化工装置中的硫化亚铁自燃
石油化工储运系统中硫化亚铁自然风险分析及防范措施
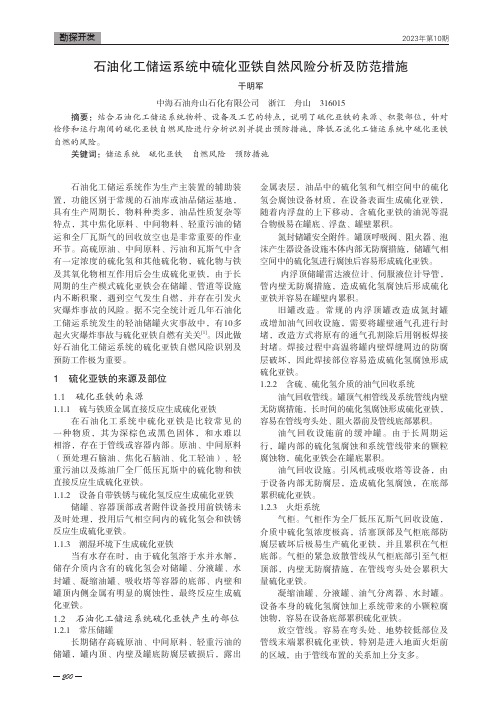
200石油化工储运系统作为生产主装置的辅助装置,功能区别于常规的石油库或油品储运基地,具有生产周期长,物料种类多,油品性质复杂等特点,其中焦化原料、中间物料、轻重污油的储运和全厂瓦斯气的回收放空也是非常重要的作业环节。
高硫原油、中间原料、污油和瓦斯气中含有一定浓度的硫化氢和其他硫化物,硫化物与铁及其氧化物相互作用后会生成硫化亚铁,由于长周期的生产模式硫化亚铁会在储罐、管道等设施内不断积聚,遇到空气发生自燃,并存在引发火灾爆炸事故的风险。
据不完全统计近几年石油化工储运系统发生的轻油储罐火灾事故中,有10多起火灾爆炸事故与硫化亚铁自燃有关关[1]。
因此做好石油化工储运系统的硫化亚铁自燃风险识别及预防工作极为重要。
1 硫化亚铁的来源及部位1.1 硫化亚铁的来源1.1.1 硫与铁质金属直接反应生成硫化亚铁在石油化工系统中硫化亚铁是比较常见的一种物质,其为深棕色或黑色固体,和水难以相溶,存在于管线或容器内部。
原油、中间原料(预处理石脑油、焦化石脑油、化工轻油)、轻重污油以及炼油厂全厂低压瓦斯中的硫化物和铁直接反应生成硫化亚铁。
1.1.2 设备自带铁锈与硫化氢反应生成硫化亚铁储罐、容器顶部或者附件设备投用前铁锈未及时处理,投用后气相空间内的硫化氢会和铁锈反应生成硫化亚铁。
1.1.3 潮湿环境下生成硫化亚铁当有水存在时,由于硫化氢溶于水并水解,储存介质内含有的硫化氢会对储罐、分液罐、水封罐、凝缩油罐、吸收塔等容器的底部、内壁和罐顶内侧金属有明显的腐蚀性,最终反应生成硫化亚铁。
1.2 石油化工储运系统硫化亚铁产生的部位1.2.1 常压储罐长期储存高硫原油、中间原料、轻重污油的储罐,罐内顶、内壁及罐底防腐层破损后,露出金属表层,油品中的硫化氢和气相空间中的硫化氢会腐蚀设备材质,在设备表面生成硫化亚铁,随着内浮盘的上下移动,含硫化亚铁的油泥等混合物极易在罐底、浮盘、罐壁累积。
氮封储罐安全附件。
罐顶呼吸阀、阻火器、泡沫产生器设备设施本体内部无防腐措施,储罐气相空间中的硫化氢进行腐蚀后容易形成硫化亚铁。
硫化亚铁自燃危害与防范技术研究进展

质量和热流的同步分析实验所得 TG-DSC 曲线进
第4期
高建村等. 硫化亚铁自燃危害与防范技术研究进展
行分析,较系统地研 究 了 FeS 氧 化 自 燃 的 热 效 应 及
动力学,计 算 了 反 应 的 活 化 能 平 均 值;通 过 Ma
l
ek
法 y(
α)-α 曲线得到 FeS 最概然机理函数为 f(
一是高温条件下(
240℃ 以上)重 质 原 油 所 含 单
质硫、硫化氢和硫醇与金属直接发生化学腐蚀,这是
性有重 要 影 响,当 水 分 适 量、气 流 量 较 大 且 FeS 粒
形式 [7]:
最常见的硫腐蚀形式。
H2S+Fe=FeS+ H2 ↑
S+Fe=FeS(高温)
RCH2CH2SH +Fe=RCHCH2 +FeS+ H2 ↑
有国外学者认 为,储 罐 壳 层 材 料 在 有 水 存 在 条
件下可腐蚀生成 α
-FeO(
OH),之后与酸性气体硫化
氢反应生成 FeS,其他介 质(
CO2 、溶 解 氧 等)的 存 在
加速了整个化学腐蚀过程
。
[
12]
二是低温条件下的电化学腐蚀。在潮湿环境下
或溶液中,储罐 内 极 易 发 生 严 重 的 电 化 学 腐 蚀。 硫
收稿日期:
2020
08
07;修回日期:
2020
09
24
基金项目:中国博士后科学基金资助项目(
2020M670202);国家级大学 生 创 新 创 业 计 划(URT)项 目(
2020J
00082);北 京 高 等 学 校 高 水 平 人 才
石化装置停工大检修防硫化亚铁自燃的对策和措施

石化装置停工大检修防硫化亚铁自燃的对策和措施
1、硫化亚铁性质。
干燥的硫化亚铁在空气中的自燃温度一般为300-350℃。
当硫化亚铁含水量在20%以下时,会导致硫化亚铁的自热,从而使硫化亚铁发生自燃。
但当硫化亚铁含水60%以上时,则可以有效抑制硫化亚铁自热和自燃现象的发生。
2、各单位在装置停工前,应根据装置特点,制定落实防止硫化亚铁自燃措施,对存在硫化亚铁自燃风险的设备、管线,要进行危害识别,并制定钝化清洗方案,通过采取化学处理的方法,消除硫化亚铁自燃的风险。
对未进行钝化清洗的塔、容器、换热器等设备,要采取有效的防范措施,防止硫化亚铁自燃。
3、含有硫化亚铁的设备、管线,在温度降至常温后方可打开,设备在拆开接触空气后,应及时安排人员用水冲洗和清洗,并在现场配置消防水带,一旦发现硫化亚铁自燃现象应立即采取喷淋等应急措施,防止硫化亚铁自燃烧坏设备和管线。
4、设备、容器未经有效彻底置换清扫前,其附属的热电偶不得提前拆除。
进入受限空间作业期间,操作人员应随时在DCS显示屏上关注设备容器内温度的变化,监控硫化亚铁自燃情况。
一旦出现异常,作业人员必须立即撤出,停止作业。
5、清扫出来的硫化亚铁应用水浇湿,进行妥善处理并及时运走,防止硫化亚铁氧化自燃引发火灾。
五、。
加氢装置检修期间硫化亚铁自燃预防与对策
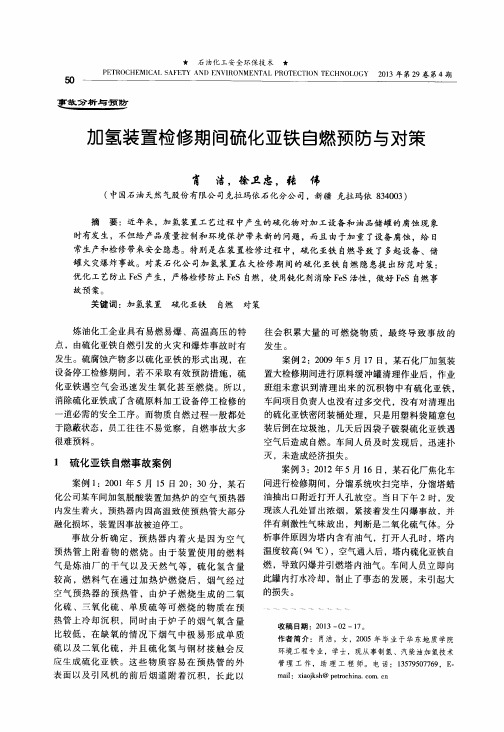
加氢精制反应过程中的硫分布情况如表2 所示:
产品名称 产量/( t ·月一) 硫化 物含 量/ ( mg·L。 1)
原料
<O.1%
表2加氢精制反应过程中的硫分布
精制 柴 油
冷高 分 底 含硫污水
冷低分底 含硫污水
74×109 <0.1%
4 95往会积 累大量的可 燃烧物质, 最终导致事 故的 发生 。
案例2:2009年5月17 Et ,某石化厂加氢装 置大检修期间进行原料缓冲罐清理作业后,作业 班组未意识到清理出来的沉积物中有硫化亚铁, 车间项目负责人也没有过多交代,没有对清理出 的硫化亚铁密闭装桶处理,只是用塑料袋随意包 装后倒在垃圾池,几天后因袋子破裂硫化亚铁遇 空气后造成自燃。车间人员及时发现后,迅速扑 灭,未造成经济损失。
表1加氢精制装置原料油性质
项目 处理量/( t ·a 。1) 混合比例,m% 油品性质
焦化石脑油
27. 29 30.07
焦 化柴油
63. 45 69. 93
