金属液态成形
第一章 金属液态成形理论基础

第一节 液态金属充型能力与流动性
0、什么是液态金属的充型能力
1)定义:
液体金属充满铸型型腔,获得尺寸精确、轮廓清晰的 成型件的能力,称为充型能力。
2)充型能力对成型的影响
充型能力不足时,会产生浇不足、冷隔、夹渣、气孔 等缺陷。
3)影响充型能力的因素
充型能力首先取决于金属本身的流动性(流动能力),同 时又受铸型性质、浇注条件和铸件结构等因素影响。
一、铸件的凝固方式
在铸件凝固过程中,其断面上一般存在三个区 域:固相区、凝固区和液相区。
1、分类
依据对铸件质量影响较大的凝固区的宽窄划分 铸件的凝固方式为如下三类:
(1)逐层凝固
纯金属和共晶成分的合金在凝固过程中不存在液、固并 存的凝固区,随着温度下降,固体层不断加厚,液体不 断减少,直达铸件中心,这种凝固方式称为逐层凝固。
机械应力
二、铸件的变形及其防止
1、变形的原因:
铸件内部残余内应力。 只有原来受拉伸部分产生压缩 变形、受压缩部分产生拉伸变 形,才能使铸件中的残余内应 力减小或消除。
平板铸件的变形
杆件的变形
床身铸件的变形
粱形铸件的弯曲变形
2、防止措施:
减小应力; 将铸件设计成对称结构,使其内应力互相平衡; 采用反变形法; 设置拉肋; 时效处理。
2、冷裂纹的特征
裂纹细小,呈连续直线状,裂缝内有金属光泽或轻 微氧化色。
3、防止措施
凡是能减少铸件内应力和降低合金脆性的因素 均能防止冷裂。 设置防裂肋亦可有效地防止铸件裂纹。
防裂肋
三、合金的吸气性
液态合金中吸入的气体,若在冷凝过程中不能溢 出,滞留在金属中,将在铸件内形成气孔。
一)气孔的危害
气孔破坏了金属的连续性,减少了其承载的有效 截面积,并在气孔附近引起应力集中,从而降低 了铸件的力学性能。 弥散性气孔还可促使显微缩松的形成,降低铸件 的气密性。
金属液态成形工艺概述

铸造产品称为: 铸件、铸锭、铸坯、铸带等
一、金属液态成形工艺特点
1. 适应性强
铸件重量:几克 ~ 几百吨 铸件壁厚:0.5 毫米 ~ 1 米 铸件长度:几毫米 ~ 十几米 铸件材质:铁碳合金(鋳铁、鋳钢)、铝合金、铜合金、
镁合金、锌合金、钛合金、复合材料等
速箱体(灰口铸铁)
精密铸造件(不锈钢)
水轮机铸件(铜合金)
箱体(铝合金)
叶轮(钛合金)
一、金属液态成形工艺特点
1. 适应性强
铸件重量:几克 ~ 几百吨 铸件壁厚:0.5 毫米 ~ 1 米 铸件长度:几毫米 ~ 十几米 铸件材质:铁碳合金(鋳铁、鋳钢)、铝合金、铜合金、
镁合金、锌合金、钛合金、复合材料等
铸造方法几乎不受零件大小、形状和结构复杂程度的限制。
轧辊
异型件
装饰件
工艺品
一、金属液态成形工艺特点
2. 尺寸精度高
铸件比锻件、焊接件的尺寸精度高,更接近于零件的尺 寸,可节约大量的金属材料和机械加工工时。
一、金属液态成形工艺特点
2. 尺寸精度高
铸件比锻件、焊接件的尺寸精度高,更接近于零件的尺 寸,可节约大量的金属材料和机械加工工时。
形成的先进铸造技术
精密、优质化
精密成形与加工 近无缺陷成形
数字、网络化
数字造型 虚拟制造
网络制造
精确铸造成形 金属熔体的纯净化、致密化
铸造工艺CAD,铸造模具CAD/CAM一体化 铸造过程宏观模拟及工艺优化 铸件组织微观模拟及性能预测 分散网络化铸造系统
高效、智能化
快速制造 自动化制造系统
智能制造
快速原形及快速制模 铸造过程自动检测与控制,铸造机器人的应用
金属的液态成形
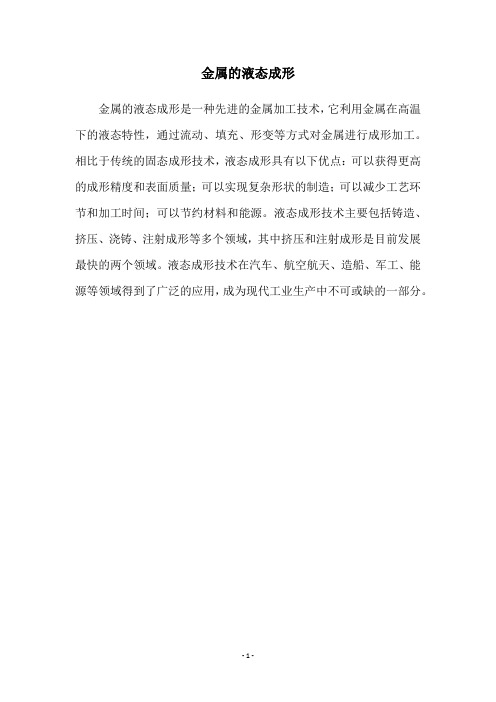
金属的液态成形
金属的液态成形是一种先进的金属加工技术,它利用金属在高温下的液态特性,通过流动、填充、形变等方式对金属进行成形加工。
相比于传统的固态成形技术,液态成形具有以下优点:可以获得更高的成形精度和表面质量;可以实现复杂形状的制造;可以减少工艺环节和加工时间;可以节约材料和能源。
液态成形技术主要包括铸造、挤压、浇铸、注射成形等多个领域,其中挤压和注射成形是目前发展最快的两个领域。
液态成形技术在汽车、航空航天、造船、军工、能源等领域得到了广泛的应用,成为现代工业生产中不可或缺的一部分。
- 1 -。
金属的液态成形
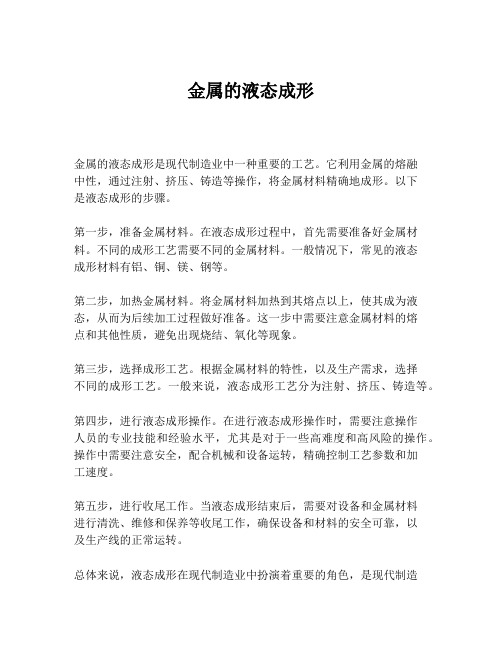
金属的液态成形
金属的液态成形是现代制造业中一种重要的工艺。
它利用金属的熔融
中性,通过注射、挤压、铸造等操作,将金属材料精确地成形。
