第六章典型零件加工与加工方法讲述案例
汽车机械制造中的零部件加工与装配案例分析
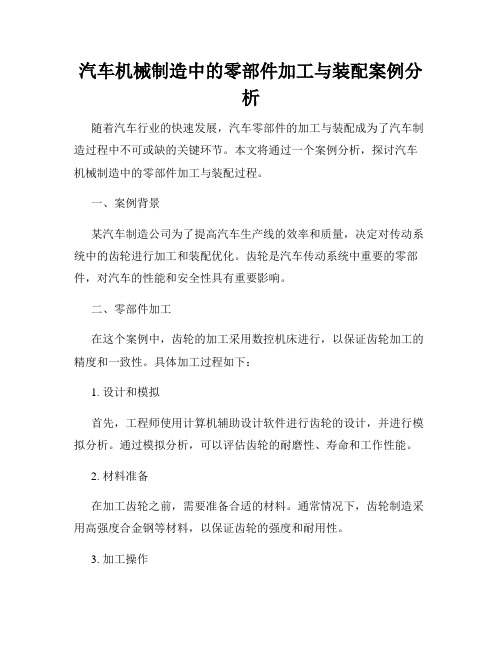
汽车机械制造中的零部件加工与装配案例分析随着汽车行业的快速发展,汽车零部件的加工与装配成为了汽车制造过程中不可或缺的关键环节。
本文将通过一个案例分析,探讨汽车机械制造中的零部件加工与装配过程。
一、案例背景某汽车制造公司为了提高汽车生产线的效率和质量,决定对传动系统中的齿轮进行加工和装配优化。
齿轮是汽车传动系统中重要的零部件,对汽车的性能和安全性具有重要影响。
二、零部件加工在这个案例中,齿轮的加工采用数控机床进行,以保证齿轮加工的精度和一致性。
具体加工过程如下:1. 设计和模拟首先,工程师使用计算机辅助设计软件进行齿轮的设计,并进行模拟分析。
通过模拟分析,可以评估齿轮的耐磨性、寿命和工作性能。
2. 材料准备在加工齿轮之前,需要准备合适的材料。
通常情况下,齿轮制造采用高强度合金钢等材料,以保证齿轮的强度和耐用性。
3. 加工操作加工齿轮的过程中,使用数控机床对材料进行切削加工。
根据设计要求,机床会自动控制加工工具的运动,将齿轮的外径、齿数等参数加工到设计要求的精度。
4. 表面处理加工完成后,齿轮的表面可能存在一些不平整和粗糙。
为了提高齿轮的耐磨性和工作平稳性,需要进行表面处理。
常见的表面处理方法包括热处理、渗碳等。
三、零部件装配在齿轮加工完成后,需要将其与其他零部件进行装配,形成完整的传动系统。
零部件装配的过程包括以下几个步骤:1. 零部件检查在装配之前,需要对每个齿轮和其他零部件进行检查,确保其质量和尺寸符合要求。
如果发现问题,需要及时修复或更换。
2. 零部件组装按照设计要求,将齿轮和其他零部件进行组装。
在组装过程中,需要根据装配图纸和工艺要求进行操作,确保每个零部件的正确位置和安装方式。
3. 调试和测试装配完成后,需要进行传动系统的调试和测试。
通过转动齿轮,检查传动的效果和顺畅度。
如果出现问题,需要及时修正,直到传动系统工作正常。
四、案例总结通过这个案例的分析,可以看出在汽车机械制造中,零部件的加工和装配对汽车的质量和性能有着决定性的影响。
典型零件加工与加工方法

对精加工前的各个表面进行加工,为精加工做好准备。
03
修正基准,确保精加工的准确性。
精加工
对零件进行最终加工,使其达到要求的尺寸、形 状和表面质量。 对重要表面进行精加工,确保其精度和光洁度。
对其他次要表面进行修整,使其符合要求。
表面处理
1
对零件表面进行涂装、喷塑、电镀等处理,以提 高其耐腐蚀性、美观性和功能性。
02 典型零件的加工方法
车削加工
01
02
03
定义
车削加工是利用车床来对 工件进行旋转切削加工的 方法。
应用
主要用于加工圆柱形、圆 锥形等回转体零件,如轴 类、盘类零件等。
特点
加工精度高,表面质量好, 生产效率高。
铣削加工
定义
铣削加工是利用铣床对工件进行切削加工的方法。
应用
主要用于加工平面、沟槽、齿轮、齿条等复杂形 状的零件。
激光加工技术
利用激光的高能量密度 特点,对零件进行快速、 精确的切割、打孔、焊 接等加工,提高加工效 率和精度。
超声波加工技术
利用超声波的振动和冲 击作用,对硬脆材料进 行高效磨削和抛光,特 别适合于加工复杂形状 的零件。
新型加工材料的研发与应用
新材料如碳纤维、钛合金等具有轻质、 高强度等特点,能够提高零件的性能 和减轻重量,为航空、汽车等产业的 发展提供有力支持。
2
根据需要选择合适的表面处理方法,如喷漆、镀 铬、渗碳等。
3
对表面处理后的零件进行质量检查和验收,确保 其符合要求。
04 典型零件的质量控制
加工精度控制
尺寸精度控制
通过合理的加工工艺和刀具选择,确保零件的尺寸精度达到要求。
形位精度控制
数控机床加工工艺第6章数控铣床加工工艺PPT课件
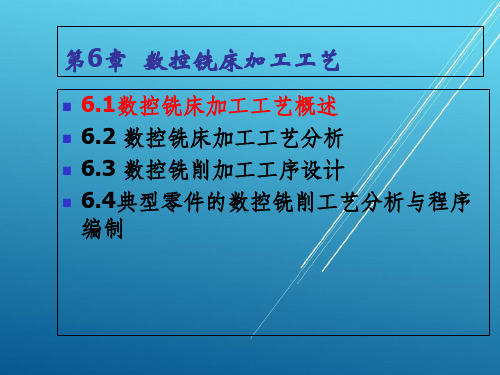
(2)零件尺寸所要求的加工精度、尺寸公差是否都可 以得到保证?
(3)内槽及缘板之间的内转接圆弧是否过小?
(4)零件铣削面的槽底圆角或腹板与缘板相交处的圆 角半径r是否太大?
(5)零件图中各加工面的凹圆弧(R与r)是否过于零乱, 是否可以统一?
(6)零件上有无统一基准以保证两次装夹加工后其相 对位置的正确性?
