纸面石膏板生产工艺技术-脱硫石膏
纸面石膏板生产工艺技术_破碎和研磨

第六章破碎和研磨粉碎和筛分1.介绍许多石膏工厂利用脱硫石膏提供一个合适大小的煅烧平台,仍有一些石膏工厂提供天然石膏的大小,这样它必须破碎,才能进入下一步处理。
粉碎是指通过施加物理力将任何物质分解成更小的碎片。
破碎和研磨是粉碎的形式选矿是一个术语,适用于通过去除材料的一些杂质来提高其质量,通常是通过物理方法而不是化学方法,虽然化学方法经常用来辅助物理方法。
2.目标我们的主要粉碎目标是用最少的能源消耗和最少的极细粉尘,将石膏石膏矿粉碎后送去煅烧或出售所需的大小。
另一个目标是粉碎石膏,例如在管磨中,改变其一些物理性质。
我们的选矿目标是将废石膏以最低的成本和最低的损失,将矿物石膏提高到轧机的质量。
更有利可图的目标有时可能是生产可销售的“废物”,例如用于水泥石的低级石膏。
3. 愿景处理的材料尺寸围很广。
有的采石场最大的石块可达2米长,重达5吨,而典型的煅烧炉用料平均颗粒大小为0.05至0.1毫米,重约0.001毫克。
显然,粉碎设备的围必须适应这些极端之间的巨大物理差异。
4.原理4.1 粉碎主要依靠四个基本原则:•压缩对岩石施加压力,直到它像胡桃夹子一样破碎。
颚式破碎机是一种典型的以这种方式工作的机器。
•力用楔子或凿子把岩石撬开。
冲压式地下破碎机就是根据这一原理工作的。
•冲击用锤子敲打岩石。
锤磨机在转子上使用大量的锤来完成这一工作。
•磨损用砂纸擦去材料的表面。
该原理适用于磨粉机、磨石机和细磨管机。
在实践中,一些机器结合了这四个原则。
此外,应用的原则在很大程度上取决于要破碎的碎片的大小。
凿子式的作用对于大的块状物很好,但对于小的块状物就不实用了;同样,大颗粒的磨损是不切实际的,但对小颗粒却非常有效,这些小颗粒可以在湍流中相互磨损。
4.2 筛分依赖于广泛的原则,但我们在石膏行业关注的两个是:•重力石膏比它的许多杂质都轻。
这一原理在许多工厂中得到了应用。
•粒径分布天然石膏中的杂质在某些粒径上比在其他粒径上收集得多。
纸面石膏板生产工艺
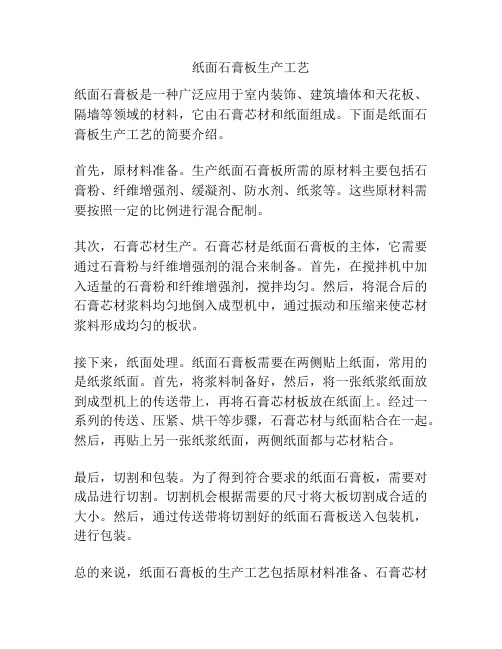
纸面石膏板生产工艺
纸面石膏板是一种广泛应用于室内装饰、建筑墙体和天花板、隔墙等领域的材料,它由石膏芯材和纸面组成。
下面是纸面石膏板生产工艺的简要介绍。
首先,原材料准备。
生产纸面石膏板所需的原材料主要包括石膏粉、纤维增强剂、缓凝剂、防水剂、纸浆等。
这些原材料需要按照一定的比例进行混合配制。
其次,石膏芯材生产。
石膏芯材是纸面石膏板的主体,它需要通过石膏粉与纤维增强剂的混合来制备。
首先,在搅拌机中加入适量的石膏粉和纤维增强剂,搅拌均匀。
然后,将混合后的石膏芯材浆料均匀地倒入成型机中,通过振动和压缩来使芯材浆料形成均匀的板状。
接下来,纸面处理。
纸面石膏板需要在两侧贴上纸面,常用的是纸浆纸面。
首先,将浆料制备好,然后,将一张纸浆纸面放到成型机上的传送带上,再将石膏芯材板放在纸面上。
经过一系列的传送、压紧、烘干等步骤,石膏芯材与纸面粘合在一起。
然后,再贴上另一张纸浆纸面,两侧纸面都与芯材粘合。
最后,切割和包装。
为了得到符合要求的纸面石膏板,需要对成品进行切割。
切割机会根据需要的尺寸将大板切割成合适的大小。
然后,通过传送带将切割好的纸面石膏板送入包装机,进行包装。
总的来说,纸面石膏板的生产工艺包括原材料准备、石膏芯材
生产、纸面处理、切割和包装等过程。
通过这些工艺步骤,能够得到优质、符合要求的纸面石膏板产品。
利用脱硫石膏制造纸面石膏板

燃料煤中 ,消除氯化物的方法是用热水洗涤 ,使其溶解 4 用脱硫石膏制造纸面石膏板
于水中 。 1. 2 钾 、钠的影响 钠是很有害的成分 ,在纸面石膏板中影响纸和石 膏芯粘结 ,钠在石膏中以 Na2 SO4 形式存在 ,在纸面石 膏板干燥时 ,Na2SO4 迁移到面纸与石膏芯之间形成一 层膜 ,石膏板干燥后 ,在常温下冷却下来 ,当温度低于 32 ℃时 , 此 时 Na2 SO4 吸 收 环 境 中 的 水 分 后 形 成
纸面石膏板生产对脱硫石膏有很高的要求 ,见表
1: 表1
纸面石膏板对脱硫石膏的质量要求
1 脱硫石膏中所含杂质对纸面石膏板性能的影响
烟气脱硫石膏作为石膏的一类 ,同样具有建筑胶 凝性能 。作为一种工业副产石膏 ,除了二水硫酸钙之 外 ,还含有一些其他的化学杂质 。 1. 1 氯化物的影响
中图分类号 : TD177. 3 文献标识码 :B
近年来 ,随着我国电力工业的发展和环境标准逐 渐规范严格 ,我国火电厂治理二氧化硫的力度不断加 大 ,其中 70 %采用石灰石 ———石膏湿法脱硫 ,据统计 , 每年可产生大约 760 万 t 的脱硫石膏 。
2 纸面石膏板生产对脱硫石膏品质的要求
