莱钢冷轧六辊可逆轧机乳化液吹扫系统综合改造
六辊可逆冷轧机机架控制系统
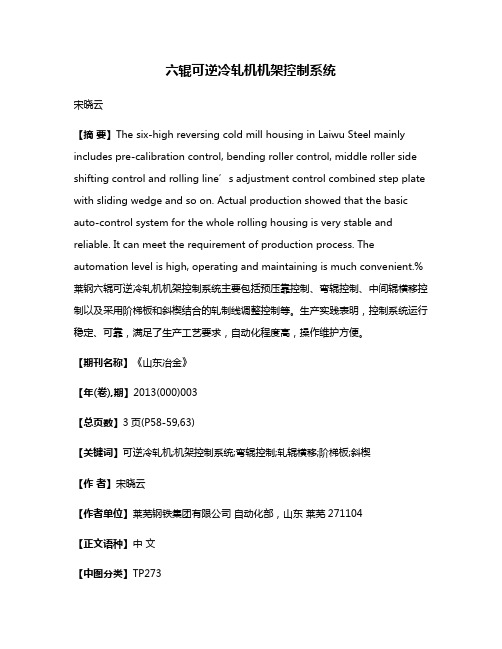
六辊可逆冷轧机机架控制系统宋晓云【摘要】The six-high reversing cold mill housing in Laiwu Steel mainly includes pre-calibration control, bending roller control, middle roller side shifting control and rolling line’s adjustment control combined step plate with sliding wedge and so on. Actual production showed that the basic auto-control system for the whole rolling housing is very stable and reliable. It can meet the requirement of production process. The automation level is high, operating and maintaining is much convenient.% 莱钢六辊可逆冷轧机机架控制系统主要包括预压靠控制、弯辊控制、中间辊横移控制以及采用阶梯板和斜楔结合的轧制线调整控制等。
生产实践表明,控制系统运行稳定、可靠,满足了生产工艺要求,自动化程度高,操作维护方便。
【期刊名称】《山东冶金》【年(卷),期】2013(000)003【总页数】3页(P58-59,63)【关键词】可逆冷轧机;机架控制系统;弯辊控制;轧辊横移;阶梯板;斜楔【作者】宋晓云【作者单位】莱芜钢铁集团有限公司自动化部,山东莱芜271104【正文语种】中文【中图分类】TP2731 前言近年来,冷轧薄板性能好、品种多、用途广的优点使冷轧薄板生产得到迅速发展,莱钢冷轧薄板是莱钢十一五期间产品结构优化的重点工程,拥有年产40 万t 的冷轧生产线,以莱钢热轧带钢为原料。
单机架冷轧机乳化液系统的改进与应用
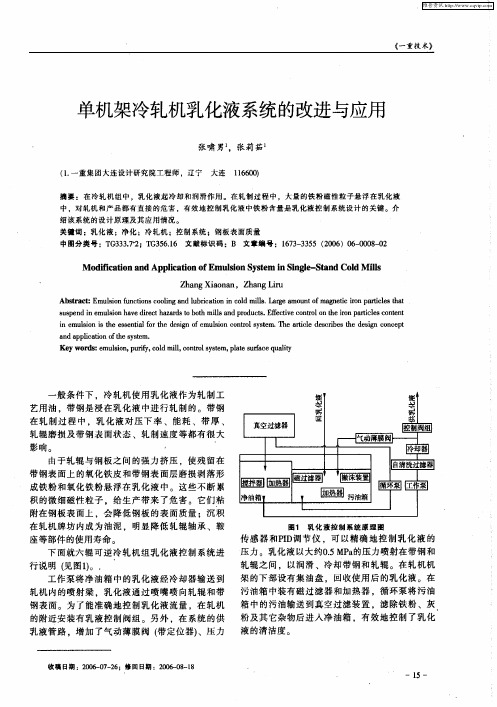
收 稿 日期 :2 0 — 7 2 ;修 回 日期 :2 0 — 8 1 060 —6 06 0 — 8
般条 件下 。冷 轧机 使 用乳 化 液作 为 轧制 工 艺 用油 。带 钢是 浸 在乳 化 液 中进 行 轧制 的。带 钢
一
在 轧 制 过程 中 。乳 化 液 对 压 下率 、能耗 、带 厚 、
轧辊 磨 损及 带钢 表 面状 态 、轧制 速 度等 都 有很 大 影 响。 一 由 于轧辊 与 钢板 之 间的 强力 挤 压 ,使 残 留在 带钢 表 面 上 的氧化 铁皮 和 带钢 表 面层磨 损 剥落 形
a da p i ai no e s se n p l t f y t m. c o h t
Ke r s e lin p r y c l l c nrl ytm, lt u a eq ai ywo d : muso , ui , odmi, o to s f l s e paes r c u  ̄ f l
s se di muso a edrc a ad ohmisa dpo u t. f ciec nrl ntei np rce o tn u p n e l nh v i t z rs ob t l n rd cs E et o t at ls ne t n i e h t l v o o h r o i c i muso ees nilfrted sg fe l o o t l ytm. h rced srb sted s n c n e t ne l ni t se t h e ino mus nc nr se T ea il e c e ei o c p i sh a o i o s t i h g
莱钢1500mm六辊可逆冷轧机的板形控制技术

高的板形 精度 的要 求 ,现 以莱钢 10 l六 辊 50f i m 可 逆 式 冷 轧 机 为 例 ,介 绍 一 下 板 形 控 制 的 新 技
术
复合波 、二次谐波等,利用弯辊较难解决。 在 轧制 过 程 中轧辊 有 一个 基本 冷 却量 ,约为
22 轧辊 分段冷 却控 制技 术 . 分段 冷却 控 制技 术 就是 通过 调 整冷却 液 的分
1 影响板形 凸度 和平坦度 的 因素
带 钢 的 凸度 由原 料 的形 状 、轧 辊 的空 载辊 形
( 原始凸度 、热凸度和磨损 曲线) 、轧辊 的弹性变 形( 即弯曲挠度和压扁) 等决定 。在普通 四辊轧机 上所 使 用 的变压 下量 法 、总轧 制压 力 控制 法 、以
受 轧制 力 变化 的 影 响 ,减少 带 钢 边部 减 薄量 和 裂
边 ,保证带材有 良好 的板形 。可轧制高精度薄带 钢 ,并 具 有大 压 下量 、提 高生 产 率 、节 约 能源 、
个冷却 区实际的冷却输 出给控制装置 ,由其打开
和关 闭 相 应 的 控制 阀 ,对 板 形 进 行 控 制 。 图 1 为 轧 机 的分段 冷却 示意 图。
Pr f eCo t o c n l g 5 0 m - v r i l l i t i t e o l n r l i Te h o o y i 1 0 m n 6 h Re e sb eCo d M l a wu S e l l La
S n a y n, MaJn o gXio u ig
莱钢 10 E 5 0 六辊单机架冷轧机 的弯辊技术 m 分为工作辊液压弯辊和中间辊液压弯辊 ,工作辊 液压弯辊有液压正弯和液压负弯 ;中间辊 只有液 压 正弯 。在轧 辊 凸度 不足 或磨 损 情况 下可 以采用 正弯,增大轧辊凸度 ,防止带钢边浪 ,而负弯可
可逆冷轧机乳化液系统改造与优化

参考文献 [1] 李玉功.冷轧带钢表面清洁度影响因素分析与对策[J].山西冶
金,2017(3):91- 93.
