机械工艺课程设计动掌工艺设计
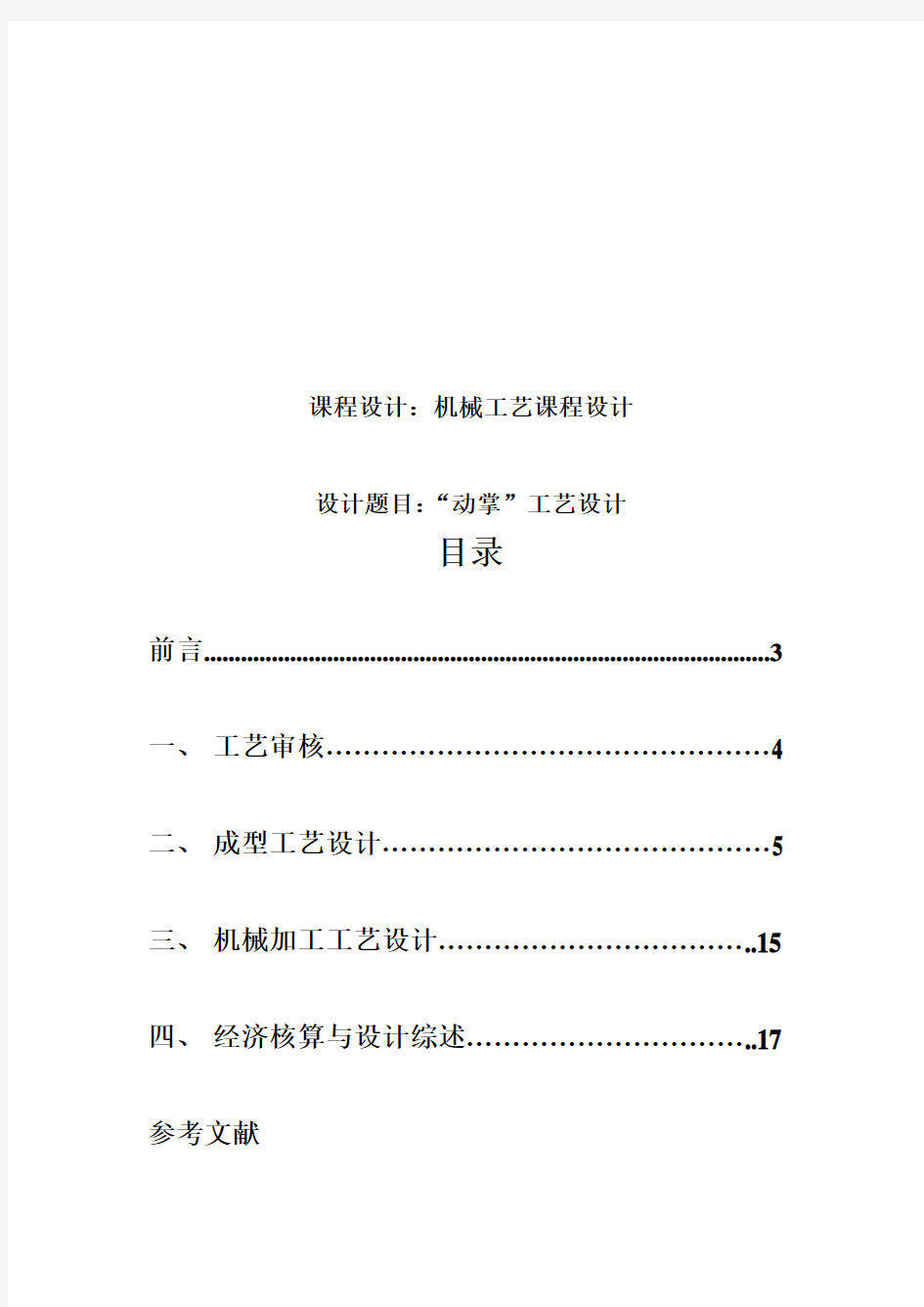
- 1、下载文档前请自行甄别文档内容的完整性,平台不提供额外的编辑、内容补充、找答案等附加服务。
- 2、"仅部分预览"的文档,不可在线预览部分如存在完整性等问题,可反馈申请退款(可完整预览的文档不适用该条件!)。
- 3、如文档侵犯您的权益,请联系客服反馈,我们会尽快为您处理(人工客服工作时间:9:00-18:30)。
课程设计:机械工艺课程设计
设计题目:“动掌”工艺设计
目录
前言 (3)
一、工艺审核 (4)
二、成型工艺设计 (5)
三、机械加工工艺设计 (15)
四、经济核算与设计综述 (17)
参考文献
前言
机械工艺课程设计,是综合运用了我们之前学过的《金属工艺学》、《机械制图》等知识,同时在金工实习所获得的知识和经验的帮助下,完成对零件的工艺审核、成形工艺设计、机械加工工艺设计、经济成本核算等一系列工作。这种细致并且接近生产实践的机械设计训练,可以把理论与实践结合起来,使所学知识得到进一步巩固、加深和拓展。
通过本次设计课程,我们的知识变得更加系统化,能力得到了锻炼和提高,这正是本门课程对于我们的意义所在。我的进步主要体现在:
一、机械制图:上机制图的能力有了很大进步,得到了更急系统的训练。并且绘图更加规范。
二、设计成型工艺:在绘制铸造工艺图的过程中,使我对分型面与浇注系统的选择,机加工余量的确定,起模斜度,砂芯和芯头,冷铁和不足以及冒口等有了更详细的了解。在选择最佳方案中有了更多的理论依据,掌握了判断原理。并且熟悉了各种参数的查找和计算方法,为以后从事工作打下了坚实的基础。
三、机械加工工艺:通过对机械加工工艺的设计,巩固了自己对车、铣、刨、磨、钳等各种工种的认识,熟悉了各种工种的加工方法和适用范围。
相信通过这次学习以及以后的各种课程,我们会成为知识丰富的人才,将来投身钢铁事业中,设计出更加科学,更具创新性的零件,增强我国机械器材的使用寿命和工作性能,为祖国的经济发展和繁荣富强出一份力。
下面就让我来介绍一下我对“动掌”的工艺设计,由于水平有限,知识面也比较狭窄,经验更加不丰富,难免会有些不科学的设计和说明,望老师能耐心加以传授和指导,帮我改正自己的错误认识和不足,提高自己的设计水平和能力。9我会努力的学习,争取让老师满意,也让自己满意。
一、工艺审核
1、数量与材料
本零件“动掌”要求加工数量为10件,根据《金属工艺学》的知识,该零件生产数量小于100件,并且重量小于100千克,属于单件、小批生产。
该零件结构比较简单,但是形状不是很规则,工作条件一般以承受摩擦力为主。故要求该零件有良好的刚性和耐磨性,采用灰铸铁材料,流动性较好,适于铸造。
2、图样
该零件图给出了主视图、左视图、俯视图和一个右视图。尺寸标注基本完整清晰,粗糙度、铸造圆角等技术要求基本明确。
3、零件的结构工艺性
(1)成型工艺的结构工艺性
材料为HT150,单件生产,采用砂型铸造中的手工造型,即可获取毛坯。该零件中有4个孔,其中φ36的孔需要铸出,剩下的2个螺纹孔和1个φ28的孔因为小于铸铁可以铸出的最小直径30mm,故需要机加工出来的。另外,长*宽为5.5*2的槽由于小于铸铁可以铸出的最小槽,故需要机加工出来。
(2)切削工艺的结构工艺性
零件外表面除了上下表面和右侧面外均无精度要求,不需要机加工。其余需要机加工的部分包括2个螺纹孔和零件中心两个孔。
以零件主视图前后两个平行平面做为粗基准定位,在虎钳上安装,φ28和φ36的孔则可以在一次加工中完成,这样就保证同轴度的要求。底平面和右端面在铣床上加工,精度和效率都比较高。2个螺纹孔需先在钻床上钻出,再攻丝。(3)装配工艺的结构工艺性
装配工艺的结构工艺性是指所设计的零件在满足使用要求的前提下,装配连接的可行性和经济性或者说机器装配的难易程度。它包括便于装配、便于拆卸和正确的装配基面。该零件没有配合要求所以装配和拆卸是比较容易的,底平面为该零件的装配基准面。
二、成形工艺设计
1、工艺方案的的制定以及确定依据
型铸造是一种传统的造型方法,它使用与各种形状、大小、批量及各种合金铸件的生产。掌握砂型铸造是合理选择铸造方法和正确设计铸件的基础。
砂型铸造的工艺流程可表述如下:
铸造工艺分析与设计→铸造工艺方案的确定→砂型制造→砂芯制造→砂型和砂芯的烘干→合型及浇注→铸件的落砂与清理→铸件缺陷分析与质量检测。
砂型铸造分为手工铸造和机器铸造两种方式,其中手工铸造操作灵活,大小铸件均适合。手工造型主要用于但见、小批生产;机器造型实现了工序机械化,适应不同形状、尺寸和不同批量铸件生产的需要。
鉴于本册课程主要涉及砂型铸造工艺流程的制定过程,所以在这里只简要介绍一下“动掌”砂型铸造的工艺方案与参数选择。
1—1、浇注位置和分型面的选择
(1)浇注位置的选择原则:
1、铸件重要的加工面应朝下。铸件上表面容易产生砂眼、气孔、夹渣等缺
陷,组织也不如下表面细致。如果这些表面难以朝下,则应尽量位于侧面。
2、铸件的大平面应该朝下。浇注过程中金属液对型腔的上表面有强烈的热辐射,型砂因急剧热膨胀和因强度下降而拱起或开裂,致使上表面容易产生夹砂或结疤缺陷。
3、为防止铸件薄壁部分产生浇不到或冷隔等缺陷,应将面积较大的薄壁部分置于铸型下部或使其处于垂直或倾斜的位置。
4、若铸件圆周表面质量要求较高,应进行立铸(三箱造型或平作立浇),以便补缩。应将厚的部分放在铸型上部,以便安置冒口,实现顺序凝固。
(2)分型面的选择原则:
1、应尽量是分型面平直、数量少。
2、应避免不必要的型芯和活块,以简化造型工艺。
3、应尽量是铸件全部或者大部分置于下箱,不仅便于造型、下芯、合型,之便于保证铸件精度。
就“动掌”而言,分型面选择方案有很多,我认为最好的方法就是不放型芯。因为对于小批量生产地零件而言,制作型芯的过程相对于整个铸造过程来说也占了很大的工作量。下面就我选择最好的方案与其他方案之一进行一下对比,阐述我选择本方案的理由。
方案一:
浇注位置和分型面如第一个视图所示
选择此浇注位置的优势有三:
一、铸件最重要的加工面粗糙度为1.6的底面,如按此方案浇注的话此重要加工面朝下,铸件此表面不容易产生砂眼、气孔、夹渣等缺陷。
二、铸件的大平面朝下。在浇注过程中此重要平面不会因金属液对型腔上表面强烈的热辐射而急剧膨胀,则不会因强度下降导致拱起或开裂而产生夹砂或结疤。
三、铸件圆周表面要求不高,所以不需要立铸。
选择此分型面的优势: