船舶制造工艺
船舶制造工艺学

船舶制造工艺学
《船舶制造工艺学》是一门研究船舶建造过程中各种工艺方法和技术的学科。
它涵盖了船舶制造的各个环节,包括船体建造、机械设备安装、涂装、下水等。
这门学科的主要内容包括:
1. 船体建造:涉及船体结构设计、板材加工、焊接技术、船体型线放样等。
2. 机械设备安装:包括主机、辅机、舵机、推进系统等设备的安装与调试。
3. 涂装工艺:研究船舶防腐涂料的选择、涂装方法和涂层质量控制。
4. 下水与试验:探讨船舶下水过程中的技术要求和安全措施,以及船舶的各种试验和检测。
5. 质量控制与管理:关注船舶制造过程中的质量保证体系、检验标准和质量管理方法。
通过学习《船舶制造工艺学》,学生可以了解船舶建造的基本流程和技术要点,掌握相关的工艺技能,为从事船舶设计、制造、维修等工作打下基础。
同时,这门学科也有助于提高船舶建造的质量和效率,保障船舶的安全性和可靠性。
造船工艺流程
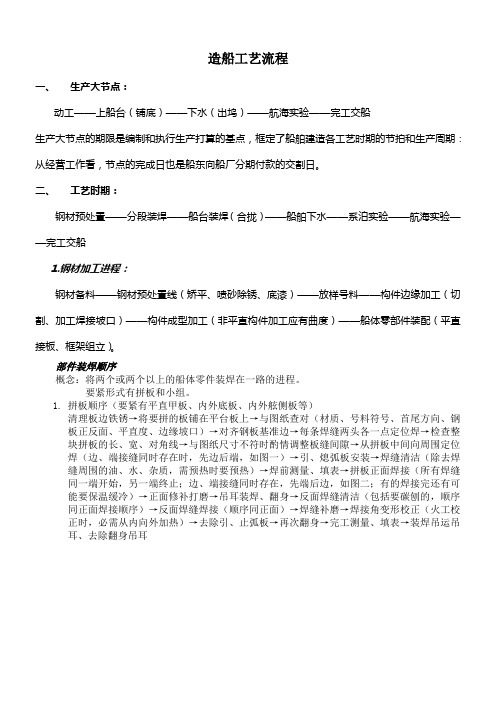
造船工艺流程一、生产大节点:动工——上船台(铺底)——下水(出坞)——航海实验——完工交船生产大节点的期限是编制和执行生产打算的基点,框定了船舶建造各工艺时期的节拍和生产周期:从经营工作看,节点的完成日也是船东向船厂分期付款的交割日。
二、工艺时期:钢材预处置——分段装焊——船台装焊(合拢)——船舶下水——系泊实验——航海实验——完工交船1.钢材加工进程:钢材备料——钢材预处置线(矫平、喷砂除锈、底漆)——放样号料——构件边缘加工(切割、加工焊接坡口)——构件成型加工(非平直构件加工应有曲度)——船体零部件装配(平直接板、框架组立)。
部件装焊顺序概念:将两个或两个以上的船体零件装焊在一路的进程。
要紧形式有拼板和小组。
1.拼板顺序(要紧有平直甲板、内外底板、内外舷侧板等)清理板边铁锈→将要拼的板铺在平台板上→与图纸查对(材质、号料符号、首尾方向、钢板正反面、平直度、边缘坡口)→对齐钢板基准边→每条焊缝两头各一点定位焊→检查整块拼板的长、宽、对角线→与图纸尺寸不符时酌情调整板缝间隙→从拼板中间向周围定位焊(边、端接缝同时存在时,先边后端,如图一)→引、熄弧板安装→焊缝清洁(除去焊缝周围的油、水、杂质,需预热时要预热)→焊前测量、填表→拼板正面焊接(所有焊缝同一端开始,另一端终止;边、端接缝同时存在,先端后边,如图二;有的焊接完还有可能要保温缓冷)→正面修补打磨→吊耳装焊、翻身→反面焊缝清洁(包括要碳刨的,顺序同正面焊接顺序)→反面焊缝焊接(顺序同正面)→焊缝补磨→焊接角变形校正(火工校正时,必需从内向外加热)→去除引、止弧板→再次翻身→完工测量、填表→装焊吊运吊耳、去除翻身吊耳11221图一装配方法(正确)装配方法(错误)图三.火工校正方向图二.焊接顺序小组顺序小组的内容包括 “T ”排、组合纵桁(肋板)、龙筋先行、机座、肋骨框 架等的组装。
“T ”排小组“T ”排分直、弯两类:直“T ”排通常采纳倒装法;弯“T ”排通常采纳侧装法。
船舶建造工艺课件

船体装配
总结词
船体装配是将加工好的船体零件和分段按照设计要求进行组装的过程。
详细描述
船体装配是船舶建造的关键环节,需要保证装配的精度和质量,以确保船体的整 体性能和使用寿命。同时,装配过程还需要考虑生产效率和成本等因素。
船舶下水与试航
总结词
船舶下水与试航是在船体装配完成后进行的,是对船舶性能的全面检验。
验、完工检验等方面的质量控制方法。
输标02入题
材料检验是质量控制的基础,涉及到原材料、外购件 、焊接材料等方面的检验和控制,以确保材料的质量 符合设计要求和规范标准。
01
03
完工检验是质量控制的最后环节,涉及到船舶整体性 能的测试和验证,以确保船舶的整体性能符合设计要
求和规范标准。
04
工序检验是质量控制的关键环节,涉及到船体结构焊 接、设备安装、涂装等方面的检验和控制,以确保各 道工序的质量符合要求。
船体设计
高速客轮的船体设计需要采用轻质材料和高强度材料,以减小船体重量和阻力。同时,需 要考虑船体的线型和船体结构,以提高航速和稳定性。
推进系统
高速客轮需要配备大功率的发动机和推进器,以确保在短途航行中能够快速到达目的地。 同时,为了减小噪音和振动,需要选择低噪音、低振动的发动机和推进器。
案例三:高速客轮的建造工艺
内部装修
豪华游艇的内部装修需要考虑材料的选择、工艺的处理和细节的处理。采用高品质的材料和精细的工 艺,打造豪华、舒适的内部空间。同时,还需考虑船员的居住和工作空间,以确保航行的顺利进行。
案例三:高速客轮的建造工艺
总结词
高速客轮主要用于城市间或岛屿间的短途运输,其建造工艺注重船体的轻巧和高速性能。 同时,为了提供良好的乘客体验,对船体的隔音和减震性能要求也很高。
分段造船工艺

分段造船工艺船舶建造是一个复杂的过程,其中分段造船工艺是关键步骤之一。
分段造船工艺是指将船体分成若干个独立的模块,然后分别进行制造和装配的工艺流程。
这种工艺使船舶建造更加高效、灵活和可控。
下面将详细介绍分段造船工艺的步骤和特点。
一、分段制造步骤1. 设计方案确定:在分段造船工艺开始之前,首先需要确定船体的设计方案。
设计方案包括船舶的结构设计、管道系统设计、电气系统设计等。
这些设计方案将作为分段制造的依据。
2. 分段制造计划编制:根据设计方案,制定分段制造计划。
计划包括分段的数量、尺寸、制造工艺和装配顺序等。
分段制造计划的编制需要考虑到船体的结构强度、制造工艺的可行性以及工期的安排等因素。
3. 材料准备:在分段制造之前,需要准备好所需的材料。
这些材料包括钢板、型钢、焊材、涂料等。
材料的选择需要根据设计要求和船舶的使用环境来确定。
4. 分段制造:根据分段制造计划,将船体分成若干个独立的模块进行制造。
制造过程包括钢板切割、型钢加工、焊接、校直和涂装等。
