模压工艺生产操作-成型工艺知识讲解
模压成型工艺流程

模压成型工艺流程模压成型工艺流程模压成型是一种常见的塑料制品加工工艺,通过热塑性塑料在高温和高压的条件下,使其在模具中快速冷却固化,形成所需的产品形状。
模压成型通常适用于生产大批量的塑料产品,具有生产效率高、产品质量稳定等优点。
下面将详细介绍一下模压成型的工艺流程。
首先,模压成型的第一步是准备原材料。
通常情况下,模压成型使用的是热塑性塑料颗粒。
在生产之前,需要对原料进行检查和筛选,确保原料无异物、无杂质。
第二步是将选好的原料放入料斗中。
料斗是一个用于存放和输送塑料颗粒的设备,其底部连接着一个加热器。
原料通过料斗进入加热器,在加热器的作用下,原料被加热至熔点。
第三步是将熔化好的塑料料利用螺杆输送机送进模具中。
螺杆输送机是一个直径逐渐变小的圆柱形装置,螺杆在内壁上旋转,将熔化好的塑料颗粒从料斗中带到模具中。
在螺杆的作用下,塑料颗粒逐渐被推入到模具的加压区域。
第四步是施加高温高压。
当塑料颗粒填满模具加压区域后,需要施加高温高压。
通过加热元件给模具加热,使模具中的塑料保持在熔化状态。
同时,通过液压系统给模具施加高压,使塑料颗粒充分融合,并填满整个模具的空腔。
第五步是冷却固化。
在塑料充分融化并填满整个模具之后,需要将模具和塑料冷却至固化状态,使产品形成所需的形状。
通常情况下,可以通过给模具注入冷却水、冷风等方式进行快速冷却。
第六步是模具开启和取出成品。
当塑料完全冷却固化后,可以将模具开启,取出成品。
通常情况下,需要用工具将成品从模具中取出,并进行后续的检验和包装操作。
最后,整个模压成型的工艺流程就完成了。
需要注意的是,模压成型工艺中需要控制好加热温度、压力和冷却速度等参数,以保证产品质量的稳定和一致性。
总的来说,模压成型是一种常见的塑料制品加工工艺,通过一系列的步骤将熔化的塑料填充到模具中,并进行高温高压和冷却固化等操作,最终形成所需的产品。
模压成型工艺具有生产效率高、产品质量稳定等优点,被广泛应用于塑料制品的生产中。
模压成型工艺
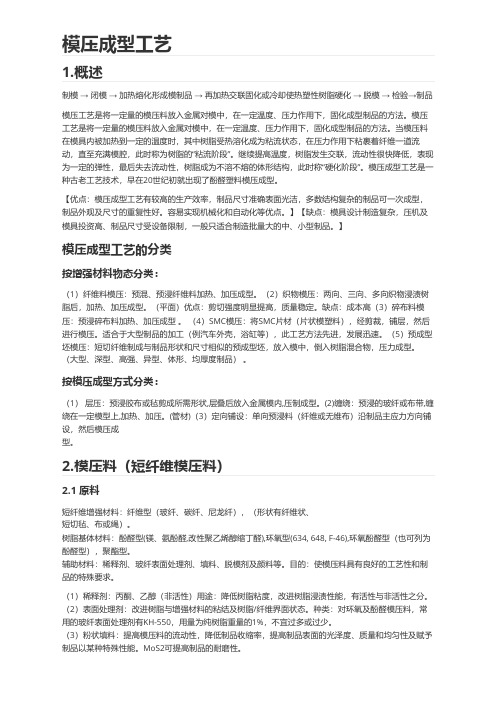
模压成型工艺1.概述制模→闭模→加热熔化形成模制品→再加热交联固化或冷却使热塑性树脂硬化→脱模→检验→制品模压工艺是将一定量的模压料放入金属对模中,在一定温度、压力作用下,固化成型制品的方法。
模压工艺是将一定量的模压料放入金属对模中,在一定温度、压力作用下,固化成型制品的方法。
当模压料在模具内被加热到一定的温度时,其中树脂受热溶化成为粘流状态,在压力作用下粘裹着纤维一道流动,直至充满模腔,此时称为树脂的“粘流阶段”。
继续提高温度,树脂发生交联,流动性很快降低,表现为一定的弹性,最后失去流动性,树脂成为不溶不熔的体形结构,此时称“硬化阶段”。
模压成型工艺是一种古老工艺技术,早在20世纪初就出现了酚醛塑料模压成型。
【优点:模压成型工艺有较高的生产效率,制品尺寸准确表面光洁,多数结构复杂的制品可一次成型,制品外观及尺寸的重复性好。
容易实现机械化和自动化等优点。
】【缺点:模具设计制造复杂,压机及模具投资高、制品尺寸受设备限制,一般只适合制造批量大的中、小型制品。
】模压成型工艺的分类按增强材料物态分类:(1)纤维料模压:预混、预浸纤维料加热、加压成型。
(2)织物模压:两向、三向、多向织物浸渍树脂后,加热、加压成型。
(平面)优点:剪切强度明显提高,质量稳定。
缺点:成本高(3)碎布料模压:预浸碎布料加热、加压成型。
(4)SMC模压:将SMC片材(片状模塑料),经剪裁,铺层,然后进行模压。
适合于大型制品的加工(例汽车外壳,浴缸等),此工艺方法先进,发展迅速。
(5)预成型坯模压:短切纤维制成与制品形状和尺寸相似的预成型坯,放入模中,倒入树脂混合物,压力成型。
(大型、深型、高强、异型、体形、均厚度制品)。
按模压成型方式分类:(1)层压:预浸胶布或毡剪成所需形状,层叠后放入金属模内,压制成型。
(2)缠绕:预浸的玻纤或布带,缠绕在一定模型上,加热、加压。
(管材)(3)定向铺设:单向预浸料(纤维或无维布)沿制品主应力方向铺设,然后模压成型。
复合材料模压成型工艺过程
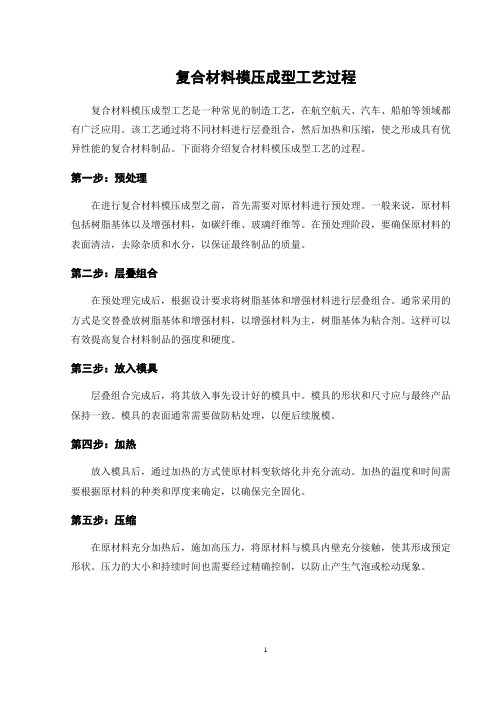
复合材料模压成型工艺过程复合材料模压成型工艺是一种常见的制造工艺,在航空航天、汽车、船舶等领域都有广泛应用。
该工艺通过将不同材料进行层叠组合,然后加热和压缩,使之形成具有优异性能的复合材料制品。
下面将介绍复合材料模压成型工艺的过程。
第一步:预处理在进行复合材料模压成型之前,首先需要对原材料进行预处理。
一般来说,原材料包括树脂基体以及增强材料,如碳纤维、玻璃纤维等。
在预处理阶段,要确保原材料的表面清洁,去除杂质和水分,以保证最终制品的质量。
第二步:层叠组合在预处理完成后,根据设计要求将树脂基体和增强材料进行层叠组合。
通常采用的方式是交替叠放树脂基体和增强材料,以增强材料为主,树脂基体为粘合剂。
这样可以有效提高复合材料制品的强度和硬度。
第三步:放入模具层叠组合完成后,将其放入事先设计好的模具中。
模具的形状和尺寸应与最终产品保持一致。
模具的表面通常需要做防粘处理,以便后续脱模。
第四步:加热放入模具后,通过加热的方式使原材料变软熔化并充分流动。
加热的温度和时间需要根据原材料的种类和厚度来确定,以确保完全固化。
第五步:压缩在原材料充分加热后,施加高压力,将原材料与模具内壁充分接触,使其形成预定形状。
压力的大小和持续时间也需要经过精确控制,以防止产生气泡或松动现象。
第六步:冷却经过加热和压缩后,复合材料开始冷却固化。
在这个过程中,保持模具的压力不变,直至完全固化为止。
冷却时间的长短取决于原材料的性质和厚度。
第七步:脱模当复合材料完全固化后,打开模具,将制成的复合材料制品取出。
在脱模的过程中,需要小心操作,以避免损坏制品表面或内部结构。
通过以上步骤,复合材料模压成型工艺完成。
这种工艺具有制作周期短、成本低、制品质量高等优点,因此在工业生产中得到广泛应用。
复合材料制品具有重量轻、强度高、耐腐蚀等特点,在现代制造业中发挥着重要作用,也在未来的发展中将有更广阔的应用前景。
模压成型工艺过程包括哪些内容
