长流程钢铁生产工艺规范导引
炼钢生产过程以及流程图详解(全)
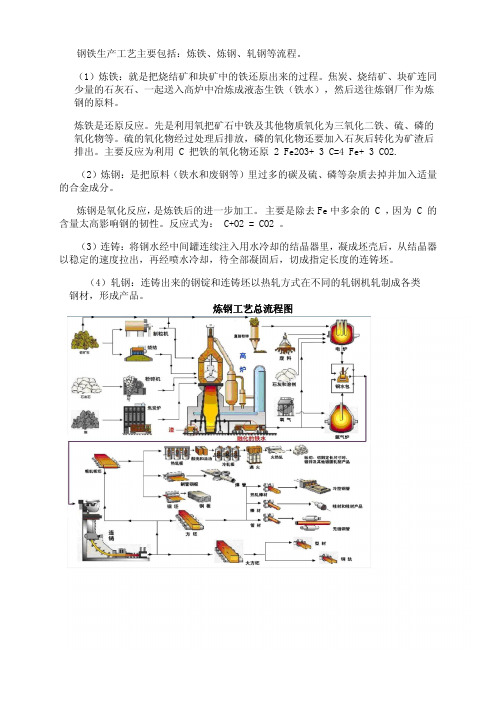
钢铁生产工艺主要包括:炼铁、炼钢、轧钢等流程。
(1)炼铁:就是把烧结矿和块矿中的铁还原出来的过程。
焦炭、烧结矿、块矿连同少量的石灰石、一起送入高炉中冶炼成液态生铁(铁水),然后送往炼钢厂作为炼钢的原料。
炼铁是还原反应。
先是利用氧把矿石中铁及其他物质氧化为三氧化二铁、硫、磷的氧化物等。
硫的氧化物经过处理后排放,磷的氧化物还要加入石灰后转化为矿渣后排出。
主要反应为利用 C 把铁的氧化物还原 2 Fe2O3+ 3 C=4 Fe+ 3 CO2.(2)炼钢:是把原料(铁水和废钢等)里过多的碳及硫、磷等杂质去掉并加入适量的合金成分。
炼钢是氧化反应,是炼铁后的进一步加工。
主要是除去Fe中多余的 C ,因为 C 的含量太高影响钢的韧性。
反应式为: C+O2 = CO2 。
(3)连铸:将钢水经中间罐连续注入用水冷却的结晶器里,凝成坯壳后,从结晶器以稳定的速度拉出,再经喷水冷却,待全部凝固后,切成指定长度的连铸坯。
(4)轧钢:连铸出来的钢锭和连铸坯以热轧方式在不同的轧钢机轧制成各类 钢材,形成产品。
炼钢工艺总流程图炼焦生产流程:炼焦作业是将焦煤经混合,破碎后加入炼焦炉内经干馏后产生热焦碳及粗焦炉气之制程。
烧结生产流程:烧结作业系将粉铁矿,各类助熔剂及细焦炭经由混拌、造粒后,经由布料系统加入烧结机,由点火炉点燃细焦炭,经由抽气风车抽风完成烧结反应,高热之烧结矿经破碎冷却、筛选后,送往高炉作为冶炼铁水之主要原料。
还原气体,还原铁矿石,产生熔融铁水与熔渣之炼铁制程。
转炉生产流程:炼钢厂先将熔铣送前处理站作脱硫脱磷处理,经转炉吹炼后,再依订单钢种特性及品质需求,送二次精炼处理站(RH真空脱气处理站、Ladle Injection盛桶吹射处理站、VOD真空吹氧脱碳处理站、STN搅拌站等)进行各种处理,调整钢液成份,最后送大钢胚及扁钢胚连续铸造机,浇铸成红热钢胚半成品,经检验、研磨或烧除表面缺陷,或直接送下游轧制成条钢、线材、钢板、钢卷及钢片等成品。
长流程钢铁流程介绍
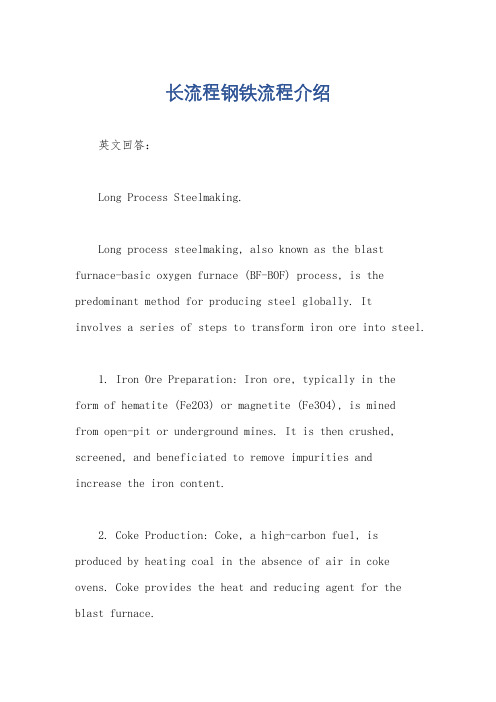
长流程钢铁流程介绍英文回答:Long Process Steelmaking.Long process steelmaking, also known as the blast furnace-basic oxygen furnace (BF-BOF) process, is the predominant method for producing steel globally. Itinvolves a series of steps to transform iron ore into steel.1. Iron Ore Preparation: Iron ore, typically in theform of hematite (Fe2O3) or magnetite (Fe3O4), is minedfrom open-pit or underground mines. It is then crushed, screened, and beneficiated to remove impurities andincrease the iron content.2. Coke Production: Coke, a high-carbon fuel, is produced by heating coal in the absence of air in coke ovens. Coke provides the heat and reducing agent for the blast furnace.3. Sintering: Iron ore fines, along with coke and flux materials (e.g., limestone), are sintered in a sintering machine to form agglomerates called sinter. Sintering enhances the strength and porosity of the iron ore, making it more suitable for the blast furnace.4. Blast Furnace Operation: The blast furnace is a large cylindrical furnace lined with refractory materials. It is charged with iron ore, sinter, coke, and flux materials. Hot air is blown into the furnace from the bottom, which reacts with the coke to produce carbon monoxide (CO). The CO gas reduces the iron oxides in the ore to form molten iron, which collects at the bottom of the