物料搬运案例PPT
合集下载
物料搬运系统设计全解ppt课件

物料搬运方程
WHY 为何搬运
WHAT
WHERE
WHEN
搬运什么 + 何地 + 何时
HOW
WHO
怎么做 + 何人做
否定
物料
+
搬运
分析物料搬运问题时需要考虑的因素
方法
(1) (2) 物理特征 数量
(3) 区域
(4) 起点与
终点
(5) 路线与
距离
(6) (7) (8) (9) 次数 速度 搬运 搬运
单位 设备
流 程 图
对于A类物料,每 种物料进行一次, 适合没有频繁和重 要的装配或拆卸工 序的产品或零件
存在重要装配的零件要将装 配过程表示清楚
严格执行突发事件上报制度、校外活 动报批 制度等 相关规 章制度 。做到 及时发 现、制 止、汇 报并处 理各类 违纪行 为或突 发事件 。
物料类 类别代
别名称
号
二、移动分析
2、移动分析方法
(1)流程分析法——每次只观察一类产品或物料,并跟随其沿 着整个生产过程收集资料,最后编制成流程图。该方法适合物 料品种很少的情况。
(2)起止点分析法——分两种做法
一是观察移动的起止点来收集资料,每次分析一条路线,并 绘制成搬运路线表。适合于路线数目不太多的情况。
控制
料、人员、 刚度)
量
设施)
类别
填写表头各项;列出所有物品或成组物品;填写每项物品的 特征;在起主导作用的特征地下划线;在确定物料类别后, 填明类别代号;备注供记载附加事项或补充说明
严格执行突发事件上报制度、校外活 动报批 制度等 相关规 章制度 。做到 及时发 现、制 止、汇 报并处 理各类 违纪行 为或突 发事件 。
WHY 为何搬运
WHAT
WHERE
WHEN
搬运什么 + 何地 + 何时
HOW
WHO
怎么做 + 何人做
否定
物料
+
搬运
分析物料搬运问题时需要考虑的因素
方法
(1) (2) 物理特征 数量
(3) 区域
(4) 起点与
终点
(5) 路线与
距离
(6) (7) (8) (9) 次数 速度 搬运 搬运
单位 设备
流 程 图
对于A类物料,每 种物料进行一次, 适合没有频繁和重 要的装配或拆卸工 序的产品或零件
存在重要装配的零件要将装 配过程表示清楚
严格执行突发事件上报制度、校外活 动报批 制度等 相关规 章制度 。做到 及时发 现、制 止、汇 报并处 理各类 违纪行 为或突 发事件 。
物料类 类别代
别名称
号
二、移动分析
2、移动分析方法
(1)流程分析法——每次只观察一类产品或物料,并跟随其沿 着整个生产过程收集资料,最后编制成流程图。该方法适合物 料品种很少的情况。
(2)起止点分析法——分两种做法
一是观察移动的起止点来收集资料,每次分析一条路线,并 绘制成搬运路线表。适合于路线数目不太多的情况。
控制
料、人员、 刚度)
量
设施)
类别
填写表头各项;列出所有物品或成组物品;填写每项物品的 特征;在起主导作用的特征地下划线;在确定物料类别后, 填明类别代号;备注供记载附加事项或补充说明
严格执行突发事件上报制度、校外活 动报批 制度等 相关规 章制度 。做到 及时发 现、制 止、汇 报并处 理各类 违纪行 为或突 发事件 。
4物料搬运系统设计.ppt

主讲 陈友玲
32
5.9 物料搬运系统分析设计方法(SHA)
5.9.1 阶段结构
弄清所分析区域的物料进出情况。 编制总体搬运方案 编制详细搬运方案 方案实施
主讲 陈友玲
33
5.9.2 程序模式:
物料分析
移动分析
方法分析(确 定合理经济的
搬运方法)
主要输入因素:P、Q、R、S、T
1、物料的分类
箱器)、搬运频率
复杂搬运设备
