冲压模具设计技术要求
冲压模具设计标准
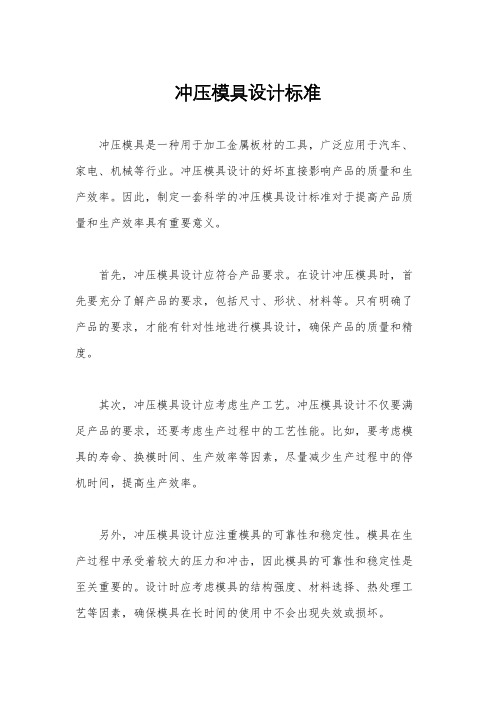
冲压模具设计标准
冲压模具是一种用于加工金属板材的工具,广泛应用于汽车、家电、机械等行业。
冲压模具设计的好坏直接影响产品的质量和生产效率。
因此,制定一套科学的冲压模具设计标准对于提高产品质量和生产效率具有重要意义。
首先,冲压模具设计应符合产品要求。
在设计冲压模具时,首先要充分了解产品的要求,包括尺寸、形状、材料等。
只有明确了产品的要求,才能有针对性地进行模具设计,确保产品的质量和精度。
其次,冲压模具设计应考虑生产工艺。
冲压模具设计不仅要满足产品的要求,还要考虑生产过程中的工艺性能。
比如,要考虑模具的寿命、换模时间、生产效率等因素,尽量减少生产过程中的停机时间,提高生产效率。
另外,冲压模具设计应注重模具的可靠性和稳定性。
模具在生产过程中承受着较大的压力和冲击,因此模具的可靠性和稳定性是至关重要的。
设计时应考虑模具的结构强度、材料选择、热处理工艺等因素,确保模具在长时间的使用中不会出现失效或损坏。
此外,冲压模具设计还应考虑模具的维护和保养。
模具在长时间的使用中,会出现磨损、变形等问题,因此设计时应考虑模具的维护和保养问题。
比如,可以在设计时考虑易损件的更换方便性,提高模具的维护效率。
最后,冲压模具设计还应符合相关的标准和规范。
在设计冲压模具时,应参照相关的国家标准和行业规范,确保模具的设计符合国家的法律法规和行业标准,保证产品的质量和安全性。
综上所述,冲压模具设计标准是保证产品质量和生产效率的重要保障。
设计人员应充分了解产品要求,考虑生产工艺,注重模具的可靠性和稳定性,同时符合相关的标准和规范,以确保设计出高质量的冲压模具。
毕业设计冲压模具设计

毕业设计冲压模具设计冲压模具设计是指根据零部件的形状和要求,通过模具设计软件对压制工艺和模具结构进行详细设计并完成加工制造的过程。
本文将以零部件的冲压模具设计为例,详细介绍冲压模具设计的步骤和关键技术。
一、冲压模具设计的步骤1.零件分析与加工工艺确定:首先对待设计的零件进行分析,了解其形状、材料及加工工艺要求。
通过对零件的尺寸测量、材料分析和工艺流程确定,确定适宜的冲压模具设计方案。
2.模具结构确定:根据零件形状和工艺要求,确定模具的基本结构形式,包括上、下模块的形状和结构、导向方式以及顶出装置的设计。
3.模具零件设计:根据模具的结构形式,对上、下模板、定位销、导柱、导套、顶出器等模具零件进行详细设计,并确定其尺寸、形位公差和表面粗糙度。
4.模具装配设计:根据模具零件的设计,进行模具的装配设计,确定模具各零件的加工工艺和装配工艺。
5.3D模型的建立:采用模具设计软件对模具的各个零件进行建模,并对其进行装配,实现模型的全面展示和动态演示。
6.模具结构的强度分析:采用有限元分析法对模具结构进行强度分析,确定模具零件的受力状态,从而提高模具的刚度和寿命。
7.模具工艺文件的编制:编制模具的工艺文件,包括工艺流程、工装设计和使用说明,为模具的制造和使用提供详细的技术支持。
二、冲压模具设计的关键技术1.零件厚度均衡设计:保证冲压零件的均衡受力,在模具的设计中尽量避免出现片厚不均的问题,从而避免在冲压过程中产生变形或裂纹等缺陷。
2.弹性顶出设计:在模具设计中合理设置顶针或顶出器,以保证冲压零件在顶出过程中不会卡死或破碎,从而提高冲压的质量和效率。
3.导向方式优化设计:合理选择导向方式,减小模具的摩擦阻力,从而提高模具的导向精度和工作寿命。
4.材料选择与热处理:合理选择模具材料,并根据工艺要求进行适当的热处理,以提高模具的硬度和耐磨性,延长模具的使用寿命。
5.模腔润滑与冷却设计:在模具设计中设置合理的润滑和冷却装置,以提高冲压的质量和效率,并减少模具的磨损和热变形。
冲压工艺技术要求

冲压工艺技术要求一、冲压工艺参数控制:1.上冲臂和下冲臂的长度应适当,以保证冲裁件在冲裁过程中的稳定性。
2.冲裁速度应适当,既要保证冲裁质量和工艺要求,又要考虑生产效率。
3.冲裁时的液压系统应保持稳定,并且能够方便地进行调整。
二、模具设计与制造:1.冲压模具应具备足够的强度和刚度,能够承受冲压过程中产生的冲击负荷,并保持高精度。
2.冲压模具的导向系统应设置合理,以确保冲裁件的准确位置和尺寸。
3.冲压模具应具备良好的冷却系统,以防止模具过热。
三、冲压材料选择:1.冲压材料应具备良好的塑性变形能力和可靠的强度。
2.冲压材料应有足够的导热性,以便迅速排出冲裁过程中产生的热量。
四、冲压质量控制:1.冲裁件的尺寸公差应在允许范围内,并且保证其功能和装配的要求。
2.冲裁件的表面质量应达到要求,不得有明显的划痕、氧化等缺陷。
3.冲裁件的强度和硬度应符合设计要求,并通过必要的检验手段进行检测。
五、冲压设备维护与保养:1.冲压设备的润滑系统应良好运行,以保证设备的正常运转和寿命。
2.冲压设备的气动系统应经常检查,以确保气动元件的正常工作。
3.冲压设备的电气系统应保持良好的绝缘,以避免电气故障。
六、人员技术要求:1.冲压工艺技术人员应具备良好的技术素养和操作技能,能够准确理解和执行工艺要求。
2.冲压工艺技术人员应经常进行培训和学习,掌握新的冲压技术和设备。
总之,冲压工艺技术要求的目的是为了保证冲压件的质量、尺寸和功能要求,并提高生产效率和设备寿命。
只有按照冲压工艺技术要求进行操作和管理,才能保证冲压加工的顺利进行。
冲压模具设计规范
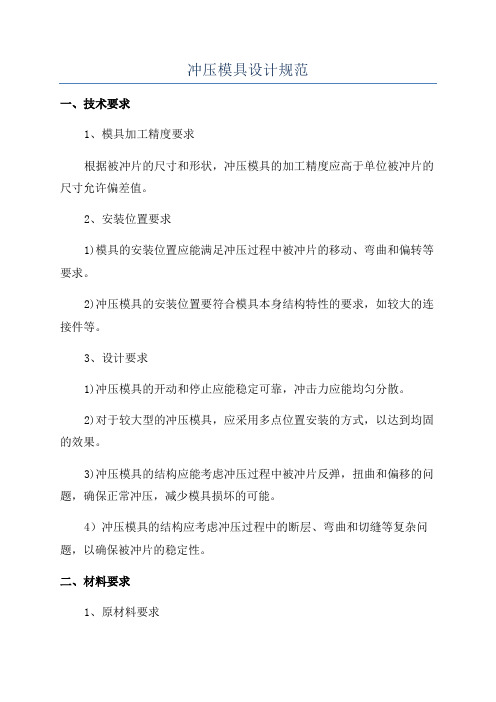
冲压模具设计规范
一、技术要求
1、模具加工精度要求
根据被冲片的尺寸和形状,冲压模具的加工精度应高于单位被冲片的尺寸允许偏差值。
2、安装位置要求
1)模具的安装位置应能满足冲压过程中被冲片的移动、弯曲和偏转等要求。
2)冲压模具的安装位置要符合模具本身结构特性的要求,如较大的连接件等。
3、设计要求
1)冲压模具的开动和停止应能稳定可靠,冲击力应能均匀分散。
2)对于较大型的冲压模具,应采用多点位置安装的方式,以达到均固的效果。
3)冲压模具的结构应能考虑冲压过程中被冲片反弹,扭曲和偏移的问题,确保正常冲压,减少模具损坏的可能。
4)冲压模具的结构应考虑冲压过程中的断层、弯曲和切缝等复杂问题,以确保被冲片的稳定性。
二、材料要求
1、原材料要求
1)冲压模具原材料应根据被冲片的材料特性、冲压工艺及模具的使用
寿命等因素确定,一般采用合金钢等。
2)冲压模具的原材料应考虑冲压过程中对其断裂、变形、冲击力以及
模具热处理等要求。
3)冲压模具的原材料质量应符合国家标准要求,保证模具的正常使用。
2、表面处理要求
冲压模具的表面处理要根据不同应用环境确定。
冲压模具设计的安全要求

冲压模具设计的安全要求1.环境安全要求:冲压模具设计需要在安全、整洁、通风良好的环境中进行。
工作区域应清晰、明亮,避免过于拥挤。
2.机械设备安全要求:冲压模具设计需要使用符合安全标准的机械设备。
