速度过慢,从而引起缓凝现象。
3.处置措施3.1 控制水胶比:严格控制水胶比,减少混凝土中可溶性物质含量,防止超时缓凝现象的发生。
预拌混凝土的超时缓凝现象及处理方法

1 预拌混凝土超 时缓凝现 象
在预拌混凝 土生产与施工 中, 为了保持预拌混凝土在一定 时间内拥有 良好 的工 作性能 , 一般要使 用含缓 凝组分 的泵送 剂。 如果 由于某种原 因造成泵送剂掺量过 大 , 可能出现 已浇 就 筑 的混凝土凝结时间超过 预期 的问题 。通常将混凝 土凝结时
物严重不足 , 以达 到终凝所需 的贯人阻力 (8MP )导致终 难 2 a , 凝被显著延长 ; 而这种缓凝成分对水化速度很快的 C 作用并 A 不明显 , 由于 c 的水化贡献 , 使混凝 土初 凝时间虽 有所延缓 , 但影 响程度不及终凝严重。 因此 , 在判断和处理超 时缓凝质量 问题 时 , 以混凝 土的 应
21 0 1年 第 1期 (总 第 2 5 期 ) 5
Nu e i 0 1T tl o2 5 mbr n2 1 ( oa N . ) 1 5
混
凝
Co r t nc ee
土
预
拌
混
凝
土
READY D D M C0NCI TE
d i1 . 6  ̄i n10 —5 0 0 0 .3 o :03 9 .s. 23 5 . 1.1 0 9 s 0 2 1 0
Abs r c : Thsp p r eci e o c p fo e i e r ig,x e m e tl ee rh do e trso v ri eadn o r ̄ wh c cu — ta t i a e srb dc n e t d o v r mert dn e p r t a i n sac e n fau e fo e mertr igc nce a r t ihi ld n
时间为 1.h而当泵送剂超掺达到 3 8 ; 5 倍及以上时 , 凝土的初凝 昆 时问达到 4 .h 5 及以上( 1 )终凝时间更在 5.h 5 > , d 8 及以上(2 ) 0 > , d
混凝土超长时间缓凝案例分析

例分析,阐述 了造成混凝土超长时间缓凝的原因、处理
过程及在处理该类事故 中应特别注意的问题 ,以供 同行 及工程建设人员借鉴。
1 案例 1
1 . 1 事故发生经过
1 9 9 6 中国公司承接的西亚国家一城市污水处理工程。
池底混凝土未初凝。现场搅拌站混凝土搅拌速度慢 ,不
能连续供应,因此要求混凝土初凝时间比平常混凝土要
混凝土超长时 间缓凝会带来一系列问题 ,首先是延
误工期,对施工进度普遍要求较快的工程来说都是很难
接受的;同时由于造成混凝土长时间缓凝原因不 同,混
凝土强度会有不 同程度下 降,如养护不到位 , 混凝土极 易失水而更使强度降低 ,特别是对表面强度影响严重。
以下就 比较典型的 3次混凝土超长时间缓凝事故案
延长 5 h以上 。