复杂运输设备
简单搬运设备
简单运输设备 距离
设备的类型、型号和数量
主讲 陈友玲
8
易燃、易损、重量、形状 水平式(滑道、推车、运输机、索道) 垂直式(升降机、起重机、卷扬机) 倾斜式(连续运输机、提升机、卷扬机) 多平面式(旋转起重机)
主讲 陈友玲
9
5.6 物料搬运设备及器皿
第五部分 物料搬运系统设计
主讲 陈友玲
1
5.1 物料搬运系统的基本概念
5.1.1 意义(从数据中看问题) 中等批量的生产车间里,零件在机床上的时间仅占生 产时间的5%,而95%的时间消耗在原材料、工具、零 件的搬运、等待上。
据统计,搬运费用占总生产费用的30%~40%
主讲 陈友玲
2
5.1.2 什么是物料搬运: 对物品进行搬上、卸下、移动的活动。 搬上、卸下——改变物料的存放状态。 移动(搬运)——改变物料的空间位置。
主讲 陈友玲
6
搬运设备选择的原则
物料搬运设备及用具 对搬运效果及
成本会有直接影响
不适宜的观点
•为了完成任务,赶快去买一台运输机或 增添一排货架(长远目标、标准化)。
•这台叉车是属于我们部门的,你们不能 随便用(部门利益与整体利益)。
物料搬运系统设计课件(PPT 41张)
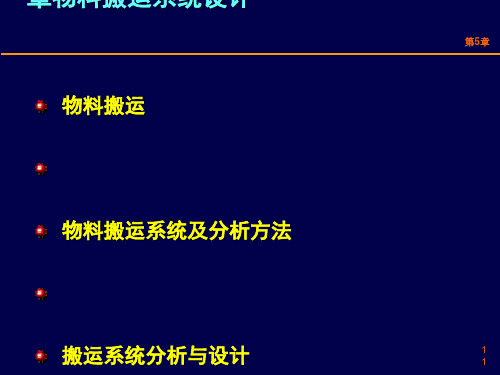
25
5.3 搬运系统分析与设计 —— 移动分析
(2) 移动分析方法:
第5章
流程分析法:每次只观察一类产品或物料, 并跟随其沿着整个生产过程收集资料,最后 编制流程图,该法适合物料品种很少的情况。 起止点分析法:两种做法 一是观察移动的起止点来收集资料,每次 分析一条路线,并绘制成搬运路线表。适 合路线数目不太多的情况。 二是对一个区域进行观察,收集运进运出 该区域的一切与物料有关的资料,并编制 成物料进出表。适合路线数目多的情况。
其他集装件作业法 机械作业法
按装卸设备作业特点:间歇作业(重程+空程),连续作业。
8
5.1 物料搬运
—— 搬运活性
第5章
一次物料搬运一般要完成装货、移动、卸货三个作业环节,最重要的
是提高搬运的活性,使装卸变得简单。 活性随物料存放状态不同,物料状态使其越容易进行搬运,则搬运活 性越高,反之则越低。
第5章
物料分类 根据物料的主要特征进行经验判断,以编制如表5-5所示 的程序: 的物料特征表,程序步骤:
列表标明所有物料的名称; 记录其物理特征或其他特征; 分析确定每种/类物料的主导/特重要的特征,以红/黑 实线标注决定作用的特征,橘黄线/黑虚线标注对分类 有特别重大影响的特征; 确定物料类别,具相似主导/特殊影响特征的归一类; 分类完毕后,即可编制物料特征表。
28
5.3 搬运系统分析与设计 —— 移动分析
第5章
(3) 编制搬运活动一览表,需对每条路线、每类物料和每项移动的相对 重要性进行标定;表中包含的具体资料: 列出每类物料,包括: 总的物流量及每类物料的物流量;
总的运输工作量及每条路线上的运输工作量;
各类物料的相对重要性等级,用元音字母AEIOU或光谱顺 序颜色代表; 整个搬运分析中,总物流量和总运输工作量填在右下角; 其他资料,如每项搬运中的具体件数。
物料搬运案例PPT
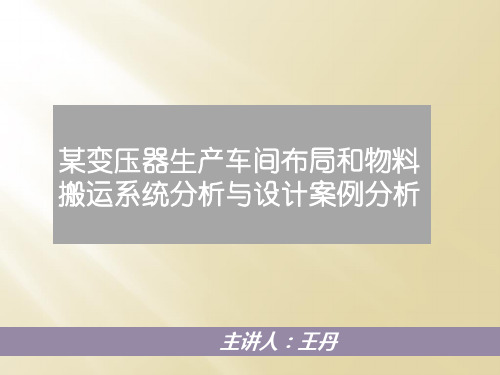
结论
通过对变压器生产各车间的布局以及物流现状进行分析,对其布局进行了调 整,并提出了新的物料搬运方案。与改善前相比,改善后缩短了搬运距离、 提高了搬运效率,并降低工人劳动强度。
ቤተ መጻሕፍቲ ባይዱ
线圈生产车间的预热区和修理区
组装车间的轭铁区和总组装区
