低压铸造机技术方案设计书
低、差压铸造-简化
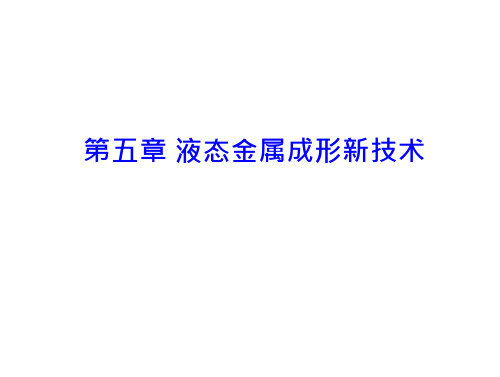
确定铸型的种类
形状一般,精度或质量 要求较高、批量较大
金属型或石墨型
铸件内腔复杂 无法用金属型芯 可用砂芯
铸件精度要求高
熔模壳型或熔模石膏型
大型铸件 精度要求不高 单件或小批生产
可用砂型
原则二:
合金充型、结晶的工艺压力为0.05~0.07MP 应确保铸型能承受这种压力
原则三:
金属液凝固自上而下
所需保压时间为宜
二、低压铸造特点
基本特点
较强的补缩能力,无需复杂的浇注 系统和大量的冒口
金属液流动较平稳,充型能力较强
浇注过程的控制比较精确,自动化 程度比较高
1. 可用于铸造形状复杂的薄壁铸件 金属液在压力下充填,流动性好,充填能力强, 有利于获得轮廓清晰的铸件
2. 铸件力学性能高 铸件在压力下凝固,补缩效果好,致密度高, 力学性能好,可用于生产耐压、防渗漏的铸件
t2– t
升液、充 型阶段
增压法下压力罐 压力随时间递增
减压法上压力罐 压力随时间递减
t4 – t
保压 阶段
t5 – t
互通 阶段
增压法下压力 罐停止充气
减压法上压力 罐停止排气
上下压力罐间 压力差降至零
压力不变直 到凝固结束
多余合金液 经升液管返 回坩埚
上下压力罐同时排气,压力消失
熔化MPa下凝固,密度比常压下提高了13.32%
保压时间
金属液面上压力升至凝固压力 后开始,至铸件完全凝固时间
时间过长 浇口残留部分多
金属利用率低
铸件取出困难
升液管清理工 作量大
时间过短 铸件中尚未凝固金属液在重力作用 下沉回坩埚,使铸件“放空”而报
精确控制 获得优质铸件的重要工艺因素 铸型种类
第2篇第1章 低压铸造

顶铸式低压铸造机
1-电热加热 保温炉
2-机架 3-供气系统
顶铸式低压铸造机特点: 一台炉上只能放一副铸型,结构简单,操作方 便,但生产效率低,生产结构复杂的铸件需要向 下抽芯时,无法设置抽芯机构。
侧铸式低压铸造机
1-电热反射 式保温炉
2-机架 3-供气系统
侧铸式低压铸造机特点: 铸型和保温炉由升液管连接,一台保温炉可供 两副铸型交替作业,也可同时作业,生产效率 高。装料、撇渣和处理金属液都较方便。这类铸 型的结构复杂。
坩埚材料有一定的高温强度、热稳定性及抗铝液 侵蚀的能力,一般采用合金铸铁或中硅球铁。在 某些特殊情况下,如铁质对某种合金有害、影响 极为严重时,可选用石墨坩埚。
3、密封盖 电阻加热炉的密封盖工作条件差,要求严格,
不但起密封作用,且要承受铸型重量及开合机构 的冲击。因此必须有足够的强度和刚度,在受热 和压力下不变形。通常使用球墨铸铁的密封盖。
陶瓷升液管
1.3.2 铸型开合机构
铸型开合机构有 手动 机械传动 气动传动 液压传动
手动铸型开合机构,其结构简单,但开合力 小,适用于小件生产。
机械传动铸型开合机构,开模力中等,只适用 于两半开模的铸型。
气动传动铸型开合机构,开合动作不平稳,有 冲击,适用于简单小件生产。
液压传动铸型开合机构,开合动作平稳,开合 力大,适用于任何铸型。
—
90
砂型低压 345~374
—
18.5~ — 84~100
铸造
48.7
砂型铸造
—
350~360 —
13
—
砂型低压 铸造
金属型低 压铸造
—
390~395 — 21~24 —
—
440~450 — 17~22 —
低压铸造机项目实施方案

第一章项目概况一、项目概况(一)项目名称低压铸造机项目(二)项目选址xx科技园对周围环境不应产生污染或对周围环境污染不超过国家有关法律和现行标准的允许范围,不会引起当地居民的不满,不会造成不良的社会影响。
(三)项目用地规模项目总用地面积12539.60平方米(折合约18.80亩)。
(四)项目用地控制指标该工程规划建筑系数68.77%,建筑容积率1.15,建设区域绿化覆盖率7.67%,固定资产投资强度181.23万元/亩。
(五)土建工程指标项目净用地面积12539.60平方米,建筑物基底占地面积8623.48平方米,总建筑面积14420.54平方米,其中:规划建设主体工程10549.35平方米,项目规划绿化面积1106.41平方米。
(六)设备选型方案项目计划购置设备共计39台(套),设备购置费967.12万元。
(七)节能分析1、项目年用电量969069.06千瓦时,折合119.10吨标准煤。
2、项目年总用水量3231.26立方米,折合0.28吨标准煤。
3、“低压铸造机项目投资建设项目”,年用电量969069.06千瓦时,年总用水量3231.26立方米,项目年综合总耗能量(当量值)119.38吨标准煤/年。
达产年综合节能量41.94吨标准煤/年,项目总节能率24.16%,能源利用效果良好。
(八)环境保护项目符合xx科技园发展规划,符合xx科技园产业结构调整规划和国家的产业发展政策;对产生的各类污染物都采取了切实可行的治理措施,严格控制在国家规定的排放标准内,项目建设不会对区域生态环境产生明显的影响。
(九)项目总投资及资金构成项目预计总投资4238.27万元,其中:固定资产投资3407.12万元,占项目总投资的80.39%;流动资金831.15万元,占项目总投资的19.61%。
(十)资金筹措该项目现阶段投资均由企业自筹。
(十一)项目预期经济效益规划目标预期达产年营业收入5859.00万元,总成本费用4411.95万元,税金及附加74.11万元,利润总额1447.05万元,利税总额1720.75万元,税后净利润1085.29万元,达产年纳税总额635.46万元;达产年投资利润率34.14%,投资利税率40.60%,投资回报率25.61%,全部投资回收期5.41年,提供就业职位106个。
