上引法连铸机组产品简介
上引法操作工艺守则
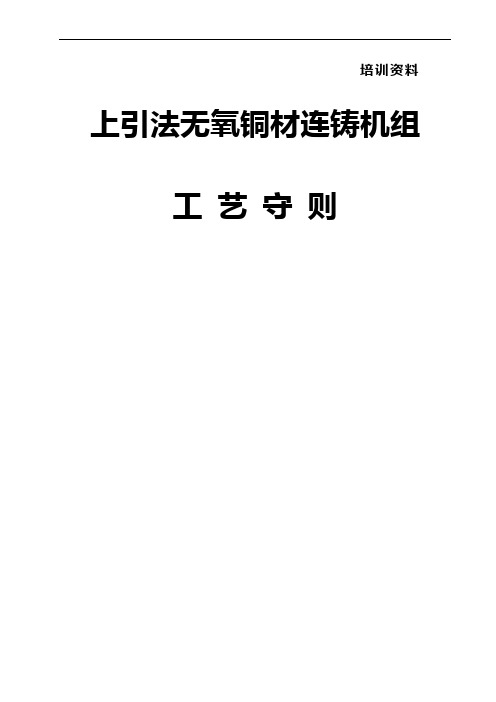
上引法无氧铜材连铸机组
工艺守则
一、主题内容与适用范围
本守则规定了上引法无氧铜材连铸工艺的材料准备、熔化炉(腔)、中间炉(腔)、保温炉(腔)操作;铸杆、收线、水系统、气源系统控制;安全生产要求及检验规范。
二、原材料、辅助材料技术要求
1.对原材料的技术要求:
1)对标准阴极铜技术要求:
由于上引法设备只进行熔化和铸造,因而不能对铜进行精炼,为了保证光亮无氧铜杆的质量,标准阴极铜应符合GB/T467-1997标准。
四、铸杆
1.结晶器准备
1)对新的和使用期超过半个月的结晶器,应进行检查,内管是否变形,密封圈是否已老化,污垢是否已清除,合格后进行水压试验,水压为1Mpa保持20分钟不漏水。1.8~2MPa保持10分钟,允许有轻微渗水。
2)准备装配石墨模时,应把结晶器内螺纹用标准丝锥,对丝牙回一遍,清除垃圾,把检验合格的石墨模,旋入结晶器,端面到位。
7)清灰工具必须涂上涂料,并烘干后使用,以防粘铜或铜液增铁。严禁将潮湿未烘干的工具浸入铜液,以免铜液爆炸,造成事故。
(1)涂料配方
石墨粉:25%~30%
水玻璃:5%
水:适量
(2)涂刷方法
当选用工具预热到150~200℃时将涂料涂刷或喷涂于用工具上,然后放于炉口烘干。
2.保温炉的操作
1)保温炉引杆腔铜液温度控制在:
若铜杆规格稍有改动,引速应作适当调整。
2)经常检查铜杆表面质量,观察结晶器、水套、线圈的进出水温度,及结晶器插入深度,液位跟踪系统工作状况,如遇异常情况,及时排除。
3)浮子要经常检查,随时调整。
五、收线
1.收线时将引锭头头部切除,将铜杆通过限位装置,穿过并夹紧收线导轮,引入收线盘内。
2.铜杆进入收线盘后,由于各铜杆之间有温度差异会产生弯曲,为保持排线整齐,可用木板轻轻拍齐。
上引连铸法生产合金铜杆

上引连铸法生产合金铜杆
王荣巧
【期刊名称】《江苏冶金》
【年(卷),期】1999(027)002
【摘要】本文就上引连铸法生产铜合金杆连铸过程中各种因素,对铜杆质量的影响及如何控制有关工艺参数进行技术探讨。
【总页数】2页(P56-57)
【作者】王荣巧
【作者单位】江苏省冶金研究所
【正文语种】中文
【中图分类】TG291
【相关文献】
1.上引法连铸铜杆质量问题的探讨 [J], 庄琴云
2.上引连铸法生产铜杆及铜杆加工 [J], 高连元
3.提高上引法连铸铜杆质量问题的探讨 [J], 叶永春
4.对国产SL—Y型上引法无氧铜杆连铸机间歇机构的改进设计 [J], 王更生
5.奥托昆普上引法连铸铜杆的质量控制 [J], 张咏生
因版权原因,仅展示原文概要,查看原文内容请购买。
基于SNAPPAC的上引法连铸机组智能化改造
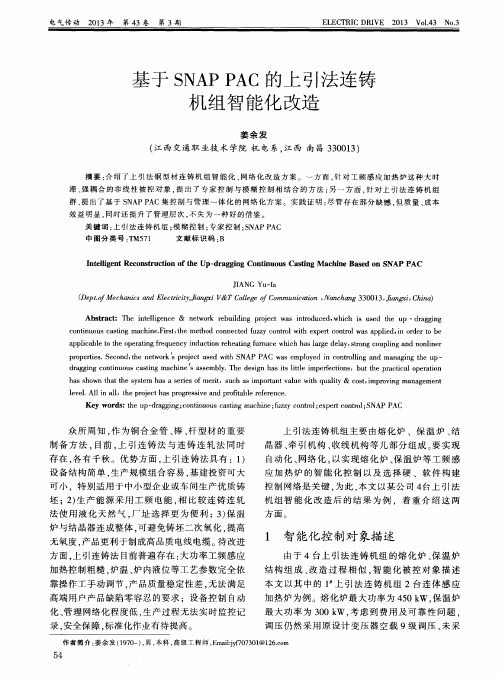
l e v e 1 . A l l i n l a l , t h e p r o j e c t h a s p r o g r e s s i v e a n d p r o f i t a b l e r e f e r e n c e . Ke y wo r d s : t h e u p — d r a g  ̄n g ; c o n t i n u o u s c a s t i n g m a c h i n e ; f u z z y c o n t r o l ; e x p e t r c o n t r o l ; S N A P P AC
J I ANG Yu — f a பைடு நூலகம்
( D e p t . f Me o c h a n i c s a n dE l e c t r i c i t y , J i ng a x i V &TC o l l e g e o fC o m mu n c i a t i o n, N nc a h a n g 3 3 0 0 1 3 , J i a n g x i , C h i n a )
d r a g g i n g c o n t i n u o u s c a s t i n g ma c h i n e s a s s e mb l y . T h e d e s i g n h a s i t s l i t t l e i mp e r f e c t i o n s ,b u t t h e p r a c i t c a l o p e r a t i o n h a s s h o w n t h a t t h e s y s t e m h a s a s e ie r s o f me i r t ,s u c h a s i mp o r t a n t v a l u e wi t h q u a l i t y& c o s t , i mp r o v i n g ma n a g e me n t
