合成闸瓦的模压成形工艺
HXD2型大功率机车合成闸瓦热压成型模具优化设计
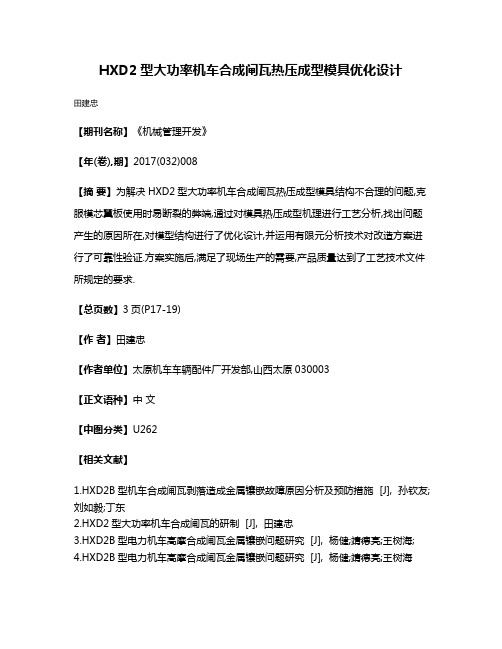
HXD2型大功率机车合成闸瓦热压成型模具优化设计
田建忠
【期刊名称】《机械管理开发》
【年(卷),期】2017(032)008
【摘要】为解决HXD2型大功率机车合成闸瓦热压成型模具结构不合理的问题,克服模芯翼板使用时易断裂的弊端,通过对模具热压成型机理进行工艺分析,找出问题产生的原因所在,对模型结构进行了优化设计,并运用有限元分析技术对改造方案进行了可靠性验证.方案实施后,满足了现场生产的需要,产品质量达到了工艺技术文件所规定的要求.
【总页数】3页(P17-19)
【作者】田建忠
【作者单位】太原机车车辆配件厂开发部,山西太原030003
【正文语种】中文
【中图分类】U262
【相关文献】
1.HXD2B型机车合成闸瓦剥落造成金属镶嵌故障原因分析及预防措施 [J], 孙钦友;刘如毅;丁东
2.HXD2型大功率机车合成闸瓦的研制 [J], 田建忠
3.HXD2B型电力机车高摩合成闸瓦金属镶嵌问题研究 [J], 杨健;靖德亮;王树海;
4.HXD2B型电力机车高摩合成闸瓦金属镶嵌问题研究 [J], 杨健;靖德亮;王树海
5.基于温度场的热压罐成型模具优化设计 [J], 吕佳镁;马贵春;郭靖宇;李云浩;郑俊旺;王政
因版权原因,仅展示原文概要,查看原文内容请购买。
HXD2型大功率机车合成闸瓦热压成型模具优化设计

作者 简介 : 田建忠( 1 9 5 8 一) , 男, 本科, 工程 师 , 从 事铁路机 车
车辆 新 产 品研 发 。
质制做的模芯经热处理后具有强度 、韧性 、淬透性 高、 淬 火 变形 小 、 切 削加 工性 能优 良的特 点 。具 体 操
总第 1 7 2期 2 0 1 7年 第 8 期
机械管理开 发
ME CHANI CAL MANAGEME N T AND D EVE L OP ME NT
T o t a l 1 7 2
No . 8, 2 0 1 7
精 每
D O I : 1 o . 1 6 5 2 5 / j . c n k i . c n l 4 - 1 1 3 4 / t h . 2 0 1 7 . 0 8 . O 8
为了简化模具结构 , 延长模具的使用寿命 , 采用了单 工位分步成型的模具结构型式 , 经 冲裁 、 拉伸 、 弯曲
变形 、弧 面整形 后定 型 ,确保 了钢背成 型 尺 寸 的要 求 。摩擦 体 主要 由丁晴橡 胶 、 酚醛树 脂 、 石墨、 钢 纤维
要牵引动力。合成 闸瓦作为大功率机车制动单元的
模 腔 内的加热 温度 为 1 6 0℃ ±5℃ , 压 力为 1 4 . 5 MP a 。 热 压成 型模 具针 对合 成 闸瓦外 轮廓 成 型尺 寸 主要 靠
外原装合成闸瓦的质量水平 ,同时也符合 国内有关 技术标准的性能指标 ,满足了进 口配件 国产化的总