(3)零件铣槽底平面时,槽底圆角半径r不要
过大。 (4)应采用统一的基准定位。在有关的铣削件
的结构工艺性实例见表6-1。
(a) R较小
(b) R较大
图6-11 内槽结构工艺性对比
(a) r较小
(b) r较大
图6-12 零件槽底平面圆弧对铣削工艺的影响
3.零件毛坯的工艺性分析
(1)毛坯应有充分、稳定的加工余量。 经验表明,数控铣削中最难保证的是加工 面与非加工面之间的尺寸,在零件图样注 明的非加工面处也增加适当的余量。
(2)平面加工方法的选择 在数控铣床上加工平面主要采用端铣 刀和立铣刀加工。粗铣的尺寸精度和表面粗糙度一般可达
IT11~IT13,Ra6.3~25;精铣的尺寸精度和表面精糙度一 般可达IT8~IT10,Ra1.6~6.3。
(3)平面轮廓加工方法的选择通常采用3坐标数控铣床进行两轴 半坐标加工。
(4)固定斜角平面加工方法的选择 固定斜角平面是与水平成成 一固定夹角的斜面,常用的加工方法如下:
1.加工方法的选择
对于数控铣床,应重点考虑几个方面:能保证零件的加工精 度和表面粗糙度的要求;使走刀路线最短,既可简化程序段, 又可减少刀具空行程时间,提高加工效率;应使数值计算简 单,程序段数量少,以减少编程工作量。
(1)内孔表面加工方法的选择
在数控铣床上加工内孔表面加工方法主要有钻孔、扩孔、铰 孔、镗孔和攻丝等,应根据被加工孔的加工要求、尺寸、具 体生产条件、批量的大小及毛坯上有无预制孔等情况合理选 用。
零件的加工方案和实例
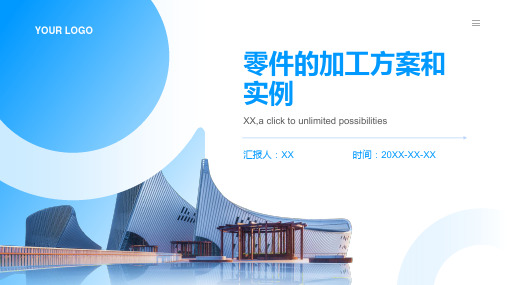
零件的分类与 包装:根据检 测结果,将零 件进行分类、
标识和包装
质量追溯:建 立质量追溯体 系,记录零件 加工过程中的 关键信息,便 于问题追溯和
解决
质量检测与检验
零件加工过程中 的质量检测
零件加工完成后 的质量检验
质量检测与检验 的方法和工具
质量检测与检验 的标准和要求
XX
THANK YOU
加工设备的确定
根据零件的尺寸和精度要求选择合适的加工设备 考虑加工设备的生产效率和加工成本 确保加工设备能够满足零件的加工工艺要求 考虑加工设备的维护和保养成本
加工参数的设定
切削速度:根据零件材料和刀具 材料选择合适的切削速度
切削深度:根据零件的厚度和刀 具的刚度确定合理的切削深度
添加标题
添加标题
汇报人:XX
汇报时间:20XX/01/01
实例二:盘类零件的加工
零件类型:盘 类零件
加工工艺:车 削、铣削、磨
削等
加工设备:车 床、铣床、磨
床等
加工实例:介 绍具体的盘类 零件加工流程
和工艺要求
实例三:箱体类零件的加工
零件类型:箱体 类零件
加工工艺:采用 铣削、钻孔、攻 丝等加工工艺
加工设备:数控 铣床、钻床、攻 丝机等
加工流程:下料、 粗加工、半精加 工、精加工、检 验
热处理问题
零件热处理变形
零件热处理硬度不足
零件热处理开裂 零件热处理表面质量差
PART 5
零件加工的质量控制
加工前的质量控制
零件加工前的质量策划
零件图纸的审核与工艺性 分析
材料的质量控制和检验
加工设备的选择与维护保 养
加工中的质量控制
零件的加工方案和实例
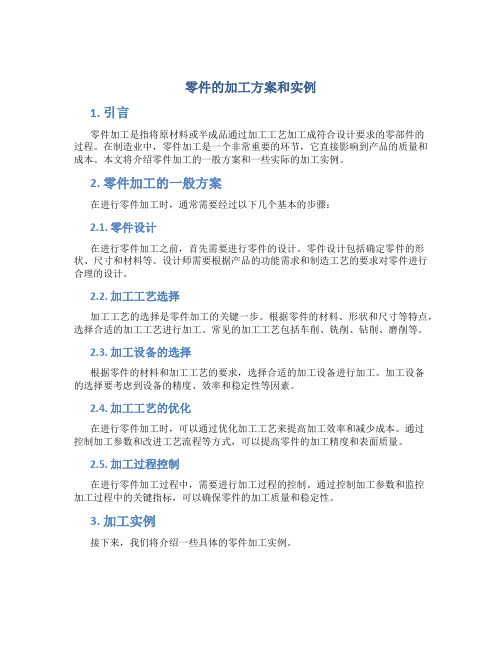
零件的加工方案和实例1. 引言零件加工是指将原材料或半成品通过加工工艺加工成符合设计要求的零部件的过程。
在制造业中,零件加工是一个非常重要的环节,它直接影响到产品的质量和成本。
本文将介绍零件加工的一般方案和一些实际的加工实例。
2. 零件加工的一般方案在进行零件加工时,通常需要经过以下几个基本的步骤:2.1. 零件设计在进行零件加工之前,首先需要进行零件的设计。
零件设计包括确定零件的形状、尺寸和材料等。
设计师需要根据产品的功能需求和制造工艺的要求对零件进行合理的设计。
2.2. 加工工艺选择加工工艺的选择是零件加工的关键一步。
根据零件的材料、形状和尺寸等特点,选择合适的加工工艺进行加工。
常见的加工工艺包括车削、铣削、钻削、磨削等。
2.3. 加工设备的选择根据零件的材料和加工工艺的要求,选择合适的加工设备进行加工。
加工设备的选择要考虑到设备的精度、效率和稳定性等因素。
2.4. 加工工艺的优化在进行零件加工时,可以通过优化加工工艺来提高加工效率和减少成本。
通过控制加工参数和改进工艺流程等方式,可以提高零件的加工精度和表面质量。
2.5. 加工过程控制在进行零件加工过程中,需要进行加工过程的控制。
通过控制加工参数和监控加工过程中的关键指标,可以确保零件的加工质量和稳定性。
3. 加工实例接下来,我们将介绍一些具体的零件加工实例。
3.1. 零件加工实例 1零件名称:齿轮材料:45# 钢加工工艺:车削、齿轮铣削加工设备:车床、铣床加工步骤: - 切削车床上按照齿轮外形进行车削; - 使用铣床对齿轮进行齿轮铣削。
3.2. 零件加工实例 2零件名称:螺栓材料:碳钢加工工艺:车削、螺纹切削加工设备:车床加工步骤:- 使用车床对螺栓进行车削;- 使用螺纹刀具对螺栓进行螺纹切削。
3.3. 零件加工实例 3零件名称:薄壁板材料:不锈钢加工工艺:激光切割、折弯加工设备:激光切割机、折弯机加工步骤: - 使用激光切割机对薄壁板进行切割; - 使用折弯机对薄壁板进行折弯成指定形状。
典型零件的机械加工工艺实例分析

