标准化工作-Standardized work
精益 六西格玛 标准化工作 Standard Work

6
Why Standardized Work ?为什么要标准化工作?
Eliminate Waste. 消除浪费
3
DMA I C
Lean6Sigma Phases精益六西格玛的阶段
This module is most applicable to the DMAIC phases of
改进阶段
ANALYZE and IMPROVE这个模块最适合DMAIC的分析和
Define
Control
Measure
Improve
Heijunka
均衡化
Standardized Work
标准化工作
Stability稳定性
Kaizen
改善
The Toyota Production System
丰田生5 产系统
What is Standardized Work ?什么是标准化工作?
DMA I C
An effective and orderly method of producing without waste. 一个没有浪 费,并且是有效和有序的生产方法
目标:最高的质量,最低的成本,最短的交货期
Just-in-Time
准时生产
Jidoka
DMA I C
Continuous Flow连续流
Takt Time
节拍时间
Pull System
拉动系统
Stop and notify of abnormalities停止、通报变异
Separate man’s work and machine’s work 人机工作分离
DMA I C
1. What is the takt time at the pacemaker?什么是节拍点的节拍时间Can the equipment support takt time?设备是否能支持节拍时间?
标准化作业流程英文缩写

标准化作业流程英文缩写SOP: The Essence of Standardized Work Processes.In the realm of business operations and management, the acronym "SOP" holds immense significance. SOP, which stands for "Standard Operating Procedure," is a set of step-by-step instructions that guide employees in carrying out routine tasks and activities within a company. These procedures aim to ensure consistency, efficiency, and compliance with industry standards or regulatory requirements.The concept of SOPs dates back to the industrial revolution, when manufacturers realized the need for standardizing production processes to increase efficiency and reduce waste. Over time, SOPs have evolved to become a crucial component of any organization seeking to optimize its operations.The Importance of SOPs.SOPs are essential for several reasons. Firstly, they provide a clear and concise reference for employees, ensuring that tasks are performed correctly and consistently. This consistency is crucial in maintainingthe quality of products or services offered by a company.Secondly, SOPs act as a training tool for new employees. By following the SOP, newcomers can quickly familiarize themselves with the company's operations and procedures, enabling them to integrate into the workforce more smoothly.Moreover, SOPs contribute to safety and compliance. In industries like healthcare or manufacturing, where safety regulations are stringent, SOPs ensure that employeesadhere to safety protocols, reducing the risk of accidentsor compliance violations.Creating Effective SOPs.Crafting effective SOPs requires a thorough understanding of the tasks involved and the objectives theyaim to achieve. Here are some key considerations when developing SOPs:1. Detail Orientation: SOPs should provide detailed step-by-step instructions, ensuring that employees know exactly what to do and how to do it.2. Clarity and Conciseness: The language used in SOPs should be clear and concise, avoiding technical jargon or