数控系统的参数设置与调试
FANUC数控系统轴设定参数的调试

FANUC数控系统轴设定参数的调试FANUC数控系统是目前工业自动化领域中使用较广泛的一种数控系统,其在机床控制系统中起到了至关重要的作用。
对于使用FANUC数控系统的机床,轴设定参数的调试是非常重要的一步。
本文将介绍FANUC数控系统轴设定参数的调试过程。
首先,为了进行轴设定参数的调试,需要对FANUC数控系统有一定的了解。
在进行参数调试之前,应该先了解轴设定参数的含义和功能。
FANUC数控系统中的轴设定参数主要包括轴号、速度、加速度、减速度、位置偏差等。
通过调整这些参数,可以对机床的运动轴进行控制,实现精准的加工。
在进行轴设定参数的调试之前,首先需要进行系统设置。
在FANUC数控系统中,通过对系统参数进行设置,可以调整机床的各项参数和控制方式。
例如,可以设置系统的坐标轴数、单位、各轴的运动方式等。
这些设置对轴设定参数的调试非常重要,因为它们会直接影响到轴的运动控制效果。
接下来,需要对各个轴的设定参数进行调试。
首先是轴号的设定。
在FANUC数控系统中,每个轴都有对应的编号,通过设置轴号,可以确定对应轴的设定参数。
例如,X轴对应轴号为1,Y轴对应轴号为2,以此类推。
然后是速度、加速度和减速度的设定。
在进行加工操作时,机床的速度和加速度对加工效果有很大的影响。
通过调整速度、加速度和减速度的设定参数,可以控制机床在加工过程中的速度和运动方式。
需要根据具体的加工要求和材料性质,合理设定这些参数。
此外,还需要调试位置偏差参数。
位置偏差是指机床运动轴在实际运动中与设定的位置之间存在的偏差。
通过调整位置偏差参数,可以实现机床轴的精确控制。
在调试时,可以采用示教器或者手动操作机床进行精调,使机床的实际运动与设定的位置尽可能接近。
最后,进行轴设定参数的测试和优化。
在设定完轴参数后,需要进行测试,观察机床的运动轨迹和加工结果是否符合要求。
如果发现运动不平稳、位置偏差过大等问题,需要进一步优化设定参数。
通过反复测试和优化,逐步调整轴设定参数,直到满足加工要求为止。
立式数控加工中心的数控系统的调试和操作技巧

立式数控加工中心的数控系统的调试和操作技巧随着现代制造技术的发展,立式数控加工中心在机械加工领域得到了广泛应用。
作为立式数控加工中心的核心部件,数控系统的调试和操作技巧对于提高加工效率和质量至关重要。
本文将介绍立式数控加工中心数控系统的调试和操作技巧,以帮助工程师和操作人员更好地实现加工任务。
一、数控系统的调试技巧1. 确保硬件连接正确:在调试数控系统之前,首先确保所有硬件设备如电机、传感器和控制器之间的连接是正确可靠的。
任何连接问题都可能导致系统无法正常工作。
2. 检查参数设置:数控系统通常具有大量的参数设置,包括速度、加速度、位置等。
在调试过程中,请确保这些参数的设置符合实际加工需求,并及时进行修正和优化。
3. 检测传感器和开关:数控系统依赖于传感器和开关来感知加工状态和位置信息。
在调试过程中,请确保传感器和开关正常工作,并及时更换故障组件。
4. 校准坐标系:数控系统的坐标系通常是基于机床的。
在调试过程中,请确保坐标系的校准准确,以保证加工精度和定位精度。
5. 测试运动和定位:在进行加工任务之前,请测试机床的各个轴的运动情况和定位精度。
如果发现问题,及时调整参数和修复设备,以确保稳定的运动和准确的定位。
二、数控系统的操作技巧1. 熟悉操作界面:不同的厂家和型号的数控系统有不同的操作界面。
在正式操作之前,请熟悉并掌握数控系统的操作界面,包括各个按钮、菜单和功能键的作用。
2. 设置工艺参数:在进行加工任务之前,请根据加工要求设置相应的工艺参数,如切削速度、刀具尺寸、进给速度等。
这些参数的设置将直接影响加工效果和质量。
3. 编写加工程序:数控系统通常需要根据加工任务编写相应的加工程序。
在编写程序时,请确保程序的正确性和完整性,并进行程序的调试和测试。
同时,建立程序库以便日后使用和维护。
4. 定位与对刀:数控机床的操作任务包括定位工件和对刀。
在进行定位和对刀操作时,请注意技巧和规范,确保工件在正确的位置上,并正确设置切削刀具的参数。
数控系统的参数设置与调整

实训三数控系统的参数设置与调整一、实验目的1、熟悉HED—21S数控系统的定义及设置方法。
2、了解参数设置对数控系统运行的作用和影响二、实训设备HNC-21TF数控系统综合实验台万用表工具三、相关知识1 、参数设置操作( 1 )常用名词几按键说明部件: HNC — 21TF 数控装置中各控制接口或功能单元权限: HNC—2lTF数控装置中,设置了三种级别的权限,即数控厂家、机床厂家、用户;不同级别的权限,可以修改的参数是不同的。
数控厂家权限级别最高,机床厂家权限其次,用户权限的级别最低。
主菜单与子菜单:在某一个菜单中,用Enter键选中某项后,若出现另一个菜单,则前者称主菜单,后者称子菜单。
菜单可以分为两种:弹出式菜单和图形按键式菜单,如图 5—1所示。