体要求 。 合成闸瓦在热压成型过程 中, 由于模具在结 构上存在不合理之处 ,造成模芯翼板处断裂现象 时 有发生, 给正常的生产带来严重 困扰 , 因此有必要针 对其结构特点进行综合考量并进行优化设计。
合成材料闸瓦制备技术

合成材料制备技术王秀飞2011年12月wangxf4346@摩擦材料发展史最初的摩擦片采用棉布最初的摩擦片采用棉布、、皮革等作为基材皮革等作为基材;;石棉基摩擦材料石棉基摩擦材料;;无石棉摩擦材料无石棉摩擦材料;;半金属摩擦材料半金属摩擦材料;;粉末冶金摩擦材料粉末冶金摩擦材料;;炭/炭复合摩擦材料炭复合摩擦材料;;炭/碳化硅复合摩擦材料碳化硅复合摩擦材料。
摩擦材料的分类按工作功能分按工作功能分::传动(离合器)和制动(刹车片)摩擦材料材料;;按产品形状按产品形状::刹车片刹车片、、刹车带刹车带、、闸瓦闸瓦、、离合器片和异型摩擦片异型摩擦片;;按材质分按材质分::石棉摩擦材料石棉摩擦材料、、无石棉摩擦材料无石棉摩擦材料、、粉末冶金摩擦材料冶金摩擦材料、、炭/炭复合摩擦材料和炭/碳化硅复合材料铁路摩擦材料种类我国的铁路摩擦材料按其摩擦材料分类,可以分为低摩闸瓦摩闸瓦、、高摩闸瓦高摩闸瓦。
按用途分类:机车用合成闸瓦和闸片机车用合成闸瓦和闸片、、货车用合成闸瓦和闸片以及客车用闸瓦和闸片瓦和闸片以及客车用闸瓦和闸片。
按推广的配方体系分:4-2低摩合成闸瓦低摩合成闸瓦、、4-2w 无石棉低摩合成闸瓦棉低摩合成闸瓦、、机车低摩合成闸瓦机车低摩合成闸瓦;;407G 高摩合成闸瓦闸瓦、、TK-81无石棉高摩合成闸瓦无石棉高摩合成闸瓦;;机车高摩闸瓦机车高摩闸瓦、、HGM-A 新型高摩合成闸瓦新型高摩合成闸瓦、、HGM-B 新型高摩闸瓦新型高摩闸瓦。
摩擦材料的技术要求适宜而稳定的摩擦系数良好的耐磨性具有良好的机械强度和物理性能 制动噪音低对偶面磨损小对摩擦材料的要求☺无石棉无石棉,,无污染化无污染化;;美国环境保护局1983提出禁止使用石棉提出禁止使用石棉,,我国于1999年开始实施GB12676-1999禁止使用石棉禁止使用石棉。
70 年代后期年代后期,,世界卫生组织证实石棉粉尘从呼吸道进入肺内世界卫生组织证实石棉粉尘从呼吸道进入肺内,,经积累可造成石棉肺外累可造成石棉肺外,,石棉还是一种致癌物质石棉还是一种致癌物质。
模压成型工艺过程包括哪些内容
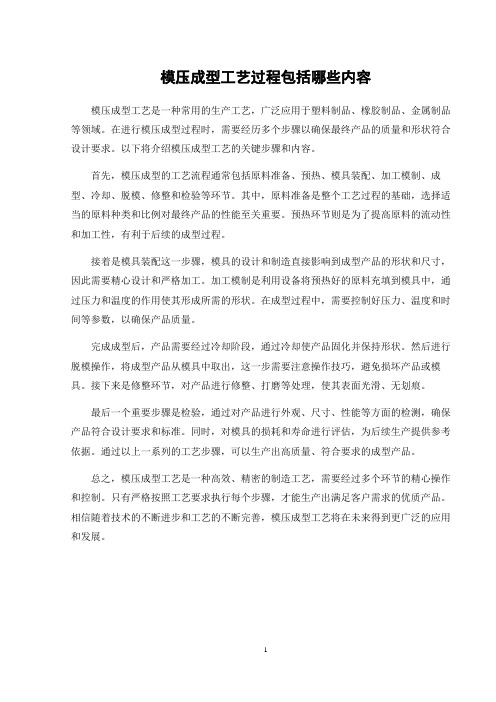
模压成型工艺过程包括哪些内容模压成型工艺是一种常用的生产工艺,广泛应用于塑料制品、橡胶制品、金属制品等领域。
在进行模压成型过程时,需要经历多个步骤以确保最终产品的质量和形状符合设计要求。
以下将介绍模压成型工艺的关键步骤和内容。
首先,模压成型的工艺流程通常包括原料准备、预热、模具装配、加工模制、成型、冷却、脱模、修整和检验等环节。
其中,原料准备是整个工艺过程的基础,选择适当的原料种类和比例对最终产品的性能至关重要。