铝合金电机壳低压砂型铸造工艺设计

铝合金电机壳低压砂型铸造工艺设计摘要:近年来,在节能减排和环保的需求下,汽车制造企业的研发重点正在由传统燃料汽车向新能源汽车转移。
铝合金电机壳作为新能源汽车的动力总成核心铸件,结构比较复杂,铸造难度大。
水冷电机壳体的侧壁环绕冷却水套的密封性是产品的重要技术要求,也是产品最大的铸造。
同时,电机壳体上、下端面以及侧壁的缩松也是工艺开发中需要避免的铸造缺陷。
随着计算机技术在铸造领域的迅速发展,通过铸造过程模拟仿真分析模拟可以预测铸造缺陷,评估工艺可行性。
关键词:铝合金电机壳;低压砂型铸造;工艺设计;前言:由于大型薄壁壳体类铸件壁的空间分布无明显规律,有必要在低压铸造设备完备的前提下针对树脂砂或石墨型低压铸造方法进行工艺试验研究,从而铸造成组织致密、尺寸精确的优质铸件这类铸件在核电装备中亦具有重要地位。
一、对象目前,型号弹上产品的壳体类铸件可以分为两大类:①四面体结构;②五面体结构。
四面体壳体铸件长一般为260~280 mm,宽140~150 mm,高120~150 mm,最小壁厚3 mm,最大壁厚10 mm。
在每个侧面的两端都有突出的台肩;要求铸件满足规定的各项技术要求;其材质选用ZL 104或ZL 114A,铸件毛坯重约20 kg;要求铸件不能有裂纹、气孔、缩松、夹杂等铸造缺陷;铸件针孔度要求为三级,局部允许四级。
以往所采用的砂型重力铸造方法不能满足技术要求。
二、铝合金电机壳低压砂型铸造工艺设计1.铸件的浇注位置。
铸件的浇注位置是指浇注时铸件在铸型中的位置。
浇注位置是根据零件的结构特点、尺寸、重量、技术要求、铸造合金特性、铸造方法以及生产车间的条件决定的。
正确的浇注位置应能保证获得健全的铸件,并使造型、造芯和清理方便。
铸件的加工面、主要工作面应尽量放在底部或侧面,以防止这些表面上产生沙眼、气孔、夹渣等铸造缺陷。
因此,根据上述要求和有利于铸件的凝固顺序,以及有利于砂心的定位和稳固支撑、使排气顺畅等的分析,砂箱中铸件数量的确定砂箱中铸件的数量一般要根据工艺要求和生产条件(生产批量及设备的相互要求和配合等)来确定。
汽车铸铝轮毂低压铸造技术分析
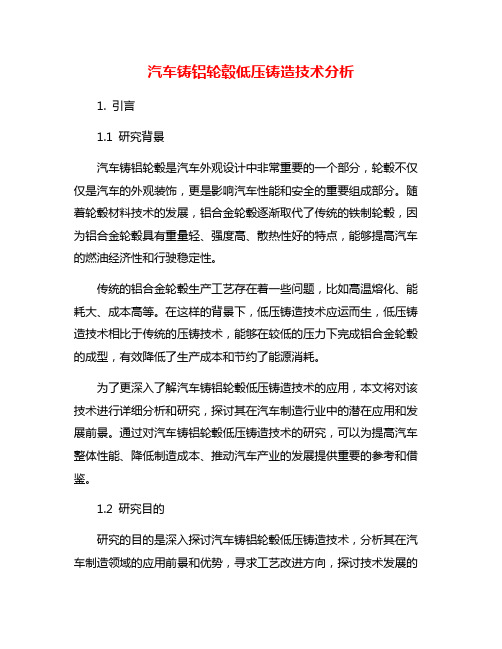
汽车铸铝轮毂低压铸造技术分析1. 引言1.1 研究背景汽车铸铝轮毂是汽车外观设计中非常重要的一个部分,轮毂不仅仅是汽车的外观装饰,更是影响汽车性能和安全的重要组成部分。
随着轮毂材料技术的发展,铝合金轮毂逐渐取代了传统的铁制轮毂,因为铝合金轮毂具有重量轻、强度高、散热性好的特点,能够提高汽车的燃油经济性和行驶稳定性。
传统的铝合金轮毂生产工艺存在着一些问题,比如高温熔化、能耗大、成本高等。
在这样的背景下,低压铸造技术应运而生,低压铸造技术相比于传统的压铸技术,能够在较低的压力下完成铝合金轮毂的成型,有效降低了生产成本和节约了能源消耗。
为了更深入了解汽车铸铝轮毂低压铸造技术的应用,本文将对该技术进行详细分析和研究,探讨其在汽车制造行业中的潜在应用和发展前景。
通过对汽车铸铝轮毂低压铸造技术的研究,可以为提高汽车整体性能、降低制造成本、推动汽车产业的发展提供重要的参考和借鉴。
1.2 研究目的研究的目的是深入探讨汽车铸铝轮毂低压铸造技术,分析其在汽车制造领域的应用前景和优势,寻求工艺改进方向,探讨技术发展的新方向。
通过对低压铸造技术的概述和分析,全面了解其在生产工艺中的具体运用,探究影响因素及其优势与劣势的比较,为提升铸铝轮毂质量和生产效率提供技术支持。
结合行业发展现状和需求,探讨汽车铸铝轮毂低压铸造技术的未来发展前景,为汽车制造业的技术升级和转型提供支持和推动。
通过本文的研究,旨在为相关领域的专业人士和研究者提供参考和借鉴,促进汽车铸造工艺的创新和提升,推动行业发展和技术进步。
1.3 研究意义研究汽车铸铝轮毂低压铸造技术的意义在于提高产品质量和生产效率,降低生产成本,延长产品使用寿命,提升汽车行驶安全性和舒适性。
通过深入研究汽车铸铝轮毂低压铸造技术,可以促进技术的进步和产业的发展,推动我国汽车制造业向更高水平迈进。
研究汽车铸铝轮毂低压铸造技术还将为相关领域的研究提供参考和借鉴,推动汽车零部件制造工艺的不断创新和完善。
低压铸造工程施工方案
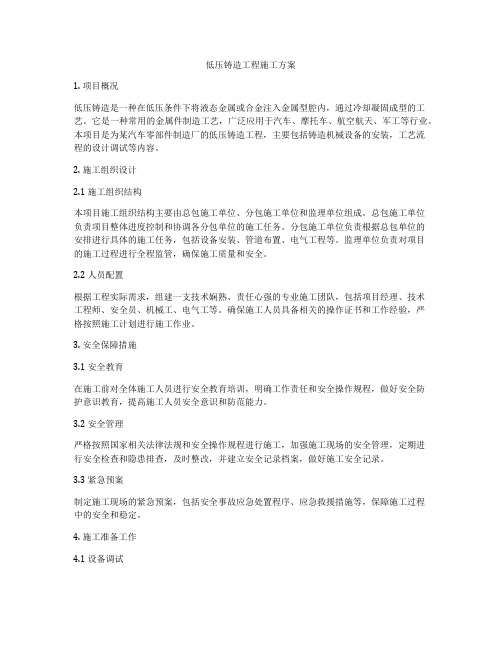
低压铸造工程施工方案1. 项目概况低压铸造是一种在低压条件下将液态金属或合金注入金属型腔内,通过冷却凝固成型的工艺。
它是一种常用的金属件制造工艺,广泛应用于汽车、摩托车、航空航天、军工等行业。
本项目是为某汽车零部件制造厂的低压铸造工程,主要包括铸造机械设备的安装,工艺流程的设计调试等内容。
2. 施工组织设计2.1 施工组织结构本项目施工组织结构主要由总包施工单位、分包施工单位和监理单位组成。
总包施工单位负责项目整体进度控制和协调各分包单位的施工任务。
分包施工单位负责根据总包单位的安排进行具体的施工任务,包括设备安装、管道布置、电气工程等。
监理单位负责对项目的施工过程进行全程监管,确保施工质量和安全。
2.2 人员配置根据工程实际需求,组建一支技术娴熟、责任心强的专业施工团队,包括项目经理、技术工程师、安全员、机械工、电气工等。
确保施工人员具备相关的操作证书和工作经验,严格按照施工计划进行施工作业。
3. 安全保障措施3.1 安全教育在施工前对全体施工人员进行安全教育培训,明确工作责任和安全操作规程,做好安全防护意识教育,提高施工人员安全意识和防范能力。