图 5—1 主菜单及子菜单参数树:各级参数组成参数树,如图 5—2所示。
图 5—2 数控装置的参数树窗口:显示和修改参数值的区域。
(2)参数查看与设置(F3一F1)。
在图 5—3所示的主操作界面下,按F3键进入“参数功能”子菜单。
命令行与菜单条的显示如图 5—4所示。
图 5—3 主操作界面图 5—4 参数功能子菜单参数查看与设置的具体操作步骤如下:①在“参数功能”子菜单下,按 F1键,系统将弹出如图5—5所示的“参数索引”子菜单图 5—5 参数索引子菜单②用↓ 、↑ 键选择要查看或设置的选项,按 Enter键进入下一级菜单或窗口;③如果所选的选项有下一级菜单,例如“坐标轴参数”,系统会弹出该选项的下一级菜单,如图5—6所示的“坐标轴参数”菜单;④用同样的方法选择、确定选项,直到所选的选项没有更下一级的菜单,此时,图形显示窗口将显示所选参数块的参数名及参数值,例如在“坐标轴参数”菜单中选择“轴0”,则显示如图5—6右上所示的“坐标轴参数一轴。
”窗口;用↓ 、↑ 、→ 、← 、 PgUp、PgDn等键移动蓝色光标条,到达所要查看或设置的参数处;图 5—6 坐标轴参数→轴 0 窗口⑤如果在此之前,用户没有进入“输入权限F3”菜单,或者输入的权限级别比待修改的参数所需的权限低,则只能查看该参数。
FAGOR数控系统参数设置方法
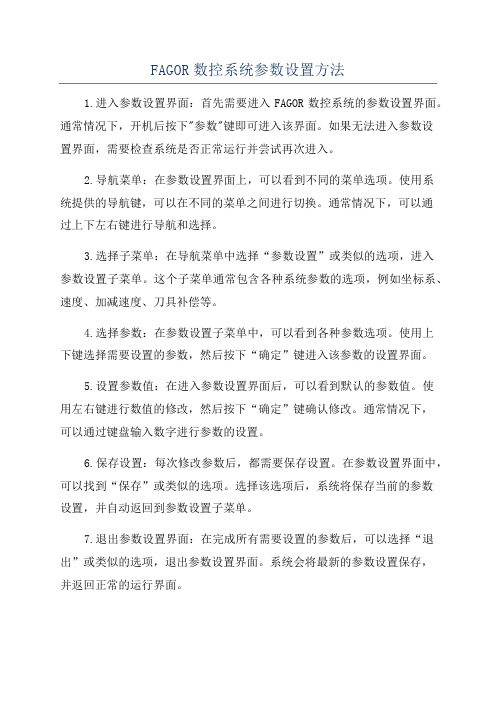
FAGOR数控系统参数设置方法1.进入参数设置界面:首先需要进入FAGOR数控系统的参数设置界面。
通常情况下,开机后按下"参数"键即可进入该界面。
如果无法进入参数设置界面,需要检查系统是否正常运行并尝试再次进入。
2.导航菜单:在参数设置界面上,可以看到不同的菜单选项。
使用系统提供的导航键,可以在不同的菜单之间进行切换。
通常情况下,可以通过上下左右键进行导航和选择。
3.选择子菜单:在导航菜单中选择“参数设置”或类似的选项,进入参数设置子菜单。
这个子菜单通常包含各种系统参数的选项,例如坐标系、速度、加减速度、刀具补偿等。
4.选择参数:在参数设置子菜单中,可以看到各种参数选项。
使用上下键选择需要设置的参数,然后按下“确定”键进入该参数的设置界面。
5.设置参数值:在进入参数设置界面后,可以看到默认的参数值。
使用左右键进行数值的修改,然后按下“确定”键确认修改。
通常情况下,可以通过键盘输入数字进行参数的设置。
6.保存设置:每次修改参数后,都需要保存设置。
在参数设置界面中,可以找到“保存”或类似的选项。
选择该选项后,系统将保存当前的参数设置,并自动返回到参数设置子菜单。
7.退出参数设置界面:在完成所有需要设置的参数后,可以选择“退出”或类似的选项,退出参数设置界面。
系统会将最新的参数设置保存,并返回正常的运行界面。
需要注意的是,FAGOR数控系统的参数设置是一项复杂而精细的工作,需要根据具体的机床和工作要求进行设置。
错误的参数设置可能导致机床无法正常运行或产生不良效果。
因此,在进行参数设置前,需要仔细了解机床的使用说明和相关技术要求,在保证安全的前提下进行设置。
同时,也建议在设置参数前备份原有的参数设置,以便出现问题时可以及时恢复。
数控机床钻孔加工参数的设置与调整
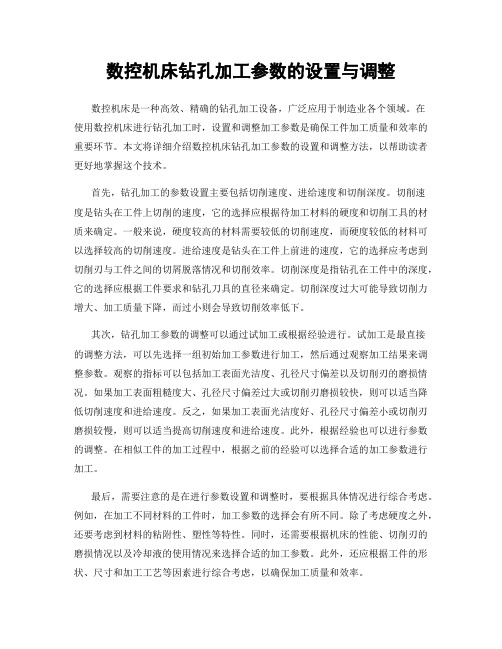
数控机床钻孔加工参数的设置与调整数控机床是一种高效、精确的钻孔加工设备,广泛应用于制造业各个领域。
在使用数控机床进行钻孔加工时,设置和调整加工参数是确保工件加工质量和效率的重要环节。
本文将详细介绍数控机床钻孔加工参数的设置和调整方法,以帮助读者更好地掌握这个技术。
首先,钻孔加工的参数设置主要包括切削速度、进给速度和切削深度。
切削速度是钻头在工件上切削的速度,它的选择应根据待加工材料的硬度和切削工具的材质来确定。
一般来说,硬度较高的材料需要较低的切削速度,而硬度较低的材料可以选择较高的切削速度。
进给速度是钻头在工件上前进的速度,它的选择应考虑到切削刃与工件之间的切屑脱落情况和切削效率。
切削深度是指钻孔在工件中的深度,它的选择应根据工件要求和钻孔刀具的直径来确定。
切削深度过大可能导致切削力增大、加工质量下降,而过小则会导致切削效率低下。
其次,钻孔加工参数的调整可以通过试加工或根据经验进行。
试加工是最直接的调整方法,可以先选择一组初始加工参数进行加工,然后通过观察加工结果来调整参数。
观察的指标可以包括加工表面光洁度、孔径尺寸偏差以及切削刃的磨损情况。
如果加工表面粗糙度大、孔径尺寸偏差过大或切削刃磨损较快,则可以适当降低切削速度和进给速度。
反之,如果加工表面光洁度好、孔径尺寸偏差小或切削刃磨损较慢,则可以适当提高切削速度和进给速度。
此外,根据经验也可以进行参数的调整。
在相似工件的加工过程中,根据之前的经验可以选择合适的加工参数进行加工。
最后,需要注意的是在进行参数设置和调整时,要根据具体情况进行综合考虑。
例如,在加工不同材料的工件时,加工参数的选择会有所不同。
