电解铜箔生产常见问题及处理
铜箔厂培训——精选推荐
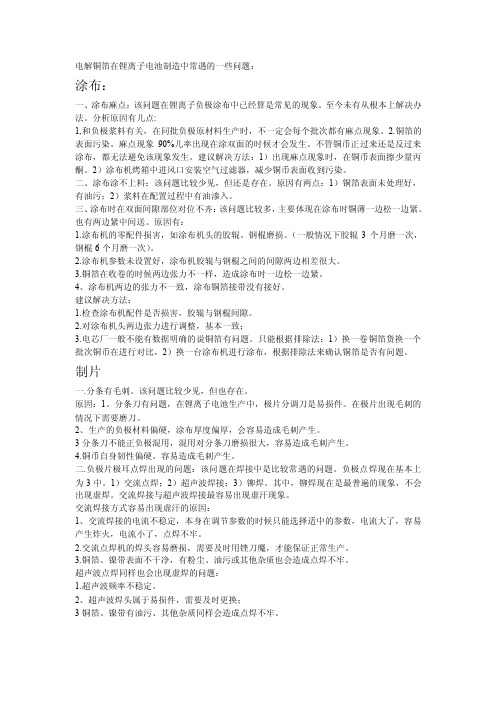
电解铜箔在锂离子电池制造中常遇的一些问题:涂布:一、涂布麻点:该问题在锂离子负极涂布中已经算是常见的现象。
至今未有从根本上解决办法。
分析原因有几点:1,和负极浆料有关,在同批负极原材料生产时,不一定会每个批次都有麻点现象。
2.铜箔的表面污染。
麻点现象90%几率出现在涂双面的时候才会发生。
不管铜币正过来还是反过来涂布,都无法避免该现象发生。
建议解决方法:1)出现麻点现象时,在铜币表面擦少量丙酮。
2)涂布机烤箱中进风口安装空气过滤器,减少铜币表面收到污染。
二、涂布涂不上料:该问题比较少见,但还是存在。
原因有两点:1)铜箔表面未处理好,有油污;2)浆料在配置过程中有油渗入。
三、涂布时在双面间隙部位对位不齐:该问题比较多,主要体现在涂布时铜薄一边松一边紧。
也有两边紧中间送。
原因有:1.涂布机的零配件损害,如涂布机头的胶辊、钢棍磨损。
(一般情况下胶辊3个月磨一次,钢棍6个月磨一次)。
2.涂布机参数未设置好,涂布机胶辊与钢棍之间的间隙两边相差很大。
3.铜箔在收卷的时候两边张力不一样,造成涂布时一边松一边紧。
4、涂布机两边的张力不一致,涂布铜箔接带没有接好。
建议解决方法:1.检查涂布机配件是否损害,胶辊与钢棍间隙。
2.对涂布机头两边张力进行调整,基本一致;3.电芯厂一般不能有数据明确的说铜箔有问题。
只能根据排除法:1)换一卷铜箔货换一个批次铜币在进行对比,2)换一台涂布机进行涂布,根据排除法来确认铜箔是否有问题。
制片一.分条有毛刺。
该问题比较少见,但也存在。
原因:1。
分条刀有问题,在锂离子电池生产中,极片分调刀是易损件。
在极片出现毛刺的情况下需要磨刀。
2、生产的负极材料偏硬,涂布厚度偏厚,会容易造成毛刺产生。
3分条刀不能正负极混用,混用对分条刀磨损很大,容易造成毛刺产生。
4.铜币自身韧性偏硬。
容易造成毛刺产生。
二.负极片极耳点焊出现的问题:该问题在焊接中是比较常遇的问题。
负极点焊现在基本上为3中。
1)交流点焊;2)超声波焊接;3)铆焊。
电解铜箔生产常见问题及处理

电解铜箔生产常见问题及处理
一、生产常见问题
1、电解池漏电
运行时出现电解池漏电现象,可能是电解池封口有问题,搭接条带有氧化物或封口螺栓松动引起的,该情况须及时检修,将封口板拆洗干净,检查搭接条是否有氧化物,如有清洗后,再重新安装封口板并加紧螺栓。
2、阴极结焦
经常出现阴极结焦,可能是由于电解池的工作温度过高,涂锌箔厚度不足,抗熔化点不够高的铜溶液导致,该情况清洗阴极,更换阴极,检查铜溶液,补充锌箔。
3、电解池燃烧
电解池经常出现燃烧,可能是由于电解池热控不当、离心机失压而导致的,该情况应及时关闭离心机,检查温控装置是否正常运转,降低电解池温度,加强温控的操作。
4、电流过大
经常出现电流过大的情况,可能是由于电解池的内电阻过小引起的,该情况及时更换电解池,更换新的电解池,并检查电解池内部的内电阻是否正常。
5、铜溶液长时间无法得到
铜溶液长时间无法得到,可能是由于电解池容积过小,铜溶液浓度过大,沉淀物淤积过多引起的,该情况应减少电解池的容积,同时减小铜溶液的浓度,清除沉淀物淤积。
二、处理措施
1、电解池漏电。
电解铜箔常见问题及解决办法

电解铜箔常见问题及解决办法摘要:现代电子工业材料中常使用到电子铜箔,电子工业的不断发展,要求其有更高的技术支持,生产电子铜箔的厂家有许多,且各厂家的生产工艺相差不大,而产出的铜箔质量可能存在一定差异。
我国电子工业的发展,不少厂家逐步生产电子铜箔,但我国这种材料的质量相比国外有非常大的差距,通常体现在放置铜箔之后出现变色情况,成品合格率也难以保障,使得电耗高成本增加,经济效益低下。
电解铜箔需要有非常高的生产实践性,本文主要分析了近年来电解铜箔生产过程中常见的问题与处理手段供参考。
关键词:电解铜箔,问题,毛刺,方法电解铜箔发展有三个阶段,第一个阶段是起步阶段,这个阶段重点在于印刷,通过铜箔来生产电路板,厚度在70-100cm之间。
第二个阶段是快速发展阶段,这个阶段的铜箔厚度在18-35cm之间,被日本铜箔业所垄断。
第三个阶段是发展成熟阶段,这个阶段生产的铜箔厚度在3-5cm之间,且在电池上应用,全球各个国家对其研究程度不等。
随着铜箔生产企业在产品质量和工艺流程上改善较大,而对比国外先进生产企业来说仍有非常大的差距。
我国进口铜箔通常是高档铜箔,出口铜箔90%以上为低档铜箔。
技术含量及附加值高的HD内层用柔性电路板及铜箔,基本上都是从国外进口。
因材料价格精度因素,我国生产企业购买的生箔机在持续工作中材料表面情况不良致使铜箔品质降低,那么对这部分企业来说,需要不断提升产品的性能,采取科学可行的方法来改进电解铜箔的表面处理工艺。
生产厂家质量有差异,但关键生产工艺及设备的原理大同小异,通常是生箔机大小不一致,后处理在点解时添加的电解添加剂不一样,工艺不一样。
在生箔机中经过电沉积,对阴极辊的转速控制下获取厚度不等的铜箔,在生产过程中容易产生一系列问题,下面将介绍常见的几个问题。
1 电解铜箔常见问题及解决办法1.1毛刺生箔机会产生毛刺,收集辊中能够发现铜箔有突出,有些毛刺还可能刺穿铜箔造成破坏,小毛刺的情况可佩带手套来感觉生箔机收卷,会有刺手感。
电解铜箔常见问题及解决对策分析
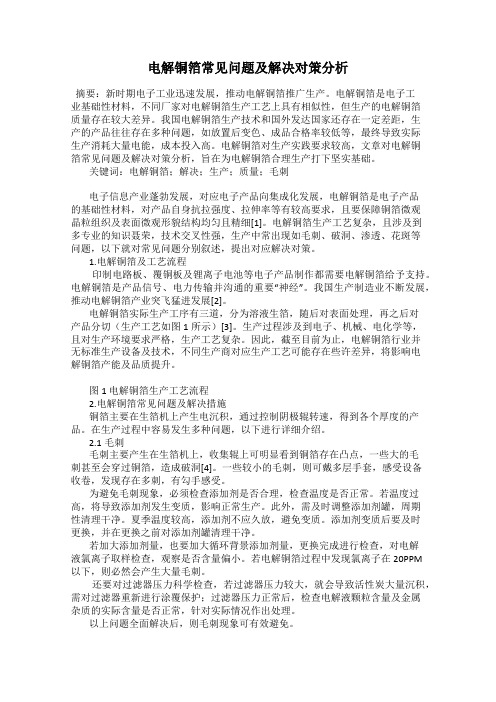
电解铜箔常见问题及解决对策分析摘要:新时期电子工业迅速发展,推动电解铜箔推广生产。
电解铜箔是电子工业基础性材料,不同厂家对电解铜箔生产工艺上具有相似性,但生产的电解铜箔质量存在较大差异。
我国电解铜箔生产技术和国外发达国家还存在一定差距,生产的产品往往存在多种问题,如放置后变色、成品合格率较低等,最终导致实际生产消耗大量电能,成本投入高。
电解铜箔对生产实践要求较高,文章对电解铜箔常见问题及解决对策分析,旨在为电解铜箔合理生产打下坚实基础。
关键词:电解铜箔;解决;生产;质量;毛刺电子信息产业蓬勃发展,对应电子产品向集成化发展,电解铜箔是电子产品的基础性材料,对产品自身抗拉强度、拉伸率等有较高要求,且要保障铜箔微观晶粒组织及表面微观形貌结构均匀且精细[1]。
电解铜箔生产工艺复杂,且涉及到多专业的知识聂荣,技术交叉性强,生产中常出现如毛刺、破洞、渗透、花斑等问题,以下就对常见问题分别叙述,提出对应解决对策。
1.电解铜箔及工艺流程印制电路板、覆铜板及锂离子电池等电子产品制作都需要电解铜箔给予支持。
电解铜箔是产品信号、电力传输并沟通的重要“神经”。
我国生产制造业不断发展,推动电解铜箔产业突飞猛进发展[2]。
电解铜箔实际生产工序有三道,分为溶液生箔,随后对表面处理,再之后对产品分切(生产工艺如图1所示)[3]。
生产过程涉及到电子、机械、电化学等,且对生产环境要求严格,生产工艺复杂。
因此,截至目前为止,电解铜箔行业并无标准生产设备及技术,不同生产商对应生产工艺可能存在些许差异,将影响电解铜箔产能及品质提升。
图1 电解铜箔生产工艺流程2.电解铜箔常见问题及解决措施铜箔主要在生箔机上产生电沉积,通过控制阴极辊转速,得到各个厚度的产品。
在生产过程中容易发生多种问题,以下进行详细介绍。
2.1毛刺毛刺主要产生在生箔机上,收集辊上可明显看到铜箔存在凸点,一些大的毛刺甚至会穿过铜箔,造成破洞[4]。
一些较小的毛刺,则可戴多层手套,感受设备收卷,发现存在多刺,有勾手感受。
铜箔不良问题及解决方法

铜箔不良问题及解决方法1、电解铜箔产生如果发现铜箔针孔、渗透点超标,主要原因:(1)电解液洁净度超标,存在油、胶等污染物;〔2)阴极表面有气孔或夹杂;(3)阴极表面有脏物附着;(4)光面铜粉严重;处理措施(1)加强过滤;(2)更换过滤芯或过滤袋;(3)添加或更换活性炭;(4)更换阴极辊或磨辊;2、压坑与划痕产生的原因:(1)揭边时铜粒子进入剥离辊等动辊与铜箔之间产生压痕,如果进入惰辊(应该转动而没有转动的导辊)与铜箔之间,产生划痕。
(2)揭边时铜粒子进入附着铜箔表面,卷入铜箔箔卷之中,造成铜箔压痕。
(3)外来杂物产生压痕与划痕,主要是空气中的大的灰尘、生箔机上方的行车震动掉下来的沙尘。
处理方法:对于压坑与划痕,只能用干毛巾或毛刷将产生压坑或划痕的导辊清理干净。
在故障高发期,建议每5分钟清理一次。
在技术上,应通过技术改造,尽可能的使与铜箔接触的导辊全部旋转,杜绝惰辊现象发生,将划痕缺陷降低到最小。
3、所谓色差,就是指箔面颜色不一致。
斑点,色带、色条等都会导致箔面色差。
色差生产原因相当复杂,主要在于:(1)生箔从阴极辊表面剥前(后)的酸洗、水洗不彻底;(2)生箔机压水辊间隙不合适;(3)现场酸雾严重,造成箔面出现大量的酸雾点;(4)阴极辊面氧化;(5)生箔烘干不彻底,生箔表面氧化;(6)阳极损坏;(8)洗涤水量偏小,没有将电解液冲洗干净,导致电解液在箔面结晶;(9)洗涤水被污染,污物、油蚀、腐蚀物、盐类、油脂等都可能导致箔面出现色差;(10)水银污染。
对于采用水银导电的企业,大量的水银点,也是导致铜箔表面色差的一个主要原因。
处理方法:应分析造成色差的原因,采取针对性的措施。
例如,如果生箔毛面有规则的褐色色带,可能是生箔机压水辊有问隙,导致冲洗水进入电解液所致,应检修调整压水辊。
4、酸性硫酸盐镀铜溶液中低浓度的Cl离子不仅是作为一种去极化剂和整平剂,这对得到较好延性是有益的;而且还会加强晶体学择优织构,引起延性的降低。
电解铜箔生产常见问题及处理
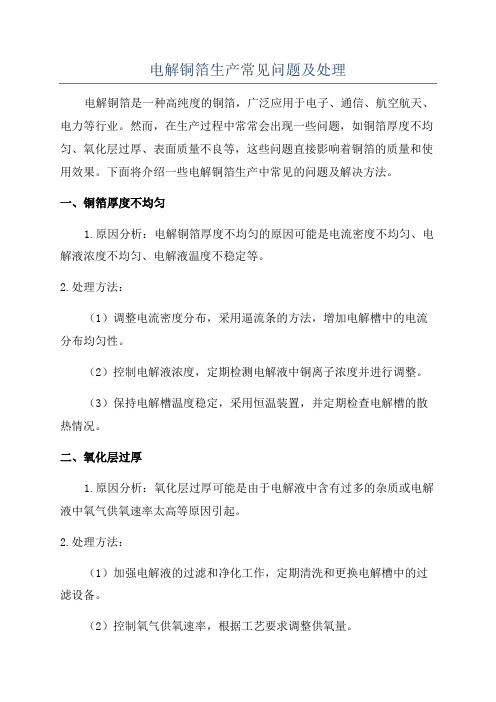
电解铜箔生产常见问题及处理电解铜箔是一种高纯度的铜箔,广泛应用于电子、通信、航空航天、电力等行业。
然而,在生产过程中常常会出现一些问题,如铜箔厚度不均匀、氧化层过厚、表面质量不良等,这些问题直接影响着铜箔的质量和使用效果。
下面将介绍一些电解铜箔生产中常见的问题及解决方法。
一、铜箔厚度不均匀1.原因分析:电解铜箔厚度不均匀的原因可能是电流密度不均匀、电解液浓度不均匀、电解液温度不稳定等。
2.处理方法:(1)调整电流密度分布,采用逼流条的方法,增加电解槽中的电流分布均匀性。
(2)控制电解液浓度,定期检测电解液中铜离子浓度并进行调整。
(3)保持电解槽温度稳定,采用恒温装置,并定期检查电解槽的散热情况。
二、氧化层过厚1.原因分析:氧化层过厚可能是由于电解液中含有过多的杂质或电解液中氧气供氧速率太高等原因引起。
2.处理方法:(1)加强电解液的过滤和净化工作,定期清洗和更换电解槽中的过滤设备。
(2)控制氧气供氧速率,根据工艺要求调整供氧量。
(3)采取适当的操作方法和电解条件,减少氧气在电解过程中的消耗。
三、表面质量不良1.原因分析:电解铜箔表面质量不良的原因可能是电解液中杂质太多、电解工艺条件不合理等。
2.处理方法:(1)加强电解液的净化工作,定期清洗和更换电解槽中的过滤设备。
(2)优化工艺条件,合理控制电解温度、电流密度、电解时间等参数。
(3)定期对电解设备进行维护和检查,确保设备的正常运转。
四、其他问题1.电解液成分不稳定:可能是由于电解槽内的溶液浓度不稳定、电解液配制不当等原因引起的。
处理方法:定期检测电解液的成分,并根据需要进行调整和补充。
2.铜箔强度不达标:可能是由于电解液的复配配比不合理、电解温度过高等原因引起的。
处理方法:调整电解液的复配配比,优化工艺条件,控制电解温度在合理范围内。
3.气泡和缺陷:可能是由于电解槽内的电解液中含有杂质、电解温度设定不合理等原因引起的。
处理方法:加强电解液的过滤和净化工作,控制电解温度在合理范围内。
试述电解铜箔常见问题及解决方法

试述电解铜箔常见问题及解决方法作者:何文龙来源:《中国科技博览》2017年第03期[摘要]电解铜箔自上世纪四十年代投入生产之后,先后应用于制造业、加工业、电子工业等,随着制造工艺的不断完善,从事电解铜箔生产制造的企业也开始尝试新的电解铜箔电解液的制造工艺流程。
基于此,本文通过对电解铜箔生产过程中常见质量问题分析,并提出了相应的问题解决对策,希望能对电解铜箔生产的同事有所帮助。
[关键词]电解铜箔;问题;对策中图分类号:TN915 文献标识码:A 文章编号:1009-914X(2017)03-0032-011 导言电解铜箔作为电子工业的基础材料之一,在电子行业中的应用十分广泛,对整个电子行业的发展有着十分重要的作用。
电解铜箔是合适的电解质溶液在一定的电流密度作用下,通过电沉积技术得到的金属铜沉积层,被广泛用于覆铜板(简称CCL)和印刷线路板(简称PCB)的生产。
铜箔是在生箔机上通过电沉积,以及控制阴极辊的转速得到不同厚度的产品的过程,在生产过程中会出现各种各样的问题。
2 电解铜箔发展史及国内外电解铜箔生产现状电解铜箔的发展可分为三个发展期:发展起步期(1955-1970年),这一时期主要是印刷电路板用铜箔开始生产,厚度为70~100μm。
快速发展期(1970-2000年),这一时期18~35μm的铜箔出现在市场并且被日本的铜箔企业垄断。
发展成熟期(2000年至今),主要是生产3~5μm的铜箔并应用于电池,世界各国对此均有不同程度的研究进展。
近年来国内铜箔生产企业在铜箔生产工艺流程以及产品质量方面均有了很大改善,但与国际先进铜箔生产企业-日本相比还有相当大的差距。
我国的进口铜箔主要是高档铜箔,而出口铜箔中90%以上是低档铜箔。
对于技术含量和附加值较高的高密度互连板(简称HDI)内层用铜箔和柔性电路板(简称FPC)用铜箔,几乎都是从日本、韩国、台湾等地进口。
由于材料加工精度的原因,国内铜箔生产企业购置的生箔机在长时间连续运行后材料表面状况不佳导致铜箔品质下降。
电解铜箔的制造方法

电解铜箔的制造方法概述电解铜箔是一种重要的金属材料,其制造方法广泛应用于电子、半导体等领域。
本文将详细介绍电解铜箔的制造方法及相关技术细节。
电解铜箔的定义电解铜箔是通过电解技术从铜离子中沉积出来的一种纯铜材料。
其表面光滑,具有优良的导电性能和机械强度,是制造高档电子产品所必需的重要材料。
电解铜箔的制造过程电解铜箔的制造过程主要包括溶液制备、电解过程、后处理等步骤。
下面分别进行详细介绍。
溶液制备制备电解铜箔的溶液通常由铜离子、酸、添加剂等组成。
其中,铜离子是电解铜箔制备的主要原料,酸可调节溶液的酸碱度,添加剂可以改善溶液的电解性能。
电解过程1.阳极制备:选择适当的铜材作为阳极,保证其纯度和表面质量。
阳极与阴极之间通过电解液连接。
2.电解槽设计:电解槽为铜箔的制备提供了必要的环境,通常采用复合结构,包括阳极槽和阴极槽。
3.电解条件设定:根据需求设置溶液的温度、电流密度等电解条件。
不同条件下,电解铜箔的性能和厚度也会有所差异。
4.电解过程:通过电解反应,铜离子在阴极上沉积成铜箔,同时在阳极上发生氧化反应,保持铜离子浓度的稳定。
后处理制备完成的电解铜箔需要进行后处理,以提高其质量和性能。
后处理主要包括去离子水洗、浸蚀、脱脂等工序。
1.去离子水洗:通过洗涤剂和去离子水去除电解槽中的杂质和余电解液,保证铜箔表面的纯净度。
2.浸蚀:使用酸性溶液对铜箔进行浸蚀,以消除铜箔表面的颗粒和不均匀结构,提高其光洁度和表面平整度。
3.脱脂:使用碱性溶液去除铜箔表面的油污,确保铜箔的清洁度。
电解铜箔的应用电解铜箔广泛应用于电子、半导体等领域。
具体应用如下:电路板制造电解铜箔是制造电路板的重要材料。
其具有良好的导电性能和机械强度,能够满足高密度、高速度的电路需求。
电子封装材料电解铜箔可以作为电子封装材料,用于制造IC封装、BGA封装等。
其表面光滑度高,能够提供良好的焊接性能和可靠性。
锂电池导电剂电解铜箔可以用作锂离子电池的导电剂。
电解铜箔毛刺缺陷的成因与对策

电解铜箔毛刺缺陷的成因与对策董景伟;牛晶晶;樊斌锋;任伟【摘要】Burr defect is easy to form on electrolytic copper foil during its production process.The microscopic morphology and composition of burr were characterized,and then the causes to burr formation were analyzed from several respects including the contents of impurities and chloride ions in electrolyte,H2SO4 and Cu2+ contents in copper dissolving tank,current density for electrolysis and thickness of copper foil in combination of years of practical production experience.Some countermeasures were given.%电解铜箔生产过程中易产生毛刺缺陷.先分析了毛刺的微观形貌和成分,再结合多年的生产实践经验,从电解液杂质和氯离子含量,溶铜罐中H2SO4和Cu2+含量,电流密度,铜箔厚度等方面分析了毛刺产生的原因,并给出了相应的解决措施.【期刊名称】《电镀与涂饰》【年(卷),期】2017(036)020【总页数】4页(P1104-1107)【关键词】电解铜箔;毛刺缺陷;铜离子;硫酸;杂质;氯离子;电流密度【作者】董景伟;牛晶晶;樊斌锋;任伟【作者单位】灵宝华鑫铜箔有限责任公司,河南灵宝472500;灵宝华鑫铜箔有限责任公司,河南灵宝472500;灵宝华鑫铜箔有限责任公司,河南灵宝472500;灵宝华鑫铜箔有限责任公司,河南灵宝472500【正文语种】中文【中图分类】TG178随着信息化产业的迅猛发展,电解铜箔作为电子信息领域的关键性基础材料,被广泛应用于覆铜板、印刷电路板以及锂离子电池制造等领域。
电解铜箔残铜产生的原因分析和解决措施
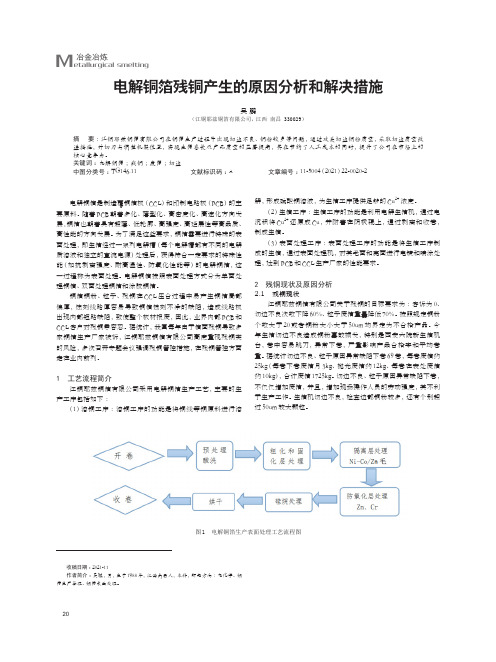
20Metallurgical smelting冶金冶炼电解铜箔残铜产生的原因分析和解决措施吴 鹏(江铜耶兹铜箔有限公司,江西 南昌 330029)摘 要:江铜耶兹铜箔有限公司在铜箔生产过程中出现切边不良、铜粉较多等问题,通过攻关切边铜粉质量,采取切边质量改进措施,并切刀与调整机架位置,实现生箔卷长及产品质量的显著提高,其在节约了人工成本的同时,提升了公司在市场上的核心竞争力。