面石膏板中会影响石膏板纸和石膏芯的结合 ,在潮湿 料 。它之所以经久不衰 ,是因为它可形成大批量生产
的条件下 ,氯会使钉子和钢筋加速生锈 ,脱硫石膏中的 的自动化作业线 ,价格相对便宜 、无化学污染 、具有优
氯含量要求控制在一定的范围内 ,氯化物主要来源于 良的防火性能 、安装简单 、施工速度快等众多优点 。
文章编号 :1007 - 046X(2004) 01 - 0046 - 01
信息报导
利用脱硫石膏制造纸面石膏板
Manufacture of Paper2Facing Plasterboard with Desulphurized Gypsum
国内生产脱硫石膏的工艺
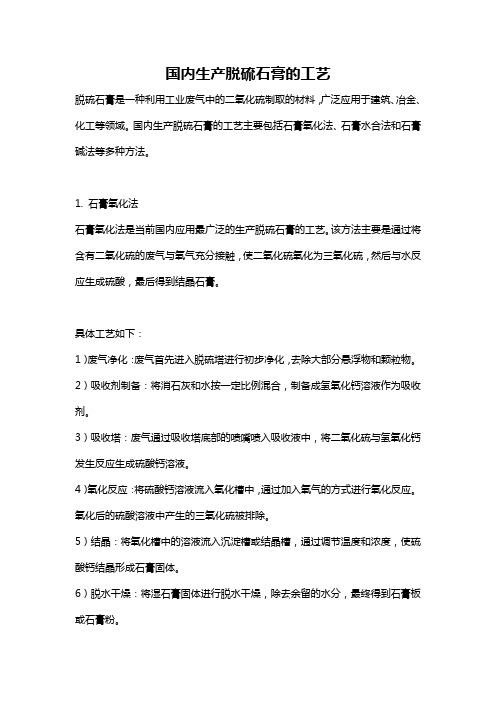
国内生产脱硫石膏的工艺脱硫石膏是一种利用工业废气中的二氧化硫制取的材料,广泛应用于建筑、冶金、化工等领域。
国内生产脱硫石膏的工艺主要包括石膏氧化法、石膏水合法和石膏碱法等多种方法。
1. 石膏氧化法石膏氧化法是当前国内应用最广泛的生产脱硫石膏的工艺。
该方法主要是通过将含有二氧化硫的废气与氧气充分接触,使二氧化硫氧化为三氧化硫,然后与水反应生成硫酸,最后得到结晶石膏。
具体工艺如下:1)废气净化:废气首先进入脱硫塔进行初步净化,去除大部分悬浮物和颗粒物。
2)吸收剂制备:将消石灰和水按一定比例混合,制备成氢氧化钙溶液作为吸收剂。
3)吸收塔:废气通过吸收塔底部的喷嘴喷入吸收液中,将二氧化硫与氢氧化钙发生反应生成硫酸钙溶液。
4)氧化反应:将硫酸钙溶液流入氧化槽中,通过加入氧气的方式进行氧化反应。
氧化后的硫酸溶液中产生的三氧化硫被排除。
5)结晶:将氧化槽中的溶液流入沉淀槽或结晶槽,通过调节温度和浓度,使硫酸钙结晶形成石膏固体。
6)脱水干燥:将湿石膏固体进行脱水干燥,除去余留的水分,最终得到石膏板或石膏粉。
2. 石膏水合法石膏水合法是利用石膏半水化的特性,将硫酸钙水合成石膏的工艺。
该方法适用于含水量较高的废气处理。
具体工艺如下:1)原料准备:将消石灰与二氧化硫废气以一定比例混合,并添加适量的水蒸气。
2)水合反应:消石灰和二氧化硫在适当的温度和湿度条件下发生水合反应,生成石膏半水合物。
3)结晶:将石膏半水合物放在低温高湿的条件下,进行结晶,形成纯度较高的石膏晶体。
4)脱水干燥:将石膏晶体通过脱水干燥的方式去除余留的水分,最终得到石膏板或石膏粉。
3. 石膏碱法石膏碱法是利用氨水或碱性废液与含二氧化硫废气中的二氧化硫反应生成硫酸铵,并通过浓缩、结晶等工艺得到脱硫石膏。
具体工艺如下:1)原料准备:将氨水或碱性废液与二氧化硫废气进行混合,使其发生反应。
2)硫酸铵制备:将氨水或碱性废液中的氨与二氧化硫反应生成硫酸铵溶液。
3)浓缩:将硫酸铵溶液进行浓缩,使其达到一定浓度。
石膏板生产工艺

3.2.2项目工艺、技术方案1、工艺原理纸面石膏板是以建筑石膏为主要原料,掺入适量添加剂做板芯,以特制的板纸为护面,经加工制成的板材。
纸面石膏板具有重量轻、隔声、隔热、加工性能强、施工方法简便的特点。
2、工艺流程简介1)熟料的制备:本项目产品采用的主要原料是电厂产出的脱硫石膏,其主要成分为CaSO4·2H2O,其经过回转窑煅烧后可得到β型半水石膏为主建筑石膏,该过程用方程式表示为:CaSO4·2H2O加热CaSO4·H2O +H2O煅烧后的建筑石膏经冷却后,储存于大料仓,以备用。
2)配料部分:备料:①改性淀粉、缓凝剂、纸浆、减水剂、水等原料经定量计量后放入水力碎煅烧磨料浆机搅拌成原料浆,然后泵入料浆储备罐备用;②发泡剂和水按比例投入发泡剂制备罐搅拌均匀,泵入发泡剂储备罐备用;③、促凝剂和熟石膏粉原料经提升输送设备进入料仓备用;配料:料浆储备罐中的浆料使用计量泵泵入到搅拌机,发泡剂使用动态发泡装置发泡后进入搅拌机,促凝剂和石膏粉使用全自动计量皮带称计量后进入搅拌机,然后所有主辅料在搅拌机混合成合格的石膏浆。
所有主辅料的添加都含括在自动控制系统中,随生产线速度的不同自动调节,以适应大规模、高速度的要求。
3、成型输送部分上纸开卷后经自动纠偏机进入成型机,下纸开卷后经自动纠偏机、刻痕机、震动平台进入成型机,搅拌机的料浆落到震动平台的下纸上进入成型机,在成型机上挤压出要求规格的石膏板,然后在凝固皮带上完成初凝、在输送辊道上完成终凝,经过定长切断机切成需要的长度(2400mm、3000mm或其它),经横向机转向,转向后两张石膏板同时离开横向机,然后使用靠拢辊道使两张板材的间距达到要求后,经分配机分配进入干燥机干燥。
4、烘干部分采用导油锅炉提供热源,经过换热器换出热风后经风机送入干燥机内部完成烘干任务,本干燥机分为7区,能很好的完成石膏板干燥的干燥曲线,干燥机采用热交换及热油管双结合,可完全按照石膏板的干燥特性进行配温、配风,可使石膏板最低能量消耗的情况下最短的时间内进行干燥,能耗量最省,是最经济的高效的石膏板干燥技术。
