汽车CAE技术的新进展——虚拟试验场(VPG)技术
虚拟试验场VPG技术汽车CAE技术的最新进展
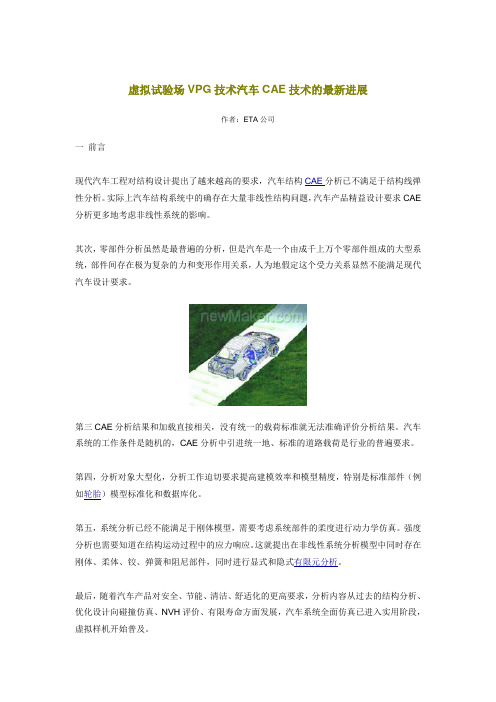
虚拟试验场VPG技术汽车CAE技术的最新进展作者:ETA公司一前言现代汽车工程对结构设计提出了越来越高的要求,汽车结构CAE分析已不满足于结构线弹性分析。
实际上汽车结构系统中的确存在大量非线性结构问题,汽车产品精益设计要求CAE 分析更多地考虑非线性系统的影响。
其次,零部件分析虽然是最普遍的分析,但是汽车是一个由成千上万个零部件组成的大型系统,部件间存在极为复杂的力和变形作用关系,人为地假定这个受力关系显然不能满足现代汽车设计要求。
第三CAE分析结果和加载直接相关,没有统一的载荷标准就无法准确评价分析结果。
汽车系统的工作条件是随机的,CAE分析中引进统一地、标准的道路载荷是行业的普遍要求。
第四,分析对象大型化,分析工作迫切要求提高建模效率和模型精度,特别是标准部件(例如轮胎)模型标准化和数据库化。
第五,系统分析已经不能满足于刚体模型,需要考虑系统部件的柔度进行动力学仿真。
强度分析也需要知道在结构运动过程中的应力响应。
这就提出在非线性系统分析模型中同时存在刚体、柔体、铰、弹簧和阻尼部件,同时进行显式和隐式有限元分析。
最后,随着汽车产品对安全、节能、清洁、舒适化的更高要求,分析内容从过去的结构分析、优化设计向碰撞仿真、NVH评价、有限寿命方面发展,汽车系统全面仿真已进入实用阶段,虚拟样机开始普及。
现代汽车工程对CAE 提出了新的要求,并且将提出更高的要求。
CAE行业只有适应这种挑战才能得到发展。
二现代非线性软件述评面对前述汽车工程对CAE软件的要求,CAE 软件业的第一个应对是纷纷发展大型高度非线性软件。
目前在世界范围内,发展最早、理论最坚实、方法最完全、能够同时进行显式和隐式有限元分析、采用超并行处理、在汽车业中用户最多的当数LS-DYNA 。
鉴于汽车CAE 界对大型高度非线性软件LS-DYNA已有全面了解,这里就不多重述。
大型商业化通用高度非线性软件,一般是面对全工程界的。
从道理上讲,功能虽然有别,但是大体上是可以满足本文第一节所提及的汽车CAE 分析要求,或部分要求。
汽车CAE工程分析

汽车CAE工程分析汽车公司建立高性能的计算机辅助工程分析系统,其专业CAE队伍与产品开发同步地广泛开展CAE应用,在指导设计、提高质量、落低开发本钞票和缩短开发周期上发扬着日益显著的作用。
CAE应用于车身开发上成熟的方面要紧有:刚度、强度、NVH分析、机构运动分析等;而车辆碰撞模拟分析、金属板件冲压成型模拟分析、疲乏分析和空气动力学分析的精度有进一步提高,已投进实际使用,完全能够用于定性分析和革新设计;虚拟试车场整车分析正在着手研究,此外还有焊装模拟分析、喷涂模拟分析等。
汽车公司建立高性能的计算机辅助工程分析系统,其专业CAE队伍与产品开发同步地广泛开展CAE应用,在指导设计、提高质量、落低开发本钞票和缩短开发周期上发扬着日益显著的作用。
CAE应用于车身开发上成熟的方面要紧有:刚度、强度〔应用于整车、大小总成与零部件分析,以实现轻量化设计〕、NVH分析〔各种振动、噪声,包括摩擦噪声、风噪声等〕、机构运动分析等;而车辆碰撞模拟分析、金属板件冲压成型模拟分析、疲乏分析和空气动力学分析的精度有进一步提高,已投进实际使用,完全能够用于定性分析和革新设计,大大减少了这些费用高、周期长的试验次数;虚拟试车场整车分析正在着手研究,此外还有焊装模拟分析、喷涂模拟分析等。
一、刚度和强度分析有限元法在机械结构强度和刚度分析方面因具有较高的计算精度而到普遍采纳,特别是在材料应力-应变的线性范围内更是如此。
另外,当考虑机械应力与热应力的偶合时,像ANSYS、NASTRAN等大型软件都提供了极为方便的分析手段。
〔1〕车架和车身的强度和刚度分析:车架和车身是汽车中结构和受力都较复杂的部件,关于全承载式的客车车身更是如此。
车架和车身有限元分析的目的在于提高其承载能力和抗变形能力、减轻其自身重量并节约材料。
另外,就整个汽车而言,当车架和车身重量减轻后,整车重量也随之落低,从而改善整车的动力性和经济性等性能。
〔2〕齿轮的弯曲曲折折曲曲折折折折应力和接触应力分析:齿轮是汽车发动机和传动系中普遍采纳的传动零件。
CAE-基于DYNA的新一代整车仿真技术