3.2 安全管理严格按照国家相关法律法规和安全操作规程进行施工,加强施工现场的安全管理,定期进行安全检查和隐患排查,及时整改,并建立安全记录档案,做好施工安全记录。
3.3 紧急预案制定施工现场的紧急预案,包括安全事故应急处置程序、应急救援措施等,保障施工过程中的安全和稳定。
4. 施工准备工作4.1 设备调试在正式施工前对低压铸造设备进行调试检验,包括液态金属或合金注入系统、型腔冷却系统、自动控制系统等,确保设备正常运转,无故障和泄漏。
4.2 施工材料准备准备好施工所需的各类材料和配件,包括铸造金属、冷却剂、模具、工具设备、电气元件等,确保施工过程中物资供应充足。
4.3 现场布置根据施工图纸和规划方案对施工现场进行合理布置,确保设备、材料、人员等资源的合理分配和利用。
电动客车水冷机壳低压铸造工艺设计与优化

电动客车水冷机壳低压铸造工艺设计与优化摘要针对电动客车电动机壳体直径较大、内壁筒状水套范围广和壁厚不均匀等特点,分析了水冷机壳的复杂结构及筒状砂芯对铝合金低压铸造顺序凝固的影响。
设计低压铸造浇注系统、模具结构和工艺参数。
通过AnyCasting软件模拟铸件凝固过程,预测壁厚不均匀产生的热节和砂芯分隔作用形成的孤立液相情况,以及由此引发部分位置容易出现的缩松缩孔等缺陷。
探究如何采用铍铜镶件、水冷镶件和气冷管等优化措施调整凝固速度,提高铸件内部组织成形致密度及生产质量。
相比一般的小型电动轿车,载客量更多的大型电动客车电动机功率较大,壳体直径也更大,驱动电机行驶过程中会产生更多的热量。
因此需要在其铝合金壳体零件内部设计更大范围的水套结构,形成内壁中空的大面积冷却水道,通过循环冷却控制电动机内部温度,提升电动机的最高转速和持续工作时间。
1水冷机壳体结构图1为某低压铸造生产的电动客车水冷机壳,其外形是直径为320 mm,高为260 mm的圆筒形状;铸件壁厚为4~8 mm,铸件材质为A356铝合金。
机壳内壁做成了中空圆筒形状环绕的冷却水套,冷却水套分布范围越大,则能使得到持续冷却的电动机续航性能越好。
但大范围的冷却水套砂芯结构,又为铝合金液体的充型过程和顺序凝固增加了困难,为低压铸造工艺设计带来一定的难度。
需要合理设计低压铸造模具结构和工艺参数,并运用CAE模拟软件进行充型模拟分析及优化改进工艺,避免低压铸造生产中凝固过程产生缺陷,提升低压铸造质量水平和生产能力。
图1:水冷机壳壳体和内部水套砂芯图2浇注系统和模具结构设计方案从图1可以看出,这种大型砂芯的存在容易增加低压铸造充型时的铝液上升阻力,并阻隔铸件部分位置壁厚的正常连接,妨碍低压铸造顺序凝固。
为了能在短时间完成铝合金液体完全注入,浇口设计为4个圆台分浇口同时注入铝液。
每个浇口最大尺寸为¢90 mm,最小处即进料口直径为¢60 mm;铝液在压力作用下经升液管先进入升液箱,再分开4个浇口均衡进入型腔,见图2a。
轻合金高压、低压、挤压、差压、半固态等铸造工艺与装备研发生产方案(一)

轻合金高压、低压、挤压、差压、半固态等铸造工艺与装备研发生产方案一、背景随着制造业的飞速发展,轻合金材料在汽车、航空航天、电子通信等领域的应用越来越广泛。
其中,高压、低压、挤压、差压和半固态等铸造工艺在轻合金制造中扮演着关键角色。
然而,当前市场上,工艺与装备的结合尚存在诸多不足,急需升级与改进。
本方案旨在提供一种全面、先进的轻合金铸造工艺与装备研发生产方案。
二、工作原理1.高压铸造:通过高压注射器将液态轻合金注入模具,冷却后获得所需形状的铸件。
此方法适用于生产大型、结构复杂的轻合金部件。
2.低压铸造:在低压下将液态轻合金注入模具,使其缓慢冷却凝固。
此方法适用于生产中小型、对细节要求高的轻合金部件。
3.挤压铸造:将液态轻合金注入模具,通过外部压力将金属填充到模具的细微部分,冷却后获得精确形状的铸件。
此方法适用于生产需要高精度、高强度的小型轻合金部件。
4.差压铸造:利用外部气压或真空度与模具内部气压的差异,将液态轻合金吸入模具,冷却后获得铸件。
此方法适用于生产大型、结构复杂的轻合金部件,能够减少气孔等缺陷。
5.半固态铸造:将轻合金在凝固点附近进行搅拌,使其处于半固态状态,然后注入模具。
此方法适用于生产具有特殊性能要求的大型轻合金部件,如飞机起落架等。
三、实施计划步骤1.市场调研与需求分析:深入了解各行业对轻合金铸造工艺与装备的需求,为研发提供方向。
2.技术研究与开发:结合现代制造技术,对高压、低压、挤压、差压、半固态等铸造工艺与装备进行深入研究,开发具有自主知识产权的技术。
3.工艺优化与实验验证:根据市场需求和技术研究结果,对各种工艺进行优化调整,并通过实验验证其有效性。
4.装备设计与制造:根据优化后的工艺需求,设计相应的铸造装备,确保其高效、稳定和安全。
5.市场推广与应用:将研发成功的工艺与装备推向市场,提供技术支持和售后服务,确保客户能够充分利用其价值。
四、适用范围本方案适用于汽车、航空航天、电子通信等行业的轻合金铸造工厂,为其提供全面、先进的铸造工艺与装备解决方案。
基于CADCAE的壳体铸件低压铸造工艺设计

3.3 结壳时间t3的确定 一般地说,采用金属型时结壳 时间比较短,有时可以取消结 壳时间,直接增压,但考虑到 该壳体有厚大部位,结壳时间 选择5 s。
3.4 增压压力只及增压速度的确定
液态金属在一定压力下进行结晶,是低压 铸造的特点之一,因此增压压力也称为结 晶压力,即充型结束后,在充型压力的基 础上,再使压力增加一定数值,有利于铸 件补缩,可有效地消除缩孔、缩松,提高 组织的致密度,但由于铸型及设备条件等 因素的限制,增压压力也不能太高。
