镀镍故障
镀镍问题与解决方案
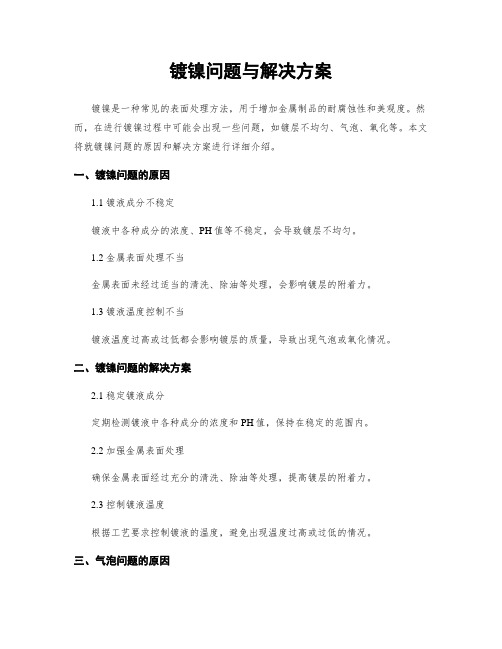
镀镍问题与解决方案镀镍是一种常见的表面处理方法,用于增加金属制品的耐腐蚀性和美观度。
然而,在进行镀镍过程中可能会出现一些问题,如镀层不均匀、气泡、氧化等。
本文将就镀镍问题的原因和解决方案进行详细介绍。
一、镀镍问题的原因1.1 镀液成分不稳定镀液中各种成分的浓度、PH值等不稳定,会导致镀层不均匀。
1.2 金属表面处理不当金属表面未经过适当的清洗、除油等处理,会影响镀层的附着力。
1.3 镀液温度控制不当镀液温度过高或过低都会影响镀层的质量,导致出现气泡或氧化情况。
二、镀镍问题的解决方案2.1 稳定镀液成分定期检测镀液中各种成分的浓度和PH值,保持在稳定的范围内。
2.2 加强金属表面处理确保金属表面经过充分的清洗、除油等处理,提高镀层的附着力。
2.3 控制镀液温度根据工艺要求控制镀液的温度,避免出现温度过高或过低的情况。
三、气泡问题的原因3.1 镀液中含有杂质镀液中可能存在杂质,导致镀层表面出现气泡。
3.2 镀液搅拌不均匀镀液搅拌不均匀会造成气泡在镀液中无法释放。
3.3 镀液中气体过多镀液中气体过多也会导致气泡问题的出现。
四、气泡问题的解决方案4.1 滤除镀液中的杂质定期对镀液进行过滤,去除其中的杂质,减少气泡问题的发生。
4.2 加强镀液搅拌确保镀液搅拌均匀,使气泡能够顺利释放。
4.3 控制镀液中气体含量适当控制镀液中气体的含量,避免气体过多导致气泡问题。
五、氧化问题的原因5.1 镀液中含氧量过高镀液中含氧量过高会导致镀层表面氧化。
5.2 镀层附着力不足镀层附着力不足会导致镀层表面容易氧化。
5.3 镀液中含有氧化物镀液中可能存在氧化物,会导致镀层表面出现氧化情况。
六、氧化问题的解决方案6.1 控制镀液中氧含量通过适当的方法控制镀液中氧含量,避免出现过高的情况。
6.2 提高镀层附着力加强金属表面处理,提高镀层的附着力,减少氧化问题的发生。
6.3 定期清洗镀液定期清洗镀液中的氧化物,保持镀液的清洁度,减少氧化问题的发生。
镀镍问题与解决方案

镀镍问题与解决方案引言概述:镀镍是一种常见的金属表面处理方法,它可以提高金属的耐腐蚀性、硬度和外观。
然而,在镀镍过程中,我们常常会遇到一些问题,如镀层不均匀、气泡、缺陷等。
为了解决这些问题,我们需要采取一些有效的解决方案。
正文内容:1. 镀层不均匀问题:1.1 控制电流密度:调整电流密度可以使镀层均匀。
在镀层不均匀的区域增加电流密度,而在均匀的区域减少电流密度。
1.2 改善搅拌条件:通过改善搅拌条件,如增加搅拌桨的数量或改变搅拌桨的位置,可以使电解液均匀分布,从而获得均匀的镀层。
2. 气泡问题:2.1 降低电流密度:气泡往往是由于过高的电流密度造成的。
降低电流密度可以减少气泡的产生。
2.2 提高搅拌效果:通过增加搅拌桨的转速或改变搅拌桨的形状,可以提高搅拌效果,将气泡从电解液中排出。
3. 缺陷问题:3.1 清洗金属表面:在镀镍之前,彻底清洗金属表面是非常重要的。
通过去除污垢、油脂和氧化物,可以减少缺陷的产生。
3.2 控制镀液温度:镀液温度对镀层质量有很大影响。
在适宜的温度范围内进行镀镍,可以减少缺陷的发生。
3.3 选择合适的镀液配方:不同的金属需要不同的镀液配方。
选择合适的镀液配方可以提高镀层的质量,减少缺陷的产生。
4. 防止镀层剥落问题:4.1 提高镀层附着力:通过在金属表面进行预处理,如机械打磨、化学处理等,可以增加镀层的附着力,防止镀层剥落。
4.2 控制镀液pH值:镀液的pH值对镀层的附着力有重要影响。
在适宜的pH范围内进行镀镍,可以提高镀层的附着力。
5. 提高镀层质量问题:5.1 优化镀液配方:通过调整镀液配方中的各种成分的比例,可以提高镀层的质量。
5.2 控制镀液温度和时间:镀液的温度和镀液时间对镀层质量有很大影响。
在适宜的温度和时间范围内进行镀镍,可以获得高质量的镀层。
总结:通过控制电流密度、改善搅拌条件、降低电流密度、提高搅拌效果、清洗金属表面、控制镀液温度、选择合适的镀液配方、提高镀层附着力、控制镀液pH值、优化镀液配方、控制镀液温度和时间等方法,可以解决镀镍过程中的一些常见问题,提高镀层的质量和均匀性,从而满足不同应用领域的需求。
镀镍问题与解决方案
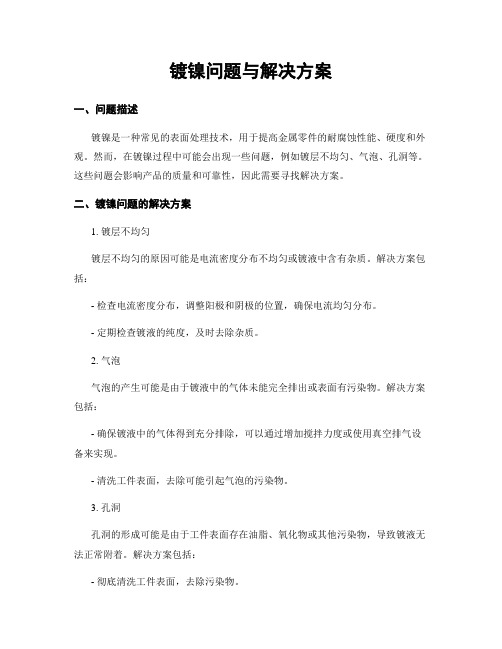
镀镍问题与解决方案一、问题描述镀镍是一种常见的表面处理技术,用于提高金属零件的耐腐蚀性能、硬度和外观。
然而,在镀镍过程中可能会出现一些问题,例如镀层不均匀、气泡、孔洞等。
这些问题会影响产品的质量和可靠性,因此需要寻找解决方案。
二、镀镍问题的解决方案1. 镀层不均匀镀层不均匀的原因可能是电流密度分布不均匀或镀液中含有杂质。
解决方案包括:- 检查电流密度分布,调整阳极和阴极的位置,确保电流均匀分布。
- 定期检查镀液的纯度,及时去除杂质。
2. 气泡气泡的产生可能是由于镀液中的气体未能完全排出或表面有污染物。
解决方案包括:- 确保镀液中的气体得到充分排除,可以通过增加搅拌力度或使用真空排气设备来实现。
- 清洗工件表面,去除可能引起气泡的污染物。
3. 孔洞孔洞的形成可能是由于工件表面存在油脂、氧化物或其他污染物,导致镀液无法正常附着。
解决方案包括:- 彻底清洗工件表面,去除污染物。
- 使用活性剂或表面活性剂改善镀液的润湿性,促进镀液与工件表面的接触。
4. 其他问题除了上述常见的问题外,镀镍过程中还可能出现其他问题,如镀层剥落、颜色不符等。
解决方案则需要根据具体情况进行调整,可能包括调整镀液配方、优化工艺参数或更换设备。
三、数据支持为了验证解决方案的有效性,可以进行一系列实验和测试,并记录相关数据。
例如:- 对镀液进行成分分析,以确保纯度满足要求。
- 对不同工艺参数下的镀层进行厚度测量,以评估镀层均匀性。
- 对镀层进行耐腐蚀性能测试,以验证解决方案对镀层质量的改进效果。