ambiguous phrasing.3. Flexibility: While SOPs provide a framework for operations, they should also allow for some flexibility to adapt to changing conditions or circumstances.4. Regular Updates: SOPs should be regularly reviewed and updated to reflect changes in processes, technology, or regulations.The Role of SOPs in Different Industries.SOPs play a pivotal role in various industries, eachwith its unique challenges and requirements.In the healthcare industry, SOPs are crucial for ensuring patient safety and compliance with strict regulatory standards. For instance, in a hospital setting, SOPs govern procedures like patient intake, medication dispensing, and surgical operations, ensuring that patients receive the highest quality of care.In the manufacturing sector, SOPs are essential for maintaining production efficiency and quality control. From assembly line procedures to quality inspection protocols, SOPs ensure that products are manufactured tospecifications and meet industry standards.In the financial industry, SOPs govern processes like client intake, investment advice, and risk management. These procedures aim to protect client interests, ensure transparency, and comply with financial regulations.Challenges and Solutions in Implementing SOPs.Despite their benefits, implementing SOPs can pose some challenges. One common issue is employee resistance, particularly among those who have been performing tasks for years using their own methods. To overcome this resistance, companies need to communicate the benefits of SOPs clearly and involve employees in the development process, making them feel like stakeholders in the changes.Another challenge is ensuring that SOPs are updated and maintained over time. As processes change or new technologies emerge, it's crucial to review and revise SOPs accordingly. This requires a dedicated team or individual responsible for monitoring changes and updating the SOPs as needed.Conclusion.In conclusion, SOPs are a vital component of any organization seeking to achieve operational excellence. They provide a framework for consistent, efficient, and compliant task execution, contributing to improved quality, safety, and employee training. By investing in thedevelopment and maintenance of SOPs, companies can ensure that their operations run smoothly, adapt to changing environments, and remain competitive in their respective industries.。
质量方法有哪些
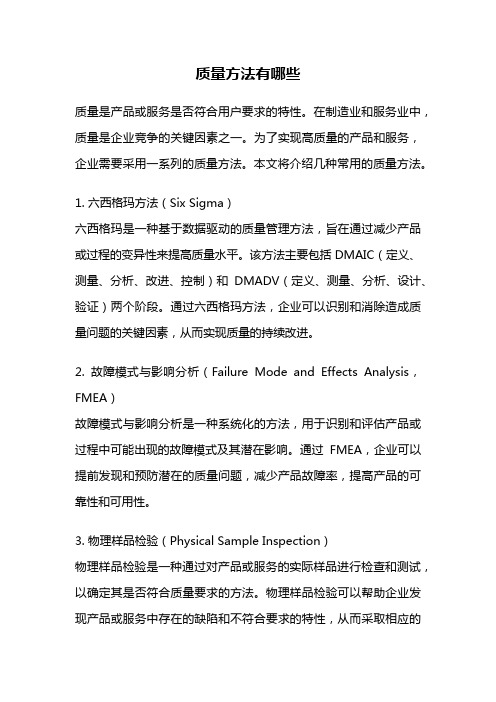
质量方法有哪些质量是产品或服务是否符合用户要求的特性。
在制造业和服务业中,质量是企业竞争的关键因素之一。
为了实现高质量的产品和服务,企业需要采用一系列的质量方法。
本文将介绍几种常用的质量方法。
1. 六西格玛方法(Six Sigma)六西格玛是一种基于数据驱动的质量管理方法,旨在通过减少产品或过程的变异性来提高质量水平。
该方法主要包括DMAIC(定义、测量、分析、改进、控制)和DMADV(定义、测量、分析、设计、验证)两个阶段。
通过六西格玛方法,企业可以识别和消除造成质量问题的关键因素,从而实现质量的持续改进。
2. 故障模式与影响分析(Failure Mode and Effects Analysis,FMEA)故障模式与影响分析是一种系统化的方法,用于识别和评估产品或过程中可能出现的故障模式及其潜在影响。
