减速器全部计算
减速器计算过程

r 2 =0.5* ������*0.32 *7.85*103 *0.01*0.32 =0.0623925kg*m2 链轮的宽度选为 10mm。 塑料轮的宽度选为 20mm,直径 D=300mm。 则 塑 料 轮 的 转 动 惯 量 为 J塑料 = ∗ ������������ 2 ∗ p ∗ l ∗ r 2 =0.5* ������ ∗
考虑滚筒同减速器相连接,其长度增长至 1200mm,则有 J=0.5* ������ * 0.032 *7.85* 103 *1.2* 0.032 = 链 轮 的 转 动 惯 量
0.19167 16
=0.01197937 kg* m2 =
1 2
J链轮
ห้องสมุดไป่ตู้
∗ ������������ 2 ∗ p ∗ l ∗
3 ������∗0,3 20 ������∗0,3
V
������∗������
=3.184rad/s =21.23rad/s
最大角速度w2 =
电动机的加速时间为 1s,则有角加速度: 最小角加速度为 β1 =3.184/1=3.184rad/s 2 最大角加速度为 β2 =21.23/1=21.23rad/s 2 则电动机的输出扭矩 T=J*β 最低速度时扭矩T1 =2*0.184786*3.184=1.176N*M 最高转速时扭矩T2 =2*0.184786*21.23=7.85 N*M 电动机的功率 P=T*W 则最低转速时:P=T1 ∗ w1 =1.176*3.184=3.746w 最高转速时:P=T2 *w2 =7.85*21.23=166.6w 考虑网带的质量和输送带上货物的质量,根据相关国家标准,滚筒 和输送带之间的摩擦力大小估计为 200N, 则有工作机所需的转矩为 Tw =F* =200*0.3*0.5=15N*M
减速器计算

mm minmm cos15八、键的选择本次设计的减速箱中共有3根十一、箱体及减速器附件说明:箱壳是安装轴系组件和所有附件的基座,它需具有足够的强度、刚度和良好的工艺性。
箱壳采用HT200灰铸铁铸造而成,易得道美观的外表,还易于切削。
为了保证箱壳有足够的刚度,常在轴承凸台上下做出刚性加固筋。
轴承采用润滑脂润滑,在轴承与轴肩连接处,采用挡油环结构。
防止箱体内全损耗系统用油将油脂洗去。
箱体底部应铸出凹入部分,以减少加工面并使支撑凸缘与地量好接触。
减速器附件:1)视孔和视孔盖箱盖上一般开有视孔,用来检查啮合,润滑和齿轮损坏情况,并用来加注润滑油。
为了防止污物落入和油滴飞出,视孔须用视孔盖、垫片和螺钉封死。
2)油面指示器油面指示器上有高油面和低油面指示孔,油面一般不能低于最低油面孔,不能高于最高油面孔。
一般油面高度为30~50mm,要浸到1~2齿,一般不超过齿轮半径的1/3。
3)油塞在箱体最底部开有放油孔,以排除油污和清洗减速器。
放油孔平时用油塞和封油圈封死。
油塞用细牙螺纹,材料为Q235钢。
封油圈采用石棉橡胶制成。
4)吊钩、吊耳为了便于搬运减速器,常在箱体上铸出吊钩和吊耳。
起调整个减速器时,一般应使用箱体上的吊钩。
对重量不大的中小型减速器,如箱盖上的吊钩、吊耳的尺寸根据减速器总重决定,才允许用来起调整个减速器,否则只用来起吊箱盖。
5)定位销为了加工时精确地镗制减速器的轴承座孔,安装时保证箱盖与箱体的相互位置,再分箱面凸缘两端装置两个直径为A7的圆锥销,以便定位。
长度应大于凸缘的总厚度,使销钉两端略伸凸缘以利装拆。
滚动轴承的外部密封装置:为了防止外界灰尘、水分等进入轴承,为了防止轴承润滑油的泄漏,在透盖上需加密封装置。
在此,我用的是毡圈式密封。
因为毡圈式密封适用于轴承润滑脂润滑,摩擦面速度不超过4~5m/s的场合。
十二、小结:心得小结附:弯矩图、扭矩图(轴1)具体参数见表格中“轴的设计”部分。
参考资料1吴克坚等主编.机械设计.北京:高等教育出版社,20032王之栎等主编.机械设计综合课程设计.北京:机械工业出版社,20033龚桂义主编.机械设计课程设计指导书.北京:高等教育出版社,19904龚桂义主编.机械设计课程设计图册.北京:高等教育出版社,19895范钦珊,蔡新.工程力学.北京:高等教育出版社,20066 宜沈平,赵傲生.计算机工程制图与机械设计.南京东南大学出版社,2004.。
计算谐波减速器的公式

计算谐波减速器的公式
谐波减速器的公式包括以下几个方面:
1. 输出转速与输入转速的关系:
输出转速 N2 = (N1 - N0) / (x + 1),其中 N1 为输入转速,N2 为输出转速,N0 为不工作时的输出转速,x 为谐波减速器的传动比。
2. 转矩放大比:
转矩放大比 K = (N1 - N0) / N2,表示谐波减速器的转矩放大效果。
K 越大,转矩放大效果越好。
3. 传动比 x 的计算:
传动比x = (0.5πD2) / (πd1),其中 D2 为输出轴的直径,d1 为驱动轴的直径。
这个公式适用于单波轴式谐波减速器。
需要注意的是,具体的谐波减速器的公式可能会根据不同的厂家和型号有所区别,上述公式仅为一般情况下的计算方法。
在实际应用中,最好参考所使用谐波减速器的说明书或咨询制造商以获取准确的计算公式。
减速器的输出精度计算公式

减速器的输出精度计算公式减速器是一种常见的机械传动装置,用于降低输入轴的转速并增加输出轴的扭矩。
在工业生产中,减速器的输出精度对于机械设备的性能和稳定性至关重要。
因此,了解减速器的输出精度计算公式对于工程师和技术人员来说是非常重要的。
减速器的输出精度通常通过齿轮传动的误差来衡量。
齿轮传动的误差包括齿轮的齿数误差、啮合间隙误差、齿轮的圆周间隙误差等。