除了考虑硬度之外,还要考虑到材料的粘附性、塑性等特性。
同时,还需要根据机床的性能、切削刃的磨损情况以及冷却液的使用情况来选择合适的加工参数。
此外,还应根据工件的形状、尺寸和加工工艺等因素进行综合考虑,以确保加工质量和效率。
综上所述,数控机床钻孔加工参数的设置和调整是确保加工质量和效率的重要环节。
D数控系统调试步骤

1.检查接线,PP72/48(de)地址拨码,MCP地址拨码开关PP72/48 PN S1: ON:1,4,9,10MCP:S2: ON:7,9,102.上电总清3.设置口令,时间,选择选项功能4.设置基本(de)机床参数N10000 $MN_AXCONF_MACHAX_NAME_TAB[0]="MX"N10000 $MN_AXCONF_MACHAX_NAME_TAB[1]="MZ"N10000 $MN_AXCONF_MACHAX_NAME_TAB[2]="MC"N10000 $MN_AXCONF_MACHAX_NAME_TAB[3]="MB"N10000 $MN_AXCONF_MACHAX_NAME_TAB[4]="MSP"N20050 $MC_AXCONF_GEOAX_ASSIGN_TAB[1]=0N20050 $MC_AXCONF_GEOAX_ASSIGN_TAB[2]=2N20070 $MC_AXCONF_MACHAX_USED[4]=5N20080 $MC_AXCONF_CHANAX_NAME_TAB[0]="X"N20080 $MC_AXCONF_CHANAX_NAME_TAB[1]="Z"N20080 $MC_AXCONF_CHANAX_NAME_TAB[2]="C"N20080 $MC_AXCONF_CHANAX_NAME_TAB[3]="B"N20080 $MC_AXCONF_CHANAX_NAME_TAB[4]="SP"N28050=300 number of R parameters设置Profinet上有效(de)模块MD12986[0]=-1 PP72/48 PNMD12986[6]=-1 MCPMD20310 bit9=1 将刀库设为模拟刀库MD20700=05.只下载MCP面板控制程序,其他程序不下载.6.驱动(de)调试7.检查PLC 输入点、输出点状态,检查接线是否有错误8.用户PLC程序调试9.报警文本(de)传入报警文本(de)初始文件需要在系统中进行创建,创建完初始文件后,拷贝到电脑中进行报警文本(de)编辑.PLC报警文本(de)传输路径如下图:PLC报警文本(de)编辑,在RCS中找到报警文本,在文件名称上点击右键在弹出(de)菜单中选择“Open with TS Editor”,弹出如上图中(de)窗口,在上图中(de)窗口中即可进行PLC报警文本(de)编辑.编辑好(de)报警文本下传到系统中再利用系统中(de)编辑功能进行报警文本显示颜色(de)修改.10.用户画面easy screen(de)传入(1)配置文件(de)拷贝:通过RCS或者U盘将文件:custom.ini,easyscreen.ini,slamconfig.ini,systemconfigration.ini 拷贝到目录System CF-Card/oem/sinumerik/hmi/cfg(2)图片文件(de)拷贝将图片文件拷贝到System CF-Card/oem/sinumerik/hmi/ico/ico640(3)画面文件(de)拷贝将文件custom拷贝到目录System CF-Card/oem/sinumerik/hmi/proj11.主轴参数(de)设置主轴参数设置,采用虚拟主轴.30300=130310=130320=130350=132000=2032010=20 JOG快速32020=10 JOG点动速度35000=135100=30035200= 速度环(de)加速度根据变频器(de)实际加速度进行设置. 36200=330DB9006.DBD8 给定转速乘倍率得到(de)速度DB9006.DBD4 给定转速。
基于FANUC数控系统的模拟主轴的参数设置与调试

基于FANUC数控系统的模拟主轴的参数设置与调试0 引言主轴是机床上带动工件或刀具运动的轴,主轴控制的效果将直接影响零件的加工精度。
模拟主轴控制是指数控系统输出模拟电压控制主轴,主轴由调速器控制的主轴电机驱动( 常用的调速器是变频器、主轴电机是三相异步电动机) ,可以实现数控机床主轴的启停、正反转以及调速控制。
基于 FANUC数控系统的主轴控制主要有模拟主轴控制和串行主轴控制两种类型。
模拟主轴系统的结构如图 1 所示。
串行主轴控制是指数控系统输出串行数据控制主轴,主轴通常由伺服驱动器控制的伺服电机驱动。
模拟主轴控制经济实用、调试方便,在中低档的数控机床中广泛使用。
图 1 模拟主轴系统结构示意图1 模拟主轴系统的组成基于 FANUC 数控系统的模拟主轴控制系统的气原理图如图 2 所示。