混合原料
90. 74
1∞.0
密度( 20℃) / ( g·e m一3)
0.7 38
0.855
O. 816
馏程,( ASTM D86) ℃ I BP/l O% 30 %/5 0% 70 %/9 0%
1硫化亚铁自燃事故案例
案例1:2001年5月15日20:30分,某石 化公司某车间加氢脱酸装置加热炉的空气预热器 内发生着火,预热器内因高温致使预热管大部分 融化损坏,装置因 事故被迫停工。
事故 分析确定 ,预热 器内着火 是因为空 气 预热管 上附着物的 燃烧。由于 装置使用的 燃料 气是炼 油厂的干气 以及天然气 等,硫化氢 含量 较高, 燃料气在通 过加热炉燃 烧后,烟气 经过 空气预 热器的预热 管,由炉子 燃烧生成的 二氧 化硫、 三氧化硫、 单质硫等可 燃烧的物质 在预 热管上 冷却沉积, 同时由于炉 子的烟气氧 含量 比较低, 在缺氧的情况下 烟气中极易形 成单质 硫以及 二氧化硫, 并且硫化氢 与钢材接触 会反 应生成 硫化亚铁。 这些物质容 易在预热管 的外 表面以及 引风机的前后 烟道附着沉积, 长此以
2020.8.10硫化亚铁(FeS)自然着火事故报告_20201121232728
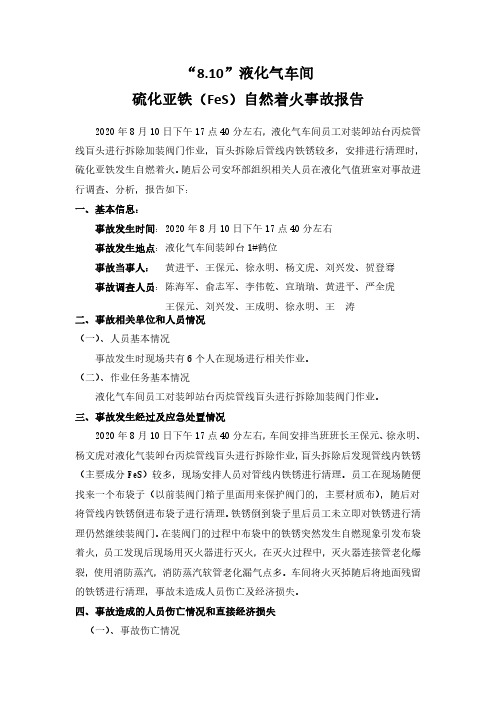
“8.10”液化气车间硫化亚铁(FeS)自然着火事故报告2020年8月10日下午17点40分左右,液化气车间员工对装卸站台丙烷管线盲头进行拆除加装阀门作业,盲头拆除后管线内铁锈较多,安排进行清理时,硫化亚铁发生自燃着火。
随后公司安环部组织相关人员在液化气值班室对事故进行调查、分析,报告如下:一、基本信息:事故发生时间:2020年8月10日下午17点40分左右事故发生地点:液化气车间装卸台1#鹤位事故当事人:黄进平、王保元、徐永明、杨文虎、刘兴发、贺登骞事故调查人员:陈海军、俞志军、李伟乾、宜瑞瑞、黄进平、严全虎王保元、刘兴发、王成明、徐永明、王涛二、事故相关单位和人员情况(一)、人员基本情况事故发生时现场共有6个人在现场进行相关作业。
(二)、作业任务基本情况液化气车间员工对装卸站台丙烷管线盲头进行拆除加装阀门作业。
三、事故发生经过及应急处置情况2020年8月10日下午17点40分左右,车间安排当班班长王保元、徐永明、杨文虎对液化气装卸台丙烷管线盲头进行拆除作业,盲头拆除后发现管线内铁锈(主要成分FeS)较多,现场安排人员对管线内铁锈进行清理。
员工在现场随便找来一个布袋子(以前装阀门箱子里面用来保护阀门的,主要材质布),随后对将管线内铁锈倒进布袋子进行清理。
铁锈倒到袋子里后员工未立即对铁锈进行清理仍然继续装阀门。
在装阀门的过程中布袋中的铁锈突然发生自燃现象引发布袋着火,员工发现后现场用灭火器进行灭火,在灭火过程中,灭火器连接管老化爆裂,使用消防蒸汽,消防蒸汽软管老化漏气点多。
车间将火灭掉随后将地面残留的铁锈进行清理,事故未造成人员伤亡及经济损失。
四、事故造成的人员伤亡情况和直接经济损失(一)、事故伤亡情况该事故未造成人员伤亡(二)、直接经济损失现场灭火使用两具35Kg的灭火器,合计560元。
五、事故发生原因和事故性质(一)、直接原因1、液化气员工在装阀门的过程中布袋中的铁锈突然发生自燃现象引发布袋着火。
硫化亚铁自燃在检维修中的危害及预防
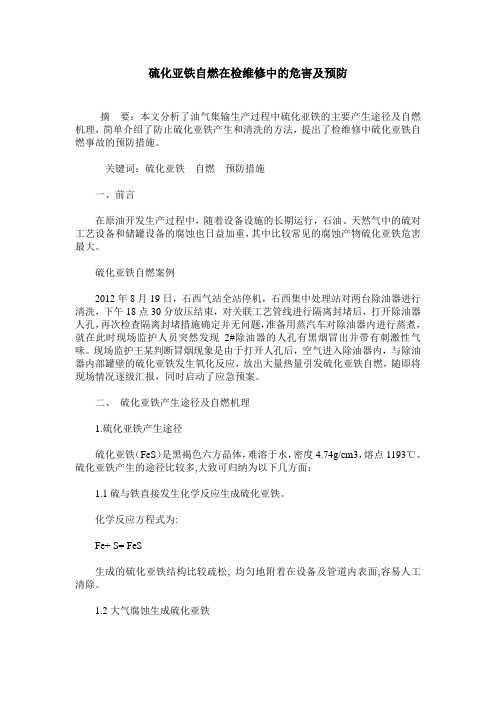
硫化亚铁自燃在检维修中的危害及预防摘要:本文分析了油气集输生产过程中硫化亚铁的主要产生途径及自燃机理,简单介绍了防止硫化亚铁产生和清洗的方法,提出了检维修中硫化亚铁自燃事故的预防措施。
关键词:硫化亚铁自燃预防措施一、前言在原油开发生产过程中,随着设备设施的长期运行,石油、天然气中的硫对工艺设备和储罐设备的腐蚀也日益加重,其中比较常见的腐蚀产物硫化亚铁危害最大。
硫化亚铁自燃案例2012年8月19日,石西气站全站停机,石西集中处理站对两台除油器进行清洗,下午18点30分放压结束,对关联工艺管线进行隔离封堵后,打开除油器人孔,再次检查隔离封堵措施确定并无问题,准备用蒸汽车对除油器内进行蒸煮,就在此时现场监护人员突然发现2#除油器的人孔有黑烟冒出并带有刺激性气味。
现场监护王某判断冒烟现象是由于打开人孔后,空气进入除油器内,与除油器内部罐壁的硫化亚铁发生氧化反应,放出大量热量引发硫化亚铁自燃,随即将现场情况逐级汇报,同时启动了应急预案。
二、硫化亚铁产生途径及自燃机理1.硫化亚铁产生途径硫化亚铁(FeS)是黑褐色六方晶体,难溶于水,密度4.74g/cm3,熔点1193℃。
硫化亚铁产生的途径比较多,大致可归纳为以下几方面:1.1硫与铁直接发生化学反应生成硫化亚铁。
化学反应方程式为:Fe+ S= FeS生成的硫化亚铁结构比较疏松, 均匀地附着在设备及管道内表面,容易人工清除。
1.2大气腐蚀生成硫化亚铁装置停工或闲置过程中,设备附件长期暴露于空气之中,会造成大气腐蚀,从而生成铁锈。
铁锈由于不易彻底清除掉,在生产中就会与硫化氢作用生成硫化亚铁。
化学反应方程式为:Fe+ O2+ H2O → Fe2O3+H2OFe2O3+H2O +H2S→FeS + H2O该反应比较容易进行, 防腐不好的设备产生硫化亚铁的可能性较大。
1.3电化学腐蚀反应生成硫化亚铁当有水存在时,储存介质内含有的硫化氢和硫醇对油罐罐底、罐壁和罐顶内侧金属有很明显的腐蚀性。
如何防止硫化亚铁自燃
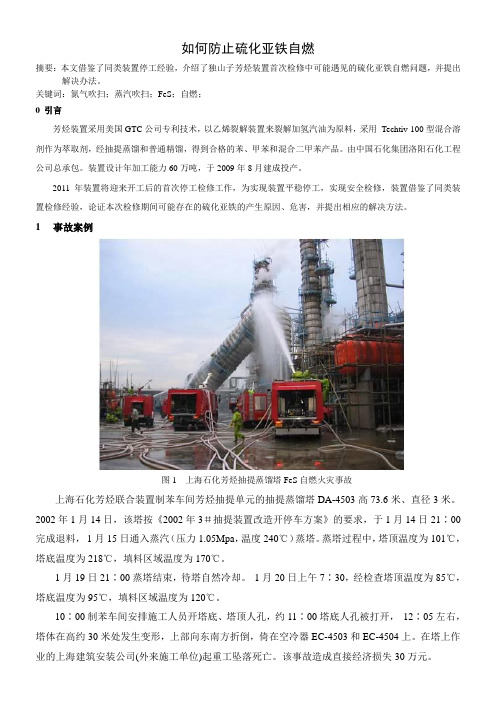
如何防止硫化亚铁自燃摘要:本文借鉴了同类装置停工经验,介绍了独山子芳烃装置首次检修中可能遇见的硫化亚铁自燃问题,并提出解决办法。
关键词:氮气吹扫;蒸汽吹扫;FeS;自燃;0 引言芳烃装置采用美国GTC公司专利技术,以乙烯裂解装置来裂解加氢汽油为原料,采用Techtiv-100型混合溶剂作为萃取剂,经抽提蒸馏和普通精馏,得到合格的苯、甲苯和混合二甲苯产品。
由中国石化集团洛阳石化工程公司总承包。
装置设计年加工能力60万吨,于2009年8月建成投产。
2011年装置将迎来开工后的首次停工检修工作,为实现装置平稳停工,实现安全检修,装置借鉴了同类装置检修经验,论证本次检修期间可能存在的硫化亚铁的产生原因、危害,并提出相应的解决方法。
