仿真车模型玩具PFMEA风险分析范例
pfmea过程潜在失效模式及后果分析案例(从原材料-加工-出货整套案例分析)

1、注射压力大 2、锁模力不够 3.模具分型面有异物
4 调节注射压力 作业准备验证,适当调
整,并进行工艺监控 清理模具分型面
产品不合格
2
C 4.塑料温度太高
调节 56
5
制品质量符合 要求
气泡
1.原料含水分、溶剂或 易挥发物
3
原料检验
2.塑料温度太高或受热 时间长,易降聚或分解
标签贴错 漏检 纸箱受潮变形 数量不准确
产品型号错
误,顾客不满 2
意
不良品混入, 影响客户使用
5
纸箱变形破损 3
顾客不满意
1
C 包装人员粗心 C 检验人员操作失误 C 纸箱堆积太高 C 仓库计数错误
3 检查、更正 3 检验、及时标记 3 检查、更正 3 检查、更正
2 42
1 21
3 18 4 60 3 27 26
3.注射压力太小
调节注射压力
4.注射柱塞退回太早 产品不合格 7 A
5.模具温度太低
调节注射温度
6.注射速度快
调节注射速度
2 42
7.在料筒加料端混入空 气
6
制品质量符合 要求
凹痕、缩水
产品不合格 7
1、流道浇口太小
4
2、塑料件太厚或厚薄 不均
3、浇口位置不当
4、注射保压时间太短 A 5、加料量不夠
过程潜在失效模式及后果分析 (PFMEA)
类型/部件: 车型年:
核心小组:
设计责任: 关键日期:
RPN DETECT
OCCUR CLASS SEV
项目
设计功能/要 求
潜在失效模式
潜在失效后果
1 原材料采购 原材料不合格
PFMEA潜在失效模式及后果影响分析案例
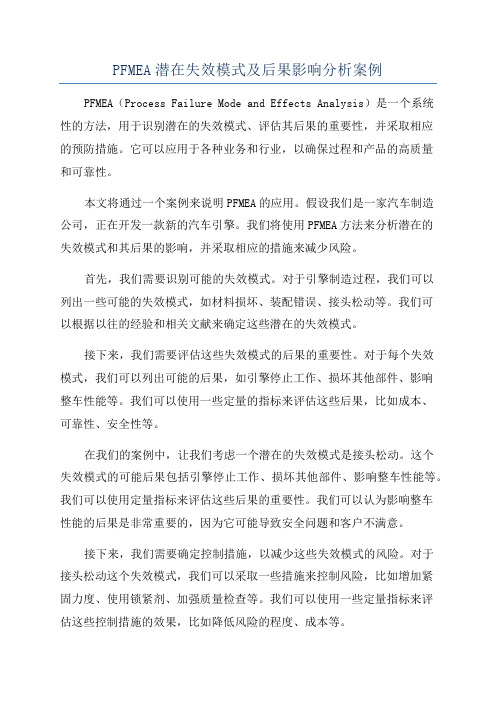
PFMEA潜在失效模式及后果影响分析案例PFMEA(Process Failure Mode and Effects Analysis)是一个系统性的方法,用于识别潜在的失效模式、评估其后果的重要性,并采取相应的预防措施。
它可以应用于各种业务和行业,以确保过程和产品的高质量和可靠性。
本文将通过一个案例来说明PFMEA的应用。
假设我们是一家汽车制造公司,正在开发一款新的汽车引擎。
我们将使用PFMEA方法来分析潜在的失效模式和其后果的影响,并采取相应的措施来减少风险。
首先,我们需要识别可能的失效模式。
对于引擎制造过程,我们可以列出一些可能的失效模式,如材料损坏、装配错误、接头松动等。
我们可以根据以往的经验和相关文献来确定这些潜在的失效模式。
接下来,我们需要评估这些失效模式的后果的重要性。
对于每个失效模式,我们可以列出可能的后果,如引擎停止工作、损坏其他部件、影响整车性能等。
我们可以使用一些定量的指标来评估这些后果,比如成本、可靠性、安全性等。
在我们的案例中,让我们考虑一个潜在的失效模式是接头松动。
这个失效模式的可能后果包括引擎停止工作、损坏其他部件、影响整车性能等。
我们可以使用定量指标来评估这些后果的重要性。
我们可以认为影响整车性能的后果是非常重要的,因为它可能导致安全问题和客户不满意。
接下来,我们需要确定控制措施,以减少这些失效模式的风险。
对于接头松动这个失效模式,我们可以采取一些措施来控制风险,比如增加紧固力度、使用锁紧剂、加强质量检查等。
我们可以使用一些定量指标来评估这些控制措施的效果,比如降低风险的程度、成本等。
最后,我们需要跟踪和更新PFMEA。
一旦我们实施了控制措施,我们需要不断跟踪失效模式的发生情况和其后果的重要性。
如果我们发现控制措施不够有效,我们可以采取进一步的改进措施,以减少风险。
通过以上的分析,我们可以有效地识别潜在的失效模式和其后果的重要性,并采取相应的预防措施来减少风险。
PFMEA是一个强大的工具,可以帮助我们提高产品和过程的质量和可靠性,从而提高客户满意度并降低成本。
玩具产品过程风险评估PFMEA(带内容)
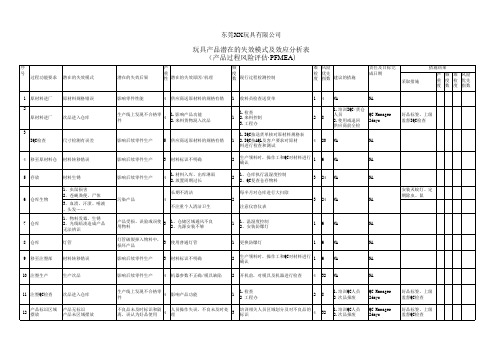
9 移至注塑部 材料转移错误
10 注塑生产
生产次品
东莞XX玩具有限公司
潜在的失效后果
玩具产品潜在的失效模式及效应分析表 (产品过程风险评估·PFMEA)
严
重 性 潜在的失效原因/机理
频
度 数 现行过程检测控制
难 风险
检 优先 度 指数 建议的措施
责任及目标完 成日期
采取措施
措施结果
严 频 难 风险 重 度 检 优先 度 数 度 指数
4 32
15 注塑部生物 16 注塑部环境
1、虫鼠损害 2、苍蝇粪便、尸体
3、血渍、汗渍、唾液 、头发……
1、物料发霉、生锈 2、光线暗淡造成产品 无法辨识
17
移至喷油部/移 印部