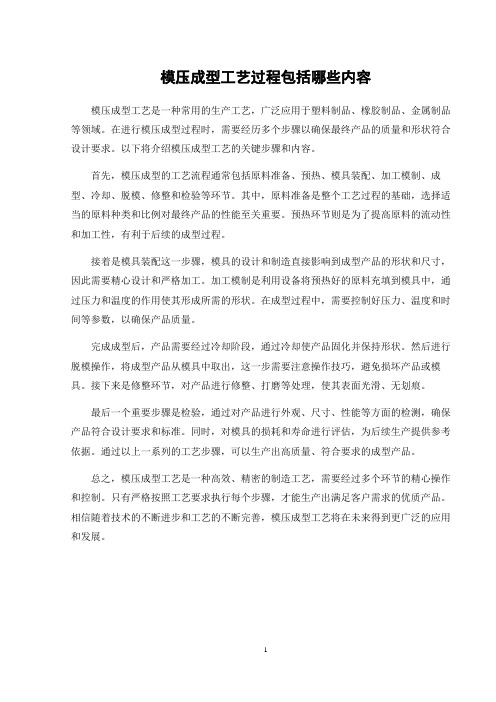
模压成型工艺过程包括哪些内容模压成型工艺是一种常用的生产工艺,广泛应用于塑料制品、橡胶制品、金属制品等领域。
在进行模压成型过程时,需要经历多个步骤以确保最终产品的质量和形状符合设计要求。
以下将介绍模压成型工艺的关键步骤和内容。
首先,模压成型的工艺流程通常包括原料准备、预热、模具装配、加工模制、成型、冷却、脱模、修整和检验等环节。
其中,原料准备是整个工艺过程的基础,选择适当的原料种类和比例对最终产品的性能至关重要。
预热环节则是为了提高原料的流动性和加工性,有利于后续的成型过程。
接着是模具装配这一步骤,模具的设计和制造直接影响到成型产品的形状和尺寸,因此需要精心设计和严格加工。
加工模制是利用设备将预热好的原料充填到模具中,通过压力和温度的作用使其形成所需的形状。
在成型过程中,需要控制好压力、温度和时间等参数,以确保产品质量。
完成成型后,产品需要经过冷却阶段,通过冷却使产品固化并保持形状。
然后进行脱模操作,将成型产品从模具中取出,这一步需要注意操作技巧,避免损坏产品或模具。
接下来是修整环节,对产品进行修整、打磨等处理,使其表面光滑、无划痕。
最后一个重要步骤是检验,通过对产品进行外观、尺寸、性能等方面的检测,确保产品符合设计要求和标准。
同时,对模具的损耗和寿命进行评估,为后续生产提供参考依据。
通过以上一系列的工艺步骤,可以生产出高质量、符合要求的成型产品。
总之,模压成型工艺是一种高效、精密的制造工艺,需要经过多个环节的精心操作和控制。
只有严格按照工艺要求执行每个步骤,才能生产出满足客户需求的优质产品。
相信随着技术的不断进步和工艺的不断完善,模压成型工艺将在未来得到更广泛的应用和发展。
1。
模压技术生产操作-成型工艺

模压技术生产操作-成型工艺简介本文档旨在介绍模压技术的生产操作中的成型工艺。
模压技术是一种常见的制造工艺,用于生产各种塑料制品。
成型工艺步骤下面是模压技术生产操作中的成型工艺步骤:1. 准备模具:选择合适的模具,确保其与要生产的产品设计相符。
2. 预热:将模具加热至适当温度,以保证塑料材料能够完全流动。
3. 准备材料:将所需塑料材料准备好,并按照要求对其进行预处理。
4. 放置材料:将预处理后的塑料材料放置在模具的预定位置。
5. 关闭模具:将模具紧密闭合,确保塑料材料受到充分压力。
6. 施加压力:通过推动模具上的压力机,施加适当压力,使塑料材料充分流动并填满模具腔体。
7. 冷却:保持模具处于所需的温度和压力条件下一段时间,使塑料材料冷却和固化。
8. 打开模具:当塑料材料完全冷却和固化后,打开模具,取出成型产品。
9. 检查和修整:对成型产品进行检查,确保其质量符合要求,如有需要,进行修整和加工。
10. 包装和存储:将成型产品进行包装,并妥善存储以待出售或使用。
注意事项在进行模压技术生产操作时,需要注意以下几点:- 操作人员应熟悉模压技术的原理和工艺要求。
- 确保模具与产品设计相符,避免产生不适配或无法实现的生产问题。
- 控制好模具的预热温度和保持时间,以保证塑料材料的流动性。
- 合理选择和处理塑料材料,确保其质量和适用性。
- 控制好施加压力的力度和时间,以保证产品的成型质量。
- 注意冷却时间和温度要求,以避免产生变形或缺陷。
- 在打开模具时要小心操作,防止损坏或意外受伤。
- 对成型产品进行严格检查,确保其符合质量要求。
以上是模压技术生产操作中的成型工艺的介绍,希望对您有所帮助。
模压成型工艺的工艺流程是什么呢

模压成型工艺的工艺流程是什么呢模压成型工艺是一种常见的制造工艺,广泛应用于塑料制品、橡胶制品、复合材料等领域。
其基本原理是通过热压或冷压的方式,使原料在模具中发生形状、尺寸和性能的变化,从而得到所需的成品。
模压成型工艺包括准备工作、预热、模具充填、加压成型、冷却、脱模等多个环节。
首先,在进行模压成型前,需要准备好充分的原料和模具。
原料通常为颗粒状或片状的材料,根据产品的要求选择合适的原料。
模具则根据产品的设计图纸制作,包括上模、下模以及必要的辅助构件。
接下来是预热步骤,即将模具加热至适当温度。
预热的目的是为了提高原料的流动性,有利于充填模具空腔并保证产品的成型质量。
预热温度和时间根据原料的种类和厚度进行调控。
模具充填是模压成型的核心步骤之一。
在预热后的模具中,将预先称量好的原料粒料投入到模具腔内。
通过振动或压实等方式,保证原料充分填充模具空腔,并使得原料可以均匀一致地分布。
加压成型是将已经充填好的模具放入压力机中进行压制的过程。
通过施加恰当的压力,原料在高温高压下发生变形和流动,以适应模具的形状。
加压的时间和力度需要根据原料的性质和产品要求进行调整。
成型完成后,需要进行冷却阶段。
冷却的目的是使得产品在模具中保持形状和尺寸稳定,同时加快产品的硬化和固化过程。
通常采用自然冷却或水冷却的方式,不同原料和产品可能需要不同的冷却时间。
最后是脱模操作,即将成品从模具中取出。
脱模时需要小心操作,避免损坏产品表面或模具结构。
有些复杂的产品可能需要采用辅助工具或特殊的脱模方法,确保产品的完整性和质量。
总的来说,模压成型工艺是一种高效、可控的制造工艺,能够生产出形状复杂、精度高的制品。
通过合理设计工艺流程和选择适当的原料,可以满足各种产品的需求,并在工业生产中发挥重要作用。
1。
模压成型工艺—模压成型操作(塑料成型加工课件)

热固性塑料在一定的合模压力和模具温度下保 持一段时间,达到一定的交联程度。
在加热加压的状态下,物料快速发生化学交联 反应,交联程度快速提高,树脂分子链由线性结构 变成三维网路结构,物料固化,物理机械性能提高。 有时候,为了提高生产效率,在制品能够不变形脱 模时就暂时结束热压固化过程,然后再通过后处理 完成固化的后期过程。
首先,要检查模具是否有油污、碎屑或异物, 并清理干净,如果需要可适当喷涂脱模剂。然后, 向模具型腔加入物料,尽可能放在模具型腔的中间, 流动阻力大的部位应多放一些料。加料量直接影响 制品的密度和尺寸,加料量过多制品易产生飞边, 厚度尺寸不精确;加料量过少则预压,使树脂充满整个型腔。 在预压过程中应让模具缓慢合紧,使树脂有足 够的时间在模腔内流动,并且避免树脂因合模过快 被空气带出,使制品造成破坏。
模压成型
模压工艺操作