1 事故案例图1 上海石化芳烃抽提蒸馏塔FeS自燃火灾事故上海石化芳烃联合装置制苯车间芳烃抽提单元的抽提蒸馏塔DA-4503高73.6米、直径3米。
2002年1月14日,该塔按《2002年3#抽提装置改造开停车方案》的要求,于1月14日21∶00完成退料,1月15日通入蒸汽(压力1.05Mpa,温度240℃)蒸塔。
蒸塔过程中,塔顶温度为101℃,塔底温度为218℃,填料区域温度为170℃。
1月19日21∶00蒸塔结束,待塔自然冷却。
1月20日上午7∶30,经检查塔顶温度为85℃,塔底温度为95℃,填料区域温度为120℃。
10∶00制苯车间安排施工人员开塔底、塔顶人孔,约11∶00塔底人孔被打开,12∶05左右,塔体在高约30米处发生变形,上部向东南方折倒,倚在空冷器EC-4503和EC-4504上。
在塔上作业的上海建筑安装公司(外来施工单位)起重工坠落死亡。
该事故造成直接经济损失30万元。
1999 年1 月茂名石化公司乙烯裂解装置稀释汽发生器(塔270)在检修过程中发生硫化亚铁自燃事故;2000 年茂名石化公司炼油厂加氢裂化车间第二分馏塔(T-106)在停汽检修时发生硫化亚铁自燃烧塔事故;2002年12月茂名石化公司二重整车间苯抽提塔-301 在停汽检修期间,发生硫化亚铁自燃塔事故;2003年9 月金陵石化公司烷基苯厂在检修中准备更换C-405 填料塔塔内件和填料,经退油、加盲板并进行了72 小时蒸汽吹扫后打开塔的人孔通风,准备交出施工时,塔内硫化亚铁遇空气发生自燃引起火灾,导致C-405塔体1/3处折断。
化工装置中的硫化亚铁自燃
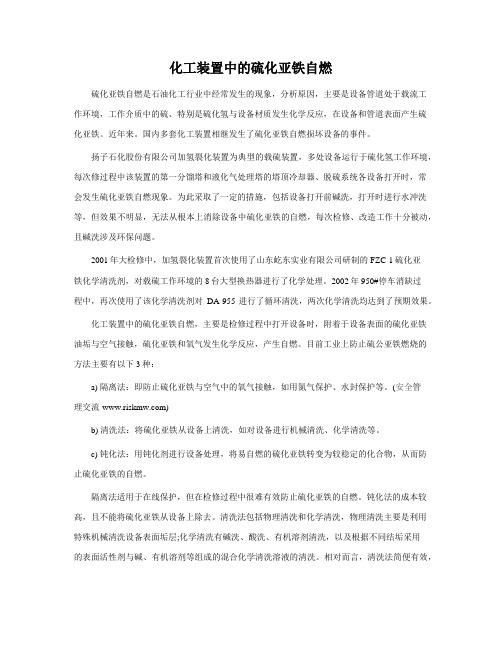
化工装置中的硫化亚铁自燃硫化亚铁自燃是石油化工行业中经常发生的现象,分析原因,主要是设备管道处于载流工作环境,工作介质中的硫、特别是硫化氢与设备材质发生化学反应,在设备和管道表面产生硫化亚铁。
近年来。
国内多套化工装置相继发生了硫化亚铁自燃损坏设备的事件。
扬子石化股份有限公司加氢裂化装置为典型的载硫装置,多处设备运行于硫化氢工作环境,每次修过程中该装置的第一分馏塔和液化气处理塔的塔顶冷却器、脱硫系统各设备打开时,常会发生硫化亚铁自燃现象。
为此采取了一定的措施,包括设备打开前碱洗,打开时进行水冲洗等,但效果不明显,无法从根本上消除设备中硫化亚铁的自燃,每次检修、改造工作十分被动,且碱洗涉及环保问题。
2001年大检修中,加氢裂化装置首次使用了山东屹东实业有限公司研制的FZC-1硫化亚铁化学清洗剂,对载硫工作环境的8台大型换热器进行了化学处理。
2002年950#停车消缺过程中,再次使用了该化学清洗剂对DA-955进行了循环清洗,两次化学清洗均达到了预期效果。
化工装置中的硫化亚铁自燃,主要是检修过程中打开设备时,附着于设备表面的硫化亚铁油垢与空气接触,硫化亚铁和氧气发生化学反应,产生自燃。
目前工业上防止硫公亚铁燃烧的方法主要有以下3种:a) 隔离法:即防止硫化亚铁与空气中的氧气接触,如用氮气保护、水封保护等。
(安全管理交流)b) 清洗法:将硫化亚铁从设备上清洗,如对设备进行机械清洗、化学清洗等。
c) 钝化法:用钝化剂进行设备处理,将易自燃的硫化亚铁转变为较稳定的化合物,从而防止硫化亚铁的自燃。
隔离法适用于在线保护,但在检修过程中很难有效防止硫化亚铁的自燃。
钝化法的成本较高,且不能将硫化亚铁从设备上除去。
清洗法包括物理清洗和化学清洗,物理清洗主要是利用特殊机械清洗设备表面垢层;化学清洗有碱洗、酸洗、有机溶剂清洗,以及根据不同结垢采用的表面活性剂与碱、有机溶剂等组成的混合化学清洗溶液的清洗。
相对而言,清洗法简便有效,而且成本低,是比较常见的方法。
尾气旁路管线硫化亚铁自燃事故

尾气旁路管线硫化亚铁自燃事故
事故经过:
硫磺回收装置尾气旁路管线是一条DN800的管线,其作用是当尾气部分需要临时停下抢修的时候,给硫磺装置克劳斯反应后的过程气直接排放到焚烧炉提供通道。
此管线没有任何的监测仪表。
2003年10月27日22:30左右,硫磺装置在停工完成后,装置处于静置状态的第一个晚上,当班操作工在巡检的过程中,发现旁路管线的裸露部分发红,当班人员立即用蒸汽对发红的部位进行掩护,避免了管线的大面积灼烧损坏。
原因分析:
1、对硫化亚铁的认识不足,装置在停工的过程中,只认识到硫化亚铁对大型设备的危害,对有可能发生硫化亚铁自燃的大型设备都进行了钝化处理,而忽略了硫化亚铁对管线的危害,没有对管线处理。
(实际上没有办法处理)
2、管线在生产过程中,由于硫蒸汽的串入,生成大量的硫化亚铁。
在装置停下静置的时候,由于空气从焚烧炉反串进入,造成管线内的硫化亚铁自燃。
第 1 页
本文部分内容来自互联网,不为其真实性及所产生的后果负责,如有异议请联系我们及时删除。
防止硫化亚铁自燃措施的细则

防止硫化亚铁自燃指导细则为规范各单位在设备开盖后,落实防止硫化亚铁自燃的措施,防止检修期间发生硫化亚铁自燃事故,特制定如下指导细则:1总体要求1.1装置停工检修前,车间领导应组织工艺、设备、安全相关人员进行风险评价,制定停工方案时,编写防硫化亚铁自燃专篇,并在方案中明确防硫化亚铁自燃给水、给蒸汽的具体位置;对易发生硫化亚铁自燃的塔、容器、换热器、反应器、管线等设备进行监控,制定内外操防硫化亚铁自燃测温记录表,在停工检修前告知全体职工和施工人员。
1.2车间要对存在硫化亚铁设备严格进行化学清洗,检查验收。
1.3打开人孔前直至整个检修施工作业结束封人孔期间,应根据风险评估结果确定在存在硫化亚铁自燃的塔、容器等设备准备好消防水枪,且随时处于备用状态。
1.4对易发生硫化亚铁自燃的塔、容器,与其相连的蒸汽管线,不要求加盲板,但要求对关闭的蒸汽阀门挂禁动牌,并绑好铁丝。
1.5清理出的含有硫化亚铁铁锈的油泥等废弃物,要督促施工单位用塑料袋包装好扎紧袋口,集中堆放在临时专用堆放池,淋水保持湿润,并及时联系安全环保处环保管理人员办理相关手续,要求施工单位及时清走处理。
2填料塔(填料在检修期间不拆出塔外)防硫化亚铁自燃措施2.1准备工作:塔开人孔前,车间要在操作室准备塑料布、捆扎用铁丝,作为应急封人孔使用。
塔打开人孔后,在每段填料层上层抽出位置人孔须接临时喷淋器(机动处制定模版),否则塔各填料段必须备有消防水枪。