预热环节则是为了提高原料的流动性和加工性,有利于后续的成型过程。
接着是模具装配这一步骤,模具的设计和制造直接影响到成型产品的形状和尺寸,因此需要精心设计和严格加工。
加工模制是利用设备将预热好的原料充填到模具中,通过压力和温度的作用使其形成所需的形状。
在成型过程中,需要控制好压力、温度和时间等参数,以确保产品质量。
完成成型后,产品需要经过冷却阶段,通过冷却使产品固化并保持形状。
然后进行脱模操作,将成型产品从模具中取出,这一步需要注意操作技巧,避免损坏产品或模具。
接下来是修整环节,对产品进行修整、打磨等处理,使其表面光滑、无划痕。
最后一个重要步骤是检验,通过对产品进行外观、尺寸、性能等方面的检测,确保产品符合设计要求和标准。
同时,对模具的损耗和寿命进行评估,为后续生产提供参考依据。
通过以上一系列的工艺步骤,可以生产出高质量、符合要求的成型产品。
总之,模压成型工艺是一种高效、精密的制造工艺,需要经过多个环节的精心操作和控制。
只有严格按照工艺要求执行每个步骤,才能生产出满足客户需求的优质产品。
相信随着技术的不断进步和工艺的不断完善,模压成型工艺将在未来得到更广泛的应用和发展。
1。
模压成型工艺过程有哪些

模压成型工艺过程有哪些模压成型是一种常见的制造工艺,用于生产各种塑料制品、橡胶制品、金属制品等。
该工艺利用高温和高压将原材料加工成所需形状的制品,广泛应用于汽车零部件、家电配件、建筑材料等领域。
下面将详细介绍模压成型工艺的过程。
材料准备阶段在模压成型工艺中,首先需要准备原材料。
根据所需制品的材质,选择相应的塑料、橡胶或金属材料,并将其加工成固体颗粒、片材或坯料的形式。
在此阶段,还需要确定好原材料的配方和比例,以确保最终制品具有所需的性能和质量。
加热和熔化阶段接下来,将准备好的原材料加入到模具中,然后通过加热设备将模具内的原料加热至熔化温度。
在高温下,原材料逐渐软化、熔化,使其能够充分填充模具的空腔,并保持所需的形状和尺寸。
压力施加阶段一旦原料完全熔化并填充了模具腔体,接下来需要施加高压力以将原料挤压并充分填充模具的所有细节部位。
通过施加足够的压力,可以确保制品表面光滑、结构均匀,避免出现气泡、缺陷等质量问题。
冷却固化阶段当原料充分填充模具并完成成型后,需要立即开始冷却固化过程,以使制品保持所需的形状和尺寸。
通过控制冷却速度和温度,可以有效地控制制品的收缩率和内部组织,确保最终制品具有理想的物理性能和外观质量。
释放和脱模阶段一旦制品完全冷却并固化,模具就可打开,从而释放成型的制品。
在释放时,需要小心地处理以避免损坏制品表面。
有时需要额外的处理步骤,比如修整边缘、去除浮边等。
最终成品可经过一定的质量检查后,进入下一道工序或直接包装出厂。
通过以上几个阶段的工艺过程,模压成型工艺能够高效地生产各种复杂形状的制品,具有成本低、生产效率高、质量稳定等优点,被广泛应用于各种工业生产领域。