(编辑:张卓娅)
Modification and Optimization of Emulsification System for
Reversible Cold Rolling Mill
Ma Jing
输送到轧机入口处进行冷却以及润滑,最终实现循
环使用。
过滤精度 30~70μm
轧死 磁性过滤器
平床过滤器
撇油器
脏箱
净箱 机械搅拌
图 1 1 500 mm 冷轧机组乳化液循环系统图
2 莱钢 1 500 mm 乳化液循环系统存在的问题 1)乳化液箱采用老式的蒸汽盘管的加热方式,
里面铺设复杂的加热蒸汽管道,容易在蒸汽管道缝 隙 造 成 油 泥 沉 淀 和 板 结 ,清 理 困 难 ,蒸 汽 加 热 效 率低。
乳化液主要是由 1%~3%的轧制油和 97%~99% 的脱盐水经搅拌配比而成的乳浊液,在轧制过程中, 在一定的温度和压力条件下,分散于乳化液中的轧 制油以物理吸附和化学吸附两种方式吸附于钢板 和轧辊表面形成油膜,为轧制提供必要的润滑、冷却 和清洗作用。因此,乳化液的性能对带材表面清洁度 有着十分重要的关系,直接影响了冷轧产品的表面 质量。 1.2 乳化液系统工作流程
发生。 3.4 乳化液磁过器改造
改造地上污油箱的箱体结构,使地上污油箱的箱 体由一个单纯的收集槽成为一个粗过滤器,挡住了 大颗粒物质的泄漏;同时,将之前的水平气动式磁过 滤器进行了拆除改造为去磁能力更强、运行更稳定 的立式磁过滤器。经过改造,污油箱的去污能力更 强,溢流进入中间油箱的乳化液清洁性得到大幅度 提高。
六辊可逆冷轧机横移-弯辊系统的控制
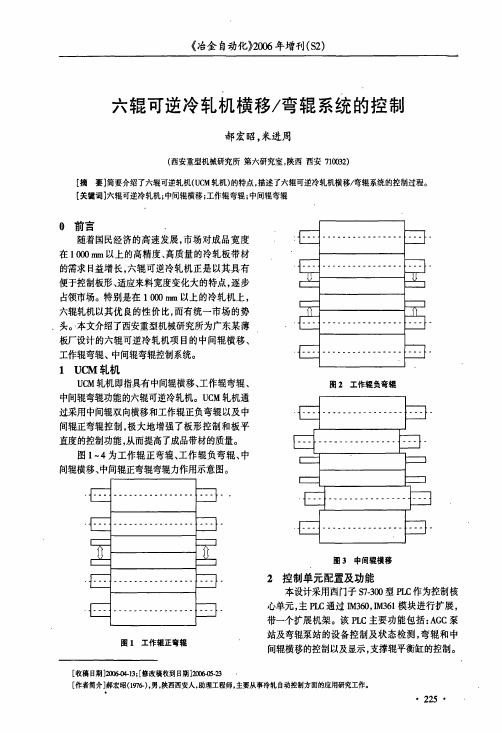
六辊可逆冷轧机横移/弯辊系统的控制
郝宏昭,米进周
(西安重型机械研究所第六研究室,陕西西安710032) [摘要]简要介绍了六辊可逆轧机(UCM轧机)的特点,描述了六辊可逆冷轧机横移/弯辊系统的控制过程。
【关键词]六辊可逆冷轧机;中间辊横移;工作辊弯辊;中间辊弯辊
O前言 随着国民经济的高速发展,市场对成品宽度
带材板形得到了更好的控制。本轧机中间辊只有
正弯辊。
4.1弯辊控制方法、
对弯辊的控制采用压力闭环控制,其控制框
图如图7所示。
[编辑:魏方]
・227・
置,方可进行换辊操作。否则将会损坏轧机辊系。
单独调节,也可以两边同时调节。
4弯辊系统的特点及控制原理
在轧制过程中,弯辊是最为常见的用于对带 刚凸度和板平直度进行连续控制的方法之一。通 过控制轧机轧辊两侧的弯辊力,改变轧辊的辊形。
弯辊控制用于控制轧机出口侧带材的板形。如果 弯辊力使辊缝减小,称之为正弯辊;反之,如果弯
E
此外通过硬线连接方式与AC,C系统通信以协助
AGC系统实现快速卸荷,与工艺PI£之间通过 MPI网通信实现AGC泵站及弯辊泵站的远程起停
匡
r——。一
及故障状态显示,控制框图如5所示。
3中间辊横移系统的特点及控制原理
中间辊横移是控制板形精度的方法之二。它
亡 E
图4中间辊正弯辊
根据带材宽度的不同而轴向移动上下两个中间
馈达到平衡,执行器输出为零,油缸不再动作。当 给定再次增减时,反馈随之增减,执行器驱动油缸
要解决这个控制问题,必须要转换思维方式,
从另外一个角度去看这个问题。首先应该明确, 其实所谓的同步只是从宏观上来说的,它实际上
莱钢冷轧单机架可逆轧机计算机控制系统

在图1 所示 的网络结构中 ,最上一层是由P 组 成,作 为操作监控系 C
图l控制系统网络结构
l 5 4
应用方法论
2器 科1 3 0年 期 1第 技
浅谈广州 东站 电缆施工质量控制
统的人机 界面 ,根据被轧带材的来料厚度 、 宽度 、材质 及成品厚度、轧 制一 艺的技术要求 ,计算总轧制道次 、各道次的压下量、各道次相应的 r 轧制力 、张力动将这些数据传送给P C C/ P L 控制系统 ,从P C L 控制系统
通讯 。
第二层是由多套P I C、传动装置及特殊 仪表组成。I 单元分散安置 / O 在各相关设备附近 , 使连接的信号线减到最少 . 大大减少了信号传输过 程 中受到干扰的机会。
