应用韧性断裂准则预测板料的成形极限图
材料的断裂和韧性PPT课件
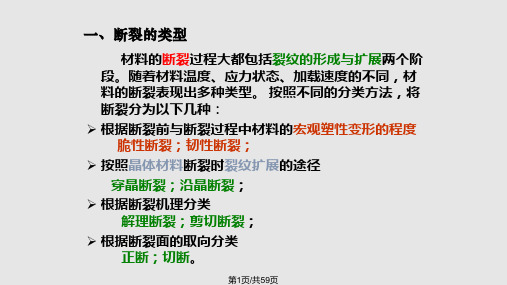
状态有关。其下标表示I型扩展类型,单位为Pa·m1/2。r
为半径向量, 为角坐标。
第30页/共59页
对于裂纹尖端处的一点,即r C,0,于是:
xx yy
KI
2 r
xy 0
(2.12)
在x轴上裂纹尖端的切应力分量为零,拉应力分量最 大,裂纹最易沿x轴方向扩展。
KI Y c KIc (2.14)
当 KI KIc 时,有裂纹,但不会扩展 破损安全
[]
许用应力: []= f / n 或 ys / n f 为断裂强度,ys 为屈服强度,n为安全系数。
缺点
没有抓住断裂的本质,不能防止低应力下的脆性断裂。
第35页/共59页
提出新的设计思想和选材原则,采用一个新的表征材料特征 的临界值:平面应变断裂韧性KIc,它也是一个材料常数,表示 材料抵抗断裂的能力,KIc越高,则断裂应力σc或临界裂纹尺寸 C越大。 根据应力场强度因子K和断裂韧度KIc的相对大小,可以建立裂 纹失稳扩展脆断的断裂K判据,即
一、断裂的类型
材料的断裂过程大都包括裂纹的形成与扩展两个阶 段。随着材料温度、应力状态、加载速度的不同,材 料的断裂表现出多种类型。 按照不同的分类方法,将 断裂分为以下几种: ➢ 根据断裂前与断裂过程中材料的宏观塑性变形的程度
脆性断裂;韧性断裂; ➢ 按照晶体材料断裂时裂纹扩展的途径
穿晶断裂;沿晶断裂; ➢ 根据断裂机理分类
2 r
cos
2
1
sin
2
sin
3
2
xy
KI cos sin cos 3 2 r 2 2 2
ij
KI
2r
一种新的板料成形极限预测判据
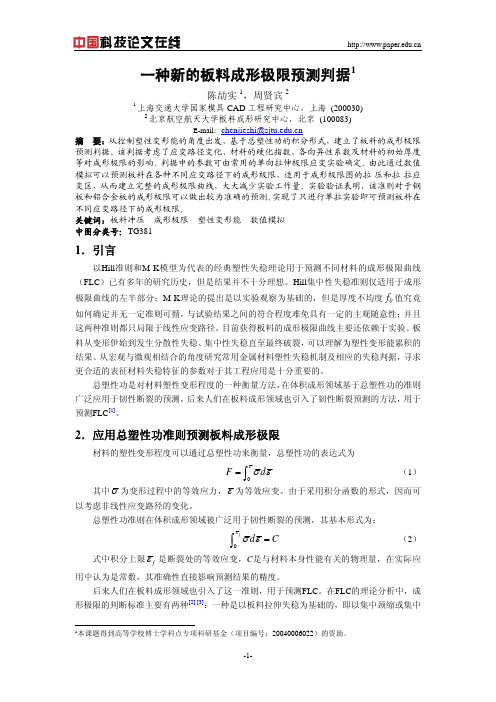
σs
(MPa)
r0
0.72 1.85 0.64
r45
1.21 1.52 0.65
r90
1.03 2.37 0.61
382.8 158.3 155.3
为节省计算时间,根据试件的对称性,只模拟四分之一试件的变形过程(图1) ,板料初 始网格划分为1mm的四边形壳单元。各种应变路径下的加载条件完全相同,板料与凹模以 及压边圈之间的摩擦系数均设为0.12,与凸模之间的摩擦系数为0.05[6],压边力为200kN,凸 模速度为10mm/ms, 模具尺寸与试验设备尺寸相同。 应变路径的变化通过改变试件尺寸来实 现,试件长度均为176mm,宽度从15mm至176mm递增。采用等向强化模型、Barlat89屈服 准则。
∫
εn
0
σ dε = C
(3)
其积分上限 ε n 为与破裂起始部位最接近,但不包含颈缩的椭圆的等效应变。 由于确定与常数C有关的材料参数需要大量的实验数据,而且是统计量,这种预测方法 不便于在工程中应用。在目前的应用中都是采用一些宏观试验数据来确定常数C。 A.M.Goijaerts[4]指出,如果确定常数C的实验加载条件与将要预测的成形过程的加载条件越 相近, 则预测的结果越与实验结果相符。 可是如果用与预测的成形过程完全相同的实验来确 定,这种方法对预测虽然具有很高的精度,但是实验相对很繁琐。目前常用的方法是用拉伸 实验法来确定,通过拉伸试样的极限应变等参数来求得准则中的材料常数。在实际应用中, 通常选取与准则中材料常数个数等同的拉伸变形实验, 并且应力状态不同, 来确定材料常数。 常用的工程方法有:单向拉伸实验,平面应变实验,等双拉实验等。 本文为确定材料常数C,采用了胀形实验中单向拉伸应变路径下的极限应变数据。为了 能够按照材料变形过程中的具体应变路径进行积分,本文采用冲压成形模拟软件Pam-Stamp 进行相同变形过程的数值模拟, 在模拟过程中当试件上第一主应变最大的单元达到此应变值 时,认为此处达到成形极限。然后将此单元的应力应变历史代入公式(3) ,计算材料常数。 采用这种方法确定材料常数的优点是可以按照单元真正的变形路径进行积分, 而不是简单的 假定为线性。 采用NUMISHEET’96[5]中提供的HS钢板、IF钢板和6111-T4铝合金板三种材料的力学性 能参数进行其成形极限实验过程的数值模拟。几种材料的材料力学性能参数见表1。
板料成形中韧性断裂准则应用研究进展

S a g a 0 0 0,Ch n ) h n h i2 0 3 ia
Ab ta t sr c :Thsp p ro e ve dt ep e it n meh d ff r n i i i h e t l o mi g, i a e v r iwe h r dci t o so o mig l t n s e tme a r n o m f whc n l d d f r n i i sr s ig a ,t ema i m o m ig t inn ai ih i cu e o mig l t te sda r m m h x mu f r n hn ig rto,f r n i t o mi g l mi da r m n u tl rc u ec i ra DFC) ig a a d d ci fa t r rt i ( e e .Th n t i p p rp i td o tt a C o l r dc e h s a e on e u h tDF c ud p e it t ef r n i to tls e twihl w lsii l a d me n i a et ec a g f o mi g h o mi gl mi fmea h e t o pa tct wel n a tmet k h h n eo r n y f p t t c o n .W h n a o tn a h i oa c u t n e d p ig FEA o mo e ,DF c u d n to l p l n o ic e n a p t d l C o l o n ya py it n r me t l — a p o c t ul o pe lsi n ls i d ma emo e ,b tt n t p i v re a p o c r a h wi a f lyc u ld ea tca d pa t a g d l u o o ese n e s p r a h. h c To a c r tl r dc o mig l t rt r n t e lc tra e f r n ei s e c si— c u aey p e itf r n i mi ,acie i o r fe tma e ilp ro ma c n e s n ewa n o d s e s be b sd sic e sn h ip n a l e ie n r a i gt eFEA d l c u a y mo e c r c . a Ke r s u t e fa t r rt ra;s e tm ea o mig;fr n i i;f i lm e tme h d ywo d :d ci r cu ec i i l e h e t lfr n o mig l t i t ee n t o m n e
金属塑性成形过程韧性断裂的准则及其数值模拟
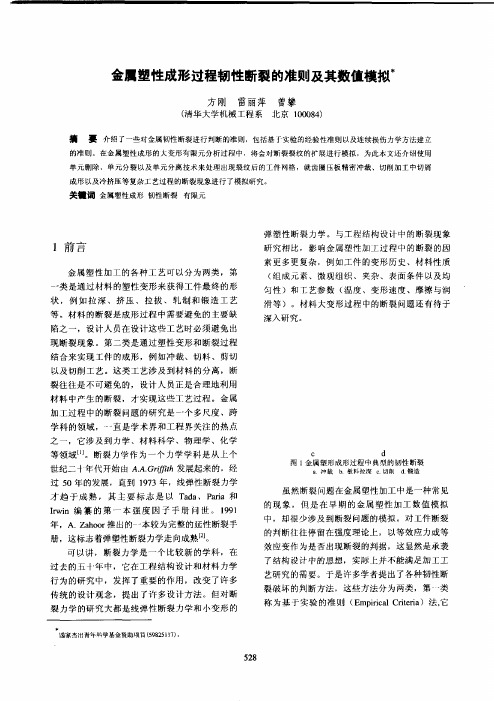
R e r y在1 9 es 9 年提出了三向应力作 i 和Tc l 6 c a ]
用下材料的韧性断裂准则为:
的应用。最后介绍作者对几个典型工艺模拟的结
果。
1 .
