铁型覆沙铸造工艺
覆膜砂铸造材料及工艺知识大全
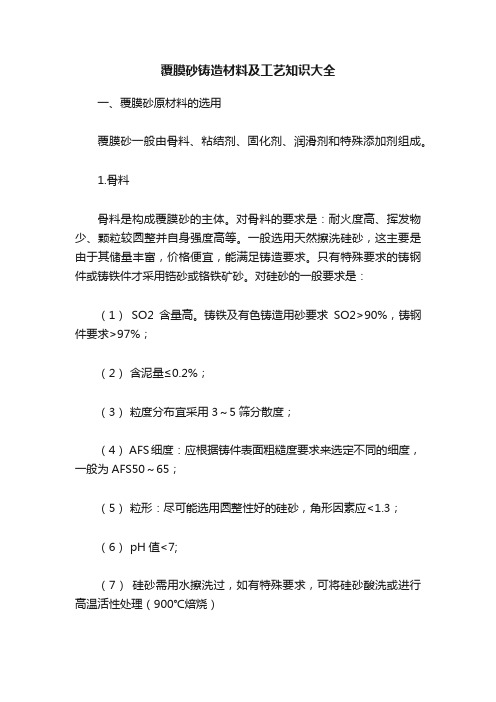
覆膜砂铸造材料及工艺知识大全一、覆膜砂原材料的选用覆膜砂一般由骨料、粘结剂、固化剂、润滑剂和特殊添加剂组成。
1.骨料骨料是构成覆膜砂的主体。
对骨料的要求是:耐火度高、挥发物少、颗粒较圆整并自身强度高等。
一般选用天然擦洗硅砂,这主要是由于其储量丰富,价格便宜,能满足铸造要求。
只有特殊要求的铸钢件或铸铁件才采用锆砂或铬铁矿砂。
对硅砂的一般要求是:(1)SO2含量高。
铸铁及有色铸造用砂要求SO2>90%,铸钢件要求>97%;(2)含泥量≤0.2%;(3)粒度分布宜采用3~5筛分散度;(4) AFS细度:应根据铸件表面粗糙度要求来选定不同的细度,一般为AFS50~65;(5)粒形:尽可能选用圆整性好的硅砂,角形因素应<1.3;(6) pH值<7;(7)硅砂需用水擦洗过,如有特殊要求,可将硅砂酸洗或进行高温活性处理(900℃焙烧)2. 粘结剂目前普遍采用酚醛类树脂作为粘结剂。
酚醛类树脂有固体和液体、热固性和热塑性之分。
目前制作覆膜砂通常采用热塑性固态酚醛树脂。
对其性能要求是:(1)聚合速度(热板法):25~27s ;(2)软化点(环球法):90~105℃;(3)流动性(斜板法):60~110mm ;(4)游离酚含量(溴化法):≤4%。
粘结剂的性能对覆膜砂的品质有很大的影响,人们一直在致力于研究如何提高酚醛树脂的性能,以及寻找酚醛树脂的替代品。
国外已开发出不同性能的专用树脂,如高强度低发气树脂、易溃散树脂,也有采用改性聚酯树脂的报道,但未得到全面推广,至今普遍采用的仍是改性酚醛树脂。
国内近年来在覆膜砂专用酚醛树脂的研究开发方面发展较快,已开发出不同的改性酚醛树脂供生产使用。
3. 固化剂、润滑剂、添加剂固化剂通常采用乌洛托品即六亚甲基四胺,分子式为(CH2)6N4,要求为工业一级品。
润滑剂一般采用硬脂酸钙。
其作用是防止覆膜砂结块,增加流动性,使型、芯表面致密及改善砂型(芯)的脱模性。
添加剂的主要作用是改善覆膜砂的性能。
铁型覆砂工艺,生产铸态QT450-10高韧性球墨铸铁

铁型覆砂工艺,生产铸态QT450-10高韧性球墨铸铁摘要:论述了铁型覆砂工艺条件下铸态QT450-10高韧性球墨铸铁的生产,分析了铸造材料、球化处理、冷却时间等主要工艺因素对铸件延伸率的影响,工艺优化后可以使铸件延伸率达到12-23%。
关键词:铁型覆砂工艺;高韧性球墨铸铁;原材料;球化处理;延伸率 1 前言铁型覆砂工艺生产的铸件因外观光洁、内部致密、尺寸精确逐步受到欢迎,逐渐成为众多轮毂厂家的选择,主要材质为QT450-10,全部采用这种工艺,但在生产过程中经常出现强度高、延伸率低、稳定性差的问题,本文与实际生产现场结合,通过对工艺的优化和调整使铸件本体延伸率稳定达到12%以上、综合成品率由94.53%提升至97%,成功解决了生产过程中的难题。
2 化学成分与原材料公司汽配产品已批量生产多年,熔炼设备采用1吨中频电炉,外购生铁和废钢,原材料配比基本固定,原铁水化学成分如表1:表1 原铁水化学成分炉次 C Si Mn P S1 3.82 1.26 0.34 0.029 0.0262 3.84 1.37 0.31 0.035 0.0313 3.84 1.27 0.33 0.032 0.0254 3.83 1.33 0.31 0.033 0.025 3.83 1.4 0.41 0.040 0.036 3.85 1.35 0.35 0.035 0.0247 3.79 1.4 0.3 0.033 0.0248 3.85 1.37 0.33 0.037 0.0279 3.84 1.37 0.40 0.036 0.02610 3.80 1.22 0.37 0.042 0.032从表1可以看出:生产过程中原铁水Mn、S含量波动较大,部分炉次Mn、S含量较高,在铸态高韧性QT450-10中,锰能阻碍共析转变的石墨化,增加、稳定和细化珠光体,部分锰也可以固溶入铁素体中,提高强度并降低韧性,增加结晶过程的过冷倾,对韧性影响很大,因此锰含量应越低越好。
四缸发动机曲轴铁型覆砂铸造工艺

球径 ≤6 0 g m, 铁 素 体 数 量 5 %~ 2 0 % , 牛 眼 状 铁素 体 数 量 ≥1 5 % 。 经 调 研 及 分 析 比 较 ,确 定 采 用 铁 型 覆 砂 铸 造 工 艺 ,预 计 年 产 量 4 5 万件 。 根 据 该 系 列 曲轴 的 结 构 特 点 , 结 合 生 产 节 拍和产 能要 求 ,每型 布置 6 件 。 按 同 时 凝 固 的 原 则 , 铁 液 从 中 间 的 两 个 平 衡 块 进 入 型 腔 , 不 设 置 补 缩 冒 口[ 1 - 3 ] 。 为 保 证 铸 件 有 较 合 理 的 冷 却 速 度 ,设计 造型 覆砂 层厚度 8 ~1 2 mm, 铁 型 壁 厚
( L i u z h o u Wu l i n g L i u j i P o we r C o . , L t d . , L i u z h o u 5 4 5 0 0 5 , Gu a n g x i , C h i n a )
Ab s t r a c t :T h e c a s t i n g p r o c e s s o f me t a l mo l d wi t h s a n d l i n e r f o r f o u r . c y l i n d e r e n g i n e c r a n k s h a f t wa s i n t r o d u c e d . T h e t e c h n o l o g i c a l p a r a me t e r s ,i n c l u d i n g mo l d i n g , me l t i n g , s p h e r o i d i z i n g , p o u r i n g a n d c l e a n i n g , we r e d e t e r mi n e d . T h e q u a l i t y c o n t r o l l i n g f a c t o r s t h r o u g h e a c h p r o d u c t i o n p r o c e s s we r e c l a r i i f e d . By u s i n g t h e me t a l mo l d wi t h s a n d l i n e r p r o c e s s i n l o we r c o s t , he t c a s t i n g s wi t h s mo o t h s u r f a c e , a c c u r a t e s i z e a n d h i g h p e r or f ma n c e a r e p r o d u c e d t o me e t he t c u s t o me r r e q u i r e me n t s . Ke y wo r d s : me t a l mo l d wi h t s a n d 1 i n e r ; d u c t i l e i r o n ; c r a n k s h a f t ; c a s t i n g p r o c e s s
铁型覆砂工艺设计及常见缺陷防止

铁型覆砂工艺设计及常见缺陷防止铁型覆砂工艺是一项先进的生产球铁件工艺,该工艺开始用于单缸曲轴s195的生产,现在已可以生产六缸曲轴,并且在6110曲轴上取得成功,在其它铸件如凸轮轴、阀体、水泵泵体、刹车嵌等铸件上也广泛应用。
1工艺参数该工艺涉及的主要参数有:收缩率,铁型壁厚,覆砂层厚度及射砂孔位置、形状、大小和数量,铸型温度,浇注系统设计以及铸件本身工艺上的要求。
1.1收缩率一般取收缩率为0.8%~1.O%。
1.2铁型壁厚及材质铁型壁厚对铸件的冷却能力、蓄热能力及铁型本体的刚度及防止变形、开裂有很大的影响。
铁型覆砂的铁型壁厚与普通金属型的设计有些区别,但两者的工作条件都较恶劣,冷热交换且温差变化都很大,因此两者对刚性和强度的要求均较高。
但金属型铸造由于高温铁液直接冲刷型壁,寿命短,易开裂。
铁型覆砂由于在金属型内腔覆上厚度为5~8,1111"1的砂层,并利用模具的加热热量将其固化,生产中将铁型的温度控制在180~300~(:范围内,所以铁型的寿命较金属型长,且具有可形成流水线生产的优点。
铁型温度的高低,与开型时间、覆砂层厚度及金属型的壁厚、工件长度有关。
壁厚大的铁型蓄热多,温度上升缓慢,铸件冷却快,开型时间短,从浇注到开型约12~15min(对于6110曲轴约需20min)。
金属型温度小于300%:,即能满足工艺要求。
据经验公式:铁型壁厚/4型=(O.6~0.8)A件,其中^4件为铸件壁厚。
6110曲轴扇板壁厚为60mm,这样铁型壁厚-4型=(().6~0.8)A件×60=36~48(Inm)。
也可根据铸型分型面尺寸平均值来选取(见下表)。
铸型分型面尺寸平均值S按下式计算:Ls=(H也)/2,其中Ⅳ为分型面长度尺寸(mm),L为分型面宽度尺寸(mm)。
对于铁型,其材料应满足下列要求:耐热性和导热性好,反复受热不变形;具有一定的强度、韧性和耐磨性;机加工性好。
在实际生产中,灰铸铁用的最多,因铸铁加工依据铸型分型面尺寸选取金属型壁厚glnl┏━━━━━━━━━━━━━━━━━━━━━┓┃00脚蛹戆蠖国锚舀曩◇{0lllij黛癣哟黪0i_j?0 ┃┣━━━━━━━┳━━━━━━━━━━━━━┫┃ <130 ┃ 15—20 ┃┣━━━━━━━╋━━━━━━━━━━━━━┫┃ 130~175 ┃ 15H20 ┃┃ ┣━━━━━━━━━━━━━┫┃ ┃——┃┃ 175~200 ┃ 2()屯 5┃┣━━━━━━━╋━━━━━━━━━━━━━┫┃ 200—5(10 ┃ 25—00 ┃┃ 500—800 ┃ 30~35 ┃┣━━━━━━━╋━━━━━━━━━━━━━┫┃ >800 ┃ 35~45 ┃┗━━━━━━━┻━━━━━━━━━━━━━┛性好、价廉,一般工厂均能自制,并且它又耐热、耐磨,是一种较合适的铁型材料,但长时间使用易出现开裂现象。
曲轴铁模覆砂铸造及其生产过程控制

曲轴铁模覆砂铸造及其生产过程控制作者:山东滨州海得曲轴有限责任公司尹士文曲轴是发动机的关键零部件之一,其性能好坏直接影响发动机的使用性能和寿命。
曲轴工作时承受着交变大负荷的弯矩、扭矩和冲击,常见的失效形式为弯曲疲劳断裂及轴颈磨损,因此要求曲轴材质具有较高的刚性和疲劳强度以及良好的耐磨损性能。
特别是最近几年涡轮增压发动机应用的增多,对曲轴内在质量和毛坯精度及毛坯面的粗糙度提出了越来越高的要求。