随着技术的不断进步和工艺的改进,模压成型在制造业中的地位将变得更加重要,为各行各业提供更多创新的解决方案。
模压工艺的成型原理是什么
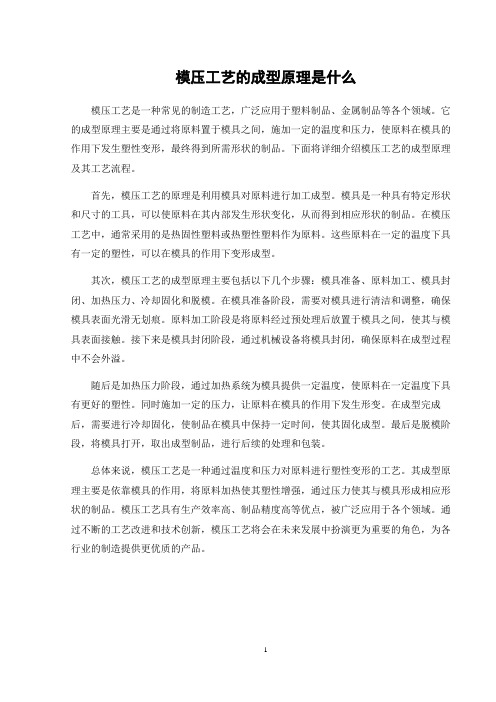
模压工艺的成型原理是什么模压工艺是一种常见的制造工艺,广泛应用于塑料制品、金属制品等各个领域。
它的成型原理主要是通过将原料置于模具之间,施加一定的温度和压力,使原料在模具的作用下发生塑性变形,最终得到所需形状的制品。
下面将详细介绍模压工艺的成型原理及其工艺流程。
首先,模压工艺的原理是利用模具对原料进行加工成型。
模具是一种具有特定形状和尺寸的工具,可以使原料在其内部发生形状变化,从而得到相应形状的制品。
在模压工艺中,通常采用的是热固性塑料或热塑性塑料作为原料。
这些原料在一定的温度下具有一定的塑性,可以在模具的作用下变形成型。
其次,模压工艺的成型原理主要包括以下几个步骤:模具准备、原料加工、模具封闭、加热压力、冷却固化和脱模。
在模具准备阶段,需要对模具进行清洁和调整,确保模具表面光滑无划痕。
原料加工阶段是将原料经过预处理后放置于模具之间,使其与模具表面接触。
接下来是模具封闭阶段,通过机械设备将模具封闭,确保原料在成型过程中不会外溢。
随后是加热压力阶段,通过加热系统为模具提供一定温度,使原料在一定温度下具有更好的塑性。
同时施加一定的压力,让原料在模具的作用下发生形变。
在成型完成后,需要进行冷却固化,使制品在模具中保持一定时间,使其固化成型。
最后是脱模阶段,将模具打开,取出成型制品,进行后续的处理和包装。
总体来说,模压工艺是一种通过温度和压力对原料进行塑性变形的工艺。
其成型原理主要是依靠模具的作用,将原料加热使其塑性增强,通过压力使其与模具形成相应形状的制品。
模压工艺具有生产效率高、制品精度高等优点,被广泛应用于各个领域。
通过不断的工艺改进和技术创新,模压工艺将会在未来发展中扮演更为重要的角色,为各行业的制造提供更优质的产品。
1。
简述模压成型的工艺原理
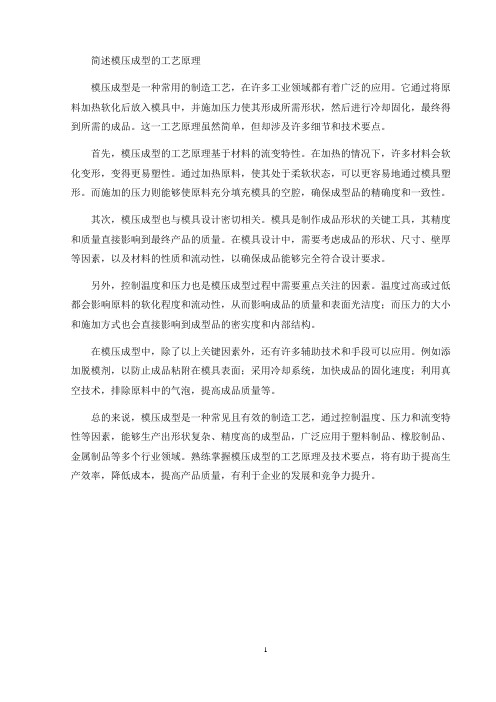
简述模压成型的工艺原理
模压成型是一种常用的制造工艺,在许多工业领域都有着广泛的应用。
它通过将原料加热软化后放入模具中,并施加压力使其形成所需形状,然后进行冷却固化,最终得到所需的成品。
这一工艺原理虽然简单,但却涉及许多细节和技术要点。
首先,模压成型的工艺原理基于材料的流变特性。
在加热的情况下,许多材料会软化变形,变得更易塑性。
通过加热原料,使其处于柔软状态,可以更容易地通过模具塑形。
而施加的压力则能够使原料充分填充模具的空腔,确保成型品的精确度和一致性。
其次,模压成型也与模具设计密切相关。
模具是制作成品形状的关键工具,其精度和质量直接影响到最终产品的质量。
在模具设计中,需要考虑成品的形状、尺寸、壁厚等因素,以及材料的性质和流动性,以确保成品能够完全符合设计要求。
另外,控制温度和压力也是模压成型过程中需要重点关注的因素。
