变换低变催化剂升温硫化注意事项
硫化过程中注意要点

硫化过程中注意要点钴钼系耐硫低变催化剂硫化过程的控制要注意以下几点:①控制好升温硫化温度。
既要控制升温速度,又要保证床层能达到硫化最终温度。
②CS2加入量和加入时间的控制。
初期加入量小,逐步增加。
升温至20 0℃左右加入CS2。
③稳定操作。
空速、电加热功率、CS2加入量是硫化操作的三个主要调节手段。
在实际操作中应稳定CS2的加入量,以调气量为主、调电加热器的功率为辅。
④硫化要完全。
从硫化时间、床层温度、炉出口H2S浓度判断硫化终点,保证催化剂达到最佳活性。
在硫化操作中,应注意:1. 用半水煤气硫化,应控制半水煤气中氧含量≤0.5%,严防氧含量超标,并作预见性调节。
用变换气硫化时应防止床层带水。
2. CS2的加入时间不能过早,也不能过晚,一般在催化剂升温至200℃左右加入。
3. 严防油污带入床层。
油污易在高温下炭化,沉积于催化剂颗粒之中,影响催化剂的活性。
油污主要来源,一是半水煤气中带油,特别是回收压缩二段余热后,半水煤气带油更多,因此要经常排放油水分离器、焦炭过滤器倒淋。
二是通过CS2带入。
CS2是有机溶剂,CS2贮罐阀门等所带油污会溶于CS2而带入床层,因此要预先把硫化系统的油清洗干净。
4. 硫化过程中要加强H2S的分析,开始每小时一次,后期半小时一次,分析结果力求准确。
5. CS2是易燃危险品,硫化时要注意安全,加强管理,谨慎操作。
用固体硫化剂代替CS2硫化比较完全。
6. 用高硫煤制得,半水煤气中H2S含量大于2g/m3(标),硫化时可以不加CS2,利用未脱硫的半水煤气自然硫化。
但硫化时间长,催化剂的活性一般不如采用CS2硫化效果好。
因此,自然硫化较少采用。
耐硫变换催化剂循环硫化方案
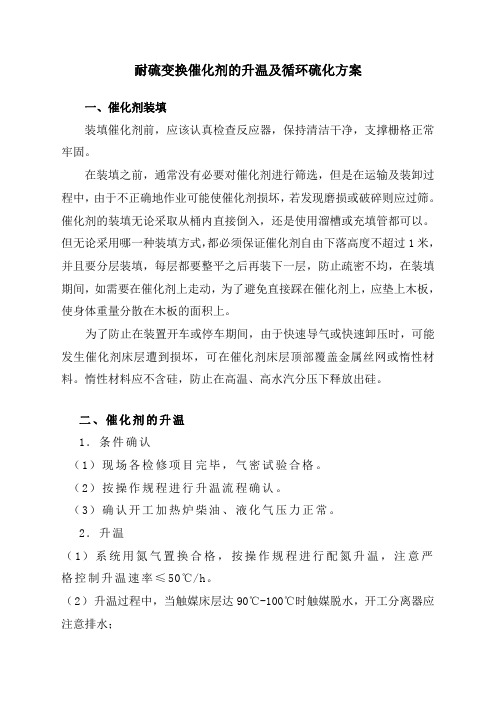
升 0.5 常温~120
30
3
0.5
120
6
温
0.5
120~220
30
3
0.5
220
6
备注 氮气量 20000Nm3/h 恒温释放吸附水
恒温拉平床层温差
三、催化剂的硫化 1、当催化剂床层温度达到 200℃~220℃时,把氢气加到氮气中,控
制反应器入口温度在 200℃~220℃,分析变换炉入口氢气含量 10%(干基) 左右。
耐硫变换催化剂的升温及循环硫化方案
一、催化剂装填 装填催化剂前,应该认真检查反应器,保持清洁干净,支撑栅格正常 牢固。 在装填之前,通常没有必要对催化剂进行筛选,但是在运输及装卸过 程中,由于不正确地作业可能使催化剂损坏,若发现磨损或破碎则应过筛。 催化剂的装填无论采取从桶内直接倒入,还是使用溜槽或充填管都可以。 但无论采用哪一种装填方式,都必须保证催化剂自由下落高度不超过 1 米, 并且要分层装填,每层都要整平之后再装下一层,防止疏密不均,在装填 期间,如需要在催化剂上走动,为了避免直接踩在催化剂上,应垫上木板, 使身体重量分散在木板的面积上。 为了防止在装置开车或停车期间,由于快速导气或快速卸压时,可能 发生催化剂床层遭到损坏,可在催化剂床层顶部覆盖金属丝网或惰性材 料。惰性材料应不含硅,防止在高温、高水汽分压下释放出硅。
H2S 分析 1 次/ 半小时
四、硫化过程中不正常情况的处理 1、床层温升缓慢 配氢量或氮气量过高,入口温度控制较低,可通过增加开工加热器的
蒸汽量,提高变换炉入口温度来控制。 2、床层温度急剧上升 二硫化碳加入过快或入口温度调节过高都可能导致温度急剧上升。可
采取的措施为:降低变换炉入口温度;减少直到停止加入二硫化碳。
全低温变换安全操作规程

全低温变换安全操作规程编制:校对:审核:批准:目录一、岗位任务………………………………………………………………二、岗位职责………………………………………………………………(一)、职权………………………………………………………………(二)、责任………………………………………………………………三、工作联系及交接班制度………………………………………………(一)、工作联系…………………………………………………………(二)、交接班制度………………………………………………………四、设备管理及维护制度…………………………………………………(一)、巡回检查制度……………………………………………………(二)、设备管理、卫生、润滑…………………………………………五、工艺规程………………………………………………………………(一)、反应原理…………………………………………………………(二)、工艺流程…………………………………………………………(三)、设备一览表………………………………………………………(四)、工艺指标与操作规程……………………………………………六、安全操作规程…………………………………………………………(一)、安全开车操作……………………………………………………(二)、安全停车操作……………………………………………………(三)、紧急停车操作……………………………………………………(四)、系统停车检修安全操作规程……………………………………(五)原始开车规程………………………………………………………(六)、不正常情况及安全处理…………………………………………(七)、安全注意事项……………………………………………………七、安全技术规程…………………………………………………………(一)、任务及特性………………………………………………………(二)、安全总则…………………………………………………………(三)、岗位操作安全细则………………………………………………八、异常情况及事故处理…………………………………………………一、岗位任务本岗位的任务是负责将来自压缩机二段的水煤气中约占38%左右的一氧化碳气体,在高温、加压条件下,借助于催化剂的作用,与蒸汽反应生成对化工生产有用的二氧化碳和氢气,既净化了气体中有害物质又节约能源。
