汽车车身饰件DFMEA-转向管柱护罩总成
汽车底盘DFMEA-转向器带横拉杆总成

小
格,规定联结力矩
风
R P N
险 顺 序
建议措 施
数
20 质量管控
20 质量管控 20 质量管控
编制人 编制日期 修订日期
职责及目 标完成日
期
赵红秀
赵红秀
赵红秀
FMEA编 号第: 1
页
共1页
措施执行后的结果
采取的措施 及完成日期
严 重 度 S
频 度 O
探 测 度 D
风险 顺序
数 RPN
10
☆
齿轮轴杆部断 裂
转向无 异响
转向异响
造成顾客行车时紧张
联结
转向无 干涉
与汽车其 它部分发
生干涉
力传递不顺畅,顾客手 感不舒适,整车回正能
力差
编制:
潜在失效模式及后果分析(DFMEA)
设计职责(部门)
底盘技术部
关键日期 核心小组
严 重 分 潜在失效原因 度 类 / 机理 S
现行设计控制
控制预防
频 度 控制探测 O
风
探 测 度
系统 子系统
部件 年型/车型 项目
转向系统 /
转向器带横拉杆总成
要求
潜在失 效模式
失效潜在影响/后果
功能
车辆突然无法转向,危 及人身安全
转向功能
转向功 能良好
完全失去 转向功能
车辆突然无法转向,危 及人身安全
潜在失效模式及后果分析(DFMEA)设计职责(ຫໍສະໝຸດ 门)底盘技术部关键日期
核心小组
严 重 分 潜在失效原因 度 类 / 机理 S
R P N
险 顺 序
建议措 施
D数
拉杆松旷
规定内球节的轴向 弹性位移
DFMEA-转向器总成
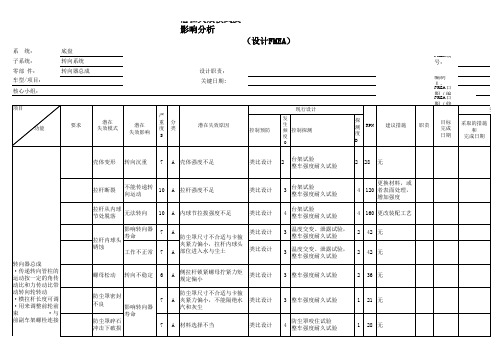
更换材料,或 4 120 者表面处理, 增加强度 4 160 更改装配工艺 2 2 42 无 42 无
拉杆从内球 无法转向 节处脱落 影响转向器 寿命 工作不正常
10 7 7
A 内球节拉拔强度不足 A
类比设计 类比设计 类比设计
4 3 3
拉杆内球头 锈蚀 转向器总成 ·传递转向管柱的 运动按一定的角传 动比和力传动比带 动转向轮转动 ·横拉杆长度可调 ·用来调整前轮前 束 ·与 前副车架螺栓连接
实施结 探 测 度 D RPN 建议措施 职责 目标 完成 日期 采取的措施 和 完成日期
功能
控制预防
壳体变形
转向沉重
7
A 壳体强度不足
类比设计
2
台架试验 整车强度耐久试验
2
28
无
拉杆断裂
不能传递转 向运动
10
A 拉杆强度不足
类比设计
3
台架试验 整车强度耐久试验 台架试验 整车强度耐久试验 温度交变、泄露试验, 整车强度耐久试验 温度交变、泄露试验, 整车强度耐久试验
控制预防
防尘罩咬粘 防尘罩寿命 降低影响转 防尘罩扭曲 向器寿命 变形 常温下破裂 不能隔绝水 低温环境破 汽和灰尘进 入转向器内 裂或变形 部 高温环境破 裂或变形
7 7 7
A 材料选择不当 A 材料选择不当 A 材料断裂强度设定过小
类比设计 类比设计 类比设计
5 6 3
钢球冲击试验 整车强度耐久试验 扭转试验 整车强度耐久试验 拉裂强度试验 强度整车耐久试验 低温密封性试验 整车强度耐久试验 耐热性试验 整车强度耐久试验
潜在失效模式及影响分析 (设计FMEA)
系 统: 子系统: 零部 件: 车型/项目: 核心小组:
新员工培训DFMEA介绍
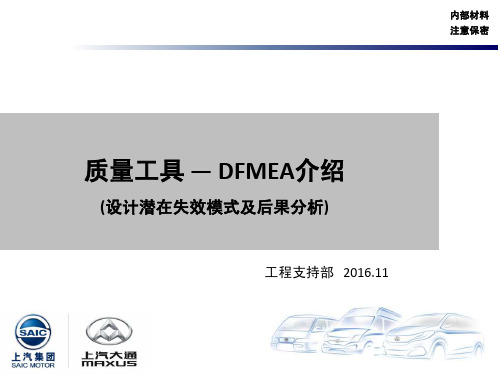
识别与分析零件相关的周边系统。 周围的系统与零件功能相关,后续作为影响因素进行分析。
方法和资源: 方块图 Block Diagram 参数图(P-图) Parameter Diagram 关系矩阵分析 BOM清单 接口图、示意图等
内部材料 注意保密
2014-5
26
二. DFMEA策划及准备
了解这些顾客,有助于更加充分地定义功能范围。
内部材料 注意保密
2014-5
18
一. FMEA发展和介绍
DFMEA在APQP中的角色
设计相关:PDT协同
历史信息 失效记录
设计过程:DRE/供应商负责
价值工程 价值分析
DFMEA
内部材料 注意保密
基于可制造性/ 装配性/维修性
的设计
设计验证计划 ADV
功能
潜在失效模式
严 级 潜在失效 频
潜在失效后果 重 别 起因/机理 度
度
现行设计控制
预防
探测
风
探险
测顺
度序
数
建议措施
措施效果
责任和目标 完成日期
采取的
严 重
频
探 测
R P
措施 度 度 度 N
1
2
3 4 567
8
9
2014-5
10
8
一. FMEA发展和介绍 DFMEA简介 — 5W
What 什么是DFMEA?
