锻造用钢锭和锻圆通用技术要求
锻件通用技术要求

1 、锻件通用技术要求(JB/ZQ4000.7-86)2 、铸件通用技术要求(JB/ZQ4000.5-86)(铸件技术要求) :铸件尺寸公差要求CT3 、焊接件通用技术要求(JB/ZQ400.3-86)1. 焊接结构件的长度尺寸公差见1-245c 尺寸和形位公差数值.plb, 适用于焊接零件和焊接组件的长度尺寸. 焊接件的直线度. 平面度和平行度公差见1-245c 尺寸和形位公差数.plb, 焊接结构件的尺寸公差与形位公差等级选用见1-245b 尺寸和形位公差等级.plb2. 标注和未标注角度的偏差见1-246a 角度偏差.plb, 角度偏差的公称尺寸以短边为基准边, 其长度从图样标明的基准点算起.3. 喷丸处理的焊接件, 为了防止钢丸钻入焊缝, 必须焊接内焊缝, 并尽量避免内室和内腔. 如果结构上必须有内室和内腔,则必须进行酸洗, 以便达到表面除锈质量等级Be(见JB/ZQ4000.10-86 附录A). 对此图样需作标注.4. 由平炉钢制造的低碳钢结构件, 可在任何温度下进行焊接. 但为了避免焊接过程产生裂纹及脆性断裂, 厚度较大的焊接件, 焊削必须根据工艺要求,进行预热和缓冷. 板厚超过30mm的重要焊接结构,焊后应立即消除内应力, 消除内应力采用550- 600℃ 回火, 或200℃局部低温回火.5. 普通低合金结构钢制造的焊接件, 必须按照焊接零件的碳当量和合金元素含量、零件的厚度、钢结构件的用途和要求进行焊前预热和焊后处理, 见表 1 .4 、涂装通用技术条件(JB/ZQ4000.10-88)1. 涂装前对物体的表面要求应符合本标准的规定.2. 除锈后的金属表面与涂底漆的间隔时间不得大于6h, 酸洗处理表面与第一次涂底漆时间不少于48h, 但无论间隔时间多少, 涂漆前表面不得有锈蚀或污染.3. 铆接件相互接触的表面, 在联接前必须涂厚度30-40 μm防锈漆. 由于加工或焊接损坏的底漆,要重新涂装.4. 不封闭的箱形结构内表面, 在组焊前必须涂厚度60-80 μ m防锈漆, 封闭的箱体结构件内表面不涂漆.5. 溜槽、漏斗、裙板内表面、平衡的重箱内表面、安全罩内表面、封闭箱且在运输过程中是敞开的内表面等, 必须涂厚度60-80 μ m防锈漆.6. 涂层的检查项目及方法应符合本标准的规定.6 、装配通用技术条件(JB/ZQ4000.9-86)1. 外购材料与零部件应具有JB/ZQ4000.1-86< 产品检验通用技术要求>中规定的检验报告与合格证.2. 用于紧固机架, 机座和压力容器压紧法兰的紧固件,在紧固后, 螺钉或螺母的端面与被紧固零件间的倾斜不得大于1°.3. 螺栓与螺母拧紧后, 螺栓应露出螺母2-4 扣, 不许露出过长或过短.120 0.10 10C=Lα △t+0.15式中:C─ 轴承外座圈与端盖间的间隙,mm.L─ 两轴承中心距,mm.α─ 轴材料的线膨胀系数(取α=12×10^( -6)△t─ 轴工作时温度与环境温度之差,℃ . 0.15 ─ 轴膨胀后剩余的间隙,mm.15. 单列圆锥滚子轴承、向心推力球轴承、双向推力球轴承向游隙按(表1)调整. 双列和四列圆锥滚子轴承在装配时均应检查其轴向游隙,并应符合(表2)的要求.四列圆锥滚子轴承内径225-3150.30-0.40 0.70-0.80 315-560 0.40-0.50 0.90-1.00120-180 0.15-0.25 180-315 0.20-0.30 315-400 0.25-0.35 400-500 0.30-0.40 500-630 0.30-0.40 630-8000.35-0.45800-1000 0.35-0.4516. 滑动轴承上、 下轴瓦的接合面要接触良好 , 无螺钉把紧的轴瓦接合面 , 用 0.05mm 和塞尺从外侧 检查, 在各处的塞入深度 , 都不得大于接合面的 1/3.17. 上、下轴瓦装配后其外圆应与相关轴承孔良好接触 , 如果图样或相关设计文件对接触率未作具 体规定时 , 应按下表的规18. 轴瓦内孔刮研后 , 应与相关轴颈接触良好 , 如图样或相关设计文件未作具体规定时 , 则按下表 的规定执行 . 轴向游隙注: 受力较小的轴瓦、接触点可在25×25mm^2的面积上, 按表中数值降低 1 个接触点.19. 上、下轴瓦接触角α 以外的部分均需刮出油楔(如下表所示C1), 楔形从瓦口开始由最大逐步过渡到零, 楔形最大值按下表中规定. 上、下轴瓦经刮研达要求并组装后, 轴瓦内径与轴顶部处的间隙值 C 应达到图样配合公差的中间值或接近上限值.20. 轴瓦中装固定销用的通孔, 应在瓦口面与相关轴承孔的开合面保持平齐的情况下, 与其配钻铰. 固定销打入后, 应与销孔紧密配合, 不得有松动现象, 销子的端面应低于轴瓦内孔2-3mm.21. 过盈配合零件在装配前必须对配合部位进行复检, 并做好记录. 过盈量应符合图样或工艺文件的规定; 与轴肩相靠的相头轮或环的端面, 以及作为装配基准的轮缘端面, 与孔的垂直度偏差应在图样规定的范围内.22. 压装的轴和套允许在引入端制作导锥, 导锥的长度不准超过配合部位长度的15%,锥度各工厂自定.23. 采用压力机压装时,应做好压力变化的记录, 压力变化应当平稳,出现异常时就进行分析,不准有压坏零件配合表面的现象. 图样有最大压入力的要求时, 应达到规定数值,不准过大或过小.24. 压装完成后,在轴肩处必须靠紧, 间隙不得大于0.10mm.25. 热装薄环或轮缘时, 在端面处应设置可靠的定位基准.