弯曲工艺及弯曲件的结构工艺性
第四节 弯曲件的工艺性
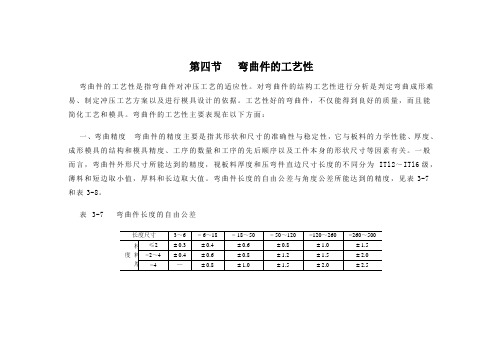
第四节弯曲件的工艺性弯曲件的工艺性是指弯曲件对冲压工艺的适应性。
对弯曲件的结构工艺性进行分析是判定弯曲成形难易、制定冲压工艺方案以及进行模具设计的依据。
工艺性好的弯曲件,不仅能得到良好的质量,而且能简化工艺和模具。
弯曲件的工艺性主要表现在以下方面:一、弯曲精度弯曲件的精度主要是指其形状和尺寸的准确性与稳定性,它与板料的力学性能、厚度、成形模具的结构和模具精度、工序的数量和工序的先后顺序以及工件本身的形状尺寸等因素有关。
一般而言,弯曲件外形尺寸所能达到的精度,视板料厚度和压弯件直边尺寸长度的不同分为ITl2~ITl6级,薄料和短边取小值,厚料和长边取大值。
弯曲件长度的自由公差与角度公差所能达到的精度,见表3-7和表3-8。
表 3-7弯曲件长度的自由公差表 3-8 弯曲件角度的自由公差对较高精度要求的弯曲件,可增加整形、校平工序以提高精度。
二、最小弯曲半径当弯曲件相对弯曲半径t r /小到一定程度时,会使弯曲件外表面纤维的拉伸应变超过材料所允许的极限而出现裂纹或折断,所以对弯曲件有一个最小弯曲半径的限制。
在保证坯料外表面纤维不发生破坏的前提下,工件能够弯成的内表面最小圆角半径,称为最小弯曲半径t r /min ,相应地t r /min 称最小相对弯曲半径。
1. 影响最小弯曲半径的因素(1)材料的力学性能 材料的塑性越好,其塑性指标(ψδ、)越高,相应地最小弯曲半径也越小。
(2)材料的纤维方向与折弯线方向的关系 轧制的扳料是各向异性的,顺着纤维方向的塑性指标高于垂直于纤维方向的塑性指标。
因此弯曲折弯线如果垂直于板料纤维方向,则t r /min 的数值小于折弯线与纤维方向平行弯曲的t r /min 值(见图3—11)。
当弯曲t r /较小的工件时,尽量使折弯线垂直于板料的纤维方向,以提高变形程度,避免外层纤维拉裂。
多向弯曲的工件,可使折弯线与板料纤维方向成一定角度(见图3—11)。
(3)板料的表面质量与坯料断面质量 坯料表面如有划伤、裂纹,或侧面(剪切或冲裁 断面)有毛刺、裂口和冷作硬化等缺陷,弯曲 时易于开裂。
弯曲工艺及弯曲件工艺性
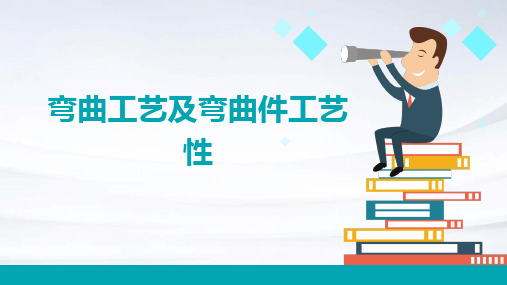
详细描述
弯曲角度的大小直接影响弯曲件的形 状和工艺难度。在选择合适的弯曲角 度时,需要考虑材料的特性、弯曲半 径以及弯曲力等因素。
弯曲半径
总结词
弯曲半径指的是弯曲过程中,弯曲中心到弯曲件表面的距离 。
详细描述
弯曲半径的大小决定了弯曲件的曲率和质量。较小的弯曲半 径可能导致材料过度应力集中,而较大的弯曲半径则可能导 致弯曲件形状不准确。
弯曲件的类型
按角度分类
根据弯曲角度的不同,弯曲件可 分为锐角件、直角件和钝角件等
。
按弯曲半径分类
根据弯曲半径的大小,弯曲件可分 为锐弯件、半弯件和全弯件等。
按材料分类
根据材料的性质,弯曲件可分为金 属弯曲件、塑料弯曲件、木质弯曲 件等。
弯曲件的特点
形状多样性
弯曲件形状多样,可根据实际需求进 行定制,满足不同领域的需求。
结构稳定性
经过合理的弯曲工艺处理,弯曲件具 有良好பைடு நூலகம்结构稳定性,能够在各种环 境下保持稳定性能。
加工精度高
现代的弯曲工艺技术可以保证高精度 的加工要求,使弯曲件具有良好的互 换性和配合性。
材料强度高
高质量的材料和先进的热处理技术可 以提高弯曲件的使用寿命和承载能力 。
03 弯曲工艺参数
弯曲角度
总结词
弯曲工艺是一种重要的金属加工 工艺,广泛应用于汽车、家电、 航空航天等领域。
弯曲工艺的分类
01
02
03
根据弯曲程度
分为简单弯曲、复杂弯曲 和扭曲弯曲。
根据弯曲方式
分为自由弯曲、夹弯和滚 弯。
根据弯曲材料
分为板料弯曲、管料弯曲 和棒料弯曲。
精选弯曲工艺与弯曲模设计
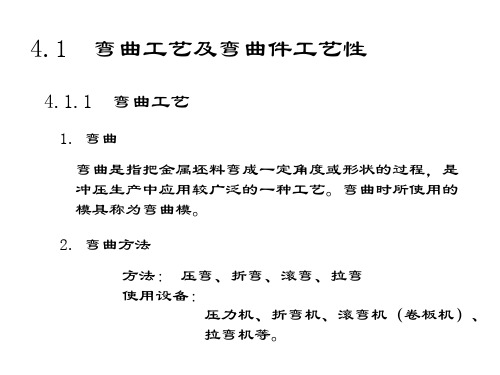
3.弯曲件的直边高度
