IMU-FSAS Datasheet(中文)
FSA221中文资料

© 2006 Fairchild Semiconductor Corporation FSA221 Rev. 1.0.3
2
元器件交易网
FSA221 USB2.0 High-Speed and Audio Switches with Negative Signal Capability
Vbus ASel Vaudio D+ R DL
Figure 1. FSA221 Analog Symbol
Switch Select Control Circuitry Rpd
GND
D+/R
D-/L
© 2006 Fairchild Semiconductor Corporation FSA221 Rev. 1.0.3
元器件交易网
Click here for this datasheet translated into Chinese!
FSA221 USB2.0 High-Speed and Audio Switches with Negative Signal Capability
November 2006
FSA221 USB2.0 High-Speed (480Mbps) and Audio Switches with Negative Signal Capability
Features
HS-USB: 4Ω Typical On Resistance Audio: 3Ω Typical On Resistance -3db Bandwidth: > 720MHz Low Power Consumption Packaged in Pb-free 10-Lead MicroPak™ (1.6 x 2.1mm), 10-pin MSOP (Preliminary) Power-off Protection on Common D+/R, D-/L Ports Automatically Detects Vbus for Switch Path Selection D+/R, D-/L Ports: 8pf Typical On Capacitance
FSA644UCX-datasheet
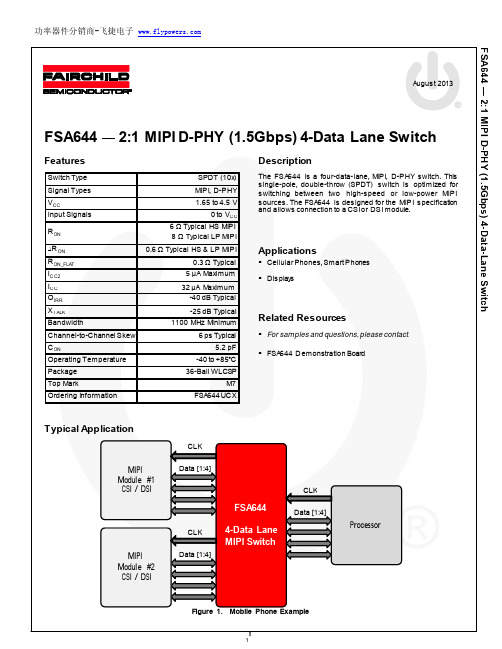
Applications
Cellular Phones, Smart Phones Displays
Related Resources
For samples and questions, please contact: FSA644 D emonstration Board
Typical Application
(1) (1)
Min.
-0.50 -0.50 -50 50 -65
Max.
+5.25 VCC 5.25
Unit
V -0.5 V mA mA
IIK IOUT
Voltage
T ST G
+150 3.5 3.5 8.0 1.5 8.0 3.5 15.0
° C
ESD
Charged Device Model, JEDEC: JESD22-C 101 IEC 61000-4-2 System Contact
Symbol
VCC VCNT RL (/OE) V V
SW
Parameter
Supply Voltage DC Input Voltage DC Switch I/O DC Output Current Storage Temperature Human Body Model, JEDEC: JESD22-A114 All Pins I/O to GND 3.5 Power to GND DC Input Diode Current
kV
Air Gap 15.0 Note: 1. The input and output negative ratings may be exceeded if the input and output diode current ratings are observed.
BC447;BC447G;BC449;BC449A;BC449AG;中文规格书,Datasheet资料

100 70 50
−5.0 V VCE = −1.0 V
30 −1.0
−2.0 −3.0 −5.0 −7.0 −10 −20 −30 −50 −70 −100 IC, COLLECTOR CURRENT (mA)
Figure 1. Current−Gain — Bandwidth Product
Figure 3. Switching Times
IC , COLLECTOR CURRENT (mA)
−1.0 k −700 −500
−300 −200
−100 −70 −50
−30 −20
−10 −1.0
CURRENT LIMIT
THERMAL LIMIT
SECOND BREAKDOWN LIMIT
VCEO
Vdc
80
100
Collector-Base Voltage BC447 BC449, BC449A
VCBO
Vdc
80
100
Emitter-Base Voltage
Collector Current − Continuous
Total Device Dissipation @ TA = 25°C Derate above 25°C
IC =
IC =
100 mA 200 mA
0.8
0.4
TJ = 25°C
0 0.02 0.05 0.1
0.2 0.5 1.0 2.0 IB, BASE CURRENT (mA)
5.0 10 20
Figure 7. Collector Saturation Region
RqVB , TEMPERATURE COEFFICIENT (mV/° C)
赛米控丹佛斯电子 SEMiX604GB176HDs 数据表

SEMiX ®4sTrench IGBT ModulesSEMiX604GB176HDsFeatures•Homogeneous Si•Trench = Trenchgate technology •V CE(sat) with positive temperature coefficient•UL recognised file no. E63532Typical Applications*•AC inverter drives •UPS•Electronic weldersAbsolute Maximum Ratings SymbolConditions Values UnitIGBT V CES 1700V I C T j =150°CT c =25°C 567A T c =80°C402A I Cnom 400A I CRMI CRM = 2xI Cnom 800A V GES -20...20V t psc V CC =1000V V GE ≤ 20V V CES ≤ 1700VT j =125°C10µs T j-55...150°C Inverse diode I F T j =150°CT c =25°C 740A T c =80°C 496A I Fnom400A I FRM I FRM = 2xI Fnom800A I FSM t p =10ms, sin 180°, T j =25°C2700A T j -40 (150)°C Module I t(RMS)T terminal =80°C600A T stg -40...125°C V isolAC sinus 50Hz, t =1min4000VCharacteristics SymbolConditions min.typ.max.UnitIGBT V CE(sat)I C =400A V GE =15V chiplevelT j =25°C 2 2.45V T j =125°C 2.5 2.9V V CE0T j =25°C 1 1.2V T j =125°C0.9 1.1V r CE V GE =15VT j =25°C 2.5 3.1m ΩT j =125°C3.94.5m ΩV GE(th)V GE =V CE , I C =16mA5.25.86.4V I CES V GE =0V V CE =1700V T j =25°C 0.124mA T j =125°C mA C ies V CE =25V V GE =0Vf =1MHz 35.3nF C oes f =1MHz 1.46nF C res f =1MHz1.17nF Q G V GE =- 8 V...+ 15 V 3732nC R Gint T j =25°C 1.88Ωt d(on)V CC =1200V I C =400A V GE =±15V R G on =3ΩR G off =3ΩT j =125°C 360ns t r T j =125°C 65ns E on T j =125°C 215mJ t d(off)T j =125°C 900ns t f T j =125°C 165ns E off T j =125°C165mJ R th(j-c)per IGBT 0.058K/WCharacteristics SymbolConditionsmin.typ.max.UnitInverse diodeV F = V EC I F =400AV GE =0V chipT j =25°C 1.5 1.70V T j =125°C 1.4 1.6V V F0T j =25°C 0.9 1.1 1.3V T j =125°C0.70.9 1.1V r FT j =25°C 1.0 1.0 1.0m ΩT j =125°C1.31.3 1.3m ΩI RRM I F =400A di/dt off =6600A/µs V GE =-15VV CC =1200VT j =125°C 560A Q rr T j=125°C131µC E rr T j =125°C 95mJR th(j-c)per diode0.081K/WModule L CE 22nH R CC'+EE'res., terminal-chip T C =25°C 0.7m ΩT C =125°C1m ΩR th(c-s)per module 0.03K/W M s to heat sink (M5)35Nm M tto terminals (M6)2.55Nm Nmw400gTemperatur Sensor R 100T c =100°C (R 25=5 k Ω)493 ± 5%ΩB 100/125R (T)=R 100exp[B 100/125(1/T-1/T 100)]; T[K];3550 ±2%K SEMiX ® 4sTrench IGBT ModulesSEMiX604GB176HDsFeatures•Homogeneous Si•Trench = Trenchgate technology •V CE(sat) with positive temperature coefficient•UL recognised file no. E63532Typical Applications*•AC inverter drives •UPS•Electronic weldersFig. 1: Typ. output characteristic, inclusive R CC'+ EE'Fig. 2: Rated current vs. temperature I C = f (T C )Fig. 3: Typ. turn-on /-off energy = f (I C )Fig. 4: Typ. turn-on /-off energy = f (R G )Fig. 5: Typ. transfer characteristic Fig. 6: Typ. gate charge characteristicFig. 7: Typ. switching times vs. I C Fig. 8: Typ. switching times vs. gate resistor R GFig. 9: Typ. transient thermal impedance Fig. 10: Typ. CAL diode forward charact., incl. R CC'+EE'Fig. 11: Typ. CAL diode peak reverse recovery current Fig. 12: Typ. CAL diode recovery chargeThis is an electrostatic discharge sensitive device (ESDS), international standard IEC 60747-1, Chapter IX* The specifications of our components may not be considered as an assurance of component characteristics. Components have to be tested for the respective application. Adjustments may be necessary. The use of SEMIKRON products in life support appliances and systems is subject to prior specification and written approval by SEMIKRON. We therefore strongly recommend prior consultation of our staff.spring configuration。
赛米控丹佛斯 配置IGBT M7芯片 SEMITRANS 3 SKM600GB12M7 数据表

Absolute Maximum Ratings Symbol Conditions Values UnitIGBT V CES T j = 25 °C 1200 V I C T j = 175 °CT c = 25 °C 779 A T c = 80 °C591 A I Cnom 600 A I CRM1200 A V GES -20 (20)V t psc V CC = 800 V V GE ≤ 15 V V CES ≤ 1200 VT j = 150 °C8 μs T j-40 (175)°C Inverse diode V RRM T j = 25 °C 1200V I FT j = 175 °CT c = 25 °C 688A T c = 80 °C513 A I FRM 1200A I FSM t p = 10 ms, sin 180°, T j = 25 °C3240A T j-40 ... 175°C Module I t(RMS)500 A T stg module without TIM-40 ... 125 °C V isolAC sinus 50 Hz, t = 1 min4000VCharacteristics Symbol Conditions min. typ. max. UnitIGBT V CE(sat)I C = 600 A V GE = 15 V chiplevel T j = 25 °C 1.55 1.88V T j = 150 °C 1.80 V V CE0chiplevel T j = 25 °C 0.87 0.95 V T j = 150 °C 0.76 V r CE V GE = 15 V chiplevelT j = 25 °C 1.13 1.55 mΩ T j = 150 °C1.73 mΩ V GE(th)V CE = 10 V, I C = 60 mA5.46 6.6 V I CES V GE = 0 V, V CE = 1200 V, T j = 25 °C5 mA C ies V CE = 10 V V GE = 0 Vf = 1 MHz120 nF C oes f = 1 MHz 3.66 nF C res f = 1 MHz1.28 nF Q G V GE = - 8V ... + 15 V 5360 nC R Gint T j = 25 °C 0.8 Ω t d(on)V CC = 600 V I C = 600 AV GE =+15/-15V R Gon = 1.2 Ω R Goff = 1 Ωdi/dt on = 8000 A/µs di/dt off = 5240 A/µs dv/dt = 5960 V/µs T j = 150 °C 260 ns t r T j = 150 °C 85 ns E on T j = 150 °C 57 mJ t d(off)T j = 150 °C 436 ns t f T j = 150 °C 95 ns E off T j = 150 °C68mJ R th(j-c)per IGBT0.066K/W R th(c-s)per IGBT, P12 (reference)0.037 K/W R th(c-s)per IGBT, HP-PCM0.02K/WIGBT M7 ModulesSKM600GB12M7Features*∙V CE(sat) with positive temperature coefficient∙ High overload capability∙ Low loss, high density IGBTs ∙ Fast & soft switching inverse CAL diodes∙ Large clearance (10 mm) and creepage distance (20 mm)∙ Insulated copper baseplate using DCB Technology (Direct Copper Bonding)∙ With integrated gate resistorTypical Applications∙ AC inverter drives ∙ UPS∙ Renewable energy systemsRemarks∙Max case temperature limited to T c = T S =125°C∙ Product reliability results are valid for T j = 150°C (recommended T j ,op = -40...