热装后轴与环或轮毂与轮缘之间的中心不准出现互相偏斜现象.26. 除铸铁轮毂与钢制轮缘在热装后可向轮毂内壁均匀浇冷水外, 其余热装零件均应自然冷却, 不准急冷.27. 零件热装时,必须靠紧轴肩或其它相关端面. 零件经过冷缩后, 零件与轴肩或其它相关端面的间隙在图样未做规定时, 不得大于配合长度尺寸的1/1000.28. 主动链轮和被动链轮齿的中心线应当重合. 其偏移误码差不得大于两链轮中心距2/1000.29. 链条非工作边的下垂度, 在图样没有具体规定时, 按两链轮中心距的1-4.5% 的规定.30. 相关的两个平面需要互研时, 只能在两个平面各自按平板或平尺刮研接近合格后,方准两件互研. 被刮研表面接触点在图样或相关设计文件无具体规定或以精磨代替刮研时, 应符合下表规定.31. 下列回转零件必须做静平衡试验1). 图样已给出不平衡力矩限值的零件2). 对于没有注明静平衡试验的回转零件, 当Q.nmax> 25时均需进行静平衡试验. 式中Q为回转零件的质量,t;nmax 为回转零件的最大转速,r/min. 当nmax≤20r/min 的以及锻造的全加工、全对称的回转零件不作静平衡试验.32. 对于需要作平衡试验,但未规定平衡精度时,按JB/ZZ4-86<< 刚体转动件的平衡>>规定的平衡精度G18执行.33. 所有铸造液压缸体等容器, 如试压工序是安排在粗加工后进行的, 而在精加工后表面又出现了气孔、裂纹、夹渣等缺陷时, 则必须重新进行试压.34. 所有钢板焊接的液压罐等容器,焊后应进行试压, 焊缝处经过切削加工时, 则要重新试压.35. 锻造或锻焊结构的液压缸等, 要采用外观、超声波探伤、液压试验等方法, 对承压的可靠性进行检验.36. 探伤表面粗糙度应达到Ra3.2 μm.37. 承压母体试压与装配后的密封试压, 如无特殊规定试验压力, 一般为工作压力的 1.5 倍.38. 零件母体承压可靠性的试压, 保压15min( 允许补压), 母体各部不准有渗漏现象.39. 装配件密封性试压, 保压2min, 不降压, 且各密封处不准有渗漏现象.。
锻造用钢锭和锻圆通用技术要求

锻造用钢锭和锻圆通用技术要求锻造用钢锭和锻圆通用技术条件1 适用范围本标准适用于锻造用钢锭和锻圆的通用外采及验收,如有特殊产品另行规定。
钢锭与锻圆的区别:钢锭:订货时按照一一对应的工作令、图号按件数进行采购或根据批量常规产品相关技术要求采购的钢锭,具有固定的相关钢锭参数;锻圆:订货时不按照图号要求,而是按批次、按重量采购,形状均为轴类,截面规格有要求,长度方向尺寸范围较宽。
2 规范性引用文件GB/T1979-2001 结构钢低倍组织缺陷评级图GB/T10561-2005 钢中非金属夹杂物含量的测定-标准评级图显微检验法SEP1584的第2版发蓝断口检测法检验钢中宏观非金属夹杂物GB/T222-2006 钢的成品化学成分允许偏差JB/T5000.15-1998 重型机械通用技术条件锻钢件无损探伤JB/T1266-2002 25MW~200MW汽轮机转盘及叶轮锻件技术要求3 技术要求3.1 材料化学成分应符合钢锭和锻圆成分表1规定。
3.2 材料用钢锭冶炼方法:采用电炉+精炼真空脱气进行冶炼。
有要求时,可用电渣重熔钢锭、真空碳脱氧或按专用技术协议。
3.3 化学成份允许偏差按GB/T222标准规定。
34CrMo、34CrNi3Mo、34CrMo1A化学成分允许偏差按JB/T1266-2002执行。
[H]、[O]、[N]成品检测值不允许超出要求值上限的10%。
3.4 锻造比的要求:锻圆锻造比≥3;3.5 锻圆直径方向允许偏差0~10mm,长度方向允许偏差0~40mm。
3.6 锻圆超声波探伤检验,结果均应符合JB/T5000.15-1998中Ⅲ级要求。
钢锭要保证锻件探伤合格,标准符合JB/T5000.15-1998的Ⅲ级。
3.7 钢锭锭身比例要确保大于等于82%。
3.8 表面质量钢锭和锻圆表面不得有肉眼可见的重皮、裂纹、折叠、结疤、夹层、锻伤、夹渣等有害缺陷。
如有上述缺陷必须清除,其清除深度不得超过尺寸下偏差的要求。
锻造技术要求

锻造技术要求一、总则1、本技术要求包括加热要求、自由锻基本工序要求,锻后冷却和热处理要求。
2、严格执行技术要求是保证产品质量的重要条件和必须的生产技术纪律,因此必须严格按技术要求进行操作。
二、操作要求1、锻造有色金属和高合金钢时,要预热上、下砧板和工模具。
2、胎模锻时,工作者应先检查模膛表面质量,并将模具均匀加热到200°C—250°C。
3、锻造过程中坯料产生缺陷应及时消除,再继续锻造,特殊情况下,允许加大局部留量,或者经中间冷却后再处理。
4、严格控制锻造温度范围,特别是关键产品和高合金钢锻件,不准低温锻造。
锻后修整温度可比终锻温度低50-80℃。
5、返修品的加热温度应低于该件的始锻温度。
三、加热要求1、加热前,要熟悉加热规范,检查有关仪器仪表、点火装置和烧咀等,以保证加热炉在正常状态下工作。
2、坯料装炉前,应清理炉膛。
3、不同截面的钢料同炉加热时,按截面大的加热规范进行加热,先锻截面小的。
4、坯料装炉时,应合理放置,加热过程中要勤翻转,保证受热均匀。
5、在保证质量的前提下,一般钢种均可快速加热,以减小材料的氧化、脱碳,提高生产率。
6、高温时,在保证燃烧的情况下,应减少过剩空气量,使炉内保持正压,以免金属过热过烧。
7、坯料装炉时要少装、勤装,避免在高温区停留的时间过长。
因故超过最大保温时间不能锻造时,应降温保温,以免坯料烧坏。
8、铜料和钢料交替使用同一加热炉。
