消除锥形穿孔机毛管端部尾圈方法探讨
锥形辊穿孔机导板的优化设计
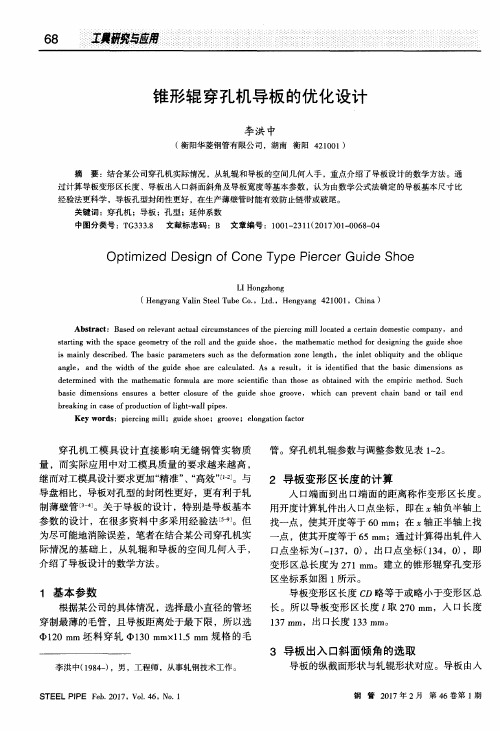
s t a r t i n g wi t h t h e s p a c e g e o me t r y o f t h e r o l l a n d t h e g u i d e s h o e ,t h e ma t h e ma t i c me t h o d f o r d e s i g n i n g t h e g u i d e s h o e
穿孑 L 机工模具设计 直接影 响无缝钢管实 物质 管 。穿孔机轧辊要求越来越高 , 继而对工模具设计要求更加“ 精准” 、 “ 高效” O - 2 3 。与 导 盘相 比,导板对 孔 型 的封 闭性 更好 ,更 有 利于 轧
i s ma i n l y d e s c r i b e d . T h e b a s i c p a r a me t e r s s u c h a s t h e d e f o r ma t i o n z o n e l e n g t h, t h e i n l e t o b l i q u i t y a n d t h e o b l i q u e a n g l e ,a n d t h e wi d t h o f t h e g u i d e s h o e a r e c a l c u l a t e d .As a r e s u l t ,i t i s i d e n t i i f e d t h a t t h e b a s i c d i me n s i o n s a s d e t e r mi n e d w i t h t h e ma t h e ma t i c f o r mu l a a r e mo r e s c i e n t i f i c t h a n t h o s e a s o b t a i n e d wi t h t h e e mp i r i c me t h o d .S u c h
关于锥形辊穿孔机轧辊转速对毛管分层缺陷影响的讨论

Dicu so fIfa n e b n y e c rRo s s in o n le c y Co e T pe Pir e Spe d o elL e n Sh l am ia i f c nt on De e t
Ti n ng a Da
se di as eyi otn. h ao u lyd fc soc  ̄ n h o etp ire rc s i ih e p e s l v r o mp r tT em jr ai eet c u igi tec n epecrpo esw t hg d a q t a n y h
js b “ i tea ge , a dta ecmmo x ln t nfrted vlp n f h h llmiaini n tre ut y bg o n l” n th o h t ne pa ai e eo me t es ela n t o u o o h ot o s t
(TajnSe l ieG o pC r.Ld, ini 0 3 ,C ia) ini te Pp ru op, t.Tajn 3 0 0 1 hn
Ab t a t t s p i t d o t h tlk h a r lt p i r e r c s ,t e c n r lo h o e t p i r e o l s r c :I o n e u a i e t e b re y e p e c rp o e s h o to ft e c n y e p e c rr l i t
Ф460mm锥形辊穿孔机主传动系统的改造
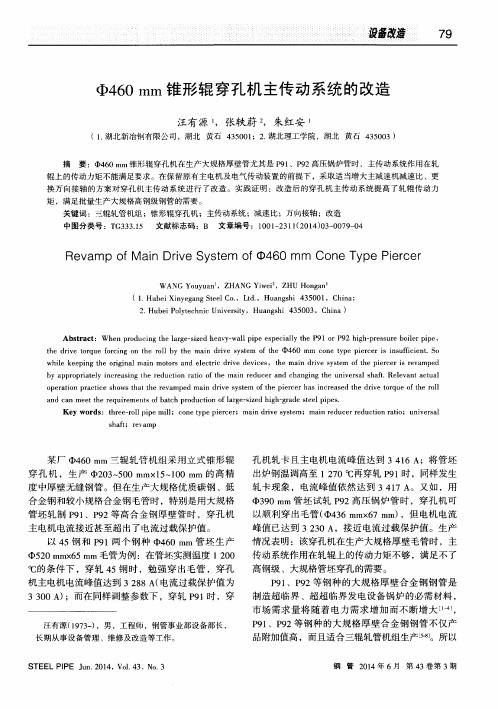
7 9
4 6 0 mm锥 形 辊 穿孑 L 机 主传 动 系统 的改造
汪有 源 ,张轶蔚 z ,朱红安 -
( 1 . 湖北新冶钢有 限公 司,湖北 黄石 4 3 5 0 0 1 ;2 . 湖北理工学院 ,湖北 黄石 4 3 5 0 0 3)
.