furnace.5. Basic Oxygen Furnace (BOF) Operation: Molten iron from the blast furnace is transferred to the BOF, which is a pear-shaped vessel lined with refractory bricks. Oxygen gas is blown into the molten iron, which oxidizesimpurities such as carbon, silicon, and manganese. These oxides form a foamy slag, which floats on top of the moltenmetal. The process produces low-carbon steel that can be used to make a variety of products.6. Continuous Casting: The molten steel from the BOF is poured into a tundish and then into a continuous casting machine. The steel is solidified and formed into slabs, blooms, or billets. These semi-finished products are usedas input materials for rolling mills.7. Rolling: Slabs, blooms, or billets are heated in reheating furnaces and then rolled into various shapes, including bars, rods, wires, and flat rolled products (e.g., sheets, coils).8. Finishing: After rolling, the steel products may undergo further processing, such as heat treatment, coating, or galvanizing, to enhance their properties and meetspecific requirements.中文回答:长流程钢铁工艺。
钢铁制造流程

将炼钢分两步进行的好处是: 可提高钢的质量, 缩短冶炼时间,简化工艺过程并降低生产成本;
炉外精炼的种类很多,大致可分为常压下炉外精 炼和真空下炉外精炼两 类。按处理方式的不同, 又可分为钢包处理型炉外精炼及钢包精炼型炉
2024/8/3
精炼——常用方法与设备
2024/8/3
精炼——工艺路径
以钢种为中心,正确选择精炼设备 CAS-OB是最简单的非真空精炼设备,多适用于 普碳钢、低合金钢等以化学成分交货的钢种; LF有很强的清洗精炼和加热功能,适宜冶炼低氧 钢、低硫钢和高合金钢;
2024/8/3
铁水预处理——脱硫
铁水在进入转炉冶炼前进行脱硫具备最佳的反应条件 铁水中含有大量Si、C.Mn等还原性好的元素,其还原性
有利于脱硫 反应,(强脱硫剂Ca、Mg等烧损少); 铁水中C.Si能大大提高S在铁水中的活度系数,致使硫较
易脱到低的 水平; 铁水中氧含量低,硫的分配系数相应有所提高,有利于
2024/8/3
转炉炼钢过程
上一炉出钢--倒完炉渣(或加添加剂)-- 补炉或溅渣--堵 出钢口--兑铁水--装废钢--下枪--加渣料(石灰、铁皮)- 点火-- 熔池升温--脱P、Si 、Mn----降枪脱碳。
看炉口的火, 听声音。看火亮度--加第二批(渣料)--提 枪化渣, 控制“返干”。
降枪控制终点(FeO), 倒炉取样测温, 出钢。 技术水平高的炉长, 一次命中率高。50%。(宝钢是付枪
2024/8/3
转炉炼钢的技术发展
1855-1856年英国人亨利.贝塞麦(Henly)开发了酸性底吹 空气转炉炼钢法;
1878年英国人托马斯(S.G.Thomas)碱性底吹空气转炉炼 钢法;
1940年廉价获得氧气后, 瑞士、奥地利开发了顶吹氧气转 炉, 1952年在奥地利林茨(Linz)和多纳维茨城(Donawitz)建 成第一座30吨碱性顶吹氧气转炉(LD转炉);或称BOF (Basic Oxygen Furnace);
长流程钢铁——生态环境部重污染天气重点行业绩效分级及减排措施
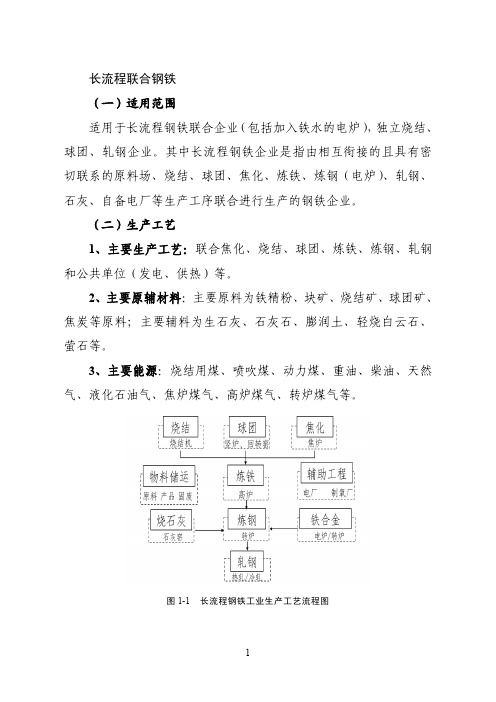
三及以上排放标准或使用新能
械全部达到国三及以上
源机械
排放标准或使用新能源
机械
参照《重污染天气重点行业移动源应急管理技术指南》
运输监管 建立门禁系统和电子台账
未达到 A、B 级要求
注 1:a 是指《排污许可证申请与核发技术规范 钢铁工业》(HJ846-2017)中规定的主要排放口
6