加热铜料时,必须用钢板将坯料与炉底、炉墙隔开。
加热铜料后的加热炉,必须用食盐彻底清理后方可加热钢料。
9、铜料与钢料不得同炉加热。
四、自由锻基本工序守则1、镦粗1、1镦粗前,坯料高度与直径(或边长)之比,不得超过2.5—3,最好在2—2.2的范围内。
1、2镦粗前,坯料高度应小于锻锤行程的75﹪。
1、3坯料两端面应平整并与轴心垂直。
1、4坯料表面不得有凹坑,裂纹等缺陷。
1、5镦粗时,要将坯料围绕其轴心线不停地转动,发生弯曲时必须立即校正。
锻件通用技术条件

锻件通用技术条件交通部上海港口机械制造厂企业标准锻件通用技术条件说明为了保证产品零部件质量,首先必须重视原材料和毛坯件质量。
原材料和毛坯件质量标准是基础标准。
在锻件方面,根据有关资料结合我厂实际制定了三种通用基础标准,即“JQ/GJ21—1—82锻件通用技术条件”“JQ/GJ21—2—82锻件毛坯质量分级标准”“JQ/GJ21—3—82锻件加工余量及尺寸公差”。
“锻件通用技术条件”是考核锻件全面质量的。
“锻件毛坯质量分级标准”主要是考核锻件外形毛坯质量。
本标准经船舶检验局上海办事处于1981年3月4日(81)沪船检字第94号文审查修正,作为起重运输机械锻造通用技术条件。
本标准适用于港口起重运输机械自由锻造,胎膜锻造的普通碳素钢,优质碳素钢和合金结构钢锻件。
对本标准中未规定的特殊要求应在其他专用技术条件中补充规定。
本标准中所以用的国标,部标或其他标准,均以最新标准为准。
一锻件试验分级1、根据设计要求,工作特性和用途,按进行的试验项目和试验数量,将锻件分为Ⅰ、Ⅱ、Ⅲ、Ⅳ、Ⅴ五级,见(表1)表1锻件试验等级硬度 HB 拉力冲击 b 实验项目试验数量典型零件σs或σαk 1Ⅰ无如标准件螺栓螺9母垫圈等。
Ⅱ√每批取5%,但不少于一般的销轴、操纵件 3杆件、高强度螺栓、传动轴等。
Ⅲ√热处理后每件试验硬减速箱传动轴、齿度轮、链轮、滚轮、联轴器零件等。
Ⅳ√√√(1)热处理后,每件变幅螺杆、轮条,做硬度试验 Q≦50T吊钩、吊(2)每批取2%做拉钩横梁螺帽、卷筒力冲击试验,但轴变幅、起升系统不少于2件Ⅴ√√√的铰轴。
(1)典型受力部件Q≧50T吊钩,横每件做实验梁,螺母大型旋转(2)非典型锻件但座圈,锻件等。
项目重量超过1000~1500Kg或长度为≧3M时都必须进行三种试验注:(1)各级锻件必须要符合“二技术要求”中各项规定(2)凡表1中未列出的机械零件,应视零件的具体作用及重要性,按“表1 所列类似性质的典型零件确定实验等级(3)表1中试验数量,均指同钢号、同一热处理的一批锻件,并允许一批锻件中包括根据各图号制造的外形尺寸近似的锻件。
锻造用钢锭技术条件

锻造用钢锭技术条件1,电炉钢锭(外购)技术条件1.1钢的化学成分符合国家标准,偏差应符合GB222。
1.2钢锭尾部圆弧与锭身应圆滑过渡,不得有台阶。
锭尾不得带有汤道把子。
1.3锭身不得有裂纹。
裂纹必须修磨,修磨处应圆滑过渡,修磨处深宽比为1:6,裂纹深度>15mm的钢锭不得镦粗使用,>20mm应判废。
1.4钢锭飞边毛刺应清理,外部粘结的砖块等非金属应清理掉。
结疤、重皮、表面气孔应清理掉。
深度<2mm的缺陷可不予清理。
1.5有接注。
冒口上涨、注入钢渣、混入绝热板等杂物的钢锭应予判废。
2电渣钢锭技术条件2.1钢的化学成分符合国家标准,偏差应符合GB222。
2.2锭型工艺参数见表12.3钢锭表面不允许有结疤、裂纹、气孔及夹渣(渣沟)。
2.4 钢锭表面裂纹清理:重量小于2吨的钢锭,清理深度单边不得大于10mm,大于2吨的钢锭单边清理深度应小于15mm,统同一截面相对两边深度之和<30mm,单边>10mm 不得镦粗使用。
2.5 清理深宽比为1:6,并圆滑过渡。
2.6 下列情况宽不清理:(1)φ400-500mm锭渣沟深度<3mm;(2)φ600-700mm锭渣沟深度<5mm;(3)φ600mm以上合工钢、冷轧辊钢、不锈钢锭渣沟深度应小于4mm。
2.7 深度<10mm渣沟,允许修磨,修磨深宽比为1:6,圆滑过渡。
渣沟深度>10mm的钢锭不可用于镦粗。
2.8 切头、切尾范围见表2,在此范围的缺陷可不清理。
2.9 钢锭报废标准(1)清理缺陷超深者(见2.4条);(2)钢锭高度小于700mm者;(3)高度重量允许偏差±2%,超正偏差部分不计产量,超负偏差不能按原合同交接。
2.10 减斤处理(1)缺陷位置超过切头、切尾长度者;(2)缩孔长度超过允许缩孔深度者(见表3);减斤长度=缩孔深度-允许缩孔深度表3(3)补缩阶段化入余头或未补缩者减斤长度为100-120mm,中间阶段化入余头报废。
(4)减斤重量=减斤长度×单位长度重量单位长度重量见表4。
锻件通用技术要求内容

其它尺寸的一般公差降一级选用, 如图样上标明一般公差为CT10 级的话,则壁厚公差选用CT11级.
5.特殊要求的公差, 应直接标注毛坯件基本尺寸的后面,如95±1.1. 特殊要求的公差可比一般公差
高或低.一般情况下不能低于1-176 小批单件毛坯尺寸公差.plb规定的公差等级围,当要求的
应力后再继续焊满坡口, 最后再做一次消除应力热处理.补焊大型或碳当量(碳当量的计算见本标
准附录A)超过0.4%的铸钢件的缺陷时, 在补焊后应立即入炉进行消除应力的热处理.
8.设计人员根据铸件的技术要求填写下表,并将此表贴在铸件图样的右上部.
(铸件技术要求) :
通用技术要求
JB/ZQ4000.5
铸件尺寸公差要求
CT
密封试验
是/否
耐压试验
是/否
注:表中空格中可补充其它技术要求.