• VPG—虚拟试验场(Virtual Proving Ground )
汽车CAE行业
革命性进展
(五大进展)
进展一:整车非线性分析
• 分析对象:整车非线 性,使汽车零部件结 构分析中载荷难以确 定的难题得以解决。
• 载荷都是真实载荷, 更能满足汽车整车性 能分析要求,如舒适 性、行驶操纵稳定性 分析的要求。
• 一种模型,多种分析
• 零部件的结构分析 • 动力学分析 • 运动学分析 • 疲劳寿命分析
• 专业评价
• 依据FMVSS 和ECE 法规进行乘 员安全保护评价。
• 根据FFT变换进行NVH评价
VPG 疲劳寿命分析
应力数据
疲劳寿命评估
VPG NVH评价
• NVH — Noise, Vibration & Harshness
• 许可用户输入保存自己的路面数据。 • 准备录用海南汽车试验场路面数据。
进展四:分析过程专业化
• 多年汽车CAE仿真工作经验 基础。
• 吸取汽车CAE用户应用经验 和专家意见。
• 配置FMVSS(美国联邦机动 车安全标准)
• 配置ECE/EEC(欧洲经济委 员会/ 汽车排放系统)
进展五:分析评价多样化
频域数据
VPG技术—汽车CAE行业的革命性进展
传统过程
VPG 过程
构造 悬挂系统模型
构造 VPG 模型
试验生成 道路载荷
构造部件模型
有限元分析
实时分析
后处理 应力结果
后处理 应力结果
专业评价
VPG 前处理器
轮胎模型生成器 悬挂数据库
碰撞 & 安全性 模型
CAE技术及其在汽车行业中的应用(最新整理)

CAE技术及其在汽车行业中的应用宋新旺(金陵科技学院机电工程学院,江苏南京211169)摘要:汽车CAE技术对降低产品开发成本、缩短产品研发周期具有重要的意义,改变了汽车研发的传统模式,国外汽车CAE技术的应用已经十分成熟,几乎渗透到了汽车开发的各个环节。
随着国内汽车自主研发能了的快速发展,汽车CAE技术作为整车开发中的核心技术之一,已经引起了主机厂足够的重视,掌握和利用好汽车CAE技术是缩短和赶超国外先进水平的关键。
关键词:CAE技术应用领域汽车行业是一个告诉发展的行业,其竞争也日趋激烈,新产品推出的速度也越来越快,这也对CAE应用提出了越来越多的要求。
CAE技术为汽车行业的高速发展提供了有力的技术保障,为企业带来了巨大的经济效益。
一、CAE技术简介1、CAE技术及CAE软件计算机辅助设计、计算机辅助制造技术已经在一些大中型企业里得到应用,并取得比较好的成绩。
计算机辅助制造技术包括:1、CAD——计算机辅助没计2、CAM——计算机辅助制造3、CAE——计算机工程分析。
以上三种计算机辅助制造技术并不完全是独立的制造辅助技术,他们通过各种软件进行交叉分析,力图实现设计与分析的一体化,以简化设计过程,从而提升产品的品质,改善产品的性能。
例如,CAD软件重在制作二维和三维的图形,以表现事物的主要特征。
对于物体的内部特征,CAD软件往往用剖视图对模型进行剖视。
但是这种表示方法并不能直观的体现复杂机构的内部构成,不利于机械的设计与进一步的改进。
这时就要建立物体的三维模型,对物体图形直接进行CAE分析。
此时,CAD/CAE技术就很好的解决了工程设计与计算相脱节的问题,对实现并进行工程设计提供了技术基础。
在互相结合交叉发展的同时,CAD,CAM,CAE又分别在自己的领域进行突破性的发展。
在这三者之中,C A E软件的主要功能是借助计算机,实现在产品生产以前对设计方案进行精确试验、分析和论证——即利用CAE技术进行真实模拟。
CAE技术及其在汽车行业中的应用

CAE技术及其在汽车行业中的应用宋新旺(金陵科技学院机电工程学院,江苏南京211169)摘要:汽车CAE技术对降低产品开发成本、缩短产品研发周期具有重要的意义,改变了汽车研发的传统模式,国外汽车CAE技术的应用已经十分成熟,几乎渗透到了汽车开发的各个环节。
随着国内汽车自主研发能了的快速发展,汽车CAE技术作为整车开发中的核心技术之一,已经引起了主机厂足够的重视,掌握和利用好汽车CAE技术是缩短和赶超国外先进水平的关键。
关键词:CAE技术应用领域汽车行业是一个告诉发展的行业,其竞争也日趋激烈,新产品推出的速度也越来越快,这也对CAE应用提出了越来越多的要求。
CAE技术为汽车行业的高速发展提供了有力的技术保障,为企业带来了巨大的经济效益。
一、CAE技术简介1、CAE技术及CAE软件计算机辅助设计、计算机辅助制造技术已经在一些大中型企业里得到应用,并取得比较好的成绩。
计算机辅助制造技术包括:1、CAD——计算机辅助没计2、CAM——计算机辅助制造3、CAE——计算机工程分析。
以上三种计算机辅助制造技术并不完全是独立的制造辅助技术,他们通过各种软件进行交叉分析,力图实现设计与分析的一体化,以简化设计过程,从而提升产品的品质,改善产品的性能。
例如,CAD软件重在制作二维和三维的图形,以表现事物的主要特征。
对于物体的内部特征,CAD软件往往用剖视图对模型进行剖视。
但是这种表示方法并不能直观的体现复杂机构的内部构成,不利于机械的设计与进一步的改进。
这时就要建立物体的三维模型,对物体图形直接进行CAE分析。
此时,CAD/CAE 技术就很好的解决了工程设计与计算相脱节的问题,对实现并进行工程设计提供了技术基础。
在互相结合交叉发展的同时,CAD,CAM,CAE又分别在自己的领域进行突破性的发展。
在这三者之中,C A E软件的主要功能是借助计算机,实现在产品生产以前对设计方案进行精确试验、分析和论证——即利用CAE技术进行真实模拟。
汽车虚拟试验技术