每个模块的制造过程需要严格按照设计要求和工艺规范进行。
5. 分段装配:分段制造完成后,将各个模块进行装配。
装配过程包括模块之间的焊接、螺栓连接、管道安装、设备安装等。
装配的顺序需要根据设计要求和工艺规范来确定,以确保各个模块能够准确无误地连接在一起。
6. 分段试验:在分段装配完成后,需要进行分段试验。
试验内容包括结构强度试验、水密性试验、设备功能试验等。
试验的目的是验证分段制造和装配的质量,以确保船体的安全性和可靠性。
二、分段造船工艺的特点1. 提高生产效率:分段造船工艺将船体分成若干个模块,不同模块可以同时制造和装配,大大提高了生产效率。
同时,分段制造可以将船体制造的风险和难度分散到各个模块中,降低了制造过程中的错误和损失。
2. 灵活性和可控性强:分段造船工艺使船舶建造过程更加灵活和可控。
每个模块都是独立制造和装配的,可以根据需要进行调整和优化。
同时,分段制造可以根据工期和资源的限制来安排制造计划,确保项目的顺利进行。
船制造工艺
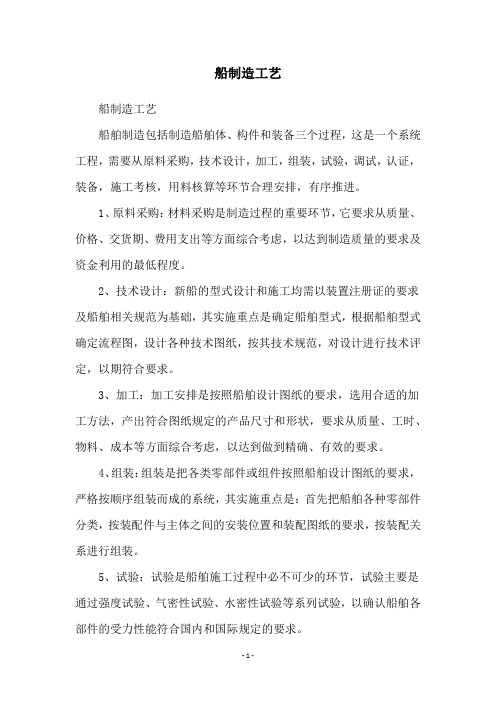
船制造工艺船制造工艺船舶制造包括制造船舶体、构件和装备三个过程,这是一个系统工程,需要从原料采购,技术设计,加工,组装,试验,调试,认证,装备,施工考核,用料核算等环节合理安排,有序推进。
1、原料采购:材料采购是制造过程的重要环节,它要求从质量、价格、交货期、费用支出等方面综合考虑,以达到制造质量的要求及资金利用的最低程度。
2、技术设计:新船的型式设计和施工均需以装置注册证的要求及船舶相关规范为基础,其实施重点是确定船舶型式,根据船舶型式确定流程图,设计各种技术图纸,按其技术规范,对设计进行技术评定,以期符合要求。
3、加工:加工安排是按照船舶设计图纸的要求,选用合适的加工方法,产出符合图纸规定的产品尺寸和形状,要求从质量、工时、物料、成本等方面综合考虑,以达到做到精确、有效的要求。
4、组装:组装是把各类零部件或组件按照船舶设计图纸的要求,严格按顺序组装而成的系统,其实施重点是:首先把船舶各种零部件分类,按装配件与主体之间的安装位置和装配图纸的要求,按装配关系进行组装。
5、试验:试验是船舶施工过程中必不可少的环节,试验主要是通过强度试验、气密性试验、水密性试验等系列试验,以确认船舶各部件的受力性能符合国内和国际规定的要求。
6、调试:调试是船舶主机件装备的过程,主要指主机件和配套各种装备的组装,此时要求检查船舶的起动、操作运行情况,调试各项主机和设备,确保试车前的安全可靠运行。
7、认证:认证是确认船舶合格的过程,需要经过系列步骤的证明,审核船舶设计文件、试验报告、体系文件等,最后经过各类检测和试验,确定满足法律规定及接受船舶施工的要求后发放合格证书。
8、装备:装备是把备件、辅料等装配到船舶上,要求从备件型号的选择,以及备件的安装位置等方面综合考虑,以达到船舶在维护、保养、操作等方面的要求。
9、施工考核:施工考核是检查船舶施工质量的过程,需要从施工过程中进行实际检查,结合图纸、技术标准及其他相关资料,对船舶各种结构件的施工质量进行评估,最终确定船舶施工质量是否符合要求。
造船工艺流程
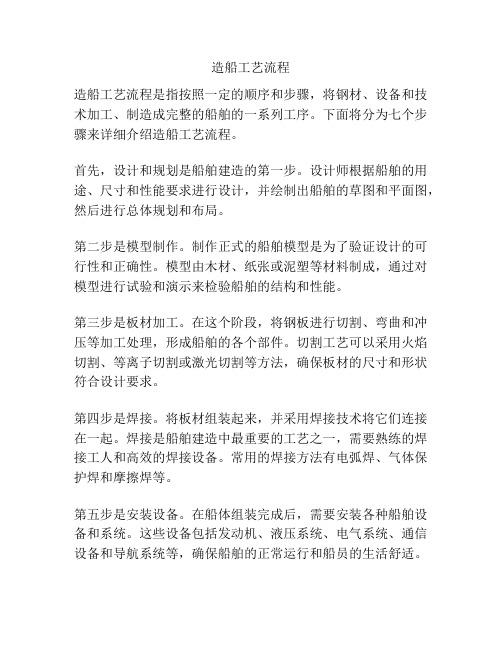
造船工艺流程造船工艺流程是指按照一定的顺序和步骤,将钢材、设备和技术加工、制造成完整的船舶的一系列工序。
下面将分为七个步骤来详细介绍造船工艺流程。
首先,设计和规划是船舶建造的第一步。
设计师根据船舶的用途、尺寸和性能要求进行设计,并绘制出船舶的草图和平面图,然后进行总体规划和布局。
第二步是模型制作。
制作正式的船舶模型是为了验证设计的可行性和正确性。
模型由木材、纸张或泥塑等材料制成,通过对模型进行试验和演示来检验船舶的结构和性能。
第三步是板材加工。
在这个阶段,将钢板进行切割、弯曲和冲压等加工处理,形成船舶的各个部件。
切割工艺可以采用火焰切割、等离子切割或激光切割等方法,确保板材的尺寸和形状符合设计要求。
第四步是焊接。
将板材组装起来,并采用焊接技术将它们连接在一起。
焊接是船舶建造中最重要的工艺之一,需要熟练的焊接工人和高效的焊接设备。
常用的焊接方法有电弧焊、气体保护焊和摩擦焊等。
第五步是安装设备。
在船体组装完成后,需要安装各种船舶设备和系统。
这些设备包括发动机、液压系统、电气系统、通信设备和导航系统等,确保船舶的正常运行和船员的生活舒适。
第六步是涂装和防腐。
在船体组装和设备安装完成后,需要进行涂装和防腐处理,以保护船舶的外部和内部结构免受海水和腐蚀的侵害。
涂装工序包括底漆、中漆和面漆的涂装,防腐工序包括防腐涂料的喷涂和涂覆。
最后一步是试航。
在船舶建造完成后,需要进行试航试验,以验证船舶的性能和功能是否符合设计要求。
试航中会测试船舶的各项指标,包括航行速度、转向性能和操纵性等。
一切正常后,船舶就可以交付给船东或船运公司。
综上所述,造船工艺流程包括设计和规划、模型制作、板材加工、焊接、安装设备、涂装和防腐,以及试航等七个步骤。
每个步骤都需要经过精确的计划和高效的操作,以确保船舶的质量和性能符合要求。
造船工艺是一项复杂而精细的工作,需要专业的技术人员和设备的支持。
船舶制造生产车间造船工艺
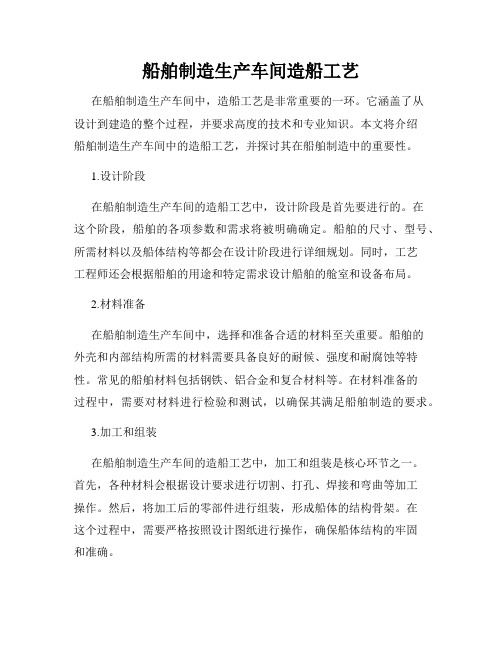
船舶制造生产车间造船工艺在船舶制造生产车间中,造船工艺是非常重要的一环。
它涵盖了从设计到建造的整个过程,并要求高度的技术和专业知识。
本文将介绍船舶制造生产车间中的造船工艺,并探讨其在船舶制造中的重要性。
1.设计阶段在船舶制造生产车间的造船工艺中,设计阶段是首先要进行的。
在这个阶段,船舶的各项参数和需求将被明确确定。
船舶的尺寸、型号、所需材料以及船体结构等都会在设计阶段进行详细规划。