3、焊接件通用技术要求(JB/ZQ400.3-86)
1.焊接结构件的长度尺寸公差见1-245c尺寸和形位公差数值.plb,适用于焊接零件和焊接组件的长度尺寸. 焊接件
的直线度.平面度和平行度公差见 1-245c尺寸和形位公差数.plb,焊接结构件的尺寸公差与形位公差等级选用见
二、锻件组别:Ⅱ
1.组别的基本标志
1)检验特性: 测定每批中锻件的硬度.
2)组成批的条件:
根据同一规进行热处理的同一钢号的锻件.
2.验收时的必要力学性能指标: HB
3.试验方法
1)力学性能: -
2)硬度: 每批中试验5%,但不少于5件.
三、锻件组别:Ⅲ
1.组别的基本标志
1)检验特性: 测定每一锻件的硬度.
钢质模锻件通用技术条件

钢质模锻件通用技术条件一、总则1.1锻件的技术条件是锻件质量的检验依据。
锻件的主要技术条件一般都标在锻件工艺卡片上,而对于工艺卡上没有注明的、技术协议书上或合同上没有规定的技术问题,在检验锻件时应该执行锻件通用技术条件中的相应规定。
1.2本技术条件适用于在模锻锤、模锻压力机、螺旋压力机或平锻机等锻压设备上进行成批、大批生产成形的钢质热模锻件(以下简称锻件)。
二、锻件的外观质量和交货重量2.1内外拔模角及其数值:锻件在冷缩时,趋向离开模壁内部分为外拔模角,用α表示。
反之为外拔模角,用β表示。
如图所示。
为了便于制造模具时采用标准刀具,拔模角应选用:0°15'、0°30'、1°00'、1°30'、3°00'、5°00'、7°00'、10°00'、12°00'、15°00'。
2.2圆角半径内、外圆角半径及数值:锻件上的凸角圆角半径为外圆半径r,凹圆角半径为内圆角半径R。
为保证锻件凸角处的最小余量,则V1=余量+零件的倒角值。
为了便于制造模具所用刀具的标准化,圆角半径数值应选用:1.0mm、1.5mm、2.0mm、2.5mm、3.0mm、4.0mm、5.0mm、6.0mm、8.0mm、10.0mm、12.0mm、15.0mm……。
圆角半径大于15mm时,逢5递增。
2.3尺寸公差:锻件图未注明的长度、宽度、高度和深度公差、直线度、平面度、错模,可按GB/T12362-1990《钢质模锻件公差及机械加工余量》所列数值确定。
2.4表面缺陷深度:锻件的表面缺陷包括凹坑、麻点、碰伤、凹凸不平、折叠和裂纹等。
锻件的表面缺陷深度是指从锻件实际表面测量所得的局部凹陷或凸起的尺寸数值,该数值不计入锻件的实测尺寸。
(1)加工面的缺陷深度:若锻件的实际尺寸恰等于其基本尺寸,则缺陷之深度不得大于锻件的名义加工余量的一半。
若锻件的实际尺寸大于或小于其基本尺寸,则缺陷的深度不得大于锻件名义加工余量之半,加上或减去单边的实际偏差值。
锻件通用技术要求
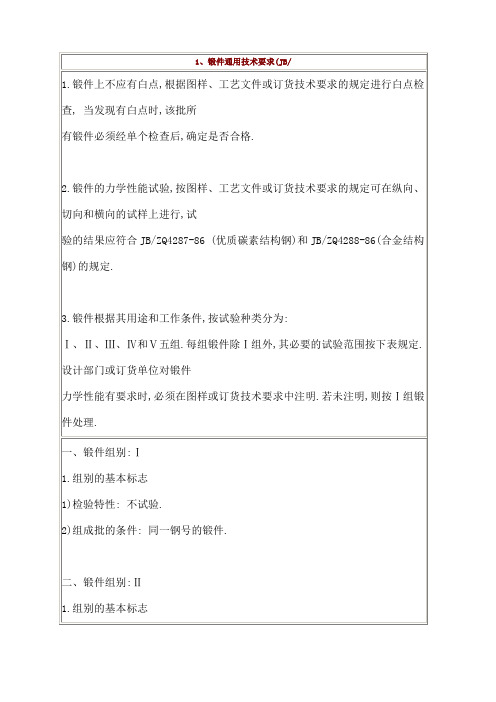
4、涂装通用技术条件(JB/
1.涂装前对物体的表面要求应符合本标准的规定.
2.除锈后的金属表面与涂底漆的间隔时间不得大于 6h,酸洗处理表面与第一次涂底漆时间不少
于 48h,但无论间隔时间多少,涂漆前表面不得有锈蚀或污染.
3.铆接件相互接触的表面, 在联接前必须涂厚度30-40μm防锈漆.由于加工或焊接损坏的底漆,
4.由平炉钢制造的低碳钢结构件, 可在任何温度下进行焊接.但为了避免焊接过程产生裂纹及脆性断裂, 厚度较大的焊
接件,焊削必须根据工艺要求,进行预热和缓冷. 板厚超过30mm的重要焊接结构,焊后应立即消除内应力,消除内应力
采用550-600℃回火,或200℃局部低温回火.
5.普通低合金结构钢制造的焊接件,必须按照焊接零件的碳当量和合金元素含量、零件的厚度、 钢结构件的用途和要求
2)组成批的条Leabharlann :?共同进行热处理的同一钢号的锻件.
2.验收时必要力学性能指标: HB
3.试验方法:
1)力学性能: -
2)硬度: 每一锻件均受试验.
四、锻件组别:Ⅳ
1.组别的基本标志
1)检验特性:?
测定每一锻件的硬度和每一批中的力学性能.
2)组成批的条件:
共同进行热处理的同一炉号的锻件.
2.验收时的必要力学性能指标:?
率在齿长和齿高方向上均不得低于50%,研合时可用0.05mm的塞尺检查齿侧隙,塞尺不得插入全齿长.
8.锥轴伸与轴孔配合表面接触应均匀, 着色研合检验时其接触率不得低于70%.
9.各类联轴器技术要求及轴向(△X)、径向(△Y)与角向(△α)的许用补偿量,应符合有关联轴器标准的规定.
10.轴承外圈与开式箱体或轴承座的各半圆孔间不准有"夹帮"现象,各半圆孔的"修帮"尺寸,不准超过下表规定的最大值.
