电解铜箔生产实践的关键
电解铜箔 书 -回复

电解铜箔书-回复电解铜箔的生产工艺及应用。
引言:电解铜箔是一种具有高纯度、均匀性好、成本低廉的精密电子材料,广泛应用于电子和通信行业。
本文将从电解铜箔的生产工艺、性能特点及应用领域三个方面进行详细介绍。
一、电解铜箔的生产工艺电解铜箔的生产工艺主要包括原料准备、电解制备和加工。
首先是原料准备,合理选择原料对电解铜箔的质量和性能具有重要影响。
常用的原料是高纯铜,通过熔炼和精炼等工艺处理,去除杂质和气体,以提高铜箔的纯度。
其次是电解制备,将经过高温处理的高纯铜片置于硫酸和铜离子溶液中,通过电解反应将铜离子还原成金属铜沉积在阴极上。
最后是加工,将电解得到的铜箔经过轧制、退火、切割等工艺加工,使其达到不同精度和尺寸的要求。
二、电解铜箔的性能特点1.高纯度:电解铜箔的纯度通常在99.8以上,可达到甚至超过99.9,确保了其优良的导电性能和电子能带结构的稳定性。
2.均匀性好:电解制备的铜箔具有均匀的厚度分布和细致的晶粒结构,提高了其机械加工性能和界面连接的可靠性。
3.良好的延展性:电解铜箔具有良好的延展性,可进行复杂形状的冲压和折弯加工,在电子器件的封装和连接中具有重要作用。
4.低氧含量:电解铜箔经过合适的退火处理,其氧含量较低,以满足一些对低氧含量要求较高的应用场景。
5.自脱附降解性:电解铜箔的表面附着性较弱,易于剥离,使其在电路板制造和三维封装等领域具有独特的应用优势。
三、电解铜箔的应用领域电解铜箔作为一种重要的电子材料,在通信、计算机、消费电子和光电子等领域具有广泛的应用。
1.印制电路板(PCB):电解铜箔作为PCB的重要材料,用于制作电路导线和接触片,满足高速传输和高频信号处理的需求。
2.电子封装:电解铜箔在电子封装中用于制作波导、隔热板、连接片等组件,提高电子器件的散热性能和连接可靠性。
3.太阳能电池板:电解铜箔在太阳能电池板制造中作为电极材料,提高能量转化效率和稳定性。
4.显示器制造:电解铜箔用于制作显示器的背板、导电层和电磁屏蔽层,提高显示效果和抗干扰能力。
电解铜箔常见问题及解决对策分析
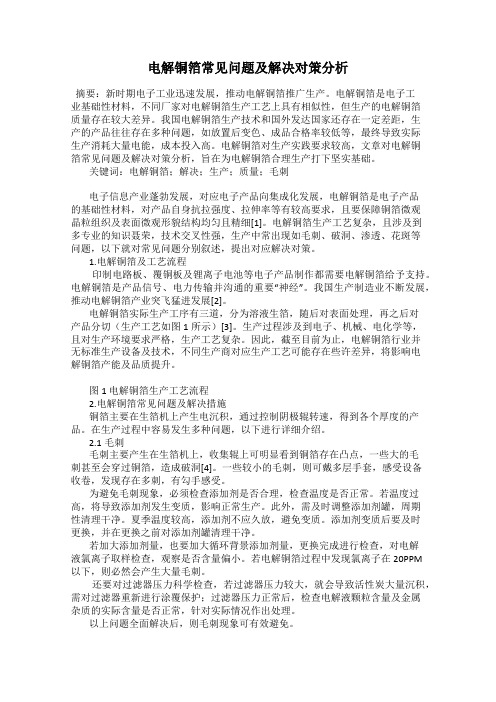
电解铜箔常见问题及解决对策分析摘要:新时期电子工业迅速发展,推动电解铜箔推广生产。
电解铜箔是电子工业基础性材料,不同厂家对电解铜箔生产工艺上具有相似性,但生产的电解铜箔质量存在较大差异。
我国电解铜箔生产技术和国外发达国家还存在一定差距,生产的产品往往存在多种问题,如放置后变色、成品合格率较低等,最终导致实际生产消耗大量电能,成本投入高。
电解铜箔对生产实践要求较高,文章对电解铜箔常见问题及解决对策分析,旨在为电解铜箔合理生产打下坚实基础。
关键词:电解铜箔;解决;生产;质量;毛刺电子信息产业蓬勃发展,对应电子产品向集成化发展,电解铜箔是电子产品的基础性材料,对产品自身抗拉强度、拉伸率等有较高要求,且要保障铜箔微观晶粒组织及表面微观形貌结构均匀且精细[1]。
电解铜箔生产工艺复杂,且涉及到多专业的知识聂荣,技术交叉性强,生产中常出现如毛刺、破洞、渗透、花斑等问题,以下就对常见问题分别叙述,提出对应解决对策。
1.电解铜箔及工艺流程印制电路板、覆铜板及锂离子电池等电子产品制作都需要电解铜箔给予支持。
电解铜箔是产品信号、电力传输并沟通的重要“神经”。
我国生产制造业不断发展,推动电解铜箔产业突飞猛进发展[2]。
电解铜箔实际生产工序有三道,分为溶液生箔,随后对表面处理,再之后对产品分切(生产工艺如图1所示)[3]。
生产过程涉及到电子、机械、电化学等,且对生产环境要求严格,生产工艺复杂。
因此,截至目前为止,电解铜箔行业并无标准生产设备及技术,不同生产商对应生产工艺可能存在些许差异,将影响电解铜箔产能及品质提升。
图1 电解铜箔生产工艺流程2.电解铜箔常见问题及解决措施铜箔主要在生箔机上产生电沉积,通过控制阴极辊转速,得到各个厚度的产品。
在生产过程中容易发生多种问题,以下进行详细介绍。
2.1毛刺毛刺主要产生在生箔机上,收集辊上可明显看到铜箔存在凸点,一些大的毛刺甚至会穿过铜箔,造成破洞[4]。
一些较小的毛刺,则可戴多层手套,感受设备收卷,发现存在多刺,有勾手感受。
电解铜箔制作工艺

电解铜箔制作工艺电解铜箔制作工艺是一种常见的金属加工工艺,用于制造电子元器件、半导体器件、印刷线路板等产品。
本文将介绍电解铜箔制作的工艺流程和关键技术。
一、电解铜箔制作工艺流程电解铜箔制作的基本工艺流程包括:基材准备、腐蚀清洗、电镀铜、镀锡、退火、切割、检验等环节。
1. 基材准备基材通常采用纯铜板或铜合金板,要求表面平整、无裂纹和氧化层。
在基材表面涂覆一层保护膜,以防止腐蚀。
2. 腐蚀清洗将基材放入腐蚀液中进行腐蚀清洗,去除基材表面的氧化层和杂质。
腐蚀液的成分和浓度需要根据不同的工艺要求进行调整,以保证清洗效果。
3. 电镀铜腐蚀清洗后的基材放入电解槽中,通过电解作用,将铜离子还原成铜金属,沉积在基材表面形成铜箔。
电解液通常由铜盐、酸、添加剂等组成,其中的添加剂可以调节电流密度、控制铜箔的颗粒度和光亮度等特性。
4. 镀锡电镀铜箔表面镀一层锡,提高铜箔的焊接性能和抗氧化性能。
镀锡工艺包括预处理、电解镀锡和后处理等步骤。
5. 退火为了消除电解铜箔中的应力和改善铜箔的机械性能,需要进行退火处理。
退火温度和时间要根据铜箔的厚度和要求进行合理选择,通常在氮气气氛中进行。
6. 切割将退火后的铜箔切割成所需尺寸的铜箔片。
切割方法有机械切割和激光切割两种,根据生产规模和要求选择合适的切割方式。
7. 检验对切割后的铜箔进行质量检验,包括外观检查、尺寸检测、化学成分分析、机械性能测试等。
只有合格的铜箔才能用于下一道工序或交付客户。
二、电解铜箔制作的关键技术1. 电解液的配方和调控技术:电解液的成分和浓度对铜箔的质量和性能有重要影响,需要根据要求进行合理配方和调控。
2. 电解工艺参数的控制:包括电流密度、电解时间、温度等参数的控制,对铜箔的厚度、颗粒度、光亮度等都有影响。
3. 腐蚀清洗技术:腐蚀清洗的时间和腐蚀液的选择都是影响清洗效果的关键因素,需要经验丰富的操作人员进行控制。
4. 镀锡工艺:镀锡层的厚度和均匀性对铜箔的性能有重要影响,需要控制电镀时间、镀锡液的成分和温度等参数。
电解铜箔的生产与技术讲座
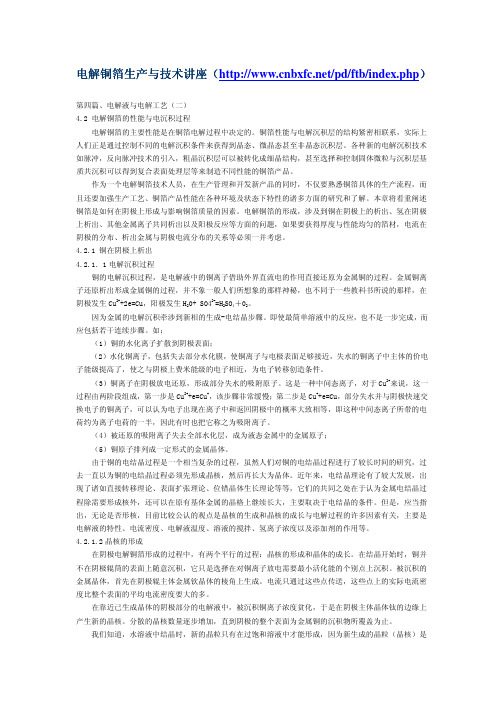