温度过高或过低都会影响原料的软化程度和流动性,从而影响成品的质量和表面光洁度;而压力的大小和施加方式也会直接影响到成型品的密实度和内部结构。
在模压成型中,除了以上关键因素外,还有许多辅助技术和手段可以应用。
例如添加脱模剂,以防止成品粘附在模具表面;采用冷却系统,加快成品的固化速度;利用真空技术,排除原料中的气泡,提高成品质量等。
总的来说,模压成型是一种常见且有效的制造工艺,通过控制温度、压力和流变特性等因素,能够生产出形状复杂、精度高的成型品,广泛应用于塑料制品、橡胶制品、金属制品等多个行业领域。
熟练掌握模压成型的工艺原理及技术要点,将有助于提高生产效率,降低成本,提高产品质量,有利于企业的发展和竞争力提升。
1。
HGM—B型高摩擦系数合成闸瓦成型工艺研究

2 . 2 . 1 成 型 压 力 的影 响
1 性 能测试
1 . 1 仪 器 设 备
铁科研 1: 3制动动力试验 台 ;无锡 X K 一 4 0 0双辊炼胶机 ; 承德 3 9 2 3冲击试验台 ; 2 0 0 t 四柱液压机 ; 西安 C S S 一 1 1 1 0 C万能 试验机 ; XH R 一 1 5 0洛氏硬度计 ; 南京 T G 2 7 9 e型电光分析天平 。
9 5 k r r g h 7 5 k m/ h 5 5 k m/ h 、 3 5 k m/ h 3 5k m/ h 5 5 k m/ h 、 7 5 k m/ h 9 5k m/ h
新 型高摩擦 系数 合成 闸瓦是 目前货 车制动 的重要 配件 , 从 2 0 0 2年开始推广到今 天已经有 1 0多年的时间 ,大量应 用的有 H G M— A和 I - I G M— B两个配方体 系。通 过几年的生产实践 发现 , 压制合成 闸瓦的过程 中容 易 出现摩擦 体表面 的起 泡和裂纹 、 钢 背梅花孔不饱满等现象 , 影响合成 闸瓦的外 观及其使用性能 。 本 文利用差热扫描量热仪 、 万能材料试验 机和 1: 3制动动力试验 台等分析和测试手段 , 系统研究 了 HG M — B型高摩擦系数合成 闸 瓦成型工艺 对其 物理力学性能和摩擦磨损性能 的影 响。
钾长石粉 : 大于 1 0 0目, 氧化钾含量不小 于 7 %; 热塑性酚醛 树脂 ( 2 1 2 3 ) : 京柳 恒业 ; 石墨 ( L 一 1 8 5 ) : 山西南 风 ; 铝 矾土 : 大于 1 5 0目, 氧化铝含量 大于 7 0 %, 山西灵丘 ; 丁腈橡胶 ( 2 6 ) : 兰州化 工; 沉淀硫 酸钡 : 1 0 0目, 河北辛 集 ; 海泡石 : 河北 明阳公 司 A型 等。 1 . 3 综 合 测 试 压 缩 强 度 :样 品 2 0 X 1 0 X 1 0 m m, 速 度 1 m m / mi n
闸瓦制造工艺流程

闸瓦制造工艺流程闸瓦制造工艺流程闸瓦是一种用于闸门启闭的重要零部件,通常由金属材料制成。
下面是闸瓦制造的工艺流程。
