催化裂化油浆系统结焦原因及解决措施
催化裂化油浆系统结焦原因及对策
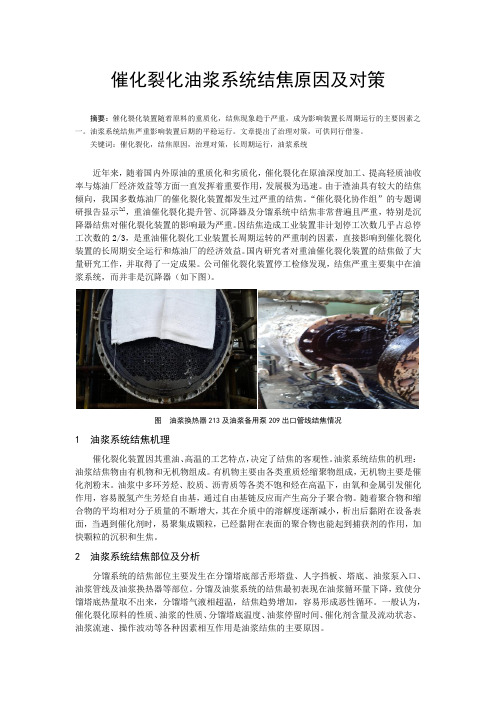
催化裂化油浆系统结焦原因及对策摘要:催化裂化装置随着原料的重质化,结焦现象趋于严重,成为影响装置长周期运行的主要因素之一。
油浆系统结焦严重影响装置后期的平稳运行。
文章提出了治理对策,可供同行借鉴。
关键词:催化裂化,结焦原因,治理对策,长周期运行,油浆系统近年来,随着国内外原油的重质化和劣质化,催化裂化在原油深度加工、提高轻质油收率与炼油厂经济效益等方面一直发挥着重要作用,发展极为迅速。
由于渣油具有较大的结焦倾向,我国多数炼油厂的催化裂化装置都发生过严重的结焦。
“催化裂化协作组”的专题调研报告显示[1],重油催化裂化提升管、沉降器及分馏系统中结焦非常普遍且严重,特别是沉降器结焦对催化裂化装置的影响最为严重。
因结焦造成工业装置非计划停工次数几乎占总停工次数的2/3,是重油催化裂化工业装置长周期运转的严重制约因素,直接影响到催化裂化装置的长周期安全运行和炼油厂的经济效益。
国内研究者对重油催化裂化装置的结焦做了大量研究工作,并取得了一定成果。
公司催化裂化装置停工检修发现,结焦严重主要集中在油浆系统,而并非是沉降器(如下图)。
图油浆换热器213及油浆备用泵209出口管线结焦情况1 油浆系统结焦机理催化裂化装置因其重油、高温的工艺特点,决定了结焦的客观性。
油浆系统结焦的机理:油浆结焦物由有机物和无机物组成。
有机物主要由各类重质烃缩聚物组成,无机物主要是催化剂粉末。
油浆中多环芳烃、胶质、沥青质等各类不饱和烃在高温下,由氧和金属引发催化作用,容易脱氢产生芳烃自由基,通过自由基链反应而产生高分子聚合物。
随着聚合物和缩合物的平均相对分子质量的不断增大,其在介质中的溶解度逐渐减小,析出后黏附在设备表面,当遇到催化剂时,易聚集成颗粒,已经黏附在表面的聚合物也能起到捕获剂的作用,加快颗粒的沉积和生焦。
2 油浆系统结焦部位及分析分馏系统的结焦部位主要发生在分馏塔底部舌形塔盘、人字挡板、塔底、油浆泵入口、油浆管线及油浆换热器等部位。
催化裂化油浆结焦原因及对策

催化裂化油浆结焦原因及对策标签:催化裂化;油浆结焦;解决对策在我国炼油厂的催化裂化过程当中,油浆系统当中产生的结焦结垢问题直接影响到了催化裂化设备的正常工作,主要是因为产生大量的结焦结垢物质,直接降低了热换器的热转化效率,同时提高了管道当中材料输送的阻力,进而造成了蜡油渣油的热转换效率降低。
系统内部产生的蒸汽量减少,同时整个反应设备在工作过程当中的能源消耗量加大,油浆当中多余的热量无法及时被排除,进而造成了整个反应系统内部的热平衡性下降,严重的情况下还直接造成油浆输送系统堵塞,进而影响到了整个生产过程的正常进行。
在最近几年发展过程当中,我国炼油厂的催化裂化原材料质量都不是非常理想,外加上在加油的催化裂化技术方面一直是难以攻克的难题。
因此,催化裂化油浆结焦和结垢的问题受到了各大化工企业的广泛关注,必须要采取相应的解决措施来解决这一问题。
1.催化裂化油浆结焦问题分析1.1温度问题的影响从催化裂化的整个反应过程中可以看出,该反应过程中会受到温度的影响,在相同的催化设备当中分馏塔的底部温度越高,那么出现的结焦现象就越明显。
针对己经产生结焦问题来讲,随着温度不断提高整个反应过程的结焦问题就更加明显,就在模拟FCC油浆的结焦单元当中所得出的结论非常明显。
1.2氧含量的影响通过模拟实验分析了FCC油浆当中产生结焦单元的具体原因,通过向试管当中通入一定量的空气或者是氧气,可以看出在不同量的空气和氧气掺入的情况下,对结焦问题的影响比较明显,其中如果空气或者氧气的参与量较大,那么结焦的问题就越严重。
由此可以看出氧气含量的多少对结焦问题的影响非常明显。
1.3固体和电效应影响通过实际的生产过程可以看出,在催化裂化反应过程当中,如果增加油浆内部的沉降器和过滤器设备之后,在产生结焦和结垢的问题上有着明显的缓解。
因此,这一现象也可以得到充分的证明,从中可以得出催化裂化反应过程中油浆当中,所存在的固体杂质对结焦问题的影响比较明显。
重油催化裂化结焦原因及改进措施

重油催化裂化结焦原因及改进措施重油催化裂化是润滑油加工工艺的一个重要环节,是提高润滑油的质量的关键技术。
在重油催化裂化过程中,结焦是一个常见的问题,会严重降低催化裂化的效率。
重油催化裂化结焦的原因,主要有三个方面:首先,催化剂受污染。
催化剂通常是复合物,容易受到空气、产品成分和其他物质的侵蚀、混入或碳化,受到污染时,催化剂性能会受到严重影响,从而导致结焦。
其次,催化剂不可逆变化。
重油催化裂化温度高,使重油催化剂发生不可逆变化,催化剂的性能也下降,从而导致结焦等问题。
最后,温度控制不当。
重油催化裂化的温度控制是很重要的,太高或太低的温度都会影响催化剂的功能,导致结焦。
为了解决重油催化裂化结焦问题,应采取一些有效的措施。
首先,科学选用催化剂。
重油催化裂化中使用的催化剂一般是催化剂复合物,应根据实际需要科学选择恰当的催化剂,降低催化剂受污染的可能性。
其次,采用稳定性好的催化剂。
重油催化裂化时,要选择温度稳定性较好的催化剂,不变性的催化剂能有效降低结焦的可能性。
再次,做好温度控制。
重油催化裂化时,温度应稳定在一定范围内,太高或太低的温度都会影响催化剂的功能,因此应做好温度控制,以保证重油催化裂化效果。
最后,改善反应条件和催化裂化技术。
采用新型催化剂和剂的组合,改善反应条件,控制反应温度和反应压力,改进催化裂化技术,进一步提高重油催化裂化的效率。
综上所述,重油催化裂化结焦的主要原因是催化剂受污染、催化剂不可逆变化以及温度控制不当。
要改善这种情况,应采取有效的措施,如科学选用催化剂、采用稳定性好的催化剂、做好温度控制、改善反应条件和催化裂化技术等。
只有真正落实这些措施,才能有效防止重油催化裂化结焦,达到质量理想。
