典型零件车削实例讲解
数控车削零件工艺分析举例

※T0404——螺纹刀:刀尖角60°,主轴转速400r/min,进给 速度2mm/r(螺距)。
数控车削加工工艺
※T0505——钻头:钻头直径16mm,主轴转速450r/min。
※T0606——内圆粗车刀:内轮廓粗加工,刀尖圆弧半径 0.8mm,切深1mm,主轴转速500r/min,进给速度100mm/min。 ※T0707——内圆精车刀:内轮廓精加工,刀尖圆弧半径 0.8mm,切深0.4mm,主轴转速800r/min,进给速度60mm/min。
*装夹Φ50外圆表面,探出65mm,粗加工零件左侧外轮廓:
2×45°倒角,Φ48外圆,R20,R16,R10圆弧。
*精加工上述轮廓。
数控车削加工工艺
*手工钻孔,孔深至尺寸要求。 *粗加工孔内轮廓。 *精加工孔内轮廓。 *调头装夹Φ48外圆,粗加工零件右侧外轮廓:2×45°倒
角,螺纹外圆,Φ36端面,锥面,Φ48外圆到圆弧面。
数控机床编程与操作
数控车削加工工艺
完成如图所示零件的加工。毛坯尺寸ф50×114,材料 45钢,零件的径向尺寸公差±0.01mm。
数控车削加工工艺
1.图纸分析 (1)加工内容: 此零件加工包括车端面,外圆,倒角,圆弧,螺纹,槽等。 (2)工件坐标系: 该零件加工需调头,从图纸上尺寸标注分析应设置2个坐标 系,2个工件零点均定于装夹后的右端面(精加工面)。
*精加工上述轮廓。 *切槽。 *螺纹加工。
数控车削加工Байду номын сангаас艺
(5)刀具的选择和切削用量的确定
※T0101——外圆粗车刀:外轮廓粗加工,刀尖圆弧半径 0.8mm, 切 深 2 mm, 主 轴 转 速 8 0 0 r/min , 进 给 速 度 150mm/min。 ※T0202——外圆精车刀:外轮廓精加工,刀尖圆弧半径 0.8mm, 切深0.5mm,主轴转速1500r/min,进给速度 80mm/min。
数控车床零件的工艺分析及编程典型实例

数控车床零件的工艺分析及编程典型实例更新日期:来源:数控工作室根据下图所示的待车削零件,材料为45号钢,其中Ф85圆柱面不加工。
在数控车床上需要进行的工序为:切削Ф80mm 和Ф62mm 外圆;R70mm 弧面、锥面、退刀槽、螺纹及倒角。
要求分析工艺过程与工艺路线,编写加工程序。
图1 车削零件图1.零件加工工艺分析(1)设定工件坐标系按基准重合原则,将工件坐标系的原点设定在零件右端面与回转轴线的交点上,如图中Op点,并通过G50指令设定换刀点相对工件坐标系原点Op的坐标位置(200,100)(2)选择刀具根据零件图的加工要求,需要加工零件的端面、圆柱面、圆锥面、圆弧面、倒角以及切割螺纹退刀槽和螺纹,共需用三把刀具。
1号刀,外圆左偏刀,刀具型号为:CL-MTGNR-2020/R/1608 ISO30。
安装在1号刀位上。
3号刀,螺纹车刀,刀具型号为:TL-LHTR-2020/R/60/1.5 ISO30。
安装在3号刀位上。
5号刀,割槽刀,刀具型号为:ER-SGTFR-2012/R/3.0-0 IS030。
安装在5号刀位上。
(3)加工方案使用1号外圆左偏刀,先粗加工后精加工零件的端面和零件各段的外表面,粗加工时留0.5mm的精车余量;使用5号割槽刀切割螺纹退刀槽;然后使用3号螺纹车刀加工螺纹。
(4)确定切削用量切削深度:粗加工设定切削深度为3mm,精加工为0.5mm。
主轴转速:根据45号钢的切削性能,加工端面和各段外表面时设定切削速度为90m/min;车螺纹时设定主轴转速为250r/min。
进给速度:粗加工时设定进给速度为200mm/min,精加工时设定进给速度为50mm/min。
车削螺纹时设定进给速度为1.5mm/r。
2.编程与操作(1)编制程序(2)程序输入数控系统将程序在数控车床MDI方式下直接输入数控系统,或通过计算机通信接口将程序输入数控机床的数控系统。
然后在CRT 屏幕上模拟切削加工,检验程序的正确性。
典型配合零件的车削加工分析
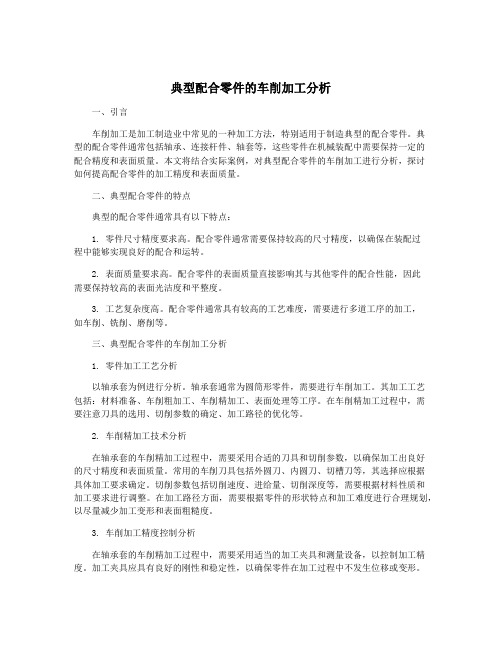
典型配合零件的车削加工分析一、引言车削加工是加工制造业中常见的一种加工方法,特别适用于制造典型的配合零件。
典型的配合零件通常包括轴承、连接杆件、轴套等,这些零件在机械装配中需要保持一定的配合精度和表面质量。
本文将结合实际案例,对典型配合零件的车削加工进行分析,探讨如何提高配合零件的加工精度和表面质量。
二、典型配合零件的特点典型的配合零件通常具有以下特点:1. 零件尺寸精度要求高。
配合零件通常需要保持较高的尺寸精度,以确保在装配过程中能够实现良好的配合和运转。
2. 表面质量要求高。
配合零件的表面质量直接影响其与其他零件的配合性能,因此需要保持较高的表面光洁度和平整度。
3. 工艺复杂度高。
配合零件通常具有较高的工艺难度,需要进行多道工序的加工,如车削、铣削、磨削等。
三、典型配合零件的车削加工分析1. 零件加工工艺分析以轴承套为例进行分析。
轴承套通常为圆筒形零件,需要进行车削加工。
其加工工艺包括:材料准备、车削粗加工、车削精加工、表面处理等工序。
在车削精加工过程中,需要注意刀具的选用、切削参数的确定、加工路径的优化等。
2. 车削精加工技术分析在轴承套的车削精加工过程中,需要采用合适的刀具和切削参数,以确保加工出良好的尺寸精度和表面质量。
常用的车削刀具包括外圆刀、内圆刀、切槽刀等,其选择应根据具体加工要求确定。