纸面石膏板生产工艺及应用
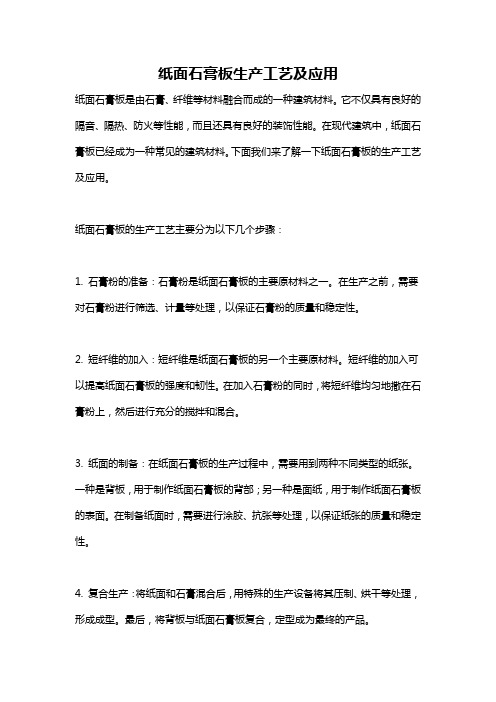
纸面石膏板生产工艺及应用纸面石膏板是由石膏、纤维等材料融合而成的一种建筑材料。
它不仅具有良好的隔音、隔热、防火等性能,而且还具有良好的装饰性能。
在现代建筑中,纸面石膏板已经成为一种常见的建筑材料。
下面我们来了解一下纸面石膏板的生产工艺及应用。
纸面石膏板的生产工艺主要分为以下几个步骤:1. 石膏粉的准备:石膏粉是纸面石膏板的主要原材料之一。
在生产之前,需要对石膏粉进行筛选、计量等处理,以保证石膏粉的质量和稳定性。
2. 短纤维的加入:短纤维是纸面石膏板的另一个主要原材料。
短纤维的加入可以提高纸面石膏板的强度和韧性。
在加入石膏粉的同时,将短纤维均匀地撒在石膏粉上,然后进行充分的搅拌和混合。
3. 纸面的制备:在纸面石膏板的生产过程中,需要用到两种不同类型的纸张。
一种是背板,用于制作纸面石膏板的背部;另一种是面纸,用于制作纸面石膏板的表面。
在制备纸面时,需要进行涂胶、抗张等处理,以保证纸张的质量和稳定性。
4. 复合生产:将纸面和石膏混合后,用特殊的生产设备将其压制、烘干等处理,形成成型。
最后,将背板与纸面石膏板复合,定型成为最终的产品。
纸面石膏板的应用非常广泛。
它主要用于室内隔断、天花板、墙面等装饰和隔音隔热等方面。
具体应用领域包括:1. 室内隔断:纸面石膏板具有良好的防火、隔音和隔热性能,非常适合用于室内隔断。
它可以有效地隔离不同的房间,创造舒适的居住和工作环境。
2. 天花板:纸面石膏板的质地轻盈,安装方便,可以使用各种造型设计,呈现出美观的视觉效果。
它还可以通过加入吸声材料等处理,增强其隔音隔热性能。
3. 墙面装饰:纸面石膏板的表面可以进行各种不同的装饰处理,如喷涂、贴壁纸等。
它不仅可以在视觉上提升房间的美观度,还具有保温和噪声隔绝等功能。
4. 其他装饰:除了以上应用领域外,纸面石膏板还可以用于其他的装饰方面,如柜子、石膏线条、壁板等。
这些产品可以温和而有效地点缀和丰富空间装饰。
总之,纸面石膏板是一种具有多种功能的优质建筑材料。
纸面石膏板生产工艺技术-石膏芯凝固和强度提高
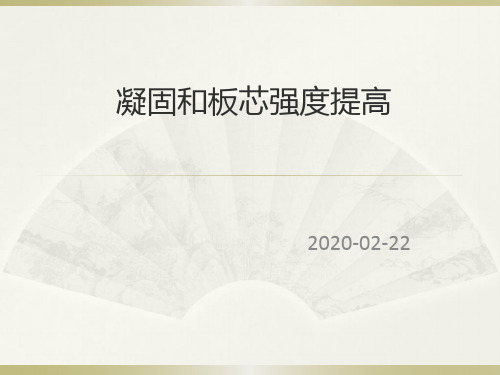
凝固和水合测试
凝固测试
薄刀片法 拇指法 – 参考一定距离用拇指感觉板的硬度 维卡仪 –初凝和终凝 撕纸光洁度
水合测试
石膏浆温度上升曲线 – 在线和离线测试 在最短烘干机入口时间下取石膏浆或湿板放入异
丙醇中,取石膏用于石膏相分析,判断水合效果。 板芯分析-进入干燥机的前缘和后缘 石膏芯强度测试
聚合物工艺可能在将来会是稳定的添加剂
影响强度的杂质
天然石膏Natural Gypsum
大多数的天然杂质不影响石膏芯强度 可溶性盐会消弱石膏芯和护面纸之间的
粘结力 白云石碳酸盐在煅烧炉中分解生成碱性
石膏浆,降低会强度 过烧产生的有机污染物会延缓并导致强
度损失 湿废料分解产生的污染物会导致强度损
过多使用促凝剂会产生过多的小晶体,从 而导致石膏板偏软。提高促凝剂的质量 (增加表面积等)以降低促凝剂的用量。
其它促凝剂
大量的无机酸 氯化物 硝酸盐 大多数硫酸盐和双硫酸盐 硫酸钾“钾”(K2SO4)是最常见
的可溶性化学促凝剂
缓凝剂
由于缓凝剂对晶体形状的影响,使用 缓凝剂通常会导致石膏芯强度的降低
失
影响强度的杂质
合成或副产品石膏中的杂质即使在非 常低的水平下也会导致强度损失
通常脱硫石膏比较正常,但过量氯离 子会降低强度。副产品石膏含有一系 列影响强度的杂质
磷石膏含有磷酸盐和磷酸 柠檬石膏中含有柠檬酸(强力缓凝剂和减
强剂)
大多数杂质通过改变晶体形状和降低 晶体之间的粘结力而导致强度损失
监测石膏芯密度与石膏芯抗压强度 的关系及与工艺效率的关系
板芯强度测试
石膏芯强度提高
强度取决于石膏晶体之间的链接互锁和结合 力
发达国家用脱硫石膏与废石膏制纸面石膏板的进程与经验
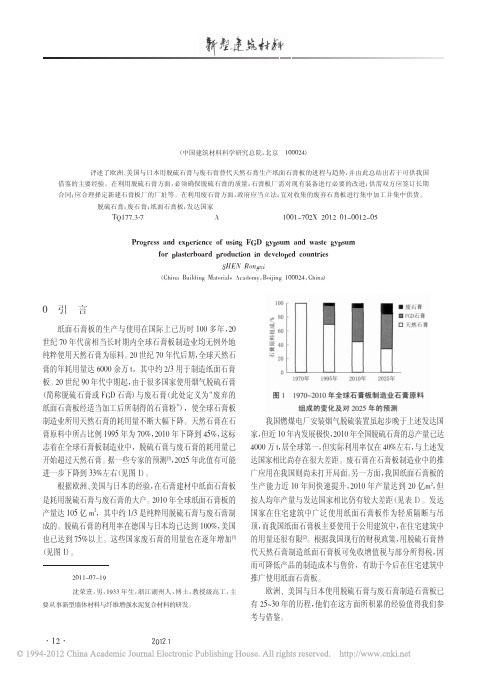
实践逐渐认识到质量符合规定要求的脱硫石膏完全可代替天 Danogips 公司与 BPB 公司生产纸面石膏板的掺量已分别达
然石膏生产此种板材。1993 年德国脱硫石膏的产量仅为 320 到 22%与 25%。
万 t,1995 年达到 500 万 t,近年已增至 700 万 t 以上。原来有
自 20 世纪末期欧盟发布建筑废弃物合理处置的政策法
些德国专家预测,由于德国政府今后将大力发展以核电为主 规以来,对废弃石膏板的再生循环使用起了很大的推动与促
的新能源,因而脱硫石膏的产量会趋于逐年下降。但在 2011 进作用[5]。例如,2002 年欧洲议会发布的 33/2002 决议中规定,
年日本大地震后发生海啸,使核电站遭受严重损坏,引发核污 石膏废弃物只能填埋于无有机废料存在的惰性填埋坑中。这