饱和塔流程三段式全低变工艺催化剂升温硫化方案

湖北双雄催化剂有限公司变换催化剂升温硫化方案1 变换催化剂硫化方案1.1 升温硫化应具备的条件:1) 系统改造完,施工方交底。
2) 变换催化剂装填完,装料口按要求封闭。
3) 罗茨机、高压机、电加热器完好备用,仪表及控制系统试用合格。
4) 管道设备保温。
5) 水、电、蒸汽等保证供应。
6) 操作人员熟悉工艺与升温硫化方案。
7) 开风机保压头,用压缩机循环送气,用压缩机调节气量。
在设备内有冷却水流动的状态下利用二水加、冷却器对高温煤气降温。
硫化升温煤气不通过脱盐水加、一水加、热水塔,关闭有关阀门,打开硫化专用线阀门,打开回压缩机一段入口循环线阀门。
硫化工艺见全低变工艺流程图:1.2 升温硫化的准备8) 按要求抽盲板,硫化系统畅通无阻。
9) 变换系统(包括硫化管线)惰气置换合格。
10) 电加热器、箩茨风机、压缩机完好备用,仪表、微机、联锁、信号齐全,试用合格。
11) 二硫化碳装入容器亩好。
每立方米新催化剂需二硫化碳:煤气全放空硫化或电炉功率偏小需150Kg,煤气循环并略放空硫化需120Kg,硫化煤气冷却方式为直接用水淋降温硫化需130Kg,每立方米旧催化剂硫化需30Kg。
氮气接入二硫化碳槽(用前要0.4MPa试露),压力升至~0.2MPa备用。
二硫化碳购买电话:139********12) 硫化时输送二硫化碳的胶管要用有纤维内网的煤气塑料管、新氧气带、新乙炔气带。
严防伪劣商品。
13) 增压机开车送气,总管置换合格,按硫化气量准备好开车风机/压缩机。
14) 分析仪器完好。
15) 水、电、汽保证供应。
1.3 升温期:(常温~210℃,电加热器出口温度≤260℃)16) 启动箩茨风机将合格不脱硫半水煤气引入变换硫化系统,压力保持0.03—0.05MPa。
17) 启动压缩机开始循环,循环气量控制8000~10000NM3/h。
压力保持0.04—0.08MPa。
18) 硫化系统循环5分钟,开启电加热器对每组分别预热后,推电升温。
催化剂预硫化操作简版

1.1.催化剂预硫化1.1.1.预硫化的准备工作1)变换催化剂升温脱水已完成,变换炉床层温度达200~220℃。
2)硫化剂已拉至现场(35t),考虑到催化剂硫化过程中损失等因素,硫化剂的准备量应为理论耗量的1.5倍。
3)21V009硫化剂罐已储存硫化剂;预硫化过程中当界位低于30%时应及时补充硫化剂。
4)联系调度引开工氢气至装置界区前备用。
开工氢气规格:压力≦1.0MPa(G),不含烯烃,氧气含量小于0.05%(V);开工氢气采样分析合格。
5)检查确认21E005、21E008、21E009已建立正常液位。
6)按岗位操作法投用工艺凝液汽提系统,工艺凝液汽提系统具备接收预硫化产生的含硫污水。
1.1.2.预硫化的注意事项1)预硫化过程中,严格按硫化曲线操作,控制好硫化温度、循环气中硫化氢及氢气浓度。
2)硫化氢未穿透催化剂床层时,催化剂床层任意温度不能大于280℃。
3)若催化剂床层温升超过30℃,则停止升温或降低注硫量,并且保持变换炉进口温度不变直至温升降至小于30℃。
4)硫化剂的加入应采取连续少量的原则加入,防止超温。
5)硫化过程中,定期检测循环气中的硫化氢浓度。
6)预硫化过程中,视采样分析结果,调整开工氢气补入量,将循环系统氢含量维持在10%~25%(V),以控制20%(V)为宜。
预硫化期间要始终保持H2含量在10%(V)以上,保证硫化剂加入后能完全氢解。
7)催化剂硫化产生的污水应密闭排往工艺凝液汽提系统。
8)若电加热器故障长时间停运:应停配氢气、停止注硫、停21K001,系统保温保压,必要时引氮气置换以降低系统内氢气浓度。
故障排除后按岗位操作法启动21K001、21E001进行硫化。
9)若注硫泵21P003不上量:催化剂停止提温,停止配氢气,尽快处理好注硫系统的故障并向催化剂注硫,重新配氢气以维持循环氢中氢浓度在指标范围内。
若注硫无法恢复正常,应监控循环气中硫化氢浓度,提高氮气补入量,以降低循环气中氢气浓度。
变换催化剂硫化升温步骤及注意事项

变换催化剂硫化升温步骤及注意事项升温步骤及注意事项用氮气(也可用半水煤气,但控制速率,注意安全)对整个CO变换系统进行置换,置换至O2含量≤0.5%(体积分数)。
然后按制定的升温流程对催化剂进行升温,升温速率控制在15-25℃/h,当催化济床层温度升至80℃时,向升温载气中配入H2;在催化剂床层温度达120℃时,恒温约4h,以利催化剂吸附水的排放及吸附氧的释放、燃烧。
升温过程注意以下几点:一、根据实际情况制定升温流程,管线盲板倒换正确;二、用载气的温度将升温速率控制在安全范围内;三、配氢时,注意分析升温载气中的O2含量,严格控制载气中的O2含量≤0.5%(体积分数),超标时用放空进行调整;四、保持升温系统压力≤0.2Mpa。