通过FMEA,企业可以提前发现和预防潜在的质量问题,减少产品故障率,提高产品的可靠性和可用性。
3. 物理样品检验(Physical Sample Inspection)物理样品检验是一种通过对产品或服务的实际样品进行检查和测试,以确定其是否符合质量要求的方法。
物理样品检验可以帮助企业发现产品或服务中存在的缺陷和不符合要求的特性,从而采取相应的措施进行改进。
4. 统计过程控制(Statistical Process Control,SPC)统计过程控制是一种基于统计方法的质量控制方法,用于监控和控制生产过程中的变异性。
通过SPC,企业可以实时监测生产过程中的关键参数,并及时采取措施纠正偏差,以确保产品的质量稳定性。
5. 5W1H分析法5W1H分析法是一种常用的问题分析方法,通过回答“什么、为什么、谁、何时、何地、如何”这六个问题,来深入了解问题的本质和根本原因。
通过5W1H分析,企业可以找出导致质量问题的关键因素,并采取相应的措施进行改进。
6. 标准化工作(Standardized Work)标准化工作是一种通过制定和遵守标准化的工作程序和方法,以实现质量的稳定性和一致性的方法。
标准化工作定义
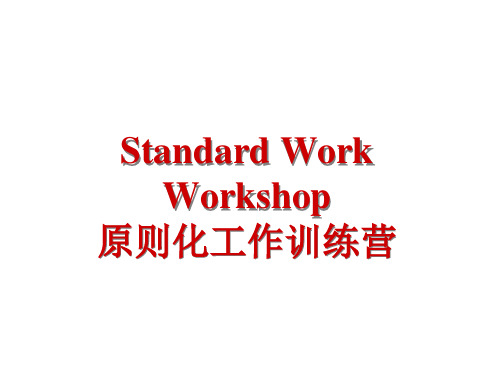
Standardized Work 原则化作业
Wait Time:等待时间
The time the operator waits while the machine completes its function
操作工等待机器完毕其操作旳时间
Standardized Work 原则化作业
目的: 实际周期
目的周期
TAKT时间
Target Cycle Time目的周期 = Takt time- special allowances特殊耗时
Actual Cycle Time = The time it takes an operator to complete one cycle of standard work. The longest operator’s actual cycle time tells us how many parts the cell is capable of running
Less 4 breaks per day @ 10 min. each
减 4次休息 = 40 min
Total Available Time
总可用时间 = 920 min
920 minutes X 60 seconds = 55,200 seconds Takt Time = 55,200sec / 1504 units = 36.7 seconds
40”
240” 40%
Part A 356” x .25 = 89” Part B 300” x .35 = 105” Part C 240” x .40 = 96”
290” Weighted Average 加权平均旳
精益管理的六大要素
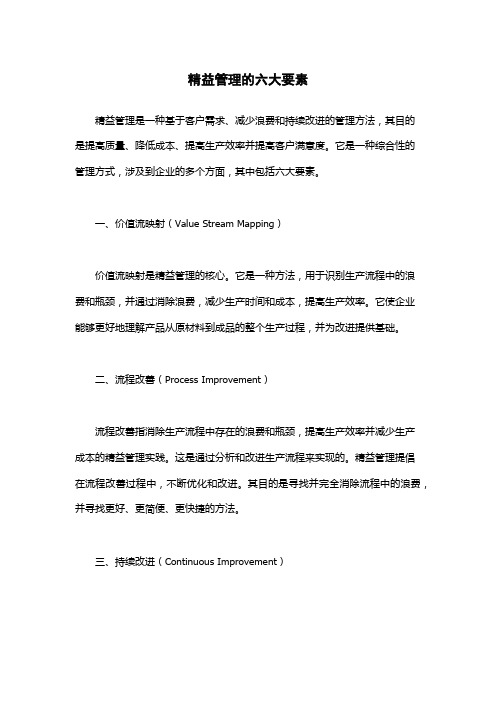
精益管理的六大要素精益管理是一种基于客户需求、减少浪费和持续改进的管理方法,其目的是提高质量、降低成本、提高生产效率并提高客户满意度。
它是一种综合性的管理方式,涉及到企业的多个方面,其中包括六大要素。
一、价值流映射(Value Stream Mapping)价值流映射是精益管理的核心。
它是一种方法,用于识别生产流程中的浪费和瓶颈,并通过消除浪费,减少生产时间和成本,提高生产效率。
它使企业能够更好地理解产品从原材料到成品的整个生产过程,并为改进提供基础。
二、流程改善(Process Improvement)流程改善指消除生产流程中存在的浪费和瓶颈,提高生产效率并减少生产成本的精益管理实践。
这是通过分析和改进生产流程来实现的。
精益管理提倡在流程改善过程中,不断优化和改进。
其目的是寻找并完全消除流程中的浪费,并寻找更好、更简便、更快捷的方法。
三、持续改进(Continuous Improvement)精益管理强调持续改进,不断挖掘和消除生产流程中的浪费和瓶颈,并寻求更好的方法来提高生产效率和质量。
它强调通过员工参与,推动改进,使持续改进成为一种企业文化。
四、标准化工作(Standardized Work)标准化工作是确保生产过程中每个员工都按照相同的标准工作方法和流程进行工作的方法。
标准化工作通过减少误差和提高效率,改善了生产流程中的质量和生产效率。
精益管理鼓励通过标准化工作来实现生产流程的稳定性。
五、建立高可靠性的供应链(Establishing a Reliable Supply Chain)建立高可靠性的供应链是精益管理的关键要素之一。
精益管理通过与供应商合作,建立高可靠性的供应链,将其视为整个生产流程的一部分。
它认为高可靠性的供应链可以帮助企业减少浪费,提高质量,并提高生产效率。
六、优化生产资源(Optimizing Production Resources)优化生产资源是通过消除不必要的资源使用和改善生产流程来提高生产效率的方法。
生产现场改善8个技巧

生产现场改善8个技巧1. 价值流图法(Value Stream Mapping):通过绘制价值流图,清晰地展示了整个生产流程中的价值、非价值和浪费步骤,从而可以针对性地进行改进。
通过消除浪费,提高工作流程,使得生产现场运转更加高效。
2.5S工作法:5S工作法分别是整理、整顿、清扫、清洁、素养的五个步骤。
这种方法通过减少时间浪费和杂乱无章的情况,提高工作效率,同时还有助于改善安全和质量问题。
3. 精益生产(Lean Production):精益生产是一种以减少资源浪费为中心的生产方式。
它通过去除无价值的步骤,减少库存,实现适应性和灵活性,提高效率和质量。
该方法可以通过改进生产流程,降低生产成本,并提高客户满意度。
4. 产能平衡(Capacity Balancing):产能平衡是指在生产过程中对工作站的工作负荷进行合理分配,以实现流程平衡。
通过产能平衡,可以避免生产线上的过度和不足,提高各个工作站的效率和产品质量。
5. 标准化工作(Standardized Work):标准化工作是通过制定一系列规程和标准来规范工作流程。
这种方法可以提供一种明确的、可复制的工作流程,使生产现场的工作更加高效和一致。
6.人员培训和技能提升:通过为员工提供培训和技能提升的机会,可以提高他们的生产能力和工作效率。
这包括传授新的生产技术、培养团队合作精神和解决问题的能力等。
7. 持续改进(Continuous Improvement):持续改进是指通过定期评估和改进生产工艺和流程来提高效率和质量。
这需要建立一种改进的文化,鼓励员工提出改进建议,并与他们一起制定和实施改进计划。
8.自动化和数字化技术的应用:通过引入自动化和数字化技术,可以大大提高生产效率和质量水平。
这包括使用机器人和自动化设备来替代手工操作,使用数据分析来优化生产过程,以及使用物联网技术来实现生产过程的实时监控。
通过采用以上八个技巧,可以有效改善生产现场,提高生产效率和产品质量,并最终提高企业的竞争力和市场份额。
工厂质量管理及QC七大手法

工厂质量管理及QC七大手法工厂质量管理及QC七大手法质量控制(Quality Control, QC)是指通过有效管理和控制过程中的各个环节,确保产品或服务能够达到预期的质量要求。
工厂质量管理及QC七大手法,是指在工厂质量管理过程中常用的七种重要方法。
下面将分别介绍这七大手法。
首先,质量控制圆圈法(Quality Control Circle, QCC)是一种由质量控制小组组成的持续改进方法。
该方法鼓励员工积极参与到质量改进活动中,通过小组成员的集体智慧和努力,不断改善工作过程和方法,提高产品质量。
第二,标准化工作方法(Standardized Work, SW)是指通过制定统一的工作流程和操作规范,确保每个员工都能按照相同的标准进行工作。
标准化工作方法的实施可以提高工作效率、降低误操作风险,从而提高产品质量。
第三,统计质量控制方法(Statistical Quality Control, SQC)是一种利用统计方法来分析和控制质量的方法。
通过采集和分析大量的质量数据,可以对生产过程进行全面的质量控制,从而及时发现和纠正潜在的质量问题,提高产品质量水平。
第四,故障模式与影响分析(Failure Mode and Effects Analysis, FMEA)是一种通过对潜在故障模式和其影响进行分析,预防和排除产品设计和生产过程中的潜在质量问题的方法。
通过FMEA的应用,可以有效降低产品故障率,提高产品可靠性和质量。
第五,质量成本管理(Quality Cost Management, QCM)是一种通过统计和分析质量相关的各种成本,以期能够全面认识和控制产品或服务质量追求所产生和可能产生的各种成本。
通过合理控制质量成本,可以提高产品或服务的性价比,进而提高市场竞争力。
第六,流程管制(Statistical Process Control, SPC)是一种通过对生产过程中的关键参数进行实时监控和及时调整,以确保产品质量稳定的方法。
精益生产管理的十大工具和实施步骤

精益生产管理的十大工具和实施步骤一、价值流分析(Value Stream Mapping):价值流分析是了解和改进产品或服务的价值流程的方法。
通过绘制价值流地图,可以清楚地看到从原料到最终交付的整个价值流程,以及其中存在的浪费和瓶颈。
通过分析和改进价值流程,可以实现生产过程的优化。
二、5S整理法:5S整理法是一种是一种工作环境整理和管理方法。
通过整理、整顿、清扫、标准化和维护这五个步骤,可以创造一个整洁、有序、高效的工作环境,提高工作效率和质量。
三、流程改进活动(Kaizen):Kaizen是一种小创新的方法,通过持续改善工作流程,减少或消除浪费,提高效率和质量。
它鼓励员工提出改进建议,并通过小规模试验和迭代改进的方式,不断优化工作流程。
四、单点教导法(One-Piece Flow):单点教导法是一种用来实现流程连续化和缩短生产周期的方法。
通过将生产任务拆分为较小的单元,并且一个接一个地完成,可以减少库存和等待时间,提高生产效率和质量。
五、标准化工作(Standardized Work):标准化工作是一种明确工作内容和作业要求的方法。
通过对工作流程进行详细的规范和记录,包括工作步骤、所需时间和所需材料等,可以确保工作一致性和质量,减少浪费和错误。
六、自动化(Automation):自动化是一种利用机械装置和技术来替代人力的方法。
通过引入自动化设备和技术,可以实现生产过程的标准化和高度自动化,提高生产效率和稳定性。
七、质量管控(Quality Control):质量管控是一种确保产品或服务质量的方法。
通过建立质量控制流程和标准,进行检验和测试,可以及时发现和纠正质量问题,保证产品或服务的一致性和可靠性。
八、产能平衡(Capacity Balancing):产能平衡是一种调整生产线中各个工位和机器的产能,以适应需求变化的方法。
通过平衡各个工位和机器的产能,可以避免瓶颈和浪费,提高整个生产线的效率。
九、持续改进(Continuous Improvement):持续改进是一种通过不断寻找和解决问题,优化工作流程和提高效率的方法。
标准化作业与sop
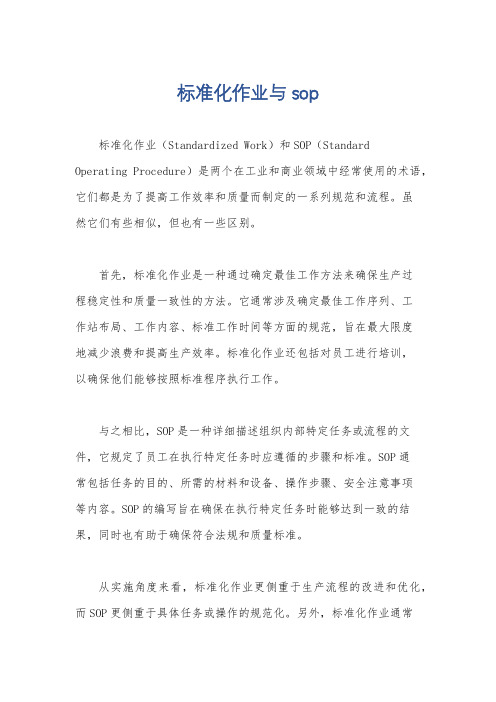
标准化作业与sop
标准化作业(Standardized Work)和SOP(Standard Operating Procedure)是两个在工业和商业领域中经常使用的术语,它们都是为了提高工作效率和质量而制定的一系列规范和流程。
虽
然它们有些相似,但也有一些区别。
首先,标准化作业是一种通过确定最佳工作方法来确保生产过
程稳定性和质量一致性的方法。
它通常涉及确定最佳工作序列、工
作站布局、工作内容、标准工作时间等方面的规范,旨在最大限度
地减少浪费和提高生产效率。
标准化作业还包括对员工进行培训,
以确保他们能够按照标准程序执行工作。
与之相比,SOP是一种详细描述组织内部特定任务或流程的文件,它规定了员工在执行特定任务时应遵循的步骤和标准。
SOP通
常包括任务的目的、所需的材料和设备、操作步骤、安全注意事项
等内容。
SOP的编写旨在确保在执行特定任务时能够达到一致的结果,同时也有助于确保符合法规和质量标准。
从实施角度来看,标准化作业更侧重于生产流程的改进和优化,而SOP更侧重于具体任务或操作的规范化。
另外,标准化作业通常
由生产部门或工程部门负责,而SOP通常由质量管理部门或专门的流程管理团队负责编写和更新。
总的来说,标准化作业和SOP都是为了确保工作流程的规范化和一致性,从而提高效率和质量。
它们在不同层面和领域都起着重要作用,是现代企业管理中不可或缺的工具。
供应链改善的精益工具和方法

供应链改善的精益工具和方法1. 价值流图(Value Stream Mapping):通过绘制一个流程图,揭示出整个供应链中的价值流和非价值流,从而识别出改进的机会。
