半导体工艺干法刻蚀气体
半导体工艺(自己总结)

只是想多了解下工艺,因为自己不是学这个的,要补课啊 ....是不是可以这么理解:1.PAD oxide :SiO2在LOCOS 和STI 形成时都被用来当作nitride 的衬垫层,如果没有这个SiO2衬垫层作为缓冲之用,LPCVD nitride 的高张力会导致wafer 产生裂缝甚至破裂,同时也作为NITRIDE ETCH 时的STOP LAYER2.SAC oxide :Sacrificial Oxide 在gate oxidation 之前移除wafer 表面的损伤和缺陷,有助于产生一个零缺陷的wafer 表面以生成高品质的gate oxide;经过HDP 后Pad Oxide 结构已经被破坏了,可能无法阻挡后面Implant 的离子。
所以生长一层Sac Oxide ,作为在后面Implant 时对Device 的保护。
3.BPSG 含硼及磷的硅化物 BPSG 乃介于Poly 之上、Metal 之下,可做为上下两层绝缘之用,加硼、磷主要目的在使回流后的Step 较平缓,以防止Metal line 溅镀上去后,造成断线4.ONO (OXIDE NITRIDE OXIDE ) 氧化层-氮化层-氧化层 半导体组件,常以ONO 三层结构做为介电质(类似电容器),以储存电荷,使得资料得以在此存取。
在此氧化层 - 氮化层 – 氧化层三层结构,其中氧化层与基晶的结合较氮化层好,而氮化层居中,则可阻挡缺陷(如pinhole )的延展,故此三层结构可互补所缺.5.space Oxide RIE Etch:猜想应当是氧化物隔离的反应离子刻蚀(RIE-Reactive Ion Etch )反应离子刻蚀是以物理溅射为主并兼有化学反应的过程。
通过物理溅射实现纵向刻蚀,同时应用化学反应来达到所要求的选择比,从而很好地控制了保真度。
刻蚀气体(主要是F 基和CL 基的气体)在高频电场(频率通常为13.56MHz )作用下产生辉光放电,使气体分子或原子发生电离,形成“等离子体”(Plasma )。
Metal干法刻蚀工艺介绍
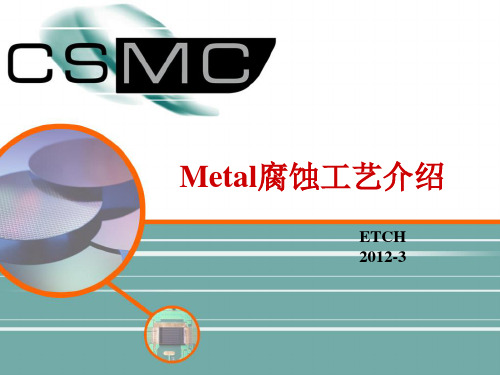
Metal腐蚀工艺介绍
ETCH 2012-3
目录:
• 简介 • Metal结构、成分 • Metal腐蚀工艺 • 常见异常介绍
IC结构:
Time(s)
20
55 External(7) 120 80*
5
10
EMP5K:
• 在EMP5K设备中,引入了磁场的设置,磁场在腐蚀工艺中 的作用: – 利于等离子体的形成; – 提高腐蚀均匀性; – 减小等离子损伤;
• Step6 圆 片 在 流 水 腔 (APM)中
• Step7 圆片传到下料片盒。
TCP9600:
设备特性:
• 耦合的等离子区; • 独立控制的可自动调谐的双射频功率源; • 受控的等离子浓度、能量; • 低压力高速率.
TCP9600:
recipe:
Description Cl2 (sccm) BCl3 (sccm) N2(sccm) O2(sccm) Ar(sccm) Pressure(mT) TCP Power(W) Bottom Power(w) He pressure(T) / He Flow MAX(sccm) End Point MODE Max Time(S) Delay Time(S) Normal Time(S) Trigger(%) DSQ RF Power(W) H2O(sccm) O2(sccm) COLD DIW COLD N2 SPIN Speed(RPM)