一、模压工艺流程
热固性塑料模压成型的工艺过程包括加料、预压、 排气、固化和脱模等。
二、操作过程
1.开机预热
先接通电源,然后启动模压机开关。将模具放 到加热板上,点击“主缸上”合模;通过控制面板 设置加热板温度,打开加热热开关启动加热,当温 度达到设置值后再恒温一段时间。
2.加料
4.排气
通过适当的卸压松模排除气体,该过程可和预 压配合进行。
热固性塑料在模压时发生化学交联反应,常伴 有水蒸汽和小分子挥发物放出,因此需要短暂的时 间打开模具,使水蒸汽、小分子挥发物和空气排除, 避免对制品造成缺陷影响。排气完成后,应在物料 还处于良好流动状态时迅速闭模,对物料加热加压。
5.固化
6.脱模
固化后让制品和模具分离。脱模速度不能过 快,否则制品容易变形,而速度过慢则会影响生 产效率。当制品脱模后,要认真清理模具,用铜 制工具取出模具上的杂志和附着物,为下一个制 品的生产做准备。
模压成型工艺过程有哪些

模压成型工艺过程有哪些模压成型是一种常见的制造工艺,用于生产各种塑料制品、橡胶制品、金属制品等。
该工艺利用高温和高压将原材料加工成所需形状的制品,广泛应用于汽车零部件、家电配件、建筑材料等领域。
下面将详细介绍模压成型工艺的过程。
材料准备阶段在模压成型工艺中,首先需要准备原材料。
根据所需制品的材质,选择相应的塑料、橡胶或金属材料,并将其加工成固体颗粒、片材或坯料的形式。
在此阶段,还需要确定好原材料的配方和比例,以确保最终制品具有所需的性能和质量。
加热和熔化阶段接下来,将准备好的原材料加入到模具中,然后通过加热设备将模具内的原料加热至熔化温度。
在高温下,原材料逐渐软化、熔化,使其能够充分填充模具的空腔,并保持所需的形状和尺寸。
压力施加阶段一旦原料完全熔化并填充了模具腔体,接下来需要施加高压力以将原料挤压并充分填充模具的所有细节部位。
通过施加足够的压力,可以确保制品表面光滑、结构均匀,避免出现气泡、缺陷等质量问题。
冷却固化阶段当原料充分填充模具并完成成型后,需要立即开始冷却固化过程,以使制品保持所需的形状和尺寸。
通过控制冷却速度和温度,可以有效地控制制品的收缩率和内部组织,确保最终制品具有理想的物理性能和外观质量。
释放和脱模阶段一旦制品完全冷却并固化,模具就可打开,从而释放成型的制品。
在释放时,需要小心地处理以避免损坏制品表面。
有时需要额外的处理步骤,比如修整边缘、去除浮边等。
最终成品可经过一定的质量检查后,进入下一道工序或直接包装出厂。
通过以上几个阶段的工艺过程,模压成型工艺能够高效地生产各种复杂形状的制品,具有成本低、生产效率高、质量稳定等优点,被广泛应用于各种工业生产领域。
随着技术的不断进步和工艺的改进,模压成型在制造业中的地位将变得更加重要,为各行各业提供更多创新的解决方案。
模压成型工艺的工艺流程是什么样的呢

模压成型工艺的工艺流程是什么样的呢模压成型工艺是一种常见的制造工艺,广泛应用于塑料制品、橡胶制品等领域,其工艺流程主要包括准备工作、原料配制、加热塑化、充填模具、模具关闭、施压成型、冷却固化等步骤。
首先是准备工作。
在进行模压成型之前,需要准备好相关的设备和模具。
确保模具表面清洁平整,无划痕和杂质。
检查模具的开合动作是否灵活顺畅,确保模具能够正常关闭。
接着是原料配制。
根据产品的设计要求,准备相应的原料,如塑料颗粒、橡胶胶料等。
根据配方要求,将原料进行称量、混合等处理,确保原料的均匀性和质量稳定性。
加热塑化是下一个步骤。
将原料放入模压机的加热装置中,通过加热和压力作用使原料塑化,达到适合于充填模具的熔融状态。
控制加热温度和时间是非常关键的,过高或过低的温度都会影响最终产品的质量。
充填模具是模压成型的重要一步。
将已塑化的原料充分注入模具腔内,确保空隙被填满,同时避免产生气泡和短充等缺陷。
这个过程通常需要根据产品结构和材料特性进行调整,以确保成型品的尺寸和形状符合要求。
模具关闭后,施加压力进行成型。
闭合好模具后,通过模压机的压力系统施加一定压力,使原料充填模具腔,并在一定温度下进行固化。
控制压力和温度的均匀性是确保产品质量稳定的关键。
最后是冷却固化。
经过一定时间的加压成型后,产品需要在模具中进行冷却固化,使其达到足够的强度和硬度。
冷却时间一般取决于产品的材料和厚度,通常需要保持足够的时间确保产品质量。
总的来说,模压成型工艺是一种高效、精密的制造工艺,通过适当的工艺参数和操作流程,可以生产出质量稳定的塑料制品和橡胶制品。
遵循正确的工艺流程,严格控制每个环节的质量要求,是保证模压成型产品质量的关键。
1。
模压成型工艺的工艺流程

模压成型工艺的工艺流程模压成型工艺,是一种常见的制造工艺,适用于塑料制品、橡胶制品等的生产过程中。
本文将介绍模压成型工艺的工艺流程,希望能为读者提供一定的了解和参考。
一、材料准备阶段模压成型工艺的第一步是进行材料的准备。
在制造过程中,通常会选用颗粒状的原料,比如塑料颗粒或橡胶颗粒。
这些原料需要按照一定的配比进行混合,以确保最终产品的质量和性能。
二、预热和塑化阶段一般情况下,模压成型工艺需要将混合好的原料进行预热和塑化处理。
预热的目的是让原料达到适合成型的温度,以便在模具中得到良好的流动性和可塑性。
塑化则是将原料完全熔化,以确保产品成型后的均匀性和一致性。
三、充模和封模阶段在原料预热和塑化完毕后,下一步是将塑化好的原料充入模具中。
充模过程需要控制好原料的充填量,以避免过多或过少造成的成型缺陷。
接着,需要封闭模具并施加压力,使得原料充分填充模具的空腔,并在压力下形成所需的形状。
四、保压和冷却阶段成型过程中的保压阶段是为了确保产品内部的结构和密度达到要求。
保压时间的长短会影响最终产品的质量,需要根据具体原料和产品来进行调整。
随后是冷却阶段,通过降低模具温度以固化原料,使产品保持所需的形状和尺寸。
五、脱模和修饰阶段当产品冷却固化后,需要将成品从模具中取出,这个过程称为脱模。
脱模时需要注意避免产品变形或损坏,可以借助特殊脱模机构或处理方式。
在脱模之后,还可能需要进行一些修饰工艺,比如去除余料、切割边角或表面处理等,以提升产品的外观和性能。
结语模压成型工艺是一项常用的制造工艺,在各种行业中都有着广泛的应用。
通过以上介绍的工艺流程,希望读者能对模压成型工艺有更深入的了解,并在实际生产中能够更好地运用和掌握这一技术。