变换催化剂硫化注意事项一、在升温、降温期间,采用大空速,要求电炉功率要大(用CS2硫化时,1m3催化剂的电炉功率为30kW,用固体硫化剂时,1m3催化剂的电炉功率要≥50kW,宜分为多组控制),以满足大负荷需要。
二、硫化期间,保持硫化载气中的H2含量≥25%,可采用部分放空和添加新鲜煤气的措施保证循环气中的H2浓度达标。
三、用CS2的加入量及硫化载气温度和流量控制催化剂床层的升温速率及热点温度,必要时可切气通蒸汽降温后再导气硫化,严禁床层温度暴涨、急降,进行强制硫化时,床层温度应控制在450-480℃,最高不得超过500℃。
四、在H2S穿透前,CS2量不可加入过多,否则会把催化剂中COO 直接还原为金属CO,CO有甲烷催化作用,不仅加剧超温,而且使硫化无法继续进行,同时损害催化剂的活性。
五、硫化系统压力应保持在0.2-0.3 Mpa。
六、因湿气硫化会使CO-MO系催化剂丧失部分活性,尤其是丧失低温活性,因此,系统保压、补氢时须用干气,并及时排放冷凝水,严禁冷凝水进入催化剂床层。
七、煤气中O2含量每升高0.1%,系统绝热温升约15℃。
O2会将催化剂中的活性组分氧化成硫酸盐,降低催化剂的活性,因此,在硫化全过程中,须严格控制煤气中O2含量<0.5%,当煤气中O2含量高时,必须迅速切气源,待O2浓度降至合格后再通气硫化。
变换催化剂升温硫化方案

新疆新业能源化工有限责任公司变换冷却装置催化剂升温硫化方案新疆新业能源化工有限责任公司二零一五年三月★内部资料,注意保密变换冷却催化剂升温硫化方案(试行本)编号:XYNH/QH-2014-01编写:王海校核:审核:审定:批准:日期:受控号:发布日期:2015年12月31日实施日期:2015年1月1日目录1:催化剂的升温2:催化剂的硫化3:硫化时的注意事项4:系统接气和开车1、催化剂的升温1.1升温前的准备工作1.1.1催化剂装填完毕,并气密合格。
1.1.2氮气系统臵换合格,各导淋取样分析O2≤0.1%。
1.1.3放入CS2备用。
有专人记录CS2的加入量和剩余量。
CS2的加入量:以每吨催化剂消耗8OKgCS2,计共计准备CS21.5吨(变换炉上段)。
1.2催化剂的升温1.2.1采用纯氮气对催化剂床层进行升温。
控制氮气的升温速率不超过50℃/h。
1.2.2催化剂床层升温一定要平稳,严格按升温曲线进行,控制好空速和升温速度,1.2.3当触媒进行自然恒温时,放水必须完全,注意排放N2分离器的导淋和各反应器出口的导淋,特别是变换炉导淋排水必须及时和完全。
1.2.4当变换炉催化剂床层温度大于180℃时,可配入H2对催化剂床层继续升温。
1.2.5排水点:D61101A/B下倒淋,D61102下倒淋,LS61102冷凝液管线倒淋。
每小时一次。
2.催化剂的硫化2.1硫化方法:采用氮气加氢气对催化剂进行硫化,严格控制床层入口H2含量为20-30%,添加CS2,对催化剂进行硫化。
2.2催化剂硫化反应方程式CS2+4H2=2H2S+CH4 +240.6KJ/molCoO+H2S=CoS+H2O +13.4KJ/molMoO3+2H2S+H2=MoS2+3H2O +48.1KJ/mol2.3催化剂的硫化2.3.1当变换炉层温度大于180℃,可配入氢气继续对催化剂床层进行升温度,氢气的配入量以H2浓度为准,使H2浓度达到20%左右。
变换升温硫化方案

变换硫化方案操作规程⑸硫化线:来自低压机的半水煤气→丝网过滤器→除油剂炉→前热交壳程→后热交管程→变换炉一段进口管1#电加热器→ 2#电加热器→变换炉二段进口管变换炉三段进口管后热交壳程→前热交管程→水加热器→冷却器→气液分离器→⑷变换炉无内保温变换炉分三段:一段上层装20m3抗毒剂、下层30 m3催化剂;二段装30 m3催化剂;三段装55m3催化B、每层底部有篦子板支撑,上面铺两层不锈钢网(3×3),两层耐火球;在触媒上面铺一层不锈钢网,其中一段压200㎜Φ30耐火球,二、三段压300㎜Φ30耐火球;底部铺耐火球目的:a、压好不锈钢网边;b、较好地防止反吹动,避免偏流。
上面铺耐火球地目的:a、气体分布均匀;b、蒸发可能带至变换炉内地水份。
2、和外部直接关联单位的主要控制指标:相关指标:变换入口H2S≥0.10g/Nm3 ;变换入口O2≤0.4%0.4%≤O2<0.8%减量:0.8%≤O2<1.0%减机:O2 ≥1.0%系统停车脱盐水指标:电导率≤5μs/cm,CL-≤5mg/L,碱度≤0.3mmol4、触媒的硫化硫化反应是将氧化态催化剂转化为硫化态产生活性CS2 +4H2 = 2H2S+CH4生成的H2S与CoO和MoO3反应生成CoS和MoS2:CoO+H2S=CoS+H2O MoO3+2H2S+H2 = MoS2+3H2OA、检查电加热器出口测温点是否灵敏,接CS2是否畅通;B、系统加蒸汽阀前加盲板;C、水加热器,冷却器水路畅通;D、CS2槽内贮满CS2,液位计清晰,槽内加压设施、CS2流量计及输送设备安装齐全;E、备好分析器具和分析药品。
⑴硫化方法:采用循环升温硫化法A、循环硫化路线:压缩二出来合格半水煤气→变换系统→回低压机一入B、关闭变换炉进口阀,打开电加热器进口阀,打开一段硫化阀,三段串联硫化,一段硫化结束后打开二段硫化阀关闭一段。
二段硫化结束后打开三段硫化阀关闭二段。