试验结束已是下午 5 : 0 0多,减水剂使用说明书 ( 说 明书未注明什么类型 ) ,在使用掺量中有一条内容是 :特
工程开工后浇筑混凝土一直使用的是 4 2 . 5级抗硫水泥 ,
42 Co AL A sH 4/ 2 01 5
殊情况下可双倍推荐掺量使用 ,推荐掺量是 1 . 2 %,而特 殊情 况未注明是何种情况及 在什么气温下使用。这样 ,
减少混凝土坍落度损失 。对于这种严重不适应 ,应当更 换减水剂品种或由减水剂厂通过调整减水剂配方来实现 或弃用该水泥。可是 由于时间紧 , 试验时掺量增加 比例
过大 ,没有充足时间反应出试验出现了问题,造成混凝 土超长时间缓凝事故的发生。
最后我们按 2 . 3 % 掺量又拌了一盘 ,结果混凝土初始坍落
成的。
其c A含量低 ( <5 %), 与减水剂具有 良好的适应性。
浅谈混凝土凝结时间及影响因素的研究
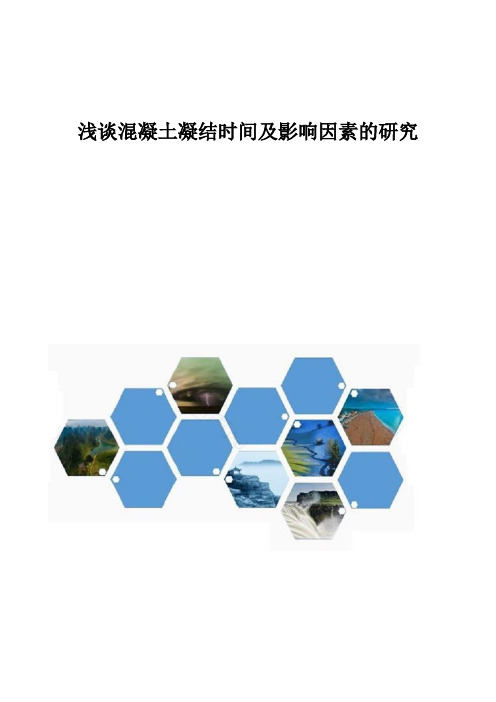
浅谈混凝土凝结时间及影响因素的研究摘要:通过对混凝土凝结时间相关文献研究分析,论述当前对混凝土凝结时间及检测方法的研究现状,总结了混凝土凝结时间影响因素,并对混凝土的反常凝结行为进行了分析讨论。
归纳表明,混凝土凝结时间主要分成初凝和终凝。
混凝土凝结时间主要受水泥熟料的矿物组成和水泥细度、集料级配、掺合料类别及掺量、外加剂、混凝土强度等级及水灰比、混凝土养护温度以及施工工艺等因素影响。
关键词:混凝土;凝结时间;影响因素;反常凝结引言英国工程师阿斯普丁(1824年)发明波特兰水泥之后,使得制作混凝土胶凝材料产生了质的变化,混凝土强度得到极大的提高并改善其它性能[1]。
预拌混凝土和商品混凝土也是当今混凝土工业发展方向。
早在20世纪40年代以原材料基地、原材料运输、配料、搅拌、输送、定量控制等形成的商品混凝土工厂就已问世[2]。
无论是从施工操作科学性的角度,还是从工程经济性的角度出发,混凝土凝结时间一直是施工单位和混凝土生产单位关心的问题。
因此研究影响混凝土凝结时间的因素,掌握如何简单有效地控制混凝土凝结时间,都具有重要的实际意义。
1 混凝土的凝结时间及测定方法混凝土的凝结时间是指水泥从加水拌和开始到失去流动性的时间即从可塑状态到固体状态所需要的时间。
水泥和水间的反应是混凝土产生凝结的主要原因,但因各种因素影响导致混凝土凝结时间与配置该混凝土所用水泥的凝结时间并不一致,这是由于水化水泥浆体中的凝结和硬化过程受到水化产物空间填充情况造成的。
因此水灰比对凝结时间有明显的影响,配置混凝土的水灰比与水泥浆体测定凝结时间不同时,会导致水泥浆体凝结时间和所配混凝土凝结时间也不相同[3]。
除此之外,混凝土凝结时间还受其他各因素影响,例如环境温度变化、混凝土中掺入某些外加剂(缓凝剂或速凝剂)等,这都将会明显影响混凝土凝结时间[4]。
目前,混凝土凝结时间常用贯入阻力方法进行测定[5]。
2 混凝土凝结时间影响因素2.1水泥的影响引起混凝土凝结的关键是混凝土中水泥石的水化反应,因此混凝土的凝结与水泥的凝结密切相关[6]。