一 ~ . 一 ~ 一 . 一 { - 一 蓁 兰 一 . ~ . ~ 一 一
摘
要 :@4 6 0 m m锥形辊穿孑 L 机在生产 大规格厚 壁管尤其是 P 9 1 、P 9 2高压锅炉管时 ,主传动系统作用在轧
辊上的传动力矩不能满足要 求。在保 留原有主 电机及 电气传 动装 置的前提下 ,采取适当增大主减速机减速比 、更 换万 向接 轴的方案对 穿孔 机主传动 系统进行 了改造 。实践证 明 :改造后 的穿孔机 主传 动系统提 高了轧辊传动 力
合金 钢 和较 小 规格合 金 钢毛 管时 ,特 别是 用 大规 格 管 坯 轧制 P 9 1 、P 9 2等 高合 金 钢厚 壁 管 时 ,穿 孔 机 主 电机 电流 接 近甚 至超 出 了电流 过载 保护 值 。
以4 5钢 和 P 9 1两 个 钢 种 @4 6 0 m m 管 坯 生 产
@3 9 0 mm管 坯 试 轧 P 9 2高 压 锅 炉管 时 ,穿 孔机 可 以顺 利 穿 出毛 管 ( @4 3 6 mi nx 6 7 mm) ,但 电机 电流
穿 孔 机 ,生 产 2 0 3 ~ 5 0 0 m mx l 5 ~ 1 0 0 m m 的 高 精
度 中厚 壁无 缝 钢管 。但 在生 产大 规格 优质 碳 钢 、低
矩 ,满 足 批 量 生 产 大 规 格 高 钢级 钢管 的需 要 。
关键词 :j 三 辊轧管机组 ;锥 形辊 穿孔 机 ;主传动 系统 ;减速 比;万向接轴 ;改造
锥形辊穿孔机的工作原理和特点

锥形辊穿孔机的工作原理和特点锥形辊(菌式)穿孔机在穿孔中可使轧辊的表面速度和金属在穿孔过程中增加的流动速度相一致,减少作用在毛管上的剪切应力,降低能耗,使毛管表面光洁、壁厚均匀。
其工作原理如图1所示。
两轧辊的轴线既倾斜又交叉,以便能够通过较大的喂入角β和辗轧角γ实现穿孔。
轧辊成圆锥形、双支撑。
轧辊的圆周速度沿着出口方向有规律地提高,并与穿孔毛管的运动速度相匹配,轧辊对毛坯有拉伸或阻碍作用。
由此使斜轧穿孔中的回转锻造效应、表面扭曲变形及圆周剪切变形都受到一定程度的抑制,使毛管内、外表扭曲变形及圆周剪切变形都受到一定程度的抑制,使毛管内、外表面缺陷大为减少。
其导卫装置可采用导板,比较先进的采用主动大导盘。
图1锥形辊穿孔机的特点如下:(1)回转锻造效应受到抑制。
为了使轧辊的布置适合于穿孔过程的进行,除了喂入角β,又设置了辗轧角γ,轧辊成锥状、双支撑。
实验结果表明,管坯和毛管的力学性能、伸长率和断面压缩率在很大程度上取决于轧辊的辗轧角和喂入角的大小。
β和γ值越大,伸长率和压缩率也越大。
金属显微镜观察表明,回转锻造效应受到明显的抑制,孔腔缺陆几乎见不到。
与此相反,以较小的喂人角和辗轧角进行穿孔时,回转锻造效应非常明显,孔腔缺陷清楚可见。
(2)金属流动合理。
在辗轧角和喂入角变化的情况下进行穿孔实验,观察喂入角β和辗轧角γ对圆周剪切变形的影响。
圆周剪切变形可用下式表达:实验中明显看出,喂入角β对圆周剪切变形有很大影响。
当β成比例增大时,γrQ值明显下降;同样,辗轧角γ增大时,γrQ也明显下降。
特别明显的是:当γ=15°、β≥14°或者γ=20°、β≥10°时,圆周剪切变形完全消失,即γrQ=O。
轧辊辗轧角和喂入角对表面扭曲变形的影响也很明显,特别是当辗轧率较高时,金属流动不产生表面扭曲而引起剪切变形。
在大辗轧角和大喂人角条件下进行穿孔,周向剪切变形和表面扭曲变形受到严格控制,甚至为零,使金属流动速度基本相同。
消除穿孔毛管尾端“铁耳子”的新工艺

