板料成形数值模拟中回弹问题的处理
板料多步冲压回弹的数值模拟研究

板料多步冲压回弹的数值模拟研究作者:江苏大学陈炜王晓路高霖摘要:回弹是板料冲压成形过程中一种常见但很难解决的现象。
首先研究了板料弯曲变形中卸载回弹的原理,然后以依维柯侧壁上内板为例,采用动态和静态算法相结合的方法,在考虑每道工序板料回弹的基础上,对其进行多步冲压回弹的数值模拟,最后对模拟结果和实验结果进行比较,验证该模拟方法提高回弹计算精度的有效性,为板料冲压成形工艺的制定提供科学依据。
关键词:回弹;多步冲压;数值模拟中图分类号:TG386.41 文献标识码:A 文章编号:1 前言通常,一个完整的冲压过程要经过拉延、整形、修边、冲孔、翻边等多步工序才能完成。
在这一过程中,回弹是板料成形工艺制定中要考虑的关键因素,零件的最终形状取决于成形后的回弹量,当回弹量超过允许容差后,就成为成形缺陷,影响零件的几何精度。
特别是近几年来由于高强度薄钢板和铝合金板材的大量使用,回弹问题更为突出。
目前,板料回弹的精确预测以及如何减小回弹量、降低残余应力成为板料成形模拟中的热点问题。
从NUMISHEET’93(第二届板料成形三维数值模拟国际会议)开始,每届会议都有关于回弹预测的标准考题(BENCHMARK),在NUMISHEET’99上,专门有一个关于回弹预测和回弹误差控制的会议专题,其中文章达到10篇,约占全部会议文章的11﹪[1];而在NUMISHEET’2002上,关于回弹预测和控制的会议专题论文达20篇之多,占到全部会议论文的21﹪以上[2]。
在实际生产中要控制和补偿回弹,提高回弹预测的精度是至关重要的[3]。
通常我们在进行板料多步冲压的回弹预测时,都忽略了板料每道工序后的卸载回弹,未将其回弹考虑到下一道工序的计算之中,然而板料的最终形状是其整个变形历史的累积效应,其变形历史等对残余应力和回弹计算都有一定影响[4],那么因忽略了每道工序后的回弹而产生的累积误差势必影响最终的回弹预测精度。
本文在进行板料多步冲压数值模拟时以依维柯侧壁上内板为例,采用动态和静态算法相结合的方法[4]来模拟其多步冲压过程,将前一道工序的回弹计算结果作为下一道工序的输入,并通过模拟结果和实验结果的对比来验证该数值模拟过程的正确性及有效性。
高速成形中减小回弹的方法及数值模拟

过 同 样 的 方 法 在 56787 中 生 成 的 网 格 模 型 如 图 % ( *) 所示。 在原凹模的模拟中发现零件的弯曲区域与凹模 的接触并不非常理想,而把凹模局部设计成图 ( % () 形状就是为了在成形过程中使材料与模具接触较理 想,减小成形后板料的内应力。更改凹模结构后的 模拟步骤和参数均与更改凹模前的模拟步骤和参数 是一致的。 最后通过计算和后处理可得到变形、 应力、 摩擦 力。求解后的变形图和应力云图如图 2 所示。 !/& 凹模更改前后模拟结果的对比 从更改凹模结构前后的数值模拟中可看出,在 零件 头 部 图 & ) 9 + 工 位 成 形 时 所 受 的 应 力 是 有 差 别
图# 排样图
元类 型 选 为 C/DE:’$&, 把 零 件 可 能 变 形 的 部 分 定 义为接触面, 单元类型选为 3F5C/’G’, 模拟中各参 数见表 ’ 所示。
会 出现零件尺寸不稳定现 象 , 而 需 要 频 繁 地 修 模 , 导致生产效率的降低。
(() 头部打薄
) * + 头部成形 图% 成形工位图
) , + 头部成形
) - + 整形
模具工业 #$$% 年第 &# 卷第 ’ 期
!"
(() 原凹模局部形状
(() 结构变形图
) * + 网格模型图 图! 原凹模局部形状及网格模型图
表"
类型 坯料 模具 弹性模量 , -.( " / " 0 "$1 # / # 0 "$
1
模拟参数表
摩擦因数 $/ & $/ & 抗剪强度 屈服强度 , -.( — &$$ , -.( #$$ —
基于数值模拟的板材渐进成形回弹技术应用研究

基于数值模拟的板材渐进成形回弹技术应用研究一、引言板材成形是现代制造业中常见的金属加工方式之一。
在板材成形过程中,由于材料性质的差异和成形过程中的应力变化,常常会产生回弹现象,影响成形件的精度和质量。
研究渐进成形回弹技术是非常重要的。
数值模拟技术是一种有效的手段,可以帮助工程师预测和分析成形过程中的各种物理现象,对于渐进成形回弹技术的研究也起着至关重要的作用。
本文将围绕基于数值模拟的板材渐进成形回弹技术应用展开研究。
二、板材渐进成形回弹技术的基本原理1. 渐进成形渐进成形是一种经典的板材成形方法,它通过逐步改变板材形状,使得板材得到需要的几何形状。
在渐进成形过程中,板材会受到复杂的应力和应变作用,从而产生回弹现象。
2. 回弹机理回弹是板材成形过程中不可避免的现象,它主要是由于成形过程中材料的弹性变形和应力释放所引起的。
当板材在成形后释放外部应力时,材料会产生弹性恢复,使得成形后的形状发生变化,导致回弹。
渐进成形回弹技术旨在通过调整成形工艺参数和工序顺序,减少或控制板材成形后的回弹变形,从而获得满足要求的成品。
这种技术需要借助数值模拟来预测和分析成形过程中的各种物理现象,以便制定合理的成形工艺参数和工序。
1. 数值模拟方法数值模拟是一种通过计算机模拟真实物理现象的方法,可以用于预测和分析成形过程中的各种物理现象,包括应力分布、应变分布、热变形等。
常见的数值模拟方法包括有限元法、有限体积法、边界元法等。
这些方法可以有效地模拟板材成形过程中的各种物理现象,为渐进成形回弹技术的研究提供必要的数据基础。
2. 渐进成形回弹数值模拟模型在板材渐进成形回弹技术的研究中,需要构建合适的数值模拟模型,用于预测和分析成形过程中的回弹变形。
这个模型需要考虑材料的本构关系、成形工艺参数、板材初形等因素,以准确地描述成形过程中的应力和应变分布,从而预测回弹变形。
3. 数值模拟与实验验证数值模拟技术的研究需要与实验验证相结合,以保证数值模拟的准确性和可靠性。
板料成形回弹模拟

第6卷第3期1999年9月塑性工程学报JOU RNAL O F PLA ST I C IT Y EN G I N EER I N GV o l16 N o13Sep t1 1999板料成形回弹模拟Ξ(北京航空航天大学 100083) 张晓静 周贤宾摘 要 本文阐述了板料成形数值模拟中回弹问题的研究历史和发展现状,总结了回弹模拟的算法,从成形过程模拟和回弹计算两方面系统分析了影响回弹模拟准确性和收敛性的主要因素及改进方向,并进一步讨论了模具设计中回弹的补偿算法。
关键词 板料成形 回弹模拟 有限元 动态显式 静态隐式1 前 言在板料成形领域,回弹是模具设计中要考虑的关键因素,零件的最终形状取决于成形后的回弹量。
回弹现象主要表现为整体卸载回弹、切边回弹和局部卸载回弹,当回弹量超过允许容差后,就成为成形缺陷,影响零件的几何精度。
因此,回弹一直是影响、制约模具和产品质量的重要因素。
随着汽车工业和航空工业的发展,对薄板壳类零件成形精度的要求越来越高,特别是近年来由于高强度薄钢板和铝合金板材的大量使用,回弹问题更为突出,成为汽车和飞机等工业领域关注的热点问题。
目前,回弹计算功能及回弹模拟精度,已成为衡量板料成形有限元模拟软件技术水平的重要标志之一。
本文旨在总结板料成形回弹模拟计算的研究历史和发展现状,分析影响回弹模拟精度的主要因素及存在问题,希望能对板料成形有限元数值模拟技术的研究者提供一些启发,也为工艺和科研人员更好地利用现有的有限元分析软件,解决工程实际问题提供一些帮助。
2 研究历史与发展现状在过去几十年间,世界各国在回弹的预测及减小方法方面作了大量的工作,建立了一些描述和预测零件回弹的数学模型。
早期的工作主要基于解析法对一些简单零件纯弯曲或拉弯成形的回弹进行分析[1,2]。
M ai H uang和Jam es C.Gerdeen[3]总结了1994年以前板料成形回弹问题的研究状况,分析了双曲度可展曲面零件的回弹规律,并介绍了大约90篇参考文献。
板料冲压成形回弹补偿修正方法及其验证_李延平

