清华大学著名战略专家,chengwei总裁的演讲21世纪新竞争环境下中国企业发展战略2
《世界级企业的核心竞争力要素》公需课课后作业答案(最全)

世界级企业的核心竞争力要素(最全)总分:100及格分数:60考试剩余时间:1时59分52秒单选题(共7题,每题5分)1、(A)是一流企业区别于一般企业最重要的标志。
A、创新能力B、企业文化C、企业家精神D、风控能力2、优秀的(B)结构为企业可持续发展提供坚实的制度保障。
A、组织B、公司治理C、薪酬制度体系D、人才竞争力3、现代企业的核心竞争力是一个以(A)为基本内核的企业某种关键资源或关键能力的组合。
A、知识、创新B、知识、文化C、契约、文化D、文化、创新4、(A)是企业生存和发展的基础,是核心竞争力。
A、资源B、企业文化C、企业家精神D、风控能力5、世界品牌实验室(World Brand Lab),连续十七年发布《世界品牌500强》,其评判依据是(A)。
A、品牌的世界影响力B、激发一线科研人员创新创业动力C、完善薪酬制度体系D、提高人才竞争力6、坚持企业属性的价值创造,用(A)来促进世界一流企业建设和实现引领。
A、改革创新B、股权出售C、股权奖励D、股权期权7、(B)在世界经济中具有重要地位,已成为全球经济的核心和风向标。
A、“世界一流军队”B、“世界一流企业”C、“一流大学”D、“一流学科”E、“一流教育”8、(C),用指标来衡量世界一流企业建设成效,加快世界一流企业建设。
A、坚持企业正确的把关定向B、坚持运用科学的系统观念C、坚持务实的实践准则D、坚持品牌和企业文化的“一体两面”9、(B),用体系的力量来推动世界一流企业建设,加快世界一流企业建设。
A、坚持企业正确的把关定向B、坚持运用科学的系统观念C、坚持务实的实践准则D、坚持品牌和企业文化的“一体两面”10、(),用不断提升全球竞争力来指导世界一流企业建设,加快世界一流企业建设。
正确答案:C、坚持动态的世界一流标准多选题(共6题,每题5分)1、世界一流企业成长的一般规律:(ABCD)。
A、创业阶段B、增长阶段C、转型阶段D、超越阶段E、突破阶段2、近年来,(ABCDE)等技术加速创新,日益融入经济社会发展各个领域和全过程。
清华大学著名战略专家演讲——企业战略 4

(四)公司目前的战略及其运行效 果
(五)公司面临哪些战略问题?(确定问题所在是制定战略的前提) 现行战略能否很好的防御五种竞争力量-特别是会激化竞争 的力量 是否应该调整当前的战略以便更好地对行业中重要的驱动因 素作出反应. 现行战略是否充分利用了公司的资源强势. 公司面临的哪些市场机会应该优先考虑,哪些该靠后,哪些 最适合公司的资源强势和能力. 要纠正公司的资源劣势和防范外部威胁,应该采取什么措施? 公司容易受到竞争对手行动的伤害程度如何? 公司是否拥有竞争优势? 现行战略的强点和弱点是什么? 是否需要采取额外的措施来提高公司的成本地位,利用新机 会,以及加强公司的竞争地位.
立即开始强化培养
原有能力
进出口交易
继续巩固加强
4. 企业核心竞争力的组成要素 (1)全体员工的知识和技能水平. )全体员工的知识和技能水平. 2)企业的技术体系. (2)企业的技术体系. (3)企业的管理体系. )企业的管理体系. (4)企业文化. )企业文化. (5)整合集成. )整合集成.
�
(四)公司目前的战略及其运行效果 1.是要成为一名低成本的领导者,还是使产品 具有差异化? 2.是聚焦于一个广泛的客户群,还是一个很小 的市场? 3.是涉及到任何价值链的每一个环节,还是专 注于几个关键环节? 4.公司的职能战略是否有效?最近的策略和行 动有哪些? 5.是否完成既定的战略目标和财务目标?业绩 是否处于行业的平均盈利水平以上?
(2)企业核心竞争力一般特征 所谓一般特征是指企业核心竞争力具有的特 征,而企业其他能力也可能不同程度地具有此 特征. ① 动态性.企业核心竞争力也有生命周期, 要防止企业核心竞争力的刚性,要不断抛弃过 时的,陈旧了的核心竞争力,不断培育新的核 心竞争力,因此需要对核心竞争力加以管理.