同时,工艺工程师还会根据船舶的用途和特定需求设计船舶的舱室和设备布局。
2.材料准备在船舶制造生产车间中,选择和准备合适的材料至关重要。
船舶的外壳和内部结构所需的材料需要具备良好的耐候、强度和耐腐蚀等特性。
常见的船舶材料包括钢铁、铝合金和复合材料等。
在材料准备的过程中,需要对材料进行检验和测试,以确保其满足船舶制造的要求。
3.加工和组装在船舶制造生产车间的造船工艺中,加工和组装是核心环节之一。
首先,各种材料会根据设计要求进行切割、打孔、焊接和弯曲等加工操作。
然后,将加工后的零部件进行组装,形成船体的结构骨架。
在这个过程中,需要严格按照设计图纸进行操作,确保船体结构的牢固和准确。
4.设备安装船舶制造生产车间中的造船工艺还包括设备的安装。
根据船舶类型和用途,不同的设备将被安装在适当的位置上。
这些设备包括动力装置、电气设备、通信设备等。
在安装过程中,需要严格遵循相关安全规范,确保设备的正常运作和乘员的安全。
5.涂装和抛光涂装和抛光是船舶制造中的最后一道工艺。
在涂装过程中,船体表面会被清洁、防锈和喷涂保护性涂层。
这些涂层可以增加船体的耐久性,延长使用寿命。
而抛光则会使船体表面更加光滑,降低水流阻力,提高航行效率。
船舶制造生产车间的造船工艺对于船舶制造具有至关重要的作用。
它能够确保船舶的质量和性能达到设计要求,并提高生产效率和工艺水平。
通过合理应用和优化造船工艺,能够提高船舶制造的竞争力,满足市场需求。
综上所述,船舶制造生产车间中的造船工艺是船舶制造过程中不可或缺的一部分。
船舶建造施工工艺
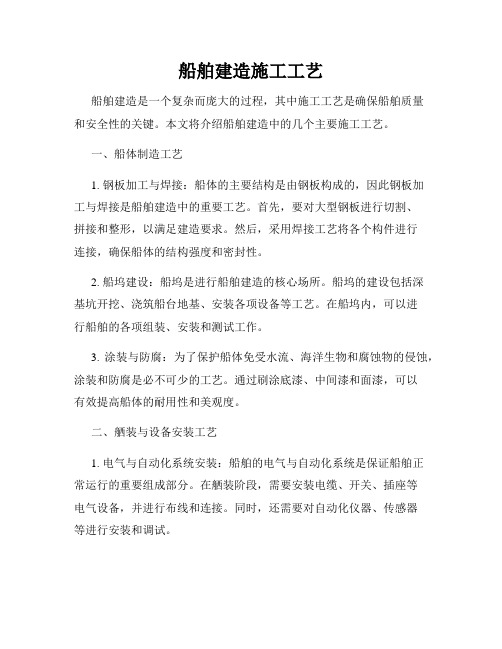
船舶建造施工工艺船舶建造是一个复杂而庞大的过程,其中施工工艺是确保船舶质量和安全性的关键。
本文将介绍船舶建造中的几个主要施工工艺。
一、船体制造工艺1. 钢板加工与焊接:船体的主要结构是由钢板构成的,因此钢板加工与焊接是船舶建造中的重要工艺。
首先,要对大型钢板进行切割、拼接和整形,以满足建造要求。
然后,采用焊接工艺将各个构件进行连接,确保船体的结构强度和密封性。
2. 船坞建设:船坞是进行船舶建造的核心场所。
船坞的建设包括深基坑开挖、浇筑船台地基、安装各项设备等工艺。
在船坞内,可以进行船舶的各项组装、安装和测试工作。
3. 涂装与防腐:为了保护船体免受水流、海洋生物和腐蚀物的侵蚀,涂装和防腐是必不可少的工艺。
通过刷涂底漆、中间漆和面漆,可以有效提高船体的耐用性和美观度。
二、舾装与设备安装工艺1. 电气与自动化系统安装:船舶的电气与自动化系统是保证船舶正常运行的重要组成部分。
在舾装阶段,需要安装电缆、开关、插座等电气设备,并进行布线和连接。
同时,还需要对自动化仪器、传感器等进行安装和调试。
2. 管道与通风系统安装:船舶的管道和通风系统包括给水管道、排水管道、燃油管道、空调通风系统等。
这些系统的安装需要严格按照设计要求进行,确保系统的正常运行和船舶内部环境的适宜性。
3. 船舶设备安装:船舶上涉及到各种设备,如发动机、推进器、锚具、舵机等。
在设备安装过程中,需要考虑设备的定位、安装和连接方式,确保其功能正常且与船舶其他系统协调配合。
三、舾装与内部装饰工艺1. 船舱隔舱板安装:船舶内部的船舱需要安装隔舱板,以便划分出不同的区域。
隔舱板可以采用钢板、玻璃钢板和木质板材等材料,通过螺栓连接或焊接固定。
2. 内饰装饰工艺:为了提高船舶的舒适度和美观度,内部装饰工艺至关重要。
这包括墙壁、天花板、地板、家具等的安装和装饰处理,同时还需考虑船舶的防火、防水和隔音要求。
四、试航与交付工艺1. 试航准备:在船舶建造完成后,需要进行试航前的准备工作。
简述船舶制造工艺的概念

简述船舶制造工艺的概念船舶制造工艺是指将设计好的船舶图纸或模型转化为实际船舶的过程,它包括了从材料准备、构件制作、组装、安装、调试到交付的全过程。
船舶制造工艺不仅涉及到各种加工技术和方法,还包括对船舶结构、强度、工艺质量等方面的要求和控制。
船舶制造工艺是整个船舶制造流程的核心环节之一,它直接决定了船舶的质量和性能。
船舶制造工艺的质量好坏,将直接影响到船舶的航行安全、寿命以及维修保养的难易程度。
因此,船舶制造工艺在船舶设计和制造过程中具有重要的地位和意义。
船舶制造工艺主要包括以下几个方面:1. 材料准备:船舶制造过程中使用的主要材料是钢材、铝合金、复合材料等。
在船舶制造工艺中,材料的准备是基础工作,包括按照设计要求选择合适的材料、对材料进行切割、整形等工艺处理。
2. 构件制作:构件制作是船舶制造工艺的关键环节,它涉及到各种加工工艺和技术,如切割、焊接、铆接、钻孔、翻边、成型等。
构件的制作质量直接影响到船舶的结构强度和工艺质量。
同时,在船舶制造过程中应按照一定的工艺要求对构件进行表面处理,如除锈、防腐、涂装等。
3. 组装和安装:构件制作后,需要进行组装和安装。
组装是指将各构件按照设计要求进行拼装,形成船体的骨架结构。
安装则是将各种设备和系统安装到船体上,包括主机设备、船舶电气设备、通信设备、导航设备、生活设备等。
在组装和安装过程中,需要对船体和设备进行定位和调整,确保各部件的精确配合。
4. 调试和检验:船舶组装和安装完成后,还需要进行调试和检验。
调试是指对船舶设备和系统进行功能检测和调整,确保其正常运行。
检验则是对船舶的结构强度、工艺质量等进行检查和验收。
船舶的调试和检验不仅需要满足相关标准和规范,还需要按照航海性能要求进行试航和验船。
5. 交付和售后服务:船舶制造工艺的最后一步是交付和售后服务。
交付是指将船舶交给船东或用户使用。
在交付前,需进行相关的文件和手续办理。
售后服务包括对船舶的定期维护、维修和改装等。
船舶工业中的先进制造技术与工艺