消除穿孔毛管尾端“铁耳子”的新工艺罗德金;褚光胜;王雪飞【摘要】介绍了毛管“铁耳子”、“铁圈圈”的分布形态、危害及其生成机理,重点分析了管坯尾端热定心消除穿孔毛管尾端“铁耳子”的新工艺.试验结果表明:采用管坯尾端热定心新工艺可有效地消除穿孔毛管尾端的“铁耳子”、“铁圈圈”,改善穿孔毛管尾端几何形状,有利于装芯棒轧制,提高作业率及成材率.【期刊名称】《钢管》【年(卷),期】2015(044)006【总页数】4页(P48-51)【关键词】热轧无缝钢管;管坯尾端;热定心;“铁耳子”【作者】罗德金;褚光胜;王雪飞【作者单位】攀钢集团成都钢钒有限公司,四川成都610303;济南斯帝图普冶金工程技术有限公司,山东济南250100;攀钢集团成都钢钒有限公司,四川成都610303【正文语种】中文【中图分类】TG333.8在热轧无缝钢管生产中,供给延伸机轧制的空心坯料(穿孔毛管)一般是由二辊斜轧穿孔机穿轧生产[1]。
穿孔机穿制毛管是热轧无缝钢管生产中的重要工序。
穿孔毛管的质量好坏直接影响成品无缝钢管的质量和产量。
由于穿孔变形的固有特点及其金属材料的内应力[2],穿制毛管尾端常常产生“铁耳子”或者“铁圈圈”,对延伸工艺造成危害,是长期困扰热轧无缝钢管生产的难题。
1 毛管“铁耳子”分布形态及危害穿孔机在穿制毛管过程结束时,穿孔毛管尾部往往产生“铁耳子”、“铁圈圈”。
这种“铁耳子”、“铁圈圈”多数在穿孔结束时脱落在穿孔机底座,被冷却水冲入氧化铁皮沟排到铁皮沉淀池。
穿孔机下部氧化铁皮沟内被水冲不走的“铁耳子”、“铁圈圈”勾结在一起,生产时间长了通常采用氧割清除。
穿孔结束未脱落而被毛管带出的“铁耳子”、“铁圈圈”呈3种形态分布在穿孔毛管尾端:①与管尾内壁端撕裂的“铁耳子”,一头自由伸出,一头与管尾体仍然连接,毛管尾端“铁耳子”如图1所示;②“铁圈圈”的一部分与管尾内壁端撕裂离开管尾体,未撕裂部分仍然与管尾体内壁端连接,毛管尾端“铁圈圈”(撕裂)如图2所示;③“铁圈圈”完好但已经伸出管尾体,仍然与管尾体内壁端连接,毛管尾端“铁圈圈”(未撕裂)如图3所示。
两种机型穿孔钢管的内螺旋产生原因及控制
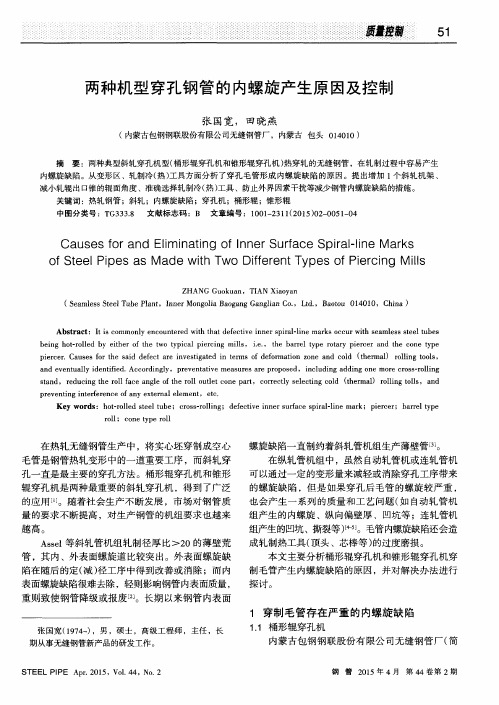
5 1
两种机型 穿孔钢 管 的内螺旋产生 原 因及控制
张 国宽 , 田晓 燕
(内蒙古包钢钢联股份有限公司无缝钢 管厂 ,内蒙古 包头 0 1 4 0 1 0)
摘
要 :两种典型斜轧穿孑 L 机型( 桶 形辊 穿孑 L 机和锥形辊穿孑 L 机) 热穿轧的无缝钢管 ,在轧制过程 中容易产生
ZH ANG Guo k ua n, TI AN Xi a oy a n
( S e a ml e s s S t e e l T u b e P l a n t ,I n n e r Mo n g o l i a B a o g a n g G a n g l i a n C o . ,L t d . ,B a o t o u 0 1 4 0 1 0 ,C h i n a)
a nd e v en t ua l l y i d en t i f i e d.Ac c or d i ng l y, pr e ve nt a t i v e me a s ur es a r e pr o po s e d, i nc l u di n g a ddi ng o ne mo r e c r o s s — r o l l i ng