电解铜箔生产与技术讲座电解铜箔生产与技术讲座((/pd/ftb/index.php ) 第四篇、电解液与电解工艺(二)4.2 电解铜箔的性能与电沉积过程电解铜箔的主要性能是在铜箔电解过程中决定的。
铜箔性能与电解沉积层的结构紧密相联系,实际上人们正是通过控制不同的电解沉积条件来获得到晶态、微晶态甚至非晶态沉积层。
各种新的电解沉积技术如脉冲,反向脉冲技术的引入,粗晶沉积层可以被转化成细晶结构,甚至选择和控制固体微粒与沉积层基质共沉积可以得到复合表面处理层等来制造不同性能的铜箔产品。
作为一个电解铜箔技术人员,在生产管理和开发新产品的同时,不仅要熟悉铜箔具体的生产流程,而且还要加强生产工艺、铜箔产品性能在各种环境及状态下特性的诸多方面的研究和了解。
本章将着重阐述铜箔是如何在阴极上形成与影响铜箔质量的因素。
电解铜箔的形成,涉及到铜在阴极上的析出、氢在阴极上析出、其他金属离子共同析出以及阳极反应等方面的问题,如果要获得厚度与性能均匀的箔材,电流在阴极的分布、析出金属与阴极电流分布的关系等必须一并考虑。
4.2.1 铜在阴极上析出4.2.1.1电解沉积过程铜的电解沉积过程,是电解液中的铜离子借助外界直流电的作用直接还原为金属铜的过程。
金属铜离子还原析出形成金属铜的过程,并不象一般人们所想象的那样神秘,也不同于一些教科书所说的那样,在阴极发生Cu 2++2e=Cu,阳极发生H 20+ SO42-=H 2SO 4+02。
因为金属的电解沉积牵涉到新相的生成-电结晶步骤。
即使最简单溶液中的反应,也不是一步完成,而应包括若干连续步骤。
如:(1)铜的水化离子扩散到阴极表面;(2)水化铜离子,包括失去部分水化膜,使铜离子与电极表面足够接近,失水的铜离子中主体的价电子能级提高了,使之与阴极上费米能级的电子相近,为电子转移创造条件。
(3)铜离子在阴极放电还原,形成部分失水的吸附原子。
这是一种中间态离子,对于Cu 2+来说,这一过程由两阶段组成,第一步是Cu 2++e=Cu +,该步骤非常缓慢;第二步是Cu ++e=Cu,部分失水并与阴极快速交换电子的铜离子,可以认为电子出现在离子中和返回阴极中的概率大致相等,即这种中间态离子所带的电荷约为离子电荷的一半,因此有时也把它称之为吸附离子。
电解铜箔的生产与技术讲座
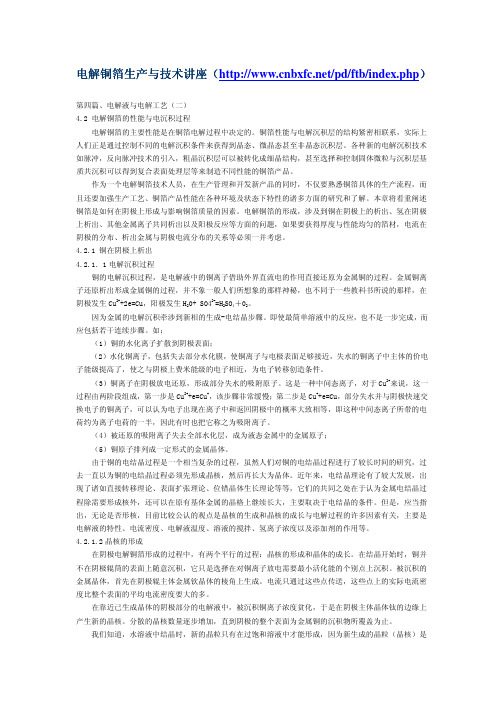
电解铜箔生产与技术讲座电解铜箔生产与技术讲座((/pd/ftb/index.php ) 第四篇、电解液与电解工艺(二)4.2 电解铜箔的性能与电沉积过程电解铜箔的主要性能是在铜箔电解过程中决定的。
铜箔性能与电解沉积层的结构紧密相联系,实际上人们正是通过控制不同的电解沉积条件来获得到晶态、微晶态甚至非晶态沉积层。
各种新的电解沉积技术如脉冲,反向脉冲技术的引入,粗晶沉积层可以被转化成细晶结构,甚至选择和控制固体微粒与沉积层基质共沉积可以得到复合表面处理层等来制造不同性能的铜箔产品。
作为一个电解铜箔技术人员,在生产管理和开发新产品的同时,不仅要熟悉铜箔具体的生产流程,而且还要加强生产工艺、铜箔产品性能在各种环境及状态下特性的诸多方面的研究和了解。
本章将着重阐述铜箔是如何在阴极上形成与影响铜箔质量的因素。
电解铜箔的形成,涉及到铜在阴极上的析出、氢在阴极上析出、其他金属离子共同析出以及阳极反应等方面的问题,如果要获得厚度与性能均匀的箔材,电流在阴极的分布、析出金属与阴极电流分布的关系等必须一并考虑。
4.2.1 铜在阴极上析出4.2.1.1电解沉积过程铜的电解沉积过程,是电解液中的铜离子借助外界直流电的作用直接还原为金属铜的过程。
金属铜离子还原析出形成金属铜的过程,并不象一般人们所想象的那样神秘,也不同于一些教科书所说的那样,在阴极发生Cu 2++2e=Cu,阳极发生H 20+ SO42-=H 2SO 4+02。
因为金属的电解沉积牵涉到新相的生成-电结晶步骤。
即使最简单溶液中的反应,也不是一步完成,而应包括若干连续步骤。
如:(1)铜的水化离子扩散到阴极表面;(2)水化铜离子,包括失去部分水化膜,使铜离子与电极表面足够接近,失水的铜离子中主体的价电子能级提高了,使之与阴极上费米能级的电子相近,为电子转移创造条件。
(3)铜离子在阴极放电还原,形成部分失水的吸附原子。
这是一种中间态离子,对于Cu 2+来说,这一过程由两阶段组成,第一步是Cu 2++e=Cu +,该步骤非常缓慢;第二步是Cu ++e=Cu,部分失水并与阴极快速交换电子的铜离子,可以认为电子出现在离子中和返回阴极中的概率大致相等,即这种中间态离子所带的电荷约为离子电荷的一半,因此有时也把它称之为吸附离子。
电解铜箔生产实践的关键

电解铜箔生产实践的关键,是通过应用一系列的生产技术和技巧,来控制铜箔的质量满足要求。
众所周知,国际标准IPC4562将印制线路用金属电解铜箔按照特性的质量保证水平差异分为三级:1级:适用于要求电路功能完整,机械性能和外观缺陷不重要的应用场合。
2级:适用于电路设计、工艺及规范一致性要求允许局部区域不一致的应用场合。
3级:适用于要求保证等级最高的应用场合。
在这三个等级中,3级的质量保证水平最高,2级的质量保证水平适中,1级的质量保证水平最低。
电解铜箔的质量缺陷主要有外观缺陷(箔材存在针孔和气隙度,麻点和压痕,缺口和撕裂,皱折,划痕)、尺寸缺陷(面积质量及厚度及偏差,箔轮廓超标)、物理性能缺陷(拉伸强度,疲劳延展性,延伸率,剥离强度,载体分离强度,金属箔表面粗糙度不能满足要求)、工艺性能不能满足要求(可蚀刻性,可焊性)以及其它性能(如纯度、质量电阻率)。
电解铜箔的最终性能,除剥离强度、可焊性等个别指标外,大多数是由生箔的性能所决定的。
而这些性能,如拉伸强度、疲劳延展性、延伸率、金属箔表面粗糙度等均与生箔(毛箔)的晶体学织构有关。
材料的晶体学织构表达了组成晶体材料的无数晶粒的取向分布方式。
晶体的每个晶粒都是各向异性的,即其性能随着测量方位的变化而变化。
用于测量这种晶体学织构的传统方法是X射线衍射法。
在大多数工程材料及常用电沉积层中,其正常晶体的取向为优势取向,这就是所谓残余各向异性,电解铜箔的织构与其自身的沉积过程密切相关,电解沉积层的形成是由形核及晶体长大两个不同的过程所控制的,而织构的发展也可能是这两个过程相互竞争的结果。
沉积超电势及间接影响超电势的每个工艺参数,如流体动力学,添加剂等在织构形成中起着首要作用。
有关研究表明,电解铜箔的生箔铜箔在小于12μm的情况下,XRD衍射图谱中的主峰为(111)面,并目(311)面呈现一定的择优取向。