2 系统 功能 1 辊缝控制。轧辊辊缝位置控制又称A C ) G 内环控制,是液压压下控 制系统基 本功能 ,在此方式下 ,将 液压缸的位置值与设定的目标值相 比 较 ,比较的偏差经特定运算后 ,送 到伺服阀去引起液压油的流动以使位 置偏差减少到零 位移测量采用高精度位移传感器 ,在油缸中心安装。 2 )辊缝 同步和倾斜控制 。由于轧机传动侧 、操作侧的液压 缸之 间 没有机械上的联结 ,而 且两侧负载不可能完全相同,设备的动态特性也 不完全一致 ,因此两侧 的运动不能保持 同步 ,同步控制的 目的就是使位 移慢的~侧加快运动 ,位移快的一侧减慢运动 ,使两侧的运动速度保持 致 。系统中采用辊缝差信号进行闭环控制。当两侧辊缝差实际直过大 时,程序发 l超极 限中断信号 ,机组快速停车。 叶 J 3)恒 轧 制 力 控 制 。 轧 制 力 控 制 也 是 液 压 压 下 控 制 系 统 的 基 本 功 能 ,在轧制力控制 方式下 , ̄ S 力控制器用来使冷轧机两侧油缸的轧制 LE I 力的实测值保持 t设定值一致 。根据油缸 的积分特性 ,将轧制力控制器 j 设 汁成 一个 比例控 制 器 。 一 4)预压靠控制 。由于辊缝取决 于: 作辊的相对位置 ,因此在每次 换辊后须萤新确定辊缝的零点 ,即需要进行轧辊预压靠。预压靠过程由 (下转 第 14 ) 5页
六辊可逆冷轧机组轧辊表面剥落原因分析及改善
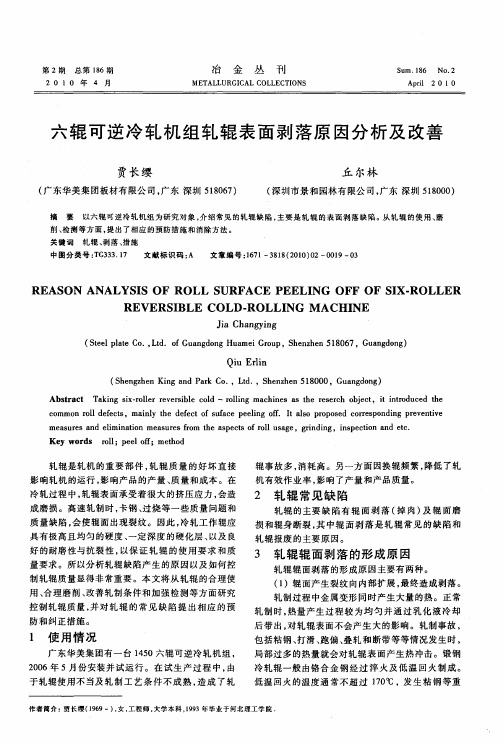
总第 16期 8
冶 金
丛 刊
S um .1 6 8
No. 2
2 0 10 年 4 月
M ETAL LURGI CAL COLLECTI ONS
Aprl 2 0 i 10
六 辊 可逆 冷 轧 机 组 轧辊 表 面剥 落原 因分 析及 改 善
具 有极 高且均 匀 的硬度 、 一定 深 度 的硬化层 、 以及 良
好 的耐磨 性与 抗裂 性 , 以保 证 轧 辊 的 使 用要 求 和 质
3 轧 辊辊 面 剥 落 的 形 成 原 因
轧 辊辊 面剥 落的形成 原 因主要 有两种 。
量要 求 。所 以分 析轧辊 缺陷产 生 的原 因 以及 如何 控
( t l l eC . Ld f un dn u m i ru , h nhn5 8 6 ,G a go g Se a o , t.o G ag o gH a e G o p S e ze 0 7 u nd n ) ep t 1
Oi ri uE l n
( h nz e iga dP r C . Ld , h nhn5 8 0 G a go g S e gh nKn n ak o , t. S e ze 10 0, un dn )
局 部过多 的热 量就会 对轧辊 表 面产 生热 冲击 。锻钢
冷 轧辊一 般 由铬合 金 钢经 过 淬 火 及 低 温 回火 制 成 。
低 温 回火 的温度 通 常不 超 过 10C,发 生粘 钢 等重 7 ̄
于轧辊 使用不 当及 轧 制工 艺 条 件 不 成 熟 , 造成 了轧
作 者 简 介 : 长 缨 (9 9一) 女 . 程 师 , 学 本 科 。9 3年毕 业 于 河 北理 工 学 院 贾 16 , 工 大 19
单机架六辊可逆冷轧机电气自动化技术方案(精)

1200六辊可逆冷轧机电气自动化系统控制方案1概述根据《1200六辊可逆冷轧机技术规格电气招标书》所提供的工艺设备和技术要求,并参考了同类型的单机架六辊可逆冷轧机的工艺技术,编写了本电气传动及基础自动化控制的技术方案。
2 供电2。
1 电气设备运行条件1)电气设备运行环境要求环境温度现场:0~40︒C电气室: 10~35︒C操作室:25±5︒C空气湿度:相对湿度≤95%且无凝露;污染等级:III级,无火灾爆炸危险、无导电性尘埃、不腐蚀金属物及不破坏绝缘介质的环境。
2)电气设备运输及储存环境要求环境温度—20~65︒C ;空气湿度及污染等级要求与运行时相同。
3)电气设备使用的电压等级及技术条件本机组所使用电气设备电压等级符合我国国家标准,主要用电设备的电压等级为:◆供电电压及频率:10±5%kV,50±1Hz◆低压供电电压:AC380/220V◆交流电动机电压:AC380V◆直流电动机电压:DC440~660V◆电磁阀:DC24V◆电磁抱闸:AC220V◆控制电压:AC220V,DC24V◆保护地:接地电阻<4Ω◆系统地:接地电阻〈4Ω2.2低压供配电辅传动供电系统(1)辅传动供电系统单线图见MCC单线图。
(2)MCC设备(见附表)由于本机组负荷较小,因此不设负荷中心。
本机组负荷MCC(即马达控制中心)将采用GGD3柜,包含MCC的受电、馈出回路、UPS系统、比例、伺服阀控制回路和照明开关柜,开关柜额定短路短时承受能>80kA/s.额定短路分断能力与电网短路电流相适应,Icu 〉50kA根据需要配置必要的电流、电压表计,端子板采用Phoenix端子。
单机架可逆冷轧机组设一套MCC,不同容量不同控制类型的回路至少有一个备用回路.注①:主传动电动机均配置有空间加热器,这些加热器是在长期停机时防止电机绕组受潮而设置的。
由本MCC供电。
注②:为了保证乳化液站的检修供电,需要检修电源或者备用一路供电回路。
莱钢1500冷轧机组乳化液系统工艺技术改造
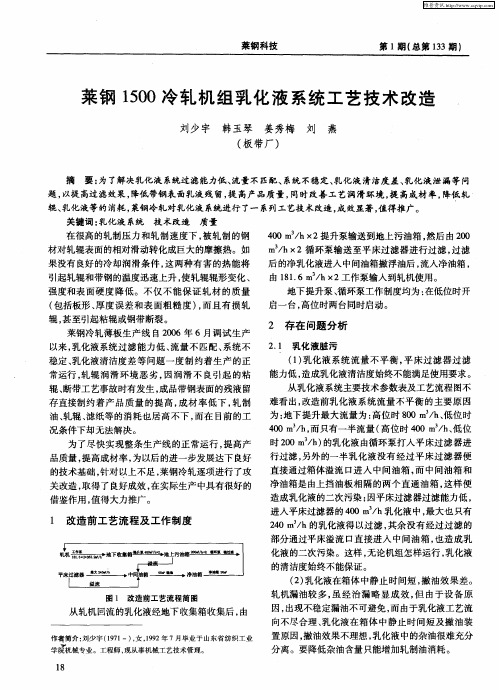
2 存在 问题分析
2 1 乳化液 脏 污 .