混凝土缓凝问题及其预防措施
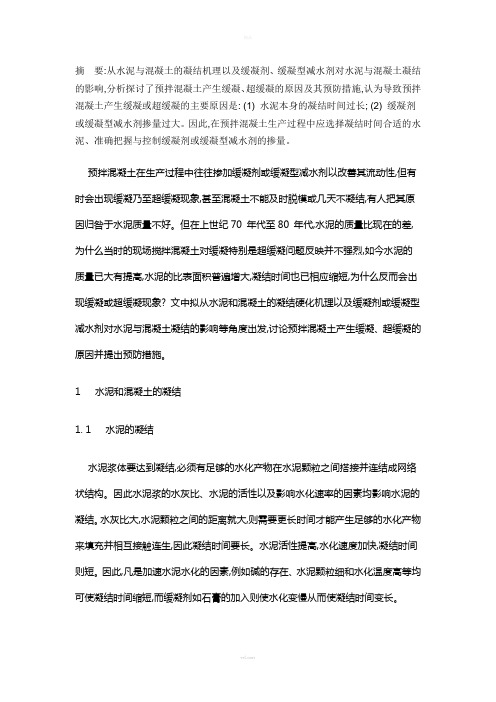
摘要:从水泥与混凝土的凝结机理以及缓凝剂、缓凝型减水剂对水泥与混凝土凝结的影响,分析探讨了预拌混凝土产生缓凝、超缓凝的原因及其预防措施,认为导致预拌混凝土产生缓凝或超缓凝的主要原因是: (1) 水泥本身的凝结时间过长; (2) 缓凝剂或缓凝型减水剂掺量过大。
因此,在预拌混凝土生产过程中应选择凝结时间合适的水泥、准确把握与控制缓凝剂或缓凝型减水剂的掺量。
预拌混凝土在生产过程中往往掺加缓凝剂或缓凝型减水剂以改善其流动性,但有时会出现缓凝乃至超缓凝现象,甚至混凝土不能及时脱模或几天不凝结,有人把其原因归咎于水泥质量不好。
但在上世纪70 年代至80 年代,水泥的质量比现在的差,为什么当时的现场搅拌混凝土对缓凝特别是超缓凝问题反映并不强烈,如今水泥的质量已大有提高,水泥的比表面积普遍增大,凝结时间也已相应缩短,为什么反而会出现缓凝或超缓凝现象? 文中拟从水泥和混凝土的凝结硬化机理以及缓凝剂或缓凝型减水剂对水泥与混凝土凝结的影响等角度出发,讨论预拌混凝土产生缓凝、超缓凝的原因并提出预防措施。
1 水泥和混凝土的凝结1. 1 水泥的凝结水泥浆体要达到凝结,必须有足够的水化产物在水泥颗粒之间搭接并连结成网络状结构。
因此水泥浆的水灰比、水泥的活性以及影响水化速率的因素均影响水泥的凝结。
水灰比大,水泥颗粒之间的距离就大,则需要更长时间才能产生足够的水化产物来填充并相互接触连生,因此凝结时间要长。
水泥活性提高,水化速度加快,凝结时间则短。
因此,凡是加速水泥水化的因素,例如碱的存在、水泥颗粒细和水化温度高等均可使凝结时间缩短,而缓凝剂如石膏的加入则使水化变慢从而使凝结时间变长。
1. 2 混凝土的凝结混凝土的凝结也是由于水泥与水反应所引起的,因此混凝土的凝结与水泥的凝结密切相关,两者在凝结时间的定义上也相似。
混凝土的凝结也是表示新拌混凝土失去施工性能、固化或产生一定的力学强度的开始,其初凝、终凝时间也纯粹是从实用意义出发而人为规定的。
水泥混凝土引起超时缓凝的现象及原因分析

水泥混凝土引起超时缓凝的现象及原因分析、水泥混凝土加水后,由于水泥的水化,随着时间的推移,浆体逐渐失去流动性、可塑性,这一过程称为混凝土的凝结。
我国标准按照美国材料试验标准(ASTMC403)提出的贯入阻力试验来确定混凝土的凝结时间。
若贯入阻力达3.5MPa和28MPa分别表示混凝土的初凝和终凝。
混凝土的初凝时间不能过快,以便施工时有足够的时间来完成混凝土的搅拌、运输、浇捣和砌筑等操作,混凝土的终凝也不能过迟,以便混凝土能够尽快的硬化,达到一定的强度,以利于下道工序的进行。
水泥混凝土凝结时可能产生的异常凝结行为主要为:假凝、瞬凝、超时缓凝和不凝。
假凝其特征是水泥和水接触后几分钟内就发生凝固,且没有明显的温度上升现象。