打水前要检查确认塔内人员、施工机具(电打磨机、电焊枪、照明器具)等撤离,开关箱已停电。
2.2打水流程要求:打水前检查各侧线塔壁阀是否关闭,打水时必须确保水从塔顶部往下淋,确保水能从上至下淋透填料。
2.3打水量:塔顶回流和消防竖管同时打水时,按正常运行最大量进行。
2.4打水时间:每天8:00打水30分钟,13:30打水30分钟,晚上收工后打水1.5小时。
(若与实际不符,由安全管理部门协调)2.5打水后事项:若塔内有施工作业,6时、11:30打水完毕,打开抽出塔壁阀(视作业层而定)将积液槽的水导出,防止水流向作业点;晚收工打水后不用打开壁阀,让积液槽的水一直往下浸泡填料。
硫化亚铁自燃原因

硫化亚铁自燃事故的预防措施基于对已发生事故的调查分析及硫化亚铁自燃机理的研究现状,预防措施主要可分为以下方面:严格控制进罐油品的硫含量,从源头上降低事故隐患。
油品脱硫的方法很多,加氢脱硫是最常见的方法,此外还有氧化脱硫、生物脱硫等非加氢脱硫方法。
1、加氢脱硫加氢脱硫是在氢气存在下,经催化剂作用将油品中的有机硫化物转化为硫化氢而除去的方法。
该法所用催化剂通常为Co-Mo-AL203由于加氢装置投资大,操作费用高,操作条件苛刻,导致油品成本大幅上升。
因此,人们一直寻求更好的脱硫工艺。
2、氧化脱硫在强氧化剂作用下,极性较低的硫醚和噻吩类化合物被氧化生成极性较高的亚砜和砜类化合物。
与传统的加氢脱硫相比较,氧化脱硫法操作条件温和,工艺投资和操作费用低,能将油中硫化物以有机硫的形式脱除,减少了环境污染。
3、生物脱硫生物脱硫,又称生物催化剂脱硫,是一种在常温、常压下利用氧、厌氧菌去除在石油中含硫杂环化合物中硫的一种新技术。
在细菌中的酶可以有选择性地氧化硫原子进而分开键,经过需氧、厌氧菌分离的含硫化合物其烃类母体的燃烧性能并不受到影响。
4、硫化亚铁的清洗和钝化硫化亚铁具有较强的活性和被螯合能力,一般硫化亚铁高效钝化剂是由一种螯合剂加入适当比例的其它有效成分合成。
螯合:由一个简单正离子(称为中心离子)和几个中性分子和离子(配位体)结合而成的复杂离子(又称络离子),含有配离子的化合物。
这种配合物称为螯合物。
螯合物比一般配合物更稳定。
把能形成螯合物的配位体叫整合剂。
5、酸洗法酸洗法是通过泵把酸液输送到需要清洗的设备中,硫化亚铁与酸液反应生成H2S,溶解在酸液中,酸洗法潜在的困难是要除去H2S 气体,如果酸的浓度过高,将会导致酸洗法不能控制H2S的产生速度,从而有大量H2S产生,如果H2S不能有效安全地除去,将会引起爆炸,除此之外酸洗法对设备产生一定的腐蚀。
6、酸洗结合化学抑制剂法在酸洗的过程中对产生的采用加入氢氧化钠的方式处理。
简析煤焦化行业硫化亚铁自燃原因及控制措施

<匕£•矣会■也2020年第45期防火防爆简析煤焦化行业硫化亚铁自燃原因及控制措施张振夫崔平山东钢铁股份有限公司莱芜分公司山东济南271104摘要:简介硫化亚铁的性质、硫化亚铁产生的原因及自燃机理;通过某焦化厂回收系统检修期间发生的闪爆事故,对煤焦化行业化产回收系统硫化亚铁自燃,从物理化学性质方面进行分析,并从管理方面找出原因;针对硫化亚铁生产和自燃特点提出预防及控制措施。
关键词:硫化亚铁;自燃;原因分析;控制措施煤焦化企业属易燃、易爆、易产生静电和对人体有一定毒害作用的生产行业。
由于化工产品具有一定的危险性,在储存、使用和检修过程中可能会引发火灾和爆炸事故,自燃事故 也是很难预料的,而宄其事故原因往往具有一定的隐蔽性。
所以,应采取怎样的预防和控制措施是谈类企业所考虑的首要问题。
1硫化亚铁的性质硫化亚铁以无色六方形结晶存在,一般为暗 褐色或灰黑色片状或粒状物,其熔点1194°C;在 潮湿空气中逐渐氧化而分解成硫和四氧化三铁,溶于酸可放出硫化氢气体,不溶于水,接 触酸或酸气能产生有毒气体;受高热分解放出有毒的气体;易燃,具刺激性,属低毒类,具 刺激作用;该物质应贮存于阴凉、通风仓库内。
应与氧化剂、酸类、食用化工原料分开存放;与空气接触便能氧化发热而自燃。
2 硫化亚铁产生的原因及自燃机理2.1 硫化亚铁产生的原因由于煤气和粗苯、焦油中含有硫化氢或硫和有机硫化物,这些硫化物对生产设备器壁上的氧化铁和铁长期腐蚀,生成硫化亚铁(F eS), 其反应式如下:Fe + 〇2 + H2O —>F e2〇3 ■H2OFe203.H20 +H2S—FeS 丄+ H202.2硫化亚铁的自燃机理可燃物不与明火接触而发生着火燃烧的现象称为自燃。
一般情况下,液体油品相对密度越小,其闪点越低,而自燃点越高;反之,液体 油品相对密度越大,闪点越高,而自燃点越低。
表1为一些物质的闪点和自燃点。
表1_些物质的闪点和自燃点物质名称闪点(°c)自燃点r c)物质名称闪点(°c)自燃点(-C)汽油<28510〜530硫化氢50260苯11.1555一氧化碳50610煤油28 〜45380-425沥青> 120280萘80515硫化亚铁40注:上述数据,由于试验条件不同,各资料有所不同,仅供参考。
典型炼油装置硫化亚铁自燃分析及对策
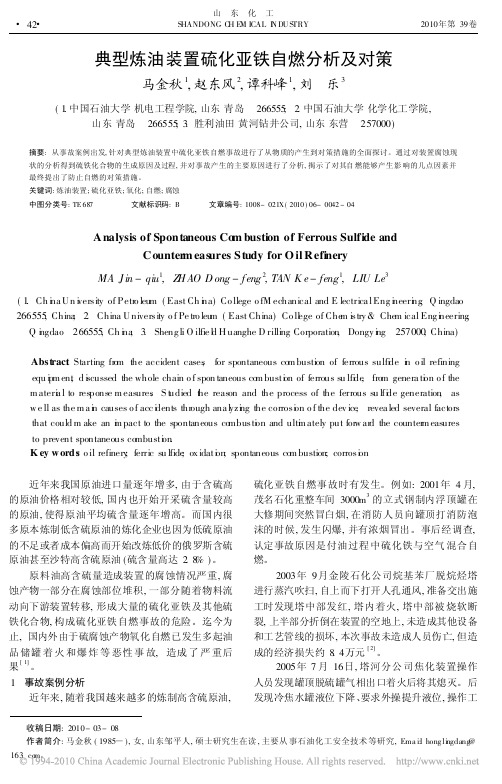
收稿日期:2010-03-08作者简介:马金秋(1985 ),女,山东邹平人,硕士研究生在读,主要从事石油化工安全技术等研究,Ema i:l hong li ngdang @163.co m 。
典型炼油装置硫化亚铁自燃分析及对策马金秋1,赵东风2,谭科峰1,刘 乐3(1.中国石油大学机电工程学院,山东青岛 266555;2.中国石油大学化学化工学院,山东青岛 266555;3.胜利油田黄河钻井公司,山东东营 257000)摘要:从事故案例出发,针对典型炼油装置中硫化亚铁自燃事故进行了从物质的产生到对策措施的全面探讨。
通过对装置腐蚀现状的分析得到硫铁化合物的生成原因及过程,并对事故产生的主要原因进行了分析,揭示了对其自燃能够产生影响的几点因素并最终提出了防止自燃的对策措施。