b e i n g h o t — r o l l e d b y e i t h e r o f t h e t wo t y p i c a l p i e r c i n g mi l l s ,i . e . ,t h e b a r r e l t y p e r o t a r y p i e r c e r a n d t h e c o n e t y p e
r o l l :c on e t y pe r o l l
去毛刺常用方法分析(全文)
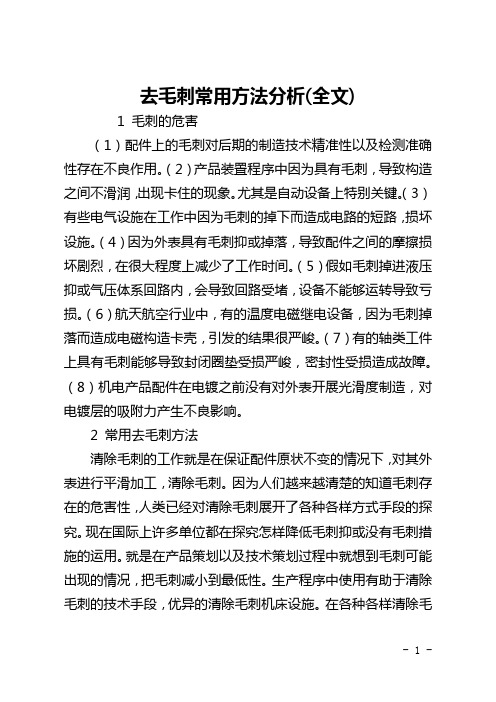
去毛刺常用方法分析(全文)1 毛刺的危害(1)配件上的毛刺对后期的制造技术精准性以及检测准确性存在不良作用。
(2)产品装置程序中因为具有毛刺,导致构造之间不滑润,出现卡住的现象。
尤其是自动设备上特别关键。
(3)有些电气设施在工作中因为毛刺的掉下而造成电路的短路,损坏设施。
(4)因为外表具有毛刺抑或掉落,导致配件之间的摩擦损坏剧烈,在很大程度上减少了工作时间。
(5)假如毛刺掉进液压抑或气压体系回路内,会导致回路受堵,设备不能够运转导致亏损。
(6)航天航空行业中,有的温度电磁继电设备,因为毛刺掉落而造成电磁构造卡壳,引发的结果很严峻。
(7)有的轴类工件上具有毛刺能够导致封闭圈垫受损严峻,密封性受损造成故障。
(8)机电产品配件在电镀之前没有对外表开展光滑度制造,对电镀层的吸附力产生不良影响。
2 常用去毛刺方法清除毛刺的工作就是在保证配件原状不变的情况下,对其外表进行平滑加工,清除毛刺。
因为人们越来越清楚的知道毛刺存在的危害性,人类已经对清除毛刺展开了各种各样方式手段的探究。
现在国际上许多单位都在探究怎样降低毛刺抑或没有毛刺措施的运用。
就是在产品策划以及技术策划过程中就想到毛刺可能出现的情况,把毛刺减小到最低性。
生产程序中使用有助于清除毛刺的技术手段,优异的清除毛刺机床设施。
在各种各样清除毛刺手段中,手工清除毛刺方式对毛刺尺寸、毛刺匀称性以及严峻性要求都不高。
但是使用机器抑或电化学方式清除毛刺就对其尺寸、匀称以及严峻性有一定程度的需求。
我们要想到工件的材料,工件制造时的手段,工件的大小、形状,出现毛刺的位置以及毛刺自身的尺寸。
在不影响零件大小精准度、外貌和方位精准度的根本上,符合最佳规范,并且还要想到不能出现二次毛刺。
在众多去毛刺方法中,机械去毛刺是最早、最广泛采纳的方法,其特点是使用简单,成本低。
使用锉刀、固结砂轮、铲刀、钢丝刷、针刷、研磨砂带及油石等带磨料的材料都属于此类方法。
但随着ZG制造业竞争日益激烈,对产品质量要求也日益提高,此类加工的零件质量精度已不能满足更为严格的标准要求。
穿孔毛管质量缺陷及其预防

四、穿孔毛管质量缺陷及其预防1穿孔是热轧无缝钢管变形的第一道工序也是最重要的变形工序之一。
其作用是将实心管坯穿制成空心毛管。
穿孔方式纵轧穿孔、斜轧穿孔。
①纵轧穿孔压力冲孔、推轧穿孔。
管坯不发生旋转。
②斜轧穿孔二辊式锥式、桶式、曼式、盘式两个轧辊两个导板。
三辊式由三个旋转的轧辊组成穿孔孔型。
管坯在轧辊的作用下一边旋转一边前进。
2穿孔毛管的质量缺陷产生原因①由管坯本身的缺陷或管坯在加热过程中产生的缺陷。
②在穿孔工序中产生的它是由于穿孔工艺参数设计或调整不正确穿孔工具形状不合理穿孔工具表面存在质量缺陷等原因造成的。
3穿孔毛管质量缺陷主要包括毛管的壁厚不均内直道、外直道表面结疤、划伤内折、外折、离层一纵轧穿孔工艺与质量缺陷1 工艺特点毛管内孔是依靠冲顶头“顶”出来的压力冲孔立式冲孔卧式冲孔推轧穿孔斜轧管坯的冲孔变形过程主要是在三向压应力状态下完成的因此对管坯中心部分的疏松和缩孔会起到压实的效果所以压力冲孔工艺可以改善管坯的低倍组织缺陷为后续延伸工序提供质量良好的冲孔坯。
