细粒浮选的工艺措施
浮选的操作方法

浮选的操作方法浮选是一种常用的矿石分离和浓缩技术,它通过气泡将矿石中的有用矿物与废石分离出来。
下面将详细介绍浮选的操作方法。
一、矿石破碎和磨矿在浮选操作之前,首先需要将矿石进行破碎和磨矿处理。
这一步骤的目的是将矿石颗粒粉碎至适当的粒度,并使矿石与水混合形成矿浆,以便后续的浮选操作。
二、药剂的添加在浮选过程中,药剂的添加非常重要。
药剂可以改变矿石表面的性质,使有用矿物与气泡更容易结合,从而实现浮选分离的目的。
常用的药剂有捕收剂、泡沫稳定剂和调节剂等。
三、搅拌和气泡生成在添加药剂后,需要进行搅拌和气泡生成。
搅拌可以使药剂均匀地分散在矿浆中,而气泡的生成则是通过将空气或其他气体注入矿浆中实现的。
气泡的生成通常是通过机械搅拌或空气增压的方式进行的。
四、矿浆进入浮选槽经过搅拌和气泡生成后,矿浆会进入浮选槽。
浮选槽通常是一个大型的槽体,内部设有隔板和槽位,用于控制矿浆的流动和分离。
五、矿浆与气泡的接触在浮选槽中,矿浆与气泡进行接触。
由于药剂的作用,有用矿物表面会吸附气泡,形成浮选泡沫。
而废石则不容易与气泡结合,仍沉入槽底。
六、泡沫的收集和排放浮选泡沫会在浮选槽中上升,最终形成泡沫层。
泡沫层通常通过槽顶的泡沫溢流槽收集,并通过管道输送到泡沫收集槽。
在泡沫收集槽中,泡沫会被进一步分离和排放,以得到有用矿物。
七、浮选尾矿处理泡沫排放后,剩余的矿浆被称为浮选尾矿。
针对浮选尾矿的处理,通常采用浓缩、脱水和处理废水等方法,以减少环境污染并实现资源的回收利用。
总结:浮选是一种基于矿石中有用矿物与废石的特性差异,利用气泡将有用矿物分离的技术。
操作方法主要包括矿石破碎和磨矿、药剂的添加、搅拌和气泡生成、矿浆进入浮选槽、矿浆与气泡的接触、泡沫的收集和排放,以及浮选尾矿处理等步骤。
通过合理的操作和药剂的使用,可以实现对矿石的有效分离和浓缩,从而提高矿石的综合利用率。
浮选技术在矿业中具有广泛的应用前景,对于提高资源利用效率和保护环境具有重要意义。
细粒煤脱水

2.给料点和溢流堰高度
① 溢流堰的高度决定着离心机沉降区的长度。
② 增加溢流堰的高度,沉降区的长度随之增加, 分离粒度和溢流中的固体含量则相应减小。 ③ 溢流堰高度增加到一定程度,分离粒度和溢 流中的固体含量变化就不显著了。 ④ 溢流堰的高度一般取转筒最大半径的0.15一 0.3。
• 给料点的位置要和溢流堰的高度要相适应, 溢流堰越低,给料点距溢流堰的水平距离 应越近。
(3)脱水工艺指标先进。滤饼水分可达到
18~22%,与相同处理能力的圆盘真空过滤
机相比,滤饼水分可降低6~10%,滤饼脱
落率提高30~40%,节电可达60~70%,且
滤液出清水,可直接作循环水,减少了细
泥在系统中循环,有利于改善浮选和过滤 效果。
压力p
压力p
1、真空过滤机
转筒真空过滤机动画
• 真空过滤机存在以下缺点: (1)滤饼脱落困难,老在盘上大转,不得不 借助人工捅饼; (2)真空过滤机滤液不能出清水,滤液浓度 高,必须返回浮选,导致细煤泥在系统内 循环,无疑增加了无用功的消耗,并恶化 了浮选和过滤效果; (3)真空泵动力消耗大; (4)滤布更换麻烦,成本也较高。
(4)卸料过程。开动滤板拉开装置,传动链 上的拉钩装置相继将滤板拉开,滤饼籍自 重脱落到产品输送胶带上运出。
精煤快速压滤机
精煤快速压滤机具有以下特点: (1)精煤快速压滤机结构设计如图2所示, 采用独立进气结构,气道不堵塞,易维护; 滤板结构上设计带有高强度双面隔膜,可 实现高压强流体进料、强气流风吹滤饼和 隔膜压榨挤压滤饼脱水,增加了脱水功能。