模压成型工艺凭借其高效、精准和成本低廉等优点,将继续在工业生产中扮演重要的角色。
模压工艺介绍
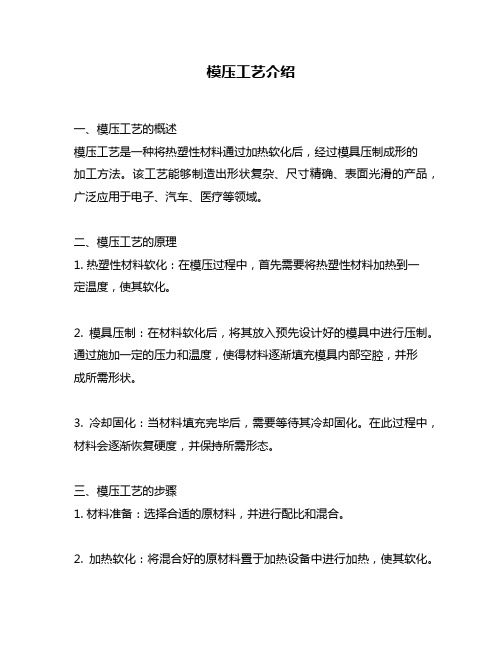
模压工艺介绍一、模压工艺的概述模压工艺是一种将热塑性材料通过加热软化后,经过模具压制成形的加工方法。
该工艺能够制造出形状复杂、尺寸精确、表面光滑的产品,广泛应用于电子、汽车、医疗等领域。
二、模压工艺的原理1. 热塑性材料软化:在模压过程中,首先需要将热塑性材料加热到一定温度,使其软化。
2. 模具压制:在材料软化后,将其放入预先设计好的模具中进行压制。
通过施加一定的压力和温度,使得材料逐渐填充模具内部空腔,并形成所需形状。
3. 冷却固化:当材料填充完毕后,需要等待其冷却固化。
在此过程中,材料会逐渐恢复硬度,并保持所需形态。
三、模压工艺的步骤1. 材料准备:选择合适的原材料,并进行配比和混合。
2. 加热软化:将混合好的原材料置于加热设备中进行加热,使其软化。
3. 模具设计:根据所需产品的形状和尺寸,设计相应的模具。
4. 模具制造:根据设计好的模具图纸,制造出需要的模具。
5. 模压成型:将软化后的材料放入模具中进行压制。
6. 冷却固化:等待材料冷却固化后,从模具中取出成品。
四、模压工艺的优点1. 生产效率高:相比于其他加工方法,模压工艺能够大幅提高生产效率,并且可以实现自动化生产。
2. 产品质量稳定:由于模压工艺能够精确控制温度和压力等参数,因此可以保证产品质量稳定性。
3. 成本低廉:相比于其他加工方法,模压工艺所需设备和材料成本较低,可以有效降低生产成本。
4. 环保节能:在生产过程中,模压工艺不会产生废气、废水等污染物质,并且能够节约能源消耗。
五、常见应用领域1. 电子行业:如手机壳、键盘、电视机壳等。
2. 汽车行业:如汽车灯罩、仪表盘、车身零件等。
3. 医疗行业:如医用注射器、输液器、雾化器等。
4. 家电行业:如洗衣机配件、冰箱配件、空调配件等。
六、模压工艺的发展趋势1. 精密化:随着科技的不断进步,模具制造技术和加工技术也在不断提高,能够制造出更加精密的产品。
2. 多样化:随着市场需求的变化,模压工艺也在不断向多样化方向发展,能够制造出更多种类的产品。
模压成型工艺—模压成型工艺(塑料成型加工课件)

四、模压时间
模压时间是指从闭模加压起,物料在模具中升温 到固化脱模的整个阶段时间,它直接影响制品的固化 程度和生产周期。模压时间与物料的种类、制品的形 状、模压压力和温度等有关,需要合理控制模压时间。
模压时间的长短对制品的性能影响很大。模压时 间短,物料固化不完全,制品物理性能较差,脱模后 易变形。时间过长则会使物料交联程度过高,使制品 产生内应力而影响物理机械性能,严重时会使制品开 裂。
因此,对模具温度的选择要综合考虑塑化流动 效果、交联固化速率和物料的热稳定性等因素。要 保证物料能充满整个模腔的同时,缩短固化时间, 还要防止物料因过热而变质。
三、热固性塑料的模压
加热软化
流动充模
交联固化
定型脱模
(1)橡胶原材料加热软化; (2)在良好的流动状态下充满整个模腔; (3)在加热条件下,发生交联反应,橡胶固化; (4)直接打开模具,将已经固化的橡胶制品取出。
模压成型
模压工艺参数
一、模压用量
指模压时的物料用量,根据制品体积或质量进行 选择。
溢式
ห้องสมุดไป่ตู้
不溢式
半溢式
二、模压压力
模压压力是指合模时,模具对塑料所施加的压力。 模压压力具有以下作用: 1.使塑料在模具中加速流动,充满模腔;增加塑料的密 实度; 2.克服物料在固化反应中的内部压力,防止制品出现肿 胀、起泡、脱层等缺陷; 3.保持固定的形状和尺寸; 4.防止制品在冷却时发生变形。
三、模压温度
热固性塑料在模压时,模具温度是影响物料塑 化流动和固化成型的主要因素,它决定模压过程中 交联反应的速度,并影响物料的充模过程和制品的 最终性能。
物料受温度的作用,其黏度和流动性会发生很 大的变化。在较低温度内,物料的流动性随温度的 上升而增加,黏度降低;在较高的温度范围内,化 学交联反应起主导作用,随温度升高交联反应迅速 加快,流动性迅速降低,制品固化。
模压成型操作指导书电子版

模压成型操作指导书电子版在现代工业生产中,模压成型是一项常见且重要的制造工艺,广泛应用于塑料、橡胶等材料的加工中。
模压成型操作指导书电子版旨在系统地介绍模压成型的操作流程、注意事项和技术要点,帮助操作人员更好地掌握这一工艺,提高生产效率和产品质量。
一、模压成型工艺概述模压成型是一种利用模具将加热软化的原料加压成型的工艺。
在模压成型过程中,需要准备好适用的原料、模具和模压设备。
操作人员应当具备丰富的操作经验和技术知识,严格按照操作规程进行操作,确保生产过程顺利进行。
二、模压成型操作流程1.准备工作:清洁模具和模压设备,检查原料质量和数量是否符合要求。
2.加热:将原料加热到适当的温度,软化原料,以便于成型。
3.装模:将软化的原料放入模具内,注意排除气泡和杂质。
4.封模:关闭模具,施加一定的压力,使原料充分填充模具腔。
5.成型:保持一定的温度和压力,等待一定时间让原料充分流动和固化。
6.冷却:待产品固化后,开模取出,放置在冷却设备中进行冷却。
7.完工:对产品进行检查,如有问题及时处理,合格产品进行包装存放。
三、模压成型操作注意事项1.操作人员应穿戴好工作服和安全防护用具,确保作业安全。
2.定期检查模具和模压设备,保持清洁,防止杂质和损坏影响生产。
3.严格按照操作流程和规程操作,避免出现操作失误和质量问题。
4.根据不同原料的特性和要求,设定合适的加热温度和压力值。
5.避免模具过热或过冷,以免影响产品质量和模具寿命。
6.对生产过程中的异常情况及时处理,确保生产不受影响。
四、模压成型技术要点1.控制原料的加热温度和加热时间,保证原料充分软化和流动性。
2.设定合适的压力值和保压时间,确保产品成型质量稳定。
3.选择适当的成型周期和冷却时间,以确保产品充分固化。
4.对产品的尺寸、外观和质量进行严格检查,确保产品符合要求。
5.不同产品可能需要不同的操作参数和工艺流程,操作人员应灵活掌握,确保生产效率和产品质量。
通过模压成型操作指导书电子版的学习和实践,操作人员可以更好地掌握模压成型工艺,提高生产效率和产品质量,为企业的发展和产品的进步做出贡献。