【专业文档】中国企业如何应对全面竞争的时代.doc
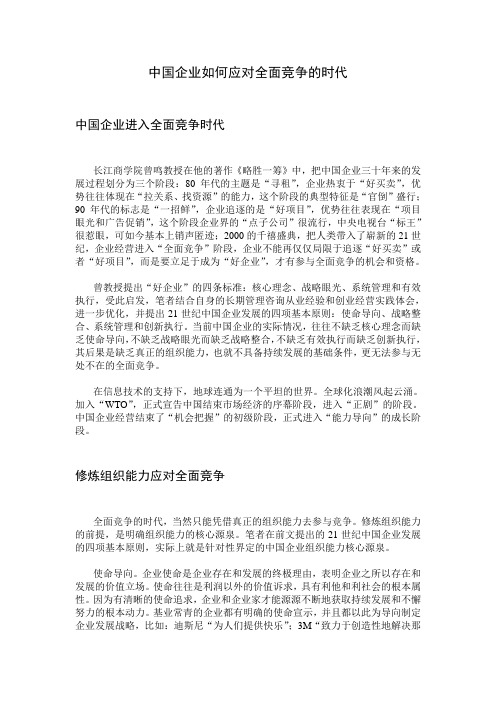
中国企业如何应对全面竞争的时代中国企业进入全面竞争时代长江商学院曾鸣教授在他的著作《略胜一筹》中,把中国企业三十年来的发展过程划分为三个阶段:80年代的主题是“寻租”,企业热衷于“好买卖”,优势往往体现在“拉关系、找资源”的能力,这个阶段的典型特征是“官倒”盛行;90年代的标志是“一招鲜”,企业追逐的是“好项目”,优势往往表现在“项目眼光和广告促销”,这个阶段企业界的“点子公司”很流行,中央电视台“标王”很惹眼,可如今基本上销声匿迹;2000的千禧盛典,把人类带入了崭新的21世纪,企业经营进入“全面竞争”阶段,企业不能再仅仅局限于追逐“好买卖”或者“好项目”,而是要立足于成为“好企业”,才有参与全面竞争的机会和资格。
曾教授提出“好企业”的四条标准:核心理念、战略眼光、系统管理和有效执行,受此启发,笔者结合自身的长期管理咨询从业经验和创业经营实践体会,进一步优化,并提出21世纪中国企业发展的四项基本原则:使命导向、战略整合、系统管理和创新执行。
当前中国企业的实际情况,往往不缺乏核心理念而缺乏使命导向,不缺乏战略眼光而缺乏战略整合,不缺乏有效执行而缺乏创新执行,其后果是缺乏真正的组织能力,也就不具备持续发展的基础条件,更无法参与无处不在的全面竞争。
在信息技术的支持下,地球连通为一个平坦的世界。
全球化浪潮风起云涌。
加入“WTO”,正式宣告中国结束市场经济的序幕阶段,进入“正剧”的阶段。
中国企业经营结束了“机会把握”的初级阶段,正式进入“能力导向”的成长阶段。
修炼组织能力应对全面竞争全面竞争的时代,当然只能凭借真正的组织能力去参与竞争。
修炼组织能力的前提,是明确组织能力的核心源泉。
笔者在前文提出的21世纪中国企业发展的四项基本原则,实际上就是针对性界定的中国企业组织能力核心源泉。
使命导向。
企业使命是企业存在和发展的终极理由,表明企业之所以存在和发展的价值立场。
使命往往是利润以外的价值诉求,具有利他和利社会的根本属性。
清华大学著名战略专家演讲——企业战略 2

世界经济一体化: ② 世界经济一体化: 全世界跨国公司数量增长一览表
20 世纪 20 世纪 1997 年 1999 年 53000 63459
60 年代 90 年代初 跨国公司数量 (个) 个 跨国公司的子公司数量 (个) 个 7276 37000
27300
170000
450000
689520
1999年跨国公司的经营状况一览 1999年跨国公司的经营状况一览 表 对外直接投资量金额 3.5 万亿美元
全球电子商务增长情况 美元
年份(年 年份 年) 销售额 营业收入 全球网页(个 全球网页 个) 互联网 上网人数 1998 500 - 3000 万 - 2000 3600 - - 3亿 2001 - 1000 - - 2002 - 11000 30 亿 - 2005 60000 - - 10 亿
单位: 单位: 亿
B. 知识经济的特点: 知识经济的特点: 知识经济的内部特征: ● 知识经济的内部特征: a. 知识成为最重要的生产要素和经济增 长的源泉. 长的源泉. b. 知识创新是知识经济发展的动力. 知识创新是知识经济发展的动力. c. 教育成为知识经济的中心,学习成为 教育成为知识经济的中心, 个人和组织生存的条件. 个人和组织生存的条件. d. 信息技术的发展是知识经济的关键因 素.
世界经济全球化及一体化对发展中国家带 来的冲击: 来的冲击 A. 发展中国家民族经济承受越来越大的压 力和冲击, 对发达国家依附性增大. 力和冲击 对发达国家依附性增大. B. 如果金融体制不完善 金融监管能力不 如果金融体制不完善, 盲目开放金融市场, 强, 盲目开放金融市场 则会削弱政府宏观金 融调控能力. 融调控能力. C. 自然环境受到污染 生态平衡遭到破坏 自然环境受到污染, 生态平衡遭到破坏, 资源浪费严重. 资源浪费严重. D. 加剧了世界经济发展的进一步不平衡. 加剧了世界经济发展的进一步不平衡. E. 发展中国家主权受到冲击和削弱. 发展中国家主权受到冲击和削弱. F. 国家经济安全受到挑战. 国家经济安全受到挑战.