稳定 、 乳化液清洁度差等问题一度制约着生产 的正
常运行 , 轧辊 润滑环境恶 劣, 因润滑 不 良引起 的粘 辊、 断带工艺事故时有发生, 成品带钢表面的残液留
() 1 乳化液系统流量不平衡 , 床过滤器 过滤 平
能力低 , 造成乳化液清洁度始终不能满足使用要求 。 从乳化液系统主要技术参数表及工艺流程图不
难看 出 , 改造 前乳 化 液 系 统 流量 不 平 衡 的 主要 原 因
存直接制约着产 品质量 的提 高, 成材率 低下 , 轧制 油、 辊、 轧 滤纸 等 的消 耗 也 居高 不 下 , 在 目前 的 工 而 况条件下却无法解决 。
为: 地下提升最大流量为 : 高位时 80m / 、 0 。h 低位时
() 5 磁过滤器过滤能力低 , 导致系统铁粉含量高。 () 6 乳化液系统原装蝶阀阀座密封均 为橡胶密 封, 由于乳化液流量 大, 并且温度较高 , 加上管路震
症结所在是 : 系统流量不平衡 、 平床过滤器及磁过滤 器过滤能力低 、 工艺流 向不尽合理等 。为了彻底解
决这些问题 , 莱钢冷轧陆续进行了工艺技术改造 。
污染 ; 另一方面, 未过滤掉的较大的橡胶块堵塞了乳 化液喷嘴 , 使轧辊局部受热严重而受损 , 时常发生轧
维普资讯 http://wwຫໍສະໝຸດ
莱钢科技
第 1 总第 13 ) 期( 3期
莱 钢 10 0冷 轧 机 组 乳化 液 系统 工 艺技 术 改造 5
刘少 宇 韩玉琴 姜秀梅 刘 燕 ( 带厂 ) 板
摘 要: 为了解决乳化液系统过滤能力低、 流量不匹配、 系统不稳 定、 乳化液清洁度差、 乳化液泄漏等 问 题, 以提高过滤效果, 降低 带钢表面乳液残留, 高产 品质量 , 提 同时改善工艺润 滑环境 , 高成材率, 提 降低 轧 辊、 乳化液等的消耗 , 莱钢冷轧对乳化液系统进行 了一系列工艺技 术改造 , 成效显著, 值得推广。
六辊可逆冷轧机道次量综合优化技术的研究

分布越均匀" 则出口带材板形越好# 反之" 如果
出口带材前张力的横向分布越差" 则出口带材板
形越差(
上述板形综合控制函数只针对单一道次" 而
单机架可逆冷轧机组在工作时为多道次轧制" 同
时单机架可逆轧机每道次之间张力耦合关系比较 弱" 可以单独自由设定" 但上个道次的出口板形
及断面形状就是下个道次的来料板形与断面形
5]452B7"" 2;eE7>XE@8A"" <-45dI>KB@"" <:dI>N@8A#" i-45d=8A"" i-45c7=8>EB7#
!"$H11>C+P32I=MO:8JBNKLO3WB7RSI8K1@Q" 9KJQ" 07) =8 %")&&&" 1E78=# #$4=K7@8=F38A78IIL78APINI=LDE 1I8KILG@L1@FJ>L@FFIJ CKL7R 3WB7RSI8K=8J [L@DINN"
<=8NE=8 ;87MILN7KO" m78EB=8AJ=@&,,&&)" 1E78=$
7,1)-3/)* :8 KEIE7AE>NRIIJ L@FF78ARL@DINN@G=N7?>E7AE N78AFINK=8J LIMILN7UFIL@FF78AS7FF" KEILI=N@8=UFI NIKK78A@GL@FF78AR=NNWB=8K7KOJ7LIDKFO=GGIDKNKEIJ7NKL7UBK7@8 @GI?7KNKL7R NE=RI=8J KEINK=U7F7KO@GL@FF78AS7FF" =NYIFF=NRL@JBDK7@8 IGG7D7I8DO=8JI8ILAOD@8NBSRK7@8 @GL@FF78AS7FFQ-FKE@BAE E7AE>NRIIJ L@FF78A7NG=NK" KEI =MIL=AIRLINNBLILIJBDK7@8 RILR=NN7NF7S7KIJ =8J LIF=K7MIFONS=FFB8JILE7AE>NRIIJ L@FF78AD@8J7K7@8NQ*@ =DE7IMID@8N7NKI8KI?7KKE7DV8INN" 8IIJ K@78DLI=NID@LLINR@8J78AR=NNIN8BSUILQ+@LLIMILN7UFIL@FF78AS7FFN" 78DLI=N78AR=NNIN8BSUILSI=8NN7A87G7D=8K78DLI=NI@GI8ILAOD@8NBSRK7@8 G@LKEII8K7LIB87KQ*@KEIRL@UFISN @GRF=KINE=RI=8J E7AE I8ILAOD@8NBSRK7@8 78 KEIE7AE>NRIIJ LIMILN7UFIL@FF78ARL@DINN" KEIL@FF78ARLINNBLI=8J R@YIL@GKEIF=NKKELIIR=NNINYILIIGGIDK7MIFOLIJBDIJ UO@RK7S7X78AR=L=SIKILNNBDE =NKEIGL@8K=8J LI=L KI8N7@8 =8J L@FF78ANRIIJ @GI=DE R=NN" KEI@UTIDK7MIGB8DK7@8N@GNE=RID@8KL@F=8J R@YILD@8KL@FG@LI=DE R=NN =LIINK=UF7NEIJ" =8J =GKILYI7AEKIJ D=FDBF=K7@8N" YE7DE JIMIF@RIJ =D@SRLIEI8N7MI@RK7S7X=K7@8 =8J NIKK78A KIDE87WBI@GL@FF78ANDEIJBFINKE=K@UTIDK=NL@FF78AR@YILB87G@LSI=DE R=NN" YE7FI=FN@K=V78A78K@G=DK@LNNBDE
冷轧机组带钢吹扫装置的改进方案

冷轧机组带钢吹扫装置的改进方案唐水清;陆兆刚;赵干波【期刊名称】《金属世界》【年(卷),期】2018(000)004【总页数】5页(P64-67,72)【作者】唐水清;陆兆刚;赵干波【作者单位】广西柳州钢铁集团有限公司,广西柳州 545002;广西柳州钢铁集团有限公司,广西柳州 545002;广西柳州钢铁集团有限公司,广西柳州 545002【正文语种】中文随着科学技术的不断进步,用户对带钢表面质量要求越来越高。
带钢吹扫装置如果不能有效吹扫干净轧制后板面的乳化液,一方面会造成俗称“油烧”的乳化液斑迹,另一方面板面会带走过多的乳化液,增加轧制油的消耗。
现有的乳化液吹扫系统大部分无法满足产品生产要求,因此,找到一种更合理完善的带钢吹扫装置已经是各冷轧厂都面临的一个亟需解决的问题。
带钢吹扫装置吹扫装置布置柳钢1550 mm冷连轧机带钢吹扫装置全部安装在一体式结构的防缠导板上,防缠导板的移进移出由液压缸带动,防缠导板上安装的可移动式的侧导板由液压马达带动。
两组喷梁布置在轧机入口,一组是喷射在工作辊辊缝间的工艺润滑喷梁,一组是喷射在工作辊辊面上由板形仪控制的分段冷却喷梁。
原设计的乳化液喷射和出口的吹扫装置布置如图1所示,带钢吹扫装置全部位于带钢的上表面,主要由三部分组成:第一部分由封闭挡板、气帘和上吹扫组成,用于阻挡防缠导板上部的乳化液,位于上防缠导板上方。
气帘是防止乳化液从防缠导板与工作辊之间间隙落到板面上,在轧辊旋转和气帘的共同作用下,该间隙区域形成低压真空区,很好地阻止了乳化液滴落到板面上。
上吹扫用于吹扫支撑辊和工作辊的辊缝区,吹扫的气流把辊身带过来的乳化液从两侧吹落到上防缠导板上,导板上的收集槽将吹落的乳化液导流到机架的两侧。
