齿轮油泵泵体夹具设计说明书
齿轮泵体加工工艺及夹具设计

齿轮泵体加工工艺及夹具设计齿轮泵体作为齿轮泵的重要组成部分,经常承受较大的工作负荷,因此其制造质量和加工工艺是影响齿轮泵质量和使用寿命的重要因素之一。
1.材料选择齿轮泵体通常采用优质灰铸铁或钢铸件,以保证其强度和耐用性能。
对于某些要求更高的场合,可采用黄铜、不锈钢等材料进行制造。
2.工艺流程齿轮泵体的加工涉及到数种不同的工艺流程,包括模具制造、铸造、初精加工、主要加工、热处理和次精加工等,其中热处理和次精加工对于提高齿轮泵体的强度和质量起到至关重要的作用。
(1)模具制造模具制造是齿轮泵体加工的第一步,模具的制造质量将直接影响到后续步骤的加工质量。
对于大型齿轮泵体,常用的模具制造方式是采用砂模铸造,而对于较小的齿轮泵体,则可以采用钢制模具进行制造。
(2)铸造铸造是齿轮泵体制造的重要步骤,铸造质量直接关系到齿轮泵体的强度和耐用性能。
在铸造过程中,要注意浇注温度、浇注压力和铸模和铁水的配比,以保证铸件的整体质量和强度。
(3)初精加工初精加工是将铸造好的齿轮泵体进行初步加工,使其基本符合要求的步骤。
该步骤主要包括锯床切割、切削刨平、光洁研磨等加工方法,以确保齿轮泵体的几何形状和表面质量符合要求。
(4)主要加工(5)热处理热处理是齿轮泵体制造的关键步骤,通过调整铸件的结构和力学性能,以提高其强度、硬度和耐腐蚀性能。
热处理方式包括淬火、回火、正火、拉伸等多种方法,不同的方式对应不同的热处理效果。
夹具是加工过程中起到固定、定位和加工辅助作用的工具,齿轮泵体加工夹具的优劣将直接影响到齿轮泵体的加工精度和质量。
齿轮泵体加工夹具的设计需要充分考虑齿轮泵体的结构特点、加工工艺和工作条件。
1.定位要准确齿轮泵体加工夹具需要具有精准定位功能,以保证齿轮泵体加工时的几何精度和相对位置精度。
定位方式应该尽可能简单可靠,且不影响加工工件的表面质量和加工精度。
2.固定要牢固在齿轮泵体加工过程中,夹具要能够牢固地固定齿轮泵体,以免在加工过程中出现晃动和位移,从而影响到加工工件的精度和质量。
(完整word版)齿轮油泵建模设计说明书(word文档良心出品)

目录1 绪论 01.1 机械专业传统的教学方式存在的问题 (1)1.2 将三维技术应用到机械类专业课的教学中 (1)2 设计概述 (2)3 设计过程 (3)3.1 齿轮油泵零件建模设计 (3)3.1.1 齿轮油泵骨架的设计 (4)3.1.2 齿轮油泵主体的设计 (5)3.1.3 齿轮油泵左盖的设计 (7)3.1.4 创建齿轮泵右侧盖的设计 (8)3.1.5 齿轮轴的设计 (8)3.1.6 其它零件的创建 (12)3.2 齿轮油泵装配设计 (13)3.2.1 虚拟装配设计 (13)3.2.2 生成爆炸图 (16)4 机构仿真及工作原理动画 (17)4.1 齿轮油泵机构仿真设计 (17)4.2 齿轮油泵工作原理动画仿真 (19)5 总结 (22)致谢 (23)参考文献 (24)1 绪论计算机辅助教学是教学发展的一个焦点,Pro/E等三维建模软件的发展以及虚拟制造技术的出现为机械类专业课教学提供了一种极好的现代化教学的工作平台[1]。
1.1 机械专业传统的教学方式存在的问题(1)在机械类课程的教学中,经常需要实物模型帮助学生理解教学内容,如果没有模型,仅仅依靠讲解,是很难讲清楚一个立体结构的。
学生缺少对实物的感官认识也就更难理解没有模型的讲解,而传统的教学方式是利用教学实物模型,但实物模型携带不方便,而且容易损坏,不便于保管。
(2)教学中存在的另一个问题是传统的教学实物模型一成不变,更新换代的速度慢,而几十年不变的教学模型已不能满足教学和科技时代不断进步的需要。
时代在发展,教学内容在不断更新,当然教学模型也要跟上教学内容的更新,要想根据教学需要更改实物模型是很困难的。
更换新实物模型成本又很高,而旧模型基本没有再利用的价值,造成很大的浪费。
(3)传统的教学模型作运动演示和运动分析也存在很多缺陷,一是学校很难保证有一套完整的机械专业的教学模型,而且成本也较大;二是有些空间的机构内部的运动很难观察到;三是装配模型时容易损坏零件,运动容易出故障;四是运动特性的分析也很困难。
齿轮泵泵体的机械加工工艺规程及工装设计(铣夹具)说明书

齿轮泵泵体的机械加工工艺规程及工装设计(铣夹具)说明书1.本文档旨在提供关于齿轮泵泵体的机械加工工艺规程和工装设计(铣夹具)的详细说明和指导。
齿轮泵泵体的机械加工是制造齿轮泵的关键环节之一,合理的加工工艺规程和工装设计可以提高加工效率和产品质量。
2. 工艺流程齿轮泵泵体的机械加工主要包括以下几个步骤:1.加工准备:进行材料准备和设备准备,并检查加工工艺和工装的准备情况。
2.粗加工:采用铣床进行泵体的外形粗加工,包括铣削泵体外形和加工入口。
3.打孔:根据设计要求,在泵体上进行打孔加工,包括入口孔、出口孔和螺纹孔等。
4.铣削:采用铣床进行泵体的平面铣削和曲面铣削加工,保证加工尺寸和平面度的精度。
5.放电加工:对泵体进行放电加工,消除加工过程中可能产生的变形和残留应力。
6.表面处理:根据需要进行砂光、抛光和喷涂等表面处理,提高产品的光洁度和耐腐蚀性。
7.检验和修整:对加工完成的泵体进行检验,包括尺寸检验、外观检验和性能测试等,如有问题则进行修整。
8.包装和出厂:对合格的泵体进行包装,并出厂交付使用。
3. 工装设计(铣夹具)为了确保齿轮泵泵体的加工质量和效率,需要设计合适的工装,提供稳定的夹持和定位功能。
下面是对铣夹具的设计要求和设计流程的详细说明:3.1 设计要求1.夹具结构要稳定,能够保持泵体加工时的定位精度和刚度。
2.夹具布局要合理,能够方便工装的安装和卸载。
3.夹具材料要具有足够的强度和硬度,以承受加工时的力和磨损。
4.夹具要考虑操作人员的安全,避免夹持和定位时的意外伤害。
5.夹具应具备较高的自适应性,以适应不同型号和尺寸的泵体加工。
3.2 设计流程1.分析加工工艺和要求,确定夹具的基本结构和功能。
2.根据泵体的几何形状和加工位置,设计夹具的定位和夹持装置。
3.确定夹具的材料和制造工艺,考虑到夹具的刚度和耐磨性。
4.进行夹具的三维设计和装配,使用CAD软件绘制夹具的工程图纸。
5.进行夹具的结构计算和强度校核,确保夹具在加工过程中能够承受所需的力和磨损。
齿轮油泵泵盖的机械加工工艺规程及工艺装备设计设计说明书

课程设计题目:齿轮油泵泵盖的机械加工工艺规程及工艺装备设计班级:姓名:指导教师:完成日期: 2011年12月29日一、设计题目泵盖零件的机械加工工艺规程及工艺装备设计(钻盲孔162Φ⨯)二、原始资料(1) 被加工零件的零件图 1张 (2) 生产类型:中批或大批大量生产三、上交材料(1) 被加工工件的零件图 1张 (2) 毛坯图 1张 (3) 机械加工工艺过程综合卡片(参附表1) 1张 (4) 与所设计夹具对应那道工序的工序卡片 1张 (4) 夹具装配图 1张 (5) 夹具体零件图 1张 (6) 课程设计说明书(5000~8000字) 1份四、进度安排(参考)(1) 熟悉零件,画零件图 2天(2) 选择工艺方案,确定工艺路线,填写工艺过程综合卡片 5天 (3) 工艺装备设计(画夹具装配图及夹具体图) 9天 (4) 编写说明书 3天 (5) 准备及答辩 2天五、指导教师评语成 绩:指导教师日 期摘要本课程设计主要内容包括齿轮油泵泵盖的加工工艺过程设计和钻16⨯盲孔的专用夹具设计,在课程设计过程中完成2Φ了零件图、毛坯图、夹具体装配图和夹具体零件图的绘制及说明书的编写。