以下
是液态成形的步骤。
第一步,准备金属材料。
在液态成形过程中,首先需要准备好金属材料。
不同的成形工艺需要不同的金属材料。
一般情况下,常见的液态
成形材料有铝、铜、镁、钢等。
第二步,加热金属材料。
将金属材料加热到其熔点以上,使其成为液态,从而为后续加工过程做好准备。
这一步中需要注意金属材料的熔
点和其他性质,避免出现烧结、氧化等现象。
第三步,选择成形工艺。
根据金属材料的特性,以及生产需求,选择
不同的成形工艺。
一般来说,液态成形工艺分为注射、挤压、铸造等。
第四步,进行液态成形操作。
在进行液态成形操作时,需要注意操作
人员的专业技能和经验水平,尤其是对于一些高难度和高风险的操作。
操作中需要注意安全,配合机械和设备运转,精确控制工艺参数和加
工速度。
第五步,进行收尾工作。
当液态成形结束后,需要对设备和金属材料
进行清洗、维修和保养等收尾工作,确保设备和材料的安全可靠,以
及生产线的正常运转。
总体来说,液态成形在现代制造业中扮演着重要的角色,是现代制造
业的重要组成部分。
液态成形工艺的精细化、自动化和智能化也正在不断提高,使其在新时代更加高效、安全、环保和持续发展。
金属液态成形工艺原理

H0
P杯
v杯2 2g
0
P腔
v内2 2g
hi (2 - 1)
1. 充填下半型 设充填下半型时需要金属液m1,充填时间为t1。 以浇口杯液面和内浇道出口建立伯努利方程(能量方程):
H0
P杯
v杯2 2g
0
P腔
v内2 2g
hi
式中:
P杯 —— 浇口杯液面压力 P腔 —— 型腔内的液面压力 v杯 —— 浇口杯液面金属流动速度 v内 —— 内浇口出口金属流动速度 hi —— 浇注系统中某段的流体压头损失
§2.2 液态金属充型过程的水力学计算
三、计算结果
计算条件: a. 浇注系统为充满流动
封闭式浇注系统; 对于开放式的型腔液面要淹过内浇道。
b. 浇口杯液面保持不变
c. 型腔内压力与外界相同,即砂型透气性要好,有排气孔
1. 充填下半型 设充填下半型时需要金属液m1,充填时间为t1。 以浇口杯液面和内浇道出口建立伯努利方程(能量方程):
γ —— 重度(=ρg)
2. 充填上半型 设充填上半型时需要金属液m2,充填时间为t2。 以浇口杯液面和内浇道出口建立伯努利方程:
H0
P杯
v杯2 2g
0
P内
v内2 2g
hi
3. 充填整个铸型
设充填时需要金属液m,充填时间为t,则
m
F内 t 2gH均
式中 m为充填铸型所需金属液; t为充填时间; 为流量系数; H均为充型平均静压头。
学的规律在一定程度上也适用于液态金属的流动过程。
§2.2 液态金属充型过程的水力学计算 一、浇注系统的结构
§2.2 液态金属充型过程的水力学计算
一、浇注系统的结构
浇注系统:引导金属液进入和充满型腔的一系列通道。
金属液态成形是将液态技术浇注到与零件的形状

1.金属液态成形是将液态金属浇注到与零件的形状,尺寸相适应的铸型型腔中,待其冷却凝固,以获得毛坯或零件的方法。
(砂型铸造和特种铸造两大类)2.铸件的凝固方式:逐层凝固、糊状凝固、中间凝固。
3.浇注条件:包括浇注温度、充型压力和浇注系统的结构。
4.合金收缩的三个阶段:1)液态收缩2)凝固收缩、3)固态收缩5.生产上防止热裂的措施:1)应尽量选择凝固温度范围小、热裂倾向小的合金。
2)应提高铸型和型芯的退让性,以减小机械应力。
3)浇注系统的设计要合理。
4)对于铸钢件和铸铁件,必须严格控制硫的含量,防止热脆性。
6.在铸造生产中,用应尽量选择共晶成分或凝固温度范围小的合金作为铸造合金。
7.影响铸件的凝固方式的主要因素是合金的结晶温度范围和铸件的温度梯度8.合金收缩率是衡量合金铸造性能优劣的主要指标之一9.体收缩率是铸件产生缩孔或缩松的根本原因;线收缩率是铸件产生应力、变形、裂纹的根本原因10.缩孔形成条件:合金在恒温或很窄的温度范围内结晶,铸件以逐层凝固的方式凝固11.防止缩孔工艺措施:就是控制铸件的凝固次序,使铸件实现顺序凝固12.液态成形内应力是铸件产生变形和裂纹的主要原因13.消除残余应力:进行应力退火,自然时效处理14.凡是减小铸件内应力或降低合金脆性的因素均能防止冷裂15.根据碳在铸铁中的存在形式分类:白口铸铁、麻口铸铁、灰铸铁。