船舶工业中的先进制造技术与工艺随着科技的不断发展与进步,船舶工业中也出现了越来越多的先进制造技术和工艺。
这些技术和工艺对于提高船舶制造效率、优化产品质量以及保证安全性都发挥了巨大的作用。
本文将就船舶工业中的先进制造技术与工艺进行详细的探讨。
1. 3D打印技术随着3D打印技术的日益成熟,其在船舶制造行业中已经得到了广泛的应用。
利用3D打印技术,可以实现零部件的快速制造,极大地提高了制造效率。
同时,该技术还可以减少零部件的重量,提高船舶的载重量。
此外,3D打印技术可以创建更加复杂的零部件,并且可以制造出更具创新性的设计。
2. 数控制造技术数控制造技术是船舶制造行业中一项非常重要的技术。
该技术可以实现复杂零部件的精密加工,提高了工作效率。
同时,数控技术可以保证零部件制造的精度,从而提高了产品质量。
此外,数控机床还具有自动化的特点,能够减少人工干预,提高了生产效率。
3. 脉冲功率激光焊接技术脉冲功率激光焊接技术是一项非常先进的船舶制造技术。
利用该技术可以实现高质量焊接,同时还可以减少对工件的影响,从而减轻了工件的变形程度。
此外,脉冲功率激光焊接技术还可以保证焊接的速度,从而提高了生产效率。
该技术在船舶制造行业中的应用已经越来越广泛。
4. 无损检测技术无损检测技术是船舶制造行业中非常重要的一项技术。
通过无损检测技术可以快速发现隐蔽的缺陷,保证产品的质量。
同时,该技术还可以避免对产品结构的影响,从而降低了零部件的损坏程度。
船舶制造行业中的无损检测技术已经得到了广泛的应用。
5. 氧化铝堆焊技术氧化铝堆焊技术是船舶制造行业中一项非常实用的技术。
利用该技术可以快速对船舶上的零部件进行堆焊,从而提高了产品的质量。
氧化铝堆焊技术还可以保证零部件之间的相互匹配,并且能够保证产品的密封性。
该技术的应用已经得到了船舶制造业的广泛认可。
6. 摩擦振动焊接技术摩擦振动焊接技术是船舶制造行业中的一项非常新颖的技术。
该技术可以实现高效、快速的焊接,同时还可以保证产品的质量。
船的制造工艺流程

船的制造工艺流程
《船的制造工艺流程》
船是人类在水上生存和活动中使用最多的交通工具之一,它的制造工艺是非常复杂的。
下面将介绍船的制造工艺流程。
1. 设计阶段:船的制造工艺流程的第一步是设计阶段。
在设计阶段,工程师和设计师们会根据客户的需求和船的用途制定船舶的设计方案。
他们会考虑船的尺寸、船体形状、船体材料、舱室布局、推进系统和船舶特性等因素,最终确定船舶的整体设计方案。
2. 材料准备:在设计完成后,船的制造工艺流程进入到材料准备阶段。
船体所需的材料通常包括钢材、铝合金、复合材料等。
这些材料需要经过切割、成形和加工等工艺,以满足船体结构的要求。
3. 钢结构制造:对于钢质船舶来说,钢结构的制造是关键的一步。
钢板需要在制造车间进行切割、焊接、翻转等工艺步骤,最终组装成船体的基本结构。
4. 装配阶段:一旦船体结构完成,就需要进行船舶的装配工作。
这包括船舶的电气设备安装、推进系统的装配、管道系统的安装等工序。
5. 油漆和防腐处理:船体制造完成后,需要进行油漆和防腐处理工艺。
这可以保护船体不受腐蚀、延长船舶的使用寿命。
6. 舾装和配件安装:最后,船的制造工艺流程进入到舾装和配件安装阶段。
这包括船舶的内饰装饰、船舶设备的安装等工序,使船舶完全装配完成。
总的来说,船的制造工艺流程包括设计、材料准备、钢结构制造、装配、油漆和防腐处理、舾装和配件安装等多个阶段。
这些工艺步骤相互配合、相互依赖,最终形成了一艘完整的船舶。
船舶制造工艺与装备技术的制造工艺设备
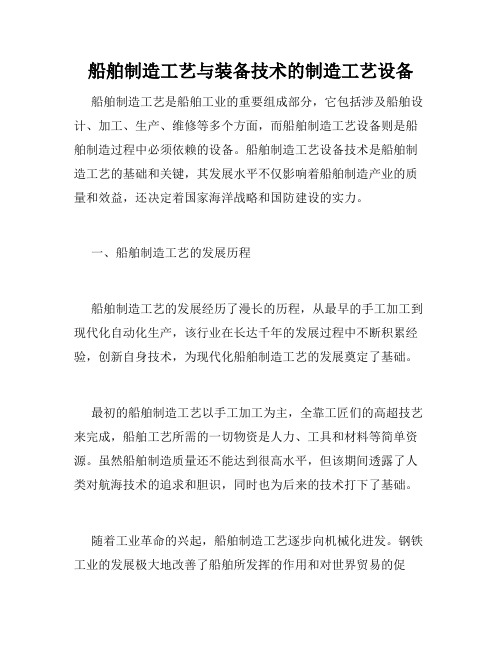
船舶制造工艺与装备技术的制造工艺设备船舶制造工艺是船舶工业的重要组成部分,它包括涉及船舶设计、加工、生产、维修等多个方面,而船舶制造工艺设备则是船舶制造过程中必须依赖的设备。
船舶制造工艺设备技术是船舶制造工艺的基础和关键,其发展水平不仅影响着船舶制造产业的质量和效益,还决定着国家海洋战略和国防建设的实力。
一、船舶制造工艺的发展历程船舶制造工艺的发展经历了漫长的历程,从最早的手工加工到现代化自动化生产,该行业在长达千年的发展过程中不断积累经验,创新自身技术,为现代化船舶制造工艺的发展奠定了基础。
最初的船舶制造工艺以手工加工为主,全靠工匠们的高超技艺来完成,船舶工艺所需的一切物资是人力、工具和材料等简单资源。
虽然船舶制造质量还不能达到很高水平,但该期间透露了人类对航海技术的追求和胆识,同时也为后来的技术打下了基础。
随着工业革命的兴起,船舶制造工艺逐步向机械化进发。
钢铁工业的发展极大地改善了船舶所发挥的作用和对世界贸易的促进。
当时半自动化设备为船舶制造做出了重大贡献,同时也为进一步的自动化发展打下了基础。
二、现代化船舶制造工艺设备技术现代化船舶制造工艺是基于机械化加工,使用世界先进的船舶制造设备,对传统制造工艺不断优化、创新,并需要加强计算机控制、精密工程技术等多种技术因素的结合。
现代化船舶制造设备的发展,可以归纳成五大类:1. 喷射成形技术大型船舶板件喷丸清理技术是机械化处理中极为重要的工艺之一,目前市面上所使用的喷射设备种类有着非常多种。
This list includes 同时,喷射技术还可以与赋形技术相结合,实现对船舶各种部件,如船桅,船体和产品一般外观质量的统一管理。
2. 铣切加工设备船舶加工铣切技术能够直接用于大型板片的加工,小版块的精密加工和塑料制品等的加工。
铣切加工技术成为高于传统的技术方案,主要体现在采用CAD/CAE/CAM多种技术手段进行设计和模拟的过程中,辅以CNC编程和加工技术等确保加工精度等方面。
船舶制造工艺

