锅炉燃烧控制系统设计
(完整版)我的工业燃煤锅炉DCS控制系统设计毕业论文设计
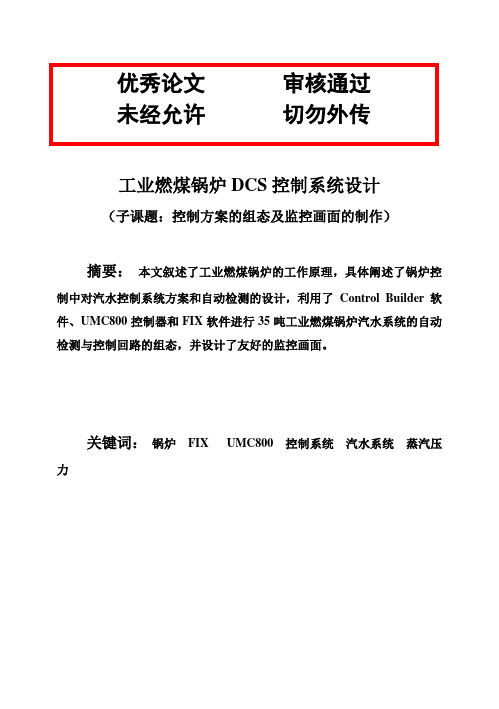
工业燃煤锅炉DCS控制系统设计(子课题:控制方案的组态及监控画面的制作)摘要:本文叙述了工业燃煤锅炉的工作原理,具体阐述了锅炉控制中对汽水控制系统方案和自动检测的设计,利用了Control Builder 软件、UMC800控制器和FIX软件进行35吨工业燃煤锅炉汽水系统的自动检测与控制回路的组态,并设计了友好的监控画面。
关键词:锅炉FIX UMC800 控制系统汽水系统蒸汽压力Abstract: the paper introduce the principle of the boiler which is used in burning coal industrial,it describes the scheme of the steam controlsystem in boiler control and the design of auto-detection. it use the Control Buildersoftware,UMC800 controller and FIX softwareto auto-detect 35t steam system in burningcoal industrial and configuration the controlloop, and designed the friendly supervisionappearance.Keyword: boiler, FIX, UMC800, control system, steam system, steam pressure引言锅炉微机控制,是近年来开发的一项新技术,它是微型计算机软件、硬件、自动控制、锅炉节能等几项技术紧密结合的产物,我国现有中、小型锅炉30多万台,每年耗煤量占我国原煤产量的13,目前大多数工业锅炉仍处于能耗高、浪费大、环境污染严重的生产状态。
提高热效率,降低耗煤量,降低耗电量,用微机进行控制是一件具有深远意义的工作。
基于PLC单片机控制中小型蒸汽锅炉智能燃烧系统

产。
4
3、锅炉引风控制
炉膛负压控制系统一般采用的控制流程图 如下图所示,调节原理比较简单属于单闭 环调节系统,它的输入量是炉膛负压输出 量是引风变频器,同时引入鼓风量作为前 馈信号。
给定蒸汽压力
+ -
引风调节单元
引风机变频器
锅炉系统
抗干扰滤波
炉膛负压信号
5
4、锅炉鼓风控制
鼓风控制系统一般采用的控制流程图如下图所示,
先通过蒸汽压力变送器经滤波后取得信号,与设 定蒸汽压力进行比较,判断出鼓风PID调节器调节 的方向和大小,通过鼓风PID调节单元计算出鼓风 变频器的输出大小
给定蒸汽压力
+ -
炉排调节单元
风煤比
炉排变频器
鼓风调节单元 抗干扰滤波
鼓风变频器 蒸汽压力信号
炉排系统
6
二、控制系统硬件设计
PLC不仅具有逻辑控制功能,而且还具有了 运算、数据处理和数据传送等功能 ,采用可编 程控制器设计的控制系统可以实现对锅炉精确地 实时自动控制,并且实现了整个系统的优化控制。 变频调速的基本原理是通过改变电动机工作电源 频率达到改变电机转速的目的,采用变频调速技 术来控制锅炉的泵与风机,可以使电动机不必总 在工频下运行,可以大大的节省电能。
2、程序设计结果,见论文P35~P37
13
四、上位机系统制作
MCGS (Monitor and Control Generated System, 通用监控系统)是一套用于快速构造和生成计算机 监控系统的组态软件,它能够在基于Microsoft (各种 32 位 Windows 平台上)运行,通过对现 场数据的采集处理,以动画显示、报警处理、流 程控制、实时曲线、历史曲线和报表输出等多种 方式向用户提供解决实际工程问题的方案,它充 分利用了 Windows图形功能完备、界面一致性好、 易学易用的特点,在自动化领域有着广泛的应用。
基于PLC的锅炉燃烧控制系统设计_毕业设计论文正文 精品
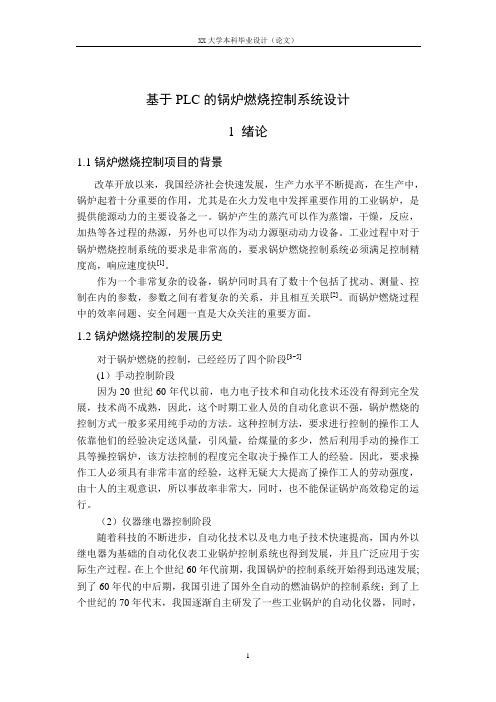
基于PLC的锅炉燃烧控制系统设计1 绪论1.1锅炉燃烧控制项目的背景改革开放以来,我国经济社会快速发展,生产力水平不断提高,在生产中,锅炉起着十分重要的作用,尤其是在火力发电中发挥重要作用的工业锅炉,是提供能源动力的主要设备之一。
锅炉产生的蒸汽可以作为蒸馏,干燥,反应,加热等各过程的热源,另外也可以作为动力源驱动动力设备。
工业过程中对于锅炉燃烧控制系统的要求是非常高的,要求锅炉燃烧控制系统必须满足控制精度高,响应速度快[1]。
作为一个非常复杂的设备,锅炉同时具有了数十个包括了扰动、测量、控制在内的参数,参数之间有着复杂的关系,并且相互关联[2]。
而锅炉燃烧过程中的效率问题、安全问题一直是大众关注的重要方面。
1.2锅炉燃烧控制的发展历史对于锅炉燃烧的控制,已经经历了四个阶段[3~5](1)手动控制阶段因为20世纪60年代以前,电力电子技术和自动化技术还没有得到完全发展,技术尚不成熟,因此,这个时期工业人员的自动化意识不强,锅炉燃烧的控制方式一般多采用纯手动的方法。
这种控制方法,要求进行控制的操作工人依靠他们的经验决定送风量,引风量,给煤量的多少,然后利用手动的操作工具等操控锅炉,该方法控制的程度完全取决于操作工人的经验。
因此,要求操作工人必须具有非常丰富的经验,这样无疑大大提高了操作工人的劳动强度,由十人的主观意识,所以事故率非常大,同时,也不能保证锅炉高效稳定的运行。
(2)仪器继电器控制阶段随着科技的不断进步,自动化技术以及电力电子技术快速提高,国内外以继电器为基础的自动化仪表工业锅炉控制系统也得到发展,并且广泛应用于实际生产过程。
在上个世纪60年代前期,我国锅炉的控制系统开始得到迅速发展;到了60年代的中后期,我国引进了国外全自动的燃油锅炉的控制系统;到了上个世纪的70年代末,我国逐渐自主研发了一些工业锅炉的自动化仪器,同时,在工业锅炉的控制系统方面也在逐步推广应用自动化技术。
在仪表继电器控制阶段,锅炉的热效率得到了提高,并且大幅度的降低了锅炉的事故率。
基于PID控制的火电厂锅炉燃烧控制系统设计和优化
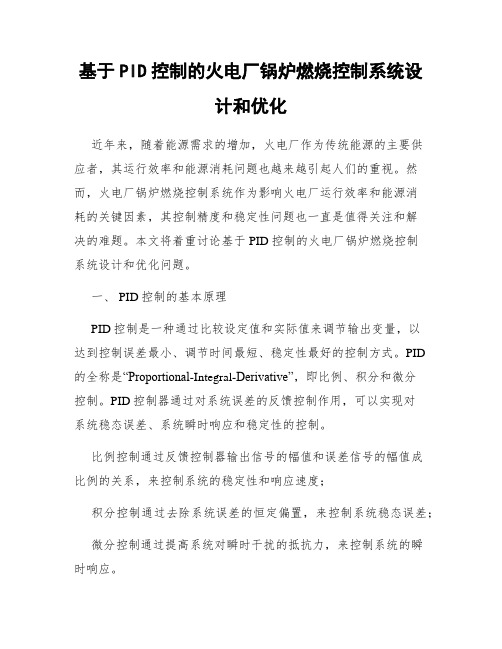
基于PID控制的火电厂锅炉燃烧控制系统设计和优化近年来,随着能源需求的增加,火电厂作为传统能源的主要供应者,其运行效率和能源消耗问题也越来越引起人们的重视。
然而,火电厂锅炉燃烧控制系统作为影响火电厂运行效率和能源消耗的关键因素,其控制精度和稳定性问题也一直是值得关注和解决的难题。
本文将着重讨论基于PID控制的火电厂锅炉燃烧控制系统设计和优化问题。
一、 PID控制的基本原理PID控制是一种通过比较设定值和实际值来调节输出变量,以达到控制误差最小、调节时间最短、稳定性最好的控制方式。
PID的全称是“Proportional-Integral-Derivative”,即比例、积分和微分控制。
PID控制器通过对系统误差的反馈控制作用,可以实现对系统稳态误差、系统瞬时响应和稳定性的控制。
比例控制通过反馈控制器输出信号的幅值和误差信号的幅值成比例的关系,来控制系统的稳定性和响应速度;积分控制通过去除系统误差的恒定偏置,来控制系统稳态误差;微分控制通过提高系统对瞬时干扰的抵抗力,来控制系统的瞬时响应。