这些误差会影响减速器的输出精度,因此需要进行精确的计算和评估。
在实际工程中,减速器的输出精度可以通过以下公式进行计算:输出精度 = 输入精度× (1 + ε1 + ε2 + ε3)。
其中,输入精度是指减速器输入轴的精度;ε1、ε2、ε3分别代表齿轮的齿数误差、啮合间隙误差和圆周间隙误差。
齿数误差是指齿轮的实际齿数与理论齿数之间的差异。
它可以通过以下公式进行计算:ε1 = (Nt Nt') / Nt'。
其中,Nt是齿轮的理论齿数,Nt'是齿轮的实际齿数。
齿数误差越小,减速器的输出精度就越高。
啮合间隙误差是指齿轮啮合时的间隙误差。
它可以通过以下公式进行计算:ε2 = (C C') / C。
其中,C是齿轮的理论啮合间隙,C'是齿轮的实际啮合间隙。
啮合间隙误差越小,减速器的输出精度就越高。
圆周间隙误差是指齿轮的圆周间隙与理论值之间的差异。
它可以通过以下公式进行计算:ε3 = (P P') / P。
其中,P是齿轮的理论圆周间隙,P'是齿轮的实际圆周间隙。
圆周间隙误差越小,减速器的输出精度就越高。
通过以上公式,可以清晰地了解减速器的输出精度是如何计算的。
工程师和技术人员可以根据实际情况,对减速器的输入精度和各种误差进行精确的测量和计算,从而评估减速器的输出精度,并采取相应的措施进行调整和改进。
除了计算输出精度,工程师和技术人员还应该关注减速器的使用和维护。
定期检查和维护减速器,及时发现和解决问题,可以有效地提高减速器的输出精度,延长其使用寿命,保证机械设备的正常运行。
减速器传动比计算公式
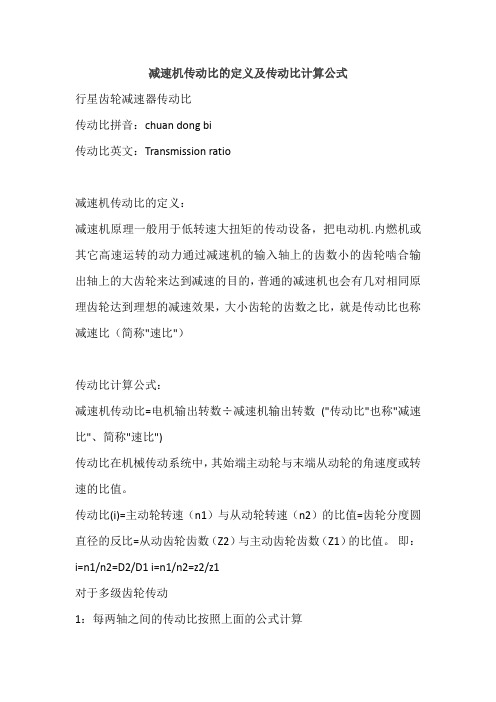
减速机传动比的定义及传动比计算公式行星齿轮减速器传动比传动比拼音:chuan dong bi传动比英文:Transmission ratio减速机传动比的定义:减速机原理一般用于低转速大扭矩的传动设备,把电动机.内燃机或其它高速运转的动力通过减速机的输入轴上的齿数小的齿轮啮合输出轴上的大齿轮来达到减速的目的,普通的减速机也会有几对相同原理齿轮达到理想的减速效果,大小齿轮的齿数之比,就是传动比也称减速比(简称"速比")传动比计算公式:减速机传动比=电机输出转数÷减速机输出转数("传动比"也称"减速比"、简称"速比")传动比在机械传动系统中,其始端主动轮与末端从动轮的角速度或转速的比值。
传动比(i)=主动轮转速(n1)与从动轮转速(n2)的比值=齿轮分度圆直径的反比=从动齿轮齿数(Z2)与主动齿轮齿数(Z1)的比值。
即:i=n1/n2=D2/D1 i=n1/n2=z2/z1对于多级齿轮传动1:每两轴之间的传动比按照上面的公式计算2:从第一轴到第n轴的总传动比按照下面公式计算: 总传动比ι=(Z2/Z1)×(Z4/Z3)×(Z6/Z5)……=(n1/n2)×(n3/n4)×(n5/n6)传动比扭矩计算公式:传动比扭矩=9550×电机功率÷电机功率输出转数×速比×使用效率(70%-96%)(同等电机功率和减速机承受范围内,传动比越大减速机输出扭矩越大转数越慢,同理传动比越小,减速机输出扭矩越小转数越快)齿轮减速机各级传动比的分配原则,主要是传动装置的结构紧凑、合理和有利于齿轮的均匀磨损。
因比齿轮减速机传动比注意以下几点:(i表示速比)1、各级传动比i值不宜过大,一般取2~6。
因传动比过大,大小齿轮的直径过分悬殊,小齿轮容易先磨损报废。
2、各级传动比i值应尽量接近,一般低速级传动比应比高速级传动比稍大,以避免低速级中心距小于高速级中心距而造成无法实现的传动结果。
行星齿轮减速器的相关计算
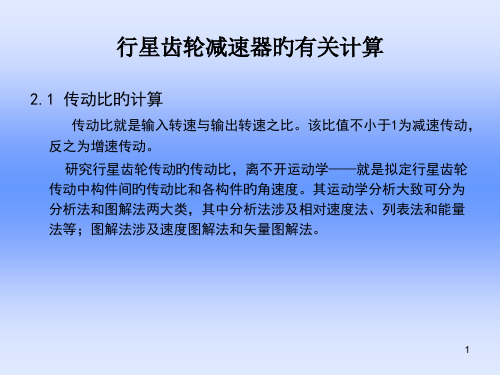
行星齿轮减速器旳有关计算
2.1.1分析法
2.1.1.1相对速度法 相对速度法又称转化机构法,首先由威尔斯(Willes)于1841年
提出旳。理论力学中旳相对运动原理,即“一种机构整体旳绝对运动 并不影响机构内部各构件间旳相对运动”。这正如一手表中旳秒针、 分针和时针旳相对运动关系不因带表人旳行动变化而变化。根据这一 相对运动原理,我们给整个行星轮系加上一种与转臂H旳角速度ωH大 小相等、方向相反旳公共角速度(-ωH)后,则行星机构中各构件间 旳相对运动关系仍保持不变。但这时转臂H将固定不动,行星轮系便 转化成了定轴齿轮传动,此假想旳定轴齿轮传动称为原行星齿轮传动 旳转化机构。这么便可用定轴齿轮传动旳传动比计算措施,首先算出 转化机构旳传动比,进而求得行星齿轮传动各构件间旳传动比。
主从动轮,则其传动比为:
H
i ab
H
a H
b
a
b
z z z H g b b
z z z H
a
g
a
(2.1-1)
4
行星齿轮减速器旳有关计算
5
行星齿轮减速器旳有关计算
6
行星齿轮减速器旳有关计算
7
行星齿轮减速器旳有关计算
8
行星齿轮减速器旳有关计算
2.1.1.2各类行星齿轮传动旳传动比计算
因为啮合副中旳小齿轮采用正变位(x1>0),当其齿数比u=z2/z1旳 值一定时,能够使小齿轮旳齿数z1<zmin,而不会产生根切现象,从而可 减小齿轮旳外形尺寸和重量。同步因为小齿轮采用正变位,其齿根厚度 增大,齿根旳最大滑动率减小,故可改善磨损情况和提升承载能力。
44
行星齿轮减速器旳有关计算
采用高度变位虽可在一定程度上改善行星齿轮传动旳性能, 但存在一定旳缺陷,如在小齿轮齿根强度提升旳同步,大齿轮旳 齿根强度有所下降;齿轮副不能采用更大旳模数等。故在行星齿 轮传动中较为广泛旳是采用角变位传动。 2.3.2.2 角度变位齿轮传动
减速机选型计算公式
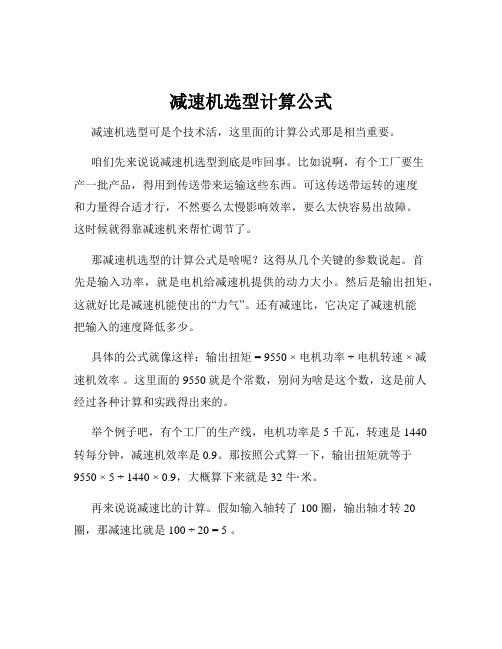