内部材料 注意保密
质量工具 — DFMEA介绍
(设计潜在失效模式及后果分析)
工程支持部 2016.11
第一部分:FMEA发展和介绍 第二部分:DFMEA策划及准备 第三部分:DFMEA分析和实施
汽车底盘DFMEA-转向管柱带助力转向总成
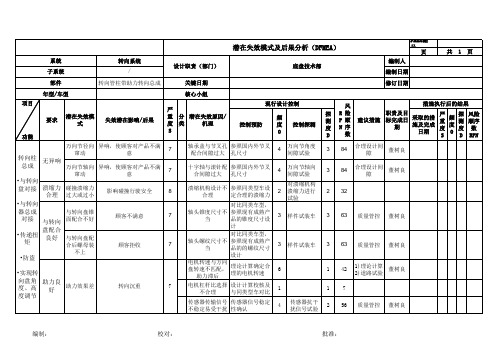
56 质量管控 董树良
编制:
校对:
批准:
理论计算确定合 理的电机转速
6
1
电机杠杆比选择 设计计算校核及
不合理
与同类型车对比
1
1
传感器传输信号 传感器信号稳定 不稳定易受干扰 性确认
4
传感器抗干 扰信号试验
2
84
合理设计间 隙
董树良
84
合理设计间 隙
董树良
32
63 质量管控 董树良
63 质量管控 董树良
42
1)理论计算 2)道路试验
董树良
7
影响碰撞行驶安全
8
•与转向
器总成
与转向盘锥
对接 与转向 面配合不好
顾客不满意
7
•传递扭 矩
盘配合 良好
与转向盘配 合后螺母装
顾客拒收
7
不上 •防盗
•实现转
向盘角 度、高
助力良 好
助力效果差
转向沉重
7
度调节
轴承盖与节叉孔 参照国内外节叉 配合间隙过大 孔尺寸
4
万向节角度 间隙试验
3
十字轴与滚针配 参照国内外节叉 合间隙过大 孔尺寸
风
措施执行后的结果
探 测 度 D
R险 P顺 N序
数
建议措施
职责及目 标完成日 采取的措
期 施及完成 日期
严 重 度 S
频 度 O
探 测 度 D
风险 顺序
数 RPN
万向节径向 异响,使顾客对产品不满
转向柱 无异响
窜动
意
7
总成
万向节轴向 异响,使顾客对产品不满
窜动
意
7
•与转向
DFMEA-底盘-液压转向系各零部件

系统:子系统:零部件名称:过程责任:零部件号:关键日期:核心小组:劳,操纵不舒服震动大²传递转向力²改变力矩²转向回正²防止对驾驶员的伤害转向系统总成潜在失效(车型/车辆类型:底盘转向系统系统:子系统:零部件名称:过程责任:零部件号:关键日期:²控制车辆方车型/车辆类型:底盘转向系统喇叭盖潜在失效(核心小组:系统:子系统:零部件名称:过程责任:零部件号:关键日期:核心小组:影响顾客生命安全转向盘总成潜在失效(车型/车辆类型:底盘转向系统系统:子系统:零部件名称:过程责任:零部件号:关键日期:核心小组:²作为组合开关、方向盘和转向联轴节的支撑²提供方向盘车型/车辆类型:底盘转向系统转向管柱带转向传动轴总成潜在失效(系统:子系统:零部件名称:过程责任:零部件号:关键日期:核心小组:转向系统液压助力转向器总成潜在失效(车型/车辆类型:底盘求²橡胶连接件限位角5.5°±2°²传递扭矩和系统:子系统:零部件名称:过程责任:零部件号:关键日期:核心小组:(车型/车辆类型:底盘转向系统转向油泵总成潜在失效²满足左右转向感觉一致转向油泵总成M03A3407100²根据发动机转速提供转向液压助力²耐久²可靠²可装配性和可维修性²工作噪音小系统:子系统:零部件名称:过程责任:零部件号:关键日期:核心小组:²可靠的输送油液保证压力转向系统高压油管总成潜在失效(车型/车辆类型:底盘系统:子系统:零部件名称:过程责任:零部件号:关键日期:核心小组:(车型/车辆类型:底盘转向系统低压油管总成潜在失效潜在失效系统:子系统:零部件名称:过程责任:零部件号:关键日期:核心小组:转向系统冷却油管总成(车型/车辆类型:底盘系统:子系统:零部件名称:过程责任:零部件号:关键日期:核心小组:常工作²储存油液,向油泵及系统供油(车型/车辆类型:底盘转向系统转向油罐总成潜在失效系统:子系统:零部件名称:过程责任:零部件号:关键日期:核心小组:转向系统防尘罩潜在失效(车型/车辆类型:底盘在失效模式及后果分析(设计FMEA)FMEA编号:编制人:修订人:第 