(五)减排措施 1、A 级企业: 鼓励结合实际,自主采取减排措施。 2、B 级企业: 黄色预警期间:停止使用国四及以下重型载货车辆(含燃气) 进行运输。 橙色预警期间:每座转炉(电炉)日出钢数不大于 36 炉, 带动整体降低生产负荷,其中烧结机、球团设备限产 10%(含) 以上,石灰窑限产 30%(含)以上,以“环评批复产能、排污许 可载明产能、前一年正常生产实际产量”三者日均值的最小值为 基准核算;停止使用国四及以下重型载货车辆(含燃气)进行运 输。 红色预警期间:每座转炉(电炉)日出钢数不大于 32 炉, 带动铁前工序、高炉和轧钢工序减产,整体降低生产负荷,其中 烧结机、球团设备限产 20%(含)以上,石灰窑限产 30%(含) 以上,以“环评批复产能、排污许可载明产能、前一年正常生产 实际产量”三者日均值的最小值为基准核算;停止使用国四及以 下重型载货车辆(含燃气)进行运输。 3、B-级企业: 黄色预警期间:焦炉负荷降至设计生产负荷的 80%以内,以 延迟出焦时间计;停止使用国四及以下重型载货车辆(含燃气) 进行运输。 橙色预警期间:每座转炉(电炉)日出钢数不大于 30 炉, 带动整体降低生产负荷,其中烧结机、球团设备,石灰窑停限产
1、按照《关于做好钢铁企业超低 焦运输满足:(1)在封闭车间内装卸物料,并设
排放评估监测工作的通知》开展无 置集尘罩等集尘装置,(2)运输车辆封闭;各料
转炉长流程冶炼优钢工艺概述

第 2 卷 第 4期 8 20 06年 8月
四川冶金
Sc u n M ealr y ih a tl g u
Vo . 8 No 4 12 .
Au , 0 6 g20
转 炉 长 流 程 冶炼 优 钢 工 艺概 述
刘永祥 王猛成 李 斌
出现以来 , 迅速在全世界兴起。我 国近年来大量出 现的民营钢铁企业主要 以电炉短流程工艺为主。 2 转炉长流程冶炼工艺 ) 现在转炉长流程 已能生产部分特钢 品种 , 如轴
吨, 1 . 占 47%, 其中特殊钢的产量为 2 0 万吨, 00 占
全 国钢产量 的 8 4%。与工业化较发达的 日 比 . 本 较 ,03 日 20 年 本特殊钢的总产量为 25 万吨 , 25 占日 本全国钢总产量 的 2 .2%。而且近年来在 F本 03 t 6 0%以上的特殊钢是转炉长流程生产 的。利用转 炉冶炼优钢在 国内也逐渐兴起。相对电炉炼钢有较
大的成本优势 , 同时在普钢面临的建筑用材, 高速线 材市场激烈的竞争下 , 利润减少甚至亏损 , 进行品种
结构调整也是大势所趋。另外 国内在机械、 汽车、 石
承钢 、 齿轮钢 、 弹簧钢、 低碳合结钢等 , 中、 主要以棒 材生产为主。主要 的工艺流程为 : 铁水预处理—— L 顶 底 复 吹——炉 外 精 炼 ( F V 、 H) D L 、 D R —— C、—— ( 一 热送连轧——成品精整。
备, 产品的实物水平较高以及对环境 的污染小的特
点。 2 我国的特殊钢的生产 基本现状及转炉长流程的
市场前 景
制成合金钢棒材产品。随着近年来转炉冶炼控制能
力的不断提高 , 炉外精炼 以及连铸技术的快速发展
钢铁流程

图1-1 钢铁生产基本流程1.钢铁生产基本流程1.1生产流程概述钢铁生产是一项系统工程,生产的基本流程如图1-1所示,首先在矿山要对铁矿石和煤炭进行采选,将精选炼焦煤和品位达到要求的铁矿石,运送到钢铁企业的原料场进行配煤或配矿、混匀,再将炼焦煤送到在焦化厂炼焦,生产符合高炉炼铁质量要求的焦炭,铁矿石送到烧结厂烧结,获得符合高炉炼铁质量要求的烧结矿。
球团厂可直接建在矿山,也可建在钢铁厂,它的任务是将细粒精矿粉造球、干燥、经高温焙烧后得到直径9~16mm球团矿。
高炉是炼铁的主要设备,使用的原料有铁矿石(包括烧结矿、球团矿和块矿)、焦炭和少量熔剂(石灰石),产品为铁水、高炉煤气和高炉渣。
铁水送至炼钢厂炼钢,高炉煤气主要用来烧热风炉,同时供炼钢厂和轧钢厂使用,高炉渣经水淬后送水泥厂生产水泥。
炼钢,目前主要有两条工艺路线,即转炉炼钢流程和电弧炉炼钢流程,通常将“高炉-铁水预处理-转炉-精炼-连铸”称为长流程,而将“废钢-电弧炉-精炼-连铸”称为短流程,短流程无需庞杂的铁前系统和高炉炼铁,因而,工艺简单、投资低、建设周期短。
但短流程生产规模相对较小,生产品种范围相对较窄,生产成本相对较高。
同时受废钢和直接还原铁供应的限制,目前,大多数短流程钢铁生产企业也开始建高炉和相应的铁前系统,电弧炉采用废钢+铁水热装技术吹氧熔炼钢水,可降低电耗,缩短冶炼周期,提高钢水品质。
炼钢厂的最终产品是连铸坯,按照形状,连铸坯分为方坯、板坯和圆坯,在轧钢厂,方坯分别被棒材、线材和型材轧机轧制成棒材、线材和型材;板坯被轧制成中厚板和薄板,圆坯被穿孔、轧制成无缝钢管。
钢铁联合企业的正常运转,除了上述主体工序外,还需要其他辅助行业为它服务,这些辅助行业包括耐火材料和石灰生产,机修、动力、制氧、供水供电等。
1.2生产系统概述钢铁生产主要包括铁前系统、高炉炼铁、炼钢厂和轧钢厂。
(1)铁前系统对钢铁联合企业来说,铁前系统主要包括烧结厂和焦化厂。
钢铁生产工艺流程DOC
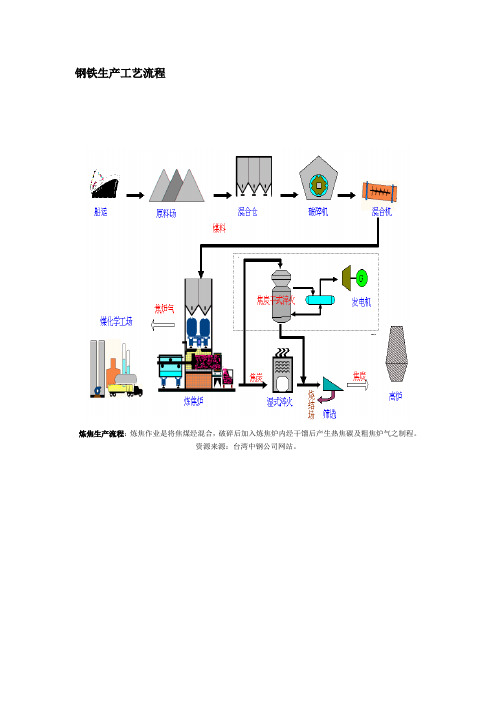
钢铁生产工艺流程炼焦生产流程:炼焦作业是将焦煤经混合,破碎后加入炼焦炉内经干馏后产生热焦碳及粗焦炉气之制程。
资源来源:台湾中钢公司网站。
烧结生产流程:烧结作业系将粉铁矿,各类助熔剂及细焦炭经由混拌、造粒后,经由布料系统加入烧结机,由点火炉点燃细焦炭,经由抽气风车抽风完成烧结反应,高热之烧结矿经破碎冷却、筛选后,送往高炉作为冶炼铁水之主要原料。
资源来源:台湾中钢公司网站。