2. 全量取样法 全量取样法就是将汽车排气试验中的全部排气采集 到一个有足够大容积的气袋中以供分析。
2020/3/4
3. 定容取样(CVS)法 定容取样法是一种接近于汽车排气扩散到大气中的 实际状态的取样法。它是用经过滤的清洁空气对样气进 行稀释,经热交换器保持恒温,使稀释样气密度保持不 变,然后在定容泵作用下,抽取固定容积流量的样气送 入大气,在定容泵入口前的流路上,将稀释样气经滤清 器、取样泵、针形阀、流量计、电磁阀抽入气袋中。取 样气体和定容泵的流量之间有严格的比例关系。
2020/3/4
2. 与国际接轨的现行国家排放标准 国家技术监督局曾于1999年3月10日颁布了4项国家汽车排 放标准。分别是«汽车排放污染物限值及测试方法»(GB14761— 1999)、«压燃式发动机和装用压燃式发动机的车辆排放污染物 排放限值及测试方法»(GB17691—1999)、«压燃式发动机和装 用燃式发动机的车辆排气可见污染物排放限值及测试方法 »(GB3847—1999)、«汽车用发动机净功率测试验方法»(GB/ T 17692—1999)。
2020/3/4
2020/3/4
第三节 汽车排放标准
1 国外汽车排放法规与控制历程
汽车排放控制最早起源于美国的加利福尼亚州, 1960年,美国加利福尼亚州颁布了世界上第一部汽车排放 法规。 1963年美国政府制定了«大气清洁法»,其后进行 了多次修订和补充,逐步严格化。从1968年起美国才有了 联邦汽车排放标准,之后几乎是逐年严格化。
• 一、VPG技术简介 • 1995年ETA(Engineering Technology Associates,
Inc.)公司提出VPG(Virtual Proving Ground,汽 车虚拟试验场)技术,构制统一平台,简化建模 过程,引入虚拟试验场,从而只需建立一个整车 模型(过程简单),能在汽车真实试验条件(真 实路面载荷)下,进行整车非线性虚拟样机仿真, 达到动态参数设计的目的。
VPG技术在汽车中的应用

2006年第7期农业装备与车辆工程【技术与交流】VPG技术在汽车中的应用胡经国1,刚宪约1,张鲁邹2,苏炳玲3(1.山东理工大学交通与车辆工程学院,山东淄博255049;2.青岛大学机电工程学院,青岛266071;3.山东交通职业学院机械系,潍坊261206)摘要:虚拟试验场(VPG)技术以整车为研究对象,以Ls-Dyna为求解工具,全面考虑各种非线性因素和实际载荷工况,可以实现对汽车的碰撞、乘员安全、疲劳寿命和NVH等的精确仿真。
VPG具有标准的路面、轮胎、悬架、假人数据库和参数化的碰撞试验方案,可以大大简化建模,提高虚拟试验的标准化。
关键词:虚拟试验场;汽车碰撞;乘员保护;NVH中图分类号:U467.1文献标识码:A文章编号:1673-3142(2006)07-0032-04TheApplicationofVPGTechniquesinAutomobileHuJingguo1,GangXianyue1,ZhangLuzou2,SuBingling3(1.SchoolofTraffic&VehicleEngineering,ShangdongUniversityofTechnology,Zibo255049,China;2.SchoolofElectromechanicalEngineering,QingdaoUniversity,Qingdao266071,China;3.MechanicDepartmentofShandongTrafficVocationalCollege,Weifang261206,China)Abstract:ThetechniqueofVIRTUALPROVINGGROUNDtakestheentirevehicleasresearchobject,andtakesLs-Dynaasthetooltogettheanswer.Ithasconsiderinmanykindsofnonlinearfactorsandtheactualloadingconditions.Itcanbeusedtorealizetheaccuratesimulationofvehiclecollision,thesafetyofcrewmembers,thefa-tiguelife,NVHandsoon.VPGhasstandarddatabaseofroadsurface,tire,suspensionsystem,andthedummy.Ithasparameterizedcollisionexperimentplanaswell.Itcansimplifythemodelinggreatlyandenhancethestan-dardizationofthevirtualexperiment.KeyWords:virtualprovingground;vehiclecrash;crewmembersprotection;NVH收稿日期:2006-03-24作者简介:胡经国(1980-),男,山东淄博人,山东理工大学交通与车辆工程学院在读硕士研究生,研究方向为车身CAD技术。
基于虚拟试验场的电动汽车动力电池包随机振动试验开发研究
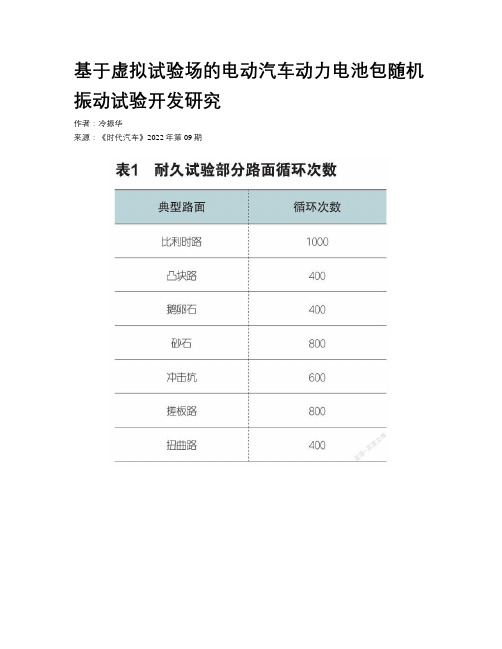
基于虚拟试验场的电动汽车动力电池包随机振动试验开发研究作者:***来源:《时代汽车》2022年第09期摘要:电动车动力电池一般布置在汽车下部车身,在车辆完整的生命周期内承受路面传递的振动激励,因此振动试验是电池包设计开发中重要的一个环节。
目前主流主机厂和电池包生产厂家在进行振动试验时一般直接引用国内外主流电池包标准中指定的振动试验标准,但电池包承受的振动激励的大小与不同车型的车身和悬架结构强相关,这就导致振动试验的标准无法模拟电池包在整车上的真实使用情况。
本文介绍了一种基于虚拟试验场技术,可以无需试验样车仅通过仿真计算获得电池包实际载荷谱,然后基于损失等效原理获得电池包振动试验所需的PSD的方法,可以在项目前期开发出与整车耐久目标相匹配的电池包振动耐久试验,提高验证的精度。
关键词:虚拟试验场电池包振动试验Abstract:The electric vehicle power battery is generally arranged in the lower body of the vehicle, and bears the vibration excitation transmitted by the road during the complete life cycle of the vehicle. Therefore, the vibration test is an important part of the design and development of the battery pack. At present, mainstream OEMs and battery pack manufacturers generally directly refer to the vibration test standards specified in the domestic and foreign mainstream battery pack standards when conducting vibration tests, but the magnitude of the vibration excitation experienced by the battery pack is strongly related to the body and suspension structure of different models, which makes the vibration test standard unable to simulate the real use of the battery pack on the vehicle. This paper introduces a method based on the virtual test field technology, which can obtain the actual load spectrum of the battery pack through simulation calculation without the need for a test vehicle, and then obtain the PSD required for the vibration test of the battery pack based on the loss equivalence principle, which can be developed in the early stage of the project. A battery pack vibration durability test that matches the vehicle's durability target is carried out to improve the verification accuracy.Key words:virtual proving ground, battery pack, vibration test1 引言当前随着国家政策的支持以及电机、电池和电控三电技术的成熟发展,各大主机厂和新势力均加大了对电动智能汽车的布局和研发投入,并且销量占比也在持续增大。
CAE-轿车设计中CAE仿真分析