第4章典型零件的机械加工工艺分析本章要点本章介绍典型零件的机械加工工艺规程制订过程及分析,主要内容如下:1.介绍机械加工工艺规程制订的原则与步骤。
2.以轴类、箱体类、拨动杆零件为例,分析零件机械加工工艺规程制订的全过程。
本章要求:通过典型零件机械加工工艺规程制订的分析,能够掌握机械加工工艺规程制订的原则和方法,能制订给定零件的机械加工工艺规程。
§4.1 机械加工工艺规程的制订原则与步骤§4.1.1机械加工工艺规程的制订原则机械加工工艺规程的制订原则是优质、高产、低成本,即在保证产品质量前提下,能尽量提高劳动生产率和降低成本。
在制订工艺规程时应注意以下问题:1.技术上的先进性在制订机械加工工艺规程时,应在充分利用本企业现有生产条件的基础上,尽可能采用国内、外先进工艺技术和经验,并保证良好的劳动条件。
2.经济上的合理性在规定的生产纲领和生产批量下,可能会出现几种能保证零件技术要求的工艺方案,此时应通过核算或相互对比,一般要求工艺成本最低。
充分利用现有生产条件,少花钱、多办事。
3.有良好的劳动条件在制订工艺方案上要注意采取机械化或自动化的措施,尽量减轻工人的劳动强度,保障生产安全、创造良好、文明的劳动条件。
由于工艺规程是直接指导生产和操作的重要技术文件,所以工艺规程还应正确、完整、统一和清晰。
所用术语、符号、计量单位、编号都要符合相应标准。
必须可靠地保证零件图上技术要求的实现。
在制订机械加工工艺规程时,如果发现零件图某一技术要求规定得不适当,只能向有关部门提出建议,不得擅自修改零件图或不按零件图去做。
§4.1.2 制订机械加工工艺规程的内容和步骤1.计算零件年生产纲领,确定生产类型。
2.对零件进行工艺分析在对零件的加工工艺规程进行制订之前,应首先对零件进行工艺分析。
其主要内容包括:(1)分析零件的作用及零件图上的技术要求。
(2)分析零件主要加工表面的尺寸、形状及位置精度、表面粗糙度以及设计基准等;(3)分析零件的材质、热处理及机械加工的工艺性。
零件的加工方案和实例

公差等级 IT13IT11 IT10IT9 IT8IT7 IT7IT6
IT13IT10 IT9IT8 IT8IT7
IT7IT6
IT7IT6
3. 孔的加工方案
表面粗糙度
加工方案
适用范围
5012.5 6.33.2 6.33.2 0.40.2
12.56.3 3.21.6 1.60.8
0.80.4
0.20.1
工序:3 名称:热处理 设备: 工序内容: 调质 HB235
工序:4 名称:半精车 设备:普通车床 工序内容: 1.精车 18.5 端面,修整中心孔; 2.精车另一端面,至长 143,
钻 M10 螺纹底孔 8.5 25 ,孔口倒角 60 ;
3.半精车一端外圆至
24
.4
0.1 0
;
4.半
精
车
另
一
端
外
(3) 锯齿形螺纹:其牙形为锯齿形,代号为B。 它只用于承受单向压力,由于它的传动效率 及强度比梯形螺纹高,常用于螺旋压力机及 水压机等单向受力机构。
5.1 螺纹的种类和用途
(4)模数螺纹:即蜗杆蜗轮螺纹,其牙形角为40º, 它具有传动比大、结构紧凑、传动平稳、自锁性 能好等特点,主要用于减速装置。
(1) 梯形螺纹:牙形角为30º,牙形为等腰梯形, 代号为Tr,它是传动螺纹的主要形式,如机床丝 杠等。
5.1 螺纹的种类和用途
(2)矩形螺纹:主要用于力的传递,其特点是传动 效率较其它螺纹高,但强度较低、对中准确性较差, 特别是磨损后轴向和径向的间隙较大,因此应用受 到了一定的限制。
5.1 螺纹的种类和用途
6.30.8
加工方案 粗车
粗车—半精车—精车
适用范围
中职课程《机械加工技术》精品教学设计之典型零件的加工工艺分析

项目六典型零件的加工工艺分析一、教学目标任务1轴类零件的加工工艺分析1.掌握轴类零件的加工工艺制定方法。
2.了解轴类零件的结构特点。
任务2套筒类零件的加工工艺分析1.掌握轴承套零件的加工工艺分析方法。
2.掌握液压缸零件的加工工艺分析方法。
3.了解套筒类零件加工中常见的工艺问题。
任务3箱体类零件的加工工艺分析1.掌握箱体零件的加工工艺分析,重点注意小批量与大批量的加工工艺的区别。
2.熟悉制定箱体工艺过程中应遵守的原则。
3.了解定位基准的选择方法。
任务4典型齿轮的加工工艺分析1.熟悉圆柱齿轮加工工艺过程的主要内容。
2.掌握圆柱齿轮加工工艺规程的编制方法。
二、课时分配本章共4个任务,本章安排4课时。
三、教学重点我们通过本项目的实施,了解轴类零件的结构特点。
了解套筒类零件加工中常见的工艺问题。
熟悉制定箱体工艺过程中应遵守的原则。
熟悉圆柱齿轮加工工艺过程的主要内容。
四、教学难点1.掌握轴类零件的加工工艺制定方法。
2.掌握轴承套零件的加工工艺分析方法。
3.掌握液压缸零件的加工工艺分析方法。
4.掌握箱体零件的加工工艺分析,重点注意小批量与大批量的加工工艺的区别。
5.掌握圆柱齿轮加工工艺规程的编制方法。
五、教学内容任务1轴类零件的加工工艺分析1.零件图样分析2.确定毛坯3.确定主要表面的加工方法4.确定定位基准5.划分阶段6.热处理工序安排7.加工尺寸和切削用量8.制定工艺过程任务2套筒类零件的加工工艺分析活动1轴承套加工工艺如图6-2所示的轴承套,其材料为ZQSn6-6-3,每批数量为200件。