高炉生产流程:高炉作业是将铁矿石、焦炭及助熔剂由高炉顶部加入炉内,再由炉下部鼓风嘴鼓入高温热风,产生还原气体,还原铁矿石,产生熔融铁水与熔渣之炼铁制程。
资源来源:台湾中钢公司网站。
转炉生产流程:炼钢厂先将熔铣送前处理站作脱硫脱磷处理,经转炉吹炼后,再依订单钢种特性及品质需求,送二次精炼处理站(RH真空脱气处理站、Ladle Injection盛桶吹射处理站、VOD真空吹氧脱碳处理站、STN搅拌站等)进行各种处理,调整钢液成份,最后送大钢胚及扁钢胚连续铸造机,浇铸成红热钢胚半成品,经检验、研磨或烧除表面缺陷,或直接送下游轧制成条钢、线材、钢板、钢卷及钢片等成品。
资源来源:台湾中钢公司网站。
连铸生产流程:连续铸造作业乃是将钢液转变成钢胚之过程。
上游处理完成之钢液,以盛钢桶运送到转台,经由钢液分配器分成数股,分别注入特定形状之铸模内,开始冷却凝固成形,生成外为凝固壳、内为钢液之铸胚,接着铸胚被引拔到弧状铸道中,经二次冷却继续凝固到完全凝固。
经矫直后再依订单长度切割成块,方块形即为大钢胚,板状形即为扁钢胚。
此半成品视需要经钢胚表面处理后,再送轧钢厂轧延。
资源来源:台湾中钢公司网站。
热轧生产流程。
热轧生产流程。
资源来源:台湾中钢公司网站。
热轧生产流程>第一热轧钢带生产流程:热轧钢带工场主要制程是将扁钢胚加热后,经粗轧机及精轧机轧延成钢带,并以层流冷却系统喷水冷却至适当温度,再由盘卷机卷成粗钢卷。
资源来源:台湾中钢公司网站。
热轧生产流程>热轧厚板剪切线布置图:主要功能为将原料钢卷上线解卷、切边、切片、整平、堆叠、及包装为成品钢板叠(HR PLATE)。
钢铁联合企业生产工艺流程

钢铁联合企业生产工艺流程下载温馨提示:该文档是我店铺精心编制而成,希望大家下载以后,能够帮助大家解决实际的问题。
文档下载后可定制随意修改,请根据实际需要进行相应的调整和使用,谢谢!并且,本店铺为大家提供各种各样类型的实用资料,如教育随笔、日记赏析、句子摘抄、古诗大全、经典美文、话题作文、工作总结、词语解析、文案摘录、其他资料等等,如想了解不同资料格式和写法,敬请关注!Download tips: This document is carefully compiled by theeditor. I hope that after you download them,they can help yousolve practical problems. The document can be customized andmodified after downloading,please adjust and use it according toactual needs, thank you!In addition, our shop provides you with various types ofpractical materials,such as educational essays, diaryappreciation,sentence excerpts,ancient poems,classic articles,topic composition,work summary,word parsing,copy excerpts,other materials and so on,want to know different data formats andwriting methods,please pay attention!钢铁联合企业是将炼铁、炼钢、轧制、热处理等工艺集成在一起的大型钢铁生产企业。
钢铁厂生产工艺流程介绍PPT钢铁生产流程
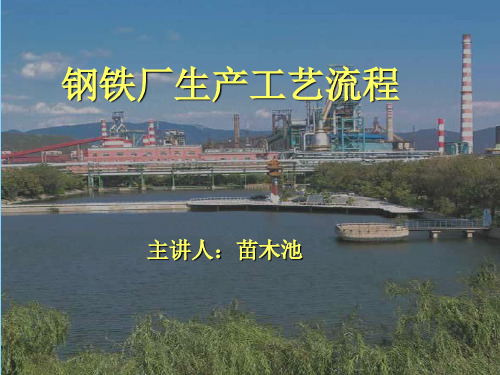
(4)二次冷却区 ·作用: -继续冷却 -支撑导向 ·要求: - 冷却效率高,传热快 - 均匀冷却,表面温度均匀 - 支撑导向部件有足够的强度和刚度 - 各段对中准确 - 快速更换
(5)铸坯导向和拉坯矫直机 ·作用: -拉坯 -矫直 -送引锭杆,调节拉速 ·引锭杆作用: -开浇时的凝固底板 -传递拉坯力 ·引锭杆形式: -挠性 -刚性
铁水预处理与 钢水炉外精炼处理工艺
பைடு நூலகம்
连铸工艺与设备
1 现代炼钢技术的发展(连铸技术的作用) (1) 1947年-1974年: 技术特点:转炉、高炉的大型化;以模铸-初 轧为核心,生产外延扩大。 (2) 1974年-1989年: 技术特点:全连铸工艺,以连铸机为核心。 (3) 1989年-现在:
技术特点:连铸-连轧工艺,以薄板 坯,连铸-连轧为代表,钢厂向紧凑化发展。
7.喷吹系统 煤粉制备、储煤罐、喷吹罐、混合器、喷枪
高炉生产技术经济指标
三、炼钢生产工艺流程
•转炉炼钢工艺; •铁水预处理工艺; •钢水炉外精炼处理工艺。
钢与生铁的区别:
首先是碳的含量,理论上一般把碳含量 小于2.11%称之钢,它的熔点在14501500℃,而生铁的熔点在1100-1200℃。
大方坯 小方坯 圆坯
600×600 160×160
φ 450
200×200 55×55 φ 100
250×250~ 450×450 240×280~ 400×560
90×90~ 150×150
φ 200~φ 300
异性坯
工字型 460×460×120
中空坯 φ 450/6100
椭圆型 120×140
最全钢铁企业制造流程