2. 5S方法(Sort, Set in Order, Shine, Standardize, Sustain):通过对工作区域进行整理、整顿、清扫、标准化和维护,提高供应链的可视性和工作效率。
3. 标准化工作(Standardized Work):将工作步骤和流程标准化,以减少变异性和提高效率。
4. 连续流(Continuous Flow):通过降低批量和减少等待时间,实现供应链中的连续流动,并减少库存和提高交付速度。
5. 快速换模(Quick Changeover):通过优化设备换模过程,减少生产线的停机时间,从而提高供应链的灵活性和响应能力。
6. 平衡生产(Balanced Production):通过在生产线上平衡工作负载,消除瓶颈和浪费,以实现流程的平稳运行。
7. 拉动生产(Pull Production):基于客户需求,通过实施“只生产所需”原则,以最大限度地减少库存和减少等待时间。
8. 设备效率改善(Overall Equipment Effectiveness, OEE):通过优化设备的可用性、性能和质量,提高供应链中设备的效率和产能。
9. 过程改善(Process Improvement):通过分析和改善供应链中的关键流程,减少浪费、提高效率和质量。
10. 价值工程(Value Engineering):通过重新设计产品和流程,提高产品的价值和供应链的效益。
11. 周期时间分析(Cycle Time Analysis):通过分析和优化供应链中的各个步骤的周期时间,减少非价值增加时间,提高交付速度。
12. 批量优化(Batch Optimization):通过优化或减少批量大小,减少库存和降低生产成本。
13. 故障模式和影响分析(Failure Mode and Effects Analysis, FMEA):通过识别和分析供应链中的潜在故障模式和其影响,采取预防措施提前消除风险。
StandardWork标准作业PPT课件
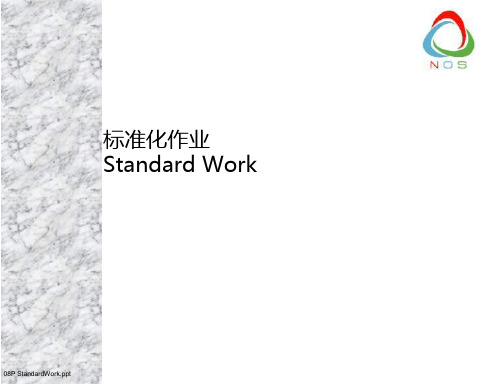
人机分析表 • Standardized Work Sheet
标准化作业书
9
Requirements of Standardized Work 标准化作业条件
Stability First! 稳定性第一
• The work station must be clean and organized
整洁的工作区域
• The work task must be repeatable
重复的操作
• The line and equipment must be reliable
可靠的生产线和设备
Quality 品质
Work 工作
标准化作业
Equipment 设备
Standard Work
10
Components of Standardized Work 标准化作业要件
• 定义并记录工作流程 • 确定的工作顺序和产出 • 为新员工提供最佳操作指示
• 流程稳定,顺畅,合乎标准 • 品质检查(自检)包含在标准作业中
Continuous
• 易于发现异常
Improvement • 改善的工具
持续改善
• 授权员工
…..终极目标是通过降低品质不良的成本提高工厂利
润
Standard Work
Standardized work sets the foundation for improvement. To apply lean tools, we must first know what we’re doing now – the state of current processes. 标准化作业是改善的基础。在运用LEAN工具进行改善前,我们先要了解现行 流程的状况。
精益生产十大技巧

精益生产十大技巧
1.价值流分析(Value Stream Mapping):通过绘制商品或服务
的价值流图,识别并消除生产过程中的浪费,提高生产效率和产品
质量。
2.单一流程布局(Single Piece Flow):推崇一次只处理一件产品,以最大程度减少库存和等待时间,提高生产速度和响应能力。
3.快速换模(___):通过优化设备布局和操作流程,尽可能减少产品切换的时间和成本,实现生产灵活性和多样化。
4.实施5S系统:通过整理、整顿、清扫、清洁和素养的五个
步骤,创造一个整洁有序的工作环境,提高工作效率和员工满意度。
5.标准化工作(Standardized Work):制定标准操作程序,并
不断监控和改进,确保每个工人都按照相同的方法高效完成工作。
6.提供员工培训和参与机会:培养员工的技术和问题解决能力,鼓励员工提出改进意见并参与决策过程,增强团队协作和改进动力。
7.收集和分析数据(Data n and Analysis):建立有效的数据收
集系统,对生产过程进行量化分析,发现并解决潜在问题,提高生
产效率和质量。
8.持续改进(Continuous Improvement):将改进作为一种文化,通过周期性评估和优化工作流程,实现持续的生产效率提升。
9.实施可视化管理(Visual Management):利用符号、标识和可视化工具,使生产过程信息透明化,促进信息传递和问题解决。
10.建立持久性团队(___):鼓励团队合作和知识共享,培养团队稳定性和承诺感,保持长期改进的动力和效果。
以上是精益生产的十大技巧,通过采用这些技巧,您可以优化生产流程、提高效率和质量,实现更加精益的生产方式。
标准化操作ppt课件
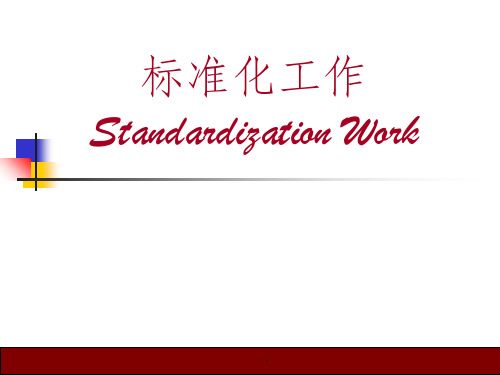
.
节拍时间(TAKT Time)
TAKT Time=
每班或每天的实际操作时间/每班或每天的客户需求量
例:每天一班实际操作时间是7小时10分钟 顾客要求一天600件产品
自动运送 -------------
--
80
1 ´ 00´´ 655
20
30´´
549
20
30´´
606
20
30´´
643
1,000 1,000
7 ´ 00´´ 820 7 ´ 00´´
500 5 ´ 00´´ 1947
.
能力表的编制说明
用秒表测定零部 件的完成时间
1. 工位顺序
2. 工序名称
3. 使用的机床编号
.
标准化工作的目标
通过有效率的劳动提高生产率 1. 通过热心的劳动实现较高的生产率 2. 实现与适时生产有关的各工序间的同步化(生产线平衡)
,为此,必须将“生产节拍”很好地贯穿到标准作业中去 3. 把在制品“标准在库量”限定在必要的最小数量
.
标准化工作的好处
1. 避免无效的动作,消除浪费,降低成本 2. 改善质量 3. 确保安全 4. 为持续改进提供基础 5. 使新人员的培训更为容易 6. 提供可视化管理控制
标准作 业顺序
TAKT Time
Work
Customer Cycle Time Sequence
.
标准 持有量
Standard Stock
确定标准作业的五个程序
❖ 确定周期时间 ❖ 确定一个单位产品的完成时间 ❖ 确定标准作业顺序 ❖ 确定在制品的标准持有量 ❖ 编制标准作业单
精益制造质量管理系统标准化作业模块ppt课件

工作场地的有序安排
=5S Workplace Organization
5 Self Discipline自律
4 Sustain保持 3 Sweep清扫 2 Sort整理 1 Sift筛选
10
标准化 Standardization
5S-筛选
5S-Sift
1,制定必需和非必需品的评判标准,消除不必要的工具,设备,材料和次品; Make judgement criteria for necessary and unnecessary, Eliminate non-essential tools, equipment , material and salvage.
不可在线上修复的缺陷
For defects that can nFilled in defect record and keep it 反馈给操作工 feedback to T/M
通知返修工段 Advise repair group
8
标准化 Standardization
: 可 疑 零 件
: 报 废 零 件
零
件
scrap dubious
repaired
线旁已不再使用的工具应去除 Tools (not used any more) attached with red label
可疑、报废零件分区域放置 Scrap/dubious part put in different colored area
Andon
操作工拉动暗灯T/M pull Andon 暗灯(Andon)=求助(HELP)
在什么时候拉动暗灯
WHEN PULL?
FPS
70% FPS
5
标准化 Standardization
车间常用英语
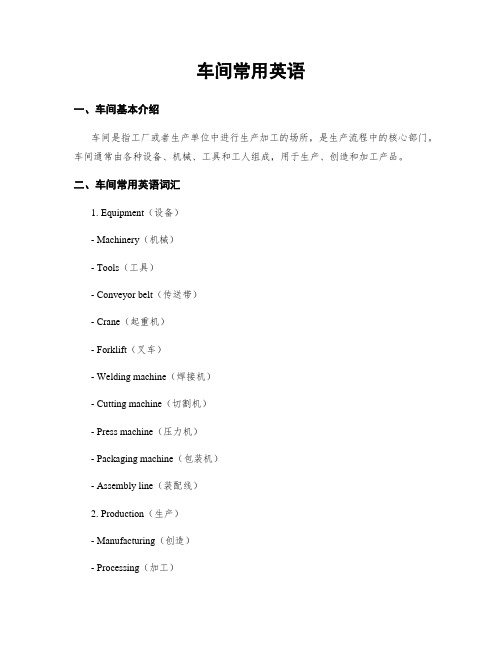
车间常用英语一、车间基本介绍车间是指工厂或者生产单位中进行生产加工的场所,是生产流程中的核心部门。
车间通常由各种设备、机械、工具和工人组成,用于生产、创造和加工产品。
二、车间常用英语词汇1. Equipment(设备)- Machinery(机械)- Tools(工具)- Conveyor belt(传送带)- Crane(起重机)- Forklift(叉车)- Welding machine(焊接机)- Cutting machine(切割机)- Press machine(压力机)- Packaging machine(包装机)- Assembly line(装配线)2. Production(生产)- Manufacturing(创造)- Processing(加工)- Assembly(装配)- Inspection(检查)- Quality control(质量控制)- Efficiency(效率)- Productivity(生产率)- Output(产量)- Waste reduction(减少浪费)3. Safety(安全)- Protective equipment(防护设备)- Safety goggles(安全护目镜)- Safety helmet(安全头盔)- Safety gloves(安全手套)- Fire extinguisher(灭火器)- Emergency exit(紧急出口)- First aid kit(急救箱)- Safety training(安全培训)- Hazardous materials(危(wei)险物质)- Accident prevention(事故预防)4. Production Process(生产流程)- Raw materials(原材料)- Work in progress(生产中的产品)- Finished products(成品)- Assembly instructions(装配说明)- Production schedule(生产计划)- Quality inspection(质量检查)- Packaging and labeling(包装和标签)- Inventory management(库存管理)- Order fulfillment(定单执行)- Shipping and logistics(运输和物流)5. Job Positions(职位)- Supervisor(主管)- Operator(操作员)- Technician(技术员)- Engineer(工程师)- Quality inspector(质检员)- Maintenance staff(维修人员)- Production planner(生产计划员)- Warehouse manager(仓库经理)- Logistics coordinator(物流协调员)- Safety officer(安全员)6. Communication(沟通)- Instructions(指示)- Report(报告)- Meeting(会议)- Announcement(公告)- Memorandum(备忘录)- Email(电子邮件)- Conversation(对话)- Training session(培训会议)- Feedback(反馈)- Collaboration(合作)7. Quality(质量)- Defect(缺陷)- Non-conformance(不符合)- Standard(标准)- Specification(规格)- Quality control plan(质量控制计划)- Quality assurance(质量保证)- Continuous improvement(持续改进)- Root cause analysis(根本原因分析)- Corrective action(纠正措施)- Customer satisfaction(客户满意度)8. Maintenance(维护)- Preventive