1. 原材料准备:选择合适的金属材料,通常使用耐磨性能好的合金钢或不锈钢。
这些材料应具有良好的耐腐蚀性和机械性能。
然后进行材料切割和钝化处理,以便于下一步的加工。
2. 加工成型:根据设计图纸,使用数控机床或其他加工设备对原材料进行加工成型。
首先进行锻造或压制,将材料加热至适当的温度后进行塑性变形,以获得所需形状和尺寸。
然后进行粗加工,包括车削、铣削以及镗削等工序。
3. 热处理:将已成型的闸瓦进行热处理,以提高其机械性能和耐磨性。
热处理工艺通常包括退火、正火和淬火等过程。
退火可以消除内部应力并提高材料的塑性。
正火可以增加材料的硬度和强度。
淬火则可以使材料产生高硬度的表面,并提高其耐磨性。
4. 进一步加工:热处理后的闸瓦需要进行进一步的加工,以提供更精确的尺寸和表面质量。
这些加工包括钻孔、修整、磨削和抛光等工序。
通过这些加工,可以保证闸瓦的尺寸和形状符合设计要求,表面光滑,无明显缺陷。
5. 表面处理:为了提高闸瓦的耐腐蚀性,需要进行表面处理。
常用的表面处理方法包括镀锌、喷涂和电镀等。
镀锌可以在闸瓦表面形成一层锌层,提供良好的耐腐蚀性。
喷涂可以使用聚合物涂料对闸瓦进行表面覆盖,提供保护。
电镀则可以在闸瓦表面形成一层金属保护层。
6. 检测和质量控制:在制造过程中,需要进行各种检测以确保闸瓦的质量。
常用的检测方法包括尺寸检测、磨损测试和硬度测试等。
通过这些检测,可以及时发现和纠正潜在的质量问题,并保证闸瓦的质量符合要求。
7. 成品包装:最后,经过检测合格的闸瓦需要进行包装,以保护其表面免受损坏和腐蚀。
通常使用塑料袋或纸箱进行包装,并在包装上标注相关信息,如产品型号、批次号和生产日期等。
以上就是闸瓦制造的工艺流程。
通过严格控制每个环节的质量,可以确保生产出高质量的闸瓦,以满足各种工程项目的需求。
模压成型的工艺过程有哪些内容
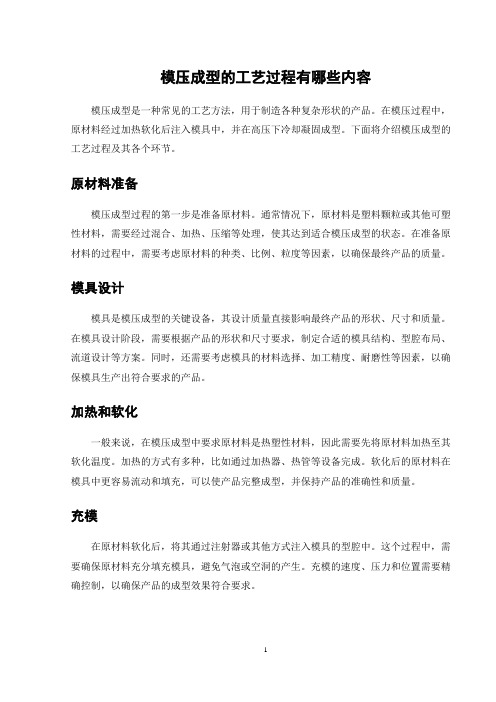
模压成型的工艺过程有哪些内容模压成型是一种常见的工艺方法,用于制造各种复杂形状的产品。
在模压过程中,原材料经过加热软化后注入模具中,并在高压下冷却凝固成型。
下面将介绍模压成型的工艺过程及其各个环节。
原材料准备模压成型过程的第一步是准备原材料。
通常情况下,原材料是塑料颗粒或其他可塑性材料,需要经过混合、加热、压缩等处理,使其达到适合模压成型的状态。
在准备原材料的过程中,需要考虑原材料的种类、比例、粒度等因素,以确保最终产品的质量。
模具设计模具是模压成型的关键设备,其设计质量直接影响最终产品的形状、尺寸和质量。
在模具设计阶段,需要根据产品的形状和尺寸要求,制定合适的模具结构、型腔布局、流道设计等方案。
同时,还需要考虑模具的材料选择、加工精度、耐磨性等因素,以确保模具生产出符合要求的产品。
加热和软化一般来说,在模压成型中要求原材料是热塑性材料,因此需要先将原材料加热至其软化温度。
加热的方式有多种,比如通过加热器、热管等设备完成。