的空气质量、保护了环境,同时也对其它欧洲国家、日本与美
欧洲在石膏板制造业中使用废石膏始于 21 世纪初期。建
国等采取相应的决策起了极大的推动与促进作用。
于斯堪的纳维亚的国际再生石膏公司(Gypsum Recycling In-
在德国由于电力工业与石膏建材工业的相互配合、密切 ternational,缩写为 GRI)最初向丹麦、芬兰与瑞典等国的石膏
染问题,德国的能源政策可能会有所调整。据此笔者认为,德 是因为废石膏中的 CaSO4 会与有机物起反应生成 H2S。欧盟
国今后 30 年内脱硫石膏产量很可能仍保持现有的水平。
议会规定此决议应在 2005 年开始执行。迄今英国已较好地执
在德国的带动下,自 20 世纪 90 年代初以来,在欧洲很多 行此决议,2010 年将原先可填埋废弃石膏制品的 1000 处减
根据欧洲、美国与日本的经验,在石膏建材中纸面石膏板 是耗用脱硫石膏与废石膏的大户。2010 年全球纸面石膏板的 产量达 105 亿 m2,其中约 1/3 是纯粹用脱硫石膏与废石膏制 成的。脱硫石膏的利用率在德国与日本均已达到 100%,美国 也已达到 75%以上。这些国家废石膏的用量也在逐年增加[1] (见图 1)。
国内外脱硫石膏处理工艺技术现状

国内外脱硫石膏处理工艺技术现状在欧洲、日本或美国,几乎所有的脱硫石膏都应用于建材行业。
我国对脱硫石膏的综合处理技术也已经初步成熟。
目前在国内外大部分的脱硫石膏用于生产纸面石膏板,而另有相当一部分的脱硫石膏用于水泥缓凝剂。
1.国内外脱硫石膏处理工艺技术现状从原材料方面来看,脱硫石膏是与天然石膏等效的原材料,但有一定差异。
主要表现在原始状态、机械性能和化学成分,特别是杂质成分上的差异,从而导致其脱水特征、力学性能、流变性能等特征上与天然石膏有所不同。
脱硫石膏经过干燥、煅烧、冷却、调性后,完全能生产出质量良好的建筑石膏及相关的石膏制品。
从石膏生产工艺技术方面来看,脱硫石膏与天然石膏也是宏观上相似,微观上有一定的区别。
主要体现在原材料的处理上有所不同,即脱硫石膏湿料的处理和煅烧工艺技术装备上有所区别。
在湿料的处理中最主要的设备是湿料仓,湿料仓分为直筒体的储料仓和带曲线形状的出料装置。
出料量的大小可调,且能保证连续稳定。
在德国由WTW公司生产制造的。
杭州中新机电技术有限公司研制的湿料仓和WTW的类似,技术性能也相近。
石膏建材制品的质量取决于建筑石膏粉的质量,而建筑石膏粉的质量是取决于石膏原材料以及煅烧的效率。
因此煅烧是脱硫石膏处理工艺技术中最为关键的。
①气流煅烧工艺气流煅烧即热气体与粉料直接接触,二水石膏迅速脱水而成半水石膏。
这种方式热利用合理,设备紧凑,使用简单,功效高。
德国GRENZEBACH公司及美国BMH公司都有这种设备,前者叫锤式烘干煅烧磨磨,后者称Delta磨。
俗称“气流煅烧磨”,这种“磨”采用高速旋转的锤子将物料抛起并击碎、击细,同时与气流相汇,完成干燥、煅烧的过程。
上述两个设备中锤体的安装方式,锤头的数量,分级器放置的方向等有所不同,但其工作原理是相同的。
锤式烘干煅烧磨集干燥—煅烧为一体,是德国GRENZEBACH公司研制的。
它是一种热烟气的锤式磨机,磨机最侧部为主传动装置,带动直径φ1600mm的转子高速旋转,转子上有多个交叉分布的锤子。
脱硫石膏生产工艺
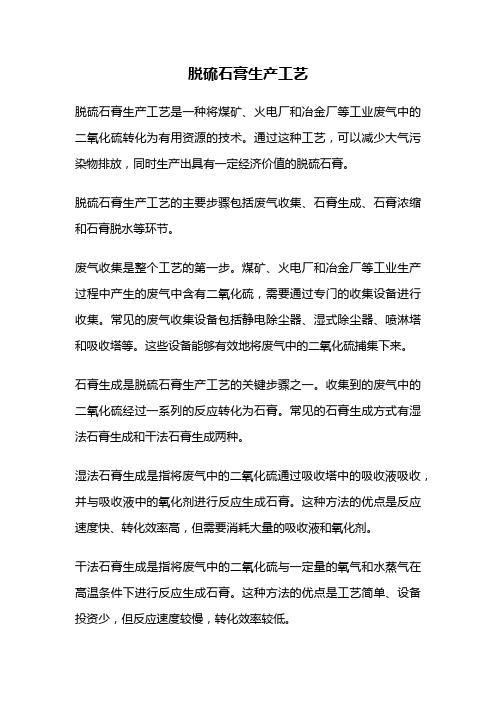
脱硫石膏生产工艺脱硫石膏生产工艺是一种将煤矿、火电厂和冶金厂等工业废气中的二氧化硫转化为有用资源的技术。
通过这种工艺,可以减少大气污染物排放,同时生产出具有一定经济价值的脱硫石膏。
脱硫石膏生产工艺的主要步骤包括废气收集、石膏生成、石膏浓缩和石膏脱水等环节。
废气收集是整个工艺的第一步。
煤矿、火电厂和冶金厂等工业生产过程中产生的废气中含有二氧化硫,需要通过专门的收集设备进行收集。
常见的废气收集设备包括静电除尘器、湿式除尘器、喷淋塔和吸收塔等。
这些设备能够有效地将废气中的二氧化硫捕集下来。
石膏生成是脱硫石膏生产工艺的关键步骤之一。
收集到的废气中的二氧化硫经过一系列的反应转化为石膏。
常见的石膏生成方式有湿法石膏生成和干法石膏生成两种。
湿法石膏生成是指将废气中的二氧化硫通过吸收塔中的吸收液吸收,并与吸收液中的氧化剂进行反应生成石膏。
这种方法的优点是反应速度快、转化效率高,但需要消耗大量的吸收液和氧化剂。
干法石膏生成是指将废气中的二氧化硫与一定量的氧气和水蒸气在高温条件下进行反应生成石膏。
这种方法的优点是工艺简单、设备投资少,但反应速度较慢,转化效率较低。
石膏浓缩是将生成的石膏浆液进行浓缩处理,去除其中的水分,提高石膏的固体含量。
常见的石膏浓缩设备有真空过滤机、压滤机和离心机等。
通过这些设备,可以将石膏浆液中的水分含量从80%左右降低到40%以下。