⑵升温硫化过程:A、系统内导入气体后,要保证有一定的循环时间,当分析电加热器入口O2≤0.5%时,启电炉升温;B、以电加热器出口温度为调节点,控制一段进口温度,根据一段温升情况,逐渐加大电炉功率(控制电炉出口温度最高不超过480℃)进入一段升温阶段;C、当催化剂温度升至60-90℃时,因催化剂在此阶段有一个脱水期,需要对各个气相导淋每半小时排放一次;D、当一段上层温度升至210℃时,向一段加CS2,进入一段硫化初期,二段升温阶段;E、当一段触媒上层温度达到300℃,入口H2S达到15——20 g∕Nm3, 二段触媒上层温度达210℃,进口H2S≥3 g∕Nm3时,进入一段硫化主期,二段硫化初期,三段升温阶段;F、当一段各点温度升至350——370℃时,恒温8h以上,并在出口三次取样分析H2S含量达10 g∕Nm3以上时为硫化结束。
催化剂预硫化过程中的注意事项是什么
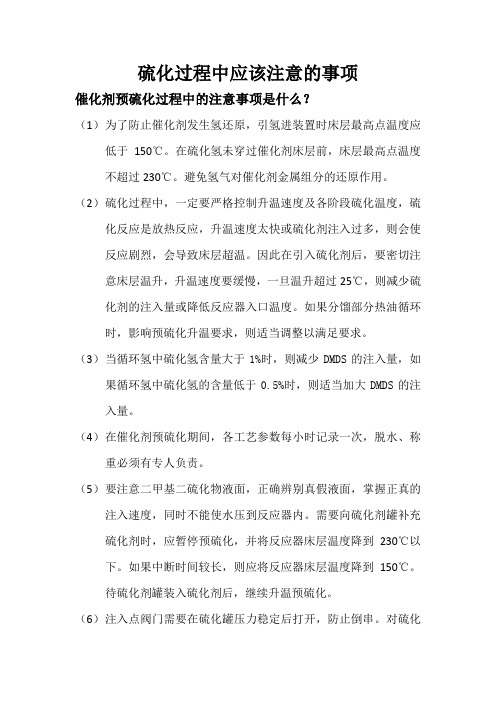
硫化过程中应该注意的事项催化剂预硫化过程中的注意事项是什么?(1)为了防止催化剂发生氢还原,引氢进装置时床层最高点温度应低于150℃。
在硫化氢未穿过催化剂床层前,床层最高点温度不超过230℃。
避免氢气对催化剂金属组分的还原作用。
(2)硫化过程中,一定要严格控制升温速度及各阶段硫化温度,硫化反应是放热反应,升温速度太快或硫化剂注入过多,则会使反应剧烈,会导致床层超温。
因此在引入硫化剂后,要密切注意床层温升,升温速度要缓慢,一旦温升超过25℃,则减少硫化剂的注入量或降低反应器入口温度。
如果分馏部分热油循环时,影响预硫化升温要求,则适当调整以满足要求。
(3)当循环氢中硫化氢含量大于1%时,则减少DMDS的注入量,如果循环氢中硫化氢的含量低于0.5%时,则适当加大DMDS的注入量。
(4)在催化剂预硫化期间,各工艺参数每小时记录一次,脱水、称重必须有专人负责。
(5)要注意二甲基二硫化物液面,正确辨别真假液面,掌握正真的注入速度,同时不能使水压到反应器内。
需要向硫化剂罐补充硫化剂时,应暂停预硫化,并将反应器床层温度降到230℃以下。
如果中断时间较长,则应将反应器床层温度降到150℃。
待硫化剂罐装入硫化剂后,继续升温预硫化。
(6)注入点阀门需要在硫化罐压力稳定后打开,防止倒串。
对硫化管线要在投用前用氮气吹扫干净。
冷高分脱水过程特别注意硫化氢中毒的预防措施,水包中的水不要一次性排完。
预硫化的终止的标志是什么?(1)反应器出入口气体露点差在3℃以内。
(2)反应器出入口气体的硫化氢浓度相同。
(3)高分无水生成。
(4)床层没有温升。
为什么新催化剂升温至150℃以前,要严格控制10-15℃/h 的温升速度?在催化剂床层从常温开始升温时,分两个阶段,常温至150℃和150-250℃。
新催化剂温度小于150℃时属于从催化剂微孔向外脱水阶段,在此阶段升温速度太快,水汽化量大,易破坏催化剂微孔,严重时导致催化剂破损,造成床层压降过大,缩短开工周期。
低温变换催化剂升温硫化总结

低温变换催化剂升温硫化总结1、概述随着我国合成氨工艺的不断改进,低温变换催化剂的应用越来越广泛。
本公司变换装置采用的就是钴钼系低变耐硫变换催化剂。
由于耐硫变换催化剂的活性组分钴和钼是以氧化态的形式分散在多孔载体上,而催化剂活性相为硫化态,因此在使用前须进行硫化处理。
催化剂的硫化是耐硫变换催化剂应用的关键步骤,直接影响着催化剂的变换活性和稳定性,也将直接影响变换工段的生产负荷、合成气质量和蒸汽消耗等。
本文以变换四段催化剂升温硫化为例,对低变催化剂升温硫化过程进行总结。
2、工艺流程叙述在低变工艺中,因催化剂装填量较大,为减少放空量,本装置采用气体循环硫化法。
工艺气从变换炉四段出来后,经气气换热器与硫化风机出口的工艺气换热,将气体热量回收,进人变冷器降温至常温,进入3#分离器分离液态水,之后工艺气进入硫化风机,维持硫化风机入口处正压,由硫化风机将工艺气送至气气换热器,然后进入电炉加热,最后进入变换炉四段。
由于在硫化过程中要消耗氢,在硫化风机入口处连续加入少量新鲜煤气。
为防止惰性气体在循环气中积累,在3#分离器处设一放空管,连续放空少量循环气,使循环气中H2体积分数维持在25%以上。
CS2从电炉出口加入。
3、升温硫化原理及过程一、硫化原理催化剂中的活性成分是以氧化态形式存在,生产时,须将其转化为硫化态才能显示出催化剂的高活性。
为加速硫化过程,通常采用外加硫化剂(CS2)方法进行,其反应方程式为:CS2 + 4H2 ←→2H2S + CH4 —246KJ/mo (氢解反应)MoO3 +2H2S +H2←→MoS2 +3H2O —48.1 KJ/molCoO + H2S ←→ COS +H2O —13.4 KJ/mol这些反应都是放热反应,特别是CS2的的氢解是很剧烈的放热反应。
二、升温硫化的过程1、升温阶段:四段硫化阀进出口保持全开,加大循环气量和严格控制电炉出口温度,在较低的温度下脱除催化剂的物理水,当触媒下层温度还在120℃以下,必须控制电炉出口温度不得超过150℃;触媒下层温度到120℃后,恒温4小时,以防脱水过猛和未脱除干净而升温使催化剂结块,物理水全部脱除干净后再升温,将温度升到220℃,再恒温2小时。
耐硫变换催化剂升温硫化改进建议

笔 者 自 19 9 2年参 加 工 作 以来 ,一直 从 事 合 成氨 厂 C O变换工 作 。在多年的 生产 实践 中总 结
出 一 些 C 耐 硫 变 换 催 化 剂 升 温 、硫 化 经 验 。 笔 O
究 。笔 者从 “ 黑龙江 龙煤东 化年产 3 0 t 成氨 0 合 k 初步设计 ” 中看到 ,变换升 温硫化 系统设计 基本