随着厚度的增加,其(220)衍射峰强度不断提高,其他晶面衍射强度则逐渐降低,当铜箔厚度达到21μm时,(220)晶面的织构系数达到92%。
电解铜箔和压延铜箔的生产方式
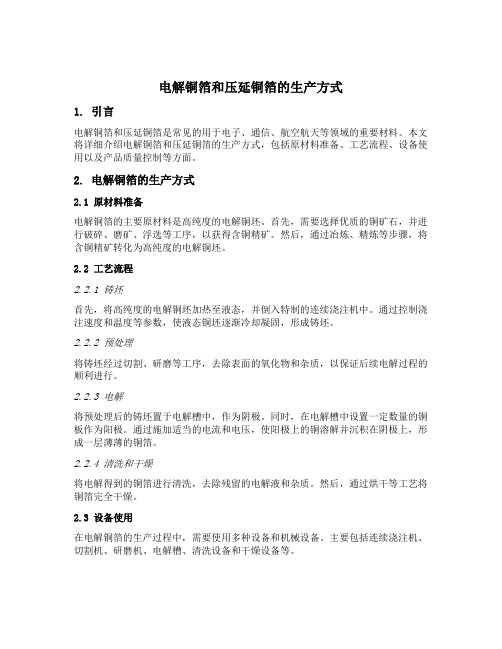
电解铜箔和压延铜箔的生产方式1. 引言电解铜箔和压延铜箔是常见的用于电子、通信、航空航天等领域的重要材料。
本文将详细介绍电解铜箔和压延铜箔的生产方式,包括原材料准备、工艺流程、设备使用以及产品质量控制等方面。
2. 电解铜箔的生产方式2.1 原材料准备电解铜箔的主要原材料是高纯度的电解铜坯。
首先,需要选择优质的铜矿石,并进行破碎、磨矿、浮选等工序,以获得含铜精矿。
然后,通过冶炼、精炼等步骤,将含铜精矿转化为高纯度的电解铜坯。
2.2 工艺流程2.2.1 铸坯首先,将高纯度的电解铜坯加热至液态,并倒入特制的连续浇注机中。
通过控制浇注速度和温度等参数,使液态铜坯逐渐冷却凝固,形成铸坯。
2.2.2 预处理将铸坯经过切割、研磨等工序,去除表面的氧化物和杂质,以保证后续电解过程的顺利进行。
2.2.3 电解将预处理后的铸坯置于电解槽中,作为阴极。
同时,在电解槽中设置一定数量的铜板作为阳极。
通过施加适当的电流和电压,使阳极上的铜溶解并沉积在阴极上,形成一层薄薄的铜箔。
2.2.4 清洗和干燥将电解得到的铜箔进行清洗,去除残留的电解液和杂质。
然后,通过烘干等工艺将铜箔完全干燥。
2.3 设备使用在电解铜箔的生产过程中,需要使用多种设备和机械设备。
主要包括连续浇注机、切割机、研磨机、电解槽、清洗设备和干燥设备等。
2.4 产品质量控制为确保生产出高质量的电解铜箔,需要进行严格的质量控制。
主要包括原材料的选择和检验、工艺参数的控制、产品表面质量的检测以及性能测试等。
同时,还需要建立健全的质量管理体系,对生产过程进行监控和改进。
3. 压延铜箔的生产方式3.1 原材料准备压延铜箔的主要原材料是电解铜箔。
通常,生产压延铜箔时会选择较薄的电解铜箔作为起始材料。
3.2 工艺流程3.2.1 加热和退火首先,将电解铜箔置于加热炉中进行加热,使其达到适当温度。
然后,进行退火处理,以提高铜箔的延展性和可塑性。
3.2.2 压延将经过退火处理的电解铜箔送入压延机中进行压下操作。
电解铜箔生产自动化关键技术及应用

电解铜箔生产自动化关键技术及应用文档下载说明Download tips: This document is carefully compiled by this editor. I hope that after you download it, it can help you solve practical problems. The document 电解铜箔生产自动化关键技术及应用can be customized and modified after downloading, please adjust and use it according to actual needs, thank you! In addition, this shop provides you with various types of practical materials, such as educational essays, diary appreciation, sentence excerpts, ancient poems, classic articles, topic composition, work summary, word parsing, copy excerpts, other materials and so on, want to know different data formats and writing methods, please pay attention!电解铜箔生产自动化是现代工业领域的重要发展方向之一。
随着科技的不断进步,自动化技术在各个行业都得到了广泛应用,而电解铜箔生产也不例外。
本文将探讨电解铜箔生产自动化的关键技术及其应用。
1. 自动化控制系统。
自动化控制系统是电解铜箔生产自动化的核心。
该系统通过传感器、执行器和控制器实现对生产过程的监测、控制和调节。
其中,关键技术包括。
电解铜箔制造过程及其生产原理
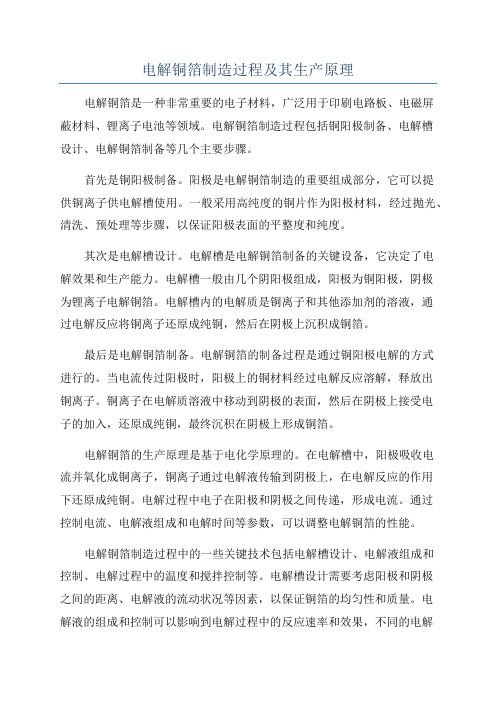
电解铜箔制造过程及其生产原理电解铜箔是一种非常重要的电子材料,广泛用于印刷电路板、电磁屏蔽材料、锂离子电池等领域。
电解铜箔制造过程包括铜阳极制备、电解槽设计、电解铜箔制备等几个主要步骤。
首先是铜阳极制备。
阳极是电解铜箔制造的重要组成部分,它可以提供铜离子供电解槽使用。
一般采用高纯度的铜片作为阳极材料,经过抛光、清洗、预处理等步骤,以保证阳极表面的平整度和纯度。
其次是电解槽设计。
电解槽是电解铜箔制备的关键设备,它决定了电解效果和生产能力。
电解槽一般由几个阴阳极组成,阳极为铜阳极,阴极为锂离子电解铜箔。
电解槽内的电解质是铜离子和其他添加剂的溶液,通过电解反应将铜离子还原成纯铜,然后在阴极上沉积成铜箔。
最后是电解铜箔制备。
电解铜箔的制备过程是通过铜阳极电解的方式进行的。
当电流传过阳极时,阳极上的铜材料经过电解反应溶解,释放出铜离子。
铜离子在电解质溶液中移动到阴极的表面,然后在阴极上接受电子的加入,还原成纯铜,最终沉积在阴极上形成铜箔。
电解铜箔的生产原理是基于电化学原理的。
在电解槽中,阳极吸收电流并氧化成铜离子,铜离子通过电解液传输到阴极上,在电解反应的作用下还原成纯铜。
电解过程中电子在阳极和阴极之间传递,形成电流。
通过控制电流、电解液组成和电解时间等参数,可以调整电解铜箔的性能。
电解铜箔制造过程中的一些关键技术包括电解槽设计、电解液组成和控制、电解过程中的温度和搅拌控制等。
电解槽设计需要考虑阳极和阴极之间的距离、电解液的流动状况等因素,以保证铜箔的均匀性和质量。
电解液的组成和控制可以影响到电解过程中的反应速率和效果,不同的电解液组成可以产生不同性能的铜箔。
另外,温度和搅拌控制可以影响到电解液的传质速率和电解效果,对于铜箔的质量和性能都是至关重要的。
总的来说,电解铜箔的制造过程是一个复杂的过程,需要多种技术参数的调整和控制,以获得高质量的电解铜箔。
这些技术参数包括电解槽设计、电解液组成和控制、温度和搅拌控制等。