+150 °C)∙For storage and case temperature with TIM see document: ″Technical Explanations Thermal Interface materials″GBSEMITRANS ® 3Characteristics Symbol Conditions min. typ. max. UnitInverse diode V F = V EC I F = 600 A V GE = 0 V chiplevel T j = 25 °C 2.14 2.46V T j = 150 °C 2.07 V V F0chiplevel T j = 25 °C 1.30 1.50 V T j = 150 °C 0.90 V r F chiplevelT j = 25 °C 1.40 1.60 mΩ T j = 150 °C1.95 mΩ I RRM V CC = 600 V I F = 600 AV GE = -15 Vdi/dt off = 8000 A/µs T j = 150 °C 555 A Q rr T j = 150 °C92 µC E rr T j = 150 °C 43mJ R th(j-c)per diode0.09K/W R th(c-s)per diode, P12 (reference) 0.038 K/W R th(c-s)per diode, HP-PCM0.021 K/W Module L CE 15nH R CC'+EE'measured per switchT j = 25 °C 0.55mΩ T j = 150 °C0.85 mΩ R th(c-s)1calculated without thermal coupling, P12 (reference)0.0093 K/W R th(c-s)2including thermal coupling,T s underneath module, P12 (reference)0.015 K/W R th(c-s)2including thermal coupling,T s underneath module, HP-PCM 0.0078K/W M s to heat sink M635 Nm M t to terminal M52.55 Nm -Nm w325 gSEMITRANS ® 3 IGBT M7 ModulesSKM600GB12M7Features*∙V CE(sat) with positive temperature coefficient∙ High overload capability∙ Low loss, high density IGBTs ∙ Fast & soft switching inverse CAL diodes∙ Large clearance (10 mm) and creepage distance (20 mm)∙ Insulated copper baseplate using DCB Technology (Direct Copper Bonding)∙ With integrated gate resistorTypical Applications∙ AC inverter drives ∙ UPS∙ Renewable energy systemsRemarks∙Max case temperature limited to T c = T S =125°C∙ Product reliability results are valid for T j = 150°C (recommended T j ,op = -40...+150 °C)∙For storage and case temperature with TIM see document: ″Technical Explanations Thermal Interface materials″GBFig. 1: Typ. output characteristic, inclusive R CC'+ EE'Fig. 2: Rated current vs. temperature I C = f (T C )Fig. 3: Typ. turn-on /-off energy = f (I C ) Fig. 4: Typ. turn-on /-off energy = f (R G )Fig. 5: Typ. transfer characteristic Fig. 6: Typ. gate charge characteristicFig. 7: Typ. switching times vs. I C Fig. 8: Typ. switching times vs. gate resistor R GFig. 9: Transient thermal impedance Fig. 10: Typ. CAL diode forward charact., incl. R CC'+ EE'Fig. 11: CAL diode peak reverse recovery current Fig. 12: Typ. CAL diode peak reverse recovery chargePinout and DimensionsGBThis is an electrostatic discharge sensitive device (ESDS) according to international standard IEC 61340.*IMPORTANT INFORMATION AND WARNINGSThe specifications of SEMIKRON products may not be considered as any guarantee or assurance of product characteristics ("Beschaffenheitsgarantie"). The specifications of SEMIKRON products describe only the usual characteristics of SEMIKRON products to be expected in typical applications, which may still vary depending on the specific application. Therefore, products must be tested for the respective application in advance. Resulting from this, application adjustments of any kind may be necessary. Any user of SEMIKRON products is responsible for the safety of their applications embedding SEMIKRON products and must take adequate safety measures to prevent the applications from causing any physical injury, fire or other problem, also if any SEMIKRON product becomes faulty. Any user is responsible for making sure that the application design and realization are compliant with all laws, regulations, norms and standards applicable to the scope of application. Unless otherwise explicitly approved by SEMIKRON in a written document signed by authorized representatives of SEMIKRON, SEMIKRON products may not be used in any applications where a failure of the product or any consequences of the use thereof can reasonably be expected to result in personal injury. No representation or warranty is given and no liability is assumed with respect to the accuracy, completeness and/or use of any information herein, including without limitation, warranties of non-infringement of intellectual property rights of any third party. SEMIKRON does not convey any license under its or a third party’s patent rights, copyrights, trade secrets or other intellectual property rights, neither does it make any representation or warranty of non-infringement of intellectual property rights of any third party which may arise from a user’s applications. Due to technical requirements our products may contain dangerous substances. For information on the types in question please contact the nearest SEMIKRON sales office. This document supersedes and replaces all previous SEMIKRON information of comparable content and scope. SEMIKRON may update and/or revise this document at any time.。
unched-5650 RF Analog Signal Generator 数据手册说明书

SPECIFICA TIONSPXI-56501.3 GHz RF Analog Signal GeneratorContents Definitions (2)Conditions (2)Frequency (2)Frequency Settling Time (3)Reference Clock (3)Internal Clock (3)Internal Reference Output (REF IN/OUT connector) (3)External Reference Input (REF IN/OUT connector) (4)Spectral Purity (4)Harmonics (5)Nonharmonics (6)Amplitude (7)Power Level Accuracy (8)Amplitude Settling Time (9)Signal-to-Noise Ratio (9)V oltage Standing Wave Ratio (VSWR) (9)Reverse Power Handling (10)Modulation (10)Frequency Modulation (FM) (10)Frequency Shift Keying (FSK) (11)On-Off Keying (OOK) (12)DC Power Requirements (14)Calibration (14)Physical Dimensions (14)Environment (15)Operating Environment (15)Storage Environment (15)Shock and Vibration (15)Compliance and Certifications (16)Safety (16)Electromagnetic Compatibility (16)CE Compliance (16)Online Product Certification (17)Environmental Management (17)DefinitionsWarranted specifications describe the performance of a model under stated operating conditions and are covered by the model warranty.The following characteristic specifications describe values that are relevant to the use of the model under stated operating conditions but are not covered by the model warranty.•Typical specifications describe the performance met by a majority of models.•Nominal specifications describe an attribute that is based on design, conformance testing, or supplemental testing.Specifications are Warranted unless otherwise noted.ConditionsMinimum or maximum warranted specifications are valid under the following conditions unless otherwise noted.•30 minutes warm-up time•Calibration cycle maintained•Temperature of 0 °C to 55 °CTypical specifications are valid under the following condition unless otherwise noted.•Over ambient temperature ranges of 23 °C ± 5 °CFrequencyRange1500 kHz to 1.3 GHzResolution<3 HzAccuracy Refer to the Reference Clock section.1Tunable down to 100 kHz with amplitude uncalibrated.2| | PXI-5650 SpecificationsFrequency Settling Time2Reference ClockInternal ClockInitial accuracy±3 ppm, maximumTemperature (15 ºC to 35 ºC)±1 ppm, maximumAging±5 ppm per year, maximumInternal Reference Output (REF IN/OUT connector) Frequency10 MHzAmplitude 1 V pk-pk into 50 ΩCoupling ACOutput impedance50 Ω2The frequency settling time specification includes only frequency settling and excludes anyresidual amplitude settling that may occur as the result of a large frequency change.3Frequency steps that span the full range of a voltage-controlled oscillator (VCO) require moresettling time than steps that remain close together within one VCO or steps that switch betweenVCOs. The maximum specification covers this worst-case frequency settling time.PXI-5650 Specifications| © National Instruments| 3External Reference Input (REF IN/OUT connector) Frequency10 MHz ±10 ppmAmplitude0.2 V pk-pk to 1.5 V pk-pk into 50 ΩInput impedance50 ΩLock time to external reference<1 sSpectral Purity4<0.8 Hz RMS, typicalResidual FM, 1 GHz (300 Hz to 3 kHz,RMS)Jitter5 (seconds, RMS), 622 MHz with<200 fs, typical1 kHz to 5 MHz jitter bandwidth4Wide loop bandwidth has very similar phase noise performance at 10 kHz offset, but this noiselevel extends to approximately 300 kHz offset before it starts rolling down at approximately 20 dB per decade until it reaches the far out noise density.5Measured at 0 dBm output power.4| | PXI-5650 SpecificationsFigure 1. Measured Phase Noise at 500 MHz and 1 GHz (0 dBm Output Power)d B c /H zFrequency Offset (Hz)Harmonics500 kHz to <1.3 GHz (0 dBm to -40 dBm output power)-15 dBc, typicalFigure 2. Typical Spectrum at 1.3 GHzP o w e r (d B m )Frequency (Hz)400 M 800 M 1.2 G 1.6 G 2 G 2.4 G –40–20–10–30–80–50–60–70500 k2.7 G0–90PXI-5650 Specifications | © National Instruments | 5Figure 3. T ypical Second Harmonic (HD 2) and Third Harmonic (HD 3) Levels (0 dBmOutput Power)H a r m o n i c L e v e l (d B C )Frequency (Hz)NonharmonicsNarrow Loop BandwidthTable 4. Nonharmonic Products at 0 dBm to -20 dBm Output Power6 | | PXI-5650 SpecificationsWide Loop BandwidthNot applicable6Subharmonic products 500 kHz to1.3 GHzAmplitudeResolution<0.1 dBMaximum available power 2 dB above maximum specified amplitude,typicalMinimum available power10 dB below minimum specified amplitude,typical6No harmonic multiplication in this band.PXI-5650 Specifications| © National Instruments| 7Figure 4. Measured Maximum Available PowerP o w e r (d B m )Frequency (Hz)400 M 600 M 800 M 200 M 1 G 1.2 G 1.3 G81214106422018160500 kPower Level Accuracy8 | | PXI-5650 SpecificationsFigure 5. Typical Power Accuracy, -40 dBm to 0 dBm, 5 dB Steps1.0–1.0–0.50.00.501 GFrequency (Hz)E r r o r (d B )1.3 G0.5 GAmplitude Settling Time0.05 dB of final value <500 ms, typical 