图 2 精煤压滤板结构示意图 1- 压滤板 2- 压滤板隔膜 3- 把手 4- 滤液管 5、6- 风管
(2)压滤脱水工艺如图3所示,采用自流与
浮选洗煤的工艺流程
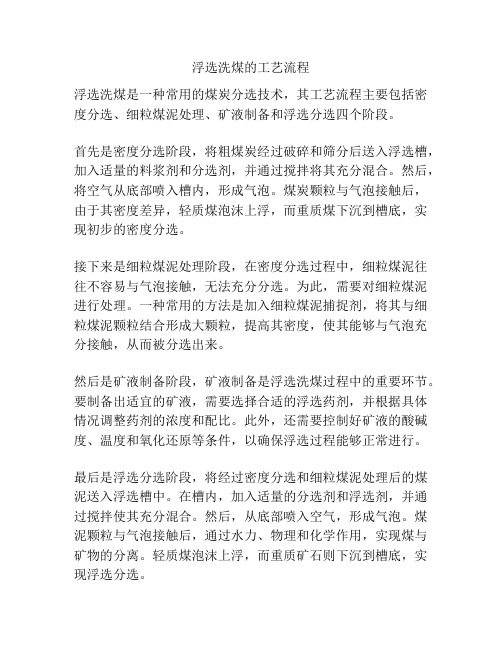
浮选洗煤的工艺流程
浮选洗煤是一种常用的煤炭分选技术,其工艺流程主要包括密度分选、细粒煤泥处理、矿液制备和浮选分选四个阶段。
首先是密度分选阶段,将粗煤炭经过破碎和筛分后送入浮选槽,加入适量的料浆剂和分选剂,并通过搅拌将其充分混合。
然后,将空气从底部喷入槽内,形成气泡。
煤炭颗粒与气泡接触后,由于其密度差异,轻质煤泡沫上浮,而重质煤下沉到槽底,实现初步的密度分选。
接下来是细粒煤泥处理阶段,在密度分选过程中,细粒煤泥往往不容易与气泡接触,无法充分分选。
为此,需要对细粒煤泥进行处理。
一种常用的方法是加入细粒煤泥捕捉剂,将其与细粒煤泥颗粒结合形成大颗粒,提高其密度,使其能够与气泡充分接触,从而被分选出来。
然后是矿液制备阶段,矿液制备是浮选洗煤过程中的重要环节。
要制备出适宜的矿液,需要选择合适的浮选药剂,并根据具体情况调整药剂的浓度和配比。
此外,还需要控制好矿液的酸碱度、温度和氧化还原等条件,以确保浮选过程能够正常进行。
最后是浮选分选阶段,将经过密度分选和细粒煤泥处理后的煤泥送入浮选槽中。
在槽内,加入适量的分选剂和浮选剂,并通过搅拌使其充分混合。
然后,从底部喷入空气,形成气泡。
煤泥颗粒与气泡接触后,通过水力、物理和化学作用,实现煤与矿物的分离。
轻质煤泡沫上浮,而重质矿石则下沉到槽底,实现浮选分选。
综上所述,浮选洗煤的工艺流程包括密度分选、细粒煤泥处理、矿液制备和浮选分选四个阶段。
通过这一工艺流程,可以将煤和矿物有效地分离,提高煤炭的质量和利用率,为煤炭行业的发展做出贡献。
极细粒矿石的浮选特点及浮选时应采取的措施

极细粒矿石的浮选特点及浮选时应采取的措施
极细粒矿石的浮选行为主要是由其胶体性质所决定的,其特点是:
1)矿泥质量小,难以气泡附着,同时易粘附在粗粒表面降低其可浮性;
2)比表面大,不仅破坏药剂的正常作用,而且占据气泡表面,还会大量消耗药剂,使浮选指标降低;其次,还会使泡沫过于稳定,给精选、浓缩作业带来困难。
浮选实践中,为了克服极细粒恶化浮选过程,常采取的措施有:
1.细泥太多时,利用分散剂减轻其影响。
分散剂常用水玻璃、六聚偏磷酸钠。
这种办法难以根本改变和解决问题,还应加强精选作业。
2.浮选前预选脱泥。
浮选脱泥就是用少量的起泡剂和捕收剂先浮出一部分矿泥,然后进行较粗粒浮选。
还可利用机械设备脱泥,机械脱泥是在浮选前用分级机(如水力旋流器)来脱除一部分细泥。
一般脱泥的粒度在10~20微米。
脱泥粒级主要由分级设备性能决定。
脱泥之后,亦能改变粗粒浮选的效果。
主要问题是细泥难以浮选处理,此时可考虑将细泥用氰化法处理。
3.泥砂分选。
细泥单独用浮选处理的工艺要求是:
1)宜用较长的浮选时间,小于10微米粒级可用40~60分钟的浮选时间;
2)高浓度(60~70%)调浆、低浓度(20%以下)浮选;
3)分段加药,加大捕收剂用量,减少起泡剂用量;
4)大充气量,小气泡,减弱上升矿流。
在实际生产中,要满足上述细泥浮选工艺要求是有困难的,因而细泥浮选的指标都不高。
亦可考虑采用泥砂分离后,砂质矿浆进行浮选处理,泥质矿浆用氰化法处理回收金;既可保证浮选条件,又能满足氰化的要求。