电解铜箔生产与技术讲座

电解铜箔生产与技术讲座电解铜箔是一种重要的电子材料,广泛应用于半导体、电子、通信、航空航天等领域。
为了加深大家对电解铜箔生产与技术的了解,今天我将为大家进行一次专题讲座。
首先,我们来介绍一下电解铜箔的生产工艺流程。
电解铜箔的生产主要分为铜铸坯制备、铸造连铸、精炼电解、机械压延等几个环节。
首先是铜铸坯制备。
制备电解铜箔的首要条件是原料的纯度和质量。
通过铜精矿的选别、脱硫、冶炼等过程,制备出高纯度的铜水。
接下来是铸造连铸。
铜水在连铸机中通过恒温槽、液位控制等技术参数的控制,将铜水注入到带有水冷铜模的连铸机中,形成坯料。
连铸机具有高效、节能、自动化的特点,可以实现对坯料的快速制备。
然后是精炼电解。
将铜坯装入电解槽中,在特定的电解液中通以直流电流,使铜阳极溶解,以阴极板上的铜箔为产物。
电解液的配方、温度、槽电流密度等参数的控制对电解效果和电解铜箔的质量有着重要影响。
最后是机械压延。
将电解铜箔经过多次的轧制、退火等工艺,使其逐渐拉薄并提高质量。
机械压延过程中需要进行冷却、润滑等技术措施,以保证铜箔的质量和表面光洁度。
接下来,我们来讲一下电解铜箔的技术要点。
首先是原料的选择和准备。
制备电解铜箔的原料需要有较高的纯度,通常要求纯度在99.95%以上,并且还需要进行初步的精炼处理。
原料中的杂质和气体含量会对电解过程产生一定的影响,因此需要通过脱气、脱硫等工艺来净化原料。
其次是电解液的配方和控制。
电解液的组成和性能决定了电解过程的效果和铜箔的质量。
通常电解液由硫酸铜、硫酸、草酸、氯化物等组成,需要控制好电解液的浓度、温度、搅拌速度等参数,以保证电解过程的稳定性和铜箔的表面质量。
另外,机械压延工艺也是电解铜箔生产过程中的关键环节。
通过合理的轧制工艺控制,可以调节电解铜箔的厚度、表面光洁度和拉伸性能。
同时,退火工艺也是重要的一环,通过适当的退火温度和时间控制,可以改善铜箔的结晶结构和力学性能。
最后,为了保证电解铜箔的质量,需要加强对生产过程的监控和质量控制。
铜箔厂实习报告总结
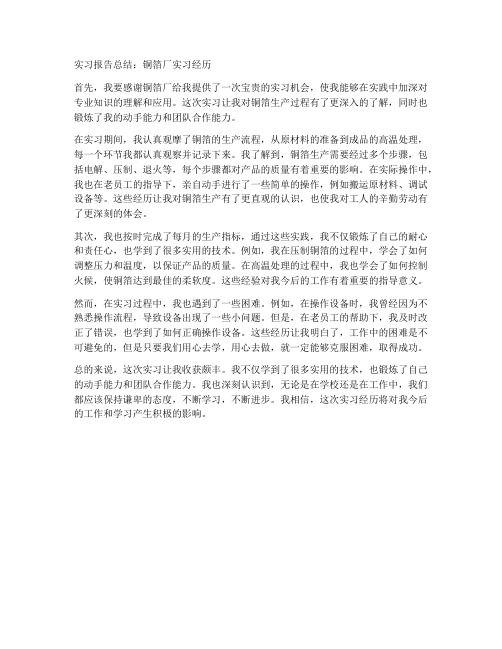
实习报告总结:铜箔厂实习经历首先,我要感谢铜箔厂给我提供了一次宝贵的实习机会,使我能够在实践中加深对专业知识的理解和应用。
这次实习让我对铜箔生产过程有了更深入的了解,同时也锻炼了我的动手能力和团队合作能力。
在实习期间,我认真观摩了铜箔的生产流程,从原材料的准备到成品的高温处理,每一个环节我都认真观察并记录下来。
我了解到,铜箔生产需要经过多个步骤,包括电解、压制、退火等,每个步骤都对产品的质量有着重要的影响。
在实际操作中,我也在老员工的指导下,亲自动手进行了一些简单的操作,例如搬运原材料、调试设备等。
这些经历让我对铜箔生产有了更直观的认识,也使我对工人的辛勤劳动有了更深刻的体会。
其次,我也按时完成了每月的生产指标,通过这些实践,我不仅锻炼了自己的耐心和责任心,也学到了很多实用的技术。
例如,我在压制铜箔的过程中,学会了如何调整压力和温度,以保证产品的质量。
在高温处理的过程中,我也学会了如何控制火候,使铜箔达到最佳的柔软度。
这些经验对我今后的工作有着重要的指导意义。
然而,在实习过程中,我也遇到了一些困难。
例如,在操作设备时,我曾经因为不熟悉操作流程,导致设备出现了一些小问题。
但是,在老员工的帮助下,我及时改正了错误,也学到了如何正确操作设备。
这些经历让我明白了,工作中的困难是不可避免的,但是只要我们用心去学,用心去做,就一定能够克服困难,取得成功。
总的来说,这次实习让我收获颇丰。
我不仅学到了很多实用的技术,也锻炼了自己的动手能力和团队合作能力。
我也深刻认识到,无论是在学校还是在工作中,我们都应该保持谦卑的态度,不断学习,不断进步。
我相信,这次实习经历将对我今后的工作和学习产生积极的影响。
电解铜箔生产常见问题及处理

电解铜箔生产常见问题及处理随着电子信息产业的发展,电子产品轻量化、集成化要求越来越高,电解铜箔作为电子行业的基础性材料,不仅对产品的抗拉强度、延伸率、抗剥离强度、防氧化性等物化性能指标提出了更高要求,而且要求铜箔微观晶粒组织和表面微观形貌结构更均匀精细。
电解铜箔生产工艺复杂,涉及专业广泛,生产过程既有机械电子设备又有电化学过程,分系统之间相互关联相互影响,相关技术大多是交叉、边缘学科,对处理实际生产中遇到的复杂问题缺乏成熟的理论支持。
本文通过对实际生产中常见问题的总结,提出了一些有参考价值的处理方法,希望能引起同行的注意和指正,引发更成熟的研究方法和处理方法。
1、溶液净化未处理箔(毛箔)的制造过程是铜箔生产中最关键的环节,绝大多数的物化性能指标与毛箔有着直接或间接的关系。
毛箔的电沉积过程离不开溶液,所以其溶液尤为重要,纯净无杂质、成分均匀稳定的毛箔溶液是生产高品质铜箔的必需条件。
实际生产中不可避免会有一些杂质通过原料铜、废箔、水、酸的加入和设备自身的磨损腐蚀进入到溶液中,因此生产中的溶液含有不溶性的微粒、可溶的离子分子基团和有机物等各种杂质,这些杂质大多数对铜箔品质有负面影响,应尽可能减少杂质进入溶液系统或采用有效方法把杂质控制在合理范围内。
不溶性微粒主要来源于原料铜的加入和废箔回用,活性炭和其它有机物吸附剂在使用中也会少量分解形成不溶性微粒。
在基箔电沉积过程中微粒夹杂于组织内或吸附于铜箔表面,造成箔面粗糙、针孔、渗透点等质量缺陷。
一般采用多级过滤的办法将微粒由大到小逐级过滤去除,过滤精度最高可以达到0. 5μm以内。
随着过滤层级的增加和过滤精度的提高溶液净化效果相应提高,铜箔组织的致密性和表面微观结构的细致性都明显优化,表现为延伸率、抗拉强度等指标的提高。
高度净化的基箔溶液是生产高品质铜箔前提条件之一。
增加过滤次数也是溶液净化的有效方法,通常循环过滤液量应为生产供液量的1.5倍以上。
提高溶液的净化,设备投入和运行费用会大幅增加,在净化工艺设计时要兼顾工艺性和经济性。
电解铜箔工艺

电解铜箔工艺电解铜箔工艺是一种制备高纯度铜箔的重要方法,广泛应用于半导体、电子、通信等领域。
本文将从工艺流程、设备和工艺参数等方面介绍电解铜箔工艺的基本知识。
一、工艺流程电解铜箔工艺的主要流程包括:准备工作、铜板切割、去脏洗涤、酸洗、电解精炼、凝固、冷轧、退火、表面处理等。
首先,需要准备高纯度铜板作为原料,并进行切割成适当尺寸的铜箔片。
然后,通过去脏洗涤和酸洗等工序,去除铜板表面的杂质和氧化物。
接下来,将铜板放入电解槽中,利用铜板作为阳极,在电解液中进行电解精炼,使铜离子在阴极上沉积成纯铜箔。
经过凝固、冷轧、退火和表面处理等工序后,最终得到高纯度、平整光滑的铜箔产品。
二、设备电解铜箔工艺所需的主要设备包括切割机、去脏洗涤槽、酸洗槽、电解槽、凝固设备、冷轧机、退火炉和表面处理设备等。
其中,电解槽是整个工艺中最关键的设备,它提供了电解液和电流,实现了铜板的电解精炼过程。
凝固设备用于将电解得到的铜板快速冷却并固化成箔状。
冷轧机和退火炉则用于对铜箔进行加工和热处理,使其具备所需的力学性能和导电性能。
三、工艺参数电解铜箔工艺中的关键工艺参数包括电解液成分、电解液浓度、电流密度、电解温度等。
电解液成分通常采用硫酸铜溶液,其浓度和其他添加剂的种类和浓度会直接影响到铜箔的纯度和表面质量。
电流密度是指单位面积上通过的电流量,其大小决定了电解速度和电解效果。
电解温度一般控制在较低的范围内,以保证电解过程的稳定性和铜箔的质量。
电解铜箔工艺具有许多优点,如制备过程简单、生产效率高、产品质量好等。
同时,也存在一些挑战和难点,如电解液的净化和循环利用、电解过程中的气泡和沉淀控制等。
为了提高电解铜箔工艺的效率和产品质量,需要不断优化工艺参数,改进设备和工艺流程,并加强对电解液的管理和控制。
电解铜箔工艺是一种重要的制备高纯度铜箔的方法,具有广泛的应用前景。
通过合理控制工艺流程、选择适当的设备和优化工艺参数,可以获得高质量的铜箔产品,满足不同领域的需求。
电解铜箔的生产与技术讲座

电解铜箔的生产与技术讲座电解铜箔是由纯铜板通过电解方式制成的一种薄片状材料。
它具有导电性好、韧性强、耐腐蚀、耐高温、易加工等优点,被广泛应用于电子、通信、航空航天、能源等领域。
本文将从原料准备、电解过程、技术要点和未来发展等方面进行讲述。
首先,原料准备是电解铜箔生产的第一步。
常用的原料是纯铜板,要求铜的纯度不低于99.95%。
在生产过程中,需要对铜板进行清洗,并采用酸洗的方法去除表面的氧化物和杂质。
只有经过准备的纯铜板,才能够保证电解过程的稳定性和产品的质量。
其次,电解过程是电解铜箔生产的核心环节。
电解过程采用了铜离子在电场作用下的迁移和沉积原理,通过控制电流密度和电解液组分,使得纯铜离子在阳极脱落,沉积在阴极形成铜箔。
电解液通常采用硫酸铜溶液,其中含有铜离子、硫酸根离子和氢离子。
在电解过程中,控制电流密度、电解温度和电解液的搅拌速度等参数,可以影响到产品的纯度、均匀度和形态。
第三,技术要点是保证电解铜箔质量的关键。
在电解过程中,要控制电流密度,使得电流均匀分布在整个铜板表面,避免出现局部电流过大引起烧穿或局部电流过小导致均匀性差的问题。
同时,保持电解液的纯度和稳定性也是关键。
定期检测电解液中的铜含量、酸碱度和杂质含量等,及时调整电解液的配比和添加剂的用量,保持电解过程的稳定性和产品质量的一致性。
最后,电解铜箔的未来发展方向是实现技术的数字化和智能化。
随着信息技术的发展,传感器、数据采集和处理技术的应用,可以对电解过程中的各项参数进行实时监测和控制。
通过物联网技术,实现设备之间的互联互通,优化生产过程和资源利用,提高产品的质量和生产效率。
此外,随着对电子产品轻薄化和高性能化的需求增加,对电解铜箔的表面光洁度、厚度均匀性和尺寸稳定性等提出了更高的要求。
因此,未来还需要进一步研究和开发新的制备方法和工艺,提升电解铜箔的性能和质量。
综上所述,电解铜箔的生产与技术涉及到原料准备、电解过程、技术要点和未来发展等方面。
电解铜箔制造工艺与技术
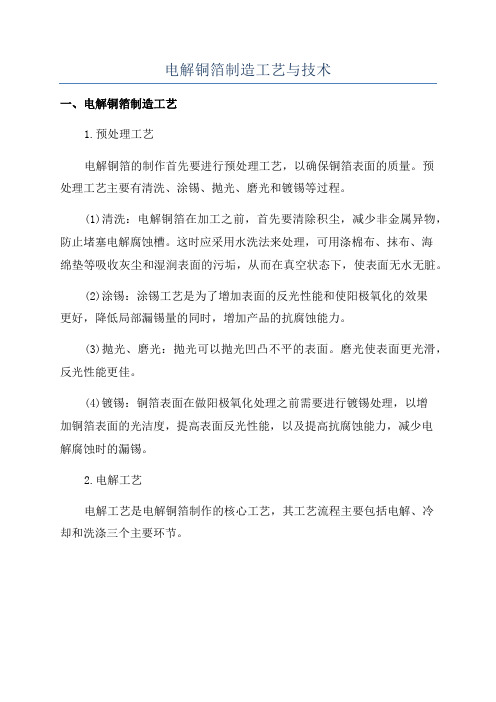
电解铜箔制造工艺与技术
一、电解铜箔制造工艺
1.预处理工艺
电解铜箔的制作首先要进行预处理工艺,以确保铜箔表面的质量。
预
处理工艺主要有清洗、涂锡、抛光、磨光和镀锡等过程。
(1)清洗:电解铜箔在加工之前,首先要清除积尘,减少非金属异物,防止堵塞电解腐蚀槽。
这时应采用水洗法来处理,可用涤棉布、抹布、海
绵垫等吸收灰尘和湿润表面的污垢,从而在真空状态下,使表面无水无脏。
(2)涂锡:涂锡工艺是为了增加表面的反光性能和使阳极氧化的效果
更好,降低局部漏锡量的同时,增加产品的抗腐蚀能力。
(3)抛光、磨光:抛光可以抛光凹凸不平的表面。
磨光使表面更光滑,反光性能更佳。
(4)镀锡:铜箔表面在做阳极氧化处理之前需要进行镀锡处理,以增
加铜箔表面的光洁度,提高表面反光性能,以及提高抗腐蚀能力,减少电
解腐蚀时的漏锡。
2.电解工艺
电解工艺是电解铜箔制作的核心工艺,其工艺流程主要包括电解、冷
却和洗涤三个主要环节。
铜箔生产实习报告
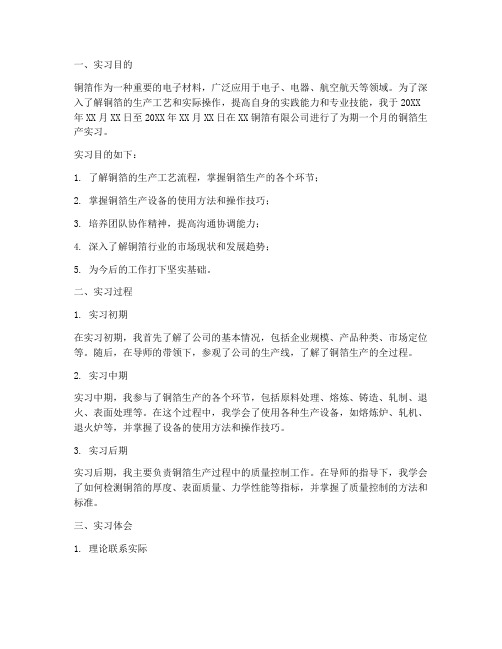
一、实习目的铜箔作为一种重要的电子材料,广泛应用于电子、电器、航空航天等领域。
为了深入了解铜箔的生产工艺和实际操作,提高自身的实践能力和专业技能,我于20XX 年XX月XX日至20XX年XX月XX日在XX铜箔有限公司进行了为期一个月的铜箔生产实习。
实习目的如下:1. 了解铜箔的生产工艺流程,掌握铜箔生产的各个环节;2. 掌握铜箔生产设备的使用方法和操作技巧;3. 培养团队协作精神,提高沟通协调能力;4. 深入了解铜箔行业的市场现状和发展趋势;5. 为今后的工作打下坚实基础。
二、实习过程1. 实习初期在实习初期,我首先了解了公司的基本情况,包括企业规模、产品种类、市场定位等。
随后,在导师的带领下,参观了公司的生产线,了解了铜箔生产的全过程。
2. 实习中期实习中期,我参与了铜箔生产的各个环节,包括原料处理、熔炼、铸造、轧制、退火、表面处理等。
在这个过程中,我学会了使用各种生产设备,如熔炼炉、轧机、退火炉等,并掌握了设备的使用方法和操作技巧。
3. 实习后期实习后期,我主要负责铜箔生产过程中的质量控制工作。
在导师的指导下,我学会了如何检测铜箔的厚度、表面质量、力学性能等指标,并掌握了质量控制的方法和标准。
三、实习体会1. 理论联系实际通过这次实习,我深刻体会到理论知识与实际操作相结合的重要性。
在生产过程中,我不仅将所学知识运用到实际工作中,还学会了如何解决实际问题。
2. 团队协作精神铜箔生产是一个复杂的过程,需要各个部门、各个岗位的密切配合。
在实习过程中,我深刻认识到团队协作精神的重要性,学会了与他人沟通、协作,共同完成工作任务。
3. 质量意识在实习过程中,我了解到质量控制是铜箔生产的关键环节。
通过学习质量控制的方法和标准,我提高了自身的质量意识,为今后的工作打下了坚实基础。
4. 市场观念实习期间,我了解了铜箔行业的市场现状和发展趋势。
这使我更加明确了自身的发展方向,为今后的职业规划提供了有益的参考。
四、实习总结通过一个月的铜箔生产实习,我收获颇丰。
电解铜箔生产工艺内部

电解铜箔生产工艺内部电解铜箔是一种常见的铜制品,广泛应用于电子、电器、通信等领域。
其生产工艺主要包括铜源选择、电解液制备、电解槽设计、电解过程控制以及铜箔后处理等环节。
首先,铜源的选择是影响电解铜箔质量的关键因素之一、一般情况下,采用电解还原法从铜盐溶液中制备电解液。
选择适合生产电解铜箔的铜盐溶液,并通过反应体系控制铜盐的浓度,以提高铜箔的质量。
其次,电解液的制备是生产电解铜箔的重要步骤。
电解液通常包括铜盐溶液、酸碱调节剂、表面活性剂等成分。
其中,铜盐溶液的浓度需要根据生产要求进行调整,酸碱调节剂用于控制电解液的酸碱度,表面活性剂则用于改善电解液的流动性和湿润性。
在电解槽设计方面,需要考虑电解液的循环和铜箔的沉积。
通常采用无纹槽设计,以减少电流密度差异对铜箔沉积均匀性的影响。
同时,还需要合理设计电流分布器,以提高电解液循环效果,保证铜箔表面质量。
电解过程控制是确保铜箔质量稳定的关键措施。
在控制电流密度和温度方面,通常采用自动控制系统。
通过实时监测电流密度和温度的变化,可以及时调整电解条件,以保持电解箔的均匀性和质量。
最后,铜箔的后处理是保证产品质量的重要环节。
一般包括:冲洗、退火、拉伸、切割等步骤。
冲洗工序是去除电解液残留和提高表面清洁度的关键步骤;退火工序通过加热和冷却来改善铜箔的结晶性能;拉伸工序则通过机械拉伸来提高铜箔的均匀性和拉伸性能;最后,通过切割工序将铜箔切割为所需尺寸。
总之,电解铜箔的生产工艺包括铜源选择、电解液制备、电解槽设计、电解过程控制以及铜箔后处理等环节。
通过合理的工艺流程,可以生产出质量稳定的电解铜箔产品。
电解铜箔生产溶铜方式及技术要求详解
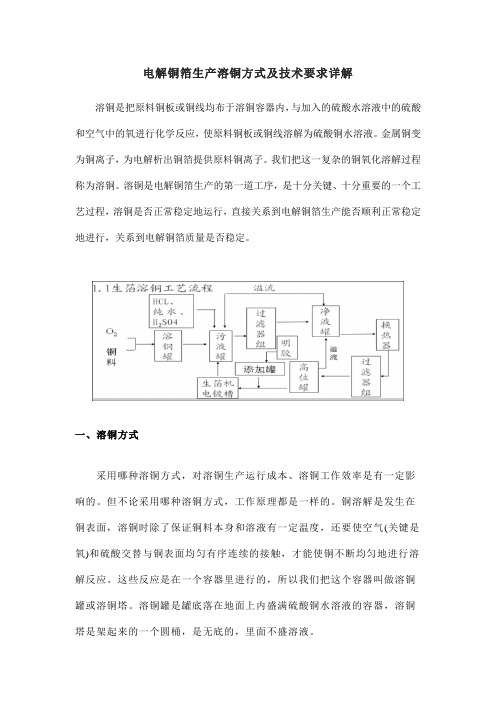
电解铜箔生产溶铜方式及技术要求详解溶铜是把原料铜板或铜线均布于溶铜容器内,与加入的硫酸水溶液中的硫酸和空气中的氧进行化学反应,使原料铜板或铜线溶解为硫酸铜水溶液。
金属铜变为铜离子,为电解析出铜箔提供原料铜离子。
我们把这一复杂的铜氧化溶解过程称为溶铜。
溶铜是电解铜箔生产的第一道工序,是十分关键、十分重要的一个工艺过程,溶铜是否正常稳定地运行,直接关系到电解铜箔生产能否顺利正常稳定地进行,关系到电解铜箔质量是否稳定。
一、溶铜方式采用哪种溶铜方式,对溶铜生产运行成本、溶铜工作效率是有一定影响的。
但不论采用哪种溶铜方式,工作原理都是一样的。
铜溶解是发生在铜表面,溶铜时除了保证铜料本身和溶液有一定温度,还要使空气(关键是氧)和硫酸交替与铜表面均匀有序连续的接触,才能使铜不断均匀地进行溶解反应。
这些反应是在一个容器里进行的,所以我们把这个容器叫做溶铜罐或溶铜塔。
溶铜罐是罐底落在地面上内盛满硫酸铜水溶液的容器,溶铜塔是架起来的一个圆桶,是无底的,里面不盛溶液。
1、浸泡式溶铜浸泡式溶铜是把原料铜板剪成小块或熔铸成线投入到溶铜罐里,硫酸水溶液和压缩空气从罐底进入,经过列管换热器加热后,从铜块缝隙间,以“Y”“Z”“S”形的流动路线,从下向上缓慢流动,在流动过程中与铜块表面接触,进行化学反应,使空气里的氧耗尽后,空气排入空中,溶液耗完了可以参加反应的部分硫酸后溢流出溶铜罐。
原料铜与氧和硫酸反应生成的铜离子,随溶液流出溶铜罐,进入电解液循环系统里,补充溶液因电解析出铜箔,溶液中减少的铜离子。
浸泡式溶铜的溶铜罐里始终装满溶液,原料铜浸泡在溶液中溶解。
浸泡式溶铜适用范围大、工艺条件宽,不受地区、气候条件影响。
溶铜罐小也能用,大也能用,气侯冷也能用,热也能用。
浸泡式溶铜一般要求溶液温度较高,大多数铜箔生产厂控制在70℃以上。
(1)浸泡式溶铜的供空气方式(也称供风方式)浸泡式溶铜一般采用无油空气压缩机供风,供风的目的一是供氧,二是用风对溶液进行搅拌,因为空压机供给的空气进出口都有过滤设备,可以去除空气里的灰尘等杂质,为溶铜提供十分洁净的空气,消除了因空气脏对电解液的污染。
电解铜箔生产常见问题及处理
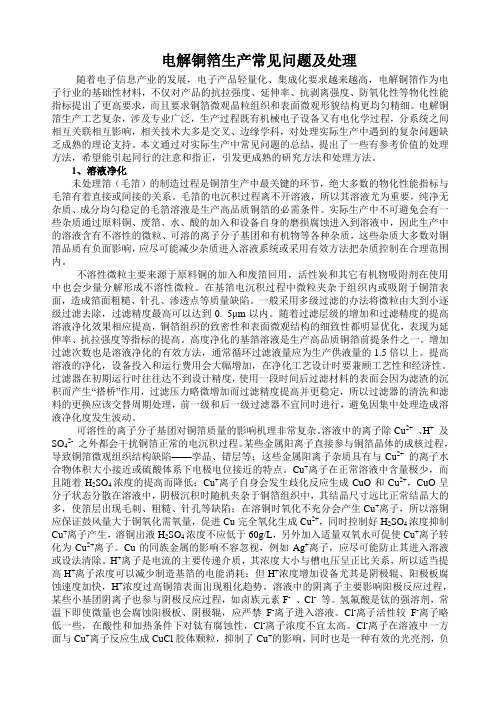
电解铜箔生产常见问题及处理随着电子信息产业的发展,电子产品轻量化、集成化要求越来越高,电解铜箔作为电子行业的基础性材料,不仅对产品的抗拉强度、延伸率、抗剥离强度、防氧化性等物化性能指标提出了更高要求,而且要求铜箔微观晶粒组织和表面微观形貌结构更均匀精细。
电解铜箔生产工艺复杂,涉及专业广泛,生产过程既有机械电子设备又有电化学过程,分系统之间相互关联相互影响,相关技术大多是交叉、边缘学科,对处理实际生产中遇到的复杂问题缺乏成熟的理论支持。
本文通过对实际生产中常见问题的总结,提出了一些有参考价值的处理方法,希望能引起同行的注意和指正,引发更成熟的研究方法和处理方法。
1、溶液净化未处理箔(毛箔)的制造过程是铜箔生产中最关键的环节,绝大多数的物化性能指标与毛箔有着直接或间接的关系。
毛箔的电沉积过程离不开溶液,所以其溶液尤为重要,纯净无杂质、成分均匀稳定的毛箔溶液是生产高品质铜箔的必需条件。
实际生产中不可避免会有一些杂质通过原料铜、废箔、水、酸的加入和设备自身的磨损腐蚀进入到溶液中,因此生产中的溶液含有不溶性的微粒、可溶的离子分子基团和有机物等各种杂质,这些杂质大多数对铜箔品质有负面影响,应尽可能减少杂质进入溶液系统或采用有效方法把杂质控制在合理范围内。
不溶性微粒主要来源于原料铜的加入和废箔回用,活性炭和其它有机物吸附剂在使用中也会少量分解形成不溶性微粒。
在基箔电沉积过程中微粒夹杂于组织内或吸附于铜箔表面,造成箔面粗糙、针孔、渗透点等质量缺陷。
一般采用多级过滤的办法将微粒由大到小逐级过滤去除,过滤精度最高可以达到0. 5μm以内。
随着过滤层级的增加和过滤精度的提高溶液净化效果相应提高,铜箔组织的致密性和表面微观结构的细致性都明显优化,表现为延伸率、抗拉强度等指标的提高。
高度净化的基箔溶液是生产高品质铜箔前提条件之一。
增加过滤次数也是溶液净化的有效方法,通常循环过滤液量应为生产供液量的1.5倍以上。
提高溶液的净化,设备投入和运行费用会大幅增加,在净化工艺设计时要兼顾工艺性和经济性。
铜箔制液实习报告