2.2浇口设计 一般来说,低压铸件的加工余量为1—2 mm,为增加补缩通道,在浇道处中心 孔内圆加工余量为10 mm,由枷O mm 变成弘0 mm,在浇道起始平面加工余量 为8mm,浇道大端直径为拍5 mm,起 模斜度为5。。在分型面设置随形集渣包, 使得最先流人的冷金属积聚到集
渣包,该处开10 mm×0.15 mm的排 气道,初始工艺模型示意图见图2。
5.3 设定收缩率(AppIy Shrinkage)
不同的材料有不同的收缩率,
为了补正体积收缩上的误差,必须 将参照模型放大。Pro/E针对这 个需要提供了一套设定收缩率的工 具,根据该件的材料及低压铸造特 征选用1%的收缩率。
5.4 建立分型面(Parting Surface) 建立分型面时首先定义各型芯分型面,最后定 义主分型面。一般都是先用增加(Add)一复制 (C叩y)一选择(select)一单独曲面(Indiv Su以) 复制模型外表面,以生成初步的分型面,再用 Modify—Add/Flat及Modify-Add/Extlllde来 建立破孔面,形成不带破孔的分型面,最后将 所有曲面合并(Merge)在一起。在所有分型面 都做完后,需要延拓到工件表面。该壳体铸件 模型共6个分型面,5个圆柱芯在复制完模型表 面后,均再做一个封闭旋转曲面合并后生成。 主分型面比较难做的是左侧法兰分型面的分割, 要用到曲线和侧像投影,然后 做一个平整面合并而成,见图8。
一种发动机铝缸体低压铸造方法

一种发动机铝缸体低压铸造方法在现代汽车工业中,发动机的性能和可靠性至关重要。
而铝缸体作为发动机的重要组成部分,其制造工艺直接影响着发动机的质量和性能。
低压铸造作为一种先进的铸造方法,在发动机铝缸体的制造中具有显著的优势。
低压铸造是一种在压力作用下,使液态金属充填铸型并凝固成形的铸造方法。
与传统的重力铸造相比,低压铸造能够更好地控制金属液的流动和凝固过程,从而获得组织致密、性能优良的铸件。
在进行发动机铝缸体低压铸造之前,需要进行一系列的准备工作。
首先是模具的设计和制造。
模具的设计要充分考虑铝缸体的结构特点和铸造工艺的要求,确保能够顺利地充填金属液并且便于脱模。
模具的材料通常选用耐高温、高强度的合金钢,以保证在铸造过程中的稳定性和耐用性。
然后是原材料的准备。
用于制造发动机铝缸体的铝合金通常需要具备良好的力学性能、耐热性能和耐腐蚀性。
常见的铝合金有 A356、A380 等。
在熔炼铝合金时,要严格控制熔炼温度、时间以及化学成分,以保证合金的质量。
接下来是低压铸造设备的调试。
低压铸造设备主要包括保温炉、升液管、加压系统和控制系统等。
在铸造前,需要对这些设备进行仔细的调试,确保其工作正常,能够准确地控制压力、温度和时间等参数。
当一切准备就绪后,就可以开始进行低压铸造过程。
首先,将熔炼好的铝合金液倒入保温炉中,并将模具预热到一定的温度。
然后,通过加压系统向保温炉内施加一定的压力,使铝合金液沿着升液管上升,充满模具型腔。
在充填过程中,要控制好压力的大小和上升速度,以保证金属液平稳、均匀地充填型腔,避免出现卷气、夹渣等缺陷。
当型腔充满后,保持一定的压力一段时间,使铸件在压力下凝固。
这有助于细化晶粒,提高铸件的组织致密性和力学性能。
凝固完成后,逐渐降低压力,使升液管内的金属液回流到保温炉中。
最后,打开模具,取出铸件。
取出的铸件需要进行清理、去除浇冒口和飞边毛刺等后续处理。
为了进一步提高铸件的性能,还可能需要进行热处理,如固溶处理和时效处理等。
最新《低压铸造法的指导手册 》
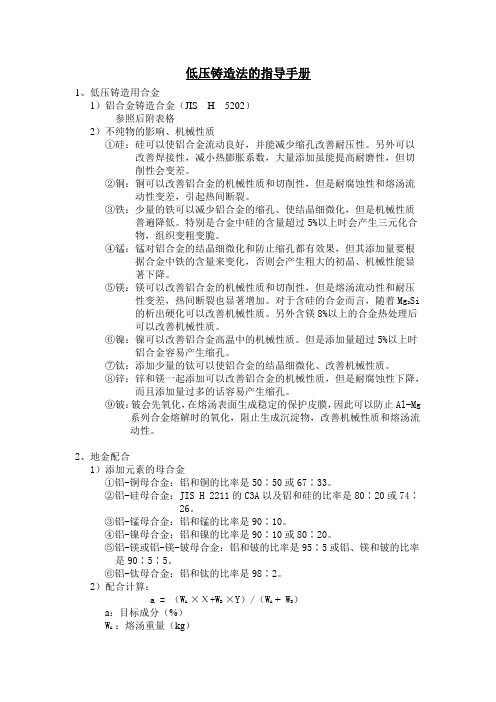
低压铸造法的指导手册1、低压铸造用合金1)铝合金铸造合金(JIS H 5202)参照后附表格2)不纯物的影响、机械性质①硅:硅可以使铝合金流动良好,并能减少缩孔改善耐压性。
另外可以改善焊接性,减小热膨胀系数,大量添加虽能提高耐磨性,但切削性会变差。
②铜:铜可以改善铝合金的机械性质和切削性,但是耐腐蚀性和熔汤流动性变差,引起热间断裂。
③铁:少量的铁可以减少铝合金的缩孔、使结晶细微化,但是机械性质普遍降低。
特别是合金中硅的含量超过5%以上时会产生三元化合物,组织变粗变脆。
④锰:锰对铝合金的结晶细微化和防止缩孔都有效果,但其添加量要根据合金中铁的含量来变化,否则会产生粗大的初晶、机械性能显著下降。
⑤镁:镁可以改善铝合金的机械性质和切削性,但是熔汤流动性和耐压性变差,热间断裂也显著增加。
对于含硅的合金而言,随着Mg2Si 的析出硬化可以改善机械性质。
另外含镁8%以上的合金热处理后可以改善机械性质。
⑥镍:镍可以改善铝合金高温中的机械性质。
但是添加量超过5%以上时铝合金容易产生缩孔。
⑦钛:添加少量的钛可以使铝合金的结晶细微化、改善机械性质。
⑧锌:锌和镁一起添加可以改善铝合金的机械性质,但是耐腐蚀性下降,而且添加量过多的话容易产生缩孔。
⑨铍:铍会先氧化,在熔汤表面生成稳定的保护皮膜,因此可以防止Al-Mg系列合金熔解时的氧化,阻止生成沉淀物,改善机械性质和熔汤流动性。
2、地金配合1)添加元素的母合金①铝-铜母合金:铝和铜的比率是50∶50或67∶33。
②铝-硅母合金:JIS H 2211的C3A以及铝和硅的比率是80∶20或74∶26。
③铝-锰母合金:铝和锰的比率是90∶10。
④铝-镍母合金:铝和镍的比率是90∶10或80∶20。
⑤铝-镁或铝-镁-铍母合金:铝和铍的比率是95∶5或铝、镁和铍的比率是90∶5∶5。
⑥铝-钛母合金:铝和钛的比率是98∶2。