2韧性断裂准则
金属在加工过程中发生的断裂大多是韧性断 裂,很少发生脆性断裂。一般认为,金属中的韧
Kc nv 1 8 a a 在 9 年首先提出的另一种分析方 ho 5
法。这种研究方法主要是从细观 ( e s l m s ce oa) 的角度进行研究,对空洞的萌生和扩展角度进
行预测,建立空洞萌生准则。因为韧性断裂的
调整,局部调整还包括单元删除 ( e tn D l o)、 e i
50 3
截
国家杰出青年科学基金资助项目( 851) 5 21 . 9 7
58 2
主要是通过标准的常规实验来获取材料的实验数 据,然后用于对材料成形过程中的韧性断裂的判 断上,它还分二种,即应力、应变和应变能准 则,这类准则的代表是 C cr t a a 准则。 ok fLt m o- h 从所分析的尺度和方法上讲,它属于宏观断裂力 学的范畴。这种方法的缺陷是简单的力学实验条
申
虽然断裂问题在金属塑性加工中是一种常见 的现象,但是在早期的金属塑性加工数值模拟 中,却很少涉及到断裂问题的模拟。对工件断裂 的判断往往停留在强度理论上,以等效应力或等 效应变作为是否出现断裂的判据,这显然是承袭 了结构设计中的思想,实际上并不能满足加工工 艺研究的需要。于是许多学者提出了各种韧性断 裂破坏的判断方法,这些方法分为两类,第 类 称为基于实验的准则 (m i a Cir ) 它 E pi l ea 法, r c r i t
世纪二十年代开始由A .r h .G咖t发展起来的, A 经
成形极限图的测试-应用和可信度分析

1 引言
汽车和摩托车的许多零件如覆盖件 、油箱等都 是用薄钢板冲压成形的 , 在冲压零件的选材和制定 冲压工艺时常常用到成形极限图 。
成形极 限图(Forming Limit Diagrams)也称成 形极限曲线(Forming Limit Curves), 常 用 FL D 或 F LC 表示 。成形极限图是 判断和评定金属薄板成 形性的最为简便和直观的方法 , 是对板材成形性能 的一种定量描述 , 是解决板材冲压问题的一个非常 有效的工具 , 同时也是对冲压工艺成败性的一种判 断曲线 。相对于通常使用的基本成形性能指标(σs , σb 和 δ)及杯突值而言 , 成形极限图可以较好地反
· 498 ·
图 4 成形极限图
图 5 成形极限曲线
说明模拟计算 F LC 具有较高的可信度 。 将极限应 变分布条带的上限连成曲线 , 所得实际测量 F LC 应 变值均大于模拟计算应变值 2 %~ 8 %。 因为实际 测量的极限应变值是板材出现颈缩或破裂附近的应 变 , 在实际使用中不应超过该值 , 所以使用模拟计算 的 F LC 进行冲压零件选材预测是较为安全的 , 模拟 计算 F LC 可以应用于实际分析 。 在使用实际测量 F LC 时 , 如 F LC 为极限应变分布条带的上限 , 选材 预测时应取较大的安全裕度 ;如 F LC 为极限应变分 布条带的平均值 , 选材预测时可取较小的安全裕度 ; 如 F LC 为极限应变分布条带的下限 , 选材预测时所
成形极限图的测试应用和可信度分析形特点的材料性能这是非常重要的问题对多种冷轧钢板的成形极限图进行了测试并与动应变测试分析系统模拟计算的成形极限曲线作了比较应用成形极限图对胀形类和拉深类实物冲压零件进行选材预测对应用成形极限图选材预测的可信度作了分析d0d1胀形状态网格圆的三种畸变状态成形极限图测试原理成形极限图可以用实验测试得到gbt158251995对试验方法作了规定自动应变测试分析系统根据有关的经验公式模拟计算出来实验测试实验测试fl试验时先在试样表面印制标准的圆网格然后将不同宽度的试样分别置于凹模与压边圈之间利用压边力压紧拉深筋以外的试样材料使之不产生材料的流动试样中部在凸模力作用下产生胀形变形并形成凸包见图测量缩颈区或破裂区附近的网格圆长轴和短轴尺寸由此计算金属薄板允许的局部表面极限应变ln100ln100为横向坐标建立表面应变坐标系
韧性断裂PPT课件
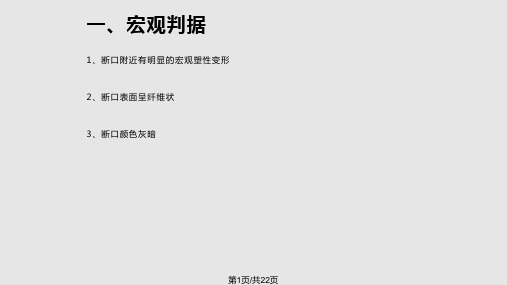
多个微裂纹通过滑移长大、聚集 连接,扩展过程需要消耗大量能 量
宏观:平行于最大剪切应力或垂 直于最大主应力方向 微观:穿晶
通过滑移变形慢速扩展
沿晶分离(可能伴有微量塑性 变形),或沿一定晶面快速劈 开,扩展过程只需要很少能量 宏观:垂直于正应力 微观:沿晶、解理
通过沿晶分离或解理快速扩展
断裂控制因素 应变控制 ε> εf
应力控制 σ> σf
第20页/共22页
项目
断口形态
断口颜色 塑性变形
断裂原因
韧性断裂和脆性断裂的比较
韧性断裂
脆性断裂
宏观:纤维状 微观:蛇形滑移、涟波、延伸、 韧窝
粗糙、灰暗
宏观:放射状(人字纹)、颗粒 状
微观:解理扇形、河流、舌状花 样、沿晶韧窝、岩石状
细瓷状、光亮
伴有大量塑性宏观变形:拉伸— —缩颈,扭转——扭角,冲击— —转角,弯曲——挠度,压缩— —镦粗
2)纤维区是断裂过程中某瞬间的裂纹前沿, 各排纤维的法线方向代表裂纹扩展方向,沿此 方向可以找到冲击力作用点。
3)微观上成撕裂型韧窝,匹配断口上韧窝 弯曲方向相同,且被拉长。
第16页/共22页
4、压缩
1)断口为剪切型。 2)裂纹走向与正应力成45°。 3)微观断口上出现半弧形韧窝,匹配断口 上弯曲方向相反。
过载或强度不足
无宏观塑性变形
材质:白点、分层、夹杂 工艺:过热、过烧、回火脆、焊 接脆、时效脆等 环境:应力腐蚀、氢脆、低温脆 应力:低应力脆断、应力状态过 硬引起的脆断
第21页/共22页
感谢您的观看!
第22页/共22页
不同形状的韧窝 第11页/共22页
无夹杂韧窝
有夹杂韧窝 第12页/共22页
应用韧性断裂准则预测盒形件拉深成形极限

应用韧性断裂准则预测盒形件拉深成形极限
杨玉英;于忠奇;王永志;孙振忠
【期刊名称】《哈尔滨工业大学学报》
【年(卷),期】2004(036)011
【摘要】目前已提出的韧性断裂准则预测板料成形极限,只在简单轴对称件中得到应用.利用作者提出的韧性断裂准则预测了铝合金板LF21,LY21(M)和钢板st17非轴对称的方盒件拉深成形极限,并与成形极限图的预测结果和实验结果进行比较.结果表明,这种方法较好地预测了盒形件拉深成形极限,为预测非轴对称件成形的断裂发生提供了一种有效的方法,也为预测复杂形状零件成形极限奠定了基础.
【总页数】4页(P1507-1510)
【作者】杨玉英;于忠奇;王永志;孙振忠
【作者单位】哈尔滨工业大学,材料科学与工程学院,黑龙江,哈尔滨,150001;哈尔滨工业大学,材料科学与工程学院,黑龙江,哈尔滨,150001;哈尔滨工业大学,材料科学与工程学院,黑龙江,哈尔滨,150001;哈尔滨工业大学,材料科学与工程学院,黑龙江,哈尔滨,150001
【正文语种】中文
【中图分类】TG386
【相关文献】
1.成形极限预测韧性断裂准则及屈服准则的影响 [J], 陈劼实;周贤宾
2.应用专家系统进行盒形件拉深成形极限的分析 [J], 郑晓丹;汪锐;何丹农
3.基于神经网络和遗传算法的板材韧性断裂准则参数优化及成形极限预测 [J], 董国疆;陈志伟;赵长财;李潇逸;杨卓云
4.应用韧性断裂准则预测不同材料的胀形极限 [J], 于忠奇;杨玉英;孙振忠
5.应用韧性断裂准则预测板料的成形极限图 [J], 余心宏;翟妮芝;翟江波
因版权原因,仅展示原文概要,查看原文内容请购买。
abaqus损伤准则总结

abaqus损伤准则总结ABAQUS中有四种初始断裂准则:在⾼应变速率下变形时,有shear failure和tensile failure(旋压⽤不到,不再介绍)对于断裂延性⾦属:可以选⽤A:韧性准则(ductile criteria)和B:剪切准则(shearcriteria)对于缩颈不稳定性可以使⽤(钣⾦):C:FLD、FLSD、M-K以及MSFLD对于铝合⾦、镁合⾦以及⾼强钢在变形过程中会出现不同机制的断裂,可能会将以上准则联合起来进⾏使⽤。
损伤的感念如下图所⽰:1.韧性断裂准则中提供的韧性断裂准则需要输⼊的参数为:1.1ABAQUS断裂应变;应⼒三轴度;应变速率要测量不同应⼒三轴度下的断裂应变需要进⾏⼤量的实验,这是不可取的。
Hooputra et al,2004通过实验和理论推导得到了在定应变速率下,断裂应变和应⼒三轴度的关系:公式中::应⼒三轴度。
即平均应⼒和屈服应⼒的⽐值;为等双轴拉伸时的应⼒三:等双轴拉伸时,断裂时的等效塑性应变,轴度,其值为2/3;为等双轴压缩时的应:等双轴压缩时,断裂时的等效塑性应变,⼒三轴度,其值为-2/3;因此,为了得到断裂时等效塑性应变和应⼒三轴度的关系,只需要求出和参数三个参数即可。
根据⽅程已得到不同应⼒三轴度下的断、裂应变。
、和在⼀个应变速率下只需要三组数据,就可以求出⽅程中的。
帮助⽂件中的建议:ABAQUS==2/3⽅程⼀(是不是:例如在杯突试验中,应⼒三轴度为已知量杯突实验和等双轴拉伸的变形时等效的,杯突实验如何在⾼温下进⾏,能否⽤双向拉伸实验代替?)=此时,通过对进⾏杯突实验的板料印制⽹格,可以得到其成形极限(。
):例如三点弯曲试验中,应⼒三轴度为已知量(印制⽅程⼆=0.57735。
⽹格测量,具体如何测量不是很清楚):例如在单轴拉伸实验中,应⼒三轴度为已知量=0.333⽅程三。
平均应⼒为屈服应⼒的三分之⼀。
SIMUWE论坛中的建议:这个应该通过单轴拉伸实验、压缩实验和纯剪切实验。
板料成形极限理论与实验研究进展
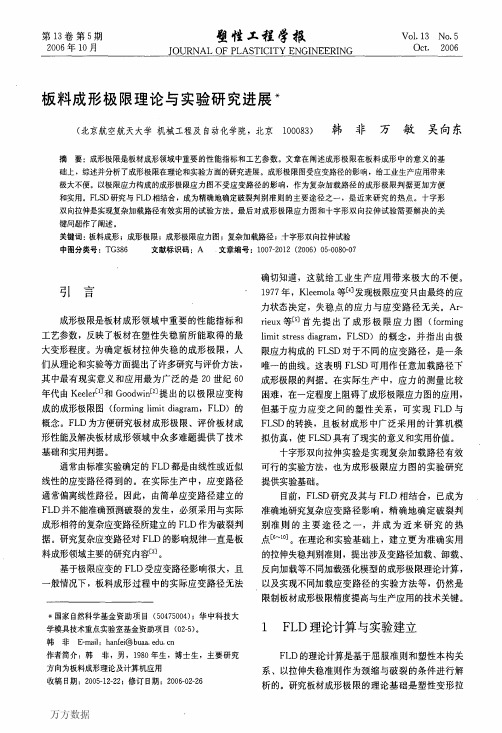
第13卷第5期2006年10月塑性工程学报JOURNALOFPLASTICITYENGINEERINGV01.13No.5Oct.2006板料成形极限理论与实验研究进展*(北京航空航天大学机械工程及自动化学院,北京100083)韩非万敏吴向东摘要:成形极限是板材成形领域中重要的性能指标和工艺参数。
文章在阐述成形极限在板料成形中的意义的基础上,综述并分析了成形极限在理论和实验方面的研究进展。
成形极限图受应变路径的影响,给工业生产应用带来极大不便。
以极限应力构成的成形极限应力图不受应变路径的影响,作为复杂加载路径的成形极限判据更加方便和实用。
FLsD研究与FLD相结合,成为精确地确定破裂判别准则的主要途径之一,是近来研究的热点。
十字形双向拉伸是实现复杂加载路径有效实用的试验方法。
最后对成形极限应力图和十字形双向拉伸试验需要解决的关键问题作了阐述。
关键词:板料成形;成形极限;成形极限应力图;复杂加载路径;十字形双向拉伸试验中图分类号:TG386文献标识码:A文章编号:1007—2012(2006)05—0080一07引言成形极限是板材成形领域中重要的性能指标和工艺参数,反映了板材在塑性失稳前所能取得的最大变形程度。
为确定板材拉伸失稳的成形极限,人们从理论和实验等方面提出了许多研究与评价方法,其中最有现实意义和应用最为广泛的是20世纪60年代由Keelercl]和GOOdwin[2]提出的以极限应变构成的成形极限图(forminglimitdiagram,FLD)的概念。
FLD为方便研究板材成形极限、评价板材成形性能及解决板材成形领域中众多难题提供了技术基础和实用判据。
通常由标准实验确定的FLD都是由线性或近似线性的应变路径得到的。
在实际生产中,应变路径通常偏离线性路径。
因此,由简单应变路径建立的FLD并不能准确预测破裂的发生,必须采用与实际成形相符的复杂应变路径所建立的FLD作为破裂判据。
研究复杂应变路径对FLD的影响规律一直是板料成形领域主要的研究内容[3]。
第7章板料成形性能与成形极限ppt课件

图7-8 网格圆畸变
.