切削参数包括切削速度、进给量、切削深度等,需要根据材料性质和加工要求进行调整。
在加工路径方面,需要根据零件的形状特点和加工难度进行合理规划,以尽量减少加工变形和表面粗糙度。
3. 车削加工精度控制分析在轴承套的车削精加工过程中,需要采用适当的加工夹具和测量设备,以控制加工精度。
加工夹具应具有良好的刚性和稳定性,以确保零件在加工过程中不发生位移或变形。
测量设备应具备高精度和高稳定性,以确保对加工尺寸和表面质量的准确测量。
通过合理的工艺控制和精密的测量,可以保证轴承套的加工精度符合要求。
四、加工实例分析下面以一起实际的加工实例进行分析。
车削加工工艺实例

车削加工工艺实例轴类零件是最常见的典型零件之一。
而阶梯轴的车削工艺是一种典型的轴类零件加工工艺,反映了轴类零件加工的大部分内容与基本规律。
结合实训教学实际,我们列举两个实训项目零件来讲解车工工艺。
一、台阶轴车削工艺步骤1.零件图见图5–12.材料:45圆钢图5–1 零件图3.车削加工工艺(1)锯床下料45#钢Φ35×123 卷尺;(2)车床上用三爪卡盘装夹伸出长度L=80;(3)车端面见平,45°车刀, n=800r/min, f=0.15~0.25mm/r,a p≤2 mm;⑷钻中心B2.5/8 B2.5 中心钻Φ1~ Φ16 钻夹头n=1120r/min;⑸车Φ25外圆,L=70 90°车刀0-150游表卡尺;n=800r/min f=0.15~0.25mm/r a p≤2 mm;⑹车18外圆L=70 90°车刀0-150 mm游表卡尺0-25mm千分尺n=800r/min .f=15~0.25mm/r a p≤2 mm;⑺倒角1×45°45°车刀n=800r/min;⑻掉头夹持另一端车Φ25外圆;⑼车端面保证总长L=120 0-150mm游表卡尺n=800r/min;⑽钻中心B2.5/8 B2.5中心钻1~ 16钻夹头n=1120r/min;⑾夹持Φ18外圆并用活顶尖顶上中心孔;⑿车Φ32外圆,L≥50 90°车刀, 25-50mm千分尺, n=800r/min, f=0.15~0.25mm/r a p≤2 mm;⒀车Φ24外圆,L=20 90°车刀, 0-150mm游表卡尺, 0-25mm千分尺, n=800r/min f=0.15~0.25mm/r a p≤2 mm;⒁倒角1×45°,45°车刀, n=800r/min;⒂打学号印记,四号字头,锤子;⒃检测。
数控车削加工工艺例题分析

5—1数控车削加工工艺——典型盘类零件例题分析:(锐角倒钝)导入内容:该零件加工材料:灰铸铁(HT400)—在结晶过程中充分石墨化的铸铁。
结晶:金属从高温液体状态冷却凝固为固体状态的过程。
灰铸铁特性:1.石墨具有脆性2.抗拉强度、塑性、韧性比刚差3.抗压强度、硬度与刚相同。
4.石墨具有良好的润滑性,能获得良好的切削性能。
耐磨性好消音减震能力好。
5.HT400使用场合多而广,适宜承受较高负荷的重要零件。
6.HT400:含义是HT灰铁,400最小抗拉强度为400Mpa7.切削的切削呈崩碎状,能减小切削与前刀面的摩擦,切削热减少,刀具使用寿命长。
新课授入:一.零件图工艺分析该盘类零件由外圆柱、沟槽、内孔等表面组成,其中多个直径尺寸有较高的精度和表面粗糙度要求。
零件图尺寸标注完整,轮廓描述清楚材料为灰铸铁,无热处理及硬度要求。
通过分析,采用以下几点工艺措施。
a)图样上面给定的尺寸精度要求较高,公差值较小,编程时取零件基本尺寸。
b)毛坯选择规则的表面粗糙度及缺陷层材料,规格为90mm*70mm 的管料。
c)为了便于加工采用调头装夹来完成零件,并预先钻好孔,选择2 #莫氏锥柄(直径14.25-23mm)号。
(钻头直径小于20mm)d)确定采用法那科(FANUC)系统加工零件。
二.确定装夹方案确定坯件采用三爪自定心卡盘定心装夹(不需要采用活动顶尖支撑:伸出长度小于2倍的最大夹持直径)三.确定加工顺序及进给路线加工顺序从粗到精,从右到左(从近到远),内外交叉原则。
a)先从右到左进行粗车(留0.2mm单边精车余量)至直径为85mm 轮廓处,然后精车轮廓(同前),再切6*2.5mm槽,最后粗——精镗直径为32mm*50mm内孔。
b)调头装夹:保证总长69mm。
从右到左粗车轮廓(留0.2mm单边精车余量)至直径为65mm轮廓处,然后精车轮廓(同前),再粗——精镗直径为20mm*15mm内孔。
四.刀具选择a)粗、精车外轮廓选择W型(80度)硬质合金外圆车刀。
典型零件车削实例讲解

典型零件车削实例项目一使用花盘装夹车削复杂零件一、基础知识花盘是一个使用铸铁制作的大圆盘,盘面上有很多长短不同呈辐射状分布的通槽或T 型槽。
用于安装各种螺钉来紧固工件,花盘可以直接安装在车床主轴上,其盘面必须与主轴轴线垂直,并且盘面平整。
花盘再使用时必须找正,安装好花盘后,装夹工件前应该认真检查以下两项内容。
1.检测花盘盘面对车床主轴轴线的端面圆跳动2.检测花盘盘面的平行度误差连杆零件【工艺分析】(1)加工表面分析。
(2)精度分析。
(3)加工路线。
【加工步骤】1.车削基准孔时的装夹步骤2.加工基准孔3.车削孔时的装夹步骤4.加工孔定位套用定位套校正中心距5.中心距检测6.两平面对基准孔轴线垂直度检测7.两孔轴线平行度误差的检测【注意事项】(1)车削内孔前,一定要认真检查花盘上所有压板、螺钉的紧固情况,然后将床鞍移到车削加工的最终位置,用手转动花盘,检查工件、附件是否与小滑板前端及刀架碰撞、以免发生事故。