其中,FANUC 0i-C 数控系统的 JA40 接口输出 0 ~ 10 V 模拟电压; 三菱 E700变频器的 2、5 端子接收JA40 接口输出的模拟电压信号,STF、STR 端子接收 JD1A 接口输出的转向信号; 主轴编码器 PG 的反馈信号输入 JA7A 接口。
图 2 模拟主轴控制电气原理图2 模拟主轴的调试从系统组成的角度,数控机床模拟主轴的调试包括 CNC 中有关主轴的参数与信号的调试,以及变频器本身的参数与信号的调试。
调试的目的是保证数控系统能够根据指令发出正确的模拟电压信号,经过变频器调速后驱动主轴正确运行。
2.1 CNC 调试CNC 调试时,主要是根据不同的控制要求,设置一些参数,将控制要求反映到主轴转速的模拟量输出上,使之与控制要求一一对应。
以基于 FANUC数控系统的某数控车床的模拟主轴控制为例,CNC的转速指令输出极限( 模拟量) 为 10 V,档位 1 ~ 3对应的最高转速分别为 1 000 r/min、2 000 r/min、4000 r / min,CNC 上设定的主轴参数如表 1 所示。
数控机床伺服参数调整方法

数控机床伺服参数调整方法1. 引言1.1 引言数、岗次等。
数控机床是一种自动化加工设备,其控制系统由伺服系统负责实现精确的位置控制和运动控制。
伺服系统中的参数设置对机床的性能和加工质量有着直接的影响。
正确调整数控机床伺服参数是保证机床正常工作和提高加工精度的重要步骤。
在实际生产中,有时会出现数控机床运行不稳定或加工质量不理想的情况,这时就需要进行伺服参数的调整。
本文将介绍数控机床伺服参数的调整方法,包括调整方法一、调整方法二、调整方法三和调整方法四。
通过本文的学习,读者将能够全面了解数控机床伺服参数的调整原理和方法,从而更好地应对各种生产实际需求,提高加工效率和质量。
2. 正文2.1 数控机床伺服参数调整方法数控机床伺服参数调整方法主要包括四种不同的调整方法,每种方法都有其独特的特点和适用场景。
下面将分别介绍这四种调整方法。
调整方法一:手动调整手动调整是最基础也是最直观的调整方法,操作人员可以通过手动旋钮或按钮来改变伺服参数,实现对机床的控制。
这种方法适用于简单的调整需求,操作简单直观,但需要操作人员对机床进行实时监控,无法实现自动化控制。
调整方法二:自动调整自动调整是通过数控系统自动优化伺服参数,根据预设的算法和规则对参数进行调整。
这种方法可以提高生产效率,减少人工干预,适用于需要大量重复调整的场景。
但需要提前设定好优化算法,以及对数控系统有一定的了解和操作技能。
调整方法三:智能调整智能调整是结合人工智能技术对伺服参数进行智能化调整,通过学习和优化算法,使得机床能够自动适应不同工件的加工要求。
这种方法能够实现个性化定制,提高加工精度和效率,但需要大量的数据支持和复杂的算法设计。
调整方法四:在线优化在线优化是在实际加工过程中根据机床工作状态和负载情况实时调整伺服参数,以达到最佳加工效果。
这种方法可以最大限度地提高加工质量和效率,但需要对机床和加工过程有深入的理解,以及高级的控制算法和技术支持。
综上所述,数控机床伺服参数调整方法有多种选择,操作人员可以根据实际需求和技术水平选择合适的调整方法,以实现最佳的加工效果和效率。
E68数控系统的减速比参数设置和分度运行调试
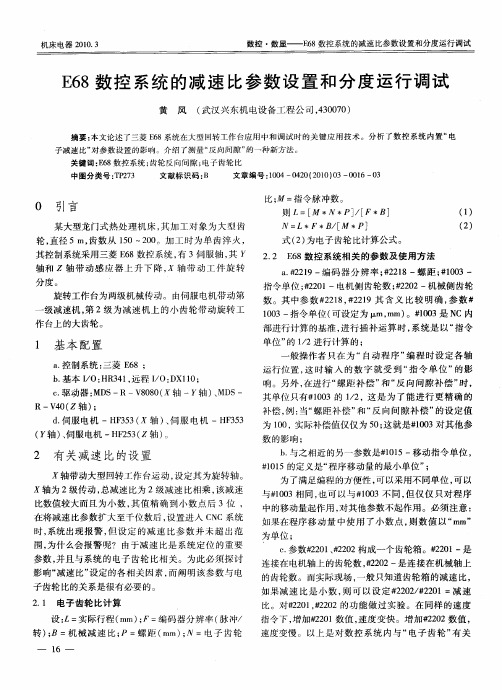
关键词 :6 E 8数控系统 ; 齿轮反向间隙 ; 电子齿 轮比
中 图分 类 号 :P 7 T 23 文 献 标 识码 : B 文 章 编 号 :0 4— 4 0 2 1 )3— 0 6— 3 10 0 2 (0 0 0 0 1 0
一
1 一 6
数 控 - 显 — — E 8数 控 系 统 的 减 速 比参 数 设置 和 分 度 运 行 调 试 数 6
机 床 电器 2 1 . 003
参数 的功能和使 用的分析 。
R— 4 ( V 0 z轴 ) ; d 伺服 电机 一H 3 3 X轴 ) 伺 服 电机 一H 33 . F5 ( 、 F5
补偿 , : 螺距补 偿 ” “ 向间 隙补偿 ” 例 当“ 和 反 的设定 值 为 10 实际补偿值仅仅 为 5 ; 0, 0 这就是 #0 3对其 他参 10
数的影响 ;
0 引言
某 大型龙 门式热 处理 机床 , 加工 对象 为大 型齿 其 轮, 直径 5I, 齿数 从 10~2 0 n 5 0 。加 工 时为单 齿 淬火 ,
比; =指令脉 冲数 。
则 L:[ M N: / F l [ B] : P]
N= l B [ L: : F / M P ] 式() 2 为电子齿轮 比计算公 式 。 2 2 E 8数 控 系统相 关的参 数及 使用方 法 . 6
如果 在程序 移 动 量 中使 用 了小数 点 , 数值 以 “ m” 则 m
为单位 ;
c 参数#2 1 #2 2构成一个齿 轮箱。# 2 1 . 20 、 0 2 2 0 一是
HNC-21T 华中数控系统参数设置与调整方法

数控系统正常运行的重要条件是必须确保正确的参数设置,不正确的参数设置与更改,可能会导致数控系统的后果,轻则会使数控系统运行不正常,重则造成数控系统损坏或人员伤亡事故。