H=
F 2( F 2(
$d ) $p )
=
F 2( d 2) - F 2( d 1) F 2( p 2) - F 2( p 1)
( 4)
可见, 如果已知两组相近的模具形状数据和对
应的冲压件形状数据, 即可计算出模具 - 冲压件偏 差频域传递函数 H 。
如果对模具 Ñ 进行补偿修正( 修正后新模具的
形状测量数据为 d * ) , 使其对应的冲压件为给出的
例系数为 H 。
# 488 #
汽车工程
2005 年 ( 第 27 卷) 第 4 期
如果设模具 Ñ 形状测量数据为 d 1、对应的冲压 件 Ñ 形状测量数据为 p 1, 模具 Ò 形状测量数据为 d 2、对应的冲压件 Ò 形状测量数据为 p 2, 在线性小
量回弹情况下, $d = d 2 - d1; $p = p 2 - p 1, 那么 由式( 3) 得
数值模拟效率高费用低由于计算模型与实际工况有差距导致计算精度较可靠性较差优化结果难以满足工程实际需要以线性闭环控制系统空间fourier变换和频域传递函数为理论基础基于模具实验迭代建立了模具回弹补偿修正算法板料冲压成形回弹补偿修正算法211回弹补偿修正系统工作原理板料冲压成形模具回弹补偿修正系统工作原理如图首先应用cad系统设计初始模具通过经国家863项目2001aa421270和十五国家科技攻关项目2001ba205b1001资助原稿收到日期为2004修改稿收到日期为2004验知识和ca仿真使模具初始设计尽量满足成形要求不存在起皱开裂等缺陷系统制作模具原型采用快速模具弧喷涂等快速制造模具在冲压机上进行样件试冲压调整工艺参数使样件没有起皱开裂等缺陷保持工艺参数稳定对试冲压样件进行三维激光扫描测量评价其尺寸误差若样件尺寸误差满足要求模具即为最终设计模具否则在保证冲压成形性能前提下按合适的模具修正方法进行模具型面修正根据模具型面修正数据制造新模具在原冲压工艺参数下进行新的样件试冲压激光扫描测量和尺寸误差评价若新样件尺寸误差满足要求新模具即为最终设计模具否则重复以上迭代过程直至满足要求为止是高度非线性的所以整个系统也是非线性的必须对其进行线性化处理才能用简单的算法实现回弹补偿
板料冲压成形及回弹有限元模拟分析

Ku=F
式中K为总刚度矩阵;u为位移向量;F为节点载荷向量。
在隐式算法中,对于第i个给定的加载增量,用Newton-Raphson迭代法,需要求解下面的方程:
板料冲压成形及回弹有限元模拟分析
摘要
回弹是板材冲压成形过程中不可避免的普遍现象,直接影响到冲压件的尺寸精度和零件最终形状。本文利用ANSYS/LS-DYNA有限元软件中的非线性动力的显式、隐式连续求解功能,模拟了板料冲压成形过程与卸载后板料回弹变形的全过程,得到了成形过程中任一时刻各处Von-Mises应力云图和应变值及卸载后板料的回弹结果,帮助我们更好的认识分析板料冲压成形以及回弹过程中物质内部的变化。
ANSYS/LS-DYNA是一个通用的显示非线性动力分析有限元程序,近年来开发的板料冲压成形数值模拟新功能,取得了很大成功。通过计算,可以观察板料冲压成形过程中的变形状态、应力状态和壁厚变化,了解可能出现的起皱和开裂现象。此外,ANSYS/LS-DYNA程序具有显式、隐式求解功能,用显式求解模拟动态成形过程,然后用隐式求解模拟线性回弹变形。这不仅能够模拟材料变形过程,而且也能较好地计算回弹现象,比较准确地得到材料最终成形状态。
关键词:板材冲压,回弹,非线性有限元分析,数值模拟
Sheet metal stamping and rebound finite element simulation analysis
Abstract
The rebound is inevitable common phenomenon in sheet metal forming process, a direct impact on the final shape to the dimensional accuracy of the stampings and parts. In this paper, the nonlinear dynamic finite element software ANSYS / LS-DYNA explicit, implicit sequential solution function to simulate thespringbackdeformation of the sheet after sheet metal stamping process and uninstall the whole process, forming process at any time throughout the Von-Misesstress cloud and strain and after unloading sheetspringbackresults, help us to a better understanding analysis sheet metal stamping and rebound process material internal changes.
CAE仿真经典文献系列之《板料冲压成形回弹的数值模拟》
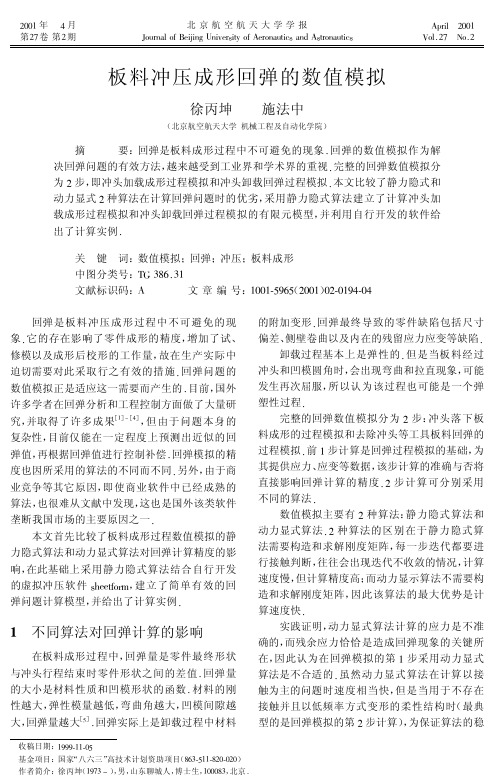
( i) ( i) 正向量; 为外力向量; 为内力向量 . P @ 位移增量由 (3) 式得到 . ( i +l) ( i) ( i) = !u + C !u 算法中的要点如下:
(3)
同的增量方法将所有接触节点力按比例卸载, 直 到接触节点力消失 . 具体的可总结如下: 首先给拉深结束后的板料一个假想的应力状 态! , 该应力与拉深结束后板料的应力 !E 相平 衡, 可以使变形板料在进行回弹分析的开始处于 静态平衡状态 . 在分析过程中, 假想应力按照步长
图3
回弹后的零件截面线形状
回弹现象进行了模拟, 证明该算法还是比较稳定 可靠的 图 1 和图 2 给出了采用该算法对轨道件 拉深成形和回弹后形状的模 拟 结 果 其 中, E 2 6 8 MPa, 3, c 8 mm, f 1, ! " 4 216 (1 537 96 #) MPa 该 零 件 为 NUMISHEET’ 标准考题 图 3 为该标准考题给出的回弹后的零 件截面线形状, 该截面线过图 2 所示 E 、 F点 对 比图 1 和图 2 可以看出, 由于残余应力作用, 轨道 件拉深卸载后发生了较为明显的回弹现象 轨道 底部与侧壁间弯曲角变大, 侧壁向外倾斜; 侧壁与 凸缘间弯曲角变小, 凸缘向下倾斜 对比图 2 和 图 3 可知, 回弹模拟结果与标准考题参考结果基
[1]Joannic D,GeIin J C Accurate simuIation of springback in 3D sheet [ A] In:NUMIFORM’ [ C] 1995 729 metaI forming processes 95 ~ 734 [2] KarafiIIis A P,Boyce M C TooIing design in sheet metaI forming [ J] Int J Mech Sci,1992,34 (2 ) : using springback caIcuIations 113 ~ 131 [ 3]Wu Longwu Iterative FEM die surface design to compensate for spri[ A ] In: [ C] NUMIFORM ’ 95 ngback in sheet metaI stampings 1995 637 ~ 641 [4]宋 黎, 杨 坚, 黄天泽 板料弯曲成形的回弹分析与工程控 制综述 [ J] 锻压技术, (1) :18 ~ 22 1996,21 [5] Shu Jawshi,Huang Chinghua Finite eIement anaIysis and optimiza“doubIe-bend”technigue [ J] Int J tion of springback reduction:the (4) :423 ~ 434 Mech TooIs Manufacture,1996,36 [6] Mercer C D,NagtegaaI J D,RebeIo N,ec al Effective appIication
板料成形回弹模拟及补偿技术研究现状
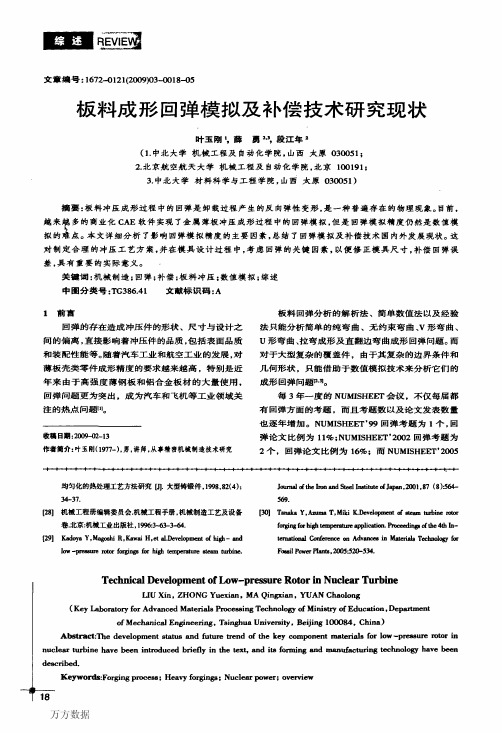
steam
turbine
rotor
forging for
application.Pmceedinss dthe 4th In—
Y,M%,oehi R。Kawai H,et a1.Development of IIigh—and
rotor
territorial C叩fe唧脱Oll Advances in M砒e血118 Technology for
收藕日期:2009-02—13 作者简介:叶玉刚(1977一),男,讲师,从事精密机械制造技术研究
成形回弹问题鲫。 每3年一度的NUMISHEET会议。不仅每届都
有回弹方面的考题。而且考题数以及论文发表数量 也逐年增加。NUMISHEET’99回弹考题为1个。回 弹论文比例为11%;NUMIsHEET’2002回弹考题为 2个,回弹论文比例为16%;而NUMlSHEET’2005
弹控制,将在线识别的冲头行程一冲压力曲线参数
作为人工神经网络的输入,以此来识别材料参数和 工艺参数,输出控制压边力以减小回弹。wu和
量:啪filli妒.1等人研究了回弹量的模具补偿方法。其基
本思想是基于有限元仿真,通过迭代算法对模具形 状进行不断修正,使得最后成形的零件在回弹后恰 好满足设计形状要求。如果冲压成形和回弹模拟精 度能够得到保证。这些回弹控制方法都能取得较满 意的结果。 国内外学者在数值模拟技术的材料模型、求解 算法、求解过程、单元技术等方面进行了大量的研 究,也取得了一定的进展叫.。.11.12一。 3.1材料模型方面的研究。
Paper-
拟,不仅接触摩擦最为严重,而且非线性问题最为突
出。单元的优劣及尺寸的影响、接触算法及摩擦模型 的科学性、本构方程及硬化规律的合理性、有限元算
板料成形回弹特征及其控制技术
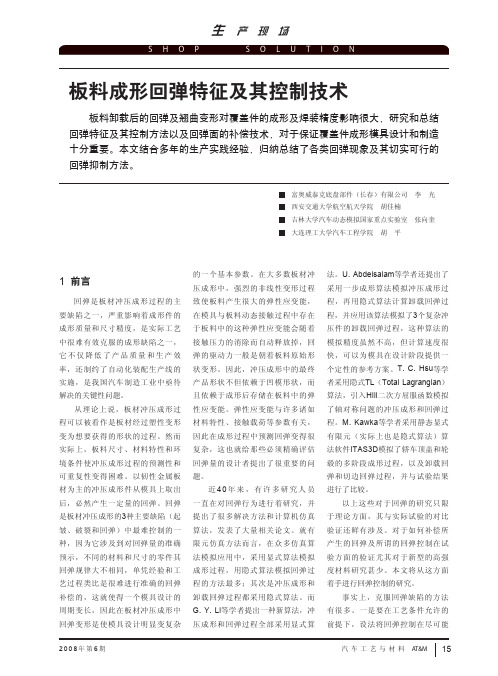
18 汽 车 工 艺 与 材 料 AT&M
2008年第6期
如图10,对板料的弯曲部位进
图6 变整体拉延成形为先部分弯曲成形后部分拉延成形的回弹抑制算法
图4 内侧圆角半径R硬化方法
这种方法对于二维形状简单的 行局部的淬火和回火处理,降低屈
度又要具有弹性的成形件产品不适 产品有效,对于三维形状的复杂产 服点,进而达到消除回弹之目的。
用。
品有时会产生不合格的效果,要注 2.10 冻结形状技术
如图4,从弯曲部位的内侧进行 压缩,以消除回弹。在板材U形弯 曲时,由于有两侧对称弯曲,采用 这种方法效果比较好。L形弯曲时, 一般面部分的材料压料力变弱,有 时会产生尺寸变差。从形状判断, 弯曲部位压力弱。对于既要保证强
弹抑制方法对于越厚的板材效果越 好。 2.5 变整体拉延成形为部分弯曲成 形的回弹控制方法
如图6,把整体拉延成形(设整 体拉延深度为90 mm)的A部(设为 60 mm)采用弯曲成形,消除板外侧 和内侧的应力差,剩余30 mm凹模的 B部,再通过拉延成形以减少回弹。
前提下,改变产品形状,增加加强 筋,可以控制和改善回弹。 2.8 负回弹方法
如图9,在加工工具表面时,设 法使板料产生负向回弹。上模返回 后,制件回弹,通过负回弹和回弹 而达到要求的产品形状。 2.9 淬火、回火抑制回弹方法
Crutonite合金
伊顿公司与一家特种金属材料研究公司共同开发的Crutonite气门材料具有全新的特性。其具有出色的耐高温、耐磨和高强 度的特性,特别适用于高性能柴油发动机和未来乘用车发动机更为复杂的燃烧环境。虽然这种新合金的性能表现和宇航超级耐 热合金相当,但镍类的特种金属使用量很少。
PACE:汽车供应商杰出贡献奖,由美国汽车工程师协会和美国汽车新闻共同评选。
板料多次弯曲成形回弹的数值模拟研究