模压工艺生产操作-成型工艺知识说解
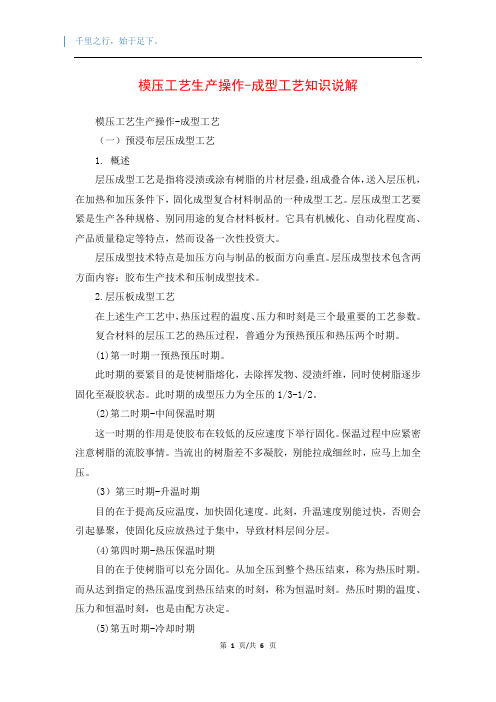
模压工艺生产操作-成型工艺知识说解模压工艺生产操作-成型工艺(一)预浸布层压成型工艺1. 概述层压成型工艺是指将浸渍或涂有树脂的片材层叠,组成叠合体,送入层压机,在加热和加压条件下,固化成型复合材料制品的一种成型工艺。
层压成型工艺要紧是生产各种规格、别同用途的复合材料板材。
它具有机械化、自动化程度高、产品质量稳定等特点,然而设备一次性投资大。
层压成型技术特点是加压方向与制品的板面方向垂直。
层压成型技术包含两方面内容:胶布生产技术和压制成型技术。
2.层压板成型工艺在上述生产工艺中,热压过程的温度、压力和时刻是三个最重要的工艺参数。
复合材料的层压工艺的热压过程,普通分为预热预压和热压两个时期。
(1)第一时期一预热预压时期。
此时期的要紧目的是使树脂熔化,去除挥发物、浸渍纤维,同时使树脂逐步固化至凝胶状态。
此时期的成型压力为全压的1/3-1/2。
(2)第二时期-中间保温时期这一时期的作用是使胶布在较低的反应速度下举行固化。
保温过程中应紧密注意树脂的流胶事情。
当流出的树脂差不多凝胶,别能拉成细丝时,应马上加全压。
(3)第三时期-升温时期目的在于提高反应温度,加快固化速度。
此刻,升温速度别能过快,否则会引起暴聚,使固化反应放热过于集中,导致材料层间分层。
(4)第四时期-热压保温时期目的在于使树脂可以充分固化。
从加全压到整个热压结束,称为热压时期。
而从达到指定的热压温度到热压结束的时刻,称为恒温时刻。
热压时期的温度、压力和恒温时刻,也是由配方决定。
(5)第五时期-冷却时期在保压的事情下,采取自然冷却或者强制冷却到室温,然后卸压,取出产品。
冷却时刻过短,容易使产品产生翘曲、开裂等现象。
冷却时刻过长,对制品质量无明显帮助,然而使生产效率明显落低。
(二)预浸料模压成型工艺预浸料模压成型工艺基本过程是:将一定量经一定预处理的模压料放入预热的模具内,施加较高的压力使模压料填充模腔。
在一定的压力和温度下使模压料逐渐固化,然后将制品从模具内取出,再举行必要的辅助加工即得产品。
模压生产工艺
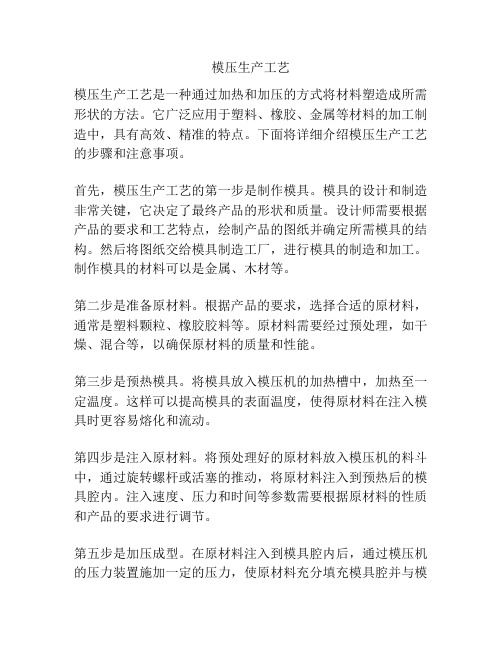
模压生产工艺模压生产工艺是一种通过加热和加压的方式将材料塑造成所需形状的方法。
它广泛应用于塑料、橡胶、金属等材料的加工制造中,具有高效、精准的特点。
下面将详细介绍模压生产工艺的步骤和注意事项。
首先,模压生产工艺的第一步是制作模具。
模具的设计和制造非常关键,它决定了最终产品的形状和质量。
设计师需要根据产品的要求和工艺特点,绘制产品的图纸并确定所需模具的结构。
然后将图纸交给模具制造工厂,进行模具的制造和加工。
制作模具的材料可以是金属、木材等。
第二步是准备原材料。
根据产品的要求,选择合适的原材料,通常是塑料颗粒、橡胶胶料等。
原材料需要经过预处理,如干燥、混合等,以确保原材料的质量和性能。
第三步是预热模具。
将模具放入模压机的加热槽中,加热至一定温度。
这样可以提高模具的表面温度,使得原材料在注入模具时更容易熔化和流动。
第四步是注入原材料。
将预处理好的原材料放入模压机的料斗中,通过旋转螺杆或活塞的推动,将原材料注入到预热后的模具腔内。
注入速度、压力和时间等参数需要根据原材料的性质和产品的要求进行调节。
第五步是加压成型。
在原材料注入到模具腔内后,通过模压机的压力装置施加一定的压力,使原材料充分填充模具腔并与模具表面接触。
同时,通过加热控制器控制模具的温度,以保持原材料的熔化状态。
加压时间和压力需要根据原材料的性质和产品的要求进行调节,以确保成型品的质量和形状。
最后一步是冷却和脱模。
经过一定的时间加压成型后,停止加压和加热,使模具和成型品自然冷却。
待成型品冷却至一定温度后,打开模具,将成型品取出。
取出后,进行质量检查和修整,如去除余料和毛刺等。
然后将成品进行包装和整理,以便后续的运输和销售。
需要注意的是,模压生产工艺需要严格控制加热温度、压力和时间等参数,以确保成型品的质量和一致性。
同时,需要根据原材料的特性和产品的要求,选择合适的设备和工艺流程。
此外,对于大型和复杂的产品,还需要考虑模具的分型、冷却和排气等问题,以克服模具的限制,保证成型品的完整性和一致性。
模压成型工艺的工艺流程是什么
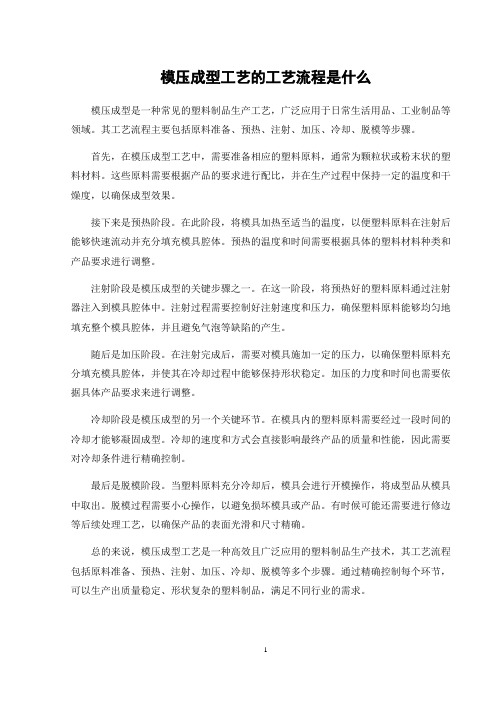
模压成型工艺的工艺流程是什么模压成型是一种常见的塑料制品生产工艺,广泛应用于日常生活用品、工业制品等领域。
其工艺流程主要包括原料准备、预热、注射、加压、冷却、脱模等步骤。
首先,在模压成型工艺中,需要准备相应的塑料原料,通常为颗粒状或粉末状的塑料材料。
这些原料需要根据产品的要求进行配比,并在生产过程中保持一定的温度和干燥度,以确保成型效果。
接下来是预热阶段。
在此阶段,将模具加热至适当的温度,以便塑料原料在注射后能够快速流动并充分填充模具腔体。
预热的温度和时间需要根据具体的塑料材料种类和产品要求进行调整。
注射阶段是模压成型的关键步骤之一。
在这一阶段,将预热好的塑料原料通过注射器注入到模具腔体中。
注射过程需要控制好注射速度和压力,确保塑料原料能够均匀地填充整个模具腔体,并且避免气泡等缺陷的产生。
随后是加压阶段。
在注射完成后,需要对模具施加一定的压力,以确保塑料原料充分填充模具腔体,并使其在冷却过程中能够保持形状稳定。
加压的力度和时间也需要依据具体产品要求来进行调整。
冷却阶段是模压成型的另一个关键环节。
在模具内的塑料原料需要经过一段时间的冷却才能够凝固成型。
冷却的速度和方式会直接影响最终产品的质量和性能,因此需要对冷却条件进行精确控制。
最后是脱模阶段。
当塑料原料充分冷却后,模具会进行开模操作,将成型品从模具中取出。
脱模过程需要小心操作,以避免损坏模具或产品。
有时候可能还需要进行修边等后续处理工艺,以确保产品的表面光滑和尺寸精确。
总的来说,模压成型工艺是一种高效且广泛应用的塑料制品生产技术,其工艺流程包括原料准备、预热、注射、加压、冷却、脱模等多个步骤。
通过精确控制每个环节,可以生产出质量稳定、形状复杂的塑料制品,满足不同行业的需求。