实习报告一、实习背景和目的本次实习是在铜箔制液工厂进行的,实习的主要目的是了解和掌握铜箔制液的基本工艺流程和操作方法,以及熟悉工厂的生产环境和安全管理措施。
通过实习,我期望能够提高自己的实践能力和专业素养,为将来的工作打下坚实的基础。
二、实习内容和过程在实习期间,我参与了铜箔制液的整个工艺流程,包括原料准备、反应釜操作、产物分离和纯化等环节。
我详细了解了铜矿石的破碎、研磨、浸出、电解和成品加工等过程,并学会了使用相关的仪器设备和操作工具。
在原料准备阶段,我参与了铜矿石的称量和投料工作,学会了如何根据化学反应的方程式计算原料的用量,并掌握了原料的储存和保管方法。
我还参与了反应釜的操作,学会了如何控制反应温度和搅拌速度,以保证反应的效率和产物的质量。
在产物分离和纯化阶段,我学会了使用过滤、离心、蒸发和结晶等方法,将反应产物中的杂质去除,并得到纯净的铜箔。
我还参与了电解过程的操作,学会了如何控制电解液的成分和电流密度,以提高电解的效率和铜箔的厚度。
三、实习收获和反思通过本次实习,我对铜箔制液的工艺流程和操作方法有了深入的了解,并提高了自己的实践能力。
我学会了使用相关的仪器设备和操作工具,掌握了生产安全和环境保护的基本知识。
我还学会了如何处理生产过程中的问题和故障,并能够进行相关的数据分析和报告撰写。
然而,在实习过程中,我也发现了自己的一些不足之处。
我发现自己在操作反应釜时,对温度的控制不够准确,导致反应的效果不够理想。
我认识到,在实际生产中,精确的操作和对设备的熟悉非常重要,需要我在今后的实践中更加注重细节和操作的精确性。
四、实习总结通过本次实习,我对铜箔制液的工艺流程和操作方法有了深入的了解,并提高了自己的实践能力。
我认识到了自己在操作中的不足之处,并决心在今后的工作中更加注重细节和操作的精确性。
我相信,这次实习对我未来的学习和工作将产生积极的影响。
- 1、下载文档前请自行甄别文档内容的完整性,平台不提供额外的编辑、内容补充、找答案等附加服务。
- 2、"仅部分预览"的文档,不可在线预览部分如存在完整性等问题,可反馈申请退款(可完整预览的文档不适用该条件!)。
- 3、如文档侵犯您的权益,请联系客服反馈,我们会尽快为您处理(人工客服工作时间:9:00-18:30)。
电解铜箔生产实践的关键,是通过应用一系列的生产技术和技巧,来控制铜箔的质量满足要求。
众所周知,国际标准IPC4562将印制线路用金属电解铜箔按照特性的质量保证水平差异分为三级:1级:适用于要求电路功能完整,机械性能和外观缺陷不重要的应用场合。
2级:适用于电路设计、工艺及规范一致性要求允许局部区域不一致的应用场合。
3级:适用于要求保证等级最高的应用场合。
在这三个等级中,3级的质量保证水平最高,2级的质量保证水平适中,1级的质量保证水平最低。
电解铜箔的质量缺陷主要有外观缺陷(箔材存在针孔和气隙度,麻点和压痕,缺口和撕裂,皱折,划痕)、尺寸缺陷(面积质量及厚度及偏差,箔轮廓超标)、物理性能缺陷(拉伸强度,疲劳延展性,延伸率,剥离强度,载体分离强度,金属箔表面粗糙度不能满足要求)、工艺性能不能满足要求(可蚀刻性,可焊性)以及其它性能(如纯度、质量电阻率)。
电解铜箔的最终性能,除剥离强度、可焊性等个别指标外,大多数是由生箔的性能所决定的。
而这些性能,如拉伸强度、疲劳延展性、延伸率、金属箔表面粗糙度等均与生箔(毛箔)的晶体学织构有关。
材料的晶体学织构表达了组成晶体材料的无数晶粒的取向分布方式。
晶体的每个晶粒都是各向异性的,即其性能随着测量方位的变化而变化。
用于测量这种晶体学织构的传统方法是X射线衍射法。
在大多数工程材料及常用电沉积层中,其正常晶体的取向为优势取向,这就是所谓残余各向异性,电解铜箔的织构与其自身的沉积过程密切相关,电解沉积层的形成是由形核及晶体长大两个不同的过程所控制的,而织构的发展也可能是这两个过程相互竞争的结果。
沉积超电势及间接影响超电势的每个工艺参数,如流体动力学,添加剂等在织构形成中起着首要作用。
有关研究表明,电解铜箔的生箔铜箔在小于12μm的情况下,XRD衍射图谱中的主峰为(111)面,并目(311)面呈现一定的择优取向。
随着厚度的增加,其(220)衍射峰强度不断提高,其他晶面衍射强度则逐渐降低,当铜箔厚度达到21μm时,(220)晶面的织构系数达到92%。
很显然,依靠简单技术使电解铜箔的性能达到压延铜箔的性能指标几乎不现实。
在生箔电解过程中,阴极基体材料的表面条件也是影响织构发展的重要因素。
电解铜箔是铜离子在阴极辊表面晶体上结晶结构的延续,铜离子电沉积在钛晶体上,并由此而生长成铜箔。
阴极钛辊表面的晶体结构决定着电解铜箔最初的结晶状态。
随着电解沉积层的增加,阴极表面基体组织对铜沉积层结晶结构的影响越来越小。
这可以从电解铜箔的毛面和光面的晶向变化上看出。
普通电解铜箔在高温时延伸率比压延铜箔低,这与其冶金结构有关。
电解铜箔竖直结构不受加热到180℃、持续1时的影响,而压延铜箔的水平结构在较低的温度下退火而重新结晶。
5.1 铜箔的内应力内应力是电解铜箔固有性能之一,其符号及数值大小与所选择的电解沉积条件有很大关系。
虽然IPC4562标准并未对电解铜箔的内应力作出明确的要求,但在实际生产中,电解铜箔的这种内应力的出现是很有害的。
例如,对于厚度小于18微米的铜箔,如果内应力过大,铜箔在裁片后卷边,导致覆铜板在叠配〔三明治)时操作困难、无法自动叠配。
对于电解铜箔内应力的起源,现有不同的理论给出了不同的解释,但都是真实应力的部分起因。
例如电解铜箔内应力的起源与阴极表面原子氢的吸附以及反应的分子氢的脱附析出有关;由于电解液条件的改变引起的外来物质及杂质共沉积会导致很复杂的内应力;另一个原因是与铜箔电沉积自身形成过程的驱动力有关;阳离子在阴极的还原需要一定的外界能量输入,其中部分能量在镀层生长时以缺陷的形式存在于晶格之中。
在电解过程中,电流密度增加时,内应力从压应力向拉应力逐渐转变,但在每个电流密度区间铜箔沉积层形貌结构几乎保持不变,内应力导致的另一个结果是当时效或加热时,铜箔沉积层结构发生转变。
电解铜箔的内应力与一系列相关的参数有关,如阴极表面材料的结构、表面条件、镀液组成和电解条件。
铜箔沉积层内应力可以通过测量设备测量,最简单的方法就是在电沉积时使用一个柔软阴极。
在同样表面条件、镀液组成和电解条件,细长的条状阴极当受到其上电沉积铜箔内应力的作用时就会发生形变,这样应力就可通过阴极材料的挠度计算出来,这也是常用的螺旋应力计的测试原理,或通过阴极材料的延伸率计算出来。