2)压板螺钉应靠近工件安装,垫块高度应与工件厚度相同。
3)车削时,主轴转速不宜过高,切削用量不宜过大,以免引起振动,影响孔的精度。
同时,转速过高时,离心力大,还容易发生事故。
项目二车削细长轴1.细长轴的加工特点工件长度跟直径之比大于25倍(L/d>25)的轴类零件称为细长轴。
加工时,需要重点解决中心架和跟刀架的使用、工件热变形伸长、合理选择车刀几何形状等3个关键技术。
2.细长轴的装夹方法细长轴通常使用一顶一夹或者两顶尖装夹法,为了增强刚性,装夹时还可以采用中心架、跟刀架或者其他辅助支承。
(1)常用装夹方法。
①中心架直接支承。
②中心架间接支承。
③一端用三爪自定心卡盘,一端用中心架。
④使用三爪跟刀架。
2)装夹细长轴的注意事项。
①当毛坯弯曲较大时,应使用四爪单动卡盘装夹,因为四爪单动卡盘可调整被夹工件的圆心位置。
当工件毛坯加工余量充足时,可以“借正”弯曲过大的毛坯部分。
②卡爪夹持毛坯不宜过长,一般为15~20 mm1~5 mm的钢丝绕一圈在夹头上充当垫块。
薄壁零件的车削方法

薄壁零件的车削方法1.用一次装夹车薄壁零件:车削短小薄壁工件时,为了保证内外圆轴线的同轴度,可用一次装夹车削。
例:薄壁衬套,材料为锡青铜,工件壁厚仅2mm,同轴度公差为0.025mm,精度要求较高。
车削方法见下图:夹持棒料,车出长度45mm,粗车内外圆均留0.5mm余量,钻,粗车内孔时,要求长度比图样长2mm即可。
以增加工件的刚性,加注切削液,使工件充分冷却后,精车内外圆至尺寸。
(油槽在半精车后拉出)切断工件,最后装夹在心轴上,车削另一端面和倒角。
2.用扇形卡爪及心轴装夹薄壁工件:例:薄壁套筒如图,车削方法:粗车留精车余量1~1.5mm,精车时,装夹在扇形软卡中,精车内孔及φ72H7,外圆φ980-0.1及端面A符合图样要求,然后以内孔和大端面为基准,夹在弹性胀力心轴上,即可精车外圆。
3.在花盘上车削薄壁工件:直径较大,尺寸精度和形位精度都较高的圆盘薄壁工件。
可装夹在花盘上加工。
车削方法:先装夹在三爪卡盘上粗车内孔及外圆,各留1~1.5mm余量,长度尺寸车至92+0.3+0.2,并精磨两端面至长度92。
然后装夹在花盘上精车内孔及外圆,精车内孔的装夹方法见图。
先在花盘端面上车出一凸台,凸台的直径和工件之间留0.5~1mm的间隙,(不用作定心)。
用螺栓,压板压紧工件端面,压紧力要均匀。
找正后,即可车削φ132H7, φ262H7内孔及内端平面。
精车外圆时的方法见下图:将三点接触压板(压板上有三条槽以让开压板)适当压紧,松开并取下压板及螺钉,即可车削外圆,使之符合图样要求.上面的压紧方法,因为压紧力在轴向,所以不容易引起变形。
4.在专用夹具上车削薄壁零件:如图,工件装上夹具后,当拧紧螺钉2时,压紧圈1便沿着斜面将工件压紧,即可车削工件的内孔,外圆及端面。
5.增加辅助支承车削薄壁零件:车削内孔精度要求高的薄壁零件时,可采用辅助支承来增加工件的刚性.6.增加工艺肋车削薄壁工件.在工件的装夹部位特制几根工艺支撑肋,使夹紧力作用在肋上,可减少变形.二.减少工件变形的方法:1.工件分粗精车,消除粗车时切削力过大而产生的变形,粗车后,使工件得到自然冷却,消除在精车时可能产生的热变形。
典型配合零件的车削加工分析

典型配合零件的车削加工分析
车削加工是一种广泛应用于机械制造领域的加工方法,通过旋转工件,并利用切削工具切削工件的材料来实现对工件的加工。
在车削加工中,零件的配合是非常重要的一个环节,因为良好的配合可以确保零件的准确性、精度和质量。
1. 轴承座的加工:车削加工常用于加工轴承座,轴承座是支撑轴承的重要零件。
在车削加工中,首先需要根据轴承的尺寸要求选择合适的材料进行加工。
然后使用车床将材料固定在主轴上,并通过切削工具对材料进行车削加工,形成轴承座的外形和内部孔径。
2. 螺纹孔的加工:螺纹孔是一种常见的零件配合形式,在车削加工中也经常进行加工。
螺纹孔的加工需要根据螺纹规格选择适当的切削工具,并通过车床进行加工。
在加工过程中,需要根据螺纹的要求来调整车床的进给速度和主轴转速,以确保螺纹孔的加工质量。
典型配合零件的车削加工是一种常见的加工方法,通过选择适当的切削工具和刀具参数,并通过车床进行加工,可以实现对零件的精确加工和配合。
在进行车削加工时,需要根据零件的尺寸、配合要求和加工工艺来选择合适的加工方法,并合理调整加工参数,以确保零件的加工质量。
[精选]典型零件加工工艺
![[精选]典型零件加工工艺](https://img.taocdn.com/s3/m/50ec52ca690203d8ce2f0066f5335a8102d2661f.png)
[精选]典型零件加工工艺(一)数控车削加工典型零件工艺分析实例1.编写如图所示零件的加工工艺。
(1)零件图分析如图所示零件,由圆弧面、外圆锥面、球面构成。
其中Φ50外圆柱面直径处不加工,而Φ40外圆柱面直径处加工精度较高。
零件材料:45钢毛坯尺寸:Φ50×110(2)零件的装夹及夹具的选择采用机床三爪自动定心卡盘,零件伸出三爪卡盘外75mm左右,以外圆定位并夹紧。
(3)加工方案及加工顺序的确定以零件右端面和中心轴作为坐标原点建立工件坐标系。
根据零件尺寸精度及技术要求,零件从右向左加工,将粗、精加工分开来考虑。
加工工艺顺序为:车削右端面→复合型车削固定循环粗、精加工右端需要加工的所有轮廓(粗车Φ44、Φ40.5、Φ34.5、Φ28.5、Φ22.5、Φ16.5外圆柱面→粗车圆弧面R14.25→精车外圆柱面Φ40.5→粗车外圆锥面→粗车外圆弧面R4.75→精车圆弧面R14→精车外圆锥面→精车外圆柱面Φ40→精车外圆弧面R5)。
(4)选择刀具选择1号刀具为90°硬质合金机夹偏刀,用于粗、精车削加工。
(5)切削用量选择粗车主轴转速n=630r/min,精车主轴转速V=110m/min,进给速度粗车为f=0.2mm/r,精车为f=0.07mm/r。
2.编写如图1-26所示的轴承套的加工工艺(1)零件图分析零件表面由内圆锥面,顺圆弧,逆圆弧和外螺纹等组成。
有多个直径尺寸与轴向尺寸有较高的尺寸精度和表面粗糙度要求(如果加工质量要求较高的表面不多可列出)。
零件材料:45号钢毛坯尺寸:φ80×112(2)零件的装夹及夹具的选择内孔加工时,以外圆定位,用三爪自动定心卡盘夹紧,需掉头装夹;加工外轮廓时,以圆锥心轴定位,用三爪卡盘夹持心轴左端,右端利用中心孔顶紧。
(3)加工方案及加工顺序的确定以零件右端面中心作为坐标原点建立工件坐标系。
根据零件尺寸精度及技术要求,确定先内后外,先粗后精的原则。
机械制造工艺-典型车削零件实例

—典型车削零件实例—
如图所示轴类零件,所用机床为TND360型数控车床,其数控车削加工 工艺分析如下:
零件图工艺分析
1、轮廓组成:该零件表面由圆柱、 圆锥、圆弧及螺纹等表面组成。 2、尺寸特点:几个精度要求较高 的尺寸,公差数值较小,编程时 取其基本尺寸 3、为便于装夹,毛坯左端预先车 出夹持部分。
确定装夹方案
左端采用三爪自Biblioteka 心卡盘定 心夹紧、右端采用活动顶尖 支承的装夹方式
确定加工顺序及进给路线
加工顺序按由粗到精、由近到远(由右到左)的原则。即先从 右到左进行粗车(留0.25mm精车余量),然后从右到左进行 精车,最后车削螺纹。
刀具选择
中心钻
35°外圆车刀
Φ 5mm中心钻 35°外圆车刀 60°外螺纹车刀
60°外螺纹车刀
刀具卡片
05
切削用量的选择
(1)背吃刀量的选择: 轮廓粗车 ap=3mm,精车ap=0.25mm 螺纹粗车 ap=0.4mm,精车ap=0.1mm
(2)主轴转速的选择: 轮廓粗n=500r/min,精车n=1200r/min 螺 纹 n=320r/min
(3)进给速度的选择: 轮廓粗车 vf=200mm /min ,精车vf= 180mm /min 螺 纹 vf= 960mm /min
06 编 写 工 艺 文 件
然后进行仿真模拟 利用数控车床加工
目总录 结 \ CONTENTS
零件图 工艺分析
确定装 夹方案
刀具选择
填写工 艺文件
切削用量 的选择
编程、仿真、 加工
—典型车削零件实例—
感谢观看
数控机床车削加工例

数控机床车削加工例数控机床在现代制造业中扮演着重要的角色,具有高效、精度高、自动化程度高等优点。
数控机床具有多种功能,车削加工是其常见的一种加工方式。
本文将介绍数控机床车削加工的例子。
一、数控车床车削加工例在数控车床车削加工中,常用的零件有轴承、法兰、轮毂、齿轮、活塞等。
下面以轴承零件为例,介绍数控车床车削加工的步骤。
1、加工轴承外圆首先需要将工件夹在三爪卡盘上,然后将加工刀具放置于车床主轴上,将工件对准刀具,并确定加工中心。
接下来,根据加工轴承外圆的要求,设置车床的加工参数,包括进给速度、回程速度、切削深度、切削速度等。
最后启动数控机床,进行加工。
2、加工轴承内孔加工轴承内孔时,需要将工件夹在弹性夹头上,并将夹头插入主轴孔中,确定夹紧力度。
然后,在车床主轴上放置加工刀具,对准工件,并设置加工参数。
最后启动数控机床进行加工。
二、数控铣床加工例数控铣床也是常见的加工设备之一,常用于加工平面、倒角、凸轮等零件。
下面以平面零件为例,介绍数控铣床加工的步骤。
1、夹紧工件首先需要将工件夹在工件台上,并固定好位置。
确保工件夹紧力度适中,不会出现松动的情况。
2、设置刀具并定位根据加工要求,选择合适的刀具进行加工。
在铣床主轴上安装刀具后,需要对准工件进行定位,确定加工位置和加工范围。
3、设置加工参数根据加工要求,设置加工参数。
包括进给速度、回程速度、切削深度、切削速度等。
加工参数设置的好坏将会影响加工效果和精度。
4、启动铣床进行加工最后,启动数控铣床进行加工。
操作过程中需要注意观察机床运行状态和工件加工情况,及时调整参数,确保加工精度和效率。
总之,数控机床车削加工是现代制造业的基础,具有广泛的应用前景和市场需求。
同时,随着科技的发展和加工技术的提高,数控机床也在不断地升级和完善,让加工更加高效、精度更高、自动化程度更高,为人类创造更多的价值。
数控车床零件加工综合实例解析21张幻灯片课件

数控机床编程与操作
②数控加工程序的编制 5.2.4 零件的数控加工
1、机遇对于有准备的头脑有特别的亲和力。
2、不求与人相比,但求超越自己,要 哭就哭 出激动 的泪水 ,要笑 就笑出 成长的 性格! 3、在你内心深处,还有无穷的潜力, 有一天 当你回 首看时 ,你就 会知道 这绝对 是真的 。 4、无论你觉得自己多么的了不起,也 永远有 人比你 更强; 无论你 觉得自 己多么 的不幸 ,永远 有人比 你更加 不幸。
32、滴水穿石不是靠力,而是因为不 舍昼夜 。 33、忍别人所不能忍的痛,吃别人所 别人所 不能吃 的苦, 是为了 收获得 不到的 收获。
34、时间是个常数,但也是个变数。 勤奋的 人无穷 多,懒 惰的人 无穷少 。—— 字严 35、不同的信念,决定不同的命运!