(4)首尾分段 (5)上层建筑等 3、分段制作阶段建造组织措施: (1)严格按批量顺序下料: 船体结构分段一般分 20 多个批次进行投料。在网络计划安排中按吊装顺序依次组织分段制作, 这是由建造法决定的。 塔式建造法: 以尾部近机舱前的一个底部分段作为基准段在船台搭载,然后向首、尾及两舷自下而上依序吊装 各分段。由于机舱分段需要安装大量设备、管路,所以需要尽早成型并吊装。 岛式建造法: 为缩短建造周期,将船体沿船长划分成 2—3 个建造区(岛),在每个建造区选择一个分段为基准 段,按塔式建造法组织建造,岛与岛之间利用“嵌补分段”进行连接。 串联建造法(一条半造船法): 当船台长度大于船长 1.5 倍,且是批量建造情况下,可以在建造第一艘船的前半段的同时,在 船台的前端建造第二艘船的尾段。待第一艘船下水后,第二艘船的尾段也完工,并移至船台尾端继续 建造其前半段,同时第三艘船的尾段又在船台的前端建造。 总段建造法: 将预先装配焊接好的环形总段按照安装顺序进行船台装配。船厂在具有大型船坞、并有总组场地 和起重能力予以保证情况下,采用总段建造法可以有效利用各主要生产资源。 (2)贯彻总装造船原则: 为充分发挥船厂主要生产设施(船台、船坞、总组场地和起重设备等)能力,应将生产主流程即 组织流水线生产的项目留在厂内,能够以中间产品组织生产和供应的次流程项目,尽可能以“分包” 形式扩散到厂外,实行“专业化生产、社会化配套”。“分包”指的是购买劳务,由船厂提供材料、图 纸、进行工艺和质量监督,分包商提供加工后的中间产品,这些产品船厂不是不能制造,而是出于经 济、负荷特别是总体效率等原因,主动将其交给分包商去制造。 (3)执行分段成品化交验: 按照“壳舾涂一体化”要求,在分段制作阶段,应将该部位的铁舾件、管舾件、电气焊接件尽可 能地全部安装上去,并完成分段涂装工事。在分段下胎交验时,上下道工序必须依据清单进行逐项检 查确认,尽可能减少施工项目在工序间的流转。分段成品化制作,虽然加大了该阶段的工作量,但从 能率测算看,同一工事项目工时消耗量,在分段舾装阶段、船台舾装阶段、水下舾装阶段的比例为— —1:5:9。目前国内船厂分段予舾装率(铁舾予舾装率、管舾予舾装率)在 80—90%左右,而日韩 船厂接近 100% 。 (4)扩大总组吊装数量:
钳工技术在船舶制造中的关键工艺与要点
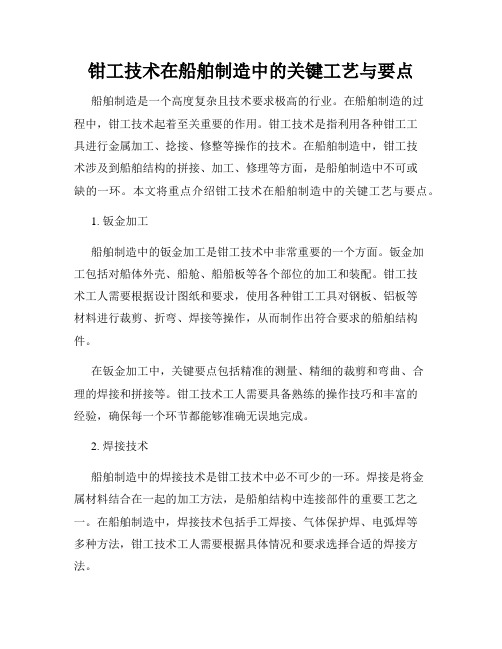
钳工技术在船舶制造中的关键工艺与要点船舶制造是一个高度复杂且技术要求极高的行业。
在船舶制造的过程中,钳工技术起着至关重要的作用。
钳工技术是指利用各种钳工工具进行金属加工、捻接、修整等操作的技术。
在船舶制造中,钳工技术涉及到船舶结构的拼接、加工、修理等方面,是船舶制造中不可或缺的一环。
本文将重点介绍钳工技术在船舶制造中的关键工艺与要点。
1. 钣金加工船舶制造中的钣金加工是钳工技术中非常重要的一个方面。
钣金加工包括对船体外壳、船舱、船船板等各个部位的加工和装配。
钳工技术工人需要根据设计图纸和要求,使用各种钳工工具对钢板、铝板等材料进行裁剪、折弯、焊接等操作,从而制作出符合要求的船舶结构件。
在钣金加工中,关键要点包括精准的测量、精细的裁剪和弯曲、合理的焊接和拼接等。
钳工技术工人需要具备熟练的操作技巧和丰富的经验,确保每一个环节都能够准确无误地完成。
2. 焊接技术船舶制造中的焊接技术是钳工技术中必不可少的一环。
焊接是将金属材料结合在一起的加工方法,是船舶结构中连接部件的重要工艺之一。
在船舶制造中,焊接技术包括手工焊接、气体保护焊、电弧焊等多种方法,钳工技术工人需要根据具体情况和要求选择合适的焊接方法。
在焊接技术中,关键要点包括焊接电流和电压的控制、焊接速度的把握、焊接接头的质量检测等。
钳工技术工人需要具备严谨的工作态度和细致的操作技巧,确保焊接接头的牢固性和质量。
3. 钻孔和螺纹加工船舶制造中的钻孔和螺纹加工是钳工技术中不可或缺的一环。
钻孔和螺纹加工是船舶结构件上的连接孔和连接螺纹的制作工艺,是船舶组装的关键环节之一。
钳工技术工人需要根据设计要求和图纸指导,使用各种钻孔和螺纹加工工具对金属材料进行加工,确保孔径和螺距的准确度和精度。
在钻孔和螺纹加工中,关键要点包括钻头和螺纹刀具的选择、加工速度和压力的控制、孔径和螺距的检测等。
钳工技术工人需要具备耐心和细心的品质,确保每一个孔和每一根螺纹都符合要求。
4. 总装与调试船舶制造的最后阶段是总装与调试,钳工技术在这一阶段同样扮演着重要的角色。
船舶制造工艺

船舶建造管理讲座之一船舶建造工艺流程简介一、造船生产管理模式的演变由焊接代替铆接建造钢质船,造船生产经历了从传统造船向现代造船的演变,主要推动力是造船技术的发展。
传统造船分两个阶段:1、常规的船体建造和舾装阶段。
在固定的造船设施上先安装龙骨系统、再安装肋骨框、最后装配外板系统等。
2、由于焊接技术的引进,船体实行分段建造;舾装分为两个阶段:分段舾装和船上舾装,即开展予舾装。
现代造船又历经以下阶段:3、由于成组技术的引进,船体实行分道建造;舾装分为三个阶段:单元舾装、分段舾装和船上舾装,即开展区域舾装。
4、由于船体建造和舾装、涂装相互结合组织,实现“壳舾涂一体化总装造船”。
5、随着造船技术的不断发展,精益造船、标准造船、数字造船、绿色造船将成为船厂的努力方向。
目前国内主要船厂一般处于三级向四级过渡阶段;国内先进船厂已达到四级水平;而象上海外高桥船厂、建设中的江南长兴岛造船基地明确提出将精益造船、标准造船、数字造船、绿色造船作为发展目标。
二、船舶建造工艺流程(一)现代造船工艺流程如下简图。
(二)船舶建造工艺流程层次上的划分依据1、生产大节点开工——上船台(铺底)——下水(出坞)——航行试验——完工交船生产大节点在工艺流程中是某工艺阶段的开工期(或上一个节点的完工期),工艺阶段一般说是两个节点间的施工期。
生产大节点的期限是编制和执行生产计划的基点,框定了船舶建造各工艺阶段的节拍和生产周期;从经营工作看,节点的完成日也是船东向船厂分期付款的交割日。