减速机选型计算公式减速机选型可是个技术活,这里面的计算公式那是相当重要。
咱们先来说说减速机选型到底是咋回事。
比如说啊,有个工厂要生产一批产品,得用到传送带来运输这些东西。
可这传送带运转的速度和力量得合适才行,不然要么太慢影响效率,要么太快容易出故障。
这时候就得靠减速机来帮忙调节了。
那减速机选型的计算公式是啥呢?这得从几个关键的参数说起。
首先是输入功率,就是电机给减速机提供的动力大小。
然后是输出扭矩,这就好比是减速机能使出的“力气”。
还有减速比,它决定了减速机能把输入的速度降低多少。
具体的公式就像这样:输出扭矩 = 9550 ×电机功率 ÷电机转速 ×减速机效率。
这里面的 9550 就是个常数,别问为啥是这个数,这是前人经过各种计算和实践得出来的。
举个例子吧,有个工厂的生产线,电机功率是 5 千瓦,转速是 1440 转每分钟,减速机效率是 0.9。
那按照公式算一下,输出扭矩就等于9550 × 5 ÷ 1440 × 0.9,大概算下来就是 32 牛·米。
再来说说减速比的计算。
假如输入轴转了 100 圈,输出轴才转 20 圈,那减速比就是 100 ÷ 20 = 5 。
不过,在实际选型的时候,可不能光盯着这些公式。
还得考虑工作环境,是高温、潮湿还是有灰尘啥的。
还有负载的特性,是平稳运行还是有冲击负载。
我记得之前去一个工厂帮忙选型,那场面真是让人头疼。
工厂里的设备又老又旧,运行起来嘎吱嘎吱响。
我就拿着本子和笔,在那一个个测量数据,计算选型。
结果算出来的减速机安装上去,一开始还挺好,没过几天就出问题了。
后来一检查,发现是因为设备老化,实际的负载比我计算的大多了。
没办法,只能重新选型,费了好大的劲。
所以啊,减速机选型可不能马虎,得综合考虑各种因素,反复计算和验证,才能选出最合适的减速机,让生产顺利进行。
总之,减速机选型的计算公式是基础,但实际应用中还得灵活多变,多观察多思考,这样才能选对减速机,让机器高效稳定地运转,为生产助力。
行星减速机减速比计算
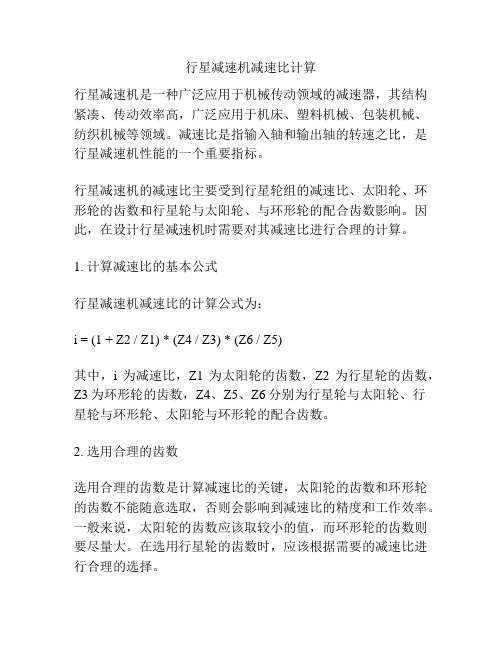
行星减速机减速比计算行星减速机是一种广泛应用于机械传动领域的减速器,其结构紧凑、传动效率高,广泛应用于机床、塑料机械、包装机械、纺织机械等领域。
减速比是指输入轴和输出轴的转速之比,是行星减速机性能的一个重要指标。
行星减速机的减速比主要受到行星轮组的减速比、太阳轮、环形轮的齿数和行星轮与太阳轮、与环形轮的配合齿数影响。
因此,在设计行星减速机时需要对其减速比进行合理的计算。
1. 计算减速比的基本公式行星减速机减速比的计算公式为:i = (1 + Z2 / Z1) * (Z4 / Z3) * (Z6 / Z5)其中,i为减速比,Z1为太阳轮的齿数,Z2为行星轮的齿数,Z3为环形轮的齿数,Z4、Z5、Z6分别为行星轮与太阳轮、行星轮与环形轮、太阳轮与环形轮的配合齿数。
2. 选用合理的齿数选用合理的齿数是计算减速比的关键,太阳轮的齿数和环形轮的齿数不能随意选取,否则会影响到减速比的精度和工作效率。
一般来说,太阳轮的齿数应该取较小的值,而环形轮的齿数则要尽量大。
在选用行星轮的齿数时,应该根据需要的减速比进行合理的选择。
3. 行星减速机的减速比分类根据行星减速机的结构和使用场合,其减速比可以分为常用的三种类型:(1)标准结构:减速比一般在3~10之间。
(2)扩展结构:减速比相对较大,达到100。
(3)多级结构:通过多个行星减速机的级联组合来实现较大的减速比,可以达到1000以上。
4. 行星减速机的选型规范在行星减速机的选型过程中,需要严格按照以下规范进行:(1)根据使用要求选择合适的减速比。
(2)根据负载要求选择合适的机型类型。
(3)根据工作环境选择合适的材质。
(4)对于高精度要求和长期工作的行星减速机,必须采用特殊的制造工艺和加工设备,确保产品的质量和稳定性。
5. 总结行星减速机的减速比是关乎其性能和使用效果的一个重要指标,其计算方法主要考虑轮组的齿数和配合方式等因素。
在选型过程中需要注意根据使用要求选择合适的减速比,同时也要根据负载要求、工作环境等多个因素进行综合考虑,确保选用的行星减速机能够满足要求。
减速器的重量如何计算公式

减速器的重量如何计算公式减速器是一种用于减慢旋转速度并增加扭矩的装置,通常用于工业生产中的机械设备和传动系统中。
减速器的重量对于其在实际应用中的使用具有重要的影响,因此需要进行准确的计算。
本文将介绍减速器重量的计算公式,并探讨在实际应用中的重要性。
减速器的重量计算公式通常包括几个主要的参数,包括减速比、输入功率、输出转矩等。
下面将介绍减速器重量的计算公式及其各个参数的含义。
首先,减速器的重量可以通过以下公式进行计算:W = (ρ V) + (F g)。
其中,W表示减速器的重量,ρ表示减速器的密度,V表示减速器的体积,F表示减速器的受力,g表示重力加速度。
减速器的密度ρ通常是由材料的密度决定的,可以通过材料的密度表进行查找。
减速器的体积V通常是通过减速器的尺寸参数进行计算得出的,可以通过减速器的设计图纸或者实际测量得到。
减速器的受力F通常是由减速器在工作状态下所受的各种力的合力,包括轴向力、径向力等。
重力加速度g通常取9.8m/s^2。
其次,减速器的重量还可以通过以下公式进行计算:W = (M g)。
其中,W表示减速器的重量,M表示减速器的质量,g表示重力加速度。
减速器的质量M通常是由减速器的材料密度和体积决定的,可以通过材料的密度表进行查找。
重力加速度g通常取9.8m/s^2。