面对全球竞争 中国企业应当有怎样的战略思维

面对全球竞争中国企业应当有怎样的战略思维?面对全球竞争,中国企业应当有怎样的战略思维?也就是说,在新的形势下,中国企业应该树立一种什么样的管理思想?这确实是大家都在思考的问题。
2000年我和几位学者一同出了一本书,书名是《中国企业管理面临的挑战与对策》,其中就提出了这个问题。
中国经济得以快速发展,企业所做的贡献是很大的。
企业是市场经济的细胞,没有千千万万个自主经营、自主决策的企业,市场经济是不可能发展起来的。
因此,认真思考和探讨企业今后靠什么发展,将有助于我们把握企业的未来。
中国经济并未过热,但是投资过热企业增长一般有两种类型,一是外延型,即靠增加投资来扩大生产能力,一是内涵型,即靠加强管理来提高经济效益。
我国近几年投资增长过快,很重要的一个原因,就是我国的企业往往偏重于外延型的发展。
我个人认为,从经济增长速度看,目前我国的经济还不能算过热,但是投资确实是过热了。
这可以从以下四个指标来分析:第一个指标是GDP对投资的弹性系数:即增加1%的投资,能够拉动GDP 增长多少。
这个系数在过去最高为1.29,2003年下降到0.38。
第二个指标是投资次年转化率:即第一年的投资有多少能够在第二年转化成GDP。
当然,投资不可能第二年就完全转化成GDP,但这一指标在一定程度上也表征着投资的效率。
从历史上看,最高是0.56,近几年只有0.21-0.24。
也就是说,每投资一块钱,第二年只有两毛多一点转化成GDP。
第三个指标是投资在GDP中所占的比重。
正常情况下占1/3左右,但2003年上升到44%。
最后一个指标是综合要素对经济增长的贡献率。
经济增长有三要素,即资本、劳力和综合要素。
综合要素包括科技、教育和管理等。
从历史上看,我国的综合要素贡献率为20-30%,发达国家达50%以上。
近两年来综合要素贡献率有所降低,有人说不到10%。
由此可见,我国的经济增长主要是靠投资拉动。
投资过热除了会降低经济效益以外,还会引起能源和运输的紧张,使经济难以持续增长。
21世纪企业的竞争
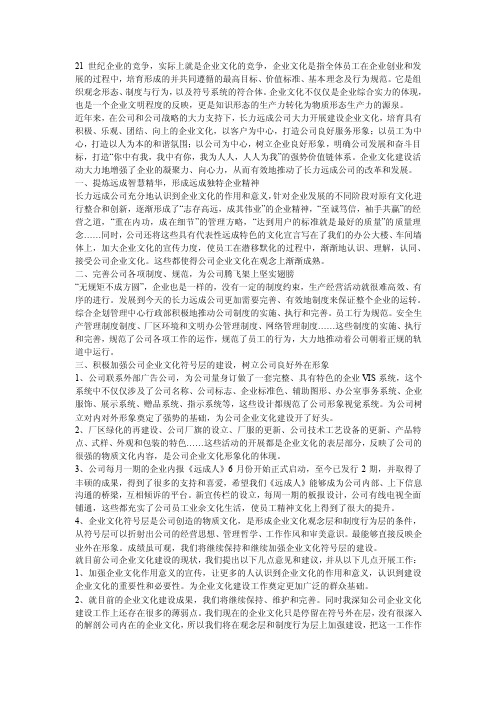
21世纪企业的竞争,实际上就是企业文化的竞争,企业文化是指全体员工在企业创业和发展的过程中,培育形成的并共同遵循的最高目标、价值标准、基本理念及行为规范。
它是组织观念形态、制度与行为,以及符号系统的符合体。
企业文化不仅仅是企业综合实力的体现,也是一个企业文明程度的反映,更是知识形态的生产力转化为物质形态生产力的源泉。
近年来,在公司和公司战略的大力支持下,长力远成公司大力开展建设企业文化,培育具有积极、乐观、团结、向上的企业文化,以客户为中心,打造公司良好服务形象;以员工为中心,打造以人为本的和谐氛围;以公司为中心,树立企业良好形象,明确公司发展和奋斗目标,打造“你中有我,我中有你,我为人人,人人为我”的强势价值链体系。
企业文化建设活动大力地增强了企业的凝聚力、向心力,从而有效地推动了长力远成公司的改革和发展。
一、提炼远成智慧精华,形成远成独特企业精神长力远成公司充分地认识到企业文化的作用和意义,针对企业发展的不同阶段对原有文化进行整合和创新,逐渐形成了“志存高远,成其伟业”的企业精神,“至诚笃信,袖手共赢”的经营之道,“重在内功,成在细节”的管理方略,“达到用户的标准就是最好的质量”的质量理念……同时,公司还将这些具有代表性远成特色的文化宣言写在了我们的办公大楼、车间墙体上,加大企业文化的宣传力度,使员工在潜移默化的过程中,渐渐地认识、理解,认同、接受公司企业文化。
这些都使得公司企业文化在观念上渐渐成熟。