泵盖零件结构较简单,而且为铸件,外表面为要求较高精度要求,铸造即可满足,与其它接触面处的端面精度要求较高,需要经过粗车、半精车加工,保证密封配合性。
本次设计针对16⨯盲孔的加工难度设计了一套专用夹2Φ具,采用一面两孔的定位方式来满足定位要求,又通过夹紧装置保证加工过程中不会产生较大误差。
其中间过程对夹紧装置进行了受力分析,保证了夹紧的可靠性。
综上所述为本次课程设计的主要内容及设计过程AbstractThe main contents of the curriculum design, including gear oil pump cover process design and process of 16⨯blind hole drilling special2Φfixture design in the curriculum design process was completed parts map, blank map of the specific folder and the folder assembly of specific parts and the manual mapping preparation.Pump parts to build a simpler structure, but also for the casting, the outer surface of the requirements for higher precision, casting can be met, contact with other Department of the higher-end precision, cars need to go through thick, semi-refined car processing, to ensure that sealed with sexual.The design for the16⨯blind hole of the processing difficulty of2Φthe design of a special fixture, using a two-hole position to meet position requirements to ensure through clamping device processing will not produce large errors. Intergovernmental process in which a clamping device for mechanical analysis, to ensure the reliability of the clamp.To sum up this meeting the main contents of the curriculum design and the design process目录1零件的工艺性分析 (1)1.1 零件的用途 (1)1.2 零件的技术要求 (1)1.3 审查零件的工艺性 (1)2零件毛坯的确定 (2)2.1零件的生产类型 (2)2.2毛坯的种类和制造方法 (2)2.3零件各表面的加工方法 (3)2.4各工序间加工余量 (3)2.5确定毛坯尺寸 (4)3机械加工工艺规程设计 (4)3.1拟定工艺路线 (4)3.2162Φ⨯孔切削用量的计算 (5)3.316⨯基本工时的计算 (6)2Φ3.4制订16⨯工序卡片 (8)2Φ4 16⨯孔的专用夹具设计 (8)2Φ4.1定位方案的设计 (8)4.2定位误差分析与计算 (9)4.3导向元件设计 (10)4.4夹紧装置的设计 (10)4.5夹具结构设计及操作简要说明 (11)5 方案综合评价与结论 (12)6体会与展望 (12)参考文献 (13)1零件的工艺性分析1.1零件的用途本次课程设计的题目是左端盖的加工以及16⨯孔的专用夹具的2Φ设计。
齿轮泵泵体工艺夹具设计 设计说明书

齿轮泵泵体工艺夹具设计说明书课题名称: 齿轮泵泵体工艺夹具设计专业:班级:姓名:学号:指导老师:年月摘要工艺规程是工装设计、制造和确定零件加工方法与加工路线的主要依据,它对组织生产、保证产品质量、提高劳动生产率、降低成本、缩短生产周期及改善劳动条件等都有着直接的影响,因此是生产中的关键工作。
夹具在机械加工中起着重要的作用,它直接影响着机械加工的质量,生产效率和成本,因此,夹具设计是机械工艺准备和施工中的一项重要工作。
本文对CB-25F型齿轮泵泵体的结构和工艺进行了分析,确定了机械加工工艺路线,制订出了零件的铸造工艺方案和机械加工工艺规程。
关键词:加工工艺;铸造工艺;工艺规程;夹具设计Abstract:The process is the base of frock design、manufacturing、the method of machining and machining route. Its function is flowing: organizing produce, controlling quality, enhancing productivity, reducing cost, reducing produce periods, improving work conditions, etc. So, the process planning is the core part of produce. Fixture is very important equipment in process of machine manufacturing because it can directly affect the quality of products and productivity and cost. So fixture designing is also a basilica portion in machine process preparative and manufacture. This thesis is about the analysis with the craftwork and the structure of the 2105 speed governor tray which is used for the diesel engine, make sure the process route, establish the foundry process project and the process planning of the parts, and design a set of appropriative fixture for the bore with diameter 10mm.Key Words:Group technology; Foundry technology; Process planning; Fixture design目录摘要 (1)1绪论 (4)2夹具的简介 (5)2.1夹具的功用、组成和分类 (5)2.2夹具设计的特点和基本要求 (6)2.3工件在夹具中的定位 (7)3机械加工工艺规程制订 (8)3.1 机械加工工艺过程的定义 (8)3.2 机械加工工艺过程的组成 (8)3.3 机械加工工艺规程的定义 (8)3.4 机械加工工艺规程的作用及内容 (9)3.5 制订机械加工工艺规程的原则及步骤 (9)4 铸造工艺方案设计 (10)4.1 确定毛坯的成形方法 (10)4.2 铸件结构工艺性分析 (10)4.3 铸造工艺方案的确定 (10)4.4 铸造工艺参数的确定 (11)4.5 型芯设计 (12)4.6 绘制铸造工艺图 (12)5 机械加工工艺规程设计 (12)5.1 基面的选择 (12)5.2 表面加工方案的选择 (13)5.3制订机械加工工艺路线 (13)5.4 确定机械加工余量及工序尺寸 (17)5.5 确定切削用量及基本工时 (21)6 夹具设计 (34)6.1 夹具设计 (34)6.2 夹具设定位基准的确定 (40)7 绘制夹具总体图 (41)总结 (42)参考文献 (46)1绪论在机械制造的各个加工工艺过程中,必须使工件在工艺系统中处于正确的位置,以保证加工质量,并提高生产效率。
(完整word版)齿轮油泵建模设计说明书(word文档良心出品)

目录1 绪论 01.1 机械专业传统的教学方式存在的问题 (1)1.2 将三维技术应用到机械类专业课的教学中 (1)2 设计概述 (2)3 设计过程 (3)3.1 齿轮油泵零件建模设计 (3)3.1.1 齿轮油泵骨架的设计 (4)3.1.2 齿轮油泵主体的设计 (5)3.1.3 齿轮油泵左盖的设计 (7)3.1.4 创建齿轮泵右侧盖的设计 (8)3.1.5 齿轮轴的设计 (8)3.1.6 其它零件的创建 (12)3.2 齿轮油泵装配设计 (13)3.2.1 虚拟装配设计 (13)3.2.2 生成爆炸图 (16)4 机构仿真及工作原理动画 (17)4.1 齿轮油泵机构仿真设计 (17)4.2 齿轮油泵工作原理动画仿真 (19)5 总结 (22)致谢 (23)参考文献 (24)1 绪论计算机辅助教学是教学发展的一个焦点,Pro/E等三维建模软件的发展以及虚拟制造技术的出现为机械类专业课教学提供了一种极好的现代化教学的工作平台[1]。
1.1 机械专业传统的教学方式存在的问题(1)在机械类课程的教学中,经常需要实物模型帮助学生理解教学内容,如果没有模型,仅仅依靠讲解,是很难讲清楚一个立体结构的。
学生缺少对实物的感官认识也就更难理解没有模型的讲解,而传统的教学方式是利用教学实物模型,但实物模型携带不方便,而且容易损坏,不便于保管。
(2)教学中存在的另一个问题是传统的教学实物模型一成不变,更新换代的速度慢,而几十年不变的教学模型已不能满足教学和科技时代不断进步的需要。
时代在发展,教学内容在不断更新,当然教学模型也要跟上教学内容的更新,要想根据教学需要更改实物模型是很困难的。
更换新实物模型成本又很高,而旧模型基本没有再利用的价值,造成很大的浪费。
(3)传统的教学模型作运动演示和运动分析也存在很多缺陷,一是学校很难保证有一套完整的机械专业的教学模型,而且成本也较大;二是有些空间的机构内部的运动很难观察到;三是装配模型时容易损坏零件,运动容易出故障;四是运动特性的分析也很困难。
机油泵传动轴支架的夹具设计说明书
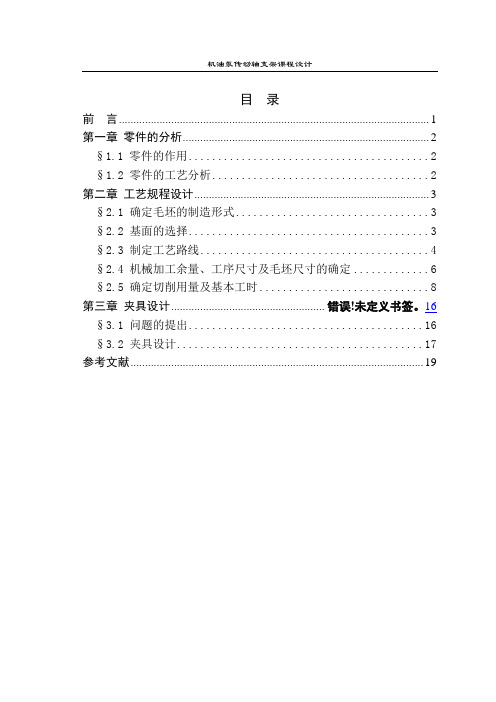
目录前言 (1)第一章零件的分析 (2)§1.1 零件的作用 (2)§1.2 零件的工艺分析 (2)第二章工艺规程设计 (3)§2.1 确定毛坯的制造形式 (3)§2.2 基面的选择 (3)§2.3 制定工艺路线 (4)§2.4 机械加工余量、工序尺寸及毛坯尺寸的确定 (6)§2.5 确定切削用量及基本工时 (8)第三章夹具设计 ............................................... 错误!未定义书签。
16§3.1 问题的提出. (16)§3.2 夹具设计 (17)参考文献 (19)前言机械制造工艺学课程设计是我们融会贯通大学所学的知识,将理论与实践相结合,对专业知识的综合运用训练,为我们即将走向自己的工作岗位打下良好的基础。
机械加工工艺是规定产品或零件机械加工工艺过程和操作方法,是指导生产的重要的技术性文件。
它直接关系到产品的质量、生产率及其加工产品的经济效益,生产规模的大小、工艺水平的高低以及解决各种工艺问题的方法和手段都要通过机械加工工艺来体现,因此工艺规程的编制的好坏是生产该产品的质量的重要保证的重要依据。
在编制工艺时须保证其合理性、科学性、完善性。
而机床夹具是为了保证产品的质量的同时提高生产的效率、改善工人的劳动强度、降低生产成本而在机床上用以装夹工件的一种装置,其作用是使工件相对于机床或刀具有个正确的位置,并在加工过程中保持这个位置不变。
它们的研究对机械工业有着很重要的意义,因此在大批量生产中,常采用专用夹具。
一、零件的分析1.1 零件的作用如右图所示,题目所给定的零件是机油泵传动轴支架。
它位于传动轴的端部。
主要作用是支承传动轴,连接油口,起到固定机油泵的作用。
是拖拉机里用到的最普遍的零件之一。
它结构简单,体积也较小,属叉架类零件。
其中φ32孔要与轴配合,要求精度较高。
齿轮泵泵体的机械加工工艺规程及工装设计(铣夹具)说明书 (2)

齿轮泵泵体的机械加工工艺规程及工装设计(铣夹具)说明书1. 引言1.1 背景齿轮泵是一种常见的液压传动装置,被广泛应用于各个领域,如汽车、工程机械、船舶等。
齿轮泵的核心部件之一是泵体,它承载着齿轮和轴的工作负荷,因此其加工精度和质量必须得到保证。
本文档旨在介绍齿轮泵泵体的机械加工工艺规程以及工装设计,特别是针对铣夹具的设计。
1.2 目的本文档的目的是提供一份详细的齿轮泵泵体加工工艺规程及工装设计说明书,以帮助操作人员正确进行泵体的加工操作,并保证最终产品的质量。
2. 加工工艺规程2.1 工艺流程以下是齿轮泵泵体的加工工艺流程:1.下料:根据设计要求选择合适的材料,并根据零件图纸进行下料。
2.粗加工:使用数控铣床对泵体进行粗加工,包括平面铣削、孔加工等。
3.热处理:根据材料要求进行热处理,以提高材料的硬度和强度。
4.精加工:利用数控铣床进行泵体的精加工,如表面加工、孔的精确定位等。
5.辅助加工:根据需要进行螺纹加工、刻线等辅助操作。
6.清洗:使用清洗剂对加工完成的泵体进行清洗,以去除杂质和油污。
7.检验:对泵体进行外观检查和尺寸检测,以验证工艺加工是否符合要求。
8.组装:将泵体与其他部件进行组装,并进行最终装配。
2.2 加工工艺要点在齿轮泵泵体的加工工艺中,有几个关键要点需要注意:1.加工前要根据零件图纸进行严格的加工准备,包括检查设备的准备情况、工艺文件的完整性等。
2.在粗加工过程中,要保持合适的切削速度和进给量,以确保加工效率和质量。
3.对于精加工过程中的平面加工和孔加工,要使用合适的刀具,并控制好切削参数,确保加工表面的光洁度和尺寸精度。
4.在热处理过程中,要控制好加热温度和保持时间,以确保材料的硬度和强度达到要求。
5.进行辅助加工时,要注意保持刀具的锋利度,并根据需求进行合适的加工操作。
6.在检验环节中,要根据严格的检验标准进行检验,以确保加工质量符合要求。
7.组装过程中,要严格控制装配间隙,并进行必要的调整和配合。
a型齿轮油泵说明书

一.测绘的目的与任务在工程制图课的学习过程中,我们已学习了机械零件及简单装配体的测绘。