PID控制器将上述三种控制模式集成在一个系统中,可以根据具体的参数进行调整。
</p>二、火电厂锅炉燃烧控制系统的基本要求火电厂锅炉燃烧控制系统作为现代火电厂的关键装置,其设计和优化一旦失误,将直接影响火电厂运行的效率和成本。
因此,我们需要对火电厂锅炉燃烧控制系统的基本要求进行了解和掌握:1. 温度控制:火电厂锅炉燃烧控制系统需要实现对锅炉内部温度的控制,以确保锅炉的安全运行和燃烧效率的提高。
2. 水位控制:火电厂锅炉燃烧控制系统需要实现对锅炉内部水位的控制,以确保锅炉的安全运行和燃烧效率的提高。
3. 火焰控制:火电厂锅炉燃烧控制系统需要实现对锅炉内部火焰的控制,以确保锅炉的安全运行和燃烧效率的提高。
以上基本要求也是PID控制在设计和优化火电厂锅炉燃烧控制系统所要考虑的因素。
三、 PID控制在火电厂锅炉燃烧控制系统中的应用针对火电厂锅炉燃烧控制系统的基本要求,PID控制器可以实现如下的应用:1.温度控制:PID控制器可以通过对锅炉内部传感器信号的反馈,实现锅炉内部温度的控制。
基于PLC的锅炉供热控制系统的设计

基于PLC的锅炉供热控制系统的设计一、本文概述随着科技的不断发展,可编程逻辑控制器(PLC)在工业自动化领域的应用日益广泛。
作为一种高效、可靠的工业控制设备,PLC以其强大的编程能力和灵活的扩展性,成为现代工业控制系统的重要组成部分。
本文旨在探讨基于PLC的锅炉供热控制系统的设计,通过对锅炉供热系统的分析,结合PLC控制技术,实现对供热系统的智能化、自动化控制,提高供热效率,降低能耗,为工业生产和居民生活提供稳定、可靠的热源。
文章首先介绍了锅炉供热系统的基本构成和工作原理,分析了传统供热系统存在的问题和不足。
然后,详细阐述了PLC控制系统的基本原理和核心功能,包括输入/输出模块、中央处理单元、编程软件等。
在此基础上,文章提出了基于PLC的锅炉供热控制系统的总体设计方案,包括系统硬件选型、软件编程、系统调试等方面。
通过本文的研究,期望能够实现对锅炉供热控制系统的优化设计,提高供热系统的控制精度和稳定性,降低运行成本,促进节能减排,为工业生产和居民生活提供更加安全、高效的供热服务。
也为相关领域的研究人员和技术人员提供有价值的参考和借鉴。
二、锅炉供热系统基础知识锅炉供热系统是一种广泛应用的热能供应系统,其主要任务是将水或其他介质加热到一定的温度,然后通过管道系统输送到各个用户端,满足各种热需求,如工业生产、居民供暖等。
该系统主要由锅炉本体、燃烧器、热交换器、控制系统和辅助设备等几部分构成。
锅炉本体是供热系统的核心设备,负责将水或其他介质加热到预定温度。
其根据燃料类型可分为燃煤锅炉、燃油锅炉、燃气锅炉、电锅炉等。
锅炉的性能参数主要包括蒸发量、蒸汽压力、蒸汽温度等。
燃烧器是锅炉的重要组成部分,负责燃料的燃烧过程。
燃烧器的性能直接影响到锅炉的热效率和污染物排放。
燃烧器需要稳定、高效、低污染,同时要适应不同的燃料类型和负荷变化。
热交换器是锅炉供热系统中的关键设备,负责将锅炉产生的热能传递给水或其他介质。
热交换器的设计应保证高效、稳定、安全,同时要考虑到热能的充分利用和防止结垢、腐蚀等问题。
锅炉燃烧过程控制系统仿真设计
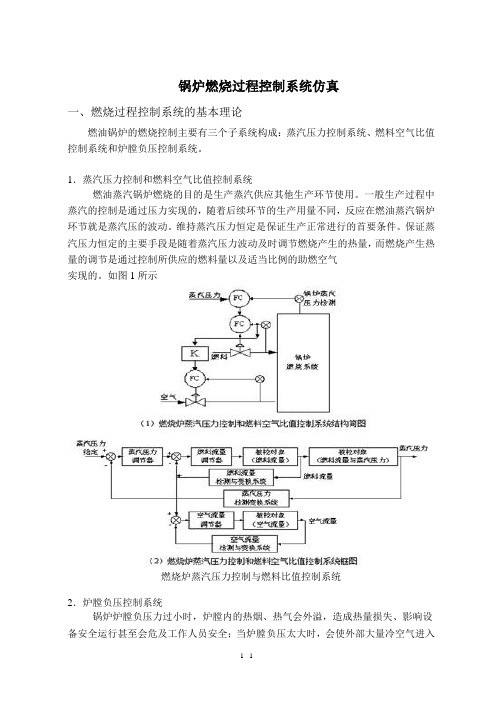
锅炉燃烧过程控制系统仿真一、燃烧过程控制系统的基本理论燃油锅炉的燃烧控制主要有三个子系统构成:蒸汽压力控制系统、燃料空气比值控制系统和炉膛负压控制系统。
1.蒸汽压力控制和燃料空气比值控制系统燃油蒸汽锅炉燃烧的目的是生产蒸汽供应其他生产环节使用。
一般生产过程中蒸汽的控制是通过压力实现的,随着后续环节的生产用量不同,反应在燃油蒸汽锅炉环节就是蒸汽压的波动。
维持蒸汽压力恒定是保证生产正常进行的首要条件。
保证蒸汽压力恒定的主要手段是随着蒸汽压力波动及时调节燃烧产生的热量,而燃烧产生热量的调节是通过控制所供应的燃料量以及适当比例的助燃空气实现的。
如图1所示燃烧炉蒸汽压力控制与燃料比值控制系统2.炉膛负压控制系统锅炉炉膛负压力过小时,炉膛内的热烟、热气会外溢,造成热量损失、影响设备安全运行甚至会危及工作人员安全;当炉膛负压太大时,会使外部大量冷空气进入炉膛,改变燃料和空气比值,增加燃料损失、热量损失和降低热效率。
保证炉膛负压的措施是引风量和送风量的平衡。
如果负压波动不大,调节引风量即可实现负压控制;当蒸汽压力波动较大时,燃料用量和送风量波动也会较大,此时,经常采用的控制方案如图2所示。
炉膛负压控制系统3、控制方案:某锅炉燃烧系统要求对系统进行蒸汽压力控制。
本项目采用燃烧炉蒸汽压力控制和姗料空气比值控制系统,并辅以炉膛负压控制的方案,控制系统框图如图所示。
二、燃烧过程控制任务燃烧过程自动调节系统的选择虽然与燃料的种类和供给系统、燃烧方式以及锅炉与负荷的联接方式都有关系,但是燃烧过程自动调节的任务都是一样的。
归纳起来,燃烧过程调节系统有三大任务。
第一个任务是维持汽压恒定。
汽压的变化表示锅炉蒸汽量和负荷的耗汽量不相适应,必须相应地改变燃料量,以改变锅炉的蒸汽量。
第二个任务是保证燃烧过程的经济性。
当燃料量改变时,必须相应地调节送风量,使它与燃料量相配合,保证燃烧过程有较高的经济性。
第三个任务是调节引风量与送风量相配合,以保证炉膛压力不变。
600MW单元机组锅炉燃烧控制系统设计
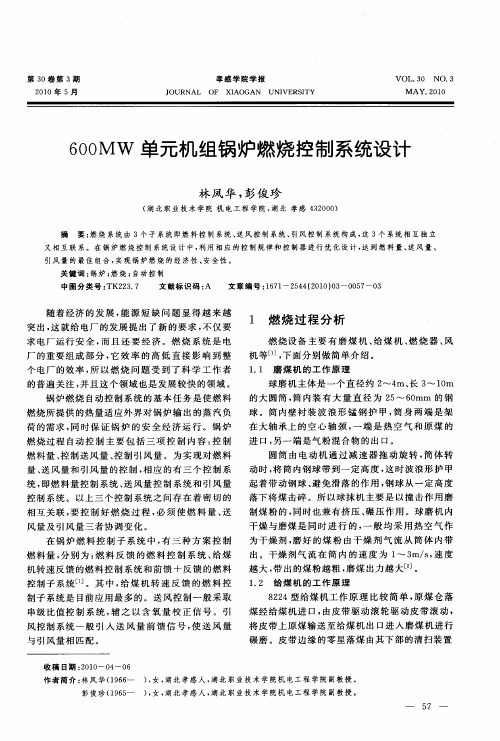
的 。电子称 重式给煤 机给煤量 的称 重原 理是 通过 轮 ,在翼 背上产 生一个 升力 ,同时必 定在翼 腹 上产 负荷传 感 器测 出的单 位 长度 皮 带上 煤 的重 量 G, 生一 个大小相 等 方 向相 反 的作 用 力 ,使 气 体排 出
再 乘 以 由编码 器 测 出 的皮 带 转速 ,就 得 到 了给 叶轮呈 螺旋 形沿 轴 向 向前 运 动 。与此 同时 ,风 机
8224型给煤 机工 作原 理 比较 简单 ,原 煤 仓 落 煤经 给煤 机进 口,由皮带 驱动滚 轮 驱 动皮 带滚 动 , 将皮 带上 原煤输 送 至给煤 机 出 口进 入磨 煤 机进 行 碾磨 。皮 带边缘 的零星落 煤 由其下 部 的清 扫装 置
收 稿 日期 :2010-04—06 作 者 简 介 :林凤 华 (1966一 ),女 ,湖北 孝 感 人 ,湖 北 职 业 技 术 学 院 机 电工 程 学 院 副 教 授 。
1 燃 烧 过 程 分 析
燃 烧设 备 主 要 有 磨 煤 机 、给 煤 机 、燃烧 器 、风 机等n],下 面分别 做简单 介 绍 。 1.1 磨 煤机 的工作 原理
球磨 机主体 是一个 直 径约 2~4m、长 3~ 10m 的大 圆筒 ,筒 内装 有 大量 直 径 为 25 60mm 的钢 球 。筒 内壁衬装 波 浪形 锰 钢 护 甲 ,筒 身 两 端 是 架 在大 轴承 上 的空 心 轴 颈 ,一端 是 热空 气 和 原 煤 的 进 口,另一 端是 气粉混 合 物 的出 口。
第 3O卷 第 3期 2010年 5月
孝 感 学 院 学 报
JOURNA L OF XIAOGAN UNIVERSITY
V 0L.3O N 0 .3 M A Y.2O1O
智能锅炉控制系统的设计与实现

智能锅炉控制系统的设计与实现随着科技的发展和人们生活水平的提高,家居设备的智能化成为了一种趋势。
在众多的智能家居设备中,智能锅炉是一种比较受欢迎的设备。
它可以通过智能控制系统实现远程控制、节能、安全等多种功能。