§1964年我国第1家氧气顶吹转炉炼钢厂在首钢建成投产,与 此同时我国太钢从奥钢联引进了2台50 t氧气顶吹转炉,使我 国的氧气顶吹转炉炼钢进入了发展的初始阶段。
PPT文档演模板
2020/11/17
最全钢铁企业制造流程
转炉炼钢
PPT文档演模板
2020/11/17
最全钢铁企业制造流程
将高温钢液连续地浇铸到一个或多个强制水冷的金属型腔内。凝 固成形后,再经二次冷却,使之凝固,且成一定形状(规格)铸坯的 工艺方法,其典型特征是生产过程的连续化。
PPT文档演模板
2020/11/17
最全钢铁企业制造流程
连铸工艺——设备
PPT文档演模板
2020/11/17
最全钢铁企业制造流程
连铸工艺——相关技术
– 振动装置 采用小振幅高频率的结晶器振动,一般频率可达0~360次/min, 振幅<10mm(有的为±4mm)。
– 二冷控制 精确控制二次喷水冷却。按不同钢种、不同拉速自动调节,均 匀冷却。尽管气-水雾冷却会增加控制上的困难、价格较高,但对特殊钢 连铸来说仍是十分必要的。
– 自动控制 采用计算机控制对稳定铸坯质量非常重要。
§看炉口的火,听声音。看火亮度--加第二批(渣料)--提 枪化渣,控制“返干”。
§降枪控制终点(FeO),倒炉取样测温,出钢。 §技术水平高的炉长,一次命中率高。50%。(宝钢是付枪)
根据分析取样结果--决定出钢(或补吹)--脱氧、合金化。
不要补吹的就是通常说的一次命中。
PPT文档演模板
2020/11/17
§ 铁水脱硫预处理的工艺方法
– 投掷法: 将脱硫剂投入铁水中 – 喷吹法: 将脱硫剂喷入铁水中 – 搅拌法(KB法): 将通过中空机械搅拌器向铁水内加入脱硫剂,搅拌脱硫。
钢铁生产工艺规范导引

钢铁生产工艺规范导引附件1:长流程钢铁生产工艺规范导引一般长流程钢铁公司所采用主要生产工艺流程为: 焦化、烧结、炼铁、炼钢、轧钢等主要生产工序。
1、长流程钢铁生产所采用主要生产工艺流程(见附图1)2、主要生产工序工艺技术文件目录见表1:表1 必备的生产工艺技术文件序号工艺技术文件名称1 焦化厂技术操作规程备煤车间技术操作规程炼焦车间技术操作规程回收(煤化工)车间技术操作规程2 烧结厂技术操作规程皮带机技术操作规程配料工技术操作规程造球技术操作规程外滚燃料技术操作规程抽风机技术操作规程看火技术操作规程单辊、热振筛、振动输送槽技术操作规程水封拉链机、热返矿圆盘技术操作规程环冷机技术操作规程电除尘器技术操作规程空气压缩机技术操作规程鼓风带式冷却机技术操作规程卸车机技术操作规程卸料系统技术操作规程铺料系统技术操作规程取料系统技术操作规程燃料系统技术操作规程筛分系统技术操作规程With an external intelligent video analysis equipment such as SAVIA, can reach the border detection, intrusion, retrograde, count, spraying, intelligent video analysis functions such as occlusion alarm with the video camera. Network video codec technology of the system in accordance with the national standard of SVAC technology required to implement data collection and Exchange. Video bit rate can be adjusted according to the image quality between 2Mbps-16M bps, to meet the application requirements monitoring process to transfer images. This reservation and municipal public security system, City Emergency Office of network interfaces. Rehabilitation centres for monitoring system monitored bythe following areas: key management areas of operating room nursing unit area; Health care corridor areas; crowded public places, toll, pharmacy Windows, medical equipment, warehouse and important protected areas; building access entrance key areas; Office area, important separation; room, equipment room and other important machines, instruments/canteen, restaurant management sites; car park management areas supervisory areas.System equipment are network cameras, power modules, switches, control