胶件转移错误
1.用错油漆 18 胶件喷油/移印 2.喷错颜色
3.喷油次品
19
喷油/移印QC检 查
次品进入仓库
污染产品
长期不清洁 4
、头发……
22
喷油/移印部环 境
1、物料发霉、生锈 2、光线暗淡造成产品 无法辨识
23 移至装配部 胶件转移错误
污染产品
长期不清洁 4
不注重个人清洁卫生
产品受损、误验或误使 用物料
3
1、车间通风不良 2、光源安装不够
影响后续零件生产 3 胶件标识不明确
每半月对车间进行大扫除 2
注意仪容仪表
3 24
1
组装次品/功能不良
污染产品
长期不清洁 4
不注重个人清洁卫生
产品受损、误验或误使 用物料
3
1、车间通风不良 2、光源安装不够
影响后续零件生产 3 人员操作失误
每半月对生产拉及工厂进行清洁 2
PFMEA(汽车产品塑胶件分析案例)
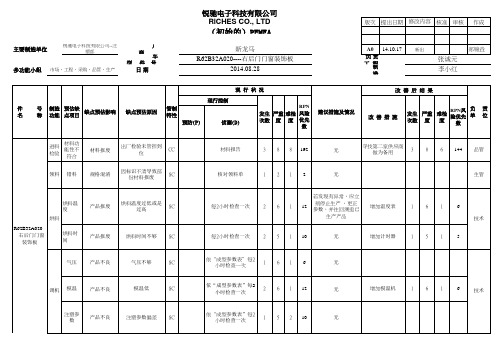
材料报废
出厂检验未管控到 位
CC
领料 错料
规格混淆
因标识不清导致部 份材料报废
SC
材料报告
3 8 8 192
核对领料单
1 21 2
无
寻找第二家供应商 做为备用
3
8
6 144
品管
无
生管
烘料温 度
烘料
R62B32A020---右后门门窗
装饰板
烘料时 间
产品报废
烘料温度过低或是 过高
SC
产品报废
烘料时间不够 SC
主要制造单位
锐驰电子科技有限公司--注 塑部
多功能小组 市场、工程、采购、品管、生产
厂 商车 型 件号 日期
锐驰电子科技有限公司 RiCHES CO., LTD
(初始的)PFMEA
新龙马 R62B32A020----右后门门窗装饰板
2014.08.28
版次 提出日期 修改内容 核准 审核 作成
A0 14.10.17 新出
发生
严重
难检
RPN风 险优先
负 单
责 位
次数 度 度 数
尺寸
报废
1.注塑工艺参数 (模温、压力、射 速)调试不当。
3
8
2
48
由专门人员进行调 试,必要时进行培训 。
由专职技术员调试 并记录到成型参数 表,首未件对比测
量
2
8
1
16
2.读数错误
SC
首未件检 测
依“成型参数表” 每2小时检查一次
2 8 5 80
3 7 4 84 由专门人员负责保养 第一个岗位人员需 2
7
3
42
要对每个产品外观
PFMEA过程失效模式及后果分析报告

科技股份某某作业文件文件编号:XXXX-XXXX.XX 版号:A/0(PFMEA)过程失效模式及后果分析作业指导书批准:审核:编制:受控状态:分发号:2016年01月15日发布2016年01月15日实施过程潜在失效模式及后果分析作业指导书(PFMEA)XXXX-XXXX.XX1目的过程潜在失效模式及后果分析,简称PFMEA。
是一种信赖度分析的工具,可以描述为一组系统化的活动,是对确定产品/过程必须做哪些事情才能使顾客满意这一过程的补充。
其目的是:(a)并评价产品/过程中的潜在失效以及该失效的后果;(b)确定能够消除或减少潜在失效发生机会的措施;(c)将全部过程形成文件。
2 X围:适用于公司用于零组件的所有新产品/过程的样品试制和批量生产。
适用于过程设计的风险性及后果的分析;适用于过程重复,周期性永不间断的改进分析。
3 术语和定义:1)PFMEA:指Process Failure Mode and Effects Analysis(过程失效模式及后果分析)的英文简称。
由负责制造/装配的工程师/小组主要采用的一种分析技术,用以最大限度地保证各种潜在的失效模式及其相关的起因/机理已得到充分的考虑和论述。
2)失效:在规定条件下(环境、操作、时间),不能完成既定功能或产品参数值和不能维持在规定的上下限之间,以及在工作X围内导致零组件的破裂卡死等损坏现象。
3)严重度(S):指一给定失效模式最严重的影响后果的级别,是单一的PFMEAX围内的相对定级结果。
严重度数值的降低只有通过设计更改或重新设计才能够实现。
4)频度(O):指某一特定的起因/机理发生的可能发生,描述出现的可能性的级别数具有相对意义,但不是绝对的。
5)探测度(D):指在零部件离开制造工序或装配之前,利用第二种现行过程控制方法找出失效起因/机理过程缺陷或后序发生的失效模式的可能性的评价指标;或者用第三种过程控制方法找出后序发生的失效模式的可能性的评价指标。
PFMEA分析范例

PFMEA分析范例PFMEA(Process Failure Mode and Effects Analysis)是一种用于识别和评估过程潜在故障模式及其影响的方法。
它帮助组织在生产过程中识别可能导致产品质量问题或客户满意度下降的潜在故障点。