本次制图测绘课是对所学工程制图课的一次综合实践与训练。
通过这次测绘,进一步巩固和提高工程制图理论及测绘技能,学会部件测绘的基本方法与步骤,进一步培养我们严肃认真的工作态度和一丝不苟的工作作风,为后续课程的学习及以后从事工程技术工作和应用高等技术解决工程实际问题打下良好的基础。
本次测绘利用五天(一周)集中进行,测绘任务是运用所学的有关制图知识,对齿轮油泵的工作原理和装配关系进行分析,结合生产实际按要求绘制出齿轮油泵的全部零件(不包括标准件)草图、装配工作图及全部非标准零件的工作,并装订成册。
二.测绘步骤1.了解测绘体1.1测绘体的用途齿轮油泵用于发动机的润滑系统,它将发动机底部油箱中的润滑油送到发动机上有关运动部件需要润滑的部位,如发动机的主轴、连杆、摇臂、凸轮颈等。
该齿轮油泵其结构大体为参照装配示意图及装配体实在泵体内装有二个齿轮,一个是主动齿轮轴6,另一个是从动齿轮轴2(均由泵体、泵盖支承),通过主动齿轮轴上的齿轮(用键连接,图中未画),传递給主动齿轮轴,并带动从动齿轮轴旋转(旋转方向见封面工作原理图)使右边吸油腔形成部分真空,润滑油被吸入并充满齿槽,由于齿轮旋转,润滑油沿着壳壁被带到左边压油腔内,由于齿轮啮合使齿槽内润滑油被挤压,从而产生高压油输出。
该齿轮油泵在750转/分钟时,油压应为0.4-0.6兆帕。
为使油压不超过该压力,在泵盖上有限压阀装置,它由螺塞16,小垫片15,弹簧14,钢珠定位圈13和钢珠12组成。
当油压超过0.6兆帕,高压油就克服弹簧压力,将钢珠阀门顶开,使润滑油自压油腔流回吸油腔,以保证整个润滑系统安全工作。
填料3、垫片7、小垫片15主要起密封防漏作用。
垫片7的厚度大小,还可以调节齿轮两侧面间隙的大小。
1.2测绘体的工作原理在泵体内装有一对互相啮合的圆柱齿轮,齿轮轴1的轴端伸出泵体,以接传动力,并通过填料3、压盖4和压紧螺母进行密封;从动齿轮8以过盈配合装在从动轴上,并加固圆柱销以防相互间转动;齿轮轴和从动小轴的轴颈以间隙配合安装在泵体和泵盖的轴孔中,泵体与泵盖是靠两个圆柱销定位,并用六个螺钉连接在一起。
齿轮油泵设计说明书

绪论一、课程设计内容根据齿轮油泵的工作原理和零件图,看懂齿轮油泵的全部零件图,并将标准件按其规定标记查出有关尺寸。
应用AutoCAD软件绘制所有正式零件图,装配图(A3图纸幅面1张),用UG绘制所有正式零件的三维图形。
二、齿轮油泵工作原理齿轮油泵示意图工作原理部分:齿轮油泵是依靠一对齿轮的传动把油升压的一种装配,泵体12内有一对齿轮,轴齿轮15是主动轮,轴齿轮16是被动轮,如下图所示。
动力从主动轮输入,从而带动被动轮一起旋转。
转动时齿轮啮合区的左方形成局部真空,压力降低将油吸入泵中,齿轮继续转动,吸入的油沿着泵体内壁被输送到啮合处的右方,压力升高,从而把高压油输往需要润滑的部位。
防渗漏:为使油泵不漏油,泵体和泵盖结合处有密封垫片13(垫片形状与泵体、泵盖结合面相同),主动轴齿轮伸出的一端处填料压盖防漏装置,由填料10、填料压盖9、螺栓组(件18、件8)组成。
连接与定位:泵体与泵盖之间用螺钉18连接,为保证相对位置的准确,用定位销11定位。
齿轮油泵工作原理拆装顺序:泵体---主动轴和被动轴---垫片、泵体—定位销—螺钉---填料---压盖三、齿轮油泵零件之间的公差配合1. 齿轮端面与泵体、泵盖之间为32K6;2. 齿顶圆与泵体内孔为Φ48H7/d7;3. 主动轴齿轮、被动轴齿轮的两支承轴与泵体、泵盖下轴孔为Φ16H7/h6;4. 填料压盖与泵体孔径为Φ32H11/d11。
四、齿轮油泵的其它技术要求1. 装配后应当转动灵活,无卡阻现象;2. 装配后未加工的外表面涂绿色。
第一章二维零件图第一章绘制三维零件图第一节、泵盖齿轮油泵泵盖如图所示。
具体建模步骤如下:图1-1 泵盖一、整体建模1、打开UG,新建模型。
在菜单栏中选择“插入”\“设计特征”\“长方体”命令。
系统弹出“长方体”对话框。
如图1-2a所示。
2、在“类型”下拉表框中选择“两点和高度”选项,单击按钮弹出点对话框设置两点位置,相对于wcs坐标系第一点位置为(42,21,0)、第二点为(-42、-21、0),在“尺寸”选项中输入高度为10mm。
齿轮油泵工艺设计和夹具设计

本科毕业设计(论文)通过答辩学科门类:单位代码:毕业设计说明书(论文)齿轮油泵工艺设计和夹具设计学生姓名所学专业班级学号指导教师二○**年**月毕业设计任务书20**年3月1日20**年3月1日目录摘要----------------------------------------------------------------------ⅡAbstract------------------------------------------------------------------Ⅲ齿轮油泵工艺设计和夹具设计------------------------------------------------------------------------1第1章引言--------------------------------------------------------------1 第2章型号意义示例------------------------------------------------------2 第3章齿轮油泵的主要性能参数--------------------------------------------3 第4章齿轮油泵的特性曲线------------------------------------------------5 第5章齿轮油泵工作原理--------------------------------------------------6 第6章齿轮油泵的主要部件------------------------------------------------76.1 叶轮----------------------------------------------------------76.2 泵壳----------------------------------------------------------76.3 泵轴----------------------------------------------------------106.4 轴承----------------------------------------------------------116.5 悬架----------------------------------------------------------116.6 机械密封------------------------------------------------------136.7 填料函--------------------------------------------------------14 第7章齿轮油泵的安装----------------------------------------------------15 第8章齿轮油泵的油泵检验标准--------------------------------------------17 