等离子腐蚀是依靠高频辉光放电形成的化学活性游离基 与被腐蚀材料发生化学反应的一种选择性腐蚀方法。气 体中总存在微量的自由电子,在外电场的作用下,电子 加速运动。当电子获得足够的能量后与气体分子发生碰 撞,使气体分子电离发出二次电子,二次电子进一步与 气体分子发生碰撞电离,产生更多的电子和离子。当电 离与复合过程达到平衡时,出现稳定的辉光放电现象, 形成稳定的等离子体(PLASMA)。等离子体中包括有 电子、离子、还有处于激发态的分子,原子及各种原子 团(统称游离基)。游离基具有高度的化学活性,正是 游离基与被腐蚀材料的表面发生化学反应,形成挥发性 的产物,使材料不断被腐蚀。
多晶干法刻蚀

多晶干法刻蚀是一种重要的半导体工艺步骤,主要应用于制造集成电路。
以下是关于多晶干法刻蚀的详细解释:
1. 刻蚀多晶硅时,必须确保掩膜上的尺寸准确地转移到多晶硅上。
2. 刻蚀后的轮廓也非常重要,例如,如果多晶硅刻蚀后栅极侧壁有倾斜,可能会屏蔽后续工艺中源极和
漏极的离子注入,导致杂质分布不均,同时沟道的长度会随栅极倾斜的程度而改变。
3. 对sio2的刻蚀选择比要足够高,这是因为需要去除阶梯残留,避免多晶硅电极间短路的发生。
同时,
多晶硅一般覆盖在很薄的栅极氧化层上,如果氧化层被完全刻蚀,则氧化层下的源极和漏极区域可能会被快速刻蚀。
4. 选择适当的刻蚀气体也是非常重要的。
CF4、SF6等F原子为主的等离子体是常用的刻蚀气体,但这类
气体也存在负载效应,即被刻蚀材料裸露在等离子体中面积较大的区域时刻蚀速率比在面积较小的区域时慢,导致局部刻蚀速率的不均匀。
5. 在干法刻蚀中,多晶硅相对于氮化硅和二氧化硅下层的选择性较差,因此需要非常精确地优化干蚀刻
配方和蚀刻时间的精细控制。
6. 另外,对于多晶硅的干法刻蚀,控制其过度刻蚀也非常重要。
这是因为过度刻蚀可能会导致多晶硅的
电阻不均匀。
总之,多晶干法刻蚀是一项复杂的工艺步骤,涉及精确的尺寸控制、化学选择性和物理特性考虑等多个方面。
半导体干法蚀刻的介绍

半导体干法蚀刻的介绍《半导体干法蚀刻:新兴技术的应用与发展》引言:半导体干法蚀刻是一种关键的制造工艺,在半导体行业中有着广泛的应用。
本文将着重介绍半导体干法蚀刻的原理、特点以及其在新兴技术领域的应用与发展。
正文:一、半导体干法蚀刻的原理半导体干法蚀刻是利用气体或等离子体与半导体表面发生反应来实现物质的去除。
通过将气体或者气体混合物注入到真空环境中,让气体产生等离子体,利用等离子体中的活性粒子或自由基对半导体表面进行化学反应或破坏性物理反应,从而移除半导体表面的一层材料。
二、半导体干法蚀刻的特点1. 制程精度高:通过控制反应气体、温度、时间等参数,可以实现较高的制程精度,满足半导体器件的要求。
2. 制程可控性强:半导体干法蚀刻过程中可以精确控制蚀刻速率和选择性,从而实现对半导体的精确加工。
3. 无需接触:与湿法蚀刻相比,半导体干法蚀刻是一种无需接触半导体表面的加工方式,可以避免因接触引起的损伤和污染。
4. 适用性广:半导体干法蚀刻可以适用于各种材料,包括硅、氮化硅、氮化铝等,可满足不同材料的蚀刻需求。
5. 环保高效:半导体干法蚀刻是一种无废液产生的加工方式,不会对环境造成污染,同时也节约了大量的水资源。
三、半导体干法蚀刻在新兴技术的应用与发展1. 三维芯片制造:随着半导体器件的发展,传统的二维芯片逐渐无法满足需求。
半导体干法蚀刻可以实现对芯片表面的精确加工,为三维芯片制造提供了重要工艺支持。
2. 纳米加工:随着纳米科技的快速发展,半导体干法蚀刻在纳米加工中广泛应用。
通过控制蚀刻参数,可以实现纳米尺寸的结构制造,为纳米电子学和纳米光学等领域的研究提供了有力支持。
3. 新型材料加工:随着新型材料的涌现,传统的湿法蚀刻技术面临挑战。
半导体干法蚀刻可以适用于新型材料的加工,如氮化硅、氮化铝等,为新型材料的应用拓展提供了技术保障。
结论:半导体干法蚀刻是一种重要的制造工艺,具有制程精度高、制程可控性强、适用性广、环保高效等特点。
半导体芯片干法刻蚀工艺
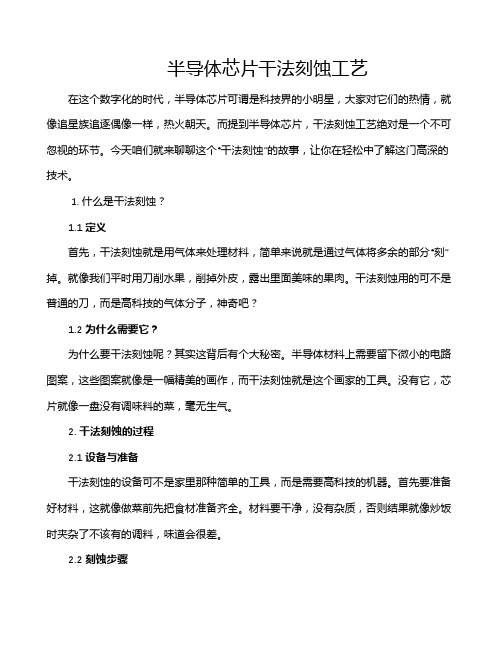