center equipment mainly to monitor digital workstation, storage devices, alarm, alarm units, UPS, LCD monitors and so on. Injury recovery, 1, 2nd floor of the used network transmission of video signal transmission mode to upload to the medical floor of the security monitoring room. Transmission fiber on the rehabilitation floor ... Control. Local monitoring center can view/control cameras as well as distribution of any remote-control center of the camera. Local control3 炼铁厂技术操作规程高炉值班室技术操作规程高炉炉前技术操作规程热风炉技术操作规程高炉主卷扬技术操作规程高炉煤气技术操作规程电除尘器技术操作规程喷煤技术操作规程空压机技术操作规程高炉值班看水工技术操作规程水泵工技术操作规程布袋除尘器技术操作规程烧结矿槽前筛分及电除尘技术操作规程铸铁机技术操作规程原燃料管理技术操作规程碾泥机技术操作规程高炉富氧系统技术操作规程无料钟炉顶技术操作规程脉冲式布袋除尘器技术技术操作规程顶燃式热风炉技术操作规程煤气干法除尘系统技术操作规程4 炼钢厂技术操作规程转炉技术操作规程转炉污泥泵送烧结技术操作规程留渣操作工艺技术规程(试行 )铁水预处理(脱硫)工艺技术操作规程(试行)方坯连铸机技术操作规程LF精炼炉技术操作规程运转车间技术操作规程5 轧钢厂工艺技术操作规程及技术文件高速线材轧钢厂工艺技术操作规程棒材轧钢厂工艺技术操作规程棒材轧钢厂轧辊技术条件高线轧钢厂轧辊技术条件3长流程钢铁生产主要工艺流程:, alarm, alarm units, UPS, LCD monitors and so on. Injury recovery, 1, 2nd floor of the used network transmission of video sievicespment are network cameras, power modules, switches, control center equipment mainly to monitor digital workstation, storage dmportant machines, instruments/canteen, restaurant management sites; car park managementareas supervisory areas. System equiher iimportant protected areas; building access entrance key areas; Office area, important separation; room, equipment room and ot sing unit area; Health care corridor areas; crowded public places, toll, pharmacy Windows, medical equipment, warehouse andom nurterfaces. Rehabilitation centres for monitoring system monitored by the following areas: key management areas of operating rotoring process to transfer images. This reservation and municipal public security system, City Emergency Office of network in16M bps, to meet the application requirements moni-nge. Video bit rate can be adjusted according to the image quality between 2Mbpsogy of the system in accordance with the national standard of SVAC technology required to implement data collection and Exchaolount, spraying, intelligent video analysis functions such as occlusion alarm with the video camera. Network video codec technWith an external intelligent video analysis equipment such as SAVIA, can reach the border detection, intrusion, retrograde, c4control