使用螺旋应力计测试仪,已知厚度的箔层的平均应力可以通过镀后螺旋金属片的挠度计算出来。
一般,我们将铜箔镀层使阴极薄片向阳极弯曲的内应力称为拉应力(张应力),使阴极薄片背向阳极弯曲的内应力称为压应力。
过大的电解铜箔内应力可以通过适当调整生箔的生产工艺来减小。
在实际操作中,我们发现铜箔内应力和电解时的电流密度大小有关。
铜箔内应力会随着电流密度的增加而增加。
事实上,由于各个铜箔企业生产工艺并不完全相同,铜箔内应力的表现方式也不相同:有的是压应力,有的表现为拉应力。
所以,对于铜箔内应力控制,没有固定的解决方案可以套用,必须根据具体的生产工艺条件而确定。
5.2、外观缺陷电解铜箔的外观缺陷主要是指箔材存在针孔和渗透点、麻点、压痕、缺口以及撕裂、皱折、划痕等缺陷。
5.2.1 针孔和渗透点所谓针孔,就是铜箔在暗室中透光检查,有直径小于1毫米的零星的微小透光孔。
渗透点则是不透光但在铜箔的一面用用渗透剂染色,在反面出现染色剂斑点的现象。
简单的讲,针孔为直孔,渗透点是曲孔。
对于PCB用电解铜箔,针孔和渗透点过去一直是电解铜箔厂家深感头疼的问题。
有关铜箔孔隙产生原因及孔隙程度是电解铜箔生产技术中一个重要的参数,尤其对于厚度小于18微米的电解铜箔,产生空隙频率更高。
目前铜箔制造厂在生产线上只能用精密仪器监测约15微米以上的针孔,对于小于15微米的针孔和所有的渗透点,只能采用染色评价法抽样测试。
针孔和渗透点在覆铜板压合过程中,融化的树脂会从铜箔孔隙中流出,在铜箔表面形成树脂点,影响覆铜板质量。
根据有关研究,电解铜箔孔隙可分为夹杂性孔隙及结晶学孔隙。
夹杂性孔隙是在电沉积初期阴极辊表面某些小面积范围内金属沉积不能发生造成的,即使后续的沉积具有一定桥接覆盖作用,这样的小面积也会孔隙核心,也叫孔隙母体。
阴极辊表面的非金属夹杂物,包括附着在阴极辊表面的溶液净化工序中漏滤的活性炭微粒、电解液中的胶质、油污和灰尘等;另一种孔隙母体为阴极辊筒表面的微孔。
电沉积不会在这些孔隙母体上形成,这是由于这些母体的导电性不好,或是由于这些孔隙母体具有与洁净基体金属材料完全不同的电化学特征,因而具有完全不同的电极反应动力学特征,有利于另一些沉积副反应的发生如氢的析出等。
由于阴辊基体金属或电解参数引起的结构缺陷产生的孔隙称做结晶学孔隙,这种情况下伪同晶现象及外延生长可能使部分镀层与基体失去良好结合和共格。
其中伪同晶现象是指铜箔镀层生长延续了阴极基体材料晶界或微观几何特征;外延生长则是在镀层与基村界面上镀层沿基体晶格完全有序地生长。
研究和生产实践证实了阴极基体的表面粗糙度及阴极辊筒金属预处理如机械磨光、化学及电化学抛光对电解铜箔的孔隙产生有巨大的决定作用。
阴极辊基体金属对电解铜箔的影响,随着基体材料上的连续吸附层的迁移引起孔隙性的周期性变化。
随着铜箔厚度的增加,基体材料通过伪同晶及外延的影响作用逐渐消失,于是铜箔铜层生长将只由电解液镀层界面的电沉积条件控制。
实际上,电解参数如电解液组成,电流密度、电流形式,电解温度及电解液流速(搅拌)都会对铜箔孔隙的形成产生巨大影响,因此,获得无孔隙铜箔的厚度将随电沉积时使用的电解液的过滤精度、添加剂及阴极材料的情况而变化。
IPC4562印制线路板用金属箔规范中提到两种评价方法:一种是等同采用IPC-TM650中2.1.2染料渗透法;另一种是取铜箔箔面朝上置于灯箱上,计算300mm x 300mm尺寸透光产生的亮点数用作评价针孔的数量,尺寸测量的分辨率要求达到25微米。
上述两种方法都是用来评价铜箔的,后一种方法的分辨率低,不能检测小的针孔。
一般而言,随着镀层厚度增加,孔隙降低。
虽然很久以前就已经认识到铜箔电沉积层的孔隙度与基体材料的有关,知道它依赖于基体材料表面条件及电沉积工艺参数,如过去使用的不锈钢阴极辊筒,很难消除铜箔针孔。
电解铜箔产生如果发现铜箔针孔、渗透点超标,主要原因:(1)电解液洁净度超标,存在油、胶等污染物;〔2)阴极表面有气孔或夹杂;(3)阴极表面有脏物附着;(4)光面铜粉严重;处理措施(1)加强过滤;(2)更换过滤芯或过滤袋;(3)添加或更换活性炭;(4)更换阴极辊或磨辊;5.2.2 压坑与划痕IPC标准规定,铜箔表面划痕深度不应超过铜箔标称厚度的20%。
划痕深度为金属箔标称厚度的5%-20%时,每300mmx300mm区域,划痕数不应超过3条。
深度小于金属箔标称厚度的5%的划痕可以忽略不计。
对于麻点和压痕,不应有直径超1.0mm的压痕及麻点海300mmx300mm区域,直径小于1.0mm的压痕及麻点不应超过2个,对直径小于标称厚度5%的压痕和麻点可以忽略不计。
压坑与划痕产生的原因:(1)揭边时铜粒子进入剥离辊等动辊与铜箔之间产生压痕,如果进入惰辊(应该转动而没有转动的导辊)与铜箔之间,产生划痕。
(2)揭边时铜粒子进入附着铜箔表面,卷入铜箔箔卷之中,造成铜箔压痕。
(3)外来杂物产生压痕与划痕,主要是空气中的大的灰尘、生箔机上方的行车震动掉下来的沙尘。
处理方法:对于压坑与划痕,只能用干毛巾或毛刷将产生压坑或划痕的导辊清理干净。
在故障高发期,建议每5分钟清理一次。
在技术上,应通过技术改造,尽可能的使与铜箔接触的导辊全部旋转,杜绝惰辊现象发生,将划痕缺陷降低到最小。
5.2.3 色差所谓色差,就是指箔面颜色不一致。
斑点,色带、色条等都会导致箔面色差。
色差生产原因相当复杂,主要在于:(1)生箔从阴极辊表面剥前(后)的酸洗、水洗不彻底;(2)生箔机压水辊间隙不合适;(3)现场酸雾严重,造成箔面出现大量的酸雾点;(4)阴极辊面氧化;(5)生箔烘干不彻底,生箔表面氧化;(6)阳极损坏;(8)洗涤水量偏小,没有将电解液冲洗干净,导致电解液在箔面结晶;(9)洗涤水被污染,污物、油蚀、腐蚀物、盐类、油脂等都可能导致箔面出现色差;(10)水银污染。
对于采用水银导电的企业,大量的水银点,也是导致铜箔表面色差的一个主要原因。
处理方法:应分析造成色差的原因,采取针对性的措施。
例如,如果生箔毛面有规则的褐色色带,可能是生箔机压水辊有问隙,导致冲洗水进入电解液所致,应检修调整压水辊。
5.3、物理性能铜箔的物理性主要包括拉伸强度、延展性等,其中对于拉伸强度,一般都能满足要求。
所谓延展性就是“一个材料承受大量的全面形变的能力”。
它包括延伸率和疲劳延性。
IPC4562标准对电解铜箔的延展性主要考察的是铜箔的延伸率,而疲劳延性仅对退火电解箔(ANN-E)、可低温退火电解箔(LTA-E)和可退火电解箔(A-E)提出了要求。