第9章齿轮油泵的操作程序------------------------------------------------21 第10章合理配置、安全运行、优质供油-------------------------------------24 第11章齿轮油泵容易发生的故障-------------------------------------------26 第12章齿轮油泵间性能的改变和换算---------------------------------------29 第13章齿轮油泵流量控制方法探讨------------------------------------------30 第14章结束语-----------------------------------------------------------31 致谢-----------------------------------------------------------------------31 参考文献-------------------------------------------------------------------32 毕业设计小结---------------------------------------------------------------33摘要油齿轮油泵吸收了KT、SB、ES、IS、XA及国外优秀油泵系列产品的优点,采用了多项油力设计及工艺方法的发明专利和实用新型专利而研制开发的高新技术系列产品。
A型齿轮油泵泵体进出油口端面螺纹底孔2×M6钻夹具3D设计
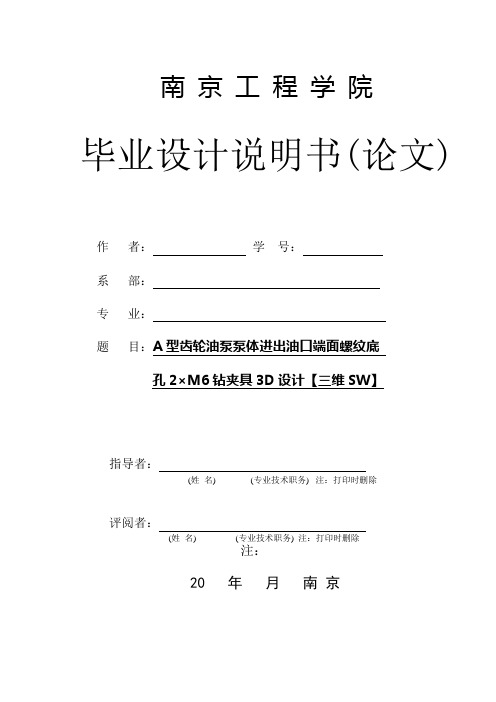
南京工程学院毕业设计说明书(论文)作者:学号:系部:专业:题目:A型齿轮油泵泵体进出油口端面螺纹底孔2×M6钻夹具3D设计【三维SW】指导者:(姓名) (专业技术职务)注:打印时删除评阅者:(姓名) (专业技术职务) 注:打印时删除注:20 年月南京毕业设计说明书(论文)中文摘要目录第1章绪论 (1)1.1 钻孔夹具方案设计 (1)1.2 了解夹具总体设计的要求 (1)1.3 钻床的发展趋势 (2)1.4钻床夹具的概述 (3)1.4.1钻床夹具的特点 (3)1.4.2钻床夹具的主要类型 (3)1.4.3钻模类型选择 (4)1.4.4钻套的选择 (4)1.4.5钻模板类型 (5)第2章钻床夹具设计特点 (6)2.1 确定夹具的类型 (6)2.2 钻模的主要类型 (6)2.3 明确设计任务,了解零件加工工艺过程 (7)2.3.1 熟悉工件零件图、本工序加工要求 (7)2.3.2 熟悉零件加工工艺过程 (7)2.4 确定定位方案 (7)第3章工件的夹紧计算及其选择 (9)3.1 工件的夹紧 (9)3.1.1 夹紧基本原理理论 (9)3.1.2 夹紧座 (10)3.1.3 夹紧压板 (10)3.1.4 夹紧螺钉 (11)3.2 夹紧力的选择 (12)3.2.1 夹紧力方向 (12)3.2.2 夹紧力的作用点 (12)3.2.3 夹紧力的计算 (12)3.2.4 夹具精度计算与分析 (14)第4章夹具结构分析与设计 (15)4.1 夹具的夹紧装置和定位装置 (15)4.2 夹具的导向 (16)4.3 钻孔与工件之间的切屑间隙 (19)4.4 钻模板 (20)4.5定位误差的分析 (20)4.6 钻套、衬套、钻模板设计与选用 (21)4.7 确定夹具体结构和总体结构 (23)4.8 三维装配图SOLIDWORKS建模 (24)4.9 夹具设计及操作的简要说明 (26)结论 (27)致谢 (29)参考文献 (30)第1章绪论1.1 钻孔夹具方案设计方案设计是夹具设计的重要阶段,它在分析各种原始资料的基础上,要完成下列设计工作:[1]①研究壳体零件原始资料,明确设计要求。
齿轮油泵泵体加工工艺及钻孔夹具设计

设计(论文)题目:齿轮油泵泵体加工工艺及夹具设计学生姓名:指导教师:二级学院:专业:班级:学号:提交日期:年月日答辩日期:年月日摘要本设计是基于齿轮油泵泵体零件的加工工艺规程及一些工序的专用夹具设计。
齿轮油泵泵体零件的主要加工表面是平面及孔系。
一般来说,保证平面的加工精度要比保证孔系的加工精度容易。
因此,本设计遵循先面后孔的原则。
并将孔与平面的加工明确划分成粗加工和精加工阶段以保证孔系加工精度。
基准选择以齿轮油泵泵体的输入轴和输出轴的支承孔作为粗基准,以顶面与两个工艺孔作为精基准。
主要加工工序安排是先以支承孔系定位加工出顶平面,再以顶平面与支承孔系定位加工出工艺孔。
在后续工序中除个别工序外均用顶平面和工艺孔定位加工其他孔系与平面。
支承孔系的加工采用的是坐标法镗孔。
整个加工过程均选用组合机床。
夹具选用专用夹具,夹紧方式多选用气动夹紧,夹紧可靠,机构可以不必自锁,因此生产效率较高,适用于大批量、流水线上加工,能够满足设计要求。
关键词:齿轮油泵泵体类零件;工艺;夹具;ABSTRACTThe design is based on the body parts of the processing order of the processes and some special fixture design. Body parts of the main plane of the surface and pore system. In general, the plane guarantee processing precision than that of holes machining precision easy. Therefore, this design follows the surface after the first hole principle. Plane with holes and the processing clearly divided into roughing and finishing stages of holes to ensure machining accuracy. Datum selection box input shaft and the output shaft of the supporting hole as a rough benchmark, with top with two holes as a precision technology reference. Main processes arrangements to support holes for positioning and processing the top plane, and then the top plane and the supporting hole location hole processing technology. In addition to the follow-up processes individual processes are made of the top plane and technological hole location hole and plane processing. Supported hole processing using the method of coordinate