钢包回转台的设计说明书
钢包回转台
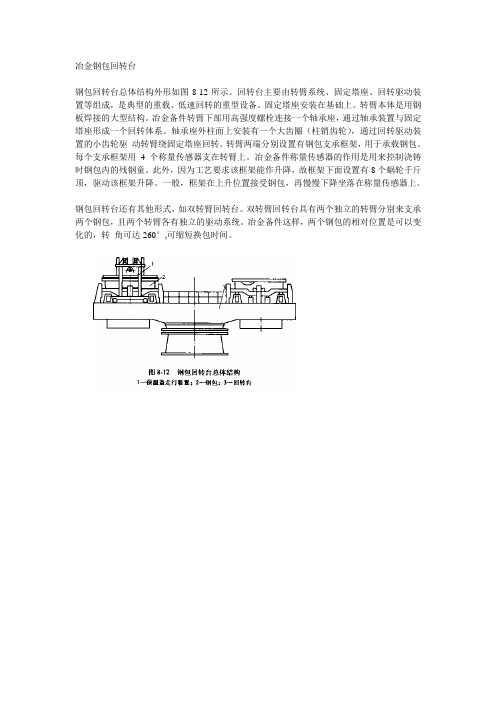
冶金钢包回转台
钢包回转台总体结构外形如图8-12所示。
回转台主要由转臂系统、固定塔座、回转驱动装置等组成,是典型的重载、低速回转的重型设备。
固定塔座安装在基础上。
转臂本体是用钢板焊接的大型结构。
冶金备件转臂下部用高强度螺栓连接一个轴承座,通过轴承装置与固定塔座形成一个回转体系。
轴承座外柱面上安装有一个大齿圈(柱销齿轮),通过回转驱动装置的小齿轮驱动转臂绕固定塔座回转。
转臂两端分别设置有钢包支承框架,用于承载钢包。
每个支承框架用4个称量传感器支在转臂上。
冶金备件称量传感器的作用是用来控制浇铸时钢包内的残钢童。
此外,因为工艺要求该框架能作升降,故框架下面设置有8个蜗轮千斤顶,驱动该框架升降。
一般,框架在上升位置接受钢包,再慢慢下降坐落在称量传感器上。
钢包回转台还有其他形式,如双转臂回转台。
双转臂回转台具有两个独立的转臂分别来支承两个钢包,且两个转臂各有独立的驱动系统。
冶金备件这样,两个钢包的相对位置是可以变化的,转角可达260°,可缩短换包时间。
钢包回转台设计优化
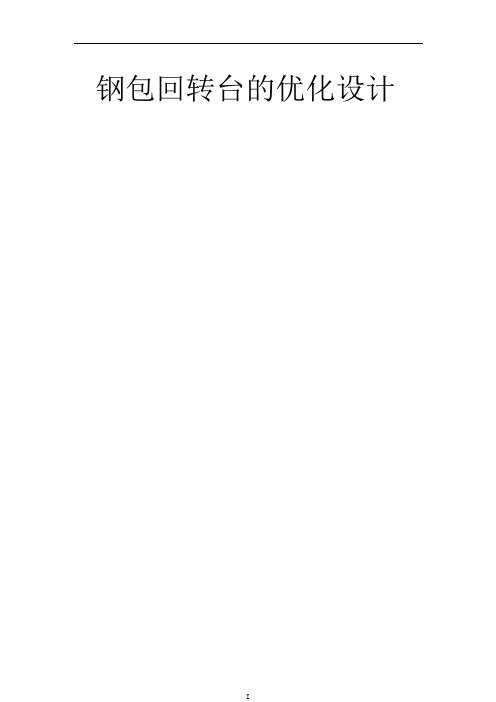
钢包回转台的优化设计摘要钢包回转台是设在连铸机浇注位置上方用于运载钢包过跨和承载钢包进行浇注的设备,是现代连铸中使用最普遍和最常见的承载钢包进行浇钢的关键机械设备。
本文对钢包回转台回转装置进行系统的设计计算,有利于优化大包回转台结构,节约成本,提高经济效益。
本课题主要对回转装置进行相关设计计算,其中包括计算驱动装置功率和电机选型校核、减速器的选型、开式齿轮校核、回转支承的选型和校核及联结螺栓和地脚螺栓的校核等。
通过设计计算,选择了满足使用要求的电动机、减速器及回转支承,对回转支承、联接螺栓和开式齿轮的校核计算表明其性能更是满足使用要求。
为钢包回转台回转装置的设计提供了理论计算的方法。
关键词:钢包回转台回转装置驱动装置电机减速器AbstractLadle Turret in continuous casting machine is pouring position over the top of the ladle used to carry cross and bearing steel casting equipment packages,it is the most commonly used in modern continuous casting and the most common bearing steel ladle for pouring the key machinery and equipment.In this paper, we make a design calculations for the Ladle Turret slewing device system, helping to optimize the large package of turret structure, reduce costs and increase the economic efficiency.This topic is mainly making a design calculation of correlation of Ladle Turret slewer , including the calculation of the drives power , the selection of the electrical machine and electrical machine ,the checking of exposed gear ,the selection and checking of exposed gear ,the checking of coupling bolt and foundation bolt.By design calculations, we chose a requirement motor, and the check calculations of gear and slewing bearings, slewing bearings, bolts and open gear show that its performance meet the requirements. It provides a theoretical calculation methods to design the Ladle Turret.Keywords:Ladle Turret Rotary device drives motor reducer目录摘要......................................................... 错误!未定义书签。
钢包回转台的设计说明书
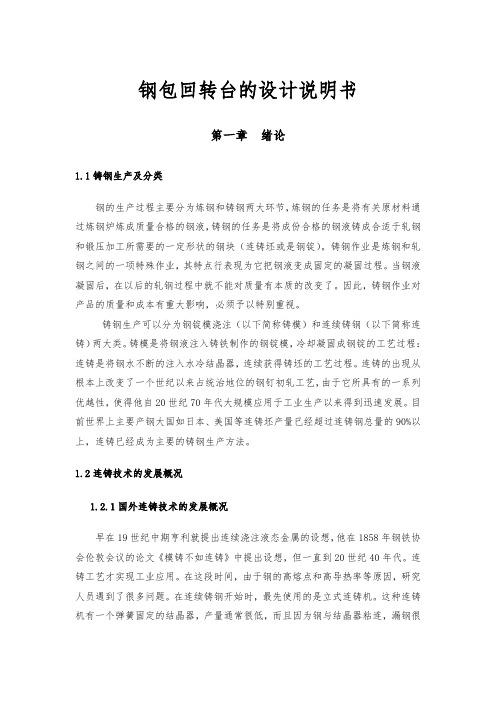
钢包回转台的设计说明书第一章绪论1.1铸钢生产及分类钢的生产过程主要分为炼钢和铸钢两大环节,炼钢的任务是将有关原材料通过炼钢炉炼成质量合格的钢液,铸钢的任务是将成份合格的钢液铸成合适于轧钢和锻压加工所需要的一定形状的钢块(连铸坯或是钢锭)。
铸钢作业是炼钢和轧钢之间的一项特殊作业,其特点行表现为它把钢液变成固定的凝固过程。
当钢液凝固后,在以后的轧钢过程中就不能对质量有本质的改变了。
因此,铸钢作业对产品的质量和成本有重大影响,必须予以特别重视。
铸钢生产可以分为钢锭模浇注(以下简称铸模)和连续铸钢(以下简称连铸)两大类。
铸模是将钢液注入铸铁制作的钢锭模,冷却凝固成钢锭的工艺过程:连铸是将钢水不断的注入水冷结晶器,连续获得铸坯的工艺过程。
连铸的出现从根本上改变了一个世纪以来占统治地位的钢钉初轧工艺,由于它所具有的一系列优越性,使得他自20世纪70年代大规模应用于工业生产以来得到迅速发展。
目前世界上主要产钢大国如日本、美国等连铸坯产量已经超过连铸钢总量的90%以上,连铸已经成为主要的铸钢生产方法。
1.2连铸技术的发展概况1.2.1国外连铸技术的发展概况早在19世纪中期亨利就提出连续浇注液态金属的设想,他在1858年钢铁协会伦敦会议的论文《模铸不如连铸》中提出设想,但一直到20世纪40年代。
连铸工艺才实现工业应用。
在这段时间,由于钢的高熔点和高导热率等原因,研究人员遇到了很多问题。