功率 4 0k ・ ,压力 为 0 a 5 W h .7 MP 。根 据 我们 多
年 的生产经 验和其 他工厂 变换催 化剂升 温硫化情
况 , 在 升 温 过 程 中 不 需 要 用 这 么 多 的气 ,实 际用 量 在 1 0 m。h左 右 。 因此 ,建 议 取 消 氮 气 鼓 风 0 0 / 0 机 ,之 后 升 温 直 接 采 用 空 分 装 置 提 供 的 0 4 a .5 MP 氮 气 。 低 压 氮 气 在 变换 炉 升 温 硫 化 时 其 他 车 间 基
是稳定 炉况和优 化工艺 条件 的首要 问题 。炭层 高
度 的不 稳 定 会 造 成 炉 内 温 度 的 波 动 。 炭 层 高 度 稳 定 后 ,并 不 是 床 层 各 区 就 能 稳 定 在 最 佳 位 置 , 还
要 进行合 理的工 艺调整 以优化 炉况 。行 。
时 ,采取 向煤气加 热器 管间 ,即变换气 体侧通 中
1 传 统 变 换 升 温硫 化 应 具 备 的 条 件
以往 变换: 升温硫化 时一般 都需要 以下条 件 : ( )升 温必 备加热 器( ) 1 炉 ;
以及开 车工作 。所 以传 统 的升温工艺 流程都 是按 照 上述 要 求 配 置 的 。传 统 的 升 温 硫 化 流 程 见
图 1
低变催化剂升温硫化方案分析

新疆梅花氨基酸有限责任公司合成氨装置低变触媒升温硫化方案编制:审核:批准:日期:2012年9月4日低变催化剂升温硫化方案一、组织机构1、领导小组: 组 长:师勇副组长: 翟风军、厂家技术服务人员 成 员: 李瑞福、调度、焦国秋、主操作 2、职责:(1)师勇负责升温开车工作的全面管理。
(2)厂家技术服务人员:负责确定升温、硫化过程中的技术指标的确定。
(3)翟风军根据厂家提出的技术要求,下达操作指令,对各项指标的执行进行监督控制。
(4)李瑞福负责升温硫化期间安全工作的监督管理 (5)调度负责升温硫化过程中上下工序及外接条件的协调。
(6)负责人员安排及操作指导 (7)执行升温硫化过程具体操作二、硫化原理:耐硫低变催化剂的主要组分为CoO 和MoO 3,催化剂在氧化态没有活性,生产应用时必须使其转化为硫化物才具有催化活性。
此次硫化剂采用CS 2。
1、C 2S 的氢解:CS 2+4H 2=CH 4+2H 2S+Q2、硫化: 1) C O O+H 2S=C O S+H 2O+Q2) MoO 3+2H 2S+H 2=MoS 2+3H 2O+Q三、触媒型号及装填数量:LYB-99 共计装填84m3。
四、一次通过流程低温变换炉上层中层 下层五、准备工作1、仪表气供应正常,所有电器、仪表(包括DCS 系统)均调试合格。
2、污水循环系统和脱硫再生循环系统正常运行。
3、低变电加热器各组电热元件测试绝缘良好备用,并指派专人负责升温还原期间的停送电工作。
4、升温硫化所需分析仪器、药品及分析人员安排到位,并准备好分析,并做好原始记录,升温硫化曲线绘制完成。
脱第二增湿器出口DN 255、岗位配备安全消防器材,包括灭火器、消防蒸汽胶管、防毒面具、长管面具等,(需备用约2m3防火沙土)。
低压蒸汽引至界区。
6、脱硫系统煤气置换完毕,低变升温系统设备、管路煤气置换合格。
7、气化工段具备连续制取合格煤气的条件,且气柜贮量在10~15米之间(前期可用空气升温,将2#、3#罗茨风机入口软连接解除)。
QCS_04催化剂的硫化过程及注意事项1
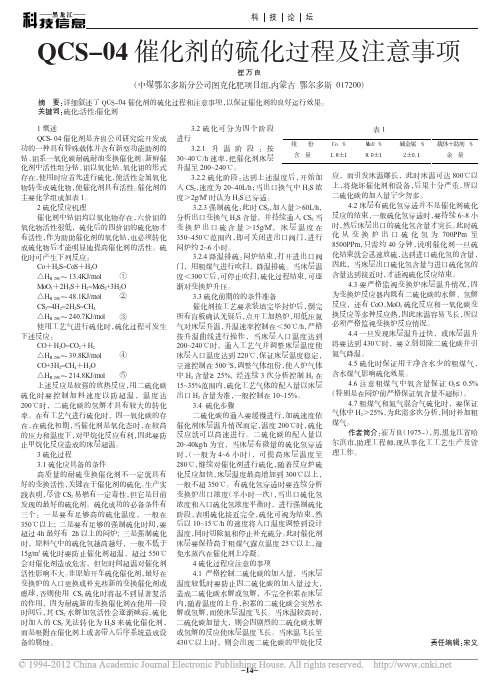
按升温曲线进行操作,当床层入口温度达到
4.4 一旦发现床层温升过快,或床层温升
200~240℃时,通入工艺气并调整床层温度使 将要达到 430℃时,要立刻切除二硫化碳并引
床层入口温度达到 220℃,保证床层温度稳定, 氮气降温。
空速控制在 500-1S,调整气体组份,使入炉气体
4.5 硫化时保证用干净含水少的粗煤气,
4.2 床层有硫化氢穿透并不是催化剂硫化
分析出口变换气 H2S 含量,并持续通入 CS2 当 反应的结束,一般硫化氢穿透时,要持续 6~8 小
变 换 炉 出 口 硫 含 量 >15g/M3, 床 层 温 度 在 时,然后床层出口的硫化氢含量才突长。此时硫
350~450℃范围内,即可关闭进出口阀门,进行 化 从 变 换 炉 出 口 硫 化 氢 为 700PPm 至
进行 3.2.1 升 温 阶 段 : 按
30~40℃/h 速率,把催化剂床层
;; ; ;; ;; ;;
;;; ;; ;;;;;;
;;; ;; ;;;;;;
;;;; ;; ;;;;;; ;;
;;;;;;
;; ;;
化剂中活性组分钴、钼以氧化钴、氧化钼的形式
存在,使用时应首先进行硫化,使活性金属氧化
物转变成硫化物,使催化剂具有活性。催化剂的
ÁÁÂ科技论坛
QCS-04 催化剂的硫化过程及注意事项
崔万良 (中煤鄂尔多斯分公司图克化肥项目组,内蒙古 鄂尔多斯 017200)
摘 要:详细叙述了 QCS-04 催化剂的硫化过程和注意事项,以保证催化剂的良好运行效果。 关键词:硫化;活性;催化剂
1 概述
3.2 硫化可分为四个阶 段
表1
QCS- 04 催化剂是齐鲁公司研究院开发成 功的一种具有特殊载体并含有新型功能助剂的 钴、钼系一氧化碳耐硫耐油变换催化剂。新鲜催
钴钼系耐硫变换催化剂使用注意事项