36、只有你学会把自己已有的成绩都 归零, 才能腾 出空间 去接纳 更多的 新东西 ,如此 才能使 自己不 断的超 越自己 。 37、突破心理障碍,才能超越自己。
数控机床编程与操作 ④刀具的选择
数控机床编程与操作 ⑤切削用量的确定
数控机床编程与操作
5.1.3基点坐标的计算及加工程序的编制 ①基点坐标的计算
数控机床编程与操作 ①基点坐标的计算
数控机床编程与操作
②数控加工程序的编制 5.1.4 零件的数控加工
数控机床编程与操作
5.2套类零件的编程与加工 5.2.1零件图纸及加工要求
25、我学习了一生,现在我还在学习, 而将来 ,只要 我还有 精力, 我还要 学习下 去。— —别林 斯基
13、你不能左右天气,但可以改变心 情。你 不能改 变容貌 ,但可 以掌握 自己。 你不能 预见明 天,但 可以珍 惜今天 。 14、我们总是对陌生人太客气,而对 亲密的 人太苛 刻。
第三讲典型轴类零件数控车削加工工艺及编程
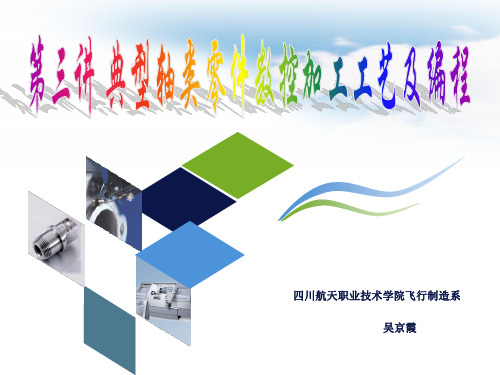
案例:轴类零件材料45钢,毛坯尺寸为Ф60mm×140mm,数量
50件,要求对该零件进行数控加工程序编制。
3.1 数控编程的工艺处理
工艺处理主要包括数控加工工艺分析、确定加工议案、切削用
量选择及编制数控加工工艺文件。
3.1.1 数控加工工艺分析
1.对零件数控加工可行性和方便性的分析
2.选择装夹定位方案 对装夹定位的要求,尽量采用通用夹具。该零件毛坯为圆
柱形棒料,各回转表面的回转轴线均为中心轴线,故可采用 车床自带的三爪卡盘进行装夹和定位。
3.确定加工路线 该零件加工顺序按由粗车到精车顺序加工,工步顺 序按同一把车刀能加工的内容连续加工的原则确定。 该零件进给路线粗加工外轮廓采用“矩形”循环; 精加工路线基本上沿零件轮廓采用“由近到远”的顺序 加工。但在具体路线的确定过程中,应注意减少空行程, 正确选择刀具切入、切出工件的方向,保证最终轮廓一 次走刀完成。
3600.021 36.0105 0.0105(36.010 0.010)
3.1.2
1.选择大小,加工精度和表面质 量等技术要求,正确合理地选择其规格和型号。
根据该零件的加工精度、表面粗糙度、结构形状、尺寸大小和 材料性质等条件,选定CK6132经济型数控车床。
该 机 床 最 大 回 转 直径为 Ф320mm~Ф160mm;最大加工长度 750mm;主轴车速范围25~1600r/min;X轴的行程为200mm,Z 轴行程为800mm;定位精度:X向0.03mm,、Z向0.04;重复定 位精度: X向0.012mm,、Z向0.016;加工精度IT6~IT7级; 表面粗糙度Ra1.6μm;电动立式四工件刀架控制系统FANUC。
度 c 。
数控车削加工实例
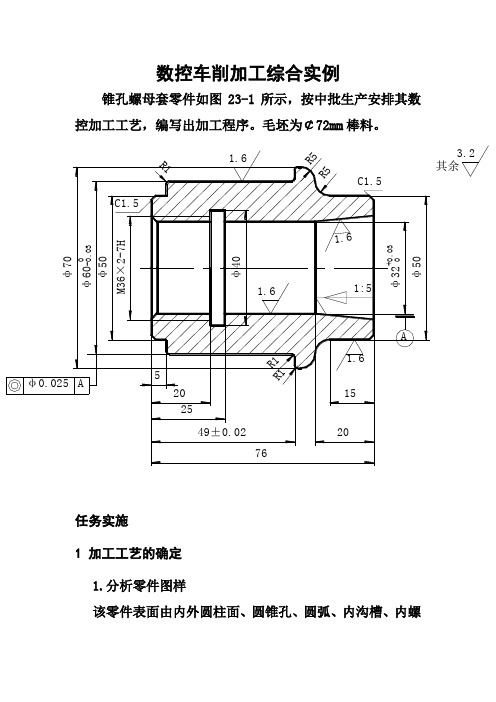
数控车削加工综合实例锥孔螺母套零件如图23-1所示,按中批生产安排其数控加工工艺,编写出加工程序。
毛坯为¢72mm 棒料。
任务实施1 加工工艺的确定 1.分析零件图样该零件表面由内外圆柱面、圆锥孔、圆弧、内沟槽、内螺其余3.2纹等表面组成。
其中多个径向尺寸和轴向尺寸有较高的尺寸精度、表面质量和位置公差要求。
2.工艺分析1)加工方案的确定根据零件的加工要求,各表面的加工方案确定为粗车→精车。
2)装夹方案的确定加工内孔时以外圆定位,用三爪自定心卡盘装夹。
加工外轮廓时,为了保证同轴度要求和便于装夹,以工件左端面和¢32孔轴线作为定位基准,为此需要设计一心轴装置(图23-2中双点划线部分),用三爪卡盘夹持心轴左端,心轴右端留有中心孔并用顶尖顶紧以提高工艺系统的刚性。
外轮廓车削心轴定位装夹方案3)加工工艺的确定(1)加工路线的确定加工路线见表23-1。
数控加工工艺路线单(2)工序30①工序卡工序卡见表。
数控加工工序卡②进给路线的确定(略)③刀具及切削参数的确定刀具及切削参数的确定见表。
数控加工刀具卡(3)工序40①工序卡工序卡见表。
数控加工工序卡②进给路线的确定(略)③刀具及切削参数的确定刀具及切削参数的确定见表。
数控加工刀具卡(3)工序50①工序卡工序卡见表。
数控加工工序卡②进给路线的确定精加工外轮廓的走刀路线如图所示,粗加工外轮廓的走刀路线略。
外轮廓车削进给路线③刀具及切削参数的确定刀具及切削参数的确定见表。
数控加工刀具卡2 参考程序编制1.工序301)工件坐标系的建立以工件左端面与轴线的交点为编程原点建立工件坐标系。
2)基点坐标计算(略)3)参考程序参考程序见表工序30参考程序2.工序401)工件坐标系的建立以工件右端面与轴线的交点为编程原点建立工件坐标系。
2)基点坐标计算(略)3)参考程序参考程序见表工序40参考程序3.工序501)工件坐标系的建立以工件右端面与轴线的交点为编程原点建立工件坐标系。
数控车削加工案例分析(二)
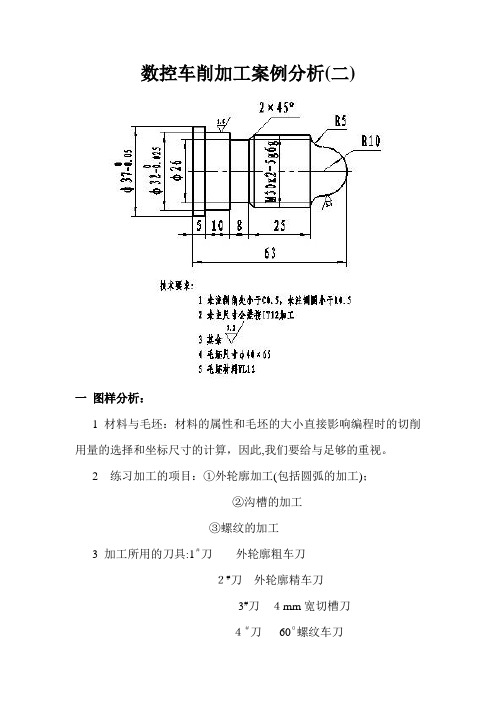
数控车削加工案例分析(二)
一图样分析:
1 材料与毛坯:材料的属性和毛坯的大小直接影响编程时的切削用量的选择和坐标尺寸的计算,因此,我们要给与足够的重视。
2练习加工的项目:①外轮廓加工(包括圆弧的加工);
②沟槽的加工
③螺纹的加工
3 加工所用的刀具:1#刀外轮廓粗车刀
2#刀外轮廓精车刀
3#刀4mm宽切槽刀
4#刀600螺纹车刀
4 技术要求:注意未注倒角、未注公差、未注表面粗糙度的要求
5 加工工序卡
二手工编写程序:
要求:1外轮廓的粗精加工使用G71\G70指令;
2 编制倒角程序;
3计算牙型高度并使用G92螺纹固定循环指令
三程序的输入与修改:
把编写好的程序输入到机床中,熟练掌握用操作面板输入程序。
四程序的校验:
利用机床上的图形模拟功能校验程序,掌握定义毛坯、判断图形。
五对刀操作:
对刀操作是数控机床学习中的重点,将重点讲述。
六零件的加工:
1 空运行、
2 单段运行、
3 自动运行
七工件的检验:
尺寸精度的控制方法:
1修改程序、2偏移坐标系、3 修改刀补值。
数控车床车削典型零件工艺分析

数控车床车削典型零件工艺分析数控车床是一种利用数控技术进行自动化车削加工的机床,广泛应用于制造业的各个领域。
下面将以数控车床车削典型零件为例进行工艺分析。
以加工一台螺杆为例,工艺分析如下:1.零件材质选择:根据螺杆的使用要求,选择适当的材料,常见的有碳钢、不锈钢等。
2.设计图纸:根据产品需求,在CAD软件中绘制螺杆的设计图纸,包括尺寸、形状等。
3.工艺规程编制:根据零件的设计要求,编制螺杆的工艺规程,包括车削工序、工艺参数、刀具选择等。
4.刀具选择:根据工艺规程选择适合的刀具,考虑切削力、刀具寿命等因素。
5.数控编程:根据工艺规程,利用CAM软件编写数控程序,确定刀具路径、切削深度、进给速度等参数。
6.夹紧装夹:将材料切割到合适的长度后,将工件固定在数控车床的主轴上,使用合适的夹具夹紧。
7.车削加工:根据数控程序进行车削加工,包括外径车削、内径车削、螺纹加工等工序。
8.检测与修正:每一道工序完成后,需要进行质量检测,确保零件尺寸、表面粗糙度等符合要求。
若发现问题,及时进行修正。
9.表面处理:根据产品要求,对螺杆表面进行处理,如抛光、镀层等。
10.质量检验:经过表面处理后,对零件进行再次质量检验,确保各项指标符合要求。
11.包装运输:将加工好的螺杆进行包装和标识,便于运输和使用。
以上是加工一台螺杆的工艺流程,数控车床的精度高、重复性好,能够高效、精确地进行复杂零件的加工。
在实际应用中,根据不同的零部件要求,工艺流程可能会有所不同,但总的来说,工艺分析包括材料选择、工艺规程编制、刀具选择、数控编程、夹紧装夹、车削加工、检测与修正、表面处理、质量检验、包装运输等环节。
通过合理的工艺分析和流程设计,可以实现零件的高效、精确加工,提高生产效率和产品质量。
外圆车削的加工工艺实例
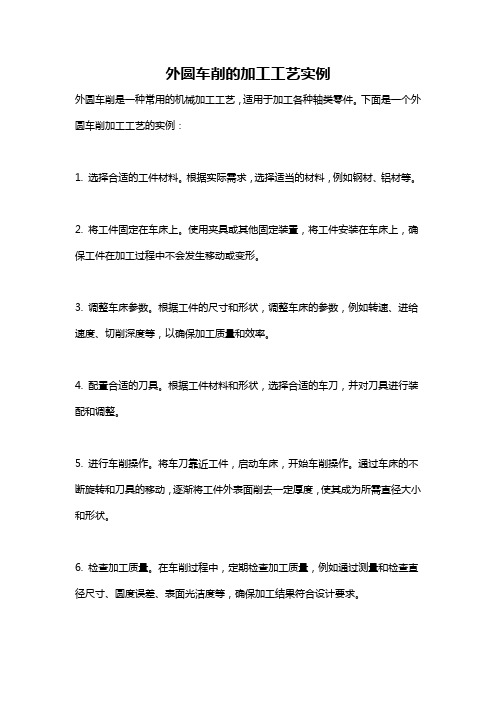
外圆车削的加工工艺实例
外圆车削是一种常用的机械加工工艺,适用于加工各种轴类零件。
下面是一个外圆车削加工工艺的实例:
1. 选择合适的工件材料。
根据实际需求,选择适当的材料,例如钢材、铝材等。
2. 将工件固定在车床上。
使用夹具或其他固定装置,将工件安装在车床上,确保工件在加工过程中不会发生移动或变形。
3. 调整车床参数。
根据工件的尺寸和形状,调整车床的参数,例如转速、进给速度、切削深度等,以确保加工质量和效率。
4. 配置合适的刀具。
根据工件材料和形状,选择合适的车刀,并对刀具进行装配和调整。
5. 进行车削操作。
将车刀靠近工件,启动车床,开始车削操作。
通过车床的不断旋转和刀具的移动,逐渐将工件外表面削去一定厚度,使其成为所需直径大小和形状。
6. 检查加工质量。
在车削过程中,定期检查加工质量,例如通过测量和检查直径尺寸、圆度误差、表面光洁度等,确保加工结果符合设计要求。
7. 完成后续处理。
如果需要,可以进行后续处理工艺,例如去除毛刺、刀痕等,并进行热处理或表面处理等,以提高工件的使用性能和外观质量。
以上是一个外圆车削加工工艺的简单实例,实际操作过程中还需要考虑各种因素,例如切削力控制、冷却润滑、切屑排除等,以确保加工的安全和稳定性。
- 1、下载文档前请自行甄别文档内容的完整性,平台不提供额外的编辑、内容补充、找答案等附加服务。
- 2、"仅部分预览"的文档,不可在线预览部分如存在完整性等问题,可反馈申请退款(可完整预览的文档不适用该条件!)。
- 3、如文档侵犯您的权益,请联系客服反馈,我们会尽快为您处理(人工客服工作时间:9:00-18:30)。