二、完善公司各项制度、规范,为公司腾飞架上坚实翅膀“无规矩不成方圆”,企业也是一样的,没有一定的制度约束,生产经营活动就很难高效、有序的进行。
发展到今天的长力远成公司更加需要完善、有效地制度来保证整个企业的运转。
综合企划管理中心行政部积极地推动公司制度的实施、执行和完善。
员工行为规范。
安全生产管理制度制度、厂区环境和文明办公管理制度、网络管理制度……这些制度的实施、执行和完善,规范了公司各项工作的运作,规范了员工的行为,大力地推动着公司朝着正规的轨道中运行。
老师简介及课程提纲:
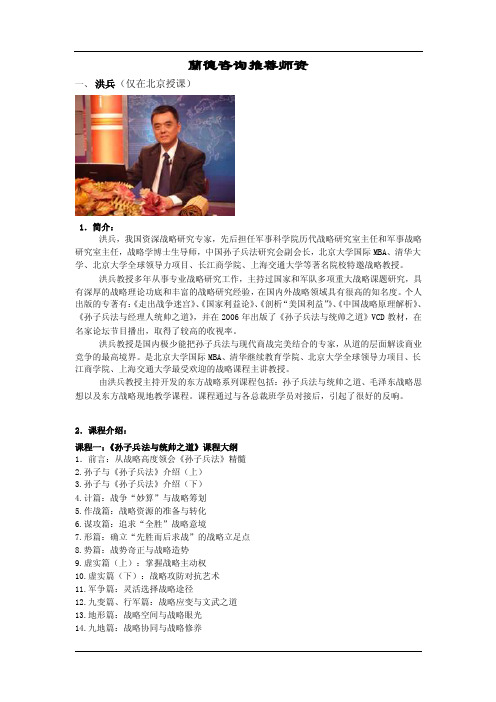
蘭德咨询推荐师资一、洪兵(仅在北京授课)1.简介:洪兵,我国资深战略研究专家,先后担任军事科学院历代战略研究室主任和军事战略研究室主任,战略学博士生导师,中国孙子兵法研究会副会长,北京大学国际MBA、清华大学、北京大学全球领导力项目、长江商学院、上海交通大学等著名院校特邀战略教授。
洪兵教授多年从事专业战略研究工作,主持过国家和军队多项重大战略课题研究,具有深厚的战略理论功底和丰富的战略研究经验,在国内外战略领域具有很高的知名度。
个人出版的专著有:《走出战争迷宫》、《国家利益论》、《剖析“美国利益”》、《中国战略原理解析》、《孙子兵法与经理人统帅之道》,并在2006年出版了《孙子兵法与统帅之道》VCD教材,在名家论坛节目播出,取得了较高的收视率。
洪兵教授是国内极少能把孙子兵法与现代商战完美结合的专家,从道的层面解读商业竞争的最高境界。
是北京大学国际MBA、清华继续教育学院、北京大学全球领导力项目、长江商学院、上海交通大学最受欢迎的战略课程主讲教授。
由洪兵教授主持开发的东方战略系列课程包括:孙子兵法与统帅之道、毛泽东战略思想以及东方战略现地教学课程。
课程通过与各总裁班学员对接后,引起了很好的反响。
2.课程介绍:课程一:《孙子兵法与统帅之道》课程大纲1.前言:从战略高度领会《孙子兵法》精髓2.孙子与《孙子兵法》介绍(上)3.孙子与《孙子兵法》介绍(下)4.计篇:战争“妙算”与战略筹划5.作战篇:战略资源的准备与转化6.谋攻篇:追求“全胜”战略意境7.形篇:确立“先胜而后求战”的战略立足点8.势篇:战势奇正与战略造势9.虚实篇(上):掌握战略主动权10.虚实篇(下):战略攻防对抗艺术11.军争篇:灵活选择战略途径12.九变篇、行军篇:战略应变与文武之道13.地形篇:战略空间与战略眼光14.九地篇:战略协同与战略修养15.火攻篇、用间篇:战略决策与战略信息16.东方战略的基本范畴与体系框架17.东方战略的神奇与魅力课程二:《全胜之道--洪兵谈孙子兵法与现代企业管理应用》二、史永翔:1.简介:中国著名企业管理顾问中国顶级实战派管理专家最具人气的企业管理教授外资跨国企业高级经理人背景曾经是中国人担任外资跨国企业的最高职位的人现担任:顶峰效益管理顾问有限公司——总裁国际经理人联合会(IMU)中国区――专家委员会主任兼首席专家中国效益管理网 CEO苏州经理人协会会长中国国家发改委国际合作中心中外经理人研究室副主任、首席专家中国清华大学研究院EMBA,客座教授人民大学商学院EMBA 客座教授中山大学EMBA《名家论坛》特约专家史永翔先生具有跨国企业高级经理人背景,历任多家外资跨国企业的财务总监、市场总监、营运总监、中国区总裁、亚太区总裁。
清华大学高级工商管理(总裁)研修班(北京)
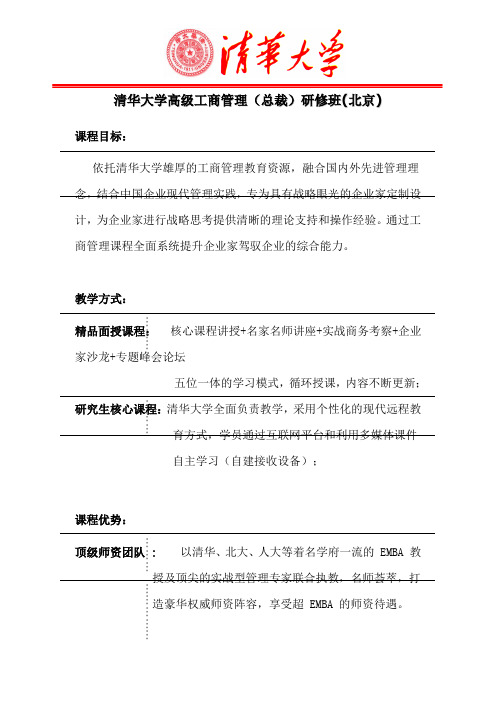
清华大学高级工商管理(总裁)研修班(北京)课程目标:依托清华大学雄厚的工商管理教育资源,融合国内外先进管理理念,结合中国企业现代管理实践,专为具有战略眼光的企业家定制设计,为企业家进行战略思考提供清晰的理论支持和操作经验。
