复合材料的分层缺陷
中温固化复合材料层压板分层缺陷注射修补工艺研究
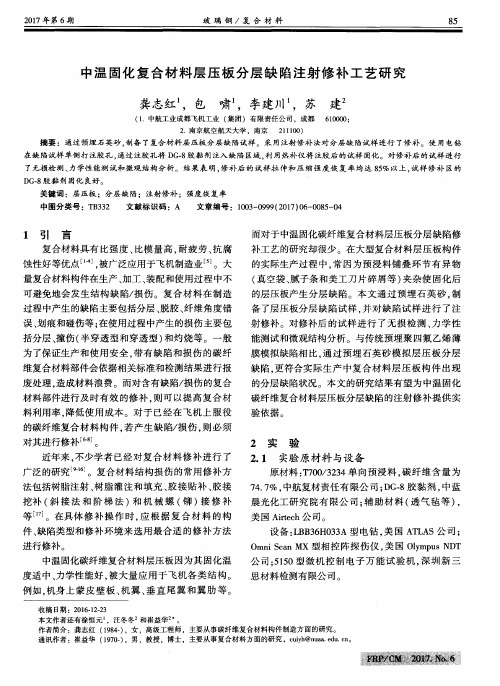
关键词 :层 压板 ;分层缺 陷:注射修补 ;强度恢 复率 中图分 类号 :T B 3 3 2 文献标识码 :A 文章编号 :1 0 0 3 — 0 9 9 9 ( 2 0 1 7 ) 0 6 — 0 0 8 5 — 0 4
1 引 言 复合材料具有 比强度 、 比模量高 , 耐疲 劳、 抗腐
碳纤 维 复合材 料层 压板 分 层缺 陷 的注射 修 补 提供 实
验依 据 。
料 利用 率 , 降低 使 用 成 本 。对 于 已经 在 飞 机上 服役 的碳纤 维 复合 材料 构 件 , 若 产 生缺 陷/ 损伤 , 则 必 须 对 其进 行修 补 [ 6 ] 。 近年来 , 不少 学 者 已经 对 复合 材 料 修 补 进 行 了 广 泛 的研究 『 9 。 。复合 材料 结 构 损 伤 的 常用 修补 方 法 包括 树脂 注射 、 树脂灌注和填充、 胶接贴补 、 胶 接 挖补 ( 斜 接 法 和 阶梯 法 ) 和机械螺 ( 铆) 接 修 补 等[ 1 引。在 具 体 修 补 操 作 时 , 应 根 据 复 合 材 料 的构
2 0 1 7年第 6期
玻 璃 钢 /复 合 材料 层 压 板 分层 缺 陷注射 修 补 工 艺研 究
龚志红 ,包 啸 ,李建川 ,苏 建
( 1 . 中航工业成都 飞机工业 ( 集团 )有限责任公司 ,成都 6 1 0 0 0 0 ;
2 . 南 京 航 空 航 天 大 学 。南 京 2 1 1 l O O )
8 6
中温 固化 复 合 材 料 层 压 板 分 层 缺 陷 注射 修 补 工 艺研 究
2 0 1 7年 6月
2 . 2 试 样 制备
而对于中温 固化碳纤维复合材料层压板分层缺陷修
民用飞机复材层压板分层缺陷修理方法研究
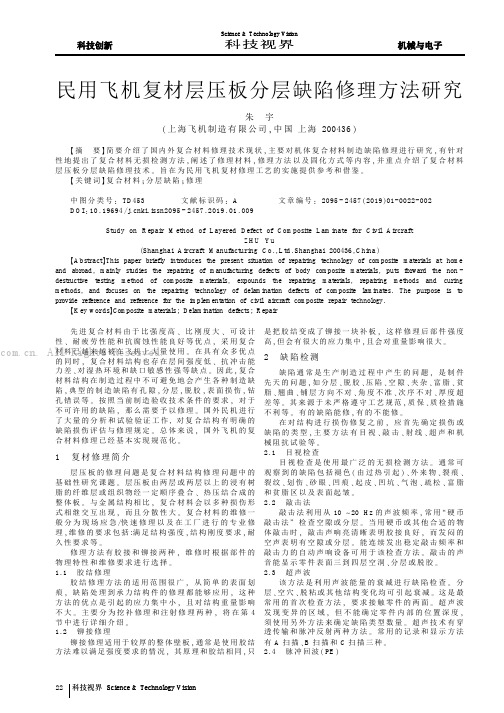
Sci ence &Technol ogy V i s i on科技视界先进复合材料由于比强度高、比刚度大、可设计性、耐疲劳性能和抗腐蚀性能良好等优点,采用复合材料已越来越被在飞机上大量使用。
在具有众多优点的同时,复合材料结构也存在层间强度低、抗冲击能力差、对湿热环境和缺口敏感性强等缺点。
因此,复合材料结构在制造过程中不可避免地会产生各种制造缺陷,典型的制造缺陷有孔隙,分层,脱胶,表面损伤,钻孔错误等。
按照当前制造验收技术条件的要求,对于不可许用的缺陷,那么需要予以修理。
国外民机进行了大量的分析和试验验证工作,对复合结构有明确的缺陷损伤评估与修理规定。
总体来说,国外飞机的复合材料修理已经基本实现规范化。
1复材修理简介层压板的修理问题是复合材料结构修理问题中的基础性研究课题。
层压板由两层或两层以上的浸有树脂的纤维层或组织物经一定顺序叠合、热压结合成的整体板。
与金属结构相比,复合材料会以多种损伤形式相继交互出现,而且分散性大。
复合材料的维修一般分为现场应急/快速修理以及在工厂进行的专业修理,维修的要求包括:满足结构强度,结构刚度要求,耐久性要求等。
修理方法有胶接和铆接两种,维修时根据部件的物理特性和维修要求进行选择。
1.1胶结修理胶结修理方法的适用范围很广,从简单的表面划痕,缺陷处理到承力结构件的修理都能够应用,这种方法的优点是引起的应力集中小,且对结构重量影响不大。
主要分为挖补修理和注射修理两种,将在第4节中进行详细介绍。
1.2铆接修理铆接修理适用于较厚的整体壁板,通常是使用胶结方法难以满足强度要求的情况,其原理和胶结相同,只是把胶结变成了铆接一块补板,这样修理后部件强度高,但会有很大的应力集中,且会对重量影响很大。
2缺陷检测缺陷通常是生产制造过程中产生的问题,是制件先天的问题,如分层、脱胶、压陷、空隙、夹杂、富脂、贫脂、翘曲、铺层方向不对、角度不准、次序不对、厚度超差等。
其来源于未严格遵守工艺规范,质保、质检措施不利等。
复合材料无损检测技术

五、超声波检测
原理:利用缺陷与基体间不同特征引起的波长吸收/反射差 异来判定被测物(20KHz);
优势
1. 操作简单;
局限
1. 不同的缺陷需使用
不同的探头; 2. 对人员要求高;
2. 可定位缺陷位置;
8
五、超声波检测
9
五、超声波检测
适用于:分层,孔隙等缺陷;
大型蜂窝结构部件、大曲面结构部件
3
三、X射线检测
原理:利用缺陷与基体间的密度差异引起的X射线吸收率;
局限
1. 设备复杂成本高; 2. 需安全防护; 3. 无法现场检测;
4
三、X射线检测
适用于:检测材料中的孔隙(黑影),裂纹(黑纹), 纤维屈曲(白纹),夹杂(白点)等 缺陷;
黑纹 白点
黑影
中小型复材部件
5
四、红外热成像检测
原理:利用缺陷与基体间不同热特征引起的温度差异来 判定被测物;
优势
1. 操作方便; 2. 设备简单; 3. 可现场检测;
局限
1. 要求工件传热性好; 2. 测试深度有限; 3. 灵敏度不高;
6
四、红外热成像检测
适用于:脱粘,分层等面积性缺陷;
复材薄板与金属胶接
复材无损检测技术
2018-4-27
目录
01-02 03-03 04-05 06-07 08-10
复材常见缺陷 复材常见检测技术 X射线检测
红外热成像检测
超声波检测
一、复材常见缺陷
分层
纤维弯曲
孔隙
基体开裂、脱粘
纤维断裂、突出
冲击、撞伤损伤
1
一、复材常见缺陷
1
分层: 存储时间过长;热膨胀系数不匹配;挥发物产生
复合材料构件分层缺陷的概率分析方法与群子理论模型

用超声 A扫 描 并 根 据 构 件 的 检测 标 准 确定 的 。在 无损检 测 中 , 通常 将底 波 消 失且 形 成 一 定 面积 的 缺