图1 铁型铁型覆砂铸造是在随型的铁型内腔(见图1)均匀覆上一层5~8mm热固化型砂而形成铸型的一种铸造工艺(见图2)。
由于铁模覆砂铸型刚度好且覆砂层比较薄,铸件冷却速度快,砂子粒度细(一般为200目),因此可显著提高铸件的尺寸精度、致密性、表面质量、晶粒的细化程度和球化率,同时可实现无冒口铸造。
图2 铁型覆砂铁模覆砂线的生产过程铁模覆砂线的生产工艺流程如图3所示。
现在铁模覆砂线的工艺布置有多种形式,以开式线形式布置居多。
因为它可以满足曲轴多品种生产冷却时间不同的要求,同时可方便地实现生产过程中铁型移动和铁型推进的机械化和自动化控制。
1.覆砂造型覆砂造型过程是铁模覆砂铸造的关键工序,它直接影响到生产的全过程和曲轴成品率的高低。
最初的铁模覆砂都是借用热芯盒射芯机,机械化程度低。
现在国内已有不少的铸造机械厂家生产专用的铁模覆砂设备,有的已可实现从合模到射完砂铁型移出的全过程PLC触摸屏全自动控制。
(1)铁型温度正常生产过程中铁型温度一般控制在230℃左右。
过低时覆膜砂不能完全固化,壳型强度低且发气量大;过高时型壳烧酥或是覆膜砂在流动的过程中就已固化,破坏型壳强度易造成曲轴粘砂和夹砂。
铁型第一次使用的加热一般有两种方法;一是把成批的铁型放入芯子窑中加热,然后逐一进行造型;二是逐一把凉铁型合模后通过模样和模板对铁型进行加热(模板上装有电热管)进行造型,这种方法新铁型第一次生产时速度比较慢。
正常生产过程可利用铁型的余热进行覆砂,不需要单独加热。
铁型覆膜砂铸造工艺
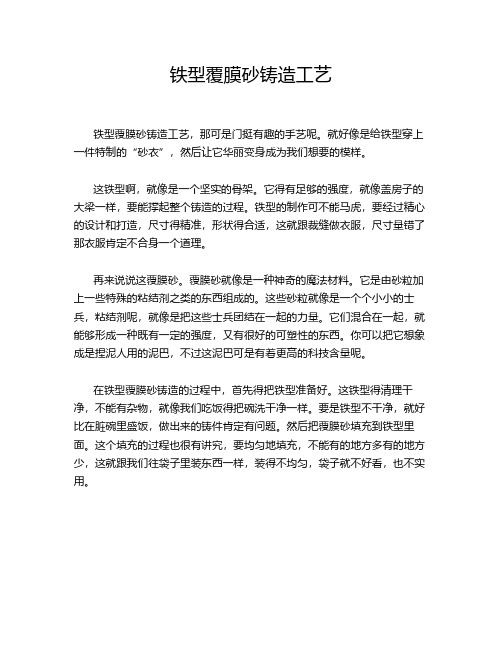
铁型覆膜砂铸造工艺铁型覆膜砂铸造工艺,那可是门挺有趣的手艺呢。
就好像是给铁型穿上一件特制的“砂衣”,然后让它华丽变身成为我们想要的模样。
这铁型啊,就像是一个坚实的骨架。
它得有足够的强度,就像盖房子的大梁一样,要能撑起整个铸造的过程。
铁型的制作可不能马虎,要经过精心的设计和打造,尺寸得精准,形状得合适,这就跟裁缝做衣服,尺寸量错了那衣服肯定不合身一个道理。
再来说说这覆膜砂。
覆膜砂就像是一种神奇的魔法材料。
它是由砂粒加上一些特殊的粘结剂之类的东西组成的。
这些砂粒就像是一个个小小的士兵,粘结剂呢,就像是把这些士兵团结在一起的力量。
它们混合在一起,就能够形成一种既有一定的强度,又有很好的可塑性的东西。
你可以把它想象成是捏泥人用的泥巴,不过这泥巴可是有着更高的科技含量呢。
在铁型覆膜砂铸造的过程中,首先得把铁型准备好。
这铁型得清理干净,不能有杂物,就像我们吃饭得把碗洗干净一样。
要是铁型不干净,就好比在脏碗里盛饭,做出来的铸件肯定有问题。
然后把覆膜砂填充到铁型里面。
这个填充的过程也很有讲究,要均匀地填充,不能有的地方多有的地方少,这就跟我们往袋子里装东西一样,装得不均匀,袋子就不好看,也不实用。
在填充完覆膜砂之后呢,就得进行紧实的操作了。
这个紧实就像是给已经站好队的士兵再加固一下防线一样。
紧实的程度得合适,太松了,做出来的铸件可能就会有孔洞,就像盖房子的时候砖头没砌好,墙上会有窟窿一样。
太紧了呢,又可能会导致其他的问题,就像是把东西塞得太满,盒子会被撑破。
接下来就是加热和硬化的过程了。
这就像是给已经穿上砂衣的铁型来一场火热的洗礼。
在合适的温度下,覆膜砂中的粘结剂就会发生反应,让整个覆膜砂变得更加坚硬。
这个温度的控制可太关键了,就像烤蛋糕一样,温度高了或者低了,蛋糕都做不好。
要是温度没控制好,这覆膜砂可能就不能很好地硬化,那最后的铸件质量肯定就不行。
脱模也是一个重要的环节。
这就像是把已经做好的模型从模具里取出来。
铁型覆膜砂工艺

铁型覆膜砂工艺哎呀,说起铁型覆膜砂工艺,这可真是个技术活儿,得慢慢道来。
这玩意儿,说白了,就是铸造行业里的一个小技巧,让铸件表面光滑,质量更上一层楼。
记得有一回,我去了一家铸造厂,亲眼见识了这铁型覆膜砂工艺的神奇。
那天,阳光正好,我跟着师傅走进了车间,一股热浪扑面而来,那感觉,就像走进了桑拿房。
师傅一边走一边给我介绍,说这铁型覆膜砂工艺啊,关键在于覆膜砂的选择和处理。
覆膜砂,听起来挺高大上的,其实就是砂子外面裹了一层膜。
这膜可不是随便什么膜,得是耐高温、抗磨损的那种。
师傅说,这膜得选好,不然铸件表面就会有缺陷,那可就麻烦大了。
接下来,就是覆膜砂的准备过程。
师傅带着我,看着工人们把覆膜砂倒进一个巨大的搅拌机里。
那机器轰隆隆地转着,覆膜砂在里面翻腾,看得我眼花缭乱。
师傅说,这搅拌得均匀,覆膜砂才能均匀地覆盖在模具上。
搅拌好了,就该上模具了。
师傅领着我走到一个巨大的铁型模具前,那模具比我人还高,看着就挺震撼的。
工人们把搅拌好的覆膜砂均匀地倒在模具上,然后用一个巨大的刮板,把覆膜砂刮平。
那动作,那叫一个熟练,看得我目瞪口呆。
覆膜砂处理好了,就该浇铸了。
师傅说,这浇铸可是个技术活,温度、速度都得控制好,不然铸件就废了。
我看着工人们把熔化的铁水倒进模具,那铁水红彤彤的,冒着热气,感觉能把人烤熟。
浇铸完了,就是冷却和脱模。
这个过程得等,等铁水冷却凝固。
我在旁边等着,心里那个急啊,就像等烤红薯出炉一样。
终于,冷却好了,工人们小心翼翼地把铸件从模具里取出来。
那铸件表面光滑,一点瑕疵都没有,看着就让人满意。
最后,师傅还给我讲了这铁型覆膜砂工艺的好处。
他说,这工艺不仅能提高铸件的质量,还能减少废品率,降低成本。