maintenance(预防性维护)- Breakdown(故障)- Repair(修理)- Lubrication(润滑)- Calibration(校准)- Replacement(更换)- Troubleshooting(故障排除)- Downtime(停机时间)- Spare parts(备件)- Equipment reliability(设备可靠性)9. Lean Manufacturing(精益生产)- Waste(浪费)- 5S methodology(5S方法论)- Value stream mapping(价值流图)- Kaizen(改善)- Just-in-time (JIT)(准时生产)- Kanban system(看板系统)- Poka-yoke(防错)- Standardized work(标准化工作)- Continuous flow(连续流)- Visual management(可视化管理)10. Performance Evaluation(绩效评估)- Key performance indicators (KPIs)(关键绩效指标)- Productivity rate(生产率)- Efficiency ratio(效率比率)- Defect rate(缺陷率)- Downtime percentage(停机时间百分比)- Cycle time(生产周期)- OEE (Overall Equipment Effectiveness)(设备综合效率)- Scrap rate(废品率)- Employee turnover rate(员工流动率)- Customer complaints(客户投诉)三、结语以上是车间常用英语的一些词汇和表达,通过学习这些常用术语,您可以更好地理解和参预车间的工作和沟通。
BIQS_标准作业培训
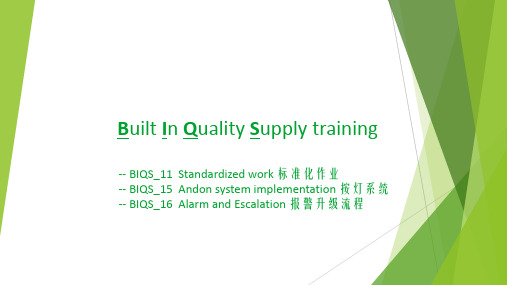
Run-Stop Switch and Light
Andon Pull Cord 4
Yellow Workstation
Light
R U N ST OP
Work Cell Example
Yellow
Workstation Light
14
Run Stop
Button
Andon Push Button
审核关注点:
Standard Task Sheet
(STS) Defines entire job, Multiple TIS may support •CyScTlSettaimskes – Time required to complete SW for a job
•Actual takt time – Time required to meet customer demand with anticipated losses (overspeed)
Occurrence will vary based on process capability
(EXAMPLEs of A&E record sheet)
ALARM PROCESS FORM Example
11
要求:
对产品缺陷要有合理的报警界限,达到界限时 要进行问题升级。根据报警升级流程,对发生 的报警要有响应(反应计划)。
审核关
1.查看检查工位(检验工位/CARE/GP12)的报
警升级流程规定,确认报警界限和升级要求是 否合理。(对CARE/GP12,所有问题的报警界限 为1) 2.查看问题记录单和报警升级记录,确认报警升 级是否实施,响应是否及时有效。
• 标准化工作是不断改进的基线.
全面质量管理的方法
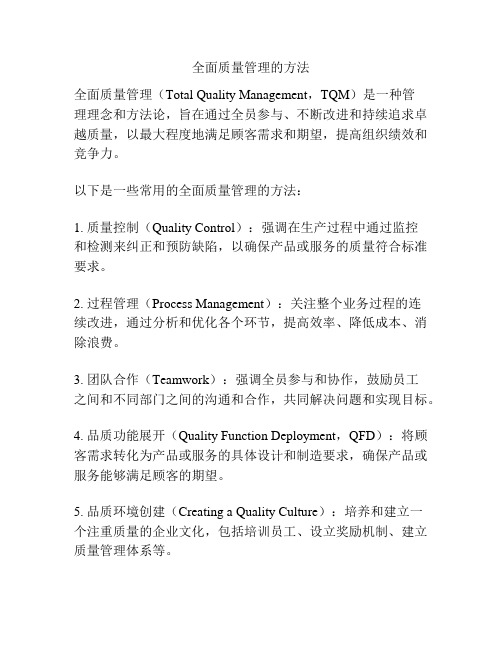
全面质量管理的方法全面质量管理(Total Quality Management,TQM)是一种管理理念和方法论,旨在通过全员参与、不断改进和持续追求卓越质量,以最大程度地满足顾客需求和期望,提高组织绩效和竞争力。
以下是一些常用的全面质量管理的方法:1. 质量控制(Quality Control):强调在生产过程中通过监控和检测来纠正和预防缺陷,以确保产品或服务的质量符合标准要求。
2. 过程管理(Process Management):关注整个业务过程的连续改进,通过分析和优化各个环节,提高效率、降低成本、消除浪费。
3. 团队合作(Teamwork):强调全员参与和协作,鼓励员工之间和不同部门之间的沟通和合作,共同解决问题和实现目标。
4. 品质功能展开(Quality Function Deployment,QFD):将顾客需求转化为产品或服务的具体设计和制造要求,确保产品或服务能够满足顾客的期望。
5. 品质环境创建(Creating a Quality Culture):培养和建立一个注重质量的企业文化,包括培训员工、设立奖励机制、建立质量管理体系等。
6. 不断改进(Continuous Improvement):推动组织持续不断地改进和创新,通过小步快跑的改进活动来提高质量、效率和创新能力。
7. 供应链管理(Supply Chain Management):与供应商和合作伙伴紧密合作,建立稳定、可靠的供应链,确保从原材料到最终产品或服务的全过程质量可控。
8. 数据分析(Data Analysis):使用数据和统计工具对质量问题和业务过程进行分析,发现问题根本原因和改进机会,做出科学的决策。
9. 标准化工作方法(Standardized Work):确立和遵守一套标准化的工作方法和流程,提高工作的可重复性和一致性,降低变异性和错误率。
10. 顾客满意度调查(Customer Satisfaction Survey):定期对顾客进行调查,了解他们的需求和意见,及时改进和适应市场需求。
- 1、下载文档前请自行甄别文档内容的完整性,平台不提供额外的编辑、内容补充、找答案等附加服务。
- 2、"仅部分预览"的文档,不可在线预览部分如存在完整性等问题,可反馈申请退款(可完整预览的文档不适用该条件!)。
- 3、如文档侵犯您的权益,请联系客服反馈,我们会尽快为您处理(人工客服工作时间:9:00-18:30)。
3
9
质检必须能够快 date: 速识别
Quality name:
标准的 WIP 需求
具体操作需要和 说明书结合
date:
6
标准化工作
Job instructions
工作说明书
what to do?