半导体芯片干法刻蚀工艺在这个数字化的时代,半导体芯片可谓是科技界的小明星,大家对它们的热情,就像追星族追逐偶像一样,热火朝天。
而提到半导体芯片,干法刻蚀工艺绝对是一个不可忽视的环节。
今天咱们就来聊聊这个“干法刻蚀”的故事,让你在轻松中了解这门高深的技术。
1. 什么是干法刻蚀?1.1 定义首先,干法刻蚀就是用气体来处理材料,简单来说就是通过气体将多余的部分“刻”掉。
就像我们平时用刀削水果,削掉外皮,露出里面美味的果肉。
干法刻蚀用的可不是普通的刀,而是高科技的气体分子,神奇吧?1.2 为什么需要它?为什么要干法刻蚀呢?其实这背后有个大秘密。
半导体材料上需要留下微小的电路图案,这些图案就像是一幅精美的画作,而干法刻蚀就是这个画家的工具。
没有它,芯片就像一盘没有调味料的菜,毫无生气。
2. 干法刻蚀的过程2.1 设备与准备干法刻蚀的设备可不是家里那种简单的工具,而是需要高科技的机器。
首先要准备好材料,这就像做菜前先把食材准备齐全。
材料要干净,没有杂质,否则结果就像炒饭时夹杂了不该有的调料,味道会很差。
2.2 刻蚀步骤接下来就是真正的“刻蚀”过程。
我们把准备好的材料放入刻蚀机中,然后把气体注入,气体和材料发生反应,把不需要的部分给“消灭”掉。
这一步就像是让一位雕刻家在大理石上精雕细琢,细致入微,最终形成我们想要的图案。
整个过程需要极高的温度和压力,真是热火朝天,紧张又刺激。
3. 干法刻蚀的优势与挑战3.1 优势干法刻蚀的优势可不少。
首先,它能实现高精度的刻蚀,就像精准的手艺人,毫不马虎。
此外,干法刻蚀能处理各种不同的材料,这样一来,适应性强,真是让人赞叹不已。
3.2 挑战不过,挑战也随之而来。
比如,气体的选择、刻蚀的速度等等,都是需要精确把控的,要是稍有差池,就可能导致整个工艺的失败。
这就像是在走钢丝,一不小心就得“摔”下来,真是心惊胆战。
4. 总结干法刻蚀工艺就像一门艺术,既有技术的严谨,也有创意的灵动。
drie干法蚀刻原理
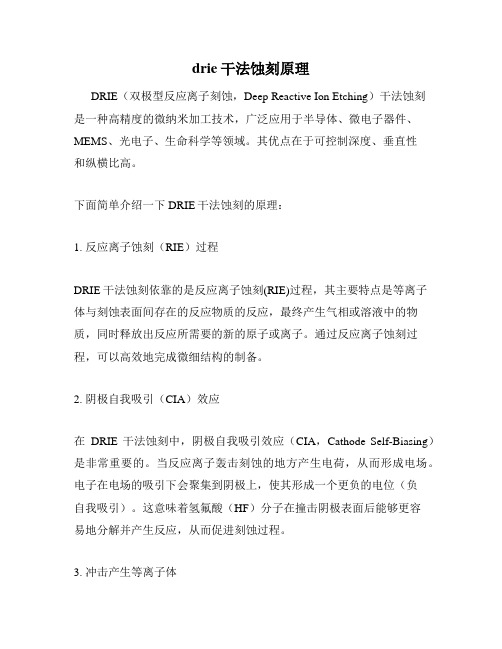
drie干法蚀刻原理DRIE(双极型反应离子刻蚀,Deep Reactive Ion Etching)干法蚀刻是一种高精度的微纳米加工技术,广泛应用于半导体、微电子器件、MEMS、光电子、生命科学等领域。
其优点在于可控制深度、垂直性和纵横比高。
下面简单介绍一下DRIE干法蚀刻的原理:1. 反应离子蚀刻(RIE)过程DRIE干法蚀刻依靠的是反应离子蚀刻(RIE)过程,其主要特点是等离子体与刻蚀表面间存在的反应物质的反应,最终产生气相或溶液中的物质,同时释放出反应所需要的新的原子或离子。
通过反应离子蚀刻过程,可以高效地完成微细结构的制备。
2. 阴极自我吸引(CIA)效应在DRIE干法蚀刻中,阴极自我吸引效应(CIA,Cathode Self-Biasing)是非常重要的。
当反应离子轰击刻蚀的地方产生电荷,从而形成电场。
电子在电场的吸引下会聚集到阴极上,使其形成一个更负的电位(负自我吸引)。
这意味着氢氟酸(HF)分子在撞击阴极表面后能够更容易地分解并产生反应,从而促进刻蚀过程。
3. 冲击产生等离子体DRIE干法蚀刻采用了高能量电离辉光放电(HEDP)的方式产生等离子体。
这种放电方式可以使气体在较低的压力下进行电离,从而产生高浓度的反应物,以保持较高的刻蚀速率和质量。
4. 双极金属反应DRIE干法蚀刻使用阴极和阳极的双金属反应体系,这种体系可以形成一种稳定的化学反应,可以产生氟化物(F^-)和钨酸根(WO4^-2 )等反应物,以加速刻蚀过程。
在DRIE干法蚀刻过程中,通过调节工艺参数如气体流速,功率密度等,可以控制反应离子轰击材料表面的能量和反应速率,有效地实现高精度加工的控制。
总之,DRIE干法蚀刻的原理是基于反应离子蚀刻、阴极自我吸引效应、等离子体和双极金属反应体系。
可以实现高精度和高质量的微纳米结构制备,是微纳加工领域中的一项重要技术。