直边高度H过小,那么直边在弯曲模上支承的长度也过小,不易形成足够的弯矩,弯曲件的形状难以控制。
如果
可加大直边高度,待弯曲成形后,再将直边的高出部分切除。
当弯曲边带有斜度时,应保证
图 4-9 直边高度要求
4.弯曲件孔边距
图 4-10 弯曲件孔边距
图 4-11 防止孔变形的措施
(5)弯曲校正力。 弯曲校正力愈大,塑性变形程度愈大,回弹愈小。
3.减小回弹的措施
1)补偿法
预先估算或试验出工件弯曲后的回弹量,在设计模具时,使弯曲件的变形量超过原设计量,工件回弹后就得到所需要的正确形状。
图 4-30 补偿法示意图
2)校正法
图 4-31 校正法示意图
校正压力集中施加在弯曲变形区,使其塑性变形成分增加,弹性变形成分减小,从而使回弹量减小。
2.弹-塑性弯曲阶段
促使材料塑性变形的弯曲力矩是逐渐增大的。由于弯曲力臂l逐渐减小,因此弯曲力处于不断上升的趋势。凸模继续下行,板料与凸模V形斜面接触后被后向弯曲。
后向弯曲
3. 塑性弯曲阶段
当凸模到达下止点时,毛坯被紧紧地压在凸模与凹模之间,使毛坯内侧弯曲半径与凸模的弯曲半径吻合,完成弯曲过程,变形由弹—塑性弯曲过渡到塑性弯曲。
2.工序安排方法
(1)简单形状一次弯曲成形
图 4-36 一道工序弯曲成形
(2)复杂形状,一般采用两次或多次弯曲成形
图 4-37 二道工序弯曲成形
图 4-38 三道工序弯曲成形
(3)对于某些结构不对称的零件,采用弯曲后再切开的方法
图 4-39 成对弯曲成形
(4)弯曲件有高精度孔时,采用先弯曲后冲孔的方法
4.4.2 弯曲力的计算
弯曲件的工艺性

对低塑性材料可采用加热弯曲以提高材料塑性变形能力,如 镁合金、钛合金等;
对较厚材料的弯曲,可以采取开工艺槽的方法,使弯曲部分 材料变薄再进行弯曲。
(2)板料弯曲的方 向性
当弯曲件的折弯线与板 料的纤维方向垂直时, 材料具有较大的伸长变 形能力,最小弯曲半径 可取较小值;
用强,从而rmin/t可取小些。
表3.9给出了一些材料的rmin/t值,设计时可供参考。
2.弯曲件的直边高度
一般直边高度H>2t,最 好H>3t。
如果不能保证H>2t,可 在弯曲部位预先压槽后再 弯曲,或适当增长直边部 分,弯曲成形后再切去多 余部分,如图3.27所示。
图3.27 弯曲件的直边高度
图3.32 两道工序弯曲成形
图3.33 三道工序弯曲成形
③ 采用对称弯曲 对具有单面几何形状 的弯曲件,将其成对 弯曲,然后切开如图 3.34所示。
图3.34 对称弯曲
④ 当弯曲件的边沿部位有缺口时,若直接弯曲容易发生叉口 现象。这种情况一般加连接带将缺口连成一体,等弯曲成形 后再将缺口多余部分切去。
如图3.30(c)所示,工艺孔直径d应该大于板料 的厚度t。
Байду номын сангаас
(a)
(b)
(c)
图3.30 防止尖角处产生裂纹的措施
5.弯曲件的形状 弯曲件的形状要尽量规则、对称。
6.弯曲件的尺寸标注 按图3.31(a)所示标注可以先冲孔落料,再
弯曲; 按图3.31(b)所示标注冲孔只能在弯曲之后,
增加了工序。
⑤ 对大批量、尺寸小的弯曲件,在条件许可下可以采用连续 工艺成形,如图3.35所示。
图3.35 连续工艺成形
第3章 弯曲工艺与弯曲模具
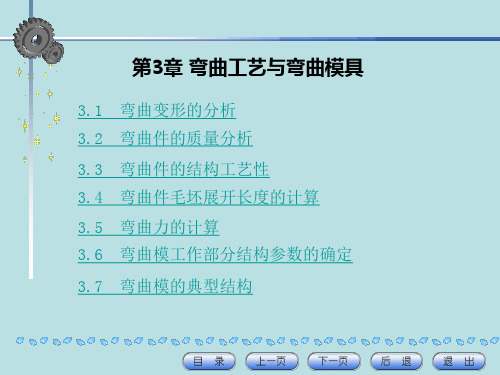
总之影响最小弯曲半径的主要因素如下:
⒈ 材料的机械性能;
⒉ 板材纤维的方向性;
⒊ 弯曲件的宽度; ⒋ 板材的表面质量和剪切断面质量;
⒌ 弯曲角;
⒍ 板材的厚度。 最小弯曲半径可按表3-1选取
表3-1 最小弯曲半径rmi
3.2.2、弯曲时的回弹及控制回弹的措施 1、弯曲回弹现象 弯曲回弹现象产生于弯曲变形结束后的卸载过程,是由其内部产生 的弹性回复力矩造成的。弯曲件卸载后的回弹,表现为弯曲件的弯曲 半径和弯曲角的变化,如图3-6所示。
(a )
(b ) (c) 图3-25 防止尖角处撕裂的措施
0 绪论 一、冲压概念
图3-26所示的零件,根据需要设置了工艺孔、槽及定位孔。图(a) 所示工件弯曲后很难达到理想的直角,甚至在弯曲过程中变宽、开 裂。如果在弯曲前加工出工艺缺口(M×N),则可以得到理想的弯 曲件。图(b)所示的工件,在弯曲处预先冲制了工艺孔,效果与 图(a)相同。图(c)所示的工件,要经过多次弯曲,图中的D是 定位工艺孔,目的是作为多次弯曲的定位基准,虽然经多次弯曲, 该零件仍保持了对称性和尺寸精度,
0 绪论 一、冲压概念
凸模下行,减小到r/t>200时,板料处于线形弹塑性状态,
即板料中心几附近区域为弹性变形,其他部分为塑性变形, 弯曲进行至r/t值大约在(200>r/t>5)时,板料进入线形全塑
性弯曲状态。
当其进一步减小到r/t3~5时,则为立体塑性弯曲,此即模 具弯曲最终状态。
• 窄板(b/t3)弯曲时,宽度 方向可以自由变形,故其应 力b0,内外层的应变状态 是立体的,应力状态是平面 的。 • 宽板(b/t>3)弯曲时,由于 宽度方向材料不能自由变形 (宽度基本不变),即
弯曲模具的基本原理
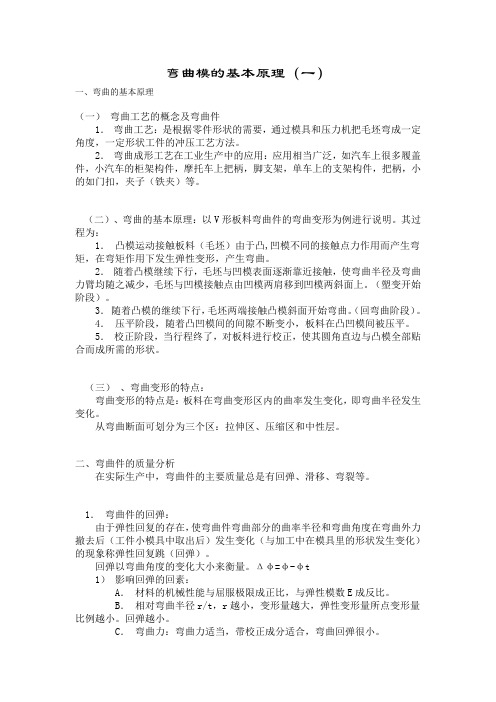
弯曲模的基本原理(一)一、弯曲的基本原理(一)弯曲工艺的概念及弯曲件1.弯曲工艺:是根据零件形状的需要,通过模具和压力机把毛坯弯成一定角度,一定形状工件的冲压工艺方法。
2.弯曲成形工艺在工业生产中的应用:应用相当广泛,如汽车上很多履盖件,小汽车的柜架构件,摩托车上把柄,脚支架,单车上的支架构件,把柄,小的如门扣,夹子(铁夹)等。
(二)、弯曲的基本原理:以V形板料弯曲件的弯曲变形为例进行说明。
其过程为:1.凸模运动接触板料(毛坯)由于凸,凹模不同的接触点力作用而产生弯矩,在弯矩作用下发生弹性变形,产生弯曲。
2.随着凸模继续下行,毛坯与凹模表面逐渐靠近接触,使弯曲半径及弯曲力臂均随之减少,毛坯与凹模接触点由凹模两肩移到凹模两斜面上。
(塑变开始阶段)。
3.随着凸模的继续下行,毛坯两端接触凸模斜面开始弯曲。
(回弯曲阶段)。
4.压平阶段,随着凸凹模间的间隙不断变小,板料在凸凹模间被压平。
5.校正阶段,当行程终了,对板料进行校正,使其圆角直边与凸模全部贴合而成所需的形状。
(三)、弯曲变形的特点:弯曲变形的特点是:板料在弯曲变形区内的曲率发生变化,即弯曲半径发生变化。
从弯曲断面可划分为三个区:拉伸区、压缩区和中性层。
二、弯曲件的质量分析在实际生产中,弯曲件的主要质量总是有回弹、滑移、弯裂等。
1.弯曲件的回弹:由于弹性回复的存在,使弯曲件弯曲部分的曲率半径和弯曲角度在弯曲外力撤去后(工件小模具中取出后)发生变化(与加工中在模具里的形状发生变化)的现象称弹性回复跳(回弹)。
回弹以弯曲角度的变化大小来衡量。
Δφ=φ-φt1)影响回弹的回素:A.材料的机械性能与屈服极限成正比,与弹性模数E成反比。
B.相对弯曲半径r/t,r越小,变形量越大,弹性变形量所点变形量比例越小。
回弹越小。
C.弯曲力:弯曲力适当,带校正成分适合,弯曲回弹很小。
D.磨擦与间隙:磨擦越大,变形区拉应力大,回弹小。
凸、凹模之间隙小,磨擦大,校正力大,回弹小。
第3章弯曲工艺与弯曲模
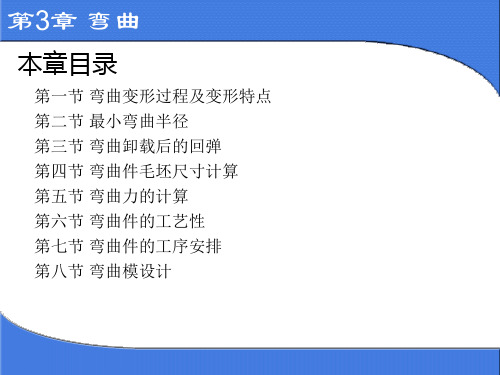
1.V形件弯曲模
图4-39 无压料装置的V形件弯曲模 1—模柄 4 、7 —定位板 2 —上模座 5 —下模座 3 —导柱导套 6 —凹模 8 —凸模
1—顶杆 4 —凸模
有压料装置的V形件弯曲模(avi4-3) 2 —定位钉 3 —模柄 5 —凹模 6 —下模座
图4-40 防止毛坯偏移的措施
图4-41 带顶料及定料销的弯曲模 1—凹模 2 —顶板 3 —定料销 4 —凸凹模 5 —反侧压块
第五节 弯曲力计算
一.校正弯曲时弯曲力计算
F=qA
式中: F—校正弯曲力(N); A— 校正部分投影面积(mm2); q—单位面积上的校正力(MPa), 值可按表3-4选取。 图3-35 校正弯曲示意图
四.压力机公称压力的确定
• 对于自由弯曲
F压机≥ 1.3(F自+Q)
式中 F压机—选用的压力机公称压力(kN); F自—自由弯曲力(kN); Q—有压料或顶件装置的压力(kN).