板料多次弯曲成形回弹的数值模拟研究发布:2009-11-17 9:38:34 来源:模具网编辑:佚名摘要:对金属板料多次弯曲成形回弹的数值模拟方法进行研究,分析并解决了模拟过程中出现的板料与模具的干涉和各次弯曲间模拟结果的数据传递等问题。
通过金属板料的二次卷圆试验并与数值模拟结果比较.模拟结果与试验结果基本相符。
采用的有限元数值模拟方法可提高预测板料多次弯曲成形后回弹量的准确度。
关键词:金属板料;多次弯曲;回弹;数值模拟1引言金属板料弯曲成形后的回弹是加工中不可避免的现象,回弹的产生使得工件的弯曲精度降低,为后续的装配及其他工作带来困难。
目前对板料弯曲成形后的回弹模拟研究多集中在板料只进行一次弯曲成形后的回弹模拟,对多次弯曲成形回弹的数值模拟研究较少。
以下介绍对板料多次弯曲成形后的回弹进行模拟研究,分析模拟中出现的问题,并提出相应的解决措施。
2板料弯曲成形后回弹的数值模拟方法研究2.1弯曲回弹数值模拟方法通常情况下,完整的弯曲回弹数值模拟计算包括板料弯曲成形加载过程的模拟和弯曲成形后回弹过程的模拟,有限元方法也分为动力显式算法和静力隐式算法。
在弯曲回弹模拟过程中应结合冲压成形的特点来选择合适的有限元算法。
静力隐式算法虽然是一种无条件稳定的算法,但其计算过程需要构造和求解刚度矩阵,求解非线性方程组,而且每一步迭代都要进行接触判断nI对于板料弯曲成形这种包含接触和摩擦高度非线性的过程分析,往往会出现迭代不收敛的情况,或即使收敛,计算时间也很长。
所以对于板料弯曲成形过程的模拟一般采用动力显式算法,以避免因迭代计算和非线性引起的收敛问题。
其有限元计算公式为:对于弯曲回弹过程的模拟由于可以采用无模法。
即在弯曲回弹模拟开始之前,首先将模具与弯曲件分离,然后加载与弯曲成形结束状态接触条件相对应的反向力学边界条件:△f=-f(f为成形结束时相对应的节点接触力),并采用增量法计算,直至所有等效节点外力趋于零。
与加载过程相比,在板料弯曲回弹过程非线性成分明显减弱,同时在进行板料的弯曲回弹模拟时,静力隐式算法更接近弯曲件回弹的本质,回弹过程的模拟更适于采用静力隐式算法,其迭代公式如下:研究表明,与其他方法相比,将显式和隐式有限元算法结合起来计算回弹的方法,具有计算效率高,计算相对准确的特点,是求解弯曲回弹问题中使用最多的一种手段伫。
U型件冲压成形回弹过程的数值模拟及参数优化