图8 线圈生产车间原始布局图
图10 总装车间原始布局图
图9 改善后线圈生产车间布局图 线圈生产车间搬运距离减少了52m
图11 改善后总装车间布局 组装车间搬运距离减少了30m
(7)搬运方案设计
根据对各车间改善后的布局,确定了车间作业单位之间的搬运路线,并测出车间 作业单位之间的搬运距离以及生产一台变压器的搬运物流量等参数后,作出搬运 活动一览表。 根据搬运活动一览表,确定搬运路线系统、搬运设备及运输单元,并将物料搬运 方法这些路线、设备、单元用规定的符号填入汇总表相应的表格内,从而形成搬 运系统方案汇总表。
(3)车间原始布局
图3 线圈生产车间原始布局图
图2 铁芯生产车间原始布局图
图4 总装车间原始布局图
(4)车间物流量分析
对各作业单位对之间的物流距离进行测量, 并结合产品生产的物流量可以得到该车间 各作业单位对之间的物流情况,根据物流 情况可做出物流距离图(F-D图)
将F—D图分成4个区域: 第一区域:物流量大距离小 第二区域:物流量大距离大 第三区域:物流量小距离小 第四区域:物流量小距离大
分别对3个车间进行优化布置,得到车间布局改善方案。
(6)改善效果
通过对车间布局进行局部调整,解决了 搬运中的交叉和倒流现象,并使得物流 路线更加清晰和简洁。每个车间的搬运 距离都有不同程度的减小。
图6 铁芯生产车间原始布局图
铁芯生产车间中的铁芯装配区和打正式钢带 区
通过对变压器生产各车间的布局以及物流现状进行分析,对其布局进行了调 整,并提出了新的物料搬运方案。与改善前相比,改善后缩短了搬运距离、 提高了搬运效率,并降低工人劳动强度。
ቤተ መጻሕፍቲ ባይዱ
线圈生产车间的预热区和修理区
组装车间的轭铁区和总组装区
图8 线圈生产车间原始布局图
图10 总装车间原始布局图
图9 改善后线圈生产车间布局图 线圈生产车间搬运距离减少了52m
图11 改善后总装车间布局 组装车间搬运距离减少了30m
(7)搬运方案设计
根据对各车间改善后的布局,确定了车间作业单位之间的搬运路线,并测出车间 作业单位之间的搬运距离以及生产一台变压器的搬运物流量等参数后,作出搬运 活动一览表。 根据搬运活动一览表,确定搬运路线系统、搬运设备及运输单元,并将物料搬运 方法这些路线、设备、单元用规定的符号填入汇总表相应的表格内,从而形成搬 运系统方案汇总表。
(3)车间原始布局
图3 线圈生产车间原始布局图
图2 铁芯生产车间原始布局图
图4 总装车间原始布局图
(4)车间物流量分析
对各作业单位对之间的物流距离进行测量, 并结合产品生产的物流量可以得到该车间 各作业单位对之间的物流情况,根据物流 情况可做出物流距离图(F-D图)
将F—D图分成4个区域: 第一区域:物流量大距离小 第二区域:物流量大距离大 第三区域:物流量小距离小 第四区域:物流量小距离大
分别对3个车间进行优化布置,得到车间布局改善方案。
(6)改善效果
通过对车间布局进行局部调整,解决了 搬运中的交叉和倒流现象,并使得物流 路线更加清晰和简洁。每个车间的搬运 距离都有不同程度的减小。
图6 铁芯生产车间原始布局图
铁芯生产车间中的铁芯装配区和打正式钢带 区
第五章物料搬运系统设计课件

第12页
四、物料搬运的活性理论
1. 搬运活性 物料存放的状态:散放地上、装箱放在地上、放在 托盘上等。 存放状态不同,物料的搬运难易程度也不同。
第13页
搬运活性:不同物料存放状态而引起的物料搬运作 业的方便(难易)程度。
装卸次数少、花费时间少的货物存放方法称为搬运
活性高。
第14页
2. 搬运活性指数
第28页