催化裂化装置结焦原因分析及对策研究
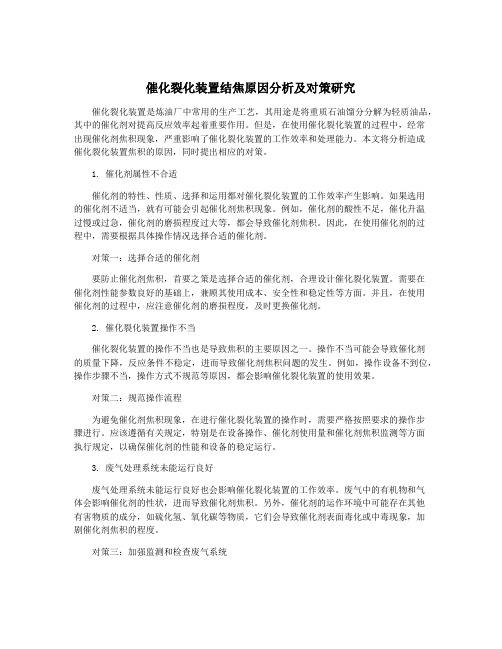
催化裂化装置结焦原因分析及对策研究催化裂化装置是炼油厂中常用的生产工艺,其用途是将重质石油馏分分解为轻质油品,其中的催化剂对提高反应效率起着重要作用。
但是,在使用催化裂化装置的过程中,经常出现催化剂焦积现象,严重影响了催化裂化装置的工作效率和处理能力。
本文将分析造成催化裂化装置焦积的原因,同时提出相应的对策。
1. 催化剂属性不合适催化剂的特性、性质、选择和运用都对催化裂化装置的工作效率产生影响。
如果选用的催化剂不适当,就有可能会引起催化剂焦积现象。
例如,催化剂的酸性不足,催化升温过慢或过急,催化剂的磨损程度过大等,都会导致催化剂焦积。
因此,在使用催化剂的过程中,需要根据具体操作情况选择合适的催化剂。
对策一:选择合适的催化剂要防止催化剂焦积,首要之策是选择合适的催化剂,合理设计催化裂化装置。
需要在催化剂性能参数良好的基础上,兼顾其使用成本、安全性和稳定性等方面。
并且,在使用催化剂的过程中,应注意催化剂的磨损程度,及时更换催化剂。
2. 催化裂化装置操作不当催化裂化装置的操作不当也是导致焦积的主要原因之一。
操作不当可能会导致催化剂的质量下降,反应条件不稳定,进而导致催化剂焦积问题的发生。
例如,操作设备不到位,操作步骤不当,操作方式不规范等原因,都会影响催化裂化装置的使用效果。
对策二:规范操作流程为避免催化剂焦积现象,在进行催化裂化装置的操作时,需要严格按照要求的操作步骤进行。
应该遵循有关规定,特别是在设备操作、催化剂使用量和催化剂焦积监测等方面执行规定,以确保催化剂的性能和设备的稳定运行。
3. 废气处理系统未能运行良好废气处理系统未能运行良好也会影响催化裂化装置的工作效率。
废气中的有机物和气体会影响催化剂的性状,进而导致催化剂焦积。
另外,催化剂的运作环境中可能存在其他有害物质的成分,如硫化氢、氧化碳等物质,它们会导致催化剂表面毒化或中毒现象,加剧催化剂焦积的程度。
对策三:加强监测和检查废气系统为避免催化剂焦积现象的发生,需要严格监测和检查废气系统,确保其正常运行。
催化裂化装置结焦原因分析及对策研究

催化裂化装置结焦原因分析及对策研究催化裂化装置是炼油厂的关键设备之一,其作用是将重质石油馏分分解成轻质产品,包括汽油、柴油和液化石油气等。
由于操作不当或设备故障等原因,催化裂化装置很容易出现结焦现象,严重影响生产效率和产品质量。
对催化裂化装置结焦原因进行分析,并制定相应的对策,对于炼油厂的稳定运行和产品质量具有重要意义。
1. 温度控制不当催化裂化装置工作温度的控制是避免结焦的关键因素之一。
如果温度过高,容易导致催化剂在装置中的积炭过多,从而引发结焦现象。
温度过低也会使催化剂在反应过程中不能充分活化,同样容易导致结焦。
保持合适的工作温度是避免结焦的重要手段。
2. 催化剂质量不良催化裂化装置中使用的催化剂质量的好坏直接影响装置的运行情况。
如果催化剂中存在杂质或者受到空气污染,会导致催化剂的活性降低,从而影响反应的进行,最终导致结焦。
3. 操作人员不当操作催化裂化装置是复杂的设备,需要操作人员具备一定的专业知识和技能。
如果操作人员不当操作,比如在设备运行时不按规定添加催化剂,或者不及时清理催化剂床中的积炭,都会加重结焦的程度。
4. 设备故障设备故障是导致催化裂化装置结焦的另一重要原因。
比如设备堵塞、管道泄漏等故障,都会导致催化剂无法正常流动或者反应不能顺利进行,最终导致结焦。
二、催化裂化装置结焦对策研究为了避免催化裂化装置结焦,首先需要严格控制工作温度。
可以通过安装温度传感器和控制系统,不断监测和调节催化裂化装置的工作温度,保证其在安全范围内稳定运行。
选择高质量的催化剂是避免催化裂化装置结焦的重要措施。
可以通过提高催化剂的制备工艺、严格控制原料质量和加强催化剂检测等手段,提高催化剂的活性和稳定性。
催化裂化装置的操作人员需要接受系统的培训,掌握装置的结构与工作原理,熟悉操作规程,了解可能影响反应的因素,提高操作技能,以减少因操作不当而导致的结焦情况。
4. 定期检查与维护为了预防催化裂化装置结焦,需要定期检查设备的运行情况,发现问题及时处理。
催化裂化油浆结垢原因及解决措施

催化裂化油浆结垢原因及解决措施1前言催化裂化装置的油浆系统设备内的结垢问题是大多数装置存在的问题。
特别是近年来,随着原料的重质化、劣质化以及加工深度的提高, 分馏塔和油浆系统结垢堵塞日益严重,造成能耗增加、装置的处理能力降低、蒸汽发生量减少、油浆多余热量无法取走,系统热平衡遭到破坏,严重影响了装置的正常操作和企业的经济效益。
结垢严重时还会造成油浆输送系统、换热系统堵塞,致使装置停车清垢,这样不仅缩短了装置的运行周期,还可能给装置的安全生产带来隐患。
由此可见,石油加工设备和管线的结垢问题已成为影响装置“安、稳、长、满、优”生产运行的一大障碍,研究能够有效防止或减轻结垢的阻垢剂已是迫在眉睫。
2 垢形成的原因及对策讨论2.1 油浆结垢原因分析2.1.1 原料结构及性质[1]催化裂化原料油日益变重,尤其是大量掺炼减压渣油以后,原料中芳烃、胶质、沥青质含量明显增加。
这就导致油浆中多环芳烃、胶质、沥青质含量增加,这些组分非常容易发生聚合产生结焦。
尤其是外甩油浆少时,加快了油浆浓缩、缩合、生焦。
2.1.2 分馏塔底温度和油浆塔底停留时间[2]分馏塔底温度和油浆在塔底停留时间过长,都会造成油浆系统结焦,使管线和冷换设备堵塞。
催化裂化一般规定塔底温度为360℃以下,但为了达到较高的轻油收率,保证经济效益,分馏塔底需维持较高的操作温度。
当油浆在高温下停留时间过长,或油浆循环量过小时,油浆中有焦生成。
2.2.3 固含量高,油浆系统介质流速低当油浆循环量小,流速低时,造成催化剂颗粒沉积在管壁和设备内部,加速结焦速度。