第41卷第10期 2007年10月上海交通大学学报J OU RNAL OF SHAN GHA I J IAO TON G UNIV ERSIT YVol.41No.10 Oct.2007 收稿日期:2006211207作者简介:王 鹏(19802),男,河南新乡人,博士生,主要研究方向为金属塑性加工过程数值模拟及优化.董湘怀(联系人),男,教授,博士生导师,电话(Tel.):021*********;E 2mail :dongxh @. 文章编号:100622467(2007)1021590204U 型件冲压成形回弹过程的数值模拟及参数优化王 鹏, 董湘怀(上海交通大学国家模具CAD 工程研究中心,上海200030)摘 要:以有限元软件ABAQU S 为平台,分别运用有限元动力显式和静力隐式方法模拟U 型件成形及卸载后的弹性回复过程,分析了压边力、摩擦以及板料厚度对回弹量的影响.以控制回弹为优化目标,结合有限元数值模拟运用基于Pareto 策略的非支配排序遗传算法(NSGA 2II )对工艺参数进行了优化设计.关键词:板料成形;回弹;数值模拟;非支配排序遗传算法;参数优化中图分类号:T G 38 文献标识码:AThe Numerical Simulation of U 2channel Springbackand Optimization of Forming ParametersW A N G Peng , DO N G X i ang 2huai(National Die &Mold CAD Eng.Research Center ,Shanghai Jiaotong Univ.,Shanghai 200030,China )Abstract :U sing a commercial FE software ABAQU S ,t he forming process including springback of a U 2channel was simulated by static implicit and dynamic explicit FEM respectively.The influence of blank holder force ,f riction conditio n and sheet t hickness o n sp ringback was investigated.To minimize spring 2back ,t he p rocess parameters were optimized by Non 2dominated Sorting Genetic Algorit hm (NSGA 2II )on Pareto combining wit h FEM simulation.Key words :sheet metal forming ;springback ;numerical simulation ;non 2dominated sorting genetic algo 2rit hm (NSGA 2II );process parameters optimization 回弹是板料冲压成形中的主要缺陷之一,回弹的存在使零件尺寸精度降低,从而增加了试模、修模和校形工作量,导致生产周期的延长及生产成本的提高.这就迫切需要深入研究回弹问题,从而有效地控制回弹,发展精确成形技术.由于影响回弹的因素颇多,且影响规律复杂[1,2],很难确定优化的工艺参数以有效控制回弹.因此,致力于将数值模拟与优化方法相结合,在分析回弹影响因素的基础上进行回弹控制的优化设计具有十分重要的学术意义和实用价值.鉴于U 型件成形是板料成形的一种典型工艺,又因为回弹现象在该工艺过程中较为显著,本文以有限元软件ABAQU S 为平台,综合运用动力显式和静力隐式有限元方法对U 型件成形的加载和卸载回弹过程进行数值模拟,基于模拟结果分析压边力、摩擦和板料厚度对回弹量的影响.进而结合数值模拟运用基于Pareto 策略的非支配排序遗传算法(NSGA 2II ),以减小回弹为优化目标对工艺参数进行优化设计,得到了优化的工艺参数.1 有限元模型及数值模拟条件1.1 有限元方法对板料成形和卸载回弹过程分两步进行数值模拟.第1步板料成形过程的模拟计算是回弹过程模拟的基础,为回弹计算提供应力、应变等数据,该步计算的准确与否将直接影响回弹计算的精度.动力显式算法不需要构造和求解刚度矩阵,在求解成形过程复杂接触问题时计算效率高、稳定性好[3,4].时间t i时物体的运动方程为M¨x i=F ext i-F int i+F H i(1)式中:M为对角化质量矩阵;x为位移;F ext为外力;F int为内力;F H为沙漏力.为得到t i+1时的物体状态,运用中心差分法:x i+12= x i-12+¨x iΔti+1+Δt i2(2)x i+1=x i+Δt i+1 x i+12(3)由此可由板坯初始几何构形逐步求出新的几何构形.第2步对回弹过程进行模拟.虽然静力隐式算法在求解包含接触的强非线性问题时效率低、收敛性差,但是在处理不存在接触并且以低频率方式变形的结构动力学问题时(最典型的是回弹模拟计算),计算稳定性好,求解效率极高[5],往往经过1步或数步迭代即可完成计算.针对U型件成形的特点,零件与冲压成形模具脱离过程中,接触边界条件非线性的影响不大,采用无模法求解回弹.无模法即在成形结束时,去除模具代之以逐步减小的接触反力作用于节点,进行迭代计算,直到节点力为零.回弹位移增量的计算公式为:KΔU=ΔF(4)ΔF=F ext-F int(5)式中:K为刚度矩阵;ΔU为节点速度增量.1.2 有限元模型模拟过程中,板料采用4节点四边形单元进行离散化,模具、压边圈及工件的几何构型与参数如图1所示.将问题视为平面应变问题,为了提高有限元模型求解的效率,取对称轴右侧的一个条状区域进行有限元建模.工件的材料参数为:弹性模量E=206GPa,泊松比ν=0.3,密度ρ=7800kg/m3,屈服应力σ0= 167.0M Pa,硬化系数A=560M Pa,硬化指数n= 0.25.模具/工件之间的摩擦力由库仑摩擦模型确定,其表达式为F f=μp(6)式中:F f为摩擦力;p为接触正压力;μ为摩擦系数.图1 板料及模具(mm)Fig.1 The sheet metal and forming die(mm)1.3 回弹角定义U型件成形后有两个约90°的弯曲,以工件卸载后两个弯角超出90°的部分θ1和θ2作为回弹角以衡量回弹量的大小,回弹角愈大说明回弹量愈大,如图2所示.回弹角的计算公式为:θ1=90°-α(7)θ2=90°-α-β(8)式中:α为工件直壁部与水平方向的夹角;β为工件法兰部与水平方向的夹角.图2 回弹角定义Fig.2 Definition of the springback2 模拟结果分析2.1 压边力对回弹的影响取摩擦系数μ=0.15,板料厚度δ=0.8mm,改变压边力F进行模拟计算.由图3(a)可见,θ1始终大于θ2.在F较小时,随着F的提高,θ1显著增大, F>1kN时,随着F的增加,θ1有缓慢减小的趋势.θ2随F的增大而显著增大,增大的幅度逐渐减小,在F>2.5kN时,θ2有所减小.在板料中的弯曲应力相对较高时,由于卸载时弯曲应力的释放导致较大的回弹,但是随着压边力的增大,压边圈与板料之间的摩擦力增大,材料流入凹模愈加困难,材料的拉伸应力占据优势,回弹量将有所下降.2.2 摩擦对回弹的影响取F=1.5kN,δ=0.8mm,改变μ进行模拟计算.由图3(b)可见,θ1始终大于θ2.随μ的增大,θ11951 第10期王 鹏,等:U型件冲压成形回弹过程的数值模拟及参数优化 呈缓慢减小趋势,θ2呈缓慢增大趋势.摩擦对抑制回弹起有利的作用[6],但在凹模圆角处,较大的摩擦阻止材料流动,使得变形不能均匀地传递到板料的所有截面,从而出现应力集中,导致在卸载后的回弹量增大,当这些不利影响大于摩擦对回弹的有利影响时,就体现为随摩擦的增大回弹呈增大的趋势.2.3 板料厚度对回弹的影响取F =1.5kN ,μ=0.15,改变δ进行模拟计算.由图3(c )可见,在δ改变过程中,θ1仍始终大于θ2.随着δ的增加,θ1缓慢增加,并且有小幅的波动.θ2随δ的增加逐渐减小.δ增加会减小卸载后的回弹量[7],但是随着δ的增加,在模具的直壁部板料与模具的间隙减小,材料与模具间的摩擦力有所增大,这将抑制材料的流动,导致凸模圆角处的变形量增大,卸载后应力的释放导致回弹有增大的趋势,所以θ1随δ的变化而有所波动.图3 工艺参数对回弹角的影响Fig.3 The influence of process parameters on springback 由分析可知,各种参数的改变对回弹量的影响错综复杂,实际生产中很难精确控制工艺参数以有效减小回弹,开展以减小回弹量为目标的参数优化设计十分必要.3 优化设计3.1 优化模型以所定义的回弹角θ1和θ2最小为优化设计目标,因此优化问题属于多目标优化的范畴.建立优化目标函数为f (θ1)=min {θ1}f (θ2)=min {θ2}(9)选用对回弹量有复杂影响的F 、μ以及δ为优化设计变量.根据在工程实际中各工艺参数的调节范围,对各设计变量施加不等式约束如下:500N ≤F ≤3kN 0.1≤μ≤0.20.6mm ≤δ≤1mm (10) 特别指出,本文是以研究各参量对回弹的影响为出发点的,对板料厚度的预选取及优化设计完全从控制回弹的工艺性考虑,而没有考虑工件的承载能力等产品要求.由此,所构造的优化问题包括2个目标,3个变量,3个约束.3.2 优化方法对于多目标优化问题,常常以加权因子等方法转化为单目标优化问题进行处理,以避免复杂的多目标优化算法的应用.但却引入了新参数,不仅新参数的选择成了一个优化问题,而且只能求出与该参数有关的一个解,这与多目标优化问题的本质是相违背的.基于Pareto 策略的多目标遗传算法着眼于在多目标优化的基础上,得到均匀的Pareto 最优解集,依据不同的设计要求和意愿,从其中选择最满意的设计结果.Pareto 解是指多目标问题的1个“不坏”的解,也叫非劣解或可接受解,所有Pareto 解的集合形成Pareto 最优解集.Pareto 方法是在多目标优化的基础上,一次性获得优化问题对应的不同权重分配情况下的所有最优解集.NSGA 2II 是一种基于Pareto 最优概念的多目标遗传算法[8].首先,随机生成父代种群,根据每个非支配解的分级水平和排挤距离为其指定虚拟适应度值.进行复制、杂交、变异等遗传运算生成具有大量个体的子代种群,父代和子代混合利用精英策略构造出新的种群,并重复循环.3.2.1 适应度值计算 Pareto 遗传算法是根据点的适应度值来判断其位置的好坏.对种群按照个体的非劣性进行快速非胜出排序,这个过程持续到整个群体的次序排列完为止.除按不受支配排序外,还需计算目标空间上的每一点与同等级相邻两点之间的排挤距离.NSGA 2II 算法中,根据每个非支配解的分级水平和排挤距离为其指定虚拟适应度值.2951上 海 交 通 大 学 学 报第41卷 3.2.2 精英策略 将群体按适应度值逐一选取个体,将这些个体中适应度最高者保存到下一代群体中,直到个体总数等于种群数量.为了防止由于选择误差或交叉和变异的破坏作用而导致当前群体的最佳个体在下一代丢失,对适应度最高的个体不进行交叉和变异,而直接复制到下一代中.这样既保证了子代中的个体在解空间中较好的分散性,又使子代中的个体具有较大的适应度.3.2.3 约束条件处理 在非线性优化算法中,约束处理是一个很关键的问题.NSGA 2II 算法采用的是基于锦标赛选择的方法来处理约束.可行解根据目标函数值定的非胜出排序水平和排挤距离给定适应度值,具有较小约束违反量的解具有优先的排序,,可以方便地为个体指定适应值,不需要罚函数.运用NSGA 2II 算法选取的主要运行参数为:种群50,染色体长度6,交叉概率0.9,变异概率0.18,运行代数为8.3.3 优化结果讨论对于所建立的优化模型,以各设计变量的约束范围中点取值为优化计算前的初始迭代点,运用NSGA 2II 算法经过约6代的优化计算,即得到趋于稳定的优化目标值.优化计算过程中目标函数之间的优化关系如图4所示,可见随着优化计算过程中的参数改变,回弹角θ1和θ2有一致的减小趋势,所得的Pareto 最优解集相对集中.说明通过对参数的调整可以有效地减小回弹角θ1和θ2,从而精确控制回弹量.图4 回弹角θ1与θ2的优化关系Fig.4 The relationship of springback angle θ1and θ2 通过对优化前后工件成形终了时内部等效应力的分布比较可以看出(见图5),采用优化参数进行成形,工件的应力值较优化前总体有所减小,尤其在工件弯角处应力值均有减小,这对于减小卸载后的回弹是有利的. 优化前采用各参数的约束范围中点取值,即F =1.5kN ,μ=0.15,δ=0.8mm ,得到回弹角θ1=(a )工件单元选取及编号(b )选取单元应力值对比图5 优化前后成形终了时工件应力分布比较Fig.5 The stress distribution comparison at the end offorming before and after optimization11.89°,θ2=7.3°.优化计算得到基于Pareto 的最优解集,可根据工艺、产品、成本等不同要求和意愿从其中选取最优结果.该优化问题得到的Pareto 最优解集相对集中,即选择两个目标函数都最小的一个解为最优解.优化后采用参数分别为F =537.36N ,μ=0.11,δ=0.998mm ,得到回弹角θ1=5.49°,θ2=0.196°.优化后目标值较优化前分别减小53.8%和97.3%,总计减小70.4%,优化效果明显.4 结 语综合运用有限元显式和隐式方法分别对U 型件的加载成形和卸载回弹过程进行数值模拟,可有效地兼顾计算效率和精度.基于模拟结果通过构造回弹角衡量回弹的大小.回弹现象不可避免,U 型件的回弹量受压边力、摩擦及板料厚度等诸多因素的耦合作用,影响规律错综复杂,难于精确控制.基于Pareto 策略的多目标优化算法NSGA 2II ,适应性强,收敛性好,在结合有限元数值模拟解决板料回弹控制的优化计算问题时,收到了理想的效果.但是由于遗传算法本身具有优化步数较多的特点,另外在与有限元模拟相结合时需每步调用有限元计算,所以其求解效率受有限元模型复杂程度的影响较大.(下转第1597页)3951 第10期王 鹏,等:U 型件冲压成形回弹过程的数值模拟及参数优化 续挤压过程中随道次的增加而呈增加趋势.参考文献:[1] Lowe T C,Valiev R Z.Producing nanoscale micro2structures through severe plastic deformation[J].JOM,2000,52(4):27-28.[2] Valiev R Z,Islamgaliev R K,Alexandrov I V.Bulknanostructured materials f rom severe plastic deforma2tion[J].Progress in Materials Science,2000,45(2):103-189.[3] Ferrase S,Segal V M,Hartwig K T,et al.Micro2structure and properties of copper and aluminum alloy3003heavily worked by equal2channel angular extru2sion[J].Metallurgical and Materials T ransactions,1997,28A(4):1047-1057.[4] Mabuchi M,Iwasaki H,Yanase K,et al.Low tem2perature superplasticity in an AZ91magnesium alloyprocessed CA E[J].Scripta Materialia,1997,36(6):681-686.[5] DeLo D P,Semiatin S L.Hot working of Ti26Al24Vequal channel angular extrusion[J].Metallurgicaland Materials T ransactions,1999,30A(9):2473-2481.[6] Saito N,Mabuchi M,Nakanishi M,et al.Applica2tion equal channel angular extrusion on strengtheningof ferritic stainless steel[J].Journal of Material Sci2ence,2001,36(13):3229-3232.[7] Segal V M.Materials processing by simple shear[J].Materials Science and E ngineering,1995,A197:157-164.[8] Kamachi M,Furukawa M,Horita Z,et al.A modelinvestigation of the shearing characteristics in equalchannel angular pressing[J].Materials Science andE ngineering,2002,A347(122):223-230.[9] Nemoto M,Horita Z,Furukawa M,et ngdon,equal2channel angular pressing:A novel tool for mi2crostructural control[J].Metals and Materials I nter2national,1998,4:1181-1190.[10] Kim H S,Seo M H,Hong S I.Finite element analy2sis of equal channel angular pressing of strain ratesensitive metals[J].Journal of Materials ProcessingT echnology,2002,130:497-503.[11] Suh J Y,K im H S,Park J W,et al.Finite elementanalysis of material flow in equal channel angularpressing[J].Scripta Materialia,2001,44:677-681.[12] Wilsdorf D K.Dislocation cells,redundant disloca2tions and the leds hypothesis[J].Scripta Materialia,1996,34:641-650.[13] G oerdeler M,Crumbach M,G ottster G,et al.Dis2location density based modeling of work hardening inthe context of integrative modeling of aluminum pro2cessing[J].Materials Science and E ngineering,2004,A387-389:266-271. (上接第1593页)参考文献:[1] 梁炳文,胡世光.板料成形塑性理论[M].北京:机械工业出版社,1987:343-348.[2] Fei Dong2ye,Hodgson P.Experimental and numericalstudies of springback in air v2bending process for coldrolled TRIP steels[J].Nuclear E ngineering and Design,2006,18(9):1847-1851.[3] Chou Inan,Huang Ching2hua.Finite element analysisand optimization of springback reduction[J].Interna2 tional Journal of Machine T ools&Manu facture,1999,39(3):517-536.[4] 夏 欣,卫原平,李发致,等.板料冲压成形工艺参数的计算机优化[J].上海交通大学学报,1999,33(2):178-180.XIA Xin,WEI Yuan2ping,L I Fa2zhi,et al.Optimiza2 tion for the process parameters of sheet metal forming[J].Journal of Shanghai Jiaotong U niversity,1999,33(2):178-180.[5] Banu M,Takamura M,Hama T,et al.Simulation ofspringback and wrinkling in stamping of a dual phase steel rail2shaped part[J].Journal of Materials Process2 ing T echnology,2006,10(4):178-184.[6] Naceur H,Guo Y Q,Ben2Elechi S.Response surfacemethodology for design of sheet forming parameters to control springback effects[J].Computers&Struc2 tures,2006,6:1-13.[7] Firat puter aided analysis and design of sheetmetal forming processes[J].Materials&Design,2006,23(3):1-11.[8] Kalyanmoy Deb,Amrit Pratap,Sameer Agarwal,etal.A fast and elitist multi2objective genetic algorithm:NSGA2II[J].IEEE T ransactions on Evolutionary Com2 putaion,2002,6(2):182-197.7951 第10期胡丽娟,等:基于位错演化理论的等径角挤压纳米微晶材料数值分析 。
解决成型回弹的措施