我听着,心里那个佩服啊,这技术,真是了不起。
总之,这铁型覆膜砂工艺,真是个神奇的技术。
它让铸件表面光滑,质量更上一层楼。
虽然过程复杂,但看到最后的成果,那点辛苦都值了。
这技术,真是铸造行业的宝贝啊。
铁型覆砂铸造的工艺特点
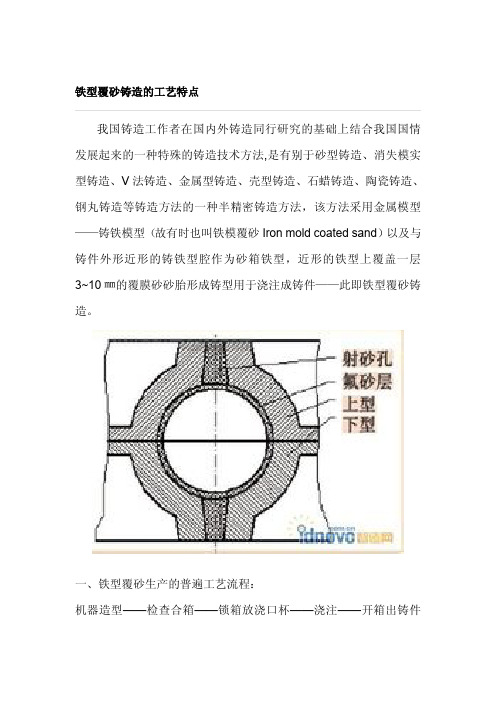
铁型覆砂铸造的工艺特点我国铸造工作者在国内外铸造同行研究的基础上结合我国国情发展起来的一种特殊的铸造技术方法,是有别于砂型铸造、消失模实型铸造、V法铸造、金属型铸造、壳型铸造、石蜡铸造、陶瓷铸造、钢丸铸造等铸造方法的一种半精密铸造方法,该方法采用金属模型——铸铁模型(故有时也叫铁模覆砂Iron mold coated sand)以及与铸件外形近形的铸铁型腔作为砂箱铁型,近形的铁型上覆盖一层3~10㎜的覆膜砂砂胎形成铸型用于浇注成铸件——此即铁型覆砂铸造。
一、铁型覆砂生产的普遍工艺流程:机器造型——检查合箱——锁箱放浇口杯——浇注——开箱出铸件——清砂——造型二、铁型覆砂铸造的工艺特点:1.铁型覆砂铸造具有砂型铸造的特点,即有一刚性砂型外壳,使得砂型整体强度高、不变形,其适应性广泛,铸件易脱模,并且定位可靠,精度高。
2.铁型覆砂铸造具有覆膜砂壳型铸造的特点,造型方便、快捷、不论什么铸件砂型,二、三分钟之内便可造型完毕,型砂密度、铸型表面硬度等通过设备保证,永远一致,并且不需要涂刷任何涂料。
既得到了光洁的铸件,又提高了铸件的形状和尺寸精度。
3.铁型覆砂铸造还具有金属型铸造的特点,铁的铸型在金属液结晶过程中有明显的冷激作用,可使铸件晶粒度细化,从而提高了铸件的综合强度,同时又由于有砂胎的存在避免了金属型铸造的短处,铸件不会产生白口,对铸铁件而言,可铸态生产各种材质,无需热处理。
4.由铁型和薄的砂胎组成的铸型锁紧后刚度高、变形小、冷却快,得到的铸件尺寸精度高、加工余量小、组织致密,特别适合球墨铸铁的生产,在生产球墨铸铁时能利用球墨铸铁的石墨化膨胀对铸件进行自补缩——实现球墨铸铁的少、无冒口铸造,得到优质铸件;因为铁型冷却快,对生产高牌号的珠光体基体的盘类、杆类、轴类铸件尤其有利。
5.一般情况下铁型覆砂生产的铸件硬度比普通铸造方法生产的铸件要高20个HB单位左右。
6.利用铸件浇注后铁型的余热进行再循环生产的覆膜砂固化,不只减少了用电,而且铸造过程呈现封闭式循环生产状态,生产占用面积很小(例如,一小时熔炼一吨铁(钢)水时,造型浇注面积有二、三百平方米就足够了),不需要砂处理设备,投资少、见效快。
铁型覆沙铸造工艺

铁型覆砂铸造技术在国外早有研究应用,1955年由美国铸铁管公司研究成功并用mono—cast法生产离心铸管。
后来我国一些科研单位和工厂也相继研采用铁型覆砂铸造工艺生产球铁曲轴,凸轮轴,阀体,水泵壳等铸件取得成功并广泛应用。
铁型覆砂工艺是利用铸造粗成形的铁型内腔(芯铁)表面覆上一层很薄的树脂砂衬所形成的铸型生产铸件的工艺。
这一工艺主要优点是铁型表面覆上一层树脂砂衬后的铸型,在浇注时的工作条件大为改善,能够有效地承受高温铁液的热冲击,型内的最高温度可由600%降低到2oo℃左右,铁型厚度方向上的温度梯度也大为降低,铁型的热应力明显降低,这对提高铁型的使用寿命非常有利,使用寿命可高达十几万次。
同时由于铁型覆砂的铸型有足够的强度和刚度,覆砂层硬度高(9O以上),可避免铸件出现胀砂、砂等缺陷,可生产重量较大的铸件。
对于球铁可充分利用铁液凝固时石墨膨胀的特性,消除缩孔、缩松等缺陷。
本工艺是在覆砂造型机上对准铁型射砂孔射砂造型,在0.4MPa压缩空气下,利用颗粒动力学原理气砂两相的动能作用,使射砂筒内射人铁型内腔的砂流连续、稠密,在短时间受热硬化。
因此覆砂层的硬度大且均匀,浇注后可获得比普通砂型铸件表面光洁、(粗糙度可达尺.12.5左右)尺寸精确(CT6—7级)、内部组织致密的铸件。
而且由于覆砂层的绝热性能,型腔又有一定的预热温度,完全可以在铁型覆砂条件下生产符合国际标准的铸态铁素体管件。
此工艺可与树脂砂和消失模铸造相媲美,可比水玻璃砂刮板造型提高生产效率lO倍以上,降低废品率10%以上,在标准允许的情况下可减轻铸件重量10%以上,减少工人25%~30%,降低生产成本10%以上,管件后处理工作量减少70%,型砂用量减少80%,水压试验合格率高达98%以上。
由于大大减少了型砂处理量,车间的环境粉尘污染明显改善,是一项先进的绿色环保铸造技术。
铁型覆砂铸造是在金属型(称为铁型)内腔覆上一薄层型砂而形成铸型的一种铸造工艺。
树酯砂和铁型覆膜砂铸造工艺

(二)铸造车间◆任务和生产纲领承担年产2万吨风电及工程机械零部件的铸件生产任务。
◆设计原则和主要工艺说明1.产品生产性质、特点本车间属批量生产。
最大铸件为30吨,材料为球铁。
2.主要工艺说明及设备选用原则树脂自硬砂工艺是国际二十世纪八、九十年代以来的最新铸造先进工艺之一,采用树脂砂工艺生产的铸件,表面光洁度好(可以达到Ra12.5-25),尺寸精确(可以达到CT7-9级),生产效率可比粘土砂工艺提高一倍以上,旧砂回用率可达95%以上,改善了铸造车间的工人作业环境,特别适合单件小批量铸件的生产,该工艺技术的先进性和优越性已为广大铸造工作者所共识。
在树脂砂工艺中,尤以呋喃树脂砂工艺和碱酚醛树脂砂工艺使用最为广泛。
采用呋喃树脂砂工艺生产铸件,成本较低。
特选定树脂自硬砂工艺为主要的生产工艺。