典型零件车削实例项目一使用花盘装夹车削复杂零件一、基础知识花盘是一个使用铸铁制作的大圆盘,盘面上有很多长短不同呈辐射状分布的通槽或T 型槽。
用于安装各种螺钉来紧固工件,花盘可以直接安装在车床主轴上,其盘面必须与主轴轴线垂直,并且盘面平整。
花盘再使用时必须找正,安装好花盘后,装夹工件前应该认真检查以下两项内容。
1.检测花盘盘面对车床主轴轴线的端面圆跳动2.检测花盘盘面的平行度误差连杆零件【工艺分析】(1)加工表面分析。
(2)精度分析。
(3)加工路线。
【加工步骤】1.车削基准孔时的装夹步骤2.加工基准孔3.车削孔时的装夹步骤4.加工孔定位套用定位套校正中心距5.中心距检测6.两平面对基准孔轴线垂直度检测7.两孔轴线平行度误差的检测【注意事项】(1)车削内孔前,一定要认真检查花盘上所有压板、螺钉的紧固情况,然后将床鞍移到车削加工的最终位置,用手转动花盘,检查工件、附件是否与小滑板前端及刀架碰撞、以免发生事故。
2)压板螺钉应靠近工件安装,垫块高度应与工件厚度相同。
3)车削时,主轴转速不宜过高,切削用量不宜过大,以免引起振动,影响孔的精度。
同时,转速过高时,离心力大,还容易发生事故。
项目二车削细长轴1.细长轴的加工特点工件长度跟直径之比大于25倍(L/d>25)的轴类零件称为细长轴。
加工时,需要重点解决中心架和跟刀架的使用、工件热变形伸长、合理选择车刀几何形状等3个关键技术。
2.细长轴的装夹方法细长轴通常使用一顶一夹或者两顶尖装夹法,为了增强刚性,装夹时还可以采用中心架、跟刀架或者其他辅助支承。
(1)常用装夹方法。
①中心架直接支承。
②中心架间接支承。
③一端用三爪自定心卡盘,一端用中心架。
④使用三爪跟刀架。
2)装夹细长轴的注意事项。
①当毛坯弯曲较大时,应使用四爪单动卡盘装夹,因为四爪单动卡盘可调整被夹工件的圆心位置。
当工件毛坯加工余量充足时,可以“借正”弯曲过大的毛坯部分。
②卡爪夹持毛坯不宜过长,一般为15~20 mm1~5 mm的钢丝绕一圈在夹头上充当垫块。
③尾座端宜采用弹性回转顶尖。
当因切削热导致工件伸长时,工件推动顶尖压缩碟形弹簧,可以有效地3.细长轴刀具的基本要求车削细长轴时,由于工件刚性差,通常选用主偏角较大的车刀。
车刀的几何形状对工件的弯曲变形和振动有明显影响。
4.典型细长轴车刀(1)90°细长轴车刀。
(2)93°细长轴精车刀。
(3)75°细长轴粗车刀。
5.切削用量选择补偿工件的热变形,避免其发生弯曲。
车削如图所示细长轴【加工分析】由于工件为光轴,长径比L/D达到50,适合采用跟刀架支承车削。
【工艺准备】(1)校直毛坯。
(2)检查并清洁三爪跟刀架。
(3)刃磨好粗车和精车时使用的外圆车刀。
【注意事项】(1)为了防止细长轴产生锥度,车削前必须调整尾座中心,使之与车床主轴同轴。
(2)粗车时应认真选择第1次切削深度,必须保证将工件毛坯一次进刀车圆,以免影响跟刀架的正常工作。
(3)车削过程中,应随时注意支承爪与工件表面的接触状态及支承爪的磨损状况,并根据实际情况作出相应调整。
(4)加工中,如发现工件出现竹节、腰鼓等缺陷时,要及时处理。
(5)车削过程中,要始终确保充分浇注切削液。
任务三车削偏心轴一、基础知识外圆与外圆或外圆与内孔的轴向相互平行但不重合的工件称为偏心工件。
外圆与外圆偏心的工件称为偏心轴,当轴向尺寸较小时又称偏心盘;外圆与内孔偏心的工件称为偏心套。
偏心工件两轴线间的距离称为偏心距e。
1.偏心件的划线(1)划工件轴线。
(2)在工件端面和四周划圈线。
(3)打样冲眼。
2.在四爪单动卡盘上车削偏心工件(1)偏心件的找正方法。
①根据已经划好的偏心圆找正。
②用百分表找正。
(2)划线找正的基本步骤。
(3)用百分表找正的操作步骤。
(4)车削过程。
(5)注意事项。
3.用三爪自定心卡盘装夹车削偏心工件第1次装夹工件对于长度较短的偏心工件,可以在三爪自定心卡盘上增加一块垫片,使工件产生偏心后再车削.(1)垫片厚度的计算。
(2)注意事项。
用三爪自定心卡盘装夹车削偏心工件4.在两顶尖间车削偏心零件对于较长的偏心轴,只要两端能钻中心孔,且具有装夹鸡心夹头的位置,都可以使用两顶尖装夹进行车削.在两顶尖间车削偏心零件(1)工艺特点。
(2)偏心中心孔的加工。
(3)注意事项。
5.在双重卡盘上车削偏心零件当偏心件批量较大时,可以采用四爪单动卡盘与三爪定心卡盘相结合的方法来装夹工件.1.划线练习(1)工艺特点。
(2)注意事项1.划线练习工件如图6-42所示:总长65 mm;偏心距e=4±0.2 mm;基准外圆φ48 mm;偏心外圆φ35 mm,长度为30mm。
表面粗糙度值为Ra3.2 。
【操作要领】(1)划线用涂剂应有良好的附着性,涂层不宜过厚,以免影响划线的清晰度。
(2)划线时,用手扶住工件,防止其移动和转动。
