包钢烧结工艺技术进步
烧结自动配料技术的开发与应用

烧结自动配料技术的开发与应用
郝建军;屈文艺;张骁
【期刊名称】《包钢科技》
【年(卷),期】2002(028)003
【摘要】通过各方面协同工作,采用各种技术手段,使配料秤、电气设备、计算机实现一体化,形成自动配料系统.自动配料系统的实现,进一步满足烧结生产的工艺要求,达到了稳定烧结矿化学成分,改善烧结矿质量的目的.
【总页数】8页(P49-56)
【作者】郝建军;屈文艺;张骁
【作者单位】包钢(集团)公司炼铁厂,内蒙古,包头,014010;包钢(集团)公司炼铁厂,内蒙古,包头,014010;包钢(集团)公司炼铁厂,内蒙古,包头,014010
【正文语种】中文
【中图分类】TF325.1
【相关文献】
1.自动配料控制新技术在烧结工艺的应用及推广 [J], 方满义
2.烧结热返矿定量给料自动控制技术的开发与应用 [J], 屈文艺;倪秀英;周洪连
3.烧结机配料工序的自动化控制技术 [J], 谭广芸
4.烧结配料自动控制技术的研究与应用 [J], 张均宾;初云祥;卢军波;李宪成;岳佩科
5.烧结法生产氧化铝自动配料技术探讨 [J], 薛文忠;杨权平;罗国平;樊文贞;刘淑清因版权原因,仅展示原文概要,查看原文内容请购买。
烧结行业发展趋势总结

烧结行业发展趋势总结烧结行业发展趋势总结烧结技术是一种重要的冶金制造技术,广泛应用于钢铁、有色金属、建材等行业。
烧结行业在我国经济和工业发展中起着至关重要的作用。
近年来,随着各种新技术的不断涌现,烧结行业发生了许多变化,如何把握烧结行业的发展趋势,对于烧结企业对未来的发展是非常必要的。
本文将从材料、工艺、环保、自动化及数字化等方面来总结烧结行业的发展趋势。
一、材料烧结行业的重要特点之一是材料的使用,因此材料的发展趋势具有非常重要的意义。
未来烧结企业将更加注重材料的多元化和高端化。
这种趋势主要体现在以下几个方面:1. 多元化的原料——烧结原料将更加广泛,以满足未来各行业的需求。
比如在钢铁工业中,烧结原料将更多地涉及废钢、废铁、废渣等。
2. 高端化的合金——烧结合金将更多地涉及多种合金元素混合的高端合金,以广泛满足高精度的行业需求。
3. 新型材料的应用——烧结技术已经开始涉及到新的材料领域,如陶瓷材料、复合材料等,未来,在这些新型材料的应用方面,烧结技术将会有更多的发展。
二、工艺工艺是烧结行业中的重要环节,随着科技的进步和市场要求的提高,工艺的发展也逐渐成为了烧结行业关注的重点。
未来,烧结企业将以更高的标准要求自己,更高效的工艺将是烧结企业不断追求的目标。
主要体现在以下几方面:1. 烧结过程的精细化——未来,烧结企业将会更加注重烧结工艺的精细化,并加强烧结过程中的监控与控制,以保证产品的质量和性能。
2. 绿色的烧结工艺——未来,烧结企业将会更加注重绿色工艺的开发与应用,减少废气、废水、废渣等污染物的排放,减少环境污染,提高企业的可持续性发展。
3. 节能的烧结工艺——未来,烧结企业将会更加注重节能技术的应用,采用高效的能源回收设备,以降低生产成本,提高经济效益。
三、环保随着环保意识的不断提高,烧结企业未来将更加注重环保问题的解决。
环保问题的解决一方面可以促进企业的可持续性发展,另一方面可以增强企业的社会责任感。
钢铁行业如何实现工艺技术革新
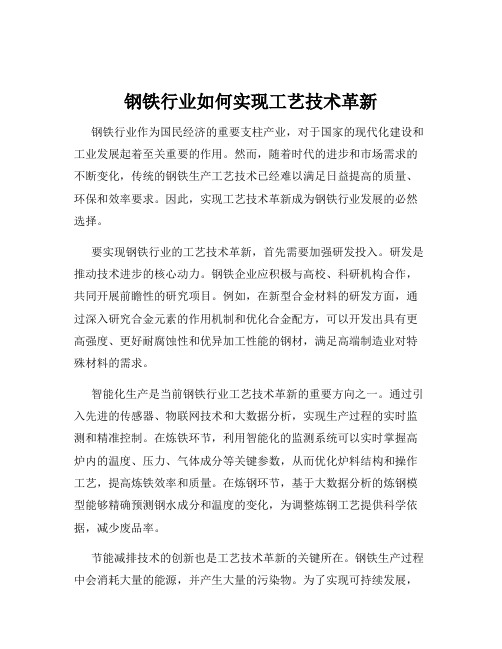
钢铁行业如何实现工艺技术革新钢铁行业作为国民经济的重要支柱产业,对于国家的现代化建设和工业发展起着至关重要的作用。
然而,随着时代的进步和市场需求的不断变化,传统的钢铁生产工艺技术已经难以满足日益提高的质量、环保和效率要求。
因此,实现工艺技术革新成为钢铁行业发展的必然选择。
要实现钢铁行业的工艺技术革新,首先需要加强研发投入。
研发是推动技术进步的核心动力。
钢铁企业应积极与高校、科研机构合作,共同开展前瞻性的研究项目。
例如,在新型合金材料的研发方面,通过深入研究合金元素的作用机制和优化合金配方,可以开发出具有更高强度、更好耐腐蚀性和优异加工性能的钢材,满足高端制造业对特殊材料的需求。
智能化生产是当前钢铁行业工艺技术革新的重要方向之一。
通过引入先进的传感器、物联网技术和大数据分析,实现生产过程的实时监测和精准控制。
在炼铁环节,利用智能化的监测系统可以实时掌握高炉内的温度、压力、气体成分等关键参数,从而优化炉料结构和操作工艺,提高炼铁效率和质量。
在炼钢环节,基于大数据分析的炼钢模型能够精确预测钢水成分和温度的变化,为调整炼钢工艺提供科学依据,减少废品率。
节能减排技术的创新也是工艺技术革新的关键所在。
钢铁生产过程中会消耗大量的能源,并产生大量的污染物。
为了实现可持续发展,必须加大对节能减排技术的研发和应用。
例如,推广干熄焦技术,不仅可以回收焦炭显热用于发电,还能减少湿法熄焦带来的环境污染。
开发和应用新型的余热回收利用系统,将生产过程中产生的余热转化为蒸汽或电能,提高能源利用效率。
同时,采用先进的脱硫、脱硝和除尘技术,降低废气排放,减少对大气环境的影响。
工艺装备的升级换代对于提高生产效率和产品质量具有重要意义。
例如,采用大型化、高效化的炼铁高炉和炼钢转炉,可以提高生产规模和生产效率。
引进高精度的轧钢设备,能够生产出尺寸精度更高、表面质量更好的钢材产品。
此外,不断更新和改进生产线上的自动化控制设备,提高生产过程的稳定性和可靠性。
钢铁烧结工艺

钢铁烧结工艺钢铁烧结工艺是一种重要的冶金工艺,用于将金属粉末通过高温烧结过程使其聚结成块状材料。
这种工艺在钢铁行业中应用广泛,具有高效、节能、环保等优点。
本文将详细介绍钢铁烧结工艺的基本原理、应用领域以及发展趋势。