a. 熔炼设备熔炼采用12、15t 中频电炉两套(配用电源总功率10000kW。
考虑浇注大件铸件的可行性)b. 混砂造型车间新增60t/h遥控升降式树脂砂混砂机1台,40t/h的树脂砂混砂机2台,10t/h的树脂砂混砂机1台。
c. 落砂机和砂再生采用二套20t落砂和二套20t/h砂处理设备。
落砂机的承载能力为20t,落砂机为采用振动电机进行落砂的新型落砂机。
再生系统为20-30t/h,由两套20t/h和30t/h的再生系统并联组成,主要由以下几大功能设备组成:振动破碎再生机+二级强力再生机+风选机+砂温调节器+PLC电气控制系统。
整套砂处理系统为强力硬再生技术,旧砂再生回用率可达95%以上。
该套系统消化吸收国外先进技术后研制开发的,目前已在国内外二百余家企业使用,用户反映良好,已成为中国知名品牌。
(三)清理车间◆任务和生产纲领清理车间将承担铸件的清理工作。
◆设计原则和主要工艺说明1.产品生产性质、特点本车间属批量生产。
最大件为机床底座。
2.设备选用原则本清理车间主要解决树脂砂车间生产的铸件清理。
新增台车式抛丸清理室(30t、50t各1台)、8-10t吊钩式抛丸清理机3台,新增1座40m3煤气发生炉。
铁型覆砂工艺及其装备的发展状况

铁型覆砂工艺及其装备的发展状况铁型覆砂工艺发达国家在60年代已开始使用,主要生产曲轴、连杆,凸轮轴,刹车毂,汽缸套等铸件,运用铁型覆砂的企业都取得了明显的经济效益。
我国运用这一工艺较国外稍晚,但发展速度很快,就目前来看,与国外运用这一工艺相比,没有很大差別,特别是近几年,铁型覆砂装备发展非常迅速,主要应用在曲轴(包括汽车、摩托车、压缩机小曲轴),凸轮轴、缸套、轮毂、制动鼓、缸体、缸盖、电梯曳引轮电梯机座以及高牌号的球铁件等,铸件运用这一工艺生产出来的铸件,可以提高铸件的工艺出品率,不管是内在质量还是表面质量都很高,机械性能明显提高,可以显著提高球铁的牌号,用户普遍反映良好。
●铁型覆砂铸造工艺铁型覆砂铸造是在粗成的金属型(铁型)内腔上通过热固化,覆上一层型砂(覆膜砂)形成铸型,铁水浇注在覆膜砂型中,形成铸件。
在设计铁型时需要经过反复模拟试验及工艺试验和生产验证,合理确定铁型重量、壁厚、覆砂层厚度及浇注系统,使铸件的充型、凝固和冷却在一个比较理想的条件下完成。
●与砂型铸造相比在铁型覆砂工艺应用以前,国内生产曲轴等大批量球铁铸件,大都采用粘土砂造型生产,很难实现无冒口铸造,而铁型覆砂铸造工艺真正实现了无冒口铸造,这主要由于铁型钢性好,冷却速度快,在浇注和凝固过程中变形小,通过对内浇口的设计,能利用球铁在凝固过程中的石墨化膨胀抵消铸件的线收缩和体收缩,使缩孔和缩松无法形成,铸件本体致密,减少废品率,提高工艺出品率。
铸态珠光体球铁,其晶粒细小,组织致密,晶核间形成裂纹倾向小,强度髙,是一般球铁铸件所期望的组织。
而砂型铸造要得到这一组织.必须严格控制铁液化学成分,生产稳定性极差,铁型覆砂铸造由于铁型导热性好,透过覆砂层快速吸收热量,使石墨细化,共晶团增加,球铁本体机械性能可达到很高的球铁牌号要求,铸件废品率下降,质量大大提高,据使用这一工艺生产曲轴的用户反映,在砂型铸造时,其废品率一般达到10-20%,而运用铁型覆砂铸造,废品率在5%以内,有时仅为1%,而且铸件的外观质量大大提高,加工余量明显减少,生产成本明显下降。
铁模覆砂铸造工艺
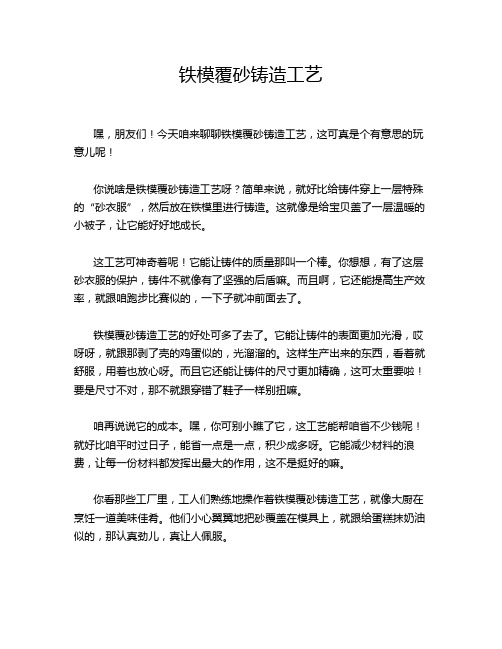
铁模覆砂铸造工艺嘿,朋友们!今天咱来聊聊铁模覆砂铸造工艺,这可真是个有意思的玩意儿呢!你说啥是铁模覆砂铸造工艺呀?简单来说,就好比给铸件穿上一层特殊的“砂衣服”,然后放在铁模里进行铸造。
这就像是给宝贝盖了一层温暖的小被子,让它能好好地成长。
这工艺可神奇着呢!它能让铸件的质量那叫一个棒。
你想想,有了这层砂衣服的保护,铸件不就像有了坚强的后盾嘛。
而且啊,它还能提高生产效率,就跟咱跑步比赛似的,一下子就冲前面去了。
铁模覆砂铸造工艺的好处可多了去了。
它能让铸件的表面更加光滑,哎呀呀,就跟那剥了壳的鸡蛋似的,光溜溜的。
这样生产出来的东西,看着就舒服,用着也放心呀。
而且它还能让铸件的尺寸更加精确,这可太重要啦!要是尺寸不对,那不就跟穿错了鞋子一样别扭嘛。
咱再说说它的成本。
嘿,你可别小瞧了它,这工艺能帮咱省不少钱呢!就好比咱平时过日子,能省一点是一点,积少成多呀。
它能减少材料的浪费,让每一份材料都发挥出最大的作用,这不是挺好的嘛。
你看那些工厂里,工人们熟练地操作着铁模覆砂铸造工艺,就像大厨在烹饪一道美味佳肴。
他们小心翼翼地把砂覆盖在模具上,就跟给蛋糕抹奶油似的,那认真劲儿,真让人佩服。
咱普通老百姓可能不太了解这工艺,但咱生活中的好多东西可都是通过它生产出来的呢。
说不定你家里的某个小物件,就是铁模覆砂铸造出来的哟!你说神奇不神奇?铁模覆砂铸造工艺就像是一个默默无闻的英雄,在背后为我们的生活提供着各种优质的产品。
它虽然不被大家所熟知,但却发挥着巨大的作用。
我们真应该好好感谢它呀!总之,铁模覆砂铸造工艺是个了不起的工艺,它为我们的生活带来了很多便利和惊喜。
让我们一起为它点赞吧!。
铁型覆砂铸造工艺技术及生产线

铁型覆砂铸造工艺技术及生产线一、简介铁型覆砂是铸造行业的一项新工艺、新技术。
它是在粗成形的金属型(称为铁型)内腔覆上一薄层型砂而形成铸型,经反复的工艺试验和生产验证后,将铁型的重量、壁厚与覆砂层厚度合理地配合,使铸件的充型、凝固和冷却过程在一个比较理想的条件下完成。