本文将介绍智能锅炉控制系统的设计与实现。
一、控制系统结构一个智能锅炉控制系统主要由以下部分组成:1.硬件部分:包括传感器、执行器、控制器、显示器等硬件设备。
2.软件部分:主要由控制算法和界面设计组成,控制算法是程序员根据控制需求编写的程序,界面设计则用于方便用户操作和管理。
3.远程通信组件:包括网络通信硬件和软件,实现远程控制和监控等功能。
二、传感器与执行器的选择为了实现智能控制,必须使用传感器来获取锅炉的状态信息,并使用执行器来控制锅炉的运行状态。
在传感器的选择上,应该选择具有高精度、快速响应、耐高温等优点的传感器。
例如,温度传感器应该选用高精度、线性度好、响应速度快、温度范围广的PTC热敏电阻或热电偶传感器。
在执行器的选择上,应该选择具有高精度、稳定可靠性、结构紧凑、响应速度快等优点的执行器。
三、控制器的设计与实现控制器是智能锅炉控制系统的核心,它主要完成控制算法的实现和与硬件设备的通讯。
控制器可以采用嵌入式控制系统、单片机、FPGA等硬件以及VC、VB、C++等软件开发工具进行设计和实现。
在控制方案的设计实现时,要结合锅炉的物理特性和工作状态,运用现代控制理论设计PID算法、模糊控制算法、神经网络控制算法等多种控制算法。
四、界面设计与人机交互一个好的界面设计可以让用户方便快捷地进行操作和管理。
界面设计可以采用电脑、手机APP、微信等多种形态,主要通过图形化的方式将控制参数和系统状态进行直观化显示。
在人机交互方面,可以使用语音、手势等更加便利的交互方式,以提高用户的操作效率和便利性。
五、远程通信组件的设计与实现远程通信组件是实现远程控制的关键,它主要通过网络实现用户对锅炉的远程控制和监控。
热电联产自备电厂设计规范中的锅炉设计要求

热电联产自备电厂设计规范中的锅炉设计要求热电联产自备电厂是指采用燃气或燃油自备发电机组,并利用废热通过余热锅炉或蒸汽轮机发电,实现电力和热能的联产。
在热电联产自备电厂设计规范中,锅炉设计是一个重要的环节。
锅炉设计直接关系到电厂的效率、安全性和环保性。
本文将从锅炉设计要求的角度探讨热电联产自备电厂设计规范中的关键问题。
一、锅炉型式选择在热电联产自备电厂设计中,应根据项目实际情况选择合适的锅炉型式。
常见的锅炉型式包括燃煤锅炉、燃气锅炉、燃油锅炉、余热锅炉等。
应根据燃料种类、发电机组类型、负荷变化等因素进行综合考虑,选择最适合的锅炉型式。
二、锅炉燃烧系统设计在热电联产自备电厂设计中,锅炉燃烧系统的设计是关键。
燃烧系统应确保燃料充分燃烧,烟气温度控制在允许范围内,减少烟气中的污染物排放。
同时,应采取合理的燃烧控制策略,确保系统稳定运行。
三、锅炉传热面设计锅炉传热面的设计是影响锅炉热效率的重要因素。
传热面应具有足够的传热面积,保证热量充分传递给工质,提高锅炉的热效率。
同时,传热面的材质和防腐蚀措施也需要充分考虑,确保锅炉的安全运行。
四、锅炉控制系统设计在热电联产自备电厂设计中,锅炉控制系统设计至关重要。
控制系统应具有良好的响应速度和准确性,确保锅炉在各种工况下安全稳定运行。
同时,应配备完善的安全保护装置,保障设备和人员的安全。
五、排放标准要求为了保护环境,热电联产自备电厂的锅炉应符合国家和地方的排放标准要求。
应采取有效的污染物控制措施,减少大气污染物的排放,保护环境和人民的健康。
六、运行维护要求热电联产自备电厂设计规范中的锅炉设计要求还包括运行维护要求。
应建立健全的运行维护管理制度,加强设备检修和维护工作,延长设备寿命,提高设备可靠性。
总之,在热电联产自备电厂设计规范中,锅炉设计是一个至关重要的环节。
设计人员应根据项目实际情况,选择合适的锅炉型式,设计合理的燃烧系统和传热面,确保锅炉的安全稳定运行,同时要符合环保标准要求,加强运行维护管理,提高设备的可靠性和效率。
基于PLC的锅炉燃烧控制系统的设计-毕业论文

摘要随着社会经济的飞速发展,城市建设规模的不断扩大,以及人们生活水平的不断提高,对城市生活供暖的用户数量和供暖质量提出了原来越高的要求。
结合现状,本论文供暖锅炉监控系统,设计了一套基于PLC和变频调速技术的供暖锅炉控制系统。
该控制系统以一台工业控制机作为上位机,以西门子S7-300可编程控制机为下位机,系统通过变频器控制电机的启动,运行和调速。
上位机监控采用WinCC设计,主要完成系统操作界面设计,实现系统启停控制,参数设定,报警联动,历史数据查询等功能。
下位机控制程序采用西门子公司的STEP7编程软件设计,主要完成模拟量信号的处理,温度和压力信号的PID控制等功能,并接受上位机的控制指令以完成风机启停控制,参数设定,循环泵的控制和其余电动机的控制。
本文设计的变频控制系统实现了锅炉燃烧过程的自动控制,系统运行稳定可靠。
采用锅炉的计算机控制和变频控制不仅可大大节约能源,促进环保,而且可以提高生产自动化水平,具有显著的经济效益和社会效益。
关键字:锅炉控制;变频调速;组态软件;PLCAbstractAlong with social economy’s swift development, the urban construction scale’s unceasing expansion , as well as the peple living standard’s unceasing enhancement , set more and more high request to the city life heating’s user quantity and the heating quality. The union present situation, the present paper heating boiler supervisory sysem, has designed a set based on PLC and the frequency conversion velocity modulation technology heating boiler control system.This control system takes the superior machine by one Industry cybertrons , west of family household S7-300 programmable controller for lower position machine ,system through frequency changer control motor’s start , movement and vclocity modulation .the superior machine monitoring software uses the three dimensional strength to control the WinCC design , mainly completes the system operation contract surface design ,realizes the system to open/stops functions and so on control ,parameter hypothesis ,warning linkage,historical data inquiry. The lower position machine control