16.根据铸铁中石墨形态分为:普通灰铸铁HT 可锻铸铁KT 球墨铸铁QT 蠕墨铸铁RuT17.铸钢分为铸造碳、铸造合金刚,其铸造性能差18.铸造工艺设计内容:铸件浇注位置和分型面的选择,工艺参数的确定,型心的数量,芯头形状及尺寸的确定,浇冒口系统、冷铁等形状、尺寸及在铸型中的布置等的确定19.塑性成形(压力加工):在外力作用下,使金属坯料产生塑性变形,获得具有一定形状、尺寸零件的成形方式。
其基本成形方式有轧制、挤压、冷拔、自由锻、模锻、板料冲压20.铸型分型面是指铸型间相互接触的表面单晶体的塑性变形主要通过滑移<位错>和孪生<转动>两种方式多晶体的塑性变形晶内分为滑移和孪生,晶间为晶粒的滑动和转动随着冷变形程度的增加,材料的力学性能也会随之发生改变金属强度硬度提高,塑性和韧性下降,称为冷变形强化,又称加工硬化,消除方式:回复再结晶金属的可锻性是指金属材料在压力加工时成形的难易程度,用(塑性),(变形抗力)两个指标衡量影响金属可锻性的因素包括金属的本质和变性条件金属塑性变形的基本定律:体积不变定律和质量守恒定律焊接是通过加热或加压或两者皆有,在使用或不使用填充材料的情况下,使两个分离金属表面的原子达到晶格距离,并形成金属键而获得不可拆接头的材料连接方法。
金属的液态成形

金属的液态成形
金属的液态成形是一种常见的金属加工方式,它利用高温使金属达到液态状态,然后通过模具的成形使其恢复原来的形状。
这种加工方式可以制造出各种各样的金属制品,如汽车发动机的零部件、航空飞行器的机身等。
液态成形的好处在于可以制造出更为精密的零部件,也可以减少材料的浪费,提高生产效率。
液态成形还可以应用于金属的再加工,如淬火、退火等,使其性能得到进一步的提升。
同时,液态成形也面临着一些挑战,如必须控制温度、压力等参数,否则可能会导致制品出现缺陷。
因此,液态成形需要高超的技术和精密的设备,才能确保制品的质量和性能。
- 1 -。
第七章 金属的液态成形

缩松:分散在铸件内部分散而细小的缩孔,大多分布在 铸件中心轴线处、冒口根部、内浇口附近或缩孔下方。形成 的原因与缩孔基本相同。 缩孔及缩松使铸件力学性能下降,防止其发生的主要 措施是“定向凝固”,通过增设冒口、冷铁等一些工艺措施 ,使凝固顺序形成向着冒口方向进行,如下图。远离冒口的 部位先凝固,冒口最后凝固,使缩松和缩孔产生在冒口处。 或在铸件厚大部位增设冷铁,以加快该处的凝固速度。
第七章 金属的液态成形
什么是金属的液态成形: 即将液态金属浇入与零件形状相适应的铸型空腔 中,待其冷却凝固,以获得毛坯或零件的工艺方法,亦 称铸造. 金属的液态成形的作用: 金属的液态成形是制造毛坯、零件的重要方法之一。 按铸型材料的不同,金属液态成形可分为砂型铸造和特 种铸造(包括压力铸造、金属型铸造等)。 其中砂型铸 造产品成本最低,应用最普遍,所生产的铸件要占铸件 总量的80%以上。但工艺过程较复杂不易控制,,铸件内 部常有缩孔、夹渣、气孔、裂纹等缺陷产生,导致铸件 力学性能,特别是冲击性能较低。
• (2) 浇注温度 • 浇注温度越高,液态合金的流动性越好,若过高,铸 件易产生缩松、粘沙等缺陷。一般浇注温度控制在:铸钢 1520~1620℃;铸铁1230~1450℃;铝合金680~780℃。 • (3)铸型填充条件 • 内浇道横截面小、型腔表面粗糙、型砂透气性差都会增加 液态合金的流动阻力;铸型材料的导热性过大,使液体金 属凝固快,同样会降低流动性。
f) 挖砂造型
活块造型是在制模时将铸件上的妨碍起模的小凸台,肋 条等这些部分作成活动的(即活块)。起模时,先起出 主体模样,然后再从侧面取出活块。其造型费时,工人 技术水平要求高。主要用于单件、小批生产带有突出部 分、难以起模的铸件。
活块造型
三箱造型的铸型由上、中、下三型构成。中型高度 需与铸件两个分型面的间距相适应。三箱造型操作 费工。主要适用于具有两个分型面的单件、小批生 产的铸件。
金属液态成形

材料成形技术基础第一章 金属液态成形金属液态成形(铸造):将液态金属在重力或外力作用下充填到型腔中,待其凝固冷却后,获得所需形状和尺寸的毛坯或零件的方法。
液态成形的优点:(1)适应性广,工艺灵活性大(材料、大小、形状几乎不受限制)(2)最适合形状复杂的箱体、机架、阀体、泵体、缸体等(3)成本较低(铸件与最终零件的形状相似、尺寸相近)主要问题:组织疏松、晶粒粗大,铸件内部常有缩孔、缩松、气孔等缺陷产生,导致铸件力学性能,特别是冲击性能较低。
分类:铸造从造型方法来分,可分为砂型铸造和特种铸造两大类。
其中砂型铸造工艺如图1-1所示。