1 页共 11 页在失效模式及后果分析(设计FMEA)FMEA编号:编制人:修订人:第 2 页共 11 页在失效模式及后果分析(设计FMEA)FMEA编号:编制人:修订人:第 3 页共 11 页在失效模式及后果分析(设计FMEA)FMEA编号:编制人:修订人:第 4 页共 11 页FMEA编号:编制人:修订人:目标完成日期度D探测预防第 5 页共 11 页在失效模式及后果分析(设计FMEA)探在失效模式及后果分析(设计FMEA)FMEA编号:编制人:修订人:第 6 页共 11 页在失效模式及后果分析(设计FMEA)FMEA编号:编制人:修订人:第 7 页共 11 页在失效模式及后果分析(设计FMEA)FMEA编号:编制人:修订人:第 8 页共 11 页在失效模式及后果分析(设计FMEA)FMEA编号:编制人:修订人:第 9 页共 11 页在失效模式及后果分析(设计FMEA)FMEA编号:编制人:修订人:第 10 页共 11 页FMEA编号:编制人:修订人:目标完成日期度D 探测预防第 11 页共 11 页在失效模式及后果分析(设计FMEA)探共 11 页共 11 页共 11 页共 11 页共 11 页共 11 页共 11 页共 11 页共 11 页共 11 页共 11 页。
系统总成DFMEA分析范例

系统:H06后视镜总成设计责任:子系统:关键日期:部件:车辆项目:团队:镜面曲率半径选择错误由于车门数据的改变,造成主机厂提供的线框数据中镜面位置不正确后视镜应满足GB15084-2013规定的反射率(≥80%)镜面太暗驾驶员看后视野时不清晰7●镜面反射率选择错误后视镜应满足GB15084-2013规定的(平均SR误差≤12.5%)镜面变形驾驶员看后视野时感觉不舒服7●镜面烤弯变形要求无未预期的风噪风噪过大或难听用户感觉刺耳不舒适3外形造型不好或镜壳与背盖间隙过大后视镜应耐腐蚀后视镜内金属件锈蚀后视镜内部零件外观不良2材料选择或表面处理不当在高温作用下,后视镜零部件(如塑料件、电机等)产生变形后视镜功能减弱或丧失(如镜面移位、不可调节/折叠、抖动等)6材料选择不合理在低温作用下,后视镜零部件(如塑料件、镜面等)产生开裂、变形等后视镜功能减弱或丧失(如镜面松动、不可调节/折叠、抖动等)6材料选择不合理部件/功能后视镜应满足GB15084-2013规定的视野视野范围小于国标GB15084-2013规定整车视野不合格或视野有盲区,不能上国家目录8●设计 FMEA H06后视镜应耐高温、低温和高湿度环境潜在失效模式失效的潜在影响严重度分级失效的潜在原因/机制在高温高湿度环境下,后视镜零部件(如塑料件、镜面等)产生开裂、变形等后视镜功能减弱或丧失(如镜面松动、不可调节/折叠、抖动等)6材料选择不合理后视镜应能耐冷热冲击在高温低温交变冲击的环境下,后视镜零部件(如塑料件、镜面等)产生开裂、变形等后视镜功能减弱或丧失(如镜面松动、不可调节/折叠、抖动等)6材料选择不合理镜杆应与镜臂牢固连接镜杆和镜臂配合和设计数据不符。
1:后视野模糊 。
2:后视镜镜壳与背盖,主镜和广角镜,镜头与镜臂之间的配合间隙不能满足要求。