0.25 dB of final value<10 ms, typicalSignal-to-Noise Ratio≥0 dBm output power<-140 dBc/Hz, typicalVoltage Standing Wave Ratio (VSWR)500 kHz to 1.3 GHz <1.8:1, typical Output impedance50 ΩPXI-5650 Specifications | © National Instruments | 9Figure 6. Measured VSWRFrequency (Hz)V S W RReverse Power HandlingRF 0.5 watts, +27 dBm 7DC25 voltsModulationFrequency Modulation (FM)Modulation waveform types Sine, triangle, square External modulation sourceNot supportedTable 8.FM T ypical Maximum Deviation7If the requested output power is less than -3 dBm, the RF reverse power handling is +15 dBm for signals ≤10 MHz.10 | | PXI-5650 SpecificationsModulation waveform frequency 1 Hz to 100 kHzCharacteristic deviation accuracy8<±3.5%Typical distortion8<0.1%SINAD8>65 dBFrequency Shift Keying (FSK)Modulation waveform typesPRBS5-order to 31-orderUser-defined Up to 1,022 bitModulation format2-FSKTable 9. FSK T ypical Maximum Deviation8 1 kHz sine wave, 10% of maximum deviation; noise bandwidth of 10 kHz.PXI-5650 Specifications| © National Instruments| 11FSK characteristic deviation accuracy (100 kHz rate, 10% of maximum deviation)<±10%Symbol ratePRBS 763 Hz to 100 kHz User-defined 763 Hz to 100 kHz Pulse shapingNot supportedFigure 7. FSK Modulation Eye Diagram, 1.0 GHz Carrier, 100 kHz Symbol Rate,500 kHz Deviation, Ninth-Order PRBS750 k 500 k 250 k0–250 k –500 k –750 k10 µ20 µ30 µ40 µ50 µTime (sec)F r e q u e n c y (H z )On-Off Keying (OOK)Modulation waveform typesPRBS 5-order to 31-order User-definedUp to 1,024 bit12 | | PXI-5650 SpecificationsTable 10. OOK T ypical AmplitudeSymbol ratePRBS 153 Hz to 100 kHz User-defined 153 Hz to 100 kHz Pulse shapingNot supportedFigure 8. OOK Diagram, 1.0 GHz Carrier, 100 kHz Symbol Rate, Ninth-Order PRBSP o w e r L e v e l (d B m )100–20–40–6050 µ100 µ150 µ200 µTime (sec)PXI-5650 Specifications | © National Instruments | 13Figure 9. OOK Diagram, 1.0 GHz Carrier, 200 kHz Symbol Rate, Ninth-Order PRBSP o w e r L e v e l (d B m )100–20–10–40–30–50–6050 µ100 µ150 µ200 µTime (sec)DC Power RequirementsCalibrationInterval1 yearPhysical DimensionsPXI-5650 module3U, one slot, PXI module 2.0 cm × 13.0 cm × 21.6 cm (0.8 in. × 5.1 in. × 8.5 in.)Weight415 g (14.6 oz)14 | | PXI-5650 SpecificationsEnvironmentMaximum altitude2,000 m (800 mbar) (at 25 °C ambienttemperature)Pollution Degree2Indoor use only.Operating EnvironmentAmbient temperature range0 °C to 55 °C (Tested in accordance withIEC 60068-2-1 and IEC 60068-2-2. MeetsMIL-PRF-28800F Class 3 low temperaturelimit and MIL-PRF-28800F Class 2 hightemperature limit.)Relative humidity range10% to 90%, noncondensing (Tested inaccordance with IEC 60068-2-56.) Storage EnvironmentAmbient temperature range-40 °C to 70 °C (Tested in accordance withIEC 60062-2-1 and IEC 60068-2-2.) Relative humidity range5% to 95%, noncondensing (Tested inaccordance with IEC 60068-2-56.)Shock and VibrationNonoperational shock30 g peak, half-sine, 11 ms pulse (Tested inaccordance with IEC 60068-2-27. Test profiledeveloped in accordance withMIL-PRF-28800F.)Random vibration nonoperating 5 Hz to 500 Hz, 2.4 g rms (Tested in accordancewith IEC 60068-2-64. Nonoperating testprofile exceeds the requirements ofMIL-PRF-28800F, Class 3.)PXI-5650 Specifications| © National Instruments| 15Compliance and CertificationsSafetyThis product is designed to meet the requirements of the following electrical equipment safety standards for measurement, control, and laboratory use:•IEC 61010-1, EN 61010-1•UL 61010-1, CSA C22.2 No. 61010-1Note For UL and other safety certifications, refer to the product label or the OnlineProduct Certification section.Electromagnetic CompatibilityThis product meets the requirements of the following EMC standards for electrical equipment for measurement, control, and laboratory use:•EN 61326-1 (IEC 61326-1): Class A emissions; Basic immunity•EN 55011 (CISPR 11): Group 1, Class A emissions•EN 55022 (CISPR 22): Class A emissions•EN 55024 (CISPR 24): Immunity•AS/NZS CISPR 11: Group 1, Class A emissions•AS/NZS CISPR 22: Class A emissions•FCC 47 CFR Part 15B: Class A emissions•ICES-001: Class A emissionsNote In the United States (per FCC 47 CFR), Class A equipment is intended foruse in commercial, light-industrial, and heavy-industrial locations. In Europe,Canada, Australia, and New Zealand (per CISPR 11), Class A equipment is intendedfor use only in heavy-industrial locations.Note Group 1 equipment (per CISPR 11) is any industrial, scientific, or medicalequipment that does not intentionally generate radio frequency energy for thetreatment of material or inspection/analysis purposes.Note For EMC declarations, certifications, and additional information, refer to theOnline Product Certification section.CE ComplianceThis product meets the essential requirements of applicable European Directives, as follows:•2014/35/EU; Low-V oltage Directive (safety)•2014/30/EU; Electromagnetic Compatibility Directive (EMC)16| | PXI-5650 SpecificationsOnline Product CertificationRefer to the product Declaration of Conformity (DoC) for additional regulatory compliance information. To obtain product certifications and the DoC for this product, visit / certification, search by model number or product line, and click the appropriate link in the Certification column.Environmental ManagementNI is committed to designing and manufacturing products in an environmentally responsible manner. NI recognizes that eliminating certain hazardous substances from our products is beneficial to the environment and to NI customers.For additional environmental information, refer to the Minimize Our Environmental Impact web page at /environment. This page contains the environmental regulations and directives with which NI complies, as well as other environmental information not included in this document.Waste Electrical and Electronic Equipment (WEEE)EU Customers At the end of the product life cycle, all NI products must bedisposed of according to local laws and regulations. For more information abouthow to recycle NI products in your region, visit /environment/weee.电子信息产品污染控制管理办法(中国RoHS)中国客户National Instruments符合中国电子信息产品中限制使用某些有害物质指令(RoHS)。
OMEGA FLSC-AMP-A 磁性传感器信号条件器说明书
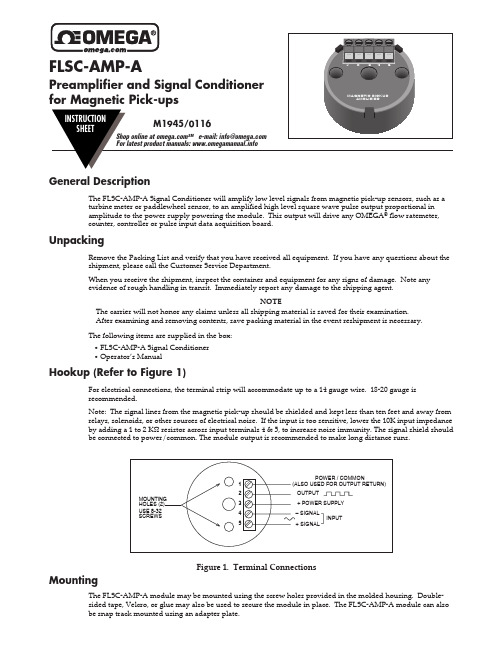
General DescriptionThe FLSC-AMP-A Signal Conditioner will amplify low level signals from magnetic pick-up sensors, such as aturbine meter or paddlewheel sensor, to an amplified high level square wave pulse output proportional inamplitude to the power supply powering the module. This output will drive any OMEGA®flow ratemeter,counter, controller or pulse input data acquisition board.UnpackingRemove the Packing List and verify that you have received all equipment. If you have any questions about theshipment, please call the Customer Service Department.When you receive the shipment, inspect the container and equipment for any signs of damage. Note anyevidence of rough handling in transit. Immediately report any damage to the shipping agent.NOTEThe carrier will not honor any claims unless all shipping material is saved for their examination.After examining and removing contents, save packing material in the event reshipment is necessary.The following items are supplied in the box:• FLSC-AMP-A Signal Conditioner• Operator’s ManualHookup (Refer to Figure 1)For electrical connections, the terminal strip will accommodate up to a 14 gauge wire. 18-20 gauge isrecommended.Note: The signal lines from the magnetic pick-up should be shielded and kept less than ten feet and away fromrelays, solenoids, or other sources of electrical noise. If the input is too sensitive, lower the 10K input impedance by adding a 1 to 2 KΩ resistor across input terminals 4 & 5, to increase noise immunity. The signal shield should be connected to power/common. The module output is recommended to make long distance runs.Figure 1. Terminal ConnectionsMountingThe FLSC-AMP-A module may be mounted using the screw holes provided in the molded housing. Double-sided tape, Velcro, or glue may also be used to secure the module in place. The FLSC-AMP-A module can alsobe snap track mounted using an adapter plate.SpecificationsPower:8 to 24 VdcInput Frequency:10 Hz to 10 KHzInput Voltage:Sinusoidal (60mV p-p at 20Hz, 150mV p-p at 20 kHz) to 50V p-pInput Impedance:10 K ohmsOutput: 100 mA sink max. with 4.7K internal pull-up resistorTemperature Range:-10 to 60°CWeight: 1 oz.DimensionsServicing North America:U.S.A.:Omega Engineering, Inc., One Omega Drive,P.O. Box 4047, Stamford, CT 06907-0047 USAToll-Free: 1-800-826-6342 (USA & Canada only) Customer Service: 1-800-622-2378 (USA & Canada only) Engineering Service: 1-800-872-9436 (USA & Canada only) Tel: (203) 359-1660Fax: (203) 359-7700e-mail:**************For Other Locations Visit/worldwide***********************The information contained in this document is believed to be correct, but OMEGA accepts no liability for any errors it contains, and reserves the right to alter specifications without notice.WARRANTY/DISCLAIMEROMEGA ENGINEERING, INC., warrants this unit to be f ree of defects in materials and workmanship for a period of 13 months from date of purchase. OMEGA’s WARRANTY adds an additional one (1) month grace period to the normal one (1) year product warranty to cover handling and shipping time. This ensures that OMEGA’s customers receive maximum coverage on each product. If the unit malfunctions, it must be returned to the factory for evaluation. OMEGA’s Customer Service Department will issue an Authorized Return (AR) number immediately upon phone or written request. Upon examination by OMEGA, if the unit is found to be defective, it will be repaired or replaced at no charge. OMEGA’s WARRANTY does not apply to defects resulting from any action of the purchaser, including but not limited to mishandling, improper interfacing, operation outside of design limits, improper repair, or unauthorized modifi cation. This WARRANTY is VOID if the unit shows evidence of having been tampered with or shows evidence of having been damaged as a result of excessive corrosion; or current, heat, moisture or vibration; improper specifi cation; misapplication; misuse or other operating conditions outside of OMEGA’s control. Components in which wear is not warranted, include but are not limited to contact points, fuses, and triacs.OMEGA is pleased to offer suggestions on the use of its various products. However, OMEGA neither assumes responsibility for any omissions or errors nor assumes liability for any damages that result from the use of its products in accordance with information provided by OMEGA, either verbal or written. OMEGA warrants only that the parts manufactured by the company will be as specifi ed and free of defects. OMEGA MAKES NO OTHER WARRANTIES OR REPRESENTATIONS OF ANY KIND WHATSOEVER, EXPRESSED OR IMPLIED, EXCEPT THAT OF TITLE, AND ALL IMPLIED WARRANTIES INCLUDING ANY WARRANTY OF MERCHANTABILITY AND FITNESS FOR A PARTICULAR PURPOSE ARE HEREBY DISCLAIMED. LIMITATION OF LIABILITY: The remedies of purchaser set forth herein are exclusive, and the total liability of OMEGA with respect to this orde r, whether based on contract, warranty, negligence, indemnifi cation, strict liability or otherwise, shall not exceed the purchase price of the component upon which liability is based. In no event shall OMEGA be liable for consequential, incidental or special damages.CONDITIONS: Equipment sold by OMEGA is not intended to be used, nor shall it be used: (1) as a “Basic Component” under 10 CFR 21 (NRC), used in or with any nuclear installation or activity; or (2) in medical applications or used on humans. Should any Product(s) be used in or with any nuclear installation or activity, medical application, used on humans, or misused in any way, OMEGA assumes no responsibility as set forth in our basic WARRANTY/DISCLAIMER language, and, additionally, purchaser will indemnify OMEGA and hold OMEGA harmless from any liability or damage whatsoever arising out of the use of the Product(s) in such a manner.RETURN REQUESTS/INQUIRIESD irect all warranty and repair requests/inquiries to the OMEGA Customer Service Department. BEFORE RETURNING ANY PRODUCT(S) TO OMEGA, PURCHASER MUST OBTAIN AN AUTHORIZED RETURN (AR) NUMBER FROM OMEGA’S CUSTOMER SERVICE DEPARTMENT (IN ORDER TO AVOID PROCESSING DELAYS). The assigned AR number should then be marked on the outside of the return package and on any correspondence.The purchaser is responsible for shipping charges, freight, insurance and proper packaging to prevent breakage in transit.FOR WARRANTY RETURNS, please have the followinginformation available BEFORE contacting OMEGA.1. Purchase order number which the product wasPURCHASED,2. Model and serial number of the product under warranty, and3. R epair instructions and/or specifi c problems relative tothe product.OMEGA’s policy is to make running changes, not model changes, whenever an improvement is possible. This affords customers the latest technology and engineering.OMEGA is a registered trademark of OMEGA ENGINEERING, INC.© COPYRIGHT 2016 OMEGA ENGINEERING, INC. All rights reserved. This document may not be copied, photocopied, translated, or reduced to any electronic medium-readable form, in whole or in part, without the prior written consent of OMEGA ENGINEERING, INC.FOR NON-WARRANTY RETURNS, consult OMEGA forcurrent repair charges. Have the following informationavailable BEFORE contacting OMEGA.1. Purchase Order number to cover the COST of the repair,2. Model and serial number of the product and3. Repair instructions and/or specifi c problemsrelative to the product.。
基于GPS和INS的测速方法比较分析
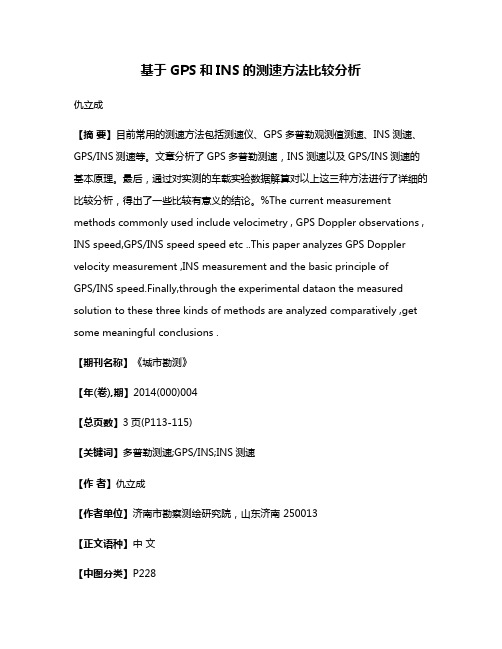
基于GPS和INS的测速方法比较分析仇立成【摘要】目前常用的测速方法包括测速仪、GPS多普勒观测值测速、INS测速、GPS/INS测速等。
文章分析了GPS多普勒测速,INS测速以及GPS/INS测速的基本原理。
最后,通过对实测的车载实验数据解算对以上这三种方法进行了详细的比较分析,得出了一些比较有意义的结论。
%The current measurement methods commonly used include velocimetry , GPS Doppler observations , INS speed,GPS/INS speed speed etc ..This paper analyzes GPS Doppler velocity measurement ,INS measurement and the basic principle ofGPS/INS speed.Finally,through the experimental dataon the measured solution to these three kinds of methods are analyzed comparatively ,get some meaningful conclusions .【期刊名称】《城市勘测》【年(卷),期】2014(000)004【总页数】3页(P113-115)【关键词】多普勒测速;GPS/INS;INS测速【作者】仇立成【作者单位】济南市勘察测绘研究院,山东济南 250013【正文语种】中文【中图分类】P228随着GPS的普及和应用,它的优势在社会各方面都有明显的体现,在测量运载体的速度方面也是如此[1]。
虽然其使用方便,但是一旦GPS卫星信号失锁,将导致多普勒观测值不能够得到,所以这也是多普勒测速的一大缺点,而GPS/INS的组合测速方式的出现打破了这一弊端,它可以在信号失锁的情况下利用INS的测量值来准确测量速度,而且当卫星信号可用时,GPS和INS两种系统的测量值可以通过数据融合更精确的测量载体速度[2]。
APM全部参数表
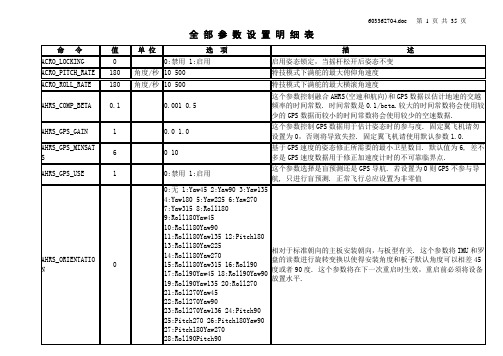
6 0 17 3300 12 3 10.57399 伏特 安培/伏 特 毫安时
1 10
0:禁用 3:仅电压 4:电压和电流
603362704.doc
第 5 页 共 35 页
模块,这个值为 10.1. 对于使用 3DR 四合一电调的 Pixhawk 这个值 为 12.02. 对于使用 PX4IO 电源模块的 PX4 这个值必须为 1. BATT_VOLT_PIN BATT2_AMP_OFFSE T BATT2_AMP_PERVO L BATT2_CAPACITY BATT2_CURR_PIN BATT2_MONITOR BATT2_VOLT_MULT BATT2_VOLT_PIN CAM_DURATION CAM_SERVO_OFF CAM_SERVO_ON 13 -1:禁 用 0:A0 13:A13 1:A1电池电压传感器的管脚对应于 A0 至 A13. 对于 APM2.5 的电源模块,这个值必须为 13. 在 PX4 上这个值 必须为 100. 对于使用电源模块的 Pixhawk 这个值必须为 2.
ARMING_DIS_RUD
0
ARMING_REQUIRE
2
0:禁用 1:解锁后油门 PWM 在 THR_MIN(怠速) 2:解锁后油门 0PWM(停转)
ARSPD_AUTOCAL ARSPD_ENABLE ARSPD_FBW_MAX ARSPD_FBW_MIN ARSPD_OFFSET
0 0 22 9 833.2711
603362704.doc
第 4 页 共 35 页
ARSPD_PIN
0
空速计连接到的模拟 IO 口. 设置这个参数为 0-9 来对应 APM2 的模拟 引脚. 使用 APM1 时设置为 64,对应于板子末端的空速计接口. 使用 PX4 时设为 11,对应于模拟空速计接口. 使用 Pixhawk 时设为 15, 对应于模拟空速计接口. 使用 EagleTree 或 MEAS I2C 空速计的 PX4 或者 Pixhawk,设置为 65. 空速计校准后的比率 这个参数允许你在皮托管里的连接顺序有影响时选择. 如果设置为 0 则顶部连接的传感器是动态压强. 如果设置为 1 则底部连接的传感 器是动态压强. 若设为 2(默认)则空速管驱动器将会接受任意一种 顺序.你可能想要指定顺序的原因在于它能够使你的空速计检测飞行 器是不是受到了过大的静压强,而这可能被解读成正空速. 1:使用 0:不使用 使用空速数据进行飞行控制 开启此项将使得在自动模式中可以使用 FBWA 的方式进行操控. 这可 以用来执行带有航点逻辑的人工增稳飞行,或可用于载荷[译注:即 飞的时候知道航点,一个个航点飞过去]. 启用后飞行员拥有和 FBWA 模式中一样的操控, 但普通的自动模式导航被完全禁用. 寻常情况 不推荐这个选项. 自动调参的激烈程度. 在较低等级的 AUTOTUNE_LEVEL 上自动调参较 为柔和, 增益较小. 对于大多数用户而言推荐 5 级. 在 0 电流情况下传感器的电压读数偏移值 当电流传感器读数为 1V 时转换得到的电流值. 对于使用 3DR 电源模 块的 APM2 或者 Pixhwak 这个值必须为 17. 对于使用 3DR 四合一电调 的 Pixhawk 这个值必须为 17. 满电电池的容量,以 mAh 计 -1:禁 用 1:A1 12:A12 2:A2 3:Pixhawk 101:PX4 设置这个参数为 0 至 13 将指定电池电流传感器的管脚对应于 A0 至 A13. 对于 APM2.5 的电源模块,这个值必须为 12. 在 PX4 上这个值 必须为 101. 对于使用电源模块的 Pixhawk 这个值必须为 3. 控制电池电流或电压监控 用来将电压传感器管脚检测到的电压值(BATT_VOLT_PIN)转换成实际 电压值(管脚电压*VOLT_MULT). 对于 APM2 或者 Pixhawk 的 3DR 电源
RFSA2013TR7;中文规格书,Datasheet资料

5V Power Supply Linear in dB Control
Characteristic Internal Temperature
Compensation
Class 1C ESD (1000V) 3.3V Version Available
Patent Pending Circuit Architecture
Broadband 50MHz to 6000MHz Frequency Range
30dB Attenuation Range +50dBm IIP3 Typical
+80dBm IIP2 Typical High 1dB Compression
7628 Thorndike Road, Greensboro, NC 27409-9421 · For sales or technical support, contact RFMD at (+1) 336-678-5570 or customerservice@.
1 of 17
(RFSA2023) Complete Solution in a Small
3mm x 3mm, QFN Package
Applications
Cellular, 3G Infrastructure WiBro, WiMax, LTE
Microwave Radio High Linearity Power Control
RFMD Green: RoHS compliant per EU Directive 2002/95/EC, halogen free per IEC 61249-2-21, < 1000ppm each of antimony trioxide in polymeric materials and red phosphorus as a flame retardant, and <2% antimony in solder.
DSEI60-06A;中文规格书,Datasheet资料

166 W
0.8...1.2 Nm
6
g
Symbol
IR
VF
VT0 rT RthJC RthCH trr IRM
Conditions
Characteristic Values typ. max.