center of the camera. Local control-or ... Control. Local monitoring center can view/control cameras as well as distribution of any remoteon flognal transmission mode to upload to the medical floor of the security monitoring room. Transmission fiber on the rehabilitati3.1焦化工序工艺流程:将无烟煤预破碎至1mm以下~与主焦煤、肥煤、1/3焦煤按一定比例配合~送至锤式粉碎机破碎混均后~进JN43,80型65孔焦炉干馏,主产品焦炭经筛分处理后~送炼铁厂使用;副产品荒煤气经煤化工公司处理~提取其中的化产品后~供后道工序,如轧钢加热炉加热钢坯,使用。
钢铁企业工艺流程

钢铁行业工艺流程钢铁生产的工艺流程大致分为:选矿,烧结,焦化,炼铁,炼钢,连铸, 轧钢等过程;辅助系统有:制氧/制氮,循环水系统,烟气除尘及煤气回收 等。
1选矿工序选矿是冶炼前的准备工作,从矿山开采下来矿石以后,首先需要将含铁、 铜、铝、锰等金属元素高的矿石甄选出来,为下一步的冶炼活动做准备。
选矿一般分为破碎、磨矿、选别三部分。
其中,破碎又分为:粗破、中破 和细破;选别依方式不同也可分为:磁选、重选、浮选等。
选矿工序原料:原矿石。
选矿工序产物:铁精矿。
选矿工序设备:矿石破碎设备:颚式破碎机、锤式破碎机。
磨矿工艺设备:球磨机、螺旋分级机。
选别工艺设备:浮选机、磁选机。
铁矿原料 钢成品原煤 粉状含铁原料 电、煤气焦化粗苯废气 焦油焦炉煤气 电 煤气 氧气 电氧气煤气块矿 辅料 废铁 水 废钢 水 电、煤气电、煤气 T 球团炉尘宣… 炉尘蒸汽高炉渣高炉煤气 转炉渣转炉煤气废气2烧结工序为了保证供给高炉的铁矿石中铁含量均匀,并且保证高炉的透气性,需要把选矿工艺产出的铁精矿制成10-25mm的块状原料。
铁矿粉造块目前主要有两种方法:烧结法和球团法。
铁矿粉造块的目的:♦去除有害杂质,回收有益元素,保护环境;♦综合利用资源,扩大炼铁用的原料种类;♦改善矿石的冶金性能,适应高炉冶炼对铁矿石的质量要求。
2.1烧结法烧结是钢铁生产工艺中的一个重要环节,它是将铁矿粉、粉(无烟煤)和石灰、高炉炉尘、轧钢皮、钢渣按一定配比混匀。
经烧结而成的有足够强度和粒度的烧结矿可作为炼铁的熟料。
烧结矿生产流程:烧结料的准备,配料与混合,烧结和产品处理;烧结矿生产原料:含铁原料、熔剂、燃料;烧结矿生产产物:烧结矿和球团矿;烧结矿生产设备:带式抽风烧结机。
电结矿 结矿精矿粉富矿粉 碎焦 高炉灰 无烟煤 轧钢皮 石灰石 白云石2.2球团法球团是把细磨铁精矿粉或其他含铁粉料添加少量添加剂混合后,在加水润湿的条件下,通过造球机滚动成球,再经过干燥焙烧,固结成为具有一定强度和冶金性能的球型含铁原料。
钢铁企业生产流程(常识版)

钢铁企业生产流程(常识版)陈富莲安徽财经大学学生陈晶刚根据讲课录音整理于中冶南方工程技术有限公司钢铁企业是我们中冶南方的主力,就是设计钢铁企业。
钢铁企业是一个庞大复杂的系统。
说起来,主要的是流程及中间辅助机构。
主要有炼铁炼钢轧钢三个系统。
为了满足这个炼铁炼钢轧钢这样的生产系统的生产。
就需要很多专业的配合。
就我们设计,就现在工厂来说,就需要很多的系统,为这个主要的生产线系统服务。
现在我们一般做设计的一些钢铁企业,一个,主要是,原来叫钢铁联合企业。
钢铁联合企业,那就是从原料开始,矿山,焦化,一直到炼铁、炼钢、轧钢以及所有辅助系统在一起,为炼铁、炼钢、轧钢服务,形成一个相互交叉,相互配合,需要在生产当中相互协调,相互衔接,这样一个相当庞大的系统。
所以我们设计院要完成这个建设就需要很多的专业。
各位可能来自不同的学校,学着不同的专业。
但是你们所学的专业对钢铁生产不是很清楚,即使学炼铁、炼钢、轧钢专业的对钢铁企业概况也不是很清楚。
为了大家能够基本清楚,基本了解钢铁企业包括那些内容,所以我给大家介绍钢铁企业生产流程。
先拿一个钢铁联合企业来说。
现在的钢铁联合一般包括刚才所介绍的部门。
我们先从主流程的第一道工序,就是炼铁开始。
这是我形象化简单炼铁高炉图。
炼铁、炼钢、轧钢这三部分,前两部分为化学作用,炼铁是还原过程,炼钢是氧化过程,到后面轧钢是一个物理过程,即把已炼好的钢坯,钢锭加工成我们需要的各种材料。
现在我们介绍炼铁。
对于我们来说,炼铁需要设计高炉,设计高炉需要从前头开始。
高炉需要原料,主要原料是三种,入炉的原料,矿石、焦碳、溶剂。
主要原料就是这三种。
就矿石,拿武钢为例,像武钢有自己的矿山,另外溶剂也有自己的矿山。
溶剂主要包括石灰石这一类,当然还有其他。
焦碳也有自己的炼焦厂,就是焦化。
像武钢,宝钢都有很大的炼焦车间,它们生产的焦碳就供给自己用。
因此就我们的钢铁设计院,我们的设计从哪里开始。
前面既要有原料储存的地方,有矿石堆,煤厂。
- 1、下载文档前请自行甄别文档内容的完整性,平台不提供额外的编辑、内容补充、找答案等附加服务。
- 2、"仅部分预览"的文档,不可在线预览部分如存在完整性等问题,可反馈申请退款(可完整预览的文档不适用该条件!)。