6镜杆和镜臂配合设计不合理后视镜镜头能可靠折叠且折叠力适中镜头折叠力过大或过小折叠力过大:有外力撞击时不易折叠;折叠力过小:行车时易抖动7●下支座定位柱弹簧工作压力过大或过小对电调总成:电调镜面的手动调节力过小行车时镜头易抖动而使后视野模糊5电机选型不当,其承载力过小镜面托板分总成拔脱力过小或感觉到横向空程镜面易脱落或抖动,无镜面或后视野模糊7托板与电机卡簧配合不合理镜头应能经受反复折叠而保持折叠功能镜头反复折叠后有空程或折叠力明显下降,行车时镜头易抖动后视镜使用一段时间后,行车时镜头易抖动视野模糊4下镜臂的凹槽与支座上的凸台直接接触,在镜头折叠时被磨损电机工作及卡止时噪声可接受电调后视镜调节噪声过大用户感觉刺耳不舒适3调节电机选型不当6数模转换误差导致数据设计失误6车身冲压件存在反弹主机厂对后视镜装配的外观效果不满意镜面能够稳定连接在镜壳中,并能进行各方向的最小8度的调节支座分总成与车身安装后外观效果应良好后视镜安装在车身上后,上下支座与车身存在断差、间隙、错位等温、低温和高湿度环境6●支座安装尺寸错误电机与基板/广角镜壳装配完好电机与基板/广角镜壳配合安装孔径不正确电机无法安装6电机安装孔径比基板/广角镜壳安装孔大基板和广角镜壳准确定位广角镜壳与镜杆相对位置偏差广角镜头与其他相配合的零件配合间隙失控6广角镜头和镜杆没有自动找正结构基板和镜杆准确定位基板与镜杆相对位置偏差主镜头与其他相配合的零件配合间隙失控6基板和镜杆没有自动找正结构镜壳与托板在调节到极限角度时有干涉电机选择不合理为镜面提供电动调节功能使用一定时间后电机调节功能失效驾驶员无法利用镜面调节开关控制镜面4电机选择不合理配的外观效果不满意主镜面调节角度在各个方向均达到8度以上主镜面分总成调节角度不够有的驾驶员看不到符合法规要求的视野5车身安装后外观效果应良好上后,上下支座与车身存在断差、间隙、错位等FMEA 号:准备人员:FMEA 日期:根据GB15084-2013规定选择曲率半径:1.主镜面/SR1200+300。
汽车车身饰件DFMEA-转向盘总成

配合不良,影 响顾客使用舒 适度,顾客不
满意
6
☆
骨架在模具中变形, 造成装饰盖板、按钮 定位偏差,从而引起
面差
利用本体模具成型形 状稳定性来定位改型 样件,本体与装饰盖 板零间隙配合,装饰 盖板略高于本体,再
2
参照M43转向盘尺寸偏 差检测报告检E测Q153转向
或过小
参考华菱H08转向盘经 验选择ZL102参照标准 QC-303,选择 20#冷
拉型钢参照标准 CB\T3078-94,辐条与 外网焊接保持1mm间隙
2
1.CAE分析;制作样件 验证,转向盘弯曲、 扭转疲劳强度试验
4
72
审核/日期:
批准/日期:
CAE分析
FMEA编号: 共页
第页
措施执行后的结果
职责及目标 完成日期
无干涉 耐溶剂性
强度
时钟弹簧插接器 影响顾客使用
安装困难与安装 舒适度,顾客
孔干涉
不满意
6
☆
时钟弹簧插接器安装 孔过小,尺寸配合间
隙过小
依照顾客提供时钟弹 簧插接器样件,设计
安装孔尺寸长 39.3mm,宽31.1mm
2
运动校核
2 24
转向盘使用一段 时间后,表面发 粘、溶胀、开裂
等
影响顾客使用 舒适度,顾客
转动灵活 性
装配牢靠,无松 动异响
装车转动过程中 有异响、晃动
顾客使用舒适 性下降,顾客
感觉不舒服
6
☆
转向盘下沉与时钟弹 盘,锥度规与锥面接 簧干涉轮毂接触面积 触面积需在50%以上, 小,转动过程中产生 花键借鉴EQ153转向盘
4
对花键与锥度一样的 转向盘进行花键、锥
转向管柱总成百科

转向管柱总成百科汽车转向管柱总成,包括上柱管、下柱管、上转向轴、下转向轴、上安装支架和下安装支架,下柱管的上端部套接在上柱管的下端部内,上转向轴设置在上柱管内,下转向轴设置在下柱管内,上转向轴和下转向轴通过花键连接,上安装支架与上柱管的中部焊接在一起,下安装支架与下柱管焊接在一起,下转向轴为两端直径大,中部直径小的柱状结构,在下转向轴中部直径小的轴端沿轴向和周向焊接若干金属弹片,弹片的周向高出下转向轴两端大直径部分,下转向轴两端大直径部分均设置有花键槽。
不仅转向管柱吸能效果好,而且溃缩后还能继续转向,安装支架还能在碰撞后够吸收部分能量。
目录• 1. 转向管柱总成分类• 2. 汽车转向管柱总成组成• 3. 转向管柱总成异响1转向管柱总成分类汽车转向管柱及传动轴总成是安装在方向盘与转向器之间的连接部件。
主要用于控制汽车行进方向、传递扭矩、吸收汽车撞击时的能量。
为满足驾驶者舒适度要求,转向管柱上下及前后方向可以调节,与点火锁安装连接后,可以实现汽车的防盗锁车功能。
根据产品工作原理可分为:机械式和电动助力式转向管柱两种。
按照结构型式可分为:普通式、溃缩吸能式、机械可调倾角式及电动可调升降式。
2汽车转向管柱总成组成汽车转向系统分为两大类:机械转向系统和动力转向系统。
其中基本的机械转向系以驾驶员的体力作为转向能源,其中所有传力件都是机械的。
机械转向系由转向操纵机构、转向器和转向传动机构三大部分组成。
3转向管柱总成异响转向泵异响主要原因可能是由于整个转向系统内部清洁度差及泵在过度疲劳的情况下运转及系统之间的匹配等问题。
在排除故障前,应首先检查整个转向系统的清洁度。
故障原因分析:(1)油杯油面过低,系统有漏油或动力转向系统中有空气。
(2)油杯内的滤芯脏造成转向泵吸油不良。
(3)转向系统内部清洁度差,造成内部零件过度磨损。
(4)油管在有堵塞、弯折或产生共振及进出油不畅现象。
(5)转向系统因过度负荷运转,造成转向泵内部的定、转子过度磨损,从而造成泵内的油液不规则运动从而产生异响声。
汽车车身饰件DFMEA-开闭件钣金

设计者
2
36
根据CAE分析报 告进行优化
设计者
2
48
根据CAE分析报 告进行优化
设计者
2
28
根据校核报告进 行优化
设计者
1
28
根据校核报告进 行优化
设计者
2017/9/20
2017/9/20
2017/9/20 2017/9/20 2017/9/20
涂胶工艺
注塑成型 工艺
冲压成型 工艺性
漏液孔
符合人机 工程
致
车门密封
达不到要 防水防尘效果 求,漏风 差,顾客抱怨
6
☆
门下垂导致上密封间 隙过大
、漏雨
CAE分析 设计校核 CAE分析
2
强检试验 (GB15743)
1
18
根据CAE结果进 行设计优化
设计者
2017/9/20
2
淋雨试验
2
24
根据校核报告进 行优化
设计者
2017/9/20
4
强化试验
2
48
根据CAE报告进 行优化
参考成熟车型和满足 GB15743-1995
2
侧撞试验
1 20
设计者 2017/9/20
外板表面 外板共振异响,
刚性差
易变形
6
☆
外板刚度不足;缺少 对外板的支撑
CAE分析
2
刚度实验
2
24
根据CAE结果进 行设计优化
设计者
2017/9/20
内外板过 软
影响安全性
9
★
结构、材料不能达 到要求
侧门到侧围及侧围门 6 ☆ 洞止口密封间隙不一
汽车车身饰件DFMEA全套资料
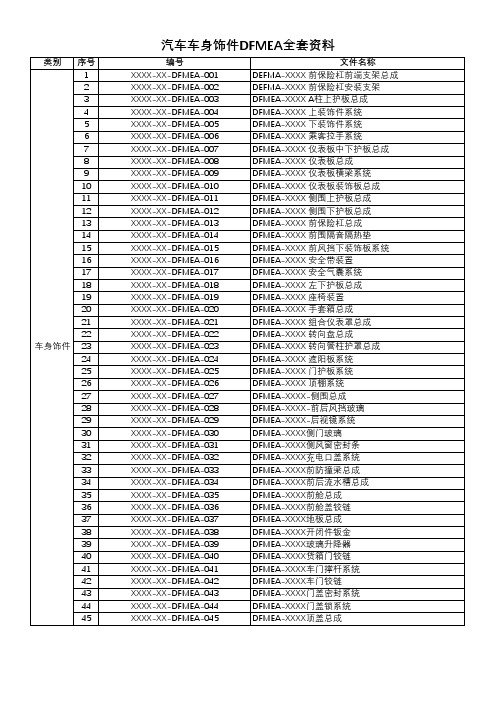
类别序号编号文件名称1XXXX-XX-DFMEA-001DEFMA-XXXX 前保险杠前端支架总成2XXXX-XX-DFMEA-002DEFMA-XXXX 前保险杠安装支架3XXXX-XX-DFMEA-003DFMEA-XXXX A柱上护板总成4XXXX-XX-DFMEA-004DFMEA-XXXX 上装饰件系统5XXXX-XX-DFMEA-005DFMEA-XXXX 下装饰件系统6XXXX-XX-DFMEA-006DFMEA-XXXX 乘客拉手系统7XXXX-XX-DFMEA-007DFMEA-XXXX 仪表板中下护板总成8XXXX-XX-DFMEA-008DFMEA-XXXX 仪表板总成9XXXX-XX-DFMEA-009DFMEA-XXXX 仪表板横梁系统10XXXX-XX-DFMEA-010DFMEA-XXXX 