上引连铸的工作原理及影响因素分析

K e r s: o i o s y wo d c ntnu u up a tng; ol to o a l y; on i o s a tn o d;nt r a e f t e c si s u i n f lo c tnu u c s i g m l i e f c o h s ld nd i i o i a lqu d
统 、熔 液 冷 却 结 晶 系 统 、牵 引 系 统 、收 线 系 统 组 成 【 l 】 0
熔化系统 : 对金属块进行加热熔化,并对熔液
作者简介 :覃 向忠 ( 9 2一) 男. 17 . 广西融水人。 高级工程师 , 事银 从 基触头材料 的研究开发和生产管理。 收稿 日期 :2 0 —1 —1 09 1 2
经过铸 造 、 挤压 、 拔 、 拉 轧制 等 加工 过 程 , 缩短 了加 工 周 期,降低 了加工 过 程 的污 染及 损耗 ;连 续 生产 能力大 ,单炉 生产 能 力可达 5 0k ,甚至 可生 产连 0 g
续 的线材 、板材 ;可根 据需 要 生产 不 同外 径 的线材 和板 材。 目前该 方法 大 量应 用于 无 氧铜 线 、钢 材 的
QI Xi n -h n , LI Zh n p n , LI H u N a g z o g e -e g U i
( i n Co i s e tia Gu l n n tElc rc l& Elcr nc Ma e ilCo Lt , ii 4 0 4 Ch n i e to i tra . d.Gu ln 5 1 0 , ia)
Ab t a t Th p i i l o t c ntn u u c s i e i m e whi h src : e r nc p e f he o i uo s p a tng qu p nt c m a f c u e wie nu a t r s r fo r m m e a or lo e t s nt o uc d. Th m a n a t r t t a i f u nc t e ua iy f t l a l y m l i i r d e e i f c o ha m y n l e e h q lt o t c tnu u up a t d he on i o s c se w ie s na y e r i a l z d.
CuSi3Mn_合金上引连铸工艺参数的研究

第14卷第6期2023年12月有色金属科学与工程Nonferrous Metals Science and EngineeringVol.14,No.6Dec. 2023CuSi3Mn 合金上引连铸工艺参数的研究胡玉军1,2, 张迎晖*1, 艾迪1, 张兵1,2, 旷军平3(1.江西理工大学材料冶金化学学部,江西 赣州 341000; 2.江西师范高等专科学校航空工程学院,江西 鹰潭 335000;3.江西广信新材料股份有限公司,江西 鹰潭 335000)摘要:CuSi3Mn 合金是一种可适用于异种金属(铜与钢)焊接且性能优越的焊接材料,然而该合金凝固区间宽、黏度大,上引连铸生产过程易出现表面裂纹、凹坑和断杆等问题。
为此,采用ProCast 有限元软件对上引连铸CuSi3Mn 合金杆成形过程进行数值模拟,研究了模具结构、上引温度、上引速度和合金成分对上引连铸过程中合金糊状区深度和凝固组织的影响规律。
结果表明,适当降低Si 含量,提高Mn 含量和上引速度,有利于细化晶粒,提高等轴晶率;降低一冷区高度和减小模具厚度、提高上引温度,可减小糊状区深度,有利于凝固组织稳定生长,但铸坯晶粒尺寸增大,等轴晶率降低。
在合金Si 含量为2.8%~3.0% (质量分数)、Mn 含量为1.0%~1.2% (质量分数),采用4号模具,控制上引速度为4~5 mm/s ,上引温度为1 040~1 140 ℃的较优条件下,可成功生产出质量合格的CuSi3Mn 合金杆。
关键词:CuSi3Mn 合金;上引连铸;数值模拟;糊状区;凝固组织中图分类号:TG291;TG146.11 文献标志码:AResearch on process parameters of CuSi3Mn alloy underupward continuous castingHU Yujun 1, 2, ZHANG Yinghui *1, AI Di 1, ZHANG Bing 1, 2, KUANG Junping 3(1. Faculty of Materials , Metallurgy and Chemistry , Jiangxi University of Science and Technology , Ganzhou 341000, Jiangxi , China ;2. School of Aeronautical Engineering , Jiangxi Teachers College , Yingtan 335000, Jiangxi , China ;3. Jiangxi Guangxin New Materials Co., Ltd., Yingtan 335000, Jiangxi , China )Abstract: CuSi3Mn alloy is an excellent welding material that can be used for welding dissimilar metals between copper and steel. However, it has some problems such as, a wide solidification temperature range, high viscosity, surface cracks, pits, broken rods in the production of upward continuous casting. In this paper, ProCast finite element method software was used to numerically simulate the upward continuous casting forming process of the CuSi3Mn alloy rod. The influence laws of alloy composition, die structure, casting temperature and casting speed on the depth of the mushy zone and solidification microstructure during the solidification process were systematically investigated. The results showed that decreasing the Si content, but increasing the Mn content and casting speed was beneficial to refine grain and increase the equiaxed crystal ratio. Reducing the first cold zone height and the die thickness but increasing the casting temperature could reduce the depth of the mushy zone, which was conducive to the stable growth of the solidified structure. However, the equiaxed crystal ratio decreased with the increasing of grain size. Finally, the CuSi3Mn alloy rod with qualified quality could be successfully produced, when its Si content was 2.8%‒3.0% (mass percentage) and Mn content 1.0%‒1.2% (mass percentage), with No.4收稿日期:2023-02-19;修回日期:2023-03-25通信作者:张迎晖(1968— ),博士,教授,主要从事金属材料组织及性能控制方面的研究。
上引法生产大载荷水冷铜导体工艺探究
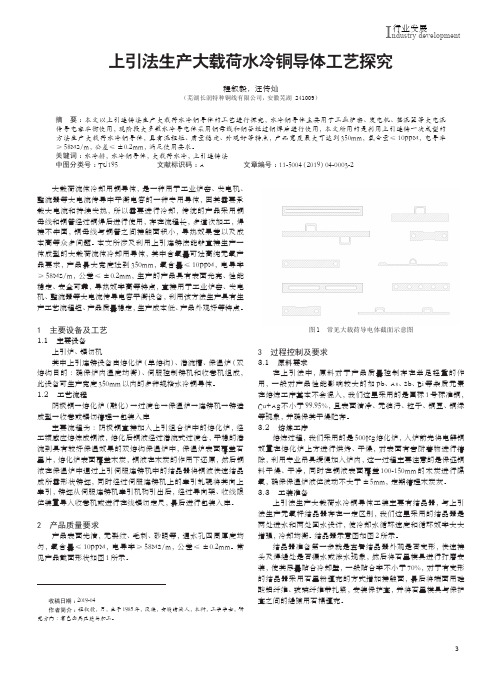
3I ndustry development行业发展上引法生产大载荷水冷铜导体工艺探究程叙毅,汪传灿(芜湖长润特种铜线有限公司,安徽芜湖 241009)摘 要:本文以上引连铸法生产大载荷水冷铜导体的工艺进行探究,水冷铜导体主要用于工业炉窑、发电机、整流器等大电流传导电容平衡使用,现阶段大多数水冷导电体采用铜母线和铜管经过铜焊后进行使用,本文所用的是利用上引连铸一次成型的方法生产大载荷水冷铜导体,具有流程短、质量稳定、外观好等特点,产品宽度最大可达到350mm,氧含量≤10PPM,电导率≥58MS/m,公差≤±0.2mm,满足使用要求。