一、钢铁烧结工艺的基本原理钢铁烧结工艺是利用金属粉末的高温烧结性质,通过加热和冷却过程使其粒子间发生扩散和结合,从而形成块状材料。
具体步骤包括原料制备、成型、烧结和冷却四个过程。
原料制备是钢铁烧结工艺的第一步,主要包括金属粉末的选择和配比。
金属粉末通常由铁粉、合金粉等组成,根据不同要求可以添加一定比例的添加剂。
配比的合理与否直接影响到烧结后材料的性能。
成型是将原料粉末按一定的形状和尺寸进行压制,使其具有一定的强度和形状稳定性。
常用的成型方式有压制、注塑、挤压等。
成型后的材料称为绿坯。
烧结是将成型后的绿坯置于高温环境中,使其发生热变形和结合。
烧结的温度通常在金属材料的熔点以下,但高于金属的晶界扩散温度。
在烧结过程中,金属粉末颗粒间会发生扩散,同时表面粒子经过短时间的高温接触,使其发生部分熔化,从而实现颗粒间的结合。
冷却是烧结后的最后一个过程,将已烧结的块状材料冷却至室温,使其具有一定的强度和形状稳定性。
冷却过程中,要注意避免过快或过慢的冷却速度,以免引起材料内部应力过大或结构不稳定。
钢铁烧结工艺广泛应用于钢铁行业的各个环节,包括铁矿石的烧结、高炉炉料的制备、铁精粉的制备等。
在铁矿石的烧结过程中,通过烧结工艺可以将低品位的铁矿石转化为高品位的烧结矿。
这样不仅提高了铁矿石的利用率,还减少了矿石资源的消耗,对环境保护也起到了积极的作用。
高炉炉料的制备是钢铁生产过程中的重要环节。
通过烧结工艺,可以将粉状的铁精粉和其他辅助材料烧结成块状的高炉炉料。
这样可以提高炉料的流动性和透气性,进一步提高高炉的冶炼效率和产量。
铁精粉的制备是钢铁烧结工艺的另一个重要应用领域。
通过烧结工艺,可以将铁精粉和其他添加剂烧结成块状的铁精矿。
冶金行业如何通过技术创新实现降本增效

冶金行业如何通过技术创新实现降本增效在当今竞争激烈的市场环境中,降本增效已成为冶金行业持续发展的关键。
随着原材料价格的波动、能源成本的上升以及环保要求的日益严格,冶金企业面临着巨大的压力。
技术创新作为推动行业进步的核心力量,为冶金行业实现降本增效提供了重要的途径。
一、优化生产工艺生产工艺的优化是冶金行业降本增效的基础。
通过采用先进的冶炼技术和流程,可以显著提高生产效率,降低能耗和原材料消耗。
例如,在炼铁过程中,推广应用高炉喷吹煤粉技术,能够减少焦炭的使用量,降低生产成本。
同时,优化高炉的操作参数,如提高风温、富氧率等,可以提高高炉的利用系数,增加铁水产量。
在炼钢环节,采用转炉顶底复合吹炼技术,可以改善熔池的搅拌效果,提高钢水的质量和收得率。
此外,应用连铸技术代替模铸,可以减少铸坯的切头切尾损失,提高金属收得率,降低生产成本。
二、智能化控制随着信息技术的快速发展,智能化控制在冶金行业中的应用越来越广泛。
通过建立智能化的生产控制系统,可以实现生产过程的精准控制,提高生产效率,降低废品率。
利用传感器、大数据分析和人工智能技术,对生产过程中的温度、压力、成分等参数进行实时监测和分析,及时调整生产操作,确保生产过程的稳定性和一致性。
例如,在轧钢过程中,通过智能化的轧制控制系统,可以精确控制轧件的尺寸和形状,减少废品的产生。
此外,智能化的设备维护管理系统可以实现对设备运行状态的实时监测和故障诊断,提前预测设备的故障隐患,进行预防性维护,降低设备的维修成本,提高设备的利用率。
三、能源管理与回收利用能源成本在冶金行业的生产成本中占据较大比重,因此加强能源管理和回收利用是实现降本增效的重要措施。
采用先进的能源管理系统,对能源的消耗进行实时监测和分析,找出能源浪费的环节,采取针对性的节能措施。
例如,对风机、水泵等设备进行变频调速改造,根据生产负荷自动调整设备的运行速度,降低电能消耗。
同时,加强余热、余压的回收利用。
烧结生产工艺改进思考
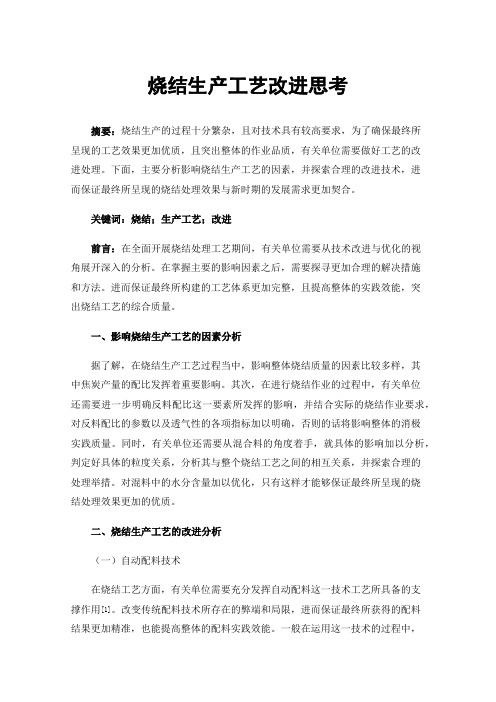
烧结生产工艺改进思考摘要:烧结生产的过程十分繁杂,且对技术具有较高要求,为了确保最终所呈现的工艺效果更加优质,且突出整体的作业品质,有关单位需要做好工艺的改进处理。
下面,主要分析影响烧结生产工艺的因素,并探索合理的改进技术,进而保证最终所呈现的烧结处理效果与新时期的发展需求更加契合。
关键词:烧结;生产工艺;改进前言:在全面开展烧结处理工艺期间,有关单位需要从技术改进与优化的视角展开深入的分析。
在掌握主要的影响因素之后,需要探寻更加合理的解决措施和方法。
进而保证最终所构建的工艺体系更加完整,且提高整体的实践效能,突出烧结工艺的综合质量。
一、影响烧结生产工艺的因素分析据了解,在烧结生产工艺过程当中,影响整体烧结质量的因素比较多样,其中焦炭产量的配比发挥着重要影响。
其次,在进行烧结作业的过程中,有关单位还需要进一步明确反料配比这一要素所发挥的影响,并结合实际的烧结作业要求,对反料配比的参数以及透气性的各项指标加以明确,否则的话将影响整体的消极实践质量。
同时,有关单位还需要从混合料的角度着手,就具体的影响加以分析,判定好具体的粒度关系,分析其与整个烧结工艺之间的相互关系,并探索合理的处理举措。
对混料中的水分含量加以优化,只有这样才能够保证最终所呈现的烧结处理效果更加的优质。
二、烧结生产工艺的改进分析(一)自动配料技术在烧结工艺方面,有关单位需要充分发挥自动配料这一技术工艺所具备的支撑作用[1]。
改变传统配料技术所存在的弊端和局限,进而保证最终所获得的配料结果更加精准,也能提高整体的配料实践效能。
一般在运用这一技术的过程中,需要根据具体的烧结工艺作业要求,备好一定数量的配合材料。
然后发挥先进技术设备的支撑作用,对其进行科学的配料处理。
在整个实践的过程中能够有效降低在人工方面的成本投入,也能够合理控制业为人工操作失误而造成的不良风险。
相较于以往的技术手段,该工艺所具备的时效性特征尤为显著,比较受到烧结工艺生产实践过程的推崇和应用,展现出独特的作用。