2)配合计算:a = (WA ×Χ+WB×Y)/(WA+ WB)a:目标成分(%)W A :熔汤重量(kg)Χ:熔汤重量的成分(%):添加地金重量(kg)WBY:添加地金的成分(%)3、熔解作业1)熔解方法熔解时最需要注意的是气体吸收和氧化。
低压铸造机设计
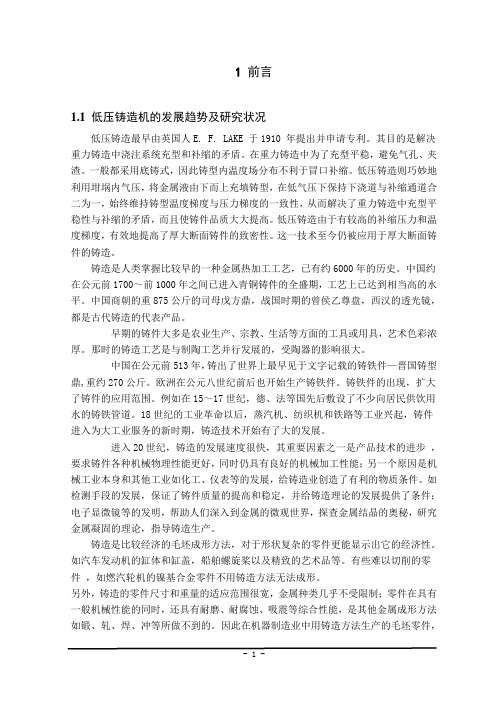
1前言1.1 低压铸造机的发展趋势及研究状况低压铸造最早由英国人E. F. LAKE 于1910 年提出并申请专利。
其目的是解决重力铸造中浇注系统充型和补缩的矛盾。
在重力铸造中为了充型平稳,避免气孔、夹渣。
一般都采用底铸式,因此铸型内温度场分布不利于冒口补缩。
低压铸造则巧妙地利用坩埚内气压,将金属液由下而上充填铸型,在低气压下保持下浇道与补缩通道合二为一,始终维持铸型温度梯度与压力梯度的一致性,从而解决了重力铸造中充型平稳性与补缩的矛盾,而且使铸件品质大大提高。
低压铸造由于有较高的补缩压力和温度梯度,有效地提高了厚大断面铸件的致密性。
这一技术至今仍被应用于厚大断面铸件的铸造。
铸造是人类掌握比较早的一种金属热加工工艺,已有约6000年的历史。
中国约在公元前1700~前1000年之间已进入青铜铸件的全盛期,工艺上已达到相当高的水平。
中国商朝的重875公斤的司母戊方鼎,战国时期的曾侯乙尊盘,西汉的透光镜,都是古代铸造的代表产品。
早期的铸件大多是农业生产、宗教、生活等方面的工具或用具,艺术色彩浓厚。
那时的铸造工艺是与制陶工艺并行发展的,受陶器的影响很大。
中国在公元前513年,铸出了世界上最早见于文字记载的铸铁件—晋国铸型鼎,重约270公斤。
欧洲在公元八世纪前后也开始生产铸铁件。
铸铁件的出现,扩大了铸件的应用范围。
例如在15~17世纪,德、法等国先后敷设了不少向居民供饮用水的铸铁管道。
18世纪的工业革命以后,蒸汽机、纺织机和铁路等工业兴起,铸件进入为大工业服务的新时期,铸造技术开始有了大的发展。
进入20世纪,铸造的发展速度很快,其重要因素之一是产品技术的进步,要求铸件各种机械物理性能更好,同时仍具有良好的机械加工性能;另一个原因是机械工业本身和其他工业如化工、仪表等的发展,给铸造业创造了有利的物质条件。
如检测手段的发展,保证了铸件质量的提高和稳定,并给铸造理论的发展提供了条件;电子显微镜等的发明,帮助人们深入到金属的微观世界,探查金属结晶的奥秘,研究金属凝固的理论,指导铸造生产。
ú

轮减速技 术,实现机械 手 3 6 0 。旋转 ,从
而 实现 了 “ 一 机 双 台 ” , 实 现 低 压 机 台 物 流 自动 化 。 ( 2 )机械 手采用气 动抱臂 、抱 臂液 压 马达 旋转 、整体 旋转 使用 减速 机 齿轮 减 速技 术 ,且 机械 手各 动作 使用 可编 程 序 控 制 技 术 , 动 作 控 制 稳 定 可 靠 , 使 得 低压铸造 机的流转 工艺更合 理。 ( 3 )设备操作 简单,一个 作业员操 作两台低压铸造机成为可能。 3 . 技 术 成 果 及应 用 前 景 铝 合 金 车 轮 低 压 铸 造 物 流 自动 化 技 标 均 达 到 设 计 要 求 , 车 轮 的 产 量 提 高 了 8 . 3 % ,能源消耗 降低 了 5 0 % ,废 品率 降低 了0 . 5 % 。机械 手运 行稳 定、性 能可 靠, 投 资 成 本 低 ,在 自动 化 改 造 中 具 有 较 好 的生产 应用 价值和 市场 推 广价 值,为 企 业 自动化技术改造提供 了方法和途径 。 参 考文 献 : [ 1 ]王建 军 . 搬 运 机 械 手仿 真 设 计 和 制作 [ J ] .机 械 设 计 与 制 造 , 2 0 1 2( 0 9 ) [ 2 ]王 战 中等 .自动 上 下 料 机 械 手 运 动 学分析及 仿真 [ J ] . 机械 设计 与制造 ,
Ac a d e m i c
学术
1 . 技 术 方 案 技术开发前公司铝合金车轮生产 中, 低压铸造机 台上操作员工的动作:车轮脱 模后 ,用料叉将车轮翻转,检 查车轮 的浇 口和 A面 情 况 ,合 格 后 进 行 水 箱 冷 却 ,冷 却 完 成 后进 行去 毛 边 、打 工 号 、 下 转 ,进 入X 光检查 工艺 。在生产 中,一个员工看 管一个机台,不仅 劳动强度大 ,生产效率 低 ,还易造 成人为磕碰伤 。因此,公司决 定 自主 研 发机 械 手 自动 化 技 术 ,通 过 购 置 机 械 手 并 进 行 改 造 ,使 其 能适 用 公 司 现 有 生 产 设 备 ; 并进 行相 关 工 艺调 整 ,解 决 现 有 物 流 瓶颈 , 降低 产 品 的报 废 率 。 1 . 1总体 方 案 设 计 利用 机械 手 自动 化技 术 ,开 发 出低 压 机 台 机 械 手 自动 化 设 备 。 这 是 用 于 辅 助 生 产 的 自动 化 设 备 , 通 过 电 气 控 制 系 统 作 用 于 机 械 、 气 动 、 液 压 等 部 件 完 成 预 设 动 作 。机 械 手 的 抱 臂 控 制 使 用 气 动 系 统 来 实 现 , 抱 臂 的 旋 转 使 用 液 压 旋 转 马达 ,因此 抱 臂 的控制 位置 准确 可靠 , 运行稳定 :机械手整体 的旋转为 3 6 0 。, 实 现 一 台 机 械 手 控 制 两 台 低 压 铸 造 机 的 功 能,其 结构 为减 速 机齿轮 减 速设 计, 旋转稳定可靠 。 该机 械手 有两 种 工作模 式 :手动 和 自动 。手动模式用于开始使用时的归零、 各 部 件 位 置 的 调 整 、 出 现 异 常 时 的 处 理 等 , 自动 模 式为 正常 生产 时使 用 。