关键词:炼油装置;硫化亚铁;氧化;自燃;腐蚀中图分类号:TE 687 文献标识码:B 文章编号:1008-021X(2010)06-0042-04Analysis of Spontaneous Co m bustion of Ferrous Sulfide andCounter m eas ures Study for O il RefineryMA J in -qiu 1,Z H AO D ong -f eng 2,TAN K e -feng 1,LIU Le3(1.Ch i n a Un i v ersity of Petr o leum (East Ch i n a)Co llege o fM echanical and E lectrica lEng i n eeri n g ,Q ingdao 266555,China ;2.China University o f Pe tro leu m (East China)Co ll e ge of Che m istry &Che m ical Eng i n eering ,Q i n gdao 266555,Ch i n a ;3.Sheng li O ilfie l d H uanghe D rilling Corporation ,Dongy i n g 257000,China)Abst ract :Starting fr o m the accident cases ,for spontaneous co m bustion of ferrous sulfi d e i n o il refining equ i p m ent ,d i s cussed the whole chain o f spon taneous co m busti o n of ferrous su lfi d e ,fro m genera ti o n o f the m ateri a l to response m easures .S t u died t h e reason and the process of the ferrous su lfi d e generation ,asw e ll as the m a i n causes o f acc i d ents thr ough ana l y zi n g the corrosi o n o f the dev ice ,revea led several factors that could m ake an i m pact to the spontaneous co mbusti o n and ulti m ately put for w ar d the counter m easures to prevent spontaneous co mbusti o n .K ey w ords :o il refinery ;ferric su lfide ;ox idati o n ;spontaneous co m bustion;corrosi o n 近年来我国原油进口量逐年增多,由于含硫高的原油价格相对较低,国内也开始开采硫含量较高的原油,使得原油平均硫含量逐年增高。
装置检修时防止硫化亚铁自燃措施

装置检修时防止硫化亚铁自燃措施(一)在装置停工检修前由安全环保部组织车间及有关部门专题讨论确定容易引起自燃的重点部位,并确定相应采取的技术措施和防范措施。
生产部、安全环保部等部门和车间一起制定详细的清洗方案和排污方案,由车间负责送各职能部门进行会签,并报公司主管领导批准执行。
(二)生产车间、安全环保部在停工方案中对高硫部位必须含有防止FeS自燃的防范措施。
对硫腐蚀不严重的部位,先进行密闭吹扫,塔顶冷却器不停,待塔内油气扫净后,改往火炬吹扫,最后进行塔顶放空和水洗;在吹扫、水洗过程中要加强塔、容器排污水的监测,尽可能排净容器中的污泥等杂质,在进行蒸汽吹扫后,要进行水洗,塔内温度冷却到安全温度以下方可通风,打开人孔后要及时组织清理垢物,以防止垢物自燃。
安全环保部安排采样分析和数据的确认反馈,确定排污的去向,在排污前车间须向生产调度和供排水车间进行通报,供排水车间改好流程准备接收后,方可进行定点定量排放,防止对污水处理场的活性污泥等形成冲击。
(三)在装置吹扫水洗完后通风、开人孔后至检修前,车间必须组织人员通水喷淋,保持塔、容器润湿。
DCS或常规显示仪表在全装置检修未全面展开前不允许停用,各岗位必须24小时仍准时准确地记录各类塔、容器内温度,以及喷淋水进出温度的变化。
同时加强巡检,对关键部位作重点监控,发现塔、容器内温度上升或有异常状况,及时打水降温处理。
生产部和安全环保部对防止硫化亚铁自燃措施落实情况进行专项检查。
(四)对一些含硫化合物较多的特殊设备如换热器等,为防止抽芯等检修时硫化亚铁自燃或出现硫化亚铁自燃后能迅速处理,要增加相应的水管线、蒸汽线等固定灭火设施。
对有破沫网的塔,要在有破沫网的塔板上引蒸汽加盖石棉布进行保护。
对有破沫网的罐,打开后立即用水喷淋,并尽快卸下清洗。
对塔、容器进行爆炸气和环保分析合格后立即进塔、容器进行浮锈、油泥的清扫,清除硫化亚铁和可燃物,确保检修安全。
硫化亚铁自燃事故预防等

化工装置中的硫化亚铁自燃(图文)硫化亚铁自燃是石油化工行业中经常发生的现象,分析原因,主要是设备管道处于载流工作环境,工作介质中的硫、特别是硫化氢与设备材质发生化学反应,在设备和管道表面产生硫化亚铁。
近年来。
国内多套化工装置相继发生了硫化亚铁自燃损坏设备的事件。
扬子石化股份有限公司加氢裂化装置为典型的载硫装置,多处设备运行于硫化氢工作环境,每次修过程中该装置的第一分馏塔和液化气处理塔的塔顶冷却器、脱硫系统各设备打开时,常会发生硫化亚铁自燃现象。
为此采取了一定的措施,包括设备打开前碱洗,打开时进行水冲洗等,但效果不明显,无法从根本上消除设备中硫化亚铁的自燃,每次检修、改造工作十分被动,且碱洗涉及环保问题。
2001年大检修中,加氢裂化装置首次使用了山东屹东实业有限公司研制的FZC-1硫化亚铁化学清洗剂,对载硫工作环境的8台大型换热器进行了化学处理。
2002年950#停车消缺过程中,再次使用了该化学清洗剂对DA-955进行了循环清洗,两次化学清洗均达到了预期效果。
化工装置中的硫化亚铁自燃,主要是检修过程中打开设备时,附着于设备表面的硫化亚铁油垢与空气接触,硫化亚铁和氧气发生化学反应,产生自燃。