四、结论镀镍问题的解决方案需要综合考虑多个因素,包括镀液配方、工艺参数、设备状况等。
通过调整这些因素,可以有效解决镀镍过程中可能出现的问题,提高产品的质量和可靠性。
在实施解决方案之前,建议进行充分的实验和测试,以确保解决方案的有效性。
同时,定期维护设备、监测镀液的纯度和质量也是保证镀镍质量的重要措施。
电镀镍故障处理

电镀镍故障处理1,镀镍层发暗镀镍层表面发暗也是常见的电镀故障之一,这种故障多数出现在低电流密度区电镀获得的镀镍层,偶尔也出现在中电流密度区或高电流密度区,低电流密度区镀镍层发暗可能是镀镍液的温度太高,阴极电流密度太小,硫酸镍浓度太低;I,4一丁炔二醇或其他次级光亮剂过多或镀液中有铜、锌杂质污染引起;中电流密度区镀镍层发暗可能是由于镀液中次级光亮剂太少,有机杂质过多或有一定量的铁杂质污染造成的;高电流密度区镀层发暗可能是镀液pH值太高,初级光亮剂太少或镀液中有少量的铬酸盐、磷酸盐及铅杂质污染引起。
此外,镀前处理不良,镀件表面有碱膜或有机物吸附膜,或底镀层(氰化镀铜等)不好也会导致光亮镍镀层出现发暗现象。
可以取镀镍液做霍耳槽试验来分析这类电镀故障,对于低电流密度区出现的发暗现象,目前有的镀镍出现了比较好的走位剂,专门使得在低电流密度范围内获得光亮镀镍层。
另外还可以观察霍耳槽试片的外观进行逐步分析,如果镀液成分所做的霍耳槽样板上镀镍层状况良好,没有出现发暗的现象,那么电镀时出现的故障,就有可能是镀前处理不良或底镀层不好造成的,应该认真检查电镀镍前的情况。
若霍耳槽试验所得的阴极样板上出现低电流密度区镀层发暗,则可以根据前面提到的可能原因进行试验确定,或者加入合适的走位剂成分最后排除这种电镀故障。
中、高电流密度区的镀镍层发暗,也可用类似的方法进行试验分析。
2,镀镍层脆性镀层发脆,往往影响镀层的加工和质量,而且镀层的脆性与镀层应力有关。
镀镍液中次级光亮剂过多或初级光亮剂太少,铜、锌、铁或有机杂质过多,pH值过高或温度过低等都会使镀镍层发脆。
检查镀镍层脆性的方法,一是将镀好镍的小零件放在手中搓摩,或将镀镍薄片零件弯曲至18009若有碎镍层脱落,说明该镍层脆性大;另外就是将镍层镀在不锈钢试片上,控制镀层厚度在10ym左右,然后把镍层剥离下来,弯曲1800,用力挤压弯曲处,若不断裂,表示镀镍层不脆,弯曲折断,该镀镍层脆性就大。
镀镍问题与解决方案
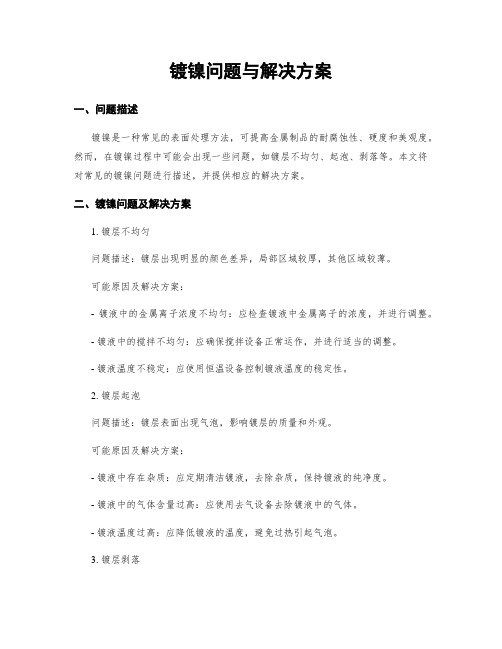
镀镍问题与解决方案一、问题描述镀镍是一种常见的表面处理方法,可提高金属制品的耐腐蚀性、硬度和美观度。
然而,在镀镍过程中可能会出现一些问题,如镀层不均匀、起泡、剥落等。
本文将对常见的镀镍问题进行描述,并提供相应的解决方案。
二、镀镍问题及解决方案1. 镀层不均匀问题描述:镀层出现明显的颜色差异,局部区域较厚,其他区域较薄。
可能原因及解决方案:- 镀液中的金属离子浓度不均匀:应检查镀液中金属离子的浓度,并进行调整。
- 镀液中的搅拌不均匀:应确保搅拌设备正常运作,并进行适当的调整。
- 镀液温度不稳定:应使用恒温设备控制镀液温度的稳定性。
2. 镀层起泡问题描述:镀层表面出现气泡,影响镀层的质量和外观。
可能原因及解决方案:- 镀液中存在杂质:应定期清洁镀液,去除杂质,保持镀液的纯净度。
- 镀液中的气体含量过高:应使用去气设备去除镀液中的气体。
- 镀液温度过高:应降低镀液的温度,避免过热引起气泡。
3. 镀层剥落问题描述:镀层与基材之间出现剥离现象,降低了镀层的附着力。
可能原因及解决方案:- 基材表面未经过充分处理:应确保基材表面清洁,去除油污和氧化物,增加镀层与基材的附着力。
- 镀液中的添加剂使用不当:应根据镀液的特性选择合适的添加剂,并按照规定的比例使用。
- 镀液中的酸碱度不适宜:应调整镀液的酸碱度,使其处于适宜的范围内。
4. 镀层颜色不符合要求问题描述:镀层的颜色与预期不符,无法满足客户的需求。
可能原因及解决方案:- 镀液中的添加剂使用不当:应根据所需颜色选择合适的添加剂,并按照规定的比例使用。
- 镀液中的金属离子浓度不适宜:应调整镀液中金属离子的浓度,以达到所需颜色。
- 镀液温度过高或过低:应控制镀液的温度,使其处于适宜的范围内。
5. 镀层出现氧化现象问题描述:镀层表面出现氧化物,影响镀层的质量和外观。
可能原因及解决方案:- 镀液中的氧含量过高:应使用除氧设备去除镀液中的氧气。
- 镀液中的添加剂使用不当:应根据镀液的特性选择合适的添加剂,并按照规定的比例使用。
镀镍问题与解决方案

镀镍问题与解决方案一、问题描述镀镍是一种常见的表面处理方法,用于提高金属制品的耐腐蚀性和装饰性。
然而,在镀镍过程中,可能会出现一些问题,如镀层不均匀、气泡、孔洞等。
这些问题会影响产品的质量和外观,因此需要找到相应的解决方案。
二、镀镍问题及解决方案1. 镀层不均匀问题描述:镀层在部分区域厚度不均匀,出现明显的颜色差异。
解决方案:- 检查电流密度:确保电流在整个镀镍过程中均匀分布,可以通过调整电流密度来解决问题。
- 检查镀液浓度:镀液浓度不均匀可能导致镀层不均匀,应确保镀液浓度均匀。
- 检查搅拌装置:搅拌装置的运行状况会影响镀液的流动性,进而影响镀层的均匀性,应确保搅拌装置正常运转。
2. 气泡问题问题描述:镀层表面出现气泡,影响镀层的光洁度和质量。
解决方案:- 检查镀液温度:镀液温度过高可能导致气泡产生,应控制镀液温度在适宜范围内。
- 检查镀液中的杂质:镀液中的杂质会促使气泡的形成,应定期清理镀液中的杂质。
- 检查镀液搅拌:充分搅拌镀液可以减少气泡的产生。
3. 孔洞问题问题描述:镀层表面出现孔洞,影响镀层的紧密性和耐腐蚀性。
解决方案:- 检查镀液成分:镀液成分不当可能导致孔洞的产生,应调整镀液成分以提高镀层的质量。
- 检查镀液pH值:镀液pH值过高或过低都会导致孔洞的产生,应保持镀液pH值在适宜范围内。
- 检查镀液搅拌:充分搅拌镀液可以减少孔洞的产生。