炼钢短流程工艺国内外现状及发展趋势

炼钢短流程工艺国内外现状及发展趋势一、引言炼钢短流程工艺是一种高效、节能、环保的炼钢技术,近年来在钢铁行业得到了越来越广泛的应用。
本文将从国内外炼钢短流程工艺的现状和发展趋势两方面展开探讨,旨在全面了解炼钢短流程工艺在钢铁生产中的地位和未来发展的方向。
二、炼钢短流程工艺的定义炼钢短流程工艺,顾名思义,即指采用高效、快捷的生产流程,通过电弧炉、转炉等设备,将废钢、废铁等原料快速熔化,然后经过连铸、轧制等工艺,最终生产出优质的钢材。
相比传统的炼钢工艺,短流程工艺具有炼钢周期短、能耗低、环境友好等优点。
三、国内外炼钢短流程工艺的现状1. 国内炼钢短流程工艺的现状从国内炼钢短流程工艺的发展历程来看,经过不断的技术创新和装备升级,我国在炼钢短流程领域已取得了长足的进步。
目前,国内许多钢铁企业已经采用了炼钢短流程工艺,如宝钢、武钢等,他们在炼钢短流程工艺上的投入和研究也取得了一定的成果。
2. 国外炼钢短流程工艺的现状与国内相比,国外在炼钢短流程工艺领域的发展历史较长。
欧美等发达国家早在20世纪80年代就开始大力推广炼钢短流程工艺,目前已建立健全了一套成熟的炼钢短流程工艺体系。
日本、韩国等亚洲国家也在炼钢短流程工艺方面取得了一些重要的进展。
四、炼钢短流程工艺的发展趋势1. 技术创新是推动炼钢短流程工艺发展的关键随着科技的不断进步,炼钢短流程工艺也在不断进行技术创新。
新型的炼钢设备、智能化的生产管理系统等技术的应用,将进一步提高炼钢效率,降低成本,推动炼钢短流程工艺向更高效、更环保的方向发展。
2. 绿色炼钢是未来发展的主流趋势随着环保意识的增强和国际环保标准的不断提高,绿色炼钢必将成为未来炼钢工艺发展的主流趋势。
炼钢短流程工艺作为一种清洁生产技术,将在未来得到更广泛的应用,成为钢铁行业的主要发展方向。
五、结语炼钢短流程工艺作为一种新兴的炼钢技术,已经在国内外得到了广泛的关注和应用。
通过对国内外炼钢短流程工艺的现状和发展趋势的分析,我们可以清晰地看到炼钢短流程工艺在钢铁行业的重要地位以及未来发展的方向。
包钢炼铁厂一烧热风烧结技术应用

分物理 热 , 可大 幅度节 约 固体燃 料 ; 烧结 料层 的温 ② 度分 布均匀 , 克服 了上 层 热量不 足 ; 由于 固体燃 料 ③
用量减 少 , 烧结 气 氛得 到 改 善 ; 由于抽 人 热 风 , ④ 料
关 键 词 : 结机 ; 风 烧 结 ; 用 烧 热 应
中圈分类 号:FP 5 T1 A.
文献标识码: B
文章 编号 :09 4 820 )6 08— 3 10 —53 (06 0 —00 0
Appia i n fHo lc to o t—b a tAi l trn tNo. o k S o f ls r S n e i g a 1W r h p o Io r n—m a i g Pln fBa tu S e lCo p. k n a to o o t e r
产 以来一直偏 低 , 导致 烧结矿 产量偏 低 , 多年来 虽然 为提 高产量 改善质 量也 做过一 些 改造 , 见效 不大 。 但 现在 的生产 水平 已不能 满足 高炉 提系数 对烧结 矿产 量 的需求 。为 了解 决 这 一 矛 盾 , 高一 烧 车 间烧 结 提 机 利用 系数 势在 必行 。20 03年 , 风 烧结 技 术在 二 热 烧车 间得到成 功 运 用 , 为一 烧 车 间进 行 热风 烧结 技
风量 8 2 3h 2 5m / 。西 侧放散 管道 内动压 2 a静压 0 8P 、
8 a 风温 18℃ 、 OP 、 0 风速 6 6m s管道 直径 15m, . / , . 风
收 稿 日期 : 0 .8 1 2 60 . 0 2
作者简 介: 邱金厚 (91 男 , 17 一) 辽宁省营 口市人 , 烧结工程师, 现任包钢炼铁厂一烧车间主任。
冶金领域新突破创新工艺提升铁水纯度的成功案例分析

冶金领域新突破创新工艺提升铁水纯度的成功案例分析在冶金领域,提升铁水纯度一直是一个重要的课题。
随着科学技术的不断发展,新的创新工艺不断涌现,为冶金工业带来了新的突破。
本文将分析几个成功的案例,说明创新工艺对提升铁水纯度的重要性。
1. 案例一:高温还原炉技术的应用高温还原炉技术是一种新型的冶炼方法,它采用高温还原反应,将在铁矿石中的杂质物质还原为易挥发的物质,通过蒸汽的带走,使得铁水中的杂质含量大幅降低。
该技术的应用大大提高了铁水的纯度,同时减少了废气排放量,具有环保和经济效益。
各大矿山企业纷纷引进高温还原炉技术,并取得了良好的效果。
2. 案例二:连铸技术的改进连铸技术是一种铸造铁水的方法,通过连续的铸造过程,可以使得铁水中的杂质更好地分离,并且有效地提高了铁水的纯度。
近年来,随着连铸技术的不断改进和创新,如真空连铸、电磁搅拌等技术的应用,铁水的纯度得到了进一步提升。
这些创新工艺不仅提高了产品质量和生产效率,还减少了能源消耗和材料浪费。
3. 案例三:氧气顶吹转炉工艺的引入氧气顶吹转炉工艺是一种将高纯氧气从炉顶喷入炉腔的冶炼方式,通过氧气的顶吹,可以有效地氧化铁水中的杂质,使其在反应过程中被吹出炉外。
此技术的引入显著提高了铁水的纯度,并且降低了操作成本和对环境的污染。
氧气顶吹转炉工艺已经广泛应用于钢铁行业,取得了令人瞩目的成果。
4. 案例四:高效过滤技术的运用高效过滤技术是一种通过过滤方法去除铁水中的杂质的技术。
传统的过滤方法效果有限,容易堵塞。
而新型的高效过滤技术通过使用特殊的过滤材料和改进的过滤设备,可以有效地提高过滤效率和耐堵塞性能,大幅度降低了铁水中的杂质含量,提高了铁水的纯度。
这项技术的应用对冶金工业产生了积极的影响,并被广泛推广应用。
综上所述,冶金领域的新突破与创新工艺在提升铁水纯度方面起到了至关重要的作用。
高温还原炉技术、连铸技术的改进、氧气顶吹转炉工艺的引入以及高效过滤技术的运用等都为提高铁水纯度带来了巨大的贡献。
中冶长天:多项硬核技术助力钢铁行业绿色低碳发展

中冶长天:多项硬核技术助力钢铁行业绿色低碳发展中冶长天先后开发了厚料层烧结技术、烧结机综合密封技术、烟气及余热烟气耦合循环、烟气深度净化技术等多项工艺装备新技术、低碳环保新技术硬核技术,助力烧结工序绿色低碳发展。
1工艺装备新技术1.1厚料层烧结技术中冶长天开发了偏析布料、强力混匀、柔性传动、超宽台车和综合控制专家系统等核心技术,发明了负压吸附式风箱端部密封技术,研制的高效节能型厚料层大型化系列烧结机,提高了料层透气性,强化了优质铁酸钙低温生成,扩大了原料的适应性,降低了固体燃耗,提高了烧结生产效率和产品质量;同时,可将烧结机漏风率控制在20%以内,大幅减少烧结电耗。
采用该技术的宝钢湛江钢铁1号550m2烧结机的料层总厚达950mm,宝钢本部二烧结600m2烧结机料层总厚达1,000mm。
同时,宝钢湛江烧结机投产时的漏风率实测值为17.9%,远低于传统密封技术的漏风率,居国际领先水平。
1.2双级冷却烧结技术该技术是采用竖式冷却原理,把原烧结机往环冷机布料的布料溜槽设计为烧结矿预冷却装置,预冷却后的烧结矿再进入环冷机进行二次冷却,以此形成烧结双级冷却系统。
其中预冷却环节采用小风慢冷冷却方式,可有效提高冷却后热风的温度,形成高品质热风(>45(ΓC)。
采用双级冷却技术,可提高余热回收效率,降低返矿率,减少环冷机冷却风量,完全实现冷却系统的“零排放”,具有很好的余热效益及环境效益。
1.3分层供热富氢烧结技术及装备随着厚料层烧结技术的发展,以偏析布料实现均热烧结的局限性日趋明显。
同时,以提供同量热值作基准比较,富氢气体燃料比固体燃料在减少碳排放方面具有更大优势。
基于上述原因,中冶长天开发了分层供热富氢烧结技术及装备,开发了天然气一氧气耦合高效喷加技术及成套关键装备,开发了低碳料层燃烧带厚度与速度测控系列关键技术。
在中天钢铁550m2烧结机富氢燃气料面喷加强化烧结工程中,颠覆传统固相燃料烧结模式,首创气固两相协同烧结新模式,通过采用少量富氢气体燃料替代大量碳系固体燃料的“以氢代碳”手段,在保证安全性、经济性和高质量指标的同时,将烧结工序固体燃料消耗量减少T7%,以单台550m2烧结机为例,折合每年减排C02约4.4万吨。
钢铁冶炼中的生产过程优化技术

钢铁冶炼中的生产过程优化技术钢铁是现代工业的重要原材料之一,其应用范围广泛,包括建筑、制造业、交通运输等众多领域。
然而,钢铁生产的过程却被认为是一种能源和环境负担较重的工业活动。
因此,优化钢铁冶炼生产过程,减少资源的浪费和环境的污染,已经成为了当今工业界的一个重要课题。
本文将从生产过程优化技术的角度,探讨如何提高钢铁冶炼的效率和节能减排。
一、高炉冶炼过程优化技术高炉是钢铁冶炼的核心设备,其冶炼效果和能耗水平是决定钢铁生产成本的关键因素之一。
在高炉冶炼过程中,常常存在煤气的浪费和二氧化碳的排放等问题。
如何减少煤气的浪费和降低二氧化碳的排放,成为了高炉优化的关键。
高炉的优化技术主要包括以下几个方面:1、煤气回收技术煤气回收技术是指利用高炉煤气中所含的热能和成分,生产煤气能和化学产品等,并将其中的一部分热能返还给高炉进行冶炼。
这种技术的优点在于可减少煤气的浪费和能源的消耗,同时还能增加煤气的利用效率。
2、CO2循环利用技术钢铁冶炼过程中,批量产生大量的二氧化碳。
如果这些二氧化碳没有得到充分利用,将成为一种环境污染。
因此,CO2循环利用技术是一个重要的解决方案。
通过为高炉注入液态二氧化碳,降低炉膛内的氧分压,从而减少砖石合金的消耗,减少炉渣质量和提高钢铁产出率。
二、烧结优化技术烧结作为钢铁冶炼的一道关键工序,其燃烧效率和能源消耗水平也对钢铁生产成本有着重要的影响。
针对烧结的优化技术主要包括以下两个方面:1、加强燃烧力度技术在烧结过程中,燃烧力度越强,能耗就越低,生产效率也就越高。
因此,加强燃烧力度技术是一种重要的烧结优化手段。
它可以通过调整烧结机、喷煤量和喷嘴位置等方面来增加燃烧强度,从而提高烧结燃烧效率和能源利用效率。
2、系统优化技术系统优化技术是指通过优化烧结压力过程、加强烧结进程控制等方式,提高烧结机的燃烧效率和生产效率。
此外,通过优化烧结热交换和回收系统等配套技术,也可以降低能耗和减少环境污染。
包钢二烧车间提高烧结机技术指标实践

收 稿 日期 :0 2O .6 2 0 .22 作 者 简 介 : 天 勇 ( 9 6 ) , 西 应 县 人 , 结 工 艺 工 程 师 , 9 7年 毕 业 于 中 央 党 校 经 济 管 理 专 业 , 任 包 钢 烁 铁 厂 二 烧 杨 16 一男 山 烧 19 现
车 问 副 主任 。
中 图分 类 号 : F 4 , T 0 64 文 献 标 识 码 : B 文 章 编 号 :0 9—5 3 (0 2 0 —0 2 —0 10 4 820 )3 0 3 3
1 前 言
包钢烧 结 厂二烧 车 间于 19 98年 l 0月将 原有 4台 7 m 烧结 机改 造 为 4台 9 m 机 上冷 却 烧 结 机 ( 冷 52 02 烧 比 1 1。改 造后 , 烧 车间 的产量 、 :) 二 质量 、 利用 系 数等
中压 蒸 汽 。 实践 证 明 , 方法 蒸 汽利 用 率低 , 该 热量 损 失大, ? 料 温度 提 高 不 明显 。另外 , 于点 火位 置 昆合 由
靠后 , 造 成 有效 烧 结 面 积 的减 少 和 混 合 料 温 度 的 也
进 行预 热 , 但效 果 不是 十分理 想 。 为 提 高 烧 结 混 合 料 温 度 进 而 提 高 烧 结 工 艺 指
8l 8l
2月
3月
0 3 8 09 6 03 7 06 8
O2 7 OO 7
7 .4 46
7 4l 5. 8 2 5l 9 4 24
4月
5月
4 3
4 4
8 6 7 2. 3
8 6 l 4l 8 2 3 l 3
6月
7月
6 5 6 7
5 5
8 .8 14
浅谈烧结节能降耗的技术途径和措施
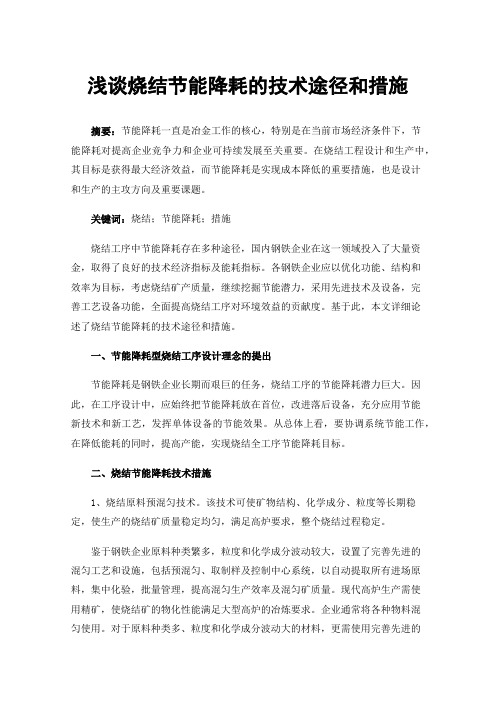
浅谈烧结节能降耗的技术途径和措施摘要:节能降耗一直是冶金工作的核心,特别是在当前市场经济条件下,节能降耗对提高企业竞争力和企业可持续发展至关重要。
在烧结工程设计和生产中,其目标是获得最大经济效益,而节能降耗是实现成本降低的重要措施,也是设计和生产的主攻方向及重要课题。
关键词:烧结;节能降耗;措施烧结工序中节能降耗存在多种途径,国内钢铁企业在这一领域投入了大量资金,取得了良好的技术经济指标及能耗指标。
各钢铁企业应以优化功能、结构和效率为目标,考虑烧结矿产质量,继续挖掘节能潜力,采用先进技术及设备,完善工艺设备功能,全面提高烧结工序对环境效益的贡献度。
基于此,本文详细论述了烧结节能降耗的技术途径和措施。
一、节能降耗型烧结工序设计理念的提出节能降耗是钢铁企业长期而艰巨的任务,烧结工序的节能降耗潜力巨大。
因此,在工序设计中,应始终把节能降耗放在首位,改进落后设备,充分应用节能新技术和新工艺,发挥单体设备的节能效果。
从总体上看,要协调系统节能工作,在降低能耗的同时,提高产能,实现烧结全工序节能降耗目标。
二、烧结节能降耗技术措施1、烧结原料预混匀技术。
该技术可使矿物结构、化学成分、粒度等长期稳定,使生产的烧结矿质量稳定均匀,满足高炉要求,整个烧结过程稳定。
鉴于钢铁企业原料种类繁多,粒度和化学成分波动较大,设置了完善先进的混匀工艺和设施,包括预混匀、取制样及控制中心系统,以自动提取所有进场原料,集中化验,批量管理,提高混匀生产效率及混匀矿质量。
现代高炉生产需使用精矿,使烧结矿的物化性能满足大型高炉的冶炼要求。
企业通常将各种物料混匀使用。
对于原料种类多、粒度和化学成分波动大的材料,更需使用完善先进的混匀工艺和设施作为技术支持,通过自动制样系统,对所有进场原料进行自动取料及集中化验,并根据不同品种、成分和定量进行堆放,实现原料的批次管理。
2、超厚料层烧结自动蓄热技术。
在烧结工艺中,蓄热量会随着料层厚度的不断增加而逐渐积累,当厚度达到180~220mm时,蓄热率为35~45%,厚度为400mm,蓄热率可达65%。
包钢自熔性复合烧结矿试验研究
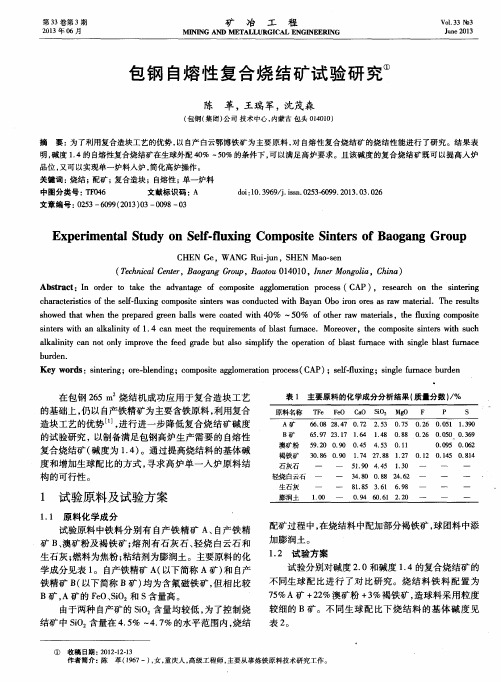
( T e c h n i c a l C e n t e r , B a o g a n g G r o u p, B a o t o u 0 1 4 0 1 0 , / n n e r Mo n g o l i a ,C h i n a ) A b s t r a c t :I n o r d e r t o t a k e t h e a d v a n t a g e o f c o mp o s i t e a g g l o m e r a t i o n p r o c e s s( C A P) ,r e s e a r c h o n t h e s i n t e r i n g
第3 3 卷第 3 期 2 0 1 3年 0 6月
矿 冶 工 程
MI NI NG AND M ETALLURGI CAL ENGI NEERI NG
V0 1 . 3 3№3
J u n e 2 01 3
包 钢 自熔 性 复 合烧 结矿 试 验 研 究①
陈 革, 王瑞 军 , 沈茂森
品位 , 又可 以实现单一炉料入炉 , 简化高炉操作 。 关键 词 : 烧结 ;配矿 ; 复合造块 ;自熔性 ; 单一炉料
中图分类号 : T F 0 4 6 文献标识码 : A d o i : 1 0 . 3 9 6 9 / j . i s s n . 0 2 5 3 - 6 0 9 9 . 2 0 1 3 . 0 3 . 0 2 6 文章 编号 : 0 2 5 3— 6 0 9 9 ( 2 0 l 3 ) 0 3— 0 0 9 8— 0 3
s h o we d t h a t w h e n t h e p r e p a r e d g r e e n b a i l s w e r e c o a t e d w i t h 4 0 % 一5 0 % o f o t h e r r a w ma t e ia r l s ,t h e l f u x i n g c o mp o s i t e s i n t e r s w i t h a n a l k a l i n i t y o f 1 . 4 c a n me e t he t r e q u i r e me n t s o f b l a s t f u r n a c e . Mo r e o v e r ,t h e c o mp o s i t e s i n t e r s wi t h s u c h a l k li a n i t y c a n n o t o n l y i mp r o v e t h e f e e d ra g d e b u t a l s o s i mp l i f y t h e o p e r a t i o n o f b l a s t f u r n a c e wi t h s i n g l e b l a s t f u r n a c e b u r d e n .
烧结新技术及其发展

烧结新技术及其发展作者:项江辉单位:安徽工业大学冶金与资源学院冶金095班学号:099014274摘要:高炉强化冶炼对精矿提出了更高的要求,可以用“高、稳、熟、小、匀、净”概括。
为实现这些基本要求为强化冶炼创造条件,采用烧结新工艺新技术以提高精矿物理化学性质,可以为高炉强化冶炼提高扎实的基础。
本文仅以提高包钢炼铁厂和首钢炼铁厂为例,粗略探讨该厂采用的烧结新工艺及其对提高精料水平强化高炉冶炼的影响及效果。
关键词:自动配科技术,强力造球技术,新式生石灰消化器,厚料层烧结技术,柔性密封新技术,热风烧结技术,烧结配加强化剂,喷洒氯化钙技术,球团矿主要新技术。
一、原理:1.1强化冶炼基本原理相对高炉常规冶炼而言,采用一切先进技术和工艺方法,缩短冶炼周期,提高高炉炼铁生产率及其综合经济效益的冶炼工艺。
高炉生产率常用高炉利用系数来表示。
式中i为冶炼强度,t/(m3?d);k为焦比,t/t。
提高冶炼强度与降低焦比是提高利用系数,强化高炉冶炼的两个主要方向。
凡能提高冶炼强度,降低焦比的技术措施和方法,都属于高炉强化冶炼的范畴。
诸如改善炉料结构,采用高炉精料,高压操作,高炉喷吹燃料,高风温以及富氧鼓风、综合鼓风、加湿鼓风和脱湿鼓风等都是高炉强化冶炼的重要内容。
此外,加强管理,如加强设备维护,降低休风(见休风与复风)率、慢风(见慢风操作)率和漏风率等,使高炉常处于全风操作状态,以增加生铁产量,降低单位生铁能耗,也是高炉强化冶炼不可忽视的内容。
但是也不能简单地得出高炉生产率与冶炼强度成正比的结论。
因为焦比在相当程度上还与冶炼强度有关,即k=f(i)。
精料是高炉强化冶炼的物质基础,强化高炉必须把精料放在首位。
精料的涵义是要求供给高炉的原料不但质量好,而且数量足。
其内容可用“高、稳、熟、小、匀、净”概括。
“高”——铁矿石的品位高,还原性高,焦炭中固定炭高,熔剂中氧化钙高,各种原料的冷态、热态机械强度高。
“稳”——各种原料的化学成分稳定,波动小。
烧结工序节能降耗的技术措施
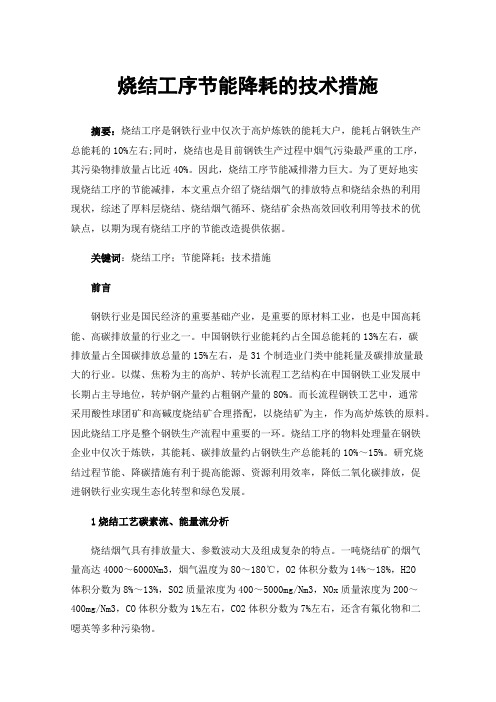
烧结工序节能降耗的技术措施摘要:烧结工序是钢铁行业中仅次于高炉炼铁的能耗大户,能耗占钢铁生产总能耗的10%左右;同时,烧结也是目前钢铁生产过程中烟气污染最严重的工序,其污染物排放量占比近40%。
因此,烧结工序节能减排潜力巨大。
为了更好地实现烧结工序的节能减排,本文重点介绍了烧结烟气的排放特点和烧结余热的利用现状,综述了厚料层烧结、烧结烟气循环、烧结矿余热高效回收利用等技术的优缺点,以期为现有烧结工序的节能改造提供依据。
关键词:烧结工序;节能降耗;技术措施前言钢铁行业是国民经济的重要基础产业,是重要的原材料工业,也是中国高耗能、高碳排放量的行业之一。
中国钢铁行业能耗约占全国总能耗的13%左右,碳排放量占全国碳排放总量的15%左右,是31个制造业门类中能耗量及碳排放量最大的行业。
以煤、焦粉为主的高炉、转炉长流程工艺结构在中国钢铁工业发展中长期占主导地位,转炉钢产量约占粗钢产量的80%。
而长流程钢铁工艺中,通常采用酸性球团矿和高碱度烧结矿合理搭配,以烧结矿为主,作为高炉炼铁的原料。
因此烧结工序是整个钢铁生产流程中重要的一环。
烧结工序的物料处理量在钢铁企业中仅次于炼铁,其能耗、碳排放量约占钢铁生产总能耗的10%~15%。
研究烧结过程节能、降碳措施有利于提高能源、资源利用效率,降低二氧化碳排放,促进钢铁行业实现生态化转型和绿色发展。
1烧结工艺碳素流、能量流分析烧结烟气具有排放量大、参数波动大及组成复杂的特点。
一吨烧结矿的烟气量高达4000~6000Nm3,烟气温度为80~180℃,O2体积分数为14%~18%,H2O体积分数为8%~13%,SO2质量浓度为400~5000mg/Nm3,NOx质量浓度为200~400mg/Nm3,CO体积分数为1%左右,CO2体积分数为7%左右,还含有氟化物和二噁英等多种污染物。
1.1烧结工艺主要功能烧结的生产过程是把精矿粉、燃料(焦粉、无烟煤)和熔剂(石灰石、白云石、生石灰)按一定比例配料混匀后,在烧结机上点火燃烧,利用燃料和铁氧化物氧化反应放出热量,使混合料局部熔化,并将散粒颗粒黏结成块状烧结矿,作为炼铁原料。
烧结工艺的发展

烧结工艺的发展烧结方法在冶金生产中的应用,起初是为了处理矿山、冶金、化工厂的废弃物(如富矿粉、高炉炉尘、轧钢皮、均热炉渣、硫酸渣等)以便回收利用。
随着钢铁工业的快速发展,矿石的开采量和矿粉的生成量亦大大增加。
据估计,每生产1t生铁需1.7~1.9t铁矿石,若是贫矿,需要的铁矿石则更多。
另外,由于长期的开采和消耗,能直接用来冶炼的富矿愈来愈少,人们不得不大量开采贫矿(含铁25%~30%)。
但贫矿直接入炉冶炼是佷不经济的,所以必须经过选矿处理。
选矿后的精矿粉,在含铁品位上是提高了,但其粒度不符合高炉冶炼要求。
因此,对开采出来的矿粉(0~8mm)和精矿粉都必须经过造块后方可用于冶炼。
我国铁矿资源丰富,但贫矿较多,约占80%以上,因此,冶炼前大都需经破碎、筛分、选矿和造块处理过程。
烧结生产的历史已有一个多世纪。
它起源于资本主义发展较早的英国、瑞典和德国。
大约在1870年前后,这些国家就开始使用烧结锅。
美国在1892年也出现烧结锅,1905年美国曾用大型烧结锅处理高炉炉尘。
世界钢铁工业上第一台带式烧结机于1910年在美国投入生产。
烧结机的面积为8.325m2(1.07m ×7.78m),当时处理高炉炉尘,每天生产烧结矿140t。
它的出现,引起烧结生产的重大革新,从此带式烧结机得到了广泛的应用。
但在1952年以前,由于钢铁工业发展缓慢,天然富矿入炉率还占很大比例,所以烧结生产的发展也不快。
烧结工业的迅速发展是近几十年的事。
日本烧结工艺完善,设备先进,技术可靠,自动化水平高,是世界上烧结技术发展最快的国家。
单机平均烧结面积达218 m2 ,400 m2以上的烧结机11台。
法国单机烧结机面积154 m2,400 m2以上的烧结机4台。
英国单机烧结机面积165 m2。
德国和意大利分别有3台和2台400 m2以上的烧结机。
菲律宾和澳大利亚分别有1台450 m2和420 m2烧结机.卢森堡和韩国各有1台400m2的烧结机。
烧结球团技术总结

先进烧结球团技术总结宋路路(内蒙古科技大学)摘要文章介绍了近年来各大钢厂的先进的烧结球团生产技术,同时提出了今后烧结球团系统进一步改进的措施。
为其它钢厂烧结球团技术的改进提出建设性的意见。
这些技术成就举世瞩目,使我国烧结、球团业得到了巨大的发展。
同时也应看到,我国烧结、球团业还有不少难题需要我们去解决、去创新,才能达到一个全新局面。
关键词烧结球团技术进步总结Summary on New Development ofSintering PelletSong Lulu(Inner Mongolia University of science&Technology )Abstract This paper introduces the major steel mills in recent years, the advanced production technology of sintered pellets, and sintered pellets were put forward measures to further improve the system. These technical achievements have attracted worldwide attention, so that our sintered pellet industry has been tremendous development. It should also be noted that China sintering, pellets industry there are many problems to solve we need to innovate in order to achieve a completely new situation.Key Words sintering Pellet Technology development Summary1 前言近年来各大钢厂实现了快速发展,生产规模显著扩大,原有的烧结球团工艺已经不能满足日益发展的需要。
包钢500万吨烧结脱硫塔火灾事故学习心得

包钢500万吨烧结脱硫塔火灾事故学习心得《包钢 500 万吨烧结脱硫塔火灾事故学习心得》小朋友们,你们知道吗?最近有一个地方发生了一件很可怕的事情,就是包钢 500 万吨烧结脱硫塔着火啦!这可真是个大事故。
我听老师讲了这件事,心里特别害怕。
我就想啊,要是没有消防员叔叔们勇敢地去灭火,那得造成多大的损失呀!我们平时在学校里做游戏、学习,多开心。
可是那些在工厂工作的叔叔阿姨们,他们要特别小心,不然就会像这次一样出危险。
通过这件事,我明白了,做事情一定要认真,不能马虎。
就像我们写作业,要是不认真,就会写错字,做错题。
以后我做什么都会认认真真的,不让错误发生。
作文二:《包钢 500 万吨烧结脱硫塔火灾事故学习心得》今天老师给我们讲了包钢的一个大事故,500 万吨烧结脱硫塔着火啦!我一听,眼睛都瞪圆了。
老师说,这个事故让很多东西都受到了损害。
我就在想,火可真是个坏东西,一不小心就会闯大祸。
我们小朋友不能玩火,在家里不能随便动打火机和火柴。
在外面看到有火的地方也要离得远远的。
我希望以后不要再有这样可怕的事故发生了,大家都能平平安安的。
作文三:《包钢 500 万吨烧结脱硫塔火灾事故学习心得》小朋友们,我要跟你们说一说包钢的那次火灾事故。
500 万吨烧结脱硫塔着火,听起来就很吓人。
我知道了事故会带来很多不好的结果,比如工厂不能正常工作了,叔叔阿姨们会很担心。
这让我想到,我们在学校里跑闹的时候也可能会摔倒受伤。
所以我们要守规矩,不能随便乱跑。
我会记住这次事故,提醒自己要注意安全。
作文四:《包钢 500 万吨烧结脱硫塔火灾事故学习心得》你们听说包钢的火灾事故了吗?500 万吨烧结脱硫塔着火啦!我听了以后心里可难受了。
我觉得那些在工厂工作的叔叔阿姨们一定要小心再小心。
就像我们过马路要左右看一样,他们工作也要注意各种危险。
从这件事我也明白了,我们要学会保护自己,不让自己受到伤害。
作文五:《包钢 500 万吨烧结脱硫塔火灾事故学习心得》小伙伴们,包钢发生了一件很严重的事,500 万吨烧结脱硫塔着火了。
- 1、下载文档前请自行甄别文档内容的完整性,平台不提供额外的编辑、内容补充、找答案等附加服务。
- 2、"仅部分预览"的文档,不可在线预览部分如存在完整性等问题,可反馈申请退款(可完整预览的文档不适用该条件!)。
- 3、如文档侵犯您的权益,请联系客服反馈,我们会尽快为您处理(人工客服工作时间:9:00-18:30)。
包钢烧结工艺技术进步尤学东杨永清段祥光(包钢(集团)公司炼铁厂,内蒙古包头014010)摘要:本文回顾了包钢烧结四十余年的发展历史,对包钢烧结产能规模扩大、工艺技术指标及质量指标的进步进行了全面阐述。
自1966年4月包钢烧结建成投产,烧结矿产量由年产24.65万吨提高到1468.98万吨,产能扩大59倍;烧结料层、烧结机作业率、烧结矿固体燃耗、工序能耗、转鼓强度、TFe品位等工艺技术质量指标均显著提升,为包钢钢铁双千万吨奠定了良好原料基础。
关键词:烧结;工艺;技术;质量Technical Progress of Sintering Process in Baotou SteelDUAN Xiang-guang(Iron-making Plant of Steel Union Co. Ltd. Of Baotou Steel (Group) Corp., Baotou 014010,Nei Monggol, China )Abstract: This paper reviews over 40-years development history of Sintering Plant of Baotou Steel. Since Sintering Plant of Baotou Steel was constructed and put into operation in April of 1966, its capacity has been expanded 59 times, and the quality indexes of process technology have been obviously promoted.1.前言1927年7月,我国地质学家丁道衡于内蒙古包头发现了以铁、稀土、铌为主的多元素共生矿床——白云鄂博矿。
新中国成立后,于1959年包钢1号高炉(1513m3)建成出铁,结束了“内蒙古手无寸铁的历史”。
在包钢炼铁几十年的发展过程中,先后经历了白云鄂博块矿,自熔性烧结矿(第一代烧结矿),高碱度、高碱度高氧化镁烧结矿(第二代烧结矿)的不同炉料结构冶炼。
通过包钢及国内科研院所广大采、选、烧、冶科研技术人员几十年的技术攻关和科研探索,历尽艰辛,基本攻克了“多、细、杂、贫”白云铁矿的选矿、细精矿的烧结(球团)及含K、Na、F 高的低熔点矿石的高炉冶炼等等技术难关。
特别是近十年来包钢高炉炼铁及铁前原料系统迅猛发展。
为了使包钢高炉炼铁指标进一步提高发展,赶超国内先进水平,就必须在精料上做文章。
对包钢烧结以往工艺技术进步的全面总结,必定会促进其今后的进一步提升,从而促进包钢高炉炼铁技术进步。
2.包钢烧结产能规模扩大最初的包钢烧结厂由前苏联国立有用矿物机械处理研究设计院设计。
院设计建设三个烧结车间共12台75m2烧结机,其中10台生产供高炉使用的烧结矿,两台生产供平炉使用的烧结矿。
后由于国内形势的变化,只建成了一个烧结车间,即现在的二烧车间。
原有四台苏联标准75m2烧结机,设计生产能力220万吨烧结矿,于1966年4-7月建成投产,到二十世纪九十年代达到年产300万吨烧结矿。
随着包钢生产的发展,四台75m2烧结机已经不能满足炼铁生产的需要,于1991年底和1995年9月先后建成两台180 m2烧结机(一烧车间)。
1998年二烧车间改造为(90+90)m2×4的机上冷却烧结机,烧结机总设计能力达到695万吨。
2004年底又新建一台265 m2烧结机(三烧车间),设计生产能力273万吨,烧结机总设计产能达到968万吨,烧结矿实际生产能力达到年产1000万吨以上。