图1-1 砂型铸造工艺流程图第一节金属液态成形工艺基础一、熔融合金的流动性及充型液态合金充满型腔是获得形状完整、轮廓清晰合格铸件的保证,铸件的很多缺陷都是在此阶段形成的。
(一)熔融合金的流动性1.流动性 液态合金充满型腔,形成轮廓清晰、形状和尺寸符合要求的优质铸件的能力,称为液态合金的流动性。
流动性差:铸件易产生浇不到、冷隔、气孔和夹杂等缺陷。
流动性好:易于充满型腔,有利于气体和非金属夹杂物上浮和对铸件进行补缩。
螺旋形流动性试样衡量合金流动性,如图1-2所示。
在常用铸造合金中,灰铸铁、硅黄铜的流动性最好,铸钢的流动性最差。
常用合金的流动性数值见表1-1。
表1-1 常用合金的流动性(砂型,试样截面8㎜×8㎜)2. 影响合金流动性的因素(1) 化学成份 纯金属和共晶成分的合金,由于是在恒温下进行结晶,液态合金从表层逐渐向中心凝固,固液界面比较光滑,对液态合金的流动阻力较小,同时,共晶成分合金的凝固温度最低,可获得较大的过热度,推迟了合金的凝固,故流动性最好;其它成分的合金是在一定温度范围内结晶的,由于初生树枝状晶体与液体金属两相共存,粗糙的固液界面使合金的流动阻力加大,合金的流动性大大下降,合金的结晶温度区间越宽,流动性越差。
Fe-C合金的流动性与含碳量之间的关系如图1-3所示。
第一章金属液态成形

第一章金属液态成形1-1什么是液态合金的充型能力?它与合金的流动性有何关系?不同化学成分的合金为何流动性不同?为什么铸钢的充型能力比铸铁差?1-2 既然提高浇注温度可提高液态合金的充型能力,但为什么又要防止浇注温度过高?1-3 缩孔与缩松对铸件质量有何影响?为何缩孔比缩松较容易防止?1-4 区分以下名词:缩孔和缩松浇不足与冷隔出气口与冒口逐层凝固与定向凝固1-5 什么是定向凝固原则?什么是同时凝固原则?上述两种凝固原则各适用于哪种场合?1-6 分析图1-73所示轨道铸件热应力的分布,并用虚线表示出铸件的变形方向。
图1-73 题1-6图1-7 分析下列情况产生气孔的可能性。
化铝时铝料油污过多起模时刷水过多椿砂过紧型芯撑有锈1-8 手工造型、机器造型各有哪些优缺点?适用条件是什么?1-9 分模造型、挖砂造型、活块造型、三箱造型各适用于哪种情况?1-10 什么是铸件的结构斜度?它与起模斜度有何不同?图1-74所示铸件的结构是否合理,应如何改正?图1-74 题1-10图1-11 何谓铸造工艺图?用途是什么?1-12 图1-75所示铸件的结构有何缺点?该如何改进?图1-75 题1-12图1-13 为什么铸件要有结构圆角?图1-76铸件上哪些圆角不够合理,应如何修改?图1-76 题1-13图1-14某厂铸造一个φ1000㎜的铸铁件,有如图1-77所示两个设计方案,分析哪个方案的结构工艺性好,简述理由。
图1-77 题1-14图1-15某厂生产如图1-78所示支腿铸铁件,其受力方向如图中箭头所示。
用户反映该铸件不仅机械加工困难,且在使用中曾发生多次断腿事故。
试分析原因,并重新设计腿部结构。
1-17下列铸件宜选用哪类铸造合金?说明理由。
坦克车履带板压气机曲轴火车轮车床床身摩托车发动机缸体减速器蜗轮汽缸套1-18 什么是熔模铸造?试述其工艺过程?1-19 金属型铸造有何优越性?为什么金属型铸造未能广泛取代砂型铸造?1-20 为什么用金属型生产铸铁件时常出现白口组织?该如何预防和消除已经产生的白口?1-21 低压铸造的工作原理与压铸有何不同?为什么低压铸造发展较为迅速?为何铝合金较常采用低压铸造?1-22 什么是离心铸造?它在圆筒件铸造中有哪些优越性?1-23 普通压铸件是否能够进行热处理,为什么?1-24 影响铸铁石墨化的主要因素是什么?为什么铸铁牌号不用化学成分来表示?1-25 灰铸铁最适于制造哪类铸件?试举车床上几种铸铁件名称,并说明选用灰铸铁而不采用铸钢的原因。
液态金属成型

gx −
1 ∂P +ν ρ ∂x
∂ 2u ∂ 2u ∂ 2u ∂ u ∂u ∂u ∂u ∂ x2 + ∂ y2 + ∂ z2 = ∂t + u ∂x + v ∂y + w∂z
∂ 2v ∂ 2v ∂ 2v ∂ v 1 ∂P ∂v ∂v ∂v gy − +ν + + 2 = + u + v + w 2 2 ρ ∂y ∂x ∂y ∂z ∂y ∂z ∂t ∂x gz − 1 ∂P +ν ρ ∂z ∂ 2w ∂ 2w ∂ 2w ∂ w ∂w ∂w ∂w ∂ x2 + ∂ y2 + ∂ z2 = ∂t + u ∂x + v ∂y + w ∂z