对于一些塑性较差不宣采用直接穿孔工艺生产的高合金无缝钢管管坯可以先进行压力冲孔再进行延伸轧制。
2 纵轧穿孔毛管质量缺陷及其预防①冲穿孔坯壁厚不均工艺原因加热温度不均造成。
预防措施a. 应保证管坯加热均匀最小阻力定律防止严重烧损。
b. 尽可能使管坯的中心线与冲杆顶杆中心线重合注意调整冲杆顶杆导向系统其间隙不能过大。
c. 防止冲杆顶杆弯曲应保证其有足够大的抗弯强度。
d. 压力冲孔机的十字头导向装置和推轧穿孔机的管坯导卫装置的调整必须保证管坯中心线与轧制中心的对准和稳定。
②冲穿孔坯内外直道a. 产生原因冲头顶头是在极其恶劣的高温、高压环境下工作的其端部一旦产生严重的变形或粘钢冲头顶头在与管坯内表面所产生的相对运动中就会将管坯内表面刮伤而形成内直道。
b. 预防措施为了防止冲穿孔坯产生内、外直道缺陷应加强对冲头顶头、冲模轧辊的冷却提高其使用寿命宜采用高强耐热钢来制造冲头顶头一旦发现粘钢就要及时修磨或更换。
无缝钢管穿孔机介绍
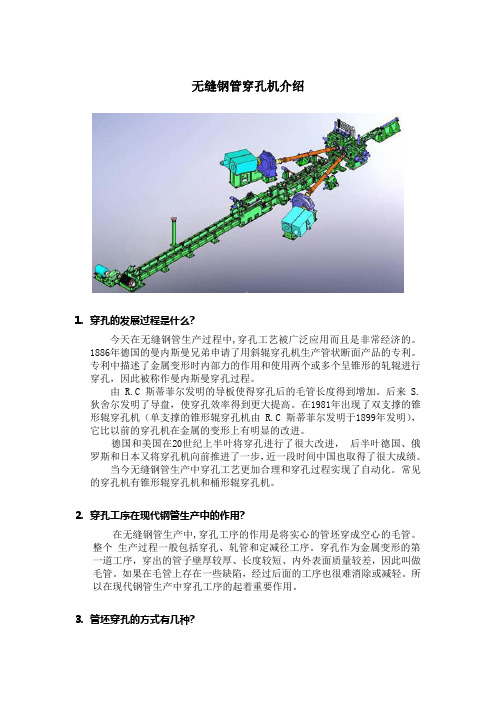
无缝钢管穿孔机介绍1.穿孔的发展过程是什么?今天在无缝钢管生产过程中,穿孔工艺被广泛应用而且是非常经济的。
1886年德国的曼内斯曼兄弟申请了用斜辊穿孔机生产管状断面产品的专利。
专利中描述了金属变形时内部力的作用和使用两个或多个呈锥形的轧辊进行穿孔,因此被称作曼内斯曼穿孔过程。
由R.C 斯蒂菲尔发明的导板使得穿孔后的毛管长度得到增加。
后来S.狄舍尔发明了导盘,使穿孔效率得到更大提高。
在1981年出现了双支撑的锥形辊穿孔机(单支撑的锥形辊穿孔机由R.C 斯蒂菲尔发明于1899年发明),它比以前的穿孔机在金属的变形上有明显的改进。
德国和美国在20世纪上半叶将穿孔进行了很大改进,后半叶德国、俄罗斯和日本又将穿孔机向前推进了一步,近一段时间中国也取得了很大成绩。
当今无缝钢管生产中穿孔工艺更加合理和穿孔过程实现了自动化。
常见的穿孔机有锥形辊穿孔机和桶形辊穿孔机。
2.穿孔工序在现代钢管生产中的作用?在无缝钢管生产中,穿孔工序的作用是将实心的管坯穿成空心的毛管。
整个生产过程一般包括穿孔、轧管和定减径工序。
穿孔作为金属变形的第一道工序,穿出的管子壁厚较厚、长度较短、内外表面质量较差,因此叫做毛管。
如果在毛管上存在一些缺陷,经过后面的工序也很难消除或减轻。
所以在现代钢管生产中穿孔工序的起着重要作用。
3.管坯穿孔的方式有几种?管坯的穿孔方式有压力穿孔,推轧穿孔和斜轧穿孔。
(1)压力穿孔压力穿孔是在压力机上穿孔,这种穿孔方式所用的原料是方坯和多边形钢锭。
工作原理是首先将加热好的方坯或钢锭装入圆形模中(此圆形模带有很小的锥度),然后压力机驱动带有冲头的冲杆将管坯中心冲出一个圆孔。
这种穿孔方式变形量很小,一般中心被冲挤开的金属正好填满方坯和圆形模的间隙,从而得到几乎无延伸的圆形毛管,延伸系数最大不超过1.1。
(2)推轧穿孔推轧穿孔是在推轧穿孔机上穿孔,这种穿孔方式是压力穿孔的改进。
把固定的圆锥形模改成带圆孔型的一对轧辊。
这对轧辊由电机带动方向旋转(两个轧辊的旋转方向相反),旋转着的轧辊将管坯咬入轧辊的孔型,而固定在孔型中的冲头便将管坯中心冲出一个圆孔。
穿孔机常见质量问题

常见质量缺陷及成因1.壁厚不均毛管壁厚不均分纵向壁厚不均和横向壁厚不均。