在连续铸钢开始时,最先使用的是立式连铸机。
这种连铸机有一个弹簧固定的结晶器,产量通常很低,而且因为钢与结晶器粘连,漏钢很常见。
振动结晶器的想法归功于德国人seigfried,他首创了有色金属的连续铸造,与1952年用于德国的钢铁厂的直结晶器立式连铸机上,这是连铸工业化规模的开始。
由于技术的限制多年只应用于小工厂,自1970年开始连铸开始应用于钢铁联合企业来生产板坯。
1.2.2我国连铸技术的发展概况我国是研究和应用连铸技术较早的国家之一,早在20世纪50年代就开始探索性的工作,60年代初进入到连铸技术工业应用阶段。
钢包回转台介绍
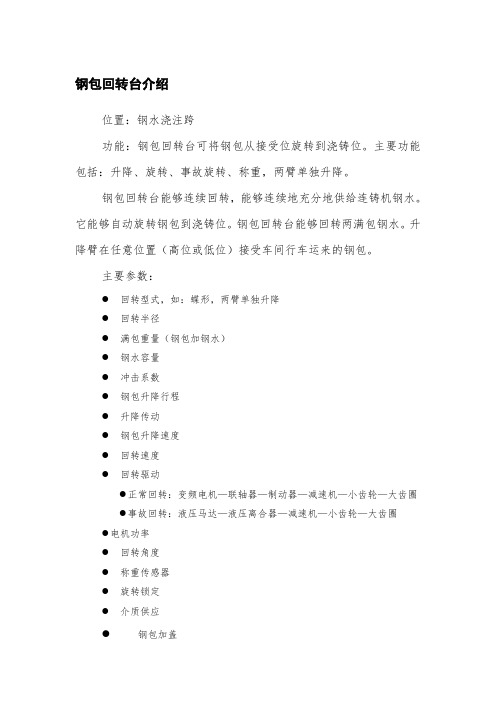
钢包回转台介绍位置:钢水浇注跨功能:钢包回转台可将钢包从接受位旋转到浇铸位。
主要功能包括:升降、旋转、事故旋转、称重,两臂单独升降。
钢包回转台能够连续回转,能够连续地充分地供给连铸机钢水。
它能够自动旋转钢包到浇铸位。
钢包回转台能够回转两满包钢水。
升降臂在任意位置(高位或低位)接受车间行车运来的钢包。
主要参数:●回转型式,如:蝶形,两臂单独升降●回转半径●满包重量(钢包加钢水)●钢水容量●冲击系数●钢包升降行程●升降传动●钢包升降速度●回转速度●回转驱动●正常回转:变频电机—联轴器—制动器—减速机—小齿轮—大齿圈●事故回转:液压马达—液压离合器—减速机—小齿轮—大齿圈●电机功率●回转角度●称重传感器●旋转锁定●介质供应●钢包加盖设备组成:钢包回转台主要由底座、回转轴承、回转体、塔座、升降臂、升降液压缸、鞍座、传动装置、称重装置、旋转锁定装置、旋转接头、电气滑环、钢包滑动水口液压缸吊挂装置、防护罩及楼梯、机上配管等组成。
底座由钢板焊接而成,安装在混凝土基础上。
底座的上部安装回转轴承。
回转轴承是大直径、三排滚子回转轴承,带外齿圈。
轴承由高强度螺栓安装在底座和回转体之间。
回转体是由钢板焊接而成,安装在回转轴承上。
塔座安装在回转体上,与回转体一起回转。
升降臂通过销轴支撑在回转体和塔座上。
钢包加盖装置也安装在塔座上。
升降臂由钢板焊接而成,升降臂通过销轴与塔座和鞍座连接。
每个臂独立升降,由液压油缸驱动。
驱动和控制允许每个钢包独立或者两个钢包同时升降。
一个钢包的升降是满速升降;两个满包同时的升降是半速。
钢包升降装置采用液压缸升降,每个臂单独升降。
鞍座是钢板焊接结构,与升降臂间通过销轴连在一起,鞍座上安装有称重传感器。
传动装置安装在混凝土基础上,正常传动通过变频电机-减速机-小齿轮—大齿圈-回转体传动。
事故传动通过液压马达、液压离合器、带动减速机-小齿轮—大齿圈-回转体的方式传动。
主驱动在正常情况下可以使2个满包以1r/min速度旋转1圈。
论述蝶式钢包回转台设计
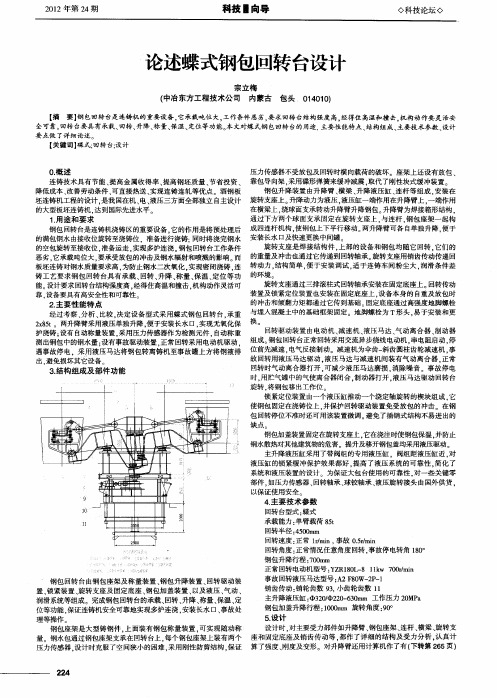
要 点做 了详 细论 述 。
【 关键词 】 碟式; 台; 回转 设计
压力传感器不受放包及 回转 节能 、 提高金 属收得率 、 提高 钢坯 质量 、 节省 投资 、 靠包导 向架 , 碟形弹簧来缓 冲减震 , 采用 取代 了刚性块式缓 冲装置 。 降低成本 、 改善劳动条件 、 可直接热送 、 实现连铸 连轧等优点。酒钢板 钢包升降装置 由升降臂 、 横梁 、 升降液压缸 、 连杆等 组成 . 安装在 坯连铸机工程 的设计 , 是我国在机、 液压三方 面全 部独立 自主设 计 旋转支座上。 电、 升降动力 为液压 , 液压缸一端作用在升降臂上 . 端作用 一 在横粱上 , 绕球面支承转 动升降臂升降钢包。 升降臂为焊接箱形结构 . 的大 型板坯连铸机 . 达到 国际先进水平 通过下方两个球 面支承固定在旋转 支座上 . 与连杆 . 钢包座架一起构 1用 途 和要 求 . 使 两升降臂可各 自单独升降 . 于 便 钢包 回转 台是连铸机浇铸区的重要设备 . 它的作 用是将 预处理后 成 四连杆机构 . 钢包上下平行移动 。 安装长水 口及快速更换 中间罐 的满包钢水 由接收位旋转至浇铸位 .准备进行浇铸: 同时将 浇完钢水 旋转支座是焊接 结构件 , 上部 的设 备和钢包均 随它回转 . 它们 的 的空包旋转至接收位 , 准备运走 。 实现多炉连 浇。 钢包 回转 台工作条件 旋转支座用销齿传 动传递 回 恶劣 , 承载吨位大 , 它 要承受放包的冲击及钢水辐射 和喷溅 的影响。 而 的重量及冲击也通过它传递 到回转轴承 。 结构简单 , 于安装调试 , 于连铸车间粉尘 大 . 便 适 润滑条件差 板坯连铸对钢水质量要求高 , 为防止钢水 二次 氧化 . 实现密闭浇铸 。 连 转动力 , 铸工艺要求 钢包 回转 台具有承 载、 回转 、 升降 、 量 、 称 保温 、 定位等 功 的环境 。 旋转支座通过三排 滚柱式 回转轴承安装在固定底座上 。 回转传动 能。 设计要求 回转 台结构强度高 , 经得住 高温和撞击 , 机构动作灵活可 装置及锁紧定位装置也 安装在 固定底座上 . 设备本身 的自重及放包 时 靠。 设备要具有高安全性和可靠性 的冲击和倾翻力矩都通 过它传 到基础 固定底座通过高强度地脚螺栓 2主 要 性 能特 点 . 易于安装和更 经过考 察 、 分析 、 比较 , 决定设备型式采用蝶 式钢包 回转 台 , 承重 与埋人混凝土中的基础 框架 固定 。地脚螺栓为 T形头 。 换。 28 t x5 。两升降臂采用液压单独升降 , 于安装长水 口. 便 实现无氧化保 回转驱动装置 由电动机 、 减速机 、 液压马达 、 动离 合器 、 气 制动器 护浇铸 ; 设有 自 动称量装置 , 采用压力传感器作 为检测元件 , 自动称重 钢包 回转台正常回转采用交流异步绕线 电动机 . 串电阻启 动. 停 测出钢包 中的钢水量 ; 设有事故驱动装置 , 正常回转采用电动机驱动 , 组成 。 位前先减速 , 电气反接制 动。减速机为伞齿一 斜齿 圆柱齿轮减速机 . 事 遇事故停 电.采用液 压马达将钢包转离铸 机至事故罐上方 将钢液排 故 回转用液压 马达 驱动 . 液压 马达与减速机间装有气 动离合器 . 常 正 出. 损坏其它设备 避免 回转 时气动离合器 打开 , 可减少 液压 马达磨损 , 消除 噪音。事故停 电 3结 构 组 成 及部 件 功 能 . 时, 用贮气罐中的气使离 合器闭合 , 制动器打开 . 液压 马达驱动 回转台 旋转 , 将钢包移出工作位 。 锁紧定位装置由一个液压 缸推动一个绕定轴旋转 的楔块组成 . 它 使钢包 固定在浇铸位上 , 并保护 回转驱动装置免受放包 的冲击 。在钢 包 回转停位不准时还可用该装 置微调 避免 了插销式结构不易进出的 缺点 。 钢包加盖装置固定在旋转支座上 . 它在浇注时使钢包保温 . 并防止 钢水散热对其他建筑物的危害 。提升及移开钢包盖均采用液压驱动。 主升降液压缸采用了带 I 阋组的专用液压缸 .阀组距液压缸 近. 对 液压缸 的锁 紧缓 冲保护效果都好 . 提高了液压系统 的可靠性 . 简化 了 系统和液压装置的设计。为保 证大包 台使用 的可靠性 。 对一些关键零 部件 , 如压力传感器 、 回转轴承、 铰轴承 、 球 液压旋转接头 由国外供 货 , 以保证使用安全