五、实验报告 分析总结铝合金的熔炼处理工艺流程,比较精炼处理、 变质处理、 振动以及冷却条件对 铝合金组织及性能的影响。
实验二、液态成型过程 CAE 实验 一、基础理论 计算机辅助工程( Computer Aided Engineering,简称 CAE)技术是一门以 CAD/CAM 技术水平的提高为发展动力,以高性能计算机及图形显示设备的推出为发展条件,以计算 力学和传热学、 流体力学等的有限元、 有限差分、 边界元、 结构优化设计及模态分析等方法为 理论基础的新技术。目前液态成型 CAE 主要以铸件的温度场模拟和流动场模拟为主,软件 水平已经达到实用化,国内外均有商品化软件出现。国外主要有德国的 MagmaSoft、美国的 ProCAST、 Flow3D、 韩国的 AnyCAST 等,国内主要有华中科技大学的华铸 CAE、 清华的 FTStar、华北工学院的 CastSoft 等。 1)温度场模拟 温度场模拟主要是利用传热学原理,分析铸件的传热过程,模拟铸件的冷却凝固进程 ,
液态金属成型

液态金属成型金属液态成型论文作者:刘永星摘要:金属液态成型又称为铸造,是将液态金属在重力或外力作用下充填到型腔中,待其冷却凝固后,获得所需形状和尺寸的毛坯或零件,即铸件的方法,它是成形毛坯或机器零件的重要方法之一。
工程材料除切削加工以外有各种成型方法,包括金属液态成型、金属塑性成形、材料连接成型、粉末冶金成型以及塑料、橡胶、陶瓷等非金属材料成型及复合材料成型等。
材料成型技术主要讲述金属材料成型和非金属材料成型,现对金属液态成型进行详细论述。
关键词:金属液态成型、成型方法、生产流程、成型原理、选择成型依据一、金属液态成形金属材料在液态下成形,具有很多优点:(1)最适合铸造形状复杂、特别是复杂内腔的铸件。
(2)适应性广,工艺灵活性大。
(3)成本较低。
但液态成形也有很多不足,如铸态组织疏松、晶粒粗大,铸件内部常有缩孔、缩松、气孔等缺陷产生,导致铸件力学性能、特别是冲击性能低于塑形成行件;铸件涉及的工序很多,不易精确控制,铸件质量不稳定;由于目前仍以砂型铸造为主,自动化程度还不够高,工作环境较差;大多数铸件只是毛坯件,需经过切削加工才能成为零件。
砂型铸造是将熔融金属浇入砂质铸型中,待凝固冷却后,将铸型破坏,取出铸件的铸造方法,是应用最为广泛的传统铸造方法,它适用于各种形状、大小及各种常用合金铸件的生产。
砂型铸造的工艺过程称为造型。
造型是砂型铸造最基本的工序,通常分为手工造型和机器造型两大类。
手工造型时,填砂、紧实和起模都用手工和手动完成。
其优点是操作灵活、适应性强、工艺装备简单、生产准备时间短。
但生产效率低、劳动强度大、铸件质量不易保证。
故手工造型只适用于单件、小批量生产。
机器造型生产率很高,是手工造型的数十倍,制造出的铸件尺寸精度高、表面粗糙度小、加工余量小,同时工人劳动条件大为改善。
但机器造型需要造型机、模板以及特质砂箱等专用机器设备,一次性投资大,生产准备时间长,故适用于成批大量生产,且以中、小型铸件为主。
第一章金属的液态成形-概述介绍

落砂清理等。 铸件的材质有铸铁、铸造碳钢、铸造合金钢、铸造有色合金
等。 优点: 1)可以生产出形状复杂,特别是具有复杂内腔的零件毛坯,如 各种箱体、床身、机架等。 2)铸造生产的适用性广,工艺灵活性大。工业上常用的金属材 料均可用来进行铸造,铸件的重量可由几克到几百吨,壁厚可 由0.5mm到1m左右。 3)铸造用原材料大都来源广泛,价格低廉,并可直接利用废机 件,故铸件成本较低。
铸造在机器制造业中应用极其广泛。农业机械:40~70% 、 机床:70~80%重量为铸件。
启 动 阀 箱体
缺点: 铸件内部组织粗大,常有缩松、气孔等铸造缺陷,导致
铸件力学性能不如锻件高。铸造工序多,而且一些工艺过程 还难以精确控制,使得铸件质量不够稳定,废品率高。
人有了知识,就会具备各种分析能力, 明辨是非的能力。 所以我们要勤恳读书,广泛阅读, 古人说“书中自有黄金屋。 ”通过阅读科技书籍,我们能丰富知识, 培养逻辑思维能力; 通过阅读文学作品,我们能提高文学鉴赏水平, 培养文学情趣; 通过阅读报刊,我们能增长见识,扩大自己的知识面。 有许多书籍还能培养我们的道德情操, 给我们巨大的精神力量, 鼓舞我们前进。
材料成形技术
第一章 金属液态成形技术(铸造)
第1章 金属的液态成形技术
液态成形(铸造): 将熔融金属浇入铸型型腔,凝固 后获得一定形状、尺寸和性能零件或毛坯的成形方法.