简述刻蚀工艺的主要作用

简述刻蚀工艺的主要作用
刻蚀工艺的主要作用是在光刻的基础上,有选择地转移图形。
具体来说,刻蚀是用化学或物理方法有选择地从硅片表面去除不需要的材料,其基本目标是在涂胶的硅片上正确地复制掩模图形。
在半导体制程中,刻蚀就是用化学的、物理的或同时使用化学和物理的方法,在光刻的基础上有选择地进行图形的转移。
刻蚀技术主要分为干法刻蚀与湿法刻蚀。
干法刻蚀主要利用反应气体与等离子体进行刻蚀;湿法刻蚀主要利用化学试剂与被刻蚀材料发生化学反应进行刻蚀。
刻蚀工艺发展历程

刻蚀工艺发展历程刻蚀工艺是一种常用的微纳加工技术,通过控制化学反应或物理过程,将材料表面的部分物质去除,从而得到所需的结构和形状。
在微电子、光学、生物医学等领域都有广泛应用。
本文将从刻蚀工艺的起源开始,逐步介绍其发展历程。
一、起源与初期发展刻蚀工艺的起源可以追溯到20世纪初期。
最早的刻蚀方法是机械刻蚀,即使用机械设备进行刻蚀,如机械雕刻机。
这种方法虽然简单粗暴,但却被广泛应用于半导体和光学器件的制造中。
随着科学技术的进步,人们开始尝试利用化学方法进行刻蚀。
1927年,美国化学家R. W. Wood首次提出了化学刻蚀的概念,并成功地利用酸性溶液对金属表面进行了刻蚀。
这一发现开启了刻蚀工艺的新篇章。
二、湿法刻蚀的发展在20世纪中叶,随着半导体工业的兴起,湿法刻蚀成为主流。
湿法刻蚀是利用酸性或碱性溶液对材料表面进行刻蚀。
最早的湿法刻蚀方法是浸泡刻蚀,即将待刻蚀的材料浸泡在溶液中,通过溶液与材料表面的化学反应来实现刻蚀。
随着对刻蚀工艺的深入研究,人们逐渐发现了湿法刻蚀的一些局限性,如刻蚀速率低、刻蚀精度不高等。
为了解决这些问题,人们开始探索新的湿法刻蚀方法。
1950年代,美国贝尔实验室研究人员发现,通过加热溶液可以显著提高刻蚀速率,这就是热刻蚀。
热刻蚀利用高温加速化学反应速率,从而提高刻蚀速率和精度。
人们还发现了选择性刻蚀的方法。
选择性刻蚀是指在刻蚀过程中,只对特定材料或特定方向进行刻蚀,而不影响其他材料或方向。
这种方法广泛应用于半导体器件的制造中,可以实现微米级的精确刻蚀。
三、干法刻蚀的崛起随着微纳加工技术的发展,湿法刻蚀逐渐暴露出一些局限性,如溶液的浓度控制困难、污染问题等。
为了解决这些问题,人们开始研究干法刻蚀。
干法刻蚀是利用气体或等离子体进行刻蚀。
最早的干法刻蚀方法是离子束刻蚀,即利用高能离子束对材料表面进行刻蚀。
离子束刻蚀可以实现高速刻蚀和高精度刻蚀,但设备复杂、成本高,限制了其应用范围。
后来,人们发现了等离子体刻蚀的方法。
八个基本半导体工艺

八个基本半导体工艺随着科技的不断进步,半导体技术在各个领域得到了广泛的应用。
半导体工艺是半导体器件制造过程中的关键环节,也是半导体产业发展的基础。
本文将介绍八个基本的半导体工艺,分别是氧化、扩散、沉积、光刻、蚀刻、离子注入、热处理和封装。
一、氧化工艺氧化工艺是指在半导体晶片表面形成氧化层的过程。
氧化层可以增强晶片的绝缘性能,并且可以作为蚀刻掩膜、电介质、层间绝缘等多种用途。
常见的氧化工艺有湿法氧化和干法氧化两种。
湿法氧化是在高温高湿的环境中,通过将晶片浸泡在氧化液中使其表面氧化。
干法氧化则是利用高温下的氧化气体与晶片表面反应来形成氧化层。
二、扩散工艺扩散工艺是指将掺杂物质(如硼、磷等)通过高温处理,使其在晶片中扩散,从而改变晶片的导电性能。
扩散工艺可以用于形成PN结、调整电阻、形成源、漏极等。
扩散工艺的关键是控制扩散温度、时间和掺杂浓度,以确保所需的电性能。
三、沉积工艺沉积工艺是将材料沉积在半导体晶片表面的过程。
常见的沉积工艺有化学气相沉积(CVD)和物理气相沉积(PVD)两种。
CVD是利用化学反应在晶片表面沉积薄膜,可以实现高纯度、均匀性好的沉积。
而PVD则是通过蒸发、溅射等物理过程,在晶片表面形成薄膜。
四、光刻工艺光刻工艺是将光敏胶涂覆在晶片表面,然后通过光刻曝光、显影等步骤,将光敏胶图案转移到晶片上的过程。
光刻工艺是制造半导体器件的核心工艺之一,可以实现微米级甚至纳米级的图案制作。
五、蚀刻工艺蚀刻工艺是通过化学反应或物理过程将晶片表面的材料去除的过程。
蚀刻工艺可以用于制作电路的开关、互连线等。
常见的蚀刻方法有湿法蚀刻和干法蚀刻两种。
湿法蚀刻是利用化学溶液对晶片表面进行腐蚀,而干法蚀刻则是通过等离子体或离子束对晶片表面进行刻蚀。
六、离子注入工艺离子注入工艺是将掺杂离子注入晶片中的过程。
离子注入可以改变晶片的导电性能和材料特性,常用于形成源漏极、调整电阻等。
离子注入工艺需要控制注入能量、剂量和深度,以确保所需的掺杂效果。
Metal干法刻蚀工艺介绍
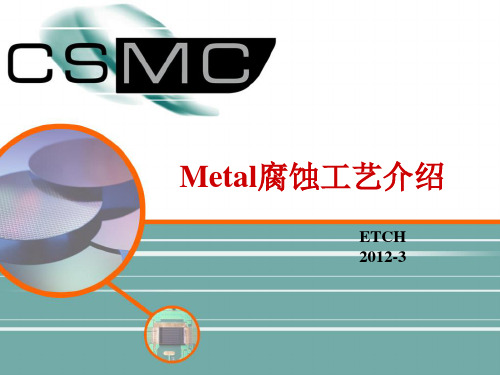
Metal结构:
• 根据工艺的不同,Metal结构也各有不同: -- Al -- AlCu -- AlSiCu -- Ti/TiN/AlCu/TiN 另外在一些工艺中, 使用: -- W (Plug) -- Cu (Cu制程) -- Ta (barrier)
Metal成分:
• 一般AL的成分: Al-Si(1.0%)、Al-Si(0.75%)-Cu(0.5%)、AlCu(0.5%)
均为ESC(Electrostatic Chuck)类型设备;
• P5K Metal:APPLIED公司产品, 高压力,单功率源设备. • DPS Metal:APPLIED公司产品,与TCP9600 同一代设备,
工作原理一致,都是低压力,双功率源设备。
TCP9600:
TCP9600:
TCP9600 圆 片 传 输 主 要 有 以 下7个步骤:
• Step1 从上料片盒取出圆 片;
• Step2 圆片自调整和找平 边;
• Step3 圆 片 通 过 上 料 腔 ( ELL ) 传 到 刻 蚀 腔 (Main Chamber);
• Step4 从刻蚀腔中取出圆 片;
• Step5 圆 片 在 去 胶 腔 (DSQ),去胶腔同时也是 下料腔(XLL);
等离子腐蚀是依靠高频辉光放电形成的化学活性游离基 与被腐蚀材料发生化学反应的一种选择性腐蚀方法。气 体中总存在微量的自由电子,在外电场的作用下,电子 加速运动。当电子获得足够的能量后与气体分子发生碰 撞,使气体分子电离发出二次电子,二次电子进一步与 气体分子发生碰撞电离,产生更多的电子和离子。当电 离与复合过程达到平衡时,出现稳定的辉光放电现象, 形成稳定的等离子体(PLASMA)。等离子体中包括有 电子、离子、还有处于激发态的分子,原子及各种原子 团(统称游离基)。游离基具有高度的化学活性,正是 游离基与被腐蚀材料的表面发生化学反应,形成挥发性 的产物,使材料不断被腐蚀。
半导体工艺(第8章)刻蚀

典型的氧化去胶是H2SO4 :H2O2=3:1;
优点:
洗涤过程十分简单,即用去离子水冲洗即 可;
但要注意,氧化剂对衬底表面也有腐蚀作 用(十分轻微);
等离子体去胶
一种近几年发展起来的一种新工艺; 不需要化学试剂,也不需要加温,因此,
器件的结构性和金属铝层都不受影响; 这对提高产品质量和可靠性有好处;
干法刻蚀是指以气体为主要媒体的刻蚀技 术,晶圆不需要液体化学品或冲洗,刻蚀 过程在干燥的状态进出系统;
干法刻蚀种类
等离子体刻蚀(以化学反应为主,较少采
用)
物理刻蚀(物理溅射作用) 反应离子刻蚀(既有化学反应,又有物理
溅射)
等离子体概念:
当对一个低压强的容器内的气体施加电压 时,这些原本中性的气体分子将被激发或 离解成各种不同的带电粒子(离子、原子 团、分子及电子)。这些离子便称为等离 子体;
如果用CF4或其他含氟的气体来进行刻蚀, 则选择性较差;
以CF3为例, 对SiO2与Si的刻蚀选择性在 10以上,但是对Si3N4与Si的刻蚀选择性仅 在3~5之间,对Si3N4与SiO2的选择性仅在 2~4之间。故近期改用NF3的等离子体进行 刻蚀,结果比较理想;
多晶硅的刻蚀
多晶硅的刻蚀比Si3N4和SiO2要复杂得多; 多晶硅栅极本身由两层不同材料组成(多
原理:
系统中通入氧气,在外加高频电磁场作用 下,氧气电离,形成等离子区;
其中活化的原子态氧约占10%~20%,他们 活性活泼,氧化能力强,与光刻胶发生反 应;
一些易于氧化的材料,用湿法清洗很容易 被氧化,如果改用干法洗,就可以避免这 一缺陷;
目前用得最多的是干法刻蚀的反应室,可 以与淀积金属的薄膜反应实相连接,经干 法清洗以去除硅片表面氧化层后,可以保 持在真空状态下,再进行表面镀膜;
干法刻蚀.
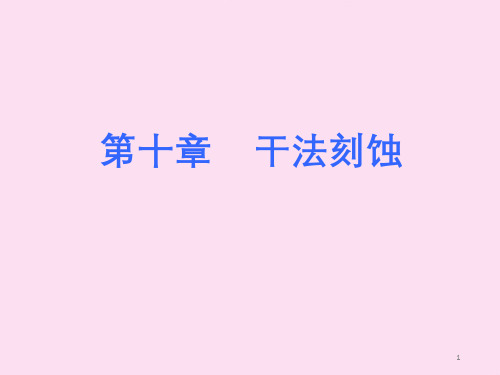
最小的光刻胶脱落或粘附问题
刻蚀速率=ΔT/t(Å /min)
Bias:凹切量或侧蚀宽度
好的片内、片间、批次间的刻蚀均匀性
等离子体刻蚀又称为激发反应气体刻蚀,属于化学刻蚀,各向同性。
② 自由基和反应原子或原子团的化学性质非常活泼,它们构成了等离子体的反应元素,自由基、反应原子或原子团与被刻蚀的材料进
行化学反应形成了等离子体刻蚀。
• 气体离化团束 (GCIB) 中束团的动能由组成原子共享,平均每个 原子的入射能量约在10 eV以下。因而,在碰撞过程中,团束原 子的整体运动使得团束仅对靶材表面的前几个原子层产生轰击效 应。
30 kV的气体离化团束设备图
28
气体离化团束加工技术
• GCIB的优点:
➢ 浅层注入,损伤小; ➢ 高产额溅射(比单原子离子高出100倍以上); ➢ 侧向溅射,利于表面平坦化; ➢ 表面清洁效率高。
9
刻蚀参数
6. 聚合物
• 聚合物是在刻蚀过程中由光刻胶中的碳与刻蚀气体和刻蚀生成物 结合在一起而形成的;能否形成侧壁聚合物取决于所使用的刻蚀 气体类型。
• 聚合物的形成有时是为了在刻蚀图形的侧壁上形成抗腐蚀膜从而 防止横向刻蚀,这样能形成高的各向异性图形,增强刻蚀的方向 性,从而实现对图形关键尺寸的良好控制。
化学反应
元素化学反应
各向同性
各向异性
选择比 刻蚀速率
低/难提高 (1:1)
高
很高 (500:1)
慢
高(5:1 ~100:1)
适中
线宽控制
好
非常差
很好
16
干法刻蚀的过程
RIE: 物理刻蚀+化学刻蚀
④由于离子轰击的方向性,遭受离子轰击的底面比未遭受离子轰击的侧面的刻蚀要快得多,达到了很好的各向异性。
半导体器件的干法刻蚀技术考核试卷

9. 硅片的掺杂类型会影响干法刻蚀的刻蚀速率。( )
10. 干法刻蚀后的硅片表面粗糙度与刻蚀时间无关。( )
五、主观题(本题共4小题,每题10分,共40分)
1. 请简述干法刻蚀与湿法刻蚀的主要区别,并说明干法刻蚀在半导体器件制造中的应用优势。(10分)
4. 通过优化刻蚀气体成分、调整反应室压力、控制刻蚀功率和温度等工艺参数,可以提高刻蚀选择比和均匀性。同时,使用钝化气体和保护层可以降低离子损伤。
2. 描述干法刻蚀过程中可能出现的几种常见问题(如刻蚀偏差、刻蚀残留等),并分析其产生原因。(10分)
3. 详细说明干法刻蚀中的各向异性刻蚀原理,以及如何通过调整工艺参数来实现更好的各向异性刻蚀效果。(10分)
4. 讨论在干法刻蚀过程中,如何优化工艺参数以提高刻蚀选择比和刻蚀均匀性,并降低离子损伤。(10分)
D.湿法刻蚀
4. 在干法刻蚀中,等离子体的作用是什么?( )
A. 生成自由基
B. 吸收热量
C. 提供反应动力
D. 以上都是
5. 下列哪种气体在干法刻蚀过程中用作钝化气体?( )
A. 氮气
B. 氧气
C. 氯气
D. 硅烷
6. 以下哪个因素会影响干法刻蚀的选择比?( )
A. 刻蚀气体种类
B. 反应室温度
C. 电路设计
D. 防止硅片受损
15. 下列哪种气体在干法刻蚀过程中用作刻蚀气体?( )
A. 氮气
B. 氧气
C. 氟化氢
D. 二氧化硫
16. 在干法刻蚀中,为什么需要控制反应室压力?( )
A. 影响刻蚀速率
B. 影响刻蚀均匀性
C. 影响选择比
半导体刻蚀工艺简介

半导体刻蚀⼯艺简介此保护膜可保护多晶硅的侧壁,进⽽形成⾮等向性刻蚀。
使⽤Cl2等离⼦体对多晶硅的刻蚀速率⽐使⽤F原⼦团慢很多,为兼顾刻蚀速率与选择⽐,有⼈使⽤SF6⽓体中添加SiCl4或CHCl3。
SF6的⽐例越⾼,刻蚀速率越快;⽽SiCl4或CHCl3的⽐例越⾼,多晶硅/SiO2的刻蚀选择⽐越⾼,刻蚀越趋向⾮等向性刻蚀。
除了Cl和F的⽓体外,溴化氢(HBr)也是⼀种常⽤的⽓体,因为在⼩于0.5µm的制程中,栅极氧化层的厚度将⼩于10nm,⽤HBr等离⼦体时多晶硅/SiO2的刻蚀选择⽐⾼于以Cl为主的等离⼦体。
4.⾦属的⼲法刻蚀⾦属刻蚀主要是互连线及多层⾦属布线的刻蚀,⾦属刻蚀有以下⼏个要求:⾼刻蚀速率(⼤于1000nm/min);⾼选择⽐,对掩蔽层⼤于4:1,对层间介质⼤于20:1;⾼的刻蚀均匀性;关键尺⼨控制好;⽆等离⼦体损伤:残留污染物少;不会腐蚀⾦属。
①铝的刻蚀。
铝是半导体制备中最主要的导线材料,具有电阻低、易于淀积和刻蚀等优点。
铝刻蚀通常采⽤加⼊卤化物的氯基⽓体,最常⽤的是BCl3。
因为铝在常温下表⾯极易氧化⽣成氧化铝,氧化铝阻碍了刻蚀的正常进⾏,⽽BCl3可将⾃然氧化层还原、保证刻蚀的进⾏,⽽且BCl3还容易与氧⽓和⽔反应,可吸收反应腔内的⽔汽和氧⽓,从⽽降低氧化铝的⽣成速率。
1.4质量评价⼀、⼲法刻蚀的终点监测近⼏年发展起来的⼲法刻蚀⼯艺,为了提⾼刻蚀精度,深⼊研究刻蚀机理,实现刻蚀设备的⾃动化,需要解决⼯艺过程的监控问题,特别是精确控制刻蚀终点。
因为⼲法刻蚀的选择性不如湿法,终点监控不当极易造成过腐蚀,甚⾄破坏下层图形。
早期的监控⽅法是计时法。
假设被刻蚀材料的膜厚已知,先通过实验确定刻蚀速率,然后在⼯艺过程中,由计时确定终点。
但由于影响刻蚀速率的因素太多(如压⼒、温度、流量、⽓体配⽐等),刻蚀速率难于重复(如前所述,对铝的等离⼦体刻蚀更是如此),不能满⾜⼯艺要求。
表1-1⼏种等离⼦体刻蚀终点检测⽅法⼆、⼲法刻蚀的质量检测刻蚀⼯艺的最后⼀步是进⾏检查以确保刻蚀的质量,通常都是⽤⾃动检测系统进⾏的。
半导体行业的工艺及其带来的环境问题
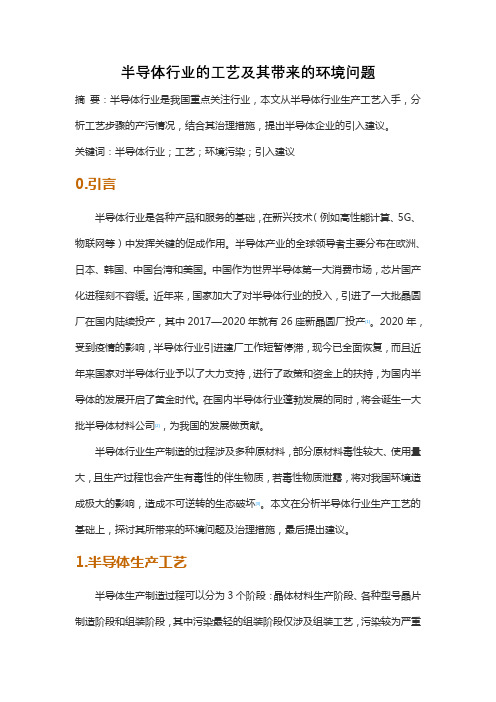
半导体行业的工艺及其带来的环境问题摘要:半导体行业是我国重点关注行业,本文从半导体行业生产工艺入手,分析工艺步骤的产污情况,结合其治理措施,提出半导体企业的引入建议。
关键词:半导体行业;工艺;环境污染;引入建议0.引言半导体行业是各种产品和服务的基础,在新兴技术(例如高性能计算、5G、物联网等)中发挥关键的促成作用。
半导体产业的全球领导者主要分布在欧洲、日本、韩国、中国台湾和美国。
中国作为世界半导体第一大消费市场,芯片国产化进程刻不容缓。
近年来,国家加大了对半导体行业的投入,引进了一大批晶圆厂在国内陆续投产,其中2017—2020年就有26座新晶圆厂投产[1]。
2020年,受到疫情的影响,半导体行业引进建厂工作短暂停滞,现今已全面恢复,而且近年来国家对半导体行业予以了大力支持,进行了政策和资金上的扶持,为国内半导体的发展开启了黄金时代。
在国内半导体行业蓬勃发展的同时,将会诞生一大批半导体材料公司[2],为我国的发展做贡献。
半导体行业生产制造的过程涉及多种原材料,部分原材料毒性较大、使用量大,且生产过程也会产生有毒性的伴生物质,若毒性物质泄露,将对我国环境造成极大的影响,造成不可逆转的生态破坏[3]。
本文在分析半导体行业生产工艺的基础上,探讨其所带来的环境问题及治理措施,最后提出建议。
1.半导体生产工艺半导体生产制造过程可以分为3个阶段:晶体材料生产阶段、各种型号晶片制造阶段和组装阶段,其中污染最轻的组装阶段仅涉及组装工艺,污染较为严重的是晶片制造阶段。
其主要工艺步骤为:清洗、键合、氧化、掺杂、光刻、刻蚀等阶段。
清洗工艺为保留芯片表面特性,采用化学溶液有效的清除半导体硅片表面的灰尘、残留有机物和吸附在表面的各种离子,主要产生各类废气及废液。
晶圆键合以有无中间过渡层可分为直接键合和中间层键合,而直接键合方式具有键合强度高的优势,是目前应用的主流,键合工序污染较小仅产生废水。
氧化是在高温惰性环境下,通入氧气或含氧水汽,将硅片表面的硅氧化生长氧化层,过程一般是将作为原料的硅晶圆片放入洁净的石英炉管中,主要产生工艺废气。
常见半导体材料的刻蚀工艺
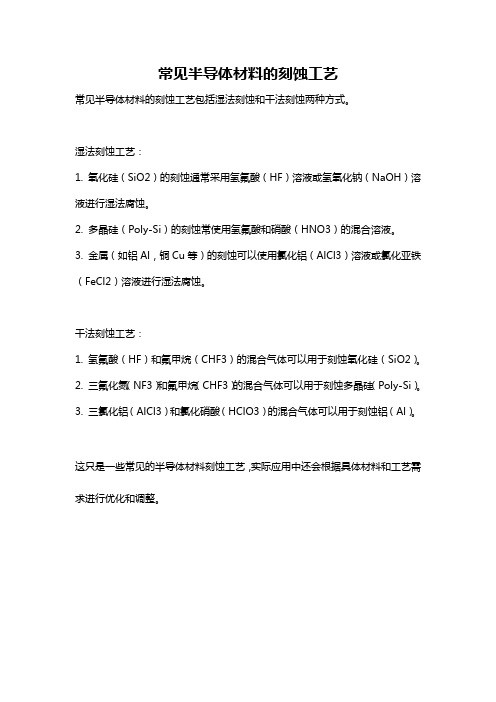
常见半导体材料的刻蚀工艺
常见半导体材料的刻蚀工艺包括湿法刻蚀和干法刻蚀两种方式。
湿法刻蚀工艺:
1. 氧化硅(SiO2)的刻蚀通常采用氢氟酸(HF)溶液或氢氧化钠(NaOH)溶液进行湿法腐蚀。
2. 多晶硅(Poly-Si)的刻蚀常使用氢氟酸和硝酸(HNO3)的混合溶液。
3. 金属(如铝Al,铜Cu等)的刻蚀可以使用氯化铝(AlCl3)溶液或氯化亚铁(FeCl2)溶液进行湿法腐蚀。
干法刻蚀工艺:
1. 氢氟酸(HF)和氟甲烷(CHF3)的混合气体可以用于刻蚀氧化硅(SiO2)。
2. 三氟化氮(NF3)和氟甲烷(CHF3)的混合气体可以用于刻蚀多晶硅(Poly-Si)。
3. 三氯化铝(AlCl3)和氯化硝酸(HClO3)的混合气体可以用于刻蚀铝(Al)。
这只是一些常见的半导体材料刻蚀工艺,实际应用中还会根据具体材料和工艺需求进行优化和调整。
第二章干法刻蚀的介绍
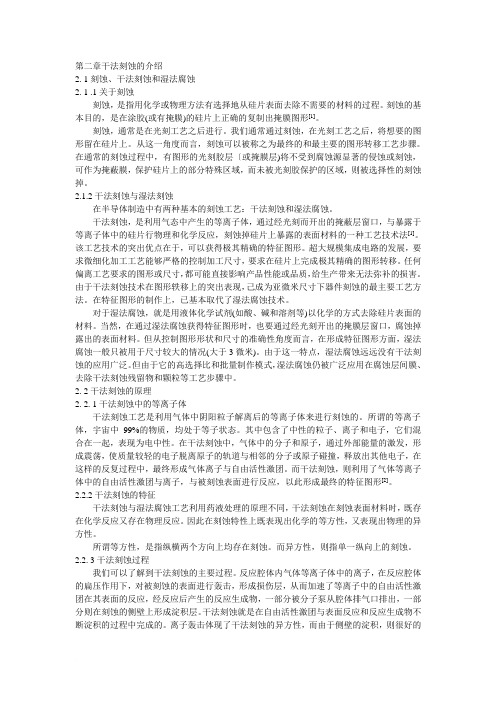
第二章干法刻蚀的介绍2. 1刻蚀、干法刻蚀和湿法腐蚀2. 1 .1关于刻蚀刻蚀,是指用化学或物理方法有选择地从硅片表面去除不需要的材料的过程。
刻蚀的基本目的,是在涂胶(或有掩膜)的硅片上正确的复制出掩膜图形[1]。
刻蚀,通常是在光刻工艺之后进行。
我们通常通过刻蚀,在光刻工艺之后,将想要的图形留在硅片上。
从这一角度而言,刻蚀可以被称之为最终的和最主要的图形转移工艺步骤。
在通常的刻蚀过程中,有图形的光刻胶层〔或掩膜层)将不受到腐蚀源显著的侵蚀或刻蚀,可作为掩蔽膜,保护硅片上的部分特殊区域,而未被光刻胶保护的区域,则被选择性的刻蚀掉。
2.1.2干法刻蚀与湿法刻蚀在半导体制造中有两种基本的刻蚀工艺:干法刻蚀和湿法腐蚀。
干法刻蚀,是利用气态中产生的等离子体,通过经光刻而开出的掩蔽层窗口,与暴露于等离子体中的硅片行物理和化学反应,刻蚀掉硅片上暴露的表面材料的一种工艺技术法[1]。
该工艺技术的突出优点在于,可以获得极其精确的特征图形。
超大规模集成电路的发展,要求微细化加工工艺能够严格的控制加工尺寸,要求在硅片上完成极其精确的图形转移。
任何偏离工艺要求的图形或尺寸,都可能直接影响产品性能或品质,给生产带来无法弥补的损害。
由于干法刻蚀技术在图形轶移上的突出表现,己成为亚微米尺寸下器件刻蚀的最主要工艺方法。
在特征图形的制作上,已基本取代了湿法腐蚀技术。
对于湿法腐蚀,就是用液体化学试剂(如酸、碱和溶剂等)以化学的方式去除硅片表面的材料。
当然,在通过湿法腐蚀获得特征图形时,也要通过经光刻开出的掩膜层窗口,腐蚀掉露出的表面材料。
但从控制图形形状和尺寸的准确性角度而言,在形成特征图形方面,湿法腐蚀一般只被用于尺寸较大的情况(大于3微米)。
由于这一特点,湿法腐蚀远远没有干法刻蚀的应用广泛。
但由于它的高选择比和批量制作模式,湿法腐蚀仍被广泛应用在腐蚀层间膜、去除干法刻蚀残留物和颗粒等工艺步骤中。
2. 2干法刻蚀的原理2. 2. 1干法刻蚀中的等离子体干法刻蚀工艺是利用气体中阴阳粒子解离后的等离子体来进行刻蚀的。
半导体工艺干法刻蚀气体
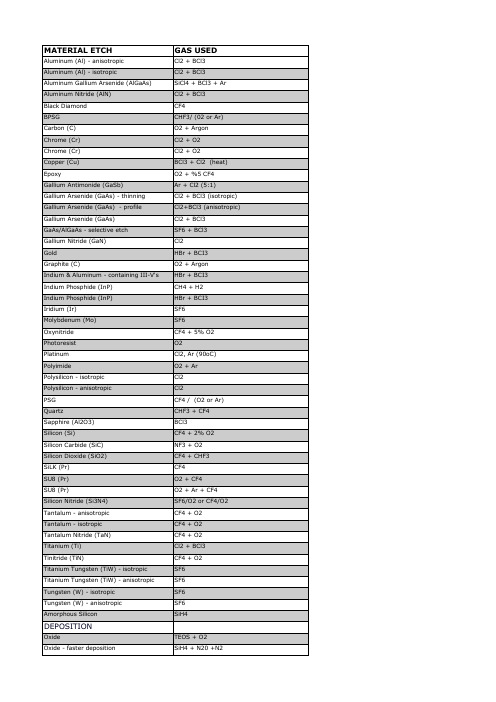