通过工商管理课程全面系统提升企业家驾驭企业的综合能力。
教学方式:精品面授课程: 核心课程讲授+名家名师讲座+实战商务考察+企业家沙龙+专题峰会论坛五位一体的学习模式,循环授课,内容不断更新;研究生核心课程:清华大学全面负责教学,采用个性化的现代远程教育方式,学员通过互联网平台和利用多媒体课件自主学习(自建接收设备);课程优势:顶级师资团队 : 以清华、北大、人大等着名学府一流的 EMBA 教授及顶尖的实战型管理专家联合执教,名师荟萃,打造豪华权威师资阵容,享受超 EMBA 的师资待遇。
……………………………………模块课程设计: 创造性的模块式课程设计,按知识的递进关系依次开展,使学习过程更为合理,更易于掌握和巩固所学知识。
严谨、周到的教学管理与服务秉承严谨治学的风格,参照 EMBA 管理模式,对教师、学员、讲义、案例、课前参考、课后指导、安排等每一个环节都进行严格管理。
力争让学习成为一个快乐的体验过程,享受学习带来的无穷乐趣。
总裁级校友会 : 遍及全国的所有学员都是企业的高层决策人员,工作经验丰富,管理基础厚实,在同等水平上展开的互动教学的效果得以显着提升,而由同学关系产生的合作、交流更是彰显校友平台的巨大价值。
全景案例分享: 所有课程均采用 MBA 案例教学讨论,学员课程既在重点城市上课,又可实现在百年名校清华大学求学的梦想,全面提升课程品质。
移动课堂授课: 主教师设在清华大学,同时按学员要求在其他优秀企业密集的地方开设移动课堂,参观学员的优秀企业。
课程设置:模块一:学习热身,自我评估与建立同学友谊…………………本模块将在以体验式训练的方式进行,通过八个体验课程的参与式训练,让学员重新认识自我,挑战并超越自我,同时迅速建立同学友谊,熔炼新团队。
清华大学著名战略专家演讲——企业战略 7
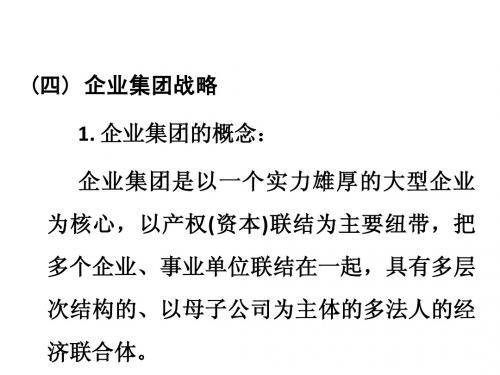
建立一个有竞争力的组织是战略实施的基础: 建立一个有竞争力的组织是战略实施的基础: (1) 战略的变化往往要求企业的组织结构发生相应的变 化 – 组织结构是战略实施的组织保证. 组织结构是战略实施的组织保证. (2)地区性的组织与产品性的组织的目标与政策描述是 地区性的组织与产品性的组织的目标与政策描述是 不一样的. 不一样的. – 组织结构往往决定了资源的分配. 组织结构往往决定了资源的分配. (3)不同企业的发展阶段,不同规模,不同的战略目标 不同企业的发展阶段, 不同企业的发展阶段 不同规模, 决定不同的组织形式. 决定不同的组织形式. – 消费品企业倾向于按照产品设置组织. 消费品企业倾向于按照产品设置组织. – 小企业采取集中式的职能结构. 小企业采取集中式的职能结构. – 中型企业采取分部结构. 中型企业采取分部结构. – 大型企业采取事业部,子公司或矩阵式组织结构. 大型企业采取事业部,子公司或矩阵式组织结构.
十三, 十三,危机管理
1. 危机管理的概念:危机管理是以市场 危机管理的概念: 竞争 中危机可能出现为目标,分析危机产生的 中危机可能出现为目标, 原因 和过程研究应付危机的规则, 和过程研究应付危机的规则,方法和企业 反危 机行为的机制, 机行为的机制,探讨企业预防危机的手段 和策 略的一门学科. 略的一门学科.
(四) 企业集团战略 1. 企业集团的概念: 企业集团的概念: 企业集团是以一个实力雄厚的大型企业 为核心,以产权(资本 联结为主要纽带, 资本)联结为主要纽带 为核心 , 以产权 资本 联结为主要纽带 , 把 多个企业,事业单位联结在一起, 多个企业,事业单位联结在一起,具有多层 次结构的, 次结构的,以母子公司为主体的多法人的经 济联合体. 济联合体.