六 轿车开发中CAE的应用
轿车产品的四个阶段, 筹划阶段; 概念设计和可行性研究; 产品设计和原型车确认; 定型生产等四个阶段。
需18-32个月时间。CAE 技术在开发工作的后三个阶段 都有十分重要的应用。
轿车更侧重时代流行潮流和舒适性,现代轿 车市场生命时间越来越短,一般变型车设计变化最 大的是车身。所以车身是轿车开发的重点
六 轿车开发中CAE的应用
产品设计重点是白车身
白车身设计的一个重点是交叉节结构的 连接方法。它对车身刚度、强度都有
较大的 影响。 必要时 应该进 行重点 分析研 究。
六 轿车开发中CAE的应用
确认设计:解决问题并进行投产准备:
l 针对实验产生的问题(疲劳、NVH、轻 量化、碰撞安全、噪声等问题)进行有目的 分析,提出问题点的焦点,改进的对策。
l 消除汽车的卡嗒声(Rattle)
l 有产品图纸、资料、试验结果。对产品 进行详细分析,结果保存为技术档案。进行 技术总结。这是验证分析条件,建立CAE规范 的大好时机。
六 轿车开发中CAE的应用
确认设计--解决问题、进行投产准备:
l 变形车开发中应用 CAE l 工艺设计和生产准用
# CAE软件的现代进展
• CAE总体发展趋势向专业化方向发 展
• CAE分析功能大幅度提高
– 分析对象: – 分析项目: – 应用科目: – 分析内容: – 分析类别:
• 分析周期与CAD设计同步
• 使用方法简化,应用和结果明确直 观
二 CAE 在汽车技术上的应用
要求对分析入口文件、模型化方法、加 载、分析结果处理、评价标准等建立本企 业的标准化的统一方法。 分析不因人 而异,分析结果纵横对比,评价客观。提 升CAE结果应用价值。不满足于 个案的对 比分析。
基于H-VPG技术的整车虚拟验证

基于H-VPG技术的整车虚拟验证马亮;袁志丹【摘要】新一代的H-VPG技术(虚拟试验场混合模型,Hybrid-Virtual Proving Ground),考虑计算量的原因首先将整车模型考虑为柔性梁结构,可精确反映实车系统的结构特点;然后用柔性梁结构的整车模型的仿真结果与实车试验数据进行对标,当两者的结果匹配后,再把柔性梁替换成柔性体结构,这样就可以通过标定后的柔性体结构的整车模型直接获得零件准确的应力结果,从而使仿真更为真实、全面与快捷。
【期刊名称】《智能制造》【年(卷),期】2018(000)008【总页数】6页(P39-44)【关键词】虚拟试验场;整车模型;技术;验证;仿真结果;柔性梁;梁结构;混合模型【作者】马亮;袁志丹【作者单位】[1]上海信聚信息技术有限公司;[1]上海信聚信息技术有限公司;【正文语种】中文【中图分类】U467.51新一代的H-VPG技术(虚拟试验场混合模型,Hybrid-VirtualProvingGround),考虑计算量的原因首先将整车模型考虑为柔性梁结构,可精确反映实车系统的结构特点;然后用柔性梁结构的整车模型的仿真结果与实车试验数据进行对标,当两者的结果匹配后,再把柔性梁替换成柔性体结构,这样就可以通过标定后的柔性体结构的整车模型直接获得零件准确的应力结果,从而使仿真更为真实、全面与快捷。
一、引言在现代机械工业中,有80%以上的结构强度破坏是由疲劳破坏所造成的。
随着机械产品运转速度的提高,疲劳破坏更加普遍。
车身是汽车的主要承载部件,尤其轿车、客车等承载式车身,是悬架、发动机和车身附件的安装基础,承受来自路面、发动机等的各种交变载荷,其疲劳强度性能对保证汽车产品的安全性和可靠性至关重要。
近年来,车身耐久性CAE分析研究已经取得了较大进展。
但是,如何高效、准确地提取整车中各个连接点的载荷仍然是其中的一个关键问题。
传统的载荷提取方法首先需要通过实车的整车道路试验,提取轮胎中心的载荷,再利用多体动力学分析,将轮胎中心的载荷分解,从而获取各个连接安装点的载荷。
基于虚拟试验场技术的汽车平顺性仿真分析