大型锻钢件用真空钢铸锭技术要求

大型锻钢件用真空钢铸锭技术要求1范围本文件规定了大型锻钢件用真空钢锭的冶炼和铸锭的质量要求、设备及仪器要求、人员要求、安全环保要求、原材料及冶金辅具、吊具要求、冶炼和铸锭工艺流程、冶炼工艺、真空铸锭工艺、记录、检验规则和试验方法以及质量证明书。
本文件适用于大型锻钢件用50吨及以上真空钢锭(以下简称为“钢锭”)的冶炼和铸锭。
2规范性引用文件下列文件中的内容通过文中的规范性引用而构成本文件必不可少的条款。
其中,注日期的引用文件,仅该日期对应的版本适用于本文件;不注日期的引用文件,其最新版本(包括所有的修改单)适用于本文件。
GB/T223(所有部分)钢铁及合金化学分析方法GB/T2272硅铁GB/T2988高铝砖GB/T3649钼铁GB/T3795锰铁GB/T3863工业氧GB/T3864工业氮GB/T4139钒铁GB/T4223废钢铁GB/T4336碳素钢和中低合金钢多元素含量的测定火花放电原子发射光谱法(常规法)GB/T4842氩GB/T5683铬铁GB/T6414铸件尺寸公差、几何公差与机械加工余量GB/T6516电解镍GB/T11170不锈钢多元素含量的测定火花放电原子发射光谱法(常规法)GB/T11261钢铁氧含量的测定脉冲加热惰气熔融-红外线吸收法GB∕T20118_一般用途钢丝绳GB/T20123钢铁总碳硫含量的测定高频感应炉燃烧后红外吸收法(常规方法)GB/T20124钢铁氮含量的测定脉冲加热惰气熔融-红外线吸收法GB/T20125低合金钢多元素含量的测定电感耦合等离子体原子发射光谱法GB/T22589镁碳砖YB/T042冶金石灰YB/T192炼钢用增碳剂YB/T5049滑板砖YB/T5051硅钙合金YB/T5217萤石YB/T5296炼钢用生铁AQ2001炼钢安全规程3术语和定义GB/T5611界定的以及下列术语和定义适用于本文件。
真空钢锭vacuum ingot通过电炉粗炼、钢包精炼加真空脱气处理、真空浇注(模铸滴流脱气或模铸滴流脱气加真空碳脱氧)的钢锭。
锻造用钢锭技术条件

锻造用钢锭技术条件锻造用钢锭技术条件1,电炉钢锭(外购)技术条件1.1钢的化学成分符合国家标准,偏差应符合GB222。
1.2钢锭尾部圆弧与锭身应圆滑过渡,不得有台阶。
锭尾不得带有汤道把子。
1.3锭身不得有裂纹。
裂纹必须修磨,修磨处应圆滑过渡,修磨处深宽比为1:6,裂纹深度>15mm的钢锭不得镦粗使用,>20mm应判废。
1.4钢锭飞边毛刺应清理,外部粘结的砖块等非金属应清理掉。
结疤、重皮、表面气孔应清理掉。
深度<2mm的缺陷可不予清理。
1.5有接注。
冒口上涨、注入钢渣、混入绝热板等杂物的钢锭应予判废。
2电渣钢锭技术条件2.1钢的化学成分符合国家标准,偏差应符合GB222。
2.2锭型工艺参数见表12.3钢锭表面不允许有结疤、裂纹、气孔及夹渣(渣沟)。
2.4 钢锭表面裂纹清理:重量小于2吨的钢锭,清理深度单边不得大于10mm,大于2吨的钢锭单边清理深度应小于15mm,统同一截面相对两边深度之和<30mm,单边>10mm 不得镦粗使用。
2.5 清理深宽比为1:6,并圆滑过渡。
2.6 下列情况宽不清理:(1)φ400-500mm锭渣沟深度<3mm;(2)φ600-700mm锭渣沟深度<5mm;(3)φ600mm以上合工钢、冷轧辊钢、不锈钢锭渣沟深度应小于4mm。
2.7 深度<10mm渣沟,允许修磨,修磨深宽比为1:6,圆滑过渡。
渣沟深度>10mm的钢锭不可用于镦粗。
2.8 切头、切尾范围见表2,在此范围的缺陷可不清理。
2.9 钢锭报废标准(1)清理缺陷超深者(见2.4条);(2)钢锭高度小于700mm者;(3)高度重量允许偏差±2%,超正偏差部分不计产量,超负偏差不能按原合同交接。
2.10 减斤处理(1)缺陷位置超过切头、切尾长度者;(2)缩孔长度超过允许缩孔深度者(见表3);减斤长度=缩孔深度-允许缩孔深度表3(3)补缩阶段化入余头或未补缩者减斤长度为100-120mm,中间阶段化入余头报废。
建筑机械与设备锻件通用技术条件
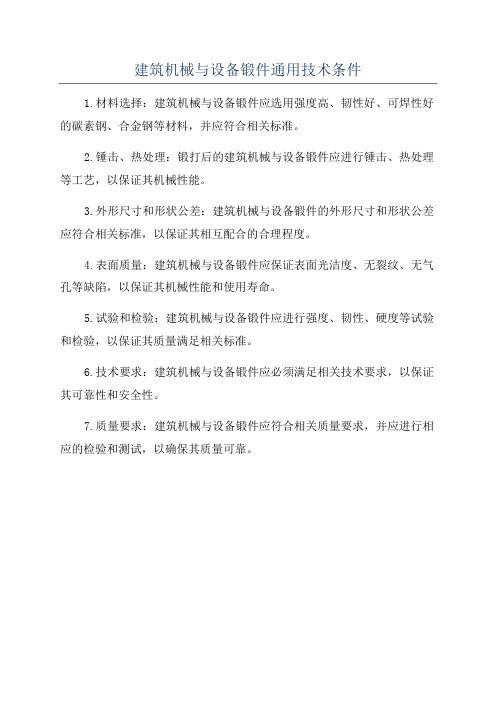
建筑机械与设备锻件通用技术条件
1.材料选择:建筑机械与设备锻件应选用强度高、韧性好、可焊性好的碳素钢、合金钢等材料,并应符合相关标准。
2.锤击、热处理:锻打后的建筑机械与设备锻件应进行锤击、热处理等工艺,以保证其机械性能。
3.外形尺寸和形状公差:建筑机械与设备锻件的外形尺寸和形状公差应符合相关标准,以保证其相互配合的合理程度。
4.表面质量:建筑机械与设备锻件应保证表面光洁度、无裂纹、无气孔等缺陷,以保证其机械性能和使用寿命。
5.试验和检验:建筑机械与设备锻件应进行强度、韧性、硬度等试验和检验,以保证其质量满足相关标准。
6.技术要求:建筑机械与设备锻件应必须满足相关技术要求,以保证其可靠性和安全性。
7.质量要求:建筑机械与设备锻件应符合相关质量要求,并应进行相应的检验和测试,以确保其质量可靠。
锻件通用技术要求优选稿

1.外购材料与零部件应具有JB/ZQ4000.1-86<产品检验通用技术要求>中规定的检验报告与合格证.