解决成型回弹的措施主要有以下几种:
1. 拉弯:这种方法是在板料弯曲的同时施加切向拉力,改变板料内部的应力状态和分布情况,让整个断面处于塑性拉伸变形范围内,卸载后内外层的回弹趋势相互抵消,减小了回弹。
2. 局部压缩:通过减薄外侧板料的厚度来增加外侧板料的长度,使内外层的回弹趋势相互抵消。
3. 多次弯曲:将弯曲成形分成多次来进行,以消除回弹。
4. 内侧圆角钝化:从弯曲部位的内侧进行压缩,以消除回弹。
5. 变整体拉延成为部分弯曲成形:将零件一部分采用弯曲成形后再通过拉延成形以减少回弹。
6. 控制残余应力:拉延时在工具的表面增加局部的凸包形状,在后道工序时再消除增加的形状,使材料内的残余应力平衡发生变化,以消除回弹。
7. 负回弹:在加工工具表面时,设法使板料产生负向回弹。
上模返回后,制件通过回弹而达到要求的形状。
8. 电磁法:利用电磁脉冲冲击材料表面,可以纠正由于回弹造成的形状和尺寸误差。
9. 控制模具和工艺参数:优化模具设计和工艺参数,如弯曲角、模具工作部分尺寸等,以降低回弹。
10. 材料选择:选择具有较低弹性模量和应变时效的材
料,或通过材料改性来降低回弹。
在解决成型回弹时,应根据实际情况选择合适的措施。
3D复杂形状板料冲压成形回弹误差补偿方法及其实验验证