本文将以汽车制造业为例,演示如何进行PFMEA分析的过程。
1. 引言在汽车制造业中,质量是一个至关重要的因素。
任何生产过程中的潜在故障都可能导致产品质量下降,给整个供应链带来巨大损失。
因此,通过PFMEA分析,我们可以及早发现并解决问题,确保汽车制造过程的稳定和可靠性。
2. PFMEA分析步骤2.1 选择一个具体的生产过程在进行PFMEA分析之前,我们需要首先选择一个特定的生产过程。
例如,汽车车身焊接过程。
2.2 列出潜在故障模式针对选择的生产过程,我们需要列出所有可能发生的潜在故障模式。
例如,焊接接头松动、焊接过程中产生过多的火花等。
2.3 确定故障模式的原因针对每个潜在故障模式,我们需要分析其产生的原因。
例如,引起焊接接头松动的原因可能是焊接接头设计不合理或焊接机器设备故障。
2.4 评估故障模式的严重性对于每个故障模式,我们需要评估其对整个生产过程和最终产品的严重性。
这可以帮助我们确定应优先解决的问题。
2.5 确定潜在故障模式的探测手段针对每个故障模式,我们需要确定探测和监控这些故障模式的方法和手段。
例如,使用检测仪器来检查焊接接头的紧固程度。
2.6 评估故障模式的发生概率针对每个故障模式,我们需要评估其发生的概率。
这可以帮助我们确定哪些故障模式最有可能发生,并据此制定相应的对策。
2.7 评估故障模式的影响程度对于每个故障模式,我们需要评估其对生产过程和最终产品的实际影响程度。
这有助于确定应对故障的优先级。
2.8 确定风险优先级综合考虑故障严重性、发生概率和影响程度,我们可以确定每个故障模式的风险优先级。
这有助于确定制定相应的修正和改进措施的优先级。
3. 结论通过PFMEA分析,我们可以全面评估汽车制造过程中潜在故障模式的风险,并据此制定相应的对策。
PFMEA分析范例
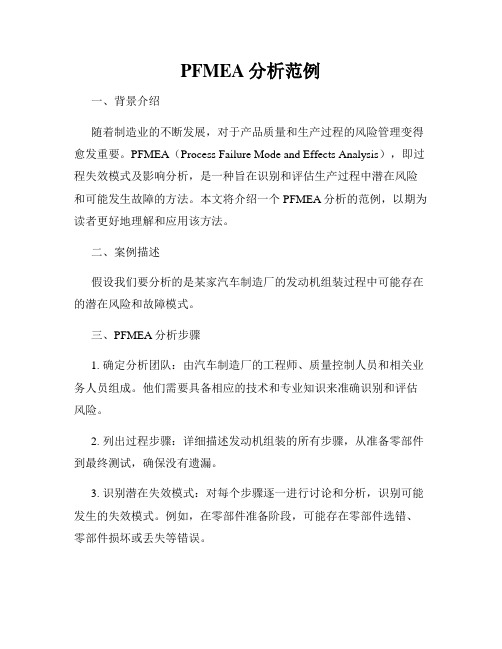
PFMEA分析范例一、背景介绍随着制造业的不断发展,对于产品质量和生产过程的风险管理变得愈发重要。
PFMEA(Process Failure Mode and Effects Analysis),即过程失效模式及影响分析,是一种旨在识别和评估生产过程中潜在风险和可能发生故障的方法。
本文将介绍一个PFMEA分析的范例,以期为读者更好地理解和应用该方法。
二、案例描述假设我们要分析的是某家汽车制造厂的发动机组装过程中可能存在的潜在风险和故障模式。
三、PFMEA分析步骤1. 确定分析团队:由汽车制造厂的工程师、质量控制人员和相关业务人员组成。
他们需要具备相应的技术和专业知识来准确识别和评估风险。
2. 列出过程步骤:详细描述发动机组装的所有步骤,从准备零部件到最终测试,确保没有遗漏。
3. 识别潜在失效模式:对每个步骤逐一进行讨论和分析,识别可能发生的失效模式。
例如,在零部件准备阶段,可能存在零部件选错、零部件损坏或丢失等错误。
4. 评估失效后果:对于每个失效模式,评估其对整个发动机性能和安全性的影响。
例如,零部件选错可能导致发动机无法正常工作或者存在严重的安全隐患。
5. 评估失效发生概率:考虑各种因素,如操作人员技能水平、设备可靠性、材料质量等,评估失效的发生概率。
例如,操作人员技能水平较低可能增加零部件选错的概率。
6. 计算风险优先级数值(RPN):根据失效的后果和发生概率,计算风险优先级数值。
RPN的计算公式为:RPN = 后果严重性 ×发生概率 ×检测能力。
例如,如果某个失效模式的后果严重性评分为10,发生概率为8,检测能力为9,则该失效模式的RPN为720。
7. 制定改进措施:对于RPN值较高的失效模式,制定相应的改进措施来降低风险。
例如,针对零部件选错,可以加强操作人员的培训和审查流程,以减少错误发生的概率。
8. 实施改进措施:将制定的改进措施纳入发动机组装过程,并确保实施有效。
仿真车玩具装配PFMEA分析范例

弹片不到位/变 形,错装
9
1.作业员操作 不良 2.物料半 ☆ 制品堆积,压变 形
3
1.FQC全检 1.作业指导书明确 2.IPQC巡检/ 要求 2.拉上物料 抽检 3.QA测 按要求摆放 试 1.作业指导书明确 要求 2.岗位培训/ 督导 1.作业指导书明确 要求 2.岗位培训/ 督导 1.作业指导书明确 要求 2.岗位培训/ 督导
FMEA 页 编
编
号 次 制
FMEA编制日期 FMEA回力驱动行驶功能 1.打开左/右车门,依次触发两种音乐,同时前车灯发白光,尾车灯发红光,表板灯发蓝光. 2.按压车前轮触发引擎声,同时前车灯发白光,尾车灯发红光,表板灯发蓝光.