浮选的工艺流程
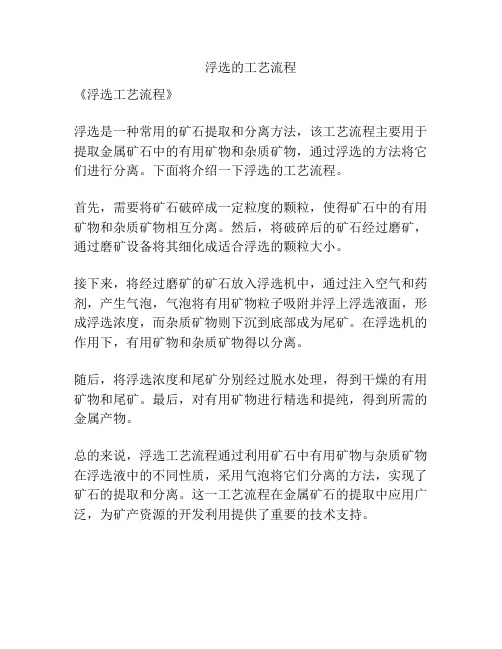
浮选的工艺流程
《浮选工艺流程》
浮选是一种常用的矿石提取和分离方法,该工艺流程主要用于提取金属矿石中的有用矿物和杂质矿物,通过浮选的方法将它们进行分离。
下面将介绍一下浮选的工艺流程。
首先,需要将矿石破碎成一定粒度的颗粒,使得矿石中的有用矿物和杂质矿物相互分离。
然后,将破碎后的矿石经过磨矿,通过磨矿设备将其细化成适合浮选的颗粒大小。
接下来,将经过磨矿的矿石放入浮选机中,通过注入空气和药剂,产生气泡,气泡将有用矿物粒子吸附并浮上浮选液面,形成浮选浓度,而杂质矿物则下沉到底部成为尾矿。
在浮选机的作用下,有用矿物和杂质矿物得以分离。
随后,将浮选浓度和尾矿分别经过脱水处理,得到干燥的有用矿物和尾矿。
最后,对有用矿物进行精选和提纯,得到所需的金属产物。
总的来说,浮选工艺流程通过利用矿石中有用矿物与杂质矿物在浮选液中的不同性质,采用气泡将它们分离的方法,实现了矿石的提取和分离。
这一工艺流程在金属矿石的提取中应用广泛,为矿产资源的开发利用提供了重要的技术支持。
浮选的工艺流程

浮选的工艺流程
浮选是一种常用的矿石选矿工艺,主要用于提取金属矿物。
其基本工艺流程如下:
1. 粗破矿石进入破碎机进行粗破:矿石经过粗破碎机破碎成较小的颗粒。
2. 细破矿石进入破碎机进行细破:经过粗破碎的矿石再次进入破碎机进行细破,使得颗粒更加细小。
3. 研磨:破碎后的矿石进入磨矿机,通过摩擦和撞击作用,使矿石颗粒更加细化。
4. 浮选药剂添加:经过研磨的矿石悬浮在水中,药剂被添加到悬浮物中,以调整矿石表面的性质,使其能够选择性地吸附气泡。
5. 酸碱调节剂的添加:根据矿石的性质,适量添加酸碱调节剂,调节矿浆的pH 值。
6. 气泡吸附:通过搅拌和注气,使气泡与药剂覆盖的矿石颗粒接触并吸附在其表面。
7. 泡沫槽收集:气泡吸附后的矿石颗粒与气泡一起浮到泡沫槽上,形成浮选泡沫。
8. 浮选精矿和尾矿分离:浮选泡沫经过泡沫槽分离,浮选精矿(含有目标金属)和尾矿(不含目标金属)分别收集。
9. 精矿脱水:浮选精矿通过脱水设备,去除部分水分。
10. 精矿浓缩:经过脱水处理的浮选精矿进一步浓缩,提高金属含量。
11. 尾矿处理:尾矿经过处理,进行排放或者作为再次选矿的原料使用。
以上是一般的浮选工艺流程,具体工艺会根据矿石的性质、选矿目标和生产要求进行调整。
细粒赤铁矿选矿工艺流程
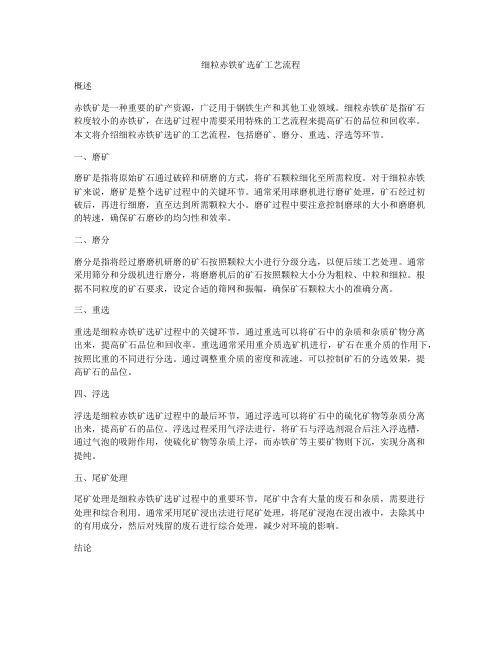
细粒赤铁矿选矿工艺流程概述赤铁矿是一种重要的矿产资源,广泛用于钢铁生产和其他工业领域。
细粒赤铁矿是指矿石粒度较小的赤铁矿,在选矿过程中需要采用特殊的工艺流程来提高矿石的品位和回收率。
本文将介绍细粒赤铁矿选矿的工艺流程,包括磨矿、磨分、重选、浮选等环节。
一、磨矿磨矿是指将原始矿石通过破碎和研磨的方式,将矿石颗粒细化至所需粒度。
对于细粒赤铁矿来说,磨矿是整个选矿过程中的关键环节。
通常采用球磨机进行磨矿处理,矿石经过初破后,再进行细磨,直至达到所需颗粒大小。
磨矿过程中要注意控制磨球的大小和磨磨机的转速,确保矿石磨砂的均匀性和效率。
二、磨分磨分是指将经过磨磨机研磨的矿石按照颗粒大小进行分级分选,以便后续工艺处理。
通常采用筛分和分级机进行磨分,将磨磨机后的矿石按照颗粒大小分为粗粒、中粒和细粒。