因此,必须了解数控系统的功能参数和熟悉相关的设置。
数控系统的功能和重要性根据参数大小划分各种不同级别。
数控系统一般设置三个级别的权限,每个访问允许用户修改参数的不同层次。
通过限制访问密码,保护重要参数来防止用户误操作造成的故障和事故,检查参数和备份不需要密码。
1HNC-21T 华中数控系统进入参数设置界面操作HNC-21T 华中数控系统在主菜单下按F10进入扩展菜单,如图1-1所示:图1-1HNC-21T 数控系统的扩展菜单界面然后按F3并输入正确口令后,再按F1进入如图1-2所示界面,此界面包含数控系统的所有六大类参数,即机床参数、轴参数、伺服参数、轴补偿参数、PMC 用户参数和过象限突跳补偿。
想要进入相应的参数界面只需按每个参数后面对应的F功能键即可。
图1-2HNC-21T 数控系统的参数界面2HNC-21T 华中数控系统各类参数的含义和内容2.1机床参数机床参数包括主轴编码器每转脉冲数,此参数一定要根据主轴实际使用的编码器脉冲发生数填写;公/英制编程选择,国内一般选择公制编程;其余是否采用断电保护机床位置、外置存储器类型、是否显示系统时间、是否显示PMC 轴和主轴编码器方向按实际情况分别填写。
2.2轴参数轴参数是与数控系统控制的各个座标轴数控系统控制参数设置,包括外部脉冲当量分子、外部脉冲当量的分母,柔和的正面和负面的极限位置,软限制的位置,方向回参考点,参考点位置,参考点开关偏移,回参考点移动速度快,回参考点定位,单向定位偏移值、最高快移速度、最高加工速度、快移加减速时间常数、快移加减速捷度时间常数、加工加减速时间常数、加工加减速捷度时间常数等相关参数。
2.3伺服参数伺服参数是伺服机构,包括伺服驱动器部件的相关参数,主要用来协调驱动与电机协调一致运动的参数。
数控机床调试知识点总结

数控机床调试知识点总结一、数控机床调试概述数控机床调试是指在数控机床安装、调试及使用过程中的一系列工作,目的是使数控机床能够正常运转,并且满足工件加工的要求。
数控机床调试是数控机床的重要环节,对于提高数控机床的加工精度和效率具有重要作用。
数控机床调试工作主要包括机床设备及附件的安装、电气系统的调试、传感器及执行机构的调试以及数控系统的参数设置和调试等内容。
二、数控机床调试技术要点1.数控机床设备及附件的安装数控机床设备及附件的安装是数控机床调试的第一步。
正确的安装可以有效地保障数控机床的正常运行。
在安装过程中,必须按照数控机床的安装图纸进行布置,确保每个零部件的位置准确无误。
另外,需要特别注意的是在安装过程中要进行合理的设备传动、夹具的安装,以及床身的水泥基础的浇筑,这些都是数控机床正常运行所必需的。
2.电气系统的调试数控机床的电气系统包括主要电路、控制电路、辅助电路等。
在调试电气系统时,需要对电气柜内电路进行检查,确保各种电缆连接正确,不互相搭线、短路、断路等现象。
此外,还需要对电气元件如接触器、断路器、继电器等进行检查和调试。
在电气系统调试完成后,还需要进行电气故障预防性测试,确保数控机床在运行过程中不会发生电气故障。
3.传感器及执行机构的调试传感器及执行机构是数控机床的重要组成部分,对于数控机床的精度、稳定性和可靠性有重要影响。
在调试这些部分时,需要仔细检查各种传感器的接线是否正确,传感器的灵敏度是否适当。
对于执行机构如伺服电机、液压执行机构等,需要进行调试以确保其运转准确、平稳。
4.数控系统的参数设置和调试数控系统是数控机床的核心部分,通过对数控系统的参数设置和调试可以有效地提高数控机床的加工精度和效率。
在进行数控系统的参数设置和调试时,需要根据具体的工件加工要求设置数控系统的加工参数,如进给速度、主轴转速、加工路径等。
此外,还需要对数控系统的各个功能进行测试,确保各种功能可以正常运行。
CNC机床加工中的数控系统调试与优化

CNC机床加工中的数控系统调试与优化在CNC机床加工中,数控系统的调试与优化是十分重要的环节。
数控系统是指通过数字计算来控制机床运动的系统,它直接影响到机床的加工精度和效率。
本文将探讨CNC机床加工中数控系统调试与优化的方法和步骤。
一、数控系统调试的步骤数控系统调试是指在安装好数控系统后,对各项功能进行测试和调试,以确保系统正常运行。
数控系统调试的步骤大致如下:1. 硬件检查与连接:检查数控系统的硬件设备是否正常,包括主机、控制面板、电机和传感器等,确保它们之间的连接正确可靠。
2. 系统参数设置:根据机床的具体要求,设置数控系统的参数,包括加工速度、加工深度、进给速度等。
3. 测试功能模块:对数控系统的各项功能模块进行测试,包括手动操作、自动操作、刀具补偿、程序编辑等。
4. 轴卡校准:调试各个轴向的运动精度,包括回零、定位和插补等功能,确保轴向的运动准确无误。
5. 测试程序运行:编写一个简单的程序,进行程序运行测试,观察机床的运动是否符合预期。
6. 调试报警和故障处理:测试系统报警和故障的处理能力,确保系统能够及时报警并处理故障。