软化后的原材料在模具中更容易流动和填充,可以使产品完整成型,并保持产品的准确性和质量。
充模在原材料软化后,将其通过注射器或其他方式注入模具的型腔中。
这个过程中,需要确保原材料充分填充模具,避免气泡或空洞的产生。
充模的速度、压力和位置需要精确控制,以确保产品的成型效果符合要求。
施加压力一旦原材料充分注入模具,就需要施加高压力使其充分填充模具型腔,并保持一定时间以确保原材料的冷却凝固。
施加的压力大小需要根据产品的形状、尺寸和要求来确定,过高或过低都可能导致产品出现瑕疵。
冷却固化在原材料充分填充模具并施加压力后,需要等待一定时间让原材料冷却固化。
冷却的速度和时间取决于原材料的种类和厚度,一般情况下需要精确控制以确保产品质量。
在冷却固化的过程中,模具温度、环境温度和湿度等因素都会对产品的质量产生影响。
脱模当原材料冷却固化后,就可以进行脱模操作。
脱模时需要小心翼翼地分离模具和产品,避免产品损坏或形状不规则。
论述模压成型的工艺流程有哪些

论述模压成型的工艺流程有哪些模压成型作为一种常见的制造工艺,被广泛应用于各种行业,如汽车制造、电子产品生产等。
其工艺流程相对复杂,涉及多个环节的操作和控制。
以下将详细介绍模压成型的工艺流程。
首先,模具设计是模压成型的第一步,决定了最终产品的形状和尺寸。
模具设计师需要根据产品的要求和材料特性,设计出合适的模具结构。
这一步需要考虑到产品的几何形状、壁厚、收缩率等因素,并进行相关的计算和模拟。
其次,原料准备是模压成型的重要环节。
在进行模压成型之前,需要准备好所需的原料,通常是塑料颗粒或其他成型材料。
这些原料需要按照一定的配比准备好,并在一定的温度下进行熔融,以便后续的成型操作。
接着,注塑是模压成型中的关键步骤之一。
在注塑过程中,将熔融的原料注入到模具中,通过高压力将原料充分填充模具腔体,使其在模具中形成所需的产品形状。
注塑操作需要控制注射速度、压力和温度等参数,以确保产品质量。
然后,冷却是模压成型中一个至关重要的阶段。
在注塑完成后,模具中的产品需要进行充分冷却,以确保产品在脱模后能够保持其形状和尺寸稳定。
冷却的过程需要控制冷却时间和方式,通常会采用冷却水或其他冷却介质来进行。
最后,脱模是模压成型的最后一步,也是产品从模具中取出的关键环节。
通过脱模机构将产品从模具中取出,并进行后续的处理,如修边、清洁等。
脱模需要考虑产品与模具的配合间隙,以防产品变形或损坏。
总的来说,模压成型的工艺流程经过模具设计、原料准备、注塑、冷却和脱模等多个环节的操作和控制。
每个环节都至关重要,需要严格控制各项参数,以确保最终产品的质量和性能。
随着制造技术的进步,模压成型工艺也在不断演进,为各行各业的生产提供更加高效、精密的制造解决方案。
1。
模压成型工艺过程包括哪些
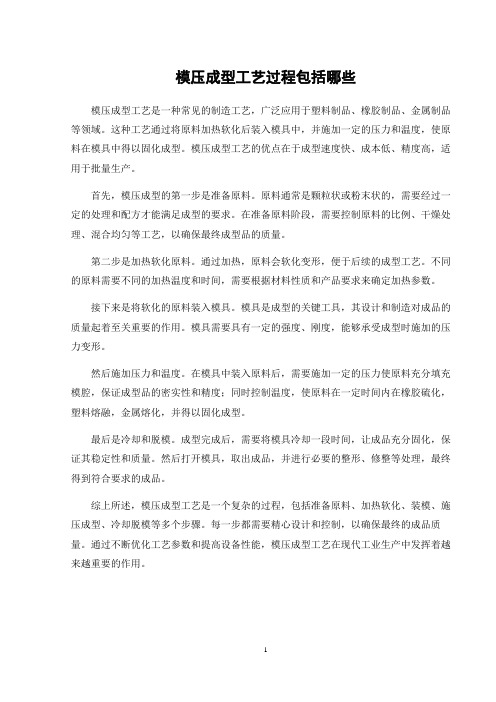
模压成型工艺过程包括哪些模压成型工艺是一种常见的制造工艺,广泛应用于塑料制品、橡胶制品、金属制品等领域。