2
54 改进作业工具
已安排夹具部 制作
9
2
2
36
2.PCB.A需正确装 PCB.A不到位,翘 到位. 起
无功能
6
◇
作业员操作不 良
3
2
36
3.车门开关不得 卡住
车门开关卡住
车门不能触发音 乐
5
作业员操作不 良
3
2
30
4.锁螺丝
螺丝用错/松动/ 滑牙
电子功能不良
5
作业员操作不 良/发料错
4
2
40
潜在失效模式及后果分析 P-FMEA
装/热烫排气管
装配到位/牢固
4
5
2
40 改进热烫工具
将铬铁头磨平
4
3
2
24
压前轮/装开关
车轮压到位(间距 1.测试不通过,不 车轮未压到位/轮 58.5±0.2mm)/不 符安规 2.行驶偏 芯压爆/压伤 得有外观缺陷 差大
9
PFMEA过程风险分析评估

产品型号/Product Model: / 关键日期/ Key Date:2020年3月18日 FMEA日期 FEMA date:2020年3月18日修订revised by:2020年4月5日核心小组:xxx xxx xxx xxx产品型号/Product Model: / 关键日期/ Key Date:2020年3月18日 FMEA日期 FEMA date:2020年3月18日修订revised by:2020年4月5日核心小组:xxx xxx xxx xxx产、设备每日点检;备每日点检;产品型号/Product Model : / 关 键 日 期/ Key Date :2020年3月18 日 FMEA 日期 FEMA date :2020年3月18日 修 订revised by :2020年4月5日核心小组:xxx xxx xxx xxx产、设备每日点检、上线前试产、设备每日点检专检验、上线前试产、设备每日点检产品型号/Product Model: / 关键日期/ Key Date:2020年3月18日 FMEA日期 FEMA date:2020年3月18日修订revised by:2020年4月5日核心小组:xxx xxx xxx xxx产品型号/Product Model: / 关键日期/ Key Date:2020年3月18日 FMEA日期 FEMA date:2020年3月18日修订revised by:2020年4月5日核心小组:xxx xxx xxx xxx产品型号/Product Model: / 关键日期/ Key Date:2020年3月18日 FMEA日期 FEMA date:2020年3月18日修订revised by:2020年4月5日核心小组:xxx xxx xxx xxx产品型号/Product Model: / 关键日期/ Key Date:2020年3月18日 FMEA日期 FEMA date:2020年3月18日修订revised by:2020年4月5日核心小组:xxx xxx xxx xxx产品型号/Product Model: / 关键日期/ Key Date:2020年3月18日 FMEA日期 FEMA date:2020年3月18日修订revised by:2020年4月5日核心小组:xxx xxx xxx xxx产品型号/Product Model: / 关键日期/ Key Date:2020年3月18日 FMEA日期 FEMA date:2020年3月18日修订revised by:2020年4月5日核心小组:xxx xxx xxx xxx1、原则上每批订单量产前均应进行风险评估,根据工厂实际,产品较为固定,生产及相应工艺较为简单,人机料法环等因素也稳定,故暂定正常生产时针对每种类型产品每年评估一次;2、人机料法环等因素或其他因素发生变更时,则也应进行风险评估;3、新产品开发时应也应进行风险评估。
PFMEA分析范例
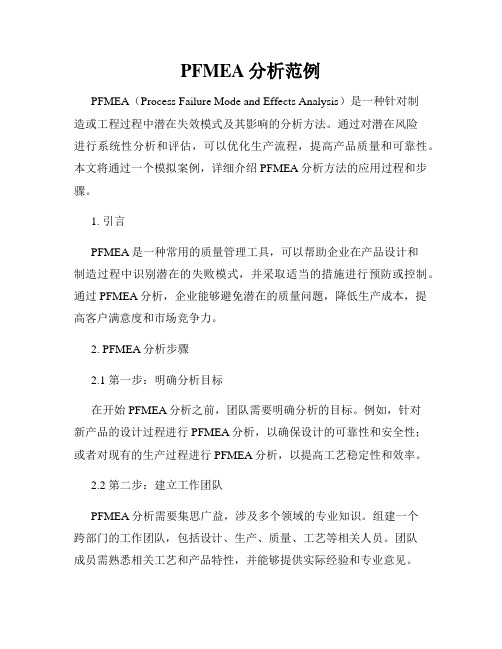
PFMEA分析范例PFMEA(Process Failure Mode and Effects Analysis)是一种针对制造或工程过程中潜在失效模式及其影响的分析方法。
通过对潜在风险进行系统性分析和评估,可以优化生产流程,提高产品质量和可靠性。
本文将通过一个模拟案例,详细介绍PFMEA分析方法的应用过程和步骤。
1. 引言PFMEA是一种常用的质量管理工具,可以帮助企业在产品设计和制造过程中识别潜在的失败模式,并采取适当的措施进行预防或控制。
通过PFMEA分析,企业能够避免潜在的质量问题,降低生产成本,提高客户满意度和市场竞争力。
2. PFMEA分析步骤2.1 第一步:明确分析目标在开始PFMEA分析之前,团队需要明确分析的目标。