根据不同粒度的矿石要求,设定合适的筛网和振幅,确保矿石颗粒大小的准确分离。
三、重选重选是细粒赤铁矿选矿过程中的关键环节,通过重选可以将矿石中的杂质和杂质矿物分离出来,提高矿石品位和回收率。
重选通常采用重介质选矿机进行,矿石在重介质的作用下,按照比重的不同进行分选。
通过调整重介质的密度和流速,可以控制矿石的分选效果,提高矿石的品位。
四、浮选浮选是细粒赤铁矿选矿过程中的最后环节,通过浮选可以将矿石中的硫化矿物等杂质分离出来,提高矿石的品位。
浮选过程采用气浮法进行,将矿石与浮选剂混合后注入浮选槽,通过气泡的吸附作用,使硫化矿物等杂质上浮,而赤铁矿等主要矿物则下沉,实现分离和提纯。
五、尾矿处理尾矿处理是细粒赤铁矿选矿过程中的重要环节,尾矿中含有大量的废石和杂质,需要进行处理和综合利用。
通常采用尾矿浸出法进行尾矿处理,将尾矿浸泡在浸出液中,去除其中的有用成分,然后对残留的废石进行综合处理,减少对环境的影响。
结论细粒赤铁矿选矿工艺流程是一项复杂的工程,需要充分考虑矿石性质和选矿要求,合理设计工艺流程,确保矿石的品位和回收率。
通过磨矿、磨分、重选、浮选等环节的顺利进行,可以有效地提高细粒赤铁矿的选矿效果,为钢铁生产和工业生产提供优质的原料。
浮选

则要根据具体问题具体情况来判断
6;给矿量变化在泡沫层中的反应
给矿量正常:
在给矿量正常(相当于适当的原矿浓度)时,浮选机各泡沫层的性质
和矿浆浓度正常时的性质一样。
给矿量加大:
在其他条件正常的情况下,当逐渐加大给矿量时,将会出现:
矿化泡沫的虚实反应.原矿品位高。药剂用
量适当,粗选头部的泡沫将正常的实【如果仰制剂用量过大,而捕收剂过小,泡沫就变的虚】在有些矿的浮选中。捕收剂用量过大。活化剂用量过大,仰止剂用量过小
时,就会发现泡沫过于适当现象。这是对浮选不利的。
浮选剂是调整泡沫尺度的主要因素。
一般情况下起泡剂
用量越大,起泡越小,石灰越大,气泡越大,仰止剂越大,起泡越小、
矿山机械百科网认为可能造成铜选矿厂浮选槽冒矿的几个原因:
1、2#油添加过量;
2、矿浆中掉进机械油;
3、石灰添加量过大;
4、尾矿闸门设计不合理或提得过高;
5、精选补加水过大,又调节不当;
泡剂粘性较大时,则泡沫层的粘性表现的突出些
捕收剂:
用量过多:
捕收剂对泡沫层的影响不如起泡剂明显,
但是当捕收剂用量不合适时依然能够在泡沫层中反应出来
当油类捕收剂用量过多时:
(1) 泡沫层中,特别是气泡接缝处可以见到小油珠
(2) 泡沫层致密、发粘,泡沫带煤多,但也含有较多的泥杂质
光滑,反而很粗糙,致使由于粗粒煤上浮的结果。在后两室,泡沫层
已不能覆盖矿浆面,气泡大小不等,明显出现气泡破灭和兼并现象(此
时气泡不连续,有大泡也有小泡),液面漂浮着致密、粗糙的泡沫薄
浮选工艺流程跟师傅学习

浮选工艺流程跟师傅学习一、浮选工艺简介浮选是一种物理化学方法,通过物理作用和化学作用的结合,将有用矿石从废石中分离出来,从而达到选矿的目的。
浮选工艺一般包括破碎、磨矿、浸取、浮选和脱泡等环节。
浮选工艺的主要原理是利用矿石颗粒表面的物理化学性质差异,使有用矿物与废石分开,实现分离。
二、浮选工艺流程1.破碎:首先将原矿经过破碎机进行初步破碎,将大块原矿分解成较小块的矿石颗粒,便于后续的选矿处理。
2.磨矿:破碎后的矿石通过磨矿机进行细磨,使矿石颗粒达到所需的细度,有利于后续的浸取和浮选处理。
3.浸取:将磨矿后的矿石浸入含有药剂的浸取槽中,药剂与矿石颗粒发生化学反应,改变矿石表面的性质,使得有用矿物与废石分开。