也就是,将经过熔化的液态金属浇注到与零件 形状、尺寸相适应的铸型中,冷却凝固后获得毛坯 或零件的一种工艺方法。
砂型铸造及铸件的浇注过程
第四章 金属的液态成形与半固态成形 第一节 液态成形

第四章金属的液态成形与半固态成形第一节液态成形一.特点1.把金属变为变形阻力小的液态金属,浇入铸型后,一次制作出所需形状的铸件。
故适应性强,工艺灵活性大,几乎所有的工程材料都可以用液态成形。
2.成形件精度高。
3.成本低廉。
4.零件力学性能差,常存有缺陷,组织疏松、晶粒粗大、质量不稳定,生产过程劳动强度大、条件差、生产率低。
二.发展史三.液态成形合金性能液态成形过程合金要发生一系列物理、化学变化,并对铸件的质量性能产生极大影响,故液态成形合金必须具有合适的性能要求。
(一)合金的充型性能作为最基本要求,液态金属要能充满铸型型腔,获得形状完整,轮廓清晰的健全铸件,并防止铸件产生浇不足,冷隔等缺陷。
影响合金充型能力的因素有:1、合金的流动性:作为合金本身性能,它与合金成分、温度、杂质含量及物理性能有关;2、浇注条件:其中包括浇注温度、充型压力与浇注系统的结构。
决定性影响的因素是温度。
在一定范围内,随着温度提高,合金的粘度减少,充型能力提高。
但超过某界限后,合金液氧化、吸气严重,易产生缩松、气孔等缺陷。
提高充型压力(增大静压头高度,压铸)可提高充型能力。
浇铸系统结构较复杂(如蛇形浇道),流动阻力增加,相同静压条件下,充型能力小。
3、铸型性质及结构铸型从合金中吸收及储存热性能的能力称蓄热能力。
材料的导热率、比热越大,它也越大。
大的蓄热能力使合金的充型能力变差,预热铸型,降低合金液与铸型温差,减缓合金液冷却速度,能提高合金的充型能力。
加强铸型结构的排气,能减少铸型的发气,提高充型效果。
铸型结构不合理,如壁厚太小,急剧变化,过大的水平面等结构能产生较大流动阻力,充型能力大大受影响。
(二)合金的收缩,铸件缩孔、缩松特征1、液态合金在冷却凝固过程中,体积、尺寸均缩小的现象称为收缩,是产生缩孔(松)、变形、裂缝的原因。
有体收缩和线收缩两种,发生在液态收缩和凝固收缩的体收缩是缩孔、缩松形成的主要原因。
固态收缩表现为铸件外形尺寸的线收缩,是产生铸造应力、变形、裂缝的主要原因。
第一节 金属的液态成形原理

决定凝固方式的因素: (1)结晶温度范围 (2)铸件断面温度场分布变化
二 液态合金的充型能力
充型: 液态合金填充铸型的过程. 充型能力 : 液态合金充满铸型型腔 , 获得形状完整 , 轮廓清晰的铸件的能力
若充型能力不足,易产生:
1)浇不足: 不能得到完整隙或凹坑 , 机械性能下 降.
2) 共晶成分流动性好:恒温凝固,固体层表面光滑,且熔点 低,过热度大;
3) 非共晶成分流动性差: 结晶在一定温度范围内进行,初 生树枝状晶阻碍液流 。 常用铸造合金中,铸铁的流动性最好,铸钢的流动性最差。
逐层凝固(好)
糊状凝固(差)
不同成分合金流动性
(过热度)
碳钢
铸铁
碳钢随着结晶温 度范围的增加而 流动性变差;亚 共晶铸铁随含碳 量的增加流动性 提高。
纵向温度分布曲线
冷铁
同时凝固— 整个铸件几乎同时凝固。
同时凝固特点:不需冒口,节约金属且工艺简单;铸件均 匀冷却,减小热应力,不易形成内应力、变形和裂纹等缺 陷,但心部缩松有时难以避免,故用于收缩小的合金和各 种合金的薄壁铸件。如灰铸铁,锡青铜,铝硅合金等。 (1)这是由于薄壁铸件的铸型冷却作用强,薄壁断面温 度梯度大,倾向于逐层凝固。因此收缩小的灰铸铁可消除 缩孔,获得致密铸件;而收缩较大的薄壁铸钢、有色合金 铸件会出现轴线缩松,但其表层组织致密。
温度
固
液
表层
中心
铸件的凝固方式
2)糊状凝固
• 结晶温度范围很宽 的合金,从铸件的 表面至心部都是固 液两相混存。 • 铸件断面上布满小 晶体,将金属液分 割开,致充型和补 缩能力变差。
温度
固
液
表层
中心
铸件的凝固方式
铸造工艺基础知识及理论

4
铸造材料
1
工艺基础 工艺性能
2
铸件生产
铸造工艺
3 工艺方法
1. 金属液态成形(铸造)工艺基础
什么是金属的液态成形:
将熔炼好的液态金属浇入与零件形 状相适应的铸型空腔中,待其冷却凝固, 以获得毛坯或零件的工艺方法,亦称铸造.