关键词:水冷排,水冷铜导体,大载荷水冷,上引连铸法中图分类号:TU195 文献标识码:A 文章编号:11-5004(2019)04-0003-2收稿日期:2019-04作者简介:程叙毅,男,生于1985年,汉族,安徽绩溪人,本科,工学学士,研究方向:有色金属压延与加工。
大载荷流体冷却用铜导体,是一种用于工业炉窑、发电机、整流器等大电流传导中平衡电容的一种专用导体,因其需要承载大电流和持续发热,所以需要进行冷却,传统的产品采用铜母线和铜管经过铜焊后进行使用,存在流程长,多道次加工,焊接不牢固,铜母线与铜管之间接触面积小,导热效果差以及成本高等众多问题。
本文所涉及利用上引连铸法能够直接生产一体成型的大载荷流体冷却用导体,其中含氧量可达高纯无氧产品要求,产品最大宽度达到350mm,氧含量≤10PPM,电导率≥58MS/m,公差≤±0.2mm,生产的产品具有表面光亮、性能稳定、安全可靠,导热效率高等特点,直接用于工业炉窑、发电机、整流器等大电流传导电容平衡设备,利用该方法生产具有生产工艺流程短、产品质量稳定,生产成本低、产品外观好等特点。
1 主要设备及工艺1.1 主要设备上引炉、锯切机其中上引连铸设备由熔化炉(单熔沟)、潜流槽、保温炉(双熔沟目的:确保炉内温度均衡)、伺服控制铸机和收卷机组成,此设备可生产宽度350mm 以内的多种规格水冷铜导体。
上引法连铸的工艺与设备
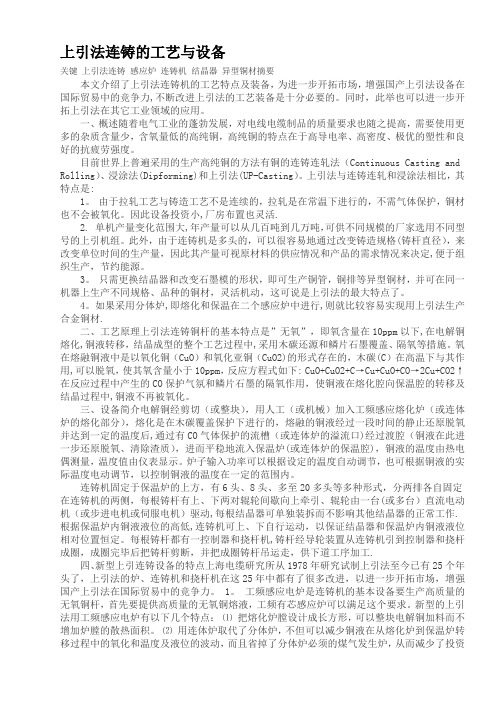
上引法连铸的工艺与设备关键上引法连铸感应炉连铸机结晶器异型铜材摘要本文介绍了上引法连铸机的工艺特点及装备,为进一步开拓市场,增强国产上引法设备在国际贸易中的竞争力,不断改进上引法的工艺装备是十分必要的。
同时,此举也可以进一步开拓上引法在其它工业领域的应用。
一、概述随着电气工业的蓬勃发展,对电线电缆制品的质量要求也随之提高,需要使用更多的杂质含量少,含氧量低的高纯铜,高纯铜的特点在于高导电率、高密度、极优的塑性和良好的抗疲劳强度。
目前世界上普遍采用的生产高纯铜的方法有铜的连铸连轧法(Continuous Casting and Rolling)、浸涂法(Dipforming)和上引法(UP-Casting)。
上引法与连铸连轧和浸涂法相比,其特点是:1。
由于拉轧工艺与铸造工艺不是连续的,拉轧是在常温下进行的,不需气体保护,铜材也不会被氧化。
因此设备投资小,厂房布置也灵活.2. 单机产量变化范围大,年产量可以从几百吨到几万吨,可供不同规模的厂家选用不同型号的上引机组。
此外,由于连铸机是多头的,可以很容易地通过改变铸造规格(铸杆直径),来改变单位时间的生产量,因此其产量可视原材料的供应情况和产品的需求情况来决定,便于组织生产,节约能源。
3。
只需更换结晶器和改变石墨模的形状,即可生产铜管,铜排等异型铜材,并可在同一机器上生产不同规格、品种的铜材,灵活机动,这可说是上引法的最大特点了。
4。
如果采用分体炉,即熔化和保温在二个感应炉中进行,则就比较容易实现用上引法生产合金铜材.二、工艺原理上引法连铸铜杆的基本特点是”无氧”,即氧含量在10ppm以下,在电解铜熔化,铜液转移,结晶成型的整个工艺过程中,采用木碳还源和鳞片石墨覆盖、隔氧等措施。
氧在熔融铜液中是以氧化铜(CuO)和氧化亚铜(CuO2)的形式存在的,木碳(C)在高温下与其作用,可以脱氧,使其氧含量小于10ppm,反应方程式如下: CuO+CuO2+C→Cu+CuO+CO→2Cu+CO2↑在反应过程中产生的CO保护气氛和鳞片石墨的隔氧作用,使铜液在熔化腔向保温腔的转移及结晶过程中,铜液不再被氧化。
无氧铜生产工艺流程

第四章工艺技术方案4.1工艺技术方案本项目采用的原材料为含铜量99%的电解铜,选用目前国内先进的蓄热式熔化炉和中频炉,用上引法连铸工艺方法生产氧的含量不大于0。
02%,杂质总含量不大于0。
05%,含铜量99。
5%以上无氧铜杆。
4.2工艺流程简述1、生产准备本项目使用的电解铜在江西省内购买。
图4—1项目生产工艺流程图2、上引法连铸工艺流程本项目采用上引法连铸工艺生产无氧铜杆。
上引法连铸铜杆的基本特点是“无氧”,即氧含量在10ppm以下。
上引法与连铸连轧和浸涂法相比,其特点是:1)由于拉扎工艺和铸造工艺不是连续的,拉扎是在常温下进行的,不需要气体保护,钢材也不会被氧化.因此设备投资小,厂房布置也灵活。
2)单机产量变化范围大,年产量可以从几百吨到几万吨,可供不同规模的厂家选用不同型号的上引机组.此外,由于连铸机是多头的,可以很容易的通过改变铸造规格(铸杆直径),来改变单位时间的产量,因此其产量可视原材料的供应情况和产品的需求情况来确定,便于组织生产、节约能源。
3)只需更换结晶器和改变石墨模的形状,即可生产铜管、铜排等异型铜材,并可在同一机器上上产不同规格、品种的铜材,灵活机动,这是上引法的中最大特点。