此时再加拌和(无须加拌和水),仍可以恢复塑性,用于浇注并以通常形式凝结;瞬凝,特征是水泥和水接触后浆体很快地凝结成为一种很粗糙的、和易性差的混合物,并在大量放热的情况下很快凝结;超时缓凝就是混凝土的终凝时间严重超过设计或预计的凝结时间。
在水泥混凝土施工过程中,如果产生异常凝结,将对工程质量造成严重的危害。
一、水泥混凝土产生超时缓凝的现象随着商品混凝土和泵送混凝土的发展,在混凝土的生产过程中通常掺加了减水剂、缓凝剂等外加剂和活性掺和料。
如果外加剂的掺量过大、或出现外加剂与水泥和活性掺和料的相容性等问题而引起的水泥混凝土凝结时间严重超过设计和预计的凝结时间造成混凝土很长时间才凝结,对强度造成损失,并影响工期,有的造成混凝土长期不凝结,使结构破坏,以致造成严重的工程事故。
二、水泥混凝土产生超时缓凝的原因1.缓凝组分的超量掺加混凝土工程中常用缓凝剂来延长凝结时间,使新拌混凝土较长时间保持塑性,以便浇注,提高施工效率,在泵送混凝土中缓凝剂和高效减水剂复合使用可以减少坍落度损失,保持良好的泵送性能。
缓凝剂和缓凝减水剂均具有一个适宜的掺量范围(按水泥质量的百分含量)如:木质素磺酸钙掺量为0.2~0.3%,葡萄糖酸钙的掺量为0.1~0.3%;工程中通常规定木质磺酸钙和葡萄糖酸钙类缓凝剂的掺量不超过0.25%。
混凝土出现凝结时间异常的原因

混凝土出现凝结时间异常的原因混凝土在实际拌制的过程中,由于环境、天气、原材料等因素的影响,会出现缓凝、假凝与速凝现象,进而影响混凝土性能,延误施工。
混凝土出现凝结时间异常的原因是什么?如何采取紧急处理措施呢?一、混凝土缓凝1、原因(1)缓凝剂超掺夏季为满足施工要求,泵送混凝土、商品混凝土等常会掺入缓凝剂,但掺量过大,易导致混凝土凝结时间严重超过设计和预计的凝结时间,甚至混凝土长期不凝结,不仅造成强度大幅度降低、延误工期,甚至给工程带来严重的质量问题。
(2)减水剂与水泥、掺合料的相容性问题减水剂的化学性质、分子量、交联度、磺化程度和平衡离子以及水泥中SO3、C3A的含量、水泥细度、碱含量等,是其主要影响因素。
若相容性差将引起混凝土超时缓凝现象。
(3)水泥掺合料为降低成本,改善水泥某些性能,在水泥生产过程中往往掺入一定量的矿物掺合料。
但掺合料品种或用量不当时,则会引起混凝土异常凝结。
如掺量过高时,可能引起超时缓凝。
(4)不恰当的施工工艺或措施在混凝土的生产和施工过程中,不恰当的施工工艺也可能引起混凝土的超时缓凝。
如混凝土在生产时拌和水中含有油类、酸、糖等,在外掺缓凝剂的条件下会造成混凝土严重的缓凝现象。
2、预防措施(1)定期校称,防止计量不准造成外加剂超掺;(2)在施工前,先经试验确定所使用的外加剂与水泥、掺合料等原材料之间的适应性及合适掺量。
(3)对每批水泥的进站要进行留样封存,发现异常,可进行追溯;(4)正确引导施工单位使用商品混凝土,杜绝不恰当的施工工艺影响使用效果。
二、混凝土假凝现象混凝土假凝是指水泥的一种不正常的早期固化或过早变硬现象。
在出机后,短时间内达到初凝,经重新搅拌后又出现可塑性,这种现象叫混凝土假凝。
1、原因造成混凝土假凝的因素很多,主要是由于水泥粉磨时磨内温度较高,使二水石膏脱水成半水石膏的缘故。
当水泥拌水后,半水石膏迅速化为二水石膏,形成针状结晶网状结构,从而引起浆体固化。
另外,某些含碱较高的水泥,硫酸钾与二水石膏生成钾石膏迅速长大,也会造成混凝土假凝。
混凝土凝结时间延长的意外缓凝事故!

混凝土凝结时间延长的意外缓凝事故!关键词:混凝土;泵送剂;缓凝组分;温度变化;意外缓凝在预拌混凝土生产中,为了适应运输和施工要求,保持新拌混凝土在一定时间内拥有良好的工作性能,一般都要使用含有缓凝组分的泵送剂。
特别是夏季,为了控制混凝土坍落度经时损失,其泵送剂中的缓凝组分比其他季节泵送剂中的缓凝组分含量高。
秋季作为夏季与冬季的过度期,其气温变化反复无常,如果由于某种原因造成泵送剂使用不当,就可能出现已浇筑的混凝土凝结时间超过预期的问题。
通常将混凝土凝结时间超过设计预期凝结时间48h(>2 d)以上的现象称之为“超时缓凝”现象。
还有一种凝结时间超过了设计预期凝结时间,但终凝时间小于24h(<1 d)的现象,我们可称之为“意外缓凝”现象。
意外缓凝与有意延长混凝土凝结时间和超时缓凝都不同,因为施工要求长时间缓凝是设计预期的、可控制的,混凝土超时缓凝是一种质量事故,而这种意外缓凝现象,后果虽然没有超缓凝事故那么严重,但也是质量失去控制的意外事故。
预拌混凝土产生意外缓凝和超时缓凝的主要原因在于胶凝材料凝结时间过长或缓凝型泵送剂掺量过大。
环境温度变低会使泵送剂的缓凝效果增加,也会使混凝土意外缓凝甚至产生超时缓凝。
实际上,随着预拌混凝土用量不断扩大,“超时缓凝”事故时有发生,而“意外缓凝”的质量失控问题可能更为普遍。
为此,本文介绍一起2011年秋季发生在内蒙古西北部地区,由于误用剩余的夏季缓凝泵送剂,遭遇气温变低时,造成混凝土凝结时间延长的意外缓凝事故。
1事故说明内蒙古西北部阴山南麓地区某项工业厂房工程,由当地商品混凝土公司供应混凝土,浇筑二层柱、梁、板,混凝土强度等级均为C30,由泵车泵送,于2011年9月28日上午8时开始浇筑到下午17时15分结束,共发 22车263方混凝土。
第二天早晨发现部分二层设备平台及楼板的混凝土未凝结,工人无法上去放线。
施工单位认为混凝土2d未凝结,随即要求商品混凝土公司前去处理。
- 1、下载文档前请自行甄别文档内容的完整性,平台不提供额外的编辑、内容补充、找答案等附加服务。
- 2、"仅部分预览"的文档,不可在线预览部分如存在完整性等问题,可反馈申请退款(可完整预览的文档不适用该条件!)。
- 3、如文档侵犯您的权益,请联系客服反馈,我们会尽快为您处理(人工客服工作时间:9:00-18:30)。
预拌混凝土超时缓凝现象的研究
摘要:本文简述混凝土超时缓凝的原因,针对本地区工程案例,研究分析了其对混凝土性能及工程质量带来的不利影响,并针对缓凝现象如何避免提出一些建议。