连铸钢包回转台安装方案(优.选)

**连铸机钢包回转台安装施工作业设计批准日期审核日期编制日期**公司2002/10/21目录1、编制依据2、工程概况2.1工程内容2.2相关条件2.3工程特点3、安装程序3.1安装流程3.2测量放线3.3底座吊装就位3.4、旋转套筒及旋转臂和其它部件的安装3.5底座找正作业操作要领3.6吊装注意事3.7吊具的强度计算4.工期计划4.1工期网络计划4.2工期控制措施4、质量方针和目标5.1质量方针5.2质量目标5.3质量保证措施5.4质量管理组织5、施工组织6、安全管理7.1安全目标7.2安全措施7.3安全管理组织8.机具及材料9.附图1、编制依据本施工作业设计编制主要依据下列技术资料1)《冶金机械设备安装工程质量检验评定标准》:连续铸钢设备,冶金工业出版社,YB 9244-922)梅钢发放的安装图与转化图3)奥钢联提供的安装说明书4)《冶金机械设备安装工程施工及验收规范》YBJ 202-835)《工程测量规范》GB50026-936)《建筑施工高处作业安全技术规范》JBJ80-917)《建筑工程施工现场供用电安全规范》GB 50194-938)《建筑机械使用安全技术规程》JBJ33-869)《工业设备、管道焊接工程施工及验收规范》GBJ236-822、工程概况2.1工程内容本施工作业设计主要包括下列内容永久基准点和中心标板的埋设;钢包回转台底座的安装与找正;旋转体的安装;两只旋转臂的安装及旋转臂升降装置的安装;旋转驱动装置安装;钢包加盖装置的安装等。
**连铸机的钢包回转台由底座(11.3t)、旋转体(40t)、旋转臂(47.7t)、旋转臂升降装置(16.5t)、上连杆(26.5t)、下连杆(6.4t)、钢包加盖装置、旋转驱动装置等机械部件组成;总重215 .32T。
该钢包回转台位于厂房③线-④线的L列行车轨道梁之下,吊装位置极其困难;其底座基础标高为+10.847m,行车梁隔热板下表面标高为+22.015m。
回转工作台设计说明书

镗铣加工中心系统设计镗铣加工中心数控回转工作台设计学 校: 昆 明 理 工 大 学专 业: 机械工程及自动化班 级: 2008级3班学生姓名: 代 祖 民指导教师: 彭 用 新教师单位: 机电工程学院教师职称: 讲 师时 间: 2012年6月The Design of Boring Milling MachiningCenter SystemSubtitle:The NC Rotary T able Design for Boring MillingMachining CenterUniversity: Kunming University of Science and Technology Major: Mechanical Engineering and Automation Grade: Grade 2008 Name: Dai Zumin Advisor: Peng Y ongxin Department: Mechanical and Electrical Engineering Date: June 2012目录摘要 (1)ABSTRACT (2)前言 (3)第1章 数控机床概述 (5)1.1 数控机床的基本概念 (5)1.1.1 什么是数控机床 (5)1.1.2 数控机床的产生 (5)1.2 数控机床的发展史 (6)1.2.1 数控机床的发展 (6)1.2.2 发展数控机床的原因及特点 (7)1.3 国内外数控技术发展现状和趋势 (9)1.3.1 高精度化 (9)1.3.2 高可靠性 (9)1.3.3 高柔性化 (10)1.3.4 复合化 (10)1.3.5 高速度化 (10)1.3.6 制造系统自动化 (11)第2章 数控机床的机械结构 (12)2.1 数控机床的构成及分类 (12)2.1.1 数控机床的构成 (12)2.1.2 功能及特点 (12)2.2 数控机床的分类 (14)2.2.1 按控制系统的特点分类 (14)2.2.2 按执行机构的伺服系统类型分类 (15)2.2.3 按数控装置类型分类 (16)2.2.4 按功能水平分类 (18)2.3 典型的数控机床 (19)2.3.1 数控车床 (19)2.3.2 数控铣床 (19)2.3.3 数控模仿形铣床 (20)2.3.4 加工中心 (21)2.3.5 数控钻床及镗床 (21)2.3.6 数控磨床 (22)2.3.7 数控电加工机床 (22)2.3.8 数控重型机床 (23)第3章 数控回转工作台 (24)3.1 五轴联动机床简介及加工特点 (24)3.1.1 简介 (25)3.1.2 加工特点 (25)3.2 五轴联动机床的结构类型 (26)3.2.1 依靠立式主轴头的回转 (27)3.2.2 依靠回转工作台的回转 (27)3.2.3 分度工作台 (28)3.3 数控回转工作台 (28)3.3.1 开环数控回转工作台 (28)3.3.2 闭环数控回转工作台 (29)第4章 回转工作台的设计及计算 (30)4.1 传动方案的分析 (30)4.1.1 方案的确定 (31)4.2 电动机的选择 (32)4.2.1 各轴的转动惯量和回转工作台的转动惯量 (32)4.3 斜齿圆柱齿轮的传动设计及计算 (33)4.3.1 第一对齿轮啮合的计算 (33)4.3.2 其他齿轮的相关参数值 (38)4.4 输出轴与轴承的校核 (39)4.5 齿轮上键的选取与校核 (43)4.5.1 取键连接的型号尺寸 (43)4.5.2 键连接的强度 (43)4.6 轴承的设计 (43)4.6.1 滚动轴承的结构 (43)4.6.2 滚动轴承的作用 (43)4.6.3 滚动轴承的性能 (44)4.6.4 滚动轴承类型的选择 (44)4.6.5 轴承的拆装 (45)4.6.6 轴承的润滑 (45)4.6.7 轴承的游隙及轴上零件的调配 (45)4.6.8 滚动轴承的配合 (46)第5章 结论 (47)结论与心得 (48)谢辞 (49)参考文献 (50)附录 (51)外语文献 (51)中文翻译 (52)摘要数控机床已经用它所显示的效益和巨大的潜力,引起了世界各国科技界和工业界的普遍重视。