(1)托盘的发展历史 ➢20世纪30年代,随着叉车在市场上出现,托盘作 为叉车的一种附属装卸搬运工具,与叉车配套使用, 从而使托盘首先在工业部门得到推广。 ➢二次世界大战间,为解决大量军用物资的快装快 卸问题,托盘得到发展。 ➢战后,随着经济复苏和发展,伴随着叉车产量的 增长,托盘得到普及。
第2页
第一节 物料搬运系统的基本概念 第二节 物料搬运设备的选择 第三节 系统化搬运分析的体系结构 第四节 系统化搬运分析的过程 第五节 系统化布置设计与系统化搬 运分析的相互关系(SLP+SHA)
第3页
第一节 物料搬运系统的基本概念
一、物料搬运的定义
物料搬运是指在同一场所范围内进行的、以改变物 料存放状态和空间位置为目的的活动,即对物料进 行的搬上、卸下、移动的活动。
第20页
七、搬运系统合理化原则
1. 不要作多余的作业:搬运本身就有可能成为沾污、
破损等影响物品价值的原因,如无必要,尽量不要
搬运。
第21页
2. 提高搬运活性:放在仓库的物品都是待运物品, 因此应使之处于易于移动的状态,将物品包装成单 件放在托盘上,或是装在车上,放在输送机上。
3. 利用重力:利用重力由高处向低处移动,有利于 节省能源。
第39页
箱式托盘的箱壁可为板式或网式;可以有盖或无 盖。
四、物料搬运的活性理论
1. 搬运活性 物料存放的状态:散放地上、装箱放在地上、放在 托盘上等。 存放状态不同,物料的搬运难易程度也不同。
第13页
搬运活性:不同物料存放状态而引起的物料搬运作 业的方便(难易)程度。
装卸次数少、花费时间少的货物存放方法称为搬运
活性高。
第14页
2. 搬运活性指数
第28页
(1)托盘的发展历史 ➢20世纪30年代,随着叉车在市场上出现,托盘作 为叉车的一种附属装卸搬运工具,与叉车配套使用, 从而使托盘首先在工业部门得到推广。 ➢二次世界大战间,为解决大量军用物资的快装快 卸问题,托盘得到发展。 ➢战后,随着经济复苏和发展,伴随着叉车产量的 增长,托盘得到普及。
第2页
第一节 物料搬运系统的基本概念 第二节 物料搬运设备的选择 第三节 系统化搬运分析的体系结构 第四节 系统化搬运分析的过程 第五节 系统化布置设计与系统化搬 运分析的相互关系(SLP+SHA)
第3页
第一节 物料搬运系统的基本概念
一、物料搬运的定义
物料搬运是指在同一场所范围内进行的、以改变物 料存放状态和空间位置为目的的活动,即对物料进 行的搬上、卸下、移动的活动。
第20页
七、搬运系统合理化原则
1. 不要作多余的作业:搬运本身就有可能成为沾污、
破损等影响物品价值的原因,如无必要,尽量不要
搬运。
第21页
2. 提高搬运活性:放在仓库的物品都是待运物品, 因此应使之处于易于移动的状态,将物品包装成单 件放在托盘上,或是装在车上,放在输送机上。
3. 利用重力:利用重力由高处向低处移动,有利于 节省能源。
第39页
箱式托盘的箱壁可为板式或网式;可以有盖或无 盖。
装卸搬运PPT课件

装卸搬运车辆是指依靠本身的运行 和装卸机构的功能,实现货物的水 平搬运和短距离运输、装卸的各种
车辆。
.
37
装卸搬运车辆的分类
• 装卸搬运车辆按照作业方式不同可分为三大类,固定平台搬运车、 牵引车和起升车辆。具体分类,如图所示。
• 按装卸搬运车辆所使用的动力进行分类,可分为电动式和内燃式。
平衡重式叉车 前移式叉车
➢ (2)美国与日本的远洋航运,一个往返需25天, 其中运输时间13天,装卸时间12天.
➢ (3)机械工厂年生产10吨产品需进行252吨次的装 卸搬运,其成本是加工成本的15.5%
.