毛管纵向壁厚不均主要由管坯长度方向上温度差造成毛管头尾壁厚差引起的。
常见的壁厚不均是壁厚不均,其特征是毛管横截面上薄壁部分或厚壁部分呈螺旋分布,主要形式有:1.1前端穿偏:毛管前端部分壁厚不均明显——管坯咬入过程不稳定,由于管坯前端断面不平,管坯椭圆度过大,入口导管尺寸过大或严重磨损,轧辊转速过高或磨损严重,导致管坯咬入更加不稳定,顶头对中不好。
——轧制线偏离管坯咬入一段距离后,轧制趋于稳定,管坯自动对中,形成前端壁厚不均。
1.2后端穿偏,毛管尾部壁厚不均——管坯温度低;顶杆弯曲后刚度不够;顶杆后部分定心辊工作不正常抱紧力不够或打开过早,造成顶杆剧烈跳动。
1.3毛管通体横向壁厚不均——管坯径向加热不均(大螺旋形分布)——两辊之间轧线偏2.外表缺陷2.1外表螺旋划伤——导盘、升降辊、定心辊等划破毛管表面。
——轧辊上有凹坑(间隔性外伤);2.2外折或发纹(呈螺旋形分布的鳞片状折叠或细发状裂纹)——材质问题或管坯过热3.内折内表面呈螺旋形或无规则分布的锯齿状折叠或裂纹,产生原因有:——管坯内部的冶炼与加工质量不好,尤其是管坯端部有较长的缩孔;——管坯加热质量不好(过热、过烧)——顶前量过大——顶头磨损或粘附金属——孔型设定不合理——芯棒磨损严重4.内结疤(硼砂)见硼砂部分5.尾端穿破——辊速过高,应适当降低——调整导盘与轧辊的间隙尽量小(1~2MM)——轧辊角度减小6.尾部穿不透——辊速过高,应适当降低——增加顶前量——关闭冷却水轧制。
穿孔机毛管“鱼尾”的产生原因及改善措施
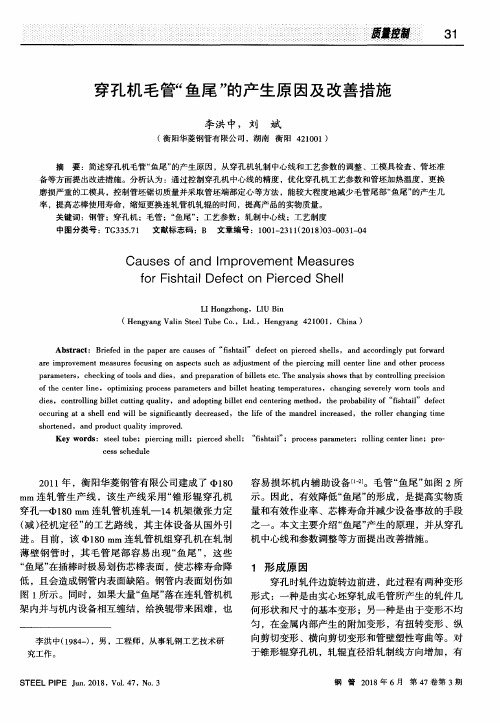
容 易损 坏 机 内辅 助 设 备 [· 。 毛管 “鱼尾 ”如 图 2所 示 。因此 ,有效 降低“鱼尾”的形成 ,是提高实物质 量和有 效 作业 率 、芯棒 寿命 并减 少设 备事 故 的手段 之一 。本文主要介绍“鱼尾”产生的原理 ,并从穿孔 机 中心线 和参 数调 整等 方 面提 出改善 措施 。
图 2 毛 管“鱼 尾 ”
效 减少 了扭 转 变形 ,但纵 向剪切 变形 依然 存 在 ,这 是 产 生 “鱼 尾 ”的根 本 原 因 。纵 向剪 切 变 形 主 要 是 由顶 头受 轴 向阻 力造 成 的 ,穿 -fbH,t ̄L辊 带 动外 层 金 属 沿 纵 向 流 动 , 而顶 头 阻 碍 内层 金 属 的 纵 向流 动 ,结 果各 层 的轴 向流 动产 生差 异 ,而 金属 是一 个
Key words: steel tube; piercing mill; pierced shell; “f ishtail”; process parameter; rolling center line; pro— cess schedul
201 1年 ,衡 阳华菱钢管有限公 司建成 了 l80 m m 连 轧 管 生 产线 ,该 生 产 线 采 用 “锥 形 辊 穿 孔 机 穿孔—中l80 mm连轧管机连轧一 l4机架微 张力定 (减 )径机定径 ”的工艺路线 ,其 主体设备从 国外 引 进 。 目前 ,该 O180 mm 连轧 管 机组 穿 孔 机 在 轧制 薄 壁 钢 管 时 ,其 毛 管 尾 部 容 易 出现 “鱼 尾 ”,这 些 “鱼尾 ”在插棒时极易划伤芯棒表面 ,使芯棒寿命 降 低 ,且会 造成 钢管 内表 面 缺 陷。钢 管 内表 面划 伤如 图 1所 示 。同时 ,如果 大 量 “鱼 尾 ”落在 连轧 管 机机 架 内并 与机 内设备 相互 缠结 ,给换 辊带来 困难 ,也