关键词:电解铜箔;残铜;废箔;切边中图分类号:TG146.11 文献标识码:A 文章编号:11-5004(2021)22-0020-2 收稿日期:2021-11作者简介:吴鹏,男,生于1988年,江西南昌人,本科,研究方向:电化学、铜箔生产管理、铜箔表面处理。
电解铜箔是制造覆铜箔板(CCL)和印制电路板(PCB)的主要原料。
随着PCB 朝着多化、薄型化、高密度化、高速化方向发展,铜箔也朝着具有超薄、低轮廓、高强度、高延展性等高品质、高性能的方向发展。
为了满足这些要求,铜箔需要进行特殊的表面处理,即生箔经过一系列电解槽(每个电解槽都有不同的电解质溶液和独立的直流电源)处理后,获得符合一定要求的特殊性能(如抗剥离强度、耐高温性、防氧化性能等)的电解铜箔,这一过程称为表面处理。
电解铜箔按照表面处理方式分为单面处理铜箔、双面处理铜箔和涂胶铜箔。
铜箔铜粉、粒子、残铜在CCL 压合过程中易产生铜箔局部偏厚,蚀刻线路厚容易导致铜箔蚀刻不净的缺陷,造成线路板出现内部短路缺陷,致使整个板材报废,因此,业界内部PCB 和CCL 客户对残铜零容忍。
据统计,我国每年由于箔面残铜导致多家铜箔生产厂家被诉,江铜耶兹铜箔有限公司高度重视残铜类的风险,多次召开专题会议强调残铜管控措施,在残铜管控方面走在业内前列。
1 工艺流程简介江铜耶兹铜箔有限公司采用电解铜箔生产工艺,主要的生产工序包括如下:(1)溶铜工序:溶铜工序的功能是将铜线等铜原料进行溶解,形成硫酸铜溶液,为生箔工序提供足够的Cu 2+浓度。
铜箔表面处理过程产生的表面质量缺陷及对策

铜箔表面处理过程产生的表面质量缺陷及对策(序2)[所属分类:专家讲座] [发布时间:2012-5-16] [发布人:任中文] [阅读次数:249] [返回](接上期)5.铜箔光面黑点(暗点)5.1 定义铜箔光面因粘贴上异物或受异物污染、腐蚀,呈现发暗的小点,叫光面黑点。
5.2判定判定方法:在日光灯下用肉眼宏观检查,黑点不明显的,颜色不太深的,不仔细看,看不出来的判为合格品;黑点轻微可见,但数量较少,黑点较小,总面积较小,不严重的判为二级品;黑点明显的,即使黑点较小,面积较小也判为废品。
即使黑点较小,但数量较多,或占有的面积较大判为废品。
5.3 危害影响铜箔表面质量,影响覆铜板表面质量,影响线路板贴膜质量。
5.4产生原因分析及解决方法(1)产生原因之一:阳极板上的溶解物和附着物的粘污酸性处理槽里的阳极板上的溶解物和附着物,在电解液的搅动下从阳极板上脱落下来,随着电解液的流动落在铜箔上,或落在下导辊上,当铜箔与导辊接触时,在导辊上的这些污物有的粘在铜箔上,铜箔上的污物有的粘在导辊上。
这些污物粘在铜箔上是一个黑点,粘在导辊上的污物在与铜箔接触时有的还是粘在铜箔上,铜箔上的污物在运行时也粘在导辊上。
随着铜箔运行,导辊每转一周,导辊上的污物就粘在铜箔上一些,直至把污物粘没有了才结束。
如果粘在导辊上的是固体颗粒,当铜箔与导辊接触上后,有颗粒的地方承受的压力大,一是能把铜箔硌出凹坑,二是使铜箔与颗粒接触非常紧密,接触点铜箔上没有溶液,在铜箔与导辊接触的这段时间里,该点受到腐蚀可能比其它地方较轻,该点与铜箔其它地方的腐蚀程度不一样,没有液的地方,因没有液膜保护,反而氧化发暗,使铜箔表面颜色深浅不一样,铜箔接触颗粒被硌着的地方可能是有凹坑的原因发暗,时间长了成为黑色氧化点。
解决方法;及时刷洗阳极板,极距小要适当加大,一般极距在80—100毫米左右,铅--银阳极可以用薄的过滤布包起来,定期清洗阳极板,更换过滤布。
最好采用铜粒可溶阳极,将铜粒装在钛筐里,随着铜粒的消耗,不断的装填补充。
电解铜箔生产常见问题及处理

电解铜箔生产常见问题及处理电解铜箔生产常见问题及处理随着电子信息产业的发展,电子产品轻量化、集成化要求越来越高,电解铜箔作为电子行业的基础性材料,不仅对产品的抗拉强度、延伸率、抗剥离强度、防氧化性等物化性能指标提出了更高要求,而且要求铜箔微观晶粒组织和表面微观形貌结构更均匀精细。
电解铜箔生产工艺复杂,涉及专业广泛,生产过程既有机械电子设备又有电化学过程,分系统之间相互关联相互影响,相关技术大多是交叉、边缘学科,对处理实际生产中遇到的复杂问题缺乏成熟的理论支持。
本文通过对实际生产中常见问题的总结,提出了一些有参考价值的处理方法,希望能引起同行的注意和指正,引发更成熟的研究方法和处理方法。
1、溶液净化未处理箔(毛箔)的制造过程是铜箔生产中最关键的环节,绝大多数的物化性能指标与毛箔有着直接或间接的关系。
毛箔的电沉积过程离不开溶液,所以其溶液尤为重要,纯净无杂质、成分均匀稳定的毛箔溶液是生产高品质铜箔的必需条件。
实际生产中不可避免会有一些杂质通过原料铜、废箔、水、酸的加入和设备自身的磨损腐蚀进入到溶液中,因此生产中的溶液含有不溶性的微粒、可溶的离子分子基团和有机物等各种杂质,这些杂质大多数对铜箔品质有负面影响,应尽可能减少杂质进入溶液系统或采用有效方法把杂质控制在合理范围内。
不溶性微粒主要来源于原料铜的加入和废箔回用,活性炭和其它有机物吸附剂在使用中也会少量分解形成不溶性微粒。
在基箔电沉积过程中微粒夹杂于组织内或吸附于铜箔表面,造成箔面粗糙、针孔、渗透点等质量缺陷。
一般采用多级过滤的办法将微粒由大到小逐级过滤去除,过滤精度最高可以达到0. 5μm以内。
随着过滤层级的增加和过滤精度的提高溶液净化效果相应提高,铜箔组织的致密性和表面微观结构的细致性都明显优化,表现为延伸率、抗拉强度等指标的提高。
高度净化的基箔溶液是生产高品质铜箔前提条件之一。
增加过滤次数也是溶液净化的有效方法,通常循环过滤液量应为生产供液量的1.5倍以上。
电解铜箔毛刺缺陷的成因与对策

电解铜箔毛刺缺陷的成因与对策引言电解铜箔是一种重要的导电材料,广泛应用于印制电路板(PCB)的制造过程中。
然而,在制造过程中,可能会出现毛刺缺陷,这严重影响了铜箔的质量和性能。
因此,深入了解电解铜箔毛刺缺陷的成因,并采取相应的对策来解决这一问题是非常重要的。
电解铜箔毛刺缺陷的成因电解铜箔的毛刺缺陷主要由以下几个因素引起:1. 电解液成分电解液中的成分是引起电解铜箔毛刺的关键因素之一。
如果电解液中铜离子浓度过高,电流密度过大,电解液温度过高,会导致铜箔表面产生过多的铜离子,并且电解液的流动状态也会影响毛刺的形成。