1。
模压成型工艺流程
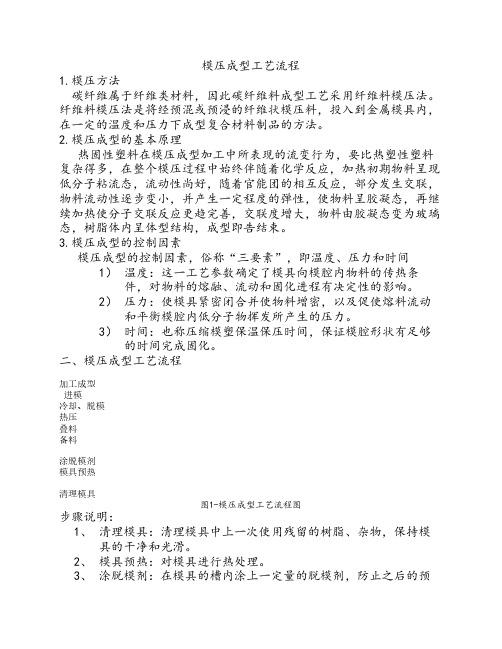
热后成型产品和模具粘在一起。 4、 备料:将即将做成产品的碳纤维的原料准备好,计算好原料的
用料面积,用料的张数。 5、 叠料:把原料一层层的叠加起来,同时对叠加的材料进行预
压,压成形状规整,质量一定的密实体。 6、 进模:把叠好的原料放置到模具中,同时在在内部放入塑料气
囊,合模,将整体放入合模机中,对内部塑料气囊加一定的恒 定压力,恒定的温度,设置恒定的时间,使其固化。 7、 冷却、脱模:对经过热压处理一段时间的模具先冷却一段时间, 然后揭开模具,进行脱模处理。 8、 加工成型:脱模后的产品需要对其进行清理,用钢刷或铜刷刮 去残留的塑料,并用压缩空气吹净,对成型的产品进行打磨, 使表面光滑整洁。
模压成型工艺流程 1.模压方法
碳纤维属于纤维类材料,因此碳纤维料成型工艺采用纤维料模压法。 纤维料模压法是将经预混或预浸的纤维状模压料,投入到金属模具内, 在一定的温度和压力下成型复合材料制品的方法。 2.模压成型的基本原理
热固性塑料在模压成型加工中所表现的流变行为,要比热塑性塑料 复杂得多,在整个模压过程中始终伴随着化学反应,加热初期物料呈现 低分子粘流态,流动性尚好,随着官能团的相互反应,部分发生交联, 物料流动性逐步变小,并产生一定程度的弹性,使物料呈胶凝态,再继 续加热使分子交联反应更趋完善,交联度增大,物料由胶凝态变为玻璃 态,树脂体内呈体型结构,成型即告结束。 3.模压成型的控制因素
二、模压成型工艺流程
加工成型 进模
冷却、脱模 热压 叠料 备料
涂脱模剂 模具预热
清理模具 图1-模压成型工艺流程图
步骤说明: 1、 清理模具:清理模具中上一次使用残留的树脂、杂物,保持模 具的干净和光滑。 2、 模具预热:对模具进行热处理。 3、 涂脱模剂:在模具的槽内涂上一定量的脱模剂,防止之后的预
模压成型的工艺过程是什么
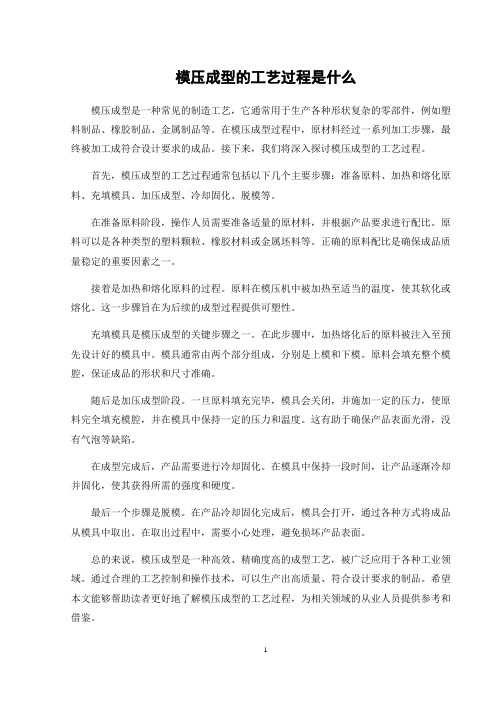
模压成型的工艺过程是什么模压成型是一种常见的制造工艺,它通常用于生产各种形状复杂的零部件,例如塑料制品、橡胶制品、金属制品等。
在模压成型过程中,原材料经过一系列加工步骤,最终被加工成符合设计要求的成品。
接下来,我们将深入探讨模压成型的工艺过程。
首先,模压成型的工艺过程通常包括以下几个主要步骤:准备原料、加热和熔化原料、充填模具、加压成型、冷却固化、脱模等。
在准备原料阶段,操作人员需要准备适量的原材料,并根据产品要求进行配比。
原料可以是各种类型的塑料颗粒、橡胶材料或金属坯料等。
正确的原料配比是确保成品质量稳定的重要因素之一。
接着是加热和熔化原料的过程。
原料在模压机中被加热至适当的温度,使其软化或熔化。
这一步骤旨在为后续的成型过程提供可塑性。
充填模具是模压成型的关键步骤之一。
在此步骤中,加热熔化后的原料被注入至预先设计好的模具中。
模具通常由两个部分组成,分别是上模和下模。
原料会填充整个模腔,保证成品的形状和尺寸准确。
随后是加压成型阶段。
一旦原料填充完毕,模具会关闭,并施加一定的压力,使原料完全填充模腔,并在模具中保持一定的压力和温度。
这有助于确保产品表面光滑,没有气泡等缺陷。
在成型完成后,产品需要进行冷却固化。
在模具中保持一段时间,让产品逐渐冷却并固化,使其获得所需的强度和硬度。
最后一个步骤是脱模。
在产品冷却固化完成后,模具会打开,通过各种方式将成品从模具中取出。
在取出过程中,需要小心处理,避免损坏产品表面。
总的来说,模压成型是一种高效、精确度高的成型工艺,被广泛应用于各种工业领域。
通过合理的工艺控制和操作技术,可以生产出高质量、符合设计要求的制品。
希望本文能够帮助读者更好地了解模压成型的工艺过程,为相关领域的从业人员提供参考和借鉴。
1。
模压成型的工艺过程有哪些内容
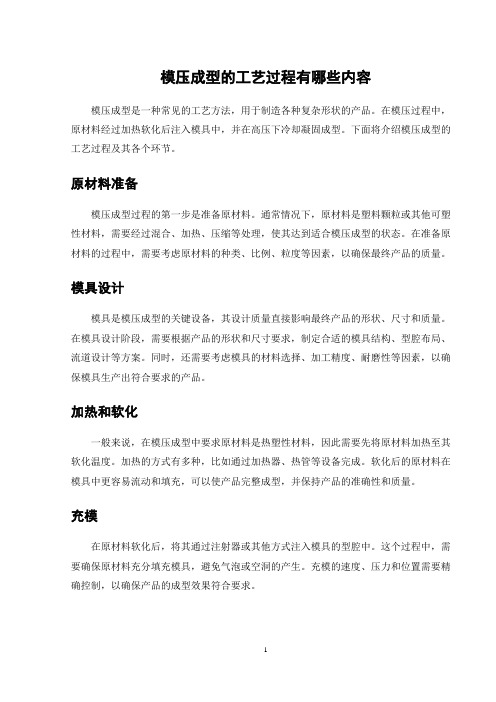
模压成型的工艺过程有哪些内容模压成型是一种常见的工艺方法,用于制造各种复杂形状的产品。
在模压过程中,原材料经过加热软化后注入模具中,并在高压下冷却凝固成型。
下面将介绍模压成型的工艺过程及其各个环节。
原材料准备模压成型过程的第一步是准备原材料。
通常情况下,原材料是塑料颗粒或其他可塑性材料,需要经过混合、加热、压缩等处理,使其达到适合模压成型的状态。
在准备原材料的过程中,需要考虑原材料的种类、比例、粒度等因素,以确保最终产品的质量。
模具设计模具是模压成型的关键设备,其设计质量直接影响最终产品的形状、尺寸和质量。
在模具设计阶段,需要根据产品的形状和尺寸要求,制定合适的模具结构、型腔布局、流道设计等方案。
同时,还需要考虑模具的材料选择、加工精度、耐磨性等因素,以确保模具生产出符合要求的产品。
加热和软化一般来说,在模压成型中要求原材料是热塑性材料,因此需要先将原材料加热至其软化温度。
加热的方式有多种,比如通过加热器、热管等设备完成。
软化后的原材料在模具中更容易流动和填充,可以使产品完整成型,并保持产品的准确性和质量。
充模在原材料软化后,将其通过注射器或其他方式注入模具的型腔中。
这个过程中,需要确保原材料充分填充模具,避免气泡或空洞的产生。
充模的速度、压力和位置需要精确控制,以确保产品的成型效果符合要求。
施加压力一旦原材料充分注入模具,就需要施加高压力使其充分填充模具型腔,并保持一定时间以确保原材料的冷却凝固。
施加的压力大小需要根据产品的形状、尺寸和要求来确定,过高或过低都可能导致产品出现瑕疵。
冷却固化在原材料充分填充模具并施加压力后,需要等待一定时间让原材料冷却固化。
冷却的速度和时间取决于原材料的种类和厚度,一般情况下需要精确控制以确保产品质量。
在冷却固化的过程中,模具温度、环境温度和湿度等因素都会对产品的质量产生影响。
脱模当原材料冷却固化后,就可以进行脱模操作。
脱模时需要小心翼翼地分离模具和产品,避免产品损坏或形状不规则。
论述模压成型的工艺流程有哪些

论述模压成型的工艺流程有哪些模压成型作为一种常见的制造工艺,被广泛应用于各种行业,如汽车制造、电子产品生产等。
其工艺流程相对复杂,涉及多个环节的操作和控制。
以下将详细介绍模压成型的工艺流程。