这种工艺通过将原料加热软化后装入模具中,并施加一定的压力和温度,使原料在模具中得以固化成型。
模压成型工艺的优点在于成型速度快、成本低、精度高,适用于批量生产。
首先,模压成型的第一步是准备原料。
原料通常是颗粒状或粉末状的,需要经过一定的处理和配方才能满足成型的要求。
在准备原料阶段,需要控制原料的比例、干燥处理、混合均匀等工艺,以确保最终成型品的质量。
第二步是加热软化原料。
通过加热,原料会软化变形,便于后续的成型工艺。
不同的原料需要不同的加热温度和时间,需要根据材料性质和产品要求来确定加热参数。
接下来是将软化的原料装入模具。
模具是成型的关键工具,其设计和制造对成品的质量起着至关重要的作用。
模具需要具有一定的强度、刚度,能够承受成型时施加的压力变形。
然后施加压力和温度。
在模具中装入原料后,需要施加一定的压力使原料充分填充模腔,保证成型品的密实性和精度;同时控制温度,使原料在一定时间内在橡胶硫化,塑料熔融,金属熔化,并得以固化成型。
最后是冷却和脱模。
成型完成后,需要将模具冷却一段时间,让成品充分固化,保证其稳定性和质量。
然后打开模具,取出成品,并进行必要的整形、修整等处理,最终得到符合要求的成品。
综上所述,模压成型工艺是一个复杂的过程,包括准备原料、加热软化、装模、施压成型、冷却脱模等多个步骤。
每一步都需要精心设计和控制,以确保最终的成品质量。
通过不断优化工艺参数和提高设备性能,模压成型工艺在现代工业生产中发挥着越来越重要的作用。
1。
闸瓦制造工艺流程
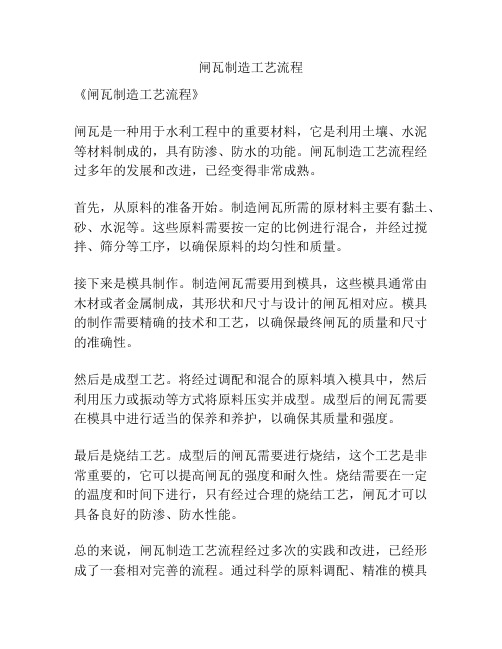
闸瓦制造工艺流程
《闸瓦制造工艺流程》
闸瓦是一种用于水利工程中的重要材料,它是利用土壤、水泥等材料制成的,具有防渗、防水的功能。
闸瓦制造工艺流程经过多年的发展和改进,已经变得非常成熟。
首先,从原料的准备开始。
制造闸瓦所需的原材料主要有黏土、砂、水泥等。
这些原料需要按一定的比例进行混合,并经过搅拌、筛分等工序,以确保原料的均匀性和质量。
接下来是模具制作。
制造闸瓦需要用到模具,这些模具通常由木材或者金属制成,其形状和尺寸与设计的闸瓦相对应。
模具的制作需要精确的技术和工艺,以确保最终闸瓦的质量和尺寸的准确性。
然后是成型工艺。
将经过调配和混合的原料填入模具中,然后利用压力或振动等方式将原料压实并成型。
成型后的闸瓦需要在模具中进行适当的保养和养护,以确保其质量和强度。
最后是烧结工艺。
成型后的闸瓦需要进行烧结,这个工艺是非常重要的,它可以提高闸瓦的强度和耐久性。
烧结需要在一定的温度和时间下进行,只有经过合理的烧结工艺,闸瓦才可以具备良好的防渗、防水性能。
总的来说,闸瓦制造工艺流程经过多次的实践和改进,已经形成了一套相对完善的流程。
通过科学的原料调配、精准的模具
制作、严格的成型和烧结工艺,可以生产出质量优良的闸瓦产品,为水利工程提供了可靠的保障。