例如,针对新产品的设计过程进行PFMEA分析,以确保设计的可靠性和安全性;或者对现有的生产过程进行PFMEA分析,以提高工艺稳定性和效率。
2.2 第二步:建立工作团队PFMEA分析需要集思广益,涉及多个领域的专业知识。
组建一个跨部门的工作团队,包括设计、生产、质量、工艺等相关人员。
团队成员需熟悉相关工艺和产品特性,并能够提供实际经验和专业意见。
2.3 第三步:识别潜在失效模式团队成员根据自身经验和知识,共同识别与分析对象相关的潜在失效模式。
失效模式可以包括设计缺陷、材料问题、加工工艺不当等。
团队成员应尽可能全面地讨论和归纳,并记录在PFMEA表中。
2.4 第四步:评估失效影响针对每一个潜在失效模式,团队成员需要评估其对产品质量、客户满意度和生产效率的影响程度。
评估标准可以根据实际情况进行设计,通常包括质量损失程度、生产变更的难易程度、不良事件的概率等。
2.5 第五步:确定原因和现有控制措施对于每一个潜在失效模式,团队需要分析其潜在原因并列出现有的控制措施。
原因分析可以采用5W1H(Who、What、When、Where、Why和How)的方法,识别可能导致失效的根本原因。
PFMEA分析范例
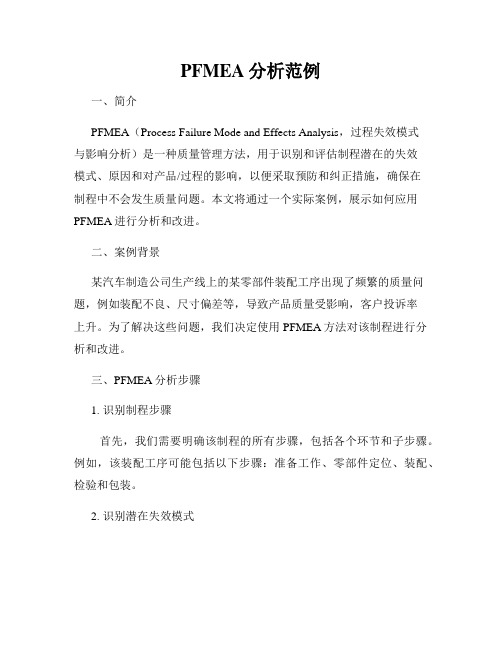
PFMEA分析范例一、简介PFMEA(Process Failure Mode and Effects Analysis,过程失效模式与影响分析)是一种质量管理方法,用于识别和评估制程潜在的失效模式、原因和对产品/过程的影响,以便采取预防和纠正措施,确保在制程中不会发生质量问题。
本文将通过一个实际案例,展示如何应用PFMEA进行分析和改进。
二、案例背景某汽车制造公司生产线上的某零部件装配工序出现了频繁的质量问题,例如装配不良、尺寸偏差等,导致产品质量受影响,客户投诉率上升。
为了解决这些问题,我们决定使用PFMEA方法对该制程进行分析和改进。
三、PFMEA分析步骤1. 识别制程步骤首先,我们需要明确该制程的所有步骤,包括各个环节和子步骤。
例如,该装配工序可能包括以下步骤:准备工作、零部件定位、装配、检验和包装。
2. 识别潜在失效模式对于每个制程步骤,我们需要识别可能的失效模式。
例如,在零部件定位步骤中可能出现的失效模式包括零部件定位不准确、零部件磨损等。
3. 评估失效影响针对每个失效模式,我们需要评估其对产品和制程的影响程度。
这可以通过制程图、统计数据和客户反馈等信息获得。
例如,零部件定位不准确可能导致装配不良、产品外观缺陷等问题。
4. 评估失效原因对于每个失效模式,我们需要分析其潜在原因。
这可以通过对制程参数、操作方法和设备条件等进行分析和检查来确定。
例如,零部件定位不准确的潜在原因可能是装配夹具磨损、工人技能不足等。
5. 评估当前控制措施针对每个失效模式和原因,我们需要评估当前是否有相应的控制措施。
如果有,需要评估其有效性和可靠性。
如果没有,需要考虑引入相应的控制措施。
例如,对于装配夹具磨损的失效原因,当前可能存在定期保养清洁措施,但其有效性需要进一步评估。
6. 制定改进措施基于对失效模式、影响、原因和控制措施的评估,我们可以制定相应的改进措施。
例如,针对装配夹具磨损的问题,我们可以考虑定期更换夹具、提供更好的保养指导等措施。
PFMEA范本案例
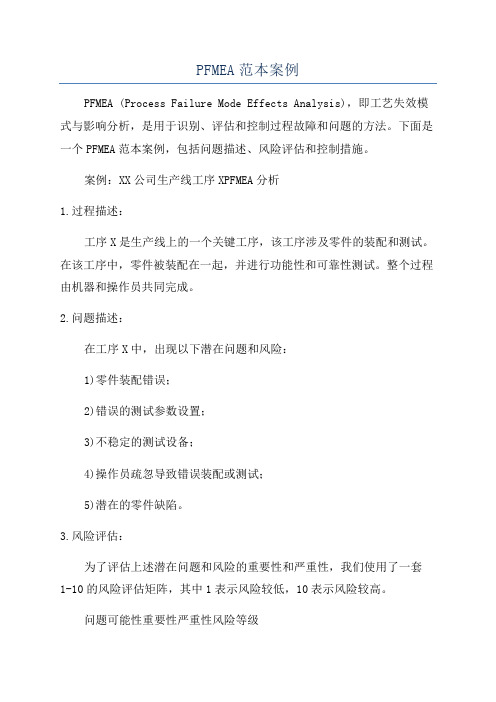
PFMEA范本案例PFMEA (Process Failure Mode Effects Analysis),即工艺失效模式与影响分析,是用于识别、评估和控制过程故障和问题的方法。
下面是一个PFMEA范本案例,包括问题描述、风险评估和控制措施。
案例:XX公司生产线工序XPFMEA分析1.过程描述:工序X是生产线上的一个关键工序,该工序涉及零件的装配和测试。
在该工序中,零件被装配在一起,并进行功能性和可靠性测试。
整个过程由机器和操作员共同完成。
2.问题描述:在工序X中,出现以下潜在问题和风险:1)零件装配错误;2)错误的测试参数设置;3)不稳定的测试设备;4)操作员疏忽导致错误装配或测试;5)潜在的零件缺陷。
3.风险评估:为了评估上述潜在问题和风险的重要性和严重性,我们使用了一套1-10的风险评估矩阵,其中1表示风险较低,10表示风险较高。
问题可能性重要性严重性风险等级零件装配错误87956错误的测试参数设置79856不稳定的测试设备58640操作员疏忽导致错误装配或测试66954潜在的零件缺陷310721注意:风险等级=可能性*重要性*严重性4.控制措施:基于上述评估结果,我们必须采取适当的控制措施来减少或消除潜在问题和风险。