(. 1 沈阳理工大学 汽车与交通学院 , 宁 沈阳 1 0 5 ; . 辽 1 1 9 2 重庆长安汽车股份有限公司 , 重庆 4 0 2 ) 0 0 0
摘要 : 于虚拟试验场 (P ) 基 V G 技术进行汽车平顺性仿真 . 了整车多体 动力学虚拟仿真模 型和随机输入路 面 建立
i f s sa l h d Th o g i lt n r s l ac lto i L DYNA , h i — o i c ee ain s i t tbi e . r e s r u h smuai e utc lua in va S— o tet me d man a c lr t o
对 于汽 车平顺性 的研 究 , 般采用 试验研 究 和理论分 析 两种方 法 . 一 试验 研究 法通 过实车试 验 , 用 “ 采 设 计一试 制一测 试一 改进一 再试 制” 的过程 进行平顺 性分 析 , 此方 法受 客 观 因素 的影 响 较大 , 试 验结 果 反 且
Ab t a t a e n te vru l r vn r u d ( G) tc n lg o e il rvn o o tsmua in, sr c :B s d o h it a o igg o n VP p e h oo y frv hced ii gc mfr i lt o
a a y e sn h ih e c e e a i n s m f R S v l e . h n i g s s e so t f e s a d d mp n l z d u i g t e we g t d a c lr to u o M a u s By c a g n u p n in s i n s n a - f e ,h e il rv n o o ti fe wa d i lt d a d e a u t d F n l , t i r v a e h t t i p r t e v h c e d i i g c mf r s a t r r s smu a e n v l a e . i a l i s e e ld t a h s a — y p o c a e l c c u l e tn o d t n t i h a c r c n e ib l y. r a h c n r fe ta t a s i g c n ii swih h g c u a y a d r l i t t o a i Ke r s e i l ;d i i g c mf r ;s s e so y wo d :v h c e rv n o o t u p n in;p we p c r ld n iy i t a r vn r u d o r s e ta e s t ;v r u l o i g g o n p
VPG技术在汽车中的应用
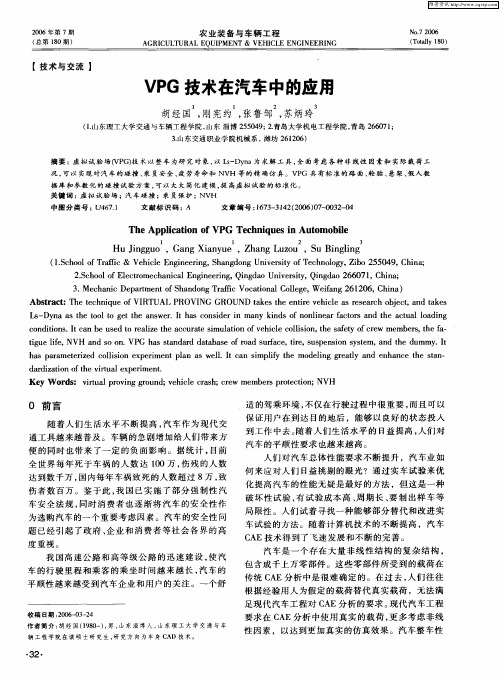
3 Me h n cDe at n fS a d n rf cVo ain l olg , efn 61 0 , h n ) . c a i p rme to h n o gT a i c t a l e W i g2 2 6 C ia o C e a
( .c o l f rf c& Ve il n i e r g S a g o g Unv ri fT c n lg , io2 5 4 ,C i a 1 h o af S oT i hceE gn e n , h n d n iest o e h oo y Z b 5 0 9 hn ; i y
( tl 8 Toal 1 0) y
【 技术与交流 】
V G技术在汽车中的应用 P
胡 经 国 , 宪 约 , 鲁 邹 苏炳 玲 刚 张 ,
(. 1 山东理 工 大学 交通 与 车辆 工程 学 院 , 山东 淄博 2 54 ; . 岛 大学 机 电工程 学 院 , 岛 26 7 ; 509 2 青 青 60 1
L —Dy a a he t o o g tt n we .I a o sd ri ny k n s o o ln a a t r n he a t a o di g s n s t o lt e he a s r th s c n i e n ma i d fn n i e r fc o a d t c u ll a n s
维普资讯
20 0 6年 第 7期 ( 总第 10期 ) 8
VPG在整车安全性分析中的特色

VPG在整车安全性分析中的特色作者:安世亚太(ANSYS-CHINA)当前,我国汽车行业面临着非常严峻的竞争形势,各汽车厂家必须提高自己的研发能力,同时还要努力降低开发和生产的成本。
与此同时,我国已发布了正面碰撞法规,并且将于2006年7月1日起正式实施侧面碰撞法规。
这些强制性法规的出台不仅对汽车的安全性提出了非常严格的要求,也不可避免地进一步导致了生产厂家开发、制造成本的提高。
CAE是可以协调这些矛盾的有效工具。
众所周知,采用CAE分析可在尚未做出样车之前模拟部件甚至整车的性能,避免了反复进行“设计—试制—测试—改进—再试制”的过程,因此大大缩短了开发周期,提高了设计质量,降低了开发成本,VPG(Virtual Proving Ground,汽车虚拟试验场)就是其中一个广受欢迎的仿真工具。
VPG——汽车虚拟试验场汽车产品开发过程中的CAE分析主要包括:一般性结构分析(刚度、强度等);噪声、振动、平顺性分析及操纵稳定性分析;结构耐久性分析;碰撞模拟分析;计算流体动力学分析;钣金成形分析等。
图1 VPG软件界面VPG是ETA公司与各大汽车厂商(如FORD、GM、DAIMLER -CHRYSLER、KIA等)经过近20年的合作,积累了丰富的汽车业CAE技术服务经验之后开发出的整车仿真软件(图1),是专门针对整车分析而开发的CAE仿真环境,可以进行整车的防撞性、安全性、NVH和耐久性等分析。
VPG提供的模型库、工具库及固化专家经验的自动化技术可将整车仿真过程中的人员数量及其工作量降到最低。
目前最新版的VPG3.0分为三个模块:VPG/PrePost、VPG/Structure、VPG/Safety。
VPG/PrePost拥有一套完整的网格划分工具以及相应的一些方便用户建模的工具。
VPG/PrePost 100%支持LS-DYNA、NASTRAN和RADIOSS,即所有的求解参数设置都可以在VPG界面中输入,无需用户额外手工编辑;提供了与多种主流CAD软件的直接接口,用户可以直接导入各种CAD数据文件;先进的后处理工具可以直接读取各种计算结果文件,并且能够进行动画演示或以X-Y曲线形式表示;自动焊点生成功能允许用户采用各种方法自动创建车身的焊点,使用户的工作效率得到进一步提高。
VPG汽车整车虚拟实验仿真

VPG汽车整车虚拟实验仿真概述VPG(Virtual Proving Ground)通过构制统一平台,简化建模过程,引入虚拟试验场,只需建立一个整车模型,就能够在汽车真实试验条件下,进行整车非线性虚拟样机仿真,达到动态参数设计的目的。
VPG技术可用于当前汽车产品开发的前沿,涵盖NVH、疲劳寿命、道路载荷预测、整车、子系统和部件的动力学和运动学分析。
并针对碰撞安全法规的要求,内置欧美碰撞安全法规和各种碰撞模型(假人、壁障、安全带等),轻松进行碰撞安全仿真。
来源于多年汽车CAE仿真应用经验的VPG技术和优秀的LSDYNA求解器,保证了VPG具有先进、专业、可靠的仿真能力,其丰富的数据库为用户提供了极大的方便,软件应用方法简单标准,以其易用性和专业性领导汽车CAE行业的最新发展趋势。
特色功能行业性最强∙专业用于汽车行业整车碰撞及乘员安全性分析的软件∙具备欧美等碰撞法规、汽车模型库等∙具备用于汽车行业分析的向导式设置方式,操作简便∙具备大量汽车行业客户友好的专业化图形界面∙具备专业化、向导式的操作界面,简单易用∙具备汽车行业专用后处理器,直接获取法规分析结果∙具备参数化建模方式,实现根据用户产品结构需求的汽车模型建模∙支持LSDYNA的所有关键字功能功能最为全面∙可进行汽车整车碰撞、乘员安全性、操纵稳定性、NVH分析∙可进行整车及子系统非线性动力学、疲劳耐久性等分析∙可进行特种车辆的防爆及动力学分析∙可进行全面的LSDYNA求解程序的前后处理强大的行业模型库∙具备多种汽车悬挂模型∙具备多种行业路面模型∙具备多种汽车轮胎模型∙具备多种碰撞假人及航空航天假人模型∙具备多种碰撞工具模型∙具备安全带模型相关模块VPG/Prepost提供适用于各种流行的MCAE求解器的网格划分和建模工具。
先进的Topology自动网格划分技术,能够满足当今最为苛刻的用户产品开发要求,可以显著减少因CAD模型修补而花费的时间。
Topology技术显著缩短了用户的建模时间。
汽车CAE技术的新进展虚拟试验场PG技术