金属的液态成形的方法:
金属的液态成形是制造毛坯、零件的重要方法之一。按铸型材 料的不同,金属液态成形可分为砂型铸造和特种铸造(包括压力铸 造、金属型铸造等).其中砂型铸造是最基本的液态成形方法,所生 产的铸件要占铸件总量的80%以上.特种铸造较适用于大批量生产, 应用范围逐渐增加。
松
的 方
方法
合理布置内浇道及确定浇铸工艺。
法
合理应用冒口、冷铁和补贴等工艺措施。
3. 铸件的生产工艺
整模造型
分模造型
手工造型
砂型铸造
活块造型 三箱造型
液
挖砂造型
态
机器造型
刮板造型
成
铸造工艺图的绘制
型
砂型铸造的工艺设计
分型面的选择
工
工艺参数的确定 浇注位置的确定
艺
金属型铸造
熔模铸造
压力铸造
特种铸造
低压铸造 陶瓷型铸造
内是由表及里的逐层凝固。在凝固过程中,如得不到合金液的 补充,在铸件最后凝固的地方就会产生缩孔.
2. 铸件的生产—缩松的形成 缩松的形成原因:
铸件最后凝固的收缩未能得到补充,或者结晶温度范围宽的 合金呈糊状凝固,凝固区域较宽,液、固两相共存,树枝晶发 达,枝晶骨架将合金液分割开的小液体区难以得到补缩所致。
合金的收缩的过程:
合金从液态冷却至室温的过程中,其体积或尺寸缩减的 现象。合金的收缩给液态成形工艺带来许多困难,会造成许 多铸造缺陷。(如:缩孔、缩松、裂纹、变形等)。
- 1、下载文档前请自行甄别文档内容的完整性,平台不提供额外的编辑、内容补充、找答案等附加服务。
- 2、"仅部分预览"的文档,不可在线预览部分如存在完整性等问题,可反馈申请退款(可完整预览的文档不适用该条件!)。
- 3、如文档侵犯您的权益,请联系客服反馈,我们会尽快为您处理(人工客服工作时间:9:00-18:30)。
2018年4月2日11:22
1.什么是金属液态成形?
金属液态成形也就是铸造,是将液态金属在重力或者其它外力作用下充填到型腔,待其凝固冷却后获得所需形状和尺寸的毛皮或零件(铸件)的工艺过程;
2.流动性
熔融合金的流动性是指其自身的流动能力。
流动性好则充填铸型能力强,尺寸易精确,外形完整,轮廓清晰;流动性不好会出现浇不足、冷隔、气孔、夹杂等缺陷;薄壁铸件对之尤其敏感。
灰铸铁、硅黄铜最好,铝硅合金次好,铸钢最差;
3.充型能力
充型能力是指熔融合金充满型腔获得轮廓清晰、形状完整的铸件的能力,与流动性、浇注条件、铸型条件等有关;
4.纯金属和共晶合金为逐层凝固,流动性好,其它成分金属随着结晶范围加大流动性变差;
5.提高浇注温度获得较大过热度有利流动充型,但不宜过高;增大充型压力、提高浇注速度有利流动充型;预热铸型、减少发气、改善透气、简化结构等等有利于充型;
6.收缩
合金收缩分为液态收缩,凝固收缩,固态收缩。
前二者合称体收缩,后者为线收缩;收缩率与金属性质有关。
浇注温度高,过余温度大,液态收缩加剧;结构复杂、铸型、型芯硬度高的逐渐收缩阻力大;实际线收缩比自由线收缩率小一些;
7.缩孔
在凝固收缩的过程中,液态收缩、凝固收缩、固态收缩造成体积不断减小,凝固收缩不能得到液态金属的有效补缩,最后凝固部分处出现倒锥形缩孔;纯金属与共晶合金逐层凝固易形成缩孔,按温度梯度顺序凝固的最后部分易缩孔,过余温度大液态收缩、凝固收缩大易形成缩孔;
8.缩松
结晶范围宽的金属以糊状凝固方式进行,一般聚集于中心轴线处、热节
处、冒口根部或缩孔下方;温差小的同时凝固条件容易形成缩松;
9.缩孔和缩松一般产生于凝固缓慢的厚壁热节处
10.缩孔和缩松的防止
采用加冷铁和补缩冒口的方式,形成一定的温度梯度,使铸件“定向凝固”,将缩松尽可能转化为缩孔并使缩孔转移到冒口中;
11.铸造内应力
铸造内应力分为热应力和机械应力,铸造内应力产生的原因是凝固之后的固态收缩过程中收缩收到阻碍。
铸造应力会造成铸件铸件变形;
12.铸造热应力
由于铸件壁厚不均匀、冷却速度不同,铸件各部分收缩不一致,因此产生热应力;一般情况下,薄壁处率先冷却受压,厚壁处后冷却受拉;
13.机械应力
固态收缩时,线收缩受到铸型或者型芯的阻碍,形成拉伸或者剪切应力,机械应力在落砂后可自行消除。
14.减小或消除应力的措施
采取同时凝固的方式,避免凝固顺序的不一致性,减小热应力,但是这会产生缩松,应该有所权衡;改善铸型和型芯的退让性,减小机械应力;加热到550至600摄氏度实施去应力退火,可以基本消除参与内应力;
15.铸件变形的防止