石膏脱水是将浓缩后的石膏进一步去除水分,使其成为具有一定固体含量的石膏产品。
常见的石膏脱水设备有矿用离心机、压滤机和烘干机等。
通过这些设备,可以将石膏中的水分含量进一步降低,提高石膏的固体含量。
脱硫石膏生产工艺的应用前景广阔。
脱硫石膏作为一种有用资源,可以应用于建材、水泥、石膏板和石膏制品等行业。
同时,脱硫石膏还可以作为土壤改良剂、污水处理剂和废水处理剂等。
通过合理利用脱硫石膏,可以实现废气资源化和循环利用,减少环境污染,促进可持续发展。
脱硫石膏生产工艺是一种将工业废气中的二氧化硫转化为有用资源的技术。
纸面石膏板生产工艺技术-石膏芯体积概念
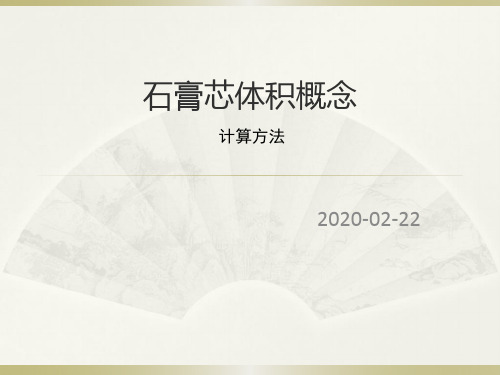
石膏芯体积
假设12.5mm的板芯是100%纯度的石 膏,但是有一半的板芯体积是空气
这种情况下(下纸=200g/m2,厚度 =0.3mm,上纸=170g/m2,厚度=0.27mm), 板的重量一般是14.21kg/m2
石膏芯的体积是50% v:v 这板也很结实,但还是太重了(通常的板
28% gypsum vol 29% gypsum vol
30% gypsum vol
650
70
75
80
85
90
石膏纯度(%)
95
100
重是8.5kg/m2,甚至更低)
石膏芯体积
假设12.5mm的板芯是100%纯度的石 膏,但是有3份的板芯体积是空气
这种情况下(下纸=200g/m2,厚度 =0.3mm,上纸=170g/m2,厚度=0.27mm), 板的重量一般7.29kg/m2
石膏芯的体积是25% v:v 这板也很结实,和大多数石膏板的重量
石膏芯体积概念
计算方法
2020-02-22
石膏芯体积
假设12.5mm实芯的石膏板而且是 100%纯度的石膏
这种情况下(下纸=200g/m2,厚度 =0.3mm,上纸=170g/m2,厚度=0.27mm) 板的重量一般达到28.05kg/m2
石膏芯的体积是100% v:v 这板很结实,但是这太重了(通常的板
再水合石膏体积(%v:v) = 石膏芯体积 总量* 工艺效率
石膏芯体积常量(参考)
板重 (kg/100m²)
1000
950
900
850
800
23% gypsum vol
24% gypsum vol
球团烟气脱硫石膏制纸面石膏板的研究

主讲人:dd
摘要:
本文以球团烟气脱硫石膏为主要原料,采用凝胶注模成型工艺, 研究制备一种新型的轻质、高强度纸面石膏板。试验对球团烟气 脱硫石膏的物化性能进行分析,研究球团烟气脱硫石膏的浆料流 变性能,单体丙烯酰胺、交联剂N,N' -亚甲基双丙烯酰胺加入量 以及发泡剂种类对纸面石膏板性能的影响试验制备的纸面石膏板 配方中,球团烟气脱硫石膏约占90%,充分利用工业副产品,降 低生产成本。
3.3 催化剂和引发剂对石膏浆初凝时间的影响
凝胶注模工艺中催化剂的加入可以使得聚合反应的活化能降低, 从而加速固化反应速率。而引发剂的作用是促使有机单体分子形 成单体自由基,引发浆料的固化反应。实验采用N,N,N,N-四甲基 乙二胺为催化剂,10%的过硫酸铵作为引发剂,引发剂和催化剂 的质量比为2:1. 随着催化剂加入量的增加,浆料初凝时间有下降趋势,引发剂 含量的增加使得浆料中形成的初级自由基的浓度增大,单体聚合 的速度加快,初凝时间,在更短的时间内石膏颗粒原位凝固,成 型效率变高。当催化剂加入量为0.1%时,初凝时间为8min,满足 凝胶注模操作要求。
4.试验结论
1、凝胶注模成型工艺技术适合纸面石膏板的板芯成型,单体丙烯酰胺(AM) 与交联剂N,N'-亚甲基双丙烯酰胺(MBAM)比例为4:2,分别占脱硫石膏总 量的4%、2%,引发剂和催化剂的加入量分别是0.2%和0.1% 2、工业发泡剂可以在球团烟气脱硫石膏制备的板芯内引入泡孔结构。工业 发泡剂加入量为1.1%,体密度降为8.7g/cm3。 3、球团烟气脱硫石膏未煅烧是主要成分是CaSO4·2H2O,通过在200℃的环 境下炒制可得到建筑石膏,主要成分是CaSO4·1/2H2O。建筑石膏制备纸面 石膏板可降低体密度,并能改善力学强度。体密度降为8.7g/cm3,抗折强 度为7.10MPa。
脱硫石膏纸盒生产的工艺流程及方法
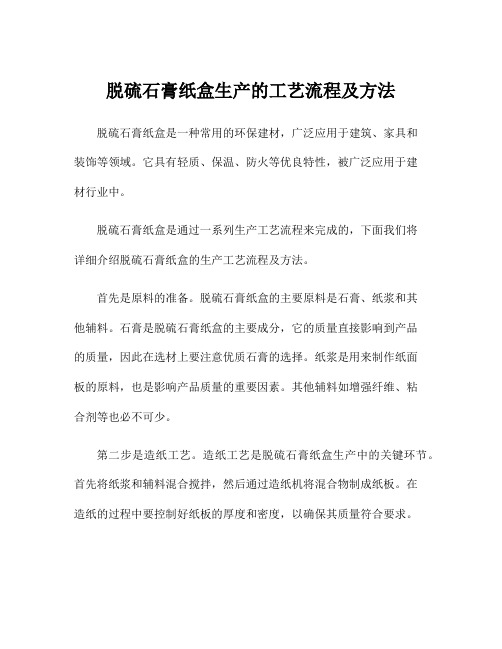
脱硫石膏纸盒生产的工艺流程及方法脱硫石膏纸盒是一种常用的环保建材,广泛应用于建筑、家具和装饰等领域。
它具有轻质、保温、防火等优良特性,被广泛应用于建材行业中。
脱硫石膏纸盒是通过一系列生产工艺流程来完成的,下面我们将详细介绍脱硫石膏纸盒的生产工艺流程及方法。
首先是原料的准备。
脱硫石膏纸盒的主要原料是石膏、纸浆和其他辅料。
石膏是脱硫石膏纸盒的主要成分,它的质量直接影响到产品的质量,因此在选材上要注意优质石膏的选择。
纸浆是用来制作纸面板的原料,也是影响产品质量的重要因素。
其他辅料如增强纤维、粘合剂等也必不可少。
第二步是造纸工艺。
造纸工艺是脱硫石膏纸盒生产中的关键环节。
首先将纸浆和辅料混合搅拌,然后通过造纸机将混合物制成纸板。
在造纸的过程中要控制好纸板的厚度和密度,以确保其质量符合要求。
第三步是石膏混合工艺。
将选好的石膏与辅料混合搅拌,然后通过搅拌机进行混合,确保石膏混合物的均匀性和稳定性。
接着将混合物倒入模具中,经过振实、加压等工艺处理,形成纸盒的基本形状。
第四步是烘干工艺。
将模具中的纸盒送入烘干室,进行烘干处理。
在烘干的过程中,要控制好温度和湿度,以确保纸盒的成型和质量。
最后是涂装和包装工艺。
将烘干后的纸盒进行涂装,增加其表面的平整度和美观度。
最后将涂装后的纸盒进行包装,以便运输和使用。
总体来说,脱硫石膏纸盒的生产工艺流程包括原料准备、造纸工艺、石膏混合工艺、烘干工艺和涂装及包装工艺。
这些工艺流程相辅相成,共同完成了脱硫石膏纸盒的生产。
此外,在生产过程中还有一些关键技术和方法需要掌握。
如在石膏混合工艺中要控制好搅拌时间和搅拌速度,以确保混合物均匀。
在烘干工艺中要控制好烘干时间和温湿度,以避免出现开裂和变形。
在涂装工艺中要选择适合的涂装材料和方法,以确保涂装效果和质量。
综上所述,脱硫石膏纸盒生产工艺流程及方法是一项综合性的工艺,它需要严格控制各个环节和细节,才能生产出质量优良的产品。
只有不断优化工艺流程,提高生产技术水平,才能更好地满足市场需求,推动行业发展。
纸面石膏板生产工艺技术-脱硫石膏

第四章脱硫石膏1. 介绍脱硫法(DSG)是电厂烟气脱硫(FGD) 工艺的产物。
在20 世纪的下半叶, “酸雨”已成为公认的问题,1988 年欧共体指令发布,要求从现有燃煤电厂二氧化硫的排放在应该减少20%,到21 世纪降低40% 以上。
当这些发电厂使用的煤中的硫被燃烧形成二氧化硫(SO2) ,二氧化硫与大气中的水结合形成硫酸(H2SO3) 时,就会产生酸雨。
SO2 + H2O = H2SO3为了除去二氧化硫,烟气用石灰石浆进行洗涤,然后氧化生成石膏:吸收SO2 + H2O = H2SO3中和H2SO3 + CaCO3 = CaSO3 + CO2 + H2O氧化CaSO3 + ?O2 + 2H20 = CaSO4.2H2O (gypsum)FGD 工厂的设计能力是每年减少28 万吨SO2 ,满负荷运行时每年将使用54 万吨石灰石生产80 万吨石膏。
每年可从该脱硫池中提取100 万吨石膏。
2.脱硫工厂以下详细介绍了FGD 工厂和工艺流程。
电厂烟气脱硫在过去十年中,人们越来越认识到有必要减少和控制燃烧矿物燃料的发电厂的二氧化硫(SO2) 排放量,从而减少酸雨的一种成分。
为此,发电厂为了改造足够的燃煤电厂的烟气脱硫(FGD), 以确保一个稳定的二氧化硫排放量下降通过剩余的世纪,因此建立一个提供FGD 设备的发电站。
.姚恒昌1大型燃烧车间成立欧洲经济共同体1988 年6月通过的《大型燃烧工厂指令》要求,到1993 年将现有工厂的二氧化硫排放量减少20% ,到1998 年减少40% ,到2003 年减少60%。
在烟气脱硫装置,由于其体积大,最有可能从烟气排放中脱除二氧化硫。
科学证据表明,排放的二氧化硫对土壤和地表水的酸度有一定影响; 它具有较长的剩余运行寿命,并且可以在现有的工厂配置中安装FGD。
此外,它与FGD 原料(石灰石)和副产品(石膏)市场的潜在来源有良好的地理位置,有足够的运输连接和任何必要改进的潜力。
- 1、下载文档前请自行甄别文档内容的完整性,平台不提供额外的编辑、内容补充、找答案等附加服务。
- 2、"仅部分预览"的文档,不可在线预览部分如存在完整性等问题,可反馈申请退款(可完整预览的文档不适用该条件!)。
- 3、如文档侵犯您的权益,请联系客服反馈,我们会尽快为您处理(人工客服工作时间:9:00-18:30)。
第四章脱硫石膏1. 介绍脱硫法(DSG)是电厂烟气脱硫(FGD)工艺的产物。
在20世纪的下半叶,“酸雨”已成为公认的问题,1988年欧共体指令发布,要求从现有燃煤电厂二氧化硫的排放在应该减少20%,到21世纪降低40%以上。
当这些发电厂使用的煤中的硫被燃烧形成二氧化硫(SO2),二氧化硫与大气中的水结合形成硫酸(H2SO3)时,就会产生酸雨。
SO2 + H2O = H2SO3为了除去二氧化硫,烟气用石灰石浆进行洗涤,然后氧化生成石膏:吸收SO2 + H2O = H2SO3中和H2SO3 + CaCO3 = CaSO3 + CO2 + H2O氧化CaSO3 + ½O2 + 2H20 = CaSO4.2H2O (gypsum) FGD工厂的设计能力是每年减少28万吨SO2,满负荷运行时每年将使用54万吨石灰石生产80万吨石膏。