目前工业上防止硫公亚铁燃烧的方法主要有以下3种:a) 隔离法:即防止硫化亚铁与空气中的氧气接触,如用氮气保护、水封保护等。
(安全管理交流)b) 清洗法:将硫化亚铁从设备上清洗,如对设备进行机械清洗、化学清洗等。
c) 钝化法:用钝化剂进行设备处理,将易自燃的硫化亚铁转变为较稳定的化合物,从而防止硫化亚铁的自燃。
隔离法适用于在线保护,但在检修过程中很难有效防止硫化亚铁的自燃。
钝化法的成本较高,且不能将硫化亚铁从设备上除去。
清洗法包括物理清洗和化学清洗,物理清洗主要是利用特殊机械清洗设备表面垢层;化学清洗有碱洗、酸洗、有机溶剂清洗,以及根据不同结垢采用的表面活性剂与碱、有机溶剂等组成的混合化学清洗溶液的清洗。
相对而言,清洗法简便有效,而且成本低,是比较常见的方法。
关于硫化亚铁(FeS)硫化铁(FeS2)的自燃现象

关于硫化亚铁(FeS)硫化铁(FeS2)的自燃现象
网络中关于硫化铁(FeS)自燃的4段论述
一、硫化亚铁的自燃温度是很高的,干燥硫化亚铁在干空气中的自燃温度一般为300-350℃,少量水(硫化亚铁中含水20%以下)的引入会导致硫化亚铁的起始自热温度降至常温,从而使硫化亚铁在常温下也能发生自热和自燃。
但含水60%以上可以有效抑制硫化亚铁自热和自燃。
目前还不明白硫化亚铁在有水的情况下自燃的机理。
二、硫化铁在空气中氧化放热是引发自燃着火事故的内在因素,连续的供氧和热量易于集聚是硫化铁自燃的外部因素。
在自然环境条件下对硫化铁进行氧化实验,实验结果表明,Fe2O3硫化后生成的硫铁化合物活性很高,具有较高的自然氧化活性,在室温下可迅速与空气中的氧气反应,同时放出大量的热。
以Fe2O3的硫化产物为典型样品,研究了环境温度、风速、硫化时间、暴露面积以及硫化铁质量对氧化升温特征的影响。
环境温度对于升温速率影响不明显;风速具有促进和抑制硫化铁自燃进程的双重作用,风速为1.5 m/s时,氧化放热强度达到最高;硫化时间长、暴露面积大以及较多的硫化铁能够加速氧化升温过程,反之则降低了硫化铁的自燃倾向性。
三、硫化亚铁本身不燃,他是发生氧化反应后放热后,热量集聚引燃可燃物。
检修过程中,一般温度在40度左右就应该控制与防范!!
四、硫化铁的自燃点大约为40℃。
自然性硫化亚铁的危害
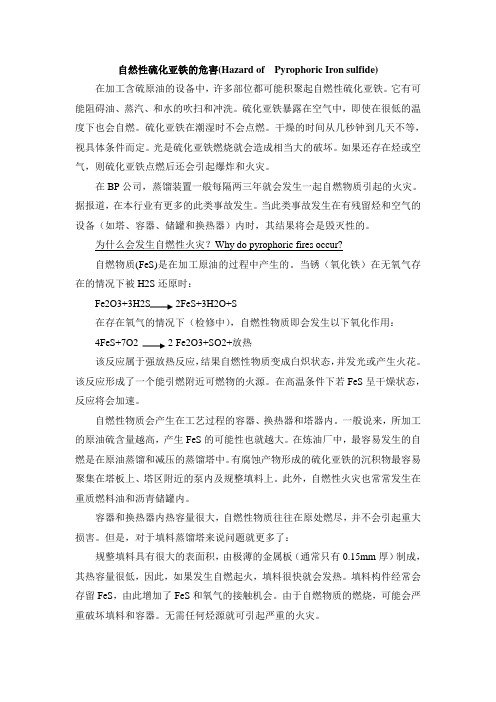
自然性硫化亚铁的危害(Hazard of Pyrophoric Iron sulfide) 在加工含硫原油的设备中,许多部位都可能积聚起自燃性硫化亚铁。
它有可能阻碍油、蒸汽、和水的吹扫和冲洗。
硫化亚铁暴露在空气中,即使在很低的温度下也会自燃。
硫化亚铁在潮湿时不会点燃。
干燥的时间从几秒钟到几天不等,视具体条件而定。
光是硫化亚铁燃烧就会造成相当大的破坏。
如果还存在烃或空气,则硫化亚铁点燃后还会引起爆炸和火灾。
在BP公司,蒸馏装置一般每隔两三年就会发生一起自燃物质引起的火灾。
据报道,在本行业有更多的此类事故发生。
当此类事故发生在有残留烃和空气的设备(如塔、容器、储罐和换热器)内时,其结果将会是毁灭性的。
为什么会发生自燃性火灾?Why do pyrophoric fires occur?自燃物质(FeS)是在加工原油的过程中产生的。
当锈(氧化铁)在无氧气存在的情况下被H2S还原时:Fe2O3+3H2S 2FeS+3H2O+S在存在氧气的情况下(检修中),自燃性物质即会发生以下氧化作用:4FeS+7O2 2 Fe2O3+SO2+放热该反应属于强放热反应,结果自燃性物质变成白炽状态,并发光或产生火花。
该反应形成了一个能引燃附近可燃物的火源。
在高温条件下若FeS呈干燥状态,反应将会加速。
自燃性物质会产生在工艺过程的容器、换热器和塔器内。
一般说来,所加工的原油硫含量越高,产生FeS的可能性也就越大。
在炼油厂中,最容易发生的自燃是在原油蒸馏和减压的蒸馏塔中。
有腐蚀产物形成的硫化亚铁的沉积物最容易聚集在塔板上、塔区附近的泵内及规整填料上。
此外,自燃性火灾也常常发生在重质燃料油和沥青储罐内。
容器和换热器内热容量很大,自燃性物质往往在原处燃尽,并不会引起重大损害。
但是,对于填料蒸馏塔来说问题就更多了:规整填料具有很大的表面积,由极薄的金属板(通常只有0.15mm厚)制成,其热容量很低,因此,如果发生自燃起火,填料很快就会发热。
石油化工装置检修过程中硫化亚铁自燃事故
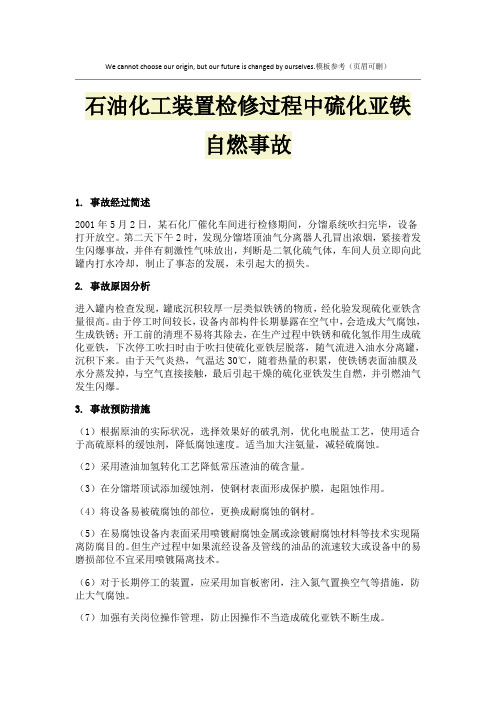
We cannot choose our origin, but our future is changed by ourselves.模板参考(页眉可删)石油化工装置检修过程中硫化亚铁自燃事故1. 事故经过简述2001年5月2日,某石化厂催化车间进行检修期间,分馏系统吹扫完毕,设备打开放空。
第二天下午2时,发现分馏塔顶油气分离器人孔冒出浓烟,紧接着发生闪爆事故,并伴有刺激性气味放出,判断是二氧化硫气体,车间人员立即向此罐内打水冷却,制止了事态的发展,未引起大的损失。
2. 事故原因分析进入罐内检查发现,罐底沉积较厚一层类似铁锈的物质,经化验发现硫化亚铁含量很高。
由于停工时间较长,设备内部构件长期暴露在空气中,会造成大气腐蚀,生成铁锈;开工前的清理不易将其除去,在生产过程中铁锈和硫化氢作用生成硫化亚铁,下次停工吹扫时由于吹扫使硫化亚铁层脱落,随气流进入油水分离罐,沉积下来。
由于天气炎热,气温达30℃,随着热量的积累,使铁锈表面油膜及水分蒸发掉,与空气直接接触,最后引起干燥的硫化亚铁发生自燃,并引燃油气发生闪爆。
3. 事故预防措施(1)根据原油的实际状况,选择效果好的破乳剂,优化电脱盐工艺,使用适合于高硫原料的缓蚀剂,降低腐蚀速度。
适当加大注氨量,减轻硫腐蚀。
(2)采用渣油加氢转化工艺降低常压渣油的硫含量。
(3)在分馏塔顶试添加缓蚀剂,使钢材表面形成保护膜,起阻蚀作用。
(4)将设备易被硫腐蚀的部位,更换成耐腐蚀的钢材。
(5)在易腐蚀设备内表面采用喷镀耐腐蚀金属或涂镀耐腐蚀材料等技术实现隔离防腐目的。
但生产过程中如果流经设备及管线的油品的流速较大或设备中的易磨损部位不宜采用喷镀隔离技术。
(6)对于长期停工的装置,应采用加盲板密闭,注入氮气置换空气等措施,防止大气腐蚀。