boring. The whole process of processing machine combinations were selected. Selection of special fixture fixture, clamping means more choice of pneumatic clamping, clamping reliable, institutions can not be locked, so the production efficiency is high, suitable for large batch, line processing, can meet the design requirements.Key words: box type parts process; fixture;目录摘要 (1)ABSTRACT (7)第1章绪论 (10)1.1 机械加工工艺概述 (10)1.2机械加工工艺流程 (10)1.3夹具概述 (11)1.4机床夹具的功能 (11)1.5机床夹具的发展趋势 (12)1.5.1机床夹具的现状 (12)1.5.2现代机床夹具的发展方向 (12)第2章加工工艺规程设计 (14)2.1零件的分析 (14)2.2齿轮油泵泵体加工的主要问题和工艺过程设计所应采取的相应措施 (14)2.2.1孔和平面的加工顺序 (14)2.2.2 孔系加工方案选择 (15)2.3齿轮油泵泵体加工定位基准的选择 (15)2.3.1粗基准的选择 (15)2.3.2精基准的选择 (16)2.4 齿轮油泵泵体加工主要工序安排 (16)2.5 机械加工余量、工序尺寸及毛坯尺寸的确定 (18)2.6确定切削用量及基本工时(机动时间)[3] (19)2.7时间定额计算及生产安排 (28)第3章钻孔夹具设计 (33)3.1研究原始质料 (33)3.2定位基准的选择 (33)3.3切削力及夹紧力的计算 (33)3.4误差分析与计算 (34)3.5 零、部件的设计与选用 (35)3.5.1定位销选用 (35)3.5.2夹紧装置的选用 (36)3.5.3 钻套、衬套、钻模板设计与选用 (36)3.6夹具设计及操作的简要说明 (38)总结 (38)参考文献 (39)致谢 (40)第1章绪论1.1 机械加工工艺概述机械加工工艺是指用机械加工的方法改变毛坯的形状、尺寸、相对位置和性质使其成为合格零件的全过程,加工工艺是工人进行加工的一个依据。
B型齿轮油泵课程设计说明书
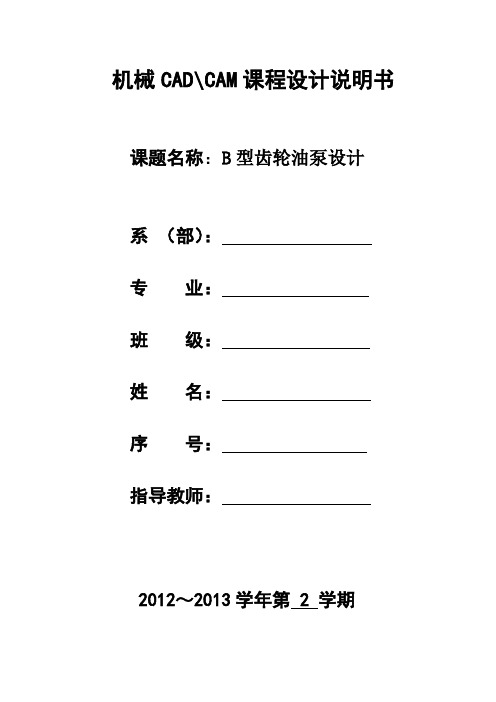
机械CAD\CAM课程设计说明书课题名称:B型齿轮油泵设计系(部):专业:班级:姓名:序号:指导教师:2012~2013学年第 2 学期目录第一章绪论 (3)第二章零件设计 (3)一、泵盖的设计 (3)二、泵体的设计 (7)三、主动轴设计 (13)四、从动轴设计 (15)五、主动齿轮设计 (16)六、从动齿轮设计 (17)七、填料螺塞设计 (18)八、调压螺柱设计 (21)九、螺栓的设计 (23)十、弹簧的设计 (23)十一、钢球的设计 (23)十二、长销设计 (23)十三、短销的设计 (23)第三章零件装配 (24)一、泵体装配图 (24)第四章爆炸图生成 (24)第五章课程设计总结• (25)第一章、绪论一.机械CAD\CAM简介机械CAD/CAM是计算机辅助设计或制造(Computer Aided Design/Computer Aided Manufacture)的简称,是当今世界发展最快的技术之一。
目前,CAD/CAM技术已经在许多领域中得到应用,其中,在机械设计及制造中CAD\CAM应用更为广泛和重要。
另外,CAD\CAM输出的结果也不仅仅是装配图和零件图,还包括设计、制造过程中应用计算机所需的各种信息。
二.本次课程设计的目的1、了解UG NX 6.0软件基本功能特点;2、学会UG NX6.0绘图基本技巧和方法及典型操作流程;3、熟练掌握零件装配方法。
三.课程设计任务1. 自行选择一个齿轮油泵,它的零件数要在15个零件以上,其中相同的零件算一个;2. 选定齿轮泵后,要先对其结构分析和尺寸确定;3. 创建零件模型,完成后进行装配,生成装配图;4. 完成装配图爆炸图;5. 课程设计总结。
第二章、零件设计一、泵盖的设计设计说明(1) 启动UG NX 6.0 软件,单击“标准”工具条中的“新建”按钮,弹出“文件新建”对话框,在“模板”中选择“模型”,在“名称”文本框中输入“benggai”,接着选择文件保存路径“E:\ug\chilunyoubenglingjian”,单击“确定”按钮,进入标准界面。
A型齿轮油泵泵体安装板底面铣夹具3D设计
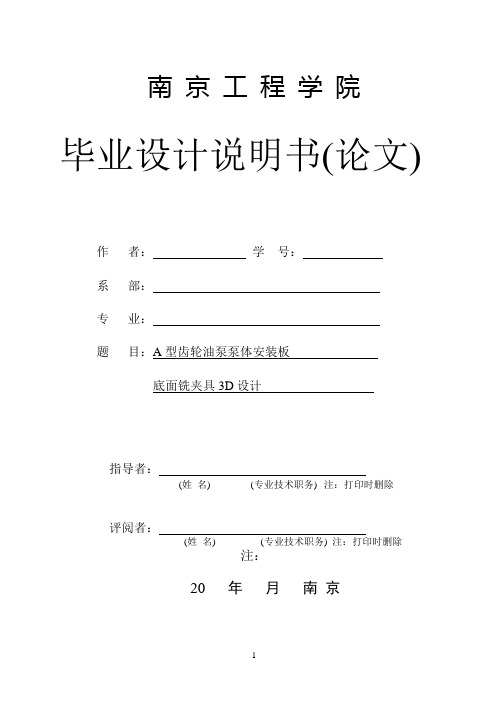
南京工程学院毕业设计说明书(论文)作者:学号:系部:专业:题目:A型齿轮油泵泵体安装板底面铣夹具3D设计指导者:(姓名) (专业技术职务)注:打印时删除评阅者:(姓名) (专业技术职务) 注:打印时删除注:20 年月南京南京工程学院毕业设计说明书(论文)毕业设计说明书(论文)中文摘要A型齿轮油泵泵体零件加工工艺及夹具设计是包括零件加工的工艺设计、工序设计以及专用夹具的设计三部分。
在工艺设计中要首先对零件进行分析,了解零件的工艺再设计出毛坯的结构,并选择好零件的加工基准,设计出零件的工艺路线;接着对零件各个工步的工序进行尺寸计算,关键是决定出各个工序的工艺装备及切削用量;然后进行专用夹具的设计,选择设计出夹具的各个组成部件,如定位元件、夹紧元件、引导元件、夹具体与机床的连接部件以及其它部件;计算出夹具定位时产生的定位误差,分析夹具结构的合理性与不足之处,并在以后设计中注意改进。
关键词工艺,工序,切削用量,夹紧,定位,误差毕业设计说明书(论文)外文摘要Title A type gear pump mounting plate bottom milling fixture design 3DAbstractDisc type parts processing technology and fixture design is the design of process design, including the parts processing process design and the three part special fixture. In the process of design should first of all parts to analyze, understand parts of the process and then design a blank structure, and choose the good parts of the machining datum, designs the process routes of the parts; then the parts each step process dimension calculation, the key is to determine the process equipment and cutting the amount of each working procedure design; then