上引法连铸工艺流程:原料通过加料机加入融化炉进行熔化、氧化、扒渣处理后,熔融的铜液经过一段时间的静置还原脱氧并达到一定的温度后,通过有CO气体保护的流槽经过渡腔(铜液在此进一步还原脱氧、清除渣质),进而平稳的流入中频炉保温静置,铜液的温度由热电偶测量,温度值由仪表显示,温度控制在1150℃±10℃.连铸机固定于中频保温炉的上方,连铸机铜液在结晶器中快速结晶连续不断地生产出铜杆,最后经双头挠杆机等辅助设备装盘成产品。
⑴加料:原料一般用加料机加入,炉头多加、炉尾少加。
加冷料时要使铜料距炉顶及烟道口有一定距离,以保证燃料燃烧和炉气流动的顺畅.加料时要保证炉膛有足够高的温度,一般应达到1300℃以上,炉内应保证零压或微负压。
上引法连铸的工艺与设备

上引法连铸的工艺与设备发布时间:2021-07-09T08:15:58.229Z 来源:《科技新时代》2021年4期作者:李庆[导读] 成为引领纯铜生产的重要工艺,因此,研究上引法连铸的工艺与设备具有重要意义。
芜湖铜冠电工有限公司 241000摘要:随着化工技术的不断发展,上引法连铸打破传统的无氧铜杆生产方式,成为更加绿色环保、节约能耗的生产方式。
为了提高我国上引法连铸工艺及设备在世界工艺生产的地位,因此,必须切实了解我国目前上引法连铸的工艺与设备,并加以创新,这样才能促进我国化工领域的快速发展。
基于此,本文主要介绍上引法连铸的工艺及设备。
关键词:上引法连铸;工艺原理;感应炉;连铸机引言随着工业化进程的不断加深,我国对工业生产水平的要求越来越高,加之,近些年来,我国资源的严重浪费,人们的资源危机意识显著提高,国家也不断倡导各行业各业绿色、节能、可持续发展。
为响应国家号召,更好地提高资源利用率,我国在纯铜的生产工艺上不断进行革新,上引法连铸的出现突破了传统生产工艺的限制,成为引领纯铜生产的重要工艺,因此,研究上引法连铸的工艺与设备具有重要意义。
一、上引法连铸概述上引法主要用于生产纯铜,为变压器、电缆等制作提供材料。
在我国,该方法最早是由上海电缆研究所提出,上引法不仅在很大程度上减少了能源浪费,而且大大提高了生产产品的质量,丰富了可生产产品的种类和规模。
与当前普遍使用的生产纯铜技术——浸除法、连铸连轧法相比,上引法具有如下特点:第一,上引法可通过适当地替换石墨模型并置换结晶器,便能在同一个生产设备上完成不同类型、不同大小的钢制品生产,例如,生产与铜排相类似的异型材料或者铜排等,该特点是上引法最为突出的亮点。
第二,利用上引法进行铜材生产时,主要利用分体炉加以实现,主要做法是将熔化和保温环节都置于第二感应炉中。
第三,使用上引法进行生产时,因为拉轧这一步骤可在无气体保护、常温条件下进行,加之,此时的铸造工艺和拉轧工艺都不具备连续性,所以,在生产用房的布置上更加灵活,在生产设备的经费投入上也相对较低。
连续铸造原理和连铸设备简介
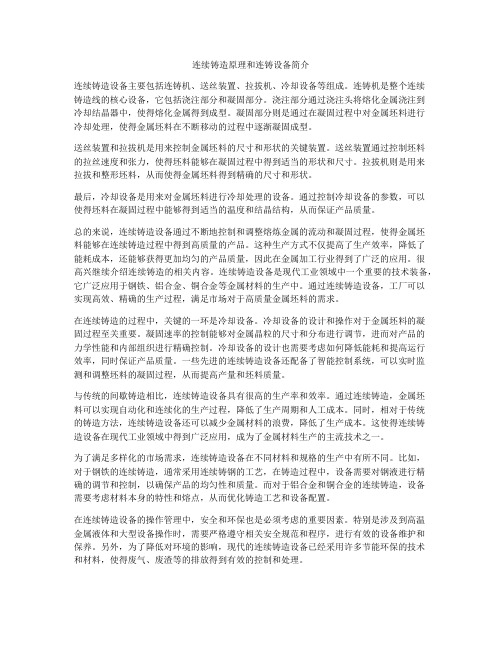
连续铸造原理和连铸设备简介连续铸造设备主要包括连铸机、送丝装置、拉拔机、冷却设备等组成。
连铸机是整个连续铸造线的核心设备,它包括浇注部分和凝固部分。
浇注部分通过浇注头将熔化金属浇注到冷却结晶器中,使得熔化金属得到成型。
凝固部分则是通过在凝固过程中对金属坯料进行冷却处理,使得金属坯料在不断移动的过程中逐渐凝固成型。
送丝装置和拉拔机是用来控制金属坯料的尺寸和形状的关键装置。
送丝装置通过控制坯料的拉丝速度和张力,使得坯料能够在凝固过程中得到适当的形状和尺寸。
拉拔机则是用来拉拔和整形坯料,从而使得金属坯料得到精确的尺寸和形状。
最后,冷却设备是用来对金属坯料进行冷却处理的设备。
通过控制冷却设备的参数,可以使得坯料在凝固过程中能够得到适当的温度和结晶结构,从而保证产品质量。
总的来说,连续铸造设备通过不断地控制和调整熔炼金属的流动和凝固过程,使得金属坯料能够在连续铸造过程中得到高质量的产品。
这种生产方式不仅提高了生产效率,降低了能耗成本,还能够获得更加均匀的产品质量,因此在金属加工行业得到了广泛的应用。
很高兴继续介绍连续铸造的相关内容。
连续铸造设备是现代工业领域中一个重要的技术装备,它广泛应用于钢铁、铝合金、铜合金等金属材料的生产中。
通过连续铸造设备,工厂可以实现高效、精确的生产过程,满足市场对于高质量金属坯料的需求。
在连续铸造的过程中,关键的一环是冷却设备。
冷却设备的设计和操作对于金属坯料的凝固过程至关重要。
凝固速率的控制能够对金属晶粒的尺寸和分布进行调节,进而对产品的力学性能和内部组织进行精确控制。
冷却设备的设计也需要考虑如何降低能耗和提高运行效率,同时保证产品质量。
一些先进的连续铸造设备还配备了智能控制系统,可以实时监测和调整坯料的凝固过程,从而提高产量和坯料质量。
与传统的间歇铸造相比,连续铸造设备具有很高的生产率和效率。