4. 其他问题除了上述常见的问题,镀镍过程中还可能出现其他问题,如黑斑、脱落等。
针对不同问题,可以采取以下解决方案:- 检查镀液中的杂质:杂质可能导致黑斑或脱落,应定期清理镀液中的杂质。
- 检查镀液温度和时间:温度和时间的控制可能影响镀层的质量,应确保镀液温度和时间在适宜范围内。
- 检查镀液pH值:pH值的不当可能导致镀层问题,应保持镀液pH值在适宜范围内。
三、总结镀镍过程中可能出现的问题包括镀层不均匀、气泡、孔洞等,这些问题会影响产品的质量和外观。
针对不同问题,可以采取相应的解决方案,如调整电流密度、镀液浓度、镀液温度和时间,清理镀液中的杂质等。
镀镍问题与解决方案
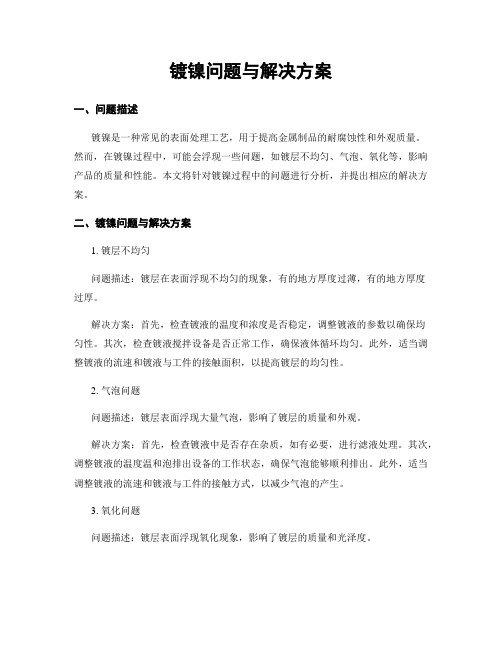
镀镍问题与解决方案一、问题描述镀镍是一种常见的表面处理工艺,用于提高金属制品的耐腐蚀性和外观质量。
然而,在镀镍过程中,可能会浮现一些问题,如镀层不均匀、气泡、氧化等,影响产品的质量和性能。
本文将针对镀镍过程中的问题进行分析,并提出相应的解决方案。
二、镀镍问题与解决方案1. 镀层不均匀问题描述:镀层在表面浮现不均匀的现象,有的地方厚度过薄,有的地方厚度过厚。
解决方案:首先,检查镀液的温度和浓度是否稳定,调整镀液的参数以确保均匀性。
其次,检查镀液搅拌设备是否正常工作,确保液体循环均匀。
此外,适当调整镀液的流速和镀液与工件的接触面积,以提高镀层的均匀性。
2. 气泡问题问题描述:镀层表面浮现大量气泡,影响了镀层的质量和外观。
解决方案:首先,检查镀液中是否存在杂质,如有必要,进行滤液处理。
其次,调整镀液的温度温和泡排出设备的工作状态,确保气泡能够顺利排出。
此外,适当调整镀液的流速和镀液与工件的接触方式,以减少气泡的产生。
3. 氧化问题问题描述:镀层表面浮现氧化现象,影响了镀层的质量和光泽度。
解决方案:首先,检查镀液中是否存在氧化剂过多的情况,如有必要,调整镀液的配方。
其次,加强镀液的循环和搅拌,以促进氧化物的排除。
此外,适当调整镀液的温度和镀液与工件的接触方式,以减少氧化的发生。
4. 色差问题问题描述:镀层表面浮现颜色不一致的现象,影响了产品的外观质量。
解决方案:首先,检查镀液中是否存在杂质或者其他污染物,如有必要,进行滤液处理。
其次,调整镀液的温度和浓度,以确保镀层颜色的一致性。
此外,加强镀液的循环和搅拌,以促进颜色的均匀分布。
5. 粘附力问题问题描述:镀层与基材之间的粘附力不够强,容易剥离或者脱落。
解决方案:首先,检查基材的表面处理是否充分,如有必要,进行打磨或者清洗。
其次,调整镀液的温度和浓度,以提高镀层与基材的结合力。
此外,加强镀液的循环和搅拌,以确保涂层能够均匀分布并与基材密切结合。
三、总结镀镍过程中可能浮现的问题包括镀层不均匀、气泡、氧化、色差和粘附力不足等。
实战:光亮镀镍故障处理解决方案

实战:光亮镀镍故障处理解决方案1前言镀镍是常见的镀种之一,它已从普通镀镍(暗镍)发展到全光亮镀镍,镀镍用的光亮剂也从无机光亮剂发展到第四代有机光亮剂。
电镀行业现用的全光亮镀镍槽液基本上是瓦特型,其配方及工艺规范除浓缩型光亮剂外,基本上大同小异。
镀镍出现故障时,应检查工艺执行情况,分析故障出现的原因,将其解决。
2故障产生原因及排除方法2.1工艺失衡2.1.1镀层光亮度不足2.1.1.1产生原因(1)光亮剂太少,主盐含量太低,阳极板太短太少,镍离子的沉积速度与迁移速度达不到平衡,致使镀层光亮度不足。
(2)pH和温度太高。
此时主盐易水解成Ni(OH)2沉淀,部分Ni(OH)2夹杂在镀层中,造成镀层光亮度不足。
(3)酸性镀铜后,零件未洗净。
此时零件表面(铜层)上有一层碱性膜,镍沉积在膜层上,致使镀层达不到镜面光亮。
2.1.1.2排除方法(1)补充主光亮剂,相应地也需补充助光剂。
按工艺要求调整主盐及其它组成,增加阳极镍板。
(2)用稀硫酸调节pH,降低温度至工艺规范。
(3)酸性镀铜后应彻底洗净零件,必要时可用稀硫酸除膜。
2.1.2镀镍层呈橘皮状2.1.2.1产生原因镀液pH太高,润湿剂过量时,润湿剂易与Ni2+作用,生成不溶性的化合物,杂乱地吸附(或沉淀)在零件表面上,造成镀层厚薄不均。
2.1.2.2排除方法加入少量活性炭吸附掉部分润湿剂,过滤后再用稀硫酸调节pH至工艺规范。
2.1.3镍层易烧焦2.1.3.1产生原因镀液中主盐太少,温度太低,pH过高,电流密度太大。
镍沉积的过程中,失去Ni2+的量与迁移到阴极附近的Ni2+量需达到动态平衡。
但是,由于主盐太少,温度太低,很低浓度的Ni2+在低温条件下只能缓慢地迁移到阴极附近放电沉积。
同时,pH太高使本来就很稀少的Ni2+还有部分生成微溶于水的浅绿色Ni(OH)2沉淀,造成镀液中Ni2+更少。
在大电流密度作用下,阴极附近的正负离子达不到平衡,致使镀层烧焦。
2.1.3.2排除方法按分析报告补充主盐,提高镀液温度,用稀硫酸调节pH至工艺规范,过滤镀液,适当调整电流密度。
镀镍问题与解决方案
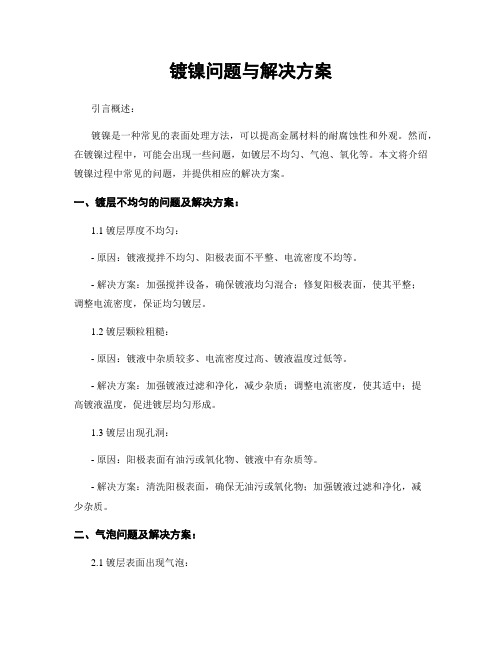
镀镍问题与解决方案引言概述:镀镍是一种常见的表面处理方法,可以提高金属材料的耐腐蚀性和外观。
然而,在镀镍过程中,可能会出现一些问题,如镀层不均匀、气泡、氧化等。
本文将介绍镀镍过程中常见的问题,并提供相应的解决方案。
一、镀层不均匀的问题及解决方案:1.1 镀层厚度不均匀:- 原因:镀液搅拌不均匀、阳极表面不平整、电流密度不均等。
- 解决方案:加强搅拌设备,确保镀液均匀混合;修复阳极表面,使其平整;调整电流密度,保证均匀镀层。
1.2 镀层颗粒粗糙:- 原因:镀液中杂质较多、电流密度过高、镀液温度过低等。
- 解决方案:加强镀液过滤和净化,减少杂质;调整电流密度,使其适中;提高镀液温度,促进镀层均匀形成。
1.3 镀层出现孔洞:- 原因:阳极表面有油污或氧化物、镀液中有杂质等。
- 解决方案:清洗阳极表面,确保无油污或氧化物;加强镀液过滤和净化,减少杂质。
二、气泡问题及解决方案:2.1 镀层表面出现气泡:- 原因:镀液中存在气体、阳极表面有油污或氧化物等。
- 解决方案:提前排除镀液中的气体;清洗阳极表面,确保无油污或氧化物。
2.2 镀层内部出现气泡:- 原因:镀液中存在气体、镀层形成速度过快等。
- 解决方案:提前排除镀液中的气体;调整镀液成分和工艺参数,使镀层形成速度适中。
2.3 镀层表面出现气孔:- 原因:镀液中存在气体、镀液温度过低等。
- 解决方案:提前排除镀液中的气体;提高镀液温度,促进气泡的释放。
三、氧化问题及解决方案:3.1 镀层表面出现氧化:- 原因:镀液中存在氧气、阳极表面有油污或氧化物等。
- 解决方案:排除镀液中的氧气;清洗阳极表面,确保无油污或氧化物。
3.2 镀层出现氧化脱落:- 原因:镀液中存在氧气、镀层厚度过大等。
- 解决方案:排除镀液中的氧气;调整镀层厚度,使其适中。
3.3 镀层颜色发生变化:- 原因:镀液中存在杂质、镀液温度过高等。
- 解决方案:加强镀液过滤和净化,减少杂质;调整镀液温度,使其适中。
镀镍问题与解决方案
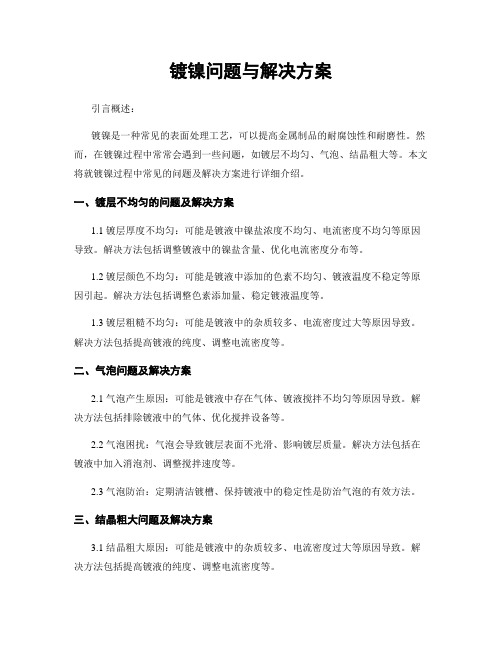
镀镍问题与解决方案引言概述:镀镍是一种常见的表面处理工艺,可以提高金属制品的耐腐蚀性和耐磨性。
然而,在镀镍过程中常常会遇到一些问题,如镀层不均匀、气泡、结晶粗大等。
本文将就镀镍过程中常见的问题及解决方案进行详细介绍。
一、镀层不均匀的问题及解决方案1.1 镀层厚度不均匀:可能是镀液中镍盐浓度不均匀、电流密度不均匀等原因导致。
解决方法包括调整镀液中的镍盐含量、优化电流密度分布等。
1.2 镀层颜色不均匀:可能是镀液中添加的色素不均匀、镀液温度不稳定等原因引起。
解决方法包括调整色素添加量、稳定镀液温度等。
1.3 镀层粗糙不均匀:可能是镀液中的杂质较多、电流密度过大等原因导致。
解决方法包括提高镀液的纯度、调整电流密度等。
二、气泡问题及解决方案2.1 气泡产生原因:可能是镀液中存在气体、镀液搅拌不均匀等原因导致。
解决方法包括排除镀液中的气体、优化搅拌设备等。
2.2 气泡困扰:气泡会导致镀层表面不光滑、影响镀层质量。
解决方法包括在镀液中加入消泡剂、调整搅拌速度等。
2.3 气泡防治:定期清洁镀槽、保持镀液中的稳定性是防治气泡的有效方法。
三、结晶粗大问题及解决方案3.1 结晶粗大原因:可能是镀液中的杂质较多、电流密度过大等原因导致。
解决方法包括提高镀液的纯度、调整电流密度等。
3.2 结晶粗大影响:结晶粗大会导致镀层表面不光滑、影响镀层的耐腐蚀性能。
解决方法包括优化镀液成分、控制电流密度等。
3.3 结晶粗大防治:定期清洁镀槽、保持镀液中的稳定性是防治结晶粗大的有效方法。
四、镀液稳定性问题及解决方案4.1 镀液变质原因:可能是镀液中的添加剂浓度不稳定、镀槽温度波动等原因导致。
解决方法包括定期检测镀液成分、保持镀槽温度稳定等。
4.2 镀液变质影响:镀液变质会导致镀层质量下降、影响镀层的性能。
解决方法包括及时更换镀液、加强镀液管理等。
4.3 镀液变质防治:定期监测镀液质量、避免镀液受到外界污染是防治镀液变质的有效方法。
五、镀层质量检测问题及解决方案5.1 镀层质量检测方法:常用的镀层质量检测方法包括厚度测量、硬度测试、显微镜观察等。
镀镍常见故障及解决办法

镀镍常见故障及解决办法(1)沉速低镀液pH值过低:测pH值调整,并控制pH在下限值。
虽然pH值较高能提高沉速,但会影响镀液稳定性。
镀液温度过低:要求温度达到规范时下槽进行施镀。
新开缸第一批工件下槽时,温度应达到上限,反应开始后,正常施镀时,温度在下限为好。
溶液主成分浓度低:分析调整,如还原剂不足时,添加还原补充液;镍离子浓度偏低时,添加镍盐补充液。
对于上规模的化学镀镍,设自动分析、补给装置是必要的,可以延长连续工作时间(由30h延至56h)和镍循环周期(由6周延至11周)。
亚磷酸根过多:弃掉部分镀液。
装载量太低:增加受镀面积至1dm2/L。
稳定剂浓度偏重:倾倒部分,少量多次加浓缩液。
(2)镀液分解(镀液呈翻腾状,出现镍粉)温度过高或局部过热:搅拌下加入温去离子水。
次亚磷酸钠大多:冲稀补加其它成分。
镀液的pH值过高:调整pH值至规范值。
机械杂质:过滤除去。
装载量过高:降至1dm2/L槽壁或设备上有沉淀物:滤出镀液,退镀清洗(用3%HNO3溶液)。
操作温度下补加液料大多:搅拌下少量多次添加。
稳定剂带出损失:添加少量稳定剂。
催化物质带入镀液:加强镀前清洗。
镀层剥离碎片:过滤镀液。
(3)镀层结合力差或起泡镀前处理不良:提高工作表面的质量,加工完成后应清除工件上所有的焊接飞溅物和焊渣。
工件表面的粗糙度应达到与精饰要求相当的粗糙义,如碳钢工件表面粗糙度Ra<1.75μm时,很难获得有良好附着力的镀层;对于严重锈蚀的非加工表面,可用角向磨光机打磨,最好采用喷砂或喷丸处理;工件镀前适当的活化处理可以提高镀层的附着力。
如合金钢、钛合金可用含氟化物的盐酸活化后,与碳钢件混装施镀;高级合金钢和铅基合金预镀化学镍;碳钢活化时注意脱碳。
温度波动太大:控制温度在较小的范围波动。
下槽温度太低:适当提高下槽温度。
清洗不良:改进清洗工序。
金属离子污染:用大面积废件镀而除去。
有机杂质污染:活化炭1-2g/L 处理。
热处理不当:调整热处理时间和温度。
镀镍故障
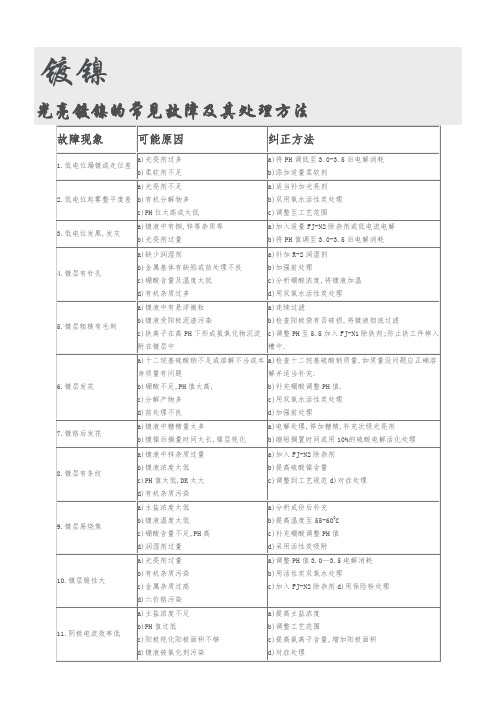
氯化镍添加过量阳极会出现异常溶解,溶液中泥渣增多,继而使镀层产生毛刺。
取出原使用的铸造镍板,改用电解镍板(电解镍板在高氯化镍溶液中溶解性比浇铸镍均匀),同时用的确良布包扎镍板,经此改进后,镀层出现毛刺问题基本得到解决
光亮镀镍电流密度过大引起镍层发雾、发花
电流密度过大会引起镀层发雾,即我们所说的烧焦。
c)分解产物多
d)前处理不良
a)检查十二烷基硫酸钠质量,如质量没问题应正确溶解并适当补充.
b)补充硼酸调整PH值.
c)用双氧水活性炭处理
d)加强前处理
7.镀铬后发花
a)镀液中糖精量太多
b)镀镍后搁量时间太长,镍层钝化
a)电解处理,停加糖精,补充次级光亮剂
b)缩短搁置时间或用10%的硫酸电解活化处理
8.镀层有条纹
溶液中镍盐含量过高引起镀镍层发雾、发花
光亮镀镍溶液中镍盐含量过高引起镀镍层发雾、发花
溶液中镍盐含量过低引起镀镍层发雾、发花
光亮镀镍出现发花较易察觉,由于活化剂、氯化镍含量的严重不足,镍阳极严重钝化,最后出现镍层发花的严重后果。
由此可见,维护镍盐含量也是保证光亮镀镍层质量的关键。
镀液pH值过高引起镀镍层发雾、发花
(6)前处理不良;
(7)氯离子含量过低。
处理方法
(1)参照上述相关处理方法除去。
(2)用低电流密度电解或活性炭吸附。
(3)调高pH值至工艺规范。
(4)整修或更换新的挂具。
(5)参照上述相关处理方法除去。
(6)检查前道镀铜后表面清洗状况,并加以彻底清洗干净。
(7)按分析结果添加氯镍至工艺规范。氯化物能减少阳极钝化,使镍阳极正常溶解,提高镀液导电能力和改善镀液的覆盖能力、分散能力。
电镀镍工艺故障的九大原因与排除

原因:硼酸不足、金属盐的浓度低、工作温度太低、电 流密度太高、PH值太高或搅拌不充分。7、沉积速率低PH 值低或电流密度低都会造成沉积速率低。8、镀层起泡或 起皮镀前处理不
良、中间断电时间过长、有机杂质污染、电流密度过大、 温度太低、PH值太高或太低、杂质的影响严重时会产生 起泡或起皮现象。9、阳极钝化阳极活化剂不足,阳极面 积太小电流密度太
会造成镍镀层的自身剥落;温度太低,也会产生剥落现象。 4、镀层脆、可焊性差当镀层受弯曲或受到某种程度的磨 损时,通常会显露出镀层的脆性,这就表明存在有机物 或重金属物质污染
。添加剂过多,使镀层中夹带的有机物和分解产物增多, 是有机物污染的主要来源,可用活性炭加以处理;重金属 杂质可用电解等方法除去。5、镀层发暗和色泽不均匀镀 层发暗和色泽不均
我们通常把小的麻点叫针孔,前处理不良、有金属关键所在。1、麻坑(针孔)麻坑是 有机物污染的结果
。大的麻坑通常说明有油污染。搅拌不良,就不能驱逐 掉气泡,这就会形成麻坑。可以使用润湿剂来减小它的 影响,我们通常把小的麻点叫针孔,前处理不良、有金 属杂质、硼酸含量太少、
匀,说明有金属污染。因为一般都是先镀铜后镀镍,所 以带入的铜溶液是主要的污染源。重要的是,要把挂具 所沾的铜溶液减少到最低程度。为了除去槽中的金属污 染,采用波纹钢板作阴极
,在0.12~0.50A/d㎡的电流密度下,电解处理。前处理 不良、底镀层不良、电流密度太小、主盐浓度太低,导 电接触不良都会影响镀层色泽。6、镀层烧伤引起镀层烧 伤的可能
镀液温度太低都会产生针孔,所以镀液维护及严格控制 流程是关键所在。2、粗糙(毛刺)粗糙就说明溶液脏,经 充分过滤就可纠正;PH太高易形成氢氧化物沉淀应加以控 制;电流密度太
高、阳极泥及补加水不纯带入杂质,严重时都将产生粗 糙(毛刺)。3、结合力低如果铜镀层未经活化去氧化层, 铜和镍之间的附着力就差,就会产生镀层剥落现象。如 果电流中断,有可能
镀镍问题与解决方案
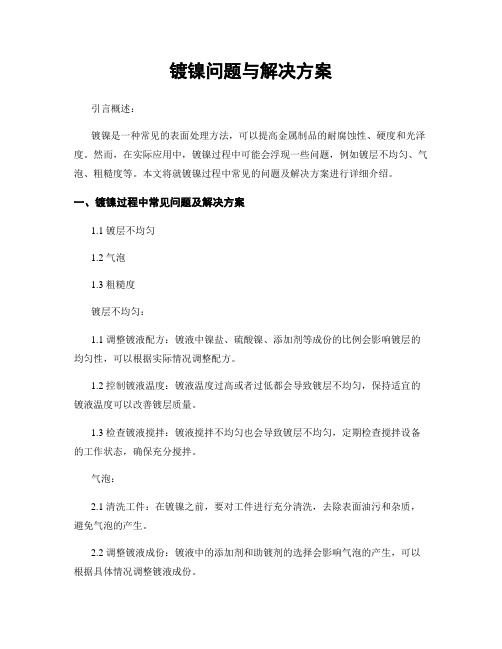
镀镍问题与解决方案引言概述:镀镍是一种常见的表面处理方法,可以提高金属制品的耐腐蚀性、硬度和光泽度。
然而,在实际应用中,镀镍过程中可能会浮现一些问题,例如镀层不均匀、气泡、粗糙度等。
本文将就镀镍过程中常见的问题及解决方案进行详细介绍。
一、镀镍过程中常见问题及解决方案1.1 镀层不均匀1.2 气泡1.3 粗糙度镀层不均匀:1.1 调整镀液配方:镀液中镍盐、硫酸镍、添加剂等成份的比例会影响镀层的均匀性,可以根据实际情况调整配方。
1.2 控制镀液温度:镀液温度过高或者过低都会导致镀层不均匀,保持适宜的镀液温度可以改善镀层质量。
1.3 检查镀液搅拌:镀液搅拌不均匀也会导致镀层不均匀,定期检查搅拌设备的工作状态,确保充分搅拌。
气泡:2.1 清洗工件:在镀镍之前,要对工件进行充分清洗,去除表面油污和杂质,避免气泡的产生。
2.2 调整镀液成份:镀液中的添加剂和助镀剂的选择会影响气泡的产生,可以根据具体情况调整镀液成份。
2.3 控制镀液搅拌速度:搅拌速度过快或者过慢都会导致气泡的产生,控制好搅拌速度可以减少气泡问题。
粗糙度:3.1 调整镀液温度:镀液温度过高或者过低都会导致镀层粗糙,保持适宜的镀液温度可以改善镀层质量。
3.2 检查镀液PH值:镀液PH值的变化也会影响镀层的粗糙度,定期检查PH 值并进行调整。
3.3 检查工件表面处理:工件表面处理不当也会导致镀层粗糙,确保工件表面平整光滑可以减少粗糙度问题。
四、结语镀镍是一种常见的表面处理方法,但在实际应用中可能会浮现一些问题。
通过调整镀液配方、控制镀液温度、检查镀液搅拌等方法,可以有效解决镀镍过程中的常见问题,提高镀层质量。
希翼本文的介绍对大家在镀镍过程中遇到问题时有所匡助。
镀镍故障

镀镍故障镀镍光亮镀镍的常见故障及其处理方法光亮镀镍故障处理针孔1. 针孔、麻点呈癣状。
大多在镀件下面产生原因镀液中铁杂质积累过多。
处理方法去除铁杂质最有效的处理方法,是用质量分数为30%的双氧水2〜4 mL/L,将镀液中二价铁氧化成三价铁;再用质量分数为5%的氢氧化钠或碳酸镍溶液调高pH值至5. 5〜6. 0,静置8 h以上,使Fe_成为Fe(on)沉淀,过滤除去。
如果不能停产,可用电解法,增大阴极面积,用0. 1 A / dm2阴极电流密度电解处理一段时间,问题得到缓解。
2. 针孔、麻点在镀件棱边和面向阳极的一面产生原因(1) 阴极电流密度过大;(2) 金属杂质积累过多;(3) 硼酸含量过低。
处理方法(1) 降低阴极电流密度。
(2) 参照上述相关处理方法除去。
(3) 根据化学分析结果添加硼酸。
镀液中硼酸含量过低,必然使pH值升高,产生氢氧化物,与镍层一起沉积,使镀层岀现针孔、麻点。
光亮镀镍层产生针孔与麻点的基本原因,是镀镍时阴极有氢气析岀,吸附在镀件表面上,阻碍镀层金属的沉积。
如果氢气泡在镀件上停留的时间长,就形成针孔;停留的时间短,就形成麻点。
因此,针孔、麻点往往混杂在一起。
结合力不良1整个镀层从基体脱落产生原因(1) 工件前处理不良;(2) 钢铁件阴极除油或化学浸蚀的时间长,基体渗氢,电镀后氢气外溢。
处理方法(1) 加强对工件在预镀前的除油、除锈和清洗工序,确保基体表面洁净。
(2) 适当缩短阴极电解除油、酸洗时间,防止工件基体渗氢。
2镀镍层起泡、脱皮产生原因(1) 复杂零件或挂具涂料绝缘层破裂而夹带溶液引起起泡;(2) 镀液中十二烷基硫酸钠含量过高。
处理方法(1) 对于复杂零件,操作时必须认真清洗所夹带的溶液;整修绝缘层破裂的挂具。
(2) 采用粉状活性炭3 g /L,将镀液进行大处理除去过量十二烷基硫酸钠。
据文献 L6论述:油污带入镀液时,由于十二烷基硫酸钠分子的定向排列,能将油污包围成一层吸附膜,此时,油污进入胶束内部的憎水基之间,成球形或层状胶束。
镀镍常见故障分析及纠正方法
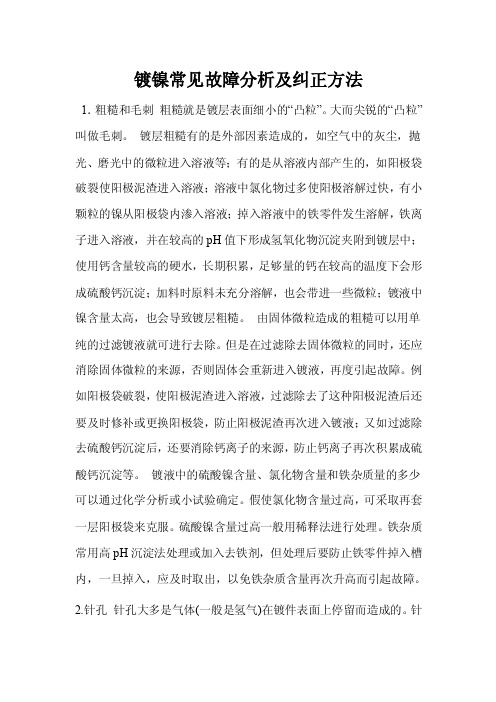
镀镍常见故障分析及纠正方法1.粗糙和毛刺粗糙就是镀层表面细小的“凸粒”。
大而尖锐的“凸粒”叫做毛刺。
镀层粗糙有的是外部因素造成的,如空气中的灰尘,抛光、磨光中的微粒进入溶液等;有的是从溶液内部产生的,如阳极袋破裂使阳极泥渣进入溶液;溶液中氯化物过多使阳极溶解过快,有小颗粒的镍从阳极袋内渗入溶液;掉入溶液中的铁零件发生溶解,铁离子进入溶液,并在较高的pH值下形成氢氧化物沉淀夹附到镀层中;使用钙含量较高的硬水,长期积累,足够量的钙在较高的温度下会形成硫酸钙沉淀;加料时原料未充分溶解,也会带进一些微粒;镀液中镍含量太高,也会导致镀层粗糙。
由固体微粒造成的粗糙可以用单纯的过滤镀液就可进行去除。
但是在过滤除去固体微粒的同时,还应消除固体微粒的来源,否则固体会重新进入镀液,再度引起故障。
例如阳极袋破裂,使阳极泥渣进入溶液,过滤除去了这种阳极泥渣后还要及时修补或更换阳极袋,防止阳极泥渣再次进入镀液;又如过滤除去硫酸钙沉淀后,还要消除钙离子的来源,防止钙离子再次积累成硫酸钙沉淀等。
镀液中的硫酸镍含量、氯化物含量和铁杂质量的多少可以通过化学分析或小试验确定。
假使氯化物含量过高,可采取再套一层阳极袋来克服。
硫酸镍含量过高一般用稀释法进行处理。
铁杂质常用高pH沉淀法处理或加入去铁剂,但处理后要防止铁零件掉入槽内,一旦掉入,应及时取出,以免铁杂质含量再次升高而引起故障。
2.针孔针孔大多是气体(一般是氢气)在镀件表面上停留而造成的。
针孔属于麻点,但针孔不同于麻点,它像流星一样,往往带有向上的“尾巴",而麻点仅仅是镀层上微小的凹坑,一般是没有向上的“尾巴"。
哪些因素会促使镍层产生针孔呢?电镀前处理不良;镀液中有油或有机杂质过多;镀液中有固体微粒;防针孔剂太少;镀液中铁等异金属杂质过多;镀液pH太高或操作电流密度过大;镀液中硼酸含量太少和镀液温度太低等都会导致镀镍层产生针孔。
由于不同原因引起的针孔现象略有不同,所以在分析故障时,首先要观察现象。
化学镀镍的常见故障
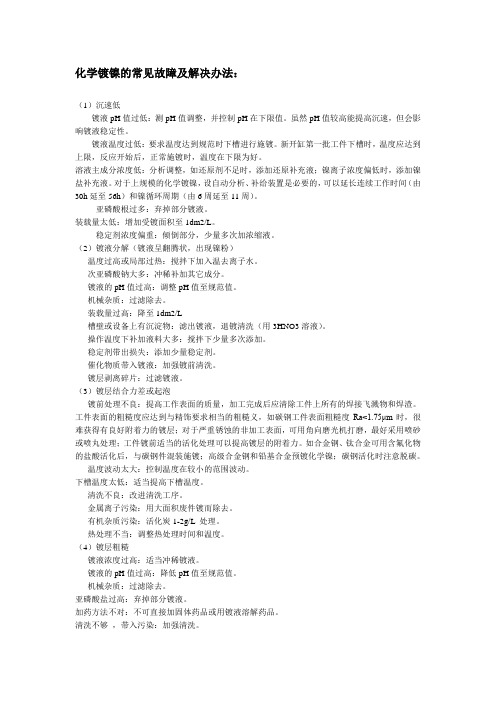
化学镀镍的常见故障及解决办法:(1)沉速低镀液pH值过低:测pH值调整,并控制pH在下限值。
虽然pH值较高能提高沉速,但会影响镀液稳定性。
镀液温度过低:要求温度达到规范时下槽进行施镀。
新开缸第一批工件下槽时,温度应达到上限,反应开始后,正常施镀时,温度在下限为好。
溶液主成分浓度低:分析调整,如还原剂不足时,添加还原补充液;镍离子浓度偏低时,添加镍盐补充液。
对于上规模的化学镀镍,设自动分析、补给装置是必要的,可以延长连续工作时间(由30h延至56h)和镍循环周期(由6周延至11周)。
亚磷酸根过多:弃掉部分镀液。
装载量太低:增加受镀面积至1dm2/L。
稳定剂浓度偏重:倾倒部分,少量多次加浓缩液。
(2)镀液分解(镀液呈翻腾状,出现镍粉)温度过高或局部过热:搅拌下加入温去离子水。
次亚磷酸钠大多:冲稀补加其它成分。
镀液的pH值过高:调整pH值至规范值。
机械杂质:过滤除去。
装载量过高:降至1dm2/L槽壁或设备上有沉淀物:滤出镀液,退镀清洗(用3HNO3溶液)。
操作温度下补加液料大多:搅拌下少量多次添加。
稳定剂带出损失:添加少量稳定剂。
催化物质带入镀液:加强镀前清洗。
镀层剥离碎片:过滤镀液。
(3)镀层结合力差或起泡镀前处理不良:提高工作表面的质量,加工完成后应清除工件上所有的焊接飞溅物和焊渣。
工件表面的粗糙度应达到与精饰要求相当的粗糙义,如碳钢工件表面粗糙度Ra<1.75μm时,很难获得有良好附着力的镀层;对于严重锈蚀的非加工表面,可用角向磨光机打磨,最好采用喷砂或喷丸处理;工件镀前适当的活化处理可以提高镀层的附着力。
如合金钢、钛合金可用含氟化物的盐酸活化后,与碳钢件混装施镀;高级合金钢和铅基合金预镀化学镍;碳钢活化时注意脱碳。
温度波动太大:控制温度在较小的范围波动。
下槽温度太低:适当提高下槽温度。
清洗不良:改进清洗工序。
金属离子污染:用大面积废件镀而除去。
有机杂质污染:活化炭1-2g/L 处理。
热处理不当:调整热处理时间和温度。
镀镍故障
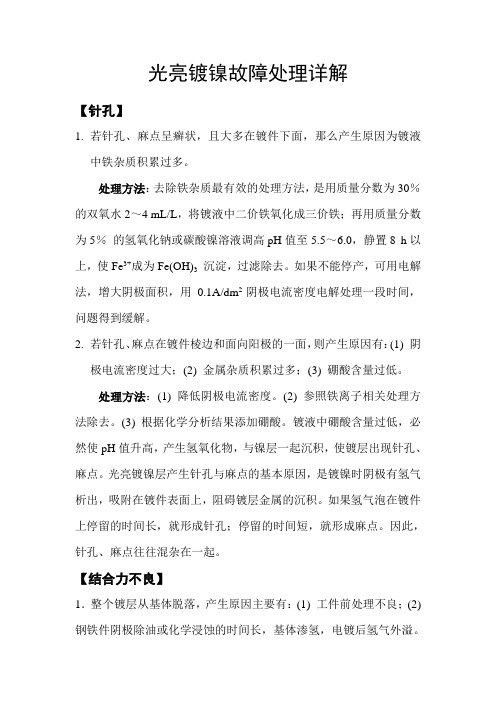
光亮镀镍故障处理详解【针孔】1.若针孔、麻点呈癣状,且大多在镀件下面,那么产生原因为镀液中铁杂质积累过多。
处理方法:去除铁杂质最有效的处理方法,是用质量分数为30%的双氧水2~4 mL/L,将镀液中二价铁氧化成三价铁;再用质量分数为5%的氢氧化钠或碳酸镍溶液调高pH值至5.5~6.0,静置8 h以上,使Fe3+成为Fe(OH)3沉淀,过滤除去。
如果不能停产,可用电解法,增大阴极面积,用0.1A/dm2阴极电流密度电解处理一段时间,问题得到缓解。
2.若针孔、麻点在镀件棱边和面向阳极的一面,则产生原因有:(1) 阴极电流密度过大;(2) 金属杂质积累过多;(3) 硼酸含量过低。
处理方法:(1) 降低阴极电流密度。
(2) 参照铁离子相关处理方法除去。
(3) 根据化学分析结果添加硼酸。
镀液中硼酸含量过低,必然使pH值升高,产生氢氧化物,与镍层一起沉积,使镀层出现针孔、麻点。
光亮镀镍层产生针孔与麻点的基本原因,是镀镍时阴极有氢气析出,吸附在镀件表面上,阻碍镀层金属的沉积。
如果氢气泡在镀件上停留的时间长,就形成针孔;停留的时间短,就形成麻点。
因此,针孔、麻点往往混杂在一起。
【结合力不良】1.整个镀层从基体脱落,产生原因主要有:(1) 工件前处理不良;(2)钢铁件阴极除油或化学浸蚀的时间长,基体渗氢,电镀后氢气外溢。
处理方法:(1) 加强对工件在预镀前的除油、除锈和清洗工序,确保基体表面洁净。
(2) 适当缩短阴极电解除油、酸洗时间,防止工件基体渗氢。
2.镀镍层起泡、脱皮,产生原因主要有:(1) 复杂零件或挂具涂料绝缘层破裂而夹带溶液引起起泡;(2)镀液中十二烷基硫酸钠含量过高。
处理方法:(1) 对于复杂零件,操作时必须认真清洗所夹带的溶液;整修绝缘层破裂的挂具。
(2)采用粉状活性炭3g/L,将镀液进行大处理除去过量十二烷基硫酸钠。
据文献论述:油污带入镀液时,由于十二烷基硫酸钠分子的定向排列,能将油污包围成一层吸附膜,此时,油污进入胶束内部的憎水基之间,成球形或层状胶束。
镀镍常见故障及解决办法
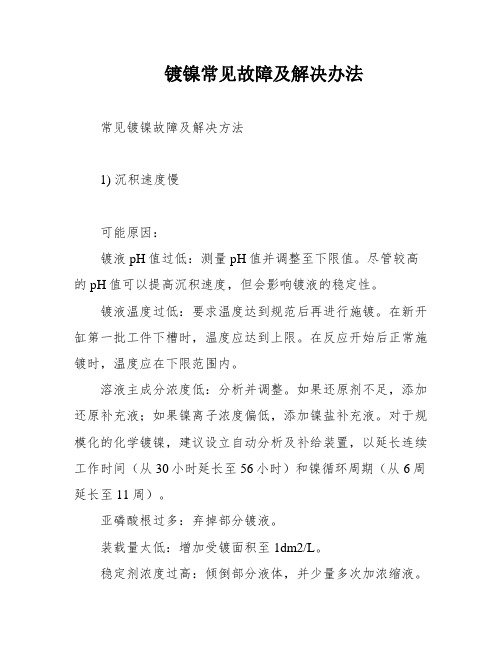
镀镍常见故障及解决办法常见镀镍故障及解决方法1) 沉积速度慢可能原因:镀液pH值过低:测量pH值并调整至下限值。
尽管较高的pH值可以提高沉积速度,但会影响镀液的稳定性。
镀液温度过低:要求温度达到规范后再进行施镀。
在新开缸第一批工件下槽时,温度应达到上限。
在反应开始后正常施镀时,温度应在下限范围内。
溶液主成分浓度低:分析并调整。
如果还原剂不足,添加还原补充液;如果镍离子浓度偏低,添加镍盐补充液。
对于规模化的化学镀镍,建议设立自动分析及补给装置,以延长连续工作时间(从30小时延长至56小时)和镍循环周期(从6周延长至11周)。
亚磷酸根过多:弃掉部分镀液。
装载量太低:增加受镀面积至1dm2/L。
稳定剂浓度过高:倾倒部分液体,并少量多次加浓缩液。
2) 镀液分解(镀液呈翻腾状,出现镍粉)可能原因:温度过高或局部过热:在搅拌的同时加入温去离子水。
次亚磷酸钠过多:冲稀补加其他成分。
镀液的pH值过高:调整pH值至规范值。
机械杂质:过滤除去。
装载量过高:降至1dm2/L。
槽壁或设备上有沉淀物:滤出镀液,退镀清洗(使用3% HNO3溶液)。
在操作温度下,少量多次添加补给液。
稳定剂带出损失:添加少量稳定剂。
催化物质带入镀液:加强镀前清洗。
镀层剥离碎片:过滤镀液。
3) 镀层结合力差或起泡可能原因:镀前处理不良:提高工作表面的质量。
加工完成后应清除工件上所有的焊接飞溅物和焊渣。
工件表面的粗糙度应达到与精饰要求相当的粗糙度。
如碳钢工件表面粗糙度Ra<1.75μm 时,很难获得有良好附着力的镀层。
对于严重锈蚀的非加工表面,可用角向磨光机打磨,最好采用喷砂或喷丸处理。
工件镀前适当的活化处理可以提高镀层的附着力。
如合金钢、钛合金可用含氟化物的盐酸活化后,与碳钢件混装施镀;高级合金钢和铅基合金预镀化学镍;碳钢活化时注意脱碳。
温度波动太大:控制温度在较小的范围内波动。
下槽温度太低:适当提高下槽温度。
清洗不良:改进清洗工序。
金属离子污染:用大面积废件镀而除去。
- 1、下载文档前请自行甄别文档内容的完整性,平台不提供额外的编辑、内容补充、找答案等附加服务。
- 2、"仅部分预览"的文档,不可在线预览部分如存在完整性等问题,可反馈申请退款(可完整预览的文档不适用该条件!)。
- 3、如文档侵犯您的权益,请联系客服反馈,我们会尽快为您处理(人工客服工作时间:9:00-18:30)。
光亮镀镍故障处理针孔1.针孔、麻点呈癣状。
大多在镀件下面产生原因镀液中铁杂质积累过多。
处理方法去除铁杂质最有效的处理方法,是用质量分数为30%的双氧水2~4 mL/L,将镀液中二价铁氧化成三价铁;再用质量分数为5%的氢氧化钠或碳酸镍溶液调高pH值至5.5~6.0,静置8 h以上,使Fe¨成为Fe(on) 沉淀,过滤除去。
如果不能停产,可用电解法,增大阴极面积,用0.1 A/dm2阴极电流密度电解处理一段时间,问题得到缓解。
2. 针孔、麻点在镀件棱边和面向阳极的一面产生原因(1)阴极电流密度过大;(2)金属杂质积累过多;(3)硼酸含量过低。
处理方法(1)降低阴极电流密度。
(2)参照上述相关处理方法除去。
(3)根据化学分析结果添加硼酸。
镀液中硼酸含量过低,必然使pH值升高,产生氢氧化物,与镍层一起沉积,使镀层出现针孔、麻点。
光亮镀镍层产生针孔与麻点的基本原因,是镀镍时阴极有氢气析出,吸附在镀件表面上,阻碍镀层金属的沉积。
如果氢气泡在镀件上停留的时间长,就形成针孔;停留的时间短,就形成麻点。
因此,针孔、麻点往往混杂在一起。
结合力不良1 整个镀层从基体脱落产生原因(1)工件前处理不良;(2)钢铁件阴极除油或化学浸蚀的时间长,基体渗氢,电镀后氢气外溢。
处理方法(1)加强对工件在预镀前的除油、除锈和清洗工序,确保基体表面洁净。
(2)适当缩短阴极电解除油、酸洗时间,防止工件基体渗氢。
2 镀镍层起泡、脱皮产生原因(1)复杂零件或挂具涂料绝缘层破裂而夹带溶液引起起泡;(2)镀液中十二烷基硫酸钠含量过高。
处理方法(1)对于复杂零件,操作时必须认真清洗所夹带的溶液;整修绝缘层破裂的挂具。
(2)采用粉状活性炭3 g/L,将镀液进行大处理除去过量十二烷基硫酸钠。
据文献L6 论述:油污带入镀液时,由于十二烷基硫酸钠分子的定向排列,能将油污包围成一层吸附膜,此时,油污进入胶束内部的憎水基之间,成球形或层状胶束。
随着十二烷基硫酸钠浓度升高,这些吸附有油污的胶束数量也增多,在电镀过程中它们被夹杂在镀层中就会起泡。
3 镀层脱皮至底铜层产生原因(I)工件镀铜(包括氰化物镀铜、酸铜)后,清洗不干净或在空气中存放时间长,表面氧化;(2)镀液中糖精含量过高(指镍层粉状脱落);(3)丁炔二醇过多(指镍层块状脱落)。
处理方法(1)加强镀铜后清洗和镀镍之前的活化工序;尽可能缩短镀铜件在空气中的停留时间。
(2)低电流密度电解处理,或用活性炭吸附。
(3)参照上述相关处理方法除去。
4 镀层从边缘脱落产生原因(1)拉应力大;(2)阴极电流密度过大;(3)铁杂质和有机物多。
处理方法(1)添加应力减少剂,如适当提高糖精含量,能使镀层具有压应力,增强镀层的延展性能。
(2)降低阴极电流密度。
(3)参照上述相关处理方法除去。
镀层脆性大产生原因(1)金属杂质积累过多,尤其是铬酸根离子;(2)硼酸含量过低;(3)(次、初级)光亮剂过多;(4)pH值过高;(5)镀液温度过低;(6)阴极电流密度过大。
处理方法(1)去除六价铬一般用保险粉或硫酸亚铁还原。
如六价铬的质量浓度为0.5 g/L时,加硫酸亚铁0.16 g/L,将pH值调高到6,温度70~C,搅拌,可将cr3 沉淀,过滤,最后把pH值调至工艺规范。
(2)按分析结果添加硼酸至正常范围。
(3)用低电流密度电解或活性炭吸附。
(4)调低pH值至工艺规范。
(5)升高镀液温度至工艺规范。
(6)降低阴极电流密度。
覆盖能力差1 低电流密度区无镀层产生原因(1)六价铬的影响;(2)(次、初级)光亮剂过多;(3)pH值过低;(4)挂具接触不良;(5)有机杂质过多;(6)前处理不良;(7)氯离子含量过低。
处理方法(1)参照上述相关处理方法除去。
(2)用低电流密度电解或活性炭吸附。
(3)调高pH值至工艺规范。
(4)整修或更换新的挂具。
(5)参照上述相关处理方法除去。
(6)检查前道镀铜后表面清洗状况,并加以彻底清洗干净。
(7)按分析结果添加氯化镍至工艺规范。
氯化物能减少阳极钝化,使镍阳极正常溶解,提高镀液导电能力和改善镀液的覆盖能力、分散能力。
2 镀不上铬或铬镀层局部“露黄”、发花(1)镍镀层表面钝化;(2)镍层上光亮剂吸附或有凝结物;(3)镀镍液中金属杂质过多。
处理方法(1)对镀镍后放置较长时间的镀件,可用质量分数为10%的硫酸溶液或用铬酸浸渍后镀铬。
(2)适当减少光亮剂,必要时用活性炭处理。
在冬季时,为了防止工件带出液在表面形成凝结物,难以在冷水中洗净。
因此,镀镍后应先在温水中清洗,然后经活化处理后镀铬,就可以消除发花现象。
(3)参照上述相关处理方法除去。
镀镍溶液pH值调整方法不当引起的故障镀镍溶液的pH值偏高,调低时用浓硫酸,结果浓硫酸虽加入不多;pH值即直线下降,后又用浓的氢氧化钠溶液由低往高调,结果pH值又调过了头,经多次反复,最后不但pH值未能调合适,还破坏了整槽镀镍溶液,先是引起溶液中不少硫酸镍的结晶析出,后又成为稠稠的浆状。
这是因为开始浓硫酸加入过量,引起溶液中不少硫酸镍结晶析出(硫酸镍溶解度降低),后又用浓氢氧化钠溶液往回调时,由于浓氢氧化钠与镍盐起化学反应,生成胶体状氢氧化镍沉淀的结果。
出现上述情况时应将溶液进行过滤,并通电处理,溶液中有关成分也应通过化验分析后进行调整,否则就会增加溶液的电阻,镀出镀层粗糙并出现针孔。
为了防止上述现象再次发生,无论在溶液的pH值由高往低调,还是由低往高调时,用的是硫酸溶液,还是氢氧化钠溶液的浓度都要稀释至3%以下,且必须边搅拌、边慢慢加入,这样pH值才不会有大的波动,也不至于出现硫酸镍的结晶析出和氢氧化镍的沉淀而造成镍盐的损耗。
光亮剂过剩对镀层质量的危害光亮镀镍溶液中的光亮剂不宜过多,有的厂家为获得更为光亮的镍层质量,任意添加过多的光亮剂,其实这样做很不妥当,这时不但镀层容易发花,还可能引起脆性,结合强度降低,镀层暴皮等一系列质量问题的发生。
防备方法:根据镀层光亮度变化的需要添加,添加时应勤加、少加,由专人负责添加并做好记录。
镀镍溶液遭铅污染爆发性地出现下列故障:工件的尖角部位明显镀焦,调小电流也不起作用,均镀能力差,镀层结合力差。
用活性炭进行处理后再用电解法进行电解处理都未见有所改善。
怀疑是受到对镀镍溶液极为敏感的铅所污染。
采取较大的阴极面积、较小的电流密度(0.1~0.2A/dm2)进行长时间的通电处理。
光亮镀镍溶液中氯离子过高引起的故障,亮镍溶液中氯化镍含量过高会引起镍阳极溶解过快,阳极泥渣增加,放电概率升高,造成操作环境恶化,镀层出现毛刺、裂纹、电流效率降低,内应力增加等一系列问题的发生。
镀镍溶液因错用铁质加温管而被污染镀镍溶液尚较清澈,见工件上的针孔多在工件的上面,有别于受到有机质污染形成的针孔(多在工件的朝下面),测得豹pH值略有升高,但还在范围之内。
从以上现象分析溶液有可能是被铁离子污染,否则针孔不可能多誉出现在工件的朝上部位,加十二烷基硫酸钠也应该有效。
除去镀镍溶液中铁离子的方法比较简单,通过添加双氧水,提高溶液的pH值至5.5后过滤,经调整pH值至4.5后试镀针孔现象完全消失。
镀镍液中混入硝酸根的故障镀镍溶液中加入硫酸镍后镀出镍层即出现灰黑色,电流效率很低,这一症状是由硝酸根引起的。
硫酸镍是由硝酸镍转化过来的,若制造工艺不够严格,很有可能有未曾洗脱的硝酸存在。
为治理这槽溶液,以通人电流使硝酸根还原为氨的方法进行处理,具体方法是:初始以0.5~1A/dm2通电5~6h,然后将电流密度降至0.1~0.2A/dm2继续处理,总通电量为:0.19/L硝酸根,则需通电1A/h,可以达到除尽的目的。
镀镍溶液中氯化镍加入过量镍层起毛刺氯化镍添加过量阳极会出现异常溶解,溶液中泥渣增多,继而使镀层产生毛刺。
取出原使用的铸造镍板,改用电解镍板(电解镍板在高氯化镍溶液中溶解性比浇铸镍均匀),同时用的确良布包扎镍板,经此改进后,镀层出现毛刺问题基本得到解决光亮镀镍电流密度过大引起镍层发雾、发花电流密度过大会引起镀层发雾,即我们所说的烧焦。
电流密度过小也同样不能获得满意的透明光亮的亮镍层。
这种情况常表现为:在一串镀件中的上下几个工件常是比较光亮,而中间的几个工件光亮度较差(这是因为一串工件中的中间部位工件的电流密度总是比较小。
镍槽中阳极面积过小引起镀镍层发雾、发花阳极面积太小,起不到应有的作用,从而引起镀层的阴、阳面,或是双面都出现雾状。
溶液中镍盐含量过高引起镀镍层发雾、发花光亮镀镍溶液中镍盐含量过高引起镀镍层发雾、发花溶液中镍盐含量过低引起镀镍层发雾、发花光亮镀镍出现发花较易察觉,由于活化剂、氯化镍含量的严重不足,镍阳极严重钝化,最后出现镍层发花的严重后果。
由此可见,维护镍盐含量也是保证光亮镀镍层质量的关键。
镀液pH值过高引起镀镍层发雾、发花电镀镍(亮镍)过程中溶液的pH值是有所上升的,这是因为电解过程中班<狐之故,为此要经常予以测定调整,否则当pH值过高时镀层中会有夹杂物,此夹杂物大多是碱式盐,从而促使镀层结晶粗糙,出现不透亮的白雾。
亮镍溶液大处理之后镀层出现发雾、发花亮镍溶液经用双氧水大处理之后镀出亮镍层严重发雾,色泽也很差,发暗,估计这种故障与大处理工艺有关,尤其是加的双氧水有可能未能充分分解。
这不但会破坏光亮剂,还可能导致镀层出现雾状,严重时还会引起镀层掉皮。
镀液温度过低影响镍层的结合强度镀镍工艺中严格控制溶液温度是保证镀层质量的一个重要环节,当溶液温度过低时,溶液中的盐类溶解度和导电率会明显降低,镍离子向阴极的扩散速度减慢,镀层内应力增加,从而影响到镀层的结合强度,为此,严格控制溶液温度是保证镀层结合强度的重要因素之一。
光亮镀镍溶液的温度低于工艺规范有以上同样的不利之外,还会使得镀层光亮范围变小、光亮度降低,若稍稍提高电流密度还容易被烧焦。
铜离子污染影响镀镍层结合强度镀镍溶液中的铜离子对镀层结合强度影响很大,当浓度稍高时会明显地出现置换铜层。
铜离子通常由以下几个途径进入镀镍槽中的:(1)化工原料或阳极质地不纯;(2)阳极铜质挂钩因接触溶液而遭到电化学溶解;(3)铜件或镀铜件接触溶液时的化学溶解;(4)擦洗铜杠时铜屑进入溶液;(5)工件镀铜后镀镍之前清洗不彻底而带进镀铜溶液。
防备方法:(1)尽可能选用较高纯度的化工原料和阳极材料;(2)阳极挂钩要远离镀液;(3)铜件或镀铜件要带电人槽;(4)擦洗铜杠时要从槽面上卸下来;(5)镀铜后进入镀镍槽之前要加强清洗;(6)常用小电流电解处理溶液;电流间断影响继镀层的结合强度电流间断多发生在镀薄片件中。
薄片件比较轻,工件挂在移动的阴极杠上挂镀时,由于阴极的移动,容易引起挂钩与阴极极杠脱离,电流间断。
防备方法:挂钩和阴极极杠都要洗刷干净(挂钩能卡住阴极杠则更好),以改善两者之间电流的传导能力,也可在一串工件的末端绑一废品,以增加工件的质量,使其牢牢压在阴极杠上,从而防止工件脱电。