二、数控系统调试的优化方法数控系统调试完毕后,还可以进行优化,以进一步提高加工效率和精度。
以下是一些常用的数控系统调试优化方法:1. 优化数控程序:对编写的数控程序进行优化,尽量减少程序的长度和运行时间,提高加工效率。
2. 优化刀具路径:对加工过程中的刀具路径进行优化,尽量减少刀具的移动距离和刀具的停顿时间,提高加工效率。
3. 优化加工参数:根据不同的加工要求,合理设置加工参数,包括进给速度、切削速度、切削深度等,以提高加工质量。
4. 优化补偿算法:调整数控系统的刀具补偿算法,以减小刀具的运动误差,提高加工精度。
5. 优化伺服控制:调试伺服控制系统,优化伺服参数,提高伺服系统的响应速度和稳定性。
6. 优化后处理:对加工后的零件进行后处理,包括去除毛刺、抛光等,以提高零件的表面质量。
数控系统连接与调试3.2.6 NC主轴参数设置

31060
DRIVE_AX_RATIO_NUMER A[0,1...5]
轴 主轴 主轴 主轴 主轴 主轴 主轴
输入值 参数定义
0 模拟主轴换档使能
3000 主轴换档最大速度
3300 主轴各档最大速度
3300 1 1
各档最大主轴监控 速度 主轴各档变比(电 机端) 主轴各档变比(主 轴端)
主轴电机与主轴并非1:1连接,电机与主轴的传动比1:2, 编码器连接在主轴上,测的是主轴的转速,非电机的转速。
轴参数号
参数名
36300
MA_ ENC_ FREQ_LIMI T
单位 Hz
轴 主轴
输入值
参数定义
55000 主轴监控频率
32020=500 手动方式下主轴转速
CK7815型数控车床主轴部件结构图
TIANJIN 中德培训中心
轴 参 数 参数名
单位
号
35010 GEAR_STEP_CHANGE_EN -
编码器与主轴连接,非与主轴电机连接。编码器的传动比 也需要设定。31070设定为1,31080设定为2。最终结果正 确。
应该是到这个转速,车床就开始自动换挡。
我们不需要自动换挡,所以该参数我们可以不予设定。
如果主轴转速一段范围内正常,但指令值变大时,主轴实际转速 总是被钳制在某个转速,那很可能是这个参数在作祟。
35110
ABLE GEAR_STEP_MAX_VELO[0 ,RPM
35130 36200
1...5 ]
GEAR_STEP_MAX_VELOLI RPM MIT[ 0,1...5 ]
AX_VELO_LIMIT[ 0,
RPM
1...5 ]
机床数控系统的校准与调试技术

机床数控系统的校准与调试技术机床数控系统在现代工业生产中起着至关重要的作用,它能够实现自动化、精确控制和高效生产。
然而,为了保证机床数控系统的正常运行和达到预期的精度要求,校准与调试工作显得尤为重要。
本文将介绍机床数控系统的校准和调试技术,以帮助工程师更好地进行相关工作。
一、机床数控系统的校准技术1. 几何误差校准机床数控系统的几何误差主要包括直线插补误差、圆弧插补误差和坐标系误差。
几何误差校准的目的是通过调整机床各个轴线的运动参数,使得实际运动轨迹与理论轨迹尽量一致。
首先,需要进行轴线直线度校准。
通过测量轴线的直线度误差,并调整相应的参考点,可以使得轴线的运动更加精确。
其次,圆弧插补误差校准是为了保证机床的圆弧插补运动能够实现高精度的运动轨迹。
最后,坐标系误差校准是为了消除坐标系变换带来的误差,需要通过仔细测量和调整机床的坐标系。
2. 系统刚度的校准机床数控系统的刚度是指在加工中所受外力作用下,机床各个轴线的变形程度。
刚度的大小直接影响着加工精度和工件质量。
因此,刚度校准是非常重要的一个环节。
在刚度校准过程中,一般会通过力传感器等设备来测量机床各个轴线的变形情况。
然后,根据测得的数据进行分析,找出影响刚度的关键因素,并进行调整和优化。
校准后的机床能够更好地抵抗外力的影响,从而提高加工精度和稳定性。
3. 系统精度补偿机床数控系统的精度补偿是通过软件或硬件方式来纠正机床在加工过程中产生的误差。
根据加工要求和测量结果,可以将误差信息输入到数控系统中,系统将自动进行误差补偿,从而提高加工精度。
精度补偿主要包括长度补偿、半径补偿和磨损补偿。
长度补偿是根据测量结果对轴向误差进行修正,以提高工件的几何尺寸精度。
半径补偿是对圆弧插补误差进行修正,保证加工出的圆弧轨迹准确无误。
磨损补偿是通过监测关键部件的磨损程度,及时进行调整和更换,以保证系统的可靠性和稳定性。
二、机床数控系统的调试技术1. 系统参数的调试机床数控系统的参数调试是指对系统的各项参数进行合理设置和调整,以保证系统能够稳定工作和达到预期的性能要求。
FANUC 0iMate MC系统参数调试步骤

FANUC 0i Mate-MC数控系统参数设定实验
数控系统参数设定
1、参数设定方法:
1)、在MDI或急停状态下。
2)、打开参数写保护:
按功能键,再按软件建,出现如下画面将参数写入一项设定为1,这时出现100号允许参数写入报警。
3)、按系统键。
4)、按参数软件键。
5)、找到期望的参数号,用输入参数值.