在低处理量情况下,提升管出口反应油气线速低,导致旋分器效率降低,反应油气携带催化剂粉尘量增加;或者,低处理量时分馏塔底油浆外甩量不足,使油浆中的催化剂颗粒大量沉积在分馏塔底,这些都造成油浆中固含量增高。
另外,由于催化剂机械强度不够,易碎裂,也是油浆中固含量大的一个原因。
2.2 减少结焦的对策2.2.1 使用阻垢剂催化剂粉末沉积问题可以用阻垢剂来控制。
催化裂解装置反应系统结焦原因分析及应对措施
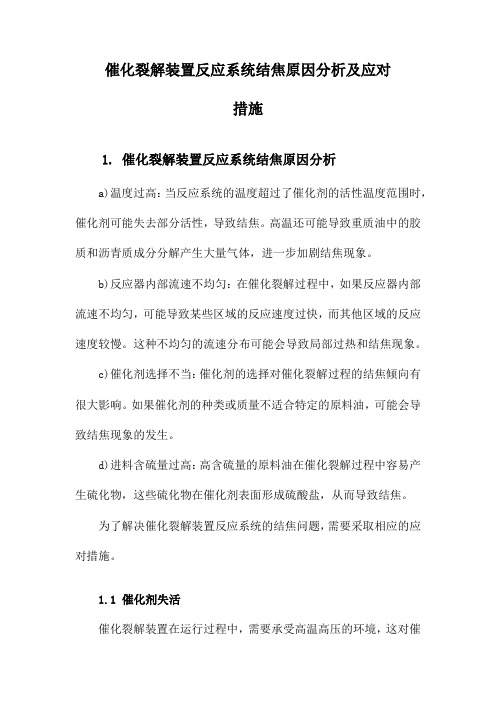
催化裂解装置反应系统结焦原因分析及应对措施1. 催化裂解装置反应系统结焦原因分析a)温度过高:当反应系统的温度超过了催化剂的活性温度范围时,催化剂可能失去部分活性,导致结焦。
高温还可能导致重质油中的胶质和沥青质成分分解产生大量气体,进一步加剧结焦现象。
b)反应器内部流速不均匀:在催化裂解过程中,如果反应器内部流速不均匀,可能导致某些区域的反应速度过快,而其他区域的反应速度较慢。
这种不均匀的流速分布可能会导致局部过热和结焦现象。
c)催化剂选择不当:催化剂的选择对催化裂解过程的结焦倾向有很大影响。
如果催化剂的种类或质量不适合特定的原料油,可能会导致结焦现象的发生。
d)进料含硫量过高:高含硫量的原料油在催化裂解过程中容易产生硫化物,这些硫化物在催化剂表面形成硫酸盐,从而导致结焦。
为了解决催化裂解装置反应系统的结焦问题,需要采取相应的应对措施。
1.1 催化剂失活催化裂解装置在运行过程中,需要承受高温高压的环境,这对催化剂的活性和稳定性提出了很高的要求。
在长时间的高温高压作用下,催化剂会发生热老化、碱腐蚀等现象,导致其活性降低甚至失活。
催化裂解装置的空速是影响催化剂活性的重要参数,如果空速过快,会导致催化剂表面的气体流速过大,从而使催化剂表面积炭速度加快,进而导致结焦现象的发生。
催化裂解装置所处理的原料油品质直接影响催化剂的使用寿命和活性。
如果原料油中杂质含量过高,如硫、磷等元素含量过高,会加速催化剂的失活过程,从而导致结焦现象的发生。
催化裂解装置的操作条件对催化剂的活性有很大影响,如温度、压力、进料量等参数设置不当,都可能导致催化剂失活,进而引发结焦现象。
选择适合催化裂解工艺条件的催化剂,并对其进行优化设计,以提高其抗高温、抗高压、抗污染等性能,从而降低催化剂失活的风险。
通过调整空速参数,使催化剂表面的气体流速保持在合适的范围内,减缓催化剂表面积炭的速度,降低结焦风险。
加强对原料油的质量监控和管理,严格控制原料油中硫、磷等有害元素的含量,降低催化剂失活的可能性。
催化裂化装置结焦原因分析及对策研究

催化裂化装置结焦原因分析及对策研究1. 引言1.1 研究背景催化裂化装置是炼油厂中重要的设备之一,其主要功能是将重质烃分子通过催化剂的作用分解成轻质烃。
在装置长期运行过程中,往往会出现结焦现象,即催化剂表面会沉积焦炭,导致装置效率下降,产品质量下降,甚至影响整个装置的安全稳定运行。
结焦问题一直是炼油行业面临的重要挑战之一,其严重影响了装置的运行效率和经济效益。
目前对于催化裂化装置结焦问题的研究仍存在许多不足之处,需要进一步深入探讨。
本文旨在对催化裂化装置结焦原因进行分析,探讨结焦对装置运行、产品质量和能耗的影响,并提出可行的对策措施,以期提高装置运行效率,保证产品质量,降低能耗,为炼油企业的可持续发展提供有力支撑。
1.2 研究目的研究目的是为了深入分析催化裂化装置结焦的原因,探讨结焦对装置运行、产品质量和能耗的影响,并提出有效的对策研究,以减少结焦现象对装置生产的不利影响,提高装置运行效率和产品质量,降低能耗消耗。
通过研究,我们希望能够为催化裂化装置的优化运行和设备管理提供有益的参考,促进装置的稳定运行和经济效益的提升。
通过对结焦问题的深入探讨和对策研究,我们将为相关行业提供科学合理的解决方案,为我国石油化工行业的发展贡献力量。
【研究目的】是本文研究工作的核心内容,也是我们研究的出发点和目标所在。
2. 正文2.1 裂化装置结焦原因分析裂化装置结焦是由于多种因素共同作用而导致的问题。
主要包括以下几个方面:1. 原料质量不佳:原料中存在硫、氮等杂质或者含硫量、含金属杂质过高,会加剧结焦的风险。
2. 操作条件不当:操作温度、压力、流速等参数控制不严,会导致裂化反应不完全,产生焦碳。
3. 催化剂失活:催化剂在长时间的使用过程中会逐渐失活,失活的催化剂无法有效促进裂化反应,容易引起结焦问题。
4. 设备老化:设备长时间运行会导致管道、换热器等部件堵塞或老化,影响流体正常流动,从而促进结焦现象的发生。
要解决裂化装置结焦问题,需要从原料选取、操作控制、催化剂管理、设备维护等方面进行全面考虑和改进。
某重油催化裂化装置结焦原因分析及其预防应对策略

某重油催化裂化装置结焦原因分析及其预防应对策略本文以某石化公司1.2Mt/年重油催化装置为例,就其运行过程中出现的装置提升管、沉降器、分馏塔底和油浆循环系统结焦问题进行了原因分析,并提出了针对性的预防应对措施。
标签:重油催化裂化装置;结焦原因;预防应对措施1.装置结焦概况该装置开工运行两个月后由于分馏塔底结焦,油浆泵出现抽空,经反复调节无效后,装置被迫停工。
停工检查发现:(1)分馏塔底严重结焦,塔底几乎全部充满了焦碳,只有油气入口处和靠近分馏塔搅拌蒸汽入口处的塔壁有空隙。
分馏塔板一层焦厚300-400mm,二层200-300mm,多块塔板被压弯变形,还有两块板脱落。
(2)油浆循环下返塔、油浆回炼线、提升管喷嘴预热线及反应集合管处分馏塔底补油线被堵塞,堵塞物为黑色半固状体。
经做苯溶解和苯不溶物灼烧后,Al2O3含量分析结果为苯溶物49%,苯不溶物为51%,Al2O3含量为4.3%(m),推算结果约含催化剂15%左右。
(3)油浆/原料换热器堵塞严重,且油浆系统调节阀磨损严重。
(4)装置停工检修期间检查发现提升管喷嘴上方1m处有大量硬质焦块,该部位人孔全部堵死。
沉降器顶有大量焦块,防焦蒸汽环管大部分被埋死。
沉降器旋分器升气管外壁有大量硬质焦块。
2.结焦原因分析2.1分馏塔底与油浆系统结焦导致分馏塔底与油浆系统结焦的因素较多,其中油浆的化学组成、分馏塔底和油浆系统的操作条件(如:分馏塔底液面、温度、催化剂固体含量、工艺管线和换热器管束流速等)是主要原因,此外,还与事故状态下的应急处理方式、分馏塔底结构形式等有关。
为提高装置负荷将部分性质恶劣的原料油大量供给重催,为提高装置轻质油收率,采取油浆部分回炼,直接导致油浆性质恶化,油浆比重长期在 1.05~1.1g/cm3运行;操作上,分馏塔底温度控制过高,油浆泵单台运行,循环量只有350t/h,油浆循环系统流速只有不足1.0m/s;为降低能耗,大量限制反应系统各部蒸汽,低负荷运行时沉降器旋分器偏离允许运行工况,导致油浆固含长期超标,这都加剧了分馏塔底与油浆系统结焦的速度。
催化裂化装置结焦原因分析及对策研究
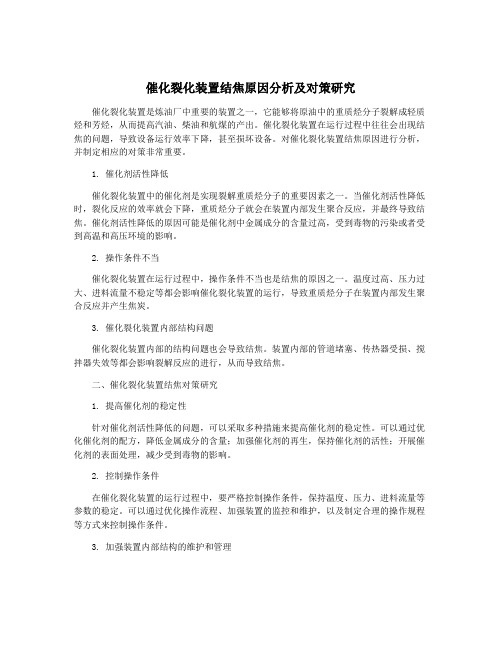
催化裂化装置结焦原因分析及对策研究催化裂化装置是炼油厂中重要的装置之一,它能够将原油中的重质烃分子裂解成轻质烃和芳烃,从而提高汽油、柴油和航煤的产出。
催化裂化装置在运行过程中往往会出现结焦的问题,导致设备运行效率下降,甚至损坏设备。
对催化裂化装置结焦原因进行分析,并制定相应的对策非常重要。
1. 催化剂活性降低催化裂化装置中的催化剂是实现裂解重质烃分子的重要因素之一。
当催化剂活性降低时,裂化反应的效率就会下降,重质烃分子就会在装置内部发生聚合反应,并最终导致结焦。
催化剂活性降低的原因可能是催化剂中金属成分的含量过高,受到毒物的污染或者受到高温和高压环境的影响。
2. 操作条件不当催化裂化装置在运行过程中,操作条件不当也是结焦的原因之一。
温度过高、压力过大、进料流量不稳定等都会影响催化裂化装置的运行,导致重质烃分子在装置内部发生聚合反应并产生焦炭。
3. 催化裂化装置内部结构问题催化裂化装置内部的结构问题也会导致结焦。
装置内部的管道堵塞、传热器受损、搅拌器失效等都会影响裂解反应的进行,从而导致结焦。
二、催化裂化装置结焦对策研究1. 提高催化剂的稳定性针对催化剂活性降低的问题,可以采取多种措施来提高催化剂的稳定性。
可以通过优化催化剂的配方,降低金属成分的含量;加强催化剂的再生,保持催化剂的活性;开展催化剂的表面处理,减少受到毒物的影响。
2. 控制操作条件在催化裂化装置的运行过程中,要严格控制操作条件,保持温度、压力、进料流量等参数的稳定。
可以通过优化操作流程、加强装置的监控和维护,以及制定合理的操作规程等方式来控制操作条件。
3. 加强装置内部结构的维护和管理为了避免装置内部结构问题导致结焦,需要加强装置的维护和管理。
定期清理管道和传热器、加强设备的检修和保养、进行装置内部结构的改进等,都可以有效减少结焦问题的发生。
催化裂化装置结焦是炼油生产中常见的问题,但通过对结焦原因的分析,并采取相应的对策,可以有效降低结焦的发生,保障装置的安全运行和生产效率。
催化裂化装置结焦原因分析及对策研究

催化裂化装置结焦原因分析及对策研究催化裂化装置作为炼油厂重要的催化反应器,在生产中经常发生结焦问题,给生产带来很大的影响,甚至导致设备损坏,因此对催化裂化装置结焦问题进行原因分析,并提出有效的对策十分必要。
1. 催化剂中杂质含量高由于催化剂生产和再生过程中无法完全除去常见的混合杂质和小颗粒杂质,会导致催化剂孔道堵塞,进而造成结焦问题。
2. 反应温度过高在高温条件下,不仅会加速化学反应过程,增加产品产量,同时也会增加碳代谢物生成的速度,导致催化剂的失活,反应产物中的重组物、聚合物和部分不饱和烃最终结焦生成焦炭,造成催化裂化装置的结焦问题。
3. 催化剂失活程度高催化剂的失活程度不仅与反应温度有关,还与催化剂寿命、催化剂产地、催化剂再生情况等因素有关。
催化剂失活对于催化裂化反应来说是十分严重的问题,因为失活催化剂难以发挥催化作用,反应会出现明显的减缓,产生结焦现象。
4. 再生效果不好在催化裂化反应中,催化剂在反应过程中会失活,在达到一定的失活程度后需要经过再生,再生后催化剂重新活化,恢复催化作用。
若再生效果不好,催化剂的失活仍没有得到很好的处理,则催化剂对重复使用无力,即使更换了新催化剂也会出现结焦现象,加剧催化裂化装置的结焦情况。
1. 增加催化剂的选择性和活性增加质量优良的催化剂,能够提高催化反应选择性,增加催化剂活性,减少结焦问题。
提高催化裂化装置的控制温度,尽可能减少炉内温度过高,能有效减少产生结焦现象的几率。
应该通过一定的方法来简化操作程序,降低操纵参数之间的变量,精度控制反应温度,以对避免产生大量结焦反应物及焦炭的生成。
3. 催化剂后续处理简单地减少现有催化剂中的杂质含量是不行的,需要加强催化剂的再生和处理过程,从催化剂再生,酸洗处理和干燥等方面入手,能够有效减少催化剂的失活程度,降低结焦发生的绝对值。
4. 悬浮固定床催化剂技术采用悬浮固定床催化剂技术,能有效提高孔道的通透性,获得更高的选率和活性,有选择性地促进催化裂化反应的进行,降低产生结焦现象的几率。
渣油催化裂化装置反应系统结焦原因分析及对策
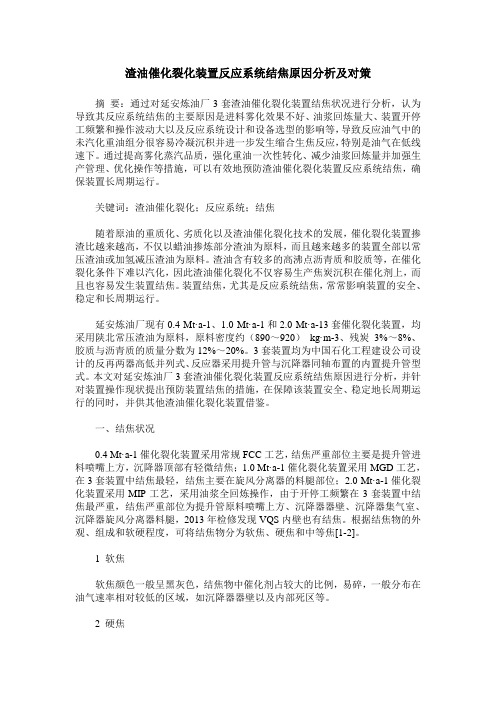
渣油催化裂化装置反应系统结焦原因分析及对策摘要:通过对延安炼油厂3套渣油催化裂化装置结焦状况进行分析,认为导致其反应系统结焦的主要原因是进料雾化效果不好、油浆回炼量大、装置开停工频繁和操作波动大以及反应系统设计和设备选型的影响等,导致反应油气中的未汽化重油组分很容易冷凝沉积并进一步发生缩合生焦反应,特别是油气在低线速下。
通过提高雾化蒸汽品质,强化重油一次性转化、减少油浆回炼量并加强生产管理、优化操作等措施,可以有效地预防渣油催化裂化装置反应系统结焦,确保装置长周期运行。