2. 电解过程参数电解过程中的参数设置也会对电解铜箔毛刺产生影响。
例如,电流密度、电解时间、电极间距等参数设置不当都会导致毛刺的形成。
3. 铜箔材料和加工工艺铜箔的质量和加工工艺也会影响毛刺的形成。
如果铜箔的表面光洁度不够高,或者加工过程中存在过度的拉伸或收缩等问题,都可能导致毛刺的形成。
电解铜箔毛刺缺陷的对策针对电解铜箔毛刺缺陷,可以采取以下一些对策来解决这一问题:1. 优化电解液成分合理选择电解液成分是降低电解铜箔毛刺的重要方法。
控制电解液中铜离子浓度、电解液流动状态和温度,能够有效减少毛刺的形成。
此外,还可以添加一些表面活性剂和溶剂来改善电解液的性质,降低毛刺的产生。
2. 调整电解过程参数合理调整电解过程中的参数设置也是减少毛刺的有效方法。
通过适当降低电流密度、控制电解时间和电极间距等,可以有效减少毛刺的形成。
3. 提高铜箔质量和加工工艺优化铜箔材料的质量和加工工艺,对降低毛刺缺陷具有重要作用。
选择高质量的铜箔材料,确保其表面光洁度,减少加工过程中的过度拉伸或收缩等缺陷,可以有效减少毛刺的形成。
4. 采取适当的表面处理技术适当的表面处理技术也能有效降低电解铜箔毛刺缺陷。
例如,采用电解抛光、机械抛光、化学抛光等方法可以改善铜箔表面的光洁度,减少毛刺的生成。
5. 做好质量控制和检测建立严格的质量控制体系和检测方法,能够及时发现电解铜箔毛刺缺陷,并采取相应的措施进行修复或替换,确保产品质量。
电解铜箔表面处理-试题
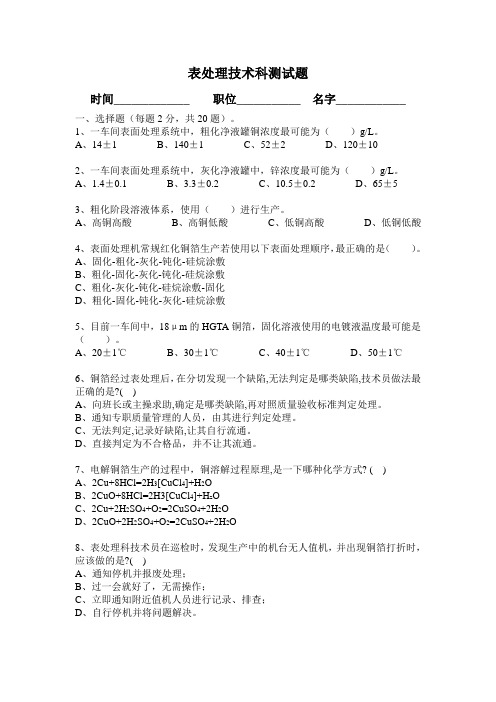
表处理技术科测试题时间_____________ 职位___________ 名字____________一、选择题(每题2分,共20题)。
1、一车间表面处理系统中,粗化净液罐铜浓度最可能为()g/L。
A、14±1B、140±1C、52±2D、120±102、一车间表面处理系统中,灰化净液罐中,锌浓度最可能为()g/L。
A、1.4±0.1B、3.3±0.2C、10.5±0.2D、65±53、粗化阶段溶液体系,使用()进行生产。
A、高铜高酸B、高铜低酸C、低铜高酸D、低铜低酸4、表面处理机常规红化铜箔生产若使用以下表面处理顺序,最正确的是()。
A、固化-粗化-灰化-钝化-硅烷涂敷B、粗化-固化-灰化-钝化-硅烷涂敷C、粗化-灰化-钝化-硅烷涂敷-固化D、粗化-固化-钝化-灰化-硅烷涂敷5、目前一车间中,18μm的HGTA铜箔,固化溶液使用的电镀液温度最可能是()。
A、20±1℃B、30±1℃C、40±1℃D、50±1℃6、铜箔经过表处理后,在分切发现一个缺陷,无法判定是哪类缺陷,技术员做法最正确的是?( )A、向班长或主操求助,确定是哪类缺陷,再对照质量验收标准判定处理。
B、通知专职质量管理的人员,由其进行判定处理。
C、无法判定,记录好缺陷,让其自行流通。
D、直接判定为不合格品,并不让其流通。
7、电解铜箔生产的过程中,铜溶解过程原理,是一下哪种化学方式? ( )A、2Cu+8HCl=2H3[CuCl4]+H2OB、2CuO+8HCl=2H3[CuCl4]+H z OC、2Cu+2H2SO4+O2=2CuSO4+2H2OD、2CuO+2H2SO4+O2=2CuSO4+2H2O8、表处理科技术员在巡检时,发现生产中的机台无人值机,并出现铜箔打折时,应该做的是?( )A、通知停机并报废处理;B、过一会就好了,无需操作;C、立即通知附近值机人员进行记录、排查;D、自行停机并将问题解决。
电解铜箔光面处理工艺
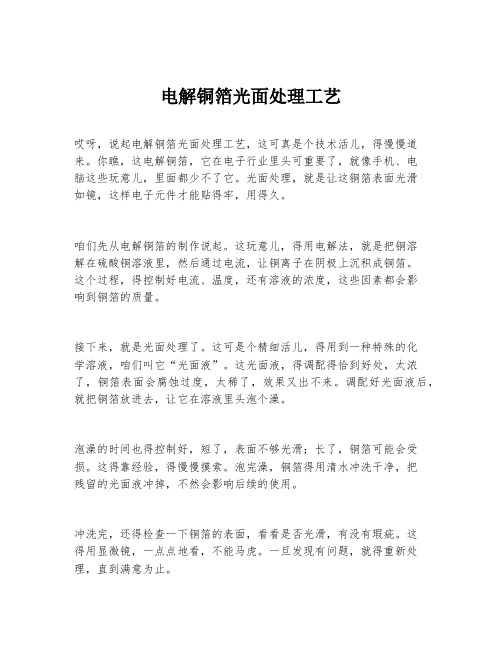
电解铜箔光面处理工艺哎呀,说起电解铜箔光面处理工艺,这可真是个技术活儿,得慢慢道来。
你瞧,这电解铜箔,它在电子行业里头可重要了,就像手机、电脑这些玩意儿,里面都少不了它。
光面处理,就是让这铜箔表面光滑如镜,这样电子元件才能贴得牢,用得久。
咱们先从电解铜箔的制作说起。
这玩意儿,得用电解法,就是把铜溶解在硫酸铜溶液里,然后通过电流,让铜离子在阴极上沉积成铜箔。
这个过程,得控制好电流、温度,还有溶液的浓度,这些因素都会影响到铜箔的质量。
接下来,就是光面处理了。
这可是个精细活儿,得用到一种特殊的化学溶液,咱们叫它“光面液”。
这光面液,得调配得恰到好处,太浓了,铜箔表面会腐蚀过度,太稀了,效果又出不来。
调配好光面液后,就把铜箔放进去,让它在溶液里头泡个澡。
泡澡的时间也得控制好,短了,表面不够光滑;长了,铜箔可能会受损。
这得靠经验,得慢慢摸索。
泡完澡,铜箔得用清水冲洗干净,把残留的光面液冲掉,不然会影响后续的使用。
冲洗完,还得检查一下铜箔的表面,看看是否光滑,有没有瑕疵。
这得用显微镜,一点点地看,不能马虎。
一旦发现有问题,就得重新处理,直到满意为止。
最后,处理好的铜箔,得小心翼翼地收起来,不能让它沾上灰尘,也不能让它受潮。
这关系到铜箔的使用寿命,可不能大意。
你看,这电解铜箔光面处理工艺,虽然听起来挺高大上的,其实就跟咱们日常生活中的一些事情差不多,都得细心、耐心,还得有点儿技巧。
这工艺,虽然复杂,但只要掌握了,就能做出高质量的铜箔,为电子行业做出贡献。
这事儿,说起来容易,做起来难,但只要用心,总能做到最好。
电解铜箔常见问题及解决方法
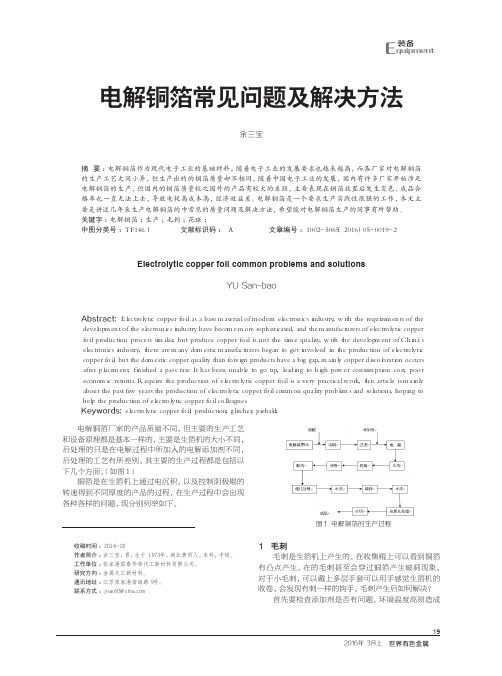
图 1 电解铜箔的生产过程
收稿时间 :2016-02 作者简介 :余三宝,男,生于 1973 年,湖北黄冈人,本科,中级。 工作单位 :张家港国泰华荣化工新材料有限公司。 研究方向 :金属化工新材料。 通讯地址 :江苏张家港南海路 9 号。 联系方式 :ysao93@sina.com
1 毛刺 毛刺是生箔机上产生的。在收集辊上可以看到铜箔
加大了添加剂的量,同时加大循环的背景的添加剂 的量。取样检测一下电解液的氯离子含量是不是偏小, 实际生产如果氯离子小于 20PPM 时,会有大量的毛刺 产生 [1]。
检查过滤器的压力,如果压力大,活性炭沉积过多, 则需要重新涂覆过滤器 ;检查电解液的颗粒含量和金属 杂质含量,是否正常。
毛刺的出现与上面 5 条有密切联系,掌握好这 5 点 毛刺基本能解决好 [2]。