汽车CAE技术的新进展虚拟试验场PG技术newmaker在现代设计流程中,CAE是创造价值的中心环节,要使CAE的作用达到最大化,需将其融入到设计全流程中,并对复杂设计对象进行“真实模拟”。
VPG技术已使这样的设计流程变为现实。
并且VPG技术和传统CAE技术相比有很大的进步,分析使用方法也大为简化和方便了。
一、概述现代汽车对结构设计提出了越来越高的要求,汽车结构分析已不满足于结构线性弹性分析。
实际上汽车结构系统中大量存在非线性结构,例如发动机、驾驶室橡胶支承、悬挂大变形、零部件间连接的能量缓冲等。
在产品要求精益设计的条件下,只应用线性分析普遍感到不足。
产品开发要求CAE更多地考虑非线性影响。
其次,汽车零部件结构分析的一个难点是分析载荷的不定因素,大量零部件结构实际所受到的载荷到底是多大,往往很难明确给出。
对此过去往往应用对比分析法,但这越来越不适应越来越高的设计要求。
第三,汽车产品设计已进入有限寿命设计阶段,这要求汽车在设计的使用期内,整车和零部件完好,不产生疲劳破坏,而达到使用期后(例如轿车一般设计寿命为八年),零部件尽可能多地达到损伤,以求产品轻量化,节约材料和节省能源。
这也对CAE分析提出了使用真实载荷的要求。
汽车整车性能,如舒适性、行驶操纵稳定性分析也不仅仅满足于结构刚性简化,还要求考虑结构变形刚度影响,进行整车非线性系统分析,以达到动态参数设计的目标。
CAE技术在飞速发展,非线性软件功能有了很大的提高,计算机硬件也提供了足够的支持,所以CAE技术满足上述汽车现代设计要求是可能的。
美国工程技术合作公司(ETA公司)推出的虚拟试验场技术(VIRTUAL PROVING GROUND ,以下简称VPG技术)即是针对上述要求发展的实用软件。
二、VPG技术VPG技术是汽车CAE技术领域中一个很有代表性的进展。
1.分析对象不再是分开的各个零部件,而是包括车身FEM模型、悬挂系(弹簧、减振器、动力控制臂)、转向梯形、车轮轮胎等整车非线性系统模型。
汽车CAE技术的新进展--虚拟试验场(VPG)技术

汽车CAE技术的新进展--虚拟试验场(VPG)技术
佚名
【期刊名称】《《CAD/CAM与制造业信息化》》
【年(卷),期】2004(000)012
【摘要】在现代设计流程中,CAE是创造价值的中心环节,要使CAE的作用达到最大化,需将其融入到设计全流程中,并对复杂设计对象进行“真实模拟”。
VPG技术已使这样的设计流程变为现实。
并且VPG技术和传统CAE技术相比有很大的进步,分析使用方法也大为简化和方便了。
【总页数】3页(P64-66)
【正文语种】中文
【相关文献】
1.基于虚拟试验场技术的汽车平顺性仿真分析 [J], 陈克;高洁;吕周泉
2.基于虚拟试验场技术的汽车侧面碰撞仿真分析 [J], 陈克;高洁;何浩然;白雪峰
3.汽车CAE技术的新进展--虚拟试验场(VPG)技术 [J], 安世亚太
4.基于虚拟试验场(VPG)整车强度耐久开发技术 [J], 路军凯;张朝军;王香云;张鸿钧
5.基于虚拟试验场(VPG)整车强度耐久开发技术 [J], 路军凯;张朝军;王香云;张鸿钧因版权原因,仅展示原文概要,查看原文内容请购买。
轻型商用车的VPG_技术及应用研究

doi:10.3969/j.issn.1005-2550.2023.03.001 收稿日期:2022-04-24轻型商用车的VPG技术及应用研究林明世,李明一,刘志敏,窦德海,季红丽(浙江远程商用车研发有限公司,杭州 325000)摘 要:为了提高悬架系统零部件耐久分析精度,减少开发周期,降低开发成本,首先本文制定了适用于轻型商用车使用场景的悬架系统耐久分析工况和试验工况,然后建立整车多提动力学模型,应用虚拟试验场(DVP)技术,进行时域下的虚拟试验场道路的整车动力学仿真,并对悬架系统零部件进行载荷分解。
最后采用分解后的载荷进行零部件的有限元分析。
该方法更真实的反映了整车在实际路面悬架受力情况,考虑因素更加全面,精度更高,分析方法更加有效。
关键词:VPG;轻型商用车;悬架;虚拟路面中图分类号:U463.34 文献标识码:A 文章编号:1005-2550(2023)03-0002-08The VPG Technology and Application Research of LightCommercial VansLIN Ming-shi, LI Ming-yi, LIU Zhi-min, DOU De-hai, JI Hong-li( Zhejiang Farizon Commercial Vehicle R&D Co., Ltd, Hangzhou 325000, China)Abstract:In order to the durability analysis accuracy of suspension system parts is improved, firstly, the development time is reduced, and costs is reduced, this paper theendurance analysis conditions and test conditions of the suspension system suitable for the usescenarios of light commercial vehicles are established, secondly, the vehicle multi-lift dynamicmodel is established, and the virtual proving ground (DVP) technology is applied, the vehicledynamics of the virtual proving ground in the time domain is simulated, and the componentload is decomposed of the suspension system parts. Finally, the decomposed load is used forthe finite element analysis(FEA) of the component. This method more realistically reflects theforce of the suspension of the whole vehicle on the actual road, and the considerations are morecomprehensive, the accuracy is higher, and the analysis method is more effective.Key Words: VPG(Virtual Proving Ground); Light Commercial Vehicle; Suspension;Characteristic Road1 前言破坏是由疲劳破坏所造成的,随着机械产品运转速度的提高,疲劳破坏更加普遍[1]。
汽车CAE技术的新进展_虚拟试验场_VPG_技术