在实际应用中,减速器的重量对于其在机械设备和传动系统中的使用具有重要的影响。
首先,减速器的重量直接影响到机械设备的安装和运输。
较重的减速器需要更大的安装和运输设备,增加了设备的成本和复杂度。
其次,减速器的重量还直接影响到机械设备的稳定性和安全性。
较重的减速器在工作过程中需要更强的支撑和固定,否则容易导致设备的不稳定和安全隐患。
因此,在设计和选择减速器时,需要充分考虑其重量对于机械设备和传动系统的影响。
在实际应用中,减速器的重量通常是通过计算得出的,可以根据减速器的设计参数和工作条件进行计算。
同时,还需要考虑到减速器的结构和材料对于其重量的影响,选择合适的材料和结构可以有效降低减速器的重量,提高其在实际应用中的使用效率和安全性。
减速器全部计算

减速器全部计算以知条件1.输送带工作拉力:F=2700KN2.输送带运动速度:V=1.3M/S3.滚筒直径:D=350mm4.卷筒效率η=0.95工作情况:5.两班制工作,连续单向运转。
6.工作环境:室内,灰尘较大,环境最高温度35度7.使用期限:4年一次大修,每年280个工作日,寿命8年。
一、传动方案拟定第二组第三个数据:设计带式输送机传动装置中的一级圆柱齿轮减速器(1)工作条件:使用年限10年,每年按300天计算,两班制工作,载荷平稳。
(2)原始数据:滚筒圆周力F=1.7KN;带速V=1.4m/s;滚筒直径D=220mm。
运动简图二、电动机的选择1、电动机类型和结构型式的选择:按已知的工作要求和条件,选用Y系列三相异步电动机。
2、确定电动机的功率:(1)传动装置的总效率:η总=η带×η2轴承×η齿轮×η联轴器×η滚筒=0.96×0.992×0.97×0.99×0.95=0.86(2)电机所需的工作功率:Pd=FV/1000η总=1700×1.4/1000×0.86=2.76KW3、确定电动机转速:滚筒轴的工作转速:Nw=60×1000V/πD=60×1000×1.4/π×220=121.5r/min根据【2】表2.2中推荐的合理传动比范围,取V带传动比Iv=2~4,单级圆柱齿轮传动比范围Ic=3~5,则合理总传动比i的范围为i=6~20,故电动机转速的可选范围为nd=i×nw=(6~20)×121.5=729~2430r/min符合这一范围的同步转速有960 r/min和1420r/min。
由【2】表8.1查出有三种适用的电动机型号、如下表方案电动机型号额定功率电动机转速(r/min)传动装置的传动比KW 同转满转总传动比带齿轮1 Y132s-6 3 1000 960 7.9 3 2.632 Y100l2-43 1500 1420 11.68 3 3.89综合考虑电动机和传动装置尺寸、重量、价格和带传动、减速器的传动比,比较两种方案可知:方案1因电动机转速低,传动装置尺寸较大,价格较高。
电机、减速器、联轴器扭矩计算及电机功率与转速的关系
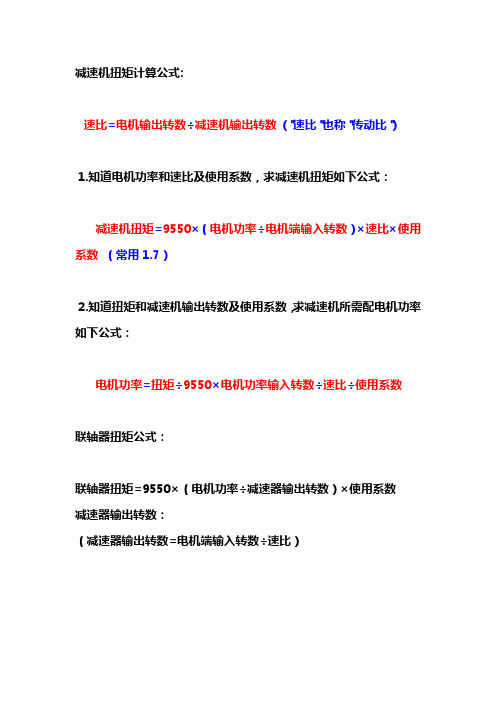
减速机扭矩计算公式:速比=电机输出转数÷减速机输出转数("速比"也称"传动比")1.知道电机功率和速比及使用系数,求减速机扭矩如下公式:减速机扭矩=9550×(电机功率÷电机端输入转数)×速比×使用系数(常用1.7)2.知道扭矩和减速机输出转数及使用系数,求减速机所需配电机功率如下公式:电机功率=扭矩÷9550×电机功率输入转数÷速比÷使用系数联轴器扭矩公式:联轴器扭矩=9550×(电机功率÷减速器输出转数)×使用系数减速器输出转数:(减速器输出转数=电机端输入转数÷速比)电机功率和转速的关系:P=T×n/9550其中P是额定功率(KW) 、n 是额定转速(分/转) 、T是额定转矩(N.m)你没给速度,假设是3000rpm,那么电机T=9550XP/n=9550X11/3000=35N.m,35X减速比847=29645N.m输出扭矩。
三角带传动速比如何计算?传动装置:电机轴转速n1=960转/分,减速机入轴转速n2 =514转/分,电机用皮带轮d1=150mm ,求减速机皮带轮d2 =? 带轮速比i=?i=n1÷n2= 960÷514=1.87根据d1/d2=n2/n1d2=d1×n1÷n2 =150×960÷514=280㎜答:减速机皮带轮直径为:280毫米; 带轮速比为: 1.87。
1.减速机用在什么设备上,以便确定安全系数SF(SF=减速机额定功率处以电机功率),安装形式(直交轴,平行轴,输出空心轴键,输出空心轴锁紧盘等)等2.提供电机功率,级数(是4P、6P还是8P电机)3.减速机周围的环境温度(决定减速机的热功率的校核)4.减速机输出轴的径向力和轴向力的校核。
减速器传动参数计算公式
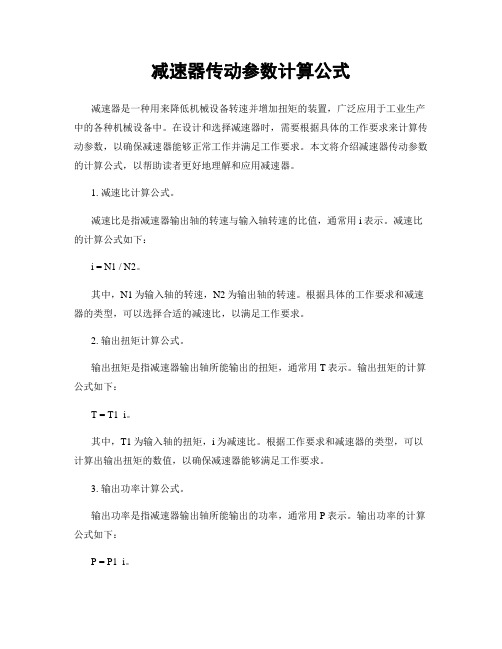
减速器传动参数计算公式减速器是一种用来降低机械设备转速并增加扭矩的装置,广泛应用于工业生产中的各种机械设备中。
在设计和选择减速器时,需要根据具体的工作要求来计算传动参数,以确保减速器能够正常工作并满足工作要求。
本文将介绍减速器传动参数的计算公式,以帮助读者更好地理解和应用减速器。
1. 减速比计算公式。
减速比是指减速器输出轴的转速与输入轴转速的比值,通常用i表示。
减速比的计算公式如下:i = N1 / N2。
其中,N1为输入轴的转速,N2为输出轴的转速。
根据具体的工作要求和减速器的类型,可以选择合适的减速比,以满足工作要求。
2. 输出扭矩计算公式。
输出扭矩是指减速器输出轴所能输出的扭矩,通常用T表示。
输出扭矩的计算公式如下:T = T1 i。
其中,T1为输入轴的扭矩,i为减速比。
根据工作要求和减速器的类型,可以计算出输出扭矩的数值,以确保减速器能够满足工作要求。
3. 输出功率计算公式。
输出功率是指减速器输出轴所能输出的功率,通常用P表示。
输出功率的计算公式如下:P = P1 i。
其中,P1为输入轴的功率,i为减速比。
根据工作要求和减速器的类型,可以计算出输出功率的数值,以确保减速器能够满足工作要求。
4. 输入功率计算公式。
输入功率是指减速器输入轴所需的功率,通常用P表示。
输入功率的计算公式如下:P = P2 / η。
其中,P2为输出轴的功率,η为传动效率。
根据工作要求和减速器的类型,可以计算出输入功率的数值,以确保减速器能够满足工作要求。
5. 传动效率计算公式。
传动效率是指减速器在传动过程中所能转换的功率与输入功率的比值,通常用η表示。
传动效率的计算公式如下:η = (P1 i) / P2。
根据工作要求和减速器的类型,可以计算出传动效率的数值,以确保减速器能够满足工作要求。
6. 转矩计算公式。
转矩是指减速器在传动过程中所产生的力矩,通常用M表示。
转矩的计算公式如下:M = T r。
其中,T为输出扭矩,r为输出轴的半径。
减速器相关计算

1.减速器的概述减速器原理减速器是指原动机与工作机之间独立封闭式传动装置。
此外,减速器也是一种动力传达机构,利用齿轮的速度转换器,将马达的问转数减速到所要的回转数,并得到较大转矩的机构。
降速同时提高输出扭矩,扭矩输出比例按电机输出乘减速比,但要注意不能超出减速器额定扭矩。
减速器的作用减速器的作用就是减速增矩,这个功能完全靠齿轮与齿轮之间的啮合完成,比较容易理解。
减速器的种类很多,按照传动类型可分为齿轮减速器、蜗杆减速器和行星减速器以及它们互相组合起来的减速器;按照传动的级数可分为单级和多级减速器;按照齿轮形状可分为圆柱齿轮减速器、圆锥齿轮减速器和圆锥一圆柱齿轮减速器;按照传动的布置形式又可分为展开式、分流式和同轴式减速器。
(1)蜗轮蜗杆减速器的土要特点是具有反向自锁功能,可以有较大的减速比,输人轴和输出轴不在同一轴线上,也不在同一平面上。
但是一般体积较大,传动效率不高,精度不高。
(2)谐波减速器的谐波传动是利用柔性元件可控的弹性变形来传递运动和动力的,体积不大、精度很高,但缺点是柔轮寿命有限、不耐冲击,刚性与金属件相比较差。
输入转速不能太高。
(3)行星齿轮减速器行星减速器一般用于在有限的空间里需要较高的转矩时,即小体积大转矩,而且它的可靠性和寿命都比正齿轮减速器要好。
(4)展开式两级圆柱齿轮减速器展开式两级圆柱齿轮减速器是两级减速器中最简单、应用最广泛的一种。
(5)两级圆锥-圆柱齿轮减速器单级圆锥齿轮减速器及两级圆锥-圆柱齿轮减速器用于需要输人轴与输出轴成90D配置的传动中。
(6)同轴式两级圆柱减速器同轴式两级圆柱减速器的径向尺寸紧凑,但径向尺寸较大。
减速器的种类繁多,如今应用于各个领域,总体的发展趋势如下:①高水平、高性能。
圆柱齿轮普遍采用渗碳淬火、磨齿,承载能力提高4倍以上,体积小、重量轻、噪声低、效率高、可靠性高。
②积木式组合设计。
基本参数采用优先数,尺寸规格整齐,零件通用性和互换性强,系列容易扩充和花样翻新,利于组织批量生产和降低成本。
减速电机计算公式

减速电机计算公式
减速电机计算公式:
1.功率计算公式:P=T·ω
其中:P(功率)=电机中轴转动部分所受力矩×转速
T(扭矩)=一般用于计算减速电机所需功率的关键参数,由载荷所产
生的力矩可计算出该数值;
ω(角速度)=以弧度/秒为单位的轴的转速,一般等于转数的乘积n·nt。
2.减速器温度计算公式:T=P/R
其中:T(温度)=系统中摩擦热所被排出的温度;
P(功率)=电机中轴转动部分所受力矩×转速;
R(容量系数)=根据减速机所用轴承、油液来确定,用于表示减速机
所能够吸收的热量容量。
3.传动比计算公式:M=N1/N2
其中:M(传动比)=减速机的输入转速N1和输出转速N2的比值
N1(输入速度)=以弧度/秒为单位的轴的输入转速
N2(输出速度)=以弧度/秒为单位的轴的输出转速。
4.电机转矩计算公式:T=P/ω
其中:T(转矩)=减速机内部所受力矩
P(功率)=电容启动机所需功率
ω(角速度)=角度/秒为单位的轴的转速。
5.摩擦系数计算公式:μ=T/F
其中:μ(摩擦系数)=由减速器所受力矩和机械摩擦力之间的比值T(扭矩)=以牛顿米为单位的减速机所受力矩
F(摩擦力)=根据不同的接触材料来测定,一般以牛顿米为单位。
行星减速器减速比计算

行星减速器减速比计算摘要:1.行星减速器简介2.减速比计算方法3.齿轮系计算方法4.减速比选择建议5.应用实例正文:一、行星减速器简介行星减速器是一种传动装置,其主要作用是降低输入转速,增加输出扭矩。
它在工业机器人、自动化设备等领域应用广泛。
行星减速器主要由太阳轮、行星轮和内齿轮组成。
太阳轮与输入轴连接,行星轮与输出轴连接,内齿轮固定。
通过太阳轮、行星轮和内齿轮的相对运动,实现输入转速与输出转速之间的减速。
二、减速比计算方法减速比是指减速机构中瞬时输入速度与输出速度的比值,用符号i 表示。
其计算公式为:i = n1 / n2,其中n1 为输入转速,n2 为输出转速。
例如,输入转速为1500r/min,输出转速为25r/min,那么其减速比则为:i = 1500 / 25 = 60:1。
三、齿轮系计算方法在行星减速器中,减速比可以通过从动齿轮齿数与主动齿轮齿数的比值来计算。
假设从动齿轮齿数为z2,主动齿轮齿数为z1,那么减速比为:i = z1 / z2。
如果是多级齿轮减速器,需要将所有相啮合的一对齿轮组的从动轮齿数与主动轮齿数相除,然后取其最小值作为减速比。