a special fixture, fixture for the various components of a design, such as the connecting part positioning device, clamping element, a guide element, clamp and the machine tool and other components; the positioning error caused calculate fixture when positioning, analysis of the rationality and deficiency of fixture structure, pay attention to improving and will design in.Keywords process, process, cutting, clamping, positioning, error目录第1章绪论 (1)1.1 夹具设计目的与意义 (1)1.2 专用夹具设计的国内外现状 (2)1.2.1 国内专用技术应用及现状 (2)1.2.2 专用工艺在国外的发展状况 (3)1.3 专用夹具设计的发展趋势 (4)第2章专用夹具的设计 (6)2.1 铣床专用夹具的主要类型 (6)2.2 铣床专用夹具的设计要点 (6)2.3 夹紧装置 (7)2.4 专用夹具的基准选择 (7)2.5 机床夹具的概述 (8)2.5.1 机床夹具的种类 (8)2.5.2 机床夹具的组成 (8)2.6 铣床夹具的分类 (9)2.7 铣削专用夹具的设计要点 (9)2.8 铣床夹具的安装 (9)2.9 工件的定位与误差分析 (10)2.9.1 工件定位的基本原理 (10)2.9.2 定位方法与定位元件 (11)2.9.3 工件的误差分析 (12)2.9.4 定位误差产生的原因 (12)2.10 夹紧装置 (13)2.10.1夹紧装置的组成 (13)2.10.2 对夹紧装置的基本要求 (13)2.10.3 夹紧力的确定 (14)2.10.4 夹紧力大小计算 (14)第3章铣削安装板底面精加工工序专用夹具的设计 (16)3.1 明确设计任务,了解零件加工工艺过程 (16)3.1.1 熟悉工件零件图、本工序加工要求 (16)3.1.2 熟悉零件加工工艺过程 (16)3.2 确定定位方案 (16)3.2.1 基准的选择 (16)3.2.2 确定定位夹紧方案 (17)3.2.3 定位元件的选择及设计 (17)3.3 定位误差的计算与分析 (18)3.4 计算切削力及实际所需的夹紧力 (19)3.5 设计夹紧机构并验算机构所能产生的夹紧力 (21)3.6 主要元件的设计与建模 (22)3.7 对刀元件及夹具体 (23)第4章夹具图的绘制 (24)4.1 工序图 (24)4.2 夹具体零件图 (24)4.3 绘制夹具装配总图 (24)4.4 标注总图上的尺寸、公差与配合和技术条件 (25)4.4.1 标注尺寸、公差与配合 (25)4.4.2制订技术条件 (25)4.5 三维装配图SOLIDWORKS建模 (26)第5章夹具工作精度分析 (30)5.1 位置尺寸70 0.10 (30)5.2平面度允差0.2mm (30)结论 (31)致谢 (32)参考文献 (33)第1章绪论1.1 夹具设计目的与意义夹具是机械制造厂里的一种工艺装备,机床夹具就是机床上用以装夹工件的一种装置,它使得工件相对于刀具或机床活动正确的位置,并在加工过程中不因外力的影响而变动。
齿轮油泵泵体夹具设计说明书

毛坯直径=Φ27mm,查①表1-20和①表2-40确定钻孔至Φ16mm,粗铰至ΦΦmm,精铰至Φ18mm,则深度尺寸为42mm
6)车M27外螺纹,车3x1槽
车M27外螺纹,加工余量为2mm,一次车削攻螺纹。
车3x1槽
粗糙度要求为Ra=25,一次车削,车槽。
第四章 确定切削用量与时间定额
其他时间的计算
在本设计中,因零件是大批量生产,故分摊到每个工件上的准备与终结时间很少忽略不计,布置工作地时间tb和休息与生理需要时间tx分别取作业时间的3%,则其他时间tb+tx可按关系式(3%+3%)*(tj+tf)
tb+tx=6%*(12.8+1.91)=0.88s
工序1加工总时间:tdj=12.8+1.91+0.88=15.59s。
工序号
工序内容
定位面
机床设备
刀具
量具
0
锻造、清砂、退火
1
粗铣M27端面
前端面,Φ40,Φ13两孔定位
立式铣床X51
面铣刀
游标卡尺
2
粗铣,半精铣前端面
M27端面
立式铣床X51
面铣刀
游标卡尺
3
粗铣,半精铣,精铣2x 40H7孔
M27端面
立式铣床X51
面铣刀
游标卡尺
4
钻,铰2x 13H7孔
M27端面
立式钻床Z515
在机床上加工工件时,为了保证加工精度,必须正确安装工件,使其相对机床切削成形运动和刀具占有正确的位置,这一过程称为“定位”。为了不因受切削力、惯性力、重力等外力作用而破坏工件已定的正确位置,还必须对其施加一定的夹紧力,这一过程称为“夹紧”。定位和夹紧的全过程称为“安装”。在机床上用来完成工件安装任务的重要工艺装备,就是各类夹具中应用最广泛的“机床夹具”。
- 1、下载文档前请自行甄别文档内容的完整性,平台不提供额外的编辑、内容补充、找答案等附加服务。
- 2、"仅部分预览"的文档,不可在线预览部分如存在完整性等问题,可反馈申请退款(可完整预览的文档不适用该条件!)。
- 3、如文档侵犯您的权益,请联系客服反馈,我们会尽快为您处理(人工客服工作时间:9:00-18:30)。
铣刀转速 n=1000*40/(3.14*80)
=178.65r/min
查①表4-15取转速n=160r/min,
则实际切削速度 v=3.14nd/1000
=3.14*160*80/1000
=40.2m/min
基本时间tj的计算:查①表5-43中铣刀铣平面(不对称铣削)的基本时间计算公式:
课程设计说明书
设计题目 设计“齿轮油泵泵体“零件的机械加工工艺规程
及工艺装备(年产量为4000件)
设 计 者:计秋华
指导教师:郭永环
徐州师范大学
机制教研室
2011年12月22日
《机械制造技术》
课程设计任务书
设计题目 设计“齿轮油泵泵体”零件的机械加工工艺规程
及工艺装备(年产量为4000件)
设计内容 1.原始零件图 1张
2.2确定毛坯的种类和生产类型
因设计条件:零件年生产量4000件,查①表1-4得,零件为中等批量生产。零件材料采用25Cr2MoVA,因金属模机器造型生产率较高,锻造件精度高,表面质量与机械性能均好,适用于大批量大量生产,因此选择金属模机器造型。同时因铸件壁厚差距不能太大,以避免造成各部分因温差悬殊而引起缩裂、缩孔与裂纹。铸件应进行人工时效。消除残余应力后再送机械加工车间加工,否则工件将产生大的变形。
查①表达式2-1得R=F-2RMA+CT/2 (外圆)(2-1)
查①表达式2-2得R=F-2RMA-CT/2(内圆)(2-2)
查①表2-1取大批量生产的毛坯铸件的公差等级为CT8,
查①表2-5取要求机械加工余量等级为F级
M27端面:查①表2-4取RMA=2
前端面:查①表2-4取RMA=2
Φ40孔:查①表2-4取RMA=2
第二章 齿轮油泵的工艺分析
2.1 齿轮泵的应用