图6-2轴承套1.轴承套的技术条件和工艺分析2.轴承套的加工工艺活动2液压缸加工工艺液压缸为典型的长套筒零件,与短套筒零件的加工方法和工件安装方式都有较大的差别。
1.液压缸的技术条件和工艺分析液压缸的材料一般有铸铁和无缝钢管两种。
如图6-3所示为用无缝钢管材料的液压缸。
为保证活塞在液压缸内移动顺利,对该液压缸内孔有圆柱度要求,对内孔轴线有直线度要求,内孔轴线与两端面间有垂直度要求,内孔轴线对两端支撑外圆(Φ82h6)的轴线有同轴度要求。
典型零件的数控铣削加工工艺讲解材料

确定零件在机床上的定位基准,以保 证加工精度和稳定性。通常选择零件 的重要表面或孔作为定位基准。
加工方法选择及切削用量确定
加工方法选择
根据零件的加工要求和机床性能,选择合适的加工方法,如铣削、钻孔、镗孔等。
切削用量确定
根据零件材料、刀具类型和机床性能等因素,确定合适的切削速度、进给量和切削深度等切削用量。
80%
Mastercam
具有强大的CAD/CAM功能,支 持2D、3D图形设计,提供多种 加工策略,适用于复杂零件的加 工。
100%
UG NX
集CAD/CAM/CAE于一体的高端 软件,具有灵活的建模、高效的 编程和精确的仿真功能。
80%
PowerMILL
专注于五轴加工、高速切削和多 轴机床编程,提供全面的加工策 略和刀具路径优化。
数控铣床的常见故障包括机械故障、电气故障、液压故障等,需要针对
不同故障类型采取相应的排查和处理措施。
02 03
故障排查方法
通过观察设备运行状态、听取异常声响、检查故障代码等方式,及时发 现并定位故障点。同时,利用专业检测仪器对设备进行详细检测,以便 更准确地找出故障原因。
处理技巧
根据故障原因,采取相应的处理措施,如更换损坏部件、调整设备参数、 清洗油路等。在处理过程中,要注意安全,避免对设备造成二次损坏。
箱体类零件
箱体类零件概述
箱体类零件是指具有复杂内腔和外形结 构的零件,如机床床身、汽车发动机缸 体等。
VS
加工特点
箱体类零件的加工需要综合考虑零件的刚 性、热变形等因素,选择合适的切削参数 和刀具。同时,还需要采用先进的加工技 术和工艺方法,如高速切削、复合加工等 ,以提高加工效率和质量。
典型零件机械加工工艺过程
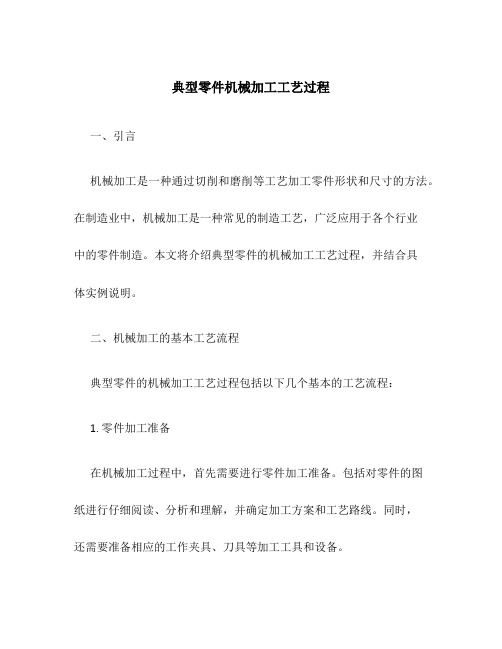
典型零件机械加工工艺过程一、引言机械加工是一种通过切削和磨削等工艺加工零件形状和尺寸的方法。
在制造业中,机械加工是一种常见的制造工艺,广泛应用于各个行业中的零件制造。
本文将介绍典型零件的机械加工工艺过程,并结合具体实例说明。
二、机械加工的基本工艺流程典型零件的机械加工工艺过程包括以下几个基本的工艺流程:1. 零件加工准备在机械加工过程中,首先需要进行零件加工准备。
包括对零件的图纸进行仔细阅读、分析和理解,并确定加工方案和工艺路线。
同时,还需要准备相应的工作夹具、刀具等加工工具和设备。
2. 零件装夹在机械加工过程中,零件装夹是一个非常关键的环节。
零件装夹的质量直接影响到加工的精度和效率。
根据零件的形状和结构,选择合适的夹具,并进行正确的装夹操作。
3. 加工工艺选择根据零件的特点和要求,选择合适的加工工艺,包括车削、铣削、钻削、刨削等。
针对不同的零件形状和材料特性,确定合适的刀具和切削参数,并进行加工工艺的选择。
4. 机床调试和加工在进行实际加工之前,需要进行机床的调试和测试。
确保机床的运转正常,并调整好各项加工参数。
然后,根据加工工艺选择,进行具体的加工操作,包括刀具路径的设定、加工速度的调整等。
5. 加工检测和调整在零件加工过程中,需要进行加工质量的检测和调整。
通过使用各种测量工具和设备,对加工后的零件进行尺寸和形状的检测。
如果不符合要求,需要及时进行调整和修正,以确保零件的加工质量。
6. 表面处理和组装完成零件的机械加工之后,还需要进行表面处理和组装。
包括去除零件表面的毛刺和氧化物,并进行必要的润滑和防护处理。
然后,根据具体的装配要求,对零件进行组装和调试。
三、案例分析为了更好地理解典型零件的机械加工工艺过程,我们以一款小型螺丝刀为例,进行具体的案例分析。
1.加工准备:仔细阅读零件图纸,了解零件的形状和加工要求。
根据图纸上的标注和尺寸要求,确定加工方案和工艺路线。
准备相应的夹具和刀具。
2.装夹:选择合适的夹具进行零件的装夹。
典型零件的加工工艺分析案例
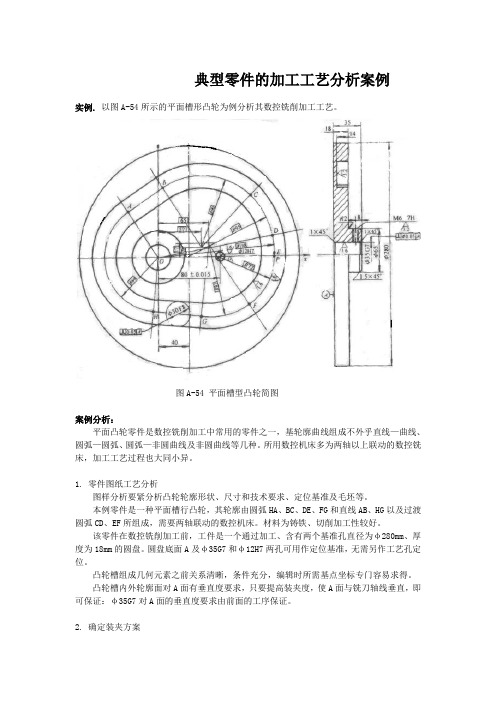
典型零件的加工工艺分析案例实例. 以图A-54所示的平面槽形凸轮为例分析其数控铣削加工工艺。
图A-54 平面槽型凸轮简图案例分析:平面凸轮零件是数控铣削加工中常用的零件之一,基轮廓曲线组成不外乎直线—曲线、圆弧—圆弧、圆弧—非圆曲线及非圆曲线等几种。
所用数控机床多为两轴以上联动的数控铣床,加工工艺过程也大同小异。
1. 零件图纸工艺分析图样分析要紧分析凸轮轮廓形状、尺寸和技术要求、定位基准及毛坯等。
本例零件是一种平面槽行凸轮,其轮廓由圆弧HA、BC、DE、FG和直线AB、HG以及过渡圆弧CD、EF所组成,需要两轴联动的数控机床。
材料为铸铁、切削加工性较好。
该零件在数控铣削加工前,工件是一个通过加工、含有两个基准孔直径为φ280mm、厚度为18mm的圆盘。
圆盘底面A及φ35G7和φ12H7两孔可用作定位基准,无需另作工艺孔定位。