关键词:混凝土超时缓凝
混凝土外加剂已成为预拌混凝土重要的组成部分,其中缓凝减水剂在预拌混凝土生产中应用最广泛的一种复合型外加剂,特别是在天气温度高、远距离运输、泵送和施工中得以应用,但有时混凝土的缓凝时间不按设计值来发展,可能出现长时间不凝的异常现象。
通常把混凝土凝结时间在超出理论设计的范围之外,长时间不凝结的非正常现象称之为混凝土的超时缓凝现象。
超时缓凝现象是一种不常见的混凝土异常凝结现象,一旦发生给施工带来诸多困难,本文就超时缓凝现象及如何减少超时缓凝影响进行分析。
1 产生超时缓凝的原因
1.1 外加剂中的缓凝组分过量
在外加剂生产过程中,由于生产管理的不严密和技术人员的疏忽大意,可能将缓凝组分添加过量,送入混凝土搅拌站后,又未采取及时有效的手段进行检查就用于生产造成了使用该批外加剂的混凝土超时缓凝。
商品混凝土企业使用的泵送剂中,缓凝组分采用有机酸和糖
等。
这些缓凝剂化合物分子上都具有一定数量的羟基(OH)、羧基(COOH),它们具有较强的极性,吸附在水泥水化物的晶核上,阻碍了结晶的继续发展,即阻碍了水泥的水化,从而延长了凝结时间。
同时,外加剂中某些减水组分,如木钙、糖钙、木钠等,也都有缓凝作用。
因此外加剂中缓凝组分过量是导致混凝土超时缓凝的一个重要因素。
1.2 水泥和粉煤灰的因素
纯水泥熟料的凝结时间很短,因为铝酸三钙(C3A)溶于水时,生成AL3+,与水化硅酸钙凝胶带相反电荷,促使稳定的水化硅酸钙凝胶很快产生凝结。
因此,在水泥熟料进行粉磨时,需加入适量的二水石膏以调节水泥的凝结时间。
石膏与铝酸三钙反应,产生难溶于水的水化铝酸三钙,这种难溶的水化物沉淀在水泥粒子的表面,将熟料粒子包裹起来,使水泥的水化作用减慢,因而延缓凝结时间。
适当的二水石膏是对水泥水化反应有益的,但掺量过大或者采用半水石膏或无水石膏代替二水石膏作调凝剂时,会造成严重的负面影响,如凝结时间异常等。
目前水泥厂SO3含量的出厂指标一般控制在 2.3%~3.0%,如果高于3.0%,就有可能影响水泥的凝结时间。
1.3 水泥与外加剂的相容性因素
在现代混凝土技术中,并不是每一种符合国家标准的水泥在使用一定的外加剂时都有同样的工作性能,同样,也不是每一种符合国家标准的外加剂对每一种水泥的流变性能的影响都一样,这就是水泥与外
加剂的相容性问题。
水泥厂的产品虽然能满足国家要求,但因为水泥的生产工艺和混合材不同,水泥的性能也有一定的差距。
1.4 混凝土生产企业的管理因素
混凝土搅拌站因生产管理过程不严密所产生的质量问题相当普遍,超时缓凝也会因为管理不到位而发生。
在外加剂的添加方式上,目前搅拌站采用电脑自动计量添加方式,这就大大减少人为因素带来的差错,但在电脑输入配合比和外加剂的称量设备的保养这些细节方面还是应该加大管理力度。
2 超时缓凝对混凝土的影响
2.1 超时缓凝对混凝土的影响
超时缓凝作为混凝土的一种不正常现象,会带来各方面不利的影响,但工程技术人员更关心的是对混凝土强的的影响。
本人以普通的C30泵送混凝土为基准,与在外加剂过掺发生超时缓凝的混凝土作对比试验。
具体数据见表1(混凝土配合比:C∶S∶G∶F∶W=302∶781∶1066∶65∶176;胶凝材料为某水泥厂P.O42.5水泥和某电厂Ⅰ级粉煤灰;外加剂为奈系缓凝高效减水剂,缓凝组分为葡萄糖酸钠)。
如表1所示。
通过上述试验数据可以看出,当外加剂在两倍的推荐掺量的时候混凝土出现超时缓凝后,其早期强度要低于正常凝结的混凝土,但只要早期护理和养护到位,超时缓凝的混凝土在凝结后的强度发展很快,甚至超过普通正常凝结的混凝土,对28天设计强度是不会产生太大的影响。
如若掺量太大,那将产生严重的后果。
2.2 超时缓凝混凝土的其他影响
混凝土超时缓凝,其凝结时间过长,工期上也就必须延长混凝土的拆模时间,会耽误工期,若过早拆模,就会导致混凝土表面拉伤,甚至结构受损。
如果混凝土超时缓凝过长,可能会影响到混凝土的后期强度,这将带来巨大的经济损失。
3 典型超时缓凝工程事故案例
3.1 某小区宿舍楼工程
该工程为框架五层,它的三层柱及四层楼面为C30混凝土,由某商品混凝土公司生产供应同时浇筑,该批混凝土在浇筑后116h内仍处于松软状态,后逐渐凝结硬化,但表观质量较差,板面拆模后留下许多蜂窝麻面,有的出现了蜘蛛网状裂缝。
8月7日在现场抽取30%构件进行实体检测,发现大部分回弹值集中在30左右,碳化值在2.0左右,经过计算评定混凝土回弹推定值的75%达不到设计值C30要求。
根据现场
结构实体检测数据及业主、监理、施工单位一致建议决定拆除该批混凝土。
3.1.1 事故原因分析
(1)该批混凝土是7月5日浇筑,当时天气特别炎热。
混凝土公司提供的商品混凝土也特别掺入了缓凝剂。
该商品混凝土公司未严格按照规范做好对外加剂的复试工作,只按外加剂厂提供的推荐掺量,同时经检测该外加剂厂家提供的外加剂产品稳定性有波动,缓凝组分未控制好,可能导致发生严重超时缓凝。
(2)该外加剂为奈系缓凝高效减水剂,缓凝组分为葡萄糖酸钠。
经检测,该外加剂有严格的掺量要求,如果超过掺量要求,缓凝时间会变得异常。
混凝土公司也未能按照要求定期对称量设备进行检查保养。
可能导致外加剂的计量不准确。
4 防止混凝土超时缓凝的建议
使用质量稳定的外加剂厂所生产的产品,而且要加强每进场批次的检验。
要使用品牌水泥,避免一些不合格的水泥,每次进场要加强检验。
同时一定要做水泥和外加剂的相容性试验。
要加强生产过程中的细节管理,严格实施搅拌计量校验制度,特别是水泥、外加剂的计量秤和控制阀门等应定期检查。
尽量避免在恶劣天气下浇筑混凝土,同时应在天气变化较大时段注意对已完成浇筑的混凝土的观察,及时调整外加剂的掺量。
5 结语
超时缓凝这种不正常现象给整个工程施工带来了不良的影响,我们要对发生的事故具体问题具体分析处理,确定结构安全使用功能能否达到设计要求,否则就应该及时返工,消除事故隐患。
要做好事前防范,避免超时缓凝的发生。