合 材料 构件 的报废 , 造 成重大 经济 损失 。 因此 , 高 品 质 与 高合格 率是 复合材 料制 造永恒 的 目标 。对 于 复 合 材料 构件 成型 工 艺质 量 的评价 , 即某 种 复 合 材料
的分层 缺 陷 , 提 出并 建立 了复 合材 料 构 件分 层 缺 陷
的概 率分析 方法 与群 子 理 论模 型 , 并 分 别利 用 这 两 种方 法对不 同构 形复合 材料构 件 的分 层缺 陷进行 了
成 型过程 ( 尤其是热压成型) 温 度 与 压 力 传 递 陷 控 制 问 题 变 得 极 为 复
构 件 分 层相 对 可 接 受 率 与反 映分 层 面积 倾 向性 的群 子 参 数 。结 果 表 明 , 两 种 统 计 方 法 对 分 层 缺 陷 的 评 价 结 果 一 致
性较好 , 构 形 复 杂 的复 合 材 料 构 件 产 生 大 分 层 的 倾 向 性 增 大且 分层 相对 可 接 受 率 较 低 。 关键词 : 复合材料 ; 工 艺 质量 ; 概率 ; 群 子 理 论
先 进 复合材料 因有 着传 统材料 无法 比拟 的综合
飞机铝蜂窝复合材料的典型缺陷检测

飞机铝蜂窝复合材料的典型缺陷检测摘要:蜂窝夹层结构复合材料在使用方面具有很好的性能,其具有比较好的强度,同时,抗冲击性能很好,在使用方面能够进行很好的设计,本文为有效检出飞机铝蜂窝复合材料的缺陷位置及缺陷大小,评估缺陷损伤程度,运用激光错位散斑检测方法对有无缺陷及缺陷位置进行了检测,并采用声阻检测方法对缺陷大小进行了评估.关键词:复合材料缺陷;激光错位散斑检测;声阻检测一、铝蜂窝夹层结构铝蜂窝芯材只要利用铝箔来实现不同方式的胶接,然后通过拉伸形成不同规格的蜂窝,芯材的性能和铝箔的厚度以及孔格的大小有直接关系,铝蜂窝芯材能够和不同蒙皮材料进行复合,这样就形成了铝蜂窝夹层结构复合材料。
铝蜂窝夹层结构复合材料具有加高的力学性能,而且,在制造成本方面比较低。
但是,铝蜂窝夹层结构复合材料在一些特定的环境中比较容易受到腐蚀,在受到冲击以后,铝蜂窝芯材会出现永久变形的情况,会导致蜂窝芯材和蒙皮发生分离的问题,导致材料的性能降低。
一些研究人员对胶接工艺对铝蜂窝夹层结构复合材料的影响进行了研究,主要从胶接剂的筛选、表面处理方法和固化工艺方面进行了论述,使用流动性比较好的胶膜,在表面处理方面采用磷酸阳极化处理方式,同时,在夹层结构方面通过对剪切强度进行对比,能够实现最佳的固化工艺。
铝蜂窝夹层结构在粘结成型方面大面积批量生产面临着非常大的问题,在固化过程中,可以对铝蜂窝夹层结构复合材料进行真空袋加压,这样铝蜂窝夹层结构复合材料的性能更好。
对铝蜂窝芯在压缩荷载作用下的荷载位移曲线特征进行研究,同时对在静态下的压缩荷载作用下的铝蜂窝变形特征进行掌握,可以从三个方向对铝蜂窝进行准静态压缩,由于材料的不同,会导致蜂窝芯出现不断的致密化,可以将不同方向的荷载位移曲线分为弹性区域、平缓区域和加速加强区域。
在轴向压缩过程中,试样在荷载最大值位置会出现失稳的情况,在失稳情况下,位移曲线会出现一些小的峰,这个过程铝蜂窝芯出现了逐步折叠失稳的情况。
层叠法制造复合材料制件分层原因分析及控制
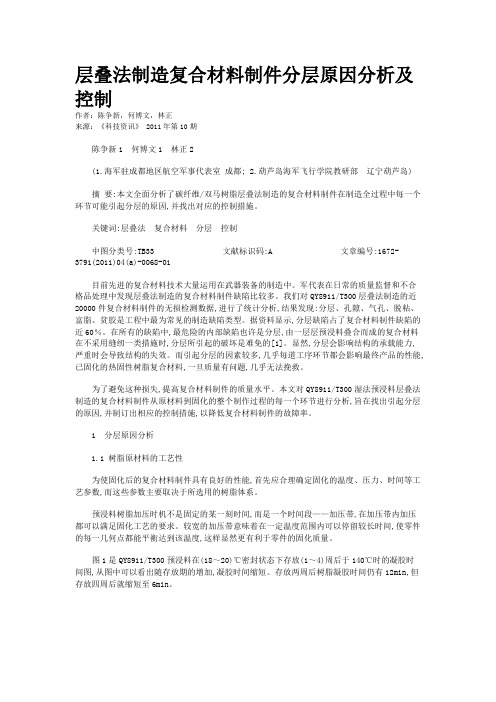
层叠法制造复合材料制件分层原因分析及控制作者:陈争新,何博文,林正来源:《科技资讯》 2011年第10期陈争新1 何博文1 林正2(1.海军驻成都地区航空军事代表室成都; 2.葫芦岛海军飞行学院教研部辽宁葫芦岛)摘要:本文全面分析了碳纤维/双马树脂层叠法制造的复合材料制件在制造全过程中每一个环节可能引起分层的原因,并找出对应的控制措施。
关键词:层叠法复合材料分层控制中图分类号:TB33 文献标识码:A 文章编号:1672-3791(2011)04(a)-0068-01目前先进的复合材料技术大量运用在武器装备的制造中。
军代表在日常的质量监督和不合格品处理中发现层叠法制造的复合材料制件缺陷比较多。
我们对QY8911/T300层叠法制造的近20000件复合材料制件的无损检测数据,进行了统计分析,结果发现:分层、孔隙、气孔、脱粘、富脂、贫胶是工程中最为常见的制造缺陷类型。
据资料显示,分层缺陷占了复合材料制件缺陷的近60%。
在所有的缺陷中,最危险的内部缺陷也许是分层,由一层层预浸料叠合而成的复合材料在不采用缝纫一类措施时,分层所引起的破坏是难免的[1]。
显然,分层会影响结构的承载能力,严重时会导致结构的失效。
而引起分层的因素较多,几乎每道工序环节都会影响最终产品的性能,已固化的热固性树脂复合材料,一旦质量有问题,几乎无法挽救。
为了避免这种损失,提高复合材料制件的质量水平。
本文对QY8911/T300湿法预浸料层叠法制造的复合材料制件从原材料到固化的整个制作过程的每一个环节进行分析,旨在找出引起分层的原因,并制订出相应的控制措施,以降低复合材料制件的故障率。
1 分层原因分析1.1 树脂原材料的工艺性为使固化后的复合材料制件具有良好的性能,首先应合理确定固化的温度、压力、时间等工艺参数,而这些参数主要取决于所选用的树脂体系。
预浸料树脂加压时机不是固定的某一刻时间,而是一个时间段——加压带,在加压带内加压都可以满足固化工艺的要求。
含分层缺陷复合材料层合板压缩强度试验研究
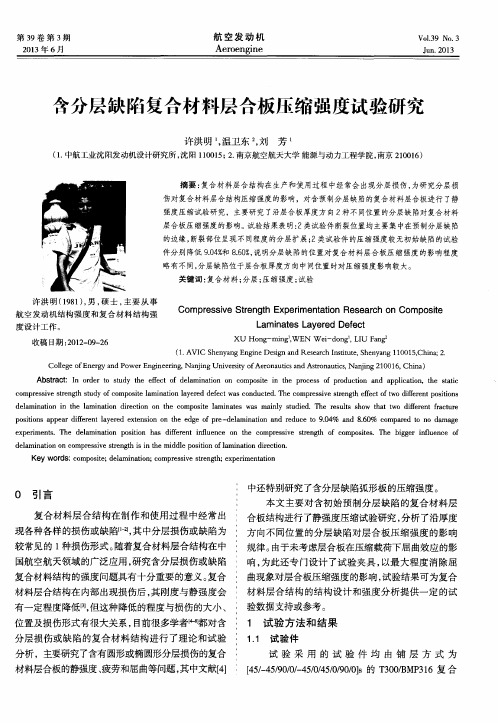
( 1 . AVI C S h e n y a n g E n g i n e De s i g n a n d Re s e a r c h I n s t i t u t e , S h e n y a n g 1 1 0 0 1 5 , Ch i n a ; 2 .
第3 9卷 第 3期
2 0 1 3年 6月
航 空 发 动 机
Ae ro e n g i n e
V0 1 - 3 9 No. 3
J u n . 2 0 1 3
含分层缺 陷 复合材 料层 合板压缩 强度试验研 究