设备应定期维护和保养,确保其正常运行,并配备相应的安全保护装置。
3.材料安全要求:冲压模具设计需要使用质量稳定、符合相关标准的材料。
材料的强度、韧性、耐磨性等性能要满足设计的要求,以确保模具的安全性和稳定性。
4.操作安全要求:冲压模具设计需要经过专业的培训和资格认证后方可操作。
操作人员需要穿戴个人防护装备,如安全帽、护目镜、防护手套等。
操作时需严格遵循操作规程,禁止在不安全的状态下工作,及时发现并及时解决安全隐患。
5.模具设计安全要求:冲压模具设计应遵循设计规范和标准,保证模具结构安全可靠,使用寿命长。
模具设计时需要考虑模具的强度、刚度、稳定性等因素,避免出现断裂、疲劳等失效现象,防止意外事故的发生。
6.模具维护安全要求:冲压模具设计后需要定期进行维护和保养,及时排除模具上的损坏、松动和变形等现象,以确保模具的正常使用。
维修和保养时需要遵守相关程序,确保人员和设备的安全。
7.废料处理安全要求:冲压模具设计会产生废料和废气,在废料和废气处理过程中要符合环保要求,避免对环境造成污染。
8.紧急救援安全要求:冲压模具设计应设立相应的紧急救援机制,如设置紧急停工按钮、紧急疏散通道、消防器材等,以应对突发事件并及时采取果断行动。
总结起来,冲压模具设计的安全要求包括环境安全、机械设备安全、材料安全、操作安全、模具设计安全、模具维护安全、废料处理安全以及紧急救援安全等多个方面。
只有在满足这些要求的前提下,冲压模具设计才能确保工作人员的安全,保障生产的顺利进行。
冲压模具制作技术要求
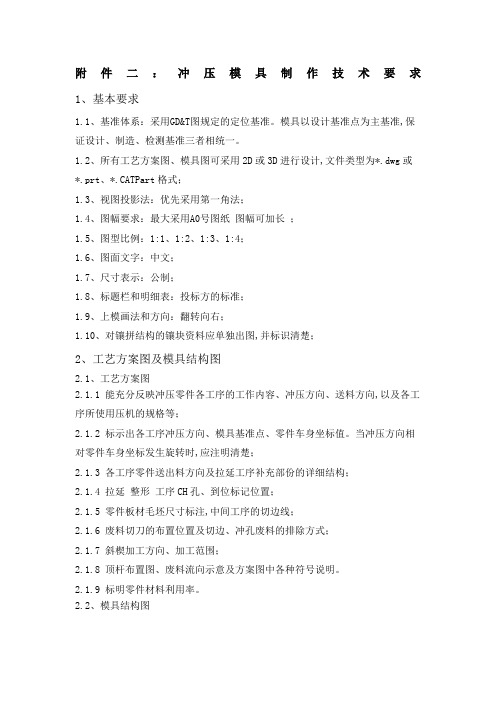
附件二:冲压模具制作技术要求1、基本要求1.1、基准体系:采用GD&T图规定的定位基准。
模具以设计基准点为主基准,保证设计、制造、检测基准三者相统一。
1.2、所有工艺方案图、模具图可采用2D或3D进行设计,文件类型为*.dwg或*.prt、*.CATPart格式;1.3、视图投影法:优先采用第一角法;1.4、图幅要求:最大采用A0号图纸图幅可加长;1.5、图型比例:1:1、1:2、1:3、1:4;1.6、图面文字:中文;1.7、尺寸表示:公制;1.8、标题栏和明细表:投标方的标准;1.9、上模画法和方向:翻转向右;1.10、对镶拼结构的镶块资料应单独出图,并标识清楚;2、工艺方案图及模具结构图2.1、工艺方案图2.1.1 能充分反映冲压零件各工序的工作内容、冲压方向、送料方向,以及各工序所使用压机的规格等;2.1.2 标示出各工序冲压方向、模具基准点、零件车身坐标值。
当冲压方向相对零件车身坐标发生旋转时,应注明清楚;2.1.3 各工序零件送出料方向及拉延工序补充部份的详细结构;2.1.4 拉延整形工序CH孔、到位标记位置;2.1.5 零件板材毛坯尺寸标注,中间工序的切边线;2.1.6 废料切刀的布置位置及切边、冲孔废料的排除方式;2.1.7 斜楔加工方向、加工范围;2.1.8 顶杆布置图、废料流向示意及方案图中各种符号说明。
2.1.9 标明零件材料利用率。
2.2、模具结构图2.2.1 模具图应充分表达模具的工作状态,反映零件的送出料方向、所用的压机型号、顶杆位置与顶杆行程等。
2.2.2 模具图应准确注明模具中心、机床中心。
模具中心应加注车身坐标系坐标值。
2.2.3 每工序模具图应有工序内容简图。
2.2.4 模具结构中含弹簧/氮气缸的应有弹力工作示意图。
2.2.5 模具使用斜楔机构的应做出斜楔行程图及斜楔断面图。
2.2.6 模具如果配备气缸顶出机构,模具图中应附加气路图。
2.2.7 工艺方案图、模具图及数模文件的命名规则如下:×××项目代号 -×××零件代号 -×××零件版本– OPx/y x表示10、20…;y表示总工序数,如共五序则为50 。
冲压工艺通用技术要求标准号
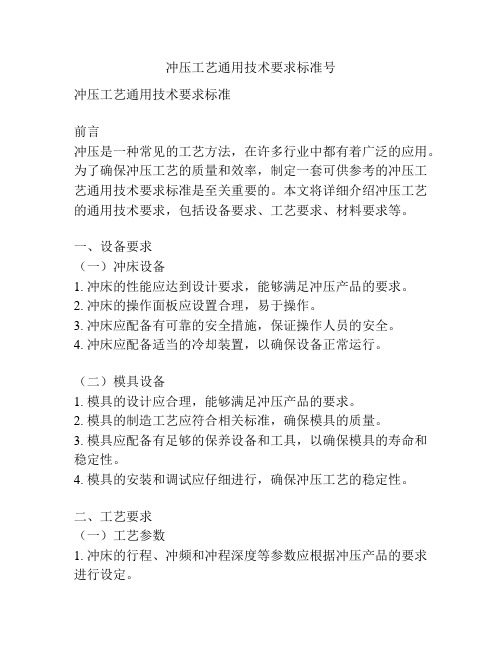
冲压工艺通用技术要求标准号冲压工艺通用技术要求标准前言冲压是一种常见的工艺方法,在许多行业中都有着广泛的应用。
为了确保冲压工艺的质量和效率,制定一套可供参考的冲压工艺通用技术要求标准是至关重要的。
本文将详细介绍冲压工艺的通用技术要求,包括设备要求、工艺要求、材料要求等。
一、设备要求(一)冲床设备1. 冲床的性能应达到设计要求,能够满足冲压产品的要求。
2. 冲床的操作面板应设置合理,易于操作。
3. 冲床应配备有可靠的安全措施,保证操作人员的安全。
4. 冲床应配备适当的冷却装置,以确保设备正常运行。
(二)模具设备1. 模具的设计应合理,能够满足冲压产品的要求。
2. 模具的制造工艺应符合相关标准,确保模具的质量。
3. 模具应配备有足够的保养设备和工具,以确保模具的寿命和稳定性。
4. 模具的安装和调试应仔细进行,确保冲压工艺的稳定性。
二、工艺要求(一)工艺参数1. 冲床的行程、冲频和冲程深度等参数应根据冲压产品的要求进行设定。
2. 冲床的行程和冲程深度应适当,以防止冲切过程中的材料损坏。
3. 冲床的冲频应合理,确保冲切效率和质量的平衡。
(二)冲裁工艺1. 冲切模具的设计应遵循工程原理,确保冲切刀具的刚性和稳定性。
2. 冲切模具的刀口应锋利、平整,以保证冲切过程中的切削质量。
3. 冲切过程中要做好冷却润滑工作,避免发生冲渣和刀具磨损。
(三)成形工艺1. 冲床的下死点和上死点应根据冲压产品的要求进行设定。
2. 冲床的下死点和上死点的位置应准确,以保证成形的精度和一致性。
3. 冲床成形过程中要注意加热和冷却,避免产生应力和变形。
三、材料要求(一)板材材料1. 板材的厚度和材质应符合冲压产品的设计要求。
2. 板材的表面应平整,无明显的划痕和变形。
3. 板材的硬度应符合冲压工艺的要求,以保证成形的顺利进行。
(二)塑性材料1. 塑性材料的表面应光滑,无明显的缺陷和杂质。
2. 塑性材料的润滑性应良好,以减少摩擦和热量的产生。
汽车冲压模具设计标准
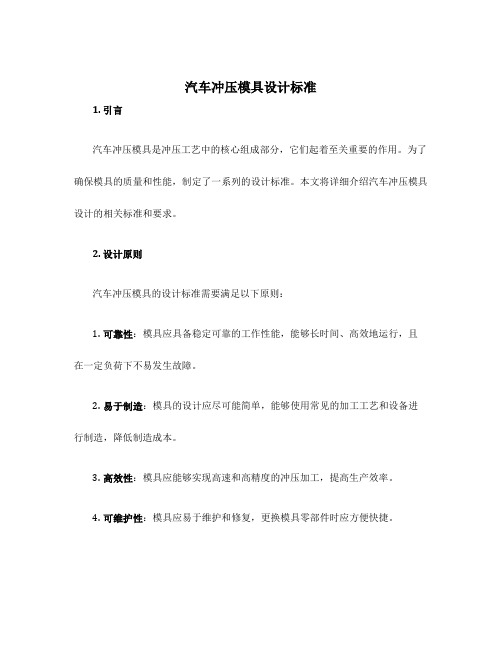
汽车冲压模具设计标准1. 引言汽车冲压模具是冲压工艺中的核心组成部分,它们起着至关重要的作用。
为了确保模具的质量和性能,制定了一系列的设计标准。
本文将详细介绍汽车冲压模具设计的相关标准和要求。
2. 设计原则汽车冲压模具的设计标准需要满足以下原则:1.可靠性:模具应具备稳定可靠的工作性能,能够长时间、高效地运行,且在一定负荷下不易发生故障。
2.易于制造:模具的设计应尽可能简单,能够使用常见的加工工艺和设备进行制造,降低制造成本。
3.高效性:模具应能够实现高速和高精度的冲压加工,提高生产效率。
4.可维护性:模具应易于维护和修复,更换模具零部件时应方便快捷。
3. 结构设计要求根据汽车冲压模具的不同类型和具体工艺要求,模具的结构设计需要满足以下要求:3.1 组合件结构汽车冲压模具通常由多个组合件组成,每个组合件都有特定的功能。