问题控制措施零件装配错误1)提供装配指导书和流程图;2)定期进行员工培训,确保操作员技能;3)引入自动化装配设备,减少人为错误。
错误的测试参数设置1)设定可编程的测试参数,并进行封装;2)详细记录正确的测试参数;3)定期进行设备校准和维护。
不稳定的测试设备1)定期进行设备维护和保养;2)评估设备的可靠性,进行适当的维护。
操作员疏忽导致错误装配或测试1)强调操作员的责任和重要性;2)建立良好的质量管理文化;3)使用自动化检测设备进行装配和测试。
潜在的零件缺陷1)加强供应商质量管理;2)引入100%检验,筛选出潜在问题。
注意:控制措施要具体、可行,并由有效的检验和监控机制支持。
玩具产品过程风险评估【玩具产品潜在的失效模式及效应分析表PFMEA】
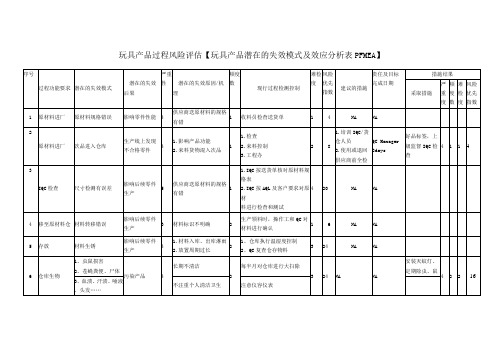
1、工厂使用利器发入记录
2、工厂使用易碎品检查记录
4
3
2
24
21
喷油/移印部生物
1、虫鼠损害
2、苍蝇粪便、尸体
污染产品
4
长期不清洁
2
每半月对车间进行大扫除
3
24
NA
NA
安装灭蚊灯、定期除虫、鼠
4
2
2
16
3、血渍、汗渍、唾液
、头发……
不注重个人清洁卫生
注意仪容仪表
22
喷油/移印部环境
1、物料发霉、生锈
2
1、仓库执行温湿度控制
2、QC复查仓存物料
3
24
NA
NA
6
仓库生物
1、虫鼠损害
2、苍蝇粪便、尸体
污染产品
4
长期不清洁
2
每半月对仓库进行大扫除
3
24
NA
NA
安装灭蚊灯、定期除虫、鼠
4
2
2
16
3、血渍、汗渍、唾液
、头发……
不注重个人清洁卫生
注意仪容仪表
7
仓库
1、物料发霉、生锈
2、光线暗淡造成产品
无法辨识
4
2
2
16
3、血渍、汗渍、唾液
、头发……
不注重个人清洁卫生
注意仪容仪表
正确佩带防护用品
26
装配部环境
1、物料发霉、生锈
2、光线暗淡造成产品
无法辨识
产品受损、误验或误使用物料
3
1、车间通风不良
2、光源安装不够
1
1、温湿度控制
2、安装LED灯
1
6
NA
PFMEA分析范例
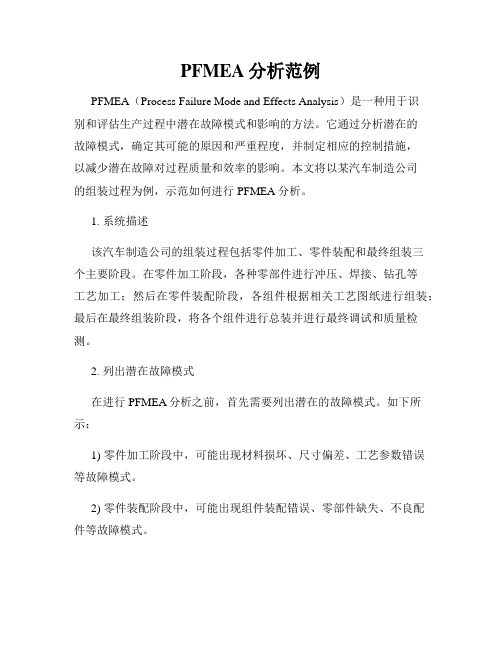
PFMEA分析范例PFMEA(Process Failure Mode and Effects Analysis)是一种用于识别和评估生产过程中潜在故障模式和影响的方法。
它通过分析潜在的故障模式,确定其可能的原因和严重程度,并制定相应的控制措施,以减少潜在故障对过程质量和效率的影响。
本文将以某汽车制造公司的组装过程为例,示范如何进行PFMEA分析。
1. 系统描述该汽车制造公司的组装过程包括零件加工、零件装配和最终组装三个主要阶段。
在零件加工阶段,各种零部件进行冲压、焊接、钻孔等工艺加工;然后在零件装配阶段,各组件根据相关工艺图纸进行组装;最后在最终组装阶段,将各个组件进行总装并进行最终调试和质量检测。
2. 列出潜在故障模式在进行PFMEA分析之前,首先需要列出潜在的故障模式。
如下所示:1) 零件加工阶段中,可能出现材料损坏、尺寸偏差、工艺参数错误等故障模式。
2) 零件装配阶段中,可能出现组件装配错误、零部件缺失、不良配件等故障模式。
3) 最终组装阶段中,可能出现组装错误、传动系统故障、电子系统故障等故障模式。
3. 评估故障原因在列出潜在故障模式之后,需评估每种故障模式的可能原因。
具体评估过程如下:1) 零件加工阶段中,材料损坏的原因可能是供应商提供的原材料质量不合格,尺寸偏差的原因可能是机床设备调整不当,工艺参数错误的原因可能是人工操作失误。
2) 零件装配阶段中,组件装配错误的原因可能是工人操作不规范,零部件缺失的原因可能是供应链管理不善,不良配件的原因可能是供应商提供的配件质量不合格。
3) 最终组装阶段中,组装错误的原因可能是工人操作失误,传动系统故障的原因可能是组装过程中零部件配合不良,电子系统故障的原因可能是控制芯片质量问题。
4. 评估故障严重程度在评估故障原因后,需要评估每种故障模式的严重程度,即故障发生时可能造成的影响程度。
具体评估过程如下:1) 零件加工阶段中,材料损坏可能导致后续组装工序无法进行,尺寸偏差可能导致产品性能下降,工艺参数错误可能导致产品质量问题。
玩具产品过程风险评估PFMEA
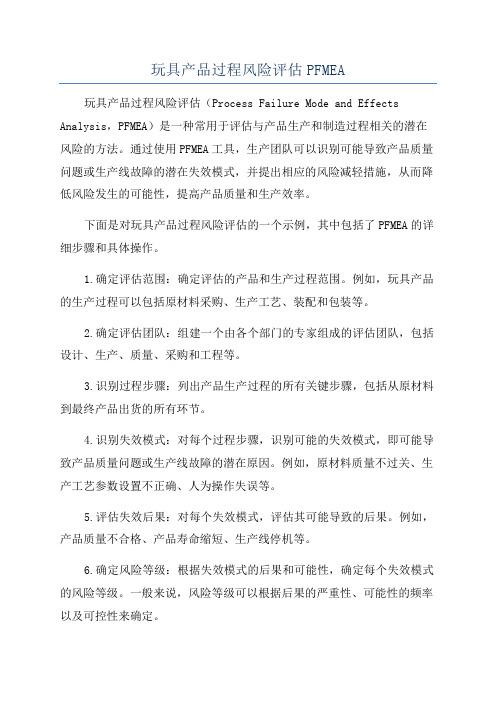
玩具产品过程风险评估PFMEA玩具产品过程风险评估(Process Failure Mode and Effects Analysis,PFMEA)是一种常用于评估与产品生产和制造过程相关的潜在风险的方法。