- 1、下载文档前请自行甄别文档内容的完整性,平台不提供额外的编辑、内容补充、找答案等附加服务。
- 2、"仅部分预览"的文档,不可在线预览部分如存在完整性等问题,可反馈申请退款(可完整预览的文档不适用该条件!)。
- 3、如文档侵犯您的权益,请联系客服反馈,我们会尽快为您处理(人工客服工作时间:9:00-18:30)。
消除锥形穿孔机毛管端部尾圈方法探讨
作者:祁继锋
来源:《科学与技术》2018年第27期
摘要:管坯在穿孔时,由于塑性变形内外表金属流动性不均匀,致使毛管尾端产生尾圈,在连轧机工序生产时会将尾圈带入钢管尾部,造成芯棒划伤或在管体内表产生轧疤,掉落在机架孔型内时会将机架辊划伤,通过优化环形炉温度加热及轧制参数(辊距、导板距、前伸量、喂入角),基本消除穿孔毛管尾圈改善钢管质量,提高轧机工模具的寿命,保证生产的连续性。
关键词:环形炉;加热工艺;穿孔机;调整参数;尾圈;消除
引言
在生产无缝钢管的穿孔工序中,毛管尾端经常会产生尾圈。
连轧机工序进行毛管插棒时,尾圈易被带入钢管内,造成芯棒划伤或在管体内表产生轧疤,掉落在机架孔型内时会将机架辊划伤,影响正常产线生产。
某些轧管厂采取管坯尾端定心的办法消除尾圈,采取改进环炉加热温度及时间,穿孔优化工艺调整参数的方法,在消除毛管尾圈方面取得了很好的效果。
1 尾圈形成原因
穿孔机在轧制加热好的管坯时,边旋转边前进,有两种变形:一种是由实心管坯轧制成毛管所产生的轧件几何形状和尺寸的基本变形;另一种是由于变形不均匀,在金属内部产生的附加变形,有扭转变形、纵向剪切变形、横向剪切变形和管壁塑性弯曲等。
对于锥形辊穿孔机,轧辊直径沿轧制线方向增加,有效减少了扭转变形,但纵向剪切变形依然存在,这是产生尾圈的根本原因。
纵向剪切变形主要是由于顶头受轴向阻力造成的,穿孔时轧辊带动外层金属沿纵向流动,而顶头阻碍内层金属的纵向流动,结果各层的轴向流动产生差异,而金属是一个整体,故各层间必然产生相互附加剪切变形和附加剪应力,致使内层金属的纵向变形速度落后于外层金属,在管坯尾端产生外凸,在辗轧过程中形成尾圈。
如果管坯内外表温度加均匀,温差较小的情况下,尾圈较小,且掉落在穿孔机孔型内;如果壁厚均匀,尾圈呈环状;如果尾端壁厚不均,则呈不规则状。
为了消除尾圈,需要尽量减小纵向剪切变形,同时还要保证钢管壁厚均匀。
2 生产中存在的问题
无缝Φ460mm PQF 连轧管生产线采用锥形辊穿孔机,其主要工艺参数如下(以Φ380 mm 管坯生产Φ325 mm×8普管为例)。
管坯外径380 mm;毛管外径430mm。
环炉各段加热温度:预热一段900℃,预热二段1110℃,加热一段1240℃,加热二段1295℃,加热三段1295℃,均热一段1285℃,均热二段1285℃,管坯在炉支数达到230支,出料节奏在65秒/
支时,管坯在炉时间4.15小时,穿孔顶头直径344mm,长度685mm,顶前压下量27.52mm,顶前压下率5.91%,相对压下率13.16%,前伸量230mm,辊距330mm,导板距370mm,顶头角度4.445,顶头正弦值0.077,入口辊面角度2.5°,出口辊面角度3.8°,入口辊面角度正弦0.044,出口辊面角度正弦值0.066,导板角度7.5°,导板角度正弦值0.13。
采用以上工艺参数生产时,毛管尾端尾圈较大,比较严重,严重的时候尾圈掉进连轧管机架之间堆满,造成轧机辊表面划伤,严重影响管体表面质量,影响正常生产。