根据测量结果,计算试样表面极限应变。
e1
d1 d0 d0
100
%
e2
d2 d0 d0
100
%
1
ln
d1 d0
ln(1
e1
)
2
ln
d2 d0ຫໍສະໝຸດ ln(1 e2 ).
如图7-9,以表面应变e2(或ε2)为横坐标、表面应变e1〔或ε1〕 为纵坐标,建立表面应变坐标系。在e1-e2坐标系中,习惯将e1 和e2分度比例为1:2,而在ε1-ε2坐标系中两者分度一般相同。 将试验测定表面极限应变量〔e1、e2〕或〔ε1、ε2〕标绘在表 面应变坐标系中。
第7章 板料成形性能与成形极限
.
板料成形性能是指板料对各种成形工 艺的适应能力。
板料成形性能主要包括成形性能、贴 模性能和定形性能。其总体构成所谓综合 成形性能,也叫做广义成形性能。其中成 形性能〔抗破裂性能〕可视为狭义的冲压 成形性能,它是目前生产中作为评定板料 冲压成形性能的主要指标。
.
贴模性能是指板料在冲压成形中取得模具 形状的能力。制件出现折皱、翘曲、塌陷和鼓 起等几何面缺陷均会使贴模性能降低。定形性 能是指制件脱模后保持其在模内既得形状的能 力,故亦称冻结性能。制件出现尺寸误差与形 状误差使定形性降低,回弹是影响板料定形性 的最主要因素。
如图76二维应变坐标系中用不同应变路径下表面极限应变量连成曲线或勾画出条带形区域称为成形极限曲线forminglimitcurve缩写flc极限应变量与极限曲线共同构成成形极限图forminglimitdiagram缩写fld23图76成形极限图fld242成形极限图fld试验将一侧表面制有网格的试样臵于凹模与压边圈之间压紧拉深筋以外的材料试样中部在外力作用下产生变形见图77其表面上的网格圆发生变形当某个局部产生缩颈或破裂时停止试验测量缩颈区或破裂区附近的网格圆长轴和短轴尺寸计算板料允许的局部表面极限主应变量e25图77试验简图26下述两种方法可获得不同应变路径下表面极限主应变
26186212_AA6111-T4铝合金变路径成形极限研究

引言 板料成形过程中的失效是板料成形过程数值模拟的一大挑
战。为了描述金属板料在冲压过程中的最大变形,Goodwin[1] 引入了成形极限曲线(FLC)的思想,它将最大塑性变形设定 在主应变和次应变的空间内。FLC自提出以来,被广泛用于确 定板料成形极限。FLC通常是通过设计用于线性应变路径的实 验来测量的。然而,复杂板料的成形过程和多步成形过程在冲 压过程中会发生剧烈的应变路径变化。实验研究表明,应变路 径的变化对板料的成形性能有很大的影响。Graf和Hosford[2]进 行了AA2008-T4的实验,以研究应变路径变化对成形极限曲线 (FLCs)的影响。一年后,Graf和Hosford[3]分享了他们关于 应变路径变化对AA6111-T4铝合金的FLCs影响的实验结果。 因此,比例应变路径下的FLC实验适用于近似线性应变路径的 板料成形失效预测,但对于复杂形状板料的冲压成形或多步成
图2 单轴拉伸预应变DF2012准则试验与预测FFLC比较
Copyright©博看网. All Rights Reserved.
科学与信息化2021年10月上 111
工业与信息化
TECHNOLOGY AND INFORMATION
平面应变拉伸下预应变的预测效果与图3中的实验结果进 行了比较。首先,应注意的是,即使在相同的应变路径下,单 调加载和卸载再加载的实验断裂应变也有很大的差异。以平面 应变为例,平面应变拉伸下的0.05预应变比单调平面应变拉伸 下的断裂应变提高了约9.4%,如图3所示。平面应变拉伸下的 0.11预应变比单调平面应变拉伸下的断裂应变提高了约26.2%。 这在理论上不能用各向同性硬化来解释。这可归因于合金的退 火或某种损伤恢复。此外,实验结果表明,平面应变拉伸下的 预应变对FFLCs的形状影响不大,DF2012准则的预测结果也表 明了这一点。预测还表明,在平面应变张力作用下,预应变对 FLC左侧的影响可以忽略,但对右侧的FLC影响不大。
5A06铝合金板材热态本构模型及韧性断裂准则

5A06铝合金板材热态本构模型及韧性断裂准则刘康宁;郎利辉;续秋玉【摘要】In order to obtain the formation characteristics of 5A06 aluminium alloy sheets,uniaxial tensile tests were conducted under different conditions. From hot tensile and fracture tests,a modified Misiolek equation was defined that extrapolated the flow stress from the diffuse necking of the metal sheet. By using a radial basis unction (RBF)artificial neural network,a Crockroft-Latham ductile fracture threshold prediction model was also developed. An evaluation of the network compared model results with experimental data. Results show that the material flow stress is very sensitive to temperature and strain rate,and the RBF artificial neural network can predict the ductile fracture threshold with a maximum error of less than 10. 6% .%为了获取材料在不同条件下成形性能指标,对5A06铝合金板材进行了热态单向拉伸试验,结合热态单向拉伸试验和韧性断裂试验结果,提出了一种修正Misiolek模型;利用修正模型的外插性能预测颈缩后板材流变应力,应用径向基函数神经网络算法建立了Cockroft-Latham韧性断裂阈值预测模型,并对该模型进行了预测精度评估.结果表明,流变应力对温度及应变速率敏感,对比径向基函数网络模型预测误差小于10.6%.【期刊名称】《西南交通大学学报》【年(卷),期】2018(053)001【总页数】5页(P214-218)【关键词】铝合金;本构模型;热态;韧性断裂准则;径向基函数网络【作者】刘康宁;郎利辉;续秋玉【作者单位】北京航天发射技术研究所,北京100076;北京航空航天大学机械工程及自动化学院,北京100191;北京航空航天大学机械工程及自动化学院,北京100191;航天材料及工艺研究所,北京100076【正文语种】中文【中图分类】TG146.2轻质合金材料一般在常温下具有较低的塑性,成形性能较差.在热态条件下的成形性大大提高,许多板材的成形技术[1]均利用了这一特点,使复杂结构薄壁类零部件的加工制造变为可能.然而在热态条件下,这类材料力学性能参数、成形极限、断裂阈值受温度、变形速度等多种因素影响,导致材料模型复杂,同时也对轻量化合金热态条件下的韧性断裂评判标准提出了更高要求.准确建立材料在相应条件下力学模型、获取材料在不同变形条件下成形性能指标一直是板材成形过程中工艺分析及工艺优化的关键.韧性断裂是板材塑性加工过程中重要的失效类型[2],多数钣金成形工艺均把韧性断裂作为材料成形极限的重要指标.基于韧性损伤理论的韧性断裂准则是预测板料成形极限指标的有效方法.国内外学者在理论及试验研究基础上提出了多种韧性断裂准则[3-4],其中应用较广的有 Cockroft-Latham 准则[5]、Brozzo 准则[6]及 Oyane 准则[7].这些准则多采用阈值控制的方法,即某处材料超过了一定阈值便认为材料发生断裂.与传统的Swift失稳理论、M-K沟槽理论相比,金属韧性断裂理论可解决具有复杂应力状态及非线性加载历史的塑性成形的断裂失效问题.同时,由于金属韧性断裂模型具有简单、参数求解方便等优点,被广泛应用于成形过程数值仿真分析[8].5A06铝合金是具有代表性的铝镁系防锈铝合金材料[9],因其具有较高的比强度并有良好的耐腐蚀性及焊接性,在航空航天领域应用十分广泛.该材料在常温下塑性较差,加热条件下成形性会有明显改善,其热变形行为较为复杂,对变形条件十分敏感.本文中通过热态单向拉伸试验,获取了不同温度及应变率条件下5A06铝合金板材颈缩前的应力-应变曲线,在对比Misiolek模型基础上,提出了修正Misiolek本构模型,利用热态本构模型外插性能及数值积分法确定不同温度及应变速率条件下的Cockroft-Latham韧性断裂阈值.利用径向基函数人工神经网络算法对5A06-O 板材断裂阈值预测模型进行了训练.在建立的断裂阈值预测模型及热态本构方程基础上,预测了200℃条件下宽板弯曲及热态胀形过程韧性断裂临界条件,并与试验数据进行了对比.1 试验1.1 热态单向拉伸试验试验选择厚度为1.5 mm的5A06-O铝合金板材,其化学成分见表1,表中:wB为质量分数.采用长春试验机研究所CCS-88000电子万能试验机,根据GB/T 4338—2006《金属材料高温拉伸试验方法》,在不同温度(150、200、250、300 ℃)、不同应变率(0.055 00、0.005 50、0.000 55 s-1)条件下进行试件的热态单向拉伸试验.通过对单向拉伸试件印制网格,获取单向拉伸状态下板材破裂处极限应变数据,利用该数据确定断裂阈值.表1 5A06-O铝合金板材化学成分Tab.1 Chemical composition of the 5A06 alloy元素 Mg Si Fe Cu Mn Zn Ti Al wB/% 5.9 0.4 0.4 0.1 0.7 0.20.06 其余单拉试验环境箱采用封闭式整体对流加热,获取共计12组数据,试样在拉伸前保温10 min,计算得到颈缩前应力-塑性应变曲线如图1所示,图中: ε为材料应变率.图1 5A06铝合金板材流动应力-塑性应变曲线Fig.1 Flow stress vs.plastic strain of the 5A06 alloy sheet由图1可以看出,在相同温度条件下,5A06铝合金板材的流变应力随着应变率的增加而增大;低于250℃后,材料变形主要以加工硬化为主,应力-塑性应变曲线近似为幂函数型,随着温度的升高(高于250℃),金属原子热运动加剧,动态回复(再结晶)效应愈加明显,此时软化机制占主导,使材料变形曲线呈现加工软化特点.另外,动态回复(再结晶)过程进行需要一定时间,较低的应变速率可使软化现象更加显著.1.2 热态宽板弯曲及胀形试验本文进行了200℃不同变形速率条件下宽板弯曲试验与胀形试验,其中,宽板弯曲试样长100 mm,两端夹持段宽度50 mm,中间平行段宽度39 mm,平行段与两端过度圆角24 mm;胀形试验内凹模直径100 mm.