4.浮选:将浸取后的矿石悬浮在水中,利用气泡的吸附作用,使有用矿物与废石分离。
有用矿物吸附气泡上浮,而废石下沉,从而实现分离。
5.脱泡:最后通过脱泡工序,将气泡从有用矿物表面去除,使得有用矿物可以被有效地回收利用。
以上就是浮选工艺的基本流程,当然,具体的工艺流程还会因矿石的类型、性质以及生产要求而有所不同。
三、师傅学习浮选工艺流程跟随师傅学习浮选工艺流程是一种非常有效的学习方式。
师傅通常有丰富的实践经验和专业知识,可以帮助学员快速掌握浮选工艺的要点,并且在实际操作中及时指导和纠正错误。
以下是我在学习浮选工艺流程中的一些体会:1.认真聆听:在学习过程中,我们应该认真聆听师傅的指导和讲解,理解相关知识和技能的要点,不断提出问题和与师傅交流讨论,以便更快地理解和掌握。
2.积极实践:在实际操作中,我们应该积极参与,亲自动手操作,锻炼操作技能和培养观察能力,通过实践来加深对浮选工艺的理解。
3.归纳总结:在学习过程中,我们要及时总结经验,发现问题并改正,不断完善自己的工艺操作技能,提高工作效率和质量。
4.关注安全:在学习和实践中,我们要时刻关注安全问题,遵守操作规程和安全规范,确保自己和他人的生命财产安全。
通过跟随师傅学习浮选工艺流程,我收获颇丰,不仅掌握了基本的浮选工艺原理和操作技能,还提高了解决问题的能力和综合素质。
细粒浮选工艺技术流程
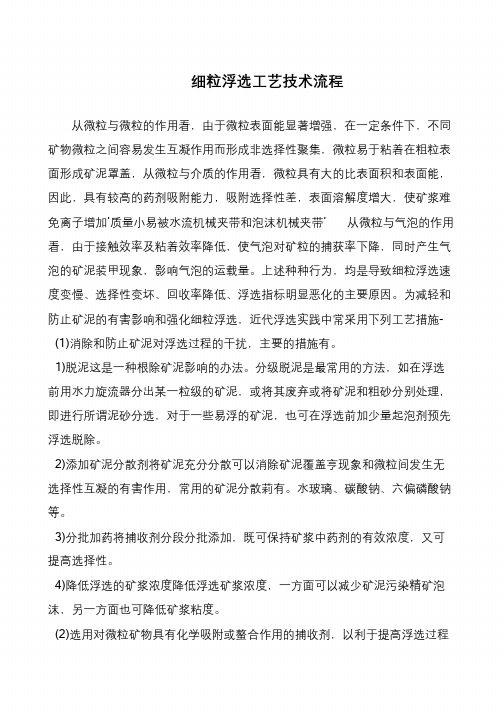
立志当早,存高远
细粒浮选工艺技术流程
从微粒与微粒的作用看,由于微粒表面能显著增强,在一定条件下,不同矿物微粒之间容易发生互凝作用而形成非选择性聚集,微粒易于粘着在粗粒表面形成矿泥罩盖,从微粒与介质的作用看,微粒具有大的比表面积和表面能,因此,具有较高的药剂吸附能力,吸附选择性差,表面溶解度增大,使矿浆难免离子增加’质量小易被水流机械夹带和泡沫机械夹带’从微粒与气泡的作用看,由于接触效率及粘着效率降低,使气泡对矿粒的捕获率下降,同时产生气泡的矿泥装甲现象,影响气泡的运载量。
上述种种行为,均是导致细粒浮选速度变慢、选择性变坏、回收率降低、浮选指标明显恶化的主要原因。
为减轻和防止矿泥的有害影响和强化细粒浮选,近代浮选实践中常采用下列工艺措施- (1)消除和防止矿泥对浮选过程的干扰,主要的措施有。
1)脱泥这是一种根除矿泥影响的办法。
分级脱泥是最常用的方法,如在浮选前用水力旋流器分出某一粒级的矿泥,或将其废弃或将矿泥和粗砂分别处理,即进行所谓泥砂分选,对于一些易浮的矿泥,也可在浮选前加少量起泡剂预先浮选脱除。
2)添加矿泥分散剂将矿泥充分分散可以消除矿泥覆盖亨现象和微粒间发生无选择性互凝的有害作用,常用的矿泥分散莉有。
水玻璃、碳酸钠、六偏磷酸钠等。
3)分批加药将捕收剂分段分批添加,既可保持矿浆中药剂的有效浓度,又可提高选择性。
4)降低浮选的矿浆浓度降低浮选矿浆浓度,一方面可以减少矿泥污染精矿泡沫,另一方面也可降低矿浆粘度。
(2)选用对微粒矿物具有化学吸附或螯合作用的捕收剂,以利于提高浮选过程。
处理细泥的工艺方法
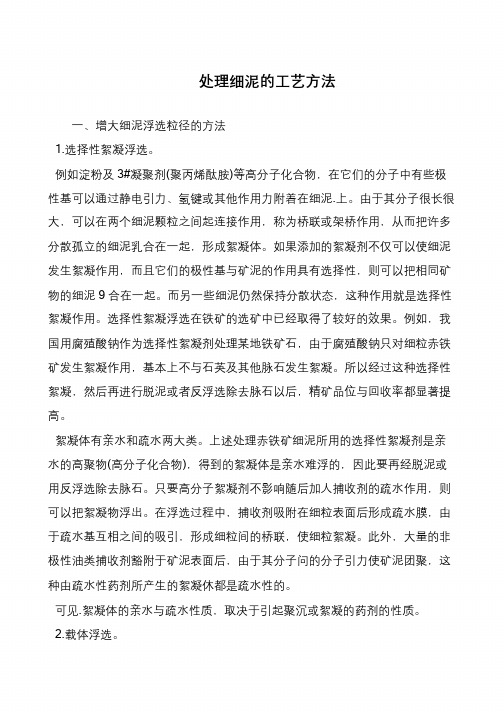
书山有路勤为径,学海无涯苦作舟
处理细泥的工艺方法
一、增大细泥浮选粒径的方法
1.选择性絮凝浮选。
例如淀粉及3#凝聚剂(聚丙烯酞胺)等高分子化合物,在它们的分子中有些极性基可以通过静电引力、氢键或其他作用力附着在细泥.上。
由于其分子很长很大,可以在两个细泥颗粒之间起连接作用,称为桥联或架桥作用,从而把许多分散孤立的细泥乳合在一起,形成絮凝体。