通过连续铸造,金属坯料可以实现自动化和连续化的生产过程,降低了生产周期和人工成本。
上引连铸法

上引连铸法上引连铸是一种连续铸造的方法,其原理是利用金属熔液冷却结晶的机理,从熔融的金属或合金熔液中缓慢连续地抽出具有一定形状的固态金属线材、板材等。
该方法的主要特点是可直接从熔融的金属或合金熔液中制取连续的线材或板材,无需经过铸造、挤压、拉拔、轧制等加工过程,缩短了加工周期,降低了加工过程的污染及损耗;连续生产能力大,单炉生产能力可达500kg,甚至可生产连续的线材、板材;可根据需要生产不同外径的线材和板材。
目前该方法大量应用于无氧铜线、钢材的生产。
2 结构组成上引连铸机主要由熔化系统、熔液液面跟踪系统、熔液冷却结晶系统、牵引系统、收线系统组成[1]。
熔化系统:对金属块进行加热熔化,并对熔液提供保温、保护等。
主要由中频感应电源、熔化坩埚及保温炉组成。
熔液液面跟踪系统:对熔融的金属液面进行跟踪测量,并通过升降机构使熔液冷却结晶系统中的结晶器能够与金属液面因不断地被抽取而发生的高度变化保持同步。
主要由碳化硅浮子、信号处理系统、升降机构组成。
熔液冷却结晶系统:对进入到结晶器内的金属熔液进行冷却凝固成形,从而获得固定形状的线材或板材。
主要由冷却水进出管道、结晶室、石墨定形管、耐火材料保护套、冷却水系统等组成。
牵引系统:对在结晶器内已形成的短小的固态金属线材或板材进行受控牵引,以获得连续的线材或板材。
收线系统:对牵引出的线材或板材进行弯圈收线,方便储存。
3 工作原理是上引连铸结晶器的结构示意图。
结晶器的下端装有耐火材料保护套、石墨定型管等,从结晶器的顶部预先插入一根外径与石墨定型管内径基本一致的金属线材做为引子(铸杆),线材通过石墨定型管并在结晶器的底端露出一小截。
通入流动的冷却水,将结晶器浸入熔液中,熔液液面不能超过耐火材料保护套的上端面。
将结晶器总成固定在牵引系统的导引轨道上。
其工作示意图见图2。
在图2中,当结晶器浸入高温金属熔液中时,原先已预插在结晶器内的线材的外露部分及结晶器h高度以内的部分会因受热而被熔化,而在结晶器内h高度以上的金属线材因受不断流动的冷却水作用而保持固态形状,因此在h高度的区域内形成了一个原始的固-液交界面,这个固-液交界面的实际位置与熔液温度以及受冷却室内流动冷却水的冷却强度有关。
上引法连铸机组产品简介
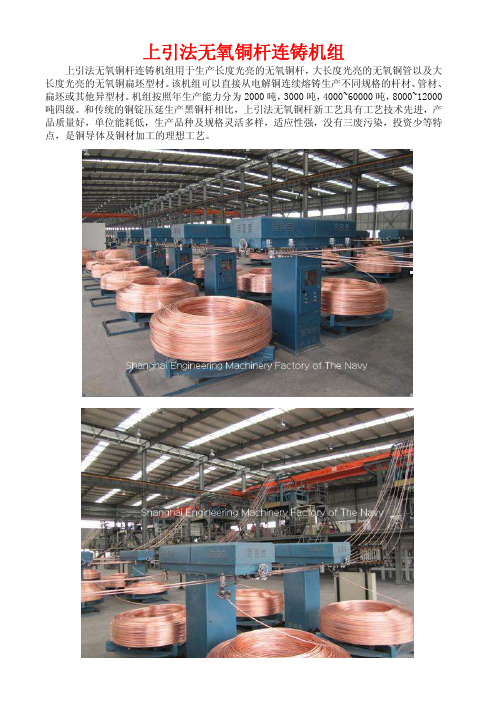
上引法无氧铜杆连铸机组上引法无氧铜杆连铸机组用于生产长度光亮的无氧铜杆,大长度光亮的无氧铜管以及大长度光亮的无氧铜扁坯型材。
该机组可以直接从电解铜连续熔铸生产不同规格的杆材、管材、扁坯或其他异型材。
机组按照年生产能力分为2000吨,3000吨,4000~60000吨,8000~12000吨四级。
和传统的铜锭压延生产黑铜杆相比,上引法无氧铜杆新工艺具有工艺技术先进,产品质量好,单位能耗低,生产品种及规格灵活多样,适应性强,没有三废污染,投资少等特点,是铜导体及铜材加工的理想工艺。
原理机组将电解铜经工频感应炉熔化成液体,通过覆盖于表面的木炭与空气隔绝(避免铜液氧化)经保温炉将铜液温度控制在1150°C±10°C,连铸机铜液在结晶器中快速结晶连续不断地生产出铜杆,最后经双头挠杆机等辅助设备装盘成产品。
无氧铜杆的技术特性铸杆比重:~8.93g/cm3铸杆抗拉强度: ≥170N/mm2铸杆伸长率: ≥35%软态导电率:不低于100%IACS(φ2m2n软线)含氧量:<10ppm机组设备组成和结构说明:该机组由工频感应炉、连铸机、导轮架、限位装置、双头挠杆机、水冷却系统、电控系统、加料系统以及测温系统等组成。
1.工频感应炉工频感应炉主要由炉体、炉架和感应器三大部分组成。
炉体外壳是钢结构,内部由耐火砖和石英砂砌筑而成,炉架起支撑整个炉子的作用,通过地脚螺栓固定在基础上。
感应器由线圈、水套、铁芯以及熔沟组成,感应器的高压侧(初级)由带水冷的线圈组成,电压可从90V~420V有级可调,感应器的低压侧(次级)由短路的熔沟组成,通电后,在电磁感应的作用下,在熔沟内部产生大电流,低电压而使其熔化并将加入的电解铜熔化。
水套和线圈均为水冷却,冷却水循环使用,由冷却水系统提供。
2. 连铸机连铸机是实现上引连铸的主要设备。
它由牵引机构、液位跟踪和结晶器三大部分组成。
牵引机构由交流伺服电机和牵引辊轮等组成,它可实现每分钟0—1000次的间歇运动并通过牵引辊轮将铸杆连续上引出来,每组牵引机构可带动5付牵引辊轮,分别牵引5根铸杆,并通过更换结晶器生产其它规格的铜杆。
上引法无氧铜杆连铸机组常见电气故障分析及处理
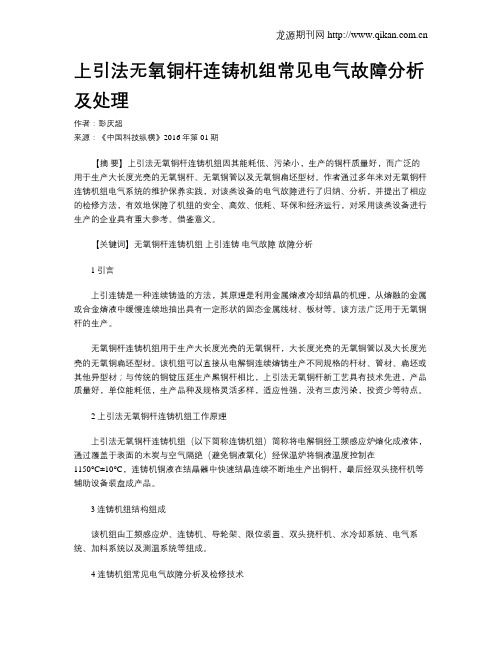