的 。VPG 技 术 开 发 者 ETA 公 司 作 为 工 程技术合作公司, 期为美国各大汽 长 车公司服务, 有丰富的技术经验和 具 软件开发能力, 于不是汽车产品制 由 造公司, 此不存在软件开发后保密 因 自用的问题, 软件是比较开放的。 因此 可 以 说 , VPG 技 术 是 当 前 汽 车 行 业 CAE 应 用 的 一 个 新 进 展 。■
轮胎是完全可以实现数据库化的。 这 是 因 为 ,这 些 结 构 对 轿 车 来 说 ,结 构 形式基本可以归纳成几种基本类型 和数量有限的几个参数来描述。 户 用 只需选择结构类型, 出参数即可产 给 生计算模型。 然用户自行建立模型 当 也是完全可以的。 时软件数据库可 同 以增加用户模型数据, 着用户应用 随 面 的 增 多 ,数 据 库 会 更 加 丰 富 。当 前 悬挂数据库保存有 McPherson 液压 减 振 器 S t r u t、 长 短 臂 Shor t - l o n g Arm、 Hotchkiss渐 变 叶 片 弹 簧 (Leaf Spring)、后 拖 臂 Trailing Arm、 五 连 杆 5-link、 四 连 杆 Quadra Link
6. 计算结果后处理完全基于现代 计算机图式化平台上, 以产生实时 可 动画、 劳预测、 力应变图、 据信 疲 应 数 号变换、 绘制数据曲线图形等。 从 以 上 所 述 内 容 不 难 看 出 , VPG 技 术 和 传 统 CAE技 术 比 有 很 大 的 特 点 和进步, 析使用方法也大为简化和 分 方便了。 例 如: 1) 整 车 分 析 中 , 免 了 ( 在 避 传 统 CAE分 析 部 件 间 受 力 关 系 难 以 确 定的困难, 在车身随机响应疲劳分 如 析中, 免了分析者必须通过样车试 避 验确定悬挂支点对车身作用力谱, 再 对这些作用力谱滤波、 强化、 数字化和 对车身支点施加谱载荷谱表等一系列 复杂工作 对车身谱分析而言) 对悬 ( 。 挂转向系统运动学和动力学分析而言, 不必将车身简化为刚体, 身对悬挂 车 转向系统的弹性和非线性变形影响可 真实计入计算分析中, 而提高了分 从 析精度。 (2) 以整车为分析对象, 边界条件 只有路面和车速。 样分析载荷实现 这 了规范化、 标准化, 使计算结果更加真 实准确, 可比性提高。 因为路面载荷数 据库是全面和权威的 如美国独立的 (
- 1、下载文档前请自行甄别文档内容的完整性,平台不提供额外的编辑、内容补充、找答案等附加服务。
- 2、"仅部分预览"的文档,不可在线预览部分如存在完整性等问题,可反馈申请退款(可完整预览的文档不适用该条件!)。
- 3、如文档侵犯您的权益,请联系客服反馈,我们会尽快为您处理(人工客服工作时间:9:00-18:30)。
汽车CAE技术的新进展——虚拟试验场(VPG)技术
CAE技术在飞速发展,非线性软件功能有了很大的提高,计算机硬件也提供了足够的支持,所以CAE技术满足上述汽车现代设计要求是可能的。
美国工程技术合作公司(ETA公司)推出的虚拟试验场技术(VIRTUAL PROVING GROUND ,以下简称VPG技术)即是针对上述要求发展的实用软件。
一、概述
现代汽车对结构设计提出了越来越高的要求,汽车结构分析已不满足于结构线性弹性分析。
实际上汽车结构系统中大量存在非线性结构,例如发动机、驾驶室橡胶支承、悬挂大变形、零部件间连接的能量缓冲等。
在产品要求精益设计的条件下,只应用线性分析普遍感到不足。
产品开发要求CAE更多地考虑非线性影响。
其次,汽车零部件结构分析的一个难点是分析载荷的不定因素,大量零部件结构实际所受到的载荷到底是多大,往往很难明确给出。
对此过去往往应用对比分析法,但这越来越不适应越来越高的设计要求。
第三,汽车产品设计已进入有限寿命设计阶段,这要求汽车在设计的使用期内,整车和零部件完好,不产生疲劳破坏,而达到使用期后(例如轿车一般设计寿命为八年),零部件尽可能多地达到损伤,以求产品轻量化,节约材料和节省能源。
这也对CAE分析提出了使用真实载荷的要求。
汽车整车性能,如舒适性、行驶操纵稳定性分析也不仅仅满足于结构刚性简化,还要求考虑结构变形刚度影响,进行整车非线性系统分析,以达到动态参数设计的目标。
CAE技术在飞速发展,非线性软件功能有了很大的提高,计算机硬件也提供了足够的支持,所以CAE技术满足上述汽车现代设计要求是可能的。
美国工程技术合作公司(ETA公司)推出的虚拟试验场技术(VIRTUAL PROVING GROUND ,以下简称VPG技术)即是针对上述要求发展的实用软件。
二、VPG技术
VPG技术是汽车CAE技术领域中一个很有代表性的进展。
1.分析对象不再是分开的各个零部件,而是包括车身FEM模型、悬挂系(弹簧、减振器、动力控制臂)、转向梯形、车轮轮胎等整车非线性系统模型。
这样,车身和悬挂系统与转向系统间难以明确的作用力关系已包含在分析模型之内。
如图1所示。
图1 整车的分析模型
2.分析模型数据库化。
众所周知,计算模型建模工作量是很大的。
但是,除车身模型是车型分析时必须建立的模型,悬挂结构、转向机构和轮胎是完全可以实现数据库化的。
这是因为,这些结构对轿车来说,结构形式基本可以归纳成几种基本类型和数量有限的几个参数来描述。
用户只需选择结构类型,给出参数即可产生计算模型。
当然用户自行建立模型也是完全可以的。
同时软件数据库可以增加用户模型数据,随着用户应用面的增多,数据库会更加丰富。
当前悬挂数据库保存有McPherson液压减振器Strut、长短臂Short-long Arm、Hotchkiss 渐变叶片弹簧(Leaf Spring)、后拖臂Trailing Arm、五连杆5-link、四连杆Quadra Link和扭杆Twist Beam 等十种结构数据库。
另外,VPG还提供对Adams接口,导入兼容的Adams悬架模型。
图2 轮胎数字化模型
图3 路面数字化模型