( ) #
图 #! 板料冲压成形环节 . C : #!, A 8 9 I C < C < ‘8 \ M ^ D D Z > A D Z B 9 M Z B A C < E E9 O E
本文以回弹 误 差 为 控 制 目 标 ! 以 线 性 闭 环 控 制
!! 引 ! 言
板料冲压是 汽 车 覆 盖 件 的 主 要 成 形 方 式 " 板 料 冲压成形过程中 普 遍 存 在 回 弹 问 题 ! 特 别 是 在 弯 曲 和浅拉深过程中 回 弹 现 象 更 为 严 重 ! 对 零 件 的 尺 寸 精度和生产效率 造 成 极 大 的 影 响 ! 有 必 要 对 其 进 行 深入的研究和有效的控制 " 模具修正是板料成形回弹控制的有效方法之一 " 以往工程上模具修 正 基 本 上 是 通 过 反 复 试 验 来 完 成 的 ! 时间长 ! 费用高 " 目前数值模拟技术发展迅速 ! 一些学者在模具回 弹 补 偿 的 数 值 模 拟 方 面 作 了 大 量
!"K, 的工作 + " 数 值 模 拟 迭 代 法 效 率 高# 费 用 低! 但
系统 # 空间 . 8 ; S C D S变 换 和 频 域 传 递 函 数 为 理 论 基 础 ! 基于模具实 验 迭 代 ! 建 立 模 具 回 弹 补 偿 修 正 算 法 " 实验证明 ! 该 方 法 可 以 较 好 地 控 制 板 料 冲 压 成 形回弹误差 "
式中 !! % % % 模具 T冲压 C D S 变 换! 即 " ( . . 1 变换
板材多点成形中回弹的数值模拟及补偿研究

1 3 回弹量 的计 算 . 为直观地反映 回弹 ,按下式计算 回弹量 :
k。一k b
= _
式 中 :k 为板 材 回弹前 的平 均 曲率 ,k 为板 材 回弹 b , 后 的平均 曲率 。
曲面 z ,) ( y x方向的曲率通过下式计算 :
k 1 一【 = +(zO ) 】 a/x () 2 ‘
用 。
板 材成形 时 ,回弹是 不可 避 免 的现 象 。在外 载 荷作 用下 板材 的变形 由塑性 变形 和 弹性 变形 两部 分
5in l。为抑制 压痕 的产 生 ,在板 料上 下两侧 分别 放 n 置 了弹性垫 ,弹性垫材料为聚氨酯 ,简化为线性弹性 模 型 ,弹性模量 取 为 10 7 M a 0 . P ,泊松 比为 04 . ,密 度为 110 k/ 5 g m 。板 材 和 基 本 体 单 元 模 型 均 采 用 S E L6 H L 13壳单元 ,其 中板材 分 为 406个单 元 ,上 9 基本体分为 1 7 82 2个单 元 ,下基本 体分 为 1 4 93 8个 单元 。 图 1 示是板厚 为 1ml 所 i,目标 曲率半 径 为 R= l 2 0ml的圆柱 面的数值 模拟 有限元模 型 。图 2所 示 0 i l
数值模拟 ,分析得 出回弹趋势 和回弹分布 ,提出通过修正基本体群成形面来补偿 回弹的方法 ,并用 B样条 曲线拟合生成 的 曲面 。经过两次补偿 ,成形件精度提高 ,证 明该方 法可以很 好地补偿多点成形 中的 回弹。研 究结果对于减小 因 回弹带来 的 误差 ,提高成形件 的成形精度具有 十分重要的意义 。 关键词 : 多点成形 ; SD N L -Y A软件 ;回弹 ; 一 显 隐式算法
f :— — _
冲压仿真中的回弹分析及在冲压梁中的应用

冲压仿真中的回弹分析及在冲压梁中的应用【摘要】回弹是板料冲压生产中产生的主要问题之一。
由于板料弹性变形的存在导致卸载后零件发生回弹,回弹的结果造成冲压件的尺寸和模具表面尺寸不符,从而影响了制造的精度,精确的计算一般冲压件的回弹量是非常困难的事,多数情况下,只能靠以往的经验,在模具设计时对将来可能产生的回弹加以补偿,但是这样的补偿往往是不准确的。
为提高冲压件的产品质量,缩短新产品开发周期,必须对回弹进行准确的预测和有效的控制。
【关键词】冲压成型;回弹;有限元模拟;模拟软件实际应用1.本项目的研究目标及意义今天,随着我国汽车工业的飞速发展,我国的模具工业也随之迅猛发展起来,笔者作为一名模具设计人员,亲身经历了模具设计手段由图板、铅笔到计算机CAD制图;由产品图到产品数模的转变。
随着冲压成形有限元仿真研究的蓬勃发展,以有限元为核心的塑性成形数值仿真技术日趋成熟,为人们认识塑性成形过程的本质规律提供了新途径,为实现塑性成形领域的虚拟制造提供了强有力的技术支持,这使得有限元仿真分析在汽车工业的应用日益受到重视。
通过成形仿真分析可以在多方面对模具企业提供强有力的支持:在设计工作的早期阶段评价模具设计、工艺补充的可行性;在试冲试模阶段进行故障分析,解决问题;在批量生产阶段用于缺陷分析,改善零件生产质量,同时可用来调整材料等级,降低成本。
有限元数值仿真技术在模具开发设计广泛应用,对传统的模具开发过程的变革产生了深远的影响。
2.板料成型及回弹模拟的基本理论2.1板材成形缺陷分析板料成形是一个具有几何非线性、材料非线性、边界条件非线性等多重非线性的非常头的力学过程。
由于影响成形过程的因素很多,因此人们不能精确控制材料的流动。
成生程中会产生各种各样的缺陷,影响零件的几何精度、表面质量和力学性能。
总的来说,零件成形的主要缺陷有起皱、破裂和回弹。
起皱是压缩失稳在薄板成形中的主要表现形式。
薄板冲压成形时,为使金属产生塑性,模具对板料施加外力,在板内产生复杂的应力状态。
板料成形回弹的数值模拟与影响因素