关键词:渣油催化裂化;反应系统;结焦随着原油的重质化、劣质化以及渣油催化裂化技术的发展,催化裂化装置掺渣比越来越高,不仅以蜡油掺炼部分渣油为原料,而且越来越多的装置全部以常压渣油或加氢减压渣油为原料。
渣油含有较多的高沸点沥青质和胶质等,在催化裂化条件下难以汽化,因此渣油催化裂化不仅容易生产焦炭沉积在催化剂上,而且也容易发生装置结焦。
装置结焦,尤其是反应系统结焦,常常影响装置的安全、稳定和长周期运行。
延安炼油厂现有0.4 Mt·a-1、1.0 Mt·a-1和2.0 Mt·a-13套催化裂化装置,均采用陕北常压渣油为原料,原料密度约(890~920)kg·m-3、残炭3%~8%、胶质与沥青质的质量分数为12%~20%。
3套装置均为中国石化工程建设公司设计的反再两器高低并列式、反应器采用提升管与沉降器同轴布置的内置提升管型式。
本文对延安炼油厂3套渣油催化裂化装置反应系统结焦原因进行分析,并针对装置操作现状提出预防装置结焦的措施,在保障该装置安全、稳定地长周期运行的同时,并供其他渣油催化裂化装置借鉴。
一、结焦状况0.4 Mt·a-1催化裂化装置采用常规FCC工艺,结焦严重部位主要是提升管进料喷嘴上方,沉降器顶部有轻微结焦;1.0 Mt·a-1催化裂化装置采用MGD工艺,在3套装置中结焦最轻,结焦主要在旋风分离器的料腿部位;2.0 Mt·a-1催化裂化装置采用MIP工艺,采用油浆全回炼操作,由于开停工频繁在3套装置中结焦最严重,结焦严重部位为提升管原料喷嘴上方、沉降器器壁、沉降器集气室、沉降器旋风分离器料腿,2013年检修发现VQS内壁也有结焦。
浅谈重油催化裂化装置油浆系统结焦与预防措施

浅谈重油催化裂化装置油浆系统结焦与预防措施针对重油催化裂化装置油浆系统结焦问题的普遍现象,结合本装置油浆系统运行状况,通过对结焦机理进行详细的分析,进一步采取有效的预防措施,很好地减少了结焦,保证了装置的长周期运行。
标签:催化裂化;油浆系统结焦;预防措施1 油浆系统的运行状况近年来,随着原油的重质化和劣质化,重油催化裂化装置成为炼油企业加工原油的重要手段之一,但油浆系统结焦问题一直困扰着正常生产。
近期催化裂化装置原料性质不断变重变差,分馏塔底油浆系统结焦倾向日趋严重。
结合我装置的出现的问题,主要存在以下表现:①油浆泵暖泵线严重堵塞;②油浆蒸汽发生器管程(油浆侧)堵塞造成发汽量严重下降,油浆蒸汽发生器抽芯清洗频繁;③油浆循环量下降,分馏塔底温度出现超温现象。
由于上述问题,直接造成分馏塔各参数偏离正常值,热量不平衡、操作困难,迫使反应处理量降低等严重后果,只能通过切换油浆蒸汽发生器进行抢修。
一方面给装置的平稳安全长周期运行带来了很大的困扰,另一方面由于操作出现异常使得生产不能实现最大的经济效益。
由于在温度升高前两周时间内油浆的固含量并不高,并且油浆循环量一直保持在较高的水平上,这样就基本上可以排除换热器因催化剂沉积造成换热效果下降的可能性。
2 结焦机理分析导致油浆系统结焦的因素是多方面的,根据结焦机理分析和实际操作的经验教训,主要有以下几方面的原因:①油浆的化学组成及性质:石油大学用催化油浆在实验室进行的热结垢实验表明:油浆中的胶质、沥青质是油浆系统结焦的主要因素,其在高温、一定时间下缩合反应增加,最终导致结焦;②分馏塔底温度:经验表明,控制分馏塔低液相温度对于防止油浆系统结焦至关重要,根据结焦机理,油浆中含有大量的稠环芳烃,在340℃以上高温条件下极易发生缩合反应,造成结焦;③停留时间和流速:油浆在管线和设备内的停留时间是影响结焦的另一重要因素,流速降低、停留时间增加给结焦创造了极为便利的条件。
按照规范要求,油浆在管道中的流速不低于1.3m/s,在换热器的管程内应控制在1. 0~1.3m/s,以防油浆在换热过程中,由于温度降低,粘度增大而结焦;④催化剂含量:油浆系统中的固含量超高,极易造成结焦,按照规范要求,固含量应严格控制在6g/L以下,有效地降低油浆固含量,对油浆系统防结焦极其有利。
重油MIP催化裂化反应系统结焦原因与防焦措施探讨

图 2 沉降器内的结焦状况
2. 5 CSC 粗旋内壁
CSC 内壁生成了一层类似于保护膜的硬焦,并有明显的“冲 刷”痕迹。这种焦非常坚硬,一般不易脱落,且达到一定厚度后 冲刷与结焦速度 达 到 平 衡,不 会 继 续 增 长。在 正 常 平 稳 生 产 过 程中不会造成危害,但是由于 CSC 设计的小环蒸汽出口设计在 旋分下料锥形段 内 壁 上,结 焦 使 小 环 蒸 汽 出 口 分 布 板 上 的 孔 几 乎完全堵死,影响了 CSC 的汽提分离效果。要防止小环蒸汽进 入升气管的分布板不被结焦堵塞,一定要注意保证 CSC 小环蒸 汽的畅通及一定的流量。
Key words: MIP; FCC; coking; countermeasures
焦炭作为催化裂 化 反 应 产 物 之 一,在 催 化 剂 上 生 焦 是 必 然 的,正常的生焦 是 两 器 热 平 衡 的 热 量 保 证。但 是 在 反 应 器 壁 等 位置上结焦却会 给 带 装 置 的 平 稳 运 行 带 来 极 大 的 安 全 隐 患,据 报道,每年都有大量的催化装置因结焦问题而非计划停工,给生 产带来极大的经济损失[1]。
2. 6 单旋的料腿
清焦前发现六个单旋的料腿有 4 个几乎结焦堵死,其余 2 个下料孔径也已 缩 得 很 小。从 现 场 割 下 来 的 料 内 的 焦 料 看,主 要成粒状物粘附在内壁。这种情况主要是由于绝大部分的催化 剂与油气在 CSC 粗旋中得到了较高的分离,在单旋中只有少量 的催化剂与大量的油气,因此,下料腿得不到很好的“冲刷”,同 时由于温差与温降,此时温度大约在 480 ~ 510 ℃ 。在此温度 下,烃类以热裂化反应为主,且热裂化反应速度较大。热裂化反 应产生不饱和的 热 裂 化 产 物 二 烯 烃,二 烯 烃 很 易 与 稠 环 芳 烃 聚
催化裂化装置结焦原因分析及对策研究
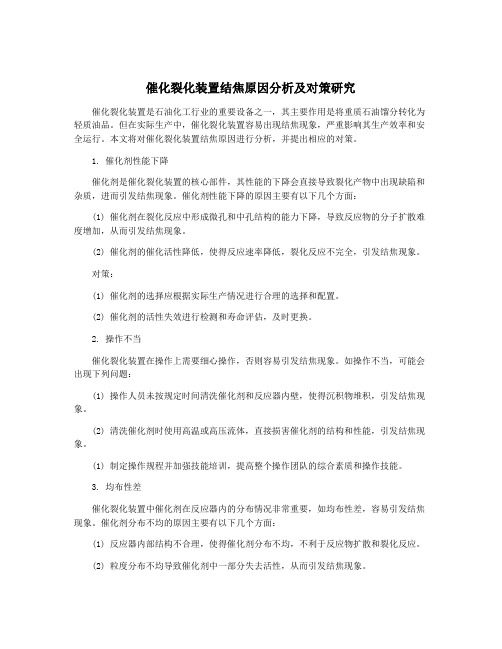
催化裂化装置结焦原因分析及对策研究催化裂化装置是石油化工行业的重要设备之一,其主要作用是将重质石油馏分转化为轻质油品。
但在实际生产中,催化裂化装置容易出现结焦现象,严重影响其生产效率和安全运行。
本文将对催化裂化装置结焦原因进行分析,并提出相应的对策。
1. 催化剂性能下降催化剂是催化裂化装置的核心部件,其性能的下降会直接导致裂化产物中出现缺陷和杂质,进而引发结焦现象。
催化剂性能下降的原因主要有以下几个方面:(1) 催化剂在裂化反应中形成微孔和中孔结构的能力下降,导致反应物的分子扩散难度增加,从而引发结焦现象。
(2) 催化剂的催化活性降低,使得反应速率降低,裂化反应不完全,引发结焦现象。
对策:(1) 催化剂的选择应根据实际生产情况进行合理的选择和配置。
(2) 催化剂的活性失效进行检测和寿命评估,及时更换。
2. 操作不当催化裂化装置在操作上需要细心操作,否则容易引发结焦现象。
如操作不当,可能会出现下列问题:(1) 操作人员未按规定时间清洗催化剂和反应器内壁,使得沉积物堆积,引发结焦现象。
(2) 清洗催化剂时使用高温或高压流体,直接损害催化剂的结构和性能,引发结焦现象。
(1) 制定操作规程并加强技能培训,提高整个操作团队的综合素质和操作技能。
3. 均布性差催化裂化装置中催化剂在反应器内的分布情况非常重要,如均布性差,容易引发结焦现象。
催化剂分布不均的原因主要有以下几个方面:(1) 反应器内部结构不合理,使得催化剂分布不均,不利于反应物扩散和裂化反应。
(2) 粒度分布不均导致催化剂中一部分失去活性,从而引发结焦现象。
(1) 反应器内部结构应尽可能合理,通过模拟进一步优化设计。
(2) 催化剂的粒度分布应做好分类,确保均布性,防止局部失活。
综上所述,针对催化裂化装置结焦问题,应该加强对催化剂的管理和维护,规范操作流程,优化反应器结构,并在操作过程中决不掉以轻心。
通过制定全面的管理和保养计划,以及严格操作规程,消除结焦隐患,提高催化裂化装置生产效率和安全运行水平。
催化裂化装置结焦原因分析及对策研究
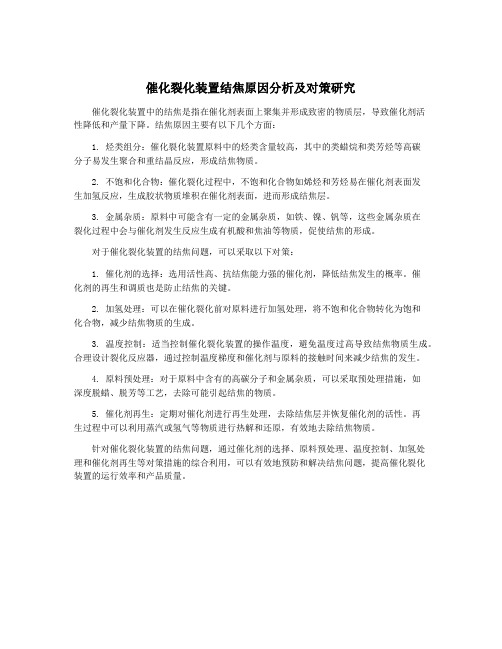
催化裂化装置结焦原因分析及对策研究催化裂化装置中的结焦是指在催化剂表面上聚集并形成致密的物质层,导致催化剂活性降低和产量下降。
结焦原因主要有以下几个方面:1. 烃类组分:催化裂化装置原料中的烃类含量较高,其中的类蜡烷和类芳烃等高碳分子易发生聚合和重结晶反应,形成结焦物质。
2. 不饱和化合物:催化裂化过程中,不饱和化合物如烯烃和芳烃易在催化剂表面发生加氢反应,生成胶状物质堆积在催化剂表面,进而形成结焦层。
3. 金属杂质:原料中可能含有一定的金属杂质,如铁、镍、钒等,这些金属杂质在裂化过程中会与催化剂发生反应生成有机酸和焦油等物质,促使结焦的形成。
对于催化裂化装置的结焦问题,可以采取以下对策:1. 催化剂的选择:选用活性高、抗结焦能力强的催化剂,降低结焦发生的概率。
催化剂的再生和调质也是防止结焦的关键。
2. 加氢处理:可以在催化裂化前对原料进行加氢处理,将不饱和化合物转化为饱和化合物,减少结焦物质的生成。
3. 温度控制:适当控制催化裂化装置的操作温度,避免温度过高导致结焦物质生成。
合理设计裂化反应器,通过控制温度梯度和催化剂与原料的接触时间来减少结焦的发生。
4. 原料预处理:对于原料中含有的高碳分子和金属杂质,可以采取预处理措施,如深度脱蜡、脱芳等工艺,去除可能引起结焦的物质。
5. 催化剂再生:定期对催化剂进行再生处理,去除结焦层并恢复催化剂的活性。
再生过程中可以利用蒸汽或氢气等物质进行热解和还原,有效地去除结焦物质。
针对催化裂化装置的结焦问题,通过催化剂的选择、原料预处理、温度控制、加氢处理和催化剂再生等对策措施的综合利用,可以有效地预防和解决结焦问题,提高催化裂化装置的运行效率和产品质量。
催化裂化装置结焦原因分析及对策研究
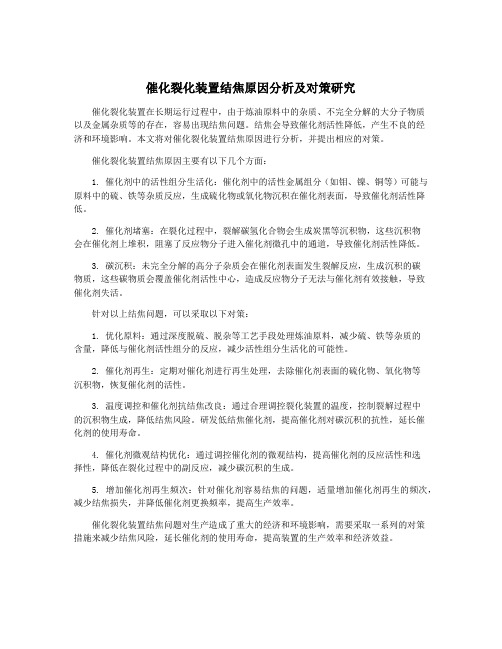
催化裂化装置结焦原因分析及对策研究催化裂化装置在长期运行过程中,由于炼油原料中的杂质、不完全分解的大分子物质以及金属杂质等的存在,容易出现结焦问题。
结焦会导致催化剂活性降低,产生不良的经济和环境影响。
本文将对催化裂化装置结焦原因进行分析,并提出相应的对策。
催化裂化装置结焦原因主要有以下几个方面:1. 催化剂中的活性组分生活化:催化剂中的活性金属组分(如钼、镍、铜等)可能与原料中的硫、铁等杂质反应,生成硫化物或氧化物沉积在催化剂表面,导致催化剂活性降低。
2. 催化剂堵塞:在裂化过程中,裂解碳氢化合物会生成炭黑等沉积物,这些沉积物会在催化剂上堆积,阻塞了反应物分子进入催化剂微孔中的通道,导致催化剂活性降低。
3. 碳沉积:未完全分解的高分子杂质会在催化剂表面发生裂解反应,生成沉积的碳物质,这些碳物质会覆盖催化剂活性中心,造成反应物分子无法与催化剂有效接触,导致催化剂失活。
针对以上结焦问题,可以采取以下对策:1. 优化原料:通过深度脱硫、脱杂等工艺手段处理炼油原料,减少硫、铁等杂质的含量,降低与催化剂活性组分的反应,减少活性组分生活化的可能性。
2. 催化剂再生:定期对催化剂进行再生处理,去除催化剂表面的硫化物、氧化物等沉积物,恢复催化剂的活性。
3. 温度调控和催化剂抗结焦改良:通过合理调控裂化装置的温度,控制裂解过程中的沉积物生成,降低结焦风险。
研发低结焦催化剂,提高催化剂对碳沉积的抗性,延长催化剂的使用寿命。
4. 催化剂微观结构优化:通过调控催化剂的微观结构,提高催化剂的反应活性和选择性,降低在裂化过程中的副反应,减少碳沉积的生成。
5. 增加催化剂再生频次:针对催化剂容易结焦的问题,适量增加催化剂再生的频次,减少结焦损失,并降低催化剂更换频率,提高生产效率。