封闭挡板用于将机架上部与出口进行有效隔离,设计在挡板上面的阶梯式导流槽负责把飞溅到挡板区域的乳化液排到机架两侧。
第二部分是下吹扫集管,位于上防缠导板的下方。
压缩空气被两根 f42.4 mm的管子引入一个集气室后,再由宽580 mm且上下两层圆弧形布置的喷嘴吹出,能够形成强有力的吹扫。
冷轧乳化液吹扫系统的改进
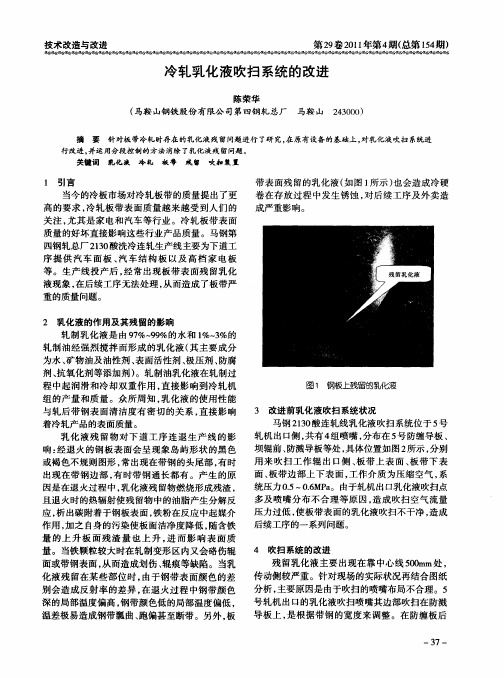
行改进 。 并运 用分段控制 的方 法消除 了乳化液残 留问题 。 关键词
1 引言
当今 的冷板 市场 对冷 轧 板 带 的质 量 提 出 了更
高的要求 , 冷轧板带表面质量越来越受到人们的 关注, 尤其是家 电和汽车等行业 。冷轧板带表面 质量的好坏直接影响这些行业产品质量 。马钢第 四钢 轧 总厂 23 酸洗 冷 连轧 生产 线 主要 为下 道 工 10 序 提供 汽 车面 板 、 汽车结 构板 以及 高档家 电板 等 。生产线投产后 , 经常出现板带表面残 留乳化 液现象 , 在后续工序无法处理 , 从而造成了板带严 重 的质 量 问题 。
带表 面 残 留的 乳化 液 ( 图 l 示 ) 会造 成 冷 硬 如 所 也 卷在存放 过程 中发生锈蚀 , 对后续工序及外卖造 成 严重 影 响 。
2 乳化液的作用及其残留的影响 轧 制 乳 化 液 是 由 9%~ 9 7 9 %的水 和 l 3 %~ %的 轧制油经强烈搅拌 而形成的乳化 液( 主要成分 其 为水 、 矿物油及 油性剂 、 表面活性剂 、 极压剂 、 防腐 剂、 抗氧化剂等添加剂 ) 。轧制油乳化液在轧制过 图 1 钢板上残 留的乳化液 程中起润滑和冷却 双重作用 , 直接影 响到冷轧机 组 的产量和质 量。众所周知 , 乳化液 的使用性能 与轧后带钢表面清洁度有 密切 的关 系 , 直接影响 3 改进前 乳化 液 吹扫 系统状 况 马钢 2 3 酸连 轧 线 乳化 液 吹 扫 系统 位 于 5 10 号 着 冷 轧产 品 的表面 质量 。 共有 4 组喷嘴 , 分布在 5 防缠导板 、 号 乳 化液 残 留物 对下 道工序 连退生 产线 的影 轧机 出口侧 , 防溅导板等处 , 具体位置如 图2 所示 , 分别 响 : 退 火 的钢 板 表 面会 呈 现 象 岛 屿 形 状 的 黑 色 坝辊前 、 经 板带上表 面 、 板带下 表 或褐色不规则图形 , 常出现在带钢的头尾部 , 有时 用来 吹扫工作 辊 出 口侧 、 面、 板带边部上下表面 , 工作介质为压缩空气 , 系 出现在带钢边部 , 有时带钢通长都有 。产生的原 .~06 P 。 因是 在退 火 过 程 中 , 化 液残 留物燃 烧 形 成残 渣 , 乳 统 压力 05 .M a 由于 轧机 出 口乳 化 液吹 扫点 造 且退火时的热辐射使残留物 中的油脂产生分解反 多及喷嘴分布不合理等原 因, 成吹扫空气流量 压力过低 , 使板带表面的乳化液吹扫不干净 , 造成 应 , 出碳附着于钢板表面 , 析 铁粉在反应中起媒介 作用 , 加之 自身的污染使板面洁净度 降低 , 随含铁 后续工序 的一系列问题 。 量 的上 升板 面残 渣 量也 上升 , 而影 响表 面质 进 量。当铁颗粒较大时在轧制变形 区内又会硌伤辊 4 吹扫 系统 的 改进 残 留乳化液主要出现在靠 中心线 50 m处 , 0r a 面或带钢表面 , 从而造成划伤 、 辊痕等缺 陷。当乳 化液残 留在某些 部位时 , 由于钢带表 面颜色 的差 传 动侧较严重 。针对现场的实际状况再结合图纸 主要原因是 由于吹扫的喷嘴布局不合理。5 别会造成反射率的差异 , 在退火过程 中钢带颜色 分析 , 号轧机 出口的乳化液吹扫喷嘴其边部吹扫在防溅 深的局部温度偏高 , 钢带颜色低的局部温度偏低 , 是根据带钢 的宽度来调整。在防缠板后 温差极易造成钢带瓢 曲、 跑偏甚至断带。另外 , 板 导板上 ,
六辊可逆冷轧机组的乳化液的研究与应用

乳化 液 的功 用 介 绍
洗。 1 乳化液的润滑功能
二 、乳 化 液成 分 及 主 要 功 能 控 制
乳化液 的性能或稳定性 的变化 ,除温度的 因素外 ,基本是 由是 内部各组分变化所造成 的。下表列出了乳化液 的一般组分及含量 。 乳化液的一般组分
组分 水 轧制油 含 量 > 8 5 % 0 . 5 %一 1 O %
在 轧钢过程 中 ,在一定 的温 度和压力 条件下 ,分散 于乳化液 中 的轧制油 以物理 吸附和化学 吸附两种方式 吸附于钢板 和轧辊表面形 成油膜 ,为轧制提供必要的润滑。作 为轧制油或乳化液的最基本的功 能 ,油品润滑 的设计和应用水平 ,对冷 轧工序最终结果有着决定性 的 影 响。良好 的润滑可以达到如下 目的[ 1 】 : ( 1 ) 节能 良好的润滑可有效降低摩擦力 ,良好 的挥发性可 降 低退火时间。 ( 2)降低辊耗 。 ( 3 ) 改善板形 好 的润滑有利于板形控制 ,可降低厚度 波动 , 有利于表 面结构 。 ( 4)提高板面清洁度及改善板 面状态 。 正常平稳 的轧制需要 轧制油提供均 衡稳定 的润 滑 ,即轧制 油除 必须保证 稳定的物理和化学特性外 ,还必须保 持数量上 的,即吸附量 的稳定。由于轧制 油通过分散于乳化液中进行应用 ,因此 ,很容易理 解 ,上述两点的控制必须 由乳化液稳定性 的控制来得以实现。 2 乳 化液的冷却性能 轧制过程 中工件发生 变形所产 生的大量 的热 ,也需要 由乳化液 带走 ,正确控制乳化液 的流量和喷射部份 ,可以有效控制板温 ,并调 节板形。在应用乳化液的冷却功能时 ,除板温的控制外 ,可 以通过乳 化液 流量 的位置 的控制 ,使 轧辊 的不 同部份产 生不同程度 的热胀冷 缩 ,达到控制板形 的 目的。
轧机工艺润滑站乳化液磁性过滤器改进

轧机工艺润滑站乳化液磁性过滤器的改进摘要:本文针对对传统轧机工艺润滑站磁性链条频繁断裂问题进行客观分析,找出造成链条断裂的各种原因,通过对磁性链条及刮铁装置的改进,成功解决了磁性链条频繁断裂的问题,减少了更换链条的次数,节约了轧钢过程中的成本,并提高了生产效率。
关键词:工艺润滑站;磁性链条;断裂;改进我公司为浙江协和薄板有限公司制作的1150六辊可逆冷轧机组在使用过程中,发现其中工艺润滑站乳化液磁性过滤器上的磁性链条断裂频繁,导致乳化液不能循环使用,需不停更换,既浪费企业资源又污染环境。
并且更换链条又比较麻烦,需要贮备大量备件,链条成本比较高,这些都造成成本增加。
一. 工艺润滑站磁性过滤器的工作原理磁性过滤器由吸铁装置、刮铁装置两部分组成:吸铁装置由上下两组材质为聚氨脂的六角链轮组和数条磁性链条缠绕在链轮上的磁性链条组成,下面那组链轮布置在乳化液收集箱箱体底部;刮铁装置主要由刮板、导向套、支架组成,它被布置在吸铁装置上下两组链轮组中间。
在工作过程中由链轮带动磁性链条循环运动,磁性链条的链节在穿过乳化液时会将乳化液从机组带来的铁屑吸在链节外圆上,将其带出乳化液,在通过刮铁装置时,刮板将铁屑从链节上刮下来,储存在支架的集屑槽中,从而净化用过的乳化液,使其能够循环使用。
二. 磁性链条频繁断裂的原因分析针对使用中出现的问题,经过仔细研究分析图纸,并观察磁性链条断裂部位并不在链节之间的铰接处,而是在链节上铰接头与不锈钢管之间的环形焊缝处,所以得出结论认为,造成磁性链条断裂的原因有两个:1. 磁性链条的链节本身焊接强度不足。