4. 企业集团公司的类型: 企业集团公司的类型: 纯粹型控股公司和混合型控股公司. 纯粹型控股公司和混合型控股公司. 5. 企业集团的类型: 企业集团的类型: (1)垂直型: 垂直型: 垂直型
企业创新发展演讲稿
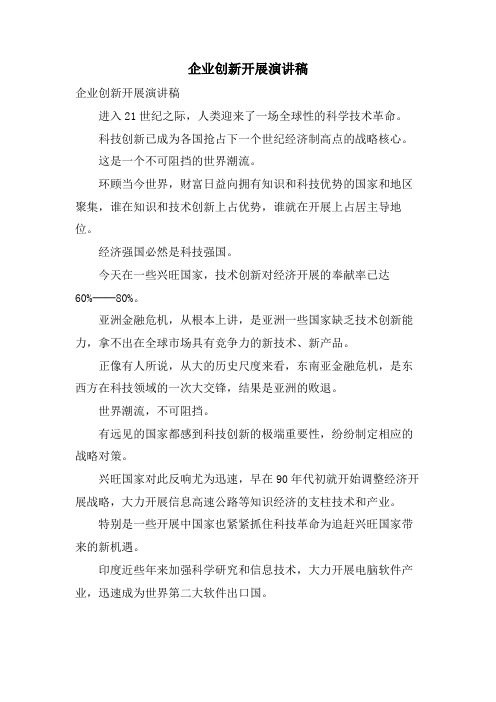
企业创新开展演讲稿企业创新开展演讲稿进入21世纪之际,人类迎来了一场全球性的科学技术革命。
科技创新已成为各国抢占下一个世纪经济制高点的战略核心。
这是一个不可阻挡的世界潮流。
环顾当今世界,财富日益向拥有知识和科技优势的国家和地区聚集,谁在知识和技术创新上占优势,谁就在开展上占居主导地位。
经济强国必然是科技强国。
今天在一些兴旺国家,技术创新对经济开展的奉献率已达60%──80%。
亚洲金融危机,从根本上讲,是亚洲一些国家缺乏技术创新能力,拿不出在全球市场具有竞争力的新技术、新产品。
正像有人所说,从大的历史尺度来看,东南亚金融危机,是东西方在科技领域的一次大交锋,结果是亚洲的败退。
世界潮流,不可阻挡。
有远见的国家都感到科技创新的极端重要性,纷纷制定相应的战略对策。
兴旺国家对此反响尤为迅速,早在90年代初就开始调整经济开展战略,大力开展信息高速公路等知识经济的支柱技术和产业。
特别是一些开展中国家也紧紧抓住科技革命为追赶兴旺国家带来的新机遇。
印度近些年来加强科学研究和信息技术,大力开展电脑软件产业,迅速成为世界第二大软件出口国。
韩国制定了“科技创新法”并成立了由总统任委员长的国家科技委员会。
我国是一个开展中国家。
新中国成立后,我们用五十年时间走完了兴旺国家需要用上百年所走过的历程,实现了工业化。
这其中的重要原因是我们掌握了国家政治命运后,整个民族的科学文化水平得到空前提高。
历史证明,技术跨越开展是后进国家追赶并超过先进国家的根本道路。
自产业革命以来,世界经济和科技的中心从英国到德国、再到美国,以及后来日本、韩国的迅速崛起,无不是依靠科技进步、实现技术跨越的结果。
新中国的历史更证明,创新是一个国家经济实现跨越式开展的动力。
六七十年代,我国成功地研制了“两弹一星”。
这一举世公认的创新极大地带动了我国科技进步,仅从1960年到1966年科研机构就试制了近4000种新材料,辐射出4800多项科技攻关工程,带动了1300多个企业,促进了一大批新兴产业的形成和开展。
清华大学著名战略专家,chengwei总裁的演讲-21世纪新竞争环境下中国企业发展战略(2)
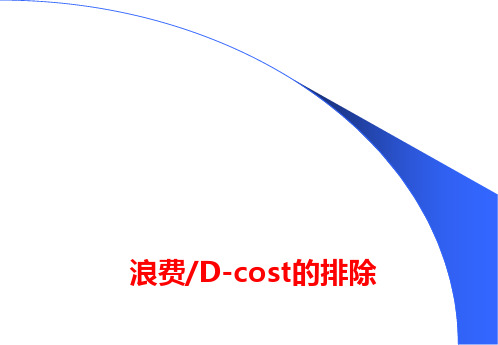
·超前生产的浪费 → 库存/搬运/管理
·转换的浪费
→ 工序变更/设备变更/熟练
·计划变更的浪费 → 步骤/剩余库存
·计划变更的浪费 → 材料定购的修正/剩余库存 ·备料提高的浪费 → 人员/经费 ·剩余设备(模具)的浪费 → 制作费/管理
·移动的浪费 ·装卸货的浪费 ·库存的浪费 ·寻找存货处的浪费
無駄=设备引起的浪费
ムダ=操作上没有任何必要的东西 =可马上省掉的东西
无效作业 会议 (无效工数)联络
表彰
间接业务 (支持业务)
制造记述 质量保证 综合 人事
产生附加价值的作业 只占总量的2成
工作的大部分都是 ムダ、無駄、むだ
产生附加价值的作业=净作业
加工部件
折弯
切断
冲压
组装 铆接
焊接
喷粉
(全部作业的2成)
浪费/D-cost的排除
改善的实施 (方法)
1) 不引入、不生产、不放出不良品 2)浪费的削减
生产效率的提高
通过排除浪費的带来利益UP
☆ 要扩大利益 是提高卖价 (Price UP ) ?,
还是削减成本(Cost) ?