2、工艺阶段钢材预处理——号料加工——零、部件装配——分段装焊——船台装焊(合拢)——拉线镗孔——船舶下水——发电机动车——主机动车——系泊试验——航海试验——完工交船3、以上工艺阶段还可以进一步进行分解。
4、工艺说明需要说明的是以上工艺阶段是按船舶建造形象进度划分的,现代造船工艺流程是并行工程,即船体建造与舾装作业是并行分道组织,涂装作业安排在分道生产线的两个小阶段之间,船体与舾装分道生产线在各阶段接续地汇入壳舾涂一体化生产流程。
船舶建造工艺流程简要介绍

船舶建造工艺流程简要介绍1.船舶设计:在开始船舶建造之前,首先需要进行船舶设计。
船舶设计师根据船舶的用途和要求制定船舶的设计方案,包括船舶的结构、外形、尺寸等。
设计完成后,会进行结构强度计算和流体力学模拟等分析,以确保船舶的安全性和性能。
2.制造船体:船舶建造的第一步是制造船体。
制造船体采用的材料通常是钢材,可以使用钢板进行焊接和组装。
首先,在船台上安装构架,然后一层一层地焊接钢制骨架和壳体。
同时,需要做好防锈处理和船舶排水系统的安装。
3.安装主要设备:主要设备包括主机、辅机、锅炉、发电机等。
安装这些设备需要进行精确的定位和调整,以确保设备正常运转和船舶性能的优化。
同时,需要进行管道的布置和安装,以保证各种系统的正常运行。
4.安装甲板设备:甲板设备包括起重设备、舱口门、缆锚设备、导航设备等。
这些设备的安装需要根据设计要求进行精确调整,同时需要对船体进行必要的加固和支撑,以确保设备的安全和船舶的稳定性。
5.配线和安装设备:船舶内部的配线和设备安装是船舶建造的重要环节。
根据设计要求,进行电缆的敷设和布线工作,安装各种仪表和控制设备,以保证船舶的正常运行和操作。
6.舾装:舾装是指船舶内饰装修工作。
包括船舶的墙面、天花板、地板和船舱的布置等。
这些工作是为了舒适和美观,旨在提供良好的居住和工作环境。
7.舾装测试和调整:舾装完成后,需要进行各项测试和调整工作。
包括船舶的平衡性测试、设备的功能测试、电气系统的测试等。
通过测试,发现问题并进行调整,以确保船舶的安全和性能。
8.船舶试航和验收:船舶建造完成后,需要进行试航和验收工作。
试航是为了检验船舶的各项性能和操作性,包括速度、操纵性、航行稳定性等。
验收是交付船舶给船东的最后一步,验收人员根据设计要求和合同规定,对船舶的各项指标进行检验和确认。
以上是船舶建造工艺流程的简要介绍。
船舶建造是一个复杂而精细的工序,需要各个环节密切配合和精确控制,以确保船舶的质量和性能。
船舶制造工艺与装备技术的制造工艺流程

船舶制造工艺与装备技术的制造工艺流程船舶制造工艺是制造船舶的核心科技,它将许多机械、电气、材料、结构等多种工艺技术综合运用,对船舶生产的各个环节进行精密把控。
在船舶制造工艺中,装备技术扮演着非常重要的角色,这项技术能够有效提升船舶制造的效率和质量。
下面,我们将会对船舶制造工艺与装备技术的制造工艺流程进行一些介绍。
一、设计与准备船舶制造工艺的第一步是进行设计,这个过程需要依据船舶的种类、规格、用途等多种信息。
完成设计后,就需要进行材料的准备工作。
船舶的制造材料一般都是钢铁、铝合金或者复合材料等,需要提前按照设计要求进行裁剪,打制成制造零件。
二、制造零件接下来,就是制造零件的工序。
这个工序需要使用各种机械、设备和工具,将材料加工成船舶的各个零部件。
这个过程需要精确地进行测量、切割、钻孔、铆接、焊接等多项工艺技术。
三、组装整体制造零件的工序完成后,就需要将它们组装成整体。
在组装整体的过程中,需要使用大型起重机等机械设备,将重量较大的零部件进行装配。
同时,也需要进行检查以确保零部件的精度符合要求。
四、封闭船体装配完成后,就需要对船舶进行封闭。
这个过程需要利用专业的封舱材料,将船体水密地封闭。
这个过程需要在密封的情况下对船舶进行真空泵抽取,以去除船内的空气,从而使封舱材料与船体紧密贴合。
五、涂装与防腐在完成封舱的过程中,也需要进行涂装和防腐的工作。
这个工序需要对船体进行洗刷、喷涂、打磨等准备工作,之后再通过特殊的涂装技术进行防污防腐处理。
六、安装设备船舶制造工艺中的一个非常重要的环节就是安装各种设备。
船舶的设备种类繁多,需要进行分类安装。
例如,船首需要安装导航雷达、控制仪器等设备;船体需要安装生活舱、动力系统、速度控制器等设备;船尾需要安装推进器、方向盘等设备。
七、试航与验收到了这个工序,就需要对船舶进行试航。
试航可以测试船舶在不同海况下的性能,以及设备是否正常运行等问题。
完成试航后,就需要对船舶进行全面的验收。
船舶制造工艺的研究与应用
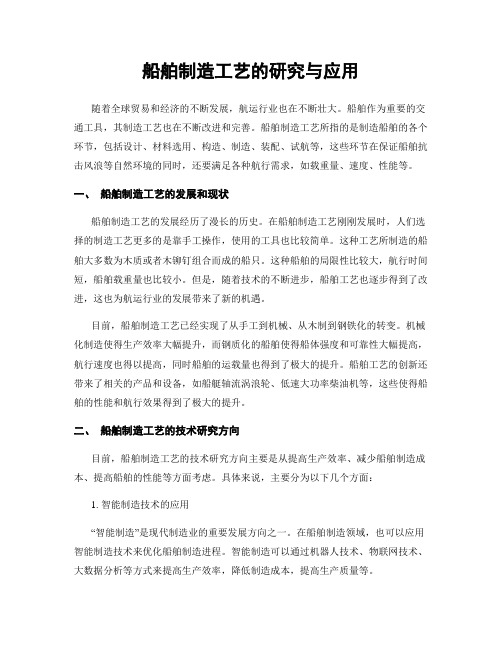
船舶制造工艺的研究与应用随着全球贸易和经济的不断发展,航运行业也在不断壮大。
船舶作为重要的交通工具,其制造工艺也在不断改进和完善。
船舶制造工艺所指的是制造船舶的各个环节,包括设计、材料选用、构造、制造、装配、试航等,这些环节在保证船舶抗击风浪等自然环境的同时,还要满足各种航行需求,如载重量、速度、性能等。
一、船舶制造工艺的发展和现状船舶制造工艺的发展经历了漫长的历史。
在船舶制造工艺刚刚发展时,人们选择的制造工艺更多的是靠手工操作,使用的工具也比较简单。
这种工艺所制造的船舶大多数为木质或者木铆钉组合而成的船只。
这种船舶的局限性比较大,航行时间短,船舶载重量也比较小。
但是,随着技术的不断进步,船舶工艺也逐步得到了改进,这也为航运行业的发展带来了新的机遇。
目前,船舶制造工艺已经实现了从手工到机械、从木制到钢铁化的转变。
机械化制造使得生产效率大幅提升,而钢质化的船舶使得船体强度和可靠性大幅提高,航行速度也得以提高,同时船舶的运载量也得到了极大的提升。