VR = VRRM VR = 0.8·VRRM VR = 0.8·VRRM
TVJ = 25°C TVJ = 25°C TVJ = 125°C
IXYS reserves the right to change limits, test conditions and dimensions
© 2007 IXYS All rights reserved
/
0549
2-2
Dimensions TO-247 AD
C
D
t = 8.3 ms (60 Hz), sine
TC = 25°C mounting torque typical
Maximum Ratings
100 A 60 A
550 A 600
480 A 520Biblioteka 1510 A2s 1490
1150 A2s 1120
-55...+150 °C 150 °C
-55...+150 °C
Fast Recovery Epitaxial Diode (FRED)
DSEI60-06A DSEI60-06AT
IFAV = 60 A VRRM = 600 V trr = 35 ms
VRSM V
600 600
VRRM V
600 600
Type
DSEI 60-06A DSEI 60-06AT
A
Omni-T D OM-USB-1608FS系列数据获取模块说明书

OM-USB-1608FS SeriesU 16-Bit Resolution U 8 Single-Ended Analog Input Channels U S imultaneous Sampling(1 A/D Converter Per Input)U U p to 400 kS/s Overall Throughput (100 kS/s Maximum for Any Channel)U 8 Digital I/OU 1 Event Counter U External Clock I/OU External Digital Trigger Input U No External Power RequiredThe OM-USB-1608FS Series consists of thefollowing low-cost, analog and digital I/O modules: • OM-USB 1608FS • OM-USB-1608FS-PLUSThese modules provide eight single-ended (SE),simultaneous-sampling 16-bit analog inputs, eight DIO, one event counter, one external digital trigger input, and one bidirectional external clock.Everything you need to begin acquiring, viewing, and storing data is included with each OM-USB-1608FS Series module, including comprehensive software support.SOFTWAREOM-USB-1608FS Series modules ship with an impressive array of software, including the newTracerDAQ ®, a full-featured, out-of-the-box data logging, viewing, and analysis application. Driver support and detailed example programs are included for Universal Library programming libraries for Microsoft ® VisualStudio ® programming languages, and other languages, including DASYLab ®, and ULx for NI LabVIEW ®(comprehensive library of Vls and example programs compatible with 32-bit and 64-bit LabVIEW v8.5through 2013) and InstaCal™ installation, calibration and test utility-powerful solutions for programmers and nonprogrammers alike. These modules operate under Microsoft Windows ® XP (32-bit only) and VISTA/7/8 (32-bit and 64-bit) operating systems.TracerDAQ-PRO Strip Chartwith Measurements.TracerDAQ Strip Chart.OM-USB-1608FS-PLUS shown smaller thanactual size.The OM-USB-1608FS Series data acquisition modules are supplied with TracerDAQ software which is acollection of four virtual instrument applications used to graphically display and store input data and generate output signals:• S trip Chart—Log and graph values acquired from analog inputs, digital inputs, temperature inputs and counter inputs• O scilloscope—Display values acquired fromanalog inputs• F unction Generator—Generate waveforms for analog outputs•R ate Generator—Generate waveforms for counter outputsT racerDAQ PRO is an enhanced version of TracerDAQ. A comparison of some of the features included in TracerDAQ vs TracerDAQ PRO is shown on the next page.digital input, event counter digital input, event counterTime-of-Day Triggering No YesFunction GeneratorANALOG INPUTBoth modules provide eight single-ended (SE) 16-bit analog input channels with a dedicated A/D converter per channel for simultaneous sampling. The devices offer software-selectable analog input ranges for±10V, ±5V, ±2V, and ±1V.SAMPLING RATEOM-USB-1608FS Series modules offer the following sampling rates when scanning continuously to computer memory (hardware-paced mode):• O M-USB-1608FS-PLUS - T otal rate of 400 kS/sdivided by the number of channels sampled;maximum rate of 100 kS/s per channel.• O M-USB-1608FS - Total rate of 100 kS/s dividedby the number of channels sampled; maximum rate of 50 kS/s per channel.SIMULTANEOUS SAMPLINGIn hardware paced mode, both modules can acquire data from up to eight channels simultaneously. The analog data is continuously acquired, converted to digital values, temporarily stored in the onboard FIFO buffer, and periodically uploaded to the computer. CHANNEL-GAIN QUEUEThe channel-gain queue lets you configure a list of channels and gains for each scan. Each channel can have a different gain setting. The gain settings are stored in a channel-gain queue list that is written to local memory on the device. The channel-gain queuelist for both modules can contain up to eight unique channels. On the OM-USB-1608FS, the channels must be consecutive and listed in increasing order. On the OM-USB-1608FS-PLUS, the channels can be non-consecutive, but still must be listed in increasing order.SPECIFICATIONSANALOG INPUTA/D Converter Type: 16-bit successive approximation typeChannels: 8 single-endedInput Configuration: Individual A/D per channel Sampling Method: SimultaneousAbsolute Maximum Input Voltage: CHx IN Relative to GND: ±15V maxInput Impedance: 100 M Ω minInput Ranges: ±10V , ±5V , ±2 V , ±1V; software-selectable per channelSampling Rate (Hardware Paced)O M-USB-1608FS: 0.6 S/s to 50 kS/s, software-selectableO M-USB-1608FS-PL US: 0.01 S/s to 100 kS/s, software-selectable ThroughputSoftware Paced: 500 S/s all channels Hardware Paced (System-Dependent):O M-USB-1608FS: (100 kS/s)/(# of channels) max,50 kS/s max for any channel O M-USB-1608FS-PL US: (400 kS/s)/(# of channels)max, 100 kS/s max for any channel B urst Scan ≤ 32,768 Total Samples (Uses Onboard FIFO):O M-USB-1608FS: (200 kS/s)/(# of channels) max,50 kS/s max for any channel O M-USB-1608FS-PL US: (800 kS/s)/(# of channels)max, 100 kS/s max for any channelDIGITAL I/OBoth modules provide eight digital I/O connections. Each digital channel is individually-configurable for input or output. When configured for input, you can use the digital I/O terminals to detect the state of any TTL level input. On the OM-USB-1608FS-PLUS, the digital I/O channels are high-drive (24 mA) connections.PULL-UP/PULL-DOWN CONFIGURATIONRecent revisions of OM-USB-1608FS Series modules have a user-configurable internal jumper to configurethe digital bits for pull-up (default) or pull-down.COUNTER INPUTThe OM-USB-1608FS-PLUS has a 32-bit event counter that can accept a signal up to 1 MHz. The internal counter increments when the TTL levels transition from low to high.EXTERNAL CLOCK I/OEach OM-USB-1608FS Series module has abidirectional external clock terminal. When configured for input, A/D conversions can be paced by an external source.The OM-USB-1608FS supports TTL-level input signals up to 50 kHz.The OM-USB-1608FS-PLUS supports TTL-level input signals up to 100 kHz.When configured for output, both devices can pace A/D conversions on a second device and acquire data from all input channels simultaneously.TRIGGER INPUTOM-USB-1608FS Series modules provide an external digital trigger input.The OM-USB-1608FS trigger mode is edge sensitive and software-selectable for rising or falling edge.The OM-USB-1608FS-PLUS trigger mode is edge or level sensitive. Edge sensitive is software-selectable for rising or falling edge. Level sensitive is software-selectable for high or low level.CALIBRATIONEach OM-USB-1608FS Series module ships fully calibrated and can be re-calibrated at the factory. The OM-USB-1608FS also supports user calibration.Gain Queue:O M-USB-1608FS: Up to eight elements; one gain element per unique, consecutive channel; software-selectableO M-USB-1608FS-PL US: Up to eight elements; one gain element per unique, ordered channel; software-selectableResolution: 16 bits±10V 5.66 mV ±10V 0.04 4.00 mV 1.66 mV*Summarizes the noise performance for OM-USB-1608FS Series devices. Noise distribution is determined by gathering 50 kS with inputs tied to ground at the user connector. Samples are gathered at the maximum specified sampling rates of 50 kS/s (OM-USB-1608FS) and 100 kS/s (OM-USB-1608FS-PLUS).ACCURACYAnalog Input DC Voltage Measurement AccuracyNo Missing Codes:OM-USB-1608FS: 15 bitsOM-USB-1608FS-P US: 16 bitsCrosstalk (Signal DC to 25 kHz): -80 dBCAL Output (OM-USB-1608FS Only): 0.625V , 1.25V , 2.5V , 5VCAL Output Accuracy (OM-USB-1608FS Only): 0.5% typ, 1.0% max (actual values used for calibration are measured and stored in EEPROM)CAL Current (OM-USB-1608FS Only): ±5 mA max Trigger Source (Software-Selectable) External Digital: TRIG_INDIGITAL INPUT/OUTPUT Digital Type:OM-USB-1608FS: CMOSOM-USB-1608FS-P US: 5V TTL Number of I/O: 8 (DIO0 through DIO7)Configuration: Independently configured for input or outputPull-Up/Pull-Down Configuration: All pins pulled up to 5V via 47 k Ω resistors (default). May be changed to pull-down using an internal jumper (OM-USB-1608FS hardware revisions E and later may be changed to pull-down using an internal user-configurable jumper. Previous revisions can be configured for pull-down at the factory).Input High Voltage Threshold: 2.0V min Input High Voltage Limit: 5.5V absolute max Input Low Voltage Threshold: 0.8V maxInput Low Voltage Limit: -0.5V absolute min; 0V recommended min Output High Voltage:OM-USB-1608FS (IOH = –2.5 mA): 3.8V min O M-USB-1608FS-PL US: 4.4V min (IOH = -50 μA); 3.76V min (IOH = -24 mA)Output Low Voltage:OM-USB-1608FS (IOL = 2.5 mA): 0.44V max O M-USB-1608FS-PL US: 0.1V max (IOL = 50 μA); 0.44V max (IOL = 24 mA)Power On and Reset State: InputEXTERNAL TRIGGERTrigger