该机 械 手应 用 了气 动 、液 压技 术 ,电气 使用 可 编 程 控 制 技 术 与 气 动 、 液 动 技 术 相 结 合 , 提 高 了机 械 手 的 自动 化 程 度 。 1 . 2机 械 手 设 计 方 案 能 保 证 机 械 手 的 抱 臂 能 抓 取 两 个 低 压 铸 造 机 的车轮 ,继 而实 现 “一机双 台” 的 目标 。 ( 2 )气 动 抱 臂 系 统 : 气 动 抱 臂 系 统 实现 了准 确无 误 的抓 取 车轮 ,且气 动件 对 现 场 的 环境 几 乎 没有 影 响 。 ( 3 )抱臂液压 马达旋转 系统 :为 实 现车轮 的旋转 ,采用液压 马达 实现 1 8 0 。 旋转 ,便 于作业 员检 查、车 轮 的放 下、 车轮的抓取 。 ( 4 )机 械 手 的配 套 设 备 :冷 却 水 箱 、 车 轮 升 降 滚 道 、 自检 台 。 ( 5 )机 械 手 采 用 气 动 、 液 压 技 术 、 减 速机 齿轮 减速 技术 ,这些 零部 件 易采 用可编程序控制 ,使其重复精度很高 。 车 轮 的修 毛 边 和 自检 ; ⑦毛 坯升 降滚道:机 械手配套 设备, 将 完成修 毛边 的 车轮 下降至 低压 铸造 机 平 台 下方 ,将 车 轮 送 入 主 滚 道 ; 由于 机 械 手 成 功 实 现 了 3 6 0 。旋转 , 使 “ 一 机 双 台 ” 成 为 现 实 。 机 械 手 其 它 的动 作是 与现有 的低 压铸 造机 的生 产节 拍 相 衔 接 , 达 到 毛 坯 流 转 自 动 化 , 继 而 将原 来作业 员的动 作 由机 械 手来 完成 , 提 高 工 作 效 率 , 降低 劳 动 强 度 。 设 备 安 装完 成后 由原 来 的一人 一台机 变 为一人 操作两台机 。 2 . 关 键 技 术 及 创 新 点 ( 1 )机 械 手 整 体 旋 转 使 用 减 速 机 齿
低压铸造作业指导书(模版)

三、安全操作要点1•铝水槽、溶化工具喷涂料并烘干备用。
2.下料比例:回炉料不得超过30%1•当班前穿戴好劳保用品。
2•下料时,先系好安全带,将炉料沿炉壁轻轻的放下,防止铝不溅起伤人。
3•在熔化过程中,要注意炉子运行情况,发现炉体振动异常、炉体发出异味、闪光等异常时,立即停电,并通知设备维修人员查找原因。
4•每天清理环境卫生,每周清理炉膛,经常检查坩埚的使用情、调整与设定:二、作业规范1.准备:1.1铝水槽烘烤喷涂料烘干备用;所用熔化工具涂料并烘干,备用;1.2检查液化气管道压力、气瓶内含气量、满瓶液化气数量;2•熔化:2.1送气打开喷火器,开始烘炉;2.2逐步把铝锭放入坩埚内融化,回炉料不得超过本次熔铝量的30%;2.3熔炼完成,把铝液上面漂浮的铝渣用漏勺清理一次;2.4把铝液加温到750,做好倒入保温炉的准备。
3•设备保养与维护:遇到生产中停电大于4小时,应将铝水舀出,盖上炉盖,让其缓慢冷却。
炉口每天至少清理1次炉渣,炉膛至少每周清理一次炉渣。
停产3天以上,必须烘炉4小时,方可生产。
4.下班前作好交接记录。
设备名称熔铝炉更改日期设备名称 精炼机 更改日期、调整与设定: 二、作业规范 三、安全操作要点1.上班穿戴好劳保用品,下班清扫环境卫生。
2•除气机要进行提前预热。
3•除气时,要注意防止铝水溅出伤人。
4•不要用潮湿的工具操作,以免铝水溅出伤人。
5•不能使用潮湿的熔剂、变质剂。
6.清理坩埚熔渣时必须用铁铲沿着坩埚壁轻轻地铲掉熔渣。
1•准备工作: 1.1工具涂料:所有熔炼工具都应涂料,并烘干备用。
若涂料脱落,应把旧涂料清理干净后,再涂新料,烘干使用。
1.2将秤量好的精炼剂放在保温炉台面上烘烤备用。
1.3把保温炉上盖卸掉,使用行车把上盖垂直缓慢吊起,防止碰伤陶瓷升液管,然后放置在炉盖保护架上;把保温炉输送到熔铝炉浇口位置,翻转熔铝炉,把铝液倒入到保温炉内; 2•铝液的精炼:铝水温度730°C 至750°C 时进行精炼处理。
低压铸造机设计范文
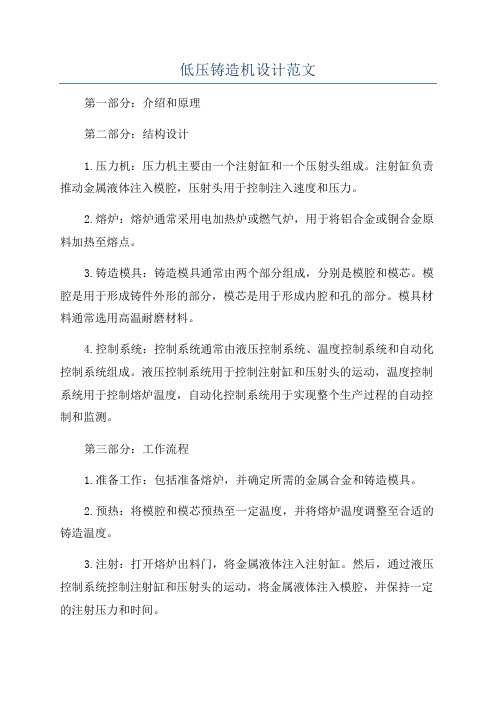
低压铸造机设计范文第一部分:介绍和原理第二部分:结构设计1.压力机:压力机主要由一个注射缸和一个压射头组成。
注射缸负责推动金属液体注入模腔,压射头用于控制注入速度和压力。
2.熔炉:熔炉通常采用电加热炉或燃气炉,用于将铝合金或铜合金原料加热至熔点。
3.铸造模具:铸造模具通常由两个部分组成,分别是模腔和模芯。
模腔是用于形成铸件外形的部分,模芯是用于形成内腔和孔的部分。
模具材料通常选用高温耐磨材料。
4.控制系统:控制系统通常由液压控制系统、温度控制系统和自动化控制系统组成。
液压控制系统用于控制注射缸和压射头的运动,温度控制系统用于控制熔炉温度,自动化控制系统用于实现整个生产过程的自动控制和监测。
第三部分:工作流程1.准备工作:包括准备熔炉,并确定所需的金属合金和铸造模具。
2.预热:将模腔和模芯预热至一定温度,并将熔炉温度调整至合适的铸造温度。
3.注射:打开熔炉出料门,将金属液体注入注射缸。
然后,通过液压控制系统控制注射缸和压射头的运动,将金属液体注入模腔,并保持一定的注射压力和时间。
4.凝固和冷却:在注射过程中,金属液体渐渐凝固并形成铸件。
此时,通过冷却系统控制模具的温度,加快铸件的凝固和冷却过程。
5.开模和取出:当铸件凝固完全后,通过液压控制系统打开模具,取出成品铸件。
第四部分:优点和应用1.铸件质量高:低压铸造机通过较低的压力和较长的注射时间,使金属液体在模腔中充型和凝固过程更加均匀,从而获得高质量的铸件。