O.3 1.4 200 590
B 4 5 3 5
2
5
l
刖,敞,珐,n;州5
0
/ /◆
/- / / /
1
2
3
图4弦长AB和材料的关系
材料
i}l
∞拍拼:{B勰拍“毖他 0
。\ \ \ \ \ \
l
2
3 材料
图5弓高CD和材料的关系
4.2板料厚度对回弹的影响 图6、7分别是板料厚度对回弹的影响的仿真结
果,图中横坐标上1、2、3分别表示板厚h为 0.78ram、1.0mm、1.2ram。由图可见,厚度越大,回弹量
本文以典型的弧形弯曲件为研究对象分析了回弹产生的力学机理qar并运用有限元分析软件9s0t0v0wts9首先通过显式算法模拟动态成形过程然后利用隐式静态算法模拟回弹变形对不同材料板厚摩擦系数等因素对回弹的影响进行了分析和比较回弹产生的力学机理板料冲压成形中包含有弯曲现象时就不可避免地产生回弹
文章编号:1672—0121(2005)03—0055—04
程。加载过程的应力、应变等数值模拟结果是回弹计 算的基础,这个过程计算的准确与否将直接影响回 弹过程模拟的计算精度。
目前,板料成形过程的模拟一般采用动态显式 算法。这是因为板材成形一般属于动态接触问题,是 一个相当复杂的过程,既有弹性变形,又有塑性变 形,还要分析预测成形过程中可能产生的缺陷。显式 算法因不涉及迭代计算和收敛性问题,无需构造刚 度矩阵就可以完成求解。动态显式算法效率高、稳定 性好,适于计算各种复杂成形问题,但用于回弹计算 时效率极低,所耗费CPU时间往往数倍于成形计 算。为此,回弹模拟的方法运用无模法,即一般的无 接触算法。该方法将回弹看作弹性变形过程,采用增 量法求解。在计算开始之前,先将模具与板料分离, 代之已与成形终了状态接触条件相对应的反向力学 边界条件,计算至所有等效节点外力趋于零时,即得 回弹的结果。静态隐式算法在求解大型成形问题时 效率低、收敛性差,但求解回弹问题时其效率极高, 往往经过一步或数步迭代即可获得很好的结果。
基于数值模拟的板材渐进成形回弹技术应用研究

基于数值模拟的板材渐进成形回弹技术应用研究一、板材渐进成形回弹技术概述板材渐进成形是一种通过搅拌滚柱不断加深对金属板材进行加工的方法,通过逐步进行成形,可以得到精度更高的金属构件。
然而在成形过程中,板材会受到应力的作用而发生一定的变形,其主要原因为材料的弹性变形,也称为回弹变形。
回弹变形会对成品的尺寸和形状产生影响,直接影响构件的精度和质量。
针对板材渐进成形回弹技术问题,传统的解决方法是通过试验来不断调整成形工艺参数,以减小回弹变形。
然而这种方法存在成本高、时间长、效果不稳定等问题。
相比之下,基于数值模拟的方法则能够快速、准确地进行模拟分析,并提供合理的成形参数,使得成形工艺得以优化。
1. 数值模拟方法数值模拟是利用计算机对工程问题进行虚拟实验和仿真的方法。
在板材渐进成形回弹技术研究中,可以采用有限元方法对板材进行数值模拟。
有限元方法将物体分割成有限数目的基本单元(如三角形、四边形等),通过求解基本单元的位移、应力等参数,再将其组合在一起,最终得到整体板材的变形情况。
2. 模拟参数的确定在进行数值模拟时,需要确定一系列成形工艺参数,如滚柱的深度、板材的性能参数等。
这些参数直接影响到模拟结果的准确性和可靠性。
需要通过试验数据和理论分析相结合的方式,来确定合理的成形工艺参数。
3. 模拟结果的分析数值模拟的最终目的是得到回弹变形的分布规律和变形量,从而找到减小回弹变形的有效方法。
模拟结果分析需要考虑不同参数对回弹变形的影响程度,找到影响较大的因素,并提出相应的优化措施。
1. 减少试验时间和成本传统的试验方法需要进行多次成形试验,并对不同参数进行调整,以找到合适的成形工艺参数。
这些试验需要花费大量的时间和成本。
而数值模拟方法可以通过计算机模拟,快速得到各种参数下的成形变形情况,减少了试验的时间和成本。
2. 提高成形精度数值模拟可以快速准确地得到板材的回弹变形情况,通过分析模拟结果,可以优化成形工艺参数,提高成形精度和产品质量。
板料回弹机理及控制