轮胎模型分为用于车身疲劳和寿命分析的轮胎模型;用于评价振动噪声NVH研究中应用的轮胎模型和用于动力学分析的轮胎模型三种类性。
疲劳分析轮胎模型,可以由内部函数构造产生、也可以从轮胎数据库中直接选择模型,许可用户直接输入试验数据,可选择SAE971100论文《用于车辆动力学分析及整车实时试验的轮胎模型的有效性》所述的模型。
用于评价振动噪声NVH研究中应用的轮胎模型有更加详细的轮胎结构,模型使用非线性材料,可以选择B.G.KAO等人研究成果:《轮胎瞬态分析与显式有限元程序》论文——《轮胎科学与技术》所应用的模型。
用于动力学分析的轮胎模型能反映三维自由和强迫振动,可适应高频谐波和随机激励的自由振动和接触振动模态。
用户可以根据分析目的选择不同的轮胎模型,一般给出轮胎型号很快即可完成轮胎建模工作。
图4 碰撞计算研究用假人模型
图5 碰撞计算障碍物模型
模型数据库还有碰撞计算研究用的假人模型、碰撞计算障碍物模型等可供用户引用。
可见,应用VPG软件最大限度地方便用户建模,简化了计算数据准备工作,同时保证模型的质量和可比性。
3.提供了全面的路面载荷。
VPG软件提供了标准典型的路面模型,是通常整车试验标准考核路面,例如:交替摆动路面(Alternate Roll)、槽形路(Pothole Tracks)、鹅卵石路(Cobblestone Tracks)、大扭曲路(Body Twist Lane)、波纹路(Ripple Tracks)、搓板路(Washboards)以及比利时石块(Belgian Block)等。
用户可以输入和保存自己的路面数据,也可以用任意三维数据构造特定的路面。
VPG软件当前提供了美国MGA汽车试验场数字化数据库,并且准备录用中国海南汽车试验场路面数据。
图6
4.从分析内容方面讲,VPG计算技术分析内容是多样化的。
一个分析模型可以进行疲劳寿命计算、振动噪声分析计算、车辆碰撞历程仿真、碰撞时乘员安全保护等多种结构非线性分析。
同时还可以进行整车非线性运动学和动力学计算,用来进行整车舒适性、高速行驶性能和操纵稳定性研究。
疲劳分析可以根据计算结果整理出疲劳曲线进行寿命预测。
振动噪声计算结果可以进行富利叶变换,进行NVH评价。
碰撞仿真结果用于结构碰撞性能研究和依据FMVSS 法规对乘员的安全作出评价。
图7 碰撞仿真模拟
运动学和动力学计算可输出内外轮角(Ackerman Angle)、转动半径(Turn Radius)、内倾刚度(Roll Stiffness)、回转半径(Scrnb Radius)、前束角(Toe Angle)、内倾(Kingpin Inclination)、刹车点头和加速沉尾(Anti-dive/Anti-lift)、外倾角(Camber Angle)、后倾角(Caster Angle)和纵向摆动(Front/Rear Roll)等参数,进行整车性能评价。
5.求解器是基于高度非线性软件LS-DYNA进行整车系统非线性分析。
从这个角度看,VPG技术是一个高度非线性分析软件的一个汽车专用接口软件和支持它的数据库。
6.计算结果后处理完全基于现代计算机图式化平台上,可以产生实时动画、疲劳预测、应力应变图、数据信号变换、绘制数据曲线图形等。
从以上所述内容不难看出,VPG技术和传统CAE技术比有很大的特点和进步,分析使用方法也大为简化和方便了。
例如:(1)在整车分析中,避免了传统CAE分析部件间受力关系难以确定的困难,如在车身随机响应疲劳分析中,避免了分析者必须通过样车试验确定悬挂支点对车身作用力谱,再对这些作用力谱滤波、强化、数字化和对车身支点施加谱载荷谱表等一系列复杂工作(对车身谱分析而言)。
对悬挂转向系统运动学和动力学分析而言,不必将车身简化为刚体,车身对悬挂转向系统的弹性和非线性变形影响可真实计入计算分析中,从而提高了分析精度。
(2)以整车为分析对象,边界条件只有路面和车速。
这样分析载荷实现了规范化、标准化,使计算结果更加真实准确,可比性提高。
因为路面载荷数据库是全面和权威的(如美国独立的汽车试验场MGA路面库),也可以是本公司使用的自行考核试验路面,分析结果更加真实可信。
(3)计算是高度非线性分析,分析中包含了结构非线性因素、车身支撑和发动机支撑等橡胶连接件的非线性因素、悬挂转向系统连接和缓冲件的非线性因素、车轮轮胎的非线性因素、轮胎和地面接触条件等。
因此分析结果中几乎排除了传统CAE技术分析时常使用的人为假定,大幅度提高计算精度。
图8
(4)在振动噪声分析中,由于模型有非常大的自由度,析出的振动频率可不受限制,完全可以得到NVH分析要求的250 赫兹内的频率模态。
NVH分析评价更加全面。
(5)整车高速行驶性能、转向稳定性能计算也不再受制于传统计算方法中自由度数量,可同时考虑车身结构变形影响,使计算结果精度提高。
三、结论
应用VPG技术可以缩短产品开发时间,节省研制费用,减少投资风险。
一般来说,可以在样车试制前即可得到产品试验结果,这即是虚拟试验场叫法的由来。
我国CAE技术应用已全面展开,单一计算模型和计算水平已达到国外同期水平,但是因为FEM方法计算结果和传统强度校核计算结果有一定区别,应用FEM进行强度校核的评价标准在大多数企业中还没有建立,因此计算结果应用受到一定限制。
这一方面要求我们尽快建立企业CAE评价标准,另一方面应该吸收国外成熟的评价数据的方法。
但是国外大型公司强度评价标准都是技术机密,准确得到这些数据是很难的。
已经应用CAE软件于汽车产品开发的用户其实大多开发了多种专业接口,其内容和上文所述大同小异,有些接口软件还将ANSYS内部评价数据库编入软件中,但这些汽车公司开发的软件,目的是自行使用,对外是不公开的。
VPG技术开发者ETA公司作为工程技术合作公司,长期为美国各大汽车公司服务,具有丰富的技术经验和软件开发能力,由于不是汽车产品制造公司,因此不存在软件开发后保密自用的问题,软件是比较开放的。
因此可以说,VPG 技术是当前汽车行业CAE应用的一个新进展。