做什么
= production sequence
生产操作的先后顺序
Standardized work chart (Visual management)
TT = 61s
频次动作
10 inspection
Position part for
A B
搬料箱 倒箱 质检
4’’/50pces 15’’/10pces 32’’/30pces
C
频次动作发生的周期 时间
8
为什么标准化工作是必要的 ?
Define a standard Safety/Ergonomic Quality Efficiency Training 培训 Clarify relation between operator, GAP Leader & Supervisor 阐明操作者, 阐明操作者,GAP班长和管理者之间的关系 班长和管理者之间的关系 Prerequisite for improvement 改进的先决条件
Standardized Work 标准化工作
标准化工作 : 基本概念
Operator has to work according to Standardized Work
操作者必须按标准化指导书工作
Supervisor is in charge of giving standardized work to operator all along the shift
培训操作者
Fig 1.
3
Granulator
4
Remove the spiked frame from the underneath bench
Remove the spiked frame from underneath the bench place it into the guides on the upper mould tool (fig 1) Ensure that the handle is pointing towards you is fully located against the censor Fig 2.
标准化指导书的目视化
Work combination table
工作结合表
create a reference = Best time + man/machine conditions 创立一个参照
工作最短时间+人员机器的等待 工作最短时间 人员机器的等待
5
标准工作图
组织描述必须注意 取决于所有班 次的最小循环 时间 Product: panel
4
标准化工作
Job instructions
工作说明书
what o do?
做什么
= production sequence
生产操作的先后顺序
Standardized work chart (Visual management)
标准工作图(目视化管理 标准工作图 目视化管理) 目视化管理
visualization of Standardized Work
Remove 控制计划来自the spiking 2 frame from the upper 于计算 tool Fold waste and place onto to stand.
主要目的
Remove the waste then place the frame onto the bench Ensure frame handle is pointing away from you and spikes are pointing upwards.
Spiking
1
4
Cavitie s Cavities
定时属于 SWC 和 SWCT
1
2
3
2
3
Fold the waste from the frame and place it onto the granulator cooling stand, using it to push the existing waste into the granulator (fig 2).
工段长负责向所有班次的操作者提供标准化指导书
Operator should wait if not enough workload but never perform a non standardized operation (safety & quality)
工作量不饱满,操作者应该等待,但永远不要做没有标准化的操作(安全和质量) 工作量不饱满,操作者应该等待,但永远不要做没有标准化的操作(安全和质量)
Need to build documents for each production configuration 为每个产品配置建立文档 Key point: Supervisor & GAP Leader have to discover the best current Standardized Work (best Cycle Time)
Signature
Approved
Name: Function:
Signature
Name: Function:
详细的质检必须 清晰的定义
SKILLED OPERATOR
Name:
Signature
P lace rejects in reject container. Reco rd o n P ro cess M o nito r Sheet. If 3 or mo re rejects fo und with same fault call Gap Leader.
技术诀窍: 技术诀窍: 主标题
Plant:
Washington
Workstation:
Document No.: Revision Level:
xxxx 4
xxx
Part Name
Bolster
= SAFETY
Line :
EQ Bolster
= TIP
Tim e:
Woodstock
Page No:
1/1
关键点:管理者和GAP班长找出当前最好的标准化工作(最小的循环时间 班长找出当前最好的标准化工作( 关键点:管理者和 班长找出当前最好的标准化工作 )
Difficulty is to have the agreement of each shift on this standard 难点在于每个班次都要认同这个标准 Supervisor & GAP Leader have to be trained to build Standardized Work (help of PSE) 管理者和GAP班长要被培训以建立标准化工作(协助PSE) 班长要被培训以建立标准化工作(协助 管理者和 班长要被培训以建立标准化工作 )
生产操作的先后顺序
Standardized work chart (Visual management)
标准工作图(目视化管理 标准工作图 目视化管理) 目视化管理
visualization of Standardized Work
标准化指导书的目视化
Work combination table
工作组合表
9
定义一个标准 安全 质量 效率
管理者 & GAP 班长的任务
To build Standardized Work 建立标准化工作 To eliminate every non standard operation 消除每个非标准操作 To train operator 培训操作者 Are responsible for Standardized Work application 对标准化工作的应用负责 To improve 改进
Cooling stand
W hite
- Take one white & green LH clip from the dispenser. - Place the green clip into the center clip position and the white into the bottom location on cavity 4. - Take one white & green RH clip from the dispencer. - Place the green clip into the center cl
Supervisor, GAP Leader check Standardized Work & improve
工段长和GAP班长检查标准化工作和改进 工段长和GAP班长检查标准化工作和改进 GAP
2
标准化工作
Job instructions
操作指导书
what to do?
做什么
= production sequence
create a reference = Best time + man/machine conditions 创立一个参照
工作最短时间+人员机器的等待 工作最短时间 人员机器的等待
3
生产说明书
STANDARD OPERATION
Part Number
FIS-F-PS-241 / EN version 01
10
管理者 & GAP 班长的任务
建立标准化工作 (由GAP班长协助管理者完成 班长协助管理者完成) 由 班长协助管理者完成 To train operator Are responsible for Standardized Work application To improve