试验前,通过电化学腐蚀法在试样表面印制直径为2.5 mm网格阵列,以测量破裂时应变.宽板弯曲试验及胀形试验分别在BSC-50AR板材成形试验机及YRJ-50板材充液热胀形-拉深试验机上进行.2 修正Misiolek本构模型金属热态本构关系反映了材料流变应力特征,是材料在热态条件下的重要力学性能,描述了应力随着应变率、温度及变形程度的变化,在制定合理热加工工艺、金属塑性变形理论研究及有限元仿真计算中均起着重要作用[10].在热态变形过程中,5A06铝合金等轻量化合金材料加工硬化、动态回复软化机制相互作用,使流变应力曲线呈现出对温度及应变率的敏感性,增加了预测难度.国内外研究学者对热环境下材料流动应力的研究多基于Arrhenius形式,热激活流动模型或其修正形式[11-13],适用于预测具有饱和应力特征的金属高温流变应力,对于温热条件下如铝合金等轻质合金材料的预测效果并不理想.单拉试验可以较为精确地获取颈缩前的板材应力-应变曲线,板材成形过程一般具有较大的变形量,当计算仿真分析过程中,板材变形程度超过单向拉伸试验中最大均匀变形量时,模拟结果会出现误差.本文通过建立适用于5A06铝合金温热状态本构模型,利用单拉试验中获取不同条件下的流变应力曲线确定模型参数,采用本构模型外插计算方法预测颈缩后材料力学性能的变化规律.对比国内外学者提出的本构模型[14-15],本文选择以Misiolek模型[16]为基础,构造该模型修正形式,以反映温度及应变率对材料流变应力的影响规律.修正Misiolek本构模型如式(1)、(2).式中:(ε0+p)n( ε,T)为幂函数强化项;em( ε,T)p为软化因子;其余物理量含义见文献[16].假定Misiolek模型各参量C、n、m分别与ξ及η呈抛物线关系.对C、n、m值进行非线性高次函数拟合,得到的修正Misiolek本构模型及模型参数如式(3)、(4),式中:M、N、P分别为不同参数的修正系数.修正Misiolek本构模型计算应力与试验数据对比如图1所示.由图1可以发现,修正Misiolek本构模型预测结果与试验应力-应变曲线较为吻合.3 韧性断裂阈值确定采用阈值控制方法确定金属韧性断裂准则,可用于预测非线性加载塑性变形过程断裂失效问题.Crockroft-Latham断裂准则是目前应用较广的韧性断裂准则[17].该准则认为,在不同温度、变形速率条件下,塑性变形最大拉应力是导致材料破坏的主要因素,单位体积拉应力功达到某一临界值时材料便发生断裂.Crockroft-Latham断裂准则所需待定变量较少,参数获取简单,预测精度较高,适用于轻质合金板材热态成形过程断裂性能预测.Crockroft-Latham断裂准则为式中:I为临界断裂应变能;珔εf为断裂发生处的等效应变;σmax为最大拉应力;珔ε为某一时刻的等效塑性应变.本文建立的5A06铝合金热态韧性断裂准则忽略了板材各向异性影响,屈服函数选用各项同性Von-Mises屈服模型及相应等效应变计算公式,利用提出的修正Misiolek本构模型外插延伸性,建立板材颈缩后流变应力曲线,并利用数值积分算法,将式(5)进行梯形积分离散化处理,得利用读数显微镜测取热态单向拉伸试验破裂点周围极限应变数据,将其作为断裂发生处的等效应变珔εf值,将式(3)~(4)代入式(6),得到5A06铝合金不同条件下Cockroft-Latham韧性断裂阈值,如表2所示.由表2可知,5A06铝合金韧性断裂阈值随温度的升高而逐渐降低,与该铝合金材料变形抗力随着温度的变化趋势一致;在低于250℃条件下,断裂阈值随着变形速度的降低而增大,这是因为变形速度越低,材料回复过程越充分,金属晶体缺陷消除程度增大,得到更大的变形量;300℃条件下该趋势与之相反,本文认为与材料在300℃条件下流变应力对变形速度敏感程度较大及应力值较低有关.表2 不同条件下5A06铝合金Crockroft-Latham韧性断裂阈值Tab.2 Crockroft-Latham fracture threshold of the 5A06 Al alloy under variousconditions MPa应变速率/s-1 温度/℃150 200 250 300 0.055 00 76.535 73.423 65.652 65.105 0.005 50 91.979 80.172 71.438 58.668 0.000 55 115.048 90.071 73.938 51.417径向基函数(RBF,radial basis function)神经网络是一种前馈型人工神经网络[18-19],基本思想是利用对中心点径向对称的非负非线性函数作为隐含层单元的“基函数”构成隐含层空间,将输入矢量映射到隐空间,以任意精度全局逼近一个非线性函数.文中利用径向基函数网络算法对5A06板材断裂阈值与变形条件关系模型网络进行了训练,建立的断裂阈值预测模型及热态本构方程,在此基础上预测200℃时,宽板弯曲及热态胀形过程韧性断裂临界条件,并与试验结果对比.典型径向基函数(RBF)神经网络通常具有3层网络结构[20],包括输入层、隐含层、输出层.RBF网络中常用的径向基函数为高斯函数,其激活函数如式(7)所示.用式(7)实现了输入矢量到隐函数空间的非负非线性映射.式中:xp-ci为欧氏范数;ci为隐含层节点中心;xp=(x1p,x2p,…,xNp)为第 p个N 维输入样本;γ 为隐含层节点归一化参数.基于径向基函数网络,由式(8)确定从隐含层空间到输出层空间的线性变换.式中:wij为隐含层到输出层的连接权值;h为隐含层的节点数;yj为与xp对应的第j个输出节点值.编写RBF神经网络模型训练程序,输入表2中的5A06铝合金不同变形条件下韧性断裂阈值,添加必要中间插值节点并归一化后,建立了该材料在150~300 ℃,应变速率在0.055 ~0.000 55 s-1间的Crockroft-Latham断裂阈值预测模型,经过27次迭代训练得到最终训练均方误差,均方误差小于1×10-6.4 试验对比分析利用建立的径向基函数神经网络,结合修正Misiolek本构模型,计算200℃时的不同变形速率、不同变形路径下Crockroft-Latham韧性断裂阈值,结果如图2所示.由图2可知,利用径向基函数网络得到的预测值与试验值较为吻合,其最大误差为10.63%,表明文中建立的韧性断裂准则预测模型能较好地预测5A06铝合金板材不同变形条件下的断裂阈值.图2 预测结果与试验结果对比Fig.2 Comparison between predicted and test results5 结论(1)通过5A06铝合金板材热态下单向拉伸试验发现,该材料应力曲线具有显著的温度敏感性及应变率敏感性特点,在250℃以上时,曲线出现软化趋势.(2)基于单向拉伸试验数据,提出了一种修正Misiolek本构模型,该模型可反映不同温度及应变速率影响下的5A06铝合金板材流变应力特征,模型预测结果与试验曲线较为吻合.(3)利用径向基函数神经网络算法,结合修正Misiolek本构模型,本文建立了5A06板材热态Crockroft-Latham韧性断裂阈值预测模型,结合热态胀形试验及宽板弯曲试验对该神经网络模型实用性进行了验证,对比结果发现,模型预测误差在10.63%内.参考文献:【相关文献】[1] LANG Lihui,LIU Kangning,CAI Gaoshen,et al.A criticalreview on specialforming processes and associated research for lightweight components based on sheet and tube materials[J].Manufacturing Review,2014,1(9):1-20.[2]杨锋平,罗金恒,张华,等.金属延性断裂准则精度的评价[J].塑性工程学报,2011,18(2):103-106.YANG Fengping,LUO Jinheng,ZHANG Hua,et al.Evaluation of ductile fracture criterions[J].Journal of Plasticity Engineering,2011,18(2):103-106.[3]虞松,陈军,阮雪榆.韧性断裂准则的试验与理论研究[J].中国机械工程,2006,17(19):2049-2052.YU Song Y,CHEN Jun,RUAN Xueyu.Experimental and theoretical research on ductile fracture criterion[J].China Mechanical Engineering,2006,17(19):2049-2052.[4]余心宏,翟妮芝,翟江波.应用韧性断裂准则预测板料的成形极限图[J].锻压技术,2007,32(5):44-47.YU Xinhong,ZHAI Nizhi,ZHAI Jiangbo.Prediction of sheet metal forming limit diagram by applying ductile fracture criterion[J].Forging and Stamping Technology,2007,32(5):44-47[5] COCKCROFT M G,LATHAM D J.Ductility and the workability of metals[J].Journal Institute of Metals,1968,96(1):33-39.[6] BROZZO P,DELUKA B,RENDINA R.A new method for the prediction of formability in metal sheets[C]∥Proceedings of the Seventh Biennial Conference on Sheet Metal Forming and Formability.[S.l.]:International Deep Drawing Research Group,1972:18-26. [7] OYANE M,SATO T,OKIMOTO K,et al.Criteria for ductile fracture and their applications[J].Journal of Mechanical Working Technology,1980,4(1):65-81.[8]叶拓,王冠,姚再起,等.汽车用6xxx系铝合金薄壁件的韧性断裂行为[J].