(7)加强有关岗位操作管理,防止因操作不当造成硫化亚铁不断生成。
(8)对于像减压塔填料,酸性水汽提塔板极易产生硫化亚铁部位,可采用酸洗、螯合物处理、氧化处理等化学方法处理。
硫化亚铁自燃事故及对策.doc
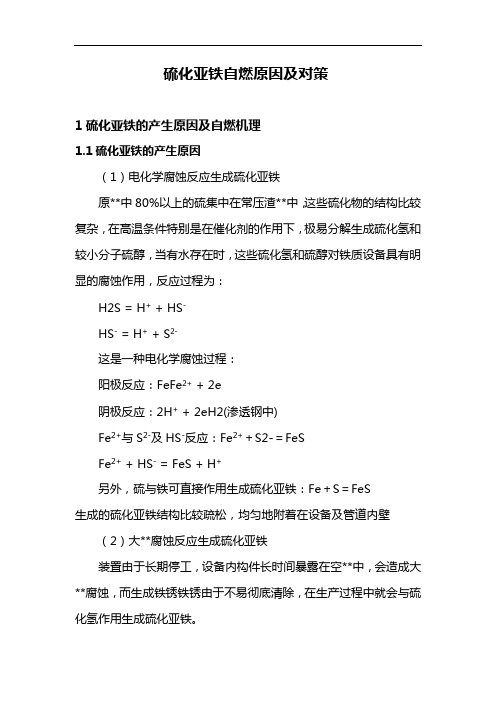
硫化亚铁自燃原因及对策1硫化亚铁的产生原因及自燃机理1.1硫化亚铁的产生原因(1)电化学腐蚀反应生成硫化亚铁原**中80%以上的硫集中在常压渣**中,这些硫化物的结构比较复杂,在高温条件特别是在催化剂的作用下,极易分解生成硫化氢和较小分子硫醇,当有水存在时,这些硫化氢和硫醇对铁质设备具有明显的腐蚀作用,反应过程为:H2S = H+ + HS-HS- = H+ + S2-这是一种电化学腐蚀过程:阳极反应:FeFe2+ + 2e阴极反应:2H+ + 2eH2(渗透钢中)Fe2+与S2-及HS-反应:Fe2++S2-=FeSFe2+ + HS- = FeS + H+另外,硫与铁可直接作用生成硫化亚铁:Fe+S=FeS生成的硫化亚铁结构比较疏松,均匀地附着在设备及管道内壁(2)大**腐蚀反应生成硫化亚铁装置由于长期停工,设备内构件长时间暴露在空**中,会造成大**腐蚀,而生成铁锈铁锈由于不易彻底清除,在生产过程中就会与硫化氢作用生成硫化亚铁。
反应式如下:Fe + O2 + H2O Fe2O3&8226;H2OFe2O3&8226;H2O + H2S FeS + H2O此反应较易进行,由于长期停工,防腐不善的装置更具有生产硫化亚铁的趋势。
1.2硫化亚铁自燃的机理及现象(1)硫化亚铁自燃的机理硫化亚铁及铁的其它硫化物在空**中受热或光照时,会发生如下反应:FeS + 3/2O2 = FeO + SO2 + 49KJ2FeO + 1/2O2 = Fe2O3 + 271KJFeS2 + O2 = FeS + SO2 + 222KJFe2S3 + 3/2O2 = Fe2O3 + 3S + 586KJ(2)硫化亚铁自燃的现象硫化亚铁自燃的过程中如没有一定的可燃物支持,将产生白色的SO2**体,常被误认为水蒸汽,伴有刺激性**味;同时放出大量的热当周围有其它可燃物(如**品)存在时,会冒出浓烟,并引发火灾和爆炸。
浅析石油化工装置检修过程中硫化亚铁自燃事故及对策.

浅析石油化工装置检修过程中硫化亚铁自燃事故及对策1前言石油化工企业是易燃易爆的生产企业, 由物质自燃引发的火灾和爆炸事故时有发生。
而物质自燃过程一般处于隐蔽状态, 往往不易为人们所觉察, 自燃事故有时是很难预料的。
绝大多数自燃事故发生在生产装置停工检修过程中:案例 1:2004年 4月 25日某催化装置因供电系统故障导致全面停工,停车过程按紧急停工步骤进行。
由于鼓风机停转, 酸性水汽提系统焚烧炉出现熄火现象, 操作人员及时将瓦斯切断,汽提塔剩余气体经焚烧炉烟囱排放,大约距停工 4-5小时后,发现焚烧尾气烟囱有浓烟冒出, 监控仪表显示烟道温度急骤上升, 车间操作人员及时切断酸性气炉口阀, 接临时蒸汽通入炉内进行吹扫; 由于发现及时处理得当避免事故进一步发展, 事后检查发现碳钢材质烟囱距地面 10米处出现严重变形。
案例 2:2001年 5月 2日, 某石化厂催化车间进行检修期间,分馏系统吹扫完毕,设备打开放空。
第二天下午 2时, 发现分馏塔顶油气分离器人孔冒出浓烟, 紧接着发生闪爆事故, 并伴有刺激性气味放出, 判断是二氧化硫气体, 车间人员立即向此罐内打水冷却, 制止了事态的发展,未引起大的损失。
表 1国内外原油含硫量表原油名称含硫量 % 时间大庆原油 0.097 1996.8胜利原油 0.77 1996.11惠州原油 0.03 1991.2辽河原油 0.1736 1984.5陆丰原油 0.1127 1998.7阿曼原油 1.0896 1997.10伊朗轻原油 1.63 1998.4伊拉克巴士拉原油 2.11 1997.12沙特轻质原油 2.03 1998.3沙特中质原油 2.56 1994.5沙特重质原油 3.09 1994.8迪拜原油 1.66 1994.2据有关资料统计,目前我国石油消费量的年增长率为 4%,而国内原油量的年产量增长率低于 1%, 不足的部分要靠进口原油来补充。
从表 1中可以看出外国进口原油含硫量较高, 特别是中东原油 , 均大于 1%,最高可达 3.09%。
- 1、下载文档前请自行甄别文档内容的完整性,平台不提供额外的编辑、内容补充、找答案等附加服务。
- 2、"仅部分预览"的文档,不可在线预览部分如存在完整性等问题,可反馈申请退款(可完整预览的文档不适用该条件!)。
- 3、如文档侵犯您的权益,请联系客服反馈,我们会尽快为您处理(人工客服工作时间:9:00-18:30)。
化工装置中的硫化亚铁自燃
硫化亚铁自燃是石油化工行业中经常发生的现象,分析原因,主要是设备管道处于载流工作环境,工作介质中的硫、特别是硫化氢与设备材质发生化学反应,在设备和管道表面产生硫化亚铁。
近年来。
国内多套化工装置相继发生了硫化亚铁自燃损坏设备的事件。
扬子石化股份有限公司加氢裂化装置为典型的载硫装置,多处设备运行于硫化氢工作环境,每次修过程中该装置的第一分馏塔和液化气处理塔的塔顶冷却器、脱硫系统各设备打开时,常会发生硫化亚铁自燃现象。
为此采取了一定的措施,包括设备打开前碱洗,打开时进行水冲洗等,但效果不明显,无法从根本上消除设备中硫化亚铁的自燃,每次检修、改造工作十分被动,且碱洗涉及环保问题。
2001年大检修中,加氢裂化装置首次使用了山东屹东实业有限公司研制的FZC-1硫化亚
铁化学清洗剂,对载硫工作环境的8台大型换热器进行了化学处理。
2002年950#停车消缺过
程中,再次使用了该化学清洗剂对DA-955进行了循环清洗,两次化学清洗均达到了预期效果。
化工装置中的硫化亚铁自燃,主要是检修过程中打开设备时,附着于设备表面的硫化亚铁油垢与空气接触,硫化亚铁和氧气发生化学反应,产生自燃。
目前工业上防止硫公亚铁燃烧的方法主要有以下3种:
a) 隔离法:即防止硫化亚铁与空气中的氧气接触,如用氮气保护、水封保护等。
(安全管
理交流)
b) 清洗法:将硫化亚铁从设备上清洗,如对设备进行机械清洗、化学清洗等。