2. 刮铁装置设计不太合理,铁屑容易滑进铜刮板与链条之间的缝隙里,一旦铁屑卡住,链条将不能向下运动,而链轮在电机带动下仍要运转,从而拉裂链节。
下面是磁性链条的磁性链节图下图是刮铁装置简图具体分析如下:1. 从磁性链条链节图中可以看出在铰接头与不锈钢管之间的环形焊缝只有1.2mm,按照我们重机行业焊接方式根本就不可能焊透,只是在表面焊了一层焊肉,经机加工与不锈钢管外圆接平后,只能留下薄薄一层,作为过渡桥梁用,掩盖铰接头与钢管之间的接缝,链节在通过刮铁装置时,铜刮板不至卡接缝里,没有焊接强度,真正起连接作用、有焊接强度的只有4-φ5的塞焊孔,焊接强度比较弱。
综合实训--六辊板带可逆冷轧机液压伺服控制系统

1150mm六辊板带可逆冷轧机液压伺服控制系统目录目录第1章绪论 (1)1.1轧机位置控制系统发展情况 (1)1.1.1 液压位置控制系统发展情况 (1)1.1.2 控制理论及技术的发展 (1)1.2国内外研究情况简介 (6)1.2.1 国外概况 (6)1.2.2 国内概况 (7)第2章液压系统原理的设计 (8)2.1技术及工艺要求 (8)2.1.1 系统的要求 (8)第3章液压伺服控制系统设计 (9)3.1液压伺服板厚控制的基本原理 (9)3.2轧机数字闭环厚度控制 (10)1.1 轧机位置控制系统发展情况:第一种是手动压下调节板厚。
最早的轧机是靠手动调节压下螺丝来进行辊缝调节的。
这种调节方式仅能设定原始辊缝,无法达到厚度控制精度的要求,因而在板带轧机上已经基本不再采用。
第二种是电动压下调节板厚。
手动压下的调节方式缺点很多,所以在电机出现之后,人们就将它用到轧机上.不仅采用电机驱动,而且压下调节也采用电动方式,由电机通过减速装置驱动压下螺丝来设定原始辊缝。
这种调节方式一般不能在线调节,无法保证严格的厚度精度,因而目前只在开坯和厚板轧机上使用,板带轧机上很少用。
第三种是液压压下调节板厚。
1.1.1液压位置控制系统发展情况:(1)是电—液双压下系统调节装置。
电—液双压下系统也是由粗调和精调两部分组成的,其中粗调部分就是一般的电动压下装置,用它来设定原始辊缝。
精调部分采用液压系统,其具体结构方式有多种。
如用液压缸推动扇形齿轮以带动压下螺丝以及将液压缸直接放在轴承座与压下螺丝或压下横粱之间等方式。
这种调节方式的精调系统较为灵活,调节精度高。
特别是这种系统的粗调系统可以是一般的电动压下,因而这种方式特别适用于对旧轧机的改造,目前仍在采用。
(2)是全液压压下调节装置。
全液压压下的厚度调节系统取消了传统的压下螺丝,用液压缸直接压下,这种厚度调节方式结构简单,灵敏度高,能够满足很严格的厚度精度要求.并可根据需要,改变轧机的当量刚度,是现代化轧机上普遍采用的厚度调节方式。
950 mm六辊可逆冷轧机工艺润滑系统改造

950 mm六辊可逆冷轧机工艺润滑系统改造王永胜;侯元新;燕照顺;陈普;朱爱美【摘要】950 mm六辊可逆冷轧机工艺润滑系统改造中,安装6台大流量的乳化液泵,乳化液平床过滤机改造为霍夫曼平床过滤机,乳化液喷射梁改造为DN80 mm的管道,在乳化液净油箱内增设机械搅拌器,乳化液加热方式由电加热改为蒸汽加热,对轧制工艺进行优化.工艺润滑系统改造完成后,月节电10.58万元,乳化液的流量提高到6 000 L/min,提高了冷轧产品板面清洁度.【期刊名称】《山东冶金》【年(卷),期】2018(040)001【总页数】1页(P73)【关键词】六辊可逆冷轧机;工艺润滑系统;乳化液泵;蒸汽加热;轧制工艺【作者】王永胜;侯元新;燕照顺;陈普;朱爱美【作者单位】山东泰山钢铁集团有限公司,山东莱芜271100;山东泰山钢铁集团有限公司,山东莱芜271100;山东泰山钢铁集团有限公司,山东莱芜271100;山东泰山钢铁集团有限公司,山东莱芜271100;山东泰山钢铁集团有限公司,山东莱芜271100【正文语种】中文【中图分类】TG333.1泰钢冷轧部950 mm六辊可逆冷轧机工艺润滑系统主要的作用是在轧制过程中对轧辊表面和钢带进行润滑和冷却。
工艺润滑系统主要包括净液输送系统和污液净化系统,以及乳化液压力、流量、方向控制装置、轧辊冷却装置等。
其中轧辊冷却装置由电磁气控阀、喷射梁及操作控制箱等组成。
喷射梁上喷嘴的开、关由PLC控制电磁气控阀实现。
在轧机牌坊前、后侧各装有6根喷射梁,形成上下各4排喷嘴,通过对喷嘴流量的调节,达到控制板形和提高板面清洁度的目的。
950 mm六辊可逆冷轧机工艺润滑系统存在以下3方面问题:1)由于乳化液系统压力低,乳化液流量达不到生产工艺要求。
2)平床过滤机经过多年的运行,设备精度下降,无法对乳化液中的杂质进行有效过滤,造成钢卷在轧制过程中产生黑斑、黄斑和板形质量等缺陷,影响产品质量的提高。
3)乳化液加热时采用48组电加热器进行加热,每组电加热器的耗电量每小时为8 kW·h,耗电量较高,提温效率低。
1450mm六辊可逆冷轧机自动控制系统的研究与应用

来料宽度 90—15 mm; 0 20
成 品厚 度 02—1 m; . . 0m 成 品 内径 5 0mm; 1 成 品 外 径 ( 0 —9 0 m 1 0 0 m; 9 最 大 轧 制 力 1 0 N; 500k
2 设 备组成
摘 要: 介绍 了 自主开发设计的 六辊 可逆冷轧机的主要参数 、 备构成及 自动控制 系统的组成 、 设 结构和功 能, 由于 自动控制 系统 采用
了 先进的网络通讯技术及灵活多变 的控制方式. 所以实 现了高 速轧制, 且保证了 产品质量。
关键词 : 辊可逆冷轧机 ; 六 自动 控 制 系统 ; 能 功 中 图分 类 号 : G3 T 3 文献标识码 : B 文章 编 号 :6 2 5 5 ( 0 0)s-o 8 0 17 - 4 X 2 1 o . 8 - 2 : o
15 l 4 0mn六辊可逆冷 轧机是 中冶陕压重工设备 有限公 司 具有 自主知识 产权 、 自主研 制开发 的机 、 、 电 液一体化 全部成
轧制速度( x 0 / i( Ma )1 0mr n8=02~08衄 ) 0 a . . ;
穿 带 速 度 1 / i。 8mr n a
运行 状态 的监视 和报警 , 液压 站 、 滑站 等的工艺 控 制 , 润 主轧
机 的速度 控制 和显示 , 开卷 机和卷取 机的恒张力 控制 , 主轧机 轧辊 负荷 平衡控 制 , 断带检测 和保护 , 上卷小 车 、 卸卷小 车、 乳Байду номын сангаас 液流量 、 向等 工艺操 作控 制 , 长计算 , L 、2级系 统进 方 带 与 DL 行信息交换 。 L 2级系统 为监控级 自动化系统 ,主要 由装 在研华工控机 中的 WiC n C监控 系统组 成 , 主要实 现 以下 功能 : 其 轧机 生产
莱钢1500冷轧机组乳化液系统工艺技术改造
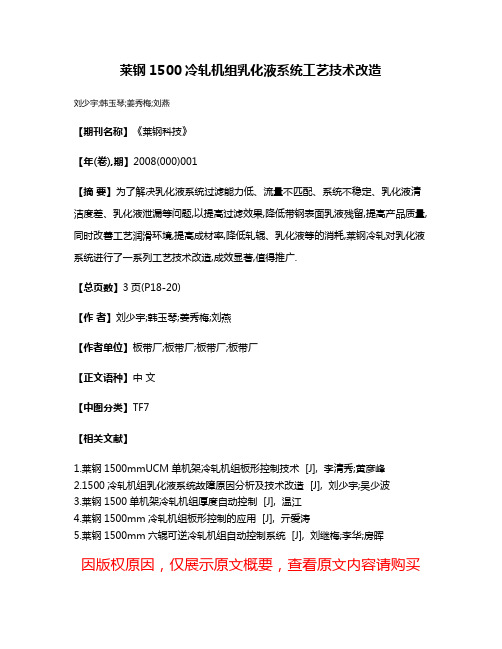
莱钢1500冷轧机组乳化液系统工艺技术改造
刘少宇;韩玉琴;姜秀梅;刘燕
【期刊名称】《莱钢科技》
【年(卷),期】2008(000)001
【摘要】为了解决乳化液系统过滤能力低、流量不匹配、系统不稳定、乳化液清洁度差、乳化液泄漏等问题,以提高过滤效果,降低带钢表面乳液残留,提高产品质量,同时改善工艺润滑环境,提高成材率,降低轧辊、乳化液等的消耗,莱钢冷轧对乳化液系统进行了一系列工艺技术改造,成效显著,值得推广.