150t炼钢连铸的钢包回转台设计

毕业设计说明书150t 炼钢连铸的钢包回转台设计源设计图纸请联系本人,参见豆丁备注。
毕业生姓名:专业:机械设计制造及其自动化学号:指导教师:所属系(部):机械电子工程系二〇一四年六月摘要钢包回转台是现代炼钢连铸生产中的主要设备之一,其作用是支撑和运载钢包进行浇铸,为实现多炉连浇创造了条件。
钢包回转台是连续铸钢设备中负荷最大、体积最大的焊接件。
它的主要组成部分是回转臂、推力轴承及塔座三部分。
为了安全运转,要求他的各个零部件有足够的强度和刚度。
本设计说明书是以江苏省镔鑫特钢材料有限公司炼钢厂的连铸车间方坯连铸机的钢包回转台为借鉴,以蝶式钢包回转台为形式进行的设计。
主要内容包括:钢包回转台传动方案的设计,回转台的结构尺寸的确定,主要零件的选择、计算与校核;电动机、减速器的选择与计算,以及钢包升降装置、称量装置、加盖装置的设计,此外,还介绍了部分主要零件具体的安装、维修、润滑、操作方法。
关键词:连铸;蝶式钢包回转台;传动方案;回转台结构尺寸。
AbstractThe ladle turret is one of the main casting equipments.Principal affect is supporting ladle and carrying to operation. For continue us casting invent a condition that working with many ladles.The ladle turret is the most load and volume jointing part in the casting equipments. It's making up of revolving arm,thrust-axletree,foundation. For the safety, needing every parts have enough intensity and rigidity.To take a basis of the dishing ladle helicoid dado for the square-circle castings BinXin Steel Iron Works. This direction is involved in many respects including drive scheme device ,Construvtion and size of helicoid dado, main pare parts calibration, motor, reduction gear, aircylinder, and ladle lifting device, locking device, weighing device, cove lifting device, elicit introduced about the concert install, lubrication and operation.Key words: casting equipment,dishing ladle helicoid dado, drive scheme, helicoid dado configurable.目录摘要 (II)Abstract (III)1 绪论 (1)1.1 国内外连铸机术的发展及我国与世界连铸技术的差距 (1)1.2 连铸机的主要设备及分类 (3)1.3 连铸机钢包旋转 (7)1.3.1 钢包旋转台的形式 (7)1.3.2 钢包旋转台的主要结构特点 (8)1.3.3 各类连铸机钢包回转台的特点 (9)1.4 钢包回转台的组成 (11)1.5 钢包回转台的工作特点 (12)2 初步确定方案 (13)2.1 已知条件 (13)2.1.1 设计题目 (13)2.1.2 技术参数及性能 (13)2.2 方案的总体布置形式 (13)2.3 回转台具体部件设计方案的确定 (13)2.3.1 钢包旋转驱动方式 (13)2.3.2 锁紧方式 (14)2.3.3 钢包盖的升降装置 (15)2.3.4 长水口机械手动作方式 (15)2.3.5 钢包升降驱动方案 (15)3 电机的计算与选择 (17)3.1钢包回转功率的计算 (17)3.1.1 基本数据的计算 (17)3.1.2 情况Ⅰ的回转功率计算 (19)3.1.3 情况Ⅱ的回转功率计算 (19)3.1.4 情况Ⅲ的回转功率计算 (20)3.2 电动机和电气马达的选择 (21)3.2.1 电动机的选择: (21)3.2.2马达的选择 (22)3.3 减速器的设计 (22)3.3.1 确定减速器的结构 (22)3.3.2 传动比的计算和分配,计算传动装置的运动和动力参数 (23)3.3.3 齿轮的设计 (24)3.3.4 轴的设计 (30)3.3.5 减速器箱体的结构尺寸 (39)4 回转台主要构件分析 (40)4.1 对回转臂进行分析 (40)4.2 滚柱回转支承 (40)4.2.1 径向滚柱的分析 (41)4.2.2 轴向滚柱的分析 (42)4.3 地脚螺栓设计与计算 (43)4.3.1 选择材料 (43)4.3.2 确定螺栓的基本数据 (43)5 销齿传动的设计与计算 (45)T (45)5.1 销轮轴转矩35.2 选材及许用应力的确定 (45)5.2.1 材料的选择 (45)5.3 销齿直径确定 (46)5.4 校核齿轮弯曲强度 (47)5.5 确定尺寸 (47)6 钢包旋转台的加盖装置的设计 (48)7 称量传感器的形式选择与容量计算 (49)8 地脚螺栓的设计与计算 (50)8.1 选材及尺寸确定 (50)8.2 螺栓工作负荷的确定 (50)9 钢包回转台设备安装、使用和维护 (52)9.1 一些设备的安装 (52)9.1.1 滚柱旋转轴承的使用方法以及安装 (52)9.1.2 提升缸的安装与拆卸 (52)9.2 钢包回转台的使用和维护 (52)总结 (54)参考文献 (55)外文资料 (56)中文翻译 (61)致谢 (65)1 绪论1.1 国内外连铸机术的发展及我国与世界连铸技术的差距把高温钢水连续不断地浇铸成具有一定断面形状和一定尺寸规格铸坯的生产工艺过程叫做连续铸钢。