K8-11系列催化剂使用注意事项一、催化剂的使用1.1 催化剂的装填装填催化剂之前,必须认真检查反应器,保持清洁干净,支撑栅格正常牢固。
为了避免在高的蒸汽分压和高温条件下损坏失去强度,催化剂床层底部支撑催化剂的金属部件应选用耐高温和耐腐蚀的惰性金属材料。
惰性材料应不含硅,防止高温、高水汽分压下释放出硅。
催化剂装填时,通常没有必要对催化剂进行过筛,如果在运输及装卸过程中,由于不正确地作业使催化剂损坏,发现有磨损或破碎现象必须过筛。
催化剂的装填无论采取从桶内直接倒入,还是使用溜槽或充填管都可以。
但无论采用哪一种装填方式,都必须避免催化剂自由下落高度超过1米,并且要分层装填,每层都要整平之后再装下一层,防止疏密不均,在装填期间,如需要在催化剂上走动,为了避免直接踩在催化剂上,应垫上木版,使身体重量分散在木版的面积上。
一般情况下,催化剂床层顶部应覆盖金属网和/或惰性材料,主要是为了防止在装置开车或停车期间因高的气体流速可能发生催化剂被吹出或湍动,可能由于气体分布不均发生催化剂床层湍动,损坏催化剂。
由于高压,原料气密度较大,为了尽可能的减小床层阻力降,应严格控制催化剂床层高度和催化剂床层高径比。
通常催化剂床层高度应控制在3〜5m催化剂床层高径比控制在1.0〜1.8。
1.2 开车1.2.1 升温为防止水蒸气在催化剂上冷凝,首次开车升温时,应使用惰性气体(Nl、H、空气或天然气)把催化剂加热到工艺气露点以上温度,最好使用2。
采用務O C /h的升温速度加热催化剂,根据最大可获得流量来设定压力,从而确保气体在催化剂上能很好分布。
在通常情况下,气体的有效线速度不应小于设计值的50%但也不应超过设计值。
当催化剂床层温度达到100C〜130C时,恒温2〜3小时排除吸附的物理水,然后继续升温至200C〜230C时,进行下一步的硫化程度。
如果最初加热选用的是空气,在引入硫化气之前,必须用氮气或蒸汽吹扫系统,以置换残余氧气。
催化剂升温硫化方案
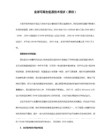
催化剂升温硫化方案一、催化剂的升温1、条件确认(1)现场各检修项目完毕,气密性试验合格,(2)按操作规程进行升温流程确认。
(3)确认开工加热炉柴油,液化压力正常。
2、升温(1)按操作规程进行配氮升温,注意严格控制升温速率≤50℃/h。
(2)当床层(一段)各点温度均达到200℃-220℃时恒温,进行下一步硫化程序。
首次开车升温时,为防止水蒸汽在催化剂上冷凝,应使用惰性气体N2把催化剂加热到工艺气露点以上温度。
采用≤50℃/h升温速度加热催化剂,根据最大可获得流量来设定压力,从而确保气体在催化剂上能很好的分布。
(3)当催化剂床层温度达到200℃-220℃时,进行下一步的硫化程度。
硫化气的切换基本上在常压或较高压力下进行,这取决于气流的方便,(注意:切换工艺气硫化前,一定要开导淋,彻底排放冷凝水)。
二、催化剂的硫化(一)采用工艺气硫化(1)确认工艺气中的硫化氢含量,最好工艺气中的硫化氢含量≥0.2%(VOL)。
(2)当催化剂床层温度达到200℃-220℃时,把湿工艺气加到氮气中(比例:湿工艺气:氮气=1:3)同氮气一起进入开工炉进行加热,控制反应器入口温度在200℃-220℃。
根据催化剂床层温度逐渐增加工艺气量,并且相应减少氮气量,直到氮气完全撤出。
(3)当硫化催化剂床层温度稳定时,再将工艺气流量增加,并控制入口温度200℃-220℃继续硫化。
(4)当有硫穿透催化剂床层时,逐步提高硫化压力和入口温度继续进行硫化,当压力为1.5MPa、入口温度230℃-250℃-时,此时变换炉出口有硫穿透,并且硫含量不再变化,可以认为硫化结束。
(5)硫化结束后,调整入口温度至正常使用要求的温度,同时增大工艺气量,提高系统压力至正常使用要求的压力。
采用补硫硫化1.加硫的位置:一般为第一变换炉前换热器的前面加硫。
2.CS2罐及加硫氮气管线,阀门配好待用。
3.取样点:变换炉入口和出口取样。
4.硫化期间4114-PVC-3保持全开。
耐硫变换催化剂装填及硫化方案
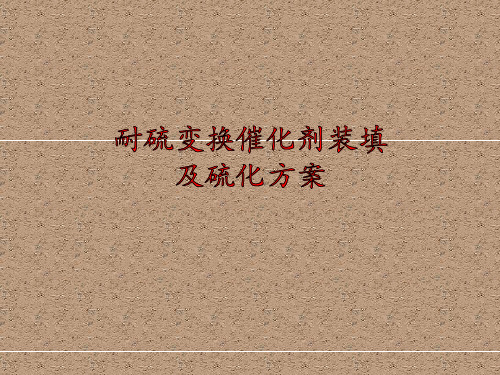
3.1.2把帆布袋接在装催化剂漏斗下面,炉内 作业人员拉住布袋出口,避免瓷球直接落到 下面摔坏。
3.1.3将瓷球铺平,确认达到所规定的高度。 注意先装50瓷球,后装25瓷球。
3.1.4催化剂卸出管也要装填上瓷球。
3.1.5将预制好的金属丝网正确地铺在瓷球上, 留出催化剂卸出管口。
3.2催化剂装填
3.2.1将催化剂装入吊斗
铺上木板,防止破损,在作业完成后,必须 把使用过的木板拿出炉外。
2.5 装填作业中,如果下雨、下雪要立即停 止作业,保护催化剂/过滤剂不被淋
湿。
2.6 在热偶套管周围充填时,注意不要造成 架空。
2.7 作业时,不要将异物带入炉内(铁片、 纸、烟头、泥土等)
2.8 应做好装填记录,包括物料的规格,型
3.2.6达到了规定的高度后,把催化剂表面推 平,把预制好的金属丝网铺在催化剂上面。 再装上300mm的瓷球。
4、四孔柱状过滤剂的装填
4.1按设计要求在所规定的位置上设置三层丝 网。
4.2 画出过滤剂装填的高度,用粉笔作上标 记。
4.3装填过滤剂至规定位置并推平。
4.4在过滤剂上设置一层丝网。再装上300mm
(3)CS2罐冲压,当罐内压力大于系统压力后, 稍开CS2罐入变换系统阀门,将CS2压入系 统,注意严禁CS2罐压力超过罐的设计压力。