10
综上可知,装卸的地位与作用是: 1、随其他物流活动产生的必要活动 ➢ 2、决定物流的速度 ➢ 3、成本在物流中所占比重高 ➢ 4、造成损失最严重的阶段
间歇作业
指在装卸搬运作业过种中有重程和空 程两个阶段,即在两次作业中存在一 个空程准备过程的作业方法。如门式
和桥式起重机作业。
连续作业法
指在装卸搬运过程中,设备不 停的作业,物资可连绵不断、 持续流水般的实现装卸作业的 方法。如带式输送机、链斗装
车机作业。
.
26
第2节 装卸搬运设备及其选择
装卸搬运设备是指用来搬移、 升降、装卸和短距离输送物
第7章 装卸搬运
➢ 在整个物流活动 过程中,装卸搬 运是不断出现和 反复进行的活动, 它出现的频率高 于其他的各种物 流活动。
.
1
学习目的
➢ 通过本章的学习,掌握现代装卸搬运的基 本概念、作业方式及准则、作业组织工作 及装卸搬运设备的选择和运用。
.
2
装卸搬运在物流各个职能中看起来最不 起眼,似乎是最微不足道,不值一提的。
装卸搬运PPT幻灯片

1、按作业性质的分类
装卸机械
搬运机械
装卸搬运机械
4.2.1 装卸搬运设备的分类
2、按机具工作原理分类
叉车类
吊车类
输送机类
作业车类
管道输送设备类
4.2.1 装卸搬运设备的分类(续1)
3、按有无动力分类
重力式装卸输送机
动力式装卸搬运机具
人力式装卸搬运机具
4.2.1 装卸搬运设备的分类(续2)
3、一般条件: (1)零担货物装卸 (2)整车货物装卸 (3)专用货车装卸
4.1.2 现代装卸搬运的作业方式(续1)
(二)单件作业法
装卸一般单件货物,通常是逐件由人力作业完成的,对于一些零散货物,诸如搬家货物等也常采用这种作业方法;长大笨重货物、不宜集装的危险货物以及行包等仍然采用单件作业法。
4.1.2 现代装卸搬运的作业方式(续25)
4.1.3 现代装卸搬运的作业准则
(一)防止无效装卸 (二)进行少消耗的装卸 (三)充分利用机械,实现“规模装卸” (四)提高“物”的装卸搬运活性
(一)防止无效装卸
无效装卸含义是消耗在有用货物必要装卸劳动之外的多余装卸劳动。
具体反映在
过多的装卸次数
4.2.2 装卸搬运设备的选择
(一)以满足现场作业为前提 (二)控制作业费用 (三)装卸搬运机械的配套
1、托盘作业法
(1)定义 托盘作业法是用托盘系列集装工具将货物形成成组货物单元,以便于采用叉车等设备实现装卸作业机械化的装卸作业方法。
4.1.2 现代装卸搬运的作业方式(续4)
LK-1111A川字型托盘
4.1.2 现代装卸搬运的作业方式(续5)
LK-1111田字型托盘
仓储与物料搬运PPT课件
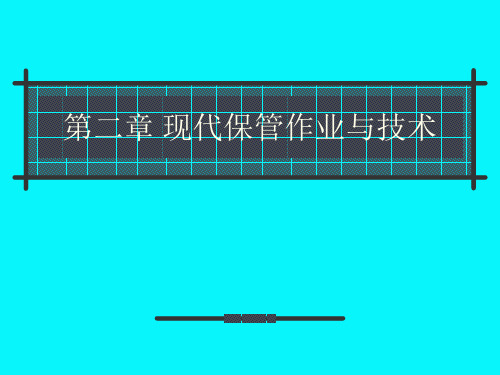
粘合剂以及天然包装材料等。 (1)木材。几乎所有的木材都可以作包装材料。用木材
作外包装,抗压、抗震性能好,但资源有限。
(2)纸及纸板。在所有包装材料中,纸的应用最广泛。它 的品种最多,消耗量也最大。特别是在运输包装、销售
包装方面,纸所占全部包装材料的比重极大。
纸和纸板作为包装材料具有独特的优点:价格低, 重量轻,可降低包装成本及节省运输费用;纸的质地细 腻、均匀、柔软,具有耐磨性,并有一定的强度,容易 粘合和印刷;不受温度的影响;容易实现自动化、机械 化的包装生产;无味、无毒,纸类包装材料用后极易处
并且作业时应戴上安全护套。
(14)储位表示原则。即把保管物品的位置给予明 确表示。此原则主要目的在于将存取单元化,并 能减少错误。尤其适用于临时人员、高龄作业员
多的仓库。
(15)明了(表示)性原则。所谓明了性原则,系指