钢包回转台
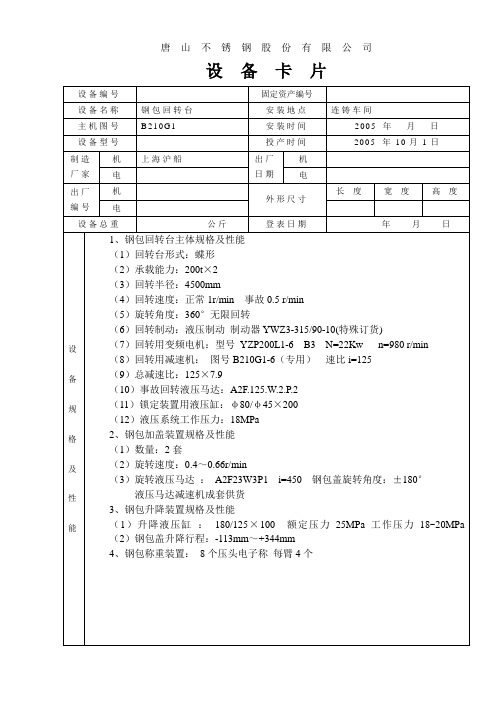
(3)回转半径:4500mm
(4)回转速度:正常1r/min事故0.5 r/min
(5)旋转角度:360°无限回转
(6)回转制动:液压制动制动器YWZ3-315/90-10(特殊订货)
(7)回转用变频电机:型号YZP200L1-6 B3N=22Kw n=980 r/min
唐山不锈钢股份有限公司
设备卡片
设备编号
固定资产编号
设备名称
钢包回转台
安装地点
连铸车间
主机图号
B210G1
安装时间
2005年月日
设备型号
投产时间
2005年10月1日
制造厂家
机
上海沪船
出厂日期
机
电
电
出厂编号
机
外形尺寸
长度
宽度
高度
电
设备总重
公斤
ቤተ መጻሕፍቲ ባይዱ登表日期
年月日
设
备
规
格
及
性
能
1、钢包回转台主体规格及性能
(1)回转台形式:蝶形
(3)旋转液压马达:A2F23W3P1i=450钢包盖旋转角度:±180°
液压马达减速机成套供货
3、钢包升降装置规格及性能
(1)升降液压缸:180/125×100额定压力25MPa工作压力18~20MPa(2)钢包盖升降行程:-113mm~+344mm
4、钢包称重装置:8个压头电子称每臂4个
关键备件目录
B210G1-13
φ540×370
2
Ps=20MPa
7
8
9
10
11
12
13
14
15
钢包回转台的设计计算

重 工 与 起 重 技 术
HEAVY INDU Srm IAL& HOIS,I1ING MACHINERY
式 中 : 承上面设备 自重 ;
G —A 侧座包 总重量 ; G厂-B侧钢包总 重量 ; K一 座包 冲击 系数 。 (4)径 向载荷
= G ×K  ̄/3 式 中 :
摘 要 :简要介绍 了钢包 回转台的作用、主要技术参数 的确 定及部分机构 的设计计算 。 关键 词 :钢 包 回转 台 ·承 载 能 力 ,回转 ,升 降
1 概 述
钢包 回转 台是连铸机生 产线的大型关键 设备之 一 , 安装在 连铸 车间钢水接受跨 和连铸跨之 间的浇 铸平 台上 ,用于接受炼 钢系统送来 的盛 满钢水 的钢 包 ,将钢包 转至连铸跨的浇注位置进行浇 注。当钢水 浇注 结束后 ,经设备旋转将 空钢包送 回炼钢 跨 ,同时 将 新 的盛 满钢水 的钢包送到 连铸 跨 ,从 而保 证连铸 机 连续浇注生产 。
(3)配 合 150t转 炉 ,回转 半 径参 数 值 通 常 采 用
5300~ 5800mm {
(4)配合 120t转 炉 ,回转半 径 参 数 值 通 常 采 用
5000~ 5500mm 。
3 t/l, ̄和部件设计计算
钢包 回转 台由回转部分 、固定部分 、润滑 系统和 电控系统所组成。
G 座包总 重量 ; 包轴 向冲 击系数 ,取 K=2;
_ 座包径 向冲击系数 ; 当采用插销 式定位时 ,取 = 150/o{ 当采用摩擦 式定位时 ,取 J8= 1 O%。 (5)倾 翻力矩 M =(G ×K-Gb)×R 式 中: 尺一 回转 半径 。 (6)综合 载荷校核 三排 滚柱 回转 支撑轴承综合 载荷 的校 核 ,按照轴 承 生产厂家提供 的各种规 格轴承 载荷 曲线 图进行 ,横 坐 标为轴 向载荷 ,竖坐标为 倾翻力 矩 。分 别将各种 工 况情 况下不 同冲击系数 的计算值 交点列于 曲线 图上 , 所 有点 处于 该规格 轴 承综合 曲线值 下面则 为计 算 校 核 通过 。 3.2 回转 传动计算 (1)回转 体与减速机传动 回转 体与减速机 采用开式齿 轮或齿销 传动 ,开 式 齿 轮和齿销传动 计算详见相 关设 计手册 。 ① 开式齿 轮传动 大齿 轮通常与 回转大轴承外环 连为一 体 ,小齿 轮 则 安装在减速机 输 出轴上 。开 式齿 轮啮合 应采用大侧 隙传动 ,为 方便 减速机 维护 安装 ,通常 在大 齿 轮和小 齿 轮之间加一过 渡齿 轮 。 ② 齿销传动 销 轮通常与 回转体相 连 ,齿轮则安 装在 减速 机输 出轴 上。 当减速机 底座 与 回转 体底座基 础分离 时 ,应 校 核 由 回转 大轴 承综合 间 隙等原 因引起 的齿销 传动 侧隙是否满足使 用要求。 (2)传动功率 确定 回转 台传动功率计算 过程 比较复杂 ,其 中最 大 的 影响因素是 回转大轴 承综合摩擦 系数 ,由于供货 厂家 不 同,其 综合摩擦 系数 变化范 围为 0.o03 ̄o.007。 目 前 ,传动功率确 定大 多根据 以往经验 采用 比照法 ,考 虑回转大 轴承供货厂 家等 因素进行设计 。以下简要介
一种钢包回转台称重装置的设计
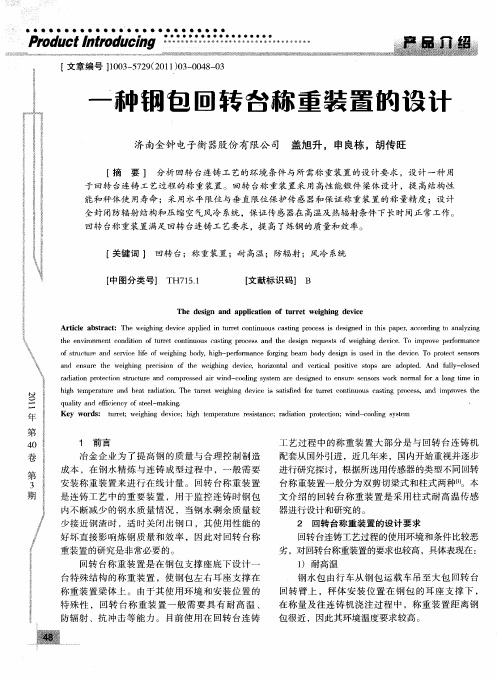
《 钢锻 件 超声 波检 验 方法》 Ⅱ级 l 2 I 。
回转 台称 重装 置 的承重 梁 的主要 受 力状 态 为垂
回 转 台称 重 装 置 安 装 在 回转 台 的 回 转 臂 上 ,
其安 装 空问受 到 回转 臂 承载 部分 尺寸 的限制 。 3 回转 台称重 装 置 S S 1 0 GD的设计 C 一 一 5
S S 10 G C 一 5 一 D采 用实 体 梁结 构 设计 ,提 高承 重梁 的 强 度 和 韧 性 来 克 服 钢 包 上 秤 时 的 冲 击 力 。实 体 梁
结 构 的 毛 坯 一 般 分 为 板 材 和 锻 件 两 种 , 而 根 据
析 如 图 3所 示 ,其 中 ,变 形 曲 线 的 比 例 为 10 : 00
于 回转 台连 铸 工 艺 过 程 中 对 钢 包 内钢 水 质 量 的控
厂 ]
L
S
F
制 ,提 高炼 钢质 量 和效 率 。 回转 台称 重 装 置 S S 10 G 由两 个 称 重 箱 C 一 5一 D
( 图 1 组 成 。托块 为钢 包 上 秤 后 耳 座 的接 触 位 如 )
针对 耐 高 温 称 重计 量 研 发 设 计 的 ,一 直 在 湘 潭 钢 铁 集 团使 用 ,在 回转 台连 铸 工艺 等 高 温 、恶 劣 环
1 重梁 2 接耳 3 一称 一连 一导 向装 置 4 一托 块 5 一高 强 度 套 6 一限 位 轴 I7 一支 撑 梁
8 一限位轴 Ⅱ9 一回转臂 1一耐高温传感器 1 一风冷系统 l一保护罩 0 l 2
图 1 称重箱
2 防辐射 )