首先,模具设计是模压成型的第一步,决定了最终产品的形状和尺寸。
模具设计师需要根据产品的要求和材料特性,设计出合适的模具结构。
这一步需要考虑到产品的几何形状、壁厚、收缩率等因素,并进行相关的计算和模拟。
其次,原料准备是模压成型的重要环节。
在进行模压成型之前,需要准备好所需的原料,通常是塑料颗粒或其他成型材料。
这些原料需要按照一定的配比准备好,并在一定的温度下进行熔融,以便后续的成型操作。
接着,注塑是模压成型中的关键步骤之一。
在注塑过程中,将熔融的原料注入到模具中,通过高压力将原料充分填充模具腔体,使其在模具中形成所需的产品形状。
注塑操作需要控制注射速度、压力和温度等参数,以确保产品质量。
然后,冷却是模压成型中一个至关重要的阶段。
在注塑完成后,模具中的产品需要进行充分冷却,以确保产品在脱模后能够保持其形状和尺寸稳定。
冷却的过程需要控制冷却时间和方式,通常会采用冷却水或其他冷却介质来进行。
最后,脱模是模压成型的最后一步,也是产品从模具中取出的关键环节。
通过脱模机构将产品从模具中取出,并进行后续的处理,如修边、清洁等。
脱模需要考虑产品与模具的配合间隙,以防产品变形或损坏。
总的来说,模压成型的工艺流程经过模具设计、原料准备、注塑、冷却和脱模等多个环节的操作和控制。
每个环节都至关重要,需要严格控制各项参数,以确保最终产品的质量和性能。
随着制造技术的进步,模压成型工艺也在不断演进,为各行各业的生产提供更加高效、精密的制造解决方案。
1。
- 1、下载文档前请自行甄别文档内容的完整性,平台不提供额外的编辑、内容补充、找答案等附加服务。
- 2、"仅部分预览"的文档,不可在线预览部分如存在完整性等问题,可反馈申请退款(可完整预览的文档不适用该条件!)。
- 3、如文档侵犯您的权益,请联系客服反馈,我们会尽快为您处理(人工客服工作时间:9:00-18:30)。
模压工艺生产操作-成型工艺(一)预浸布层压成型工艺1. 概述层压成型工艺是指将浸渍或涂有树脂的片材层叠,组成叠合体,送入层压机,在加热和加压条件下,固化成型复合材料制品的一种成型工艺。
层压成型工艺主要是生产各种规格、不同用途的复合材料板材。
它具有机械化、自动化程度高、产品质量稳定等特点,但是设备一次性投资大。
层压成型技术特点是加压方向与制品的板面方向垂直。
层压成型技术包含两方面内容:胶布生产技术和压制成型技术。
2.层压板成型工艺在上述生产工艺中,热压过程的温度、压力和时间是三个最重要的工艺参数。
复合材料的层压工艺的热压过程,一般分为预热预压和热压两个阶段。
(1)第一阶段一预热预压阶段。
此阶段的主要目的是使树脂熔化,去除挥发物、浸渍纤维,并且使树脂逐步固化至凝胶状态。
此阶段的成型压力为全压的1/3-1/2。
(2)第二阶段-中间保温阶段这一阶段的作用是使胶布在较低的反应速度下进行固化。
保温过程中应密切注意树脂的流胶情况。
当流出的树脂已经凝胶,不能拉成细丝时,应立即加全压。
(3)第三阶段-升温阶段目的在于提高反应温度,加快固化速度。
此时,升温速度不能过快,否则会引起暴聚,使固化反应放热过于集中,导致材料层间分层。
(4)第四阶段-热压保温阶段目的在于使树脂能够充分固化。
从加全压到整个热压结束,称为热压阶段。
而从达到指定的热压温度到热压结束的时间,称为恒温时间。
热压阶段的温度、压力和恒温时间,也是由配方决定。
(5)第五阶段-冷却阶段在保压的情况下,采取自然冷却或者强制冷却到室温,然后卸压,取出产品。
冷却时间过短,容易使产品产生翘曲、开裂等现象。
冷却时间过长,对制品质量无明显帮助,但是使生产效率明显降低。
(二)预浸料模压成型工艺预浸料模压成型工艺基本过程是:将一定量经一定预处理的模压料放入预热的模具内,施加较高的压力使模压料填充模腔。
在一定的压力和温度下使模压料逐渐固化,然后将制品从模具内取出,再进行必要的辅助加工即得产品。
1.压制前的准备(1)装料量的计算在模压成型工艺中,对于不同尺寸的模压制品要进行装料量的估算,以保证制品几何尺寸的精确,防止物料不足造成废品,或者物料损失过多而浪费材料。
常用的估算方法有①形状、尺寸简单估算法,将复杂形状的制品简化成一系列简单的标准形状,进行装料量的估算:②密度比较法,对比模压制品及相应制品的密度,已知相应制品的重量,即可估算出模压制品的装料量:③注型比较法,在模压制品模具中,用树脂、石蜡等注型材料注成产品,再按注型材料的密度、重量及制品的密度求出制品的装料量。
(2)脱模剂的涂刷在模压成型工艺中,除使用内脱模剂外,还在模具型腔表面上涂刷外脱模剂,常用的有油酸、石蜡、硬脂酸、硬脂酸锌、有机硅油、硅脂和硅橡胶等。
所涂刷的脱模剂在满足脱模要求的前提下,用量尽量少些,涂刷要均匀。
一般情况下,酚醛型模压料多用有机油、油酸、硬脂酸等脱模剂,环氧或环氧酚醛型模压料多用硅脂和有机硅油脱模剂,聚酯型模压料多用硬脂酸锌、硅脂等脱模剂。
(3)预压将松散的粉状或纤维状的模压料预先用冷压法压成重量一定、形状规整的密实体。
采用预压作业可提高生产效率、改善劳动条件,有利于产品质量的提高。
(4)预热在压制前将模压料加热,去除水分和其它挥发份,可以提高固化速率,缩短压制周期;增进制品固化的均匀性,提高制品的物理机械性能,提高模压料的流动性。
(5)表压值的计算在模压工艺中,首先要根据制品所要求的成型压力,计算出压机的表压值。
成型压力是指制品水平投影面上单位面积所承受的压力。
它和表压值之间存在的函数关系。
在模压成型工艺中,成型压力的大小决定于模压料的品种和制品结构的复杂程度,成型压力是选择压机吨位的依据。
2压制工艺(1)装料和装模往模具中加入制品所需用的模压料过程称为装料,装料量按估算结果,经试压后确定。
装模应遵循下列原则:物料流动路程最短:物料铺设应均匀;对于狭小流道和死角,应预先进行料的铺设。
(2)模压温度制度模压温度制度主要包括装模温度、升温速率、成型温度和保温时间的选择。
①装模温度装模温度是指将物料放入模腔时模具的温度,它主要取决于物料的品种和模压料的质量指标。
一般地,模压料挥发份含量高,不溶性树脂含量低时,装模温度较低。
反之,要适当提高装模温度。
制品结构复杂及大型制品装模温度一般宜在室温-90℃范围内。
②升温速率指由装模温度到最高压制温度地升温速率。
对快速模压工艺,装模温度即为压制温度,不存在升温速率问题。