船舶工艺的创新还带来了相关的产品和设备,如船艇轴流涡浪轮、低速大功率柴油机等,这些使得船舶的性能和航行效果得到了极大的提升。
二、船舶制造工艺的技术研究方向目前,船舶制造工艺的技术研究方向主要是从提高生产效率、减少船舶制造成本、提高船舶的性能等方面考虑。
具体来说,主要分为以下几个方面:1. 智能制造技术的应用“智能制造”是现代制造业的重要发展方向之一。
在船舶制造领域,也可以应用智能制造技术来优化船舶制造进程。
智能制造可以通过机器人技术、物联网技术、大数据分析等方式来提高生产效率,降低制造成本,提高生产质量等。
2. 材料的选用与应用材料的选用对于船舶制造的质量和性能有很大影响,目前,船舶制造业正逐步向复合材料、大型铸造等领域转变。
其中,在复合材料中,纤维增强复合材料(FRP)被认为是船舶制造领域的重要材料,因为它具有良好的强度、韧性和耐腐蚀性能。
3. 舾装设计优化舾装设计是船舶制造的重要环节之一。
2024年船舶制造工艺培训资料
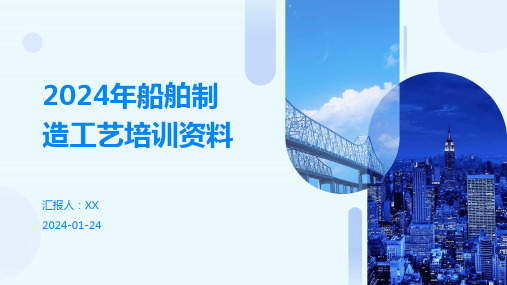
消防设备
用于船舶火灾的预防 和应急救援,包括灭 火器、消防泵、消防 水带等部分。
舾装设备安装工艺流程
安装前准备
熟悉图纸和安装工艺要求,准备安装 所需的工具和设备,检查设备的质量 和完整性。
设备安装
按照图纸和工艺要求,将设备安装在 指定的位置,并进行初步的固定和调 整。
调试与测试
对安装完成的设备进行调试和测试, 确保其正常运转和符合设计要求。
安全防护措施及应急处理
安全防护设施
配备齐全的安全防护设施,如安全警示标识、防护栏、安全帽等 ,确保员工人身安全。
安全操作规程
制定详细的安全操作规程,对员工进行安全培训,提高员工安全意 识。
应急处理措施
建立完善的应急处理机制,包括应急预案制定、应急演练、应急救 援等,确保在突发事件发生时能够迅速响应,减少损失。
工艺特点
船舶制造涉及大量金属材料的加工和焊接,对精度和质量要求高,同时需要应 对复杂的海洋环境,因此具有独特的工艺特点,如大型化、高精度、高可靠性 等。
船舶制造行业现状及发展趋势
行业现状
当前,全球船舶制造市场呈现多元化格局,亚洲地区逐渐成 为船舶制造的中心。随着环保要求的提高和新能源技术的发 展,绿色、智能船舶成为行业发展的重要方向。
2024年船舶制 造工艺培训资料
汇报人:XX 20体结构与建造工艺 • 舾装设备与安装工艺 • 涂装与防腐技术 • 焊接技术与质量控制 • 生产管理与安全保障
01
CATALOGUE
船舶制造工艺概述
船舶制造流程及工艺特点
船舶制造流程
包括初步设计、详细设计、生产设计、材料采购、加工制造、装配调试、试航 交船等阶段。
A
B
C
船舶建造工艺流程
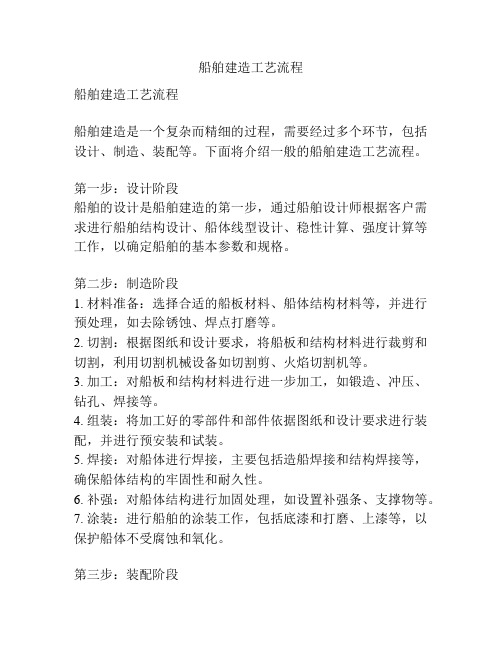
船舶建造工艺流程船舶建造工艺流程船舶建造是一个复杂而精细的过程,需要经过多个环节,包括设计、制造、装配等。
下面将介绍一般的船舶建造工艺流程。
第一步:设计阶段船舶的设计是船舶建造的第一步,通过船舶设计师根据客户需求进行船舶结构设计、船体线型设计、稳性计算、强度计算等工作,以确定船舶的基本参数和规格。
第二步:制造阶段1. 材料准备:选择合适的船板材料、船体结构材料等,并进行预处理,如去除锈蚀、焊点打磨等。
2. 切割:根据图纸和设计要求,将船板和结构材料进行裁剪和切割,利用切割机械设备如切割剪、火焰切割机等。
3. 加工:对船板和结构材料进行进一步加工,如锻造、冲压、钻孔、焊接等。
4. 组装:将加工好的零部件和部件依据图纸和设计要求进行装配,并进行预安装和试装。
5. 焊接:对船体进行焊接,主要包括造船焊接和结构焊接等,确保船体结构的牢固性和耐久性。
6. 补强:对船体结构进行加固处理,如设置补强条、支撑物等。
7. 涂装:进行船舶的涂装工作,包括底漆和打磨、上漆等,以保护船体不受腐蚀和氧化。
第三步:装配阶段1. 机电设备装配:将各类船舶机电设备,如发动机、燃油系统、电气设备、舵机等安装到船体内部。
2. 船舶设施安装:安装各类船舶设施,如舱室、舱门、舷窗等。
3. 舱内装饰:进行舱室的内部装饰,包括地板、墙面、天花板、家具等的安装。
4. 船舶系统调试:对船体进行系统调试,确保各类设备正常运行。
第四步:试航阶段在船舶建造完成后,需要进行试航以验证船舶的性能和安全性,主要包括船舶的航行性能、操纵性能,以及各类设备的运行状况等。
第五步:交付阶段船舶建造完成并通过试航后,进行最后的验收和交付工作。
在交付阶段,船舶建造方需向客户交付船舶,并提供相关的船舶资料和证书。
总结:船舶建造工艺流程是一个复杂而精细的过程,需要经过设计、制造、装配、试航等多个环节。
只有在每个环节都严格按照要求操作,并进行合理的协调和配合,才能保证船舶建造的质量和安全性。
- 1、下载文档前请自行甄别文档内容的完整性,平台不提供额外的编辑、内容补充、找答案等附加服务。
- 2、"仅部分预览"的文档,不可在线预览部分如存在完整性等问题,可反馈申请退款(可完整预览的文档不适用该条件!)。
- 3、如文档侵犯您的权益,请联系客服反馈,我们会尽快为您处理(人工客服工作时间:9:00-18:30)。
二、船舶建造工艺流程
(一)现代造船工艺流程如下简图。
(二)船舶建造工艺流程层次上的划分依据 1、生产大节点 开工——上船台(铺底)——下水(出坞)——航行试验——完工交船 生产大节点在工艺流程中是某工艺阶段的开工期(或上一个节点的完工期),工艺阶段一般说是
两个节点间的施工期。生产大节点的期限是编制和执行生产计划的基点,框定了船舶建造各工艺阶段 的节拍和生产周期;从经营工作看,节点的完成日也是船东向船厂分期付款的交割日。
船舶建造管理讲座之一 船舶建造工艺流程简介
一、造船生产管理模式的演变