中国有色金属学报,2014,24(4):878-887.YE Tuo,WANG Guan,YAO Zaiqi,et al.Ductile fracture behavior of 6xxx aluminum alloy thin-walled components of automobile[J].The Chinese Journal of Nonferrous Metals,2014,24(4):878.[9]张红霞,吴广贺,闫志峰,等.5A06铝合金及其焊接接头的疲劳断裂行为[J].中国有色金属学报,2013,23(2):327-335.ZHANG Hongxia,WU Guanghe,YAN Zhifeng,etal.Fatigue fracture behavior of 5A06 aluminum alloy and its welded joint[J].The Chinese Journal of Nonferrous Metals,2013,23(2):327-335.[10] LIN Yongcheng, CHEN Mingsong, ZHANG Jun.Modeling of flow stress of42CrMo steel under hot compression[J].Materials Science and Engineering:A,2009,499(1):88-92.[11] YIN Fei,HUA Lin,MAO Huajie,et al.Constitutive modeling for flow behavior of GCr15 steel under hot compression experiments[J].Materials and Design,2013,43:393-401.[12] GUPTA AK, ANIRUBHV K, SINGH SK.Constitutive models to predict flow stress in austenitic stainless steel316 atelevated temperatures[J].Materials and Design,2013,43:410-418.[13] PENG Xiaona,GUO Hongzhen,SHI Zhifeng,et al.Constitutive equations forhigh temperature flow stress of TC4-DT alloy incorporating strain,strain rate andtemperature[J].Materials& Design,2013,50(17):198-206.[14] CHABOCHE J L.A review of some plasticity and viscoplasticity constitutive theories [J].International Journal of Plasticity,2008,24(10):1642-1693.[15] GRONOSTAJSKI Z.The constitutive equations for FEM analysis[J]. Journal of Materials Processing Technology,2000,106(1):40-44.[16] MISIOLEK Z, KOWALCZYK J, KASTNER P.Investigation of plastic flow stressesof Zn and its alloys[J].Arch.Hutn,1977,22(1):71-88.[17] FAGERHOLT E,DORUM C,BORVIK T,et al.Experimental and numerical investigation of fracture in a cast aluminum alloy[J].International Journal of Solids and Structures,2010,47(24):3352-3365.[18]缪报通,陈发来.径向基函数神经网络在散乱数据插值中的应用[J].中国科学技术大学学报,2001,31(2):135-142.MIAO Baotong,CHEN Falai.Applications of radius basisfunction neuralnetworks in scattered data interpolation[J].Journal of University of Science and Technology of China,2001,31(2):135-142.[19]王炜,吴耿锋,张博锋,等.径向基函数(RBF)神经网络及其应用[J].地震,2005,25(2):19-25.WANG Wei,WU Gengfeng,ZHANG Bofeng,et al.Neural networks of radial basis function(RBF)and it's application to earthquake prediction[J].Earthquake,2005,25(2):19-25.[20]张晓斌,孙宇,代珊.基于径向基神经网络杯形件拉深成形变压边力预测技术研究[J].机械科学与技术,2007,24(8):36-38.ZHANG Xiaobin,SUN Yu,DAI Shan.A study on the prediction technology of variable blank-holding force for deep drawing forming of cup shaped parts based on radial basis neural network[J].Journal of Machine Design,2007,24(8):36-38.。
数值模拟中应用最小厚度准则预测板料成形极限

数值模拟中应用最小厚度准则预测板料成形极限
陈劼实;周贤宾;刘长丽
【期刊名称】《中国机械工程》
【年(卷),期】2006(000)0S1
【摘要】在数值模拟中应用最小厚度作为成形极限判据,研究最小厚度值与应变路径的关系。
如果对从单向拉伸到双向等拉之间的各种近似线性应变路径均应用相同最小厚度值作为判据,那么得到的极限应变点呈近似线性分布。
对实验数据点与计算点的相对位置关系进行分析,发现两者之间的比值存在着近似指数函数的关系。
对拉-压区和拉-拉区分别采用两段指数函数对最小厚度值进行修正,使其成为与应变路径相关的变量。
采用修正后的最小厚度准则作为数值模拟中极限应变的判据,对ST14钢等三种材料成形极限的预测取得了较好的结果。
【总页数】4页(P)
【作者】陈劼实;周贤宾;刘长丽
【作者单位】北京航空航天大学;北京航空航天大学;北京;100083
【正文语种】中文
【中图分类】TG386
【相关文献】
1.基于Oyane韧性断裂准则的板料成形极限预测 [J], 余心宏;翟妮芝;翟江波
2.晶体塑性模型在体心立方金属板料成形极限计算中的应用 [J], 杨梅;董湘怀
3.板料成形极限的理论预测与数值模拟研究 [J], 陈劼实;周贤宾
4.金属板料单点渐进成形极限的数值模拟预测 [J], 李磊;周晚林;HUSSAING
5.应用韧性断裂准则预测板料的成形极限图 [J], 余心宏;翟妮芝;翟江波
因版权原因,仅展示原文概要,查看原文内容请购买。
成形极限图试验

成形极限图试验成形极限图(FLD)或成形极限曲线(FLC)是板料冲压成形性能发展过程中的较新成果.成形极限图的试验方法如下所述:1)在试验用坯料上制备好坐标网格;2)以一定的加载方式使坯料产生胀形变形,测出试件破裂或失稳时的应变ε1、ε2(长、短轴方向);3)改变坯料尺寸或加载条件,重复2)项试验,测得另一状态下的ε1、ε2;4)取得一定量的数值后,在平面坐标图上描绘出各试验点,然后圆滑连线,作出FLD.成形极限曲线将整个图形分成如1所示的三部分:安全区、破裂区及临界区.图1 成形极限图及其用法于大型复杂薄板冲压件成形时,凹模内毛坯产生破裂的情况较多.这一部分毛坯一般是在拉应力作用下成形的,变形区内产生的断裂是延性断裂.掌握板材拉伸失稳理论,利用成形极限图,可以对这种破坏问题较快地作出判断,找出原因,提出相应的解决办法.拉伸失稳理论是计算建立成形极限图的基础.拉伸失稳是指在拉应力作用下,材料在板平面方向内失去了塑性变形稳定性而产生缩颈,并随这发生破裂.拉伸失稳可分为分散失稳和集中失稳两种.分散性失稳是指板料的塑性变形达到一定程度后,变形开始出现在材料内某些性能不均匀或厚度不均匀的部位,载荷开始随变形程度增大而减小,由于应变硬化,这些缩颈能在一定的尺寸范围内转移,使材料在这个范围内产生一种亚稳定的塑性流动,故载荷下降比较缓慢.但由于材料的硬化增强,变形抗力又有所提高,最后,最薄弱的环节逐渐显示出来,缩颈就逐步集中到某一狭窄区段,这样就逐渐形成了集中失稳.产生集中失稳时,缩颈点也不能再转移出去,此时金属产生不稳定流动,由于这时承载面急剧减小,变形;力也就急剧下降,很快就异致破坏.成形极限是指材料不发生塑性失稳破坏时的极限应变值.但由于目前失稳理论的计算值还不能准确反映实际冲压成形中毛坯的变形极限,在实际生产中普遍应用由实验得到的成形极限图.成形极限图(FLD),也称成形极限线(FLC)是对板材成形性能的一种定量描述,同时也是对冲压工艺成败性的一种判断曲线.它比用总体成形极限参数,如胀形系数、翻边系数等来判断是否能成形更为方便而准确. 成形极限图(FLD)是板材在不同应变路径下的局部失稳极限应变和(相对应变)或和(真实应变)构成的条带形区域或曲线(图1-14).它全面反映了板材在单向和双向拉应力作用下的局部成形极限.在板材成形中,板平面内的两主应变的任意组合,只要落在成形极限图中的成形极限曲线上,板材变形时就会产生破裂;反之则是安全.图1-14中的条带形区域称为界区,变形如位于临界区,表明此处板材有濒临于破裂的危险.由此可见,FLD是判断和评定板材成形性能的最为简便和直观的方法,是解决板材冲压成形问题的一个非常有效的工具.图1-14 成形极限图(FLD)一、成形极限图(FLD)的制作目前,试验确定板材成形极限图的方法是:在毛坯(试样)表面预先作出一定形状的风格.冲压成形后,观察、测定网格尺寸的变化量,经过计算,即可得到网格所在位置的应变.对变形区内各点网格尺寸的变化进行测量与计算,可得到应变的分布.网格图形如图1-15所示.图1-16是采用圆形网格,在变形网格变成椭圆形状,椭圆的长、短轴方向就是主轴方向,主应变数值为相应应变:长轴应变:短轴应变:真实应变:长轴应变:短轴应变:图1-15 常用网络形式a) 圆形网络b) 组合网络c) 叠加网络图1-16 网络的变形二、FLD在生产中的应用成形极限图与应变分析网格法结合在一起.