每年可从该脱硫池中提取100万吨石膏。
2.脱硫工厂以下详细介绍了FGD工厂和工艺流程。
电厂烟气脱硫在过去十年中,人们越来越认识到有必要减少和控制燃烧矿物燃料的发电厂的二氧化硫(SO2)排放量,从而减少酸雨的一种成分。
为此,发电厂为了改造足够的燃煤电厂的烟气脱硫(FGD),以确保一个稳定的二氧化硫排放量下降通过剩余的世纪,因此建立一个提供FGD设备的发电站。
.大型燃烧车间成立欧洲经济共同体1988年6月通过的《大型燃烧工厂指令》要求,到1993年将现有工厂的二氧化硫排放量减少20%,到1998年减少40%,到2003年减少60%。
在烟气脱硫装置,由于其体积大,最有可能从烟气排放中脱除二氧化硫。
科学证据表明,排放的二氧化硫对土壤和地表水的酸度有一定影响;它具有较长的剩余运行寿命,并且可以在现有的工厂配置中安装FGD。
此外,它与FGD原料(石灰石)和副产品(石膏)市场的潜在来源有良好的地理位置,有足够的运输连接和任何必要改进的潜力。
FGD工厂可以减少二氧化硫的排放,当前两个机组投入使用并投入全面商业运行时。
届时使用含硫量高达2.8%的煤炭,每年可减少28万吨二氧化硫自1980年以来,对减少二氧化硫排放的许多方法进行了设计研究。
这包括使用低硫燃料、煤炭清洁、煤/水混合物、流化床燃烧、煤炭气化、联合循环和使用天然气的联合循环燃气轮机。
得出的结论是,电厂只需要考虑其中两项。
这些是石灰岩/石膏系统(生产石膏)和再生系统(生产硫酸)。
有石膏和硫酸的市场。
石灰石/石膏体系是应用最广泛的体系,占世界FGD工厂的主要比例,因此决定选择这种经过良好验证的体系作为FGD工厂。
但是,硫酸的生产是有市场的,因此今后可能要记住这一点。
石灰石/石膏系统具有高效的吸引力,是一种具有市场价值的产品,可用于建筑行业制作墙板、石膏和水泥,也可用于垃圾填埋场和土地复垦的安全处置。
电厂预计每年将消耗约54万吨石灰石,在全站运转并使用煤炭的情况下,将产生约80万吨石膏。
生产的石膏纯度高,氯含量低,适合加工成各种石膏制品,如墙板。
工艺化学的最佳条件取决于对吸收塔再循环浆体的物理化学成分的控制。
这涉及平衡相互竞争的要求,以便达成一项折衷方案,从而使石膏具有令人满意的吸收效率、耗电量和质量。
化学过程描述烟气中的酸性气体二氧化硫被吸收到水基浆体中,然后与浆体中的碱性组分反应中和,在本例中,碱性组分为石灰石中的碳酸钙。
该反应的产物进一步与空气接触,与氧气反应产生高质量的石膏副产品,主要是硫酸钙二水合物,随后从泥浆中除去。
化学工艺烟气脱硫是通过碱性浆液与烟气接触而实现的。
脱硫过程的化学过程是复杂的,但可以简单地表示为三个阶段的过程,包括:吸收SO2+H2O→H2SO3中和H2SO3+CaCO3→CaSO3+CO2+H2O氧化CaSO3+½O2+2H2O→CaSO42H2O要脱硫的烟气首先通过气体/气体加热器冷却,并经过两个预饱和阶段。
过程的物理描述吸收剂浆液与吸收塔内的烟气接触。
烟气向上流动与向下流动的浆体喷淋形成逆流,这是整个过程的吸收阶段。
含二氧化硫的吸收剂浆液落在吸收塔的底部,在此过程中发生中和。
向浆体中注入压缩空气,使钙、硫化合物氧化形成固体硫酸钙产品。
将新鲜原料石灰石引入吸收塔池中,在吸收塔池底部提取石膏浆体时,补充的吸收剂浆体再循环至吸收塔顶部。
在FGD安装一节中对所涉及的工艺设备作了更详细的说明。
通常电厂FGD装置的设计准则如下:•能够从烟气中除去90%的二氧化硫•获得至少97.5%的可用性•能够在两次大停电之间运行38个月•拥有40年的生命•生产墙板质量石膏•以含硫量不超过2.8%及氯气含量不超过0.6%的煤所产生的气体,达致操作设计锅炉炉单元的烟气通过升压风机从静电除尘器进入烟气脱硫装置,然后进入吸收装置,在吸收装置中,二氧化硫通过含石灰石的浆液喷淋去除。
烟气脱硫装置排出的气体以成对的烟道排放到现有烟囱的大气中。
在吸收过程中,烟气的温度会降低,但离开烟囱的烟气必须具有足够的浮力,以确保其上升和扩散。
因此,提供了一种气体/气体再热器,用于在气体进入吸收塔之前对其进行冷却,并在吸收塔和烟囱之间对其进行再加热。
石灰石准备碎石灰石由物料处理厂运往三个石灰石沙坑,每个沙坑的容量为860公吨。
采用喂料方式,以最高50.5吨/小时的速度喂给湿式石灰石球磨机。
这些卧式机器装有大型钢球,当磨机的滚筒旋转时,钢球会压碎石灰石。
产生的石灰浆机从轧机流入石灰岩磨水力旋流器贮水槽,从那里是石灰石水力旋流器,泵的水力旋流器溢流通过浆饲料箱转移到吸收器,包含超大颗粒的底流返回到磨机。
石灰石浆槽充满后,旋流器系统进入回收模式。
每单位满载所需石灰石量为450公吨/24小时;这是基于指定的最低质量石灰石。
过程描述烟气,通过现有的静电除尘器和风机,在温度为115°C - 130°C到脱硫增压风扇的压力增加到克服的阻力脱硫工厂气体通道。