用视觉,使保管场所及保管品能够容易识别的原 则。 如颜色看板、布条、标记符号等方式,让 作业员一目了然,并能产生联想而帮助记忆。
第二章 现代保管作业与技术
主要内容
第一节 基本保管作业方法 第二节 分拣配货作业 第三节 包装作业 第四节 现代保管技术
第一节 基本保管作业方法
保管作业的原则
(1)靠近仓库出口原则。即将刚刚到达的或经常 要用的商品指派到离出入口最近的空储位上。
(2)以周转率为基础原则。即 按照商品在仓库的周转率(销 售量除以存货量)来排定储位。 首先依周转率由大到小排一序 列,再将此序列分为若干段, (通常分为三至五段)属于一 段中的货品列为同一级指定储
形象地说,又类似于一个播种者,一次取出几亩 地所需的种子,在地中边巡回边播撒,所以又形象称
之为播种分拣式配货作业。
分货式配货作业的特点
作外包装,抗压、抗震性能好,但资源有限。
(2)纸及纸板。在所有包装材料中,纸的应用最广泛。它 的品种最多,消耗量也最大。特别是在运输包装、销售
包装方面,纸所占全部包装材料的比重极大。
纸和纸板作为包装材料具有独特的优点:价格低, 重量轻,可降低包装成本及节省运输费用;纸的质地细 腻、均匀、柔软,具有耐磨性,并有一定的强度,容易 粘合和印刷;不受温度的影响;容易实现自动化、机械 化的包装生产;无味、无毒,纸类包装材料用后极易处
并且作业时应戴上安全护套。
(14)储位表示原则。即把保管物品的位置给予明 确表示。此原则主要目的在于将存取单元化,并 能减少错误。尤其适用于临时人员、高龄作业员
多的仓库。
(15)明了(表示)性原则。所谓明了性原则,系指
用视觉,使保管场所及保管品能够容易识别的原 则。 如颜色看板、布条、标记符号等方式,让 作业员一目了然,并能产生联想而帮助记忆。
第二章 现代保管作业与技术
主要内容
第一节 基本保管作业方法 第二节 分拣配货作业 第三节 包装作业 第四节 现代保管技术
第一节 基本保管作业方法
保管作业的原则
(1)靠近仓库出口原则。即将刚刚到达的或经常 要用的商品指派到离出入口最近的空储位上。
(2)以周转率为基础原则。即 按照商品在仓库的周转率(销 售量除以存货量)来排定储位。 首先依周转率由大到小排一序 列,再将此序列分为若干段, (通常分为三至五段)属于一 段中的货品列为同一级指定储
形象地说,又类似于一个播种者,一次取出几亩 地所需的种子,在地中边巡回边播撒,所以又形象称
之为播种分拣式配货作业。
分货式配货作业的特点
物料搬运系统设计PPT课件
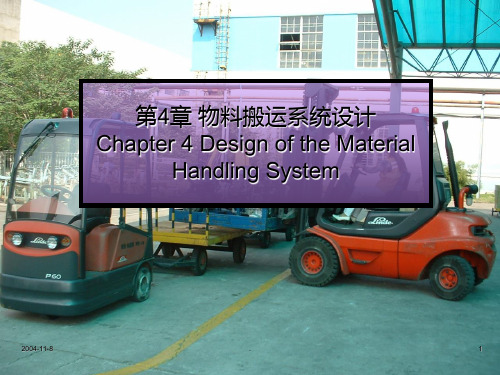
和服务水平。工作的衡量可以用运量乘以运距来衡量,即W=F*D。
(4) 人机工效原则。在设计物料搬运作业和选择设备时,要考虑人的作业
能力和局限性,以保证安全和有效的作业。
(5) 集装单元化原则。尽可能采用标准容器与装载工具集装物料,以利搬
运过程的标准化、集装化。
2004-11-8
5
10原则续
(6) 充分利用空间原则。最大可能地充分利用建筑物的整个空间,包括高 度方向。不要忘了往上看。
(7) 系统化原则。尽可能广泛地把各种搬运活动当作一个整体,使之组成 相互协调的搬运系统。其范围包括收货、检验、储存、生产、检验、包装、 成品储存、发货、运输和反向物流等。
(8) 自动化原则。应当采用合理的作业机械化和/或自动化,以提高作业 效率、反应速度和一致性,降低成本并消除重复性和有潜在不安全性的人 工作业。
即对物料、产品、零部件或其他物品进行搬上、卸下、 移动的活动,如装卸、移动、分类、堆码、理货和取货 等作业都属于物料搬运活动。