procedure uses Siemen’s STEP7 programming software design , mainly completes the simulation quantity signal processing , temperature and pressure signal functions and so on PID control , and receives the superior machine control command to complete the air blower to open/stops the control , the parameter hypothesis, the circulating pump control and other electric motor’s control.This article designs the frequency conversion processs automatic control, the systems operation is stable, is reliable. Uses boiler’s computer control and the frequency converseon control noe only may save the energy greatly, the promotion environmental protection moreover may raise the production automation level, has the remarkable economic efficiency and the social efficiency.Key Words:Boiler control;Frequency conversion velocity modulation ;Configuration Software;PLC目录摘要 0Abstract (1)第1章概述 (4)1.1 项目背景及课题的研究意义 (4)1.2 供暖锅炉控制的国内外研究现状 (5)1.3锅炉控制系统的发展趋势 (6)1.4本文所做工作 (7)第2章系统方案设计 (9)2.1锅炉控制研究简介 (9)2.2 总体设计思路 (9)2.3方案比较 (10)2.3.1方案1 (10)2.3.2 方案2 (10)2.4方案论证与方案确定 (11)第3章硬件设计 (12)3.1 用户系统框图 (12)3.2 锅炉系统的理论分析 (13)3.2.1变频调速基本原理 (13)3.2.2变频调速在供暖锅炉中的应用 (13)3.2.3变频调速节能分析 (14)3.3燃烧过程控制 (19)3.4锅炉控制系统设计 (20)3.5控制系统构成介绍 (21)第4章软件设计 (25)4.1 S7-300系列PLC简介 (26)4.2 PLC编程语言简介 (28)4.2.1 PLC编程语言的国际标准 (28)4.2.2复合数据类型与参数类型 (29)4.2.3系统存储器 (29)4.2.4 S7-300 CPU中的寄存器 (30)4.3 STEP7 的原理 (31)4.3.1 STEP7概述 (31)4.3.2 硬件组态与参数设置 (32)4.3.3 符号表 (36)4.3.4 逻辑块 (37)4.3程序设计 (38)4.4通信系统 (41)4.5人机界面 (43)4.5.1监控软件WinCC介绍 (43)4.5.2监控系统设计 (45)4.5.3锅炉监控界面设计 (49)第5章结论 (53)5.1 成果的创造性和先进性 (53)5.2作用意义(经济效益和社会意义) (53)5.3 推广应用范围和前景 (53)5.4 需要进一步改进之处 (54)参考文献 (55)外文资料翻译 (56)外文翻译原文 (56)外文翻译译文 (68)致谢 (75)附录 (76)附录1 程序清单 (76)附录2 I/O点数分配表 (96)附录3 物理参数比较表 (97)第1章概述1.1 项目背景及课题的研究意义工业锅炉是工业生产和集中供热过程中重要的动力设备。
基于PLC的锅炉控制系统的设计

基于PLC的锅炉控制系统的设计本文介绍基于PLC的锅炉控制系统的设计的背景和目的。
锅炉控制系统是基于PLC(可编程逻辑控制器)的设计,采用了分布式控制策略。
整体架构包括以下几个组成部分:1.控制器控制器是锅炉控制系统的核心部分,由PLC实现。
PLC具备高速计算能力和强大的输入输出功能,可以对各个设备进行监控和控制。
它接收来自传感器的输入信号,并根据预设的逻辑和算法进行实时处理,向执行器发送输出信号以控制设备运行。
2.传感器传感器负责将锅炉系统的各个参数转化为电信号,并传输给PLC进行处理。
常见的传感器包括温度传感器、压力传感器、流量传感器等。
3.执行器执行器根据PLC的控制信号来执行相应的操作,如调节燃料供给、控制排放阀等。
它们与PLC之间通过信号线或总线进行连接。
4.人机界面人机界面提供给操作员与锅炉控制系统进行交互的界面。
它可以是触摸屏、计算机软件等形式,用于监视系统运行状态、设定参数以及显示报警信息等。
5.通信模块通信模块用于实现锅炉控制系统与外部设备的数据传输和通信。
它可以连接到局域网或远程服务器,实现与其他系统或监控中心的数据交互。
6.电源供应为了保证锅炉控制系统的稳定运行,需要提供可靠的电源供应。
这可以通过备用电源或UPS(不间断电源)来实现。
综上所述,基于PLC的锅炉控制系统采用分布式控制策略,通过控制器、传感器、执行器、人机界面、通信模块和电源供应等组成部分协同工作,实现对锅炉设备的监控和控制。
本文介绍基于PLC的锅炉控制系统所采用的控制策略和算法。
控制策略是指通过采取不同的控制方法和算法,在锅炉运行中实现温度、压力、流量等参数的稳定控制。
基于PLC的锅炉控制系统采用了以下主要的控制策略:PID控制:PID(比例、积分、微分)控制是一种常用的控制方法。
它通过根据控制对象的偏差来调节控制器的输出,使得偏差逐渐趋向于零,从而实现控制目标。
在锅炉控制系统中,PID控制常用于调节温度、压力和流量等参数。
燃油蒸汽锅炉的燃烧控制系统的设计和仿真
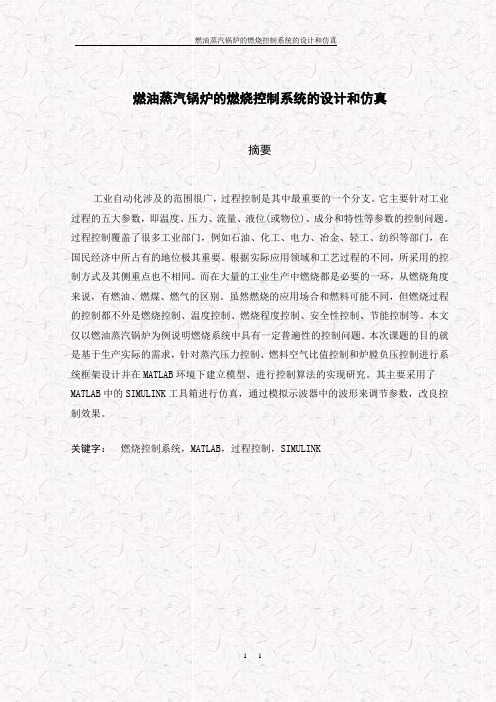
燃油蒸汽锅炉的燃烧控制系统的设计和仿真摘要工业自动化涉及的范围很广,过程控制是其中最重要的一个分支。
它主要针对工业过程的五大参数,即温度、压力、流量、液位(或物位)、成分和特性等参数的控制问题。
过程控制覆盖了很多工业部门,例如石油、化工、电力、冶金、轻工、纺织等部门,在国民经济中所占有的地位极其重要。
根据实际应用领域和工艺过程的不同,所采用的控制方式及其侧重点也不相同。
而在大量的工业生产中燃烧都是必要的一环,从燃烧角度来说,有燃油、燃煤、燃气的区别。
虽然燃烧的应用场合和燃料可能不同,但燃烧过程的控制都不外是燃烧控制、温度控制、燃烧程度控制、安全性控制、节能控制等。
本文仅以燃油蒸汽锅炉为例说明燃烧系统中具有一定普遍性的控制问题。
本次课题的目的就是基于生产实际的需求,针对蒸汽压力控制、燃料空气比值控制和炉膛负压控制进行系统框架设计并在MATLAB环境下建立模型、进行控制算法的实现研究。
其主要采用了MATLAB中的SIMULINK工具箱进行仿真,通过模拟示波器中的波形来调节参数,改良控制效果。