【总页数】3页(P18-20)
【作者】刘少宇;韩玉琴;姜秀梅;刘燕
【作者单位】板带厂;板带厂;板带厂;板带厂
【正文语种】中文
【中图分类】TF7
【相关文献】
1.莱钢1500mmUCM单机架冷轧机组板形控制技术 [J], 李清秀;黄彦峰
2.1500冷轧机组乳化液系统故障原因分析及技术改造 [J], 刘少宇;吴少波
3.莱钢1500单机架冷轧机组厚度自动控制 [J], 温江
4.莱钢1500mm冷轧机组板形控制的应用 [J], 亓爱涛
5.莱钢1500mm六辊可逆冷轧机组自动控制系统 [J], 刘继梅;李华;房晖
因版权原因,仅展示原文概要,查看原文内容请购买。
1420酸轧机组乳化液吹扫装置的分析及改进

喷 嘴吹 出 的压缩 空气 在 防缠板 前端 与表 面 的 乳 化 将
离开本 来 的流 动方 向并 随着 凸 出的物 体表 面流 动
・
3 6・
梅 山科 技
21 0 0年第 6期 压缩 空气 从 进 口输 入 , 入 环形 腔 , 由环 进 并
乳 化液 。
置 ,交 替 布 置 ,保 证 在 任 意 带 宽 都 能 抽 吸 到 乳
化液。
1 2 应 用 原 理 .
2 缝式 喷嘴 )
位 于上 防缠 板 的前 端 , 缝 式 从
气幕 的产 生 主要 是 依 靠 压 缩 空 气 , 用 的是 应 柯 恩 达空 气放 大效 应 , 流体 ( 流或 气 流 ) 有 即 水 具
1 直 吹喷 嘴 ) 上 防 缠 板 上 方 安 装 有 2个 喷
将 4根钢 管 固定 在 支 架 上 , 管 头部 环 形 喷 嘴 对 钢
正 轧辊 辊缝 。通 过 压缩 空气 吹扫 , 带 钢 上 表 面 将
残 留的少 量乳 化 液 吹 向 带 钢两 侧 , 乳 化 液 从 带 使
钢 的两侧 流下 , 由下 一 步 的抽 吸 式喷 嘴吸 走 。 4 抽 吸式 喷 嘴 安 装 在 下 防 缠 板 上 ,将 带 )
钢 边缘 和下 表 面上残 留的乳化 液 吸净 ,直 接排放 到 乳化 液收 集槽 中。抽 吸 的范 围覆 盖 了带材 宽度
变化 的范 围 ,沿 带材 方 向设 置 了前 后两 排抽 吸装
嘴, 固定在 牌坊 窗 口的横 梁 上 , 喷嘴 正对 着上 工作
辊 与上 中间辊 之 问 的辊 缝 , 于 吹 扫辊 缝 之 间 的 用
的倾 向。当流体 与其流 过 的物 体表 面之 间存 在表
- 1、下载文档前请自行甄别文档内容的完整性,平台不提供额外的编辑、内容补充、找答案等附加服务。
- 2、"仅部分预览"的文档,不可在线预览部分如存在完整性等问题,可反馈申请退款(可完整预览的文档不适用该条件!)。
- 3、如文档侵犯您的权益,请联系客服反馈,我们会尽快为您处理(人工客服工作时间:9:00-18:30)。
莱钢冷轧六辊可逆轧机乳化液吹扫系统综合改造
为消除带钢表面乳化液斑,提高冷轧带钢表面质量,莱钢银山型钢冷轧薄板对乳化液吹扫系统进行综合改造。
通过对防缠导板、板面吹扫系统、乳化液喷射系统、电控设计四个方面进行优化设计改造,有效解决了原乳化液吹扫系统所带来的带钢表面质量问题。
标签:防缠导板;板面吹扫系统;乳化液喷射系统;电控设计
1概述
冷轧带钢在轧制过程中,乳化液作为轧制润滑和冷却的介质在轧钢过程中起着非常重要的作用。
同时在轧制过程中乳化液能否从带钢板面充分吹扫干净对轧后板面质量影响非常大。
目前冷轧生产线可逆轧机面临的最大问题就是轧后板面乳化液不能有效吹扫干净,造成乳化液斑迹缺陷(根据严重程度从褐色到黑色),俗称“油烧”斑迹。
乳化液斑迹实际上是乳化液在较高的温度下(一般80度以上)与板面发生化学反应的结果,乳化斑迹在脱脂段无法清洗掉。
而且在罩式退火阶段,乳化液斑迹也很难被去除。
所以目前乳化液斑迹是困扰冷轧生产线提高产品质量的一个重要缺陷,尤其是罩退投产后,对以生产退火板为主的工艺来说,板面乳化液斑迹缺陷将是制约产品质量提高的一大瓶颈。
2吹扫现状分析及存在问题
⑴吹扫系统无法将带钢表面的乳化液彻底吹净
目前的乳化液吹扫系统设计比较简单,由一对乳化液挡辊、空气吹扫梁以及安装在吹扫梁上的空气喷嘴组成。
首先,由挡辊封住带钢从机架中带出的大部分乳化液,然后通过空气吹扫板面残留的部分乳化液。
在实际生产中,乳化液一旦聚集在板面上,通过吹扫很难完全从板面上去除,只是在带钢表面沿吹扫方向将乳化液“摊平”:在钢板板面乳化液较多时候,不能有效去除板面的乳化液;而乳化液较少的时候,通过吹扫的作用在板面上会形成明显的吹扫斑纹。
⑵挡辊的封堵效果不佳
乳化液挡辊对于轧制较厚的产品时对乳化液的封堵效果较好,但当轧制薄规格产品时由于板型不易控制,当出现中浪、1/4浪或边浪时,挡辊不能充分贴住带钢表面,会有乳化液连续或不连续地从挡辊缝隙中带出而夹带到钢带板面,乳化液的封堵效果不佳。
并且挡辊有时和高速运动的带钢不能同步旋转,划伤带钢表面造成表面缺陷。
⑶防缠导板故障率高无法正常投入使用
由于冷轧生产对辊面光洁度要求高,一旦出现划痕将直接影响到带材表面的光洁度,因此工作辊的更换比较频繁。
换辊时需要将防缠导板移出,换辊结束后再将防缠导板移回。
当出现带钢断带、跑偏、堆钢后极易造成防缠导板的脱落、漏油和变形,轻者造成机构的无法动作影响换辊,重者造成工作辊划伤,甚至无法穿带。
由于该机构处于内部,检修人员无法进入,维修耗时长,严重影响生产效率。
3改造方案
轧机在生产过程中出现的斑迹主要是由于目前的带钢表面吹扫系统存在较大的设计缺陷引起,为了从根本上解决目前乳化液夹带造成的板面质量问题,需要对目前板面吹扫系统、乳化液喷射系统以及断带防缠与保护系统进行综合改造。
3.1防缠导板
在轧机工作辊出口侧轧制线的上方和下方分别安装防缠导板,其作用一是用于穿带时引导带头,二是断带时防止带钢缠住工作辊,三是保护乳化液喷射系统和空气吹扫系统的喷梁和喷嘴。