电解铜箔的生产,但国内的铜箔质量较之国外的产品有较大的差距,主要表现在铜箔放置后发生变色、成品合
格率也一直无法上去,导致电耗高成本高,经济效益差。电解铜箔是一个要求生产实践性很强的工作,本文主
要是讲述几年来生产电解铜箔的中常见的质量问题及解决方法,希望能对电解铜箔生产的同事有所帮助。
关键字 :电解铜箔 ;生产 ;毛刺 ;花斑 ;
电解铜箔厂家的产品质量不同,但主要的生产工艺 和设备原理都是基本一样的,主要是生箔机的大小不同, 后处理的只是在电解过程中所加入的电解添加剂不同, 后处理的工艺有所差别,其主要的生产过程都是包括以 下几个方面。(如图 1)
铜箔是在生箔机上通过电沉积,以及控制阴极辊的 转速得到不同厚度的产品的过程,在生产过程中会出现 各种各样的问题,现分别列举如下。
Abstract: Electrolytic copper foil as a base material of modern electronics industry, with the requirements of the development of the electronics industry have become more sophisticated, and the manufacturers of electrolytic copper foil production process similar, but produce copper foil is not the same quality, with the development of China's electronics industry, there are many domestic manufacturers began to get involved in the production of electrolytic copper foil, but the domestic copper quality than foreign products have a big gap, mainly copper discoloration occurs after placement, finished a pass rate It has been unable to go up, leading to high power consumption cost, poor economic returns. Require the production of electrolytic copper foil is a very practical work, this article is mainly about the past few years the production of electrolytic copper foil common quality problems and solutions, hoping to help the production of electrolytic copper foil colleagues. Keywords: electrolytic copper foil; production; glitches; piebald;
电解铜箔生产溶铜方式及技术要求详解
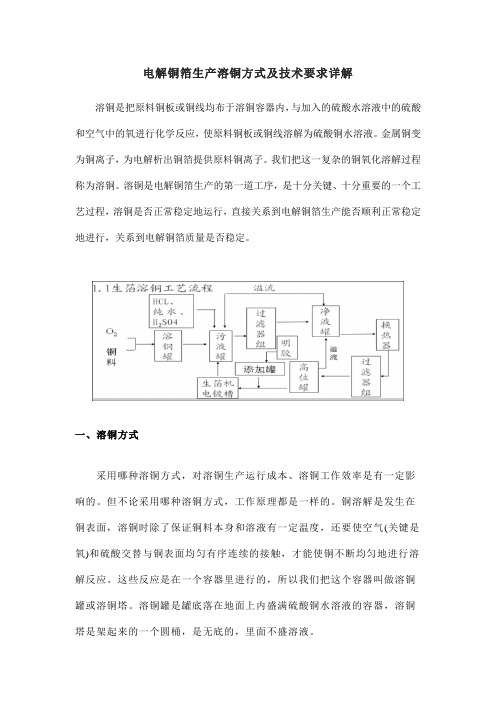
电解铜箔生产溶铜方式及技术要求详解溶铜是把原料铜板或铜线均布于溶铜容器内,与加入的硫酸水溶液中的硫酸和空气中的氧进行化学反应,使原料铜板或铜线溶解为硫酸铜水溶液。
金属铜变为铜离子,为电解析出铜箔提供原料铜离子。
我们把这一复杂的铜氧化溶解过程称为溶铜。
溶铜是电解铜箔生产的第一道工序,是十分关键、十分重要的一个工艺过程,溶铜是否正常稳定地运行,直接关系到电解铜箔生产能否顺利正常稳定地进行,关系到电解铜箔质量是否稳定。
一、溶铜方式采用哪种溶铜方式,对溶铜生产运行成本、溶铜工作效率是有一定影响的。
但不论采用哪种溶铜方式,工作原理都是一样的。
铜溶解是发生在铜表面,溶铜时除了保证铜料本身和溶液有一定温度,还要使空气(关键是氧)和硫酸交替与铜表面均匀有序连续的接触,才能使铜不断均匀地进行溶解反应。
这些反应是在一个容器里进行的,所以我们把这个容器叫做溶铜罐或溶铜塔。
溶铜罐是罐底落在地面上内盛满硫酸铜水溶液的容器,溶铜塔是架起来的一个圆桶,是无底的,里面不盛溶液。
1、浸泡式溶铜浸泡式溶铜是把原料铜板剪成小块或熔铸成线投入到溶铜罐里,硫酸水溶液和压缩空气从罐底进入,经过列管换热器加热后,从铜块缝隙间,以“Y”“Z”“S”形的流动路线,从下向上缓慢流动,在流动过程中与铜块表面接触,进行化学反应,使空气里的氧耗尽后,空气排入空中,溶液耗完了可以参加反应的部分硫酸后溢流出溶铜罐。
原料铜与氧和硫酸反应生成的铜离子,随溶液流出溶铜罐,进入电解液循环系统里,补充溶液因电解析出铜箔,溶液中减少的铜离子。
浸泡式溶铜的溶铜罐里始终装满溶液,原料铜浸泡在溶液中溶解。
浸泡式溶铜适用范围大、工艺条件宽,不受地区、气候条件影响。
溶铜罐小也能用,大也能用,气侯冷也能用,热也能用。
浸泡式溶铜一般要求溶液温度较高,大多数铜箔生产厂控制在70℃以上。
(1)浸泡式溶铜的供空气方式(也称供风方式)浸泡式溶铜一般采用无油空气压缩机供风,供风的目的一是供氧,二是用风对溶液进行搅拌,因为空压机供给的空气进出口都有过滤设备,可以去除空气里的灰尘等杂质,为溶铜提供十分洁净的空气,消除了因空气脏对电解液的污染。
浅谈电解铜箔常见问题
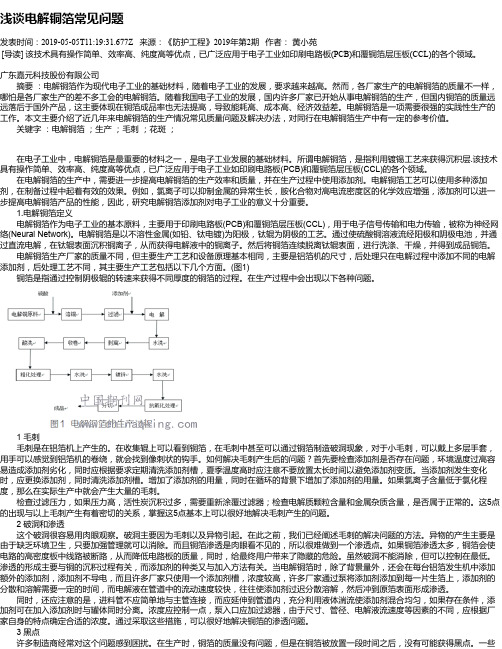
浅谈电解铜箔常见问题发表时间:2019-05-05T11:19:31.677Z 来源:《防护工程》2019年第2期作者:黄小苑[导读] 该技术具有操作简单、效率高、纯度高等优点,已广泛应用于电子工业如印刷电路板(PCB)和覆铜箔层压板(CCL)的各个领域。
广东嘉元科技股份有限公司摘要:电解铜箔作为现代电子工业的基础材料,随着电子工业的发展,要求越来越高。
然而,各厂家生产的电解铜箔的质量不一样,哪怕是各厂家生产的差不多工会的电解铜箔。