关键字:燃烧控制系统,MATLAB,过程控制,SIMULINKTHE DESIGN AND SIMULATION OF THE COMBUSTION CONTROL SYSTEM BASED ON FUEL STEAM BOILERABSTRACTIndustrial automation involve a very wide range, while process control is one of the most important branches. It mainly refer to control techniques of five industrial processes parameters which are temperature, pressure, and flow, liquid level (or bits), composition and characteristics. Process control covers many industries, such as petroleum, chemical industry, electric power, metallurgy, light industry and textile department.It occupied an extremely important position of the national economy.The control modes and their emphasis depend on the different actual application and process bustion is essential in the industrial production.Burning speaking, it can be divide into fuel, coal and gas. Although burning applications and fuel combustion process may be different, the control of burning process all involve burning control, temperature control and burning level control, safety control, degree of saving energy control etc. This paper only to take fuel steam boiler combustion system as an example,it illustrates the control problems with certain universality in the combustion system. The purpose of this subject is to design the system framework for steam pressure control, fuel air ratio control and hearth negative pressure based on the actual production needs, also make model in the MATLAB environment as well as research for the algorithm of control . It mainly uses the MATLAB and SIMULINK toolbox, adjusting the parameters in terms of the waveform of oscilloscope.As a result, the control effect improved.Key words:,combustion control system,MATLAB, process control, SIMULINK目录摘要 (I)ABSTRACT (II)前言 (1)1绪论-------------------------------------------------------------------------------------------------61.1 研究目的及意义-------------------------------------------------------------------------------------------61.2相关领域的研究现状--------------------------------------------------------------------------------------61.2.1燃油蒸汽锅炉发展和现状-----------------------------------------------------------------61.2.2燃烧控制系统的简介--------------------------------------------------------------------------------81.3 论文的章节安排2 燃油蒸汽锅炉燃烧控制系统控制原理---------------------------------------------------------62.1 系统基本结构与设备--------------------------------------------------------------------------------------62.2 主要控制技术及要求-----------------------------------------------------------------------------102.2.1稳定蒸汽母管的压力-------------------------------------------------------------------------------122.2.2维持锅炉燃烧的最佳状态和经济性-------------------------------------------------------------122.2.3维持炉膛负压在一定范围------------------------------------------------------------------------ 122.2.4锅炉燃烧系统控制对象的特性-------------------------------------------------------------------123 蒸汽压力控制、燃料空气比值控制和炉膛负压控制的基本模型建立-------------------143.1蒸汽压力控制系统和燃料空气比值控制系统基本模型--------------------------------------------143.2炉膛负压控制系统----------------------------------------------------------------------------------------154 