6)、参数输入完毕,把参数写保护关闭,方法参照第2步,把参数写入设定为0即可。
重新断电启动。
2、主要参数设定
运用参数设定帮助功能进行设定操作,按键3次,出现如下画面
需要设定的有“轴设定",“伺服设定”,“主轴设定”。
1)、轴设定:按软件键,
移动光标移到“轴设定”上
按软件键,进入轴设定参数界面。
用数字键输入需要的参数按确定参数输入。
需要轴设定的参数有如下:
2)、伺服设定参数
把光标移到伺服设定上
点软件键点扩展软件键
点软件键
伺服参数初始化:把把初始化设定位里的参数全部设置为0,重新断电上电,伺服设定的初始化就完成了.
所有参数设置完毕,点设定就可以了。
3)、主轴设定参数
把光标移到主轴设定上
点软件键
参数设置完毕点设定,重新断电启动就可以了.。
数控系统的参数设置与调试

数控系统的参数设置与调试一、实验目的与要求1. 熟悉并掌握数控系统参数的定义及设置方法2. 了解参数的设置对数控系统运行的作用及影响二、实验仪器与设备QS-CNC-T1 智能网络化数控系统综合实验台三、实验相关知识数控系统正常运行的重要条件是必须保证各种参数的正确设定,不正确的参数设置与更改,可能造成严重的后果。
因此,必须理解参数的功能,熟悉设定值。
数控系统按参数的功能和重要性大小划分了不同的级别,允许用户修改一定级别的参数,通过权限口令的限制对重要的参数进行保护,防止用户因误操作而造成故障和事故。
四、实验内容与步骤内容1. 掌握数控系统常用参数的功能及设置方法;2. 对轴数据、传动系统参数、主轴参数、软限位等相关参数进行设定;3. 观察参数修改后对机床运行状态的影响。
步骤1. 轴数据设置(1)按软件:诊断→机床数据→轴数据(2)按软件轴+或轴-选择相应的坐标轴。
首先选择X 轴。
(3)按↑或↓,将光标移至30130,输入数值()确定。
(4)按↓,将光标移至30240,输入数值()确定。
(5)按搜索→输入要查询的机床数据号“34200”按确认,光标立即定位刀所要查询的机床数据34200 上,输入设定值()按确定。
(6)按轴+,选择Z轴。
重复步骤4-7:设定30130=(),30240=(),34200=()。
(7)按调试→调试开关→NC ,选择正常上电启动,确认。
2. 传动系统的机械参数设定(1)设定下列参数:31020=1000,31400=1000(步进电机步距角 1.8 度,采用5 细分,则:360/1.8*5=1000)31030=5 丝杠螺距,单位:mm31050=1,31060=1 即减速比31050/31060=1/1=1说明: 以上设定的操作步骤,先选定X 轴参数,再设定Z 轴参数。
下面其它参数设定的操作步骤与此相同,不再赘述。
(2)设定相关的速度(X 轴、Z 轴)32000=3000;最大轴速度mm/min;32010=3000;点动快速mm/min;32020=2000;点动速度mm/min;32260=3000;电机额定转速;36200=11500;坐标速度极限。
- 1、下载文档前请自行甄别文档内容的完整性,平台不提供额外的编辑、内容补充、找答案等附加服务。
- 2、"仅部分预览"的文档,不可在线预览部分如存在完整性等问题,可反馈申请退款(可完整预览的文档不适用该条件!)。
- 3、如文档侵犯您的权益,请联系客服反馈,我们会尽快为您处理(人工客服工作时间:9:00-18:30)。
数控系统的参数设置与调试
一、实验目的与要求
1. 熟悉并掌握数控系统参数的定义及设置方法
2. 了解参数的设置对数控系统运行的作用及影响
二、实验仪器与设备
QS-CNC-T1 智能网络化数控系统综合实验台
三、实验相关知识
数控系统正常运行的重要条件是必须保证各种参数的正确设定,不正确的参数设置与更改,可能造成严重的后果。
因此,必须理解参数的功能,熟悉设定值。
数控系统按参数的功能和重要性大小划分了不同的级别,允许用户修改一定级别的参数,通过权限口令的限制对重要的参数进行保护,防止用户因误操作而造成故障和事故。
四、实验内容与步骤
内容1. 掌握数控系统常用参数的功能及设置方法;
2. 对轴数据、传动系统参数、主轴参数、软限位等相关参数进行设定;
3. 观察参数修改后对机床运行状态的影响。
步骤1. 轴数据设置
(1)按软件:诊断→机床数据→轴数据
(2)按软件轴+或轴-选择相应的坐标轴。
首先选择X 轴。
(3)按↑或↓,将光标移至30130,输入数值()确定。
(4)按↓,将光标移至30240,输入数值()确定。
(5)按搜索→输入要查询的机床数据号“34200”按确认,光标立即定位刀所要查询的机床数据34200 上,输入设定值()按确定。
(6)按轴+,选择Z轴。
重复步骤4-7:设定30130=(),30240=(),34200=()。