模具的组合件结构应满足以下要求:•简单可靠:组合件设计应尽可能简单,避免过多的连接点和复杂的结构,以提高稳定性和可靠性。
•便于组装和拆卸:组装和拆卸组合件时应方便快捷,避免使用过多的紧固件和工具,节约时间和人力成本。
•可互换性:组合件之间的连接应采用标准化的接口和紧固件,以实现模具部件的互换和共用。
3.2 材料选择汽车冲压模具的材料选择应满足以下要求:•硬度:模具材料应具有足够的硬度,以保证冲压过程中的切削和变形性能。
•耐磨性:模具材料应具有良好的耐磨性能,能够在长时间冲压加工中保持良好的表面质量。
•耐腐蚀性:模具材料应具有一定的抗腐蚀性能,能够应对冲压工艺中的润滑剂和金属氧化物的腐蚀。
•导热性:模具材料应具有良好的导热性能,以加速冲压工艺中的冷却和卸载过程。
3.3 寿命设计模具的寿命设计应考虑以下因素:•材料疲劳:模具在长时间使用过程中可能会发生疲劳损伤,设计时应考虑增加材料的强度和耐疲劳性能。
•应力集中:模具在冲压过程中会受到较大的应力,应避免应力集中,通过结构设计和材料选择来缓解应力分布。
冲压模具技术要求
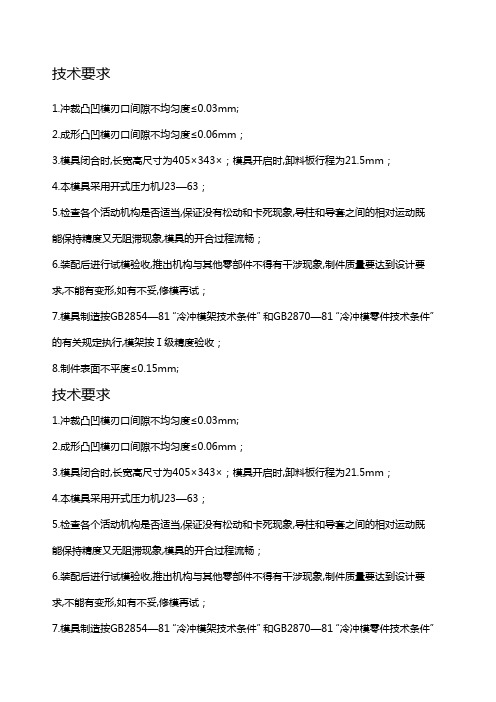
技术要求1.冲裁凸凹模刃口间隙不均匀度≤0.03mm;2.成形凸凹模刃口间隙不均匀度≤0.06mm;3.模具闭合时,长宽高尺寸为405×343×;模具开启时,卸料板行程为21.5mm;4.本模具采用开式压力机J23—63;5.检查各个活动机构是否适当,保证没有松动和卡死现象,导柱和导套之间的相对运动既能保持精度又无阻滞现象,模具的开合过程流畅;6.装配后进行试模验收,推出机构与其他零部件不得有干涉现象,制件质量要达到设计要求,不能有变形,如有不妥,修模再试;7.模具制造按GB2854—81“冷冲模架技术条件”和GB2870—81“冷冲模零件技术条件”的有关规定执行,模架按Ⅰ级精度验收;8.制件表面不平度≤0.15mm;技术要求1.冲裁凸凹模刃口间隙不均匀度≤0.03mm;2.成形凸凹模刃口间隙不均匀度≤0.06mm;3.模具闭合时,长宽高尺寸为405×343×;模具开启时,卸料板行程为21.5mm;4.本模具采用开式压力机J23—63;5.检查各个活动机构是否适当,保证没有松动和卡死现象,导柱和导套之间的相对运动既能保持精度又无阻滞现象,模具的开合过程流畅;6.装配后进行试模验收,推出机构与其他零部件不得有干涉现象,制件质量要达到设计要求,不能有变形,如有不妥,修模再试;7.模具制造按GB2854—81“冷冲模架技术条件”和GB2870—81“冷冲模零件技术条件”的有关规定执行,模架按Ⅰ级精度验收;8.制件表面不平度≤0.15mm;技术要求1.本模具为倒装落料拉深冲孔复合模,由于要求在凸缘上冲孔,故要在拉深完全完成的前提下进行冲孔.2.该模具闭合高度为233mm.3.本模具使用J21-25开式压力机.4.模具制造按照GB2854-81"冷冲模架技术条件"和GB2870-81"冷冲模零件技术要求"的有关规定执行.5.冲裁与拉深间隙都要均匀.冲裁双边间隙Zmin=0.1mm Zmax=0.14mm,拉深双边间隙Z=1.1mm6.导柱导套的轴线与模座上下面垂直公差为4级.。
冲压模具制作技术要求

冲压模具制作技术要求冲压模具是冲压工艺中使用的重要工具,其质量直接影响到冲压件的精度和质量。
因此,冲压模具制作技术要求较高,主要包括以下几个方面:一、模具设计要求:1.合理性原则:模具设计应考虑到冲压件的材料性质、形状、尺寸等因素,使模具结构合理、工作稳定。
2.精度要求:模具设计应考虑到冲压件的精度要求,合理设置定位、导向装置,并确保模具的定位精度以及冲压件的位置和尺寸精度。
3.可靠性要求:模具设计应考虑到使用寿命、可靠性等要求,并采用高强度、高耐磨材料制作。
4.便于加工和调试:模具设计应考虑到加工工艺、制造难度,以及调试和维修的便捷性。
二、模具制造要求:1.材料选用:模具材料应具有好的热处理性能、硬度、耐磨性和韧性,常用的材料有工具钢、合金钢等。
2.加工工艺:模具制造过程中应采用先进的加工工艺,包括车、铣、磨、电火花等工艺。
尤其是模具的加工精度和表面粗糙度要求较高。
3.系统模具加工:对于大型、复杂的模具,应采用CNC加工、数控加工等系统模具加工工艺,提高加工精度和效率。
4.热处理工艺:模具经过车削、铣削等加工后应进行热处理,以获得所需的硬度和韧性。
热处理过程要控制温度、时间等参数,并进行合理的淬火和回火处理。
5.表面处理:模具表面应进行合适的处理,以提高其耐磨性和抗腐蚀性。
常用的表面处理方法包括氮化、镀铬等。
三、模具调试和测试要求:1.模具调试:模具制造完成后,需要进行调试工作,包括模具的总装和零件的调试,以确保模具的正常使用和冲压件的质量。
2.测试和检验:模具制作完成后,需进行各项性能测试和质量检验,包括模具的尺寸测量、冲压件的检验等,以确保模具的性能和质量达到设计要求。
四、模具维护和保养要求:1.定期保养:模具在使用中需要定期进行维护和保养,包括润滑、清洁等,以延长模具使用寿命。
2.磨损修复:模具在使用中可能出现磨损和损坏,需要进行修复工作,包括砂轮修复、电火花修复等,保证模具的尺寸精度和使用寿命。
冲压模具设计标准
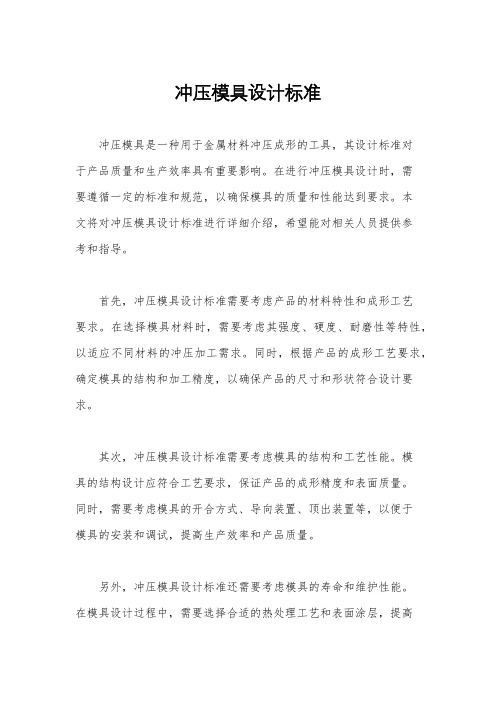
冲压模具设计标准冲压模具是一种用于金属材料冲压成形的工具,其设计标准对于产品质量和生产效率具有重要影响。
在进行冲压模具设计时,需要遵循一定的标准和规范,以确保模具的质量和性能达到要求。
本文将对冲压模具设计标准进行详细介绍,希望能对相关人员提供参考和指导。
首先,冲压模具设计标准需要考虑产品的材料特性和成形工艺要求。
在选择模具材料时,需要考虑其强度、硬度、耐磨性等特性,以适应不同材料的冲压加工需求。
同时,根据产品的成形工艺要求,确定模具的结构和加工精度,以确保产品的尺寸和形状符合设计要求。
其次,冲压模具设计标准需要考虑模具的结构和工艺性能。
模具的结构设计应符合工艺要求,保证产品的成形精度和表面质量。
同时,需要考虑模具的开合方式、导向装置、顶出装置等,以便于模具的安装和调试,提高生产效率和产品质量。
另外,冲压模具设计标准还需要考虑模具的寿命和维护性能。
在模具设计过程中,需要选择合适的热处理工艺和表面涂层,提高模具的耐磨性和使用寿命。
同时,需要考虑模具的易损件和易损部位,设计合理的维护通道和更换方式,以便于模具的维护和保养。
最后,冲压模具设计标准还需要考虑模具的安全性和可靠性。
在模具设计过程中,需要考虑模具的安全保护装置、操作人员的人身安全和设备的可靠性,以确保生产过程安全稳定。
综上所述,冲压模具设计标准涉及产品的材料特性、成形工艺要求、模具的结构和工艺性能、模具的寿命和维护性能、模具的安全性和可靠性等方面。
只有严格按照设计标准进行模具设计,才能确保模具的质量和性能达到要求,提高生产效率,降低生产成本,保证产品质量,提升企业竞争力。