如果添加的絮凝剂不仅可以使细泥发生絮凝作用,而且它们的极性基与矿泥的作用具有选择性,则可以把相同矿物的细泥9 合在一起。
而另一些细泥仍然保持分散状态,这种作用就是选择性絮凝作用。
选择性絮凝浮选在铁矿的选矿中已经取得了较好的效果。
例如,我国用腐殖酸钠作为选择性絮凝剂处理某地铁矿石,由于腐殖酸钠只对细粒赤铁矿发生絮凝作用,基本上不与石英及其他脉石发生絮凝。
所以经过这种选择性絮凝,然后再进行脱泥或者反浮选除去脉石以后,精矿品位与回收率都显著提高。
絮凝体有亲水和疏水两大类。
上述处理赤铁矿细泥所用的选择性絮凝剂是亲水的高聚物(高分子化合物),得到的絮凝体是亲水难浮的,因此要再经脱泥或用反浮选除去脉石。
只要高分子絮凝剂不影响随后加人捕收剂的疏水作用,则可以把絮凝物浮出。
在浮选过程中,捕收剂吸附在细粒表面后形成疏水膜,由于疏水基互相之间的吸引,形成细粒间的桥联,使细粒絮凝。
此外,大量的非极性油类捕收剂豁附于矿泥表面后,由于其分子问的分子引力使矿泥团聚,这种由疏水性药剂所产生的絮凝休都是疏水性的。
可见.絮凝体的亲水与疏水性质,取决于引起聚沉或絮凝的药剂的性质。
2.载体浮选。
第五章 浮选工艺过程

矿物的可浮性与矿物的粒度有密切的关系
图中列出了两个选矿 厂铜、铅、锌回收率与粒 度关系的实际资料。从图 中可以看出,小于10μm 或大于100μm的矿粒,其 可浮性明显降低。因此, 只有中等粒度的矿粒才具 有最佳的可浮性。
二、粗粒浮选的工艺措施
1. 调节药方:调节药方的目的是在于提高矿物与气泡的固 着强度,加快矿化气泡的升浮速度。可从药剂选择,用药 量等方面加以考虑。 (1)药剂的选择 (2)合理地增加药剂浓度 2. 调节充气情况:调节充气情况包括调节气量和充气质量。 (1)提高充气量 (2)提高充气质量 3. 选择浮选机:在选择浮选机时,应注意选取充气量大, 搅拌力强,能析出微泡的浅槽型浮选机,才有利于粗粒物 料的分选。 (1)搅拌力强 (2)选用浅槽型浮选机
二、矿浆浓度对浮选的影响
1. 回收率
2. 精矿质量 3. 药剂质量 4. 浮选机的质量 5. 浮选时间 6. 水电消耗
三、分级调浆的概念及作用
调浆:把原矿或适宜浓度的矿浆,。依次加入浮选剂, 并搅拌混匀,从而保证浮选过程正常有效地进行。 分级调浆:根据不同粒度不同调浆条件,矿浆按粗细粒 级分级或两支或三支进行调浆。 分级调浆的粒度界限可通过实验来确定。
四、药剂的预处理
同一种药剂,由于使用方法的不同,其用量和效果都 不同,特别在水中溶解度小或不溶的药剂,更加明显。 1.配制水溶液:对于易溶于水的,一般配成5-10%的水 溶液使用,如黄药,硫酸铜,苏打等等。 2.加溶剂配制:一些不溶于水,但溶于某些溶剂的药剂, 可以将其溶于溶剂中,如油到不溶于水,但溶于煤油;白 药溶于邻甲苯胺等,先将其溶解,然后使用,可以提高其 捕收作用。 3.配制成悬浮液或乳浊液:一些不易溶的固体药剂,可 配成池浊液或悬浮液使用。例如,石灰在水中溶解度极小, 20℃时约为0.17%,随着温度反而减小,因此将石灰磨至 100-10μm,与水混合搅拌制成石灰乳使用。
浮选工艺技术
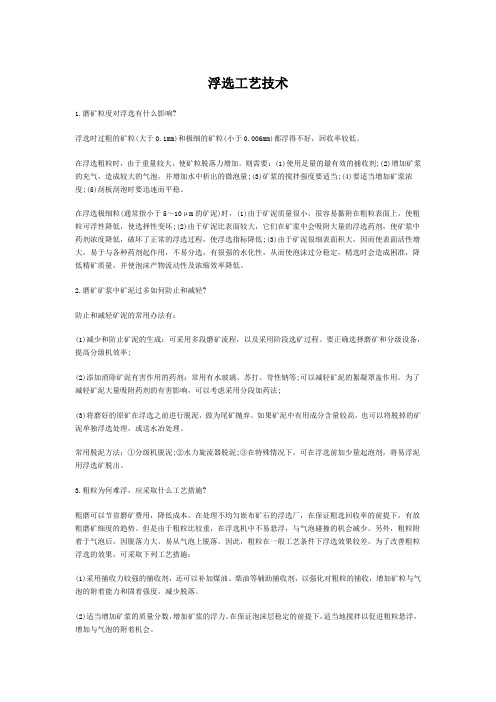
浮选工艺技术1.磨矿粒度对浮选有什么影响?浮选时过粗的矿粒(大于0.1mm)和极细的矿粒(小于0.006mm)都浮得不好,回收率较低。
在浮选粗粒时,由于重量较大,使矿粒脱落力增加。