通过使用PFMEA工具,生产团队可以识别可能导致产品质量问题或生产线故障的潜在失效模式,并提出相应的风险减轻措施,从而降低风险发生的可能性,提高产品质量和生产效率。
下面是对玩具产品过程风险评估的一个示例,其中包括了PFMEA的详细步骤和具体操作。
1.确定评估范围:确定评估的产品和生产过程范围。
例如,玩具产品的生产过程可以包括原材料采购、生产工艺、装配和包装等。
2.确定评估团队:组建一个由各个部门的专家组成的评估团队,包括设计、生产、质量、采购和工程等。
3.识别过程步骤:列出产品生产过程的所有关键步骤,包括从原材料到最终产品出货的所有环节。
4.识别失效模式:对每个过程步骤,识别可能的失效模式,即可能导致产品质量问题或生产线故障的潜在原因。
例如,原材料质量不过关、生产工艺参数设置不正确、人为操作失误等。
5.评估失效后果:对每个失效模式,评估其可能导致的后果。
例如,产品质量不合格、产品寿命缩短、生产线停机等。
6.确定风险等级:根据失效模式的后果和可能性,确定每个失效模式的风险等级。
一般来说,风险等级可以根据后果的严重性、可能性的频率以及可控性来确定。
7.制定措施:对于高风险的失效模式,制定相应的控制措施,以减少风险的发生可能性或后果的严重性。
例如,提高原材料检验标准、优化生产工艺参数、提供操作培训等。
8.验证效果:在实施控制措施后,验证其是否有效降低了风险。
可以通过持续监控产品质量和生产线运行情况来评估控制措施的有效性。
9.定期复评:定期对玩具产品的生产过程进行复评,以确认控制措施的有效性并识别新的风险。
10.记录和追踪:将PFMEA的结果和控制措施记录下来,并建立追踪机制,以便随时查阅和跟踪控制措施的实施情况和效果。
PFMEA分析范例

PFMEA分析范例PFMEA(Potential Failure Mode and Effects Analysis)是一种常用于产品设计和生产过程中的风险评估工具。
它通过系统地识别潜在的失效模式,并评估这些失效对产品性能、生产效率和客户满意度的影响,从而帮助企业采取相应的措施来预防和降低潜在失效的风险。
本文将以汽车制造业为例,介绍PFMEA分析的具体步骤和相关应用。
1. 背景介绍汽车制造业面临着严格的质量要求和市场竞争压力。
在生产过程中,如果存在失效模式而未能及时发现或纠正,将会导致产品质量问题、客户投诉以及生产效率下降等严重后果。
因此,采用PFMEA分析方法能够帮助企业降低失效风险,提高产品质量和生产效率。
2. PFMEA分析步骤2.1 制定团队PFMEA分析需要跨职能团队共同参与,包括设计工程师、生产工程师、供应商等相关人员。
团队成员应根据其专业知识和经验来确定潜在失效模式及其影响因素。
2.2 识别失效模式团队成员根据产品设计和制造过程,逐一识别可能存在的失效模式。
例如,在汽车制造过程中,可能存在供应商提供零部件质量不合标准、零部件装配不准确等失效模式。
2.3 评估失效影响针对每个失效模式,团队成员评估其对产品性能、生产效率和客户满意度的影响程度。
评估指标可以根据实际情况进行确定,如利用5W1H法(What、When、Where、Why、How)来进行细致拆解。
2.4 评估失效原因团队成员分析导致每种失效模式的潜在原因,可以运用鱼骨图(也称因果图)或5W1H法来帮助识别。
例如,失效模式为零部件装配不准确,潜在原因可能包括操作员技能不足、装配工具磨损等。
2.5 制定控制措施团队成员针对每个失效模式及其原因,制定相应的控制措施,以预防或降低失效风险。
控制措施可以包括提高操作员培训、更换装配工具等。
2.6 评估控制效果实施控制措施后,团队成员应不定期进行监控和评估,以确定措施的有效性。
如果控制措施无效,需要重新进行评估并采取其他措施。
PFMEA分析范例

PFMEA分析范例1. 简介PFMEA (Process Failure Mode and Effects Analysis),即过程失效模式及影响分析,是一种系统性的风险评估工具,用于识别并预防制造过程中潜在的失败模式及其潜在影响。
本文将通过一个范例来详细介绍PFMEA分析的步骤和方法。
2. 背景假设某家汽车制造公司计划引入一种新的生产工艺,目标是提高汽车制造的效率和品质。
在引入新工艺之前,进行PFMEA分析是非常重要的,以确保对潜在的失败模式和影响有清晰的认识,并制定相应的预防措施。
3. PFMEA分析步骤PFMEA分析通常包括以下几个步骤:3.1 选择分析的过程首先,确定需要进行PFMEA分析的过程,例如汽车装配过程中的焊接环节。
3.2 列出潜在的失效模式然后,针对该过程列出所有可能的失效模式,例如焊接不牢固、焊接位置偏移等。
3.3 评估失效的严重性对于每个失效模式,评估其对产品品质和客户满意度的潜在影响程度,并分配相应的分数或等级。
3.4 确定失效的原因分析失效模式发生的原因,包括人、机、料、法、环等因素,并找到可能的根本原因。
3.5 评估失效的发现控制能力评估当前的检测和控制措施对该失效模式的发现能力,并分配相应的分数或等级。
3.6 计算风险优先级数根据失效严重性、失效发生概率和失效发现控制能力,计算每个失效模式的风险优先级数(RPN)。
3.7 制定预防措施针对风险优先级数较高的失效模式,制定相应的预防措施和改进计划,并跟踪实施情况和改进效果。
4. 范例分析以焊接过程中焊接不牢固为例,进行PFMEA分析。
4.1 失效模式:焊接不牢固- 严重性评估:影响产品结构强度,客户满意度较高 (评分:9)- 失效原因:焊接温度不足、焊接时间不足、焊接压力不足- 发现控制能力:目前使用目视检测,发现率较低 (评分:4)- 风险优先级数:9 x 4 x 4 = 1444.2 预防措施- 加强焊接工艺参数监控,确保温度、时间和压力符合规范要求- 引入可靠的自动化焊接设备,提高焊接质量和一致性- 增加额外的目视检测环节,提高焊接不牢固的发现率5. 结论通过PFMEA分析,针对焊接不牢固失效模式,我们提出了一系列的预防措施,旨在降低风险优先级数,确保焊接过程的稳定性和产品品质。
PFMEA分析范例
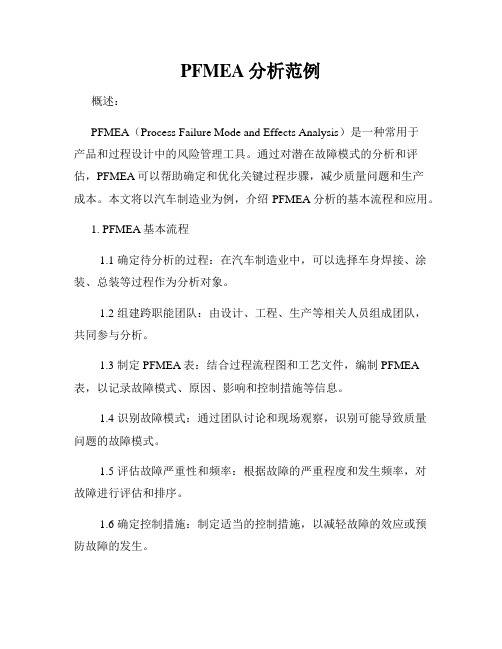
PFMEA分析范例概述:PFMEA(Process Failure Mode and Effects Analysis)是一种常用于产品和过程设计中的风险管理工具。
通过对潜在故障模式的分析和评估,PFMEA可以帮助确定和优化关键过程步骤,减少质量问题和生产成本。
本文将以汽车制造业为例,介绍PFMEA分析的基本流程和应用。
1. PFMEA基本流程1.1 确定待分析的过程:在汽车制造业中,可以选择车身焊接、涂装、总装等过程作为分析对象。
1.2 组建跨职能团队:由设计、工程、生产等相关人员组成团队,共同参与分析。
1.3 制定PFMEA表:结合过程流程图和工艺文件,编制PFMEA 表,以记录故障模式、原因、影响和控制措施等信息。
1.4 识别故障模式:通过团队讨论和现场观察,识别可能导致质量问题的故障模式。
1.5 评估故障严重性和频率:根据故障的严重程度和发生频率,对故障进行评估和排序。
1.6 确定控制措施:制定适当的控制措施,以减轻故障的效应或预防故障的发生。
1.7 评估控制措施的有效性:对已实施的控制措施进行评估,确保其有效性。
1.8 持续改进:根据实际应用情况,持续改进并更新PFMEA表。
2. 汽车制造业中的PFMEA应用2.1 车身焊接过程2.1.1 故障模式:焊接接头断裂2.1.2 原因分析:焊接参数不合适、焊缝设计不合理等2.1.3 故障影响:车身刚性降低,安全性能下降2.1.4 控制措施:优化焊接参数、改进焊缝设计、加强焊接工艺监控2.2 涂装过程2.2.1 故障模式:漏涂、起皮2.2.2 原因分析:喷涂设备故障、工艺流程不合理等2.2.3 故障影响:外观质量下降,耐候性降低2.2.4 控制措施:定期维护喷涂设备、优化涂装工艺、加强质量检查2.3 总装过程2.3.1 故障模式:装配错误、零部件损坏2.3.2 原因分析:装配工序缺失、操作不规范等2.3.3 故障影响:功能失效,客户投诉2.3.4 控制措施:明确装配流程、培训装配人员、加强质量把关3. PFMEA分析的效益通过PFMEA分析,汽车制造企业可以实现以下效益:3.1 降低质量成本:通过确定和控制潜在故障点,减少质量问题的发生,降低质量成本。
- 1、下载文档前请自行甄别文档内容的完整性,平台不提供额外的编辑、内容补充、找答案等附加服务。
- 2、"仅部分预览"的文档,不可在线预览部分如存在完整性等问题,可反馈申请退款(可完整预览的文档不适用该条件!)。
- 3、如文档侵犯您的权益,请联系客服反馈,我们会尽快为您处理(人工客服工作时间:9:00-18:30)。
潜在失效模式及后果分析-来料检验潜在失效模式及后果分析-物料贮存潜在失效模式及后果分析-领料潜在失效模式及后果分析-混料/加料潜在失效模式及后果分析-烘料潜在失效模式及后果分析-装/卸模潜在失效模式及后果分析-注塑成型潜在失效模式及后果分析-首件检验潜在失效模式及后果分析-IPQC巡检潜在失效模式及后果分析-产品喷印
11、潜在失效模式及后果分析-装配12、
潜在失效模式及后果分析-入库、贮存、出货仿真车模型玩具PFMEA风险分析范例
目录
1、2、9、10、3、4、5、6、7、
8、。