仪表板装饰板总成11XXXX-XX-DFMEA-011DFMEA-XXXX 侧围上护板总成12XXXX-XX-DFMEA-012DFMEA-XXXX 侧围下护板总成13XXXX-XX-DFMEA-013DFMEA-XXXX 前保险杠总成14XXXX-XX-DFMEA-014DFMEA-XXXX 前围隔音隔热垫15XXXX-XX-DFMEA-015DFMEA-XXXX 前风挡下装饰板系统16XXXX-XX-DFMEA-016DFMEA-XXXX 安全带装置17XXXX-XX-DFMEA-017DFMEA-XXXX 安全气囊系统18XXXX-XX-DFMEA-018DFMEA-XXXX 左下护板总成19XXXX-XX-DFMEA-019DFMEA-XXXX 座椅装置20XXXX-XX-DFMEA-020DFMEA-XXXX 手套箱总成21XXXX-XX-DFMEA-021DFMEA-XXXX 组合仪表罩总成22XXXX-XX-DFMEA-022DFMEA-XXXX 转向盘总成23XXXX-XX-DFMEA-023DFMEA-XXXX 转向管柱护罩总成24XXXX-XX-DFMEA-024DFMEA-XXXX 遮阳板系统25XXXX-XX-DFMEA-025DFMEA-XXXX 门护板系统26XXXX-XX-DFMEA-026DFMEA-XXXX 顶棚系统27XXXX-XX-DFMEA-027DFMEA-XXXX-侧围总成28XXXX-XX-DFMEA-028DFMEA-XXXX-前后风挡玻璃29XXXX-XX-DFMEA-029DFMEA-XXXX-后视镜系统30XXXX-XX-DFMEA-030DFMEA-XXXX侧门玻璃31XXXX-XX-DFMEA-031DFMEA-XXXX侧风窗密封条32XXXX-XX-DFMEA-032DFMEA-XXXX充电口盖系统33XXXX-XX-DFMEA-033DFMEA-XXXX前防撞梁总成34XXXX-XX-DFMEA-034DFMEA-XXXX前后流水槽总成35XXXX-XX-DFMEA-035DFMEA-XXXX前舱总成36XXXX-XX-DFMEA-036DFMEA-XXXX前舱盖铰链37XXXX-XX-DFMEA-037DFMEA-XXXX地板总成38XXXX-XX-DFMEA-038DFMEA-XXXX开闭件钣金39XXXX-XX-DFMEA-039DFMEA-XXXX玻璃升降器40XXXX-XX-DFMEA-040DFMEA-XXXX货箱门铰链41XXXX-XX-DFMEA-041DFMEA-XXXX车门撑杆系统42XXXX-XX-DFMEA-042DFMEA-XXXX车门铰链43XXXX-XX-DFMEA-043DFMEA-XXXX门盖密封系统44XXXX-XX-DFMEA-044DFMEA-XXXX门盖锁系统45XXXX-XX-DFMEA-045DFMEA-XXXX顶盖总成车身饰件汽车车身饰件DFMEA全套资料。
DFMEA-电动转向管柱总成
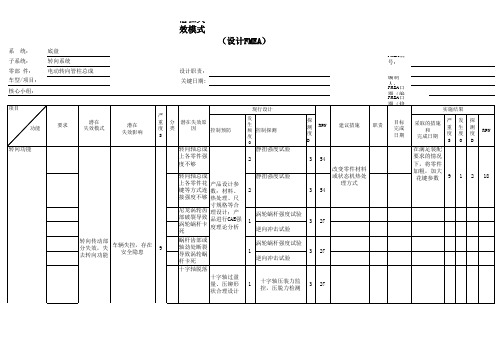
转向舒适性
功能
RPN
转向回正差
需手动回正 转向控制策 ECU控制上增 略无回正补 加回正补偿 偿
程序完善,整车匹 4 配验证
3
84
传感器增加角 度信号,实现 主回 正功能
修改助力曲 线 整车匹配、装车验 证 3 整车匹配、装车验 证 2 42 重新选择阻尼 、摩擦补偿控 制策略 重新选择阻 尼、摩擦补 偿控制策略 修改助力曲线 7 2 2 28
响应波动