四、减速比选择建议在选择行星减速器时,应根据实际应用需求选择合适的减速比。
减速比过大会导致输出转速过低,影响设备的工作效率;减速比过小会导致输出扭矩不足,影响设备的承载能力。
五、应用实例假设一个机器人手臂需要实现一个动作,其动作范围为100 度。
假设手臂的驱动电机转速为3000r/min,那么通过行星减速器降低转速后,输出轴的转速应为:n2 = n1 * i = 3000 * 60 / 12 = 1500r/min。
机械原理减速器公式汇总
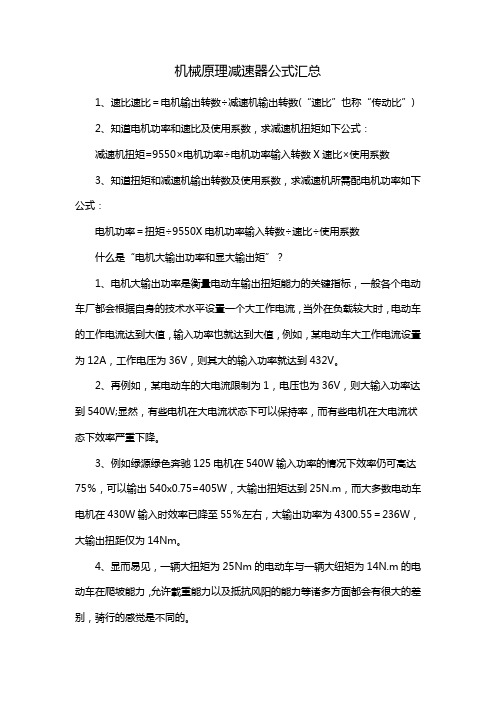
机械原理减速器公式汇总
1、速比速比=电机输出转数÷减速机输出转数(“速比”也称“传动比”)
2、知道电机功率和速比及使用系数,求减速机扭矩如下公式:
减速机扭矩=9550×电机功率÷电机功率输入转数X速比×使用系数
3、知道扭矩和减速机输出转数及使用系数,求减速机所需配电机功率如下公式:
电机功率=扭矩÷9550X电机功率输入转数÷速比÷使用系数
什么是“电机大输出功率和显大输出矩”?
1、电机大输出功率是衡量电动车输出扭矩能力的关键指标,一般各个电动车厂都会根据自身的技术水平设置一个大工作电流,当外在负载较大时,电动车的工作电流达到大值,输入功率也就达到大值,例如,某电动车大工作电流设置为12A,工作电压为36V,则其大的输入功率就达到432V。
2、再例如,某电动车的大电流限制为1,电压也为36V,则大输入功率达到540W;显然,有些电机在大电流状态下可以保持率,而有些电机在大电流状态下效率严重下降。
3、例如绿源绿色奔驰125电机在540W输入功率的情况下效率仍可高达75%,可以输出540x0.75=405W,大输出扭矩达到25N.m,而大多数电动车电机在430W输入时效率已降至55%左右,大输出功率为4300.55=236W,大输出扭距仅为14Nm。
4、显而易见,一辆大扭矩为25Nm的电动车与一辆大纽矩为14N.m的电动车在爬坡能力,允许載重能力以及抵抗风阳的能力等诸多方面都会有很大的差别,骑行的感觉是不同的。
5、消费者在购车时若需对车辆的大输出扭矩进行试验,简单的方法是“负重爬坡”。
减速器设计计算及说明书

减速器设计计算及说明书
目录
一、总体方案设计 (1)
二、运动参数设计 (2)
三、主要零件的计算 (6)
四、减速器的润滑、密封及装油量的计算 (23)
一、总体方案设计
二、运动参数设计
=65r/min
所选电动机的额定功率,取,选择电动机三相异步电动机,其额定转速
三、主要零件的计算
按图6-7MQ线查得轮齿弯曲疲劳极限应力为:,。
,;
,
,则
查图6-16,得两轮复合齿形系数为,,
代入计算,于是
;按图6-7MQ线查得轮齿弯曲疲劳极限应力为:
,;
,
,则
;弹性系数查表
取a=210mm,按经验式,取。
,。
,
四、减速器的润滑、密封及装油量的计算
时,轴承可选用油润滑润滑,通过在箱体上开油沟以达到润)飞溅润滑:当齿轮圆周速度
)刮板润滑:当齿轮圆周速度很低(。
一级蜗杆减速器计算公式

一级蜗杆减速器计算公式一级蜗杆减速器是一种常用的传动装置,它通过蜗杆和蜗轮的组合来实现速度的减小和扭矩的增大。
在工业生产中,一级蜗杆减速器被广泛应用于各种机械设备中,如输送机、搅拌机、搅拌机、冷却机等。
在设计和选择一级蜗杆减速器时,需要进行一定的计算和分析,以确保其能够满足实际工作需求。
本文将介绍一级蜗杆减速器的计算公式及其应用。
一级蜗杆减速器的基本结构包括蜗杆、蜗轮、壳体、轴承、润滑系统等部件。
其中,蜗杆和蜗轮是传动的核心部件,其传动比的计算是设计和选择一级蜗杆减速器的重要依据。
传动比是指蜗轮的转速与蜗杆的转速之比,通常用i表示。
传动比的计算公式如下:i = Z2 / Z1。
其中,Z2为蜗轮的齿数,Z1为蜗杆的螺旋线数。
根据这个公式,我们可以通过已知的蜗轮齿数和蜗杆螺旋线数来计算出一级蜗杆减速器的传动比。
传动比的大小直接影响到输出轴的转速和扭矩,因此在实际应用中需要根据具体的工作要求来选择合适的传动比。
除了传动比之外,一级蜗杆减速器的设计还需要考虑到功率、效率、轴向力、径向力等因素。
在实际工程中,我们需要根据具体的工作条件和要求来计算和选择合适的一级蜗杆减速器。
下面将介绍一些常用的计算公式和方法。
1. 功率计算。
一级蜗杆减速器的功率计算是设计过程中的关键环节。
通常情况下,我们需要根据输入端的功率和转速来计算输出端的功率。
功率的计算公式如下:P2 = P1 η。
其中,P1为输入端的功率,η为传动效率。
传动效率是指蜗杆减速器在传动过程中损耗的功率与输入功率之比,通常取值在0.9~0.95之间。
通过这个公式,我们可以根据输入端的功率和传动效率来计算出输出端的功率,从而确定一级蜗杆减速器的适用范围。
2. 轴向力和径向力计算。
在一级蜗杆减速器的设计和选择过程中,还需要考虑到轴向力和径向力的计算。
轴向力和径向力是蜗杆减速器在工作过程中产生的力,其大小直接影响到轴承和壳体的选型和设计。
轴向力和径向力的计算公式如下:Fa = F tan(α)。
行星减速器减速比计算

行星减速器减速比计算
【最新版】
目录
1.行星减速器简介
2.减速比的定义和计算方法
3.行星减速器的齿轮系计算方法
4.减速比的应用和选择
5.结论
正文
一、行星减速器简介
行星减速器是一种传动装置,其主要作用是降低输入转速,提高输出扭矩。
它在工业生产和机械设备中应用广泛,具有结构紧凑、传动比稳定、噪音低、效率高等优点。
二、减速比的定义和计算方法
减速比是指减速机构中瞬时输入速度与输出速度的比值,用符号 i 表示。
其计算方法为:减速比 = n1 / n2,其中 n1 为输入转速,n2 为输出转速。