2.用于紧固机架,机座和压力容器压紧法兰的紧固件,在紧固后,螺钉或螺母的端面与被紧固零件间的倾斜不得大于1°.
3.螺栓与螺母拧紧后,螺栓应露出螺母 2-4扣,不许露出过长或过短.
(铸件技术要求) :
通用技术要求
JB/ZQ4000.5
铸件尺寸公差要求
CT
密封试验?
是/否
耐压试验?
是/否
注:表中空格中可补充其它技术要求.
3、焊接件通用技术要求(JB/ZQ400.3-86)
1.焊接结构件的长度尺寸公差见1-245c尺寸和形位公差数值.plb,适用于焊接零件和焊接组件的长度尺寸. 焊接件
公称尺寸
加工方法
切削加工
冷作成形
0.5-3(≤)
±0.1?
±0.15
3-6?
±0.1?
±0.2
6-30?
±0.2?
±0.5
30-120?
±0.3?
±0.8
120-400?
±0.5?
±1.2
400-1000?
±0.8?
±2
1000-2000?
±1.2?
±3
2000-4000?
±2?
±4
4000-8000?
一、锻件组别:Ⅰ
1.组别的基本标志
1)检验特性: 不试验.
2)组成批的条件: 同一钢号的锻件.
二、锻件组别:Ⅱ
1.组别的基本标志
1)检验特性: 测定每批中锻件的硬度.
2)组成批的条件:
根据同一规范进行热处理的同一钢号的锻件.
压机上自由锻件通用技术条件

压机上自由锻件通用技术条件摘自ZBJ32001—88一、订货条件1、所需要的数量和材质。
2、需方提供零件图和粗加工图1)如需方仅提供零件图,则需在图样注明热处理条件(余量),工艺夹头及试棒的尺寸和位置。
2)如需方仅提供粗加工图,则需在图样上注明零件尺寸、工艺夹头及试棒的尺寸和位置。
3)需方应在合同中规定锻件的组别,如无规定组别,则按Ⅰ类组别锻件交货。
4)交货状态。
锻件力学性能分组锻件级别组别的基本标志验收的力学性能指标试验数量检验特性组成批的条件拉伸、冲击试验硬度试验Ⅰ不试验Ⅱ测定每批次锻件的硬度同一热处理规范同一钢号的锻件HB每批试验工件Ⅲ测定每一锻件的硬度每一个锻件单个验收HB每一锻件均受试验Ⅳ测定每一锻件的硬度和每批次中锻件的力学性能同炉热处理的统一熔炼号的锻件бb、бs、ф、б5、аk、HB每批试验工件每一锻件均受试验Ⅴ测定每一锻件的力学性能每一个锻件均单个验收бb、бs、б、ф、аk、HB每一锻件均受试验每一锻件均受试验注:1.Ⅳ、Ⅴ类锻件的硬度值不作为验收依据;其验收的力学性能指标项目在必要时,可以由供需双方商定。
2.试棒一般留在锻件上,特殊情况经需方认可方可单独锻造,但必须和它所代表的锻件使用同炉钢液,具有相同的锻造比和锻造方法,并同炉热处理。
二、锻件制造1、锻造用钢应是镇静钢,其化学成分应符合:GBT699—1999、GB/T700—1988、GB/T1591—1994、GB/T3077—1999、GB/T1298—1986、GB/T1299—1985、GB/T1221—1992和GB/T1220—1992的规定。
国标(部标)以外的钢号按合同规定。
1、锻造用钢锭或钢坯应有合格证书。
3、钢锭和钢坯在锻造前必须将影响锻件质量的表面缺陷全部清除,钢锭锻造时两端应有足够的切除量。
4、锻件生产过程中极热、锻造、锻后冷却、热处理和校正等,均按供方的工艺规范执行,重要锻件应有必要的技术记录。
5.锻件应有足够的变形量,从而确保达到锻件的质量要求。
锻材标准 国标
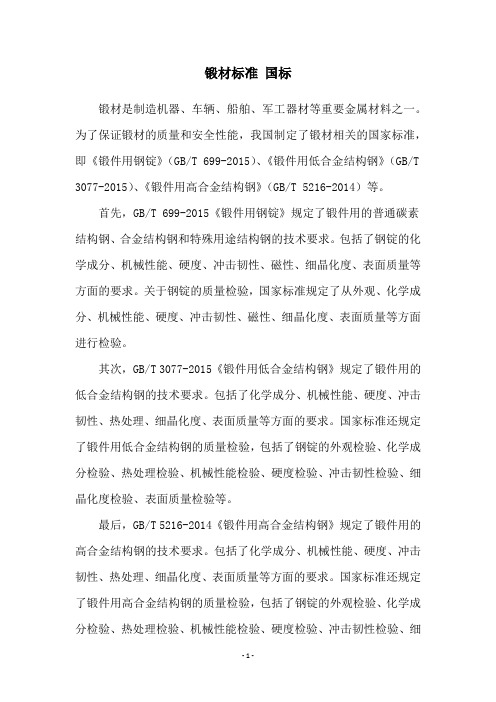
锻材标准国标锻材是制造机器、车辆、船舶、军工器材等重要金属材料之一。
为了保证锻材的质量和安全性能,我国制定了锻材相关的国家标准,即《锻件用钢锭》(GB/T 699-2015)、《锻件用低合金结构钢》(GB/T 3077-2015)、《锻件用高合金结构钢》(GB/T 5216-2014)等。
首先,GB/T 699-2015《锻件用钢锭》规定了锻件用的普通碳素结构钢、合金结构钢和特殊用途结构钢的技术要求。
包括了钢锭的化学成分、机械性能、硬度、冲击韧性、磁性、细晶化度、表面质量等方面的要求。
关于钢锭的质量检验,国家标准规定了从外观、化学成分、机械性能、硬度、冲击韧性、磁性、细晶化度、表面质量等方面进行检验。
其次,GB/T 3077-2015《锻件用低合金结构钢》规定了锻件用的低合金结构钢的技术要求。
包括了化学成分、机械性能、硬度、冲击韧性、热处理、细晶化度、表面质量等方面的要求。
国家标准还规定了锻件用低合金结构钢的质量检验,包括了钢锭的外观检验、化学成分检验、热处理检验、机械性能检验、硬度检验、冲击韧性检验、细晶化度检验、表面质量检验等。
最后,GB/T 5216-2014《锻件用高合金结构钢》规定了锻件用的高合金结构钢的技术要求。
包括了化学成分、机械性能、硬度、冲击韧性、热处理、细晶化度、表面质量等方面的要求。
国家标准还规定了锻件用高合金结构钢的质量检验,包括了钢锭的外观检验、化学成分检验、热处理检验、机械性能检验、硬度检验、冲击韧性检验、细晶化度检验、表面质量检验等。
总之,锻材是重要的金属材料之一,国家标准的制定对于保证锻材的质量和安全性能具有重要意义。
只有加强对锻材的质量监管和质量检验,才能在生产过程中确保锻件的质量稳定和可靠性,保障国家安全和人民生命财产安全。
锻件技术规范15

受控号:
修订状态
更改单编号
更改页次
更改内容简述
批准人
生效日期
1
2
3
4
5
发布日期:2008年05月20日实施日期:2008年05月20日
黑龙江北方有限责任公司技术标准
文件编号:HNVC/JW-15 NO.11
第0次修订
标题:锻件要求技术规范
修订日期:
实施日期:2010.11.20
版号:A
页码:1/2
1目的
规定本公司生产产品的原辅材料—锻件的技术公司产品用碳素钢和合金钢锻件。
3职责
3.1技术部负责制定产品零件的锻件技术要求。