MATLAB环境下控制算法的研究---------------------------------------------------------------184.1系统辨识---------------------------------------------------------------------------------------------------184.2控制系统参数整定---------------------------------------------------------------------------------------184.3控制系统SIMULINK仿真-----------------------------------------------------------------------------245 结论-------------------------------------------------------------------------------------------------28 参考文献-------------------------------------------------------------------------------------------------28 致谢-------------------------------------------------------------------------------------------------------29附录-------------------------------------------------------------------------------------------------------46 译文及原文----------------------------------------------------------------------------------------------501 绪论1.1 引言锅炉是重要的工业设备,应用于炼油、冶金、化工、轻工等行业。
锅炉燃烧过程控制系统

乘法器为燃料调节对象的一部分,选择合适的函数f(x),则可以做到不管给煤 机投入的台数如何,都可以保持燃料调节对象增益不变,这样就不必调整燃 料调节器的控制参数了。增益调整与平衡器(GAIN CHANGER & BALANCER),就是完成该功能。
三、风煤交叉限制
为了在机组增、减负荷动态过程中,使燃料得到充分燃烧就要保证有足够的风 量。需要保持一定的过量空气系数,因此,在机组增负荷时,就要求先加风 后加煤;在机组减负荷时,就要求先减煤后减风。这样就存在一个风煤交叉
~ 发电机
Pem
3UI
cos
3
EqU Xd
sin
2.汽机跟随控制方式
锅炉控制 系统
燃烧率μB
锅炉
BD
汽轮机 主控器
TD 汽轮机控制 系统
锅炉 主控器
- p0
+ pT
μT 调节阀
汽轮机
图2 汽机跟随控制方式
+
P0
— —
PE
~ 发电机
3.机炉协调控制方式
BD
锅炉控制 系统
燃烧率μB
锅炉
锅炉主控器
锅炉燃烧过程控制系统
第一节 概述
一、单元机组的基本控制方式
(1)锅炉跟随控制方式 (2)汽机跟随控制方式 (3)机炉协调控制方式
1.锅炉跟随控制方式
BD
锅炉控制 系统
锅炉 主控器
燃烧率μB
锅炉
+ p0 —
pT
TD
汽轮机控制 系统
μT 调节阀
汽轮机 主控器
汽轮 机
图1 锅炉跟随控制方式
+ P0
— PE
GV
(s)
KV (Ts 1)2
锅炉燃烧系统的控制系统设计

3)汽轮发电机组接受锅炉提供的过热蒸汽,推动高压汽轮机转子,进而带动发电机转子转动,产生电能。同时,温度和压力都降低的蒸汽冷凝为凝结水,又被作为给水进入锅炉汽水系统,从而加以循环利用,节约资源。
1.2 单元机组的出力控制
对电网来说,要求单元机组的出力能快速适应负荷的需求,而机组的出力大小事由锅炉和汽轮机共同决定的。两者在适应负荷变化的能力上有很大的差别:锅炉从给水到形成过热蒸汽式一个惯性较大的热交换过程,而汽轮机从蒸汽进入到产生电能是一个反应相对较快的环节。如何合理地控制锅炉和汽轮机的各自出力[3],使其彼此适应,最终满足负荷需求是出力控制的核心任务。
图1-1火力发电厂主要工艺流程图
1.1锅炉控制
锅炉是化工、炼油、发电等工业生产过程中必不可少的重要动力设备。锅炉控制的目的是供给合格的蒸汽,使锅炉产汽量适应负荷需要,同时保证燃烧的经济性、安全性[2]。要实现该控制目的,必须对锅炉生产过程中的各个主要工艺参数进行严格控制。
负
荷
给水量 锅筒水位
减温水量 过热蒸汽温度
理论和实践已证明,烟气中的各种成分,如O2、CO2、CO和未燃烧烃的含量,基本上可以反映燃料燃烧的情况,最简便的方法是用烟气中的含氧量A来表示。根据燃烧时的化学反应方程式,可以计算出使燃料完全燃烧所需要的含氧量,进而可以折算出所需的空气量,称为理想空气量,用QT表示。但实际上完全燃烧时所需的空气量QP,要超过理论计算的QT,既要有一定的过剩空气量。由于烟气的热损失占锅炉热损失的绝大部分,当过剩空气量增多时,会使炉膛温度降低,同时使烟气热损失增加。因此,过剩空气量对不同的燃料都有一个最优值,以达到最优经济燃烧。
(完整版)锅炉燃烧系统的控制系统设计

(完整版)锅炉燃烧系统的控制系统设计⽬录1锅炉⼯艺简介 (1)1.1锅炉的基本结构 (1)1.2⼯艺流程 (2)1.2煤粉制备常⽤系统 (3)2 锅炉燃烧控制 (4)2.1燃烧控制系统简介 (4)2.2燃料控制 (4)2.2.1燃料燃烧的调整 (4)2.2.2燃烧调节的⽬的 (5)2.2.3直吹式制粉系统锅炉的燃料量的调节 (5)2.2.4影响炉内燃烧的因素 (6)2.3锅炉燃烧的控制要求 (11)2.3.1 锅炉汽压的调整 (11)3锅炉燃烧控制系统设计 (14)3.1锅炉燃烧系统蒸汽压⼒控制 (14)3.1.1该⽅案采⽤串级控制来完成对锅炉蒸汽压⼒的控制 (14)3.2燃烧过程中烟⽓氧含量闭环控制 (17)3.2.1 锅炉的热效率 (18)3.2.2反作⽤及控制阀的开闭形式选择 (20)3.2.3 控制系统参数整定 (20)3.3炉膛的负压控制与有关安全保护保护系统 (21)3.3.1炉膛负压控制系统 (22)3.3.2防⽌回⽕的连锁控制系统 (23)3.3.3防⽌脱⽕的选择控制系统 (24)3.4控制系统单元元件的选择(选型) (24)3.4.1蒸汽压⼒变送器选择 (24)3.4.2 燃料流量变送器的选⽤ (24)4 DCS控制系统控制锅炉燃烧 (26)4.1DCS集散控制系统 (26)4.2基本构成 (27)锅炉燃烧系统的控制4.3锅炉⾃动燃烧控制系统 (31)总结 (33)致谢 (34)参考⽂献 (35)1锅炉⼯艺简介1.1锅炉的基本结构锅炉整体的结构包括锅炉本体和辅助设备两⼤部分。
1、锅炉本体锅炉中的炉膛、锅筒、燃烧器、⽔冷壁、过热器、省煤器、空⽓预热器、构架和炉墙等主要部件构成⽣产蒸汽的核⼼部分,称为锅炉本体。
锅炉本体中两个最主要的部件是炉膛和锅筒。
炉膛⼜称燃烧室,是供燃料燃烧的空间。
将固体燃料放在炉排上进⾏⽕床燃烧的炉膛称为层燃炉,⼜称⽕床炉;将液体、⽓体或磨成粉状的固体燃料喷⼊⽕室燃烧的炉膛称为室燃炉,⼜称⽕室炉;空⽓将煤粒托起使其呈沸腾状态燃烧、适于燃烧劣质燃料的炉膛称为沸腾炉,⼜称流化床炉;利⽤空⽓流使煤粒⾼速旋转并强烈⽕烧的圆筒形炉膛称为旋风炉。
燃气锅炉燃烧控制系统设计与优化