(3)划线平台表面与游标高度尺底座底面应光洁无毛刺,平台表面可薄涂一层机油,以减小游标卡尺移动的摩擦阻力。
(4)样冲尖应仔细刃磨,要求圆且尖;敲击样冲时,应使样冲与标示线条垂直;冲偏心轴孔时更要注意,防止产生偏心误差;偏心圆圆周上样冲眼一般均匀打4个即可。
2.在四爪单动卡盘上车削偏心工件被加工工件为一偏心套,基准是φ40 mm,深度为45 mm的阶台孔,8级精度,表面粗糙度为Ra1.6 。
偏心套偏心套【加工步骤】(1)用三爪自定心卡盘夹持毛坯外圆45 mm,长10 mm,表面粗糙度Ra值为6.3 m。
(245 mm外圆,校正并夹紧。
(3)车平端面,粗、精车外圆至尺寸。
倒角(4)钻孔mm,深44 mm。
(5)粗、精车内孔,孔口倒角(6)工件调头夹持(垫铜片),校正并夹紧,切去工艺凸台,车端面,保证总长65 mm,倒角。
(7)划线,并在偏心圆上打样冲眼。
(8)在工件上垫铜皮,使用四爪单动卡盘夹持工件,校正并夹紧工件(923 mm。
(10)粗车和精车内孔,孔口倒角C1(两处)。
项目四车削简单曲轴一、基础知识曲轴是一种偏心零件,在压力机以及内燃机中应用广泛,根据曲轴曲柄颈数量多少的不同,可以分为单拐、双拐、四拐、六拐和八拐等。
典型曲轴的结构1.曲轴的结构单拐曲轴和两拐曲轴为简单曲轴,其毛坯一般采用锻件或者球墨铸铁制造。
双拐曲轴的结构主要包括主轴颈、曲柄颈、曲柄臂以及轴肩等。
曲轴的加工原理与偏心轴和偏心套相似,加工时要确保被加工的曲柄颈轴线与车床主轴轴线重合,其中主轴颈轴线与曲柄颈轴线之间的距离即为偏心距。
双拐曲轴的结构2.曲轴的技术要求对曲轴除了要求较高的尺寸精度、形状和位置精度以及表面质量外,还包括以下要求。
(1)钢质曲轴的毛坯通常采用锻件,以获得致密金属组织和高强度,毛坯还要进行正火或调质等措施,改善毛坯质量。
(2)曲柄轴颈与轴肩的链接圆角必须光洁圆滑,曲轴上不应有压痕、凹坑、拉毛和划伤等现象,以防止应力集中,降低产品寿命。
(3)曲柄精加工完毕后,应该使用超声波或磁性探伤并进行动平衡试验。
(4)主轴颈、曲柄颈的直径尺寸公差等级为IT6;轴颈长度公差等级为IT9~IT10;圆度和圆柱度公差控制在尺寸公差的一半之内。
表面粗糙度为Ra:1.25~0.63 μm。
(5)主轴颈与曲柄颈的平行度为100 mm内不大于0.02 mm,各曲柄颈的位置度不大于±20 mm。
3.曲轴的生产方法曲轴的生产方法根据生产规模的不同而有所差异。
其加工关键技术是解决定位、装夹问题和增加系统刚性问题。
(1)小批生产时,通常采用通用机床和通用夹具,配以必要的少量专用夹具。
(2)成批生产时,仍以通用机床为主,但是较多地使用专用夹具,以提高生产率和保证加工精度。
(3)大量生产时,广泛采用高效专用机床和专用夹具。
4.定位基准的选择(1)为保证各段主轴颈的同轴度,粗基准应选择主轴颈轴线,即以两顶尖为定位基准。
(2)为保证主轴颈与曲柄颈的平行度和位置度,应选择主轴颈为精基准。
5.曲轴的加工工艺(1)简单曲轴的车削方法与较长的偏心轴车削方法基本相同,采用中心孔定位,在两顶尖间装夹。
(2)由于曲轴结构较一般偏心轴复杂,车削时还应采用一定的工艺措施。
(3)如图6-47所示双拐曲轴上有2个曲柄颈,二者互成180°,通常要求两曲柄颈的轴线与主轴颈的轴线平行,两曲柄颈之间的角度误差以及曲柄的偏心距符合设计要求。
(4)曲轴两端的主轴颈尺寸一般较小,不能直接在轴端钻出曲柄颈中心孔,同时曲轴刚度较低,在车削过程中应采取措施提高刚度。
6.使用两顶尖装夹车削曲轴加工曲轴时,在工件主轴颈处预留工艺轴颈,使两端工艺轴颈端面足够大,能钻出主轴颈中心孔和曲柄颈中心孔,一共3组中心孔。
待零件加工完毕后,再车去工艺轴颈。
(1)当两顶尖定在中心孔A上时,可车削外圆。
(2)当两顶尖定在中心孔B1和B2上时,可分别车削2个曲柄颈。
(3)再次以中心孔A为基准,车削主轴颈,最后车去两端的偏心中心孔B1中心孔的应用轴颈的工艺使用7.使用偏心夹板装夹车削曲轴对于两端无法钻中心孔的曲轴,可以在其两端装上圆心偏心夹板,用偏心夹板上的中心孔将曲轴装夹在两顶尖间来车削曲柄颈。
装夹偏心夹板时需要仔细找正.使用偏心夹板装夹曲轴8.增加刚性的措施曲轴刚度低,除了采用粗车、半精车和精车等不同加工阶段以减少因为加工余量大、断续切削引起的冲击、振动对曲轴变形的影响外,为增加加工时的刚度,防止变形,应在曲柄颈对面的空挡处用支承螺钉支承。
9.注意事项(1)在曲轴加工过程中,通常应安排热处理(调制)工序,调制后,应该仔细修研中心孔,才能进行后续车削工作。
(2)车削偏心距较大的曲轴时,应进行静平衡校正。
(3)为提高加工工艺系统的刚度,宜采用硬质合金固定顶尖。
10.曲轴的检测(1)偏心距的检测。
(2)轴颈平行度的检测。
加工如图所示单拐曲轴。