c) 钝化法:用钝化剂进行设备处理,将易自燃的硫化亚铁转变为较稳定的化合物,从而防止硫化亚铁的自燃。
隔离法适用于在线保护,但在检修过程中很难有效防止硫化亚铁的自燃。
钝化法的成本较高,且不能将硫化亚铁从设备上除去。
清洗法包括物理清洗和化学清洗,物理清洗主要是利用特殊机械清洗设备表面垢层;化学清洗有碱洗、酸洗、有机溶剂清洗,以及根据不同结垢采用
的表面活性剂与碱、有机溶剂等组成的混合化学清洗溶液的清洗。
相对而言,清洗法简便有效,
而且成本低,是比较常见的方法。
目前广泛采用的炼化设备的化学清洗,实际上是传统的清洗法与钝化法相结合,即在化学清洗剂中再适当地添加了钝化剂的成份。
石油化工设备上的硫化亚铁,表现为硫化亚铁针对不同设备环境,分别与轻油、重油或焦油混杂在一起,形成的吸附于设备金属表面的含硫化亚铁油垢。
因此,清作设备表面的硫化亚铁,不是简单的清除硫化亚铁,而且要兼顾清除渍垢,以便清除深层的硫化亚铁。
FZC-1型硫化亚铁化学清洗剂,是基于硫化亚铁较高的活性和被螯合能力的原理,由一种
螯合剂加入适当比例的碱、表面活性剂、缓蚀剂等有效成分合成,具有很强的水溶性和分解性,对设备的腐蚀性低。
螯合剂主要用来使硫化亚铁转化为可溶性的氧化铁和硫,并使硫化氢的释放减少;碱的作用一般是脱脂;表面活性剂的作用则是加强螯合剂在油垢层的渗透,有利于深层
硫化亚铁的脱除;缓蚀剂则是在金属表面形成保护膜,这样可以减少设备清洗后,在使用过程
中硫化亚铁的生成,起到对设备的保护作用。
FZC-1硫化亚铁高效化学清洗剂的主要物化性质见表1:
表1 FZC-1 硫化亚铁高效化学清洗剂的技术指标
3.1首次使用
加氢裂化装置有多台换热器处于高H2S浓度工作环境,其中分馏脱戊烷塔顶水冷器介质
中H 2浓度正常达4%(wt),液化气处理单元5台换热器介质中H2S浓度均为100ppm,脱硫单
元的3台换热器介质中湿H2S浓度正常为2.5%(wt)。
极高学H2S导致了严重的设备腐蚀,产
生了大量的的硫化亚铁,每次检修过程中上述换热器都会发生硫化亚铁自燃现象。
2001年大
检查修中,首次使用清洗剂对上述设备进行了化学处理。
3.1.1配量
根据设备上FeS的集结程度,FZC-1化学清洗剂与水按一定比例配量使用,其有效配比范围为11~20。
在本次化学处理中,FZC-1化学清洗剂与水按1:10(剂:水)的配比配量使用。
3.1.2化学处理前的准备工作
为了有效、快速地将加氢裂化装置换热器内集结的硫化亚铁处理干净,提高钝化剂的利用率,缩短清洗时间,根据化学处理方案具体要求,在停工过程中对设备进行了倒空、隔离、高温蒸煮。
3.1.3化学清洗流程
8台大型换热器清洗流程示意简图见图1。
图1 钝化清洗换热器流程图示意图
3.1.4清洗步骤
a) 在装置现场,根据水冷器的流通体积,安10%的溶液浓度准备化学清洗剂;
b)将化学清洗剂在配液槽中与水混合均匀制成10%的溶液;
c)通过加剂泵由临时管线注入换热器,再由换热器上部返回配液槽;
d)循环2~4小时;
e)随着表洗过程的进行,化学清洗剂溶液的颜色逐步变淡,直至无色,此时清洗过程结束。
清洗剂使用情况见表2。
表2清洗剂使用情况一览表
3.1.5废液处理
清洗结束后,对各换热器的化学清洗液最终采样分析,其结果见表3。
表3 清洗污水分析表
由表3可见,该化学清洗剂剂对硫化亚铁有较强的化学清洗效果,废液符合直接排放标准,可直接排放至污水处理场。
3.1.6清洗效果
打开化学清洗后的换热器,换热器管束表面已没有明显的硫化亚铁沉积物;个别硫化亚铁
油垢沉积比较严重的换热器如EA-985,化学清洗后其管束表面的油垢亦已明显减少、松软。
各换热器打开过程中未再出现硫化亚铁自燃的现象,大部分换热器管束表面洁净,有金属光泽,表面钝化层呈现黑褐色,换热器检修过程中未再出现硫化亚铁尘块随风飘扬的现象。
3.2再次使用
2002年5月,加氢装置950#脱硫系统因塔底再沸器EA-958腐蚀严重,再生塔DA-955塔被迫停车消缺,为防止检修中DA-955塔盘及管线出现硫化亚铁自燃现象,厂技术科与加氢裂化车间研究决定再次使用FZC-1硫化亚铁高效化学清洗剂对DA-955塔进行循环清洗。
DA-955循环冲洗流程见图2。
图2 DA-955循环冲洗示意图
3.2.1化学处理范围
a) 再生塔塔釜(是本次清洗的主要对象);
b)再生塔内壁、塔盘、集油箱等塔内构件。
3.2.2化学处理前的准备工作
本次化学清洗安排在停工过程中的两次蒸塔、洗塔进行之后进行,因为此时塔内构件上附着的大部分油泥已被洗掉,药液进入进可以更加充分地与构件进行接触,提高药液利用率,缩短清洗时间。
3.2.3化学清洗流程
冲洗循环液由加剂泵抽出,经DA-955塔顶回流管线进入DA-955,保持DA-955塔底液面
在80%,再由塔釜返回至配液槽进行循环冲洗。
3.2.4钝化步骤
a)错开FC-9527正线截止阀的法兰以及DA-955塔釜至FA-954截止阀的法兰,并分别接上临时软管;
b)将32.5t水加入配液槽中并启动加剂泵入再生塔;
c)当塔底液面L9518为80%时打开DA-955塔釜返回到配液槽的截止阀;
d)将3.25t化学清洗剂加入配液槽;
e)流程改为闭路循环,冲洗4小时;
f)停加剂泵,关DA-955塔釜返回到配液槽的截止阀,浸泡DA-955塔釜12小时。
3.2.5废液处理
FeS钝化剂为红褐色,3.25t钝化剂加入装置系统后循环冲洗水由透明逐渐变为混浊,并产生悬浮物及黑色的微粒,溶液上部有较明显的油迹,对循环溶液采样分析,其结果如表4所示。
表4清洗污水分析表
分析表明污水完全达到向处理场排放的标准。
3.2.6清洗效果
a)开人孔后对塔内气体的分析:氧含量20.17%,含H2S≤5ppm,具备了进塔施工的条件;
b)进入塔内检查,塔盘表面洁净,有金属光泽。
塔内无异味,但集油箱内油泥仍积存较多,后用消防水清洗。
在整个检修过程中,塔内没有出现自燃冒烟的现象,使用FZC-1化学清洗剂达到了预期的清洗效果。
a) FZC-1型硫化亚铁化学清洗剂应用过程简单、快捷,无环保问题;
b) FZC-1型硫化亚铁化学清洗剂防止硫化亚铁自燃效果明显;
c) 石化装置多为载硫工作环境,发生硫化亚铁自燃的现象日趋增多。
加氢裂化装置应用FZC-1型硫化亚铁化学清洗剂,值得借鉴和推广。