燃气锅炉燃烧控制系统设计与优化一、燃气锅炉燃烧控制系统的重要性燃气锅炉是一种非常重要的热能设备,它主要通过燃烧天然气或液化气来提供供暖和热水等热能。
而燃烧是燃气锅炉运行的核心环节,燃烧效率的高低直接影响到锅炉的能源利用效率、经济性以及环保性。
因此,在燃气锅炉的设计中,燃烧控制系统至关重要。
一般来说,燃烧控制系统包括点火系统、燃气调节系统、燃烧控制系统、排烟系统以及火焰监测系统等多个部件。
这些部件共同协作,通过自动化控制实现燃烧的精确、稳定、高效的控制,为燃气锅炉提供可靠的技术支持。
二、燃气锅炉燃烧控制系统的设计(一)燃气调节系统燃气调节系统主要通过减压阀、调压阀等部件,实现对燃气的调控、减压、稳压等操作。
在设计中,需要充分考虑天然气的控制范围、加热功率等因素,以保证系统的稳定性和可靠性。
(二)点火系统点火系统主要包括点火电极、火焰检测器等部件。
点火电极采用电弧点火的方式,需保证点火高压电源的正常使用。
火焰检测器通过监测燃烧过程中的火焰信号,保障燃烧安全。
(三)燃烧控制系统燃烧控制系统是整个燃烧控制系统的核心环节,它通过对燃气、空气的比例、流量进行调节,控制燃烧过程中的温度、压力等参数。
在设计中需要根据锅炉的功率、热效率和应用要求,合理选择燃烧控制器、比例阀、执行器等部件。
(四)排烟系统排烟系统通过对燃烧产生的烟气进行处理和净化,保证其排放符合环保标准。
在设计中需要考虑锅炉排放的烟气含量、排放的方式等因素,选用合适的净化设备。
(五)火焰监测器火焰监测器用于监测锅炉内火焰状态,及时预警燃烧故障,保障燃烧安全。
设计中需要考虑其稳定性、可靠性、精度等因素,保证监测结果的准确性和及时性。
三、燃气锅炉燃烧控制系统的优化(一)优化燃烧控制燃烧控制是燃气锅炉燃烧效率的重要影响因素,因此需要通过合理的控制方式,实现燃烧的高效率、低耗能和低排放。
其中,流量控制方式可以在燃烧过程中实现燃料和空气的匹配,提高燃烧效率;焓控制方式则通过对水的温度、压力等参数进行调节,保证热能的正常传递。
锅炉燃烧控制系统的优化设计
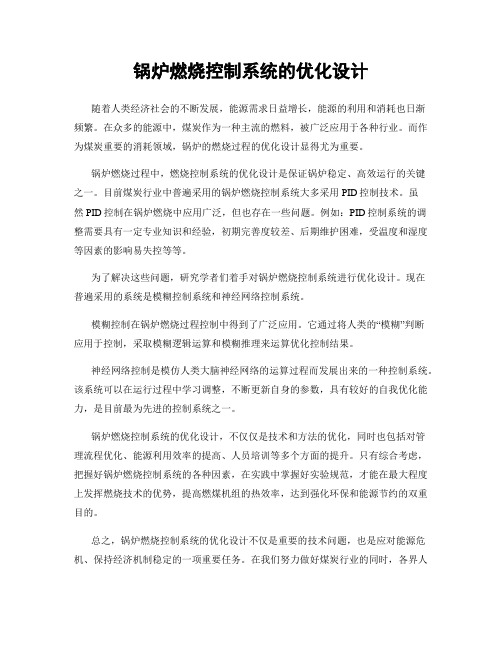
锅炉燃烧控制系统的优化设计随着人类经济社会的不断发展,能源需求日益增长,能源的利用和消耗也日渐频繁。
在众多的能源中,煤炭作为一种主流的燃料,被广泛应用于各种行业。
而作为煤炭重要的消耗领域,锅炉的燃烧过程的优化设计显得尤为重要。
锅炉燃烧过程中,燃烧控制系统的优化设计是保证锅炉稳定、高效运行的关键之一。
目前煤炭行业中普遍采用的锅炉燃烧控制系统大多采用PID控制技术。
虽然PID控制在锅炉燃烧中应用广泛,但也存在一些问题。
例如:PID控制系统的调整需要具有一定专业知识和经验,初期完善度较差、后期维护困难,受温度和湿度等因素的影响易失控等等。
为了解决这些问题,研究学者们着手对锅炉燃烧控制系统进行优化设计。
现在普遍采用的系统是模糊控制系统和神经网络控制系统。
模糊控制在锅炉燃烧过程控制中得到了广泛应用。
它通过将人类的“模糊”判断应用于控制,采取模糊逻辑运算和模糊推理来运算优化控制结果。
神经网络控制是模仿人类大脑神经网络的运算过程而发展出来的一种控制系统。
该系统可以在运行过程中学习调整,不断更新自身的参数,具有较好的自我优化能力,是目前最为先进的控制系统之一。
锅炉燃烧控制系统的优化设计,不仅仅是技术和方法的优化,同时也包括对管理流程优化、能源利用效率的提高、人员培训等多个方面的提升。
只有综合考虑,把握好锅炉燃烧控制系统的各种因素,在实践中掌握好实验规范,才能在最大程度上发挥燃烧技术的优势,提高燃煤机组的热效率,达到强化环保和能源节约的双重目的。
总之,锅炉燃烧控制系统的优化设计不仅是重要的技术问题,也是应对能源危机、保持经济机制稳定的一项重要任务。
在我们努力做好煤炭行业的同时,各界人士也需要共同努力,协力推进煤炭行业的能源优化、安全生产和环境保护事业,在创造更多人类福祉的同时最大限度地提高可持续发展的利润率。
- 1、下载文档前请自行甄别文档内容的完整性,平台不提供额外的编辑、内容补充、找答案等附加服务。
- 2、"仅部分预览"的文档,不可在线预览部分如存在完整性等问题,可反馈申请退款(可完整预览的文档不适用该条件!)。
- 3、如文档侵犯您的权益,请联系客服反馈,我们会尽快为您处理(人工客服工作时间:9:00-18:30)。
摘要锅炉燃烧控制系统最重要的任务是保持锅炉蒸汽压力稳定。
当负载量改变,使蒸汽压力的变化,通过调节燃料量(或送风量),从而改变炉膛发热量,最终使蒸汽压力稳定。
其次,我们应该保证燃料的经济燃烧,既不能因为空气不足而冒黑烟,也不能因为空气过多而导致热量损失增加。
所以燃料量和空气量应保持一定的比例,或者说烟气中的氧气浓度应保持在一定的值。
最后,鼓风量还要和引风量要相配合,以保持恒定的炉腾负压。
如果负压太小,炉烟气外冒会影响设备和操作员工的安全;如果负压过大,使大量冷空气漏入炉中,导致热损失增加,降低了燃烧效率。
关键字:燃烧控制串级控制炉膛负压联机控制一、工业锅炉的工作过程1.1锅炉简介锅炉结构如图所示,主要包括炉膛、汽包、省煤器、炉排以及给水粟、鼓风机、引风机、炉排电机等重要设备。
煤炭通过斜皮带机和平皮带机送至炉排,然后在炉膛内燃烧,最后随排澄电机排出。
炉腊内的烟气则通过省煤器交换热量以较低温状态被引风机排出。
而给水粟则将储水库里的水先经过省煤器送至汽包,其给水量可通过给水调节阀控制。
汽包内的蒸汽通过蒸汽管向外输送以供使用。
锅炉系统主要输入变量是给水量、送风量、给煤量、引风量、蒸汽负荷等,主要输出变量是蒸汽压力、汽包水位、烟气含氧量和炉膛负压、蒸汽流量等。
所以锅炉系统是一个多输入,多输出且相互关联的复杂的控制对象。
系统的输入变量其实就是我们控制方法的控制量,根据控制量的不同可将锅炉系统划分为若干个子控制系统:给煤系统、送风系统、引风系统和汽包水位系统。
当然他们都有自己主要的调节对象,分别为:蒸汽压力、烟气含氧量、炉腊负压、汽包水位。
锅炉控制系统的控制指标为:蒸汽压力在期望压力的±1%,空气燃烧比应该保证±0.4%的过量氧气,汽包水位应控制在±5cni。
其中给煤系统、送风系统、引风系统之间又有紧密的关系,三者共同组成了锅炉燃烧控制系统。
1.2为锅炉结构和工艺流程示意图燃烧的煤层厚度通过闸板控制,炉排转速可由交流变频调速电机控制。
尾部受热面有省煤器和空气预热器。
锅炉结构和工艺流程示意图给水通过省煤器预热后给锅炉上水,空气经空气预热器后由炉排左右两侧6个风道进入,烟气通过除尘器除尘,由引风机送至烟囱排放,主蒸汽经过过热器送至汽柜和用汽部门。
鼓风机、引风机都是由交流变频器来控制,通过调节鼓风机、引风机的速度来实现控制鼓风量、引风量。
二、锅炉燃烧的控制要求2.1锅炉燃烧过程的任务、被控变量和操纵变量控制系统被控变量操纵变量控制目的锅炉燃烧控制系统蒸汽出口压力烟气成分炉膛负压燃料流量送风流量引风流量蒸汽负荷平衡燃烧的完全和经济性锅炉运行的安全性锅炉燃烧控制系统的基本任务是使燃料燃烧所产生的热量适应蒸汽负荷要求,同时保证锅炉的经济、安全运行。
为适应蒸汽负荷的变化,应及时调节燃料量。
为完全燃烧,应控制燃烧量与空气的比值,使过剩的空气系数满足要求,为防止燃烧过程中火焰或烟气外喷,应控制炉膛的负压。
这三项控制任务互相影响。
另外,从安全角度考虑,需设置安全控制系统即设置防止回火的联锁控制系统和防脱火的联锁控制系统。