许洪 明 , 温卫 东 , 刘 芳 。
( 1 . 中航工业沈阳发动机设计 研究 所 , 沈阳 1 1 0 0 1 5 ; 2 . 南京航空航天大学 能源与动力工程学 院, 南京 2 1 0 0 1 6 )
许洪明( 1 9 8 1 ) , 男, 硕士 , 主 要 从 事 航空 发动机 结构 强度和 复合 材料 结构 强
度设计 工作 。 收稿 日期 : 2 0 1 2 — 0 9 — 2 6
Co mp r e s s i v e St r e n g t h Ex p e r i me n t a t i o n Re s e ar c h o n Co mp o s i t e
c o mp r e s s i v e s t r e n g t h s t u d y o f c o mp o s i t e l a mi n a t i o n l a y e r e d d e f e c t w a s c o n d u c t e d . T h e c o mp r e s s i v e s t r e n g t h e f f e c t o f t wo d i f f e r e n t p o s i t i o n s d e l a mi n a t i o n i n t h e l a mi n a t i o n d i r e c t i o n o n t h e c o mp o s i t e l a mi n a t e s w a s ma i n l y s t u d i e d .T h e r e s u l t s s h o w t h a t t wo d i f f e r e n t f r a c t u r e p o s i t i o n s a p p e a r d i f f e r e n t l a y e r e d e x t e n s i o n o n t h e e d g e o f p r e - d e l a mi n a t i o n a n d r e d u c e t o 9 . 0 4 % a n d 8 . 6 0 % c o mp a r e d t o n o d a ma g e e x p e i r me n t s .T h e d e l a mi n a t i o n p o s i t i o n h a s d i f f e r e n t i n l f u e n c e o n t h e c o mp r e s s i v e s t r e n g t h o f c o mp o s i t e s .T h e b i g g e r i n l f u e n c e o f d e l a mi n a t i o n o n c o mp r e s s i v e s t r e n g t h i s i n t h e mi d d l e p o s i t i o n o f l a mi n a t i o n d i r e c t i o n . K e y wo r d s : c o mp o s i t e ; d e l a mi n a t i o n ; c o mp r e s s i v e s t r e n g t h ; e x p e i r me n t a t i o n
复合材料成型缺陷分析与控制

复合材料成型缺陷分析与控制在现代工业领域中,复合材料因其优异的性能,如高强度、高刚度、良好的耐腐蚀性等,被广泛应用于航空航天、汽车、船舶、体育器材等众多领域。
然而,复合材料的成型过程并非一帆风顺,常常会出现各种缺陷,这些缺陷不仅影响产品的外观质量,更可能严重削弱其性能和可靠性,甚至导致产品报废。
因此,对复合材料成型缺陷进行深入分析,并采取有效的控制措施,具有至关重要的意义。
一、复合材料成型缺陷的类型及成因(一)孔隙孔隙是复合材料成型中最常见的缺陷之一。
它表现为材料内部存在的微小空洞,其成因较为复杂。
树脂浸润纤维不充分、固化过程中产生的挥发物无法及时排出、成型压力不足等都可能导致孔隙的产生。
孔隙的存在会降低材料的强度和刚度,影响其耐疲劳性能和耐腐蚀性。
(二)分层分层指的是复合材料层间的分离现象。
通常是由于层间结合力不足、成型过程中的冲击或振动、树脂固化不均匀等原因引起的。
分层会显著降低复合材料的层间强度,使其承载能力大幅下降。
(三)纤维弯曲和断裂在成型过程中,纤维可能会发生弯曲和断裂。
这可能是由于纤维在铺放过程中受到不当的张力或压力,或者在模具中流动的树脂对纤维产生了剪切作用。
纤维的弯曲和断裂会直接影响复合材料的力学性能,使其强度和刚度达不到设计要求。
(四)树脂富脂和贫脂区树脂分布不均匀会导致富脂区和贫脂区的出现。
富脂区树脂含量过高,会增加材料的重量和成本,同时降低其强度;贫脂区则由于树脂不足,无法充分浸润和保护纤维,影响复合材料的性能和耐久性。
(五)表面缺陷表面缺陷包括表面粗糙、凹坑、鼓包等。
这可能是由于模具表面不光滑、脱模剂使用不当、树脂固化收缩不均等原因造成的。
表面缺陷不仅影响产品的外观质量,还可能成为应力集中点,降低材料的使用寿命。
二、复合材料成型缺陷的影响(一)力学性能下降孔隙、分层、纤维弯曲和断裂等缺陷都会导致复合材料的力学性能,如强度、刚度、韧性等下降。
这使得复合材料在使用过程中无法承受预期的载荷,增加了失效的风险。
分层损伤导致层合复合材料刚度下降的估算

分层损伤导致层合复合材料刚度下降的估算随着复合材料在航空航天、船舶和工程等领域的普及,对层合复合材料刚度下降的影响研究变得越来越重要。
一种常见的影响层合复合材料刚度下降的因素是复合材料的分层损伤。
分层损伤是指复合材料的表面层受到外力的作用后,表面层之间的破裂,导致层合复合材料的刚度下降。
同时,它还可能会对复合材料的性能产生负面影响,如改变结构形态、影响力学性能、降低耐久性能等。
为了评估分层损伤对层合复合材料刚度下降的影响,从实验和数值模拟的角度出发,采用破裂力学原理有效地预测表面层的破裂模式。
实验研究表明,分层损伤引起的层合复合材料刚度下降是由复合材料的材料特性,如各层的粘结剂和表面上的缺陷等因素所决定的。
在实验中,首先将层合复合材料放置在测试缝口中,再通过加载负荷来测定复合材料的刚度,以及不同类型的损伤对层合复合材料刚度的影响。
结果表明,与不受损复合材料相比,受到分层损伤的复合材料的抗压强度减弱,耐久性能明显降低,刚度显著下降。
另外,采用数值模拟法预测分层损伤的影响也是有效的。
在数值模拟中,采用有限元法,建立层合复合材料的数值模型。
在不同的损伤层次上,分析各材料的应力分布,有助于更好地理解层合复合材料刚度下降的机理。
综上所述,通过对实验和数值模拟,可以有效地评估分层损伤对层合复合材料刚度下降的影响。
在此基础上,还可以考虑一些有效的
改进措施,如提高层合复合材料的固结强度、改善表面缺陷和实施有效的防护措施等,以期望提高复合材料的刚度和耐久性能。
复合材料的分层缺陷

复合材料的分层缺陷引言目前被广泛用于飞机承力构件的纤维增强树脂基复合材料(CFRP)主要是层合板与层合结构。
在层合板的制造过程中,常由于许多不确定的因素,使复合材料结构发生分层、孔隙、气孔等等不同形式的缺陷;同时,复合材料层合板在装配与服役过程中所受到低能冲击很容易引发各种形式的损伤。
由于增强纤维铺设方向的不一致常导致铺层间刚度的不匹配,引发较高的层间应力,而层间应力的主要传递介质是较弱的树脂基体,因此对于复合材料层合板,分层是其主要的损伤形式。
有报导统计,复合材料层合板在加工、装配和使用过程中产生的分层损伤,占缺陷件的50%以上[1]。
分层常存在于结构内部,无法根据表面状态检测出来,并且分层的存在极大地降低了结构的刚度,特别在压缩载荷作用下,由于发生局部屈曲而导致分层扩展,使结构在低于其压缩强度时发生破坏。
在飞机研制与制造过程中,复合材料层合板的分层损伤问题一直是难以解决的结构问题之一,也是影响CFRP 在结构组分中应用的主要限制因素。
因此,如何充分地结合试验测试,利用数值模拟的方法评估分层的许和容限,成为决定飞机结构综合性能的亟待解决的关键问题。
1.1分层产生的原因Pagano 和Schoeppner [2] 根据复合材料构件的形状,将分层产生的原因分为两类。
第一类为曲率构件,工程中常见的曲率构件包括扇形体、管状结构、圆柱形结构、球形结构和压力容器等;第二类为变厚度截面,工程中常见于薄层板与补强件连接区域、自由边界处、粘合连接处及螺栓接合处等。
在上述结构件中,临近的两铺层极易在法向和剪切向应力作用下发生脱胶和形成层间裂纹。
以外,温湿效应、层板制备和服役状态等亦是分层产生的原因。
由于纤维与树脂的热膨胀系数以及吸湿率均存在差异,因此,不同铺层易在固化过程产生不同程度的收缩并在吸收湿气后产生不同程度的膨胀,不同程度的收缩与膨胀所产生的剩余压力是导致分层的源头之一[3,4] 。
在层合板的制备过程中,由于手工铺设质量具有分散性,极易形成富树脂区,进而引发树脂固化时铺层间的收缩程度差异,使层间具有较低的力学特性,极易形成分层[5,6] 。
纤维增强复合材料层合结构冲击损伤

纤维增强复合材料层合结构冲击损伤编辑整理:尊敬的读者朋友们:这里是精品文档编辑中心,本文档内容是由我和我的同事精心编辑整理后发布的,发布之前我们对文中内容进行仔细校对,但是难免会有疏漏的地方,但是任然希望(纤维增强复合材料层合结构冲击损伤)的内容能够给您的工作和学习带来便利。
同时也真诚的希望收到您的建议和反馈,这将是我们进步的源泉,前进的动力。
本文可编辑可修改,如果觉得对您有帮助请收藏以便随时查阅,最后祝您生活愉快业绩进步,以下为纤维增强复合材料层合结构冲击损伤的全部内容。
复合材料定义:复合材料通常由基体材料和增强材料两大组分构成,它不仅保持了组分材料自身的优良性能,而且通过材料互补改善或突出某些特殊性能。
改变组分材料品种或比例,可以得到不同品种和性能的复合材料。
复合材料分类:复合材料可分为金属基复合材料与非金属基复合材料,非金属基复合材料可分为树脂基复合材料与陶瓷基复合材料,树脂基复合材料具有质量轻、易于加工和改型等优点.复合材料特点:1.具有较高的比强度和比刚度2.具有良好的抗疲劳性能3.具有良好的减振性能4.具有良好的可设计性复合材料中的主要缺陷:先进复合材料中的缺陷类型一般包括: 孔隙、夹杂、裂纹、疏松、纤维分层与断裂、纤维与基体界面开裂、纤维卷曲、富胶或贫胶、纤维体积百分比超差、纤维基体界面结合不好、铺层或纤维方向误差、缺层、铺层搭接过多、厚度偏离、磨损、划伤等。
其中孔隙、分层与夹杂是最主要的缺陷。
材料中的缺陷可能只是一种类型,也可能是好几种类型的缺陷同时存在.缺陷对复合材料性能的影响:复合材料在成型、固化、使用过程中产生各种缺陷,不同的缺陷对复合材料性能都有着或多或少的影响。
孔隙是复合材料中常见的缺陷之一,过多的孔隙可降低复合材料层间剪切强度约30 %。
当受冲击及长期疲劳时 ,富脂及贫脂区首先开裂,这也标志着这些区域的力学性能不同程度降低。
纤维束的断裂也可使碳纤维复合材料拉伸强度下降约25 %,压缩强度损失约11 %。
热压罐成型复合材料成型工艺的常见缺陷及对策
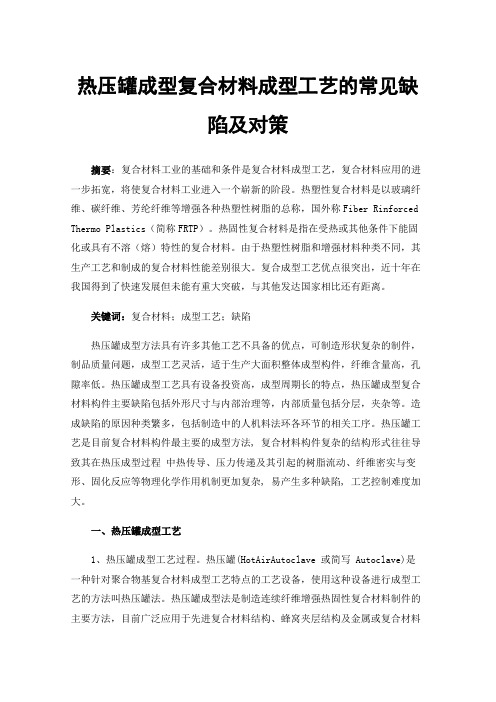
热压罐成型复合材料成型工艺的常见缺陷及对策摘要:复合材料工业的基础和条件是复合材料成型工艺,复合材料应用的进一步拓宽,将使复合材料工业进入一个崭新的阶段。
热塑性复合材料是以玻璃纤维、碳纤维、芳纶纤维等增强各种热塑性树脂的总称,国外称Fiber Rinforced Thermo Plastics(简称FRTP)。
热固性复合材料是指在受热或其他条件下能固化或具有不溶(熔)特性的复合材料。
由于热塑性树脂和增强材料种类不同,其生产工艺和制成的复合材料性能差别很大。
复合成型工艺优点很突出,近十年在我国得到了快速发展但未能有重大突破,与其他发达国家相比还有距离。
关键词:复合材料;成型工艺;缺陷热压罐成型方法具有许多其他工艺不具备的优点,可制造形状复杂的制件,制品质量问题,成型工艺灵活,适于生产大面积整体成型构件,纤维含量高,孔隙率低。
热压罐成型工艺具有设备投资高,成型周期长的特点,热压罐成型复合材料构件主要缺陷包括外形尺寸与内部治理等,内部质量包括分层,夹杂等。
造成缺陷的原因种类繁多,包括制造中的人机料法环各环节的相关工序。
热压罐工艺是目前复合材料构件最主要的成型方法, 复合材料构件复杂的结构形式往往导致其在热压成型过程中热传导、压力传递及其引起的树脂流动、纤维密实与变形、固化反应等物理化学作用机制更加复杂, 易产生多种缺陷, 工艺控制难度加大。
一、热压罐成型工艺1、热压罐成型工艺过程。
热压罐(HotAirAutoclave 或简写 Autoclave)是一种针对聚合物基复合材料成型工艺特点的工艺设备,使用这种设备进行成型工艺的方法叫热压罐法。
热压罐成型法是制造连续纤维增强热固性复合材料制件的主要方法,目前广泛应用于先进复合材料结构、蜂窝夹层结构及金属或复合材料胶接结构的成型中。
热压罐成型法也有一定的局限性,结构很复杂的构件,用该方法成型有一定困难。
同时此法对模具的设计技术要求很高,模具必须有良好的导热性、热态刚性和气密性。
碳纤维复合材料分层缺陷的超声相控阵检测方法
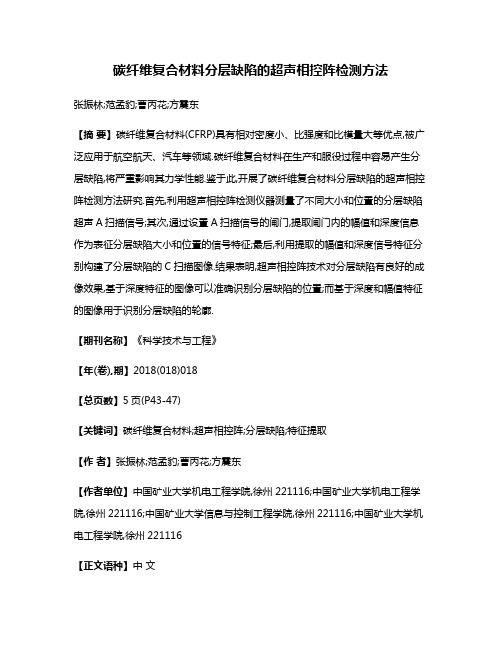
碳纤维复合材料分层缺陷的超声相控阵检测方法张振林;范孟豹;曹丙花;方震东【摘要】碳纤维复合材料(CFRP)具有相对密度小、比强度和比模量大等优点,被广泛应用于航空航天、汽车等领域.碳纤维复合材料在生产和服役过程中容易产生分层缺陷,将严重影响其力学性能.鉴于此,开展了碳纤维复合材料分层缺陷的超声相控阵检测方法研究.首先,利用超声相控阵检测仪器测量了不同大小和位置的分层缺陷超声A扫描信号;其次,通过设置A扫描信号的闸门,提取闸门内的幅值和深度信息作为表征分层缺陷大小和位置的信号特征;最后,利用提取的幅值和深度信号特征分别构建了分层缺陷的C扫描图像.结果表明,超声相控阵技术对分层缺陷有良好的成像效果,基于深度特征的图像可以准确识别分层缺陷的位置;而基于深度和幅值特征的图像用于识别分层缺陷的轮廓.【期刊名称】《科学技术与工程》【年(卷),期】2018(018)018【总页数】5页(P43-47)【关键词】碳纤维复合材料;超声相控阵;分层缺陷;特征提取【作者】张振林;范孟豹;曹丙花;方震东【作者单位】中国矿业大学机电工程学院,徐州221116;中国矿业大学机电工程学院,徐州221116;中国矿业大学信息与控制工程学院,徐州221116;中国矿业大学机电工程学院,徐州221116【正文语种】中文【中图分类】TB553碳纤维复合材料(carbon fiber reinforced plastics, CFRP)是由两种或两种以上不同性质的材料经过某种工艺合成一体后,所组成的具有优越性能的多相固体材料。
由于其具有相对密度小、比强度和比模量大、化学稳定性高等优良的综合性能,被广泛应用于航空航天、国防工程、汽车工业等领域[1]。
碳纤维复合材料在生产和服役过程中不可避免的会产生各种各样的缺陷,如分层、脱粘、裂纹、吻接、气孔、夹杂、孔隙、冲击损伤等 [2]。
分层是最主要的缺陷之一,它是指相邻层之间的局部分离或附着力不足,脱胶或开裂,分层降低了材料的压缩强度和刚度,影响材料结构的完整性。
碳纤维复合材料分层缺陷的超声相控阵检测方法研究

192研究与探索Research and Exploration ·智能检测与诊断中国设备工程 2024.01 (上)情况,因此本次实验采用无损检测方式来完成。
通过对该类型的复合材料内部不同位置的分层情况进行检测,可以得到较准确的检测结果,从而能够更加全面地掌握该类复合材料的质量状况,并且也有利于后续工作的开展。
此外,针对该类型的碳纤维复合材料,还要选择合适的检测设备以及相应的检测工艺参数等,以保证最终获得的检测数据具有较高的可靠度。
为了使所设计的检测方案能够顺利实施,首先,应当建立一个合理的实验平台,然后再利用相关的检测仪器对其实施检测操作。
在这个过程中,主要是将超声波换能器安装到试块上,同时使用螺栓固定住探头,最后再把它们放到指定的检测区域内。
需要注意的是,在实际的检测操作前,一定要提前做好准备工作,比如,对检测对象进行清理、碳纤维不打磨和除锈等,这样才能够确保检测效果符合要求。
另外,在正式开始检测前,也可以先进行预试验,通过多次反复地调整来确定最佳的检测位置以及检测角度等,从而提高最终的检测质量与效率。
在完成这些准备工作后,就可以开展具体的检测操作,并且还要保证每次都按照同样的步骤来进行,以便更好地控制误差问题。
一般来说,如果检测对象为碳纤维复合材料,那么就应该采用线扫描方式;但如果是金属材料焊缝时,则最好还是扇扫描方式。
一般情况下,在检测时会采用相控阵技术来实现对碳纤维复合材料的检测,但是由于该种技术具有很强的复杂性,所以要经过大量实践经验的积累,才可以获得良好的应用效果。
2.3 实验流程通过零度线性聚焦法则,我们将从第一个晶片开始激活,并在第64个晶片结束时进行电子扫描,每个阵元的聚焦深度为二毫米,并使用3000m/s 的纵波进行测量。
当所有晶片都被激发后,对于每层的厚度,可以计算出其声速,然后再用这种方式确定该区域内是否存在缺陷。
如果发现了缺陷,那么就要继续沿着垂直方向逐渐移动探头来检查缺陷的位置、大小以及形状等信息。
热压罐成型复合材料复杂结构对制造缺陷的影响规律
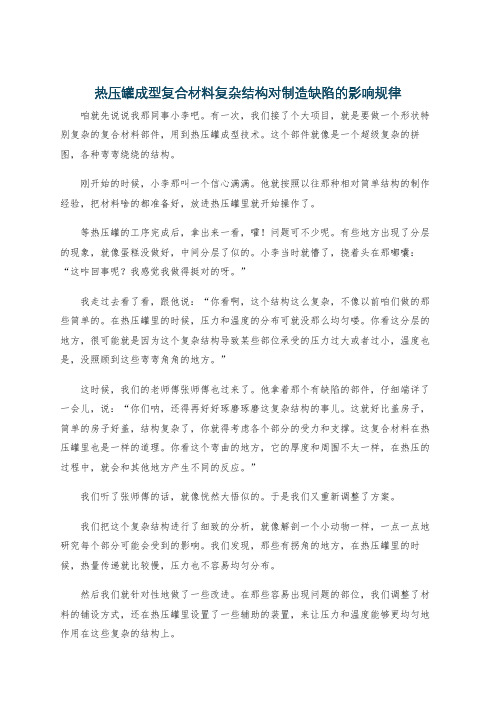
热压罐成型复合材料复杂结构对制造缺陷的影响规律咱就先说说我那同事小李吧。
有一次,我们接了个大项目,就是要做一个形状特别复杂的复合材料部件,用到热压罐成型技术。
这个部件就像是一个超级复杂的拼图,各种弯弯绕绕的结构。
刚开始的时候,小李那叫一个信心满满。
他就按照以往那种相对简单结构的制作经验,把材料啥的都准备好,放进热压罐里就开始操作了。
等热压罐的工序完成后,拿出来一看,嚯!问题可不少呢。
有些地方出现了分层的现象,就像蛋糕没做好,中间分层了似的。
小李当时就懵了,挠着头在那嘟囔:“这咋回事呢?我感觉我做得挺对的呀。
”我走过去看了看,跟他说:“你看啊,这个结构这么复杂,不像以前咱们做的那些简单的。
在热压罐里的时候,压力和温度的分布可就没那么均匀喽。
你看这分层的地方,很可能就是因为这个复杂结构导致某些部位承受的压力过大或者过小,温度也是,没照顾到这些弯弯角角的地方。
”这时候,我们的老师傅张师傅也过来了。
他拿着那个有缺陷的部件,仔细端详了一会儿,说:“你们呐,还得再好好琢磨琢磨这复杂结构的事儿。
这就好比盖房子,简单的房子好盖,结构复杂了,你就得考虑各个部分的受力和支撑。
这复合材料在热压罐里也是一样的道理。
你看这个弯曲的地方,它的厚度和周围不太一样,在热压的过程中,就会和其他地方产生不同的反应。
”我们听了张师傅的话,就像恍然大悟似的。
于是我们又重新调整了方案。
我们把这个复杂结构进行了细致的分析,就像解剖一个小动物一样,一点一点地研究每个部分可能会受到的影响。
我们发现,那些有拐角的地方,在热压罐里的时候,热量传递就比较慢,压力也不容易均匀分布。
然后我们就针对性地做了一些改进。
在那些容易出现问题的部位,我们调整了材料的铺设方式,还在热压罐里设置了一些辅助的装置,来让压力和温度能够更均匀地作用在这些复杂的结构上。
经过这么一番折腾,我们又重新做了一个部件。
这次从热压罐里拿出来的时候,那效果可就大不一样了。
虽然还有一些小瑕疵,但是分层这种大问题可就没有了。
碳纤维增强复合材料缺陷类型
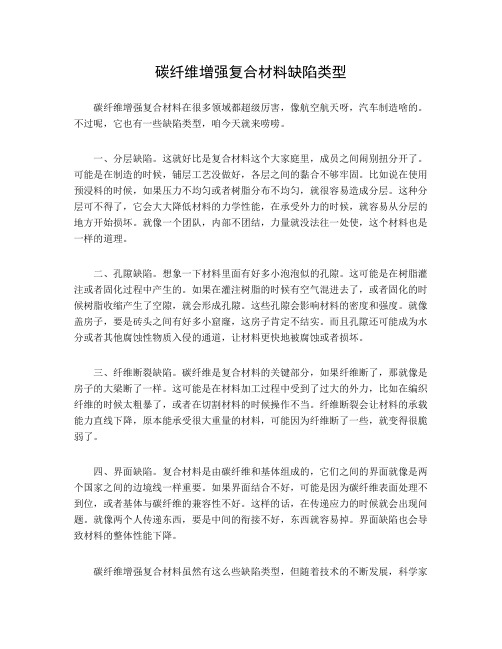
碳纤维增强复合材料缺陷类型碳纤维增强复合材料在很多领域都超级厉害,像航空航天呀,汽车制造啥的。
不过呢,它也有一些缺陷类型,咱今天就来唠唠。
一、分层缺陷。
这就好比是复合材料这个大家庭里,成员之间闹别扭分开了。
可能是在制造的时候,铺层工艺没做好,各层之间的黏合不够牢固。
比如说在使用预浸料的时候,如果压力不均匀或者树脂分布不均匀,就很容易造成分层。
这种分层可不得了,它会大大降低材料的力学性能,在承受外力的时候,就容易从分层的地方开始损坏。
就像一个团队,内部不团结,力量就没法往一处使,这个材料也是一样的道理。
二、孔隙缺陷。
想象一下材料里面有好多小泡泡似的孔隙。
这可能是在树脂灌注或者固化过程中产生的。
如果在灌注树脂的时候有空气混进去了,或者固化的时候树脂收缩产生了空隙,就会形成孔隙。
这些孔隙会影响材料的密度和强度。
就像盖房子,要是砖头之间有好多小窟窿,这房子肯定不结实。
而且孔隙还可能成为水分或者其他腐蚀性物质入侵的通道,让材料更快地被腐蚀或者损坏。
三、纤维断裂缺陷。
碳纤维是复合材料的关键部分,如果纤维断了,那就像是房子的大梁断了一样。
这可能是在材料加工过程中受到了过大的外力,比如在编织纤维的时候太粗暴了,或者在切割材料的时候操作不当。
纤维断裂会让材料的承载能力直线下降,原本能承受很大重量的材料,可能因为纤维断了一些,就变得很脆弱了。
四、界面缺陷。
复合材料是由碳纤维和基体组成的,它们之间的界面就像是两个国家之间的边境线一样重要。
如果界面结合不好,可能是因为碳纤维表面处理不到位,或者基体与碳纤维的兼容性不好。
这样的话,在传递应力的时候就会出现问题。
就像两个人传递东西,要是中间的衔接不好,东西就容易掉。
界面缺陷也会导致材料的整体性能下降。
碳纤维增强复合材料虽然有这么些缺陷类型,但随着技术的不断发展,科学家们肯定会找到更多更好的方法来克服这些问题,让这种材料发挥出更大的优势。
- 1、下载文档前请自行甄别文档内容的完整性,平台不提供额外的编辑、内容补充、找答案等附加服务。
- 2、"仅部分预览"的文档,不可在线预览部分如存在完整性等问题,可反馈申请退款(可完整预览的文档不适用该条件!)。
- 3、如文档侵犯您的权益,请联系客服反馈,我们会尽快为您处理(人工客服工作时间:9:00-18:30)。
复合材料的分层缺陷引言目前被广泛用于飞机承力构件的纤维增强树脂基复合材料(CFRP)主要是层合板与层合结构。
在层合板的制造过程中,常由于许多不确定的因素,使复合材料结构发生分层、孔隙、气孔等等不同形式的缺陷;同时,复合材料层合板在装配与服役过程中所受到低能冲击很容易引发各种形式的损伤。
由于增强纤维铺设方向的不一致常导致铺层间刚度的不匹配,引发较高的层间应力,而层间应力的主要传递介质是较弱的树脂基体,因此对于复合材料层合板,分层是其主要的损伤形式。
有报导统计,复合材料层合板在加工、装配和使用过程中产生的分层损伤,占缺陷件的 50%以上[1]。
分层常存在于结构内部,无法根据表面状态检测出来,并且分层的存在极大地降低了结构的刚度,特别在压缩载荷作用下,由于发生局部屈曲而导致分层扩展,使结构在低于其压缩强度时发生破坏。
在飞机研制与制造过程中,复合材料层合板的分层损伤问题一直是难以解决的结构问题之一,也是影响 CFRP 在结构组分中应用的主要限制因素。
因此,如何充分地结合试验测试,利用数值模拟的方法评估分层的许和容限,成为决定飞机结构综合性能的亟待解决的关键问题。
1.1 分层产生的原因Pagano 和 Schoeppner[2]根据复合材料构件的形状,将分层产生的原因分为两类。
第一类为曲率构件,工程中常见的曲率构件包括扇形体、管状结构、圆柱形结构、球形结构和压力容器等;第二类为变厚度截面,工程中常见于薄层板与补强件连接区域、自由边界处、粘合连接处及螺栓接合处等。
在上述结构件中,临近的两铺层极易在法向和剪切向应力作用下发生脱胶和形成层间裂纹。
以外,温湿效应、层板制备和服役状态等亦是分层产生的原因。
由于纤维与树脂的热膨胀系数以及吸湿率均存在差异,因此,不同铺层易在固化过程产生不同程度的收缩并在吸收湿气后产生不同程度的膨胀,不同程度的收缩与膨胀所产生的剩余压力是导致分层的源头之一[3, 4]。
在层合板的制备过程中,由于手工铺设质量具有分散性,极易形成富树脂区,进而引发树脂固化时铺层间的收缩程度差异,使层间具有较低的力学特性,极易形成分层 [5,6]。
在服役过程中,低 速冲击所产生的横向集中力是层合板结构形成分层的重要原因之一。
冲击引发的 临近铺层间的内部损伤、层合板制造过程中工具的掉落、复合材料部件的组装及 维修以及军用飞机及结构的弹道冲击等均会引发层间分层。
1.2分层的种类[5, 6]将分层分为内部分层(Internal delaminations)和浅表分层(Near-surface delaminationS 两类。
其中,内部分层源自层合板的内部铺层,由 于树脂裂纹和铺层界面间相互作用而形成,它的存在会降低结构件的承载能力。
特别是在压缩载荷作用下,层合板的弯曲行为受到严重影响(如图 1)。
虽然分 层将层合板分为两个部分,但是由于两个子层板变形间的相互作用, 层合板呈现 相似的偏转状态,发生整体屈曲。
浅表分层产生于层合板接近表面的浅层位置, 呈现出比内部分层更为复杂的 分层行为。
分层区域的变形受到厚子板的影响相对更小,浅表处的分层部分并不 定受较厚的子板的牵制而变形,因此对于浅表分层,不仅需要考虑浅表分层的 扩展,还需要考虑分层子板的局部稳定性。
根据载荷形式及分层状态可将浅表分 层分为如图2所示的种类。
Bolotin a)hl图1内部分层及对结构稳定性的影响图2浅表分层的种类在分层产生后,内部分层和浅表分层在静承载和疲劳载荷作用下可能发生分 层扩展,层合板的强度和稳定性明显下降。
确定分层缺陷的形式对复合材料结构 的完整性是十分层重要的。
1.3分层的微观结构在微观尺度下,层间裂纹扩展后将在裂纹前缘形成损伤区域。
根据树脂的韧性和应力水平(I 型,II 型,山 型和混合型,如图3所示),损伤区域的尺寸 和形状呈现不同的状态。
剪切载荷下裂纹尖端应力场的衰减较缓慢,因此 和III 型裂纹尖端的损伤区域比I 型区域广。
此外,受树脂基体的影响,脆性 与韧性树脂基体的损伤状态具有明显的区别。
在脆性树脂体系下,I 型裂纹尖端的损伤区域会发生微裂纹的合并和生长以 及纤维一树脂间的脱胶现象,上述现象都会诱发裂纹前进,其中,脱胶行为的发生常伴随着纤维桥接和纤维断裂现象的发生。
而对于剪切模式的II 型和III 型 分层,裂纹前缘处的微裂纹发生合并的现象,并与铺层角度呈 45°方向扩展, 直至到达富树脂区域。
界面处微裂纹的合并在纤维间的树脂区域呈现锯齿状, 如 图4所示。
而对于韧性材料体系,裂纹前缘的塑性变形推进裂纹扩展,呈现出 韧性断裂并伴随层间脱层现象的发生[7]f) n Liigc hucklcii iivith ^ccoiidtify trickII 型 张开型分空 fl > Open in tension A2厂7 bl 张幵的屈曲型分星 b'l Open buck led17》Ckiscti inlunsion 2仆.2h r 计边第庸曲型命层 ei F4gc buckled 二A-11)阖^^的叩曲乜专打』 出 Closed bu^kkd 2k 7 :次裂紋的边嫌砺曲刮分层mi. j图3 I型、II型和III型裂纹拓展模式a)____________b)图4层间II型分层的扩展模式:(a)裂纹尖端处微裂纹的形成;(b)微裂纹的生长及张开;(C)微裂纹的合并及剪切尖端的形成2准静态下分层行为预测方法分层力学由前苏联的固体物理学家Obreimoff (1894-1981)最先着手研究,1930年,他在题名“The Splitting Strength of Mica”⑹ 的论文中详细讨论了层间断裂韧性并研究了在剪切力作用下云母试样的分层现象。
时至今日,分层的力学问题在吸引重多科研工作者兴趣的同时,已取得了突出的成果,分层行为的预测方法发展成为强度理论方法、断裂力学方法和损伤力学方法等三类。
2.1强度理论方法强度理论方法是研究分层问题的传统方法,是以结构或材料抵抗损伤发生的能力为基础,通过将材料内部的节点应力与界面强度的大小进行比较来判断界面是否发生分层。
该预测分层损伤的方法由Whitney等[9]首先提出;在进一步应用平均应力准则的基础上,Kim等[11]对受拉、压载荷作用下的层合板的分层产生时的临界载荷值进行了预测。
但是由于不连续铺层端部易出现应力奇异, 应力准则方法高度依赖网格尺寸;且由于平均应力准则或点应力准则都引入了特征长度的概念,而特征长度并没有很强的理论基础,使该方法不能够准确地预测分层扩展行为[12] 02.2线弹性断裂力学方法断裂力学方法通过计算裂纹尖端应力场与裂纹尖端张开位移来评价界面的损伤状态。
在忽略材料非线性的前提下,可以采用线弹性断裂力学方法(LEFM)有效地预测分层扩展状态,该方法的核心内容为裂纹尖端能量释放率的计算。
计算应变能释放率的常用方法包括虚裂纹扩展技术(VCCT)、J积分、虚裂纹扩张和刚度微分方法等,通过比较应变能释放率分量的组合式与某临界值间的关系, 可以对分层的状态进行预测。
2.3损伤力学方法损伤力学方法是通过引入微缺陷 /微裂纹的面积等形式的损伤变量来预测界面处分层状态,相比断裂力学方法,该方法不仅可以预测已存在裂纹的扩展状态,更重要的是,可以预测新裂纹的产生。
以内聚力理论为基础,该方法考虑了复合材料基体与增强相间以化学反应的形式生成的一层界面物质层,以界面参数的形式,充分地反映了界面物质层的模量、强度和韧性等材料参数。
内聚力裂纹模型由Dugdale [13]和Barenblatt [14]首次提出:材料在屈服应力的作用下,会在裂纹前缘形成薄的塑性区域,在该区域范围内的裂纹表面有应力作用,此作用力为“内聚力”;而与之相对的裂纹表面不受任何应力作用的区域为断裂区(如图 5所示)。
虽然内聚力模型属于局部损伤模型[15],对网格具有依赖性,但由于其支持网格间的相互独立,因此可以方便地实现网格的充分细化,达到准确计算的目的。
采用内聚力模型方法可以同时预测分层的产生和扩展,可以同时完成损伤容限和强度分析。
参考文献:1王雪明 , 谢富原 , 李敏 , 王菲 , 张佐光 . 热压罐成型复合材料构件分层缺陷影响因素分析. 第十五届全国复合材料学术会议 . 20082N. J. Pagano, G. A.Schoeppner. Delamination of polymer matrix composites:problems andassessment,(Ed.) Anonymous Kelly, A.; Zweben, D., Oxford (UK).20003T. E. Tay, F. Shen. Analysis of delamination growth in laminated composites withconsideration for residual thermal stress effects. Journal of Composite Materials.2002, 36(11):1299~13204 A. S. Crasto, R. Y. Kim. Hygrothermal influence on the free -edge delaminationof composites under compressive loading, In: Composite Materials: Fatigue and Fracture 6, (Ed.) Anonymous Armanios, E.A., Philadelphia. 1997:381~3935V. V. Bolotin. Delaminations in composite structures: Its origin, buckling, growth and stability. Composites Part B-Engineering. 1996, 27(2):29~1456V. V. Bolotin. Mechanics of delaminations in laminate composite structures.Mechanics of Composite Materials. 2001, 37(-56):367~380 7W. L. Bradley, C. R. Corleto, D. P. Goetz. Fracture physics of delamination of composite materials. AFOSR-TR-88-0020. 19878N. Blanco. Variable mixed-mode delamination in composite laminates under fatigue conditions: testing and analysis. PhD Thesis, University of Girona.20059I. W. Obreimoff. The splitting strength of mica. Proceedings of the Royal Society of London A. 1930, 127:290-29710J. M. Whitney, R. J. Nuismer. Stress Fracture Criteria for Laminated Composite Containing Stress Concentrations. Journal of Composite Materials. 1974, 8: 253-26511R. Y. Kim, S. R. Soni. Experimental and Analytical Studies on the Onset of Delamination in Laminated Composites. Journal of Composite Materials. 1984,18: 70-8012Z. Petrossian, M. R. Wisnom. Prediction of delamination initiation and growth from discontinuous plies using interface elements. Composites Part A. 1998, 29A:503-51513D. S. Dugdale. Yielding of steel sheets containing slits. Journal of the Mechanics and Physics of Solids. 1960, 8:100-10414G. Barenblatt. The mathematical theory of equilibrium cracks in brittle fracture.Advances in Applied Mechanics. 1962, 7:55-12915Z. P. Ba?ant, M. Jir d seNonlocal integral formulations of plasticity and damage:survey of progress. J. Engineering Mechanics. 2002, 128:11-19149。