利益
提高卖价(Price UP) 可能吗?
卖价
成本 要素 成本
有即使贵也能被顾客购买的商品魅力吗? 卖价由用戸决定
=能马上省掉的东西
待工
堆放部件
寻找
解包装
放置
走着去取部件
考虑
除掉粉尘
返工
部件、工装的换手操作
能马上小简
何谓浪费、 D-Cost ?
在各经过,「从开始确实」不被进行为了发生, 多余的费用的总计,无效成本
Defect Cost. Do it right the first time. Do it right next time.
清华大学讲师亲自讲解企业如何在竞争中取胜!

清华大学讲师亲自讲解企业如何在竞争中取胜!产业竞争的本质到底是什么?一个产业在竞争体系中,它的本质,不是规模。
我们改革开放30年,相当一大批快速成长的企业,追求的都是规模大,不一定是品质高,不一定是效率高。
只觉得规模大就好,地多、厂房多、设备多、人多、贷款多......所以他追求的是大。
内在的隐含是我大到不能死,我大到能绑架政府,绑架银行,就得必须给我钱,我才能持续发展。
这些年,我在国内看到好多企业,也遇到一个现象,就是这些企业已经沦为现金流依赖型企业。
什么意思呢?他不追求有利润,只求现金流不断,活着就好了。
所以他经常,新的贷款来还老的贷款,然后再有新的贷款,再还上一个贷款,反正不停的通过一轮一轮这种方式来做。
但是他追求大,他觉得放眼望去几百亩地是我的,放眼望去,这几十间厂房是我的,他感觉还挺好。
其实你仔细看总资产规模可能达八十个亿,但是负债率可能达到百分九十几,其实这样的公司还是比较脆弱的。
这个时候问题来了,到底我们走到今天做企业,是追求规模至上还是效率至上?其实在产业的整个逻辑体系中,隐含了一个内在标准:产业竞争的本质,不是规模大小,而是效率的高低,效率的来源是速度,不是规模,就是谁比谁更快。
我的资金周转速度比你快,我的产品研发速度比你快,我的整个生产周期比你短,我的物流供应链比你用时短......谁能够快速反应市场,反应客户可能才是第一位的。
在强调一遍产业竞争的本质是效率,效率的来源是速度而不是规模。
我们做企业应该要强化我们的内在运转速度和内在运转效率,响应和支持业务的高速发展。
在这个过程中,我们也经常遇到很多企业他说:“你赶紧来看看我们家的管理,我们家管理特别乱。
”我就问:“你们家管理乱成什么样子呢?”他说:“流程冗长、职责不清、管理混乱、岗位设置不合理、人浮于事、工资奖金绩效考核不公平。
”我就问:“现在这个行业是不是在快速发展?”他说:“对。
”我说:“你们公司是不是很挣钱?”他说:“是。
- 1、下载文档前请自行甄别文档内容的完整性,平台不提供额外的编辑、内容补充、找答案等附加服务。
- 2、"仅部分预览"的文档,不可在线预览部分如存在完整性等问题,可反馈申请退款(可完整预览的文档不适用该条件!)。
- 3、如文档侵犯您的权益,请联系客服反馈,我们会尽快为您处理(人工客服工作时间:9:00-18:30)。
不产生附加价值的作业=附带作业(作业总量的6~7成左右)
むだ=现在的作业环境、条件下有必要
本来不必要的东西
调整
修整
改善
测定
用手递送成品、部件
检查
部件、工装等的分配、供应
清扫
各种机械、工装的使用
手动
按按钮钮的的操作操作
复位操作
無駄=因设备引起的浪费 油压、空压作业的空转 多余的设备 超需求生产
改善
ムダ=在作业上不必要的作业
意见的调查
哇!!!
好巨大呀!
DSoenfyecHtuCmoasntC. a缺pi陷tal成Co本rp.
销售额? ⇒
万元
浪费额? 30% ⇒
万元
若能将这些削减的话会立即产生利益
以从业人员 2000人来算的话
一个人就是
万元
让我们减少浪费吧!!