式中:δ — 伸长率; r — 弯曲件内表面圆角半径(mm); η— 变薄系数; t — 材料厚度(mm); ρ—应变中性层曲率半径(mm) 。
则弯曲半径 r= ρ(1+δ)- ηt 若以断面收缩率Ψ表示变形程度,则Ψ与δ有如下关系: δ= Ψ/(1- Ψ) 根据式(4-15), ρ=(r/t+ η/2)ηβt,当板料宽度大于板料厚度3 倍时,则 ρ=(r/t+ η/2)ηt 将上式与式(4-19)代入式(4-18),化简后得:
3.弯曲件上孔的位置
t < 2mm, l ≥ t; t ≥ 2mm, l ≥ 2t.
图4-33 弯曲件上的孔边距离
4.弯曲件上增添工艺孔和工艺槽
图4-34 防止尖角处撕裂的措施
弯曲工艺与弯曲模

弯曲后断面变化
⒊ 弯曲件中性层位置
在计算弯曲件的毛坯尺 寸时,必须首先确定中性层 的位置,中性层位置可用其 弯曲半径ρ确定,ρ可按以下 经验公式计算:
式中: ρ—中性层弯曲半径,mm; r—内弯曲半径,mm; t—材料厚度,mm; x——中性层位移系数,查表。
中性层位移系数
三、弯曲件展开长度
1.定义: 弯曲件在弯曲之前的展平尺寸。 2.作用:是零件毛坯下料的依据,是加工出合格
零件的基本保证。
3.计算:只需计算中性层展开尺寸即可。
(1)对于圆角半径r>0.5t的弯曲件展开长度 根据弯曲前后中性层尺寸不变的原则计算,
即其展开长度等于所有直线段及弯曲部分中性层 展开长度之和。 例如:
向两侧移动为凸模上行腾出足够空间。
4.帽罩形弯曲模(四角弯曲模 )
(1)帽罩形件一次弯曲模
特点及应用:
外角C处的弯曲线的
位置在弯曲过程中是变化
的,因此,材料在弯曲时
边有变薄现象。
用于工件弯曲高度
不大的场合。
低帽罩形件一次弯曲模
高帽罩形件一次弯曲模 1-凸凹模 2-凹模 3-活动凸模 4-顶杆
式中: FZ —材料在冲压行程结束时的弯曲力,N;
b —弯曲件宽度,mm; r—弯曲件内弯曲半径,mm ;
t—弯曲件厚度,mm;
K—安全系数,一般可取K=1.3;
—材料强度极限,MPa
4. 校正弯曲的弯曲力计算
校正弯曲示意图 当弯曲件在冲压结束时受模具的校正时,弯 曲校正力计算式为:
式中:Fj—弯曲校正力,N A—工件被校正部分的投影面积 mm 2 q—单位校正力,MPa,其数值查表
模具设计基础-第三章 弯曲工艺与弯曲模具设计

V形弯曲板材受力情况
1-凸模 2-凹模
2.弯曲变形过程
自由弯曲 弹性弯曲
校正弯曲 塑性弯曲
弯曲效果:表现为弯曲半径和弯曲中心角的变化(减小)。
3.弯曲变形分析
研究材料的变形,常采用网格法。根据坐标网格的变 化情况来分析弯曲变形时毛坯的变形特点。
• 防止弯裂的措施如下。 • (1) 使用表面质量好的毛坯。 • (2) 采用合理的模具间隙,改善润滑条件,减少弯曲时毛
坯的流动阻力。 • (3) 制件的相对弯曲半径大于最小相对弯曲半径。若不能
满足时,应分两次或多次进行弯曲。 • (4) 对于塑性差或加工硬化较严重的毛坯,先退火后弯曲
。 • (5) 把毛坯有毛刺的一面置于变形区的内侧。
Hale Waihona Puke 2、滑移——指在弯曲过程中,毛坯沿凹模口滑动时由于 两边所承受摩擦阻力不同而出现的毛坯向左或向右移动的现象, 使弯曲件的尺寸精度达不到要求。
形成滑移的主要原因是毛坯沿凹模口滑动时两边所受的摩 擦阻力不相等,如图 所示。其中,图(a)为制件形状不对称而 造成的滑移;图(b)为凹模口两边圆角不相等造成的滑移;图(c) 为制件两边弯曲角不同而造成的滑移。
角度回弹量 Δθ是指模具在闭合状态时工件弯曲角θ 与弯 曲后工件的实际角度 θ0 的差值,即 Δ θ = θ0 − θ
1.影响回弹的主要因素 影响回弹的因素很多,主要有以下方面。 (1)材料的力学性能。屈服极限σs越高,材料在一定变 形程度下,其变形区断面内的应力也越大,因而引起更大 的弹性变形,所以回弹值也大。弹性模量 E 越大,则抵抗 弹性变形的能力越强,所以回弹值越小。 (2)材料的相对弯曲半径 r/t。随着 r/t的减小,塑性变 形成分变大,回弹量降低。
弯曲与弯曲模具设计

二、弯曲件的工艺计算
2.弯曲力的计算
(1)自由弯曲力对于V形件,有
F自
0.6kbt 2 b
rt
对于U形件,有
F自
0.7kbt 2 b
rt
(2)校正弯曲力如果弯曲件在冲压行程结束时受到模具的校正
(见图3-27)
上一页 下一页
第四节 弯曲件的工艺特性及工艺计 算
二、弯曲件的工艺计算
(3)顶件力或压料力
上一页 下一页
第四节 弯曲件的工艺特性及工艺计 算
一、弯曲件的工艺性
(6)增添连接带和定位工艺孔 如图3-22所示。 (7尺寸标注 尺寸标注对弯曲件的工艺性有很大的影响。 如图3-23所示。
上一页 下一页
第四节 弯曲件的工艺特性及工艺计 算
二、弯曲件的工艺计算
1.弯曲件展开长度的确定
第三章 弯曲与弯曲模具设计
第一节 弯曲技术概述 第二节 弯曲变形过程分析 第三节 弯曲件坯料尺寸的计算 第四节 弯曲件的工艺特性及工艺计算 第五节 弯曲件的工序安排 第六节 弯曲模典型结构及结构设计
第一节 弯曲技术概述
弯曲是利用压力使金属板料、管料、棒料或型材在模具中弯 成一定曲率、一定角度和形状的变形工序。弯曲工艺在冲压 生产中占有很大的比例,应用相当广泛,如汽车纵梁、电器 仪表壳体、支架、铰链等,都是用弯曲方法成型的。