(4)CS2和工艺气量的控制:在入口取样,控 制H2S+CS2含量3—5g/NM3,控制H2含量 在10%左右。
(5)控制床层温升T<20C/h,若床层温度上 升较快,应立即减少或停止加CS2量,同时 适当减少工艺气(或H2)量或增加N2量。
(6)注意随时分析出口H2S的含量,当出口
(6)注意随时分析出口H2S的含量,当出口 出现H2S时,可以适当提高入口温度。当 入口温度达到250--260C时,至少保持2h, 出口有H2S时,再慢慢提高入口温度,达 到300C,同时将入口总硫量提高到8--10 g/NM3。当出口气体中H2S含量维持在 4000-5000ppm时,可以认为硫化已结束。
低变催化剂的升温与还原
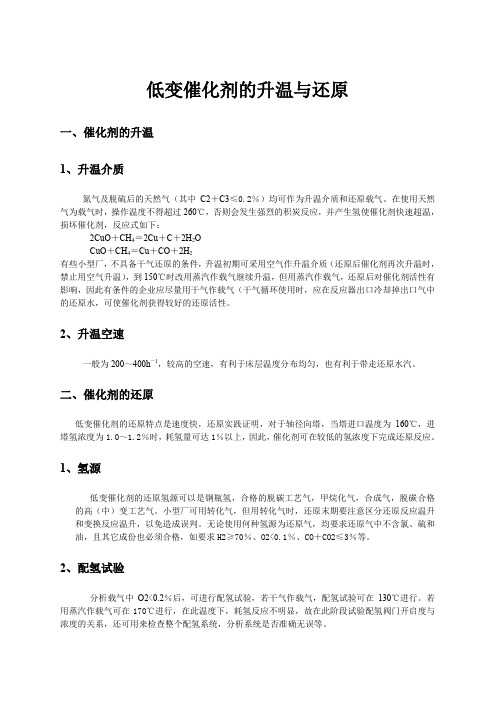
低变催化剂的升温与还原一、催化剂的升温1、升温介质氮气及脱硫后的天然气(其中C2+C3≤0.2%)均可作为升温介质和还原载气。
在使用天然气为载气时,操作温度不得超过260℃,否则会发生强烈的积炭反应,并产生氢使催化剂快速超温,损坏催化剂,反应式如下:2CuO+CH4=2Cu+C+2H2OCuO+CH4=Cu+CO+2H2有些小型厂,不具备干气还原的条件,升温初期可采用空气作升温介质(还原后催化剂再次升温时,禁止用空气升温),到150℃时改用蒸汽作载气继续升温,但用蒸汽作载气,还原后对催化剂活性有影响,因此有条件的企业应尽量用干气作载气(干气循环使用时,应在反应器出口冷却掉出口气中的还原水,可使催化剂获得较好的还原活性。
2、升温空速一般为200~400h-1,较高的空速,有利于床层温度分布均匀,也有利于带走还原水汽。
二、催化剂的还原低变催化剂的还原特点是速度快,还原实践证明,对于轴径向塔,当塔进口温度为160℃,进塔氢浓度为1.0~1.2%时,耗氢量可达1%以上,因此,催化剂可在较低的氢浓度下完成还原反应。
1、氢源低变催化剂的还原氢源可以是钢瓶氢,合格的脱碳工艺气,甲烷化气,合成气,脱碳合格的高(中)变工艺气。
小型厂可用转化气,但用转化气时,还原末期要注意区分还原反应温升和变换反应温升,以免造成误判。
无论使用何种氢源为还原气,均要求还原气中不含氯、硫和油,且其它成份也必须合格,如要求H2≥70%、O2<0.1%、CO+CO2≤3%等。
2、配氢试验分析载气中O2<0.2%后,可进行配氢试验,若干气作载气,配氢试验可在130℃进行。
若用蒸汽作载气可在170℃进行,在此温度下,耗氢反应不明显,故在此阶段试验配氢阀门开启度与浓度的关系,还可用来检查整个配氢系统,分析系统是否准确无误等。
加压下氢分压高,反应速度加快,温度难以控制。
因此小型厂还原压力通常在0.3MPa以下,大中型厂还原压力则在0.5MPa以下进行。
变换触媒升温硫化方案

变换触媒升温硫化方案1 触媒升温硫化前的准备工作(1)变换炉R2001触媒装填完毕。
(2)变换系统吹除、气密性试验完成。
(3)V2009已经装入CS2待用。
(4)DW、S3、S4、LN及仪表空气等公用工程均送至界区。
(5)各仪表调试合格,一次表根部阀打开。
(6)各自调阀、控制阀、手动阀均灵活好用,安全阀及安全装置调试合格。
(7)开工加热炉F2001已经符合使用条件。
(8)除氧给水系统已经具备条件。
(9)硫化所用分析仪器完好,药品备齐。
(10)升温曲线、图表、记录本、画图铅笔、直尺备好待用。
(11)硫化所用H2已经就为待用。
2 置换2.1置换前的确认⑴按《变换原始开车盲板确认表》对变换系统盲板确认变换原始开车盲板确认表⑶按《变换原始开车阀门确认表》对变换手动阀确认。
变换手动阀确认表(4)调节阀确认变换及冷凝液系统调节阀关闭。
2.2变换气系统置换⑴ 统置换路线⑶ 置换步骤① 联系调度变换系统置换。
② 确认MV2001关闭,现场打开开工氮气双手动阀,通氮气置换。
③打开PV2006置换气放空去火炬,用PV2006控制升压,压力PICA2006稳定在0.3MPa 时投自动。
④ 微开AV2003和TV2006。
① 按单体操作规程启动氮气循环风机C2001,启动后打开C2001前阀。
② 在洗氨T2001出口取样分析 O 2≦0.1%为置换合格,系统保压。
2.3变换冷凝液及气提系统置换 ⑴ 置换路线 ① 通知硫回收变换气提不凝汽需要放空。
② 打开PV2007和PV2009。
③ 确认冷凝液泵ⅠP2001和冷凝液泵ⅡP2002进口阀关闭。
① 打开LV2003和LV2009及前后手阀,给冷凝液气提系统送LN置换。
② 在气提塔T2002出口取样分析,O 2≦0.5%时,置换合格。
③关闭LV2003和LV2009及前后手阀,停止置换。
关闭PV2007和PV2009。
3 水煤气废锅E2001和低压蒸汽废锅E2004投运①确认E2001/E2004放空阀打开,并网阀关闭。
- 1、下载文档前请自行甄别文档内容的完整性,平台不提供额外的编辑、内容补充、找答案等附加服务。
- 2、"仅部分预览"的文档,不可在线预览部分如存在完整性等问题,可反馈申请退款(可完整预览的文档不适用该条件!)。
- 3、如文档侵犯您的权益,请联系客服反馈,我们会尽快为您处理(人工客服工作时间:9:00-18:30)。
变换低变催化剂升温硫化注意事项1. 硫化准备工作
(1) 触媒升温硫化需在系统吹扫、试压、触媒装填好后进行。
(2) 检查低变、变脱及脱碳系统技改项目、清理项目均已完工,不影响触媒升温、开车进行。