气体进入气/气加热器冷却到90°C。
热火放弃转轮再生气体/释放气体加热器来加热处理气体冷却到80°C以上回到脱硫后烟囱。
进气烟道气进入吸收塔下部区域的速度,其设计目的是将预饱和区内的扰动降至最低。
吸收体进口管道是用水清洗的,以防止固体在湿/干界面堆积和结垢,这也有助于冷却进入的烟气。
紧急提供喷雾淬火的烟气,假如温度超过110°C。
然后气体通过吸收塔预饱和区,在预饱和区安装分配板,以促进通过吸收塔的均匀流动模式。
配流板下端面与气体同时清洗,采用向上指向的吸收体浆液喷嘴。
这些连同向下指向的喷嘴,是由预饱和喷雾泵在压力下提供的。
在这一过程中,粉煤灰和非硫酸气体也被大量吸收。
FGD 洗涤单元部分.FGD灰岩浆和石膏浓缩段单元主要的二氧化硫吸收(以及任何剩余气体和灰尘的冲刷)发生在气体被循环泥浆擦洗的过程中,这些泥浆从吸收塔的底部抽取,并从分设在塔内五个不同高度的喷嘴中喷射出来。
泥浆液滴向下(逆流)喷射到气体流中,每个喷射液位都有自己的专用循环泵由于过程化学的结果,再循环浆体主要是石膏,按重量计算约17%为固体,0.67%为石灰石。
污水池中的一部分浆液被不断地抽出,泵入石膏分离和脱水阶段进行处理。
根据需要,通过操作不同数量的喷雾水平(阶段)来调整烟道气中SO2的不同浓度(由燃烧的煤炭产生)。
为了达到所需的吸收效率,本设计要求煤中1.06%的硫分三步使用,2.0%的硫分四步使用,2.8%的硫分五步使用。
经过洗涤的气体通过三组雪佛龙气体分离器进入燃气/燃气加热器。
前两个除雾器组(设置为垂直流动)位于吸收塔顶部,第三个除雾器组(设置为水平流动)位于吸收塔出口管道内。
选择这种组合是为了获得最佳的液滴去除效率。
除雾器被分成若干部分,这些部分被间歇性和周期性地清洗,以防止固体颗粒堆积。
第二排的除雾器用工艺水清洗。
收集洗涤物并与更多的工艺补水一起用于清洗第一个除雾器组。
工厂所需的所有工艺用水都是从工厂的冷却系统中提取的。
它以多种方式进入工艺系统,主要是作为吸收剂蒸发损失的补充,以及除雾器和离心洗涤。
正常情况下,每台机组满载时的工艺用水量为3150吨/天。
在最后一节冷却处理,现在在约50°C,通过气体/气体加热器,其温度提高到80°C以上排放烟囱。
石膏分离和脱水吸收体浆液从池底提取,利用水力旋流系统进行一次石膏分离。
不论烟气的入口SO2浓度如何,抽提都是按恒定速率进行的。
水力旋流系统的初级阶段产生一个含有粗石膏晶体的下流,按重量计算,石膏的浓度约为45%。
然后将这些增稠的浆液泵入位于普通工厂区域的脱水系统。
溢流从一次旋流器通过二次旋流器进料槽,从二次旋流器进料槽泵入二次旋流器。
以石膏为主的一次旋流回流到吸收塔,二次旋流溢流是将系统中的氯化物净化的手段,以及主要由粉煤灰和石灰石中的一些杂质组成的“细粉”。
这条小溪在被抽到污水处理厂之前,会经过当地的一个净化池。
石膏脱水离心机系统接收来自一次旋流器下流的稠化浆液。
该系统由42台立式离心机、间歇式离心机组成,其生产的产品含有约8%的游离水分,需要将石膏脱水到这一水平,以使其适合于输送机和轨道车辆的搬运。
离心机被分成6组,每组7台机器,每组机器将产品卸到各自的输送机上。
此外,一系列输送机将脱水石膏输送到石膏储存大楼。
离心机除去的浓缩液,连同饼洗、篮洗水,以及任何补充水,被用作石灰石磨机生产石灰石浆的水。
石灰石的运输和储存石灰石处理厂负责从铁路或公路上运送压碎的石灰石。
交付的货物分为重150吨的铁路料斗或重63吨的公路料斗,并配有变速牵引杆给料机和装载输送机,然后将其排放到石灰石仓库。
在铁路运输的情况下(每列火车最多1500t),材料处理是通过100%重复的设备流。
道路处理是通过一条输送管道进入石灰岩商店。
物料在仓库内的分配是通过重复的穿梭输送机进行的。
利用门式刮板回收机对石灰岩储层中的物料进行回收。
这台机器和输送石灰石到沙坑的输送机是复制的。
每条管道的输送能力为100%,通过穿梭输送机将其输送到地堡。
此外,公司还提供了一系列额外的设备,包括磁选机、皮带秤、垃圾筛、接线楼转移装置、应急跳绳设备等。
回收设备是独立的工厂包装,通过电缆卷筒提供完整的电力供应。
工厂配备了防尘设备。
除卸轨作业外,全厂实行远程操作。
现场储存35600t石灰石,消耗14天,由6x660兆瓦燃煤机组脱硫,脱硫煤含硫量为2.0%,氯含量为0.3%。
石灰石可以以最高每天3420吨的速度被送入加工厂的燃料库。
石膏的处理石膏副产品将用于石膏板和相关产品的商业生产。
任何不符合规格的石膏,将与粉末状燃料灰混合,在允许的处置范围内储存在专门地方。
石膏物料处理场通过石膏输送机将脱水石膏从脱水厂房中提取。
交付速率最高可达600t/hr,这取决于正在使用的离心机数量。
石膏通过一系列输送机输送至可容纳58880t石膏的有盖石膏库,在库内分布采用穿梭输送机。