这样,就最大限度地消除了铸件产生铸造缺陷的大部分因素,大大提高了铸件的质量。
其次,在实际生产中实现球铁件的铸态生产和无冒口铸铁,因此简化了生产工序和节约了生产成本。
此外,用砂量极少,铸造车间一般都不设砂处理工部,减少了设备投资,又改善了铸造车间的劳动条件。
该工艺最重要的优点是节能、节材、优质。
目前我院已为国内二十多个省市自治区的60几家企业设计建成了80余条铁型覆砂铸造生产线用于曲轴、凸轮轴、平衡轴、缸套、液压阀、壳体、齿轮等铸件的大批量生产,本项目七次获国家、省(部)级科技进步奖,是国家和机械部“八五”“九五”重点新技术推广计划项目。
我院是该项目的技术依托单位。
二、社会经济效益与砂型铸造相比,生产成本降低20%;节约型砂90%以及不需设砂处理工部;实现了无冒口铸造,工艺出品率在90%以上;提高球化等级1-2级,铸态性能达QT800;显著改善了铸造车间的劳动条件。
三、合作方式1、委托设计和咨询:项目规划,生产线及工装模具设计;2、工程承包:提供生产线及工装模具全套设备、调试、培训直至试生产。
3、另可提供3种型号的小型射芯机。
联系人:黄列群*************潘东杰*************温州市新城数码城1805室浙江省机电设计研究院温州分院姚兴海Tel:*************,135****5501Fax:*************E-mail:**************。
铁模覆砂工艺铸造排气管(百度文库)

-23-
感谢亲观看此幻灯片,此课件部分内容来源于网络, 如有侵权请及时联系我们删除,谢谢配合!
1:按照覆砂层厚度为10mm,则 铸件在共析点放出的热量使得覆砂层 温度可以升高到718℃;
2:按照覆砂层厚度为8mm,则 铸件在共析点放出的热量使得覆砂层 温度可以升高到847℃;
-17-
铁型设计
公司图标
8mm覆砂层会升 高到此温度,高于共 析点
共析温度
10mm覆砂层会升 高到此温度,和共析 点接近
21d25mm铁型设计模具装在造型主机公司图标装好坭开箱出来的铸件22总结公司图标总结自补缩能力强等特点铸件组织致密缩孔缩松废品率大大降低并且对比潮模戒者树脂砂方式生产的排气管铁模覆砂工艺由于具备冷却快尺寸准确变形小原材料和生产成本较低
薄壁排气管铸件的 铁模覆砂工艺
二零一三年八月
内容提要
1:薄壁排气管铸件介绍 2:当前国内铸造工艺优缺点概述 3:铁模覆砂工艺介绍 4:模具设计 5:铁型设计 6:现场工艺控制 7:质量状况 8:总结
公司图标
一、薄壁排气管铸件介绍
-2-
目录
公司图标
车用无水冷排气管是一种薄壁小件,毛坯重量6-8千克,壁厚4.5-6mm,通常 牌号有QT450-10、RuT300、RuTSi4Mo、QTSi4Mo等
-3-
公司图标
材 质:RuT300
组 织:蠕化率≥50% ,F+P
拉伸强度:≥300MPa 延 伸 率:≥1.5%
为了确定排气管铸件的覆砂层厚度,我们做了下面的模型具体分 析。
-15-
铁型设计
为了确定覆砂层厚度,我 们从排气管壁厚切取
10*10mm单元,做定量 分析
公司图标
用覆砂铁型铸造工艺生产球铁列车刹车盘

用覆砂铁型铸造工艺生产球铁列车刹车盘摘要:本文对各种铸造球铁刹车盘的工艺进行了介绍,并对覆砂铸铁工艺和粘土砂湿法铸造工艺进行了实验比较。
结果显示,粘土砂湿法铸件球有缩孔缺陷,但是球少、球化率低;覆砂铸铁件球化无缩松缺陷,特点是球多、球化率高,经过大量生产的覆砂铁型工艺,铸件质量稳定。
关键词:覆砂铁型;铸造工艺;球铁;列车刹车盘汽车底盘的重要安全部件是轮毂球墨铸铁铸件。
当前,大部分采用粘土砂湿法制造,这些部位的热接点分散,壁厚不均匀,而且容易出现缩孔倾向或是缩孔,采用覆砂铁型铸造工艺,对球化等级、铸件效益、粒度、密度等铸件显着改进提高了铸件的整体力学性能覆砂铁型生产线也提高了工人的劳动力、强度和工作环境,减少制造过程中的环境污染,提高生产效率,满足绿色铸造要求,取得明显的社会效益和经济效益。
一、覆砂铁型铸造工艺概念覆砂铁型工艺在模具与铁型(砂箱)内腔之间留有6-10m的缝网,在特定温度下注入覆膜砂并固化,将覆膜砂包覆在模具的内表面,获得模具型腔,并教导如何使用这种覆砂铁型铸件。
其最大特点是高速冷却,铰链式刚性强,可细化铸件晶粒,大幅度提高力学性能。
型腔去除极其刚性,铁型代替了传统的砂箱,在铸件的凝固过程中,可以利用石墨化膨胀阶段模具壁的高刚度来实现自补缩,一个过渡层是覆砂层,由于其厚度,可以通过来改变铸件的冷却速度,可以在适当的范围内调整。
提高冷却速度对缩短珠光体片距和细化晶粒有很大的作用。
二、铁型覆砂工艺特点首先,铁型(砂箱)顺应产品形状,中间圆周覆砂,厚度为6~10mm,成本低,用砂量少。
其次,废砂收集后,送专业厂家回收,完全再利用。
无需投资砂处理设备或场地,环保,成本低。
第三,覆膜砂强度高、致密、铸件尺寸精度高、铁型(铸铁)强度和柔韧性高、组织致密、重量轻、加工余量小、铸件自补缩强,工艺良率高,一般无需设置臂口供给。
第四,铁型导热快,薄砂涂层,铸件冷却快,粒度小,无需添加过多的贵重合金,易获得较高的力学性能。
- 1、下载文档前请自行甄别文档内容的完整性,平台不提供额外的编辑、内容补充、找答案等附加服务。
- 2、"仅部分预览"的文档,不可在线预览部分如存在完整性等问题,可反馈申请退款(可完整预览的文档不适用该条件!)。