在实车上进 电机控制参 行匹配后调 数不匹配 整PID控制参 数 发飘,没有路 感,顾客对产品 不满意 方向盘偏重,顾 客对助力不满意 方向盘重,顾客 对产品不满意 7 控制程序设 整车运行试 计不合理 验 控制程序设 整车运行试 计不合理 验 出厂性能检 测 控制器失效 整车运行试 验 EPS总成空载 转向系统摩 转向力矩控 擦力大, 制 转向回正差 需手动回正
2
总成性能100%检 测;装车验证
2
28
助力过大
2
整车匹配、装车验 证 整车匹配、装车验 证 整车匹配、装车验 证
2
24
整车匹配、装 车验证 整车匹配、装 车验证 整车匹配、装 车验证
助力过小
2
2
24
无助力 转向舒适性
2
2
28
3
空载力矩100%性能 检测
1
21
系
统:
底盘 转向系统 电动转向管柱总成 设计职责: 关键日期: 编制人: FMEA日期(编制): FMEA日期(修订):
1
产品型式试验
3
27
各连接部位 车辆失控,存在 失效,失去 安全隐患 转向功能
9
1
静扭、疲劳试验
3
汽车车身饰件DFMEA-组合仪表罩总成

☆
撞距离要求
100mm
驶员造成更多伤
组合仪表罩总成视野
组合仪表罩 总成不可遮 挡仪表可视
区域
组合仪表在视野 可视范围内不被 遮挡,视野清晰
仪表视野遮挡
看不清仪 表,影响驾 驶员安全性
和舒适性
8
☆
可靠耐久性/可靠性/环 境条件/温度湿度
组合仪表罩 总成
高温变形翘曲, 轮廓和曲面歪斜 仪表板系统及其 、高温接合面分 子系统需要在 离、高温气泡、 95%的车辆使用 粉化、渗出、缩 温度和湿度条件 孔、高温纹理消 下功能可靠 失、高温装饰层 膨胀、高温变形 、功能失效低温
间隙定义不合理
相互配合结构符合BP 规范IP-11021
数据评审/设 3 计校核/实车 2
验证
1、节点审
核,M2节点
3
仪表板系统对M1数据进
3
行评审确认
组合仪表罩总成卡子 卡紧力不够,卡口结 构未按照数据调整到
位
1、概念设计时,此项 校核不充分 2、设计评审
设计时未考虑组仪表 设计时做好组合仪表 罩总成单独拆卸空间 罩单独拆DMU校核
齐
灰边
怨
4
☆
组合仪表罩总成 组合仪表罩总成
与组合仪表配合 与组合仪表间隙
规避摩擦异响
不合理
间隙小产生 摩擦异响
4
☆
组合仪表罩 总成满足紧 固良好的要
求
组合仪表罩总成 禁锢良好
组合仪表罩总成 禁锢不良,组合
仪表罩易晃动
舒适度不 佳,影响内 饰质量评价
4
☆
组合仪表罩 总成
组合仪表罩总成 在不拆卸仪表板 条件下具备维修
要求
组合仪表罩要拆 卸仪表板才能维
FMEA-左A柱上护板总成
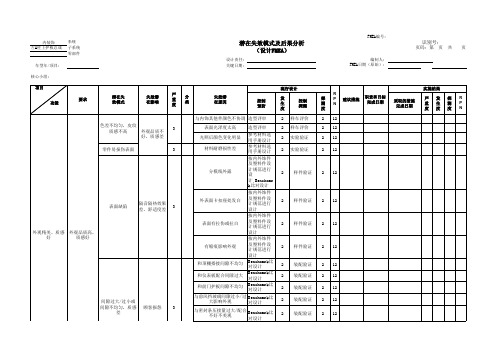
用手册设计 合理选用材
3
汽车产品中 有毒有害物
料
质的限量要
求进行检测
R
按HJ/T400-
2007车内挥
按
发性有机物
材料选用不当
2005/673/EC 3 和醛酮类物
设计
质采样测定 方法进行检
测
R
A柱尺寸过大
参考标杆车 设计,CAE分 3 析
CAE分析, 样车评价
参考标杆车
A柱布局位置不合理 设计,CAE分 2
及塑料件设
分模线外露
计规范进行 设
2
样件验证
计,Benchmar
k比对设计
按内外饰件
外表面卡扣座处发白
及塑料件设 计规范进行
2
样件验证
设计
按内外饰件
表面有拉伤或拉白
及塑料件设 计规范进行
2
样件验证
设计
按内外饰件
有缩痕影响外观
及塑料件设 计规范进行
2
样件验证
设计
和顶棚搭接间隙不均匀
Benchmark比 对设计
2005气味标准 大于3级
害乘员健康
8
要求)
满足GB11552- 1999《轿车内 部凸出物》和 ECE R21法规要 求
不满足GB11552- 1999《轿车内部凸 出物》和ECE R21 法规要求
碰撞时乘员受 到伤害
9
铅、汞、镉、六价
有毒有害物质 超标