催化裂化装置结焦问题对生产造成了重大的经济和环境影响,需要采取一系列的对策措施来减少结焦风险,延长催化剂的使用寿命,提高装置的生产效率和经济效益。
重油催化裂化结焦原因及改进措施

重油催化裂化结焦原因及改进措施重油催化裂化结焦,也被称为下游结焦,是指重油在催化裂化过程中的一种现象,它的出现会给裂化过程带来很多不便,使裂化效果受到一定的影响,因此重油催化裂化结焦的定量与质量是催化裂化产品质量的关键因素。
结焦的主要原因是催化剂不均匀的分布。
当反应催化剂在重油催化裂化剂中的分布不均匀时,部分反应区域的催化剂不足,从而导致反应产物积累,进而形成结焦物。
此外,反应条件不合理也是造成结焦的重要原因,包括反应温度过高或者反应温度不稳定,反应压力过高、反应压力不稳定,反应液体的层数、反应时间过长等等。
另外,重油催化裂化结焦还可能是由于原料重油中夹带的杂质或者水分、油类离子过高等原因造成的。
在重油中,各种杂质如烃、氧化物、含碳水等不易被催化裂化,如果温度和压力条件不合适,就可能形成结焦物。
另外,当重油中含碳水离子过高时,它们会结合形成结焦物,也会对裂化过程造成影响。
二、改进措施(1)优化催化剂的使用。
要想有效的解决重油催化裂化结焦的问题,首先要保证催化剂的分布均匀,可以采用多种方法,如加入悬浮剂等,以改善催化剂的可利用性,使催化剂均匀地分布在反应液中,从而提高反应效率。
(2)优化反应条件。
反应条件的优化是降低结焦率的重要措施。
反应温度和反应压力不能过高,应当根据重油类型和反应条件来选择合适的反应温度和反应压力,保证反应稳定。
另外,反应时间也不能过长,否则反应产物容易积累,形成结焦物。
(3)改善原料重油质量。
原料重油中存在的杂质和水分都会影响重油催化裂化的效果,要想获得较好的催化裂化效果,首先应该提高原料重油的质量,如选择质量较好的原料重油,做好原料重油的净化和精制等,以提高催化裂化效果。
三、结论重油催化裂化结焦是指重油在催化裂化过程中出现的现象,它的出现会给裂化过程带来一定的影响,常见的原因有:催化剂分布不均匀、反应条件不合理、原料重油中夹带的杂质或者水分、油类离子过高等。
改善重油催化裂化结焦的措施有:优化催化剂的使用、优化反应条件、改善原料重油质量等。
油浆系统结焦原因及控制对策
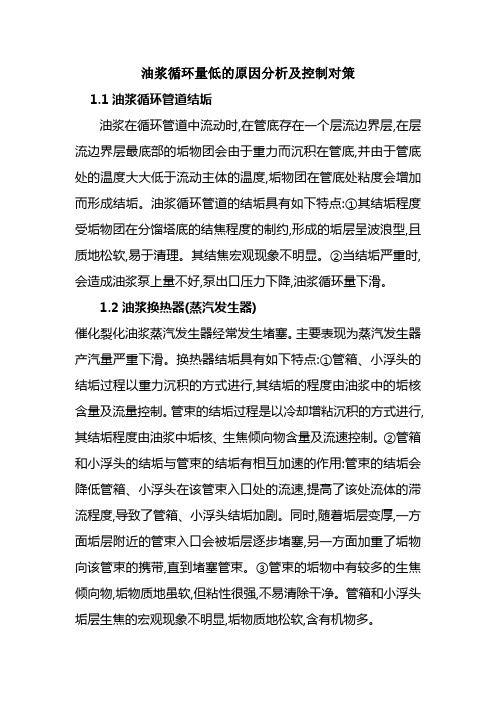
油浆循环量低的原因分析及控制对策1.1油浆循环管道结垢油浆在循环管道中流动时,在管底存在一个层流边界层,在层流边界层最底部的垢物团会由于重力而沉积在管底,并由于管底处的温度大大低于流动主体的温度,垢物团在管底处粘度会增加而形成结垢。
油浆循环管道的结垢具有如下特点:①其结垢程度受垢物团在分馏塔底的结焦程度的制约,形成的垢层呈波浪型,且质地松软,易于清理。
其结焦宏观现象不明显。
②当结垢严重时,会造成油浆泵上量不好,泵出口压力下降,油浆循环量下滑。
1.2油浆换热器(蒸汽发生器)催化裂化油浆蒸汽发生器经常发生堵塞。
主要表现为蒸汽发生器产汽量严重下滑。
换热器结垢具有如下特点:①管箱、小浮头的结垢过程以重力沉积的方式进行,其结垢的程度由油浆中的垢核含量及流量控制。
管束的结垢过程是以冷却增粘沉积的方式进行,其结垢程度由油浆中垢核、生焦倾向物含量及流速控制。
②管箱和小浮头的结垢与管束的结垢有相互加速的作用:管束的结垢会降低管箱、小浮头在该管束入口处的流速,提高了该处流体的滞流程度,导致了管箱、小浮头结垢加剧。
同时,随着垢层变厚,一方面垢层附近的管束入口会被垢层逐步堵塞,另一方面加重了垢物向该管束的携带,直到堵塞管束。
③管束的垢物中有较多的生焦倾向物,垢物质地虽软,但粘性很强,不易清除干净。
管箱和小浮头垢层生焦的宏观现象不明显,垢物质地松软,含有机物多。
1.3 分馏塔底油浆在分馏系统的流动中,随着垢物团的增长,在重力和粘性力的作用下,垢物团会落入液相慢流区并沉积在器壁上。
分馏塔塔径较大,塔底维持稳定的液面,因此油浆在塔底具有最长的停留时间。
并且油浆在塔底流动的线速并不均一,在塔的底部存在缓流区和死区,在塔壁存在滞流边界层,这些为垢物团的重力沉积创造了必要条件。
循环油浆在脱过热段与反应油气(有来自大油气管道的碎焦)进行传热和洗涤的结果造成在塔底油浆具有全塔最高的液相温度以及最高的垢核浓度。
塔底油浆主体温度高,垢物团上的生焦倾向物的热聚反应就会加剧,循环油浆在塔底液面高,停留时间延长,也会发生更多的热缩合反应。
- 1、下载文档前请自行甄别文档内容的完整性,平台不提供额外的编辑、内容补充、找答案等附加服务。
- 2、"仅部分预览"的文档,不可在线预览部分如存在完整性等问题,可反馈申请退款(可完整预览的文档不适用该条件!)。
- 3、如文档侵犯您的权益,请联系客服反馈,我们会尽快为您处理(人工客服工作时间:9:00-18:30)。
汽油
( %) 481 66 48122
液化气 总液收率
( %) 191 42 191 88
( %) 851 60 851 88
备注 :反应温度 、处理量等保持不变 ;数据采用平均值 。
由表 1 可以看出 ,塔底温度的不同对产品收率无 明显影响 。
41 3 控制停留时间
蒸汽量 (t/ h)
使用前
275 31 6
使用后 241 10
从表 2 可以看出 ,当油浆注入阻垢剂后 ,换热效 果随之明显好转 ,油浆返塔温度降低 ,蒸汽量增加 。
通过采取以上措施 ,保证了装置的长周期平稳 运行 ,降低了工人的劳动强度 。避免了因油浆系统 堵塞而导致的停工抢修事件的发生 。
催化油浆结焦 、结垢是越来越普遍的现象 ,也是 一个原因较复杂的问题 。各炼厂应根据自己的实际 情况 ,分析原因 ,找出适合自身的工艺操作条件 ,以 取得较好的阻垢效果 。
41 5 添加阻垢剂
选用合适的油浆阻垢剂 ,从装置投用起连续注 入 ,防止油浆中不溶物附着在换热器的管壁 。