凸轮槽组成几何元素之前关系清晰,条件充分,编辑时所需基点坐标专门容易求得。
凸轮槽内外轮廓面对A面有垂直度要求,只要提高装夹度,使A面与铣刀轴线垂直,即可保证:φ35G7对A面的垂直度要求由前面的工序保证。
2. 确定装夹方案一样大型凸轮可用等高垫块垫在工作台上,然后用压板螺栓在凸轮的孔上压紧。
外轮廓平面盘形凸轮的垫板要小于凸轮的轮廓尺寸,不与铣刀发生干涉。
对小型凸轮,一样用心轴定位,压紧即可。
依照图A-54所示凸轮的结构特点,采纳〝一面两孔〞定位,设计一〝一面两销〞专用夹具。
用一块320mm×320mm×40mm的垫块,在垫块上分别精镗φ35mm及φ12mm两个定位销孔的中心连接线与机床的x轴平行,垫块的平面要保证与工作台面平行,并用百分表检查。
图A-55为本例凸轮零件的装夹方案示意图。
采纳双螺母夹紧,提高装夹刚性,防止铣削时因螺母松动引起的振动。
图A-55凸轮装夹示意图3. 确定进给路线进给路线包括平面内进给和深度进给两部分路线。
对平面内进给,对外凸轮廓从切线方向切入,对内凹轮廓从过渡圆弧切入。
典型零件机械加工工艺与实例

典型零件机械加工工艺与实例一、引言在制造业中,机械加工是一项至关重要的工艺,它用于将原材料加工成各种形状和尺寸的零件。
典型零件机械加工工艺是指那些在机械加工过程中常见且广泛应用的工艺方法。
本文将探讨几种典型的零件机械加工工艺,并提供实例进行说明。
二、铣削加工铣削加工是一种常见的机械加工工艺,通过旋转刀具将工件上的材料切削掉,从而得到所需形状和尺寸的零件。
铣削加工可以分为平面铣削、立铣、端铣等多种形式。
2.1 平面铣削平面铣削是将刀具与工件平行或近似平行于工件表面进行切削的加工方式。
它适用于平面、凸轮槽、直齿轮等零件的加工。
平面铣削的实例包括制作平面底座、平面销轴等。
2.2 立铣立铣是将刀具与工件垂直或近似垂直于工件表面进行切削的加工方式。
它适用于开槽、钻孔、倒角等零件的加工。
立铣的实例包括制作键槽、孔加工等。
2.3 端铣端铣是将刀具与工件端面进行切削的加工方式。
它适用于平面、凹槽、凸齿轮等零件的加工。
端铣的实例包括制作平面销轴端面、齿轮端面等。
三、车削加工车削加工是通过旋转工件,并将刀具沿工件轴向移动,将工件上的材料切削掉的加工方式。
车削加工可分为外圆车削和内圆车削两种形式。
3.1 外圆车削外圆车削是将刀具与工件外表面接触,并进行切削的加工方式。
它适用于制作轴、销轴、螺纹等零件。
外圆车削的实例包括制作轴、销轴等。
3.2 内圆车削内圆车削是将刀具放置在工件内部,并进行切削的加工方式。
它适用于制作孔、内螺纹等零件。
内圆车削的实例包括制作孔、内螺纹等。
四、钻削加工钻削加工是通过旋转刀具,使刀具的尖端与工件接触,并将工件上的材料切削掉的加工方式。
钻削加工适用于制作孔、沉孔等零件。
4.1 钻孔钻孔是将刀具的尖端放置在工件上,并进行切削的加工方式。
它适用于制作各种规格和深度的孔。
钻孔的实例包括制作螺纹孔、沉孔等。
五、铣床加工铣床加工是一种常用的机械加工工艺,它通过铣刀在工件上进行切削,得到所需形状和尺寸的零件。
双主轴双刀塔车削中心上典型零件的加工
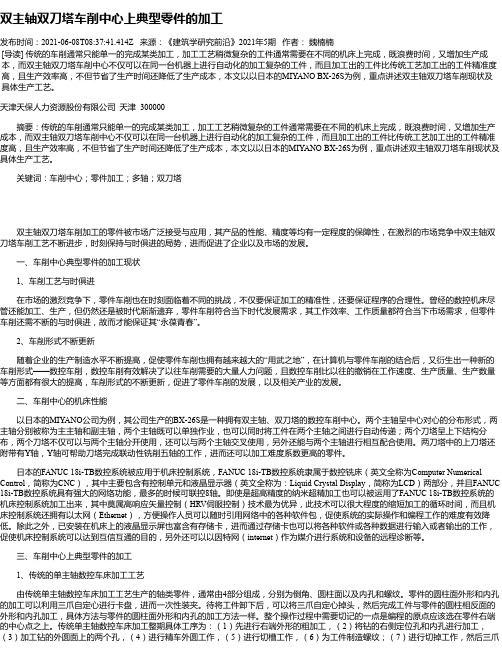
双主轴双刀塔车削中心上典型零件的加工发布时间:2021-06-08T08:37:41.414Z 来源:《建筑学研究前沿》2021年5期作者:魏楠楠[导读] 传统的车削通常只能单一的完成某类加工,加工工艺稍微复杂的工件通常需要在不同的机床上完成,既浪费时间,又增加生产成本,而双主轴双刀塔车削中心不仅可以在同一台机器上进行自动化的加工复杂的工件,而且加工出的工件比传统工艺加工出的工件精准度高,且生产效率高,不但节省了生产时间还降低了生产成本,本文以以日本的MIYANO BX-26S为例,重点讲述双主轴双刀塔车削现状及具体生产工艺。
天津天保人力资源股份有限公司天津 300000摘要:传统的车削通常只能单一的完成某类加工,加工工艺稍微复杂的工件通常需要在不同的机床上完成,既浪费时间,又增加生产成本,而双主轴双刀塔车削中心不仅可以在同一台机器上进行自动化的加工复杂的工件,而且加工出的工件比传统工艺加工出的工件精准度高,且生产效率高,不但节省了生产时间还降低了生产成本,本文以以日本的MIYANO BX-26S为例,重点讲述双主轴双刀塔车削现状及具体生产工艺。
关键词:车削中心;零件加工;多轴;双刀塔双主轴双刀塔车削加工的零件被市场广泛接受与应用,其产品的性能、精度等均有一定程度的保障性,在激烈的市场竞争中双主轴双刀塔车削工艺不断进步,时刻保持与时俱进的局势,进而促进了企业以及市场的发展。
一、车削中心典型零件的加工现状1、车削工艺与时俱进在市场的激烈竞争下,零件车削也在时刻面临着不同的挑战,不仅要保证加工的精准性,还要保证程序的合理性。
曾经的数控机床尽管还能加工、生产,但仍然还是被时代渐渐遗弃,零件车削符合当下时代发展需求,其工作效率、工作质量都符合当下市场需求,但零件车削还需不断的与时俱进,故而才能保证其“永葆青春”。
2、车削形式不断更新随着企业的生产制造水平不断提高,促使零件车削也拥有越来越大的“用武之地”,在计算机与零件车削的结合后,又衍生出一种新的车削形式——数控车削,数控车削有效解决了以往车削需要的大量人力问题,且数控车削比以往的撤销在工作速度、生产质量、生产数量等方面都有很大的提高,车削形式的不断更新,促进了零件车削的发展,以及相关产业的发展。