可以分析解决许多生产实际问题.这种方法用于分析解决问题的原理是:首先通过试验方法获得研究零件所用板材的成形极限图.再将网格系统制作在研究零件的毛坯表面划变形危险区,坯料成形为零件后,测定其网格的变化量,计算出应变值.将应变值标注在所用材料的成形极限图上.这时零件的变形危险区域便可准确加以判断.成形极限图的应用大致有以下几方面:1)解决冲模调试中的破裂问题:2)判断所设计工艺过程的安全裕度,选用合适的冲压材料;3)可用于冲压成形过程的监视和寻找故障.FLD应用举例:为消除破裂指出应采取的工艺措施.将汽车覆盖件上某一危险部位的应变值标注到所用材料的成形极限图上(图1-17).如果覆盖件上危险部位的应变位于B处,要增加其安全,由图中看出:应减小或增大,最好兼而有之.减小需降低椭圆长轴方向的流动阻力,还可以采用在方向减小坯料尺寸,增大模具圆角半径,改善其润滑条件等方法来实现.如要增加,需增加椭圆短轴方向的流动阻力,实现的方法是在这一方向上增加坯料尺寸,减小模具圆角,在垂直于短轴方向设置拉深肋等.若覆盖件危险部位的应变位于D处,要增加其安全性,可以减小或减小的代数着手,应注意的是,减小的代数值应减小短轴方向的流动阻力.通过上述分析可见,汽车覆盖件成形中,对其成形质量影响较大的工艺参数是:模具圆角半径、坯料形状和尺寸、压边力、润滑状态等,成形工艺设计的优劣,在很大程度上取决于合理选择这些工艺参数,成形极限图提供了合理选择和优化工艺参数的途径.图1-17 用FLD预见危险性图 3.0.1 各种常见弯曲件3.1 弯曲变形过程及变形特点< 弯曲变形过程>在压力机上采用压弯模具对板料进行压弯是弯曲工艺中运用最多的方法.弯曲变形的过程一般经历弹性弯曲变形、弹-塑性弯曲变形、塑性弯曲变形三个阶段.现以常见的V 形件弯曲为例,如图3.1.1 所示.板料从平面弯曲成一定角度和形状,其变形过程是围绕着弯曲圆角区域展开的,弯曲圆角区域为主要变形区.弯曲开始时,模具的凸、凹模分别与板料在 A 、B 处相接触. 设凸模在 A 处施加的弯曲力为 2F (见图 3.1.1 a ).这时在 B 处(凹模与板料的接触支点则产生反作用力并与弯曲力构成弯曲力矩M = F·(L 1 /2),使板料产生弯曲.在弯曲的开始阶段,弯曲圆角半径r很大,弯曲力矩很小,仅引起材料的弹性弯曲变形.图3.1.1 弯曲过程随着凸模进入凹模深度的增大,凹模与板料的接触处位置发生变化,支点 B 沿凹模斜面不断下移,弯曲力臂 L 逐渐减小,即 L n < L 3 < L 2 < L 1 . 同时弯曲圆角半径 r 亦逐渐减小,即 r n < r 3 < r 2 < r 1 ,板料的弯曲变形程度进一步加大.弯曲变形程度可以用相对弯曲半径 r/t表示,t为板料的厚度. r/t 越小,表明弯曲变形程度越大.一般认为当相对弯曲半径r/t>200时,弯曲区材料即开始进入弹-塑性弯曲阶段,毛坯变形区内(弯曲半径发生变化的部分)料厚的内外表面首先开始出现塑性变形,随后塑性变形向毛坯内部扩展.在弹-塑性弯曲变形过程中,促使材料变形的弯曲力矩逐渐增大,弯曲力臂L继续减小,弯曲力则不断加大.凸模继续下行,当相对弯曲半径 r/t<200时,变形由弹 -塑性弯曲逐渐过渡到塑性变形.这时弯曲圆角变形区内弹性变形部分所占比例已经很小,可以忽略不计,视板料截面都已进入塑性变形状态.最终,B 点以上部分在与凸模的V形斜面接触后被反向弯曲,再与凹模斜面逐渐靠紧,直至板料与凸、凹模完全贴紧.若弯曲终了时,凸模与板料、凹模三者贴合后凸模不再下压,称为自由弯曲.若凸模再下压,对板料再增加一定的压力,则称为校正弯曲,这时弯曲力将急剧上升. 校正弯曲与自由弯曲的凸模下止点位置是不同的,校正弯曲使弯曲件在下止点受到刚性镦压,减小了工件的回弹(进一步论述见本章第 3.2.2节).< 板料弯曲的塑性变形特点>为了观察板料弯曲时的金属流动情况,便于分析材料的变形特点,可以采用在弯曲前的板料侧表面设置正方形网格的方法.通常用机械刻线或照相腐蚀制作网格,然后用工具显微镜观察测量弯曲前后网格的尺寸和形状变化情况,如图 3.1.2a〕所示.弯曲前,材料侧面线条均为直线 , 组成大小一致的正方形小格,纵向网格线长度aa =bb.弯曲后,通过观察网格形状的变化,(如图 3.1.2b 所示)可以看出弯曲变形具有以下特点:图3.1.2 弯曲变形分析一.弯曲圆角部分是弯曲变形的主要区域可以观察到位于弯曲圆角部分的网格发生了显著的变化,原来的正方形网格变成了扇形.靠近圆角部分的直边有少量变形,而其余直边部分的网格仍保持原状,没有变形.说明弯曲变形的区域主要发生在弯曲圆角部分.二.弯曲变形区内的中性层在弯曲圆角变形区内,板料内侧(靠近凸模一侧)的纵向网格线长度缩短,愈靠近内侧愈短.比较弯曲前后相应位置的网格线长度,可以看出圆弧为最短,远小于弯曲前的直线长度,说明内侧材料受压缩.而板料外侧(靠近凹模一侧)的纵向网格线长度伸长,愈靠近外侧愈长.最外侧的圆弧长度为最长,明显大于弯曲前的直线长度,说明外侧材料受到拉伸.从板料弯曲外侧纵向网格线长度的伸长过渡到内侧长度的缩短,长度是逐渐改变的.由于材料的连续性,在伸长和缩短两个变形区域之间,其中必定有一层金属纤维材料的长度在弯曲前后保持不变,这一金属层称为应变中性层(见图 3-3 中的 O-O 层). 应变中性层长度的确定是今后进行弯曲件毛坯展开尺寸计算的重要依据.当弯曲变形程度很小时,应变中性层的位置基本上处于材料厚度的中心,但当弯曲变形程度较大时,可以发现应变中性层向材料内侧移动,变形量愈大,内移量愈大 .三.变形区材料厚度变薄的现象弯曲变形程度较大时,变形区外侧材料受拉伸长,使得厚度方向的材料减薄;变形区内侧材料受压,使得厚度方向的材料增厚.由于应变中性层位置的内移,外侧的减薄区域随之扩大,内侧的增厚区域逐渐缩小,外侧的减薄量大于内侧的增厚量,因此使弯曲变形区的材料厚度变薄. 变形程度愈大,变薄现象愈严重.变薄后的厚度t′ =ηt,(η是变薄系数,根据实验测定,η值总是小于 1 ).四.变形区横断面的变形板料的相对宽度 b/t ( b 是板料的宽度, t 是板料的厚度)对弯曲变形区的材料变形有很大影响.一般将相对宽度 b/t >3 的板料称为宽板,相对宽度b/t ≤ 3 的称为窄板.窄板弯曲时,宽度方向的变形不受约束.由于弯曲变形区外侧材料受拉引起板料宽度方向收缩,内侧材料受压引起板料宽度方向增厚,其横断面形状变成了外窄内宽的扇形(见图 3-4a ).变形区横断面形状尺寸发生改变称为畸变.宽板弯曲时,在宽度方向的变形会受到相邻部分材料的制约,材料不易流动,因此其横断面形状变化较小,仅在两端会出现少量变形(见图 3-4b ),由于相对于宽度尺寸而言数值较小,横断面形状基本保持为矩形. 虽然宽板弯曲仅存在少量畸变,但是在某些弯曲件生产场合,如铰链加工制造,需要两个宽板弯曲件的配合时,这种畸变可能会影响产品的质量.当弯曲件质量要求高时,上述畸变可以采取在变形部位预做圆弧切口的方法加以防止.<>板料塑性弯曲时,变形区内的应力和应变状态取决于弯曲变形程度以及弯曲毛坯的相对宽度 b/t.如图3-5所示,取材料的微小立方单元体表述弯曲变形区的应力和应变状态, σθ、εθ表示切向 (纵向、长度方向) 应力、应变,σ r 、ε r 表示径向(厚度方向)的应力、应变,σ b 、ε b 表示宽度方向的应力、应变.从图中可以看出,对于宽板弯曲或窄板弯曲,变形区的应力和应变状态在切向和径向是完全相同的,仅在宽度方向有所不同.图 3.1.3 自由弯曲时的应力应变状态一. 应力状态在切向:外侧材料受拉,切向应力σθ为正;内侧材料受压,切向应力σθ为负. 切向应力为绝对值最大的主应力.外侧拉应力与内侧压应力间的分界层称为应力中性层,当弯曲变形程度很大时也有向内侧移动的特性.应变中性层的内移总是滞后于应力中性层,这是由于应力中性层的内移,使外侧拉应力区域不断向内侧压应力区域扩展,原中性层内侧附近的材料层由压缩变形转变为拉伸变形,从而造成了应变中性层的内移.在径向:由于变形区各层金属间的相互挤压作用,内侧、外侧同为受压,径向应力σr 均为负值. 在径向压应力σr 的作用下,切向应力σθ的分布性质产生了显著的变化,外侧拉应力的数值小于内侧区域的压应力.只有使拉应力区域扩大,压应力区域减小,才能重新保持弯曲时的静力平衡条件,因此应力中性层必将内移相对弯曲半径 r/t越小,径向压应力σ r 对应力中性层内移的作用越显著.在宽度方向:窄板弯曲时,由于材料在宽度方向的变形不受约束,因此内、外侧的应力均接近于零. 宽板弯曲时,在宽度方向材料流动受阻、变形困难,结果在弯曲变形区外侧产生阻止材料沿宽度方向收缩的拉应力,σ b 为正,而在变形区内侧产生阻止材料沿宽度方向增宽的压应力,σ b 为负.由于窄板弯曲和宽板弯曲在板宽方向变形的不同,所以窄板弯曲的应力状态是平面的,宽板弯曲的应力状态是立体的.二.应变状态在切向:外侧材料受拉,切向应变εθ为正,内侧材料受压缩,切向应变εθ为负,切向应变εθ为绝对值最大的主应变.在径向:根据塑性变形体积不变条件条件:εθ + εr + ε b = 0 ,εr 、ε b 必定和最大的切向应变εθ符号相反.因为弯曲变形区外侧的切向主应变εθ为拉应变,所以外侧的径向应变εr为压应变;而变形区内侧的切向主应变εθ为压应变,所以内侧的径向应变ε r为拉应变.在宽度方向:窄板弯曲时,由于材料在宽度方向上可自由变形,所以变形区外侧应变ε b 为压应变;而变形区内侧应变ε b 为拉应变.宽板弯曲时,因材料流动受阻,弯曲后板宽基本不变.故内外侧沿宽度方向的应变几乎为零(ε b ≈ 0),仅在两端有少量应变.综上所述,可以认为窄板弯曲的应变状态是立体的,而宽板弯曲的应变状态是平面的.图3.1.4 板料弯曲后的翘曲由于宽板弯曲时,沿宽度方向上的变形区外侧为拉应力(σ b 为正);内侧为压应力(σ b 为负),在弯曲过程中,这两个拉压相反的应力在弯曲件宽度方向(即横断面方向)会形成力矩 MB.弯曲结束后外加力去除,在宽度方向将引起与力矩 MB方向相反的弯曲形变,即弓形翘曲(如图3-6所示).对于弯曲宽度相对很大的细长件或宽度在板厚10倍以下的弯曲件,横断面上的翘曲十分明显,应采用工艺措施予以解决(见本章第 3.4.1节图3-48) .。
成形极限预测韧性断裂准则及屈服准则的影响
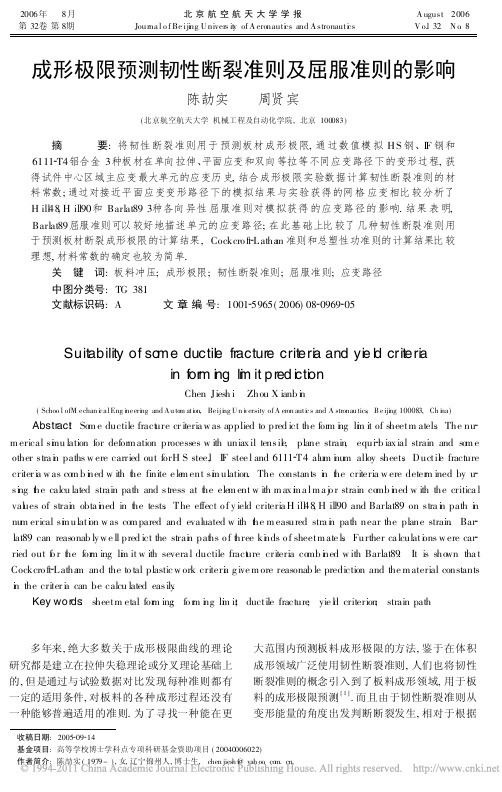
( 北京航空航天大学 机械工程及自动化学院, 北京 100083 )
摘
要: 将韧性 断裂准则用于 预测板材成形 极限, 通 过数值模 拟 H S 钢、IF 钢和
6111 T4铝合金 3种板材在单向拉伸、平面应变和双向等拉等不同应变路径下的变形过程, 获
得试件中心区域主应变最大单元的应变历史, 结合成形极限实验数据计算韧性断裂准则的材
理想, 材料常数的确定也较为简单.