则需要:(1)使用足量的最有效的捕收剂;(2)增加矿浆的充气,造成较大的气泡,并增加水中析出的微泡量;(3)矿浆的搅拌强度要适当;(4)要适当增加矿浆浓度;(5)刮板刮泡时要迅速而平稳。
在浮选极细粒(通常指小于5~10μm的矿泥)时,(1)由于矿泥质量很小,很容易黏附在粗粒表面上,使粗粒可浮性降低,使选择性变坏;(2)由于矿泥比表面较大,它们在矿浆中会吸附大量的浮选药剂,使矿浆中药剂浓度降低,破坏了正常的浮选过程,使浮选指标降低;(3)由于矿泥很细表面积大,因而使表面活性增大,易于与各种药剂起作用,不易分选,有很强的水化性,从而使泡沫过分稳定,精选时会造成困准,降低精矿质量,并使泡沫产物流动性及浓缩效率降低。
2.磨矿矿浆中矿泥过多如何防止和减轻?防止和减轻矿泥的常用办法有:(1)减少和防止矿泥的生成:可采用多段磨矿流程,以及采用阶段选矿过程。
要正确选择磨矿和分级设备,提高分级机效率;(2)添加消除矿泥有害作用的药剂:常用有水玻璃、苏打、苛性钠等;可以减轻矿泥的絮凝罩盖作用。
为了减轻矿泥大量吸附药剂的有害影响,可以考虑采用分段加药法;(3)将磨好的原矿在浮选之前进行脱泥,做为尾矿抛弃。
如果矿泥中有用成分含量较高,也可以将脱掉的矿泥单独浮选处理,或送水冶处理。
常用脱泥方法:①分级机脱泥;②水力旋流器脱泥;③在特殊情况下,可在浮选前加少量起泡剂,将易浮泥用浮选矿脱出。
3.粗粒为何难浮,应采取什么工艺措施?粗磨可以节省磨矿费用,降低成本。
在处理不均匀嵌布矿石的浮选厂,在保证粗选回收率的前提下,有放粗磨矿细度的趋势。
但是由于粗粒比较重,在浮选机中不易悬浮,与气泡碰撞的机会减少。
另外,粗粒附着于气泡后,因脱落力大,易从气泡上脱落。
浮选工艺粒度与药剂制度
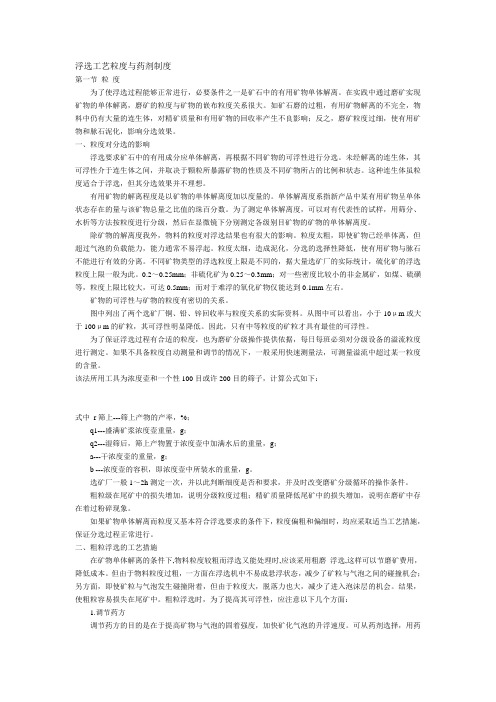
浮选工艺粒度与药剂制度第一节粒度为了使浮选过程能够正常进行,必要条件之一是矿石中的有用矿物单体解离。
在实践中通过磨矿实现矿物的单体解离,磨矿的粒度与矿物的嵌布粒度关系很大。
如矿石磨的过粗,有用矿物解离的不完全,物料中仍有大量的连生体,对精矿质量和有用矿物的回收率产生不良影响;反之,磨矿粒度过细,使有用矿物和脉石泥化,影响分选效果。
一、粒度对分选的影响浮选要求矿石中的有用成分应单体解离,再根据不同矿物的可浮性进行分选。
未经解离的连生体,其可浮性介于连生体之间,并取决于颗粒所暴露矿物的性质及不同矿物所占的比例和状态。
这种连生体虽粒度适合于浮选,但其分选效果并不理想。
有用矿物的解离程度是以矿物的单体解离度加以度量的。
单体解离度系指新产品中某有用矿物呈单体状态存在的量与该矿物总量之比值的珠百分数。
为了测定单体解离度,可以对有代表性的试样,用筛分、水析等方法按粒度进行分级,然后在显微镜下分别测定各级别目矿物的矿物的单体解离度。
除矿物的解离度我外,物料的粒度对浮选结果也有很大的影响。
粒度太粗,即使矿物已经单体离,但超过气泡的负载能力,能力通常不易浮起。
粒度太细,造成泥化,分选的选择性降低,使有用矿物与脉石不能进行有效的分离。
不同矿物类型的浮选粒度上限是不同的,据大量选矿厂的实际统计,硫化矿的浮选粒度上限一般为此。
0.2~0.25mm;非硫化矿为0.25~0.3mm;对一些密度比较小的非金属矿,如煤、硫磺等,粒度上限比较大,可达0.5mm;而对于难浮的氧化矿物仅能达到0.1mm左右。
矿物的可浮性与矿物的粒度有密切的关系。