Source (External Digital): TRIG_IN Trigger Mode (Software-Selectable):O M-USB-1608FS: Edge sensitive: user configurable for CMOS compatible rising or falling edge O M-USB-1608FS-PL US: Edge sensitive or level sensitive: user configurable for CMOS compatible rising or falling edge, high or low level Trigger Latency:OM-USB-1608FS: 10 μs maxO M-USB-1608FS-PLUS: 2 μs + 1 pacer clock cycle max Trigger Pulse Width: 1 μs minInput Type: Schmitt trigger, 47 k Ω pull-down to ground Schmitt Trigger Hysteresis: 1.01V typ, 0.6V min, 1.5V maxInput High Voltage Threshold: 2.43V typ, 1.9V min, 3.1V maxInput High Voltage Limit: 5.5V absolute maxInput Low Voltage Threshold: 1.42V typ, 1.0V min, 2.0V maxInput Low Voltage Limit: -0.5V absolute min, 0V recommended minEXTERNAL CLOCK I/O Pin Name: SYNCPin Type: BidirectionalDirection (Software-Selectable):Input: Receives A/D pacer clock from external source; Output: Outputs internal A/D pacer clockOrdering Example: OM-USB-1608FS 8-channel 100 kS/s simultaneous analog input USB data acquisition module and OCW-1, OMEGACARE SM extends standard 1-year warranty to a total of 2 years.Input Clock Rate:OM-USB-1608FS: 50 kHz maxOM-USB-1608FS-P US: 100 kHz max Clock Pulse Width: Input: 1 μs min Output:OM-USB-1608FS: 5 μs minOM-USB-1608FS-P US: 4 μs minInput Clock Mode: Edge sensitive, rising edgeInput Type: Schmitt trigger, 47 k Ω pull-down to ground Schmitt Trigger Hysteresis: 1.01V typ, 0.6V min, 1.5V maxInput High Voltage Threshold: 2.43V typ, 1.9V min, 3.1V maxInput High Voltage Limit: 5.5V absolute maxInput Low Voltage Threshold: 1.42V typ, 1.0V min, 2.0V maxInput Low Voltage Limit: -0.5V absolute min, 0V recommended minOutput High Voltage: 4.4V min (IOH = -50 μA), 3.80V min (IOH = -8 mA)Output Low Voltage: 0.1V max (IOL = 50 μA), 0.44V max (IOL = 8 mA)COUNTERPin Name: CTRCounter Type: Event counter Number Of Channels: 1Input Type: Schmitt trigger, 47 k Ω pull-down to ground Input Source: CTR screw terminal Resolution: 32 bitsSchmitt Trigger Hysteresis: 1.01V typ, 0.6V min, 1.5V maxInput High Voltage Threshold: 2.43V typ, 1.9V min, 3.1V maxInput High Voltage Limit: 5.5V absolute maxInput Low Voltage Threshold: 1.42V typ, 1.0V min, 2.0V maxInput Low Voltage Limit: -0.5V absolute min, 0V recommended minInput Frequency: 1 MHz max High Pulse Width: 500 ns min Low Pulse Width: 500 ns minPOWERSupply CurrentUSB Enumeration: < 100 mAIncluding DIO and SYNC Output Loading: < 500 mA +5V USB Power Available (Connected to Externally-Powered Root Port Hub or a Self-Powered Hub): 4.5V min, 5.25V maxOutput Current (Total Amount of Current that can be Sourced from the USB 5V and Digital Outputs): 300 mA maxMEMORYData FIFO: 32,768 samples, 65,536 bytes EEPROM:OM-USB-1608FS: 1024 bytesOM-USB-1608FS-P US: 2048 bytesGENERALOperating Temperature Range: 0 to 70°C (32 to 158°F), 0 to 90% RH non-condensing Storage Temperature Range: -40 to 70°C(-40 to 158°F), 0 to 90% RH non-condensingCommunications: USB 2.0 hi-speed mode (480Mbps) is recommended; otherwise USB 1.1 full-speed mode (12 Mbps)Microcontroller Type: High performance 32-bit RISC Signal I/O Connector Type: Screw terminal USB Cable Length: 3 m (9.84') max Dimensions: 79 L x 82 W x 27 mm H (3.10 x 3.20 x 1.05") Weight: 91 g (3.2 oz)OMEGACARE SM extended warranty program is available for models shown on this page. Ask your sales representative for full details when placing an order. OMEGACARE SM covers parts,labor and equivalent loaners.。
IMU-FSAS Datasheet(中文)
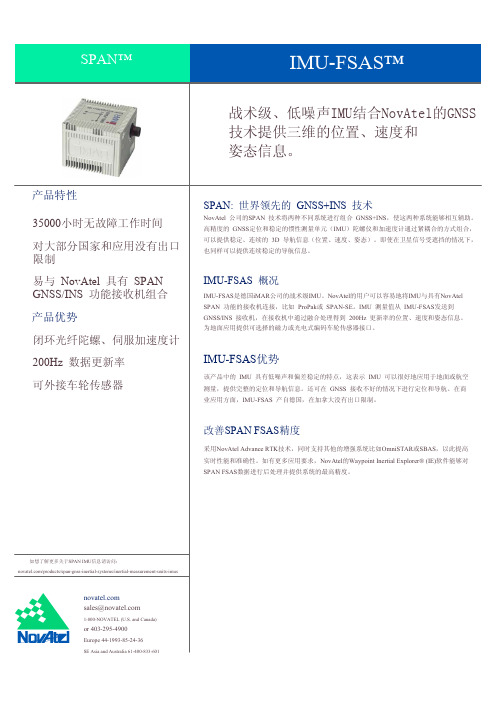
产品特性Version 4 -Specifications subject to change without notice. ©2010 NovAtel Inc. All rights reserved. ProPak, Inertial Explorer, RT-20, Waypoint and NovAtel are registered trademarks of NovAtel Inc.SPAN, IMU-FSAS and RT-2 are trademarks of NovAtel Inc.Printed in Canada. D10150IMU-FSAS August 2010想了解该产品的更多信息请访问/assets/Documents/Papers/FSAS.pdf1 典型值。
性能规格如GPS 系统的特点,受US DOD 业务退化,电离层和对流层,卫星几何,基线长度,多径效应和有意或无意的干扰源的影响 2 只有GPS 可用。
3静态收敛后的预计精度 4 当SPAN 的定位模式为RTK 时。
5出口许可限制操作515m/S 6 GNSS 接收机能持续跟踪达4g7使用IE 后处理如见处理的结果。
.Statements related to the export of products are based solely on NovAtel’s experience in Canada, are not binding in any way and exportability may be different with respect to the export regulations in effect in another country. The responsibility for re-export of product from a Customer’s facility is solely the responsibility of the Customer.。
布罗尼卡6x6cm单反相机技术数据表说明书
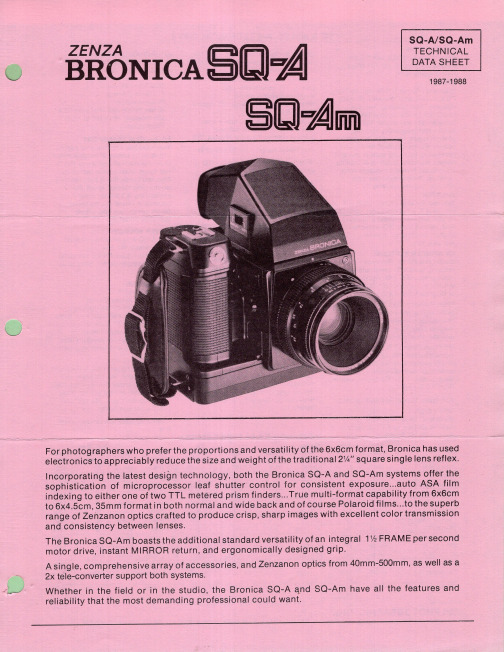
BZERNZOA NICA~a::U:!(sfilU....~~
sa-A/sa-Am
TECHNICAL DATA SHEET
1987-1988
For photographers who prefer the proportionBronica has used electronics to appreciably reduce the size and weight of the traditionaI2%" square single lens reflex.
POWER SOURCE: (SO-AlSO-Am) Single 6 volt silver oxide battery, No. 544 (SO-Am only) Six AA 1.5 volt (only) alkaline-manganese for motor drive operation.
Prism Finder: Total reflection eye-level prism with laterally correct upright image. Approximate viewfinder magnification ".75x. Range of diopters available from -4.5 to +1.5.
ADIS16405 IMU 在四旋翼飞行器姿态测量的应用
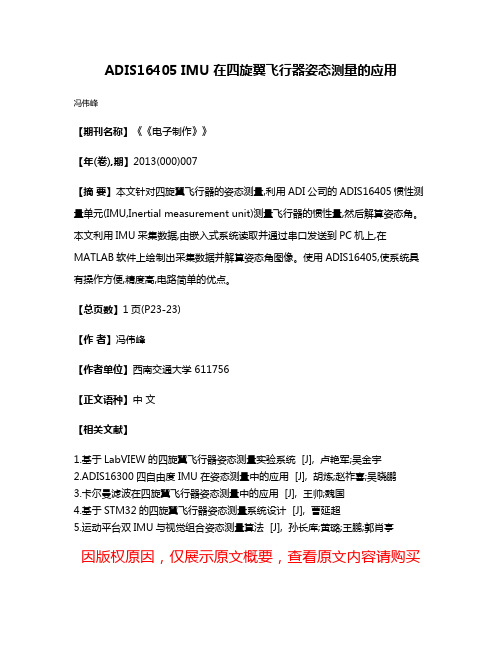
ADIS16405 IMU 在四旋翼飞行器姿态测量的应用
冯伟峰
【期刊名称】《《电子制作》》
【年(卷),期】2013(000)007
【摘要】本文针对四旋翼飞行器的姿态测量,利用ADI公司的ADIS16405惯性测量单元(IMU,Inertial measurement unit)测量飞行器的惯性量,然后解算姿态角。
本文利用IMU采集数据,由嵌入式系统读取并通过串口发送到PC机上,在MATLAB软件上绘制出采集数据并解算姿态角图像。
使用ADIS16405,使系统具有操作方便,精度高,电路简单的优点。
【总页数】1页(P23-23)
【作者】冯伟峰
【作者单位】西南交通大学 611756
【正文语种】中文
【相关文献】
1.基于LabVIEW的四旋翼飞行器姿态测量实验系统 [J], 卢艳军;吴金宇
2.ADIS16300四自由度IMU在姿态测量中的应用 [J], 胡炼;赵祚喜;吴晓鹏
3.卡尔曼滤波在四旋翼飞行器姿态测量中的应用 [J], 王帅;魏国
4.基于STM32的四旋翼飞行器姿态测量系统设计 [J], 曹延超
5.运动平台双IMU与视觉组合姿态测量算法 [J], 孙长库;黄璐;王鹏;郭肖亭
因版权原因,仅展示原文概要,查看原文内容请购买。
赛米控丹佛斯 芯片 SKCD 81 C 065 I4F 数据表
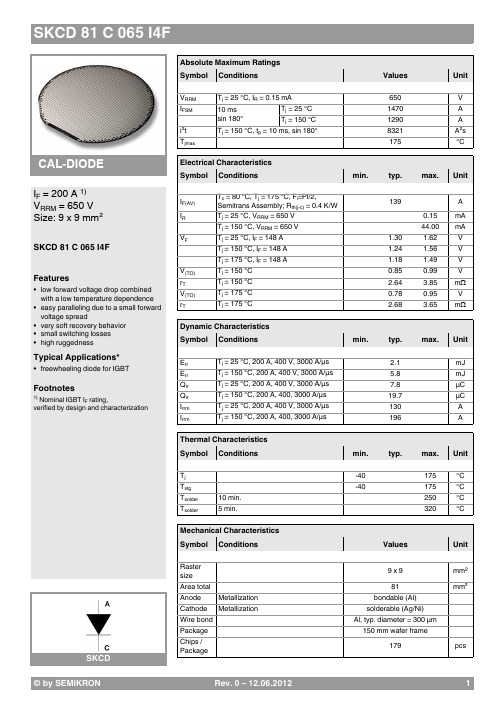
1CAL-DIODESKCDI F = 200 A 1)V RRM = 650 V Size: 9 x 9 mm²SKCD 81 C 065 I4FFeatures•low forward voltage drop combined with a low temperature dependence •easy paralleling due to a small forward voltage spread•very soft recovery behavior •small switching losses •high ruggednessTypical Applications*•freewheeling diode for IGBTFootnotes1)Nominal IGBT I F rating,verified by design and characterizationAbsolute Maximum Ratings SymbolConditionsValuesUnitV RRM T j =25°C,I R =0.15mA 650V I FSM 10ms sin 180°T j =25°C 1470A T j =150°C1290A i²t T j =150°C, t p =10ms, sin 180°8321A²s T jmax175°CElectrical Characteristics SymbolConditionsmin.typ.max.UnitI F(AV)T c =80°C,T j =175°C, F i =PI/2,Semitrans Assembly; R th(j-c) = 0.4 K/W 139AI R T j =25°C,V RRM =650V 0.15mA T j =150°C, V RRM =650V 44.00mA V FT j =25°C,I F =148A 1.30 1.62V T j =150°C, I F =148A 1.24 1.56V T j =175°C, I F =148A1.18 1.49V V (TO)T j =150°C 0.850.99V r T T j =150°C2.643.85m ΩV (TO)T j =175°C 0.780.95V r TT j =175°C2.683.65m ΩDynamic Characteristics SymbolConditionsmin.typ.max.UnitE rr T j =25°C, 200A, 400V, 3000A/µs 2.1mJ E rr T j =150°C, 200A, 400V, 3000A/µs 5.8mJ Q rr T j =25°C, 200A, 400V, 3000A/µs 7.8µC Q rr T j =150°C, 200A, 400, 3000A/µs 19.7µC I rrm T j =25°C, 200A, 400V, 3000A/µs 130A I rrmT j =150°C, 200A, 400, 3000A/µs196AThermal Characteristics SymbolConditions min.typ.max.UnitT j -40175°C T stg -40175°C T solder 10min.250°C T solder5min.320°CMechanical Characteristics SymbolConditions ValuesUnitRaster size 9 x 9mm 2Area total 81mm²Anode Metallization bondable (Al)Cathode Metallizationsolderable (Ag/Ni)Wire bond Al, typ. diameter = 300 µm Package 150 mm wafer frameChips / Package179pcs2This is an electrostatic discharge sensitive device (ESDS), international standard IEC 60747-1, Chapter IX* The specifications of our components may not be considered as an assurance of component characteristics. Components have to be tested for the respective application. Adjustments may be necessary. The use of SEMIKRON products in life support appliances and systems is subject to prior specification and written approval by SEMIKRON. We therefore strongly recommend prior consultation of our staff.Fig. 1: Rated current vs. thermal resistance。
诺瓦特尔-SPAN