所示为V形件弯曲的变形过程。 2.弯曲变形特点 为了分析板料弯曲变形的规律,将试验用的长方形板料的 侧面画成正方形网格,如图3-4(a)所示,然后弯曲,观察其
变形特点,弯曲后情况如图3-4(b)所示。
下一页
第二节 弯曲变形过程分析
一、弯曲的变形特点
(1)变形区主要在弯曲件的圆角部分,圆角区内的正方形网 格变成厂扇形。
弯曲工艺与弯曲模

5.7 弯曲模类型及典型结构
1. V形件弯曲模 这类形状的弯曲件可以用两种方法弯曲: (1)是沿着工件弯曲角的角平分线方向弯曲,称为V
形弯曲; (2)是垂直于工件一条边的方向弯曲,称为L形弯曲;
Y
L形件弯曲模
2、U形件弯曲模
(1)U形弯曲模在一次 弯曲过程中可以形成 两个弯曲角,右图为 U形件弯曲模结构 。
弯曲原理——弯曲变形特点(P83-P84) (重点)
(采用网格法分析弯曲时金属的变形规律)
分析结果: a、弯曲变形主要发生在弯曲圆角区;
弯曲角与弯曲带中心角
b、内层受压变短,外层受拉变长,中层不变; 中性层弯曲半径ρ=r+xt
变形程度的表示方法:
相对弯曲半径 r/t 来表示,其小,则 弯曲程度越大;
当弯曲件的折弯线与板料的纤维方向垂直时,材料具有 较大的伸长变形能力,最小弯曲半径可取较小值;
反之,如果弯曲 件的折弯线平行 于纤维方向,则 最小弯曲半径要 取大值;在双向 弯曲时,应该使 折弯线与材料纤 维方向成一定的 夹角,如图3.8所 示。
图 3.8 弯曲方向对弯曲半径的影响
(3)板宽
πα2 180
(r2
xt)
πα3 180
(r3
xt)
弯曲半径r<0.5t: 按体积不变原则进行计算。
注意事项:
∵弯曲件展开长度公式为经验公式
或
中t的公差、r、α、x的微小误差
∴展开长度计算数据不准确
∴弯曲模的制作顺序:
先作弯曲模→通过弯曲件实际尺寸调整展 开长度数据→确定展开毛坯准确落料刃口尺 寸→制作落料模。
③ 凹模刃口处的圆角 半径不等,圆角半径 小的摩擦力大,弯曲 件向圆角半径小的一 边滑移,如图3.16所 示。
弯曲工艺及弯曲件的结构工艺性

四. 弯曲件的结构工艺性
弯曲件尺寸标注
应有利于减少冲压工序
弯曲件精度
一般不高于IT13级,角度公差大于±15′。
一. 弯曲工艺
弯曲概念
将板料、型材、管材或棒料等按设计要求弯成一定 的角度和一定的曲率,形成所需形状零件的冲压工序。
一. 弯曲工艺
弯曲分类
➢压弯 ➢折弯 ➢滚弯 ➢拉弯
二. 弯曲变形过程
弯曲变形过程:以简单V形件为例
二. 弯曲变形过程
弯曲工序分类
➢自由弯曲
弯曲结束时,凸模、凹模、毛坯三 者相吻合,凸模不再下压。
四. 弯曲件的结构工艺性
当直边高度H<2t时: ①加工艺余料
②在弯曲内R处压凹坑
四. 弯曲件的结构工艺性
弯曲件的孔边距
➢使孔处于弯曲变形区之外: 先冲孔后弯曲
要求:当t<2mm时,s≥t; 当t≥2mm时,s≥2t。
➢不满足上述要求时:必须先弯曲,再冲孔。
四. 弯曲件的结构工艺性
弯曲线位置
弯曲线不应位于弯曲件宽度的突变处,以免发 生撕裂现象。
四. 弯曲件的结构工艺性
纠正措施
①将弯曲线移动一定距离,避开宽度突变处 。
四. 弯曲件的结构工艺性
②事先冲出止裂孔或止裂槽
并满足b≥t,h=t+r+b/2的条件
四. 弯曲件的结构工艺性
定位工艺孔
采用孔定位能有效防止毛坯在弯曲中产生偏移,有利 于保证制件质量。如果毛坯上没有适合于定位的孔,最 好能增添定位用的工艺孔。
最适宜弯曲的r18Ni9Ti不锈钢等。
较硬材料弯曲时,需增加工序改变性能: ①先退火处理后弯曲,最后淬火。 ②加热后弯曲。
四. 弯曲件的结构工艺性
形状尺寸
弯曲件的工艺性

弯曲件的工艺性一.弯曲件的结构与尺寸1.弯曲件的形状由零件图可知该弯曲件是左右对称的且在变形区附近没有缺口,所以不需要在连接带,但是最好在配料上预先增添定位工艺孔。
2.弯曲件的相对弯曲半径由零件图可知该弯曲件的相对弯曲半径r/t=1.5/1.5=1,所以该弯曲件受回弹的影响不大,精度易保证。
3.弯曲件的弯边高度由零件图可知该弯曲件的弯边高度h>r+2t。
所以零件不需要改变。
4.弯曲件的孔边距离由零件图可知t=1.5,所以孔边距离L>t就行了。
而该零件的孔边距离L=2.5>1.5,无需采取措施来保证孔不产生变形。
5.避免弯曲根部开裂为了避免弯曲根部撕裂,应该使不弯曲部分退出万曲线外,即b≥r,由零件图可知满足条件。
6.弯曲件的尺寸标注因为弯曲件的尺寸标注不同会影响冲压工序安排,因为该零件的孔位置精度不受坏料的展开长度影响,所以采用a类标注法标注。
二.弯曲件的精度弯曲件的精度受坏料定位、偏移、回弹、翘曲等因素影响,弯曲的工序数目越多,精度也越低。
对精度的要求合理一般都在IT13级以下角度公差大于15′。
结合零件图可以知道该弯曲件的精度满足条件。
三.弯曲件的材料由零件图可知该弯曲件的材料为08冷轧钢板。
弯曲工艺的方案设计一.弯曲工艺类型1.确定工艺类型由零件图可知,该零件需要先冲裁,再进行弯曲才能够形成。
二.弯曲工艺次数因为弯曲的次数越多,精度就越低,而且对模具的设计要求和生产要求都比较高,所以弯曲的次数尽量的少。
因为该零件可以一次弯曲就完成,所以我选择该弯曲件的弯曲次数为一次。
三.弯曲工艺顺序由零件图可知该零件应该先冲裁下料,然后可以冲孔,最后再弯曲成型。
弯曲件的展开尺寸计算一.弯曲中性层位置的确定由教材P215可知中性层的位置以曲率ρ表示,ρ=r+xt查表5-8可知ρ=1.5+1.5×0.32=1.98二.弯曲件的展开尺寸计算查教材P216表5-9结合零件图,结合前面工艺性次数分析可知Lz=l1+2l2+3l3+t=25+2×9+3×30+1.5=134.5弯曲力的计算一.自由弯曲的弯曲力由零件图可知该零件的材料的坏料不厚,万曲线较长,弯曲半径相对较大,材料强度较大。
模具设计基础-第三章 弯曲工艺与弯曲模具设计ppt课件

自由弯曲 弹性弯曲
校正弯曲 塑性弯曲
弯曲效果:表现为弯曲半径和弯曲中心角的变化(具设计
3.弯曲变形分析 研究材料的变形,常采用网格法。根据坐标网格的变
化情况来分析弯曲变形时毛坯的变形特点。
模具设计基础 第三章 弯曲工艺与弯曲模具设计
(1)弯曲变形区的位置 通过对网格的观察,可见弯曲圆角部分的网格发生了显 著的变化,原来的正方形网格变成了扇形。靠近圆角部分的 直边有少量变形,而其余直边部分的网格仍保持原状,没有 变形。说明弯曲变形的区域主要发生在弯曲圆角区,即弯曲 带中心角α 范围内。
模具设计基础
—弯曲工艺与弯曲模具设计
.
模具设计基础 第三章 弯曲工艺与弯曲模具设计
了解弯曲工艺及弯曲件的结构工艺性分析,理解弯 曲变形过程分析,理解弯曲件的质量问题及防止措施, 掌握弯曲工艺设计和弯曲模具典型结构组成及工作过程 分析。
应该具备的能力:具备弯曲件的工艺性分析、工艺 计算和典型结构选择的基本能力,初步具备根据弯曲件 质量问题正确分析原因并给出防止措施的能力。
模具设计基础 第三章 弯曲工艺与弯曲模具设计
二、弯曲件回弹
材料在弯曲过程中,伴随着塑性变形总存在着弹性变形, 弯曲力消失后,塑性变形部分保留下来,而弹性变形部分要恢 复,从而使弯曲件与弯曲模的形状并不完全一致,这种现象称 为弯曲件的回弹。回弹是所有弯曲件都存在的问题,只不过是 回弹量大小而已。回弹量的大小通常用角度回弹量 Δθ 和曲率 回弹量 Δ r 来表示。
模具设计基础 第三章 弯曲工艺与弯曲模具设计
弯曲件在生产生活中经常见到,如下图所示的电器元 件和弯管均为弯曲件。这些产品的共同特点是:不管是板 类件还是管形件,都有一定的弯曲角度。另外,很多弯曲 件上有孔,是先冲孔还是先弯曲,如何判断并制定加工的 先后顺序呢?
第三章 弯曲工艺及弯曲模总结

3.1 弯曲变形3.2 最小相对弯曲半径3.3 弯曲件的回弹3.4 弯曲件的工艺性3.5 弯曲件的展开尺寸计算353.6弯曲力的计算3.7 弯曲模工作部分设计373.8 凸、凹模工作部分的尺寸与公差3.9 弯曲模的典型结构及弯曲模具中主要零部件制造工艺过程示例弯曲:在冲压力的作用下,把平板坯料弯折成一定角度和形状的种塑性成型工艺。
定角度和形状的一种分类:压弯、折弯、扭弯、滚弯和拉弯。
弯曲模:弯曲工艺使用的冲模。
压弯的典型形状典型的压弯工件第一节弯曲变形一、板料的弯曲过程、板料的弯曲过程在弯曲过程中,板料的弯曲半径123......n r r r r ,,,,和支点距离随凸模的下行逐渐减小,12......n l l l ,,,随凸模的下行逐渐减小而弯曲终了时,板料与凸模完全贴合凸、凹模完全贴合。
第一节弯曲变形通过网格试验观察弯曲变形特点。
二、弯曲变形的特点①弯曲件的圆角部分是弯曲变形的主要变形区弯曲变形有以下几个特点:变形区的材料外侧伸长,内侧缩短,中性层长度不变。
②弯曲变形区的应变中性层应变中性层是指在变形前后金属纤维的长度没有发生改变的那一层金属纤维。
③变形区材料厚度变薄的现象变形程度愈大,变薄现象愈严重,变薄后的厚度为。
④变形区横截面的变化变形区横断面形状尺寸发生改变称为畸变主要影响因素为板料的相1t t η=(宽板) :横断面几乎不变;变形区横断面形状尺寸发生改变称为畸变。
主要影响因素为板料的相对宽度。
3B t>(窄板) :断面变成了内宽外窄的扇形。
3B t <第一节弯曲变形应变状态应力状态三、变形区和应力应变状态εσ长度内区压应变,外区拉应变,内区压应力,外区拉应力,绝对值最大绝对值最大厚度内区拉应变,外区压应变,变形区引起压应力,由表及里递t σ变变与符号相反表面,由表及里递增窄板内区拉伸窄板θε0t σ=宽度窄板:内区拉伸,外区压缩窄板:宽板:内区压应力,0ε≈0ϕσ=宽板:外区拉应力ϕ第一节弯曲变形三、变形区和应力应变状态第二节最小相对弯曲半径设中性层半径为,弯曲中心角为,则最外层金属(半径为的ρα为R)的伸长率为δ外()()aa oo R R ραρ−−−===oo δραρ外另设中性层位置在半径为处,且弯曲后厚度保持不变,则,故有2r t ρ=+R r t =+将两式联立则有()(2)21=r t r t t rδ+−+==外将两式联立,则有2221r t t r t +++第二节最小相对弯曲半径影响最小相对弯曲半径的因素主要有以下几方面:材料的塑性及热处理状态板料的表面和侧面质量弯曲方向弯曲中心角各种材料在不同状态下的最小相对弯曲半径的数值可参见表33。
培训单元2弯曲工艺和弯曲模结构.

图 1.2 V 形件弯曲变形过程
3.弯曲变形特点(1/3)
图 1.3 弯曲前后网格变化
3.弯曲变形特点(2/3)
图 1.4 弯曲角与弯曲带中心角
图 1.5 中性层位置的确定
3.弯曲变形特点(3/3)
图 1.6 板料宽度方向变形情况
4.弯曲件的结构工艺性
• ① 弯曲件的形状
图 1.7 弯曲件的对称性
图 2.10 大圆两次弯曲模 1—凸模;2—凹模;3—定位板
5.圆形件弯曲模
图 2.11 大圆一次弯曲模 1—弹顶装置;2—转动凹模;3—凸模;4—支撑
5.圆形件弯曲模
图 2.12 小圆两次弯曲成形
图 2.6 两次弯曲成形
3.帽形件弯曲模
图 2.6 两次弯曲成形
3.帽形件弯曲模
图 2.8 复合弯曲模一次弯曲成形 1—凸凹模;2—活动凸模;3—凹模;4—顶板
4.Z 形件弯曲模
图 2.9 Z 形件弯曲模 1—顶件板;2—托板;3—橡胶;4—压柱;5—上模座;6—凹模;7—凸模;8— 下模板
5.圆形件弯曲模
2.U 形件弯曲模
图 2.4 使用回转凹模的U 形件弯曲模 1—凸模;2—定位板;3—弹簧;4—回转凹模;5—限位钉
2.U 形件弯曲模
图 2.5 使用斜楔结构的U形件弯曲模 1—斜楔;2—凸模支杆;3,9—弹簧;4—上模座;5—凸模;6—定位销;7, 8—活动凹模;10—下模座;11—滚柱
3.帽形件弯曲模
1.V 形件弯曲模
图 2.1 V 形件弯曲模 1—顶杆;2—定位钉;3—模柄;4—凸模;5—凹模;6—下模
1.L 形弯曲模
图 2.2 L 形件弯曲模 1—凸模;2—凹模;3—定位销;4—压料板;5—挡块;6—定位板
第3章 弯曲工艺与弯曲模具
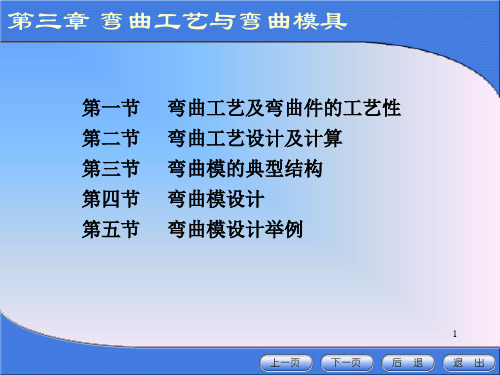
另一种克服回弹的有效方法:采用 摆动式凹模 ,而凸模侧 壁应有补偿回弹角β ;当材料厚度负偏差较大时,可设计成凸、 凹模间隙可调的弯曲模。
在弯曲件直边端部纵向加压。 用橡胶或聚氨酯代替刚性金属凹模能减小回弹。
23
弯曲时的偏移
板料在弯曲过程中沿凹模圆角滑移时,会受到凹模圆角 处摩擦阻力的作用。当板料各边所受的摩擦阻力不等时,有 可能使毛坯在弯曲过程中沿工件的长度方向产生移动,使工 件两直边的高度不符合图样的要求,这种现象称为偏移。
第二节 弯曲工艺设计及计算
一、弯曲变形过程
V形件弯曲是最基本的弯曲变形。
弯曲变形过程
r0 r1 r2 r
l0 l1 l2 lK
弯曲结果:表现为弯曲半径和弯曲力臂的变化(减小)。
弯曲半径逐渐减小:弯曲变形部分的变形程度逐渐增加。 弯曲力臂逐渐减小:弯曲变形过程中板料与凹模之间有相对滑移。
铰支板弯曲模
37
二、连续模
对于批量大、尺寸较小的弯曲件,为了提高生产率,操作 安全,保证产品质量等,可以采用连续弯曲模进行多工位的冲 裁、压弯、切断连续工艺成形。
三、复合模
对于尺寸不大的弯曲件,还可以采用复合模,即在压力 机一次行程内,在模具同一位置上完成落料、弯曲、冲孔等 几种不同工序。
两次弯曲复合的弯曲模
38
第四节 弯曲模工作部分结构参数的确定
一、弯曲凸模圆角半径
r rmin r rmin
r凸=r
r凸=rmin
当r/t>10时,则应考虑回弹,将凸模圆角半径r凸 加以修正。
39
二、凹模圆角半径
凹模圆角半径不能过小,否则弯矩的力臂减小,毛坯沿凹 模圆角滑进时阻力增大,从耐增加弯曲力,并使毛坯表面擦伤。
弯曲件的工艺性

弯曲件的工艺性弯曲件是一种常见的金属加工零部件,广泛应用于汽车、航空航天、机械制造等领域。
其工艺性包括材料选型、工艺流程、设备选择、工艺参数控制等多个方面。
下面将就弯曲件的工艺性进行详细介绍。
首先是材料选型。
弯曲件通常采用金属材料,如碳钢、不锈钢、铝合金等。
不同材料具有不同的机械性能和加工特性,对于弯曲件的加工而言,需要根据实际工艺要求和使用环境选择合适的材料。
比如在需要弯曲件具有良好的强度和耐腐蚀性能时,通常选择不锈钢或铝合金材料;在需要弯曲件具有较高刚度和耐磨性能时,通常选择碳钢材料。
在进行材料选型时,还需要考虑材料的可焊性、可切削性等加工性能,以确保能够满足弯曲件的加工要求。
其次是工艺流程。
弯曲件的加工通常包括剪切、冲压、弯曲等工艺步骤。
在进行工艺流程规划时,需要考虑弯曲件的结构形状、尺寸精度、表面质量等要求,合理确定各个工序的顺序和参数。
比如在进行弯曲工艺时,通常需要考虑弯曲角度、弯曲半径、弯曲顺序等因素,以确保弯曲件能够满足设计要求。
此外,在工艺流程中还需要考虑材料的变形性能、回弹性能等因素,以避免产生裂纹、变形等不良现象。
再次是设备选择。
弯曲件的加工通常采用液压机、数控折弯机、卷板机等设备进行。
对于不同形状和尺寸的弯曲件,需要选择合适的设备进行加工。
比如在进行复杂曲线的弯曲时,通常选择数控折弯机进行加工;在进行长尺寸的弯曲件加工时,通常选择卷板机进行加工。
在进行设备选择时,还需要考虑设备的加工精度、稳定性、安全性等因素,以确保能够满足弯曲件的加工要求。
最后是工艺参数控制。
在进行弯曲件的加工过程中,需要严格控制各项工艺参数,包括温度、压力、速度、润滑剂等。
比如在进行弯曲工艺时,需要控制弯曲角度、弯曲速度、弯曲压力等参数,以确保弯曲件能够达到设计要求。
同时还需要对材料的预热、冷却等过程进行控制,以避免产生内应力、变形等问题。
在进行工艺参数控制时,通常采用数控技术进行,以提高加工精度和稳定性。
- 1、下载文档前请自行甄别文档内容的完整性,平台不提供额外的编辑、内容补充、找答案等附加服务。
- 2、"仅部分预览"的文档,不可在线预览部分如存在完整性等问题,可反馈申请退款(可完整预览的文档不适用该条件!)。
- 3、如文档侵犯您的权益,请联系客服反馈,我们会尽快为您处理(人工客服工作时间:9:00-18:30)。
当弯曲中,凸模、凹模、毛坯三 者相吻合后,凸模继续下压,使毛坯 产生进一步的塑性变形。
三. 弯曲变形分析
方法:网格法
变形情况
弯曲变形区:圆弧区
长度变化
外R处:伸长 内r处:缩短 内有一层中性层:长度不变
三. 弯曲变形分析
中性层长度计算公式
r xt
式中:ρ——中性层弯曲半径,mm; r——弯曲半径,mm; t——材料厚度,mm; x——中性层位移系数。
三. 弯曲变形分析
; 外R拉长减薄
∴变形区内厚度t↓
三. 弯曲变形分析
宽度变化
窄板(毛坯宽度与厚度之比b/t≤3)弯曲时:内宽外窄
宽板(毛坯宽度与厚度之比b/t>3)弯曲时:变形不明显
四. 弯曲件的结构工艺性
材料要求: 足够的塑性,较低的屈服极限
四. 弯曲件的结构工艺性
纠正措施
①将弯曲线移动一定距离,避开宽度突变处 。
四. 弯曲件的结构工艺性
②事先冲出止裂孔或止裂槽
并满足b≥t,h=t+r+b/2的条件
四. 弯曲件的结构工艺性
定位工艺孔
采用孔定位能有效防止毛坯在弯曲中产生偏移,有利 于保证制件质量。如果毛坯上没有适合于定位的孔,最 好能增添定位用的工艺孔。
四. 弯曲件的结构工艺性
当直边高度H<2t时: ①加工艺余料
②在弯曲内R处压凹坑
四. 弯曲件的结构工艺性
弯曲件的孔边距
使孔处于弯曲变形区之外:
先冲孔后弯曲
要求:当t<2mm时,s≥t; 当t≥2mm时,s≥2t。
不满足上述要求时:必须先弯曲,再冲孔。
四. 弯曲件的结构工艺性
弯曲线位置
弯曲线不应位于弯曲件宽度的突变处,以免发 生撕裂现象。
四. 弯曲件的结构工艺性
弯曲件尺寸标注
应有利于减少冲压工序
弯曲件精度
一般不高于IT13级,角度公差大于±15′。
一. 弯曲工艺
弯曲概念
将板料、型材、管材或棒料等按设计要求弯成一定 的角度和一定的曲率,形成所需形状零件的冲压工序。
一. 弯曲工艺
弯曲分类
压弯
折弯
滚弯 拉弯
二. 弯曲变形过程
弯曲变形过程:以简单V形件为例
二. 弯曲变形过程
弯曲工序分类
自由弯曲
弯曲结束时,凸模、凹模、毛坯三 者相吻合,凸模不再下压。
弯曲件弯曲部分的内角半径,用r表示。
最小弯曲半径
弯曲件弯曲时外R处不弯裂的最小内角半径,用rmin表示。
四. 弯曲件的结构工艺性
最小弯曲半径的经验取值
四. 弯曲件的结构工艺性
四. 弯曲件的结构工艺性
弯曲件的直边高度
弯曲直边高度
指弯曲件非变形区的直边的长度,用H表示。
直边高度的要求
H≥2t
最适宜弯曲的材料:
低碳钢(08、10)、紫铜、黄铜、软 铝、1Cr18Ni9Ti不锈钢等。
较硬材料弯曲时,需增加工序改变性能:
①先退火处理后弯曲,最后淬火。 ②加热后弯曲。
四. 弯曲件的结构工艺性
形状尺寸
弯曲件的形状:
弯曲件形状对称,对应r 相等
四. 弯曲件的结构工艺性
最小弯曲半径
弯曲半径