关 键 词: 板料冲压; 成形极限; 韧性断裂准则; 屈服准则; 应变路径
中图分类号: TG 381
文献标识码: A
文 章 编 号: 1001 5965( 2006) 08 0969 05
Suitability of some ductile fracture criteria and yie ld criteria in form ing lmi it pred iction
2006年 8月 第 32卷 第 8期
北京航空航天大学学报 Journa l o f Be ijing U nivers ity of A eronautics and A stronautics
A ugust 2006 V o.l 32 N o 8
成形极限预测韧性断裂准则及屈服准则的影响
陈劼实 周贤宾
图 1 数 值模拟中建立的模型
第 8期
陈劼实等 : 成形极限预测韧性断裂准则及屈服准则的影响
97 1
边圈之间的摩擦系数为 0. 12, 与凸模之间的摩擦 系数 为 0. 05, 压边 力为 200 kN, 凸 模速度 为 10 mm /m s. 应变路径的变化通过改变试件尺寸来实 现, 试件长度为 176mm, 宽 度从 15~ 176mm 递 增.
成形极限图的原理及应用
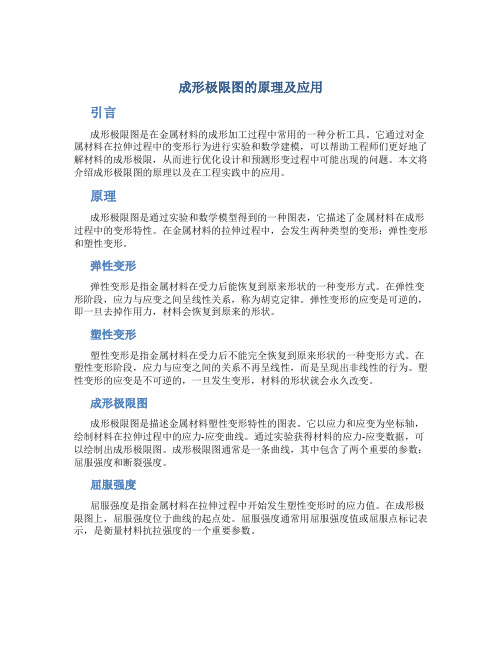
成形极限图的原理及应用引言成形极限图是在金属材料的成形加工过程中常用的一种分析工具。
它通过对金属材料在拉伸过程中的变形行为进行实验和数学建模,可以帮助工程师们更好地了解材料的成形极限,从而进行优化设计和预测形变过程中可能出现的问题。
本文将介绍成形极限图的原理以及在工程实践中的应用。
原理成形极限图是通过实验和数学模型得到的一种图表,它描述了金属材料在成形过程中的变形特性。
在金属材料的拉伸过程中,会发生两种类型的变形:弹性变形和塑性变形。
弹性变形弹性变形是指金属材料在受力后能恢复到原来形状的一种变形方式。
在弹性变形阶段,应力与应变之间呈线性关系,称为胡克定律。
弹性变形的应变是可逆的,即一旦去掉作用力,材料会恢复到原来的形状。
塑性变形塑性变形是指金属材料在受力后不能完全恢复到原来形状的一种变形方式。
在塑性变形阶段,应力与应变之间的关系不再呈线性,而是呈现出非线性的行为。
塑性变形的应变是不可逆的,一旦发生变形,材料的形状就会永久改变。
成形极限图成形极限图是描述金属材料塑性变形特性的图表。
它以应力和应变为坐标轴,绘制材料在拉伸过程中的应力-应变曲线。
通过实验获得材料的应力-应变数据,可以绘制出成形极限图。
成形极限图通常是一条曲线,其中包含了两个重要的参数:屈服强度和断裂强度。
屈服强度屈服强度是指金属材料在拉伸过程中开始发生塑性变形时的应力值。
在成形极限图上,屈服强度位于曲线的起点处。
屈服强度通常用屈服强度值或屈服点标记表示,是衡量材料抗拉强度的一个重要参数。
断裂强度断裂强度是指金属材料在拉伸过程中完全断裂时的应力值。
在成形极限图上,断裂强度位于曲线的终点处。
断裂强度是衡量材料脆性和韧性的一个重要指标,一般来说,断裂强度越高,材料的韧性越好。
应用成形极限图在工程实践中有着广泛的应用。
以下列举了几个常见的应用领域:1.材料选择与优化:通过绘制成形极限图,工程师们可以比较不同材料的成形性能,选择最合适的材料进行工程设计。
成形极限图-钢铁百科

成形极限图(forming Iimit diagram)由金属薄板在各种应变状态时所能达到的极限应变值所构成的图形,简称FLD。
它用来表示金属薄板在出现局部变薄(失稳或颈缩)和断裂之前可能达到的变形水平。
(见薄板成形性)极限应变值可采用板成形网格测量技术实际测定或通过理论计算得到。
通过实验,求得一种材料在各种应力应变状态下的成形极限点,然后把这些点标注到以对数应变ε1和ε2(或工程应变e1,e2)为坐标轴的直角坐标系中,即可得到实验成形极限图(图1)。
由于影响因素很多,判据不一,实验成形极限图数据比较分散,常形成一定宽度的条带,称为临界区。
在临界区以上为破裂区,在临界区以下为安全区。
图1 实验成形极限图Ⅰ-安全区;Ⅱ-临界区;Ⅲ-破裂区板材的硬化指数n、塑性应变比r值、厚度、应变路径、应变梯度、应变速率和网格测量方法等对成形极限曲线的形状和位置都有很大影响。
(1)板材n、r值的影响。
n值增加时,材料的强化效应大,会提高应变分布的均匀性,因而使成形极限曲线提高。
图2是根据M-K理论(见拉伸失稳)计算的结果。
根据M-K理论计算,r值增大时,拉一拉区的极限应变值降低。
但皮尔斯(R.Pearce)的试验结果显示,除了平面应变状态以外,r值对成形极限曲线影响不太显著,但可看出r值下降,极限应变值也下降。
图2 n值对成形极限曲线的影响(2)板材厚度的影响。
实验和理论分析的结果都表明,成形极限曲线随着初始板材厚度的减薄而降低。
这是因为当初始板厚较薄时,由板材的表面缺陷而产生的板厚不均匀性以及内部缺陷而使实际板厚下降,变形不均等问题比板厚较厚时更加严重。
因此,在相同变形条件下,薄的板材容易先发生局部失稳并达到成形极限。
另外,薄的板材在变形时应变梯度小,周围材料对危险区材料的补偿作用小,也会降低成形极限。
(3)应变路径的影响。
在多工序板材成形或单工序复杂零件成形时,零件上点的应变轨迹不一定再遵循简单加载定律,因而由简单加载条件得到的成形极限曲线就不一定能直接使用。
基于LEMAITRE损伤理论的韧性断裂准则建立及板料成形极限预测论文奋斗篇1217
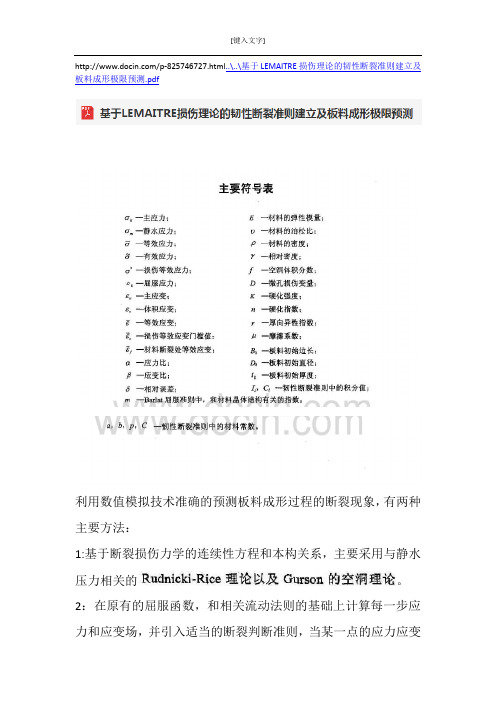
/p-825746727.html..\..\基于LEMAITRE损伤理论的韧性断裂准则建立及板料成形极限预测.pdf
利用数值模拟技术准确的预测板料成形过程的断裂现象,有两种
主要方法:
1:基于断裂损伤力学的连续性方程和本构关系,主要采用与静水
压力相关的。
2:在原有的屈服函数,和相关流动法则的基础上计算每一步应力和应变场,并引入适当的断裂判断准则,当某一点的应力应变
关系满足断裂准则时,即认为断裂产生
问题:关键在于提出准确的断裂准则,目前断裂的方法很多,如成形极限图(FLD)成形极限应力图(FLSD)最大变薄率,应变率突变准则,厚度梯度准则以及韧性断裂准则(DFC)
当前,在板料成形有限元模拟技术中,应用FLD是预测断裂发生的主要方法。
板料成形极限的预测方法及其研究进展
常见的方法:极限应力法:成形极限图:
极限应变常采用的是成形极限图
下表为几种成形极限的理论研究:
众多FLD的理论研究中,极限的判断标准有两种:
1:以板料拉伸失稳为基础,以颈缩出现作为成形极限(局部缩颈,对于塑性差的如铝合金镁合金就不行了,还有就是缩颈不明显的)2:以断裂出现作为成形极限。
建立在损伤力学的基础上。
(测量极限
应变比前者困难)
FLD不能预测从单拉到双拉的所有变形路径的成形极限,只是适合其他一部分,
最大变薄率:
对于有明显的缩颈的板料来说是可以的
目前韧性断裂建立在损伤思想基础上,可以分为两类:
韧性断裂准则:
韧性断裂的物理机制:
McClintock以损伤思想为背景导出如下公式:
国内::??。
- 1、下载文档前请自行甄别文档内容的完整性,平台不提供额外的编辑、内容补充、找答案等附加服务。
- 2、"仅部分预览"的文档,不可在线预览部分如存在完整性等问题,可反馈申请退款(可完整预览的文档不适用该条件!)。
- 3、如文档侵犯您的权益,请联系客服反馈,我们会尽快为您处理(人工客服工作时间:9:00-18:30)。
F( y - z ) 2 + G( z - x ) 2 + H ( x - y) 2 +
2L
2 yz
+
ቤተ መጻሕፍቲ ባይዱ
2M
2 zx
+
2N
2 xy
-
1=
0
( 7)
式中 x 、 y 、 z # # # 拉伸屈服应力 ( MP a)
xy 、 yz 、 z x # # # 剪切屈服应力 ( M Pa)
F、G、H 、L 、M、N # ## 与屈服应力有关
比值 在整个单向拉伸和平面拉伸测试的过程中可
1
分别表示为:
3 韧性断裂准则及材料常数的确定
引入韧性断裂准则要解决两个问题: 准则的结 构及其常数的确定, 它们直接影响预测和分析结果 的正确性。
冲压时板料变形区处于三向压应力状态, 材料 在狭窄的凸、凹模间隙附近形成了局部的塑性剪切
m = 1 2( 2+ r ) = 2( 2 + r ) ( 单向拉伸) ( 5)
- 应变曲线。两种材料的应力- 应变可分别描述为:
A 5182 O : = 570( 0 0011+ ) 0 21
( 1)
M ild st eel: = 625( 0 0069 + ) 0 23 ( 2)