壁厚的15%且不大于6mm,面积不超过所在表面的20%时,允许进行补焊。
4.9低倍组织和金相组织
4.9.1锻件不应存在白点,如发现有白点,则该锻件应予以报废,且与该锻件同熔炼炉号、
同炉热处理的锻件均应逐个检验。
4.9.2锻件不得存在过烧现象,过烧的锻件应予以报废。
4.9.3在含H2S环境下,使用的锻件材料必须符合《API6A材料要求规范》,及MR0175要求。
3.2质量部负责产品锻件的检验。
3.3供销部负责确认合格分供方。
4内容
4.1锻件分为承压锻件和非承压锻件。
4.2锻件用钢。
4.2.1锻件用钢应符合GB699、GB700、GB3077、及GB1591的规定。
4.2.2锻件用钢应采用平炉、电炉或纯氧吹转炉冶炼的镇静钢,也可以经供需双方协商,采
用热加工用轧材或钢锭(改制的钢坯)制成。
4.5补焊
4.5.1只有在公司质量部同意下,才能允许补焊。
4.5.2补焊按《焊接和钎焊作业规范》JHBW/JW05执行。
锻钢通用技术要求

日本工业标准(JIS G 0306)1.适用范围这份日本工业标准详细拟定了应用于生产制造、试验、检验的锻钢件的通用技术要求。
注:在本标准中,{}中所给出的单位和数值采用国际标准单位制,这里仅做说明。
标准中的传统单位和数值应该被换算为1991年1月1日以后实行的国际标准制单位。
2.定义及分类标准中主要条款的定义分类如下:(1)钢锻件:钢锭以及通过锻造、轧制或锻压等方法生产出来的钢材,采用冲压、锤击、锻轧、环形轧制等热加工工艺进行加工之后,通常再进行热处理以获取特定的机械性能。
(2)轴类件:这类物体可以被加工成轴,比如直轴、台阶轴、法兰轴以及带轴的齿轮等,这些都有着圆形的截面,并且轴向长度大于其外径。
(3)筒形件:这类物体都是圆筒状,轴向长度大于其外径。
筒状锻件都是中空的,但是这种中空不是由冲孔和机加工工艺做出。
(4)环形件:这类锻件都是环形,并且轴向长度小于或等于其外径。
环状锻件都需要经过锻造扩孔工艺,不是由冲孔和机加工工艺做出。
(5)饼状件:这类锻件包括规则形状和不规则形状板件,并且轴向长度不大于其外径。
这种板状锻件的最后工序都是墩粗,不是由剪切轴类材料的工艺做出。
3.加工方法3.1 钢锭钢锭是由充分消除了内部缩孔和成分偏析的镇静钢加工而成。
3.2 锻造采用压力、锤击、锻轧、环形轧制等热加工工艺对钢锭进行加工的方法。
经过锻造、轧制或锻轧的钢材可以代替钢锭使用。
热加工工艺和锻造比的选定标准如下:(1)热加工热加工应该作用到锻件的每一部分,并且逐渐均匀过渡到材料的芯部。
通过热加工获得最终的形状和尺寸,并获得尽可能与锻件使用过程中出现的应力相适应的金属流线方向。
(2)锻造比(1)锻件锻造比的确定应该遵照以下标准:(a)对于轴类和筒状锻件,当只采用锻造加工时,主体截面部分大于3S,其它部分大于1.5S,当采用锻轧时,主体截面部分应该大于5S,其它部分大于3S。
(b)对于环形锻件,当采用压力、锻锤以及环形轧机进行锻造扩孔处理时锻造比应该大于3S。
- 1、下载文档前请自行甄别文档内容的完整性,平台不提供额外的编辑、内容补充、找答案等附加服务。
- 2、"仅部分预览"的文档,不可在线预览部分如存在完整性等问题,可反馈申请退款(可完整预览的文档不适用该条件!)。
- 3、如文档侵犯您的权益,请联系客服反馈,我们会尽快为您处理(人工客服工作时间:9:00-18:30)。
锻造用钢锭和锻圆通用技术条件
1 适用范围
本标准适用于锻造用钢锭和锻圆的通用外采及验收,如有特殊产品另行规定。
钢锭与锻圆的区别:
钢锭:订货时按照一一对应的工作令、图号按件数进行采购或根据批量常规产品相关技术要求采购的钢锭,具有固定的相关钢锭参数;
锻圆:订货时不按照图号要求,而是按批次、按重量采购,形状均为轴类,截面规格有要求,长度方向尺寸范围较宽。
2 规范性引用文件
GB/T1979-2001 结构钢低倍组织缺陷评级图
GB/T10561-2005 钢中非金属夹杂物含量的测定-标准评级图显微检验法SEP1584的第2版发蓝断口检测法检验钢中宏观非金属夹杂物
GB/T222-2006 钢的成品化学成分允许偏差
JB/T5000.15-1998 重型机械通用技术条件锻钢件无损探伤
JB/T1266-2002 25MW~200MW汽轮机转盘及叶轮锻件技术要求
3 技术要求
3.1 材料化学成分应符合钢锭和锻圆成分表1规定。
3.2 材料用钢锭冶炼方法:采用电炉+精炼真空脱气进行冶炼。
有要求时,可用电渣重熔钢锭、真空碳脱氧或按专用技术协议。
3.3 化学成份允许偏差按GB/T222标准规定。
34CrMo、34CrNi3Mo、34CrMo1A化学成分允许偏差按JB/T1266-2002执行。
[H]、[O]、[N]成品检测值不允许超出要求值上限的10%。
3.4 锻造比的要求:锻圆锻造比≥3;
3.5 锻圆直径方向允许偏差0~10mm,长度方向允许偏差0~40mm。
3.6 锻圆超声波探伤检验,结果均应符合JB/T5000.15-1998中Ⅲ级要求。
钢锭要保证锻件探伤合格,标准符合JB/T5000.15-1998的Ⅲ级。
3.7 钢锭锭身比例要确保大于等于82%。
3.8 表面质量
钢锭和锻圆表面不得有肉眼可见的重皮、裂纹、折叠、结疤、夹层、锻伤、夹渣等有害缺陷。
如有上述缺陷必须清除,其清除深度不得超过尺寸下偏差的要求。
决不允许对材料进行补焊处理。
3.8.1钢锭几何形状应符合供方向需方提供的钢锭外形尺寸,钢锭高度尺寸偏差最大允许值为±0.3%;钢锭冒口浇注高度应符合要求,最大正偏差不得超过3%,最大负偏差不得超过5%。
3.8.3.钢锭冒口要求收缩良好,以冒口端均匀收缩成弧度“盘面形”为宜。
如冒口处明显收缩不好,去掉保护渣等露出钢面,测量凹坑最低点到冒口顶端平面的垂直距离大于或者等于冒口高度的1/3时,钢锭拒收。
3.8.