2.生产效率高:低压铸造机的工作速度较快,每小时可生产大量铸件。
3.成本低:低压铸造机的设备成本较低,同时生产过程中的能耗也相对较低。
- 1、下载文档前请自行甄别文档内容的完整性,平台不提供额外的编辑、内容补充、找答案等附加服务。
- 2、"仅部分预览"的文档,不可在线预览部分如存在完整性等问题,可反馈申请退款(可完整预览的文档不适用该条件!)。
- 3、如文档侵犯您的权益,请联系客服反馈,我们会尽快为您处理(人工客服工作时间:9:00-18:30)。
低压铸造机技术案书一、序言1.1设计目标低压铸造机是铝合金低压铸造的通用设备,可广泛应用于汽车、摩托车、纺织机械与航空航天等工业中铝合金铸件的生产。
本技术案是为了采用低压铸造机完成本公司铝合金模具浇铸使用而设计。
1.2设计原则安全,稳定,可靠,有效1.3设计依据和参考标准主要依据了统计局、商务部、发改委、国务院发展研究中心、中国海关总署、低压铸造机行业相关协会、国外相关刊物的基础信息以及低压铸造机行业专业研究单位等公布和提供的大量资料。
1.4适用围本案适用于本公司所有使用铝合金铸件的低压灌浇注产品。
二、需求分析2.1技术现状我国低压铸造机技术经过几十年研究与发展,在结构,原理,功能上基本接近进口机水平,在国汽车缸盖生厂商已经得到用户认可,但国产机同进口机相比在外观、铸造工艺、机械精度、自动控制及算法等精细面还是有所差距。
本公司产品在经过一至五代液压铸造机的基础上采用电控系统来完成铝合金模型的铸造过程,有待于进一步试验和使用验证。
2.2需求针对公司目前产品现状,需完成采用电控设计的低压铸造机来实现铝合金浇铸的过程,达到降低生产成本,提高铸件质量和满足生产安全,提高生产率,提升自动化程度的目的需求。
三、硬件系统技术案设计低压铸造机原理是将熔融的金属液加入密闭的保温炉,用液面加压系统给密封的保温炉充一定的干燥的压缩空气,使保温炉的金属液通过升液管缓慢注入金属模型腔,在压力作用下结晶成形,再经过自动开模并取件,完成低压铸造工艺过程。
3.1整体系统设计系统架构主要由数据采集处理系统和通信系统构成。
采集处理系统在主控系统采用PLC的基础上主要由以下几部分:炉温控制系统,液面加压系统,开合模及顶出系统,模具冷却系统,型腔温度及液面检测系统,人机界面,操控面板,工艺参数采集系统和报警系统组成。
其中,型腔液面检测与液面加压系统共同构成闭合回路。
主控通过工业以太网交换机与服务器/客户端建立联系,进行数据通讯。
图1 主系统搭建框图上位机系统采用B/S架构,即浏览器和服务器结构。
它是随着Internet技术的兴起,对C/S结构的一种变化或者改进的结构。
在这种结构下,用户工作界面是通过WWW浏览器来实现,极少部分事务逻辑在前端(Browser)实现,但是主要事务逻辑在服务器端(Server)实现。
B/S结构最大的优点就是可以在任地进行操作而不用安装任专门的软件。
只要有一台能上网的电脑就能使用,客户端零维护。
系统的扩展性非常容易,只要能上网,再由系统管理员分配一个用户名和密码,就可以使用了。
远程通信系统即PLC和服务器工作站之间的通讯采用工业以太网进行通信,这样可以很便的和其它系统进行集成。
本设计系统暂时不对上位机和远程通讯进行设计,但在相关系统中预留相关接口,以备后续工作中需要使用。
3.1.1案设计本案在10路子系统的基础上搭建低压铸造机的实现过程,通过采集相关的电压电流信号、温度和压力信号等输入主控器中,然后进行相关算法的计算和数据分析处理后进行输出,从而实现多路子系统同时可控,共同完成整体系统操作,实现铝合金铸造过程。
图2 系统流程图3.1.2设计特点本设计在液压铸造的基础上采用变频器通过电机来控制合分模的过程,实现电力环节的节能环保;炉温,型腔,浇口实现温度灵敏控制,通过主控器及时处理和反馈,达到精度控制的要求;实时报警系统可以及时检测系统故障,保证生产安全有序进行;上位机控制可以及时观测到系统整体运行状态,保证作业的顺利进行,并利于告警和故障信息的及时处理;整机系统配合完整,达到生产任务需求。
3.2分系统设计分系统搭建主要由以下各个环节构成,各个子系统的稳定运行保证了整体系统的功能实现,从而满足系统稳定可靠安全有效的运行。
3.2.1 PLC主控系统主控系统由几个小系统搭建完成,包括输入采集系统、数据处理系统、实时显示系统、操作系统和数据输出系统。
除了实现对各个子系统进行监控外,还需要采集设备工作状态的信息,故障信息以及生产工艺参数,以提供给服务器进行工艺分析及优化使用。
本系统主要完成模拟物理量的采集,将其送入控制器中,在控制器中进行数据处理和分析,然后将有关模拟量分别同步进行显示和输出;通过以太网交换机上传至服务器,进行数据储存和调用,在浏览器可以直接进行系统观测和设定,直观便的对系统进行全程监控和处理。
3.2.2 炉温控制系统本子系统主要完成保温炉温度的检测,通过硅碳棒辐射加热,利用热电偶采集,将炉温度信号送入主控制器进行处理,同时在已经设定的温度值基础上进行比较,通过误差控制借助温控仪和调功器来调整实时温度,达到满足系统温度稳定运行的要求。
图3 炉温控制流程3.2.3 型腔温度及液面控制系统本子系统主要完成型腔温度和位置的检测,将型腔温度信号送入主控制器,在已经设定的温度值基础上进行比较,通过误差控制借助电加热棒或模温机来调整实时温度,达到系统温度运行的需求;同时使用超声波传感器来检测液面位置,使模具在压力值下保持位置稳定,通过压控仪器或主控系统来控制压力维持液面高度,以利于更好的铸模。