我厂使用的阻垢剂型号是 SF22 ,使用的效果可 以从表 2 中看出 ,表中的数据为当催化裂化油浆系 统发生结垢时 ,加入阻垢剂 ,油浆系统部分条件的变 化。
表 2 阻垢剂的使用效果
项目 油浆返塔温度 ( ℃)
多环芳烃 、胶质 、沥青质在高温下容易脱氢产生 芳烃自由基 ,后者相互结合形成分子量更大的缩合
物 ,直至焦炭 。油浆中各类不饱和烃在高温下 ,由氧 和金属引发催化作用 ,通过自由基链反应而产生高 分子聚合物 。随着聚合物和缩合物的分子量不断增 大 ,在介质中的溶解度逐渐减小 ,析出后粘附在设备 表面 ,当遇到有催化剂聚集成的颗粒 ,这些高分子的 聚合物可起到粘合剂的作用 ,使颗粒的聚集大大加 快 ,已经粘附在表面的聚合物也能起到捕获剂的作 用 ,加快颗粒的沉积 。
在分馏塔底保持较短的停留时间 ,尽量将流量 保持在油浆泵的上限 ,维持较低的分馏塔液面 ,以避 免油浆在高温情况下结焦 。分馏塔底停留时间控制 在适宜范围内 (3 —5min) 。
41 4 提高流速
为使油浆循环系统的管道和设备不结焦 ,油浆 在管道中的流速应不低于 11 5 —21 0m/ s ,在换热器 的管程内宜控制在 11 2 —21 0m/ s 。换热器的副线启 用应当慎重 ,确保油浆换热器内流速不低于 11 2 m/ s ,避免油浆在换热过程中 ,由于油温降低 ,粘度增大 而结垢 。
我们对装置采用如下措施以防止系统结焦 : ⑴油浆回炼量维持合适的量 ,不宜太低 ; ⑵油浆连续外甩 ,占日处理量的 2 % ; ⑶每班分析一次固含量 ,当固含量大于 01 6 % 时 ,适当加大外甩量 ; ⑷定 期 测 油 浆 密 度 , 控 制 油 浆 密 度 不 大 于 11 0g/ cm3 。
31 2 分馏塔底温度
分馏塔底温度是导致油浆系统结焦的直接原 因 。随着温度的升高 ,轻馏分逐渐蒸发 ,油浆浓缩 , 生焦性能增强 。同时 ,油浆中的烯烃 、多环芳烃产生 缩合反应 。当温度升高到一定值时 ,缩合反应速度 会变得很快 。
31 3 油浆的停留时间
当油浆在某一高温下停留时间足够长时 ,油浆 中将有焦炭生成 。
46
四川化工 第 8 卷 2005 年第 2 期
31 4 流速过低
当油浆在管道中的流速过低时 ,容易使缩合物 沉积在管道表面而富集 。聚集的缩合物进一步反 应 ,生成“软焦”。
4 防止油浆系统结焦的措施
41 1 降低固含量
油浆中的固体催化剂对油浆系统结焦影响很 大 。催化剂沉积在分馏塔底 ,由于催化剂的吸附作 用而减少了油浆液滴积聚的核心 ,而油浆中催化剂 固体颗粒的碰撞会加快其沉降速度 ,使催化剂颗粒 大量沉积于分馏塔底 ,在合适的条件下形成结焦 。 油浆的相对密度反映油浆的性质 ,相对密度大 ,说明 含有更多的高沸点 、大分子成份 。结焦潜质多 ,容易 造成油浆系统的结焦 ,同时也增加了回炼油浆在提 升管中的结焦 。
第 2 期 催化裂化油浆系统结焦原因及解决措施
45
催化裂化油浆系统结焦原因及解决措施
沙胜利 (河南濮阳县中原油田石油化工总厂 ,濮阳 ,457061)
摘 要 讨论了催化裂化油浆系统的结焦机理及原因 ,结合我厂实际 ,讨论了解决的方法和取得的效 果。
关键词 :催化裂化 油浆 结焦 阻垢剂
41 2 采用较低的塔底温度
降低循环油浆返塔温度 ,加大油浆返塔下部入
口量 。用急冷油浆急冷 ,既可加强对塔底的冲涮作
用 ,防止催化剂堆积在分馏塔底的缓流区而引起结
焦 ,又可使塔底油浆快速降温 ,防止油浆组分因高温
聚合生焦 。我装置是 500kt/ a 催化裂化装置 ( RFC2
CU) ,在实际操作中我装置分馏塔底的温度控制在
1 前言
催化裂化油浆系统结焦问题是普遍存在的问 题 。分馏塔底和油浆系统的结焦 、结垢会造成系统 压力降的增加 、油浆循环量的降低 ,造成能耗增加 、 取热效率低 、装置的处理能力降低 。严重时会造成 油浆系统循环中断 ,迫使装置停工清垢 。我厂油浆 系统就多次发生堵塞造成停工 。1998 年 3 月 ,油浆 系统严重堵塞 ,致使油浆上下返塔堵塞 ,装置被迫停 工抢修 。2000 年 5 月 ,由于沉降器催化剂流损 ,管 线及换热器 ,甚至油浆泵堵死 ,装置停工检修 。2002 年 5 月 ,由于油浆换热器严重堵塞 ,又一次被迫停 工 。由此可见 ,催化裂化装置油浆系统结焦问题已 成为影响装置“安 、稳 、长 、满 、优”生产运行的一大障 碍 。成为催化装置领导 、技术人员关心的问题 。通 过借鉴其他厂的经验和采用一些新技术 、新措施 ,我 厂探索出一套减少油浆系统结焦的系列措施 。这些 应用于生产实践后 ,取的了很好的效果 。
3 油浆结垢原因分析
31 1 油浆性质
油浆性质变差是油浆系统结焦的重要原因之 一 。例如 ,油浆粘度增大将影响其流动性能 。固体 含量增大会使结焦性能增强 。油浆中含有大量的多 环芳烃和一定量的高分子烯烃 ,在高温下极易发生 缩合反应 。随着催化裂化掺炼重油比的增加 ,油浆 中的多环芳烃含量增加 ,相对密度增大 ,油浆因缩合 而生焦的能力增强 。
330 ℃以下 ,效果非常好 。
有资料显示 ,降低塔底温度则可能导致部分轻
组分溶解在塔底油浆里 ,从而影响收率 。为研究塔
底温度与产品收率的关系 ,我们作了对比实验 ,结果
见表 1 。
表 1 塔底温度与产品收率的对比实验结果
时间
塔底温度 ( ℃)
03 年 3 月 10 日 345
03 年 3 月 14 日 318
2 油浆系统结垢的机理
尽管不同油浆的组成差别较大 ,但油浆中胶质 和重质烃含量普遍都高 ,这些成分在高温下都极易 生焦成垢 。
油浆结垢物由有机物和无机物组成 。有机物主 要由各类烃和缩聚物组成 。烃类有链烷烃 、单环芳 烃和多环芳烃 ; 缩聚物主要由沥青质 、高分子聚合 物 、芳烃聚合物和焦炭组成 。结垢物中的无机物主 要是催化剂粉末 。