- 3、如文档侵犯您的权益,请联系客服反馈,我们会尽快为您处理(人工客服工作时间:9:00-18:30)。
铁型覆砂铸造技术在国外早有研究应用,1955年由美国铸铁管公司研究成功并用mono—cast法生产离心铸管。
后来我国一些科研单位和工厂也相继研采用铁型覆砂铸造工艺生产球铁曲轴,凸轮轴,阀体,水泵壳等铸件取得成功并广泛应用。
铁型覆砂工艺是利用铸造粗成形的铁型内腔(芯铁)表面覆上一层很薄的树脂砂衬所形成的铸型生产铸件的工艺。
这一工艺主要优点是铁型表面覆上一层树脂砂衬后的铸型,在浇注时的工作条件大为改善,能够有效地承受高温铁液的热冲击,型内的最高温度可由600%降低到2oo C左右,铁型厚度方向上的温度梯度也大为降低,铁型的热应力明显降低,这对提高铁型的使用寿命非常有利,使用寿命可高达十几万次。
同时由于铁型覆砂的铸型有足够的强度和刚度,覆砂层硬度高(9O以上),可避免铸件出现胀砂、砂等缺陷,可生产重量较大的铸件。
对于球铁可充分利用铁液凝固时石墨膨胀的特性,消除缩孔、缩松等缺陷。
本工艺是在覆砂造型机上对准铁型射砂孔射砂造型,在0• 4MPa压缩空气下,利用颗粒动力学原理气砂两相的动能作用,使射砂筒内射人铁型内腔的砂流连续、稠密,在短时间受热硬化。
因此覆砂层的硬度大且均匀,浇注后可获得比普通砂型铸件表面光洁、(粗糙度可达尺.12. 5左右)尺寸精确(CT6 —7级)、内部组织致密的铸件。
而且由于覆砂层的绝热性能,型腔又有一定的预热温度,完全可以在铁型覆砂条件下生产符合国际标准的铸态铁素体管件。
此工艺可与树脂砂和消失模铸造相媲美,可比水玻璃砂刮板造型提高生产效率10倍以上,降低废品率10%以上,在标准允许的情况下可减轻铸件重量10%以上,减少工人25%〜30%,降低生产成本10%以上,管件后处理工作量减少70%,型砂用量减少80%,水压试验合格率高达98%以上。
由于大大减少了型砂处理量,车间的环境粉尘污染明显改善,是一项先进的绿色环保铸造技术。
铁型覆砂铸造是在金属型(称为铁型)内腔覆上一薄层型砂而形成铸型的一种铸造工艺。
由于覆砂层比较薄(4〜8mm ),因此采用比较贵的高质量造型材料,在经济上也是合理的,其结果是使铸件质量大大改善和废品显著减少;由于铁型覆砂铸型刚度很好,从而显著地提高了铸件的尺寸精度和致密性。
德国、前苏联等国于60年代前后开始把铁型覆砂铸造应用于铸造生产,主要用于生产球铁曲轴、杀U车毂、刹车盘、缸套、炸弹壳、坦克履带和电机底座等30余种铸件。
我国对铁型覆砂铸造的应用性研究起始于70年代初,至1979年,浙江省机电设计研究院和永康拖拉机厂等单位合作,首次将该工艺用于S195曲轴毛坯的批量铸造生产,同时,完成了对该工艺所生产的球铁曲轴性能的考核评价,在疲劳强度(疲劳极限应力o-1的比较)、断裂强度(门槛值△ Kth的比较以及断裂韧性K1C的比较)和使用寿命(10000h台架耐久试验对比)等方面,与砂型铸造曲轴进行了大量的试验对比,皆优于砂型铸造。
在其后的10余年里,该工艺不断在应用中提高完善,至90年代初,已有7家企业应用了该工艺,尤其是单缸曲轴和四缸曲轴的铁型覆砂铸造工艺取得了很大的成功。
这段时期的代表企业是永康拖拉机厂、上虞动力机厂、望都曲轴连杆厂、皖北曲轴厂、金华内燃机配件厂、常州柴油机厂等。
1991 年国家计委将铁型覆砂铸造批准为国家八五”重点新技术推广项目,并把浙江省机电设计研究院作为该项目的技术依托单位,这对于我国铁型覆砂铸造技术的发展起了巨大的推动作用。
我院承担了该推广项目后,在其后的5〜6年时间里基本上解决了铁型覆砂铸造用于批量生产的一系列问题。
①设计和定型了覆砂造型机,解决了长期以来由射芯机改装代用的问题;②定型规范了标准的铁型覆砂铸造生产线,使原来比较简单的铁型覆砂铸造生产线得到了改进,在上海球铁厂等企业应用;③铁型覆砂铸造应用扩大到铸造工艺难度较大的一些铸件,例如六缸曲轴和三缸曲轴等;④将覆膜砂引入铁型覆砂铸造生产中,大大提高了覆砂造型质量;⑤铁型覆砂铸造工艺设计进一步规范, 设计水平也大大提高,并开发了铁型覆砂铸造过程的计算机模拟软件和引入了铁型覆砂铸造工艺的计算机辅助设计软件。
目前,全国已有近百家企业应用了铁型覆砂铸造工艺生产球铁曲轴、凸轮轴、平衡轴、耐压阀体、缸套,耐磨齿盘等30余种铸件,估计年产铸件在10X104t左右。
比较典型的企业有上海汽车铸造总厂球铁厂、沈阳第一曲轴厂、广西百矿集团、宜兴机械总厂、山东九羊集团、浙江曙光曲轴厂、本溪天缘曲轴厂、保定电影机械厂、山西潞城曲轴厂、河北辛集曲轴厂等。
但是由于这些企业引入该工艺的方式不同:有委托我院进行设计或承建的,也有自行仿造开发的。
因此他们对铁型覆砂铸造工艺的掌握程度相差甚远。
仅以铁型覆砂铸造废品率为例,不少掌握得比较好的企业可稳定在3%左右,取得了非常好的经济效益。
但也有少数企业的铁型覆砂铸造废品率却高达20%左右,这大大地抵消了该工艺来该产生的的经济效益。
究其原因,发现是由于这些企业还没有完全掌握该工艺的设计和生产要领,以及疏于生产管理所致。
铁型覆砂铸造工艺设计及实际生产主要解决:①铁型壁厚和覆砂层厚度及二者的配合,以满足不同壁厚和不同材质铸件对凝固和冷却的不同要求;②便捷和经济的覆砂成型方法,以满足不同铸件对表面质量和尺寸精度的要求;③工艺参数。
如浇注系统、射砂系统、排气系统等的确定;④批量生产的实现。
例如生产线及覆砂主机和辅机的设计定型;⑤工艺规程的制定,例如浇注、冷却和开箱等规程,以及铸件成分的调整等。
2铁型覆砂铸造的热交换特点液态金属浇入铁型覆砂铸型以后,铸件一一覆砂层一一铁型”是一个不稳定的热交换系统。
为了使问题简化,假设铸件是半元限的;并假设系统中各组元的温度场按直线规律分布的。
令 -分别表示铸件与覆砂 层、铁型与覆砂层之间热交换强度的两个传热准则。
k1是铸件热阻与覆砂层热阻之比; k2是铁型的热阻与覆砂层热阻之比。
将 k1和k2结 合起来考虑,随着覆砂层厚度的变化,有以下三种实际上可能发生的铸件一一覆砂层一一铁型”间不同的传热情况: ① 当k wi, k2w 1时,覆砂层在正常的厚度之内,铸件的冷却速度随着覆砂层厚度的减少而增大。
② 当覆砂层的厚度超过某一厚度以后, 铁型对铸件冷却已不产生影响, 这时就相当于普通的砂型铸造或树脂砂铸造。
由于覆砂层的导热系数比铁型的导热系数小得多,所以铸件冷却缓慢。
③ 当k ± 1, k2仝1时,覆砂层厚度太薄,这时就相当于金属型 铸造了。
以上热交换特点已为实验所证实, 当曲轴(cm -14 )铁型覆砂 铸造的覆砂层厚度从4〜32mm 逐渐变化时,曲轴组织中的渗碳体量不断减少, 珠光体量和铁素体量不断增加。
而当覆砂层 厚度小于4mm 时,铸件的冷却强度与金属型(厚涂料)相近;覆砂层大于32mm 时,则其冷却强度相当于普通树脂砂 铸造了。
当铁型覆砂铸造用于各种不同铸件的生产时,就是通过试验或经验类比,以确定不同的覆砂 层厚度和铁型厚度来控制铸件的凝固速度。
例如在 490Q 球铁曲轴铁型覆砂 铸造工艺设计 中,取图1表示系统的一部分,显然,同样的比热流 q 通过了系统中各个组元:图1铸件一覆砂层一铁型的温度分布覆砂层厚度为5〜8mm,铁型壁厚为20〜30mm,生产出了优质的无冒口铸态球铁,其主要原因:①覆砂层有效地调节了铸件的冷却速度,一方面使铸件不易出现白口,另一方面又使冷却速度大于砂型铸造。
如图2所示,当铁水浇入铁型覆砂铸型后,经8min铸件温度降到930 C左右,而砂型要降到同样温度,就需要24min,冷却速度提高了3倍左右,其结果使铸件的机械性能显著提高。
②铁型无退让性,但很薄的覆砂层却能适当减少铸型的收缩阻力;而铁型所具有的刚性,又有效地利用了球铁在凝固过程中的石墨化膨胀,实现了无冒口铸造;由于覆砂层薄,型腔不易变形,铸件精度比砂型大为提高。
1-铁型覆砂2-砂型图2球铁浇注后的冷却曲线3铁型覆砂铸件的冷却速度影响铁型覆砂铸件冷却速度的因素有铸件壁厚、铸件材质、浇注温度、覆砂层厚度、覆砂层的材料、铁型厚度、铁型材质和铸型温度等因素。
在此,仅讨论铸件壁厚(be)、覆砂层厚度(bm)及铁型厚度(bi)的影响。
3.1 be、bm和bi对铸件冷却的影响图3是在下列实验条件下做出的不同铸件壁厚(分别是10mm、20mm、40mm、80mm )、不同覆砂层厚度(分别是4mm和32mm )以及不同铁型壁厚(分别是32mm和8mm )对铁型覆砂铸件冷却速度的影响情况:铸件化学成分3.52%C、2.46%Si、0.80%Mn、0.18%P、0.031%S,覆砂层化学成分为:石英砂90%,粘土8%,煤粉2%,水分3%。
min>图3铸件壁厚、覆砂层厚度、铁型壁厚对冷却速度的影响从图3可见:①铸件壁厚、覆砂层厚度和铁型壁厚共同影响铸件的冷却速度。
因此,在实际生产中,应根据不同的铸件壁厚来选择合适的铁型厚度和覆砂层厚度,以得到所需的冷却速度。
②不同厚度的铸件可以通过选择合适的覆砂层厚度和铁型壁厚得到相同的冷却速度,例如图3中的I 区表示厚度为10mm 和20mm、n区表示20mm 和40mm、in区表示40mm 和80mm铸件冷却范围之间的重叠。
③虽然可以改变bm和bi使不同厚度的铸件获得相同的冷却速度,但并非任何厚度的铸件都可获相同的冷却速度,在本实验条件下,厚度为10mm和厚度为40mm的铸件就不能获得完全一样的冷却速度(曲线没有重叠部分)。
3.2覆砂厚度(bm )和铁型壁厚(bi)的选择bm和bi 一般都是根据经验或实验确定,这里介绍一种图表法。
图4是用以确定铁型覆砂铸造应用范围的曲线图表,适用于铸件厚度(be)从10〜80mm,开箱温度600 C的条件。
纵座标为冷却时间。
图右边曲线的横座标上标有覆砂层厚度,它可以从已知的铸件冷却到600 C所需要的时间以及各种铸件厚度而查定,而且在所求的铸件壁厚中(10、20、40、80mm )已知一个,那么覆砂层厚度及铁型厚度的确定是很方便的。
从左半部曲线的横座标上找到相应的be(比如be=20mm)画一条水平线,如果这两条线相交在画有剖面线的曲线范围里,那么表明这种铸件适宜采用铁型覆砂铸造。
把这条水平线向右延伸,它便伸入be=20mm的区域里,在这个区域里引一根垂直线向下就可得到所需要的覆砂层厚度。
但应使这根垂线尽可能地向右边画,以便得到最小的覆砂层厚度及铁型厚度。
如果所需确定的覆砂层厚度不在这个范围以内,则可按照类似方法从邻近的曲线范围中去找。
如果铸件的壁厚各处不均匀,则先看一下这个铸件能否采用铁型覆砂铸造,然后按照各个壁 厚来确定其覆砂层厚度及铁型厚度。
例如,一个铸件具有 15mm 、30mm 和45mm 三种不同的壁厚,同上在图 4的左半部按照这三个壁厚数值引三根垂线,然后使其与一根水平线 相交,它们的交点应尽可能处在铁型覆砂范围里。