随着我国电子工业的发展,国内许多厂家已开始从事电解铜箔的生产,但国内铜箔的质量远远落后于国外产品,这主要体现在铜箔成品率也无法提高,导致能耗高、成本高、经济效益差。
电解铜箔是一项需要很强的实践性生产的工作。
本文主要介绍了近几年来电解铜箔的生产情况常见质量问题及解决办法,对同行在电解铜箔生产中有一定的参考价值。
关键字:电解铜箔;生产;毛刺;花斑;在电子工业中,电解铜箔是最重要的材料之一,是电子工业发展的基础材料。
所谓电解铜箔,是指利用镀锡工艺来获得沉积层.该技术具有操作简单、效率高、纯度高等优点,已广泛应用于电子工业如印刷电路板(PCB)和覆铜箔层压板(CCL)的各个领域。
在电解铜箔的生产中,需要进一步提高电解铜箔的生产效率和质量,并在生产过程中使用添加剂。
电解铜箔工艺可以使用多种添加剂,在制备过程中起着有效的效果。
例如,氯离子可以抑制金属的异常生长,胺化合物对高电流密度区的化学效应增强,添加剂可以进一步提高电解铜箔产品的性能,因此,研究电解铜箔添加剂对电子工业的意义十分重要。
1.电解铜箔定义电解铜箔作为电子工业的基本原料,主要用于印刷电路板(PCB)和覆铜箔层压板(CCL),用于电子信号传输和电力传输,被称为神经网络(Neural Network)。
电解铜箔是以不溶性金属(如铅、钛电镀)为阳极,钛辊为阴极的工艺。
通过使硫酸铜溶液流经阳极和阴极电池,并通过直流电解,在钛辊表面沉积铜离子,从而获得电解液中的铜离子。
- 1、下载文档前请自行甄别文档内容的完整性,平台不提供额外的编辑、内容补充、找答案等附加服务。
- 2、"仅部分预览"的文档,不可在线预览部分如存在完整性等问题,可反馈申请退款(可完整预览的文档不适用该条件!)。
- 3、如文档侵犯您的权益,请联系客服反馈,我们会尽快为您处理(人工客服工作时间:9:00-18:30)。
电解铜箔生产常见问题及处理随着电子信息产业的发展,电子产品轻量化、集成化要求越来越高,电解铜箔作为电子行业的基础性材料,不仅对产品的抗拉强度、延伸率、抗剥离强度、防氧化性等物化性能指标提出了更高要求,而且要求铜箔微观晶粒组织和表面微观形貌结构更均匀精细。
电解铜箔生产工艺复杂,涉及专业广泛,生产过程既有机械电子设备又有电化学过程,分系统之间相互关联相互影响,相关技术大多是交叉、边缘学科,对处理实际生产中遇到的复杂问题缺乏成熟的理论支持。
本文通过对实际生产中常见问题的总结,提出了一些有参考价值的处理方法,希望能引起同行的注意和指正,引发更成熟的研究方法和处理方法。
1、溶液净化未处理箔(毛箔)的制造过程是铜箔生产中最关键的环节,绝大多数的物化性能指标与毛箔有着直接或间接的关系。
毛箔的电沉积过程离不开溶液,所以其溶液尤为重要,纯净无杂质、成分均匀稳定的毛箔溶液是生产高品质铜箔的必需条件。
实际生产中不可避免会有一些杂质通过原料铜、废箔、水、酸的加入和设备自身的磨损腐蚀进入到溶液中,因此生产中的溶液含有不溶性的微粒、可溶的离子分子基团和有机物等各种杂质,这些杂质大多数对铜箔品质有负面影响,应尽可能减少杂质进入溶液系统或采用有效方法把杂质控制在合理范围内。
不溶性微粒主要来源于原料铜的加入和废箔回用,活性炭和其它有机物吸附剂在使用中也会少量分解形成不溶性微粒。
在基箔电沉积过程中微粒夹杂于组织内或吸附于铜箔表面,造成箔面粗糙、针孔、渗透点等质量缺陷。
一般采用多级过滤的办法将微粒由大到小逐级过滤去除,过滤精度最高可以达到0. 5μm以内。
随着过滤层级的增加和过滤精度的提高溶液净化效果相应提高,铜箔组织的致密性和表面微观结构的细致性都明显优化,表现为延伸率、抗拉强度等指标的提高。
高度净化的基箔溶液是生产高品质铜箔前提条件之一。
增加过滤次数也是溶液净化的有效方法,通常循环过滤液量应为生产供液量的1.5倍以上。
提高溶液的净化,设备投入和运行费用会大幅增加,在净化工艺设计时要兼顾工艺性和经济性。
过滤器在初期运行时往往达不到设计精度,使用一段时间后过滤材料的表面会因为滤渣的沉积而产生“搭桥”作用,过滤压力略微增加而过滤精度提高并更稳定,所以过滤器的清洗和滤料的更换应该交替周期处理,前一级和后一级过滤器不宜同时进行,避免因集中处理造成溶液净化度发生波动。
可溶性的离子分子基团对铜箔质量的影响机理非常复杂。
溶液中的离子除Cu2+、H+及SO42-之外都会干扰铜箔正常的电沉积过程。
某些金属阳离子直接参与铜箔晶体的成核过程,导致铜箔微观组织结构缺陷——孪晶、错层等;这些金属阳离子杂质具有与Cu2+的离子水合物体积大小接近或硫酸体系下电极电位接近的特点。
Cu+离子在正常溶液中含量极少,而且随着H2SO4浓度的提高而降低;Cu+离子自身会发生歧化反应生成Cu0和Cu2+,Cu0呈分子状态分散在溶液中,阴极沉积时随机夹杂于铜箔组织中,其结晶尺寸远比正常结晶大的多,使箔层出现毛刺、粗糙、针孔等缺陷;在溶铜时氧化不充分会产生Cu+离子,所以溶铜应保证鼓风量大于铜氧化需氧量,促进Cu完全氧化生成Cu2+,同时控制好H2SO4浓度抑制Cu+离子产生,溶铜出液H2SO4浓度不应低于60g/l,另外加入适量双氧水可促使Cu+离子转化为Cu2+离子。
Cu的同族金属的影响不容忽视,例如Ag+离子,应尽可能防止其进入溶液或设法清除。
H+离子是电流的主要传递介质,其浓度大小与槽电压呈正比关系,所以适当提高H+离子浓度可以减少制造基箔的电能消耗;但H+浓度增加设备尤其是阴极辊、阳极板腐蚀速度加快,H+浓度过高铜箔表面出现粗化趋势。
溶液中的阴离子主要影响阳极反应过程,某些小基团阴离子也参与阴极反应过程,如卤族元素F-、Cl- 等。
氢氟酸是钛的强溶剂,常温下即使微量也会腐蚀阳极板、阴极辊,应严禁F-离子进入溶液。
Cl-离子活性较F-离子略低一些,在酸性和加热条件下对钛有腐蚀性,Cl-离子浓度不宜太高。
Cl-离子在溶液中一方面与Cu+离子反应生成CuCl胶体颗粒,抑制了Cu+的影响,同时也是一种有效的光亮剂,负电性的Cl-离子因电场作用虽然只有少量在阴极附近,仍然参与了Cu2+的阴极沉积过程。
Cl-离子的存在影响了Cu的转化结晶速度,提高了阴极极化,使铜箔晶粒组织和表面均匀细致。
氯离子的浓度范围10—50mg/l,浓度太低不能发挥光亮剂作用,浓度过高铜箔表面粗糙并产生毛刺,设备腐蚀速度加快。