- 3、如文档侵犯您的权益,请联系客服反馈,我们会尽快为您处理(人工客服工作时间:9:00-18:30)。
附件1:
长流程钢铁生产工艺规范导引
一般长流程钢铁公司所采用主要生产工艺流程为:焦化、烧结、炼铁、炼钢、轧钢等主要生产工序。
1、长流程钢铁生产所采用主要生产工艺流程(见附图1)
2、主要生产工序工艺技术文件目录见表1:
表1 必备的生产工艺技术文件
3长流程钢铁生产主要工艺流程:
3.1 焦化工序工艺流程:
将无烟煤预破碎至1mm 以下,与主焦煤、肥煤、1/3 焦煤按一定比例配合,送至锤式粉碎机破碎混均后,进JN43 -80 型65 孔焦炉干馏,主产品焦炭经筛分处理后,送炼铁厂使用;副产品荒煤气经煤化工公司处理,提取其中的化产品后,供后道工序(如轧钢加热炉加热钢坯)使用。
该工序中应用直接配无烟煤炼焦工艺,取代配合煤中部分烟煤,在不降低焦炭总体质量的前提下,充分利用福建省内的白煤资源,对于降低成本,解决紧张资源具有现实的战略意义。
该工序的主要经济技术指标控制要求:①吨焦精煤耗W 1280kg/t、②冶金焦率》94%。
3.2 烧结工序工艺流程:将精矿、澳矿、印矿、烧结粉、富矿及回收的轧钢氧化铁皮、钢渣进行预配料,并进行中和平铺堆取,得到混合均匀的各种带铁原料。
加入生石灰及预先破碎的煤粉进行混合,送至造球系统配入水及外滚焦粉进行造球,而后送入烧结机进行布料、点火烧结,成品烧结矿经破碎及筛分冷却后送入炼铁高炉使用,一小部分筛下物即返矿返回配料系统回收再行配料循环使用。
该工序中运用的小球、低温热风烧结技术,通过造球改善烧结的状态,对提高烧结矿性能,降低固体燃料耗具有实用价值。
该工序的主要经济技术指标控制要求:①固体燃料耗W 45kg标煤/t、②烧结矿平均品位》55%、③转鼓指数》64%、④返矿率W17%。
3.3 炼铁工序工艺流程:
将破碎筛分好的冶金焦炭(除自产外,尚有一部分外购焦)、烧结矿,及配加一定的球团矿、块矿或焦丁、煤块、废铁按一定的比例顺序送入高炉,在前述中的燃料及喷煤、富氧、鼓风的燃烧作用下,在高炉内发生分解还原反
应,分离出铁水及高炉渣,产生高炉煤气,铁水除一小部分铸为铸造用生铁外,绝大部分作为炼钢用铁水送入炼钢厂混铁炉备用;高炉炉渣经冲渣后的水渣可作为水泥厂的配料外售;高炉煤气净化后供焦化厂焦炉加热及炼铁热风炉等用户使用。
该工序的主要经济技术指标控制要求:①铁矿石耗w 1660kg/t、
②高炉入炉焦比w 420kg/t、③高炉喷煤比》100 kg/t。
3.4 炼钢工序工艺流程:
将预先处理的废钢铁加入转炉,从混铁炉取出铁水兑入,加入石灰等造渣材料并予以吹氧冶炼,经出钢配加各类铁合金,成分合格后送至吹氩站进行吹氩、吹氮调温或喂丝,合格的钢水送至连铸机进行浇注成连铸坯送至轧钢厂轧制。
对于特殊要求的钢种还需配备铁水预处理设施及LF 精炼炉等工序并结合上述的转炉及连铸工序来生产合格连铸坯。
在冶炼过程产生的转炉煤气,经净化处理后供炼钢内部烘钢包及并网使用,转炉污泥水及钢渣经处理后,返回烧结工序中配入循环使用。
该工序中应用转炉溅渣护炉技术、小方坯全连铸技术等先进技术提高炉衬寿命及金属收得率等。
该工序的主要经济技术指标控制要求:①转炉钢铁料耗w 1075kg/t、②氧气耗w70m 3/t、③石灰耗w 80 kg /t。
3.5 轧钢工艺流程
a)棒材轧钢厂工艺流程:
将热送坯或冷坯送入步进式加热炉进行加热,进入架小型全连轧机组的粗轧、中轧、精轧道次进行轧制(包括飞剪切头、尾),后经倍尺飞剪切成倍尺上冷床进行冷却,经定尺剪切后,定尺材经支数计数后自动打捆称重标
牌后入库;非定尺材经手动打包称重标牌入库。
轧制中产生的切头、尾及中间冷条废钢经处理后回收至炼钢转炉使用,产生的氧化铁皮回收至烧结工序中配加循环使用。
b)高速线材轧钢厂工艺流程:将连铸坯送入步进式加热炉进行加热,进入高架式机组的粗轧、中轧、预精轧、精轧道次进行轧制(包括飞剪切头、尾),中间穿水冷却,经吐丝机形成线圈,经风冷辊道运输机冷却和集卷,P &F 线输送冷却,压紧自动打包,称重、标牌后入库。
轧制中产生的切头、尾及中间冷条废钢经处理后回收至炼钢转炉使用,产生的氧化铁皮回收至烧结工序中配加循环使用。
该工序的主要经济技术指标控制要求:①棒材厂的成材率(含负偏差率)羽00%、②棒材厂的定尺率》97%、③高线厂的成材率》96%。
3.6 最终产品的工艺水平要求为保证最终产品的工艺水平及特色,要求采用转炉炼钢静态控制技术、钢包底吹氩技术、转炉小方坯全连铸技术、连铸全过程保
护浇注,氢氧火焰切割技术,热送热装技术的等一系列冶炼、连铸技术的推广应用,以确保提供了化学成分稳定、尺寸、外观优良的连铸坯。
主要成品棒材、高速线材轧钢作业线应实现连续化、自动化,使其生产具有高效、低耗的特色。
加热采用步进底式加热炉,棒材轧钢厂采用全连续式轧机,并设有轧后穿水冷却系统,采用高精度倍尺飞剪和齿条步进式冷床,可进行6-12 米不等的成品定尺剪切及自动计数、自动打捆,从而确保产品的质量指标达标准要求,生产出化学成分稳定、性能优良、外形尺寸,表面质量、定尺可靠、外观打包整齐的棒材产品。
低碳热轧圆盘条采用全连续式轧机轧制,采用控轧、控冷技术、设有轧后穿水冷却系统及散卷冷却、P—F 冷却系统,机械自动打包,确保按标准组织生产的产品质量指标,提供化学成分稳定、通
条力学、工艺性能均匀、稳定,外形尺寸、表面质量等品质优良、大盘重、外观打包整齐的高速线材盘条产品。