S S 10 G C 一 5 一 D称 重装 置 的 使用 环境 和 使 用频 率 ,要 求 实 体 梁 具 有 较 高 的强 度 和 韧 性 。根 据 成 型 ] 艺 一 的特 点 ,锻 件 较 板 材 的结 构 性 能 更 适 合 于 回转 台
60t钢包回转台设计3
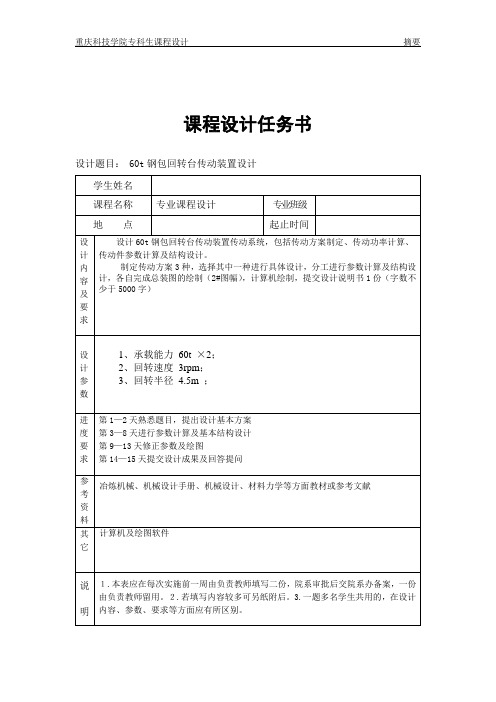
课程设计任务书设计题目:60t钢包回转台传动装置设计学生姓名课程名称专业课程设计专业班级地点起止时间设计内容及要求设计60t钢包回转台传动装置传动系统,包括传动方案制定、传动功率计算、传动件参数计算及结构设计。
制定传动方案3种,选择其中一种进行具体设计,分工进行参数计算及结构设计,各自完成总装图的绘制(2#图幅),计算机绘制,提交设计说明书1份(字数不少于5000字)设计参数1、承载能力60t ×2;2、回转速度3rpm;3、回转半径4.5m ;进度要求第1—2天熟悉题目,提出设计基本方案第3—8天进行参数计算及基本结构设计第9—13天修正参数及绘图第14—15天提交设计成果及回答提问参考资料冶炼机械、机械设计手册、机械设计、材料力学等方面教材或参考文献其它计算机及绘图软件说明1.本表应在每次实施前一周由负责教师填写二份,院系审批后交院系办备案,一份由负责教师留用。
2.若填写内容较多可另纸附后。
3.一题多名学生共用的,在设计内容、参数、要求等方面应有所区别。
目录摘要…………………………………………………………………………………1 绪论……………………………………………………………………………………………1.1盛钢桶的发展史…………………………………………………………………1.2传动装置的总体设计……………………………………………………………1.2.1传动装置的组成方……………………………………………………………1.2.2传动方案的确定…………………………………………………………………2直齿圆锥齿轮设计…………………………………………………………2.1 第一级传动齿轮的设计……………………………………………………2.2 第二级传动齿轮的设计……………………………………………………3 轴的设计3.1 传动第一级轴的设计………………………………………………………3.2 传动第二级轴的设计………………………………………………………3.3 传动第三级轴的设计………………………………………………………4 轴上键的选取5 设备的安装与维护6 心得体会7 参考文献摘要炼钢炉练出的连铸用合格钢水装入盛钢桶,经吹气调温或真空脱气处理后,由盛钢桶运载设备送至连铸机浇铸平台。
毕业设计-钢包回转台联接螺栓的有限元分析
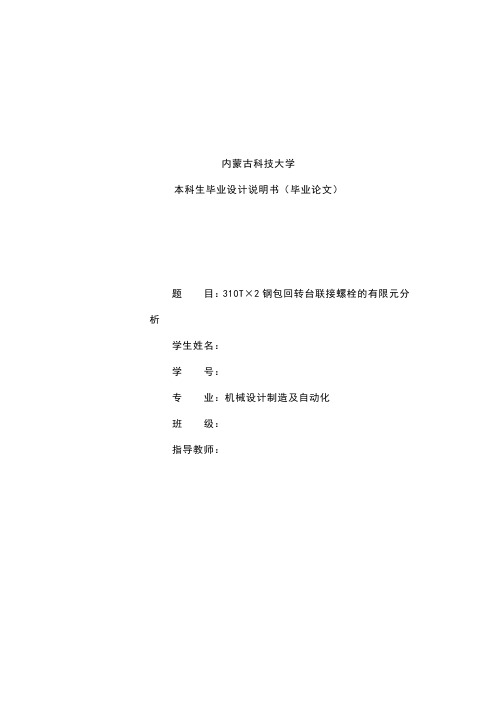
内蒙古科技大学本科生毕业设计说明书(毕业论文)题目:310T×2钢包回转台联接螺栓的有限元分析学生姓名:学号:专业:机械设计制造及自动化班级:指导教师:目录中文摘要Abstract第一章绪论1.1现代连铸机的结构特征1.2钢包回转台的组成1.3钢包回转台的基本形式1.4钢包回转台回转支承存在的问题1.5三排滚柱式回转支承的形式与特点1.6钢包回转台的载荷特点1.7钢包回转台的工作原理及工艺流程第二章钢包回转台的载荷参数及螺栓受力计算2.1 钢包回转台的载荷参数2.2 钢包回转台各种工作状况分析2.3 钢包回转台基础载荷和螺栓受力计算2.3.1钢包回转台联接螺栓承载能力的计算2.3.2钢包回转台联接螺栓的最大工作外负载2.3.3回转支承联接螺栓的预紧力Py及预紧扭矩My 2.3.4计算钢包回转台联接螺栓的疲劳强度的安全系数2.3.5对于三排滚柱式回转支承安装螺栓承载能力的计算第三章钢包回转台联接螺栓受力分析的方法3.1 有限元方法的发展3.2 有限元法分析的一般步骤3.2.1 结构离散化3.2.2 单元分析3.2.3 整体分析3.3 ANSYS软件的介绍3.4 ANSYS有限元分析的典型步骤3.4.1 建立有限元模型3.4.2 加载和求解3.4.2.1定义分析类型和设置分析选项3.4.2.2施加载荷3.4.2.3选择求解方法2.4.3结果后处理3.4.3 结果后处理第四章钢包回转台联接螺栓的有限元分析4.1 实体模型的建立4.2 有限元模型4.2.1 设置单元属性4.2.2.1选择单元类型4.2.2.2设置单元实常数4.2.2.3设置材料属性4.3 实体模型的网格划分4.4载荷及约束的施加结束语致谢参考文献摘要本设计题目是310T*2钢包回转台联接螺栓的有限元分析。
目标是利用ANSYS 软件进行对钢包回转台联接螺栓进行有限元分析。
对钢包回转台底座选用了三排滚柱式回转支承,同时介绍三排滚柱式回转支承的原理、选型方法与计算。
连铸连轧生产:钢包及钢包回转台
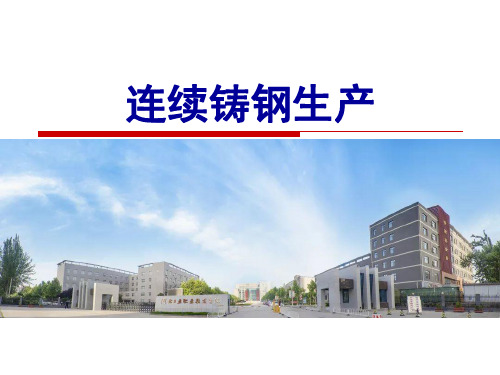
2.2.2钢包回转台
3 钢包回转台主要参数,主要包括承载能力、回转速度、
回转半径、升降行程、升降速度等
型式 单臂承载 双侧承载 旋转半径 主驱动 事故驱动 旋转速度 旋转角度 提升高度 提升速度 称重设备 供电方式 锁紧装置
为了减少钢包浇注末期剩余钢水量,钢包底部设计成向水 口方向倾斜3%~5%,或者设计成阶梯型包底。
1 钢包容量以及尺寸形状确定
正常出钢量
1 钢包容量以及尺寸形状确定
钢包主要系列参数
容量/t
容积 /m³
金属 包衬 总重/t 部分 重量/t 重量/t
上部 直径 /mm
25 4.65 6.64 4.89 11.53 2140 50 9.16 15.47 6.75 22.22 2695 90 15.32 18.69 16.40 35.09 3110 130 20.50 29.00 16.50 45.5 3484 200 30.80 40.60 29.00 69.60 3934 260 40.20 47.50 32.00 79.50 4450
2 钢包的结构 (9)钢包内衬,由保温层、永久层和工作层组成。
正在砌筑中的钢包
已经砌筑好的钢包内衬
2.2.1 钢包
3 钢包清理操作 一炉钢水浇注完毕后,钢包
需要进行清理后才能再次使用, 具体作业过程包括以下几方面:
(1)首先将钢包内剩余的钢 水及残渣倒尽
(2)钢包横卧,清理包口冷 钢残渣以及包底冷钢
(2)加强箍,为了保证钢包的坚固性和刚度,防止变形, 在钢包外壳焊有加强箍和加强筋。
(3)耳轴,在钢包两侧各装一个耳轴,用于天车调运钢包 ,为了保证钢包在吊运、浇注过程中保持稳定,耳轴位置一般 比钢包满载时重心高200~400mm。