溶液中的可溶性杂质在正常生产时多数在合理浓度范围内波动,不会影响铜箔品质,少量杂质会随着生产时间延长在溶液中逐渐积累,有时管理不善或生产事故造成杂质超标,需要去除过量的杂质以保持溶液洁净。
小电流电解法是一种有效的去除杂质方法,应用范围广而且使用过程不会造成新的污染,通常电流密度控制在100A/m2以内,电流和液流量根据时间呈梯度调整,在阴极辊表面会沉积出富集杂质元素的铜镀层。
有机吸附剂可以和某些杂质生成絮凝物,利用这个特性可以通过活性炭过滤去除杂质。
化学沉淀法会生成难以过滤的细小颗粒,造成二次污染,应慎重使用。
有机物杂质主要来自明胶、原料铜油污、设备润滑油脂等。
明胶在溶液中受Cu2+离子影响和电场作用,会失去活性发生凝聚变成有害物质。
活性炭可以吸附变质明胶并且对明胶的浓度有调控作用,但是活性炭对油脂类的去除效果不理想。
油污、油脂杂质容易造成铜箔针孔,应加强原材料的清洗,从源头上防止油污进入溶液。
加入双氧水或用紫外线照射可促进油脂的分解,再利用活性炭吸附去除。
硅藻土也是一种有效的有机吸附剂,而且对溶液中某些杂质离子有选择吸附的能力,用于铜箔生产的硅藻土应经过特殊的预处理,使用中要加强溶液的过滤。
2、阴极辊表面质量与抛光由于阴极辊表面是铜箔沉积成箔的基础,辊面质量不仅与铜箔光面的表观质量有直接关系,而且对铜箔的内在质量和粗糙(毛)面微观形态有间接影响,所以阴极辊抛光是铜箔生产的关键工序。
制造阴极辊的钛材是一种稀有高熔点金属,具有比强度大、塑性高的特点,高纯钛的延伸率可达到50%以上,常温下与空气接触表面会形成致密的氧化物保护层,耐化学腐蚀性能优异。
钛的性能与材料纯度有很大关系,钛的间隙杂质如过渡族元素、硼族、碳族、氮族、氢等使其晶格发生畸变,防腐性能和塑性显著降低,强度得到大幅度提高。
制造阴极辊一般使用高纯度的TA1钛材,常温下为体心立方晶格的α相,经过强力旋压加工,表面晶粒得到进一步细化。
阴极辊的抛光工艺通常分为研磨(粗抛光)和抛光(精抛光)两个工序,通过研磨可以消除新使用阴极辊表面车削加工痕迹和已使用阴极辊表面氧化、损伤,进一步的抛光工序使辊面色泽均匀柔和、微观结构细腻,满足高档铜箔生产工艺要求。
研磨工序的关键是确保磨料和磨削钛屑不能在辊面积留。
不论采用砂带研磨还是采用PVA磨轮研磨,从辊面磨削下来的钛屑和脱落的磨料容易黏附在钛辊表面,形成橘皮、划伤、表面硬化等质量缺陷。
选择合适的研磨材料、调整研磨材料对辊面的磨削速度、控制研磨材料对辊面的压力、加强辊面清洗,是解决辊面抛光质量缺陷的有效途径。
经过研磨的辊面光洁度要达到0.5um以内。
抛光(精抛光)材料一般采用疏松纤维状材料制成的抛光轮,磨料黏结在纤维表面,抛光时由于纤维的弹性作用,磨料在辊面呈现弹跳点击式磨削。
在电子显微镜下放大1000倍观察铜箔光面微观形貌可以看出,研磨后微观表面沿纵向有浅沟状刮削痕迹,抛光微观辊面呈现点状浅坑,所以抛光后的阴极辊更加均匀柔和,表面光洁度可以达到0.3um以内,生产的铜箔纵向和横向之间物化性能指标更为接近。
由于铜箔沉积是在辊面的“复制叠加”过程,粗糙面的微观峰谷结构与辊面光洁度有间接关系,辊面的微观表面构造是铜箔电结晶的生长点。
抛光时需要注意控制抛光轮对辊面的接触面大小和接触压力,增加抛光轮的摆动频率。
阴极辊在空气中很快形成钝化膜,所以辊面抛光要随时保持湿润状态,防止辊面氧化变色。
3、生箔电解过程电解生箔工艺和普通硫酸盐镀铜原理有相似之处,但其生产目标、工艺参数、设备结构都完全不同。
铜箔生产是高速电沉积过程,通过提高Cu2+离子浓度、提高溶液温度、增加溶液流量和缩小阴阳极间距来实现快速电沉积的目的。
铜箔阴极沉积是典型的硫酸单盐高速电沉积过程,Cu2+以水化离子形式存在于溶液中,阴极还原经历几个阶段。
首先是Cu2+的水化离子在电场作用下迁移到阴极表面液层,离子水化数降低或水化层重排:(m – n)H2O Z m H2O - n H2O →Cu2+Z Cu2+ (m>n)失水的Cu2+水化离子得电子还原过程分步进行,得到一个电子转化成Cu+水化离子,继续得到电子生成Cu原子吸附在阴极表面:(m – n)H2O + e Z Cu2+(m – n)H2O Z⇔Cu+(m –Z(m – n)H2O + e ⇔Cu Z Cu+ n)H2O吸附原子失去水化层进入金属晶格形成致密的结晶组织;(m – n)H2O - (m – n)H2O→Z Cu Cu10-2A/cm2,电极反应速度很快,几乎不存在电化学极化现象,在没有其它工艺条件配合的情况下不容易生成结晶细致的铜层。
由于Cu 的电极电势远高于氢离子的析出电势,Cu的阴极沉积极少出现析氢现象。
Z Cu的阴极交换电流高达3生箔的阳极过程是析氧反应,可溶性铅合金阳极和不溶性钛阳极的反应稍有不同。
铅阳极表面氧化生成PbO,PbO导电性不佳而且结构疏松容易脱落,PbO在电场和O的双重作用下继续得到电子生成棕黑色的过氧化铅PbO2,PbO2导电性优良结构致密,是铅阳极的主要导电层,而且阻止了铅阳极继续氧化,提高了铅阳极的使用寿命。
电解生箔的主要工艺参数和工艺条件有:Cu2+浓度,H2SO4浓度,添加剂,温度,电流密度,溶液流量等。
Cu2+浓度范围一般控制在70—100g/l,Cu2+含量低溶液的分散能力好但极限电流密度降低,Cu2+含量高可以提高极限电流密度,从而提高设备生产能力,但是硫酸铜结晶容易析出造成管道堵塞,而且溶液分散能力下降导致铜箔粗糙。
H2SO4是主要的导电介质,一般控制在80—120g/l,由于共同离子效应,提高H2SO4浓度可以提高阴极极化作用,使铜箔结晶细致,而且可以降低电解电压;H2SO4浓度过高会导致硫酸铜容易结晶析出,设备腐蚀速度加快。
经常使用的添加剂有明胶、改性明胶、硫脲等高分子有机物,主要作为整平剂使用,共同特点是分子具有正负两性结构。
根据金属离子还原的表面扩散理论,Cu2+转变成吸附原子后沿阴极表面到达生长点并进入晶格,整平剂由于两性结构,其正电性一端优先吸附在阴极表面的放电点,抑制了Cu在阴极表面的集中沉积,促使阴极表面形成更多的次一级的生长点,提高了阴极极化,有利于获得细小的晶粒,使铜箔电沉积更均匀。