图中列出了两个选矿厂铜、铅、锌回收率与粒度关系的实际资料。
从图中可以看出,小于10μm或大于100μm的矿粒,其可浮性明显降低。
因此,只有中等粒度的矿粒才具有最佳的可浮性。
为了保证浮选过程有合适的粒度,也为磨矿分级操作提供依据,每日每班必须对分级设备的溢流粒度进行测定。
如果不具备粒度自动测量和调节的情况下,一般采用快速测量法,可测量溢流中超过某一粒度的含量。
- 1、下载文档前请自行甄别文档内容的完整性,平台不提供额外的编辑、内容补充、找答案等附加服务。
- 2、"仅部分预览"的文档,不可在线预览部分如存在完整性等问题,可反馈申请退款(可完整预览的文档不适用该条件!)。
- 3、如文档侵犯您的权益,请联系客服反馈,我们会尽快为您处理(人工客服工作时间:9:00-18:30)。
1 细粒浮选的工艺措施
矿泥的影响及消除措施
一般选矿所谓的矿泥,常常是指-200目的颗粒级,而浮选中的矿泥是指-18UM 或-10UM 的细粒级。
矿泥分原生矿和次生矿泥。
原生矿泥主要是矿石中的各种泥质矿物,如高岭土、娟云母、褐铁矿、绿泥石、碳质页岩等;次生矿泥是在破碎、磨矿、运输、搅拌等过程中形成的。
由于矿泥具有质量小、比表面大等性质,所以对浮选产生了一些列不利的影响,其中主要有:易夹杂与泡沫中上浮,降低了精矿质量;罩盖在粗粒矿物上,妨碍其浮选,降低回收率;吸附大量的浮选药剂,增加药耗;增加矿浆黏度,使浮选机充气条件变坏;细泥溶解度较大,使矿浆中“难免离子”增加。
大量矿泥的存在,往往会破坏浮选过程,恶化浮选指标。
为了消除或减少矿泥对浮选的影响,可以采取下列工艺措施;
(1)添加矿泥分散剂。
将矿泥分散可以消除矿泥罩盖于其他矿物表面的有害作用常用的矿泥分散剂水玻璃、碳酸钠、氢氧化钠、六偏磷酸钠等。
(2)分段、分批加药。
要随时保持矿浆中药剂的有效浓度,将药剂分段、分批添加,可避免药剂一次性加入时,被矿泥吸收造成无畏的消耗。
(3)采用较稀矿浆。
减轻矿泥对精矿泡沫的污染,降低矿浆黏度。
(4)脱泥。
是消除矿泥影响的根本方法。
常采用分级脱泥,或选择性分散后再分级脱泥,实现“泥砂分选”。
此外,浮选前可添加少量起泡剂或专门药方浮出矿泥。
细粒浮选
对于细粒嵌布的矿物,经细磨产生的所谓细粒的浮选,可采用某些强化细粒浮选的措施,主要包括:
(1)选择或采用对微细粒矿物具有化学吸附或螯合作用的浮选药剂,提高浮选过程的选择性。
(2)选择性絮凝浮选。
采用絮凝剂选择性絮凝目的矿物或非目的矿物,已用于细粒赤铁矿选别。
(3)载体浮选。
利用适合浮选的粒级的矿粒作载体,是细粒罩盖于载体上浮,载体可用同类矿物,也可用异类矿物,如用黄铁矿作载体浮选细粒的金。
(4)团絮浮选,有称乳化浮选。
微细粒矿物经捕收剂处理,在中性油的作用下,形成带矿的油状泡沫或有膜。
其操作工艺条件分为两类:捕收剂与中性油先配成乳化液加入;在高浓度(达70%固体)矿浆中,分别按先后次序加入中性油及捕收剂,强烈搅拌,控制时间,然后刮出上层泡沫。
(5)微泡浮选。
减小气泡尺寸,有利于增加气-液界面,增加微细粒间的碰撞和粘附概率。
主要工艺有:电解浮选和真空浮选。
电解浮选是利用电解方法获得0.02-0.06MM 的微泡。
用于浮选细粒锡石时,单用电解氢气泡浮选,与常规浮选相比,粗选回收率由33.5%提高到79.5%,同时品味还提高了0.8%。
真空浮选则是采用降压装置,从溶液中析出0.1-0.5MM 的微泡。
用于浮选细粒重晶石时,与常规浮选相比,精矿品味和回收率均有大幅度提高。