2004-11-8
4
4.1.2 物料搬运的原则
国际物料管理协会下属的物料搬运研究所浓:美国物料搬运教育大学与产业联系理事会
1.3 ~ 2.3:有效利用传送带、自动导引车。
2.3以上:从设备、方法方面进一步减少搬运工序数。
总之,活性系数越高,所需人工越少,但设备投入越 多。在进行搬运系统设计时,不应机械地认为活性系数 越高越好,而应综合考虑。
移动
装车
4
支垫
3
运走
装箱
2
升起
散放
1
搬起
0
集中
2004-11-8
11
4.1.4 物料搬运的单元化与标准化
- 1、下载文档前请自行甄别文档内容的完整性,平台不提供额外的编辑、内容补充、找答案等附加服务。
- 2、"仅部分预览"的文档,不可在线预览部分如存在完整性等问题,可反馈申请退款(可完整预览的文档不适用该条件!)。
- 3、如文档侵犯您的权益,请联系客服反馈,我们会尽快为您处理(人工客服工作时间:9:00-18:30)。
第一区域
第二区域
第三区域
第四区域
原则:使总的搬运费用最小,F与D应遵
循反比规律。 由图5可知,有4对作业单位处于F—D图 的第二区域,即作业单位之间存在物流量大 搬运距离也大的情况,说明该车间的物料搬 运系统存在不合理的地方,需要进行改进。 图5 工厂现时物流F-D图 (F为物流量,D为作业单位间距离)
某变压器生产车间布局和物料 搬运系统分析与设计案例分析
主讲人:王丹
第一部分
物料搬运系统知识点回顾
(1)物料搬运 (2)物料搬运系统 (3)物料搬运系统的主要对象 (4)物料搬运系统的管理内容 (5)物料搬运系统设计的重要性 (6)物料搬运系统设计的理论过程 (7)物料搬运系统设计的实际应用过程
(1)物料搬运:在物流过程同
一场所范围内进行的、以改变物料的 存放状态和空间位置为主要目的的活 动。 装卸-----竖直方向 搬运-----水平方向
(2)物料搬运系统:将一系
列的相关设备或装置用于一个过程或 系统,协调合理地进行移动、储存和 控制。
(3)物料搬运系统研究对 象:主要是生产物流系统。
(4)物料搬运系统管理 内容有 5 个方面:
组装车间的轭铁区和总组装区
图8 线圈生产车间原始布局图
图10 总装车间原始布局图
图9 改善后线圈生产车间布局图 线圈生产车间搬运距离减少了52m
图11 改善后总装车间布局 组装车间搬运距离减少了30m
(7)搬运方案设计
根据对各车间改善后的布局,确定了车间作业单位之间的搬运路线,并测出车间 作业单位之间的搬运距离以及生产一台变压器的搬运物流量等参数后,作出搬运 活动一览表。 根据搬运活动一览表,确定搬运路线系统、搬运设备及运输单元,并将物料搬运 方法这些路线、设备、单元用规定的符号填入汇总表相应的表格内,从而形成搬 运系统方案汇总表。
(6)物料搬运系统设计的理论过程:
第II阶段是分析工厂内部各车间或 各厂房间的物料搬运。 第III阶段是分析具体工位间或者设 备间的物料搬运。
(7)物料搬运系统设计的实际应用过程
首先对现有车间生产设施、 生产工艺流程序现场调研, 搜集原始有关数据信息, 应用系统布置设计(SLP) 的技术,建立车间设施布 局改进的计划方案; 然后应用搬运系统设计 (SHA)的方法,对布局 改善后的车间物料搬运系 统现状进行研究分析,运 用数学规划的方法建立搬 运设备配置的线性规划模 型,根据生产和搬运信息, 配置某种类型的搬运工具 及其数量。
第二部分
变压器生产车间布局和物料搬 运系统分析与设计案例分析