最初采取管坯锯切设备后,设计定心机设备,使用碳棒进行电磁波定心,能够起到一定作用,但效率太低,并且成本高,设备稳定性较差,以出现故障,不能满足生产需要;后来采取人工气割定心,但是工人劳动强度大,气割定心质量也不能得到保证。
因此决定从环炉加热质量及穿孔工艺的角度着手解决这个问题。
3 合理加热管坯,优化穿孔轧制参数
由尾圈的形成机理可知,消除尾圈的产生需要尽量减少纵向剪切变形,Φ460 mm PQF 连轧管机组设计Φ48m环形炉使用天然气进行加热管坯,按照管坯加热速度7分钟/厘米的加热速度,根据能量传递规律,炉内的管坯加热主要通过辐射进行加热,保证加热的均匀性,减小内外温差值,目前的加热模式不能满足在炉时间及热量的均匀渗透,穿孔的轧制参数也不利于金属的流动的均匀性,为保证管坯在炉时间及温度的渗透性,减小内外温差,增加穿孔轧制时轧件变形时金属的均匀流动性,因此考虑重新调整环形炉布料角度及加热温度,调整穿孔孔型参数,理论上环形炉进行炉底设计槽位,增加布料的均匀性,按照同一角度布料,可以将在炉支数由230支增加到260支,在炉时间延长0.5小时,保证了加热的均匀性;增大加热段度数,提高预热二段的温度,保证加热时的渗透性;将温度整体提高,各段加热温度:预热一段900℃,预热二段1160℃,加热一段1260℃,加热二段1315℃,加热三段1315℃,均热一段1280℃,均热二段1280℃,增加热辐射的整体能量,适当拉大加热段与均热段的温差,防止管坯表面温度过高里面温度低的现象,造成穿孔不咬。
第二,优化穿孔轧制参数,理论上要求顶头辗轧段母线与轧辊旋转时辊面弧线平行,才能够保证钢管壁厚均匀。
利用Auto CAD 软件对穿孔变形进行三维模拟,要求穿孔变形尽量平缓、防止集中变形,以达到减少轧件纵向剪切变形的目的,因此对穿孔前伸量的值进行增加优化。
加长的原则一是保证轧辊入口锥长度满足咬入条件,其二是保证穿孔二次咬入。
孔型椭圆度进行优化,减小导板距增大辊距,使椭圆度减小,便于轧制时的变形,在有效减小纵向剪切变形。
调整喂入角,减小喂入角,均匀轧辊的线速度,增强轧制时的稳定性。
调整穿孔速降比,采取慢快慢的轧制模式,在抛钢时慢速有利于金属流动的均匀性,从而减少扭曲变形。
4 生产应用情况
优化前,生产325×8普管系列时,穿孔后毛管尾端尾圈严重,连轧插棒时时把尾圈带到钢管内,直接造成质量降级处理,后工序探伤掉队率达到60%以上,连续生产3 个班次后,钢管表面出现外轧疤,检查发现连轧管机辊面划伤非常严重,造成生产中断更换轧机机架。
优化设计后,采用调整后的轧制参数,生产顺利,毛管尾端平整,无尾圈或尾圈很小。
优化前,采用
原来加热工艺及轧制参数轧制毛管2635支,出现尾圈的就有2031支,所占比例为77.08%;优化设计后,轧制毛管2169支,只有36支出现铁耳子,所占比例为1.66%。
优化设计前后出现尾圈的比例由77.08降为1.66%,探伤合格率提升到96%以上,基本上消除了毛管尾端尾圈。
检查钢管质量时没有发现钢管内壁压入尾圈的现象;芯棒表面的划伤也大大得到了改善,连轧及更换机架时发现机架间尾圈也非常少,在軋辊使用周期内再也没有发生因轧辊表面被划伤而更换的情况。
5 结语
穿孔机穿孔时毛管尾端产生尾圈,在连轧管机穿棒时带入钢管内,不仅影响钢管表面质量,还容易划伤芯棒,降低芯棒使用寿命;尾圈还容易掉进连轧管机机架间,造成轧辊表面划伤。
通过优化环形炉加热工艺及调整轧制参数,基本消除了穿孔毛管尾圈,即使个别情况出现尾圈,也非常小,连轧插棒时不会把尾圈带到钢管内,也不会影响产品质量及正常的生产。
(作者单位:烟台鲁宝钢管)。