毕业论文(设计):典型零件加工工艺设计及加工

毕业设计(论文)任务书学生姓名学号所在系部机械工程系所学专业数控技术所在班级E-mail 联系电话毕业设计(论文)题目典型零件的加工工艺设计及加工指导教师职称工作单位及所从事专业联系方式姓名教授讲师本课题是根据高职数控技术专业教学计划选定的,旨在通过本课题的研究,使学生全面理解数控技术专业知识、掌握典型零件的工艺设计、如何确定工序、还有刀具、夹具及数控车床如何的选用。
帮助学生走上工作岗位时能尽快胜任工作。
专业方向、基本理论及设计内容(设计要求和设计步骤要求详细到章节):1、本课题的设立是典型零件的加工;2、基本理论依据是:数控加工工艺、机械基础和机械技术、金属切削原理与刀具、数控机床加工程序的编制;3、设计要求:通过轴类零件加工工艺分析设计设计,使我们在拟定工工艺分析方案过程中,得到方案分析、结构工艺性、机械制图、零件设计、编写技术文件和查阅技术资料的等方面的综合训练,树立正确的设计思想,掌握基本的设计方法,并培养学生具有初步的结构分析、结构设计与计算能力,并阐述了在机械加工实习课中如何对盖板零件进行工艺分析,从而提高工件质量。
5总结总结这次设计所遇到的问题,进一步提高自己的设计能力,动手能力,工艺的编制能力等主要参考文献、资料:1、刘战术主编.《数控机床及其维修》.人民邮电出版社出版2、荣维芝主编.《数控机床加工程序的编制》.机械工业出版社3、焦小明主编.《机械加工技术》.机械工业出版社4、田春霞主编.《数控加工技术》.机械工业出版社5、陈立德主编.《机械设计基础》.高等教育出版社6、周开勤主编.《机械零件手册》高等教育出版社7、刘力主编.《机械制图》.高等教育出版社出版8、《机床设计手册》编写组主编.《机床设计手册之零件设计》.机械工业出版社出版9、《数控机床编程及原理》.机械工业出版社出版10、《金属切削机床设计》.上海科学技术出版社教研室审批意见专业教研室主任签字:(盖章)系部审批意见系部主任签字:(盖章)目录摘要 (1)前言 (2)第一章、零件图样工艺分析1.1零件图的分析 (3)1.2零件结构工艺分析 (4)第二章、选择加工设备与刀、夹、量具2.1加工设备的选择 (5)2.2刀具的选择 (6)2.3夹具的选择 (7)2.4量具的选择 (8)第三章、数控车削加工的对刀3.1对刀的概念 (9)3.2确定对刀点或对刀基准点的一般原则 (10)第四章、加工工艺规程设计4.1加工顺序的安排 (11)4.2装夹方式 (12)4.3定位基准的选择 (13)第五章、切削用量的选择5.1切削深度的选择 (14)5.2进给量的选择 (15)第六章、工艺文件的填写6.1数控刀具卡 (17)6.2数控工序卡 (18)第七章、程序的编制7.1编程方法 (19)7.2编制程序 (22)第八章、心得体会 (25)总结 (25)参考文献 (26)摘要本零件在设计加工过程中分析了轴的特点及作用,介绍了轴的数控加工工艺设计与程序编制。
典型零件加工工艺分析

智能化加工技术
总结词
智能化加工技术是典型零件加工工艺的未来发展方向,它通过引入人工智能、机器学习等技术,实现 加工过程的自动化、智能化和柔性化。
详细描述
智能化加工技术包括智能调度、智能监测、自适应控制等技术。这些技术能够实时监测和调整加工过 程,提高加工过程的稳定性和可靠性,减少人为因素对加工结果的影响,进一步提高零件的加工质量 和效率。
典型零件的加工要求
精度要求
典型零件的加工精度要求较高, 需要达到一定的尺寸、形状和位 置精度。
表面质量要求
典型零件的表面质量对其性能和 使用寿命有重要影响,需要达到 一定的表面粗糙度要求。
加工效率要求
为了降低生产成本和提高生产效 率,典型零件的加工需要采用高 效、高精度的加工设备和工艺方 法。
02
详细描述
在工艺流程分析中,需要了解零件的加工顺序、各阶段的加工方法和所使用的 设备、工装等,同时对每个阶段的加工余量进行评估和控制,以确保最终的加 工质量和效率。
工艺参数分析
总结词
对典型零件加工过程中的各项工艺参数进行深入分析,包括切削用量、刀具参数、夹具 定位等。
详细描述
工艺参数分析是加工工艺中的重要环节,通过对切削速度、进给速度、背吃刀量等切削 用量的优化,以及对刀具材料、几何参数、切削液等的合理选择,可以提高加工效率、 降低能耗和减少刀具磨损。同时,夹具的定位和夹紧方式也需要根据零件的具体要求进
行合理设计。
工艺装备分析
总结词
对典型零件加工过程中所需的工艺装备进行全面分析,包括机床、刀具、夹具、量具等。
详细描述
工艺装备是实现零件加工的基础条件,通过对机床的性能参数、精度和可靠性进行分析,以及对刀具、夹具、量 具等的选用和调整,可以确保加工过程的稳定性和准确性。同时,还需要对工艺装备的维护和保养进行合理安排 ,以确保其长期使用效果。
典型零件加工与加工方法

了解典型零件加工与不同的加工方法对于制造业至关重要。本演示将介绍常 见的零件加工方法,并提供对典型零件加工的深入了解。
常见的零件加工方法
1 铣削
2 钻孔
通过使用切孔,以便安装螺栓 或其他组件。
3 精密车削
4 焊接