连铸钢包回转台安装方案
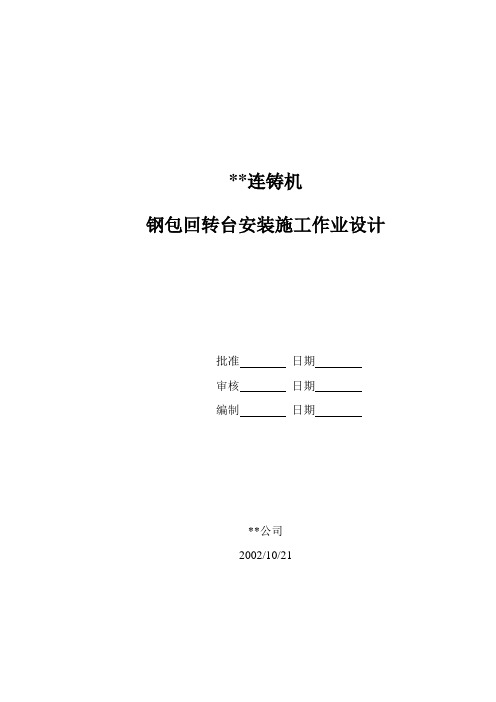
**连铸机钢包回转台安装施工作业设计批准日期审核日期编制日期**公司2002/10/21目录1、编制依据2、工程概况2.1工程内容2.2相关条件2.3工程特点3、安装程序3.1安装流程3.2测量放线3.3底座吊装就位3.4、旋转套筒及旋转臂和其它部件的安装3.5底座找正作业操作要领3.6吊装注意事3.7吊具的强度计算4.工期计划4.1工期网络计划4.2工期控制措施4、质量方针和目标5.1质量方针5.2质量目标5.3质量保证措施5.4质量管理组织5、施工组织6、安全管理7.1安全目标7.2安全措施7.3安全管理组织8.机具及材料9.附图1、编制依据本施工作业设计编制主要依据下列技术资料1)《冶金机械设备安装工程质量检验评定标准》:连续铸钢设备,冶金工业出版社,YB 9244-922)梅钢发放的安装图与转化图3)奥钢联提供的安装说明书4)《冶金机械设备安装工程施工及验收规范》YBJ 202-835)《工程测量规范》GB50026-936)《建筑施工高处作业安全技术规范》JBJ80-917)《建筑工程施工现场供用电安全规范》GB 50194-938)《建筑机械使用安全技术规程》JBJ33-869)《工业设备、管道焊接工程施工及验收规范》GBJ236-822、工程概况2.1工程内容本施工作业设计主要包括下列内容永久基准点和中心标板的埋设;钢包回转台底座的安装与找正;旋转体的安装;两只旋转臂的安装及旋转臂升降装置的安装;旋转驱动装置安装;钢包加盖装置的安装等。
**连铸机的钢包回转台由底座(11.3t)、旋转体(40t)、旋转臂(47.7t)、旋转臂升降装置(16.5t)、上连杆(26.5t)、下连杆(6.4t)、钢包加盖装置、旋转驱动装置等机械部件组成;总重215 .32T。
该钢包回转台位于厂房③线-④线的L列行车轨道梁之下,吊装位置极其困难;其底座基础标高为+10.847m,行车梁隔热板下表面标高为+22.015m。
- 1、下载文档前请自行甄别文档内容的完整性,平台不提供额外的编辑、内容补充、找答案等附加服务。
- 2、"仅部分预览"的文档,不可在线预览部分如存在完整性等问题,可反馈申请退款(可完整预览的文档不适用该条件!)。
- 3、如文档侵犯您的权益,请联系客服反馈,我们会尽快为您处理(人工客服工作时间:9:00-18:30)。
钢包回转台的设计说明书第一章绪论1.1铸钢生产及分类钢的生产过程主要分为炼钢和铸钢两大环节,炼钢的任务是将有关原材料通过炼钢炉炼成质量合格的钢液,铸钢的任务是将成份合格的钢液铸成合适于轧钢和锻压加工所需要的一定形状的钢块(连铸坯或是钢锭)。
铸钢作业是链接炼钢和轧钢之间的一项特殊作业,其特点行表现为它把钢液变成固定的凝固过程。
当钢液凝固后,在以后的轧钢过程中就不能对质量有本质的改变了。
因此,铸钢作业对产品的质量和成本有重大影响,必须予以特别重视。
铸钢生产可以分为钢锭模浇注(以下简称铸模)和连续铸钢(以下简称连铸)两大类。
铸模是将钢液注入铸铁制作的钢锭模内,冷却凝固成钢锭的工艺过程:连铸是将钢水不断的注入水冷结晶器内,连续获得铸坯的工艺过程。
连铸的出现从根本上改变了一个世纪以来占统治地位的钢钉初轧工艺,由于它所具有的一系列优越性,使得他自20世纪70年代大规模应用于工业生产以来得到迅速发展。
目前世界上主要产钢大国如日本、美国等连铸坯产量已经超过连铸钢总量的90%以上,连铸已经成为主要的铸钢生产方法。
1.2连铸技术的发展概况1.2.1国外连铸技术的发展概况早在19世纪中期亨利就提出连续浇注液态金属的设想,他在1858年钢铁协会伦敦会议的论文《模铸不如连铸》中提出设想,但一直到20世纪40年代。
连铸工艺才实现工业应用。
在这段时间内,由于钢的高熔点和高导热率等原因,研究人员遇到了很多问题。
在连续铸钢开始时,最先使用的是立式连铸机。
这种连铸机有一个弹簧固定的结晶器,产量通常很低,而且因为钢与结晶器粘连,漏钢很常见。
振动结晶器的想法归功于德国人seigfried,他首创了有色金属的连续铸造,与1952年用于德国的钢铁厂的直结晶器立式连铸机上,这是连铸工业化规模的开始。
由于技术的限制多年内只应用于小工厂,自1970年开始连铸开始应用于钢铁联合企业来生产板坯。
1.2.2我国连铸技术的发展概况我国是研究和应用连铸技术较早的国家之一,早在20世纪50年代就开始探索性的工作,60年代初进入到连铸技术工业应用阶段。
但是,从60年代末到70年代末,连铸技术几乎停滞不前。
1982年统计数字表明,世界平均连铸比为30%左右,而中国的连铸比仅为6.2%。
连铸坯的吨数与总铸坯(锭)的吨数之比叫做连铸比,它是衡量一个国家或一个钢铁企业生产发展水平的重要标志之一,也是连铸设备、工艺、管理以及和连铸有关的各生产环节发展水平的综合体现。
1970年至1980年,世界平均连铸比从4.4%发展到28.4%,中国的连铸比从2.1%发展到6.2%;至1990年,世界和中国的连铸比分别发展到62.8%和22.4%;到2001年,又分别发展到87.6%和92.0%。
2003年,中国连铸比达到95.3%左右,估计世界平均连铸比2003年接近90%。
从统计数字可以看出,中国的连铸技术在近10多年内得到了迅速发展。
以板坯连铸机为例,主要表现在:●板坯连铸机本体设备的四个关键设备明显落后于国外。
结晶器国外已采用紧凑式结构,我们还是老式的带外框架的结构;国内外新投产的板坯连铸机几乎全部采用液压振动装置,而我们还有许多新上的是机械电机振动装置;零号扇形段国外能够液压远程调辊缝,而我们还是液压垫块式结构;扇形段国外均能够液压夹紧、远程调辊缝和动态轻压下,而我们还是垫块式的停机调辊缝结构。
●除以上四大设备与国外相比存在一定差距外,配套设备中许多小的地方也存在不同程度的差距●液压系统、电气控制系统也在某些方面存在差距●连铸生产应用软件差距最大●国内技术资源不能有效整合1.2.3中国连铸技术水平与工业发达国家的差距虽然中国的连铸起步较早,尤其是最近十几年的飞速发展,已经使中国的连铸技术达到了很高的水平,而且中国的连铸技术也在国外得到应用,但是中国的连铸技术还存在还存在很多不足,和发达的工业国家相比还有很大的差距,其具体表现在:(1)目前的国外的常规连铸生产已趋成熟,连铸机的作业率普遍率大于80%,大型板坯连铸机连铸约为100—200t钢才漏钢一次,已基本可生产无缺陷铸坯。