板料回弹机理及控制摘要:回弹是板料冲压成形中普遍存在的现象,回弹的存在直接影响到冲压件的形状尺寸精度,产生后续的质量、装配问题。
因此,回弹问题不但是工业生产中需解决的一个实际问题,也是学术界长期关注的热点。
关键词:板料回弹;机理;控制回弹是板料加工中最常见的废次品形式之一,也是弯曲工艺中的技术难点之一。
同时,它也是板料冲压成形过程中的主要缺陷之一,严重影响了质件的尺寸精度和外观的质量,是实际工艺中很难掌握的一个缺陷。
一、板料回弹现象回弹是卸载过程产生的反向弹性变形,是板料冲压成形过程中存在的一种普遍现象。
在弯曲和托深过程中,回弹现象尤为严重,对零件的尺寸精度、生产效率和经济效益产生极大的影响。
二、板料回弹机理板料在外加弯曲力矩的作用下,首先发生弹性弯曲变形,在弹性弯曲阶段,对弯曲半径很大,板料内弯曲半径与凸模圆角半径不相重合,板料变形很小。
在弯曲变形区内,板料弯曲内侧(靠近凸模一边)的材料受到压缩而缩短,应力状态是单向受压。
板料弯曲外侧(靠近凹模的一边)受拉而伸长,应力状态是单向受拉。
弯曲内、外表面到中心,其缩短与伸长的程度逐渐变小,在缩短与伸长的两个变形区之间,有一纤维层长度始终不变即应变为零,称为应变中性层。
同样,在拉应力向压应力过渡之间,存在一个切向应力为零的应力层,称为应力中性层。
在一般情况下可认为两个不同性质的中性层重合在一起,简称为中性层。
随着弯矩的增加,板料弯曲变形增大,板料内外表层金属先达到屈服极限,板料开始由弹性变形阶段转入弹塑性变形阶段,其应力分布随着弯矩的不断增加,塑性变形区由表层向内扩展,板料中间的弹性变形区逐渐变小,最后整个断面进入塑性状态。
图1中第二副图显示了反向加了弯矩所产生的应力变化图。
第三副图显示的是残余应力图,即是能产生回弹的应力。
弯曲回弹的主要原因由于材料弹性变形引起。
板料弯曲时,内层受压应力,外层受拉应力。
弹塑性弯曲时,这两种应力尽管超过屈服应力。
但实际上从拉应力过渡到压应力时,中间总会有一段应力小于屈服应力的弹性变形区,由于弹性区的存在,弯曲卸载后工件必然产生回弹。
板材成形回弹过程数值模拟方法研究①
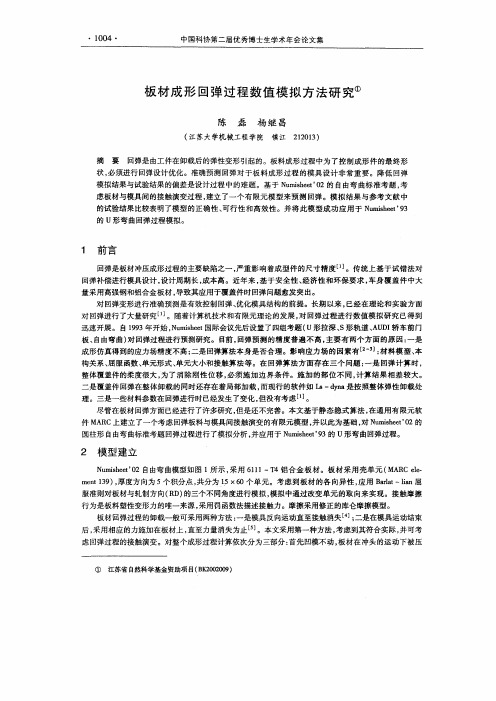
对回 弹进行了 大量研究〔 ’ 〕 。随着计算机技术和有限 元理论的发展, 对回弹过程进行数值模拟研究已得到
迅速开展。自1 9 9 3 年开始, N u m i s h e e t 国际会议先后设置了四组考题( U形拉深、 S 形轨道、 A U D I 轿车前门 板、 自由弯曲) 对回弹过程进行预测研究。目 前, 回弹预测的精度普遍不高, 主要有两个方面的原因: 一是
1 前言
回 弹 是 板材冲 压 成形过程的 主 要缺陷 之 一, 严重影响 着 成型件的尺寸精度川。 传统上基于 试错法对
回弹补偿进行模具设计, 设计周期长, 成本高。近年来, 基于安全性、 经济性和环保要求, 车身覆盖件中大 量采用高强钢和铝合金板材, 导致其应用于覆盖件时回弹问题愈发突出。 对回弹变形进行准确预测是有效控制回弹、 优化模具结构的前提。 长期以来, 已经在理论和实验方面
板材回 弹 过程的 卸载一 般可采用 两种 方法: 一 是模 具反向 运动直至 接触消失[ ]; ’ 二是 在 模具运动 结束 后, 采用相应的 力 施加 在板材上, 直至力 量消失 为 止[ [ 5 1 。 本 文采 用第一种方 法, 考虑到 其符 合实际, 并可考
虑回弹过程的接触演变。对整个成形过程计算依次分为三部分: 首先凹模不动, 板材在冲头的运动下被压
[ 2 ] N a r k e e r a n N a r a s i m h a n , M i c h a e l L o v e l l , P r e d i c t i n g s p r i n g b a c k i n s h e e t m e t a l f o r m i n g ; a n e x p l i c i t t o i m p l i c i t s e q u e n t i a l s o l u - t i o n p r o c e d u e, r F i n i t e E l e m e n t s i n A n a l y s i s a n d D e s i g n , 3 3 ( 1 9 9 9 ) ; 2 9 一 4 2
- 1、下载文档前请自行甄别文档内容的完整性,平台不提供额外的编辑、内容补充、找答案等附加服务。
- 2、"仅部分预览"的文档,不可在线预览部分如存在完整性等问题,可反馈申请退款(可完整预览的文档不适用该条件!)。
- 3、如文档侵犯您的权益,请联系客服反馈,我们会尽快为您处理(人工客服工作时间:9:00-18:30)。
机 电技 术 弹 计算 值与单 元尺 寸成 反 比关系 , 元尺 寸越 小 , 单 计 算 回弹量 越大 ;反 之 , 回弹量越 小 ,甚至 出现 反 向回弹 ,结果 表 明 ,坯 料 单元尺 寸 为模 具 圆角 半径的 1 / , 回弹结果 与实验 结 果最接 近 。 回 2时 弹 算法 本 身 的影 响因素 主要 有 :一 是设置 边 界条 件 以防止 刚体 运动 时 ,施加 部位 不 同 ,计 算 结果 会有 很大 的差 异 ;二是 回 弹过程 不 能简单 地 理解 为弹 性卸 载过 程 ,可 能伴有 局部 加 载过程 ,而在 模拟 过程 中没有 考虑 。 1 回弹 的计算方 法 . 2 回弹 模拟 的精 度 不仅 与成 形过 程 的模 拟 精度 有关 ,而且还 与 回弹 计算 方法 、 回弹模 型 的选 择 等密 切相 关 。回弹模 型有 两种 ,有 模法 和无模 法 。
因造 成 的L:一 是板 料成 形 过程 有 限元 模 型模 拟 5 J 精 度 不够 准确 ;二 是 回弹模 型 的选取 与 回弹算 法
况,计算速度慢,但计算精度高;而动力显示算 法 不需要 构造 和求 解 刚度矩 阵 ,不用 进 行迭代 收
敛判 断 ,计算 速度 快 ,但计 算精 度要 差 一些 。为
[-3 1 ]
,
回弹 由此 越 来越 受 到 学术 界 的关 注 ,有 限
元数值模拟技术的引入,为推动回弹问题的解决 提 供 了有 利 的工具 。
计 算 回弹 的真正 目的在 于 以计 算 出的 回弹量 为依 据来 修 正模具 ,从 而缩 短模 具 设计 时 间、提 高 效率 、降低 成本 。如何准 确 的预测 回弹 、提 高 回弹 的模 拟精 度成 了板 料成 形有 限元 数值 模拟 的
关键词 :板料成形;回弹:数值模拟
中图分类号:T 3 6 文献标识码: 文章编号 :17 .8 12 1)60 1 3 G8 A 6 24 0 (0 10 .9 . 0
板 料冲 压成 形是 一个 集几 何非 线性 、材 料非 线 性 和 边 界 条 件 非 线 性 为 一 体 的高 度 非 线 性 问
模具单元坯料单元尺寸的确定与模具圆角半径 的 大小有密切 的关系,有资料表明,当流过模具 圆 角处的单元尺寸为模具圆角半径 的 1 ~1 / / 2 3时, 应 力 、应变 场模 拟 结果 最优 。大 量文 献表 明 , 回
作 者简 介 :解婧 陶(94 ) 18 - ,助教 ,硕 士研 究生 ,研 究方 向:塑 性成形 及模 具 C D C E A /A 。
第6 期
机 电技术
9 1
一
板料成形数值模拟中பைடு நூலகம்弹问题 的处理
解婧 陶
f 福建船政交通职业学院,福建 福州 3 0 0 ) 5 0 7
摘
要 :在分析 了板料成形回弹特性 的基础上 ,列 出了回弹 的影响因素 ,提 出了回弹计算方法,最后运用 自主开 发
的三维板料成形数值模拟 软件 S E 3 HE T D对盒 形件 回弹进行 了数值模拟 。
计算 精度 。
数值模拟算法有两种:静力隐式算法和动力
显示 算法 。两种算 法 的 区别 在 于静 力隐 式算法 需 要构 造和 求解 刚度 矩 阵 ,并 且每 一迭 代加 载步 都 要进 行接 触判 断在 计 算过程 中会 出现 不 收敛 的情
目前,回弹模拟精度普遍不高,不同的软件
之 间的模拟 结 果也 差别 很大 ,主 要 是两方 面 的原
题 ,变 形过 程 中常涉及 到大 位 移和 大转 动 。这 些
拟实 例 。
1 板料 卸载回弹的数值模拟研究
11 板 料卸 载 回弹 的原 理及 影响 因素 . 板 料在 外 力 的作 用 下发 生塑 性变 形时 ,其 变 形都 是 由弹性 变形 和塑 性变 形两 部 分组成 ,从而 造 成 回弹 由弹 性 回弹与 塑性 回弹 两部 分组 成 。弹 性变 形 区材料 的弹 性恢 复 引起 了弹 性 回弹 ,其关
精度不高。前者的影响因素有:材料模型、本构 关系 、动态 接 触算 法 、单元 形式 和 单元尺 寸大 小
等 。其 中单元 尺寸对 回弹 的影 响非 常的 明显 ,对
了保证回弹的计算精度 ,大多数学者建议采用静 力隐式算法。本文首先给出了回弹计算前的一些 准备条件 ,在 比较 了回弹算法的基础上采用静力 隐式算法结合 自主开发 的板料有限元数值模拟软 件 S E T D, H E 3 建立了回弹计算模型, 并给出了模
热 点和难 点 。 NU S E ’3开始 , 从 MIHE T 9 每届会 议
键是凸模与凹模之间的间隙大于板料厚度所致 , 材料 的屈 服应 力 、模具 间 隙及板 料 厚度 是影 响弹
性 回弹 的主要 因素 ;塑 性变 形 区材料 的弹 性恢 复 引起 了塑 性 回弹 ,其关 键 是卸载 过程 中残 余应 力 的释 放 引起 的,残余 应 力及 材料 厚度 是 引起塑 性
复 杂性 引起 了板 料成 形 的诸如 起皱 、破 裂和 回弹 等 质量 缺 陷 ,其 中回弹 是 最难 以控 制 的  ̄】 2。零 件 最终 形状 取决 于成 形后 的 回弹量 ,随 着汽 车 、
航天、航空事业的发展,特别是近年来高强度钢
板 和铝 合金 板 的大量 使用 , 回弹 问题越 来越 突 出
回弹 的主要 因素 。
完整 的板 料 回弹 数值 模拟 可 以分 为两 步 :板 料 加 载成 形过 程模 拟和 卸载 回弹 过程 模拟 。这 两 个 过程 既相互 独立 又相 互 关联 ,前者 为后 者提 供 成 形 最后 一步 的应 力 、应变 等数 据 ,成形 模拟 的
都有 关于 回弹预测 的标 准考 题 ,有关 回弹预测 和
回 弹 误 差 控 制 的 会 议 专 题 论 文 逐 届 增 加 , 到
NUMIHE T2 0 ,有 关 回弹 预测和 控 制 的会 议 S E ’02 专题 论文 更是 占到 了全部 会议 论文 的 2%, 由此 1 可 见对 回弹 的关注程 度L。 4 J
整个过程中的任何误差都会积累到回弹阶段,所 以成 形过程 计 算 的准确 与 否将直 接影 响到 回弹 的