其工作模式为:奇数道次轧制运行时,出口侧防缠导板与工作辊之间保持一定的距离,入口侧喷射梁进行乳化液冷却喷射,防缠板组进入机架防护位置并带动吹扫装置一并进入辊区工作。
偶道次轧制运行时,防缠导板移出并保持一定的距离,为工作辊乳化液喷梁留出喷射空间,同时起到保护乳化液喷梁和喷嘴的作用。
防缠导板的移进和移出是通过液压控制来实现。
防缠导板移出通过限位来检测,在移出的限位被激活后,表明防缠导板已退出,液压控制中断,电磁阀失电;防缠导板移进时的位置通过机械位置来调整,在防缠导板安装后根据实际最大辊径来确定导板移进的最大机械行程和位置,此时,液压控制并不中断,电磁阀始终保持移进方向的得电工作状态。
轧机更换工作辊/中间辊/支承辊之前,防缠导板移出,使辊系进出时有必需的工作空间。
3.2板面吹扫系统
针对轧机吹扫的实际情况,对轧机吹扫系统进行全面改造,在机架内增设集防缠导板于一体的吹扫机构和抽吸装置,上防缠导板单侧布置二排吹扫装置、下防缠板采用抵近式抽吸装置设计,有效封闭来自于中间辊、支撑辊冷却带出的乳化液溅落到轧制后的带钢表面,如图1所示。
(1)上防缠导板
A.采用底部封闭式设计(目前的防缠导板由于机架内乳化液喷射系统的布局及换辊轨道的布置原因,底部设计成镂空的)。
B.上防缠导板的边沿增加乳化液收集导流槽,保证溅落到防缠导板上的乳化液顺导槽流到机架的两侧,而不流到带钢表面。
C.在防缠导板工作状态,防缠导板与工作辊之间留有一必要的间隙,为防止乳化液从该间隙落到板面上,在防缠导板上设计特殊的气刀,同时通过轧辊的旋转作用,在该间隙区域形成低压真空区,进一步隔离乳化液往板面滴落。
(2)第一排吹扫
在上防缠导板的上方安装第一排吹扫,吹扫工作辊和中间辊的辊缝区,利用吹扫的气流收集从所有辊身带出的乳化液,收集的乳化液被气流带到防缠导板的收集槽内,乳化液从收集槽流到机架的两侧,避免流到板面上。
(3)第二排吹扫
在上防缠导板的内下方安装第二排吹扫,主要干燥带钢表面,吹净带钢表面残余的乳化液。
在带钢出辊缝区很短的距离内,乳化液在板面上还没有时间和空间形成条状时,迅速将板面的乳化液吹离板面,干燥带钢表面。
第二排吹扫与上防缠导板同时动作,在断带等异常情况下,防缠导板起到保护吹嘴的作用。
(4)下防缠板
安装在板带下方,采用贴近的抽吸装置用于抽吸板带下表面的乳化液。
抽吸
装置采用小体积流量的压缩空气产生高速、大体积的低压气流。
体外供给的压缩空气进入一个环形的气室,压缩空气被环形气缝节流后,沿抽吸环形腔的周围产生高速的气流,该高速气流引起一个压力差,从而带动周围大量的空气通过真空抽吸装置实现去和带钢下表面乳化液的作用。
抽吸装置与下防缠导板同时动作,并贴近带钢下表面,在断带等异常情况下,防缠导板起到保护抽吸器的作用。
(5)上表面附加防溢吹扫系统
目前,在轧制换向阶段,积累在带钢上表面的乳化液非常容易卷到钢卷中,造成头尾比较严重的乳化液斑迹。
为了有效消除换向过程中造成的夹带,在轧机的双侧增加防溢吹扫机构。
(6)气源及喷嘴选择
①出入口防溢吹扫喷梁:单侧采用复合双排形式,根据最大板面的宽度1500mm,单排布置15个209型喷嘴,双排三段合计30个,以每段双排10各喷嘴的布局耗气量约114Nm3/h,该喷梁耗气量约为342Nm3/h,则出入口喷梁耗气总量为684Nm3/h。
②出口辊缝区域吹扫:安装710型喷嘴双件组合,单件耗气量约为216Nm3/h,双件组合耗气量约为432Nm3/h。
③上防缠导板吹扫:上防缠导板上布置有上表面次边部吹扫、边部吹扫以及辊面气刀吹扫三部分。
次边部吹扫安装710型喷嘴双件组合,耗气量约为432Nm3/h;安装在上板顶端贴近辊面的辊面气刀耗气量约为400Nm3/h;边部吹扫安装710型喷嘴双件组合,总耗气量约为432Nm3/h。
④空气抽吸器:安装在下板近前端贴近带钢下表面的空气抽吸器,共16套,单套耗气量约为19.3Nm3/h,总耗气量约为310Nm3/h。
⑤下表面吹扫:安装在卷取机方向的出口固定导板台下方位置,705型喷嘴,总耗气量约为570Nm3/h。
综上,整个吹扫系统的改造总耗气量约为3056Nm3/h,吹扫压力为0.6-0.7MPa。
吹扫喷嘴选用思万特的冷轧带钢用N973空气吹扫静音喷嘴。
3.3乳化液喷射系统
由于目前机架内安装防缠导板的空间非常小,主要是由于换辊轨道梁和辊缝冷却的乳化液喷射梁占据了防缠导板的主要位置,所以需要对现有入口、出口乳化液喷梁的安装位置和机架内乳化液管道需要进行改造和调整,为增装防缠板留出必要的空间。
3.4电控设计
在现场轧机操作面板上安装防缠导板控制系统,分别控制轧机入口和出口侧上下防缠导板的进出,按钮的输入信号输入到现场总线中(ET200),控制和驱动防缠导板的液压设备。
防缠导板使用限位检测元件确认实际位置状况。
在轧制时如果机架出口的防缠导板在进入位置时,机架入口的防缠导板必须在退出位置,轧机入口侧的乳化液喷射,轧机出口侧的吹扫投入工作。
轧机机架乳化液喷射选用分段控制方式。
轧机机架吹扫控制选用两段控制,分为中段和边部吹扫。
在一般正常轧制时机架的吹扫将全部打开,但是在轧制最小宽度带钢时,操作人员可以根据带钢的实际情况,将边部的带钢吹扫关闭。
电气关于软件的修改,在原有PLC上进行修改和优化,不再新增PLC。
4结语
改造后,通过乳化液吹扫系统有效的工作可以达到各种规格的带钢表面基本无肉眼可见的乳化液液滴,基本消除带钢表面乳化液残留而导致的乳化液斑迹。
防缠导板投入使用后,大大减少高速断带造成的带钢缠辊;同时防缠导板还可以在断带时有效地防护吹扫喷嘴和乳化液喷嘴等机架内重要装备,免受高速断带时带钢的冲击。