通过将工件放置在旋转刀具上,将切削工 具与工件接触,以削除材料并形成所需形 状。
将两个或多个工件加热到熔点,并通过熔 化金属填充材料,将它们结合在一起。
常见的典型零件加工
1轴
轴是一种常见的零件,通常用于传递转动运动,例如在机械和车辆中。
2 齿轮
齿轮是一种具有齿形的圆盘状零件,用于传递动力和控制运动。
3 锥齿轮
锥齿轮是一种带有斜面齿的齿轮,常用于传递旋转运动和改变轴的位置。
加工方法选择与优缺点对比
铣削
优点: - 适用于复杂形 状的零件 - 可以高效加工 大量工件
缺点: - 设备和工具成 本较高
钻孔
优点: - 快速且简单的 加工方法 - 适用于钻孔操 作的工件
缺点: - 只能用于单一 操作
精密车削
优点: - 可以实现高精 度的加工 - 适用于各种材 料缺点: - 加工速度较慢
焊接
优点: - 可将多个工件 牢固连接 - 适用于加工不 可切削材料
缺点: - 需要高温和特 殊设备
总结
典型零件加工涉及许多不同的加工方法和技术。选择合适的加工方法与零件 需求相匹配,可以提高产品品质和生产效率。
- 1、下载文档前请自行甄别文档内容的完整性,平台不提供额外的编辑、内容补充、找答案等附加服务。
- 2、"仅部分预览"的文档,不可在线预览部分如存在完整性等问题,可反馈申请退款(可完整预览的文档不适用该条件!)。
- 3、如文档侵犯您的权益,请联系客服反馈,我们会尽快为您处理(人工客服工作时间:9:00-18:30)。
(三)轴类零件的材料、毛坯及热处理 1、轴类零件的材料
轴类零件应根据不同工作条件和使用要求,选用 不同的材料和不同的热处理,以获得所需的强度、韧 性和耐磨性。 2、轴类零件的毛坯
轴类零件最常用的毛坯是圆棒料和锻件,只有某 些大型或结构复杂的轴(如曲轴),在性能允许时才采 用铸件。 3、轴类零件的热处理 轴的质量除与所选钢材种类有关外,还与热处理 有关。
图6-50
图6-51
第三节 箱体加工
一、概述 (一)箱体零件的功用与结构特点 箱体的种类很多,按箱体的功用,可分为主轴箱、 变速箱、操纵箱、进给箱等。
图6-52
(二)箱体零件的主要技术要求
图6-53
1、孔径精度
孔径的尺寸误差和形状误差会造成轴承与孔的配合不良。 2、孔的位置精度 同一轴线上各孔的同轴度误差和孔端面对轴线的垂直度 误差,影响轴和轴承装配到箱体内出现歪斜,会造成主轴径 向圆跳动和轴向圆跳动,也加剧了轴承磨损。 3、主要平面的精度 装配基准面的平面度影响主轴箱与床身连接时的接触刚 度,其在加工过程中常作为定位基准面时会影响孔的加工精 度,因此规定底面和导向面必须平直。 4、孔径精度
(4)次要表面加工顺序安排 主轴上的花键、键槽、螺纹、横向小孔等 次要表面加工,通常安排在外圆精车、粗磨之后 或精磨外圆之前进行。
(四)主轴的检验 检验的依据是主轴工作图。检验按一定的顺序进 行,先检验各段外圆的尺寸精度、素线平行度和圆度, 用外观比较法检验各表面的表面粗糙度及表面缺陷, 然后在专用检验夹具上测量位置偏差。
2、铣削螺纹
图6-30
3、磨削螺纹
4、滚轧螺纹
图6-31
图6-32
(四)丝杠的检验
图6-33
图6-34
七、轴类零件高效自动化加工
1、双主轴、双刀架卧式数控车床
图6-35
2、车铣复合加工中心
图6-36
第二节 套筒零件加工
一、概述 (一)套筒零件的功用与结构特点
图6-37
(二)套筒零件的技术要求 1、孔的技术要求
图6-47
3、内孔研磨 内孔研磨的原理与外圆研磨相同,孔研磨工艺的特点 也与外圆研磨类同,只是使用的研具有些区别。
4、内孔滚压(或挤压)
图6-48
孔的滚压加工原理与外圆滚压相同。由于滚压加工效 率高,近年来已采用滚压(或挤压)工艺来代替珩磨工艺。
图6-49
四、套筒零件高效自动化加工
随着先进制造技术发展,机械制造业面临技术升级,一 种新颖的“立式双主轴车削中心”很适合两个端面、内孔和 外圆均需加工的短套筒零件的高效自动化加工。 该车削中心是由一套正置数控立车加工单元和一套倒置 数控立车加工单元组合而成。两个加工单元的电气控制,采 用了具有极强网络功能的双通道CNC系统;工件上料采用上 料机械手3,加工工件在两个单元之间传送,配置有随行自 动卡盘6;每个加工单元配备了多刀位转塔动力刀架4和8; 还配套有自动上下料传送装置2和7,可实现全自动加工。
图6-54
2)大批量生产,采用顶面及两个销孔(一面两孔)作 定位基准面。
图6-55
(1)粗基准的选择
为保证重要加工面的余量均匀,箱体零件一般都选择 重要孔(如主轴孔)为粗基准,但随着生产类型不同, 实现以主轴孔为粗基准的工件装夹方式是不同的。 1) 中小批量生产时,由于毛坯精度较低,一般采用 划线找正。 2) 大批大量生产时,毛坯制造精度较高,可直接以 主轴孔在夹具上定位,采用专用夹具装夹,此类专用 夹具可参阅机床夹具图册。
达2~12mm)和缓慢的进给速度进行磨削,也称为蠕
动磨削或深磨。
图6-6
(4)高效深磨 高效深磨:高效深磨可直观地看成是缓进给 磨削和超高速磨削的结合。
(5)砂带磨削 砂带磨削:它是用涂满砂粒的环状布带(即 砂带)作为切削工具的一种加工方法。
图6-7
图6-8
(6)宽砂轮磨削和多片砂轮磨削 宽砂轮磨削和多片砂轮磨削的实质就是增加 砂轮宽度。
图6-22
五、曲轴加工的工艺特点