上引法无氧铜杆连铸机组常见电气故障分析及处理作者:彭庆超来源:《中国科技纵横》2016年第01期【摘要】上引法无氧铜杆连铸机组因其能耗低、污染小,生产的铜杆质量好,而广泛的用于生产大长度光亮的无氧铜杆、无氧铜管以及无氧铜扁坯型材。
作者通过多年来对无氧铜杆连铸机组电气系统的维护保养实践,对该类设备的电气故障进行了归纳、分析,并提出了相应的检修方法,有效地保障了机组的安全、高效、低耗、环保和经济运行,对采用该类设备进行生产的企业具有重大参考、借鉴意义。
【关键词】无氧铜杆连铸机组上引连铸电气故障故障分析1引言上引连铸是一种连续铸造的方法,其原理是利用金属熔液冷却结晶的机理,从熔融的金属或合金熔液中缓慢连续地抽出具有一定形状的固态金属线材、板材等。
该方法广泛用于无氧铜杆的生产。
无氧铜杆连铸机组用于生产大长度光亮的无氧铜杆,大长度光亮的无氧铜管以及大长度光亮的无氧铜扁坯型材。
该机组可以直接从电解铜连续熔铸生产不同规格的杆材、管材、扁坯或其他异型材;与传统的铜锭压延生产黑铜杆相比,上引法无氧铜杆新工艺具有技术先进,产品质量好,单位能耗低,生产品种及规格灵活多样,适应性强,没有三废污染,投资少等特点。
2 上引法无氧铜杆连铸机组工作原理上引法无氧铜杆连铸机组(以下简称连铸机组)简称将电解铜经工频感应炉熔化成液体,通过覆盖于表面的木炭与空气隔绝(避免铜液氧化)经保温炉将铜液温度控制在1150°C±10°C,连铸机铜液在结晶器中快速结晶连续不断地生产出铜杆,最后经双头挠杆机等辅助设备装盘成产品。
3连铸机组结构组成该机组由工频感应炉、连铸机、导轮架、限位装置、双头挠杆机、水冷却系统、电气系统、加料系统以及测温系统等组成。
4 连铸机组常见电气故障分析及检修技术因作者长期从事连铸机组的电气系统的日常保养、维修工作,故本文重点对连铸机组的电气故障进行分析并阐述相应的检查、检修方法。
4.1水套、线圈堵塞故障分析:冷却水长时间循环使用,水内混入杂质,致使水套和线圈堵塞。
连续铸造原理和连铸设备简介
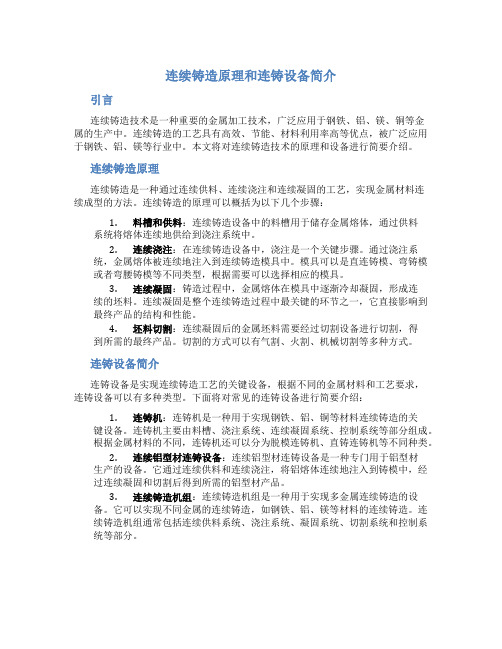
连续铸造原理和连铸设备简介引言连续铸造技术是一种重要的金属加工技术,广泛应用于钢铁、铝、镁、铜等金属的生产中。
连续铸造的工艺具有高效、节能、材料利用率高等优点,被广泛应用于钢铁、铝、镁等行业中。
本文将对连续铸造技术的原理和设备进行简要介绍。
连续铸造原理连续铸造是一种通过连续供料、连续浇注和连续凝固的工艺,实现金属材料连续成型的方法。
连续铸造的原理可以概括为以下几个步骤:1.料槽和供料:连续铸造设备中的料槽用于储存金属熔体,通过供料系统将熔体连续地供给到浇注系统中。
2.连续浇注:在连续铸造设备中,浇注是一个关键步骤。
通过浇注系统,金属熔体被连续地注入到连续铸造模具中。
模具可以是直连铸模、弯铸模或者弯腰铸模等不同类型,根据需要可以选择相应的模具。
3.连续凝固:铸造过程中,金属熔体在模具中逐渐冷却凝固,形成连续的坯料。
连续凝固是整个连续铸造过程中最关键的环节之一,它直接影响到最终产品的结构和性能。
4.坯料切割:连续凝固后的金属坯料需要经过切割设备进行切割,得到所需的最终产品。
切割的方式可以有气割、火割、机械切割等多种方式。
连铸设备简介连铸设备是实现连续铸造工艺的关键设备,根据不同的金属材料和工艺要求,连铸设备可以有多种类型。
下面将对常见的连铸设备进行简要介绍:1.连铸机:连铸机是一种用于实现钢铁、铝、铜等材料连续铸造的关键设备。
连铸机主要由料槽、浇注系统、连续凝固系统、控制系统等部分组成。
根据金属材料的不同,连铸机还可以分为脱模连铸机、直铸连铸机等不同种类。
2.连续铝型材连铸设备:连续铝型材连铸设备是一种专门用于铝型材生产的设备。
它通过连续供料和连续浇注,将铝熔体连续地注入到铸模中,经过连续凝固和切割后得到所需的铝型材产品。
3.连续铸造机组:连续铸造机组是一种用于实现多金属连续铸造的设备。
它可以实现不同金属的连续铸造,如钢铁、铝、镁等材料的连续铸造。
连续铸造机组通常包括连续供料系统、浇注系统、凝固系统、切割系统和控制系统等部分。
连铸主要设备介绍页PPT文档
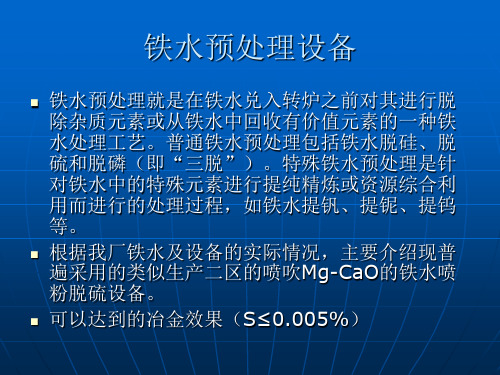
氮气管路
精炼设备简介
一、二次冶金工艺流程: 高炉——铁水预处理——转炉——钢水二次精
炼——连铸 二、主要的精炼方式: 二次精炼就是对转炉钢水根据目的进行炉外(相
长水口操作机构位于长水口操作平台上, 并有一个保护罩以防钢水喷溅。
液压动力来源是铸机主液压系统。
9、结晶器确定铸坯的断面形状,钢液在结晶器内 开始冷却凝固,并形成足够的坯壳。是连铸机上 最关键的部件之一,成为连铸机的心脏。
结晶器的主要部件包括结晶器框架、结晶器插入 件宽边、结晶器插入件窄边、结晶器足辊、窄面 铸坯导向辊及结晶器罩等组成。
2、钢包回转台
连铸机生产过程中,用于承载和转送钢水包,