何谓muda/無駄(浪费)? 生产效率100%的理论值(生产能力上限) 与生产能力现状的差值就是浪費
增加很多工人的劳务费
搬运不会产生价值、但会发生费用
检查也不会产生价值、只会发生费用
消耗的部分作为材料费可用销售额来填补, 但未被使用的部分需补贴费用 一組动作中,包含伸手、运送 等无价值动作,这将増加成本 原材料的不良損耗、修理工人的劳务费等发生, 原价被提高
导入CELL(单元)生产方式 只制造需要的产品
成品等的保管
产品等的搬运
产品的数量核对
票据等的打印
改造改班进吉工工装幸厂田(马工厂来(西爱亚知县) )
运转设备的监视
重物的长距离搬运
产品作成过多的话那个管理
改善事例
ムダ、無駄、むだ
业务 作业
直接业务 设计 制造
有效作业 有效工数
不产生附加价值的作业=附带作业
むだ=现在的作业环境下必要, 本来不需要的东西
应该排除的3个浪费
库存浪费
库存是最大的浪费,会 掩盖真正的浪费
①有无超过需要以上的货物滞留 ②工作者是否手头没活干空闲 ③有无工序间的停顿和在制积存
滞留的浪费 待工的浪费 生产过多的浪费
搬运浪费
只是将物品从A搬到B,时 间、劳力(动作),设备 浪费成为浪费
①可否减少搬运的动作? ②可否减少搬动物品的距离? ③能否去掉放置物品的动作
(排除浪费后的成本)
结论
排除包含在投入 中(劳动费,经费)中 的浪費→生产率提高。 成本削减→利益扩大。
1.这样的现实使得获利及资金筹措恶化
产品的装卸 设备的故障
等待接收材料
寻找材料和工具 修复,修理
缺陷产品
因缺件引起的停线
幸田工厂(爱知县) 槟城工厂(马来西亚)
2.这样的工作「阻碍效率的主要原因=是徒劳」
生产效率的构成 現場
投入量
生产效率只有80% 就说明存在20% 的浪費
产品或者 服务
产出量
無駄/浪費=不能将投入量转化为产出量的要素
在进行生产效率改善前有必要掌握 生产能力上限理论值
应该排除的3个浪费
「所谓『浪费」是指无论花多少时间也不能转化成钱(利益)的作业、 动作,以及由此产生的人・物料 ・钱 ・空间
经营革新
浪费/D-cost的排除
改善的实施 (方法)
1) 不引入、不生产、不放出不良品 2)浪费的削减
生产效率的提高
通过排除浪費的带来利益UP
☆ 要扩大利益 是提高卖价 (Price UP ) ?,
还是削减成本(Cost) ?
利益
提高卖价(Price UP) 可能吗?
卖价
成本 要素 成本
有即使贵也能被顾客购买的商品魅力吗? 卖价由用戸决定
=能马上省掉的东西
待工
堆放部件
寻找
解包装
放置
走着去取部件
考虑
除掉粉尘
返工
部件、工装的换手操作
能马上小简
何谓浪费、 D-Cost ?
在各经过,「从开始确实」不被进行为了发生, 多余的费用的总计,无效成本
Defect Cost. Do it right the first time. Do it right next time.
用线体均衡分析法 排除瓶颈工序
通过物流设计,布局改善, 达到最小限度的搬运
「从最初开始正确·DIRTFT」的指 导和彻底防止复发/防患于未然
看板方式与店/冰箱、领取方式 的组合
工作领域的设计和作业 标准书的整理・整备及指导
动作浪费
不良.修正的浪费 加工本身的浪费 待工的浪费
库存的浪费
生产过多的浪费
停滞的浪费
搬运的浪费
时间的浪费 动作的浪费 设备的浪费
生产现场浪费的发现方法
动作浪费
动作的浪费是指花在操 作上的时间浪费
①是否在最佳位子上工作 (工作区30㎝以内) ②有返工动作吗 ? (重新排列) ③能否缩短工作时间 (方法·工夹具改善) ④工作本身可否减少
从工厂这个视角来归结,有7种浪費
7种浪费
1
生产不必要产 品的浪費
2
操作者工作负荷 不满的浪費
3
进行无价值工作 的浪費
4
检查等安全性 工序设置的浪費
5
不必要原材料 库存的浪费
6 多余动作的浪费
7
生产了不良品· 缺陷品的浪费
对经营的不良影响
索尼的改善
只会增加货架投入和管理成本 产生仓库费等原来不必要的费用
浪费 (与原价利益关系)
如果能够消去这部分浪费,就能直接转化成利益。
如果进行成本分析muda(浪費)能的 演员的效果
利益拡大
经费 劳务费 材料费
经费
注意不到 的浪费
劳务费
材料费
生产效率的产生构造
投入量
生产现场
产出量
生产效率=
产出量 投入量
(与成本利益关系) (包含浪费的原价)
無駄=设备引起的浪费
ムダ=操作上没有任何必要的东西 =可马上省掉的东西
无效作业 会议 (无效工数)联络
表彰
间接业务 (支持业务)
制造记述 质量保证 综合 人事
产生附加价值的作业 只占总量的2成
工作的大部分都是 ムダ、無駄、むだ
产生附加价值的作业=净作业
加工部件
折弯
切断
冲压
组装 铆接
焊接
喷粉
(全部作业的2成)
缺陷成本 从开始就做对 下次也要做对
使D-Cost可视化 是业务改善的第1歩
何谓浪费、 D-Cost ?
检查 补偿保证 产品报废 再订货·再生产
销售额的 5~8%
合起来的话占销 售额的15~28% ,是可见浪费的 4~5倍
能看见
原材料·零部件的报废 回收·修理
看不见
制造工序重新评估
设计变更
工作标准重新评估/修改
顾客版权使用费的丧失
销售额的 15~20%
替换件的评价
包括看不见的损失 冰山的全部 即 D-cost
既存顾客的丧失
生产线的切换
进入新市场的失败
销售额的丧失
检查机能重新评估 工作者的再训练
供应商的评价 质量控制重新评估/修改
安全性/可靠性重新评估
应急线的设定 竞争对手先取得专利权
减价偿还的负担增加 库存的增加