三、燃烧控制基本控制方案锅炉的燃烧控制对于锅炉的安全、高效运行和节能降耗都具有重要意义,其控制和管理随之要求也越来越高。
燃料控制的任务在于进入锅炉的燃料量随时与蒸汽压力要求相适应。
因为蒸汽压力是衡量锅炉热量平衡的标志,燃料又是影响蒸汽压力的主要因素,因此蒸汽压力可以作为燃料控制系统的被调量。
锅炉蒸汽压力是燃烧过程调节对象的主要被控量,引起蒸汽压力变化的因素有很多,如燃料量、送风量、给水量、蒸汽流量以及各种使燃烧工况发生变化的原因。
它受到的主要扰动分为内扰(燃料的变化)和外扰(蒸汽流量的改变)。
由于每个系统的输入输出之间都一定的系统延迟,即当输入变化的时候系统输出不能够马上反应其变化从而是系统的控制不及时。
3.1基本控制方案一:3.1.1串级控制控制系统描述:(1)蒸汽压力为主被控变量,燃料量为副被控变量组成的串级控制系统。
(2)燃料量为主动量,空气量为从动量的比值控制系统。
特点:(1)确保燃料量与空气量的比值关系,当燃料量变化时,空气量能够跟踪燃料量变化。
(2)送风量的变化滞后于燃料量的变化。
以蒸汽压力为被调节量,以燃料量为调节量的串级控制系统设计如图所示。
蒸汽出口压力控制方框系统控制方案:燃料阀空气阀蒸汽出口压力控制系统3.1.2控制器正反作用及控制阀的气关气开形式选择:1)主控制器:选择反作用,因为当阀的开度增大后,燃料的流量增加,阀的开度为(+),变送器为(+),所以控制器也为(+)所以控制器选择反作用2)副控制器:选择反作用,因为当阀的开度增大后,蒸汽的温度升高压力增大,阀的开度为(+),变送器为(+),所以控制器也为+所以控制器选择反作3)控制阀:气开型因为当锅炉出现事故时阀门一定得是关闭的,否则的话在事故出现后阀门是开的话使燃料流出。
会加重事故。
3.2基本控制方案二:3.2.1燃烧过程中烟气氧含量闭环控制然烧过程控制保证燃料和空气的比值关系,并不保证燃料的完全燃烧。
燃料的完全燃烧与燃料的质量(含水量、灰粉等)、热值等因素有关。
不同的锅炉负荷下,燃料量和空气量的最佳比值会不同。
因此,需要有一个检查燃料完全燃烧的控制指标,并根据该指标控制送风量的大小。
衡量燃烧过程是否完全燃烧的常用控制指标是烟气中的含氧量。
它在上述的方案中基础上,加入了烟道气中氧含量的控制回路。
这是一个以烟道气中氧含量为控制目标的燃料流量与空气流量的变比值控制系统,也称烟气氧含量的闭环控制系统。
此方案可以保证锅炉的最经济燃烧。
前述方案一,虽然也考虑了燃料与空气流量的比值控制,但它不能在整个生产过程中始终保证最经济燃烧。
因为,其一:在不同的负荷下,两流量的最优比值是不同的;其二:燃料的成分有可能会变化;其三:流量的不准确。
这些因素都会不同程度的影响到燃料的不完全燃烧或空气的过量,造成炉子热效率下降。
这就是燃料流量定比值控制系统的缺点。
为了改善这一情况,最好有一指标来闭环修正两流量的比值。
因此,常用烟气中含氧量作为检查燃料完全燃烧的控制指标,并根据该指标控制送风量。
3.2.2 锅炉的热效率锅炉的热效率主要反映在烟气成分(主要是含氧量)和烟气温度上。
烟气中各种成分例如:氧气、二氧化碳、一氧化碳和未燃烧烃含量基本可反映燃料的燃烧情况。
常用的含氧量用表示。
理论空气量是根据燃烧反应方程式,计算出的完全燃烧时所需的空气量。
实际空气量是实际燃烧过程的中所需的空气量,。
超过理论空气量的这部分空气量称为过剩空气量。
过剩空气量增大,炉膛温度降低越多,烟气中带走的热损失也越大。
不同的空气量有最佳值(对于液体,过剩空气量约为8%~15%),如下图:不完全燃烧的损失总能量损失最高效率区-20 过剩空气量%过剩空气量与能量损失的关系常用过剩空气系数a 表示过剩空气量,定义为:a=过剩空气系数很难直接测量,它与烟气中氧量有关。
a=21/21-Ao8 6 42 010 20 30 40 过剩空气量%过剩空气量与烟气含氧量、锅炉效率的关系上图显示了过剩空气系数a 与烟气含氧量、锅炉效率的关系。
当a 在1~过滤效率过氧量1、6范围内时,过剩空气系数a 与烟气接近直线。
当a 在1、08~1、15(最佳过剩空气量8%~15%)时,烟气含氧量最优值为1、6%~3%。
从上图也可看到,约在过剩空气量为15%~18%时,锅炉有最高效率。
因此,用烟气含氧量作为锅炉燃烧的经济指标。
以烟气为被调节量,以燃料量为调节量的串级控制系统设计如图所示。
烟气含氧量控制系统与锅炉燃烧控制系统一起实现锅炉的经济燃烧闭环控制系统如下图:烟气含氧量闭环控制系统,该系统是在原逻辑提量和减量控制系统的基础上将原来的定比值改为变比值控制,变比值器的比值由含氧控制器AC 输出。
当烟气中的含氧量变化时,表明燃烧过程中过剩空气发生变化,因此通过AC 及时调节燃料和空气的比值,使燃烧过程达到经济的目的。
实施时应注意,快速反映烟气含氧量,对烟气含氧量的检测变送系统应选择正确。
目前,常选用氧化锆氧量仪表检测烟气中的含氧量。
空气调节器燃料控制器控制 阀副对 象主对 象送燃料量变送器烟气含氧量变送器输出量比值器送空气量变送器输入量烟气含氧的闭环控制系统方框图控制方案:燃料量蒸汽压力空气量烟气含氧量燃料阀空气阀烟气含氧的闭环控制系统3.2.3控制器正反作用及控制阀的气关气开形式选择:1)主控制器:选择反作用,因为当烟气的含氧量增大后,空气量应减小,阀的开度为(+),变送器为(+),所以控制器也为(+)所以控制器选择反作用。
2)副控制器:选择正作用,因为当阀的开度增大后,燃料流量增大,阀的开度为(+),变送器为(+),所以控制器也为(+)所以控制器选择正作。
3)控制阀:气开型因为当锅炉出现事故时阀门一定得是关闭的,否则的话在事故出现后阀门是开的话使燃料流出。
会加重事故。
3.3.1上述两方案的有缺点通过对上述两种方案的详细说明,从中可以看出各种方案都有其优、缺点:方案一: 主要优点:燃料流量是随蒸汽负荷而变化的,这样可保持蒸汽出口压力的稳定,又可以保持蒸汽出口压力的稳定,又可使燃空比维持一定,系统控制简单,使用仪表少。
主要缺点:燃料燃烧不能完全燃烧,当燃料或空气回路各自出现干扰时,不能严格保持动态的燃料与空气比的不变。
方案二: 主要优点:可以保证锅炉燃烧过程的空气与燃料比值最优燃烧比,防止由于流量测量的误差以及燃料的质量的变化。
另外,锅炉负荷不同时,可以保持两者的最优比有一定的不同。
主要缺点:虽然可以做到保证燃烧时刻处于最经济状态,但是其控制系统、 检测设备相对来说都比较复杂,其中氧含量检测设备以目前的技术来说还不能保证检测结果十分精确,其总体控制效果不能达到理论上的水平系统控制较复杂,仪表多,容易出问题,而且仪表仪器价格昂贵。
3.4.1、控制系统参数整定控制系统中滞后产生的主要原因有:对系统变量的测量、系统中设备的物理性质及物或信号的传递等。
在实际工程控制问题中,有时因滞后系统的影响不大而在系统的设计或模型中将滞后省略。
但是在更多的实际工程中,滞后是不能省略的,而且有些控制过程中,滞后往往是时变的,即滞后是时间t 的函数。
所以这些对象的纯滞后时间对控制系统的控制性能都极为不利,它使系统的稳定性降低,动态特性变坏。
由于整个控制系统存在滞后,整个系统具有一阶环节和二阶环节来近似的等效一阶滞后环节τs e Ts K s G -+=1)( 二阶滞后环节 τs e s T s T Ks G -++=)1)(1()(21在现场环境中,参数变化是时时刻刻的,很难用一个固定的数学公式将炉温的变化规律总结出来。
所以在规定的要求范围内,对一些情况进行近似处理是很合理和必要的。