GM-14915112 Rev 9December 2016QUICK START GUIDEThis guide provides the basic information you need to set up and begin using your SPAN system.SPAN SYSTEM COMPONENTSA SPAN system requires the following primary components:• A SPAN capable OEM6 receiver (enclosure or receiver card)•An IMU (see the IMU Type column in Table 4, CONNECTIMU Commands )• A quality, dual-frequency GNSS antenna such as the GNSS-502 or GNSS-802. See the NovAtel website (/products/gnss-antennas/) for information on a variety of quality antennas available to meet your form factor and performance needs.•Cables to connect the components. See Table 2, SPAN System Cables for FlexPak6 or Table 3, SPAN System Cables for ProPak6.• A power supply for the OEM6 receiver.For the receiver power requirements, refer to the OEM6 Family Installation and Operation User Manual (OM-20000128) or ProPak6 User Manual (OM-20000148) available on the NovAtel web site (/support/manuals/).• A power supply for the IMU.For the IMU power requirements, see Table 1, IMU Power Supply Requirements .SET UP YOUR SPAN HARDWARE Complete the following steps to set up and power your SPAN system.1.Mount the IMU and antenna securely to a vehicle.For the simplest operation, align the Y-axis of the IMU with the forward axis (direction of travel) of the vehicle. Ensure the Z-axis is pointing up.Ensure that the GNSS antenna and IMU cannot move relative to each other. The distance and relative direction between them must be fixed.If you want to use the same power supply for the receiver and the IMU, make sure the power supply meets the requirements of both the receiver and the IMU. This procedure focuses on a SPAN system with a FlexPak6 or ProPak6 receiver. Forinformation about SPAN system installation with other OEM6 receivers, see the SPAN onOEM6 User Manual (OM-20000139) found on the NovAtel web site (/support/manuals/).Figure 1: Connect FlexPak6 to IMU-ISA-100C, IMU-LN200, IMU-HG1900, IMU-µIMU, IMU-IGM,2.Connect the IMU to the receiver using the IMU interface cable.•For a system with a FlexPak6, connect the IMU interface cable to the COM2 port. See Figure 1,Connect FlexPak6 to IMU-ISA-100C, IMU-LN200, IMU-HG1900, IMU-µIMU, IMU-IGM, UIMU-HG1700, UIMU-LCI or UIMU-LN200, on page 2.For a system with a FlexPak6 and an IMU-ISA-100C, IMU-ISA-100, IMU-LN200, IMU-HG1900 or IMU-µIMU, connect pin 5 to pin 9 on the I/O port. This changes the COM2 port protocol to RS-422. •For a system with a FlexPak6 and an IMU-FSAS, IMU-CPT or IMU-KVH1750, connect the FlexPak Y Adapter cable to the FlexPak6 ports labeled COM 2 and I/O . Then, connect the IMU to the FlexPak Y Adapter cable using the IMU interface cable. See Figure 2, Connect FlexPak6 to IMU-KVH1750, IMU-CPT or IMU-FSAS, on page 3.•For a system with a ProPak6, connect the IMU interface cable to the COM3/IMU port. See Figure 3, Connect ProPak6 to UIMU-HG1700, UIMU-LCI, UIMU-LN200, IMU-FSAS, IMU-ISA-100C, IMU-LN200, IMU-HG1900 or IMU-µIMU, on page 4.For additional connection diagrams, see the SPAN on OEM6 User Manual (OM-20000139)available on the NovAtel web site (/support/manuals/).3.Connect a USB cable from the computer to the USB port on the receiver.Make sure you have installed the USB drivers. The USB drivers are available from the NovAtel website at /support/search/items/PC%20Software.To use a serial connection, connect a null modem serial cable from the computer to the COM port on the receiver.For information about using Ethernet to connect to the receiver, see the OEM6 Family Installation and Operation User Manual (OM-20000128) or ProPak6 User Manual (OM-20000148) found on the NovAtel web site (/support/manuals/).4.Connect the GNSS antenna to the antenna port on the receiver using an appropriate antenna cable. Figure 3: Connect ProPak6 to UIMU-HG1700, UIMU-LCI, UIMU-LN200, IMU-FSAS, IMU-ISA-100C,IMU-LN200, IMU-HG1900 or IMU-µIMU5.Connect the power cable to the power port on the receiver.On a FlexPak6 or ProPak6, line up the red mark on the power cable connector with the red mark on the receiver’s power port and insert power cable.If using an IMU-ISA-100C, IMU-ISA-100, IMU-LN200, IMU-HG1900 or IMU-µIMU, connect the IMU power cable to the power port on the IMU.6.Connect the receiver and the IMU to the power supply.The power LED lights when the receiver is properly powered.Table 1: IMU Power Supply Requirements The FlexPak6 requires a power supply that provides 6-36 V DC and is capable of at least 5 W.The ProPak6 requires a power supply that provides 9-36 V DC and is capable of at least 15 W.If you are using the same power supply for the IMU, make sure the voltage range meets the IMU requirements and there is sufficient power for both the receiver and the IMU.If you are using the stack up interface cable (01019013) to connect an IMU-IGM to a FlexPak6, the FlexPak6 provides power to the IMU-IGM.Operation of the SPAN system is not affected by the order in which you power up the IMU and receiver. If you are using custom cables for your installation, rather than the NovAtel cables listed inTable 2, be aware of the following.The FlexPak6 provides an output voltage on pin 4 of COM 2 (POUT) that is at the same voltage as the FlexPak6 power source. To ensure that any equipment you connect to COM 2 will not be damaged, refer to the COM 2 pinout in the OEM6 Family Installation and Operation User Manual found on the NovAtel web site at /support/manuals/.The ProPak6 provides an output voltage on pin 4 of COM1 and COM2 (Vout) that is the samevoltage at the ProPak6 power source. To ensure that any equipment you connect to COM1 orCOM2 will not be damaged, refer to the COM port pinout in the ProPak6 User Manual found on the NovAtel web site at /support/manuals/. On the ProPak6 this output voltage can be turned on or off using the COMVOUT command.Do not use the POUT output voltage to power an IMU.IMU-CPT+9 to +18 V DC iIMU-FSAS+10 to +34 V DC IMU-HG1900+10 to +34 V DC IMU-IGM+10 to +30 V DC IMU-ISA-100IMU-ISA-100C+10 to +34 V DC IMU-KVH1750+9 to +36 V DC IMU-LN200+10 to +34 V DC IMU-µIMU+10 to +34 V DC UIMU-HG1700(AG58 and AG62)+12 to +28 V DC UIMU-LCI+12 to +28 V DC UIMU-LN200+12 to +28 V DCIf the receiver is installed in a vehicle, it is recommended that a dedicated battery be provided for the receiver that is isolated from the engine starter battery. When a vehicle engine is started, the voltage on the starter battery can dip to 9.6 V DC or cut-out to ancillary equipment causing the receiver and/or IMU to lose lock and calibration settings.For an alternative power source:a.Cut the 12 V car adapter from the power cable.b.Tie the exposed wires to a DC power supply.c.Install a user supplied 6 A slow blow fuse at the alternate power source to protect the powersupply wiring and your warranty.Be sure to connect the red and orange or green wires to the positive side of the power supply and connect the black and brown or white wires to the negative side of the power supply. Since the 12V car adapter on the supplied adapter cable incorporates a 6A fuse, a usersupplied 6A slow blow fuse in a suitable holder must be used at the alternate power source toprotect both the power supply and your warranty.The car adapter is not recommended for use if your power source is greater than 12V.Vehicle Main BatteryAuxiliary BatteryBattery Isolatorfrom VehicleAlternatorto Vehicle ElectricalSystema.These cables are for the FlexPak6. For information about the cables for other OEM6 receivers, see the OEM6 Family Installation and Operation User Manual (OM-20000128).FlexPak6 to UIMU-LN200, UIMU-HG1700 orUIMU-LCI01018977, Universal IMU Enclosure Interface Cable FlexPak6 to IMU-HG1900, IMU-ISA-100,IMU-ISA-100C, IMU-LN200 or IMU-µIMU01019319, IMU Enclosure Interface Cable IMU-HG1900, IMU-ISA-100, IMU-ISA-100C,IMU-LN200 or IMU-µIMU to power60723136, IMU Enclosure Power Cable FlexPak6 to IMU-CPT 01018966, IMU-CPT Interface Cable and01018948, FlexPak Y Adapter CableFlexPak6 to iIMU-FSAS 01018977, Universal IMU Enclosure Interface Cableand01018948, FlexPak Y Adapter CableFlexPak6 to IMU-IGM 01019013, IMU-IGM Stack Up Cableor01019016, IMU-IGM Interface CableFlexPak6 to IMU-KVH175001019211, IMU-KVH1750 Interface Cableand01018948, FlexPak Y Adapter CableFlexPak6 to computer 60323078, USB A to mini B cableor01017658, Null Modem Serial cableFlexPak6 to antenna User supplied RF antenna cableFlexPak6 to power 01017663, 12 V Power cableFlexPak6 to modem or radio 01018520, Straight Through Serial cableFlexPak6 to additional outputs(e.g. Ethernet, CAN Bus, PPS)01018649, I/O Breakout CableINSTALL THE PC UTILITIES1.Install the NovAtel Connect ™ PC Utilities and USB drivers.CONFIGURE THE SPAN SYSTEMThere are two methods to configure the SPAN system:•Configure SPAN Manually•Configure SPAN Using NovAtel Connect™Configure SPAN ManuallyFollow these steps to enable INS as part of the SPAN system using software commands:a.These cables are for the ProPak6. For information about the cables for other OEM6 receivers, see the OEM6 Family Installation and Operation User Manual (OM-20000128).ProPak6 to UIMU-LN200, UIMU-HG1700,UIMU-LCI or iIMU-FSAS01018977, Universal IMU Enclosure Interface Cable ProPak6 to IMU-HG1900, IMU-ISA-100,IMU-ISA-100C, IMU-LN200 or IMU-µIMU01019319, IMU Enclosure Interface Cable IMU-HG1900, IMU-ISA-100, IMU-ISA-100C,IMU-LN200 or IMU-µIMU to power60723136, IMU Enclosure Power Cable ProPak6 to IMU-CPT01018966, IMU-CPT Interface Cable ProPak6 to IMU-IGM01019016, IMU-IGM Interface Cable ProPak6 to IMU-KVH175001019211, IMU-KVH1750 Interface Cable ProPak6 to computer60323078, USB A to mini B cable or 01017658, Null Modem Serial cable ProPak6 to antennaUser supplied RF antenna cable ProPak6 to power01017663, 12 V Power cable ProPak6 to modem or radio01018520, Straight Through Serial cable ProPak6 I/O port(Event I/O, PPS)01018649, I/O Cable or 01019148, I/O Cable ProPak6 Expansion port(COM7, COM8, COM9, COM10, CAN1, CAN2)01019154, Expansion CableTo access and download the most current version of the NovAtel Connect PC Utilities and USBdrivers, go to the NovAtel website at /support/search/items/PC%20Software .1.Establish a connection to the OEM6 receiver.Refer to the receiver Quick Start Guide for information about connecting to the receiver and entering commands.A GNSS antenna must be connected and tracking