图4 型腔温度控制流程图5 型腔液面控制流程3.2.4浇口温度控制系统为了防止铝液在浇注口温度过低结晶,从而影响浇注质量,需要对浇注口的温度进行检测并控制。
本子系统主要通过热电偶完成浇口温度的检测,将浇口温度信号送入主控制器,在已经设定的温度值基础上进行比较,通过误差控制借助温控仪调节电加热棒或硅碳棒来调整实时温度,达到系统温度运行的需求。
图6 浇口控制流程3.2.5变频合分模控制系统本子系统主要完成对分合模臂的控制,通过变频器驱动电机正反转来实现分合木模臂的推进和送出,并通过频率的控制来进行速度和行程的调节,其控制过程主要在变频器实现完成。
图7 变频控制流程3.2.6液面夹压力控制系统本子系统主要完成对型腔模具位置信号的检测,通过控制液面夹压力值来控制液体位置,气压源压力经过滤减压阀后达到稳定值,实现过程是将压力信号作为控制信号,位置信号为输出信号,通过闭环实现对位置的控制。
本控制可集成于主控系统来实现。
图8 液面夹压力控制流程3.2.7模具冷却系统本子系统主要完成采用热电偶采集后的模具温度控制,通过与设定温度值进行比较,当温度值高于设定值则进行降温,采用水冷或者风冷的式,当温度值低于设定值时候,采用电加热棒进行加热,主要目的是在于降温,使模型迅速冷却。
图9 冷却控制流程3.2.8人机界面在设备工作现场设置人机界面,用于显示设备工作状态参数以及工艺参数。
人机界面主要用于对工作模式的选择(自动/手动),系统参数的获取(压强,温度,电压,电流等),并显示相关参数趋势曲线,实时监测系统运行状态,为系统运行运行进行保障。
3.2.9操作面板操作面板主要用来控制电源的通断,电机的启停,以及各个机械臂的推进和缩出,同时进行各个位置量的检测输出等,如电源指示,合分模到位信号等。
在现场适用于对设备进行调试以及人工操作。
3.2.10报警系统本部分报警主要对各个子系统温度、电压电流、压强等实时物理量超过阈值的及时报警,实现系统响应及时,处理故障有效的检测作用,保证系统在无误差的系统环境下安全可靠运行。
四、软件系统技术案设计在以上硬件系统架构的基础上,进行软件系统设计。
软件部分主要包括以下部分:温控软件设计(主要包括炉温控制,型腔温度控制,浇口温度控制),功率(电压电流)软件设计,位置信号软件设计,压力控制系统软件设计,人机界面和报警软件设计。
其中,温控部分包括保温炉温度控制,浇口温度控制,型腔温度控制;功率(电压电流)控制主要针对电机控制;压强控制主要指液面压力控制;人机界面包括各显示和操作软件设计;报警主要针对故障报警系统设计。
本部分可外协完成,通过系统集成实现整机系统的安全运作。
4.1温控系统软件设计温控软件设计主要包三大部分,上述已经介绍,其基本控制原理相同,主要流程框图可参考同一设计。
主要系统检测量为实时温度值,本温度值通过温度传感器或热电偶取得。
图10 温控程序流程图炉温控制系统中,调节器主要是调功器和硅碳棒;型腔温度控制系统中,主要指的是可控硅和电加热棒或模温机;浇口温度也可采用可控硅和电加热棒;此流程在模具冷却中也可能用到,如果模具温度低于设定值,也可能需要电加热器进行加热处理。
注:此处调节器调节过程涉及到下节中介绍的功率调节,功率调节可视为其一部分流程控制,为便于理解,将功率调节式单独列成一节,功率调节不仅仅在温度调节中使用,在电机控制环节也采用。
4.2功率系统软件设计功率系统主要指的是对电流电压或功率的控制,通过移相调节或频率改变占空比等来调节输出电流电压功率值,此处也指单独的电流调节或电压调节。
功率调节涉及到以下几个环节:炉温控制中调功器用以调节硅碳棒加热功率,型腔温度调节过控制环节使得电加热设备或模温机改变功率大小,浇口温度控制系统中电加热功率的大小,电机通过变频器控制合分模速度和位置。
本节主要介绍变频器控制电机进行合分模样过程。
变频器控制电机运行是一个串级调速过程,环为速度控制,外环为位置控制,通过调节变频器的频率来改变占空比,从而输出电压或电流值,进而控制速度大小,实现位置到达的过程。
在此过程中由于电压电流发生变化引起功率变动,因而归于功率调节。
由于负载变化引起的功率变化可以实现节约电能的过程,实现功率因数最大化,达到控制负载,节约能量的效果。
可以通过控制电机的正反转实现分模和合模过程。
图11 系统控制流程图图12 系统程序流程图变频器部通过设定的频率来调节电流和电压值,根据输出来控制电机的正反转以及速度和位置,在运行过程中不断的进行速度和位置校正,最终稳定停止。
4.3位置系统软件设计位置控制系统主要通过测量装置完成对最终停止或动态变化量的取值,然后送入控制器进行数据处理后送入执行结构进行输出,最终达到系统稳定要求。
图12 系统流程图图13 系统程序流程图系统中执行结构包括型腔液面控制的执行器,当液面压力低于预定值时,需要通过加压使得铝液上升至型腔某位置,此时可以通过控制器发出指令或通过压控相关器件发出指令,能够发出指令的控制单元构成执行机构。
4.4压力系统软件设计压力系统与型腔液面构成闭环控制熊,单纯压力系统为开环控制,通过检测液面液位来增加或减少压力,使得铝液结晶在型腔,达到铸造模型的要求,开环流程图如下:图14 系统程序流程图4.5人机界面在设备工作现场设置人机界面,用于显示设备工作状态参数以及工艺参数。
人机界面主要实现两大功能,一是完成对工作式和模式的控制,二是对物理量采集后计算结果的输出,包括数字量输出和图形输出。
此部分流程图相对复杂,在此不作具体绘制。
4.6报警系统报警主要是对设定值与实际值比较后的结果输出进行处理,流程图相对简单,即输出结果与设定结果比较,如果输出值大于设定值则报警系统启动,可以通过指示灯或报警器提示。