(1)产品工艺流程 (2)搬运存在的问题 (3)车间原始布局 (4)物流量分析 (5)车间布局改善 (6)改善效果分析 (7)搬运方案设计
(1)产品工艺流程
某特种变压器公司以生产干式变压器为 主,该公司主要有3个生产车间,分别 为铁芯生产车间、线圈(包括低压线圈 和高压线圈)生产车间和总装车间。
(5)车间布局改善
为了使生产过程中的物流搬运路线缩短,将工序相邻的作业单位尽量布置在一起。
对铁芯、低压线圈和高压线圈生产以及变压器组装的物流路线分析发现,铁芯生产 车间中的铁芯装配区和打正式钢带区,线圈生产车间的预热区和修而使得作业间的物流出现了交叉和 回流并形成了较大的物流搬运距离。 分别对3个车间进行优化布置,得到车间布局改善方案。
搬运,数量,时间,空间和控制。
一般机械工厂物料搬运系统管 理内容有5个方面:
质量、数量、时间、场所、成本
每次搬运物料的数量决定了物料搬 运设备的类型和性质,同时也决定 了货物运输的单件成本。
(5)物料搬运系统设计的重要性:
企业生产中,物料搬运费用直接影响企业生产成本和资金周转率,物料的运输费用 是总成本的 20% ~50%,从原材料的输入到成品的输出,物料的实际加工时间是生产 周期的 5% ~ 10%,其余时间都处于停滞状态或搬运状态。而通过对工厂布局优良的 设计可使物料运输费用降低至少 10% ~ 30%。物料搬运体系的合理设计,对产 品加工质量,降低成本,缩短生产时间,物流经营体制,资金的回转和企业的经 营效益都有很大的帮助和提高。
图表符号 图1 干式变压器生产工艺流程图
(2)搬运存在的问题
据现场调研发现车间搬运主要存在的问题有: 搬运通道不畅通,存在交叉、回流现象; 搬运路线曲折; 搬运活动未从系统考虑; 搬运设备缺乏柔性; 搬运系统与生产系统不均衡等。 图3 线圈生产车间原始布局图
(3)车间原始布局
图2 铁芯生产车间原始布局图
目前,各车间运用机动叉车进行原材料搬运,总组装车间使用行车进行搬运, 其他工序间的搬运使用手动叉车进行搬运。由于线圈生产车间的每个线圈的 重量都在80kg以上,因此线圈生产车间的工序间搬运需要2人同时进行; 另外,在线圈生产过程中,浇注和固化工序中的化学物品对搬运人员身体会 造成伤害。 通过对比搬运方式,制定出以下的搬运方案: ①铁芯生产车间采用机动叉车进行搬运,这样能降低搬运强度,使搬运方式 更加合理; ②线圈生产车间采用行车搬运,由于线圈生产工序较多,搬运的次数多、线 圈较重,采用行车搬运,能减少搬运人员,提高搬运效率,同时又能减少因 浇注和固化工序中化学物品对搬运人员带来的身体伤害。
(6)改善效果
通过对车间布局进行局部调整,解决了 搬运中的交叉和倒流现象,并使得物流 路线更加清晰和简洁。每个车间的搬运 距离都有不同程度的减小。
图6 铁芯生产车间原始布局图
铁芯生产车间中的铁芯装配区和打正式钢带 区 铁芯车间搬运距离减少了15m 图7 改善后铁芯生产车间布局
线圈生产车间的预热区和修理区
结论
通过对变压器生产各车间的布局以及物流现状进行分析,对其布局进行了调 整,并提出了新的物料搬运方案。与改善前相比,改善后缩短了搬运距离、 提高了搬运效率,并降低工人劳动强度。
谢谢! (*^__^*) 嘻嘻……
图4 总装车间原始布局图
(4)车间物流量分析
对各作业单位对之间的物流距离进行测量, 并结合产品生产的物流量可以得到该车间 各作业单位对之间的物流情况,根据物流 情况可做出物流距离图(F-D图) 将F—D图分成4个区域: 第一区域:物流量大距离小 第二区域:物流量大距离大 第三区域:物流量小距离小 第四区域:物流量小距离大