(7)按调试→调试开关→NC ,选择正常上电启动,确认。
2. 传动系统的机械参数设定
(1)设定下列参数:
31020=1000,31400=1000
(步进电机步距角 1.8 度,采用5 细分,则:360/1.8*5=1000)
31030=5 丝杠螺距,单位:mm
31050=1,31060=1 即减速比31050/31060=1/1=1
说明: 以上设定的操作步骤,先选定X 轴参数,再设定Z 轴参数。
下面其它参数设定的操作步骤与此相同,不再赘述。
(2)设定相关的速度(X 轴、Z 轴)
32000=3000;最大轴速度mm/min;
32010=3000;点动快速mm/min;
32020=2000;点动速度mm/min;
32260=3000;电机额定转速;
36200=11500;坐标速度极限。
(3)系统重新上电。
按调试→调试开关→NC,选择正常上电启动按确认;系统重上电。
自动计算步进电机最大频率:
(3000/60)转/秒³1000脉冲/转=50000 脉冲/秒=50000Hz
检查31350参数,应该为50000
输入监控频率(X 轴、Z轴)
36300=300000;即步进频率极限
3. 设定参考点
34000=1;减速开关有效;
34020=4000;寻找减速开关速度;
34060=5.0;寻找接近开关的最大距离;
34040=300;寻找零脉冲速度;
34070=200;参考点定位速度;
34010=0;减速开关方向正;
34050=1;接近开关方向正。
为进一步理解所设定参数,可选作以下实验:
(1)设定34000=0;减速开关无效。
(2)按复位键,使设定的所有参数有效。
(3)执行回参考点操作,观察系统运行是否正常。
(4)将参数34000 恢复为1。
4. 设定坐标软限位
(1)设定
36100=-1;轴负向软限位值;
36110=200;轴正向软限位值;
(2)按键,使设定的参数有效。
(3)长按+X 、+Z 来移动坐标轴到极限位置,观察屏幕上显示的轴位置坐标。
为进一步理解所设参数,可选做以下实验:
(1)设定
34100=0;参考点位置值;
36100=-5;轴负向软限位值:
36110=5; 轴正向软限位值;
(2)按//,使设定的参数有效。
(3)手动方式移动坐标轴。
出现“010621”报警号
(4)按诊断,阅读故障说明
(5)恢复34100=50,36100=-1,36110=200。
5. 主轴参数调试
(1)设定:
30130=1,有±10V 模拟量输出;
30200=1,主轴有编码器反馈;
(2)因为主轴安装了编码器,因而应设定下列主轴参数:
30240=2,因为主轴带测量系统;
31020=1024,编码器每转脉冲数;
32260=1000,主轴额定转速;
36200=5000,最大主轴监控速度;
(3)设定:36300=300000,主轴监控频率;
(4)统重新上电,使设定参数有效:按→调试→调试开关→NC,选正常上电启动按确认。
6. 数据保护
(1)关闭口令:调试→关闭口令
(2)机内数据存储
在系统内部把后备受时间限制的存储器中数据保存到永久存储器,一般用于以下情况:
系统关机超过50 小时,则必须进行内部数据保护
对重要数据进行了修改,建议立即进行内部数据保护
诊断→调试→数据存储
(3)机外数据保护
选择“通讯/数据输出”将数据文件通过RS232接口送到外部PC 中。
五、实验结论
1轴数据设置:选择X 轴,将光标移至30130输入数值2, 30240输入数值3, 34200输入数值2。
选择Z 轴,将光标移至30130输入数值2, 30240输入数值3, 34200输入数值2。
此时不出现报警。
2:改变传动系统的机械参数设定;(X ,Z轴)
参数31020=1500,31400=1500,31030=1,31050=2,31060=1
速度32000=4000,32010=4000,32020=3000,32260=4000,36200=12000
检查结果:31350=100000,现象:X轴速度变快
故障:Z轴31020为2000时不匹配,出现报警号26015,Z轴非法机床数据SMA-STEP-RESOL[0],Z轴编码器:对驱动器和位置控制所配置的分辨率不一样。
改变31020=1000重新上电排除故障。
3设定参考点:当34000=0时减速开关无效;当34000=1时减速开关有效,其现象x轴从+126到+142为减速阶段。
4设定坐标软限位:X轴为-168~+200时为实际位置,其范围不会超程。
手动方式移动超程时出现“021614”报警号。
解除超程后消除报警。
5主轴参数调试:当31020=1500时出现报警号“34200”:SMA-ENC-REFP-MODE[0],改变主轴31020=1024后重新上电排除故障。
6:保存数据。