而中国连铸机生产稳定性较差,事故相对比较多,作业率偏低,连铸质量还有一定差距。
(2)连铸连轧技术在国外已经产业化或加快产业化步伐。
目前,外国以投产和在投产建设的薄板坯连铸连轧线约为50套,薄带连铸以建设多台工业实验机组,预计不久就能实现产业化,而中国还处在起步阶段。
(3)国外高效连铸技术进一步的发展。
国外低碳板坯普遍大于2m/min,最高可达3;130×130mm和150×150mm低碳方坯最大拉速超过4m/min和3.5m/min,连铸机生产效率大大提高,而且中国还存在较大差距。
(4)国外的连铸生产自动控制水平迅速提高。
国外连铸机中以普遍采用结晶器液面检测与控制技术,主计算机铸坯质量跟踪和判定技术、漏钢预报警与控制技术在大型板坯连铸机中得到使用,智能化技术也有了很大的发展。
而中国自行设计的连铸机总体控制水平还是很低。
(5)国外精炼比迅速提高,相关配套技术同步发展。
目前,国外精炼比超过70%,中间包耐材寿命一般可达到30h/包,最高约为100h/包。
而中国精炼比仅为20%,中间包最高寿命30h/包。
(6)合金钢连铸比国外较高,目前国外合金连铸比一般已达到80%以上,最高可达到92%中国低于这个水平。
近几年,我国经济发展较快,冶金企业投放的技改资金比较大,新上项目很多,连续铸钢项目也较多,但连铸机设备和技术大部分还是靠引进。
我国薄板坯连铸连轧已经引进了将近10条生产线;从2000年开始,我国先后全部引进或引进核心部位设备与技术的常规板坯连铸机共有24台27流,还有继续引进的趋势;中薄板坯连铸机、异型坯连铸机全部引进;大方坯连铸机也有引进的倾向。
其原因主要是我国连铸技术与国外先进水平还存在一定差距。
1.3连铸机的主要设备及分类连铸机主要由钢包运载装置、中间包、中间包运载装置、结晶器、结晶器振动装置、二次冷却装置、拉坯矫直机、引锭装置、切割装置和铸坯运出装置等部分组成。
钢包运载装置主要有浇注车和钢包回转台两种方式,目前绝大部分新设计的连铸机都采用钢包回转台。
它的主要作用是运载钢包,并支撑钢包进行浇注作业。
采用钢包回转台还可快速更换钢包,实现多炉连铸。
中间包是钢包和结晶器之间用来接受钢液的过渡装置,它用来稳定钢流,减小钢流对结晶器中坯壳的冲刷;并使钢液在中间包内有合理的流动和适当长的停留时间,以保证钢液温度均匀及非金属夹杂物分离上浮;对于多流连铸机由中间包对钢液进行分流;在多炉连浇时,中间包中贮存的钢液在更换钢包时起到衔接的作用。
中间包运载装置有中间包车和中间包回转台,它是用来支撑、运输、更换中间包的设备。
结晶器是一个特殊的水冷钢模,钢液在结晶器内冷却、初步凝固成形,并形成一定的坯壳厚度,以保证铸坯被拉出结晶器时,坯壳不被拉漏、不产生变形和裂纹等缺陷。
因此它是连铸机的关键设备。
结晶器振动装置是使结晶器能按一定的要求做上下往复运动,以防止初生坯壳与结晶器粘连而被拉裂。
二次冷却装置主要由喷水冷却装置和铸坯支撑装置组成。
它的作用是:向铸坯直接喷水,使其完全凝固;通过夹辊和侧导辊对带有液芯的铸坯起支撑和导向作用,防止并限制铸坯发生鼓肚、变形和漏钢事故。
拉坯矫直机的作用是在浇注过程中克服铸坯与结晶器及二冷区的阻力,顺利地将铸坯拉出,并对弧形铸坯进行矫直。
在浇注前,它还要将引锭装置送入结晶器内。
引锭装置包括引锭头和引锭杆两部分,它的作用是在开浇时作为结晶器的“活底”,堵住结晶器的下口,并使钢液在引锭杆头部凝固;通过拉矫机的牵引,铸坯随引锭杆从结晶器下口拉出。
引锭杆拉出拉矫机后,将引锭杆脱去,进入正常拉坯状态。
切割装置的作用是在铸坯行进过程中,将它切割成所需要的定尺长度。
铸坯运出装置包括辊道、推钢机、冷床等,由它们完成铸坯的输送、冷却等作业。
连铸机可以按多种方法进行分类:(1)按结晶器的运动方式,连铸机可分为固定式(即振动式)和移动式两类。
前者是现在生产上常用的以水冷、底部敞口的铜质结晶器为特征的“常规”连铸机;后者是轮式、轮带式等结晶器随铸坯一起运动的连铸机。
(2)按连铸机结构的外形可分为立式连铸机,如图1.1所示为立式连铸机、立弯式连铸机,如图1..3所示为立弯式连铸机、弧形连铸机(包括直结晶器多点弯曲型、直结晶器弧形、弧形多半径弧形等,图1-9 多半径弧形连铸机。
)、水平连铸机,图1-10水平式连铸机。
(3)按铸坯断面的形状和大小可分为:方坯连铸机(断面不大于150×150mm 的叫小Ф方坯;大于150×150mm的叫大方坯,矩形断面的长和宽小于3 的也称为方坯连铸机),图1-6是普罗迪公司的弧形小方坯连铸机,图1-7弧形大方坯连铸机,图1-8弧形小方坯连铸机;板坯连铸机(铸坯断面为长方形,其宽厚比一般在3以上);圆坯连铸机(铸坯断面为圆形,直径Ф60~Ф400mm);异形坯连铸机(浇注异形断面,如H型、空心管等);方、板坯兼用连铸机(在一台铸机上既能浇注板坯也能浇注方坯);薄板坯连铸机(铸坯厚度为40~80mm的薄板坯料)等。
(4)按铸坯所承受的钢液静压头,即铸机垂直高度(H)与铸坯厚度(D)比值的大小,可将连铸机分为高头型(H/D>50,铸机机型为立式或立弯式)、标准头型(H/D为40~50,铸机机型为带直线段的弧形或弧形)、低头型(H/D为20~40,铸机机型为弧形或椭圆形)和超低头型(H/D<20,铸机机型为椭圆形)4种。
随着炼钢和炉外精炼技术的提高,浇注前及浇注过程中对钢液纯净度的有效控制,低头和超低头连铸机的采用逐渐增多。
(5)其他一些提法。
其他经常用到的名称有台数、机数和流数等。
如图1.3所示为旋转式连铸机。
1)立式连铸机立式连铸机的结晶器、二次冷却装置、拉坯装置及切割铸坯装置等都是布置在垂直的中心线上,如图1.1所示。
立式连铸机的优点是钢水在垂直的方向凝固,其所含的非金属夹杂物,上浮时不受阻碍,容易分离出来。
另一方面,铸坯不经过弯曲或矫直,不会产生因弯曲或矫直所造成的缺陷,因此它特别适用于优质钢及高合金钢的浇铸。
它的缺点是设备较高,一般是35~45mm,因此需要较高的厂房,或较深的地坑。
钢水的提升及铸坯的运送,都比较麻烦。
近10年来,除了少数特殊钢厂以外,很少采用这种机型。
图1.1 双流立式连铸机1- 运坯车;2- 中间包;3-结晶器;4-二冷夹辊;5-拉辊;6- 拉辊驱动装置; 7-飞剪;8-翻钢斗;9- 运输链2)旋转式连铸机旋转式连铸机也叫离心式连铸机,也是一种立式连铸机。
其特点是结晶器、导辊及拉辊都和铸坯一起围绕其垂直中心线以一定的速度旋转,铸坯是在一边旋转一边下行的运动中凝固的。
这种铸机适用于浇铸圆坯。