satellites for operation.2.Issue the CONNECTIMU command to specify the type of IMU and the receiver port connected to theIMU (see Table 4, CONNECTIMU Commands).Table 4: CONNECTIMU CommandsADIS-16488CONNECTIMU COMx a IMU_ADIS16488HG1700 AG11CONNECTIMU COMx a IMU_HG1700_AG11HG1700 AG17CONNECTIMU COMx a IMU_HG1700_AG17HG1700 AG58CONNECTIMU COMx a IMU_HG1700_AG58HG1700 AG62CONNECTIMU COMx a IMU_HG1700_AG62HG1900 CA50CONNECTIMU COMx a IMU_HG1900_CA50HG1930 CA50CONNECTIMU COMx a IMU_HG1930_CA50iIMU-FSAS CONNECTIMU COMx b IMU_IMAR_FSASIMU-CPT CONNECTIMU COMx b IMU_KVH_COTSIMU-IGM-A1CONNECTIMU COMx a IMU_ADIS16488IMU-IGM-S1CONNECTIMU COMx a IMU_STIM300IMU-ISA-100CONNECTIMU COMx b IMU_ISA100IMU-ISA-100C CONNECTIMU COMx b IMU_ISA100CIMU-ISA-100 (400 Hz)CONNECTIMU COMx b IMU_ISA100_400HZIMU-ISA-100C (400 Hz)CONNECTIMU COMx b IMU_ISA100C_400HZIMU-KVH1725CONNECTIMU COMx b IMU_KVH_1725IMU-KVH1750CONNECTIMU COMx b IMU_KVH_1750IMU-µIMU CONNECTIMU COMx a IMU_LITEF_MICROIMULCI-1CONNECTIMU COMx a IMU_LITEF_LCI1LN-200CONNECTIMU COMx a IMU_LN200STIM300CONNECTIMU COMx a IMU_STIM300a.For systems with a ProPak6 receiver, you must use COM3/IMU for the IMU.For systems with a FlexPak6 receiver, COM2 is the recommended serial port for theIMU, however you can use COM1 or COM2 for these IMUs.If you are using the OEM615+MIC board stack, you must use COM1.b.For the IMU-ISA-100, IMU-ISA-100C, iIMU-FSAS, IMU-CPT, IMU-KVH1725 and IMU-KVH1750, you must use COM2 on the FlexPak6 or COM3/IMU on the ProPak6.Basic configuration of the SPAN system is now complete. The inertial filter starts once the GNSS solution is solved and the IMU is connected.3.Enter the distance from the IMU to the GNSS antenna using the SETIMUTOANTOFFSET command.The offset between the antenna phase center and the IMU axes must remain constant and be known accurately. The X (pitch), Y (roll) and Z (azimuth) directions are clearly marked on the IMU enclosure. The SETIMUTOANTOFFSET parameters are (where the standard deviation fields are optional): x_offset y_offset z_offset [x_stdev] [y_stdev] [z_stdev]A typical RTK GNSS solution is accurate to a few centimetres. For the GNSS+INS system to have this level of accuracy, the offset must be measured to within a centimetre. Any offset error between the two systems shows up directly in the output position. For example, a 10 cm error in recording this offset will result in at least a 10 cm error in the output.If it is impossible to measure the IMU to GNSS antenna offset precisely, the offset can be estimated by carrying out the Lever Arm Calibration Routine. Refer to the SPAN on OEM6 User Manual(OM-20000139) for details.Configure SPAN Using NovAtel Connect ™Follow these steps to enable INS as part of the SPAN system using the NovAtel Connect software utility:1.Start a NovAtel Connect session and establish a connection to the OEM6 receiver.Refer to the receiver Quick Start Guide for information about connecting to the receiver.2.Select Wizards | SPAN Alignment from the NovAtel Connect toolbar. This wizard takes you through thesteps to complete a coarse or kinematic alignment, select the type of IMU and configure the receiver port to accept IMU data.Configuration for AlignmentA coarse alignment routine requires the vehicle to remain stationary for at least 1 minute. If that is not possible, an alternate, kinematic alignment routine is available. The kinematic or moving alignment is performed by estimating the attitude from the GNSS velocity vector and injecting it into the SPAN filter as the initial system attitude. The Lever Arm Calibration Routine is not available for the ADIS-16488, IMU-CPT, IMU-IGM, HG1930 or STIM300 IMUs.Static coarse alignment is not available for the ADIS-16488, IMU-CPT, IMU-IGM, HG1930 or STIM300 IMUs. Use the kinematic alignment instead. Regardless of system configuration and IMU orientation, the SETIMUORIENTATION andVEHICLEBODYROTATION commands must be sent to the receiver before attempting akinematic alignment. See the SPAN on OEM6 Firmware Reference Manual (OM-20000144) for information about these commands.11LOG SPAN DATARaw GNSS, IMU and navigation data (position, velocity, attitude) are available from the system as ASCII or binary logs.Data can be collected through NovAtel Connect using the Logging Control Window , or sent out the receiver COM port to user-supplied data collection software.For post-processing applications, collect the data shown in the Post-Process Data section of this guide.For real-time applications, the GNSS+INS solution is available through the logs listed in the SPAN on OEM6 Firmware Reference Manual (OM-20000144) including INSPOS, INSVEL, INSATT and INSPVA. These logs can be collected at rates up to the IMU data rate; however, there are some rate restrictions. Refer to the Data Collection section in the SPAN Operation chapter of the SPAN on OEM6 User Manual (OM-20000139).OPERATE THE SPAN SYSTEMThe system is ready to go once it is powered and the GNSS and INS are configured using the previously shown commands.Observe the status of the system in the NovAtel Connect INS Window or in the status field of any of the INS solution logs (for example INSPOS, INSVEL, INSATT and INSPVA).If performing a static alignment, allow the system to be stationary for at least 1 minute after the GNSS solution is computed for its initial system alignment. If performing a kinematic alignment, move the vehicle forward at a speed faster than 5 m/s. The following status stages may be observed:•The status changes from INS_INACTIVE through DETERMINING_ORIENTATION,WAITING_INITIALPOS and INS_ALIGNING as the initial alignment routine starts.•The status changes to INS_ALIGNMENT_COMPLETE when the alignment is complete. After some motion (stops, starts and turns), the attitude solution converges to within specifications and the status changes to INS_SOLUTION_GOOD.•The status may occasionally change to INS_SOLUTION_FREE. This status indicates that the inertial solution has detected poor quality GNSS positions from the receiver due to limited satellite visibility or high multipath conditions. The inertial filter may choose to disregard this information and wait for the GNSS quality to improve. The solution is still valid during these times, it is simply a notification that the GNSS+INS solution is more reliable than the GNSS-only solution. INS data is available after the receiver’s time status has reached FINESTEERING. Therefore,an antenna must be connected for the system to function.12POST-PROCESS DATAPost-processing requires collection of simultaneous data from the base and rover stations. This includes accurate coordinates of the base station and accurate measurement of the IMU to antenna separation.Collect the following data for post-processing:•From the base station•RANGECMPB ontime 1•RAWEPHEMB onchanged•GLOEPHEMERISB onchanged (if using GLONASS)•From the rover station(s)•RANGECMPB ontime 1•RAWEPHEMB onchanged•GLOEPHEMERISB onchanged (if using GLONASS)•RAWIMUSXB onnew•IMUTOANTOFFSETSB onchanged•VEHICLEBODYROTATIONB onchanged•HEADINGB onnew (if using ALIGN dual antenna solution)SPAN system output is compatible with Inertial Explorer ® post-processing software from the Waypoint ® Products Group, NovAtel Inc. Visit our website at /products/software/ for details.QUESTIONS OR COMMENTSIf you have any questions or comments regarding your SPAN system, contact NovAtel Customer Service using one of these methodsLog a Case and Search Knowledge :Website:/supportLog a Case, Search Knowledge and View Your Case History : (login required)Web Portal:https:///community/loginEmail :*******************Telephone :U.S. and Canada:1-800-NOVATEL (1-800-668-2835)International:+1-403-295-4900NovAtel, SPAN, OEM6, Inertial Explorer, and Waypoint are registered trademarks of NovAtel Inc.FlexPak6, ProPak6, NovAtel Connect and IMU-IGM are trademarks of NovAtel Inc.Windows is a registered trademark of Microsoft Corporation.© Copyright 2016 NovAtel Inc. All rights reserved.Printed in Canada on recycled paper. Recyclable.Unpublished rights reserved under international copyright laws.。
- 1、下载文档前请自行甄别文档内容的完整性,平台不提供额外的编辑、内容补充、找答案等附加服务。
- 2、"仅部分预览"的文档,不可在线预览部分如存在完整性等问题,可反馈申请退款(可完整预览的文档不适用该条件!)。
- 3、如文档侵犯您的权益,请联系客服反馈,我们会尽快为您处理(人工客服工作时间:9:00-18:30)。
产品特性
Version 4 -Specifications subject to change without notice. ©2010 NovAtel Inc. All rights reserved. ProPak, Inertial Explorer, RT-20, Waypoint and NovAtel are registered trademarks of NovAtel Inc.
SPAN, IMU-FSAS and RT-2 are trademarks of NovAtel Inc.
Printed in Canada. D10150
IMU-FSAS August 2010
想了解该产品的更多信息请访问
/assets/Documents/Papers/FSAS.pdf
1 典型值。
性能规格如GPS 系统的特点,受US DOD 业务退化,电离层和对流层,卫星几何,基线长度,多径效应和有意或无意的
干扰源的影响 2 只有GPS 可用。
3静态收敛后的预计精度 4 当SPAN 的定位模式为RTK 时。
5出口许可限制操作515m/S 6 GNSS 接收机能持续跟踪达4g
7使用IE 后处理如见处理的结果。
.
Statements related to the export of products are based solely on NovAtel’s experience in Canada, are not binding in any way and exportability may be different with respect to the export regulations in effect in another country. The responsibility for re-export of product from a Customer’s facility is solely the responsibility of the Customer.。