式中 # # # 等效应力 ( MP a)
# # # 等效应变
表 1 材料拉伸性能
Table 1 Tensile properties of the materials
的异性参数
图 2 各向异性系数对单向拉伸和平面拉伸 应力、应变比的影响
Fig 2 Ef fect of normal anis ot ropy param et er on t he st ress an d st rain rat io of uniaxial t ensil e and plan st rain s tr et chin g
YU Xin hong, ZHAI Ni zhi, ZHAI Jiang bo ( Department of M at erials Science and Eng ineering , N or thwestern P olytechnical U niver sity, Xi an 710072, China)
成形极限图的实验确定方法根据试件受力方式 的不同主要分为两种, 如图 1 所示。一种是使用圆 柱型扁平冲头深拉延的 平板面法![ 5] ( 图 1a) ; 另 一种 是 使用 半 球 型冲 头 胀 形 的 曲 面 法![ 6] ( 图 1b) , 但后者比前者应用更 加广泛。本文 尝试用实 验和模拟相结合的方法获得 F L D, 先通过实验测得 相关的材料参数, 再用软件 EAT / dy naf orm 模拟半 球型冲头胀形 实验, 得到随 时间历史变化 的应力、 应变值, 代入韧性断裂准则找出破裂点, 绘制 F LD 图。
∃f 1+ a m d = C 0
( 3)
2 材料本构关系
测试材料为铝合金板 A5182 O 和 SPCC, 厚度
d= 1 0 m m。表 1 是这两种材料标准单向拉伸测试
测得的材料性能参数, 其值为与扎制方向成 0∀、45∀、
90∀三个方向的平均值。其中强度系数 F、屈服应力
s 、应变硬化指数 n 用来描述材料本构关系, 即应力
带, 经历了弹塑性变形、剧烈的塑性变形和韧性断 裂。从微观角度来说, 材料在大变形下会出现损伤, 伴随着微观空穴的长大和聚合, 直至许多空穴聚集 在一起产生裂纹, 引起韧性断裂。所以, 韧性断裂 准则 也 既 是 一 种 损 伤 断 裂 准 则。 M c Clint ock、 Cockcrof t 和 L atham、Br ozzo 等人都提出了损伤断 裂准则[ 7] , 但这些准则均未考虑金属大变形的影响, 在实际应用中有较大局限性。Oy ane 等[ 8] 考虑到静 水应力可以抑制或加速韧性破坏, 不仅能定量地表 示瞬时的损伤状态, 更体现了加载过程中整个应力 - 应变历史对材料的劣化效应。假定韧性损伤达到 一定值时破裂发生, 提 出了 ( 3) 式 的 Oy ane 损伤 断裂准则, 应用较 广的是其 整化的 ( 4) 式 Oy ane 韧性断裂准则, 本文也 用的是 ( 4) 式 Oy ane 韧性 断裂准则进行成形极限图的预测。
第 32 卷 第 5 期 V ol 32 N o 5
锻压技术
FORGING & STAMPING TECHNOLOGY
2007 年 10 月 Oct. 2007
应用韧性断裂准则预测板料的成形极限图
余心宏* , 翟妮芝, 翟江波
( 西北工业大学 材料科学与工 程学院, 陕西 西安 710072)
摘要: 将 O yan 韧性断裂准则引入数值模拟预 测板料 的成形极 限图 ( FL D) 。讨论了 各向异 性系数 对不同 应变状 态
杨氏 材料 模量/
GP a A5182 O 69 6
强度 系数/ MPa 570
应变硬 各向异 屈服强 拉伸
化指数 性系数 度 s/ 强度/
n
r
MPa MPa
0 21 0 93 135 285
延伸 率/ %
21 9
S PCC 207 625 0 23 1 17 199 346 36 6
∃f m + C1 d = C2 0
( 4)
式中 f # # # 断裂发生处的等效应变 m # # # 静水应力 ( MP a)
C # # # 裂纹出现时的临界损伤值
a、C1 、C2 # # # 材料常数
材料常数至少需要两种应变条件下的破裂应变
才能确定。表 2 是单向拉伸和平面拉伸实验的颈缩 部位测得的断裂应变[ 3, 5] 。
表 2 材料 的断裂应变
Abstract: T o predict the form ing limit diag rams ( FL D) of sheet metals, Oyan ductile fracture crit er io n w as intr oduced into numerical simulatio n. T he inf luence o f nor mal aniso tro pic coefficient on the item in different str ains of the cr iterion w ere discussed and mater ial constants in the cr iterion w ere o btained by testing the fr actur e str ains of uniax ial t ensile and plan str ain st retching . T he fo rming limit w as predicted in t he male punch bulging t est by substituting the v alues o f stress and strain o f every time step o bt ained fro m numer ical simulation into ductile fracture cr iter ion. O yan ductile fractur e cr iterion was applied to predict the FL D of A 5182 O and SP CC. T he results indicate t hat the combinat ion o f ductile fracture cr iterion and numer ical simulat ion can successfully predict the form ing limit diag ram o f sheet metals. Keywords: for ming limit diag ram; duct ile fr act ur e criter ion; numer ical simulation
第5期
余心宏等: 应用韧性断裂准则预测板料的成形极限图
45
图 1 成形极限图实验装置 ( a) In plane 测试装置 ( b) O ut of plane 测试装置 Fig 1 Ex perim ent equipm ent of form ing l imit diagrams ( a) In plane t est ing equipment ( b) Out of plane t esting equipment
图。
关键词: 成形极限图; 韧性断裂准则; 数值模拟
中图分类号: TG386 41
文献标识码: A
文章编号: 1000 3940 ( 2007) 05 0044 04
Predicti on of sheet metal forming limi t diagram by applying ductile fracture criterion
1 引言
板料冲压成形过程是一个涉及材料非线性、几 何非线 性 和 复 杂 接 触 摩 擦状 况 的 大 变 形 力 学 过 程[ 1, 2] , 其变形的复杂 性使得断裂等 板料失效的准 确预测变的困难。断裂预测最常用的是 20 世纪 60 年 代 Keeler 和 Backof en 提 出 的 成 形 极 限 图 ( F L D) 。但想要得到各种板料的成形极限图, 靠人 工实验工作重、耗时长、耗材多、花费高, 且应变 路径是 近 线 性, 与 实 际 生 产 差 异 较 大。 传 统 的 Sw ift 、H il l、M K 沟槽! 以及 S R 理论模型虽然 是板材成形极限预测的有效工具, 但都不能准确预 测塑性差、破裂时无明显颈缩现象的铝合金板。因 此, 需要一种合适的成形极限准则正确分析成形过 程, 而源自于韧性损伤理论的韧性断裂准则正是预 测板料成形极限的一种有效方法。各国学者在各种 假设的基础上已提出多种韧性断裂准则, 其中应用