能以最短的时间将钢水包从接收位置转送至浇注
位置。钢包的加速、减速及定位通过PLC系统和
行程开关来完成。另外,也可采用手动回转模式。
由于回转台设置了两个回转臂,因而可实现多炉
连浇,减少了车间吊车作业。每个臂可独立提升,
两臂同时旋转,并具有钢包加盖功能,实现钢水
为使中间罐浸入式水口在浇注位对准结晶器, 在车上设有行走方式微调(变频调速)和横向 微调机构。中间罐车的升降机构,可把侵入式 水口插入结晶器内。称量装置可称量中间罐内 的钢水重量。
4、带盖中间罐:用于贮存及分配钢水。钢包内的 钢水注入中间罐后,在其中均匀温度及成分,钢 水中的非金属夹杂物充分上浮,然后通过安装在 下面的浸入式水口由塞棒控制送入结晶器内。
对于转炉)处理。为了创造最佳的冶金反应条件, 所采用的基本手段不外乎搅拌、真空、加热、渣 洗、喷吹及喂丝等几种或几种的组合。 根据主要 功能,常见的精炼设备有: 吹氩设备、喂丝设备、LF炉 、DH、RH、LVD、 ASEA-SKF、V0D等
- 1、下载文档前请自行甄别文档内容的完整性,平台不提供额外的编辑、内容补充、找答案等附加服务。
- 2、"仅部分预览"的文档,不可在线预览部分如存在完整性等问题,可反馈申请退款(可完整预览的文档不适用该条件!)。
- 3、如文档侵犯您的权益,请联系客服反馈,我们会尽快为您处理(人工客服工作时间:9:00-18:30)。
上引法无氧铜杆连铸机组
上引法无氧铜杆连铸机组用于生产长度光亮的无氧铜杆,大长度光亮的无氧铜管以及大长度光亮的无氧铜扁坯型材。
该机组可以直接从电解铜连续熔铸生产不同规格的杆材、管材、扁坯或其他异型材。
机组按照年生产能力分为2000吨,3000吨,4000~60000吨,8000~12000吨四级。
和传统的铜锭压延生产黑铜杆相比,上引法无氧铜杆新工艺具有工艺技术先进,产品质量好,单位能耗低,生产品种及规格灵活多样,适应性强,没有三废污染,投资少等特点,是铜导体及铜材加工的理想工艺。
原理
机组将电解铜经工频感应炉熔化成液体,通过覆盖于表面的木炭与空气隔绝(避免铜液氧化)经保温炉将铜液温度控制在1150°C±10°C,连铸机铜液在结晶器中快速结晶连续不断地生产出铜杆,最后经双头挠杆机等辅助设备装盘成产品。
无氧铜杆的技术特性
铸杆比重:~8.93g/cm3
铸杆抗拉强度: ≥170N/mm2
铸杆伸长率: ≥35%
软态导电率:不低于100%IACS(φ2m2n软线)
含氧量:<10ppm
机组设备组成和结构说明:
该机组由工频感应炉、连铸机、导轮架、限位装置、双头挠杆机、水冷却系统、电控系统、加料系统以及测温系统等组成。
1.工频感应炉
工频感应炉主要由炉体、炉架和感应器三大部分组成。
炉体外壳是钢结构,内部由耐火砖和石英砂砌筑而成,炉架起支撑整个炉子的作用,通过地脚螺栓固定在基础上。
感应器由线圈、水套、铁芯以及熔沟组成,感应器的高压侧(初级)由带水冷的线圈组成,电压可从90V~420V有级可调,感应器的低压侧(次级)由短路的熔沟组成,通电后,在电磁感应的作用下,在熔沟内部产生大电流,低电压而使其熔化并将加入的电解铜熔化。
水套和线圈均为水冷却,冷却水循环使用,由冷却水系统提供。
2. 连铸机
连铸机是实现上引连铸的主要设备。
它由牵引机构、液位跟踪和结晶器三大部分组成。
牵引机构由交流伺服电机和牵引辊轮等组成,它可实现每分钟0—1000次的间歇运动并通过牵引辊轮将铸杆连续上引出来,每组牵引机构可带动5付牵引辊轮,分别牵引5根铸杆,并通过更换结晶器生产其它规格的铜杆。
液位跟踪系统可保证连铸机上结晶器插入铜液的深度相对稳定,确保连铸生产的连续性。
结晶器可将液态的铜快速冷却成固态铜并实现热交换,每根结晶器都能单独更换和控制而不影响其它结晶器的正常工作。
结晶器
3.导轮架
导轮架布置是在连铸机的上方,主要由平台、支架、竖导轮和滚筒组成,它使铸杆平滑地导入各组双头挠杆机,互不干扰。
4.限位装置
限位装置是在导轮架和双头挠杆机之间设置的二台装置,它由6组24V低压上、下限位,通过铜杆与上下限位的接触来控制双头挠杆机的速度。
5.双头挠杆机
双头挠杆机是由牵引辊轮,成圈装置和收线转盘组成,每组双头挠杆机由二台电动机分别驱动两套装置收圈两根铜杆,曲率自动调整。
6.水冷系统
水冷系统是一个独立的循环供水系统,保证以0.2~0.4Mpa的冷却水供结晶器、水套和线圈冷却,它主要由120m3水池、水泵、管道和冷却塔组成,保证进水温度在20~30°C,流量在50m3/h左右。
电器系统由电源系统、控制系统组成,电源系统通过若干电源柜将电源分别供给每个感应器,控制系统保证机组正常生产。
加料系统分别为机械整块电解铜加料,它保证电解铜连续供给熔化炉。
测温系统由铜液温度和冷却水温度两大部分组成,测温的结果分别显示在温度计上以达到对设备的生产监控。