(一)概述 1、曲轴的功用和结构特点
曲轴是将直线运动转变成旋转运动,或将旋转运动 变成直线运动的零件。
2、曲轴的主要技术要求 3、曲轴的材料与毛坯 曲轴工作时要承受很大的转矩及交变的弯曲应力, 容易产生扭振、折断及轴颈磨损,因此选取材料应 有较高的强度、冲击韧性、疲劳强度和耐磨性。
二、箱体机械加工工艺过程及工艺分析
(一)箱体零件机械加工工艺过程 箱体零件的结构复杂,要加工的部位多,依批量大 小和各企业的实际条件,其加工方法是不同的。 (二)箱体零件机械加工工艺过程分析 1、定位基准的选择 (1)精基准的选择
箱体加工精基准的选择与生产批量大小有关。
1)单件小批生产,用设计基准作定位基准。
第六章 典型零件加工与加工方法
第一节 第二节 第三节 第四节 第五节 第六节 轴类零件加工 套筒零件加工 箱体加工 圆柱齿轮加工 活塞加工 连杆加工
第一节 轴类零件加工
一、概述
(一)轴类零件的功用与结构特点
图6-1
(二)轴类零件的技术要求
1、尺寸精度 2、形状精度 3、位置精度 4、表面粗糙度
图6-2
(二)曲轴加工的工艺特点
图6-23
1、主要工艺过程
其主要阶段有:
1)加工中心孔→粗、精车主轴颈。
2)粗、精磨主轴颈→铣角度定位平台→车连杆轴颈 →加工一些次要表面→中间检查。
3)中频淬火→半精磨主轴颈。 4)粗、精磨连杆轴颈。 5)精磨主轴颈→铣键槽。
6)两端孔加工→动平衡→超精加工主轴颈和连杆轴 颈→最终检查。
(三)箱体材料及毛坯 箱体毛坯制造方法有两种:一种是铸造,另一种 是焊接。对金属切削机床的箱体,由于形状较为复杂, 而铸铁具有成形容易、可加工性良好、吸振性佳、成 本低等优点,所以一般都采用铸铁。对于动力机械中 的某些箱体及减速器壳体,除要求结构紧凑、形状复 杂外,还要求体积小、重量轻,所以可采用铝合金压 铸;压铸毛坯因其不易产生缩孔和缩松应用十分广泛。 对于承受重载和冲击的工程机械、锻压机床的箱体, 可采用铸钢件或钢板焊接。某些简易箱体为了缩短毛 坯制造周期,也常采用钢板焊接而成,但焊接件的残 余应力较难消除干净。
图6-4
三、外圆表面的精加工和光整加工 (一)外圆表面的磨削加工方法 1、常见的外圆磨削方法 常见的外圆磨削方法有两种:中心磨削法、无心磨 削法。 中心磨削法,是以工件轴线为回转中心的磨削
方法。
无心磨削法,工件轴心处于自由状态,是以被磨削 的外圆表面定位,属于自位基准定位的加工方法
2、提高磨削精度和生产率的方法
图6-9
(7)点磨削
点磨削:点
磨削是在精磨工序中
以点接触方式对外圆
进行高速磨削。
图6-10
图6-11
(二)外圆表面的光整加工方法
1、研磨
图6-12
2、抛光
抛光与研磨方法类似,是用手工或在抛光机、砂带 磨床上进行的一种光整加工方法。
3、超精加工
图6-13
超精加工切削过程分为四个阶段:
2、外圆表面的技术要求
3、孔与外圆的同轴度要求 4、孔轴线与端面的垂直度要求
图6-38
(三)套筒零件的材料与毛坯
二、套筒零件加工工艺过程与工艺分析 (一)套筒零件加工工艺过程 (二)套筒零件加工工艺过程分析 1、定位基准的选择——保证套筒表面位置精度的方法 液压缸内、外表面轴线的同轴度以及端面与孔轴线 的垂直度要求较高,若能在一次安装中完成内、外表面 及端面的加工,则可获得很高的位置精度。 2、防止加工中套筒变形的措施
二、轴类零件加工工艺过程与工艺分析
(一)主轴的技术条件分析 (二)卧式车床主轴加工工艺过程
(三)卧式车床主轴加工工艺过程分析
1、定位基准的选择与转换
图6-3
2、工序顺序的安排
(1)加工阶段划分 对主轴加工阶段的划分大体如下:①荒加 工阶段为准备毛坯;②正火后,粗加工阶段为铣 端面、钻中心孔、粗车外圆;③调质处理后,半 精加工阶段是半精车外圆、端面、锥孔;④表面 淬火后,精加工阶段是主要表面的精加工,包括 粗、精磨各级外圆、精磨支承轴颈、锥孔。 各阶段的划分大致以热处理为界。整个主 轴加工的工艺过程,就是以主要表面(特别是支承 轴颈)的粗加工、半精加工和精加工为主线,穿插 其他表面的加工工序组成。
提高磨削生产率大体有两条途径:一是缩短辅助时 间;二是改变磨削用量以及增大磨削面积。
(1)高精度磨削
高精度磨削:使工件的表面粗糙度Ra值在 0.16μ m以下的磨削方法,称为高精度磨削。
图6-5
(2)高速磨削 高速磨削:它是指砂轮线速度高于50m/s的 磨削加工。
(3)深切缓进给磨削 深切缓进给磨削:它是以很大的背吃刀量(可
2)金相组织要有较高的稳定性,以保证丝杠在长期使 用中不丧失原有的精度。
3)具有良好的热处理工艺性(淬透性好、热处理变形小、不易产生裂纹),并能获得较高的硬度、良好的 耐磨性。 4)应有良好的加工性,易切削、不易发生粘刀或啃刀。
(二)丝杠加工的工艺特点
图6-29
(三)丝杠螺纹加工方法 1、车削螺纹
图6-16
(3)用硬质合金顶尖修研 (4)用中心孔磨床磨削中心孔
图6-17 图6-18
(二)锥孔磨削方法 1、研磨 主轴锥孔对主轴支承轴颈的径向圆跳动,是机床的 主要精度指标之一,因此锥孔加工是关键工序。
图6-19
(三)花键加工方法
1、花键的铣削加工
图6-20
图6-21
2、花键的磨削加工
(2)外圆表面的加工顺序
应先加工大直径外圆,然后加工小直径外 圆,以免一开始就降低了工件的刚度。