由焊接代替铆接建造钢质船,造船生产经历了从传统造船向现代造船的演变,主要推动力是造船 技术的发展。
传统造船分两个阶段: 1、常规的船体建造和舾装阶段。在固定的造船设施上先安装龙骨系统、再安装肋骨框、最后装 配外板系统等。 2、由于焊接技术的引进,船体实行分段建造;舾装分为两个阶段:分段舾装和船上舾装,即开 展予舾装。 现代造船又历经以下阶段: 3、由于成组技术的引进,船体实行分道建造;舾装分为三个阶段:单元舾装、分段舾装和船上 舾装,即开展区域舾装。 4、由于船体建造和舾装、涂装相互结合组织,实现“壳舾涂一体化总装造船”。 5、随着造船技术的不断发展,精益造船、标准造船、数字造船、绿色造船将成为船厂的努力方 向。 目前国内主要船厂一般处于三级向四级过渡阶段;国内先进船厂已达到四级水平;而象上海外高 桥船厂、建设中的江南长兴岛造船基地明确提出将精益造船、标准造船、数字造船、绿色造船作为发 展目标。
三、船舶建造过程的控制(应用于现代造船模式)
(一)钢料加工阶段 1、钢料加工过程 钢材备料——钢材预处理线(矫平、喷砂除锈、底漆件成型加工(非平直构件加工成应有曲度)——船体零部件装配(平面接板、 框架组立)。
2、船厂比较关注的问题 (1)钢料供应。船厂是钢材消耗大户,从产业关系看应该与钢厂建立利益共享的战略伙伴关系。 如有的船厂与钢厂签订了长期合作协议,每年锁定一个钢材基价,既减少了受钢材市场价格波动影响, 并能够保证供货期限和数量;有的船厂享有钢材优惠价格(如每吨下浮 50 元);还有的钢厂直接投 资船厂成为股东单位等。 (2)钢料加工应形成分道加工的路径。大型船厂为组织分段组装流水线生产,在钢料加工阶段 就要求相应加工后的构件定向、有序地传输到平面分段流水线、曲面分段流水线和型材加工流水线。 在大连船务钢料加工车间:平直构件加工、带曲度构件加工压制、型材加工及弯制、构件小组立等, 已形成划分明确的加工区域。 (3)提高钢材利用率是船厂降本增效永恒的主题。目前国内船厂钢材利用率(主船体钢材利用 率、钢材综合利用率)一般在 85—90%左右,其中中远川崎达到 94%,日本船厂可达到 95%以上。钢 材利用率状况受到船型及设计、管理、场地等多因素影响。 努力开展船体与舾装同步设计,以提高一次套料利用率; 在钢料加工中心留有充分的余料堆放、分检、再利用场地,一是可调用余料进行二次套料;二是 利用余料切割法兰、肘板、人孔盖等预制件;三是调用余料补充工装。 尽可能根据用料尺寸,多规格在钢厂组织定尺订货(这是日本船厂保持高水平利用率的优势)。 (二)分段制作阶段 1、分段是构成船体结构的实体。根据船舶建造工艺、场地条件、起重能力、周期要求等,一艘 3—6 万吨级船舶分段划分大致在 100—200 个(大型船体结构如 MPF1000 钻井储油船分段划分 351 个)。 2、分段名称 分段按几何特征可分为: (1)平面分段:平面板列带有骨架的单层平面板架; (2)曲面分段:平面板列带有骨架的单层曲面板架; (3)半立体分段:两层或两层以上板架所组成的不封闭分段; (4)立体分段:两层或两层以上板架所组成的封闭分段; (5)总段:主船体沿船长划分,其深度和宽度等于该处船深和船宽的环形分段。特别需要指出 的是:立体分段和总段是由若干平面分段和曲面分段所组成,由于平面分段和曲面分段是分段建造中 的基本单位,作为船舶建造主流程,必须组织流水线生产。 分段按其结构所属部位可分为: (1)底部分段 (2)舷侧分段 (3)甲板分段
(4)首尾分段 (5)上层建筑等 3、分段制作阶段建造组织措施: (1)严格按批量顺序下料: 船体结构分段一般分 20 多个批次进行投料。在网络计划安排中按吊装顺序依次组织分段制作, 这是由建造法决定的。 塔式建造法: 以尾部近机舱前的一个底部分段作为基准段在船台搭载,然后向首、尾及两舷自下而上依序吊装 各分段。由于机舱分段需要安装大量设备、管路,所以需要尽早成型并吊装。 岛式建造法: 为缩短建造周期,将船体沿船长划分成 2—3 个建造区(岛),在每个建造区选择一个分段为基准 段,按塔式建造法组织建造,岛与岛之间利用“嵌补分段”进行连接。 串联建造法(一条半造船法): 当船台长度大于船长 1.5 倍,且是批量建造情况下,可以在建造第一艘船的前半段的同时,在 船台的前端建造第二艘船的尾段。待第一艘船下水后,第二艘船的尾段也完工,并移至船台尾端继续 建造其前半段,同时第三艘船的尾段又在船台的前端建造。 总段建造法: 将预先装配焊接好的环形总段按照安装顺序进行船台装配。船厂在具有大型船坞、并有总组场地 和起重能力予以保证情况下,采用总段建造法可以有效利用各主要生产资源。 (2)贯彻总装造船原则: 为充分发挥船厂主要生产设施(船台、船坞、总组场地和起重设备等)能力,应将生产主流程即 组织流水线生产的项目留在厂内,能够以中间产品组织生产和供应的次流程项目,尽可能以“分包” 形式扩散到厂外,实行“专业化生产、社会化配套”。“分包”指的是购买劳务,由船厂提供材料、图 纸、进行工艺和质量监督,分包商提供加工后的中间产品,这些产品船厂不是不能制造,而是出于经 济、负荷特别是总体效率等原因,主动将其交给分包商去制造。 (3)执行分段成品化交验: 按照“壳舾涂一体化”要求,在分段制作阶段,应将该部位的铁舾件、管舾件、电气焊接件尽可 能地全部安装上去,并完成分段涂装工事。在分段下胎交验时,上下道工序必须依据清单进行逐项检 查确认,尽可能减少施工项目在工序间的流转。分段成品化制作,虽然加大了该阶段的工作量,但从 能率测算看,同一工事项目工时消耗量,在分段舾装阶段、船台舾装阶段、水下舾装阶段的比例为— —1:5:9。目前国内船厂分段予舾装率(铁舾予舾装率、管舾予舾装率)在 80—90%左右,而日韩 船厂接近 100% 。 (4)扩大总组吊装数量: