蒸汽无痕高光注塑技术
高光无痕注塑技术介绍

热变温急冷急热高光无痕注塑RHCM技术优势★ 消除产品表面熔接线;★ 增强原料流动填充效果,提高生产效率★ 提高产品表面光洁度,使之达到镜面效果;★ 产品无需后序喷漆加工处理;;★ 解决加纤产品所产生的浮纤现象。
热变温急冷急热高光无痕注塑RHCM技术分类①蒸汽高光无痕辅助成型技术该工艺加热介质为高温高压的饱和蒸汽,在蒸汽热效控制器的作用下,高温高压蒸汽,冷却水以及压缩空气按顺序输入至模具,使模具相应部位的温度急速升高及降低,从而使塑料制品获得良好表面。
该技术适合于大型热变温无痕注塑成型产品,如大型平板类显示器或相似产品,系当前最为广泛使用的热变温高光无痕注塑系统技术。
高温高压蒸汽通常来自于市政、电厂等机构的商品化管道蒸汽或企业外购的工业蒸汽燃气锅炉自制蒸汽,目前很多企业通过加装小型电加热环保蒸汽发生器自制蒸汽。
蒸汽压力和温度越高,生产效率越高,同时生产的稳定性以及产品的表面高光效果越好。
目前工业化生产中,当饱和蒸汽压力达到2.2MPa时,可以适配任何高光材料的温度要求。
②电热辅助成型技术既在多功能电热控制的作用下,将内置在模具中的加热元件迅速通电加温,使模具相应部位的温度升高及降低,从而使塑料制品获得良好表面质量的成型方法。
适合于小型热变温无痕注塑成型产品,如小尺寸平板类显示器或相似产品,但其模具技术较为复杂,模具冷却问题难度较大,且模具内置电加热部件的损耗寿命问题不太稳定,目前其应用领域和普及程度比蒸汽辅助技术还有差距。
③过热水辅助成型技术在过热水热效控制器的作用下,将热水机产生的高温热水(110-120度),冷却水以及压缩空气进行顺序切换输入至模具水路,从而达到使模具相应部位的温度升高及降低的整套设备。
④热油辅助成型技术设备在热油热效控制器的作用下,将热油机产生的高温热油与常温冷油进行顺序切换输入至模具油路,从而达到使用模具相应部位的温度升高及降低的整套设备。
在上述技术设备中,蒸汽辅助成型技术和电热辅助成型技术系当前主流的高光无痕技术方向,蒸汽辅助成型技术主要针对大中型产品;电热辅助成型技术则面向小型产品,该两项技术由于其高光效果完美、加热效率高、工艺稳定性高、良品率高等显著特点,在实际生产中已几乎涵盖了目前所有批量生产的高光无痕产品。
浅谈蒸汽无痕高光注塑技术
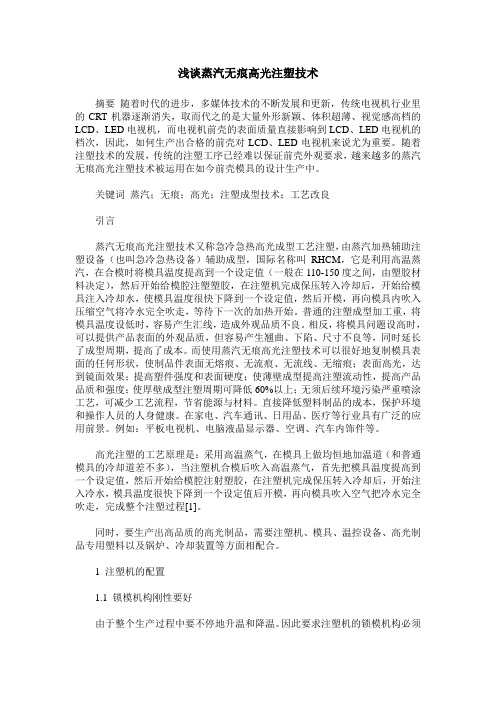
浅谈蒸汽无痕高光注塑技术摘要随着时代的进步,多媒体技术的不断发展和更新,传统电视机行业里的CRT机器逐渐消失,取而代之的是大量外形新颖、体积超薄、视觉感高档的LCD、LED电视机,而电视机前壳的表面质量直接影响到LCD、LED电视机的档次,因此,如何生产出合格的前壳对LCD、LED电视机来说尤为重要。
随着注塑技术的发展,传统的注塑工序已经难以保证前壳外观要求,越来越多的蒸汽无痕高光注塑技术被运用在如今前壳模具的设计生产中。
关键词蒸汽;无痕;高光;注塑成型技术;工艺改良引言蒸汽无痕高光注塑技术又称急冷急热高光成型工艺注塑,由蒸汽加热辅助注塑设备(也叫急冷急热设备)辅助成型,国际名称叫RHCM,它是利用高温蒸汽,在合模时将模具温度提高到一个设定值(一般在110-150度之间,由塑胶材料决定),然后开始给模腔注塑塑胶,在注塑机完成保压转入冷却后,开始给模具注入冷却水,使模具温度很快下降到一个设定值,然后开模,再向模具内吹入压缩空气将冷水完全吹走,等待下一次的加热开始。
普通的注塑成型加工重,将模具温度设低时,容易产生汇线,造成外观品质不良。
相反,将模具问题设高时,可以提供产品表面的外观品质,但容易产生翘曲、下陷、尺寸不良等,同时延长了成型周期,提高了成本。
而使用蒸汽无痕高光注塑技术可以很好地复制模具表面的任何形状,使制品件表面无熔痕、无流痕、无流线、无缩痕;表面高光,达到镜面效果;提高塑件强度和表面硬度;使薄壁成型提高注塑流动性,提高产品品质和强度;使厚壁成型注塑周期可降低60%以上;无须后续环境污染严重喷涂工艺,可减少工艺流程,节省能源与材料。
直接降低塑料制品的成本,保护环境和操作人员的人身健康。
在家电、汽车通讯、日用品、医疗等行业具有广泛的应用前景。
例如:平板电视机、电脑液晶显示器、空调、汽车内饰件等。
高光注塑的工艺原理是:采用高温蒸气,在模具上做均恒地加温道(和普通模具的冷却道差不多),当注塑机合模后吹入高温蒸气,首先把模具温度提高到一个设定值,然后开始给模腔注射塑胶,在注塑机完成保压转入冷却后,开始注入冷水,模具温度很快下降到一个设定值后开模,再向模具吹入空气把冷水完全吹走,完成整个注塑过程[1]。
蒸汽注塑技术的一些事儿

蒸汽注塑技术的一些事儿如何生产出无熔痕、无流痕、无流线、无缩痕,表面高光的外壳产品,对于平板电视机、电脑液晶显示器、空调、汽车内饰件来说尤为重要。
使用高光注塑技术就可以很好地解决此问题。
高光注塑的工艺原理在合模前及合模过程中对模具进行加温、合模完成后,温度达到设定条件即进行注射。
注射过程中模具继续维持高温,这样可以使胶料注射时在模具内保持很好的流动性。
注射完成,在保压冷却时,则对模具进行降温处理,又可以大大缩短制品的冷却时间,从而提高生产效率。
蒸汽无痕高光注塑技术目前在国内尚属于一项先进的生产工艺。
由于这一技术大大改善了制品的表面质量和表面强度,并可取消后续的喷涂或喷漆等工艺、既保护了环境和操作人员的人身健康,又因减少工艺流程,省去了昂贵的二次加工费用,在大幅度降低生产成本的同时,节省能源与材料。
传统工艺传统的做法是采用模温机对模具进行加温,但这种方法的不足之处如下:①无法满足高光注塑中快速升温及快速降温的需要;②升温幅度较小,制品表面的熔接痕只能得到减轻而无法消除;③由于塑料硬度越高,流动性越差。
因此采用此种工艺制品表面的硬度只能达到HB级无法满足实际使用需要;④模具升温时受热膨胀,降温时又会收缩,使锁模力很不稳定。
容易造成制品打不满,烧焦,内应力大等各种缺陷。
高光注塑技术在传统工艺基础上发展而来的蒸汽高光注塑技术则针对以上缺陷分别做了改进:①此技术在模具中开水管,需要升温时通蒸汽,需要降温时通冷水,冷却完毕后则用压缩空气将残留水分吹出,以确保能实现快速升温、降温;②以最大程度地消除熔接痕夹、水纹缺胶等各种制品故障;③由于升温幅度较大,宜使用H甚至2H硬度级别的塑料,使制品表面硬度大大提高;④由于在模具内部开设管道时,只对模具内表面进行升温或降温,模具的整体膨胀较小,因此减少了由于锁模力的不稳定而带来的各种制品缺陷。
RHCM高光无痕注塑成型
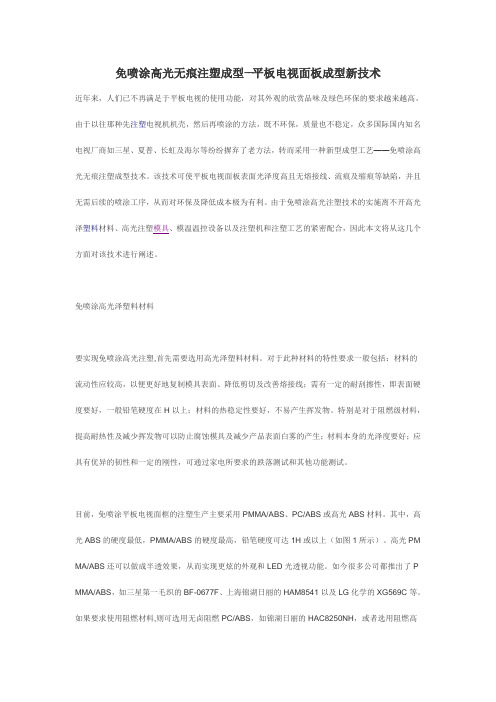
免喷涂高光无痕注塑成型--平板电视面板成型新技术近年来,人们已不再满足于平板电视的使用功能,对其外观的欣赏品味及绿色环保的要求越来越高。
由于以往那种先注塑电视机机壳,然后再喷涂的方法,既不环保,质量也不稳定,众多国际国内知名电视厂商如三星、夏普、长虹及海尔等纷纷摒弃了老方法,转而采用一种新型成型工艺——免喷涂高光无痕注塑成型技术。
该技术可使平板电视面板表面光泽度高且无熔接线、流痕及缩痕等缺陷,并且无需后续的喷涂工序,从而对环保及降低成本极为有利。
由于免喷涂高光注塑技术的实施离不开高光泽塑料材料、高光注塑模具、模温温控设备以及注塑机和注塑工艺的紧密配合,因此本文将从这几个方面对该技术进行阐述。
免喷涂高光泽塑料材料要实现免喷涂高光注塑,首先需要选用高光泽塑料材料。
对于此种材料的特性要求一般包括:材料的流动性应较高,以便更好地复制模具表面、降低剪切及改善熔接线;需有一定的耐刮擦性,即表面硬度要好,一般铅笔硬度在H以上;材料的热稳定性要好,不易产生挥发物。
特别是对于阻燃级材料,提高耐热性及减少挥发物可以防止腐蚀模具及减少产品表面白雾的产生;材料本身的光泽度要好;应具有优异的韧性和一定的刚性,可通过家电所要求的跌落测试和其他功能测试。
目前,免喷涂平板电视面框的注塑生产主要采用PMMA/ABS、PC/ABS或高光ABS材料。
其中,高光ABS的硬度最低,PMMA/ABS的硬度最高,铅笔硬度可达1H或以上(如图1所示)。
高光PM MA/ABS还可以做成半透效果,从而实现更炫的外观和LED光透视功能。
如今很多公司都推出了P MMA/ABS,如三星第一毛织的BF-0677F、上海锦湖日丽的HAM8541以及LG化学的XG569C等。
如果要求使用阻燃材料,则可选用无卤阻燃PC/ABS,如锦湖日丽的HAC8250NH,或者选用阻燃高光ABS,如上海锦湖日丽的HFA705G。
电视机厂商可根据产品的不同要求选用不同型号的材料。
高光蒸汽注塑模具技术

排气槽(红色) 集气槽(黄色)
排气孔
20~50mm
图12
料流末端的排气镶件(红色)
图13
高光蒸汽模具加工工艺特点
加工条件:
1、CNC加工:表面光洁度0.005mm以内。 2、孔加工:蒸汽孔偏摆度<=0.3‰,孔壁光滑,抵御急热急
冷,提高模具寿命。 3、配模:活动顺畅,较普通模具在热涨方向松配,太紧烧
死,太松披风。 4、抛光:关键要素---高光效果决定产品品质。
注塑机的要求:
温控设备要形成闭环,灵敏度高。 无尘车间生产,用专用保护膜包装保护。 熟悉高模注塑特点,熟悉调机缺陷解决思路。
高光模具后期保养
模具保养:清理排气槽+专用洗剂清洗型腔+专用防锈油。
综合:高模比普模高约20%~40%。
高光蒸汽注塑技术将会被广泛应用和迅速扩展,模具研发 具有广阔市场前景。
特点四:高温模具设计问题点解决。
中托边
I
中托边 采用青铜加石墨材料制做中托边和导套机构,有效防止模
具拖伤和保证开合模顺畅。
II
中间位置设计前后模定位机构,有效保证模具合模准确定 位,同时中间位置避免模具膨胀装配不顺畅情况。
III
设计可转式斜顶座结构,消除加工精度误差造 成装配上的影响,减少装配工作量。
• 高模具材料: 1、模具钢ቤተ መጻሕፍቲ ባይዱ:
S136、NAK80、LKM838H、LKM818H、 CENA#1 2、塑胶材料: PMMA/ABS、PC/ABS、高光ABS、HIPS
• 高模特点:配件耐热性。
1、高模加热和冷却 加长连接管直接进出,取消防水圈。见下页图片。
高光无痕注塑模具设计规范

高光无痕注塑模具设计规范高光无痕注塑模具设计制造规范一、高光无痕注塑的原理:1、模具成型对温度要求较高(一般为80°~130°左右),在注塑转入保压后改用冷却水,使模具降温至60°~70°度。
在较高的模温下保压成型有利于消除熔接痕、流痕、产品内应力等缺陷。
因此模具在工作时需进行加热处理,为了防止热量损失,一般都会在定模侧加树脂隔热板。
2、模腔表面极度光亮(一般为镜面2级或更高)。
高光模具生产出的产品能够直接用于装机,无需做任何表面处理。
因此它对模具钢材及塑胶材料的要求都很高。
3、热流道系统的热咀较多。
每个热咀必须带封针且有独立的气道,经过电磁阀及时间继电器等进行单独控制,实现分时进胶,从而达到控制甚至消除熔接痕的目的。
4、模具加热的方式一般有水蒸汽加热(见图1)和加热棒加热(见图2)两种。
水蒸汽加热方式是经过特定的模温机在注塑过程中经过模具通蒸汽,从而使模具快速升温;在注塑完后改一般温水(或者冰水)使模具快速降温。
加热棒加热方式是在注塑过程中经过在内模料里面加加热棒使模具快速升温;在注塑完成后经过内模料里面的运水(常温水或者冰水)或者叠层模料底部的铝材(铝材里面通运水)使模具温度快速降温。
(图1)(图2)二、模具材料(一)产品表面普通要求的模具材料可用NK80(日本大同);(二)高光要求的产品选用S136H(瑞典)、CEANA1(日立);(三)NK80可不用淬火处理;S136应在粗加工后淬火至52度;CEANA1号本身具备42度也不需要淬火处理(建议用此材料,因不影响后续加工或改动);(四)德国葛利兹品牌中也有不错的选择:CPM40\GEST80三、模具水道设计(一)水道采用5mm-6mm大小的孔;水嘴用1\8或3\8的牙(模具侧),另一侧用3\4英制螺纹;管件材料用不锈钢管;(二)水道一侧离产品面最近不低于5mm-6mm;水道平行产品面且均匀排布(原则中心距15mm分布,);热电偶应设计在两水道中间,深度在50mm左右;且每套模具的PT100是一配一的,保持它的精确度,埋在模具模仁内,与热流道的热电偶一样,用线连接到模具外侧,转接插座,PT100要有对应的插头与其对接。
蒸汽模高光注塑技术(急冷急热模)-应用探讨

三、3.1蒸塑件汽结构模的技优化术设计中的关键技术
蒸汽模成型技术作为高光无熔痕成型技 术之一,其塑件的结构设计与普通塑件不同, 即需要根据高光无熔痕模具的成型特点对塑 件进行优化设计,如制件的脱模斜度、圆角 过渡、螺钉柱固定结构等都需要调整,以满 足高光无熔痕注塑成型的工艺要求。
三、3.2蒸成型汽过模程模技拟和术浇注中系统的优化关键技术
二、2.2蒸模具汽温度模控技制系术统 所涉及的设备
模具温度控制系统包括: 冷却塔、蒸汽锅炉、 压缩机、高光温度控制柜等生产设备。该温 度控制系统有时也可用高光蒸汽模温机代替。 高光温度控制柜是系统非常关键的一部分, 它根据模具上的温度传感器反馈的温度控制 着高温蒸汽和冷却水的切换,并与注塑机控 制系统实时互换信号,从而进行熔体的注射、 保压以及开模顶出动作,以完成整个注塑过 程!整个注塑成型。
前后的对比。 从图3(a)可以看出,制件在Z轴方向的变形比较严重,翘曲现象
明显。从图3(b)可以看出,在Moldflow软件进行优化以后,Z 轴方向设置术与优中化 的关键技术
由于蒸汽管道和冷却管道是共用的,因此正确设置管道尤 型技术对蒸汽管道的排布讲究合理性和有效性。合理的排 提高注塑效率,而且起到使塑件受热和冷却更加均匀,减 的作用。其设计原则是:根据塑件形状特征来设计模具的 的随形冷却管道,实现模腔内部熔体温度的动态控制,使 动达到最佳状态。
蒸汽高光注塑技术 应用探讨
蒸1汽模技术的基本原理 蒸2汽模技术所涉及的设备
目录 蒸3汽模技术中的关键技术
蒸4汽模技术的优势 蒸汽5 模成型的主要影响因素
一蒸、汽模蒸成型汽技术模的技成型术工艺的过程基是: 本原理
模具合模后,首先在加热冷却管道内通入高 温蒸汽,把模具温度提高到一个高的设定值, 然后注射塑料熔体,在保压转入冷却后,用 气压吹走通道内的残留蒸汽,开始注入冷水, 使模具温度快速下降到一个设定值,再向加 热冷却管道内通入空气,把冷水完全吹走, 开模取制件,然后进入下一次注塑循环。
RHCM高光无痕注塑系统技术介绍

奥德模温机RHCM高光无痕注塑系统技术介绍2010-5-29 点击:29次180℃过热水“RHCM高光无痕注塑”系统技术介绍:RHCM高光无痕注塑又被称为RHCM (Rapid Heat Cycle Moulding),还有在行业中如:冷热成型,高低温注塑,急冷急热注塑,热变温注塑.高光免喷涂技术等叫法,目前行业中使用效果最好最经济的方法是采用高温过热水加热+水冷却,该技术是透过运用180℃过热水将模具表面快速升温,令成型模腔表面温度达到树脂塑料的玻璃转移温度(Tg – Glass Transition Temperature)以上,然后开始进行射出成型,当完成模腔填充过程后,立即利用水(经处理)作为冷却媒体使模具表面温度急速下降,从而改变塑料产品表面特性。
RHCM “高光无痕注塑”技术发展至今已近4年之多,早期是日本.韩国的3 D蒸汽无痕注塑技术在汽车.家电行业的到广泛的应用,但是由于使用的加热源是采用锅炉产生的蒸汽来给模具加热,所以采用锅炉蒸汽加热的方式会受到地方环保和安全的限制,最重要的是采用锅炉产生的蒸汽给模具加热后,蒸汽没有办法得到回收造成的高成本问题,一直一创新为企业长期发展为根源的奥德公司在2006年初就看到国内这块市场的空白,并成立了专门针对过热水的高光无痕项目研发团队,在2007年初成功推向市场,经过半年的市场考验和用户考核,奥德公司所研发的GWS高光无痕注塑模温控制系统(急速升降模温系统)获得了塑料行业的技术创新奖, 同时获得国家审批专利证书(专利号:ZL。
2008.2.0205521.0), 并得到国内知名的液晶电视及其他高光产品外壳(如惠州TCL.台湾广达集团.广州毅昌科技,无锡金悦.青岛恒佳...昆山亿盛..)等数十家生产厂家的广泛使用,使用RHCM “高光无痕注塑”技术生产LCD液晶平板电视外壳,其中主要优点是可以使树脂塑料产品外壳拥有高光泽度;消除了传统注塑成型工艺存在的熔接痕.结合线.(加波纤产品的浮纤)问题,并省却了产品二次加工的必要和有关的成本(例如:喷漆.UV…..)。
浅谈高光无痕注塑模具及成型技术
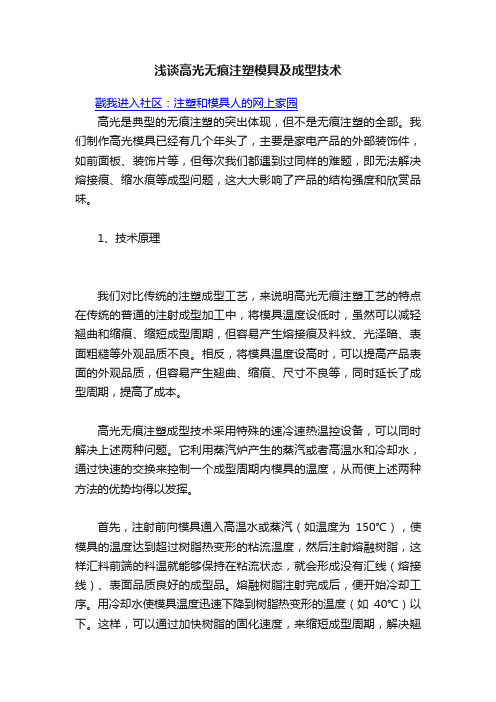
浅谈高光无痕注塑模具及成型技术戳我进入社区:注塑和模具人的网上家园高光是典型的无痕注塑的突出体现,但不是无痕注塑的全部。
我们制作高光模具已经有几个年头了,主要是家电产品的外部装饰件,如前面板、装饰片等,但每次我们都遇到过同样的难题,即无法解决熔接痕、缩水痕等成型问题,这大大影响了产品的结构强度和欣赏品味。
1、技术原理我们对比传统的注塑成型工艺,来说明高光无痕注塑工艺的特点在传统的普通的注射成型加工中,将模具温度设低时,虽然可以减轻翘曲和缩痕、缩短成型周期,但容易产生熔接痕及料纹、光泽暗、表面粗糙等外观品质不良。
相反,将模具温度设高时,可以提高产品表面的外观品质,但容易产生翘曲、缩痕、尺寸不良等,同时延长了成型周期,提高了成本。
高光无痕注塑成型技术采用特殊的速冷速热温控设备,可以同时解决上述两种问题。
它利用蒸汽炉产生的蒸汽或者高温水和冷却水,通过快速的交换来控制一个成型周期内模具的温度,从而使上述两种方法的优势均得以发挥。
首先,注射前向模具通入高温水或蒸汽(如温度为150℃),使模具的温度达到超过树脂热变形的粘流温度,然后注射熔融树脂,这样汇料前端的料温就能够保持在粘流状态,就会形成没有汇线(熔接线)、表面品质良好的成型品。
熔融树脂注射完成后,便开始冷却工序。
用冷却水使模具温度迅速下降到树脂热变形的温度(如40℃)以下。
这样,可以通过加快树脂的固化速度,来缩短成型周期,解决翘曲、下陷等问题。
高光无痕注塑可消除产品表面溶接线、溶接痕、波纹及银丝纹,彻底解决塑料产品的表面缩水现象,并使产品表面光洁度达到镜面水平,几乎可以完全再现模具的表面状态,达到无痕的效果。
产品不需要喷涂的后续加工,有效降低成本,缩短交货时间。
此外,高光注塑还可解决加纤产品所产生的浮纤现象,从而使产品品质更加完美。
在薄壁成型中,在高温下注入熔融树脂有助于提高注塑流动性,降低注射压力,避免浇不足和困气等问题,提高产品质量与强度。
而且通过成型后的速冷,也可以降低收缩应力,使脱模变得容易。
注塑主题演讲
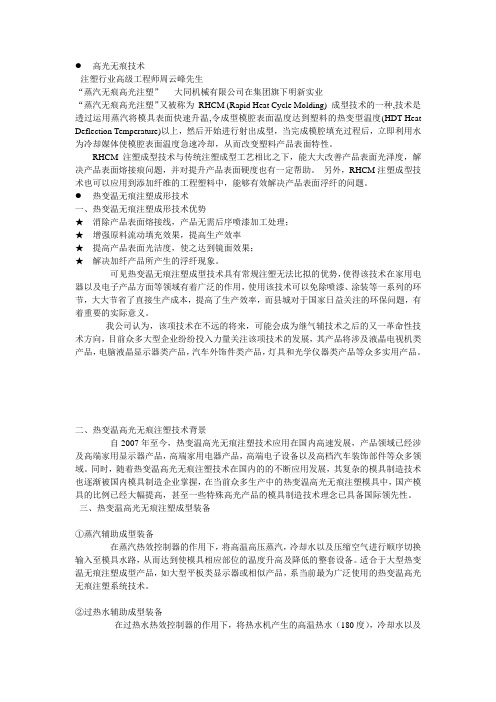
●高光无痕技术--注塑行业高级工程师周云峰先生“蒸汽无痕高光注塑”----大同机械有限公司在集团旗下明新实业“蒸汽无痕高光注塑”又被称为RHCM (Rapid Heat Cycle Molding) 成型技术的一种,技术是透过运用蒸汽将模具表面快速升温,令成型模腔表面温度达到塑料的热变型温度(HDT-Heat Deflection Temperature)以上,然后开始进行射出成型,当完成模腔填充过程后,立即利用水为冷却媒体使模腔表面温度急速冷却,从而改变塑料产品表面特性。
RHCM注塑成型技术与传统注塑成型工艺相比之下,能大大改善产品表面光泽度,解决产品表面熔接痕问题,并对提升产品表面硬度也有一定帮助。
另外,RHCM注塑成型技术也可以应用到添加纤维的工程塑料中,能够有效解决产品表面浮纤的问题。
●热变温无痕注塑成形技术一、热变温无痕注塑成形技术优势★消除产品表面熔接线,产品无需后序喷漆加工处理;★增强原料流动填充效果,提高生产效率★提高产品表面光洁度,使之达到镜面效果;★解决加纤产品所产生的浮纤现象。
可见热变温无痕注塑成型技术具有常规注塑无法比拟的优势,使得该技术在家用电器以及电子产品方面等领域有着广泛的作用,使用该技术可以免除喷漆、涂装等一系列的环节,大大节省了直接生产成本,提高了生产效率,而县城对于国家日益关注的环保问题,有着重要的实际意义。
我公司认为,该项技术在不远的将来,可能会成为继气辅技术之后的又一革命性技术方向,目前众多大型企业纷纷投入力量关注该项技术的发展,其产品将涉及液晶电视机类产品,电脑液晶显示器类产品,汽车外饰件类产品,灯具和光学仪器类产品等众多实用产品。
二、热变温高光无痕注塑技术背景自2007年至今,热变温高光无痕注塑技术应用在国内高速发展,产品领域已经涉及高端家用显示器产品,高端家用电器产品,高端电子设备以及高档汽车装饰部件等众多领域。
同时,随着热变温高光无痕注塑技术在国内的的不断应用发展,其复杂的模具制造技术也逐渐被国内模具制造企业掌握,在当前众多生产中的热变温高光无痕注塑模具中,国产模具的比例已经大幅提高,甚至一些特殊高光产品的模具制造技术理念已具备国际领先性。
高光无痕注塑技术

高光无痕注塑成型技术高光无痕注塑成型是近年来在注塑行业中快速发展的一种新型技术。
该技术采用高光泽的塑料材料,使用精密的高光模具,利用先进的模温控制系统实现动态的温度控制,以克服表面流痕和熔接痕等不良缺陷,使产品表面达到高光亮的无痕镜面效果,提高产品强度和质量;同时,速冷可大幅缩短注射周期,提高生产效率;产品无需后续的喷涂加工,保护环境的同时有效降低了成本,是一种绿色制造技术。
广泛应用于音响等视听电器的面板、平板电视、液晶显示器、洗衣机、空调、汽车内外饰件、车灯、光学仪器等家电、汽车、通讯、医疗等行业。
高光无痕注塑成型技术采用特殊的速冷速热温控设备,在注射时快速且均匀地把模具表面加热到指定的温度(达到甚至超过塑料的粘流态温度),使物料始终保持粘流态,几乎没有冻结层,这样就会形成没有熔接线、表面良好的成型品;而在冷却时能快速转换为急剧冷却来缩短成型周期,解决翘曲、缩水问题,这就是高光无痕注射成型的技术原理。
其控制过程如图1所示。
模貝急速加热〔如I2&T!>图1:高光注塑的控制过程高光无痕注塑的技术关键点在于模温控制系统、高光泽塑料材料和高光注塑模具三方面。
(1)先进的模温控制系统模温控制系统是高光注塑成型最关键的技术,其设备由高速制热装置、快速冷却装置、控制装置组成,并能够和注塑机信号互锁,实现闭环控制。
按加热方式不同,可分为蒸汽式、电热式、热水式、高油温式和感应加热式模温控制技术,而目前使用较多的是蒸汽式和电加热式两种温控技术:①蒸汽快速模温技术:简称蒸汽模,模具的加热通过高压蒸汽实现,模具表面最高温度达到160°C甚至更高。
冷却时快速转换成低温水对模具进行冷却。
该技术需要锅炉快速产生足够量的蒸汽,但由于生产过程中蒸汽不可循环利用,致使其运行成本较高。
在2005年韩国三星电子开始使用该技术生产LCD液晶平板电视外壳。
(可否不要?)②电加热的快速模温技术:典型的为韩国NADA公司的E-MOLD(ElectricityMold)技术。
蒸汽辅助注塑模具介绍
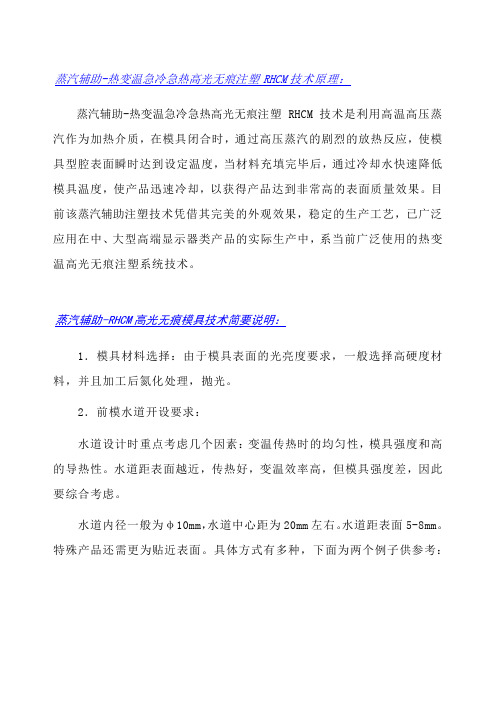
蒸汽辅助-热变温急冷急热高光无痕注塑RHCM技术原理:
蒸汽辅助-热变温急冷急热高光无痕注塑RHCM技术是利用高温高压蒸汽作为加热介质,在模具闭合时,通过高压蒸汽的剧烈的放热反应,使模具型腔表面瞬时达到设定温度,当材料充填完毕后,通过冷却水快速降低模具温度,使产品迅速冷却,以获得产品达到非常高的表面质量效果。
目前该蒸汽辅助注塑技术凭借其完美的外观效果,稳定的生产工艺,已广泛应用在中、大型高端显示器类产品的实际生产中,系当前广泛使用的热变温高光无痕注塑系统技术。
蒸汽辅助-RHCM高光无痕模具技术简要说明:
1.模具材料选择:由于模具表面的光亮度要求,一般选择高硬度材料,并且加工后氮化处理,抛光。
2.前模水道开设要求:
水道设计时重点考虑几个因素:变温传热时的均匀性,模具强度和高的导热性。
水道距表面越近,传热好,变温效率高,但模具强度差,因此要综合考虑。
水道内径一般为φ10mm,水道中心距为20mm左右。
水道距表面5-8mm。
特殊产品还需更为贴近表面。
具体方式有多种,下面为两个例子供参考:
1
3.热电隅埋设要点:可根据模具大小,在每边埋设1-2个热电隅(一般为K 型,实际参与控制的热电隅只有一个,其余测温只为观察)。
埋设点一般距模具表面3-5mm,热电隅孔垂直于水道,埋设时一定要确保电隅探测点与模具紧密接触,热电隅测出的温度主要用于工艺参考,
相对值的重要性大于绝对值(很多工厂实际生产时,当工艺稳定后,不用温度控制,而直接用动作时间周期来控制。
见下图:
4.模具后模:一般后模用油温机保持恒温50-600C。
免喷涂注塑成型-高光无痕模具设计制造经验规范

1、高光急冷急热模采用高温蒸气,在模具上做均恒的加温通道,当注塑机合 模后吹入高温蒸气,把模具型腔温度提高到设定值(一般为80°~130°左右), 然后开始给模型注胶,在注塑机完成保压转入冷却后,开始注冷水,模温降到 (60°~70°度)后,开模,再向模具吹入空气把冷水吹走,完成整个注塑过程。
四、设计重点:隔热系统
1、模具定模镶芯或动模镶芯四面要做到掏空处理;模框与镶芯要有一定的间隙(视模具 材料的热膨胀系数,单面1mm)。防止模框膨胀,以减少模芯于模框的接触面,做到使 热能损耗最小化;模芯与模框的锁定采用斜契式或其它类似方式,前端采用隔热效果明 显的粉尘树脂或其它材料(如石棉板)。 2、模框与镶芯的详细结构,模框的冷却水非常重要,为防止模仁中的热能传至模框, 要在靠近导柱位臵,上下排布一圈运水。?? 3、导套运动部位尽可能采用石墨材料或者把导柱前端避空处理,配合处只要保证 25mm长度就足够了;
二、高光模温机设备厂家
高光模温机1 (宁波捷信特)
高光模温机2 (北京中拓)
三、高光 产品案例分享
AP31上饰板面板
材质:高光PC
钢材:型腔ASTM-VIP(斯堪纳),预硬HRC40-44
尺寸ห้องสมุดไป่ตู้239*409*78
型芯1.2738 (布德鲁斯),预硬HRC29-33
重量:165g
四、设计重点:产品分析要点 高光模具对产品结构要求很严格,越光亮的产品对光的折射效果越敏感,表面稍 有缺陷很快就会被发现,因此如何解决缩水问题是高光产品的首要问题。 一般PC或PC+ABS材料的产品筋位厚度不超过主体胶位厚度的0.5倍便不会缩水, 或者说缩水较小不易被发现,可忽略不计。但对高光产品而言,这样的要求远远不够, 还需将产品筋位的厚度减小到不超过主体胶位厚度的1/3,对于螺丝柱位还必须做火山 口式斜顶结构。
无痕蒸汽模具介绍

Page 1高光无痕蒸汽模具介绍• • • • 免喷涂高光无痕注塑技术介绍 免喷涂高光无痕注塑技术应用范围 高光蒸汽模具的特点 Basis在高光模具方面的技术优势镜面后无高光高光产品Page 2成功案例:电视机面壳系列19寸24寸42寸 46寸Page 3高光蒸汽模具的特点• 高光模具对产品结构的要求 高光模具对产品的结构有些特殊的要求,众 所周知,越是光亮的产品表面对光的反射越敏 感,表面稍有缺陷就很容易被发现,因此如何解 决缩水是一个很重要的问题。
高光产 品柱位 非高光产 品柱位Page 4高光模具结构上的特点 首先由于高光模具使用了一些特殊的设备,所以在设计时需要考虑到各个设 备之间的安装连接的匹配性,并且由于模具是在高温环境下工作,所以还要 考虑到各部件的耐热性。
1、高光模具的加热和冷却 当塑胶材料被注塑到模具的型腔中时,在合理的温度范围内,模具型腔表面 温度越高,产品的表面质量越好,产品内应力也越小。
因此,要想获得好的 产品表面质量,尽可能的提高型腔表面温度是个很好的途径。
所以高光模具 对汽道的排布比较讲究,好的汽道排布不仅可以大大提高注塑效率,而且在 改善产品质量方面可以起到重要作用。
高光模具的汽道不仅要均匀而且必须 要充分,这样通过模温机就可以很容易达到所要求的温度;同时,最好采用 加长连接管直接将模芯运水或蒸汽引出而不要采用密封圈的形式,这样可防 止模具长期在高温下作业,致使密封圈老化,可降低模具的维修成本。
见下 页图片。
值得一提的是,为了安全起见高光模具的运水管必须采用耐高温油管,以防 高温高压下水管爆裂,发生事故。
•Page 5Page 62、汽路设计特点: 一定要跟随产品的表面形状设计(图1)。
这也是高光模的一个局限 性,因为如果产品的形状比较复杂时,汽路设计要跟随产品表面的形 状就比较困难(图2),所以高光模具目前主要应用在平板类产品的 模具上。
图1图2Page 7对于高光蒸汽模具中的水路及油路的密封,为了安 全一般采用双密封圈设计,并且密封圈要保证可耐 高温。
高光蒸汽注塑模具技术

高温蒸汽 进出接头
最低层(兰色) 为高温蒸汽
上面一层(黄 色)为冷水
最上面一层 (白色)温水
高温蒸汽接头材料: 不锈钢
2、汽路设计特点:与产品一倍间距8~10mm封:双密封圈设计,可耐高温(图3)。 对于汽路、水路、油路-----堵铜+堵头, 防泄露(图4-5),减少维修保养。
蒸 汽 加 热 控 制 台
注入蒸汽 吹出蒸汽 注入冷水 冷水回流
2 模1
注塑 高 光 达到注塑温度 模 达到顶出温度 具
顶出
注塑、保 压、补塑
开模、取 出产品
温控设备
高蒸模运用:
1 汽车零件 2 办公设备、家电或机壳 3 LCD透光板、镜头、光学仪器 4 簿壁外壳 5 精密板件
镜面后无高光
高光产品
排气系统(图12、13)
高光效果与流痕,排气重点:
1、 分型排气。排气槽尺寸宽度为3~8mm,长度为5~ 10mm,间距20~40mm左右。集气槽0.5~1.5mm深, >=50%区域设计。
2、镶件排气。对于深骨位产品,在料流的末端设计组合式 镶件,避免困气。
3、顶针、司筒排气。在不溢料的前提,有意增加顶针、司 筒和模芯之间的间隙,进行排气。
高光注塑介绍
• 高光成型:温控设备---高表面质量。分为: • 热恒温高注技术:热油机90°---注塑生产。优
点:工艺简单,成本低;缺点:高光一般,强度 差,易变形。 • 热变温高技术:模温升120°注塑, 50°- 70° 保压,高光无痕。优点:变形小,周期适当。
高光蒸汽注塑技术称为继气辅技术之后的又一革命性技术!
高光蒸汽注塑模具 技术交流与分享
课程大纲
1、高光蒸汽模具概念和流程。 2、高光蒸汽模具设备和运用范围。 3、产品工艺和高光蒸汽模具设计特点。 4、高光蒸汽模具排气系统设计。 5、高光蒸汽模具加工工艺、注塑与保养。 6、高光蒸汽模具设计案例说明与分享。 7、高光模具与产品展示。 8、高光蒸汽模具意义和设计标准。
蒸汽直接加热模腔的高光注塑技术研究
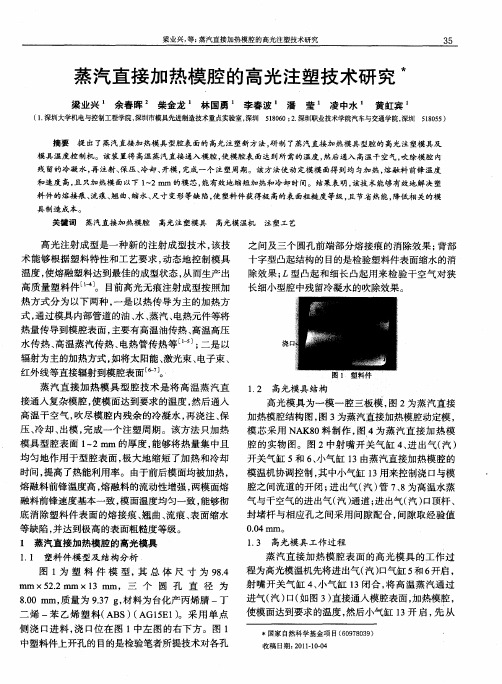
了 厶 ( 正交试验表 , 3) 以信噪 比( Ⅳ) / 为分析依 据 , 用 方差 和正 交 多项式 的手段 , 利 对影 响塑 料件 表 面粗 糙 度 的各 种 因素 进行 研 究 ¨ 得 出合 理 的注 塑 ,
工 艺过 程 如 图 7 示 。 所
\
赠
值 ( a) ( b)
辐射为主的加热方式。 如将太 阳能、 激光束 、 电子束 、
浇口
红外线等直接辐射到模腔表面 。
蒸 汽直接加热模具型腔技术 是将 高温蒸汽直
图 1 塑料 件
1 2 高光模 具 求的温度 , 然后通人 高光模具为一模一腔三板模 , 2 图 为蒸汽直接 高温干空气 , 吹尽模腔 内残余的冷凝水 , 再浇注 、 保 加 热模 腔结构 图 , 3 蒸 汽直接 加 热模腔 动定 模 , 图 为 压、 冷却 、 出模 , 完成一个注塑周期 。该方法只加热 模 芯 采 用 NA 0料 制作 , 4为 蒸 汽 直 接 加 热 模 K8 图 模具型腔表面 1 2t n的厚度 , — r u 能够将热量集 中且 腔 的实物 图。图 2中射嘴开关气缸 4 进 出气( ) 、 汽 均匀地作用于型腔表面 , 极大地缩短了加热和冷却 开关气缸 5 6 小气缸 1 和 、 3由蒸汽直接加热模腔的
图 l 模 腔 表 面温 度 与 塑料 件 表 面粗糙 度 的 关 系 l
图 1 示 水蒸 气 通 人 时 间与 模 腔 表 面温 度 的 2所
关系。从 图 l 可知 , 2 水蒸气在 5S 内即可将模腔表 面温度 提高至 10 如果继续通入 水蒸气 , 2 ℃; 模腔
表 面 温度 升 高速 度 明显 放 缓 , 在 2 后 逐 步接 近 并 0S 15 , 4 ℃ 故在 一个稳 定 的成 型周期 内 , 水蒸 气 (6 ℃ 、 10 8 6 a 加热 的时 间控制 在 4S 1 ) MP 左右 即可 。
蒸汽模高光注塑技术(急冷急热模)-应用探讨ppt课件
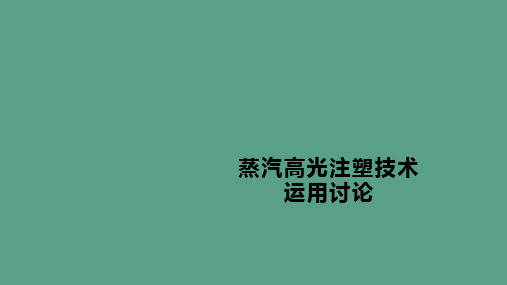
;
目录
1 蒸汽模技术的根本原理 2 蒸汽模技术所涉及的设备 3 蒸汽模技术中的关键技术 4 蒸汽模技术的优势 5 蒸汽模成型的主要影响要素
;
一、蒸汽模技术的根本原理
蒸汽模成型技术的成型工艺过程是: 模具合模后,首先在加热冷却管道内通入高温蒸汽,把模具温度提高到一个高 的设定值,然后注射塑料熔体,在保压转入冷却后,用气压吹走通道内的残留 蒸汽,开场注入冷水,使模具温度快速下降到一个设定值,再向加热冷却管道 内通入空气,把冷水完全吹走,开模取制件,然后进入下一次注塑循环。
三、蒸汽模技术中的关键技术
3.1 塑件构造的优化设计 蒸汽模成型技术作为高光无熔痕成型技术之一,其塑件的构造设计与普通塑件 不同,即需求根据高光无熔痕模具的成型特点对塑件进展优化设计,如制件的 脱模斜度、圆角过渡、螺钉柱固定构造等都需求调整,以满足高光无熔痕注塑 成型的工艺要求。
三、蒸汽模技术中的关键技术
二、蒸汽模技术所涉及的设备
2.2 模具温度控制系统 模具温度控制系统包括: 冷却塔、蒸汽锅炉、紧缩机、高光温度控制柜等消费 设备。该温度控制系统有时也可用高光蒸汽模温机替代。高光温度控制柜是系 统非常关键的一部分,它根据模具上的温度传感器反响的温度控制着高温蒸汽 和冷却水的切换,并与注塑机控制系统实时互换信号,从而进展熔体的注射、 保压以及开模顶出动作,以完成整个注塑过程!整个注塑成型。
从图3〔a〕可以看出,制件在Z轴方向的变形比较严重,翘曲景象明显。从图3〔b〕可以 看出,在Moldflow软件进展优化以后,Z轴方向的变形明显减小,翘曲景象不明显。
三、蒸汽模技术中的关键技术
3.3 蒸汽管道的设置与优化 由于蒸汽管道和冷却管道是共用的,因此正确设置管道尤为关键。而蒸汽模成 型技术对蒸汽管道的排布讲究合理性和有效性。合理的排布管道不仅可以大大 提高注塑效率,而且起到使塑件受热和冷却更加均匀,减少内应力和翘曲变形 的作用。其设计原那么是:根据塑件外形特征来设计模具的型腔构造和环绕型腔 的随形冷却管道,实现模腔内部熔体温度的动态控制,使熔体在模腔中的流 动到达最正确形状。
- 1、下载文档前请自行甄别文档内容的完整性,平台不提供额外的编辑、内容补充、找答案等附加服务。
- 2、"仅部分预览"的文档,不可在线预览部分如存在完整性等问题,可反馈申请退款(可完整预览的文档不适用该条件!)。
- 3、如文档侵犯您的权益,请联系客服反馈,我们会尽快为您处理(人工客服工作时间:9:00-18:30)。
蒸汽无痕高光注塑技术
(时间:2008-11-20 10:47:10 共有
989人次浏览)
蒸汽无痕高光注塑技术是透过运用蒸汽将模具表面快速升温,令成型模腔表面温度达到树脂塑料的玻璃转移温度(Tg – Glass Transition Temperature)以上,然后开始进行射出成型,当完成模腔填充过程后,立即利用水(经处理)作为冷却媒体使模具
表面温度急速下降,从而改变塑料产品表面特性。
RHCM “蒸汽无痕高光注塑”技术发展至今已近4年之多,由2004年德国K-Show 中正式开始公布,直到2007年中国电视生产商才开始使用在生产液晶平板电视外壳上。
其实早在2005年韩国Samsung (三星) 公司已开始使用RHCM “蒸汽无痕高光注塑”技术生产LCD 液晶平板电视外壳,其中主要优点是可以使树脂塑料产品外壳拥有高光泽度;消除了传统注塑成型工艺存在的熔接痕问题,并省却了产品二次加工的必要
和有关的成本
RHCM 注塑成型技术与传统注塑成型工艺相比之下,能大大改善产品表面光泽度,解决产品表面熔接痕问题,并对提升产品表面硬度也有一定帮助. 另外,RHCM 注塑成型技术也可以应用到添加纤维的工程塑料中,能够有效解决产品表面浮纤的问题。
RHCM 是如何消除产品表面熔接痕?
熔接痕的形成是由两股或以上的融熔塑料在射出成型的填充过程中,融熔塑料流的波形前端在模腔中相遇会合,如果模腔表面温度不足或流体遇合压力不足,便会造成合流端无法完全熔合,形成产品表面出现熔接痕缺陷;另外,如塑料中含有添加物(例如: 色母),在熔合位置更会出现较为明显的颜色差异。
然而,运用RHCM 注塑技术,让我们可以在每次开始进行射出成型过程之前,把模腔表面温度快速提升至树脂塑料的热变形温度以上(HDT)
,从而大大增加融熔塑料在模腔内的流动性,减低融熔塑料
与模腔表面之间的磨擦阻力,显著地消除传统注塑工艺产品表面的熔接痕问题。
除此之外,RHCM配合特殊工程塑料更可生产出无痕高光泽度的树脂产品,省却产品因
表面外观要求,而进行的二次加工
RHCM如何解决产品表面浮纤问题?
RHCM技术另一项优点是,能够显著消除添加纤维的改性工程塑料产品表面纤维外露的问题。
一般在传统注塑成型中,玻纤会随融熔塑料流向而定向,如果在填充过程中,因模腔表面温度不足会导致融熔塑料突然在模壁固化,玻纤便会出现无法完全被树脂包裹。
另外,玻纤与树脂塑料收缩特性的差异,当成型产品冷却后,玻纤便会更容易外露于产品表面上。
而,运用RHCM注塑技术,我们能借着控制模腔表面加热和冷却的时间变化,改变树脂塑料产品表面的结晶状态,能够有效消除因玻纤外露于产品表面影响外观性的问题。
日本SONY公司生产的PSP掌上游戏机,背壳也是采用RHCM技术去降低塑料外壳表面的浮纤问题。