而慢速模压工艺,应依据模压料树脂的类型、制品的厚度选择适当的升温速率。
③成型温度树脂在固化过程中会放出或吸收一定的热量,根据放热量可判断树脂缩聚反应的程度,从而为确定成型温度提供依据。
一般情况下,先确定一个比较大的温度范围,再通过工艺-性能试验选择合理的成型温度。
成型温度与模压料的品种有很大关系。
成型温度过高,树脂反应速度过快,物料流动性降低过快,常出现早期局部固化,无法充满模腔。
温度过低,制品保温时间不足,则会出现固化不完全等缺陷。
④保温时间指在成型压力和成型温度下保温的时间,其作用是使制品固化完全和消除内应力.保温时间的长短取决于模压料的品种、成型温度的高低和制品的结构尺寸和性能。
⑤降温在慢速成型中,保温结束后要在一定压力下逐渐降温,模具温度降至60℃以下时,方可进行脱模操作。
降温方式有自然冷却和强制降温两种。
快速压制工艺可不采用降温操作,待保温结束后即可在成型温度下脱模,取出制品。
3)压力设置压力设置包括成型压力、合模速度、加压时机、放气等。
①成型压力成型压力是指制品水平投影面积上所承受的压力。
它的作用是克服物料中挥发物产生的蒸汽压,避免制品产生气泡、分层、结构松散等缺陷,同时也可增加物料的流动性,便于物料充满模具型腔的各个角落,使制品结构密实,机械强度提高。
成型压力的选择取决于两个方面的因素:a模压料的种类及质量指标。
如酚醛模压料的成型压力一般为30-50MPa,环氧酚醛模压料的成型压力为5-30MPa,聚酯型模压料的成型压力为7-10MPa。
b制品结构形状尺寸。
对于结构复杂,壁厚较厚的制品,其成型压力要适当增加。
外观性能及平滑度要求高的制品一般也选择较高的成型压力。
②合模速度装模后,上下模闭合的过程称为合模。
上模下行要快,但在与模压料将接触时,其速度要放慢。
下行快,有利于操作和提高效率;合模要慢,有利于模内气体的充分排除,减少气泡、砂眼等缺陷的产生。
③加压时机合模后,进行加压操作。
加压时机的选择对制品的质量有很大的影响。
加压过早,树脂反应程度低,分子质量小,粘度低,树脂在压力下易流失,在制品中产生树脂集聚或局部纤维裸露。
加压过迟,树脂反应程度高,粘度大,物料流动性差,难以充满模腔,形成废品。
通常,快速成型不存在加压时机的选择。
④卸压排气将物料中残余的挥发物、固化反应放出的低分子化合物及带入物料的空气排除过程称为排气。
其目的是为了保证制品的密实性,避免制品产生气泡、分层现象。
(4)制品后处理制品后处理是指将已脱模的制品在较高温度下进一步加热固化一段时间,其目的是保证树脂的完全固化,提高制品尺寸稳定性和电性能,消除制品中的内应力,减少制品变形。
有时也可根据实际情况,采用冷模方法,矫正产品变形,防止翘曲和收缩。
在模压制品定型出模后,为满足制品设计要求还应建立毛边打磨和辅助加工工序。
毛边打磨是去除制品成型时在边缘部位的毛刺飞边,打磨时一定要注意方法和方向,否则,很有可能把与毛边相连的局部打磨掉。
对于一些结构复杂的产品,往往还需进行机械加工来满足设计要求。
模压制品对机械加工是很敏感的。
如加工不当,很容易产生破裂、分层。
3.典型配方模压成型工艺选定何种工艺主要取决于模压料类型,此外还应考虑生产效率及制品结构、尺寸性能要求等。
4.典型预浸料和性能国内预浸料绝大部分用于制造体育休闲用品,基本是各公司自产自用,或从国外进口。
国内已具备采用多种预浸工艺生产预浸料的能力,包括溶液法、直接热熔法、热熔胶膜法等。
能制造单向预浸料,也能制造各种织物预浸料,研究开发树脂体系约30个,包括环氧、酚醛、双马、聚酞亚胺、氰酸酯等。
拥有不同基体、不同增强材料制成的预浸料约50个品种,可以满足不同使用温度、不同功能、不同结构、不同成形方法对预浸料的要求。
(三)SMC模压成型工艺SMC模压成型工艺过程,主要有以下几个工序1.压制前准备(1)SMC的质量检查 SMC片材的质量对成型工艺过程及制品质量有很大的影响。
因此,压制前必须了解料的质量,如树脂糊配方、树脂糊的增稠曲线、玻纤含量、玻纤浸润剂类型。
单重、薄膜剥离性,硬度及质量均匀性等。
(2)剪裁按制品的结构形状,加料位置,流程决定片材剪裁的形状与尺寸,制作样板,再按样板裁料。
剪裁的形状多为方形或圆形,尺寸多按制品表面投影面积的40%一80%。
为防止外界杂质的污染,上下薄膜在装料前才揭去。
(3)设备的准备①熟悉压机的各项操作参数,尤其要调整好工作压力和压机运行速度及台面平行度等。
②模具安装一定要水平,并确保安装位置在压机台面的中心,压制前要先彻底清理模具,并涂脱模剂。
加料前要用干净纱布将脱模剂擦均,以免影响制品外观。
对于新模具,用前须去油。
2.加料(1)加料量的确定每个制品的加料量在首次压制时可按下式计算加料量/g=制品体积/cm3X1.8 /g(2)加料面积的确定加料面积的大小,直接影响到制品的密实程度,料的流动距离和制品表面质量。
它与SMC的流动与固化特性、制品性能要求、模具结构等有关。
一般加料面积为40%-80%,过小会因流程过长而导致玻纤取向。
降低强度,增加波纹度,甚至不能充满模腔。
过大,不利于排气,易产生制品内裂纹。
(3) 加料位置与方式加料位置与方式直接影响到制品的外观,强度与方向性。
通常情况下,料的加料位置应在模腔中部。
对于非对称性复杂制品,加料位置必须确保成型时料流同时到达模具成型内腔各端部。
加料方式必须有利于排气。
多层片材叠合时,最好将料块按上小下大呈宝塔形叠置。
另外,料块尽量不要分开加,否则会产生空气裹集和熔接区,导致制品强度下降。
3.成型当料块进入模腔后,压机快速下行。
当上、下模吻合时,缓慢施加所需成型压力,经过一定的固化制度后,制品成型结束。
成型过程中,要合理地选定各种成型工艺参数及压机操作条件。
(1)成型温度成型温度的高低,取决于树脂糊的固化体系、制品厚度,生产效率和制品结构的复杂程度。
成型温度必须保证固化体系引发、交联反应的顺利进行,并实现完全的固化。
一般来说,厚度大的制品所选择的成型温度应比薄壁制品低,这样可以防止过高温度在厚制品内部产生过度的热积聚。
如制品厚度为25~32mm,其成型温度为135-145℃。
而更薄制品可在171℃下成型。
成型温度的提高,可缩短相应的固化时间;反之,当成型温度降低时,则需延长相应的固化时间。