随着包钢炼铁产能的进一步扩大,2006年又新建两台265 m2烧结机(四烧车间),设计生产能力550万吨,烧结机总设计产能达到1518万吨,2008年将一烧2#烧结机扩容至210 m2,目前烧结矿实际生产能力达到年产1500万吨以上。
按年产1000万吨生铁,矿比1674Kg/t,高炉返矿率17.5%,目前烧结矿产能可保证高炉烧结矿配比75%左右。
为包钢实现钢铁双千万吨和“十一五”期末实现销售收入和资产总值双百亿美元,奠定了良好的原料基础3.包钢烧结工艺技术指标进步到1986年原冶金工业部组织的包钢铁前技术攻关结束,通过提高烧结矿冷强度的技术攻关,改善烧结矿冶金性能试验攻关,包钢烧结“双强化”试验研究,高碱度烧结矿的试验研究与生产,高氧化镁烧结矿的试验研究与生产等一系列试验研究与技术攻关,包钢烧结技术质量指标显著改善。
至二十世纪八十年代末期,年产量由24.65万吨,提高到302.30万吨;烧结机利用系数由0.62t/m2.h,提高到1.31t/m2.h;烧结矿转鼓强度由76.88%,提高到83.55%(+5mm,原冶金部标准);烧结固体燃耗由182.30Kg/t,降至83.67Kg/t;同时烧结矿冶金性能也有了显著改善,促进了高炉冶炼指标的全面提升。
进入二十世纪九十年代后,伴随我国钢铁业的迅猛发展,包钢烧结借鉴国内外先进技术,各项指标显著提高。
以下就近二十年来包钢烧结技术进步简单总结。
3.1厚料层烧结以细精矿为主要原料条件和传统的烧结工艺是造成我国烧结工业落后的主要原因之一。
厚料层烧结是二十世纪七十年代烧结工艺的一个重大发展。
厚料层烧结不仅使热利用率提高,燃料消耗相应降低,而且因烧结过程自动蓄热量增加,高温保持时间延长,表层返矿量相对降低,减少了烧结过程不均匀带来的影响,使烧结矿的结构均匀,质量提高,成品率和转鼓提高,固体燃耗和烧结矿FeO降低。
料层厚度越高,烧结固体燃耗愈低。
我国主要钢铁企业烧结生产统计表明烧结料层每提高10 mm,燃耗可降低l~3 kg/t[1]。
但综合考虑烧结矿各项指标,烧结料层厚度宜控制在700~750 mm。
根据包钢四个烧结车间设备状况及实际生产情况,分别采取了提高台车挡板,降低底料厚度等不同措施,以提高烧结有效料层厚度。
截至2009年5月,除一烧车间1#烧结机料层630mm,其余所有烧结机料层提高到700mm。
另外,一烧车间底料由100mm降至80mm;二烧车间由80mm降至60mm;三烧车间80mm降至60mm;四烧车间100mm-80mm降至60mm-40mm。
3.2热风烧结技术应用多年以来,国内外对烧结余热的回收利用进行了大量的研究。
据日本某钢铁厂热平衡测试数据,烧结机的热收入中88%的热能由焦粉燃料提供,点火用烟气带入6% ,高炉瓦斯灰中的炭燃烧带入4%;热支出项目中,水分蒸发耗热占18.2% ,石灰石分解热占15.2% ,烧结矿显热占28.2%和废气显热占31.8%。
由此可见,烧结厂余热回收的重点应为烧结废(烟)气余热和烧结矿(产品)显热回收[2]。
50年代研究的热风烧结,可节约固体燃料20%~30% ,节约烧结总热量10%~13%热风烧结可使料层中温度分布较均匀,克服普通烧结上层温度不足、烧结矿强度低、粉末多,下层温度高、烧结矿FeO含量高的缺点,从而改善饶结矿的质量。
但是,热风烧结并没在生产中得到应用,主要原因是没有找到经济的热风风源及其利用技术[3]。
包钢根据各烧结车间实际情况分别采取了不同的热风烧结工艺,其中一烧、三烧和四烧采用无动力送风装备,二烧采用加压风机。
具体参数见下表:3.3小球烧结推广应用因为新型小球烧结法可以显著改善烧结料层的透气性,实现厚料层、高氧位、低温烧结操作制度,促进烧结矿中针状或柱状铁酸钙胶结相的生成。
因此,该技术所制得的烧结矿具有强度高、燃耗低、冶金性能好的特点,是深受高炉欢迎的优质烧结矿[4]。
早在1998年二烧车间改造时,包钢就与北京钢铁研究总院合作开发了“小球烧结”一系列新技术,以促进二烧车间提高烧结矿产质量,降低消耗。
其核心技术为:强化混合料制粒,混合料预热,偏析布料。
取得成功后,又推广到一烧车间的两台烧结机。
在后期建设的三烧和四烧车间的三台265m2烧结机上进行了改进,将原来的一台二混制粒机改为两台并行的混制粒机,进一步强化混合料制粒;将原来控制横向偏析的梭式布料器改进为摆动皮带。
3.4增加外矿配比1973年包钢进行了“双强化”试验研究,通过配加庞家堡矿减弱了包钢矿的特殊性,减少了枪晶石含量,改善了烧结矿宏观结构,提高了烧结矿转鼓强度。
随后的试验验证了包头矿特殊性是制约包钢高炉冶炼强化的主要原因。
保证稳定的外矿比例是今后应坚持的方向[5]。
随着包钢整体规模的不断扩大,烧结含铁料中外购(包括进口矿)的比例逐步增多,烧结矿的各项技术质量指标也得以改进。
3.5降低烧结矿SiO2,提高烧结矿TFe品位低硅烧结能改善烧结矿冶金性能;减少高炉冶炼过程中产生的渣量;减薄软熔层,提高滴落带的透气性,因而有利于高炉顺行和降低焦比。
包钢低硅烧结矿成矿且保持相当高的机械强度的关键是:高碱度、低硅和厚料层,降低了影响包钢烧结矿强度的“玻璃质”含量,同时使烧结矿的铁酸钙含量大大提高[6]。
20世纪70年代后,为改进包钢烧结矿矿物组成、显微结构、机械强度及烧结机生产率等技术质量指标,采取了配加庞家堡矿、中贫矿、褐铁矿等高硅矿的措施,取得了一定的效果,但也带来了一系列负面影响。
20世纪90年代后,随着选矿技术进步,精矿SiO2逐步降低;烧结减少或取消高硅矿的配加,烧结矿的SiO2逐步降低,TFe品位逐渐提高。
4.包钢烧结质量指标进步随着各种新技术的不断应用,包钢烧结矿各项技术经济指标显著改善。
从1966年至2008年烧结矿TFe含量提高13.12%;FeO含量降低48.48%;SiO2含量降低50.52%;F含量降低83.90%;烧结固体燃耗降低68.34%;烧结工序能耗降低59.69%(1979年至2008年)。
具体数据见图3-8。
图3 历年包钢烧结矿TFe变化图4 历年包钢烧结矿FeO变化图5 历年包钢烧结矿SiO2变化图6 历年包钢烧结矿F变化图7 历年包钢烧结固体燃耗变化图8 历年包钢烧结工序能耗变化5.结束语5.1到1986年原冶金工业部组织的包钢铁前技术攻关结束,通过提高烧结矿冷强度的技术攻关,改善烧结矿冶金性能试验攻关,包钢烧结“双强化”试验研究,高碱度烧结矿的试验研究与生产,高氧化镁烧结矿的试验研究与生产等一系列试验研究与技术攻关,包钢烧结技术质量指标显著改善。
至二十世纪八十年代末期,年产量由24.65万吨,提高到302.30万吨;烧结机利用系数由0.62t/m2.h,提高到1.31t/m2.h;烧结矿转鼓强度由76.88%,提高到83.55%(+5mm,原冶金部标准);烧结固体燃耗由182.30Kg/t,降至83.67Kg/t;同时烧结矿冶金性能也有了显著改善,促进了高炉冶炼指标的全面提升。
5.2进入二十世纪九十年代后,包钢烧结工程技术人员从包钢实际出发,继续降本增效,提高产量,改善质量的科研技术攻关,从1966年至2008年烧结矿TFe含量提高13.12%;FeO含量降低48.48%;SiO2含量降低50.52%;F含量降低83.90%;烧结固体燃耗降低68.34%;烧结工序能耗降低59.69%(1979年至2008年)。