4.表面质量应光洁无裂纹、结疤、重皮、接痕等。
一般钢种有深度(或高度)大于5毫米(≤5吨钢锭)和7毫米(>5吨钢锭)的锭身表面缺陷,重要钢种(包括叶轮钢、转子钢、等)有深度(或高度)大于3毫米(≤5吨钢锭)和5毫米(>5吨钢锭)的锭身表面缺陷须进行修磨。
钢锭经修磨后,其凹坑深度不超过钢锭大头直径的3%,其凹坑深度与宽度之比应不小于1:4。
每支钢锭修磨处不超过3处;同一断面上不超过2处,其凹坑深度之和不超过大头直径的5%。
修磨处应圆滑,清理缺陷后打磨光洁。
3.8.5.钢锭的重量应符合相应的公称重量,最大偏差:20吨以上钢锭重量,不得超过±1.5%;10-20吨之间的钢锭重量不得超过±2.0%;10吨以下不得超过±2.5%。
抽检率:同规格钢锭大于10支以上时,抽检率不低于20%;小于10支时,至少抽检2支。
3.8.6.钢锭回厂后成份复检时,用光谱仪靠进锭身底部、锭身中部、锭身冒口端打三点。
3.9 试验方法、检验规则
锻圆必须保证以下高低倍检验结果:在锻圆上取低倍试片,进行低倍检测。
同一熔炼炉号任抽一支,在冒口端(或相当于冒口端)取样,按GB/T1979-2001规定做酸浸低倍组织检查,低倍级别检测符合下表2:
表1
3
备注:表内未注明的残余Cr、Ni含量各不大于0.30%,其它残余合金元素总量≤1.00%。
4
4. 标识及检测细则
4.1锻圆上用钢印及油漆笔同时标明冒口端(用“M”标识)、底部端(用“S”标识)或非底部及冒口端(用“Z”标识),回厂后据标识进行相关复检。
4.2确保锻造用钢锭的冒口端重皮等缺陷与底部端水口切除干净。
4.3供方自检成品分析及高低倍时,按冶炼炉号从锻圆的冒口端与底部端同时取样,分别出具报告(高倍取样位置按标准执行,即距表面1/2半径处);若锻圆截面≥400mm,需在上述检测基础上,,取样位置要增加位于钢锭冒口端及底部的1/2直径处(即中心位置)的检测,每端按90°方向取四个高低倍试样,一并出具报告,并注明取样位置,如“冒口1/2直径”等。
同时在已取样检测的锻圆上注明“已取样”。
材料回厂后,分公司在本冶炼炉次进行过上述取样检测之外的锻圆上取样复检。
4.4 锻圆必须有钢锭镦粗工序后拔长,并保证锻圆锻造比≥3。
4.5 材料尽量做到整炉批次提供,冶炼炉次最少化。
5 检验和验收
5.1 每支锻圆应依次分行打印材料牌号、熔炼炉号(同一炉号多件时应在炉号后面加编序号)、截面规格、长度尺寸,并明确注明冒口端,具体要求按第6条执行。
5.2 供方应向需方提供锻圆、钢锭合格证,内容包括:供货方名称、材料牌号、冶炼方法、化学成分、冶炼炉号、锻比、交货状态、高低倍报告、超声波探伤报告(毛坯参考)、出厂日期、数量等。
并提供原始钢锭冶炼化学成份报告单。
5.3 需方按冶炼炉号进行100%复检,在供方标明“已取样”之外的锻圆上取样,分别在底部端、冒口端切取试片,进行成品分析和高低倍检测(高倍取样位置为距表面1/2半径处),其中对于≥Φ500锻圆进行高倍检测时,需在上述检
测基础上,取样位置要增加位于钢锭冒口端及底部的1/2直径处(即中心位置)的检测,每端按90°方向取四个高低倍试样,并分别出具报告,同时在报告中明确注明取样位置。
5.4 产品制造过程保证在供方厂内完成,不能转包到第三方制造,如需转包,必须征得需方的书面同意方可实施。
5.5 供方应积极配合需方的现场监造、验收和不定期的现场抽查工作,但需方的监造、验收不免除供方的质量责任。
6 钢锭、锻圆钢印打印规定
6.1 打印内容:
6.1.1每支钢锭在底部端用10号字打印材料牌号、熔炼炉号、锭型重量,并要求用油漆笔书写或喷涂放大的标识。
锻圆在底部端用10号字逐件打印材料牌号、熔炼炉号、规格,并要求用油漆笔书写或喷涂放大的标识
6.2 材料牌号打印
印记中的打印材料牌号表示方法与现行材料标准相符合。
6.3 钢锭、锻圆端面钢印打印图示见图1。