希望本文能够对冲压模具设计提供一定的参考和指导,促进模具设计水平的提高。
公司冲压模具设计规范

公司冲压模具设计规范冲压模具设计规范一、总则(一)、目的为提升冲压模具的设计效率,完善模具设计流程,尽量幸免模具设计中显现的失误,规范模具图纸的绘制;同时,为加大公司内部人员之间的学习与交流,为模具设计人员提供必要的技术支持及常用资料的检索,特制订本规范。
(二)、适用范畴本规范适用于公司各有关部室、工场、子公司。
(三)、内容本规范中的内容要紧包括冲压模具的具体设计流程和各设计流程节点中的注意要点及规定事项,(不含级进模及大型模具)。
二、冲压模具设计所涉及的标准GB/T14662-2006冲模技术条件GB/T20914.1-2007冲模氮气弹簧第1部分:通用规格GB/T20914.2-2007冲模氮气弹簧第2部分:附件规格G B/T20915.1-2007冲模弹性体压缩弹簧第1部分:通用规格GB/T20915.2-2007冲模弹性体压缩弹簧第2部分:附件规格GB/T23562.1-2009冲模钢板下模座第1部分:后侧导柱下模座GB/T23562.2-2009冲模钢板下模座第2部分:对角导柱下模座GB/T23562.3-2009冲模钢板下模座第3部分:中间导柱下模座GB/T23562.4-2009冲模钢板下模座第4部分:四导柱下模座GB/T23563.1-2009冲模滚动导向钢板模架第1部分:后侧导柱模架GB/T23563.2-2009冲模滚动导向钢板模架第2部分:对角导柱模架GB/T23563.3-2009冲模滚动导向钢板模架第3部分:中间导柱模架GB/T23563.4-2009冲模滚动导向钢板模架第4部分:四导柱模架GB/T23564.1-2009冲模滚动导向钢板上模座第1部分:后侧导柱上模座GB/T23564.2-2009冲模滚动导向钢板上模座第2部分:对角导柱上模座GB/T23564.3-2009冲模滚动导向钢板上模座第3部分:中间导柱上模座GB/T23564.4-2009冲模滚动导向钢板上模座第3部分:中间导柱模架GB/T23565.1-2009冲模滚动导向钢板模架第1部分:后侧导柱模架GB/T23565.2-2009冲模滚动导向钢板模架第2部分:对角导柱模架GB/T23565.3-2009冲模滚动导向钢板模架第3部分:中间导柱模架GB/T23565.4-2009冲模滚动导向钢板模架第4部分:四导柱模架GB/T23566.1-2009冲模滚动导向钢板上模座第1部分:后侧导柱上模座GB/T23566.2-2009冲模滚动导向钢板上模座第2部分:对角导柱上模座GB/T23566.3-2009冲模滑动导向钢板上模座第3部分:中间导柱上模座GB/T2851-2008冲模滑动导向模架GB/T2852-2008冲模滚动导向模架GB/T2855.1-2008冲模滑动导向模座第1部分:上模座GB/T2855.2-2008冲模滑动导向模座第2部分:下模座GB/T2856.1-2008冲模滚动导向模座第1部分:上模座GB/T2856.2-2008冲模滚动导向模座第2部分:下模座GB/T2861.10-2008冲模导向装置第10部分:垫圈GB/T2861.11-2008冲模导向装置第11部分:压板GB/T2861.1-2008冲模导向装置第1部分:滑动导向导柱GB/T2861.2-2008冲模导向装置第2部分:滚动导向导柱GB/T2861.3-2008冲模导向装置第3部分:滑动导向导套GB/T2861.4-2008冲模导向装置第4部分:滚动导向导套GB/T2861.5-2008冲模导向装置第5部分:钢球保持圈GB/T2861.6-2008冲模导向装置第6部分:圆柱螺旋压缩弹簧GB/T2861.7-2008冲模导向装置第7部分:滑动导向可卸导柱GB/T2861.8-2008冲模导向装置第8部分:滚动导向可卸导柱GB/T2861.9-2008冲模导向装置第9部分:衬套GB/T35666.4-2009冲模滑动导向钢板上模座第4部分:四导柱上模座GB/T8845-2006冲模术语GB 2863.1-81冷冲模凸、凹模A型圆凸模GB 2863.2-81冷冲模凸、凹模B型圆凸模GB 2863.3-81冷冲模凸、凹模快换圆凸模GB 2863.4-81冷冲模凸、凹模圆凹模GB 2863.5-81冷冲模凸、凹模带肩圆凹模GB 2858.4-81冷冲模模板圆形凹模板GB 2866.1-81冷冲模挡料和弹顶装置始用挡料装置GB 2866.2-81冷冲模挡料和弹顶装置弹簧芯柱GB 2866.3-81冷冲模挡料和弹顶装置弹簧侧压装置GB 2866.4-81冷冲模挡料和弹顶装置侧压簧片GB 2866.5-81冷冲模挡料和弹顶装置弹簧弹顶挡料装置GB 2866.6-81冷冲模挡料和弹顶装置扭簧弹顶挡料装置GB 2866.7-81冷冲模挡料和弹顶装置橡胶弹顶挡料销GB 2866.8-81冷冲模挡料和弹顶装置回带式挡料装置GB 2866.9-81冷冲模挡料和弹顶装置钢球弹顶装置GB 2866.10-81冷冲模挡料和弹顶装置弹簧弹顶装置GB 2866.11-81冷冲模挡料和弹顶装置固定挡料销GB 2864.1-81冷冲模导正销A型导正销GB 2864.2-81冷冲模导正销B型导正销GB 2864.3-81冷冲模导正销C型导正销GB 2864.4-81冷冲模导正销D型导正销GB 2862.1-81冷冲模模柄压入式模柄GB 2862.2-81冷冲模模柄旋入式模柄GB 2862.3-81冷冲模模柄凸缘模柄GB 2862.4-81冷冲模模柄槽形模柄GB 2862.5-81冷冲模模柄通用模柄GB 2862.6-81冷冲模模柄浮动模柄GB 2862.7-81冷冲模模柄推入式活动模柄GB/T2851.1-90冲模滑动导向模架对角导柱模架GB/T2851.3-90冲模滑动导向模架后侧导柱模架GB/T2851.4-90冲模滑动导向模架后侧导柱窄形模架GB/T 2851.5-90冲模滑动导向模架中间导柱模架GB/T2851.6-90冲模滑动导向模架中间导柱圆形模架GB/T2851.7-90冲模滑动导向模架四导柱模架GB/T2852.1-90冲模滚动导向模架对角导柱模架GB/T2852.2-90冲模滚动导向模架中间导柱模架GB/T2852.3-90冲模滚动导向模架四导柱模架GB/T2852.4-90冲模滚动导向模架后侧导柱模架GB/T2855.1-90冲模滑动导向模座对角导柱上模座GB/T2855.2-90冲模滑动导向模座对角导柱下模座GB/T2855.5-90冲模滑动导向模座后侧导柱上模座GB/T2855.6-90冲模滑动导向模座后侧导柱下模座GB/T2855.7-90冲模滑动导向模座后侧导柱窄形上模座GB/T2855.8-90冲模滑动导向模座后侧导柱窄形下模座GB/T2855.9-90冲模滑动导向模座中间导柱上模座GB/T2855.10-90冲模滑动导向模座中间导柱下模座GB/T2855.11-90冲模滑动导向模座中间导柱圆形上模座GB/T2855.12-90冲模滑动导向模座中间导柱圆形下模座GB/T2855.13-90冲模滑动导向模座四导柱上模座GB/T2855.14-90冲模滑动导向模座四导柱下模座GB/T2856.1-90冲模滚动导向模座对角导柱上模座GB/T2856.2-90冲模滚动导向模座对角导柱下模座GB/T2856.3-90冲模滚动导向模座中间导柱上模座GB/T2856.4-90冲模滚动导向模座中间导柱下模座GB/T2856.5-90冲模滚动导向模座四导柱上模座GB/T2856.6-90冲模滚动导向模座四导柱下模座GB/T2856.7-90冲模滚动导向模座后侧导柱上模座GB/T2856.8-90冲模滚动导向模座后侧导柱下模座GB2857.1-81冷冲模通用模座带柄圆形上模座GB2857.2-81冷冲模通用模座带柄矩形上模座GB2857.3-81冷冲模通用模座钢板模座GB2857.4-81冷冲模通用模座模座GB2857.5-81冷冲模通用模座A型下模座GB2857.6-81冷冲模通用模座B型下模座GB2857.7-81冷冲模通用模应C型下模座GB2857.8-81冷冲模通用模座弯曲模下模座JB/T5825-2008冲模圆柱头直杆圆凸模JB/T5826-2008冲模圆柱头缩杆圆凸模JB/T5827-2008冲模60°锥头直杆圆凸模JB/T5828-2008冲模60°锥头缩杆圆凸模JB/T5829-2008冲模球锁紧圆凸模JB/T5830-2008冲模圆凸模JB/T6058-1992冲模用钢及其热处理技术条件JB/T6499.1-1992切边模导柱JB/T6499.2-1992切边模导套JB/T7643.1-2008冲模模板第1部分:矩形凹模板JB/T7643.2-2008冲模模板第2部分:矩形固定板JB/T7643.3-2008冲模模板第3部分:矩形垫板JB/T7643.4-2008冲模模板第4部分:圆形凹模板JB/T7643.5-2008冲模模板第5部分:圆形固定板JB/T7643.6-2008冲模模板第6部分:圆形垫板JB/T7644.1-2008冲模单凸模模板第1部分:单凸模固定板JB/T7644.2-2008冲模单凸模模板第2部分:单凸模垫板JB/T7644.3-2008冲模单凸模模板第3部分:偏装单凸模固定板JB/T7644.4-2008冲模单凸模模板第4部分:偏装单凸模垫板JB/T7644.5-2008冲模单凸模模板第5部分:球锁紧单凸模固定板JB/T7644.6-2008冲模单凸模模板球锁紧单凸模垫板JB/T7644.7-2008冲模单凸模模板第7部分:球锁紧偏装单凸模固定板JB/T7644.8-2008冲模单凸模模板第8部分:球锁紧偏装单凸模垫板JB/T7645.1-2008冲模导向装置第1部分:A型小导柱JB/T7645.2-2008冲模导向装置第2部分:B型小导柱JB/T7645.3-2008冲模导向装置第3部分:小导套JB/T7645.4-2008冲模导向装置第4部分:压板固定式导柱JB/T7645.5-2008冲模导向装置第5部分:压板固定式导套JB/T7645.6-2008冲模导向装置第6部分:压板JB/T7645.7-2008冲模导向装置第7部分:导柱座JB/T7645.8-2008冲模导向装置第8部分:导套座JB/T7646.1-2008冲模模柄第1部分:压入式模柄J B/T7646.2-2008冲模模柄第2部分:旋入式模柄JB/T7646.3-2008冲模模柄第3部分:凸缘模柄JB/T7646.4-2008冲模模柄第4部分:槽形模柄JB/T7646.5-2008冲模模柄第5部分:浮动模柄JB/T7646.6-2008冲模模柄第6部分:推入式活动模柄JB/T7647.1-2008冲模导正销第1部分:A型导正销JB/T7647.2-2008冲模导正销第2部分:B型导正销JB/T7647.3-2008冲模导正销第3部分:C型导正销JB/T7647.4-2008冲模导正销第4部分:D型导正销JB/T7648.1-2008冲模侧刃和导料装置第1部分:侧刃JB/T7648.2-2008冲模侧刃和导料装置第2部分:A型侧刃挡块JB/T7648.3-2008冲模侧刃和导料装置第3部分:B型侧刃挡块JB/T7648.4-2008冲模侧刃和导料装置第4部分:C型侧刃挡块JB/T7648.5-2008冲模侧刃和导料装置第5部分:导料板JB/T7648.6-2008冲模侧刃和导料装置第6部分:承料板JB/T7648.7-2008冲模侧刃和导料装置第7部分:A型抬料销JB/T7648.8-2008冲模侧刃和导料装置第8部分:B型抬料销JB/T7649.10-2008冲模挡料和弹顶装置第10部分:固定挡料销JB/T7649.1-2008冲模挡料和弹顶装置第1部分:始用挡料装置JB/T7649.2-2008冲模挡料和弹顶装置第2部分:弹簧芯柱JB/T7649.3-2008冲模挡料和弹顶装置第3部分:弹簧侧压装置JB/T7649.4-2008冲模挡料和弹顶装置第4部分:侧压簧片JB/T7649.5-2008冲模挡料和弹顶装置第5部分:弹簧弹顶挡料装置JB/T7649.6-2008冲模挡料和弹顶装置第6部分:扭簧弹顶挡料装置JB/T7649.7-2008冲模挡料和弹顶装置第7部分:回带式挡料装置JB/T7649.8-2008冲模挡料和弹顶装置第8部分:钢珠弹顶装置JB/T7649.9-2008冲模挡料和弹顶装置第9部分:活动挡料销JB/T7650.1-2008冲模卸料装置第1部分: 带肩推杆JB/T7650.2-2008冲模卸料装置第2部分: 带螺纹推杆JB/T7650.3-2008冲模卸料装置第3部分: 顶杆JB/T7650.4-2008冲模卸料装置第4部分: 顶板JB/T7650.5-2008冲模卸料装置第5部分: 圆柱头卸料螺钉JB/T7650.6-2008冲模卸料装置第6部分: 圆柱头内六角卸料螺钉JB/T7650.7-2008冲模卸料装置第7部分: 定距套件JB/T7650.8-2008冲模卸料装置第8部分: 调剂垫圈JB/T7651.1-2008冲模废料切刀第1部分:圆废料切刀JB/T7651.2-2008冲模废料切刀第2部分:方废料切刀JB/T7652.1-2008冲模限位支承装置第一部分:支承套件JB/T7652.2-2008冲模限位支承装置第一部分:限位柱JB/T7653-2008冲模零件技术条件JB/T8050-2008冲模模架技术条件JB/T8070-2008冲模模架零件技术条件JB/T8071-2008冲模模架精度检查三、冲压模具的设计流程(一)、冲压模具的设计流程:1、冲压件的工艺性分析。
浅谈冲压模具设计及要求

浅谈冲压模具设计及要求冲压模具设计是指根据产品的形状和尺寸要求,制作适用于金属材料冲压生产的模具。
冲压模具设计的目标是实现高效率、高质量的生产过程,提高产品的精度和一致性,降低生产成本。
冲压模具设计的基本要求包括以下几个方面:1. 产品形状和尺寸的要求:冲压模具设计首先要满足产品的形状和尺寸要求。
模具的结构和构造要能够实现产品的所需形状和尺寸的加工过程,并能够保证产品的精度和一致性。
2. 材料选择和热处理要求:冲压模具的材料选择要根据产品的材料和加工要求来确定。
常用的材料有合金钢、硬质合金和高速钢等。
冲压模具还需要进行必要的热处理,以提高其硬度、强度和耐磨性。
3. 结构设计要合理:冲压模具的结构设计要合理,能够满足生产加工的要求。
模具的结构应当简单、明了,易于制作和维护。
模具的各个部件之间的配合要良好,能够确保冲压生产的准确性和稳定性。
4. 寿命和易损件设计要考虑:冲压模具的寿命是衡量其质量的重要指标。
在模具设计过程中要考虑到其寿命的要求,并采取相应的设计措施来延长模具的使用寿命。
对于易损件,如模具座、切口等,还要进行重点考虑和设计,以确保其使用寿命和易更换的特点。
5. 加工工艺要符合生产能力:冲压模具的加工工艺要符合生产能力的要求。
模具的制作工艺应当合理,能够满足生产的要求,并尽量减少加工工序和工时。
还应当考虑到生产设备的限制和条件,以便保证冲压生产的顺利进行。
冲压模具设计的过程是一个综合考虑产品要求、材料要求、加工工艺要求等多个因素的过程。
在进行冲压模具设计时,需要进行详细的产品分析和模具设计计算,充分考虑各种因素的影响,以确保设计的准确性和合理性。
冲压模具设计技术要求
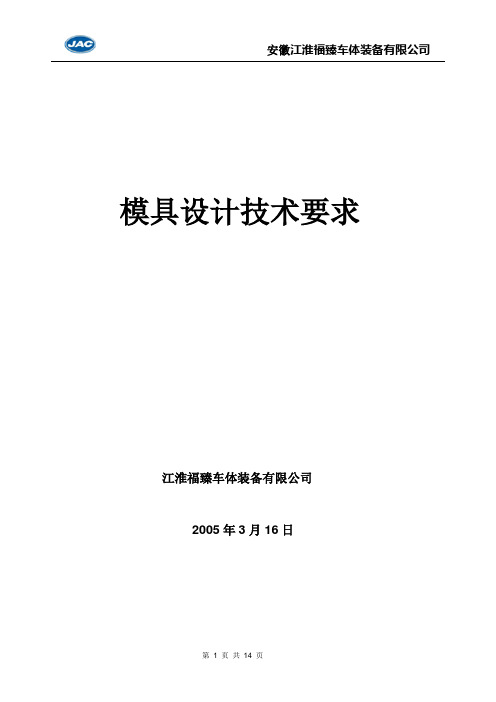
模具设计技术要求江淮福臻车体装备有限公司2005年3月16日甲方:安徽江淮福臻车体装备有限公司乙方:安徽江淮福臻车体装备有限公司(以下简称甲方)委托(以下简称乙方)设计项目中个冲压件套模具,为保证设计质量,经双方认真协商达成以下协议。
一、所设计冲压件的资料序号零件名称件号材质材料厚度模具套数使用的生产线备注123456789101112合计注:1 各工序模具使用生产线及设备在工艺方案会签时确定2 模具详细资料见工程图(DL)二、双方承担的工作和责任1、甲方1)提供完整、清晰的产品图纸和数模,产品更改时提供书面通知,明确更改内容;2)提供设备规格(附后);3)负责确定设计所选用标准件的厂家;4)负责工程图、模具图纸的会签及泡沫模型实物状态的确认;5)负责确定工程图及模具图纸的会签日期。
2、乙方1)审查工艺合理性,对无法完成的工序提交双方讨论,经甲方、乙方双方审查完成甲方签字后方可进行更改;2)自双方签订订货合同日起,乙方按甲方确定的会签日期进行设计及会签;3)乙方必须向甲方提供完整的电子版工程(DL)图(工序内容完整,图形表示清晰)和其他相关图纸、资料;4)乙方必须对所设计的图纸进行认真校对和审核,电子版图纸上必须有设计人员、校对人员、审核人员的签名;5)所有结论前的产品及工艺更改,涉及到设计内容的则需要修改相应工程图、模具图及检具图。
对于工作量较大的,增加费用问题与甲方协商解决;6)按甲方清单注明的零件需做成型模拟分析的,提供模拟结果并对结果负责;7)乙方所设计模具必须符合甲方自动化生产要求:机械手上下件、气动挺件、废料自动滑出等;8)如甲方在生产制造过程中对乙方所设计的图纸存在疑问,乙方有责任在24小时内派技术人员对现场进行解疑及指导。
三、模具寿命及冲压线分布1、开发模具生产纲领要求:总寿命万辆,(双、单)班万辆/年。
2、冲压设备流水分布图示:1) A线:2000 1000 800 8000 1000ES2) B1线:10008008006306303) B2线:120080063063080010004) C1线:6304004004006305)C2线:630400400400400四、制图标准的基本要求1、乙方在进行工艺方案和模具设计时,应按本协议要求执行,如设计时有超出本协议的内容,可双方协商解决。
冲压模具设计技术要求
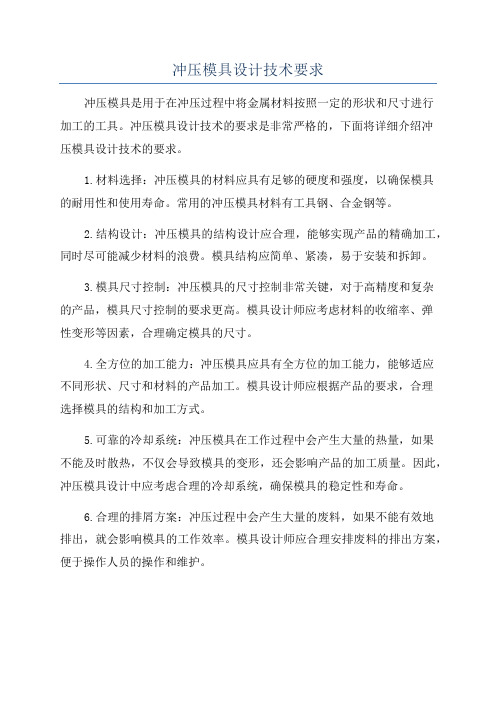
冲压模具设计技术要求冲压模具是用于在冲压过程中将金属材料按照一定的形状和尺寸进行加工的工具。
冲压模具设计技术的要求是非常严格的,下面将详细介绍冲压模具设计技术的要求。
1.材料选择:冲压模具的材料应具有足够的硬度和强度,以确保模具的耐用性和使用寿命。
常用的冲压模具材料有工具钢、合金钢等。
2.结构设计:冲压模具的结构设计应合理,能够实现产品的精确加工,同时尽可能减少材料的浪费。
模具结构应简单、紧凑,易于安装和拆卸。
3.模具尺寸控制:冲压模具的尺寸控制非常关键,对于高精度和复杂的产品,模具尺寸控制的要求更高。
模具设计师应考虑材料的收缩率、弹性变形等因素,合理确定模具的尺寸。
4.全方位的加工能力:冲压模具应具有全方位的加工能力,能够适应不同形状、尺寸和材料的产品加工。
模具设计师应根据产品的要求,合理选择模具的结构和加工方式。
5.可靠的冷却系统:冲压模具在工作过程中会产生大量的热量,如果不能及时散热,不仅会导致模具的变形,还会影响产品的加工质量。
因此,冲压模具设计中应考虑合理的冷却系统,确保模具的稳定性和寿命。
6.合理的排屑方案:冲压过程中会产生大量的废料,如果不能有效地排出,就会影响模具的工作效率。
模具设计师应合理安排废料的排出方案,便于操作人员的操作和维护。
7.安全性和可维护性:冲压模具设计应考虑到操作人员的安全,避免因操作不当导致事故发生。
同时,冲压模具应具备可维护性,便于检修和更换损坏的部件。
8.尽量减少模具的使用成本:在冲压模具设计中,应尽量减少模具的使用成本,包括原材料成本、制造成本和维护成本等。
通过合理的结构设计和材料选择,可以有效降低模具的使用成本。
总之,冲压模具设计技术要求严格,设计师需要综合考虑材料、结构、尺寸控制、加工能力、冷却系统、废料排出、安全性和可维护性等多个因素,以确保模具的质量和使用寿命。
只有具备专业的技术知识和丰富的实践经验,才能设计出高质量、高效率的冲压模具。
冲压模具标准及技术要求

第14章冲压模具标准及技术要求冲模标准是指在冲模设计与制造中应该遵循和执行的技术规范和标准。
制订冲模标准的意义有以下几个方面:1.可以缩短模具设计与制造周期因为模具结构及制造精度与冲压件的形状、尺寸精度以及生产的批量有关,所以冲模的种类繁多而且结构十分的复杂。
比如精密级进模的模具零件有时上百个(甚至更多),这样使得模具的设计与制造周期很长。
而实现模具标准化后,所有的标准件都可以外购,从而减化了模具的设计、减少了模具零件的制造工作量,最终的结构就是缩短了模具的制造周期。
2.有利于保证质量可以稳定和保证模具设计质量和制造中必须达到的质量规范,以保证冲压件的质量。
3.有利于模具的计算机辅助设计与制造模具技术标准使实现模具计算机辅助设计与制造的基础,可以这样说:没有模具标准化就没有模具的计算机辅助设计与制造。
4.有利于国际国内的交流与合作技术名词术语、技术条件的规范化、标准化将有利于国内、国际的商业贸易和技术交流,增强企业、国家的技术经济实力。
我国在模具行业中推广使用的模具标准是经国家技术监督局批准的国家标准(GB)和机械行业标准(JB)。
另外还有国际模具标准化组织ISO/TC29/SC8制订的冲模和成形模标准。
除此之外,由于我国一些企业从国外引进了大量级进模与汽车覆盖件模具,随着模具的引进,国外冲模标准也在我国一些企业中引用,如日本三住商事株式会议(MISUMI)的Face 标准,德国STRACK公司标准,美国DANLY公司标准等。
由于篇幅的原因,本篇只介绍常用的GB、JB及部分日本的Face标准。
14.1设计冲模时常用的标准我国已颁布的冲模技术标准见表14-1。
表14-1表14-1我国已颁布的冲模标准分类标准名称标准代号基础工艺质量1)冲模术语2)冲压件尺寸公差3)冲压件角度公差4)冲压件形状和位置未注公差5)冲压件未注公差尺寸极限偏差6)冲裁间隙7)冲模技术条件8)金属冷冲压件结构要素9)金属冷冲压件通用技术条件10)精密冲裁件通用技术条件GB/T8845-2006GB/T13914-2002GB/T13915-2002GB/T13196-2002GB/T15055-2007GB/T16743-1997GB/T14662-2006JB/T4378.1-1999JB/T4378.2-1999JB/T6958-1993设计冲压模具还应该执行和采用国家基础标准有:公差与配合标准;形状与位置公差;表面粗糙度标准;机械制图标准;尺寸及尺寸系列。
冲压模具设计标准dwg
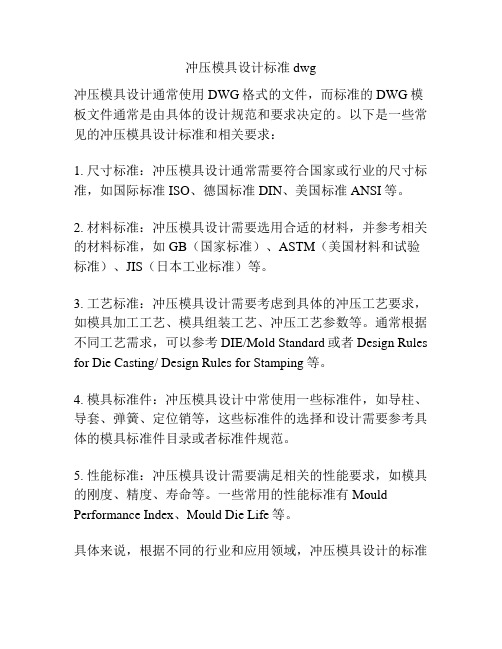
冲压模具设计标准dwg
冲压模具设计通常使用DWG格式的文件,而标准的DWG模板文件通常是由具体的设计规范和要求决定的。
以下是一些常见的冲压模具设计标准和相关要求:
1. 尺寸标准:冲压模具设计通常需要符合国家或行业的尺寸标准,如国际标准ISO、德国标准DIN、美国标准ANSI等。
2. 材料标准:冲压模具设计需要选用合适的材料,并参考相关的材料标准,如GB(国家标准)、ASTM(美国材料和试验标准)、JIS(日本工业标准)等。
3. 工艺标准:冲压模具设计需要考虑到具体的冲压工艺要求,如模具加工工艺、模具组装工艺、冲压工艺参数等。
通常根据不同工艺需求,可以参考DIE/Mold Standard或者Design Rules for Die Casting/ Design Rules for Stamping等。
4. 模具标准件:冲压模具设计中常使用一些标准件,如导柱、导套、弹簧、定位销等,这些标准件的选择和设计需要参考具体的模具标准件目录或者标准件规范。
5. 性能标准:冲压模具设计需要满足相关的性能要求,如模具的刚度、精度、寿命等。
一些常用的性能标准有Mould Performance Index、Mould Die Life等。
具体来说,根据不同的行业和应用领域,冲压模具设计的标准
和要求会有所差异。
因此,在冲压模具设计过程中,应根据具体需求参考相关的标准和规范,以确保设计的质量和可靠性。
- 1、下载文档前请自行甄别文档内容的完整性,平台不提供额外的编辑、内容补充、找答案等附加服务。
- 2、"仅部分预览"的文档,不可在线预览部分如存在完整性等问题,可反馈申请退款(可完整预览的文档不适用该条件!)。
- 3、如文档侵犯您的权益,请联系客服反馈,我们会尽快为您处理(人工客服工作时间:9:00-18:30)。
模具设计技术要求江淮福臻车体装备有限公司2005年3月16日甲方:安徽江淮福臻车体装备有限公司乙方:安徽江淮福臻车体装备有限公司(以下简称甲方)委托(以下简称乙方)设计项目中个冲压件套模具,为保证设计质量,经双方认真协商达成以下协议。
一、所设计冲压件的资料序号零件名称件号材质材料厚度模具套数使用的生产线备注123456789101112合计注:1 各工序模具使用生产线及设备在工艺方案会签时确定2 模具详细资料见工程图(DL)二、双方承担的工作和责任1、甲方1)提供完整、清晰的产品图纸和数模,产品更改时提供书面通知,明确更改内容;2)提供设备规格(附后);3)负责确定设计所选用标准件的厂家;4)负责工程图、模具图纸的会签及泡沫模型实物状态的确认;5)负责确定工程图及模具图纸的会签日期。
2、乙方1)审查工艺合理性,对无法完成的工序提交双方讨论,经甲方、乙方双方审查完成甲方签字后方可进行更改;2)自双方签订订货合同日起,乙方按甲方确定的会签日期进行设计及会签;3)乙方必须向甲方提供完整的电子版工程(DL)图(工序内容完整,图形表示清晰)和其他相关图纸、资料;4)乙方必须对所设计的图纸进行认真校对和审核,电子版图纸上必须有设计人员、校对人员、审核人员的签名;5)所有结论前的产品及工艺更改,涉及到设计内容的则需要修改相应工程图、模具图及检具图。
对于工作量较大的,增加费用问题与甲方协商解决;6)按甲方清单注明的零件需做成型模拟分析的,提供模拟结果并对结果负责;7)乙方所设计模具必须符合甲方自动化生产要求:机械手上下件、气动挺件、废料自动滑出等;8)如甲方在生产制造过程中对乙方所设计的图纸存在疑问,乙方有责任在24小时内派技术人员对现场进行解疑及指导。
三、模具寿命及冲压线分布1、开发模具生产纲领要求:总寿命万辆,(双、单)班万辆/年。
2、冲压设备流水分布图示:1) A线:2000 1000 800 800 1000ES2) B1线:10008008006306303) B2线:120080063063080010004) C1线:6304004004006305)C2线:630400400400400四、制图标准的基本要求1、乙方在进行工艺方案和模具设计时,应按本协议要求执行,如设计时有超出本协议的内容,可双方协商解决。
2、除特殊注明外,所有图纸资料必须符合机械制图国家标准GB4457~4460-84,GB131-83。
3、所有工程图(DL)、模具图按2D进行设计,文件类型为dwg格式。
4、图面要求:1)视图投影法:第一角法;2)图幅要求:按机械制图国家标准;3)图型比例:1:1,1:2,1:3;4)图纸标题栏:甲方标准;5)零件明细表:甲方标准;6)零件图作图样式:左侧零件;7)对镶拼结构的镶块资料应单独出图,并标识清楚。
五、工程图(DL图)设计技术要求:1、工程图必须表达清楚,尺寸完整正确,能正确指导工艺数模设计及模具设计。
2、工程图必须正确反映以下内容:1)完成零件冲压加工的所有工序数及各工序加工内容,并用不同符号加以区分,工序用OP10(1/n)、OP20(2/n)、… Opx0(x/n) … n/n表示;n为零件工序总数。
2)模具图号采用:零件图号---- OPx0(x/n) ----工作内容(常用英文缩写),例如:65493-7A00-OP20(2/4)-TR+PI+CTR,(DR---拉延、TR---修边、PI—冲孔、RST---整形、C---侧)3)各工序冲压加工方向。
当加工方向相对零件车身坐标发生旋转时,应注明其旋转角度;4)各工序零件送进、流出方向;5)废料切刀的布置位置及切边、冲孔废料的排除方式;6)各工序模具设计基准点、基准线与零件车身坐标之间的对应关系;7)拉延工艺补充部分的详细图形,计算回弹量及修正措施;8)拉延工序到位标记位置(安放在切除的废料部位),C/H孔位置,左右件标记L/R位置;9)零件板材毛坯尺寸标注,中间工序的切边线及其完整尺寸标注;10)斜楔加工方向、加工范围及结构简图;11)各加工工序草图(含工序名称,工序加工内容,使用设备,模具代号等);12)顶杆布置图、废料流向示意及方案图中各种符号说明。
六、工艺数模技术要求:1、工艺建模采用三维合格的正版软件,甲方接受CATIA V5R11的Part文件格式或IGES文件格式。
2、零件工艺数模尺寸满足工艺方案设计要求,零件型面尺寸按甲方提供的产品数据,误差不超过0.01mm。
3、所有零件在建模中的坐标以零件工艺方案的基准点坐标为准。
4、所有的零部件数模均应保持参数化。
5、所建数模对称部分不用另外重建数模,只针对非对称部分进行局部建模。
6、每副模具的特殊线(切边线、分模线等)应计算并作出相应的线框模型和线型颜色区分。
7、文件的命名规则:模具的数模文件用甲方提供的该模具的代号命名,一副模具只对应一个文件,不再另建零件数据文件。
例如:CV7 5401601 CM3-1,代表零件5401601共3序中的第1序。
七、模具结构设计技术要求:1、所有模具在结构设计上必须符合甲方自动化生产要求:机械手上下件、自动传感、气动挺件、废料自动滑出等;但同时要考虑手动上下件,以免因自动线故障而影响生产;2、模具在正常使用状态下,按3000~5000件冲次为期限定期维护为前提,按可以生产30万件进行模具设计。
3、所有需数控加工的模具零件应设加工基准孔φ16H7深20mm共3处。
4、按甲方的要求,确定下模送料高度(资料会签时,由甲方技术人员确定)。
5、模具导向类型为自润滑式导柱、导套、导板,导柱、导套要用螺钉固定,导板后要设置背托。
6、模具导向型式:带有侧整形、侧切边冲孔型模具(具有侧向受力,且带有切边、冲孔的模具)要采用导板+导柱导套形式导向,其导向件尺寸按标准选用。
7、模具的起重类型:所有模具原则上要求采用吊耳式起重,对于小型模具允许采用铸入式起重棒;重量超过20公斤零件要设计起重螺栓的位置,起重螺栓的规格M12、M16、M20。
8、模具必须具有足够的安全性,设计时必须考虑安全螺钉或侧销。
(具体形式见修边冲孔模样图)9、必须保证零件在模具内定位可靠,每工序完成后零件不粘模,具有良好的生产可操作性。
10、模具按甲方提供的设备工艺参数进行设计,保证模具在给定设备上的可生产性;模具长、宽应控制在工作台面以内,结构必须紧凑。
11、模具高度:同一零件(含其对称件)的模具封闭高度原则上保持一致,如因结构原因高度发生变化时需得到甲方技术人员的确认。
12、冲压模具上均设置自由状态下的弹性支撑或刚性支撑(具体形式在模具图设计会签时确定),并设计模具限位器和安全平台(尺寸150x150)。
13、所有模具在结构上如无特殊要求则均设计成单动式。
14、模具在设计上,应考虑安装防反措施。
15、在模具上应设置标牌位置(190x160)(具体要求见后面)。
16、标准件选用:选用北京世茂、永茂、日本三住或日本三协,气缸及气动元件选用SMC,并备有相应备件和明细。
17、所有斜楔机构原则上均需选用标准件,以保证其使用的可靠性、准确性及互换性,如无法选择标准件的,会签时双方协商确定。
18、在设计上必须考虑铸造工艺性、加工工艺性和维修过程中的方便性。
八、模具结构设计的基本要求:1、压板槽数量及尺寸W尺寸上底板下底板W<1000 ≥4≥41000<W<2000 ≥6 ≥62000<W ≥8≥6备注:具体情况会签时确定大型模具:A=50、B=60中小模具:A=40、B=50备注:压板槽位置尺寸根据压床垫板配合设计2、模具的安装及定位在上下模底板压床中心线上设计出铸造“V”形槽,在下模增加快速定位(位置按压床规格设计),直径60,上下模均设计加工键槽宽28深20,如图:3、废料切刀布置形式废料切刀应如上图布置,以便于废料的排除4、在设计侧面减轻孔时应考虑公司标识及铸字区域位置(如图)九、几种典型模具的具体要求:1、拉延模、成型模1) 铸件壁厚:材料厚度 A B C D E F J H K G M≤1.550 50 40 40 40 40 30 30 30 40-50 30>1.5 55 55 45 40 40 40 35 35 30 40-50 352) 模具材料:凸模、凹模、压料圈具均采用MoCr铸铁。
当料厚>2.5时,压料面要求采用锻件镶块形式,以确保模具的使用寿命。
3) 凸模、凹模、压料圈等淬火硬度HRC50以上,淬火部分不允许有软点;凹模口必须光滑均匀,手感不允许有波纹,淬硬层2mm以上。
4) 当一级托杆不能满足使用要求时应采用铸腿结构,托杆接触面必须保证直径60mm以上,模具闭合状态距下底面为20mm以上。
5) 拉延成型模具带有刃口时必须辅以导柱导向。
6) 顶杆、墩死块、平衡垫等受力区位置要设有支撑加强筋2、修边冲孔模1) 铸件壁厚材料厚度 A B C D E F G J H L ≤1.545 40 40 35 30 30 40 35 30 25>1.5 50 45 40 40 35 35 40 40 35 302) 模具材料:通常凸模、凹模、废料刀在t≤1.5时采用铸造空冷钢,火焰淬火HRC55-60; 在t >1.5时采用SKD11或D2,淬火HRC58—62;退料板采用HT300,上下底板等采用HT250。
3) 修边凸凹模镶块当t≥1.2时加靠背或配键,模具上≤φ10的圆孔或异型孔,在设计时采用快换式,且在图纸明细栏备注中注明其凸模、凹模各备3套,凹模要求全部用镶套结构,特殊情况由甲方会签确定。
4) 要求外切边废料单件滑出模具外,其废料长度不允许超过450mm,对于内部废料较大的要求设置废料滑道滑出模体(废料滑道角度不小于20度);对于小于30㎜孔类废料允许使用废料盒,但要求满足每批次300--500件,且便于人工排除(具体要求在模具图设计会签时确定)。
5)大型模具要求使用侧销机构;对于中小型使用安全螺钉的模具,要求如上图采用倒装式,以便于安装与维修。
6)压料体设计时要考虑加工底面或弹簧座时的支撑:要求设计四处直径40的等高凸台(在加工型面时加工掉),且要考虑机床加工时的装夹位置。
3、翻边整形模1) 铸件壁厚:材料厚度 A B C D E F G K H≤1.545 35 35 35 40 40 40 25 25-30>1.5 50 40 40 40 40 40 40 30 30-352)模具材料:上、下模座:HT250。
压料板:不参与成型时采用HT300, 参与成型时采用MoCr铸铁。
凸、凹模:采用镶块形式,当材料厚度t≤1.5时采用MoCr铸铁,淬火HRC50-55,当材料厚度t>1.5时采用SKD11或D2,淬火HRC58-62。