例如,输入转速为 1500r/min,输出转速为 25r/min,那么其减速比则为:i = 1500 / 25 = 60:1。
三、行星减速器的齿轮系计算方法
行星减速器的齿轮系计算方法分为两步。
首先,根据行星轮系的结构,确定太阳轮、行星轮和内齿轮的齿数,分别记作 z1、z2 和 z3。
然后,根据齿轮系的传动比,计算出各齿轮的齿数。
具体计算方法为:
1.行星轮与太阳轮的减速比:i1 = z3 / z1;
2.行星轮与内齿轮的减速比:i2 = z2 / z3;
3.总减速比:i = i1 * i2。
四、减速比的应用和选择
在实际应用中,减速比的选择要根据具体需求来确定。
首先,根据设备所需扭矩和速度,计算出理论减速比。
然后,根据行星减速器的效率、噪音等因素,选择合适的减速比。
五、结论
行星减速器是一种重要的传动装置,减速比的计算和选择是其设计和应用的关键。
- 1、下载文档前请自行甄别文档内容的完整性,平台不提供额外的编辑、内容补充、找答案等附加服务。
- 2、"仅部分预览"的文档,不可在线预览部分如存在完整性等问题,可反馈申请退款(可完整预览的文档不适用该条件!)。
- 3、如文档侵犯您的权益,请联系客服反馈,我们会尽快为您处理(人工客服工作时间:9:00-18:30)。
以知条件1.输送带工作拉力:F=2700KN2.输送带运动速度:V=1.3M/S3.滚筒直径:D=350mm4.卷筒效率η=0.95工作情况:5.两班制工作,连续单向运转。
6.工作环境:室内,灰尘较大,环境最高温度35度7.使用期限:4年一次大修,每年280个工作日,寿命8年。
一、传动方案拟定第二组第三个数据:设计带式输送机传动装置中的一级圆柱齿轮减速器(1)工作条件:使用年限10年,每年按300天计算,两班制工作,载荷平稳。
(2)原始数据:滚筒圆周力F=1.7KN;带速V=1.4m/s;滚筒直径D=220mm。
运动简图二、电动机的选择1、电动机类型和结构型式的选择:按已知的工作要求和条件,选用Y系列三相异步电动机。
2、确定电动机的功率:(1)传动装置的总效率:η总=η带×η2轴承×η齿轮×η联轴器×η滚筒=0.96×0.992×0.97×0.99×0.95=0.86(2)电机所需的工作功率:Pd=FV/1000η总=1700×1.4/1000×0.86=2.76KW3、确定电动机转速:滚筒轴的工作转速:Nw=60×1000V/πD=60×1000×1.4/π×220=121.5r/min根据【2】表2.2中推荐的合理传动比范围,取V带传动比Iv=2~4,单级圆柱齿轮传动比范围Ic=3~5,则合理总传动比i的范围为i=6~20,故电动机转速的可选范围为nd=i×nw=(6~20)×121.5=729~2430r/min符合这一范围的同步转速有960 r/min和1420r/min。
由【2】表8.1查出有三种适用的电动机型号、如下表方案电动机型号额定功率电动机转速(r/min)传动装置的传动比KW 同转满转总传动比带齿轮1 Y132s-6 3 1000 960 7.9 3 2.632 Y100l2-43 1500 1420 11.68 3 3.89综合考虑电动机和传动装置尺寸、重量、价格和带传动、减速器的传动比,比较两种方案可知:方案1因电动机转速低,传动装置尺寸较大,价格较高。
方案2适中。
故选择电动机型号Y100l2-4。
4、确定电动机型号根据以上选用的电动机类型,所需的额定功率及同步转速,选定电动机型号为Y100l2-4。
其主要性能:额定功率:3KW,满载转速1420r/min,额定转矩2.2。
三、计算总传动比及分配各级的传动比1、总传动比:i总=n电动/n筒=1420/121.5=11.682、分配各级传动比(1)取i带=3(2)∵i总=i齿×i 带π∴i齿=i总/i带=11.68/3=3.89四、运动参数及动力参数计算1、计算各轴转速(r/min)nI=nm/i带=1420/3=473.33(r/min)nII=nI/i齿=473.33/3.89=121.67(r/min)滚筒nw=nII=473.33/3.89=121.67(r/min)2、计算各轴的功率(KW)PI=Pd×η带=2.76×0.96=2.64KWPII=PI×η轴承×η齿轮=2.64×0.99×0.97=2.53KW3、计算各轴转矩Td=9.55Pd/nm=9550×2.76/1420=18.56N?mTI=9.55p2入/n1 =9550x2.64/473.33=53.26N?mTII =9.55p2入/n2=9550x2.53/121.67=198.58N?m五、传动零件的设计计算1、皮带轮传动的设计计算(1)选择普通V带截型由课本[1]P189表10-8得:kA=1.2 P=2.76KWPC=KAP=1.2×2.76=3.3KW据PC=3.3KW和n1=473.33r/min由课本[1]P189图10-12得:选用A型V带(2)确定带轮基准直径,并验算带速由[1]课本P190表10-9,取dd1=95mm>dmin=75dd2=i带dd1(1-ε)=3×95×(1-0.02)=279.30 mm由课本[1]P190表10-9,取dd2=280带速V:V=πdd1n1/60×1000=π×95×1420/60×1000=7.06m/s在5~25m/s范围内,带速合适。
(3)确定带长和中心距初定中心距a0=500mmLd=2a0+π(dd1+dd2)/2+(dd2-dd1)2/4a0=2×500+3.14(95+280)+(280-95)2/4×450=1605.8mm根据课本[1]表(10-6)选取相近的Ld=1600mm确定中心距a≈a0+(Ld-Ld0)/2=500+(1600-1605.8)/2=497mm(4) 验算小带轮包角α1=1800-57.30 ×(dd2-dd1)/a=1800-57.30×(280-95)/497=158.670>1200(适用)(5)确定带的根数单根V带传递的额定功率.据dd1和n1,查课本图10-9得P1=1.4KWi≠1时单根V带的额定功率增量.据带型及i查[1]表10-2得△P1=0.17KW查[1]表10-3,得Kα=0.94;查[1]表10-4得KL=0.99Z= PC/[(P1+△P1)KαKL]=3.3/[(1.4+0.17) ×0.94×0.99]=2.26 (取3根)(6) 计算轴上压力由课本[1]表10-5查得q=0.1kg/m,由课本式(10-20)单根V带的初拉力:F0=500PC/ZV[(2.5/Kα)-1]+qV2=500x3.3/[3x7.06(2.5/0.94-1)]+0.10x7.062 =134.3kN则作用在轴承的压力FQFQ=2ZF0sin(α1/2)=2×3×134.3sin(158.67o/2)=791.9N2、齿轮传动的设计计算(1)选择齿轮材料与热处理:所设计齿轮传动属于闭式传动,通常齿轮采用软齿面。
查阅表[1] 表6-8,选用价格便宜便于制造的材料,小齿轮材料为45钢,调质,齿面硬度260HBS;大齿轮材料也为45钢,正火处理,硬度为215HBS;精度等级:运输机是一般机器,速度不高,故选8级精度。
(2)按齿面接触疲劳强度设计由d1≥ (6712×kT1(u+1)/φdu[σH]2)1/3确定有关参数如下:传动比i齿=3.89取小齿轮齿数Z1=20。
则大齿轮齿数:Z2=iZ1= ×20=77.8取z2=78由课本表6-12取φd=1.1(3)转矩T1T1=9.55×106×P1/n1=9.55×106×2.61/473.33=52660N?mm(4)载荷系数k : 取k=1.2(5)许用接触应力[σH][σH]= σHlim ZN/SHmin 由课本[1]图6-37查得:σHlim1=610Mpa σHlim2=500Mpa接触疲劳寿命系数Zn:按一年300个工作日,每天16h计算,由公式N=60njtn 计算N1=60×473.33×10×300×18=1.36x109N2=N/i=1.36x109 /3.89=3.4×108查[1]课本图6-38中曲线1,得ZN1=1 ZN2=1.05按一般可靠度要求选取安全系数SHmin=1.0[σH]1=σHlim1ZN1/SHmin=610x1/1=610 Mpa[σH]2=σHlim2ZN2/SHmin=500x1.05/1=525Mpa故得:d1≥ (6712×kT1(u+1)/φdu[σH]2)1/3=49.04mm模数:m=d1/Z1=49.04/20=2.45mm取课本[1]P79标准模数第一数列上的值,m=2.5(6)校核齿根弯曲疲劳强度σ bb=2KT1YFS/bmd1确定有关参数和系数分度圆直径:d1=mZ1=2.5×20mm=50mmd2=mZ2=2.5×78mm=195mm齿宽:b=φdd1=1.1×50mm=55mm取b2=55mm b1=60mm(7)复合齿形因数YFs 由课本[1]图6-40得:YFS1=4.35,YFS2=3.95(8)许用弯曲应力[σbb]根据课本[1]P116:[σbb]= σbblim YN/SFmin由课本[1]图6-41得弯曲疲劳极限σbblim应为:σbblim1=490Mpa σbblim2 =410Mpa由课本[1]图6-42得弯曲疲劳寿命系数YN:YN1=1 YN2=1弯曲疲劳的最小安全系数SFmin :按一般可靠性要求,取SFmin =1计算得弯曲疲劳许用应力为[σbb1]=σbblim1 YN1/SFmin=490×1/1=490Mpa[σbb2]= σbblim2 YN2/SFmin =410×1/1=410Mpa校核计算σbb1=2kT1YFS1/ b1md1=71.86pa< [σbb1]σbb2=2kT1YFS2/ b2md1=72.61Mpa< [σbb2]故轮齿齿根弯曲疲劳强度足够(9)计算齿轮传动的中心矩aa=(d1+d2)/2= (50+195)/2=122.5mm(10)计算齿轮的圆周速度V计算圆周速度V=πn1d1/60×1000=3.14×473.33×50/60×1000=1.23m/s因为V<6m/s,故取8级精度合适.六、轴的设计计算从动轴设计1、选择轴的材料确定许用应力选轴的材料为45号钢,调质处理。
查[2]表13-1可知:σb=650Mpa,σs=360Mpa,查[2]表13-6可知:[σb+1]bb=215Mpa[σ0]bb=102Mpa,[σ-1]bb=60Mpa2、按扭转强度估算轴的最小直径单级齿轮减速器的低速轴为转轴,输出端与联轴器相接,从结构要求考虑,输出端轴径应最小,最小直径为:d≥C查[2]表13-5可得,45钢取C=118则d≥118×(2.53/121.67)1/3mm=32.44mm考虑键槽的影响以及联轴器孔径系列标准,取d=35mm3、齿轮上作用力的计算齿轮所受的转矩:T=9.55×106P/n=9.55×106×2.53/121.67=198582 N齿轮作用力:圆周力:Ft=2T/d=2×198582/195N=2036N径向力:Fr=Fttan200=2036×tan200=741N4、轴的结构设计轴结构设计时,需要考虑轴系中相配零件的尺寸以及轴上零件的固定方式,按比例绘制轴系结构草图。