铬含量超标:不满 足QCC JT098-2008 危害乘员健康 汽车产品中有毒有
实验验证
实验验证 实验验证
R 材料阻燃性差,水平燃烧 参考材料选
速率超过100mm/分钟 用手册设计
- 1、下载文档前请自行甄别文档内容的完整性,平台不提供额外的编辑、内容补充、找答案等附加服务。
- 2、"仅部分预览"的文档,不可在线预览部分如存在完整性等问题,可反馈申请退款(可完整预览的文档不适用该条件!)。
- 3、如文档侵犯您的权益,请联系客服反馈,我们会尽快为您处理(人工客服工作时间:9:00-18:30)。
转向管柱护罩总 成上下调节时周
边间隙大
影响外观, 客户不满意
4
☆
1、设计不合理 2、未做遮物帘
外观匹配
转向管 柱护罩 总成初 始位置 与仪表 板周圈 间隙不
均匀
转向管柱护罩总 成初始位置与仪 表板周圈间隙满 足≥6.5mm要求
由于公差的原 因,导致转向管 柱护罩总成与仪 表板周圈间隙不
均匀
向管柱护罩总成跟仪 表板配合时在任何位 置间隙均匀,且满足
3
数据评审/ 设计校核
3
36
≥6.5mm要求
批准/日期:
第页
措施执行后的结果
频 度 O
探 测 度 D
风 险 顺 序 数
数
选用已验证燃烧特性
的材料(燃烧速度≤ 75mm/min)作为仪表板
1
燃烧性能 实验测试
1
10
系统的材料
建议措施
职责及目标 完成日期
措施执行后的结果
采取 的措 施及 完成 日期
严 重 度 S
选择耐候性符合相关 定义要求的材料
2
耐光色牢 度实验
3
24
皮纹区域定义表,根 据皮纹形式合理的脱 模角
5
模具可行 性分析
4
调整A面满足脱模角要 80 求;粗皮纹脱模角≥7°
细皮纹脱模角3-5°
材料厂家和牌号选择 从材料库里面选择, 要求:腰线以下阳光 3 不易照到的零部件:
9ቤተ መጻሕፍቲ ባይዱ±2℃/24h
3
45
1、节点审
核
1、人机工程研究;
对M2数据
2、参考设计要求布置 3 进行评审 3 36
3、增加遮物帘
确认;
2、增加遮
物帘
1、数据校核时保证转
转向管 柱护罩
总成
仪表板系统及其 子系统需要在 95%的车辆使用
温度和湿度条件 下功能可靠
、高温接合面分 离、高温气泡、 粉化、渗出、缩 孔、高温纹理消 失、高温装饰层 膨胀、高温变形
外观差,顾 客不满意
5
☆
材料选择不合理
、功能失效低温
脆裂
外观匹配
转向管 柱护罩
总成
转向管柱护罩总 成匹配符合DTS 要求,无内部结
护罩与仪表 板周圈间隙 不一致,感 官质量差, 降低客户满
意度
编制/日期:
会签/日期:
4 ☆ 间隙设计不合理 审核/日期:
潜在失效模式及后果分析(DFMEA)
车身部
编制人 编制日期 修订日期
FMEA编号: 共页
第页
现行设计控制
控制预防 (规范)
频度 控制探测 探测 数O (试验) 度D
风 R险 P顺 N序
系统 子系统 零部件 年型/车型
项目 功能
潜在失效模式及后
内饰系统 仪表板系统 转向管柱护罩总成
设计职责(部门) 关键日期 核心小组
要求
严
潜在失效模式
失效潜在影 响
重 度 数
分 类
S
失效潜在原因 /机理
仪表板
安全法规
零部件 满足阻
燃要求
GB8410-2006材 料的燃烧速率≤ 100mm/min
材料阻燃性不符 合法规要求
整车无法销 售
1 0
★ 材料规格定义错误
性能
满足耐 老化要
求
不褪色(灰度≥ 4级)
褪色
外观不良消 费者不满
4
☆
材料牌号设计定义不 对
外观
表面质 量定好
外观质量好,皮 纹清晰
零件可视表面皮 纹缺失
感官质量 差,降低顾 客满意度
4
☆
结构原因,脱模角度 不够
高温变形翘曲,
轮廓和曲面歪斜
可靠耐久 性/可靠性 /环境条件 /温度湿度