机油泵是在润滑系统中,可迫使机油自油底壳送到引擎运动件的装置。用来使机油压力升高和保证一定的油量,向各摩擦表面强制供油的部件,内燃机广泛采用齿轮式和
转子式机油泵,齿轮式油泵结构简单,加工方便,工作可靠,使用寿命长,泵油压力高,得到广泛应用
图2-1齿轮油泵泵体零件简图
麻花钻、扩孔钻
卡尺、塞规
5
钻6xM6螺纹孔
M27端面
立式铣床Z515
麻花钻
卡尺、塞规
6
钻2x4T15孔
M27端面
立式钻床Z515
麻花钻
卡尺、塞规
7
粗铣底面
前端面,Φ40,Φ13两孔定位
卧式铣床XW60
面铣刀
游标卡尺
8
钻,扩M27内孔
前端面,Φ40,Φ13两孔定位
立式钻床Z515
麻花钻、扩孔钻
卡尺、塞规
5)钻,扩Φ18内孔
毛坯直径=Φ27mm,查①表1-20和①表2-40确定钻孔至Φ16mm,粗铰至ΦΦmm,精铰至Φ18mm,则深度尺寸为42mm
6)车M27外螺纹,车3x1槽
车M27外螺纹,加工余量为2mm,一次车削攻螺纹。
车3x1槽
粗糙度要求为Ra=25,一次车削,车槽。
第四章 确定切削用量与时间定额
Ln=Ln-1±Zn-1 (n≥1) (3-1)
因此,确定了加工余量后,即可根据设计尺寸推算出各工序尺寸,上式只适用较简单的工序尺寸的确定,对于较复杂的工序尺寸的确定需要要进行尺寸链的换算。
1)粗铣M27端面
查②表8-34取磨平面加工余量=2mm。
2)粗铣、半精铣前端面,粗铣,半精铣,精铣2x 40H7孔内端面
机床夹具是随机械加工技术发展的。机床夹具由适用单件小批量生产的用夹具发展到大批量生产的专用夹具、随行夹具,经历了市场的发展和技术的推动。随着现在市场需要的多样化、多品种、中小批量及短周期的生产方式在世界贸易中逐渐成为主导方式,传统的专为某个零件的一道工艺设计制造的专用夹具已经不能适应这种生产方式的要求。因此,适用于多品种、中小批量生产特点的通用可调夹具、组合夹具、成组夹具等应运而生。数控技术的进步与发展,使得数控机床、加工中心在机械加工中广泛运用,数控机床夹具也迅速的发展起来。
4.1切削用量的选择原则
合理地选择切削用量,对保证加工精度和表面质量,提高生产率和刀具耐用度等,都有很大的影响。
选择切削用量是指要选定切削深度、进给量和切削速度。在这3个因素中,对刀具耐用度影响最大的是切削速度,其次是进给量,而切削深度影响最小,对表面粗糙度影响最大的是进给量,而对切削力影响最大的则是切削速度。因此,在粗加工阶段,应考虑选择尽可能大的切削深度,其次是选择较大的进给量,最后确定一个合适的切削速度。在半精、精加工阶段,由于加工精度和表面质量的要求较高,因此一般均选择较小的切削深度和进给量,在保证刀具耐用度的前提下,应选取较高的切削速度,以保证加工质量和生产率的要求。
工序号
工序内容
定位面
机床设备
刀具
量具
0
锻造、清砂、退火
1
粗铣M27端面
前端面,Φ40,Φ13两孔定位
立式铣床X51
面铣刀
游标卡尺
2
粗铣,半精铣前端面
M27端面
立式铣床X51
面铣刀
游标卡尺
3
粗铣,半精铣,精铣2x 40H7孔
M27端面
立式铣床X51
面铣刀
游标卡尺
4
钻,铰2x 13H7孔
M27端面
立式钻床Z515
第六章夹具体设计26
第一章 绪论
1.1 机械加工工艺概述及发展趋势
机械加工工艺是制造技术的灵魂、核心和关键。产品从设计变为现实是必须通过加工才能完成的,工艺是设计和制造的桥梁,设计的可行性往往会受到工艺的制约,工艺往往会成为“瓶颈”,不是所有设计的产品都能加工出来,也不是所有的设计产品通过加工能达到预定技术性能要求的。
4.2切削用量、时间定额的计算
以下为主要加工工序的切削用量及要求另外计算的工序的切削用量:
1)工序号1:粗铣M27端面
背吃刀量的确定:由上述可知粗铣ap=粗铣余量=2mm
进给量的确定:查①5-7按机床功率取每齿进给量fz=0.08mm/z
铣削速度的计.9m/min
第三章 工艺设计
3.1基准的选择
3.1.1精基准的选择
选择泵体的M27端面作为精基准。该零件上的很多孔都可以采用它作为基准进行加工,遵循了“基准统一”原则,同时M27端面亦为设计基准,遵循了“基准重合”原则。
3.1.2粗基准的选择
作为粗基准应平整,没有飞边、毛刺等表面缺欠,故选择零件前端面作为粗基准。
前端面:查②表8-33取半精铣余量1mm,则粗铣余量=总加工余量-半精铣余量-磨削余量=2-1=1mm。
粗铣,半精铣,精铣2x 40H7孔内端面:查②表8-33取粗铣余量1mm,半精铣余量0.5mm,则精铣加工余量为2-1-0.5=0.5mm.
3)钻,铰2x 13H7孔,钻6xM6螺纹孔,钻2x4T15定位孔.
=178.65r/min
查①表4-15取转速n=160r/min,
则实际切削速度 v=3.14nd/1000
④ 先平面后孔。这是因为平面定位比较稳定可靠,所以对于箱体、支架、连杆等类平面轮廓尺寸较大的零件,常先加工平面。
⑤ 除用为基准的平面外,精度越高,粗糙度Ra值越小的表面应放在后面加工以防止划伤
⑥表面位置尺寸及公差标注方式也影响工序顺序,应力求能直接保证或使尺寸链数日减少。
3.2工艺方案
表3-1齿轮油泵泵体工艺路线及设备、工装的选用
加工技术的发展往往是从工艺突破的,近年来加工工艺技术有了很大的发展,现代制造技术已经不的单独的加工方法和工匠的“手艺”,已经发展成为一个系统,在制造工艺理论和技术上有了很大的发展,例如在加工理论方面主要有:加工成形机理和技术、精度原理和技术、相似性原理和成组技术、工艺决策原理和技术等。由于近些年制造工艺技术的发展,工艺内同有了很大的扩展,工艺技术水平有了很大提高:计算机技术、数控技术的发展是制造工艺自动化技术和工艺质量管理工作产生了革命性变化;同时,与工艺有关的许多标准已进行了修订,并且制定了一些新的标准。
2.机械加工工艺综合卡 1张
3.工序卡 1张
4.夹具装配图 1张
5.夹具体零件图 1张
6.设计说明书 1份
班 级:08机42
学 生: 计秋华
指导教师:郭永环
院系主任:韩继光
徐州师范大学
2011年12月22日
摘要
在机械制造的机械加工、检验、装配、焊接和热处理等冷热工艺过程中,使用着大量的夹具,用以安装加工对象,使之占有正确的位置,以保证零件和产品的质量,并提高生产率。
1.2机床夹具的概述及发展趋势
在机械制造的切削加工、检验、装配、焊接和热处理等工艺过程中,要使用大量的夹具来安装加工对象,使其占有正确的位置,以保证零件和产品的加工质量,并提高生产率,从而提高其经济性。把工件迅速固定在正确位置上,完成切削加工、检验、装配、焊接和热处理等工作所使用的工艺装备称为夹具。把机床上用来完成工件装夹任务所使用的工艺装备称为机床夹具。
在机床上加工工件时,为了保证加工精度,必须正确安装工件,使其相对机床切削成形运动和刀具占有正确的位置,这一过程称为“定位”。为了不因受切削力、惯性力、重力等外力作用而破坏工件已定的正确位置,还必须对其施加一定的夹紧力,这一过程称为“夹紧”。定位和夹紧的全过程称为“安装”。在机床上用来完成工件安装任务的重要工艺装备,就是各类夹具中应用最广泛的“机床夹具”。
9
车M27外螺纹
Φ13孔
CA6140车床
车刀
卡尺、塞规
10
车3x1槽
Φ13孔
CA6140车床
车刀
卡尺、塞规
17
去毛刺
钳工台
平锉
18
最终检验
塞规、百分表、卡尺等
3.3 工序尺寸的确定