(3) 所有电器(包括微机)、仪表、自调阀、照明、信号、报警、联锁等安装、调试好备用。
(4) 系统中阀门、丝杆加油活动一次。
(5) 人员定岗培训完成,并充分熟悉升温、开车方案,做到心中有数。
(6) 所有380V、10000V运转设备试车,完好备用,不影响开车进度。
新设备预先先经单体试车或联动试车后备用。
(7) 电加热调试合格备用,连入硫化系统,脱盐水、循环水送好备用。
(8) 现场杂物清理干净,地沟盖板盖好,消防器材及防护用品完好备用。
(9) 检查低变炉所用填料、触媒,升温用CS2均己到货,并清点其型号、规格、数量是否符合要求,生产厂家也需出具产品质量、性能文件等。
检查触媒、填料层上、下铺的钢丝网,耐火球是否齐全,品种、数量是否一致。
(10) 硫化方案是否已到岗位。
(11) 二硫化碳贮罐严禁有油污,所沾油可用热碱水或二硫化碳清洗;并经耐压(0.5MPa)试验,确保所有连接阀门无泄漏。
(12) 硫化用的胶管要用有纤维内网的煤气塑料管,一定要检查带壁中有否线网。
无线网者为伪劣商品,极易被二硫化碳溶胀而堵塞。
或者使用Φ10的纤维内网的塑料水管。
2. 升温硫化方案
硫化用二硫化碳作硫化剂,可用放空或循环硫化法,硫化过程中系统尽量常压,严防蒸汽和水进入。
升温硫化方案表如下:
阶段时间 h 空速h-1 床层温度℃加CS2量l/h 备注
升温期 4~6 200-300 200-220 用半水煤气置换系统、然后启动电炉
硫化期~16 200-300 200-300 40-100 侍出口气体中H2S>3g/ m3。
床层穿透。
强化期~12 200-200 350-450 60-120 要求出口气体中H2S>10g/m3。
降温
置换 4~6 200-300 180-200 直至出口硫化氢含量≤1g/m3。
,并入系统。
说明:每2小时分析变换炉出口气H2S浓度一次,当H2S>3 g/NM3,每1小时分析一次;每半小时分析一次O2含量。
3. 硫化操作
3.1. 硫化准备
硫化升温前先用惰性气体再通入煤气置换系统,注意各死角及升温管线的置换。
3.2. 升温期
常温~210℃(4~6h)。
(1) 用惰性气、半水煤气置换合格后转为半水煤气升温,半水煤气走硫化的工艺流程。
保持系统常压,电炉出口温度恒定在230~250℃,此时低变炉进口温度达~210℃,床层温度为210℃~常温。
(2) 升温期间,煤气中O2<0.5%,防止电加热器起火爆炸,严格控制系统压力不得超过0.1MPa,以防电加热器超压。
(3) 在煤气升温结束前,硫化罐应按要求装填好CS2,检查制氮机所送管线是否通畅,升压至0.1~0.2MPa备用。
3.3. 硫化期
(1) 待低变炉进口温度达210℃,即可用N2将CS2压入系统,用硫化罐出口流量计控制CS2加入量,保证入炉CS2浓度为5~10g/m3,开始硫化。
(2) 控制电炉出口温度200~250℃。
催化剂床层温度200~300℃,时间约为8~10小时,待于出口硫化氢≥ 3g/NM3,可认为硫化初期结
束。
(3) 硫化时密切注意床层温度,用电加热器组数、CS2加入量及煤气量等调节床层温度。
(4) 硫化时炉进口H2含量应保证≥25%,便于CS2氢解。
3.4. 强化期
催化剂层各点为400~450℃,保持~4小时出口H2S含量≥10g/NM3,强化硫化结束。
3.5. 降温置换阶段
(1) 硫化至各段均进入降温置换阶段,控制电炉出口温度200℃,待床层温度降至≤300℃,然后停止加 CS2置换。
(2) 联系检修拆、加盲板后,即可导气制合格变换气开车。
(3) 变换常压放空运行两小时后至变换气成分合格后方可向后工序送气。
(4) 注意事项:
(1) 升温硫化严格按要求进行,升温期间,单点温度不得超过500℃,升温速率严格按30∽50℃/h进行。
(2) 硫化过程中,严格控制进口煤气中O2%,严防O2含量跑高造成炉温急骤上升,烧毁触媒, CS2也需根据进口H2S含量及时加减,以防加入过多,炉温急剧上升,或加入过少,硫化太慢。
(3) 发现温度有暴涨趋势,应立即查明原因,并作预见性调节,以防烧坏触媒。
(4) 要严格注意排冷凝水后才能进入后设备。
(5) 整个硫化过程为常压操作。
(6) 系统启运电炉必须先检查是否冷却水,然后通气,最后启动,停车时,先停电炉后切气。
热水加热器、软水加热器需先通水再送气。
(7) 操作人员必须熟悉工艺流程,阀门位置及各副线。
(8) 半水煤气升温时,需注意及时排放油水分离器导淋及投运除油过滤器,以防水带入电炉及触媒层。
(9) 硫化过程中,如遇CS2着火,O2含量跑高、断脱盐水等意外情况,应立即“三停一关”,即停电炉,停CS2,停煤气,关放空。
(10) 认真填写升温记录表。
附:硫化原理
B303Q催化剂是一种钴钼系耐硫低温催化剂,其主要组分为:氧化钴(CoO)、三氧化钼(MoO3)。
在使用前需要将其活化—硫化,使氧化态的钴、钼转化为硫化物,才具有高活性。
具体方法是以半水煤气为载体,以二硫化碳为硫化剂,在180-200℃以上连续加入CS2与氢气发生氢解反应生成H2S,与CoO、MoO3反应生成CoS、MoS2。
化学反应为:
MoO3+2H2S+H2=MoS2+3H2O ΔH0=-48.2KJ/mol
CoO+H2S=CoO+H2O ΔH0=-13.4KJ/mol
CS2+H2=2 H2S+CH4 ΔH0=-240KJ/mol。