减小铸造内应力或者用对称结构让内应力抵消可以防止变形;利用反变形法,在变形方向上预先设计形状补偿变形;设置防变形肋板;在切削加工前实施去应力退火,消除内应力;
16.热裂纹及其减小
铸件在凝固末期已经具有完整的固态骨架,由于铸型和型芯的阻挡,会造成机械应力,一旦机械应力超过高温下的强度极限,那么就会导致热裂纹的产生;热裂纹短而宽,形状曲折,缝内有氧化色;结晶范围大的合金容易产生热裂纹。
应该尽量使用热裂倾向小的合金,改善铸件结构,改善铸型和型芯的退让性;
17.冷裂纹及其减小
在较低温度下,铸造内应力超过材料强度极限就会产生冷裂纹;冷裂纹细小连续呈光滑直线状,多出现于受拉应力部位;脆性大、塑性差的材料容易产生冷裂纹;因此可以用减小脆性的方法减小冷裂纹,比如减小磷的含
量;
18.常见的铸造缺陷有浇不足(形状不完整)、冷隔(完整但有未融合裂缝)、缩孔、缩松、夹砂、变形、裂纹、粘砂、胀砂等等;
18.砂型铸造的造型分为手工造型和机器造型。
手工造型分为田沙、紧实、起模。
手工造型的具体方法有两箱造型、三箱造型、地坑造型、脱箱造型(合型后取出砂箱只留下砂型,浇注时可加套箱固定。
);整模造型、挖砂造型、假箱造型、分模造型、活块造型、刮板造型等等;
19.机器造型中的震压造型的过程是装砂、震击、压实和起模,起模方法有顶箱、漏模和翻转,其特点是采用模板造型和两箱造型;
20.造芯时其内部有通气道,中间有芯骨,一般烘干使用;
21.砂型的铸造工艺设计
1)浇注位置选择
重要加工面应该位于下面或者侧面;宽大平面应该朝向下方;大面积薄壁应该处于铸型下部,处于垂直或者倾斜位置;易产生缩孔的铸件的粗大部分应该处于上部或者侧面,便于与冒口配合;尽量减少型芯数量便于安放固定和排气;
2)分型面的选择
便于起模,最好在最大截面处、尽量平直、数量尽量少尽量避免活块和使用型芯;尽量是重要加工面和加工基准面处于同一砂箱内保证精度;尽量使型腔和主要型芯位于下型;
22.铸件工艺参数的确定
铸件的工艺参数包括机加工余量(手册)和最小铸出孔(表,一般30-50左右),起模斜度(一般15分到3度)、收缩率(铸铁1%)、型芯头(分为水平型芯头和垂直型芯头);
23.铸造工艺图
铸造工艺图应该包括浇注位置、分型面、加工余量、起模斜度、收缩率、浇冒系统、冷铁布置、型芯等;
24.铸件结构工艺性
1)外形力求简单
避免铸件外形侧凹,减少分型面;尽可能使分型面平直;加强肋与凸台的设计应该不妨碍起模;铸件侧壁应该有起模斜度;
2)内腔简单
尽量少或不用型芯;使用型芯应该便于型芯的固定、定位、排气和清理;3)铸件壁厚适度
壁厚要大于最小铸造壁厚(查表);壁厚也不应该过厚,防止晶粒粗大和缩孔缩松;壁厚应该力求均匀;利于实现定向凝固;
4)壁间连接
转弯处应为圆角;不同壁厚厚度要逐步过渡;连接要避免交叉和锐角;轮辐避免收缩受阻,可取奇数艮或者采用弯曲轮辐;
5)避免过大水平面,有的要改成斜面锥面等等
6)可采用加强肋和对称式的结构起到加强作用
25.特种铸造
1)熔模铸造
熔模铸造又称失蜡法,或者熔模精密铸造,具有较高的尺寸精度和表面质量;
熔模铸造的一般步骤是制造蜡模、制造型壳(石英粉、水玻璃、氯化铵溶液)、热水中脱蜡、焙烧型壳、浇注、脱壳清理;
熔模铸造适用于生产叶轮叶片、切削刀具、飞机汽车等上的小型零件;2)金属型铸造
金属型铸造是在重力作用下将液态金属浇注进金属铸型中获得铸件的方法;
金属型分为水平分型、垂直分型和复合分型三种结构;
金属型的工艺过程应该注意铸型排气、铸型涂料、铸型预热和开型时间;其优点是尺寸精度高、表面粗糙度小、冷却快因此晶粒小,一型多铸效率高;
其缺点是透气性差、退让性差、铸造形状简单;
3)压力铸造
压力铸造是将熔融合金在高压条件下高速充型,并在压力下凝固成形的精密铸造工艺;
根据坩埚与压室是否连在一起,压铸机分为冷压室压铸机和热压室压铸机,进而分为立式和卧式压铸机;
其优点是精度高、表面质量好、金属充型能力好、晶粒细小强度硬度高、可压铸形状复杂零件;
其缺点是容易产生缩松,尺寸受限,设备成本比较高;
4)低压铸造
低压铸造是指液态金属在较低压力作用下由下而上充填型腔,并在压力下凝固成铸件的方法;
5)离心铸造
离心铸造是将熔融金属浇入旋转的铸型中,在离心力的作用下充填铸型并凝固成形的一种方法;
6)此外还有挤压铸造(液态模锻)、实型铸造等等。